深切缓进给强力成形磨削的特点及磨削缺陷和防止措施
各种磨削加工特点介绍
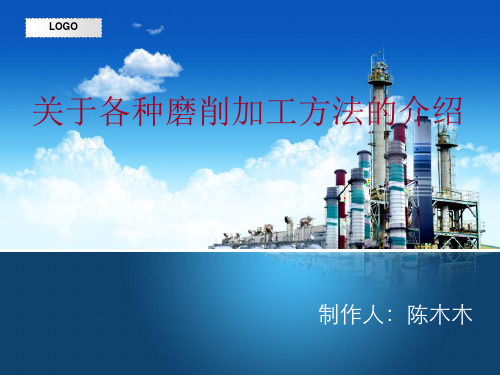
磨削方法:纵磨法和横磨法
纵磨法:加工精度高,Ra值较小,生产 率低,广泛用于各种类型的生 产中;
横磨法:加工精度低,Ra值较大,生产 率高,只适用于大批量生产中 磨削刚度较好、精度较低、长 度较短的轴类零件上的外圆表 面和成形面。
加工方法:周磨法、端磨法(磨平面)
①周磨法:加工精度高,表面粗糙度Ra值小, 但生产率较低,多用于单件小批生产中,大 批大量生产中亦可使用。 ②端磨法:生产率较高,但加工质量略差于周 磨法,多用于大批大量生产中磨削精度要求 不太高的平面。
恒力磨削
横磨法的特殊形式。磨削时,无 论外界因素如磨削余量、工件材料硬 度、砂轮钝化程度等如何变化,砂轮 始终以预定的压力压向工件,直到磨 削结束为止。
恒压力磨削加工质量稳定,生产 率高,避免砂轮超负荷工作,操作安 全。
宽砂轮与多砂轮磨削
宽砂轮磨削是用增大磨削宽度来提 高磨削效率的。 宽砂轮外圆磨削采用横磨法,主要 用于大批量生产中,如磨削花键轴、 电机轴等。尺寸公差等级可达IT6,Ra 值可达0.4 μ m。 多砂轮磨削是宽砂轮磨削的另一种 形式。主要用于大批量生产中外圆和 平面的磨削。
各种表面:内外圆表面、圆锥面、平面、齿面、螺旋面 各种材料:普通塑性材料、铸件等脆材、淬硬钢、硬质 合金、宝石等高硬度难切削材料。
(3)磨削速度高、耗能多,切削效率低,磨削温度 高,工件表面易产生烧伤、残余应力等缺陷。 (4)砂轮有一定的自锐性。
LOGO
多砂轮磨削
砂带磨削
定义:利用砂带,根据加工要求以相应 的接触方式对工件进行加工的方 法称为砂带磨削。是一种新型高 效工艺方法。 特点:效率高、磨削热少,散热条件好。 砂带磨削的工件,其表面变形强 化程度和残余应力均大大低于砂 轮磨削。
磨削的工艺特点及应用范围

磨削的工艺特点及应用范围磨削是一种通过将磨料与工件接触并相对运动,以去除工件表面的材料来达到加工目的的工艺。
它是机械加工中常用的一种精密加工工艺,具有以下几个特点和应用范围。
首先,磨削具有高精度的特点。
由于磨削采用磨料的物理磨损作用,能够在工件表面形成较高的精度和光洁度。
这使得磨削可以在高要求的部件上进行加工,如模具、精密仪器零部件等。
其次,磨削具有高表面质量的优势。
由于磨削可产生微细破碎和位移切削,所以能够在工件表面形成比较光滑及均匀的表面。
磨削加工可将工件表面粗糙度控制在很低的范围内,以满足高精度零部件的要求。
第三,磨削可以加工各种材料。
由于磨料多种多样,几乎可以加工所有的工程材料,如钢、铸铁、有色金属、陶瓷、石材等。
而且磨削还可以加工硬度高、韧性好的材料,如硬质合金、高速钢等。
因此,磨削具有广泛的应用范围。
第四,磨削是一种高效率的加工方法。
尽管磨削是一种相对慢速的金属切削方式,但具有高的切削效率。
这是由于磨削通过很薄的材料去除率来实现加工,而它的单位材料去除率比其他加工方法要高得多。
此外,磨削可以实现连续加工,大大提高了生产效率。
第五,磨削可以加工各种形状的工件,如平面、曲面、孔等。
通过不同形状的磨具和磨料,可以加工出各种不同形状和精度要求的工件。
并且,由于磨削是一种柔性的加工方法,它可以根据加工需要进行不同的修整,以满足不同的要求。
最后,磨削还可以改善材料的机械性能和表面质量。
通过磨削可以降低材料的表面硬度和残余应力,从而提高材料的疲劳寿命和抗腐蚀性能。
此外,磨削还可以消除工件的加工硬化层,提高工件的尺寸精度和表面质量。
总之,磨削是一种高精度、高效率、多功能的加工方法。
它在航空航天、汽车、机床制造、电子仪器、模具制造等领域广泛应用。
在未来,随着科学技术的不断发展,磨削将更加趋向智能化,更好地满足不同领域对于精密加工的需求。
磨削缺陷分析与解决

磨削缺陷分析与解决1.产生原因及影响因素零件的磨削精度指零件在磨削加工后,其形状、尺寸及表面相互位置三方面与理想零件的符合程度。
一般说来,形状精度高于尺寸精度,而位置精度也应高于尺寸精度。
磨削加工中的误差主要来源与两方面。
一是磨床-夹具-砂轮组成的工艺系统本身误差;二是磨削过程中出现的载荷和各种干扰:包括力变形、热变形、振动、磨损等引起的误差。
而在磨削过程中,使砂轮与工件位置改变以降低磨削精度的主要原因有:⑴.由磨削力引起的磨床和工件弹性变形;⑵.磨床和工件的热变形;⑶.磨床和工件的振动;⑷.砂轮磨损后其形状、尺寸变化;⑸.工装、夹具的损坏或变形;⑹.导轨、轴承和轴等部件的非弹性变形。
其中磨削过程中的弹性变形是主要的影响因素,它会使砂轮的实际切入深度与输入切入深度不一致,这一变化是由“砂轮架—砂轮轴承-砂轮轴-工件-工件支承”的弹性系统刚性决定。
一般为消除这种原因带来的误差常在行程进给磨削后,停止相互间的进给,仅依靠弹性回复力维持磨削,即光磨阶段(又叫清火花磨削),从而消除残留余量。
当然造成磨削误差的其它因素液很多如:工件磨削形状误差,工件热变形,磨粒切刃引起的塑性变形,砂轮的磨损等。
2.对工件的影响:降低工件使用寿命;降低工件抗疲劳强度;特殊特性的尺寸精度误差易影响工件使用,如轴承孔尺寸的控制,尺寸过小,安装不到轴上;过大,易引起振动,影响轴承使用寿命等。
3.解决方法:增加系统刚性;减少上工序加工留量,以减小磨削厚度,从而减小磨削力降低残留应力;增加光磨时间;及时修整砂轮,及时检查工装、夹具、轴承完好性及电主轴的振动性等;精细的选择砂轮,如挑选细粒度,硬度较大,组织稍紧密的砂轮;选用导热性好的砂轮(如CBN 砂轮);采用冷却性能优良的磨削液以减少因热变形引起的误差。
