成形磨削
模具制造工艺思考题答案
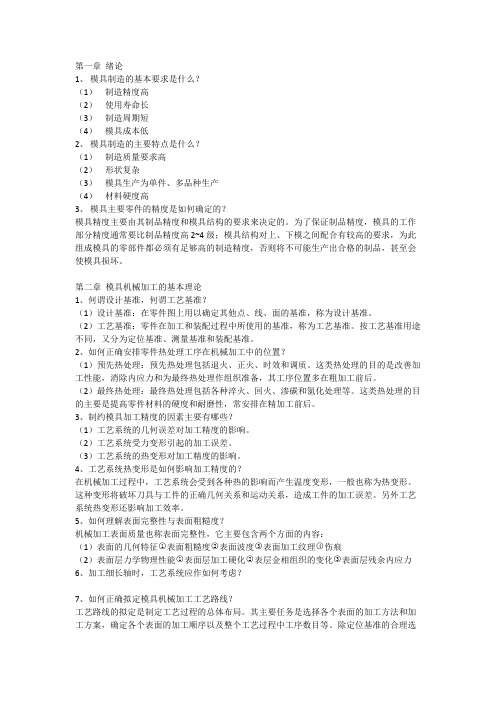
第一章绪论1、模具制造的基本要求是什么?(1)制造精度高(2)使用寿命长(3)制造周期短(4)模具成本低2、模具制造的主要特点是什么?(1)制造质量要求高(2)形状复杂(3)模具生产为单件、多品种生产(4)材料硬度高3、模具主要零件的精度是如何确定的?模具精度主要由其制品精度和模具结构的要求来决定的。
为了保证制品精度,模具的工作部分精度通常要比制品精度高2~4级;模具结构对上、下模之间配合有较高的要求,为此组成模具的零部件都必须有足够高的制造精度,否则将不可能生产出合格的制品,甚至会使模具损坏。
第二章模具机械加工的基本理论1、何谓设计基准,何谓工艺基准?(1)设计基准:在零件图上用以确定其他点、线、面的基准,称为设计基准。
(2)工艺基准:零件在加工和装配过程中所使用的基准,称为工艺基准。
按工艺基准用途不同,又分为定位基准、测量基准和装配基准。
2、如何正确安排零件热处理工序在机械加工中的位置?(1)预先热处理:预先热处理包括退火、正火、时效和调质。
这类热处理的目的是改善加工性能,消除内应力和为最终热处理作组织准备,其工序位置多在粗加工前后。
(2)最终热处理:最终热处理包括各种淬火、回火、渗碳和氮化处理等。
这类热处理的目的主要是提高零件材料的硬度和耐磨性,常安排在精加工前后。
3、制约模具加工精度的因素主要有哪些?(1)工艺系统的几何误差对加工精度的影响。
(2)工艺系统受力变形引起的加工误差。
(3)工艺系统的热变形对加工精度的影响。
4、工艺系统热变形是如何影响加工精度的?在机械加工过程中,工艺系统会受到各种热的影响而产生温度变形,一般也称为热变形。
这种变形将破坏刀具与工件的正确几何关系和运动关系,造成工件的加工误差。
另外工艺系统热变形还影响加工效率。
5、如何理解表面完整性与表面粗糙度?机械加工表面质量也称表面完整性,它主要包含两个方面的内容:○1○2○3○4(1)表面的几何特征表面粗糙度表面波度表面加工纹理伤痕○1○2○3(2)表面层力学物理性能表面层加工硬化表层金相组织的变化表面层残余内应力6、加工细长轴时,工艺系统应作如何考虑?7、如何正确拟定模具机械加工工艺路线?工艺路线的拟定是制定工艺过程的总体布局。
深切缓进给强力成形磨削的特点及磨削缺陷和防止措施

来源于:注塑财富网深切缓进给强力成形磨削的特点及磨削缺陷和防止措施一、前言:深切缓进给强力成形磨削,是通过每次为几~几十毫米的磨削深度,20~300mm/min 的缓慢进给速度的磨削。
也称缓进给磨削,蠕动磨削和铣削法磨削。
目前这种磨削已得到较多的应用。
这种磨削方法,可将锻、铸件毛坯不经其它加工,直接磨出工件所要求的表面形状与尺寸。
特别适合于加工各种成形表面和沟槽。
如汽轮机和航空发动机的叶片根槽、连杆齿形结合面、各种齿形槽、各种叶片泵和真空泵转子槽。
我厂螺杆泵转子齿形螺旋槽,就是用这种磨削方法加工成形的。
它的加工精度可达到0.001mm,表面粗糙度可达Ra0.4~0.2μm。
它的加工效率,是普通磨削的几百倍,可以和车削、铣削相比。
二、深切缓进给强力磨削的特点:1.生产效率高。
它的磨削效率是普通磨削的几百倍到上千倍。
磨削深度大、砂轮与接触的弧长很大,因此单位时间通过磨削区的磨粒数量是普通磨削的几百倍以上,从而可充分发挥机床和砂轮的潜力。
它的加工效率可以和车削、铣削相比。
单位小时的金属去除率,可达几百公斤。
2.砂轮耐用度高。
深切缓进给强力磨削时,砂轮以缓慢的速度切入工件,避免了磨粒与工件边缘的撞击,改善了磨削条件,使磨削过程平稳、不振动,因而提高了砂轮的耐用度。
再因,这种磨削时,是利用砂轮的周边磨削,当砂轮磨钝后,只需对砂轮的外周进行少量的修整,可以使砂轮得到充分利用。
3.冷却条件好,磨削表面粗糙度低,加工精度好。
这种磨削,一般采用高压大流量冷却系统,加之在磨削时采用顺磨,冷却液易进入磨削区,对砂轮和工件表面进行冲洗,防止粒挤入工件表面和磨屑嵌入砂轮表面。
磨削后的工件表面粗糙度可达Ra0.4~0.2μm。
由于砂轮的耐用度高,砂轮外圆轮廓形状保持性长,所以加工出来的工件不但加工精度高,而且质量稳定。
4.适于磨削难切削材料。
对于难切削材料,可采用深切缓进给强力磨削加工型面精度要求高的工件。
采用多次成形修整砂轮,对工件型面进行粗磨、半精磨和精磨,来保证工件的形状和尺寸精度。
成形磨削的加工原理

成形磨削的加工原理
成形磨削是一种通过磨削砂轮的旋转来加工工件的方法。
它的加工原理主要包括以下几个步骤:
1. 砂轮进给:砂轮被安装在磨床的主轴上,并以高速旋转。
工件被安装在工作台上,然后由工作台控制移动。
砂轮和工件之间有一个逐渐减小的间隙。
2. 磨粒切削:砂轮的旋转会使磨粒与工件接触并切削工件表面。
磨粒是在砂轮上固定的砂粒,具有尖锐的边缘。
当磨粒与工件接触时,通过切削和抛光的作用,将工件表面的材料去除。
3. 磨屑去除:在磨削过程中,被去除的工件材料以磨屑的形式产生。
这些磨屑会被冲洗液或喷气等方法及时清除,以防止堵塞磨削过程并影响加工质量。
4. 磨削力的形成:在磨削过程中,磨粒对工件表面施加力,使其发生变形和剥离。
这些力包括切削力、磨削力和垂向力。
切削力是指磨粒对工件的切割力,垂向力是指砂轮对工件施加的垂直力,磨削力是指切削力和垂向力的合力。
总的来说,成形磨削通过砂轮的旋转和磨粒的切削作用,将工件表面的材料去除,从而达到精加工和改善工件表面质量的目的。
加工原理的关键在于砂轮和工件之间的切削作用和力的相互作用。
凸凹模型面成形磨削工艺

