酸洗资料及冷拔常用缺陷
冷拔钢管产品缺陷一览表
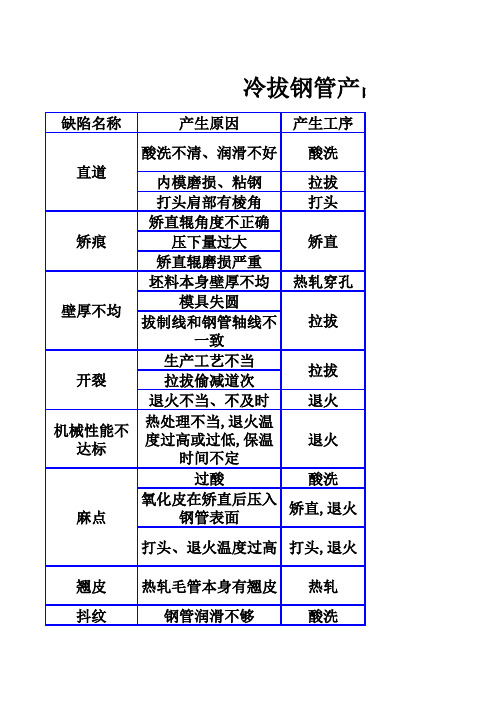
冷拔钢管产品缺缺陷名称
产生原因产生工序酸洗不清、润滑不好酸洗内模磨损、粘钢拉拔
打头肩部有棱角打头
矫直辊角度不正确
压下量过大
矫直辊磨损严重
坯料本身壁厚不均热轧穿孔
模具失圆拔制线和钢管轴线不
一致
生产工艺不当拉拔偷减道次
退火不当、不及时退火机械性能不达标热处理不当,退火温度过高或过低,保温时间不定
退火过酸酸洗
氧化皮在矫直后压入钢管表面
矫直,退火打头、退火温度过高打头,退火翘皮
热轧毛管本身有翘皮热轧抖纹钢管润滑不够酸洗
直道矫痕壁厚不均开裂麻点矫直拉拔拉拔
配模错误模具磨损严重老头管
管头尾切不净切管切管工责任心不够切管拉车衬内模过后拉拔
成品长度达
不到要求拉拔尺寸超差
产品缺陷一览表
预防措施及解决方法备注加强酸洗管理,保证酸洗质量
经常检查模具,及时更换
打头时要保证肩部圆滑
认真调整矫直机,经常检查、修磨辊面
严格按工艺要求控制壁厚
经常检查模具,及时更换
调整拔管机
合理安排工艺,严格按工艺生产
严格执行热处理工艺制度
严格执行热处理工艺制度
控制酸洗温度和时间
减少氧化铁皮的厚度
控制打头退火温度,不得过烧
投料时加强检查,及时修磨
掌握好酸洗磷化皂化时间和成分调整
加强责任心,认真检查模具,及时更换
加强切管工的责任心
加强切管工的责任心,提高自身的水平
保证衬芯到位。
冷拔管常见缺陷产生原因及预防和消除方法

[选取日期]冷拔无缝钢管常见的缺陷特征产生的原因及预防和消除方法2010年10月08日孟相欣冷拔无缝钢管常见的缺陷特征产生的原因及预防和消除方法一、折迭拔制后,钢管内外表面呈现直线或螺旋方向的折迭,局部或通长的出现在钢管上。
产生的原因:管料表面有折迭或夹杂物,有严重擦伤和裂纹,管料磨修处有棱角或深宽比(H/b)不够。
预防和消除方法:严格把好穿孔热轧质量关。
二、尺寸超差(包括壁厚超差,壁厚不均,直径超差,椭圆偏心)直径超过了标准的偏差,在同一截面上管壁一边薄,一边厚,直径不等,长短轴之差超出标准规定。
产生的原因:1、拔制模具选择不当,或芯棒(内模)调整不当。
2、内外模设计制造不合理或磨损严重,或硬度不够造成变形磨损。
3、热处理时间长,温度高,或热处理性能不均匀。
4、增减壁的规律控制不当。
5、拔制表编制不合格。
6、钢管矫直时被压扁,造成误差较大。
预防和消除方法:1、正确设计和选配拔管模具。
2、正确执行热处理制度,均匀加热。
3、正确调制矫直机,经常校对拔管机各部件和量具。
4、掌握不同钢种、不同规格钢管的增减壁规律。
5、正确合理编制拔制表。
6、椭圆度出格可重新矫直,局部椭圆度出格可切除。
三、划道钢管表面上呈现纵向直线的划痕称为划道,划道长短不一,宽窄不等,多为沟状,可见沟底。
产生的原因:1、拔模表面不光滑,有裂纹或粘结金属。
2、锤头过度部分有棱角,工具磨损。
3、欠酸洗或毛管上残存氧化铁皮。
4、磷化、皂化工序操作不当。
5、内外模以损坏或磨损严重。
6、中间退火不均,变形量不足。
预防和消除方法:1、提高拔管模具的表面质量。
2、钢管酸洗后,氧化铁皮要冲洗干净。
3、锤头过度部分要圆滑无棱角。
4勤检查模具和钢管的表面,发现问题及时处理。
四、斗纹钢管表面沿长度方向呈高低不平的环形波浪或波浪逐个相同排列,局部或通长出现在钢管内外表面上。