二、工件表面粗糙度1.产生原因及影响因素表面粗糙度指加工表面具有较小间距和峰谷所组成微观几何形状特征。
它是大量磨粒在工件表面进行切削后留下的微观痕迹的集合。
磨削有哪些原理特点
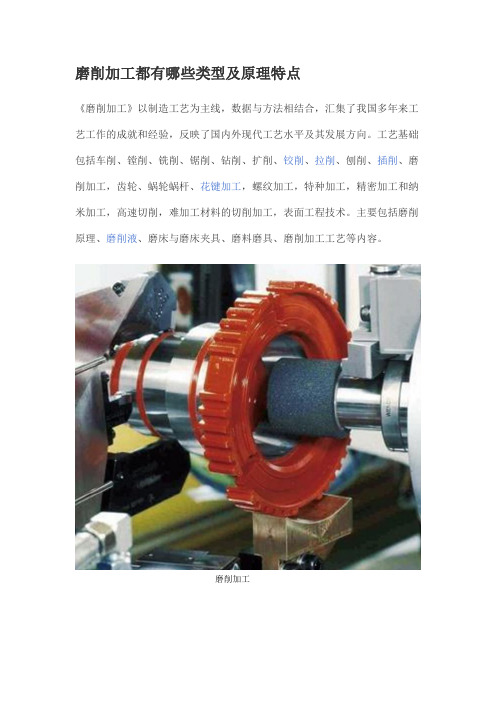
磨削加工都有哪些类型及原理特点《磨削加工》以制造工艺为主线,数据与方法相结合,汇集了我国多年来工艺工作的成就和经验,反映了国内外现代工艺水平及其发展方向。
工艺基础包括车削、镗削、铣削、锯削、钻削、扩削、铰削、拉削、刨削、插削、磨削加工,齿轮、蜗轮蜗杆、花键加工,螺纹加工,特种加工,精密加工和纳米加工,高速切削,难加工材料的切削加工,表面工程技术。
主要包括磨削原理、磨削液、磨床与磨床夹具、磨料磨具、磨削加工工艺等内容。
磨削加工磨削加工1、外圆磨削主要在外圆磨床上进行,用以磨削轴类工件的外圆柱、外圆锥和轴肩端面。
磨削时,工件低速旋转,如果工件同时作纵向往复移动并在纵向移动的每次单行程或双行程后砂轮相对工件作横向进给,称为纵向磨削法。
如果砂轮宽度大于被磨削表面的长度,则工件在磨削过程中不作纵向移动,而是砂轮相对工件连续进行横向进给,称为切入磨削法。
一般切入磨削法效率高于纵向磨削法。
如果将砂轮修整成成形面,切入磨削法可加工成形的外表面。
2、内圆磨削主要用于在内圆磨床、万能外圆磨床和坐标磨床上磨削工件的圆柱孔、圆锥孔和孔端面。
一般采用纵向磨削法。
磨削成形内表面时,可采用切入磨削法。
在坐标磨床上磨削内孔时,工件固定在工作台上,砂轮除作高速旋转外,还绕所磨孔的中心线作行星运动。
内圆磨削时,由于砂轮直径小,磨削速度常常低于30米/秒、耐磨性是普通砂轮的20-100倍,极大的减少了砂轮的修正及更换频率。
3、平面磨削主要用于在平面磨床上磨削平面、沟槽等。
平面磨削有两种:用砂轮外圆表面磨削的称为周边磨削,一般使用卧轴平面磨床,如用成形砂轮也可加工各种成形面;用砂轮端面磨削的称为端面磨削,一般使用立轴平面磨床。
4、无心磨削一般在无心磨床上进行,用以磨削工件外圆。
磨削时,工件不用顶尖定心和支承,而是放在砂轮与导轮之间,由其下方的托板支承,并由导轮带动旋转。
当导轮轴线与砂轮轴线调整成斜交1°~6°时,工件能边旋转边自动沿轴向作纵向进给运动,这称为贯穿磨削。
简述磨削的加工特点及加工范围

简述磨削的加工特点及加工范围
磨削是一种使用磨料进行切削加工的工艺,具有以下几个特点:1. 精度高:由于磨料的有机结构,磨削可以获得非常高的加工精度和表面质量。
2. 表面质量好:磨削可以得到较光滑的表面质量,无需进行额外的调整和磨光。
3. 切削力小:由于磨料颗粒的独立切削作用,磨削的切削力较小,有利于提高切削效率和延长刀具寿命。
4. 适应性强:磨削适用于各种硬度和材料的加工,包括金属、非金属、薄膜、陶瓷等。
5. 可广泛应用于精密加工:磨削常用于精密零件的加工,如轴承、汽车传动零件、空气动力部件等。
磨削的加工范围包括:
1. 尺寸精度要求高的大型工件:磨削可以保证大工件的尺寸精度和表面质量。
2. 复杂形状、高精度的工件:磨削可以对复杂形状和高精度要求的工件进行加工,如曲线曲面、螺纹等。
3. 高硬度材料的零件:磨削适用于处理高硬度材料,如硬质合金、陶瓷等。
4. 无法使用其他加工方法的材料和零件:对于一些特殊材料和形状复杂的零件,磨削可以是唯一的加工选择。
5. 高表面质量要求的工件:磨削可以获得非常好的表面质量,适用于有高表面质量要求的工件,如光学元件、模具等。
磨削加工的特点(新版)
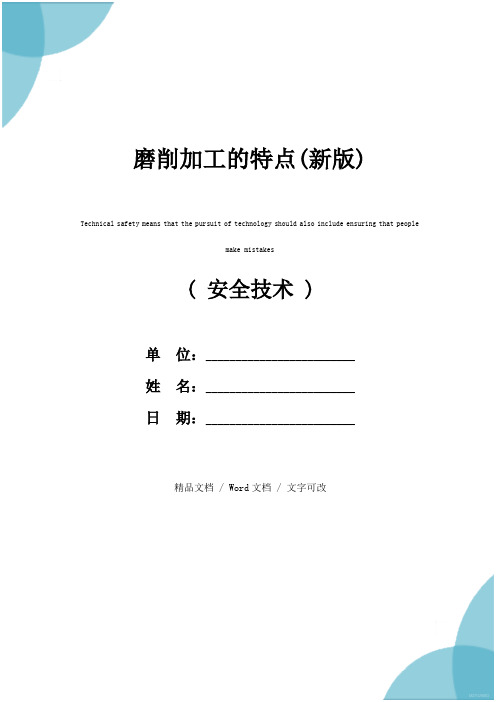
( 安全技术 )单位:_________________________姓名:_________________________日期:_________________________精品文档 / Word文档 / 文字可改磨削加工的特点(新版)Technical safety means that the pursuit of technology should also include ensuring that peoplemake mistakes磨削加工的特点(新版)磨削加工是借助磨具的切削作用,除去工作表面的多余层,使工件表面质量达到预定要求的加工方法。
进行磨削加工的机床称为磨床。
磨削加工应用范围很广,通常作为零件(特别是淬硬零件)精加工工序,可以获得很高的加工精度和表面质量,可以用于粗加工、切割加工等。
从安全角度来看,磨削加工有以下特点:1、磨具的运转速度高。
普通磨削可达30-50m/s,高速磨削可达45-60m/s甚至更高,其速度还有日益提高的趋势。
2、磨具的非均质结构。
磨具是由磨料,结合剂和气孔三要素组成的复合结构,其结构强度大大低于由单一均匀才智组成的一半金属切削刀具。
3、磨削的高热现象。
磨具的高速运动、磨削加工的多刃性和微量切削,都会产生大量的磨削热,不仅可能烧伤工件表面,而且高温时磨具本身发生物理、化学变化、产生热反应力、降低磨具的强度。
4、磨具的自砺现象。
在磨削力度作用下,磨钝的磨粒自身脆裂或脱落的现象,称为磨具的自砺性。
磨削过程中的磨具自砺作用以及修正磨具的作业,都会产生大量磨削粉尘。
云博创意设计MzYunBo Creative Design Co., Ltd.。
辊磨削工艺与常见磨削缺陷控制方法

轧辊磨削工艺与常见磨削缺陷控制摘要:本文通过对磨床磨削的基本原理及加工特点,轧辊磨床的基本结构与运动方式,磨床的冷却与润滑及轧辊磨削工艺等方面的阐述,分析了轧辊磨削中常见缺陷的原因并提出预防措施。