成形磨削工艺多用于模具刃口形状以及 成形磨削工艺多用于模具刃口形状以及 模具刃口形状 凹模拼块型面的成型加工 成型加工, 凸、凹模拼块型面的成型加工,它们的 外轮廓为多条直线与圆弧所组成。如图 外轮廓为多条直线与圆弧所组成。
一、成形磨削概述
进行磨削时,需将外形轮廓分为若干直 进行磨削时,需将外形轮廓分为若干直 线或圆弧段,然后,按一定顺序逐段磨 线或圆弧段,然后,按一定顺序逐段磨 削成形,以达到图样的尺寸、 削成形,以达到图样的尺寸、形状及其 精度要求,这样的加工方式称为成形磨 精度要求,这样的加工方式称为成形磨 削。
图3-27
四、成形磨削的顺序
模具凸模、 模具凸模、凹模拼块一般由多圆弧面和 多角度平面相互平滑、 多角度平面相互平滑、光顺的连接成封 闭的柱状、型孔等,即构成凸模、 闭的柱状、型孔等,即构成凸模、凹模 的刃口。 后图) 的刃口。(后图) 成型磨削时,根据工件形状与技术要求, 成型磨削时,根据工件形状与技术要求, 采用分段磨削,并在实际加工中, 采用分段磨削,并在实际加工中,有时 会仿形法、范成法混合使用。 会仿形法、范成法混合使用。
工件的装夹方式: 工件的装夹方式:
夹具如图所示 组成部分:正弦分度头、尾座、底座
工件定位、安装在夹具中的方式有: 工件定位、安装在夹具中的方式有: 心轴装夹、 心轴装夹、双顶尖装夹
利用正弦头右侧的分度头, 利用正弦头右侧的分度头,可控制工件 的回转角度, 的回转角度,要求一般精度时可直接在分度盘 上读取,要求精度高时, 上读取,要求精度高时,可在垫板与正弦圆柱 间垫量块调节。 间垫量块调节。 加工时, 加工时,被磨表面的尺寸是采用比较测 量法测定的,测定依据是夹具中性线, 量法测定的,测定依据是夹具中性线,用比较 测量器、量块、百分表找到比较测量面, 测量器、量块、百分表找到比较测量面,当被 加工面与比较测量面等高时( 加工面与比较测量面等高时(即百分表读数一 致时),加工也就完成了。 ),加工也就完成了 致时),加工也就完成了。
成形磨削中砂轮修整精度的研究

削 的工 件 轮 廓精 度 主要 取 决 于 被修 整 砂
轮 的轮廓精度如何 ( 在此不考 虑砂轮轴线 和 工 件 回 转 轴 线 在 安 装 高 度 方 向 的 偏 差 ) ,一 般采 用带有 金 刚石 笔 的修整器 摆
动或 沿靠模移动修 整砂轮 ,笔尖 相对砂轮 的位置决定 砂轮 的轮廓精度 ,但是要精 确 调 整金 刚石 笔 尖 的指 向相 对 砂轮 轴 心
维普资讯
机 械产 品与科 技
20 0 2年第 3期
。研究与设计 。
成形 磨 削 中砂轮 修整 精 度 的研 究
装备分公司 姚 斌
摘要
技术部
王建 军
党为 民
成 形 磨 削一 般 采 用 金 刚 石 笔 来修 整 所 需 要 的 砂 轮 形 状 ,金 刚 石 笔
机械 产 品与科技
20 0 2年第 3期
于仓库 、码头 、货 场 、车站 中的短距离转
运 作业 。 ( 变 型能力强 , 2) 只要对基本 型的油 缸 、车体 进行改 动 ,就 可派 生出从 0 — . 5 3 的系列产 品 , 可变型为 大高度起重车 t 也
辆及货叉 超长 、超宽 ,车体超低等产 品 ,
和砂 轮轴 心线 不 等高 引 起 的砂 轮 廓 形 误
差 l : 为
l ’( =, X)一,( X)
A2=4 ”一X √ 一X R 一 尺
针 对第二种 情况 的廓形误差 3 : 为
3 =h ( X) 一h ( ± )
在 机床上 是一个定值 ,由上式计算 可知 ,当砂 轮半径 r被修得越小 ,轮廓误 f 差 就越 大 ,被 加工 的工 件轮廓 度误差
式中
h ( —— 砂轮 轮廓母 线沿砂 轮 X)
成形磨削在模具制造中的应用

成形磨削在模具制造中的应用董海涛【摘要】介绍了非圆型凸模采用成形磨削的一般工艺流程以及成形磨削的原理和成型磨削方法;用实例详细介绍了成形砂轮磨削法修整砂轮的工具和工艺过程,简要说明了成型夹具磨削法的工艺要点;成形磨削有提高加工精度和减少加工时间的优势,被广泛应用在模具企业的精密模具制造中.【期刊名称】《机械工程师》【年(卷),期】2014(000)005【总页数】3页(P55-57)【关键词】成形磨削;砂轮;成形夹具;模具制造;金刚笔【作者】董海涛【作者单位】山西机电职业技术学院,山西长治046011【正文语种】中文【中图分类】TH162模具技术已经成为衡量一个国家产品制造水平的重要标志之一,模具工业是我国国民经济的基础产业之一,近年来我国模具制造水平明显提高,而精密化是模具制造发展的一个趋势,模具中凸模、型芯、镶拼凹模和镶拼型腔等具有复杂截面形状的零件精加工时,需要采用成形磨削的加工方法。
用成型磨削加工代替传统的电火花加工,可使加工时间缩短60%左右[1]。
1.1 非圆型凸模采用成形磨削加工的工艺流程图1为非圆型凸模的几种结构形式,它的精加工一般采用成形磨削的方法,具体工艺流程如下:1)毛坯准备,用圆钢锻成六面体;2)退火处理;3)刨削或铣削6个面,留单面余量0.4 mm;4)磨上、下两平面及基准面;5)钳工划线,钻孔、攻螺纹;6)用铣床加工外形(留磨削余量);7)淬火;8)磨削上、下两平面;9)成形磨削;10)精修。
1.2 成形磨削的原理成形磨削的原理就是把复杂零件的轮廓分解为若干线段和圆弧,然后按照一定工艺顺序逐段磨削,使其在衔接处平整光滑,达到产品的设计要求[2]。
成形磨削具有精度高、效率高等优点,磨削精度可达IT5~IT6,表面粗糙度为Ra0.4,最低可达Ra0.1。
成形磨削常采用成形磨床或者平面磨床。
1.3 成形磨削的方法成形磨削的方法有很多种,常用的有成形砂轮磨削法和成形夹具磨削法。
第8讲成形磨削