产生的原因:1、热处理后的性能不均,热轧时低温钢造成性能不均。
2、酸洗后冲洗不干净,磷化不良导致皂化不均。
冷拔质量缺陷与解决办法

冷拔质量缺陷与解决办法冷拔质量缺陷与解决办法划道和擦伤:划道和擦伤缺陷的特征是,在钢管的内外表面上呈现纵向宜线形的长短不一的划痕,多为沟状,但也可能是凸起的条纹。
产生划道和擦伤的主要原因是:在管料上有内划道在拔制时未能消除,钢管上残留着氧化铁皮,模具粘钢,模具强度和硬度不够或不均,模具出现碎裂和磨损,锤头不良,锤头过渡部分的尖锐梭角损伤了模具等。
为了防止产生划道和擦伤应该提高拔制前各准备工序的质量和使用强度及硬度高、光洁度好的模具1.表面铸造缺陷1 拉伤(1)特征:①沿开模方向铸件表面呈线条状的拉伤痕迹,有一定深度,严重时为整面拉伤;②金属与模具表面粘和,导致铸件表面缺料。
(2)产生原因:①模具型腔表面有损伤;②出模方向无斜度或斜度过小;③顶出不平衡;④模具松动:(3)处理方法:①修理模具表面损伤;(修理后光洁度一定要好)②修正斜度,提高模具表面光洁度;③调整顶杆,使顶出力平衡;④紧固模具;2.锤头原因;(1)产生原因:毛管上残存氧化皮(2)处理方法:锤头过度部分要圆滑无棱角。
2.打头不足原因:要求对φ60的无缝钢管进行打头时的推进翻转设计,要求要有动力系统有关参数选择和相关计算以及结构参数设计计算,才能减少缺陷,保持正常生产工艺。
3、冷拔钢管退火:常见的退火工艺有:再结晶退火,去应力退火,球化退火,完全退火等。
退火的目的:主要是降低金属材料的硬度,提高塑性,以利切削加工或压力加工,减少残余应力,提高组织和成分的均匀化,或为后道热处理作好组织准备等。
拔断出现拔断的主要原因是:中间退火不均,变形量不足。
润滑的质量不好,锤头不合乎要求,在锤头前的加热时产生了过热或过烧。
冷轧厂酸洗工艺段常见表面缺陷及预防
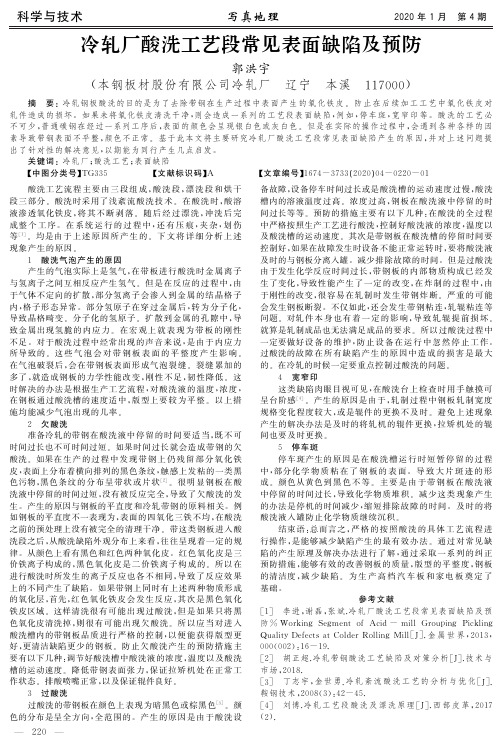
冷轧厂酸洗工艺段常见表面缺陷及预防郭洪宇(本钢板材股份有限公司冷轧厂㊀辽宁㊀本溪㊀117000)摘㊀要:冷轧钢板酸洗的目的是为了去除带钢在生产过程中表面产生的氧化铁皮.防止在后续加工工艺中氧化铁皮对轧件造成的损坏.如果未将氧化铁皮清洗干净,则会造成一系列的工艺段表面缺陷,例如,停车斑,宽窄印等.酸洗的工艺必不可少,普通碳钢在经过一系列工序后,表面的颜色会呈现银白色或灰白色.但是在实际的操作过程中,会遇到各种各样的因素导致带钢表面不平整,颜色不正常.基于此本文将主要研究冷轧厂酸洗工艺段常见表面缺陷产生的原因,并对上述问题提出了针对性的解决意见,以期能为同行产生几点启发.关键词:冷轧厂;酸洗工艺;表面缺陷ʌ中图分类号ɔT G 335㊀㊀㊀㊀㊀ʌ文献标识码ɔA㊀㊀㊀㊀㊀ʌ文章编号ɔ1674-3733(2020)04-0220-01㊀㊀酸洗工艺流程主要由三段组成,酸洗段,漂洗段和烘干段三部分.酸洗时采用了浅紊流酸洗技术.在酸洗时,酸溶液渗透氧化铁皮,将其不断剥落.随后经过漂洗,冲洗后完成整个工序.在系统运行的过程中,还有压痕,夹杂,划伤等[1].均是由于上述原因所产生的.下文将详细分析上述现象产生的原因.1㊀酸洗气泡产生的原因产生的气泡实际上是氢气,在带板进行酸洗时金属离子与氢离子之间互相反应产生氢气.但是在反应的过程中,由于气体不定向的扩散,部分氢离子会渗入到金属的结晶格子内,格子形态异常.