关键词:轧辊磨削工艺缺陷控制1 .磨床磨削的基本原理及加工特点1.1磨削的基本原理磨削是金属切削加工方法之一,它是以砂轮切入工件,从而得到一定的儿何形状、尺寸精度和表面光洁度较高的零件。
磨削的基本原理:以极高速度旋转的砂轮作为刀具,切入以一定速度旋转或移动的工件中,砂轮的磨粒在工件表面强烈而高速的旋转(每一磨粒完成一次切削时间只有万分之几秒),强行擦过工件,挤压表面,磨削力使工件材料发生弹性变形和塑性变形,材料组织发生内部相对移动,此间产生极高的切削温度,锋利的磨粒迫使材料脱离工件,形成切屑。
1.2磨削加工的特点磨削加工得到极广泛的应用,它有以下的特点:1)磨削加工可以获得很高的精度和表面光洁度。
一般磨床可以达到1~2级精度,表面光洁度可达到▽7~▽10,高精度的磨削光洁度可达到▽12,精度可达到0.002毫米。
2)可以加工材料范围宽。
可加工软材料,如铸铁、有色金属等,还可以加工淬火钢,如CrMn钢、T12钢、20钢经渗炭淬火等,而且可以加工硬质合金。
3)磨削加工用于精加工过程中。
磨削加工的切削深度较小,在一次行程中所能切去金属层较薄,因此只能用精加工过程中。
2. 轧辊磨床的基本结构与磨床磨削运动2.1 轧辊磨床的基本结构用于对轧辊进行成形磨削的磨床即是轧辊磨床。
轧辊磨床是外圆磨床的一个分支,是一种专用磨床。
轧辊磨床一般为轧辊移动式,其基本结构由床身、头架、尾座、砂轮架、主轴、冷却液系统和电控设备等组成。
1)床身床身是保证磨削精度的基础。
轧辊磨床,其床身用来支承轧辊,砂轮架是固定的。
2)头架用来驱动轧辊,为保证驱动的平稳性和减震,一般采用多级皮带传动。
3)尾座尾座由上下两部分组成,下部延床身移动,上部可横向移动,以使两顶尖联机与砂轮轴线平行。
简述磨削的工艺特点

简述磨削的工艺特点磨削是一种常见的金属加工工艺,用于将工件的表面进行细磨、精磨和抛光,以达到提高工件精度和表面质量的目的。
磨削的工艺特点主要包括以下几个方面:1. 磨削具有高精度和高表面质量的特点。
相比于其他金属加工工艺,磨削可以实现更高的加工精度,达到更高的表面质量要求。
磨削可以将工件的精度提高到数微米甚至亚微米级别,使得工件表面光洁度达到较高的要求。
2. 磨削具有广泛的适用性。
磨削可以适用于各种形状的工件,包括平面、曲面、圆柱面、锥面等。
而且,磨削可以加工各种不同材料的工件,如钢、铸铁、铜、铝、塑料等。
这使得磨削成为一种非常常用的金属加工工艺。
3. 磨削可以实现高效率的加工。
尽管磨削相对于其他加工工艺来说,加工速度较慢,但是磨削可以同时进行多个工件的加工,从而提高了加工效率。
此外,磨削切削速度较低,磨削过程中不会产生较高的切削温度,从而减少了工件的热变形和残余应力。
4. 磨削可以实现较高的加工精度。
通过磨削工艺,可以实现工件的高精度要求。
磨削过程中,磨削刀具的尺寸几乎不会发生变化,因此可以保证工件的尺寸精度。
同时,磨削可以去除工件表面的氧化皮、毛刺等缺陷,提高工件的表面质量。
5. 磨削可以改善工件的机械性能。
磨削可以消除工件表面的残余应力,并提高工件的表面硬度。
此外,通过磨削可以改善工件的耐磨性、抗疲劳性和抗腐蚀性能,提高工件的使用寿命。
总结起来,磨削作为一种常见的金属加工工艺,具有高精度、高表面质量、广泛适用、高效率、高加工精度和改善机械性能的特点。
在实际的工程应用中,磨削工艺被广泛应用于各个行业,如航空航天、汽车制造、机械制造等领域。
磨削工艺的发展也为工件的加工质量提升和工艺效率提高提供了有效的手段。
强力成形磨削概述及我国强力成形削的发展与应用(一)
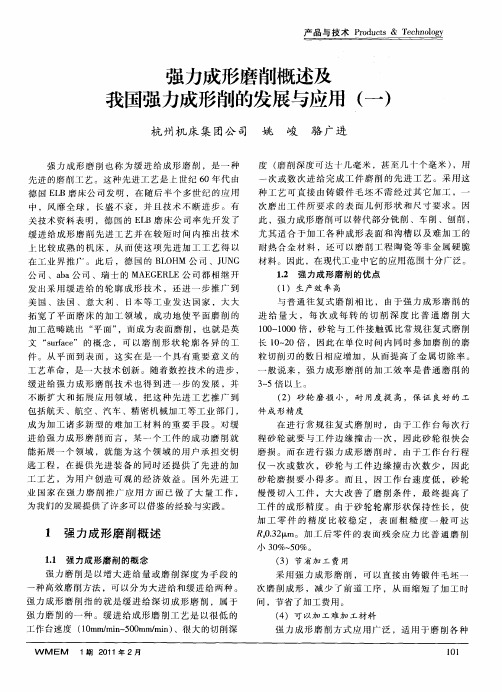
文 “ufc ” 的 概 念 ,可 以磨 削 形 状 轮 廓 各 异 的 工 sr e a
件 。从 平 面 到表 面 ,这 实 在 是一 个 具 有 重 要 意 义 的
工艺 革命 ,是 一 大技术 创 新 。随 着数 控技 术 的进 步 ,
缓 进 给 强 力成 形 磨 削 技 术也 得 到进 比 ,由 于强 力 成 形 磨 削 的 进 给 量 大 ,每 次 或 每 转 的切 削 深 度 比 普 通 磨 削 大 10 1 0 0 ~ 0 0倍 ,砂轮 与 工 件 接触 弧 比常 规往 复 式 磨 削 长 1 ~ 0倍 ,因此 在 单 位 时 间 内 同 时参 加 磨 削 的磨 02 粒切 削 刃 的数 目相 应增 加 ,从 而提 高 了金 属切 除率 。
小 3 %~ 0 。 0 5%
为我们 的发展 提供 了许多 可 以借鉴 的经验 与实践 。
强 力成 形磨 削概 述
11 强力成 形磨 削的概念 . 强 力 磨 削 是 以增 大 进 给 量 或磨 削 深度 为手 段 的
一
( )节省加 工 费用 3
采 用 强力 成 形 磨 削 ,可 以 直 接 由铸 锻 件 毛 坯 一 次 磨 削 成形 ,减 少 了前 道 工 序 ,从 而缩 短 了加 工 时
般 说 来 ,强 力 成 形 磨 削 的加 工 效 率 是 普 通 磨 削 的
( ) 砂 轮 磨 损 小 , 耐 用 度 提 高 , 保 证 良 好 的 工 2
3 5倍 以上 。 ~
件 成 形 精 度
不断 扩 大 和拓 展 应 用 领 域 ,把 这种 先 进 工 艺 推 广 到 包 括航 天 、航 空 、汽 车 、精密 机 械加 工等 工业 部 门 ,
磨削烧伤、磨削裂纹及控制措施
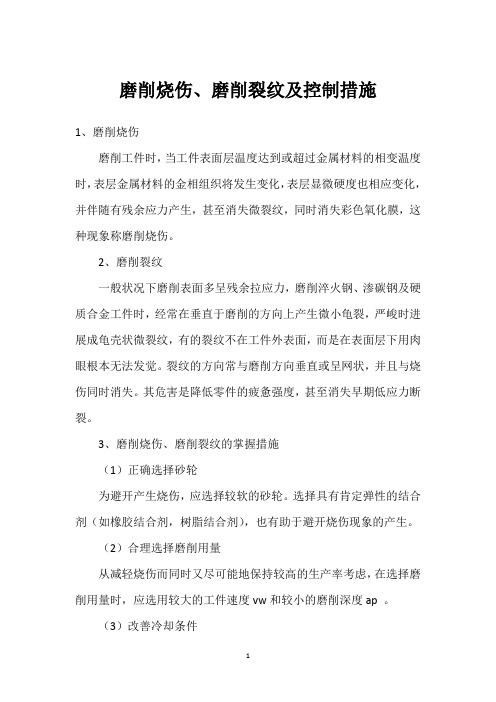
磨削烧伤、磨削裂纹及控制措施1、磨削烧伤磨削工件时,当工件表面层温度达到或超过金属材料的相变温度时,表层金属材料的金相组织将发生变化,表层显微硬度也相应变化,并伴随有残余应力产生,甚至消失微裂纹,同时消失彩色氧化膜,这种现象称磨削烧伤。