削时,应控制砂轮左侧宽度b=1mm~2mm左右,磨到距两圆弧切点
1mm~2mm处停止进给。按上述控制方法,逆时针回转磨出另一半
圆弧面。
第8讲成形磨削
10
⑥磨削R2mm圆弧面。R2mm的圆弧面用成型砂轮磨削。为此,应
将砂轮两侧修整出R2mm的凸圆弧,如图3.27(f)、(g)所示。将
弦圆柱12之间垫入适当尺寸的量块进行控制。精度可达
10″~30″。
第8讲成形磨削
3
例如,工件需要回转的角度为α,转动前正弦分度盘的位置如图 3.21(a)所示,转过角度α后正弦分度盘的位置如图3.21(b)、(c)
所示。为控制转角垫入的量块尺寸按下式计算:
h在1=图h-3.D22s1i(naα)所-d示/2的情况或下,如果hα2==h0+,D2则sinα-hd0/=2h-d/2 式中:h1、h2——控制工件回转角需要垫入的量块尺寸;
代入上式得:
h1=27.86mm
检测斜面3的量块尺
寸为h/=50mm。
第8讲成形磨削
9
将工件回转100°,使斜面4处于水平位置。磨削斜面4到要求尺寸,
其操作过程和磨削斜面3相同。
④磨削R35mm的圆弧面。将工件回转130°
使R35mm的圆弧面处于磨削位置,如图(d)所
示。通过分中夹具使工件作圆周进给,磨
此,在夹具两顶尖间装一根直径为d 的标准圆柱,如图3.25所
示。在测量调整器的量块支承面上放置尺寸为(50+d/2)的量块 后,调整量块座的位置,并用百分表进行测量。使量块上平面 与标准圆柱面的最高点等高后,将量块座固定。
第8讲成形磨削
7
当工件上被测量表面的位置高于夹具回转中心线h'(若被测 量表面为凸圆弧面,则h'为圆弧半径)时,只要在量块支承面上 放置尺寸为(50+ h')的量块,用百分表检测量块上平面与被测
成形磨削的原理
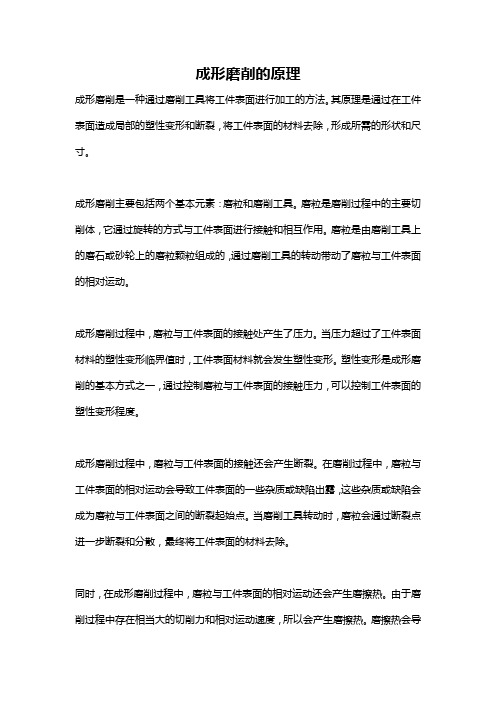
成形磨削的原理成形磨削是一种通过磨削工具将工件表面进行加工的方法。
其原理是通过在工件表面造成局部的塑性变形和断裂,将工件表面的材料去除,形成所需的形状和尺寸。
成形磨削主要包括两个基本元素:磨粒和磨削工具。
磨粒是磨削过程中的主要切削体,它通过旋转的方式与工件表面进行接触和相互作用。
磨粒是由磨削工具上的磨石或砂轮上的磨粒颗粒组成的,通过磨削工具的转动带动了磨粒与工件表面的相对运动。
成形磨削过程中,磨粒与工件表面的接触处产生了压力。
当压力超过了工件表面材料的塑性变形临界值时,工件表面材料就会发生塑性变形。
塑性变形是成形磨削的基本方式之一,通过控制磨粒与工件表面的接触压力,可以控制工件表面的塑性变形程度。
成形磨削过程中,磨粒与工件表面的接触还会产生断裂。
在磨削过程中,磨粒与工件表面的相对运动会导致工件表面的一些杂质或缺陷出露,这些杂质或缺陷会成为磨粒与工件表面之间的断裂起始点。
当磨削工具转动时,磨粒会通过断裂点进一步断裂和分散,最终将工件表面的材料去除。
同时,在成形磨削过程中,磨粒与工件表面的相对运动还会产生磨擦热。
由于磨削过程中存在相当大的切削力和相对运动速度,所以会产生磨擦热。
磨擦热会导致磨削区域的温度升高,这会进一步增强版面材料的塑性变形和断裂。
在成形磨削过程中,工件表面的材料不仅被塑性变形和断裂,还会受到磨削工具的磨削力的剪切和压缩。
这些力的作用下,工件表面的材料会发生塑性变形和切削断裂。
这种切削方式主要取决于磨削工具上的磨粒形状和磨粒与工件表面的接触情况。
除了以上基本原理之外,成形磨削还受到其他一些因素的影响,如切削液的使用、磨削速度、磨削力等。
切削液的使用可以降低磨削过程中的摩擦和磨损,从而提高磨削效果。
磨削速度的选择可以影响磨粒与工件表面的相对运动速度,从而影响磨削的效率和质量。
磨削力的大小则直接影响了工件表面的塑性变形和断裂程度。
总之,成形磨削是一种通过磨削工具将工件表面进行加工的方法,它的主要原理是通过控制磨粒与工件表面之间的接触压力,引起工件表面材料的塑性变形和断裂,从而达到加工工件表面的目的。
简述在平面磨床上进行零件成形磨削的几种方法
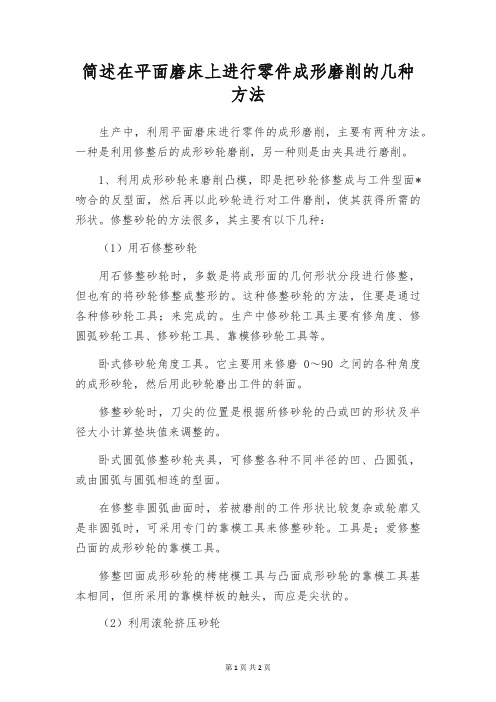
简述在平面磨床上进行零件成形磨削的几种方法生产中,利用平面磨床进行零件的成形磨削,主要有两种方法。
一种是利用修整后的成形砂轮磨削,另一种则是由夹具进行磨削。
1、利用成形砂轮来磨削凸模,即是把砂轮修整成与工件型面*吻合的反型面,然后再以此砂轮进行对工件磨削,使其获得所需的形状。
修整砂轮的方法很多,其主要有以下几种:(1)用石修整砂轮用石修整砂轮时,多数是将成形面的几何形状分段进行修整,但也有的将砂轮修整成整形的。
这种修整砂轮的方法,住要是通过各种修砂轮工具;来完成的。
生产中修砂轮工具主要有修角度、修圆弧砂轮工具、修砂轮工具、靠模修砂轮工具等。
卧式修砂轮角度工具。
它主要用来修磨0~90之间的各种角度的成形砂轮,然后用此砂轮磨出工件的斜面。
修整砂轮时,刀尖的位置是根据所修砂轮的凸或凹的形状及半径大小计算垫块值来调整的。
卧式圆弧修整砂轮夹具,可修整各种不同半径的凹、凸圆弧,或由圆弧与圆弧相连的型面。
在修整非圆弧曲面时,若被磨削的工件形状比较复杂或轮廓又是非圆弧时,可采用专门的靠模工具来修整砂轮。
工具是;爱修整凸面的成形砂轮的靠模工具。
修整凹面成形砂轮的栲栳模工具与凸面成形砂轮的靠模工具基本相同,但所采用的靠模样板的触头,而应是尖状的。
(2)利用滚轮挤压砂轮挤压的滚轮型面尺寸与零件型面尺寸相同,轮周开有辐向不等距的直槽斜槽,其槽宽 1.5~2.5mm,深度应超过成形部分低点 2.5 mm以上。
其槽主要起切削刃作用,并能容纳挤下来的砂粒。
材与挤轮中心线成10~15斜角,在1~2条的直槽内嵌入铁片,在挤压精加工后,铁片也加工成形,可用此铁片检查磨削的型面和成形砂轮或反面滚轮。
滚轮的直径一般为50~60mm.挤压砂轮工具,主要由两个顶针构成。
活年个针由电动机通过带轮或齿轮传动。
当滚论逐渐压向砂轮时,在压力作用下,使砂轮终获得所需要的形状。
挤压砂轮工具在使用时,安装在平面磨床的磁力工作台上。
在安装时,必须时滚轮的轴线与砂轮的轴线平行。
修形内斜齿轮成形磨削技术研究