部分氢原子在穿过金属后,转为分子化,导致晶格畸变.分子化的氢原子.扩散到金属的孔隙中,导致金属出现氢脆的内应力.在宏观上就表现为带板的刚性不足.对于酸洗过程中经常出现的声音来说,是由于内应力所导致的.这些气泡会对带钢板表面的平整度产生影响.在气泡破裂后,会在带钢板表面形成气泡裂缝.裂缝累加的多了,就造成钢板的力学性能改变,刚性不足,韧性降低.这时解决的办法是根据生产工艺流程,对酸洗液的温度,浓度,在钢板通过酸洗槽的速度适中,版型上要较为平整.以上措施均能减少气泡出现的几率.2㊀欠酸洗准备冷轧的带钢在酸洗液中停留的时间要适当,既不可时间过长也不可时间过短.如果时间过长就会造成带钢的欠酸洗.如果在生产的过程中发现带钢上仍残留部分氧化铁皮,表面上分布着横向排列的黑色条纹,触感上发粘的一类黑色污物,黑色条纹的分布呈带状或片状[2].很明显钢板在酸洗液中停留的时间过短,没有被反应完全,导致了欠酸洗的发生.产生的原因与钢板的平直度和冷轧带钢的原料相关.例如钢板的平直度不一表现为,表面的四氧化三铁不均,在酸洗之前的预处理上没有被完全的清理干净.带这类钢板进入酸洗段之后,从酸洗缺陷外观分布上来看,往往呈现着一定的规律.从颜色上看有黑色和红色两种氧化皮.红色氧化皮是三价铁离子构成的,黑色氧化皮是二价铁离子构成的.所以在进行酸洗时所发生的离子反应也各不相同,导致了反应效果上的不同产生了缺陷.如果带钢上同时有上述两种物质形成的氧化层,首先,红色氧化铁皮会发生反应,其次是黑色氧化铁皮区域.这样清洗很有可能出现过酸洗,但是如果只将黑色氧化皮清洗掉,则很有可能出现欠酸洗.所以应当对进入酸洗槽内的带钢板品质进行严格的控制,以便能获得版型更好,更清洁缺陷更少的钢板.防止欠酸洗产生的预防措施主要有以下几种:调节好酸洗槽中酸洗液的浓度,温度以及酸洗槽的运动速度.降低带钢表面张力,保证拉矫机处在正常工作状态.排酸喷嘴正常,以及保证辊件良好.3㊀过酸洗过酸洗的带钢板在颜色上表现为暗黑色或棕黑色[3].颜色的分布是呈全方向,全范围的.产生的原因是由于酸洗设备故障,设备停车时间过长或是酸洗槽的运动速度过慢,酸洗槽内的溶液温度过高.浓度过高,钢板在酸洗液中停留的时间过长等等.预防的措施主要有以下几种:在酸洗的全过程中严格按照生产工艺进行酸洗,控制好酸洗液的浓度,温度以及酸洗槽的运动速度.其次是带钢板在酸洗槽的停留时间要控制好,如果在故障发生时设备不能正常运转时,要将酸洗液及时的与钢板分离入罐.减少排除故障的时间.但是过酸洗由于发生化学反应时间过长,带钢板的内部物质构成已经发生了变化,导致性能产生了一定的改变,在炸制的过程中,由于刚性的改变,很容易在轧制时发生带钢炸断.严重的可能会发生钢板断裂.不仅如此,还会发生带钢粘连,轧辊粘连等问题.对轧件本身也有着一定的影响,导致轧辊提前损坏.就算是轧制成品也无法满足成品的要求.所以过酸洗过程中一定要做好设备的维护,防止设备在运行中忽然停止工作.过酸洗的故障在所有缺陷产生的原因中造成的损害是最大的.在冷轧的时候一定要重点控制过酸洗的问题.4㊀宽窄印这类缺陷肉眼目视可见,在酸洗台上检查时用手触摸可呈台阶感[4].产生的原因是由于,轧制过程中钢板轧制宽度规格变化程度较大,或是辊件的更换不及时.避免上述现象产生的解决办法是及时的将轧机的辊件更换,拉矫机处的辊间也要及时更换.5㊀停车斑停车斑产生的原因是在酸洗槽运行时短暂停留的过程中,部分化学物质粘在了钢板的表面.导致大片斑迹的形成.