2、磨削裂纹一般状况下磨削表面多呈残余拉应力,磨削淬火钢、渗碳钢及硬质合金工件时,经常在垂直于磨削的方向上产生微小龟裂,严峻时进展成龟壳状微裂纹,有的裂纹不在工件外表面,而是在表面层下用肉眼根本无法发觉。
裂纹的方向常与磨削方向垂直或呈网状,并且与烧伤同时消失。
其危害是降低零件的疲惫强度,甚至消失早期低应力断裂。
3、磨削烧伤、磨削裂纹的掌握措施(1)正确选择砂轮为避开产生烧伤,应选择较软的砂轮。
选择具有肯定弹性的结合剂(如橡胶结合剂,树脂结合剂),也有助于避开烧伤现象的产生。
(2)合理选择磨削用量从减轻烧伤而同时又尽可能地保持较高的生产率考虑,在选择磨削用量时,应选用较大的工件速度vw和较小的磨削深度ap 。
(3)改善冷却条件① 采纳高压大流量法此法不但可以增加冷却作用,而且也增加了对砂轮的冲洗作用,使砂轮不易堵塞。
② 安装带空气挡板的喷嘴此法可以减轻高速回转砂轮表面处的高压附着气流作用,使磨削液能顺当喷注到磨削区。
③ 采纳磨削液雾化法或内冷却法采纳特地装置将磨削液雾化,使其带走大量磨削热,增加冷却效果;也可采纳内冷却砂轮,其工作原理如图所示。
经过严格过滤的磨削液由锥形套1经空心主轴法兰套2引入砂轮的中心腔3内,由于离心力的作用,磨削液经由砂轮内部有径向小孔的薄壁套4的孔隙甩出,直接浇注到磨削区。
图内冷却砂轮结构1-锥形盖2-主轴法兰套3-砂轮中心腔4-薄壁套。
数控深切削缓进给磨床的设计(纵向和横向进给机构部分)说明书(已处理)

数控深切削缓进给磨床的设计(纵向和横向进给机构部分)说明书学号: 24091900276南湖学院毕业设计题目数控深切削缓进给磨床的设计(纵向和横向进给机构部分)作者届别2013届系别机械与电子工程系专业机械设计制造及其自动化指导老师职称副教授完成时间 2013年5月20日摘要本文是对数控深切削缓进给成型磨床的纵向和横向进给机构部分进行设计。
本设计课题以广西桂林广陆量具厂生产的数显游标卡尺为加工对象。
本设计的磨床采用机电一体化设计原理,通过采用CBN砂轮,缓进给工艺,数控系统等措施保证加工精度。
在本磨床的数控系统中,以8051单片机为核心,利用I/O输入输出设备,通过步进电机实施对工作台的自动调整和控制。
本课题通过键盘对工作台的移动直线距离进行控制,提高了系统控制的准确性,稳定性;采用光电隔离技术,提高了系统的抗干扰能力;采用步进电机进行控制,使系统工作平稳,同时大大缩减了系统调节时间。
关键词:数控;深切削;缓进给;磨床;设计AbstractThis paper introduced design principle for the longitudinal feed and cross feed mechanism of a numerical control deep cutting slow-feed shaping grinding machine. The design issues to Guilin, Guangxi Lu Guang Measuring Tool Factory production of digital vernier caliper target for processing.The grinding machine adopt electro-mechanics’ integrating design principle and guarantee the machining precision through introducing the grinding wheel of CBN, slow-feed craft and numerical control system, etc. Regard chip microcomputer 80C51 as the core in the numerical control system of the grinding machine, utilize I/O equipmentand realize the worktable auto-conditioning through controlling step motor.This issue through the keyboard on the table straight from the mobile control and improve the accuracy of the system control, stability; improve the accuracy controlled and stability; Adopting photoelectric isolation technology, improve systematic anti-interference ability; Introducing the step motor to control, make the system work steadily and shorten systematic regulation time greatly at same time.Keywords: numerical control; deep cutting; slow-feed; grinding machine; design目录第一章综述 11.1课题来源 11.2 缓进给磨削技术 11.3 缓进给磨削机理 51.3.1 砂轮与工件的接触长度与接触时间 5 1.3.2 磨削力 51.4 超精密砂轮磨削技术 