修形内斜齿轮成形磨削技术研究修形内斜齿轮成形磨削技术研究摘要:内斜齿轮是一种常用的传动元件,在工业领域中广泛应用。
本文针对内斜齿轮的成形磨削技术进行了研究,通过实验和分析得出了修形内斜齿轮磨削的关键技术,以及在实际应用中的注意事项。
研究结果表明,修形内斜齿轮磨削技术能够提高内斜齿轮的制造精度和传动效率,具有较好的应用前景。
1. 引言内斜齿轮是一种通过斜齿面传递运动和转矩的机械元件。
其外形特点是齿轮传动轴承滚动的斜面,它可以将扭矩变为推力,并且可以实现大范围的传动比。
因此,内斜齿轮广泛应用于汽车、航空、航天和工业生产等领域。
然而,内斜齿轮在制造过程中存在一些难题,如加工难度大、制造精度低等。
为了提高内斜齿轮的制造精度和传动效率,本文进行了修形内斜齿轮成形磨削技术的研究。
2. 修形内斜齿轮磨削的关键技术2.1 磨削工艺参数的选择磨削工艺参数的选择对于修形内斜齿轮磨削技术至关重要。
合理选择磨削速度、进给速度、磨削深度等参数,可以有效控制加工精度和表面质量。
实验结果表明,在磨削过程中,应尽量选择较小的磨削速度和进给速度,以避免过大的磨削热量对内斜齿轮的影响。
2.2 磨削刀具的选择磨削刀具的选择对于修形内斜齿轮磨削技术的效果有重要影响。
应尽量选择具有较高抗磨性和较好切削性能的磨削刀具。
实验结果表明,使用合适的磨削刀具可以提高内斜齿轮的表面质量和加工精度。
2.3 磨削润滑液的选择磨削润滑液对于修形内斜齿轮磨削技术的效果同样非常重要。
合适的磨削润滑液可以有效降低磨削热和摩擦系数,提高内斜齿轮的表面质量。
实验结果表明,在磨削过程中,应尽量选择含有较高润滑性能的润滑液。
3. 修形内斜齿轮磨削技术的实验研究针对修形内斜齿轮磨削技术,本文开展了一系列实验研究。
实验采用了不同的磨削工艺参数、磨削刀具和磨削润滑液,对修形内斜齿轮进行了磨削加工。
通过对实验数据的观察和分析,得出了如下结论:1) 较小的磨削速度和进给速度有利于提高内斜齿轮的表面质量和加工精度;2) 合适的磨削刀具有助于提高内斜齿轮的加工精度和表面质量;3) 含有较高润滑性能的润滑液可以有效降低磨削热和摩擦系数,提高内斜齿轮的表面质量。
强力成形磨削概述及我国强力成形磨削的发展与应用(二)

号 的 叶 片磨 削 ,只 需 更换 金 刚滚 轮 即可 。 批量 生 产 中 ,只需 对 第 一 个 叶 片 进行 对 刀 调 试 。按 照 叶 片榫 由 于 蜂 窝 段 工 件 圆 弧 面 半 径 往 往 在 80 0 mm~ 10 m 左右 ,且设 计要 求 工件 蜂 窝孔 的轴 线均 应指 00 m 向工 作 圆 弧表 面 的 中心 轴 线 。 这 就要 求 磨 削 的 蜂窝 表 面 圆弧半径 精度较 高 。需要 机 床 、y轴 进 行数控 联 动 磨 削 。 涡轮 发 动 机 密 封 环组 件 的工 作 温 度 大 约
16 0
产 品与技 术 Po u t rd cs& T c n l y e h o g o
是 6 0 9 0 , 目前大 多选 用 具有 良好 抗 氧化 性 和 5 ~ 0 ℃
止 ,机 床 已批 量 提供 给 国内近 1 0家汽 车 零部 件 制造 企 业 。杭 机 在 为 用户 提 供 加 工 设 备 的同 时 ,把 可靠
31 在 飞机 制造工 业 中发挥作 用 .
蜂 窝 结 构 。根 据 每 级 涡 轮 叶 片 工作 环 境 的 不 同 ,有 的采 用本 体 结 构 ,大 多 采用 由 多个 扇 形 镶 块组 件 拼 合 成 一 个 密封 环 。而 单 个 的 扇 形镶 块 的蜂 窝 段 弧 面 往往 是 由磨削 加工完 成 的。
的先 进 工 艺 连 同机 床 一 起 提 供 给 用 户 。针 对 汽 车转
向齿 条磨 削 宽度 在 2 0 m、切 深在 5 m- 0 m,且 0r a m 1r a 材 料是 实体 的 实际 情况 ,MK 7 5 × 0数控 强 成形 L 10 1
成形磨削的概念