6第二章磨床总体布局设计72.1 加工要求72.2 机床简介72.3 技术规格72.3.1 主要规格72.3.2 加工范围72.3.3 工作台72.3.4 磨头82.3.5 冷却和清洁系统82.3.6 电动机总功率82.4 工作精度82.4.1 尺寸精度82.4.2 表面粗糙度 82.5 特殊附件82.5.1 专用砂轮82.5.2 专用夹具82.5.3 砂轮成型修整器82.5.4 单点式金刚笔和金刚滚轮8第三章纵向进给机构设计93.1 步进电机的选型93.2 滚珠丝杠的选择123.3 滚珠丝杠的支承133.4 滚珠丝杠与电动机的联接14第四章横向进给机构设计164.1 横向进给传动机构的选用164.2 横向进给梯形螺杆的耐磨性验算16 4.3 螺杆刚度的验算174.4 横向导轨的计算18第五章数控硬件电路设计195.1 硬件电路总体方案的确定195.2 主控制器CPU的选择195.3 机床的控制功能205.4键盘显示器接口电路205.4.1 I/O扩展电路设计215.4.2 键盘显示器接口电路225.5 步进电机驱动电路225.6 其他辅助电路设计245.6.1 单片机8051的时钟电路245.6.2 复位电路245.6.3 越界报警电路25设计总结26参考文献27第一章综述1.1课题来源本课题设计的是一台数控深切削缓进给成型磨床,以磨削难以加工的3Cr13材料不锈钢游标卡尺尺身两面的沟槽。
金属常见加工工艺缺陷的特征、原因、影响及措施

1.表面粗糙
加工表面粗糙度不符合工艺图纸或设计图纸要求。使用中降低疲劳性能和零件使用寿命。, 刀刃不光洁不仅会增大切削变形,而且使刃口锯齿状缺陷全部复印到已加工表面,降低加工表 面粗糙度。
2.深沟痕
加工表面存在有单独深沟痕。使用中将成为应力集中的根源。导致疲劳断裂。零件硬度低、 塑性大、切削速度较小或者切削厚度加大等,可使前刀面形成积削瘤。由于积削瘤的金属在形 成过程中受到剧烈变形而强化,使它的硬度远高于被切削金属,则相当于一个圆钝的刃口并伸 出刀刃之外,而在已加工表面留下纵向不规则的沟痕。
2.锈蚀 钢材表面锈蚀以后,断裂韧性降低,脆蚀增加,冷冲时容易在锈蚀处出现裂纹。较严重的
局部表面,裂纹边缘粗糙,形如锯齿,无固定的分布取向。
二.由于材料内部缺陷导致冲裂
1.球化退火不良 冷冲压多是一次成型,且变形量较大。它要求冷冲用钢必须具有较低的屈强比和较高的塑
性,因此常用低碳结构钢,低合金结构银来加工冷冲零件。钢的显微组织要求为球状珠光体, 但由于材料球化退火不良,容易得到铁素体和片状珠光体或铁素体和片、粒状珠光体。由于片 状珠光体硬度高、塑性差,对于变形量较大的冲压加工极为不利,冲压裂纹多呈透镜状,穿晶 扩展。
2.拉穿
拉伸件底部拉穿,多属拉应力超过材料抗拉强度所致。
3.波浪形
在拉伸过程中,由于坯料边缘在切线方向受到压缩而产生波浪形。
4.折皱
拉伸件表面折皱。拉伸所用坯料的厚度越小,拉深的深度越大,越容易产生折皱。为了防 止折皱产生,可用压板把坯料压紧。
5.横向裂口
S15A 经下料——镦饼——退冲火——制——收口——成型等 20 余道工序加工成成品。其 中,共经过三次冲制,冲制前采用中频感应加热退火工艺对冲制工件进行软化,而深冲件上横 向裂口的产生是在第二次冲制时开始出现,在第三次冲制后发现最多。裂口附近的表层金属有 全脱碳和氧化铁沿裂口分布的现象。
磨削加工是机械制造中最常用的加工方法之一
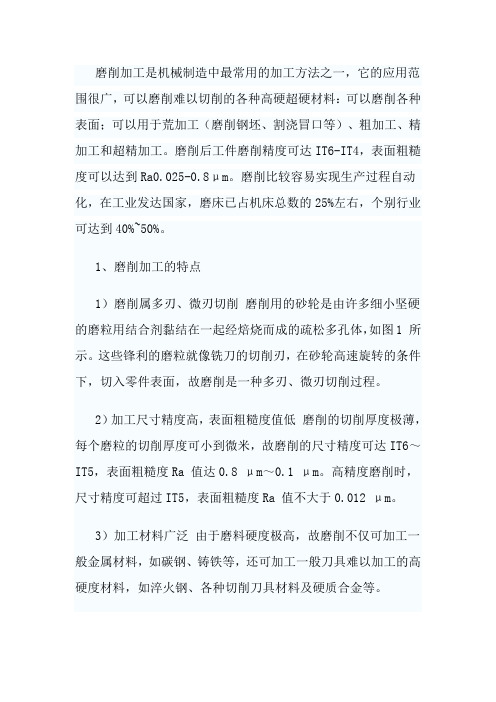
磨削加工是机械制造中最常用的加工方法之一,它的应用范围很广,可以磨削难以切削的各种高硬超硬材料:可以磨削各种表面;可以用于荒加工(磨削钢坯、割浇冒口等)、粗加工、精加工和超精加工。
磨削后工件磨削精度可达IT6-IT4,表面粗糙度可以达到Ra0.025-0.8μm。
磨削比较容易实现生产过程自动化,在工业发达国家,磨床已占机床总数的25%左右,个别行业可达到40%~50%。
1、磨削加工的特点1)磨削属多刃、微刃切削磨削用的砂轮是由许多细小坚硬的磨粒用结合剂黏结在一起经焙烧而成的疏松多孔体,如图1 所示。
这些锋利的磨粒就像铣刀的切削刃,在砂轮高速旋转的条件下,切入零件表面,故磨削是一种多刃、微刃切削过程。
2)加工尺寸精度高,表面粗糙度值低磨削的切削厚度极薄,每个磨粒的切削厚度可小到微米,故磨削的尺寸精度可达IT6~IT5,表面粗糙度Ra 值达0.8 μm~0.1 μm。
高精度磨削时,尺寸精度可超过IT5,表面粗糙度Ra 值不大于0.012 μm。
3)加工材料广泛由于磨料硬度极高,故磨削不仅可加工一般金属材料,如碳钢、铸铁等,还可加工一般刀具难以加工的高硬度材料,如淬火钢、各种切削刀具材料及硬质合金等。
4)砂轮有自锐性当作用在磨粒上的切削力超过磨粒的极限强度时,磨粒就会破碎,形成新的锋利棱角进行磨削;当此切削力超过结合剂的黏结强度时,钝化的磨粒就会自行脱落,使砂轮表面露出一层新鲜锋利的磨粒,从而使磨削加工能够继续进行。
砂轮的这种自行推陈出新、保持自身锋利的性能称为自锐性。
砂轮有自锐性可使砂轮连续进行加工,这是其他刀具没有的特性。
5)磨削温度高磨削过程中,由于切削速度很高,产生大量切削热,温度超过1000℃。
同时,高温的磨屑在空气中发生氧化作用,产生火花。
在如此高温下,将会使零件材料性能改变而影响质量。
因此,为减少摩擦和迅速散热,降低磨削温度,及时冲走屑末,以保证零件表面质量,磨削时需使用大量切削液。
常见磨削缺陷的产生原因及消除方法.doc

产生原因
消除办法
直波形(多
①砂轮磨钝滑及时修理;
①及时修砂轮;
角型)
②砂轮不平衡和修整不好;
②平衡好砂轮;
③消除轴承与主轴配合间隙;
③磨床王轴或轴承破损;
④砂轮园周速过大;
④调选好转速;
⑤砂轮硬度过大。
⑤选择适当硬度。
螺旋形
①砂轮主轴有轴向串动;
①消除砂轮主轴轴向串动;
②砂轮轴心线和工件轴心线不垂
磨削液不清洁
更换磨削液
烧伤
砂轮硬度高,粒度细,组织紧
重新选择砂轮
砂轮修整过细,磨钝后无及时修整
增大修整量、修整次数
冷却液流量小
增大冷却液流量
工件有锥
度
工件与机床的弹性变形
减少进给量,降低磨削力
砂轮磨耗快,组织不均
提咼砂轮硬度、组织均匀性
细长杆弯曲鼓形(长度/直径〉
10)
细长杆刚性差,在磨削力作用下,工件产生弯曲变形,并出现让刀现象,形成中间磨得少,两头磨得多而形成鼓形。
②调好砂轮轴心线与工件轴心
直;
线平衡;
③砂轮修整表面凹凸不平;
③修整好砂轮;
④纵向进给量太大。
④纵向进给量适当。
划伤和划
①磨粒脱落在砂轮与工作台之间;
①消除砂轮;
痕
②冷却液过滤不清洁。
②冷却液过滤干净,清洗过滤器。
轧辊辊身
①磨削用量过大,如砂办圆周速度
①相应提高轧辊圆周速度,减
表面烧伤
过大或工件圆周速度过低,磨削深
小切削深度;
度过大;
②正确选择砂轮。散热条件差
②砂轮硬度过高,磨削时磨粒变纯
时,应选择硬度低、粒度号小
常见的磨削缺陷及消除方法

工作台速度过高
适当改变
3
外圆工件有凸度,中间直径大两端小
工件磨削时朝离开砂轮方向弯
使用中心架磨削
使用中心架后支承块顶得太松或直径磨小后没及时调整支承块
重新调整支承块
砂轮在工件两端出刀太多
重新调整
停留床身工作台纵向导轨原始精度丧失
重新刮研
4
外圆工件有凹度,中间直径小两端大
中心架顶力大
调整支承块
常见的磨削缺陷及消除方法
序号
磨削缺陷
原因
消除方法
1
磨削表面有直波纹
机床以外的振动
消除或者隔离振源
砂轮主轴间隙过大
按规定重新调整(厂家调整)
砂轮没平衡好
重新平衡
砂轮太硬
换用较软的砂轮
砂轮变钝
重新修整
工件在两顶尖间顶得太松
调整尾架套筒的弹簧力
细长工件没有使用中心架或者数量太少或中心架的支承专人顶得太松或太紧
床身工作台纵向导轨原始精度丧失
重新刮研
两端磨削时间比中间部分短
增加砂轮在工件两端的出刀量或稍加停留
5
磨削表面划伤
冷却液不清洁
换新冷却液并精细过滤
砂轮与工件接触面间有脱落的磨粒
砂轮修整后将表面刷净或加大冷却液流量,增加其洗涤性能
6
磨削表面烧伤甚至有裂纹
砂轮过硬
换用较软的砂轮
进给量太大
调小
砂轮修整不够锋利或变钝
重研或消除污物
工件不平衡
降低工件转速或用附加的平衡重量,将工件平衡
工件回转不正常
检查各传动件找出原因或消除之
头架轴承孔或尾架顶尖套筒孔原始精度丧失
拆下修复或更换
重新修整或换新金刚刀
深切缓进给强力成形磨削的特点及磨削缺陷的防止措施

深切缓进给强力成形磨削的特点及磨削缺陷的防止措施郑文虎
【期刊名称】《金属加工:冷加工》
【年(卷),期】2006(000)003
【总页数】2页(P36-37)
【作者】郑文虎
【作者单位】南口机车车辆厂,北京昌平,102202
【正文语种】中文
【相关文献】
1.缓进给深切削的强力磨削工艺在剥线钳制造中的应用 [J], 杨琦;
2.热管砂轮缓进给深切磨削钛合金试验 [J], 陈琛;傅玉灿;赫青山;陈佳佳;张玮
3.缓进深切成形强力磨削应用研究 [J], 陈希哲
4.平面碳化硅深切削缓进给磨削力的正交试验研究 [J], 杨绪啟;姚巨坤;田欣利;江宏亮
5.深沟槽的缓进给强力磨削工艺和磨削表面质量 [J], 郑焕文;马正元;张春元
因版权原因,仅展示原文概要,查看原文内容请购买。
高效率的强力成形磨削

高效率的强力成形磨削作者:杭州机床集团公司周昕高效、高精度、低成本强力成形磨削技术从20世纪60年代后期开始被投入应用,是一项先进的工艺技术,它是在砂轮线速度保持常规磨削情况不变的情况下加大切深量、工作台作缓速运动、一次进给的磨削方法。
至今,强力成形磨削技术日臻成熟与完善,已广泛应用于航天航空、汽车、机械等行业。
强力成形磨削机床的布局结构如图1所示,其加工工艺特点主要表现为:有较大的切削深度,砂轮一次切入量可达几毫米到十几毫米;其二,由于磨削切削深度大,磨削力和磨削热都很大,这样限制了工件的进给速度,一般纵向进给速度为30~250mm/min;其三,强迫冷却——因为磨削切削深度大,砂轮同时工作的磨粒多,每一个磨粒都是一个切削刃,由于切削长度长,屑成丝状金属,在撕裂变形过程中产生很大的热量,甚至可以将磨屑熔化形成焊珠并使零件表面烧伤,因此冷却液应必须以一定的压力和流量送入磨削区,起到强迫冷却作用,将砂轮所产生的的热量迅速带走,同时冲掉附着在砂轮表面上的一部分丝状磨屑。
由此也可见强力成形磨削相对普通往复磨削的优点:生产效率高,平均是一般普通磨削的3~5倍;工件成形快,可以从毛坯直接加工到成品,不需要预加工,简化了工序,节省了工时,降低了成本;成形精度高,表面质量好;可以实现自动化磨削循环等。
图1 数控强力成形磨床布局结构示意图自主研发随着制造技术和控制技术的不断发展,国际上的强力成形磨削机床日新月异,产品具有越来越高的技术含量和性价比,在我国,以杭州机床集团公司的产品为代表的强力成形磨削机床也已打破了以往我国此类高端数控机床完全依赖进口的局面,极大地提高了我国制造业,尤其是航空航天和汽车制造业的装备水平。
目前,杭州机床集团公司的数控强力成形磨床已形成系列产品——台面宽度规格200~500mm,长度630~2500mm,其中以MKLD7140数控强力双磨头磨床和MKL7150×16/2七轴五联动的数控叶冠圆弧强力成形磨床最具代表性。
磨削加工的特点是什么

磨削加工的特色是什么
.