成形磨削的概念成形磨削是一种精密磨削加工方法,通过使用特殊形状的砂轮将工件的外形加工成所需形状和尺寸的技术。
它广泛应用于精密磨削领域,如航空航天、汽车制造、模具制造、工具制造等。
成形磨削相比传统的磨削方法具有许多优势。
首先,其砂轮可以根据需要制作成各种形状,如平面、圆柱、球形、齿轮等,因此可以实现各种复杂外形的加工。
这使得成形磨削成为高精度、高效率的加工方法,尤其适用于要求外形特殊的零部件的制造。
其次,成形磨削可以实现无心磨削,即砂轮可以根据工件的轮廓形成相应的磨削轮廓,从而使得加工后的工件轮廓与模具或砂轮的轮廓一致。
这种特性使得成形磨削可以用于加工各种非圆形的工件,如凸轮、槽孔、齿轮等。
与其他加工方法相比,成形磨削具有更高的精度和更好的表面质量。
第三,成形磨削具有较大的自适应能力。
由于砂轮可以根据工件轮廓变形,因此在加工时可以自动调整切削参数,使得加工过程更加稳定和可靠。
这种自适应能力使得成形磨削能够应对工件形状复杂、切削条件发生变化等情况,提高加工效率和质量。
成形磨削的加工过程主要包括以下几个步骤:首先,选择合适的砂轮,并安装在磨床主轴上。
其次,根据工件的轮廓形状调整砂轮的位置和方向,并固定在磨床上。
然后,通过调节磨床的进给量和转速,使得砂轮与工件表面接触,并开始进行磨削。
在磨削过程中,砂轮会根据工件的轮廓变形,从而使得磨削的切削条件逐渐适应工件的形状。
最后,根据需要进行润滑和冷却处理,以保证加工质量。
成形磨削还可以与其他加工方法结合使用,如电火花加工、齿轮加工等。
这种组合加工可以进一步提高加工的精度和效率。
此外,成形磨削还可以与数控技术相结合,实现自动化和智能化加工,提高生产效率和质量。
总之,成形磨削是一种重要的精密磨削加工方法,其特点是可以根据工件的轮廓形状来磨削,并具有较高的精度、表面质量和自适应能力。
在工业生产中,成形磨削广泛应用于各种外形复杂、精度要求高的零部件的制造,对提高飞机、汽车、机床等行业产品的质量和性能具有重要意义。
成形磨床磨削的原理和办法是什么

成形磨床磨削的原理和办法是什么
在磨床模具制作中,使用成形磨削的办法来精加工凸模、凹模及型腔模块和型心,是当时最常用的,也是最有用的一种加工办法。
零件通常在热处理后进行成形磨削加工,减小了因为热处理后零件变形对模具精度的影响。
成形磨削加工的特点是质量好、精度高、加工速度快。
①成形磨削的原理模具的成形零件如凸模刃口及型腔拼块的几许形状,通常由鬃毛砖圆弧与直线
或圆弧与圆弧等几许线形分解成若干直线、圆弧等简略的几许线形,然后分段进行磨削,使其连接成油滑,光整并契合图样的一种磨削加工办法。
/
②成形磨削的办法成形磨削的办法主要有两种。
一种是在平面磨床上选用修整后的成形砂轮或专用卡具进行成形磨削。
另一种办法是使用光学曲线磨床、坐标磨床、全能东西磨床等专用成形磨床磨削。
因为设备条件的约束,当前在中小型工厂大多仍使用一般平面磨床进行成形磨削。
强力成形磨削概述及我国强力成形削的发展与应用(一)
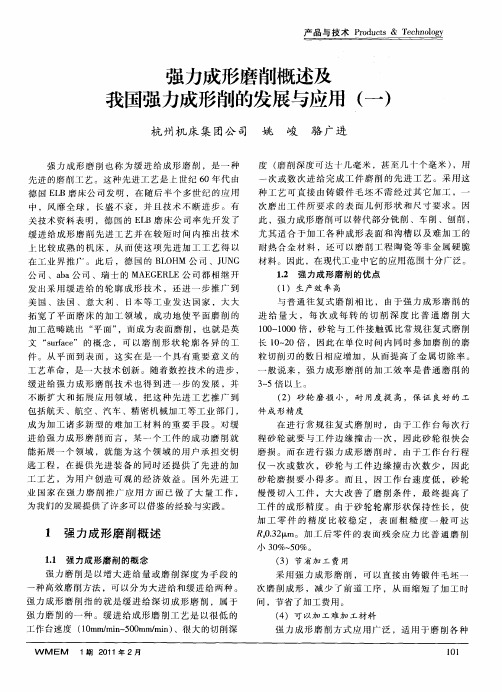
文 “ufc ” 的 概 念 ,可 以磨 削 形 状 轮 廓 各 异 的 工 sr e a
件 。从 平 面 到表 面 ,这 实 在 是一 个 具 有 重 要 意 义 的
工艺 革命 ,是 一 大技术 创 新 。随 着数 控技 术 的进 步 ,
缓 进 给 强 力成 形 磨 削 技 术也 得 到进 比 ,由 于强 力 成 形 磨 削 的 进 给 量 大 ,每 次 或 每 转 的切 削 深 度 比 普 通 磨 削 大 10 1 0 0 ~ 0 0倍 ,砂轮 与 工 件 接触 弧 比常 规往 复 式 磨 削 长 1 ~ 0倍 ,因此 在 单 位 时 间 内 同 时参 加 磨 削 的磨 02 粒切 削 刃 的数 目相 应增 加 ,从 而提 高 了金 属切 除率 。
小 3 %~ 0 。 0 5%
为我们 的发展 提供 了许多 可 以借鉴 的经验 与实践 。
强 力成 形磨 削概 述
11 强力成 形磨 削的概念 . 强 力 磨 削 是 以增 大 进 给 量 或磨 削 深度 为手 段 的
一
( )节省加 工 费用 3
采 用 强力 成 形 磨 削 ,可 以 直 接 由铸 锻 件 毛 坯 一 次 磨 削 成形 ,减 少 了前 道 工 序 ,从 而缩 短 了加 工 时
般 说 来 ,强 力 成 形 磨 削 的加 工 效 率 是 普 通 磨 削 的
( ) 砂 轮 磨 损 小 , 耐 用 度 提 高 , 保 证 良 好 的 工 2
3 5倍 以上 。 ~
件 成 形 精 度
不断 扩 大 和拓 展 应 用 领 域 ,把 这种 先 进 工 艺 推 广 到 包 括航 天 、航 空 、汽 车 、精密 机 械加 工等 工业 部 门 ,
成形磨削中砂轮修整精度的研究

转半径 。
心线的位置 比较难 , 势必对母 线 为 曲线 的特殊 回转 面 工 件加 工精 度 带 来 影 响 , 文 对 这 些 位 置 误 差 影 响 进 本 行 了分 析 。 2 金 刚 石 笔 尖 的 位 置 误 差 对 工 件精 度 的 影 响 通 过 研 究 分 析 发 现 , 母 线 为 曲 线 的 特 殊 回转 面 对 工 件 , 修 整 砂 轮 的误 差 来 源 主要 有 两 方 面 : 是 笔尖 被 一 的指 向及 其 运 动 方 向 没 有 通 过 砂 轮 的 回转 轴 心 线 ; 二 是 在修 整 器 中 , 尖 指 向不 通 过 砂 轮 回 转 母 线 的 曲 率 笔 中心。下面对这两方面的误差做一个分 析。 对 于 第 一 种 误 差 的 来 源 ( 图 1 , 刚 石 笔 尖 和 见 )金 砂 轮 轴 心 线 不 等 高 相 差 ( 尖 安 装 时 要 顺 着 砂 轮 的 笔 转 向方 向倾 斜 ) 。 当金 刚 石 笔 尖 通 过 砂 轮 的 回 转 轴 心 线 时 , =0 , 第1 次修 整砂轮后砂轮母线半径沿轴方 向分 布为 :
不 同, 又分两种情况 进行 分析 。 当被 修整 曲线 为单 圆
式 中 h( 为 砂 轮 轮 廓 母 线 沿 砂 轮 轴 心 线 ( 轴 ) ) 的分 布 函数 , 为 第 , 修 整 后 , 轮 廓 形 沿 轴 向 的 最 小 回 次 砂
弧 , 刚石笔尖做摆动运动修 整砂 轮 ; 金 当被修 整 曲线为 多 圆 弧 或 不 规 则 曲 线 时 , 般 采 用 金 刚 石 笔 沿 靠 模 平 一 移修 整砂轮廓形 ; 果金 刚 石笔尖 指 向不 通过 砂轮母 如
r )= h( ( )+
如 果 金 刚石 笔 尖 不 通 过 砂 轮 的 回 转 轴 心 线 , 即 ≠0 为 了方 便 计 算 结 果 的 对 比 性 , 取 为 第 ,次 修 , 仍 整 后 砂 轮 廓 形 沿 轴 向 的 最 小 回转 半 径 , 修 整 砂 轮 后 则 砂 轮 母 线 半 径 沿 轴 向分 布 为 :
齿轮成形磨削工艺流程