磨削加工的特色是什么?
磨削是一种常用的半精加工和精加工方法,砂轮是磨削的切削工具,磨削是由砂轮表面大批随机散布的磨粒在工件表面进行滑擦、刻划和切削三种作用的综合结果。
磨削的根本特色以下:
1.磨削的切削速度高,致使磨削温度高。
一般外圆磨削时v=35m/s,高速磨削v>50m/s。
磨削产生的切削
热80%~90%传入工件(10%~15%传入砂轮,1%~10%由磨屑带走),加上砂轮的导热性很差,易造成工件表面烧伤和微裂纹。
因
此,磨削时应采纳大批的切削液以降低磨削温度。
2.能获取高的加工精度和小的表面粗拙度值加工精度可达IT6-IT4,表面粗
糙度值可达μm。
磨削不只能够精加工,还可以够粗磨、荒磨、重载荷磨削。
3.磨削的背向磨削力大因磨粒负前角很大,且切削刃钝圆半径rn较大,致使
背向磨削力大于切向磨削力,造成砂轮与工件的接触宽度较大。
会惹起工件、夹
具及机床产生弹性变形,影响加工精度。
所以,在加工刚性较差的工件时(如磨
削修长轴),应采纳相应的举措,防备因工件变形而影响加工精度。
4.砂轮有自锐作用在磨削过程中,磨粒有破裂产生较尖利的新棱角,及磨粒
的零落而露出一层新的尖利磨粒,能够局部地恢复砂轮的切削能力,这类现象叫做砂轮的自锐作用,有益于磨削加工。
5.能加工高硬度资料磨削除能够加工铸铁、碳钢、合金钢等一般构造资料外,
还可以加工一般刀具难以切削的高硬度资料,如淬火钢、硬质合金、陶瓷和玻璃等。
但不宜精加工塑性较大的有色金属工件。
'.
1。
不锈钢的磨削问题及解决方案

不锈钢的磨削问题及解决方案不锈钢是指在大气中或在某些腐蚀性介质中具有一定的耐腐蚀能力的钢种。
因为具有这些优点而被广泛应用于现在社会的不同行业。
一:不锈钢的分类:马氏体不锈钢(常用牌号有1Cr13、2Cr13、8Cr13、1Cr17Ni2等)铁素体不锈钢(常用牌号有0Cr13、1Cr14S、1Cr17、1Cr17Ti等)奥氏体不锈钢(常用牌号有1Cr18Ni9Ti、0Cr18Ni9、1Cr18Ni9等)奥氏体—铁素体不锈钢(常用牌号有1Cr18Ni11Si4AlTi、0Cr21Ni5Ti等)沉淀硬化型不锈钢(常用牌号有0Cr17NiCu4Nb、0Cu17Ni7Al、0Cr15Ni7Mo2Al等)按成分可分为:Cr系(SUS400)、Cr-Ni系(SUS300)、Cr-Mn-Ni(SUS200)、硬化系(SUS600)二.磨削不锈钢中的特点:1.不锈钢的韧性大,热强度高,而砂轮磨粒的切削刃具有较大的负前角,磨削过程中磨屑不容易被切离,切削阻力大,挤压、摩擦剧烈。
单位面积磨削力很大,磨削温度可达1000℃~1500℃。
同时,在高温高压的作用下,磨屑易粘附在砂轮上,填满磨粒问的空隙,使磨粒失去切削作用。
不锈钢的类型不同,产生砂轮堵塞的情况也不相同,如磨削耐浓硝酸不锈钢及耐热不锈钢,粘附、堵塞现象比1Cr18NiTi严重,而1Cr13、2Cr13等马氏体不锈钢就比较轻。
2.不锈钢的导热系数小,磨削时的高温不易导出,工件表面易产生烧伤、退火等现象,退火层深度有时可达0.01~0.02 mm。
磨削过程中产生严重的挤压变形,导致磨削表面产生加工硬化,特别是磨削奥氏体不锈钢时,由于奥氏体组织不够稳定,磨后易产生马氏体组织,使表面硬化严重。
3.不锈钢的线膨胀系数大,在磨削热的作用下易产生变形,其尺寸难以控制。
尤其是薄壁和细长的零件,此现象更为严重。
4.多数类型的不锈钢不能被磁化,在平面磨削时,只能靠机械夹固或专用夹具来夹持工件,利用工件侧面夹紧工件,产生变形和造成形状或尺寸误差,薄板工件更为突出。
磨削加工特点是什么?在加工平易造成什么伤害?
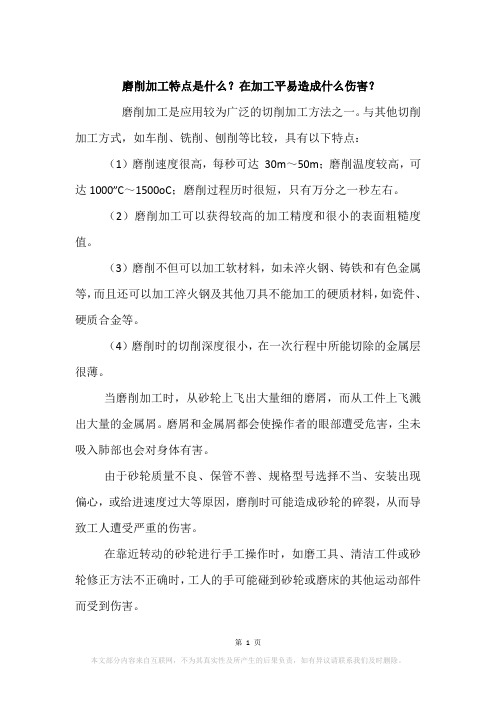
磨削加工特点是什么?在加工平易造成什么伤害?
磨削加工是应用较为广泛的切削加工方法之一。
与其他切削加工方式,如车削、铣削、刨削等比较,具有以下特点:
(1)磨削速度很高,每秒可达30m~50m;磨削温度较高,可达1000”C~1500oC;磨削过程历时很短,只有万分之一秒左右。
(2)磨削加工可以获得较高的加工精度和很小的表面粗糙度值。
(3)磨削不但可以加工软材料,如未淬火钢、铸铁和有色金属等,而且还可以加工淬火钢及其他刀具不能加工的硬质材料,如瓷件、硬质合金等。
(4)磨削时的切削深度很小,在一次行程中所能切除的金属层很薄。
当磨削加工时,从砂轮上飞出大量细的磨屑,而从工件上飞溅出大量的金属屑。
磨屑和金属屑都会使操作者的眼部遭受危害,尘未吸入肺部也会对身体有害。
由于砂轮质量不良、保管不善、规格型号选择不当、安装出现偏心,或给进速度过大等原因,磨削时可能造成砂轮的碎裂,从而导致工人遭受严重的伤害。
在靠近转动的砂轮进行手工操作时,如磨工具、清洁工件或砂轮修正方法不正确时,工人的手可能碰到砂轮或磨床的其他运动部件而受到伤害。
磨削加工时产生的噪音最高可达110dB以上,如不采取降低噪声措施,也会影响健康。
- 1、下载文档前请自行甄别文档内容的完整性,平台不提供额外的编辑、内容补充、找答案等附加服务。
- 2、"仅部分预览"的文档,不可在线预览部分如存在完整性等问题,可反馈申请退款(可完整预览的文档不适用该条件!)。
- 3、如文档侵犯您的权益,请联系客服反馈,我们会尽快为您处理(人工客服工作时间:9:00-18:30)。
来源于:注塑财富网
深切缓进给强力成形磨削的特点及磨削缺陷和防止措施
一、前言:
深切缓进给强力成形磨削,是通过每次为几~几十毫米的磨削深度,20~300mm/min 的缓慢进给速度的磨削。
也称缓进给磨削,蠕动磨削和铣削法磨削。
目前这种磨削已得到较多的应用。
这种磨削方法,可将锻、铸件毛坯不经其它加工,直接磨出工件所要求的表面形状与尺寸。
特别适合于加工各种成形表面和沟槽。
如汽轮机和航空发动机的叶片根槽、连杆齿形结合面、各种齿形槽、各种叶片泵和真空泵转子槽。
我厂螺杆泵转子齿形螺旋槽,就是用这种磨削方法加工成形的。
它的加工精度可达到0.001mm,表面粗糙度可达Ra0.4~0.2μm。
它的加工效率,是普通磨削的几百倍,可以和车削、铣削相比。
二、深切缓进给强力磨削的特点:
1.生产效率高。
它的磨削效率是普通磨削的几百倍到上千倍。
磨削深度大、砂轮与接触的弧长很大,因此单位时间通过磨削区的磨粒数量是普通磨削的几百倍以上,从而可充分发挥机床和砂轮的潜力。
它的加工效率可以和车削、铣削相比。
单位小时的金属去除率,可达几百公斤。
2.砂轮耐用度高。
深切缓进给强力磨削时,砂轮以缓慢的速度切入工件,避免了磨粒与工件边缘的撞击,改善了磨削条件,使磨削过程平稳、不振动,因而提高了砂轮的耐用度。
再因,这种磨削时,是利用砂轮的周边磨削,当砂轮磨钝后,只需对砂轮的外周进行少量的修整,可以使砂轮得到充分利用。
3.冷却条件好,磨削表面粗糙度低,加工精度好。
这种磨削,一般采用高压大流量冷却系统,加之在磨削时采用顺磨,冷却液易进入磨削区,对砂轮和工件表面进行冲洗,防止粒挤入工件表面和磨屑嵌入砂轮表面。
磨削后的工件表面粗糙度可达Ra0.4~0.2μm。
由于砂轮的耐用度高,砂轮外圆轮廓形状保持性长,所以加工出来的工件不但加工精度高,而且质量稳定。
4.适于磨削难切削材料。
对于难切削材料,可采用深切缓进给强力磨削加工型面精度要求高的工件。
采用多次成形修整砂轮,对工件型面进行粗磨、半精磨和精磨,来保证工件的形状和尺寸精度。
5.被精磨表面不易产生烧伤,工件表面质量好。
这是由于深切缓进给强力磨削采用的是组织疏松的大气孔砂轮,而且粒度较粗、硬度较软。
还配有高压冲洗和高压冷却装置,能将大部分热带走,一般的情况下,不易产生烧伤。
这种磨削加工后的工件表面残余应力比普通磨削小30~50%。
三、深切缓进给强力磨削工件表面缺陷产生的原因与防止措施
1.烧伤。
这主要是磨削时冷却不充分,砂轮硬度高,自锐性差,砂轮不锋利,修整时
进给量太小或光修时间长,金刚滚轮与砂轮速比不对,砂轮气孔堵塞和磨削深度过大等原因。
当工件表面出现黄、褐、紫、青、灰色的氧化铁膜时,使工件表层深38~96μm的组织发生变化、硬度降低,直接影响工件的使用性能。
所以磨削烧伤,是磨削中的主要缺陷之一。
防止措施是:调整冷却液喷嘴的位置与角度,使冷却液进入磨削区,并增大流量与压力,合理选择砂轮硬度,采用软和超软砂轮,合理选择砂轮参数,使光修时间减少,以使砂轮锋利,应使光修整砂轮在0~30r以内,合理选择磨削用量,减少磨削深度。
2.工件表面出现波纹或粗糙度大。
主要原因是工件进给量过大,修整砂轮时光修时间过长,金刚石滚轮磨损和冷却液不干净。
防止措施是:适当降低工件进给速度,减少砂轮光修时间,检查金刚石滚轮是否磨损,如磨损,应更换金刚石滚轮,检查冷却液过滤系统是否有故障,或更换冷却液。
3.工件表面有振动痕迹。
其原因是:磨削过程有自激振动,砂轮表面磨损不均匀,磨削深度过大和机床功率不足。
消除措施是:调整砂轮主轴轴承和各溜板间的间隙,提高机床运动的刚度,仔细平衡砂轮,合理选择砂轮修整参数并及时修整砂轮,合理选择磨削用量和砂轮驱动功率。
4.型面误差大。
其原因是砂轮过软和砂轮修整不正确,及修整砂轮的滚轮磨损,工件安装位置不正确和磨削力过大。
防止的措施是:根据型面精度要求,合理选择砂轮硬度,以避免砂轮脱粒过快而使砂轮失去型面精度,修整或更换修整砂轮的金刚石滚轮,正确安装和调整砂轮磨削位置,合理选择磨削用量,适当减小磨削深度和工件进给速度。
5.沟槽、凸橼或转角处宽度尺寸超差。
这主要是砂轮主轴与金刚石滚轮的轴向间隙过大,砂轮修整不正确和金钢石滚轮磨损。
防止措施是:渊整砂轮主轴轴承与滚轮的轴向间隙,修理或更换金刚石滚轮。
我厂进口的TG350E螺杆浆螺杆专用磨床,在磨削螺杆型线中,有时出现烧伤现象。
烧伤产生的部位,在螺杆型线面的中间。
分析其原因,排除了砂轮特性和冷却系统的影响。
发现有烧伤现象时,工件所烧伤部位与砂轮相应处,磨屑堵塞砂轮较严重。
这可能是此处磨削深度大,砂轮与工件磨削时接触弧长,磨粒切下的金属体积大,加之此材料的硬度较低(45号钢调质HB250左右),磨粒是很大的负前角切削(人于-30°),切屑变形大所致。
适当的降低了磨削深度,此烧伤问题得到解决。
四、结论:
1.深切缓进给强力磨削,多在成形磨削时采用。
它具有高生产效率、磨削表面质量和加工精度高的特点,并适合于难切削材料的成形磨削加工。
2.合理选用砂轮特性和磨削条件及合理参数,是消除磨削缺陷的根本措施。
但必须分析具体情况,予以实施。