齿轮成形磨削工艺流程齿轮成形磨削工艺流程是一种用于生产高精度齿轮的加工方法。
下面将详细介绍齿轮成形磨削的工艺流程。
第一步是选择合适的齿轮材料。
常见的齿轮材料有钢、铸铁和有色金属等。
根据实际应用需求和工作环境选择合适的材料。
第二步是齿轮设计。
根据使用要求,确定齿轮的模数、压力角、齿形等参数,并绘制齿轮图纸。
第三步是齿轮成形。
首先,根据齿轮参数和图纸,制作成形刀具。
然后,将齿轮材料固定在齿轮成形机上,通过成形刀具的运动,将齿轮材料按照图纸上的形状切削成形。
成形过程中需要保证加工速度和切削深度等参数的准确控制,以确保成品的准确度和表面质量。
第四步是齿轮硬化。
成形后的齿轮需要进行热处理,提高其硬度和耐磨性。
常见的硬化方式有渗碳、淬火和电渗碳等。
硬化过程中需要控制温度、时间和冷却速度等参数,以获得理想的硬化效果。
第五步是齿轮磨削。
经过硬化的齿轮表面会形成一层较硬的外表,需要进行磨削以提高其表面质量和准确度。
磨削工艺中需要使用专用的磨削设备和磨削刀具,按照齿轮参数和要求进行磨削操作。
磨削过程中需要注意切削液的选择和冷却,以避免磨削过程中过热对齿轮造成损伤。
第六步是齿轮检测。
完成磨削后的齿轮需要进行检测以确保其质量和准确度。
常见的检测方法有齿弧测量、齿距测量和齿宽测量等。
通过检测可以检查齿轮的形状、尺寸和表面质量等参数,以确保齿轮的功能和使用效果。
最后一步是齿轮组装。
完成所有工艺后,齿轮可以进行组装,用于各种机械设备中。
组装过程中需要注意齿轮的配合间隙和装配精度,以确保齿轮在工作中的可靠性和正常运行。
总之,齿轮成形磨削工艺流程是一套复杂而严谨的加工方法。
通过选择合适的材料、精确的成形、适当的热处理和精细的磨削,可以生产出高精度的齿轮。
在实际应用中,还要根据具体需求对工艺流程进行调整和优化,以满足不同的工程要求和使用环境。
在未来的发展中,齿轮成形磨削工艺流程将不断完善和创新,为齿轮加工提供更高效、更精确的解决方案。
第4章 成形磨削夹具

出版社
理工分社
图4.9 修整圆弧砂轮
14
机械制造工艺装备
出版社
理工分社
4.3 成形磨削常用的夹具及应用 4.3.1 平面磨削常用夹具 具有相互垂直、平行精度要求的六面体模板 是模具中的基本构件。为此,将模板正确定位、 夹紧于磨床工作台上进行平面磨削是常用的加工 方法。其正确定位、夹紧的常用夹具有以下几种: 磁性吸盘、 (1)磁性吸盘、导磁铁 磁铁吸盘和常用的导磁铁如图4.10、图4.11 所示。
机械制造工艺装备
出版社
理工分社
第 4章
成形磨削夹具
磨削加工是模具工件或机械零件加工工艺过程 中的精加工工序或最终工序。因此,经磨削后的加 工面,必须保证加工面的粗糙度要求,保证加工面 的形状、尺寸、位置精度符合设计精度的要求。所 以,与其他工艺系统一样,夹具也是磨削工艺系统 中的关键技术。而在模具或机械制造中,利用成形 磨削的方法加工凸模、凹模及电火花加工用的电极 是目前最常用的一种工艺方法。
2
机械制造工艺装备
出版社
理工分社
图4.1 复杂模具零件的形状
3
机械制造工艺装备
出版社
理工分社
图4.2 成形磨削的两种方法
4
机械制造工艺装备
出版社
理工分社
(2)夹具磨削法 将工件按一定的条件装在专用夹具上,在加 工过程中通过夹具的调节使工件固定或不断改变 位置,从而使工件获得所需的形状,如图4.2(b) 所示。利用夹具磨削法对工件进行磨削其加工精 度很高,甚至可以达到零件具有互换性。 成形磨削的专用夹具主要有磨平面及斜面用 夹具、分度磨削夹具、万能夹具及磨大圆弧夹具 等几种。
5
机械制造工艺装备
出版社
理工分社
砂轮磨削 基本术语-最新国标

砂轮磨削基本术语1 范围本文件界定了磨削工艺用基本术语及其定义、部分术语的符号和计量单位。
本文件适用于磨削专业及相关行业。
2 规范性引用文件下列文件中的内容通过文中的规范性引用而构成本文件必不可少的条款。
其中,注日期的引用文件,仅该日期对应的版本适用于本文件;不注日期的引用文件,其最新版本(包括所有的修改单)适用于本文件。
GB/T 12204—2010 金属切削基本术语(ISO 8002-1:1982,ISO 8002-3:1984,ISO 8002-4:1984,MOD)GB/T 19660—2005 工业自动化系统与集成机床数值控制坐标系和运动命名(ISO 841:2001,IDT)ISO 3002-2:1982 切削和磨削的基本参量第2部分:刀具作用部分的几何参量与刀具和切削角度相关的基本转换公式3 通用规定符号和下标除另有规定外,在GB/T 12204—2010及ISO 3002-2:1982中定义的基本符号与下列符号一起在磨削中使用。
——A=面积;——l=长度;——b=宽度;适当处增加下标,其中包括:——s与砂轮有关的量,例如v s=砂轮圆周速度;——w与工件有关的量,例如v w=工件的圆周速度;——m与工作台或工件支撑物、砂轮支撑物有关的参量(见3.2);——d与修整或整形工艺或整形工具有关的参量;——'(字码右上角的撇号)表示与单位有效砂轮宽度(4.6.2)或与单位有效砂轮轮廓线长度(4.6.1)有关的参量,例如F'=F/b。
工作台table在本文件中,术语工作台是指对机床床身作运动的机床部件。
工作台可以是支持工件的亦可以是支持砂轮的。
仅在圆柱面磨削(6.1.2)的情况下,才使工件作相对于工作台的连续转动。
除此情况外,非主运动的其他所有运动都被视为是由工作台提供的。
公称值和实际值nominal value and real value参量的公称值是在机床上设定的值,而实际值则计入了工件的变形、砂轮的变形、机床的变形以及砂轮的磨损。
精密成形磨削工艺参数的仿真研究

·20·机械2018 年第 10 期 第 45 卷精密成形磨削工艺参数的仿真研究李志伟 1,张沭玥 2(1.四川省机械研究设计院,四川 成都 610063;2.西南交通大学 机械工程学院,四川 成都 610031)摘要:为研究精密成型磨削过程中工艺参数的选择,利用 CAD 软件建立摆线齿轮成型磨削三维模型,在Deform-3D 有限元软件中设置相应仿真参数,仿真分析砂轮线速度、摆线轮进给速度对磨削后表面粗糙度、磨削力、材料去除量及砂轮磨损量的影响。
结果表明:齿轮表面粗糙度随砂轮线速度的增加而减小,随摆线轮进给速度的增加而增加,随打磨次数的增加而减小;在进入成形磨满磨过程后,法向力峰值将会基本稳定在切向力峰值的三倍;随着进给速度增加,磨耗比存在波浪形起伏的变化。
关键词:成形磨;材料去除;表面粗糙度;磨削力;磨耗比中图分类号:TP391文献标志码:Adoi:10.3969/j.issn.1006-0316.2018.10.005文章编号:1006-0316 (2018) 10-0020-08Simulation Study on Simulation Precision Forming Grinding Process Parameters LI Zhiwei1,ZHANG Shuyue2( 1.Sichuan Machinery Research and Design Institute, Chengdu 610063, China; 2.Tribology Research Institute, Southwest Jiaotong University, Chengdu 610031, China ) Abstract:In order to study the selection of process parameters in precision forming grinding, a three- dimensional model of cycloidal gear forming grinding is established by using CAD software. The corresponding simulation parameters are set up in DEFORM-3D finite element software. The effects of grinding wheel linear speed and cycloidal wheel feed speed on the surface roughness and grinding force after grinding are simulated and analyzed. The influence of material removal and wheel wear is also discussed. The results show that the surface roughness of the gear decreases with the increase of the linear velocity of the grinding wheel, increases with the increase of the feed velocity of the cycloid wheel, and decreases with the increase of the grinding times. After entering the full grinding process, the peak value of normal force will be basically stabilized at three times the peak value of tangential force. With the increase of feed speed, the variation of the grinding ratio is undulating. Key words:forming grinding;material removal;surface roughness;grinding force;grinding ratio磨削是实现机械零部件表面形态和尺寸精 确加工的极为重要的手段。
- 1、下载文档前请自行甄别文档内容的完整性,平台不提供额外的编辑、内容补充、找答案等附加服务。
- 2、"仅部分预览"的文档,不可在线预览部分如存在完整性等问题,可反馈申请退款(可完整预览的文档不适用该条件!)。
- 3、如文档侵犯您的权益,请联系客服反馈,我们会尽快为您处理(人工客服工作时间:9:00-18:30)。
4
工件在正弦分中夹具上的装夹方法有两种。 1、心轴装夹法 如果是带圆柱孔的工件,且孔的轴线正好与 被磨削圆弧面的轴线重合,可在该孔中插入心轴,利用心轴两端 的顶尖孔定位,将工件支承在正弦分中夹具的两顶尖之间进行磨 削,如图3.22所示。夹具主轴回转时,通过鸡心夹头5和拨盘带 动工件一起转动。若工件上没有圆柱孔,在技术要求允许的情况 下,也可在工件上作出穿心轴用的工艺孔。
14
2、用精密平口钳装夹工件 利用精密平口钳端部 (或侧面)上的螺孔,用螺钉和垫柱将精密平口钳拉紧 在夹具的转盘上,如图3.30所示,再用平口钳夹持工 件。这种装夹方法,操作简单、方便,但一次装夹只 能磨出工件上的部分表面。
15
3、用电磁台装夹工件 利用小型电磁台端部(或 侧面)上的螺孔,用螺钉和垫柱将其拉紧在转盘上, 如图3.31所示,用电磁力吸住工件。这种方法,装 夹迅速、方便。但工件必须以平面定位,一次装夹 也只能磨削工件上的部分表面。
10
⑥磨削R2mm圆弧面。R2mm的圆弧面用成型砂轮磨削。为此,应 将砂轮两侧修整出R2mm的凸圆弧,如图3.27(f)、(g)所示。将 工件回转140°使斜面3(或4)处于水平位置。调整机床使砂轮 圆周和斜面微微接触,如图3.27(f)所示。再将工件逆时针转 过一适当角度,砂轮横向进给(或手动)使其侧面与R15mm的圆 弧面微微接触,如图3.27(g)所示。顺时针回转工件,磨凹圆 弧到砂轮圆周与斜面微微接触为止。用同样的方法磨出另一个 R2mm圆弧面。 在磨削过程中,检 测被磨削表面尺寸的量 块,均按被磨削表面的 平均尺寸计算。从以上 磨削实例来看,用正弦 分中夹具配合成型砂轮, 也可以磨出某些带凹圆 弧的成型表面。
采用回转法磨削圆弧面时,为了把磨削圆弧的工艺中 心调整到夹具主轴的回转轴线上,就需要计算出各工 艺中心的坐标。同时在回转磨削过程中,为了不使砂 轮超越被磨削的圆弧长度而切入相邻表面,还要计算 出被磨削圆弧的圆心角,以便在磨削时控制工件的回 转角度。 19
采用回转法磨削圆弧面时,为了把磨削圆弧的工艺 中心调整到夹具主轴的回转轴线上,就需要计算出 各工艺中心的坐标。同时在回转磨削过程中,为了 不使砂轮超越被磨削的圆弧长度而切入相邻表面, 还要计算出被磨削圆弧的圆心角,以便在磨削时控 制工件的回转角度。 磨削平面时,为了将被磨削的平面转到水平(或 垂直)位置进行磨削,需要知道这些平面对坐标轴的 倾斜角度。为了对被磨削平面进行测量,还应计算 出被磨削平面与工艺中心之间的距离。 总之,用万能夹具进行成型磨削,按工艺要求 应进行下列计算: ①各工艺中心的坐标尺寸; 20 ② 各平面至对应工艺中心的垂直距离;
13
夹具装夹部分用来装夹工件,根据不同的加工对象,可以 采用以下几种装夹方法。 1、用螺钉与垫柱装夹工件 如图3.29所示,利用凸模端面上 的螺孔,通过螺钉3、垫柱2将工件拉紧在夹具的转盘1上。垫柱 和螺钉的长度要保证砂轮在磨削中超越工件的定位面时,不至 和夹具相碰。为了保证定位精度,要求垫柱高度一致,以免工 件产生偏斜。转盘1装在万能夹 具的小滑板上,可绕轴线O—O 旋转,便于调整工件在圆周方 向上的相对位置。螺母5和螺钉 6用来将转盘压紧在小滑板上。 这种装夹方法,可以在一次装 夹后将凸模的刃口轮廓全部磨 出。
1
2
工件支承在两顶尖之间,顶尖座4可沿底座上的T形槽移动, 用螺钉3固定,旋转手轮5能使尾顶尖6移动,用以调节工件和 顶尖间的松紧程度。顶尖7装在主轴的锥孔内。转动手轮(图中 未显示),通过蜗杆13、蜗轮9传动,带动主轴和通过鸡心夹头
装夹的工件及装在主轴后端的分度盘11一起转动。使工件实现
圆周进给,磨出圆弧面。分度盘的作用是控制工件的回转角度, 其工作原理如图3.21所示。分度盘上有四个正弦圆柱,其中心
6
使用正弦分中夹具进行成型磨削,被磨削表面的尺寸以夹具 中心线为基准,用测量调整器、量块和百分表进行比较测量。 为了能对高于或低于夹具回转中心线的表面都能进行测量,一 般将量块支承面的位置调整到低于夹具回转中心线50mm处。为 此,在夹具两顶尖间装一根直径为d 的标准圆柱,如图3.25所 示。在测量调整器的量块支承面上放置尺寸为(50+d/2)的量块 后,调整量块座的位置,并用百分表进行测量。使量块上平面 与标准圆柱面的最高点等高后,2,调整平面1到水平位置,磨削该平面到要求尺寸, 如图3.27(b)所示。检查平面尺寸的量块为(50+16.988)mm。 将工件回转180°,磨削平面2到要求尺寸,其操作过程与平面1 相同。 ③ 磨削斜面3和4。将工件回转40°,使斜面3处于水平位置, 如图3.27(c)所示。磨削斜面3到尺寸,在砂轮横向进给到距圆弧 与斜面的切点1mm~2mm处停止进给,以免切入凹圆弧。控制工件 回转角度的 量块尺寸为: D h1=h- 2 sin40°-d/2 设分中夹具的h=70mm, D 2 =50mm,d=20mm 代入上式得: h1=27.86mm 检测斜面3的量块尺 寸为h/=50mm。
第8讲 成形磨削 (正弦分中夹具、万能夹具 )
教学目标:掌握正弦分中夹具的装夹方法和磨削工 艺;掌握万能夹具的装夹方法和磨削工艺 。 知识点:正弦分中夹具的适用范围;万能夹具的组 成及适用范围;磨削工艺计算。 (三)正弦分中夹具 正弦分中夹具主要用来磨凸模上同一轴线的不同 圆弧面、等分槽及平面。 夹具结构如图3.20所示。
5
2、双顶尖装夹法 当工件上没有圆柱孔,不具备作出穿心轴 的工艺孔的条件时,可采用双顶尖装夹工件,如图3.23所示。 夹具上除前后顶尖外,还装有一个副顶尖,与此相对应,凸模 上除两端的主顶尖孔外还有一个副顶尖孔,主顶尖孔用来将工 件正确定位。副顶尖孔连同副顶尖用来拨动工件回转。副顶尖 成弯曲状,可以在叉形滑板的槽内上下移动,用螺母3调节其 伸出的长短并锁紧。因此它有较大的适应范围。采用双顶尖装 夹工件,要求各顶尖 与顶尖孔配合良好, 不能有轴向窜动;要 防止主顶尖孔与顶尖 配合过松,副顶尖对 工件的轴向推力过大, 使工件产生歪斜,影 响加工精度,如 图3.24所示。
11
(四)万能夹具 万能夹具是成型磨床的主要部件,也可在平面磨 床或万能工具磨床上使用。 万能夹具的结构如图3.28所示。它由十字滑板、 回转部分、分度装置和工件的装夹部分组成。
12
十字滑板由固定在主轴5上的滑板座4、中滑板11和小滑板2 组成。转动丝杆3能使中滑板11沿滑板4上的导轨上下移动。转 动丝杆10能使小滑板2沿中滑板11上的导轨移动。两个移动方向 互相垂直,用以将安装在转盘上的工件调整到适当位置。 回转部分由蜗杆(图中未画出)及蜗轮6和主轴5组成。用手 轮12转动蜗杆,通过蜗轮6带动主轴、分度盘8、十字滑板和工 件一起转动。 分度装置用来控制工件的回转角度,由分度盘8来实现。分 度盘的结构原理与正弦分中夹具的分度盘完全相同,对回转角 度精度要求不高的工件,其转角大小直接由分度盘圆柱面上的 刻度和游标7读出,精度为3′。对回转角度精度要求高的工件, 其转角大小由量块控制。精度为10″~ 30″ 。 万能夹具比正弦分中夹具更为完善,它能使工件回转,并通 过十字滑板调整工件的回转中心,因此能磨削不同轴线的圆弧 面。
18
成型磨削的工艺尺寸换算,应按照加工中调整和测 量的需要确定。加工中为了进行磨削和测量,工件需 要绕着某些回转中心转动。工件绕着转动的回转中心 称为成型磨削的工艺中心。一般情况下工件上有几段 用回转法磨削的圆弧,就有几个工艺中心(同心圆弧 例外)。
对那些半径很小不适宜用回转法磨削的圆弧面,常 采用成型砂轮进行磨削,它们的圆心不作为工艺中心。
7
当工件上被测量表面的位置高于夹具回转中心线h'(若被测 量表面为凸圆弧面,则h'为圆弧半径)时,只要在量块支承面上 放置尺寸为(50+ h')的量块,用百分表检测量块上平面与被测 量表面的等高性,当两者读数相同时,表明工件已加工到所要 求的尺寸。若被测量表面低于夹具的回转中心h',则量块支承 面上放置的量块尺寸为(50-h')。测量方法与上述相同。若被测 表面是凹圆弧面,则测量圆弧的最低点。 例3 图3.26所示凸模,在平面磨床 上用正弦分中夹具磨削刃口的轮廓形状。 各面所留磨削余量为0.15mm~0.2mm。 磨削过程如下: ①将正弦分中夹具置于机床的工作台 上校正。装夹工件,检查各面是否有足 够的磨削余量,检查方法如图3.27(a) 所示。
③各平面对所选定坐标轴的倾斜角度; ④某些圆弧面的圆心角;(当磨圆弧时,工件可自由回转而 不致于碰伤其它表面的,不必计算圆心角) 为了提高计算的精确度,在计算过程中,三角函数及一般 数值计算应精确到小数点后六位,运算的最终结果精确到小数 点后二位或三位。 举例 图3.33所示为凸模零件图,用万能夹具进行刃口轮 廓的磨削加工。其步骤如下。 ①工艺尺寸换算 a.确定并计算工艺中心和工 艺坐标 图3.33所示工件上所有 的圆弧都可用回转法磨削,因此 需要计算工件的所有回转中心的 坐标O1、O2、O3。为了计算中心坐 标,首先建立图3.34所示的XOY直 50 角坐标系。
16
万能夹具能磨削刃口由直线和凸、凹圆弧组成的形状复杂的 凹模。磨削平面时可利用夹具将被加工表面调整到水平(或垂直) 位置,用砂轮的圆周(或端面)进行磨削; 磨削圆弧时可以利用十字滑板将圆弧的圆 心调整到夹具主轴的回转轴线上,用回转 法进行磨削。 万能夹具中心高度用测量调整器来测 量,如图3.32所示。测量调整器的使用方 法是利用测量平台基面至夹具中心的固定 距离(该距离在测量平台位置不变时为定 值50mm),根据工件被测表面位于夹具中 心的上方或下方,来增减被测尺寸的量块 值,并用百分表对工件磨削面与量块面比 较,直至读数相等。
均处于直径为D的圆周上,并将所在圆周四等分。
磨削时,如果工件回转角度的精度要求不高,则转角可直 接由分度盘外圆面上的刻度和读数指示器10读出(见图3.20)。
精度可达到3′。若回转角的精度要求较高,可在量块垫板14
和正弦圆柱12之间垫入适当尺寸的量块进行控制。精度可达 10″~30″。