颜色从黄色到黑色不等.主要是由于带钢板在酸洗液中停留的时间过长,导致化学物质堆积.减少这类现象产生的办法是停机的时间减少,缩短排除故障的时间.及时的将酸洗液入罐防止化学物质继续沉积.结束语:总而言之,严格的按照酸洗的具体工艺流程进行操作,是能够减少缺陷产生的最有效办法.通过对常见缺陷的产生原理及解决办法进行了解,通过采取一系列的纠正预防措施,能够有效的改善钢板的质量,版型的平整度,钢板的清洁度,减少缺陷.为生产高档汽车板和家电板奠定了基础.参考文献[1]㊀李进,谢磊,张斌.冷轧厂酸洗工艺段常见表面缺陷及预防%W o r k i n g S e g m e n to f A c i d-m i l l G r o u p i n g P i c k l i n gQ u a l i t y D e f e c t s a tC o l d e rR o l l i n g Mi l l [J ].金属世界,2013,000(002):16-19.[2]㊀胡正超.冷轧带钢酸洗工艺缺陷及对策分析[J ].技术与市场,2018.[3]㊀丁志宇,金世勇.冷轧紊流酸洗工艺的分析与优化[J ].鞍钢技术,2008(3):42-45.[4]㊀刘博.冷轧工艺段酸洗及漂洗原理[J ].西部皮革,2017(2).022 科学与技术写真地理2020年1月㊀第4期。
酸洗缺陷分析

酸洗缺陷分析在冷轧带钢生产中的酸洗工序,有时因酸洗条件不理想,操作不当或某些设备不良,可能会造成各种酸洗缺陷,归结起来,大致有以下几种:1、酸洗不均带钢表面个别或局部地方残留着未被酸洗掉的氧化铁皮斑点。
产生原因:①带钢在酸洗前没有松卷或松卷不均,表面有相互贴紧现象,酸液不易与其反应。
②酸洗前,带钢表面上有油污等未被清除干净,而阻碍了带钢与酸反应,③酸洗中,未将带钢反复提升或充分揽动酸液也会产生酸洗不匀的情况。
2、酸洗不足带钢表面残留着未被酸洗掉的氧化皮,用手抹有黑灰。
产生原因:①酸液的温度低,浓度不够,或带钢在酸液中的停留时间不够,②剥壳处理未达到预先要求,酸洗不足的带钢,轻者轧制后带钢表面颜色发暗,严重者氧化铁皮被轧入呈黑斑,氧化铁皮也可能粘在轧辊表面上,大块的氧化铁皮使带钢轧制时不延伸,而造成轧制后带钢出现浪形等缺陷。
解决方法是重新进行酸洗。
3、点状腐蚀带钢表面上产生点或带状的凹坑。
产生原因:①酸液温度过高、浓度过高;②酸洗时间过长,③酸洗缓蚀剂量不足,至使带钢表面逐渐变粗糙成麻面。
点状腐蚀的带钢,延伸性大大降低,在轧制过程中很容易断裂或破碎,坯料上的细微点状腐蚀一般可通过冷轧得到清除,而成品带钢的点状腐蚀是一种不可清除的缺陷。
4、酸渍、水渍带钢酸洗后,表面被锈蚀,呈黄色。
产生原因:①带钢表面经清洗后还残存着少量的酸质,中和不完全,②带钢表面没有完全干燥而与空气中氧发生反应而锈蚀。
解决方法:清洗槽尽量采用活水,提高中和槽中碱的含量和温度,或增加烘干工序,也可采用钝化处理。
5、氢脆带钢表面呈现外观为条状的小鼓泡,鼓泡破裂后呈黑色细小裂缝,没有破裂的经轧制后便破裂或裂缝延伸、扩大。
并且是无规律的,它直接影响带钢的韧性和塑性。
产生原因:带钢吸收酸洗过程中所析出的氢。
解决方法:严格按酸洗工艺制度进行酸洗,采用缓蚀剂,酸洗后,采用烘干或将带钢置于空气或清水中若干时间。
6、黑斑带钢表面呈现形状不同的黑色或成片的黑印。
冷轧带钢酸洗工艺缺陷及对策分析探讨
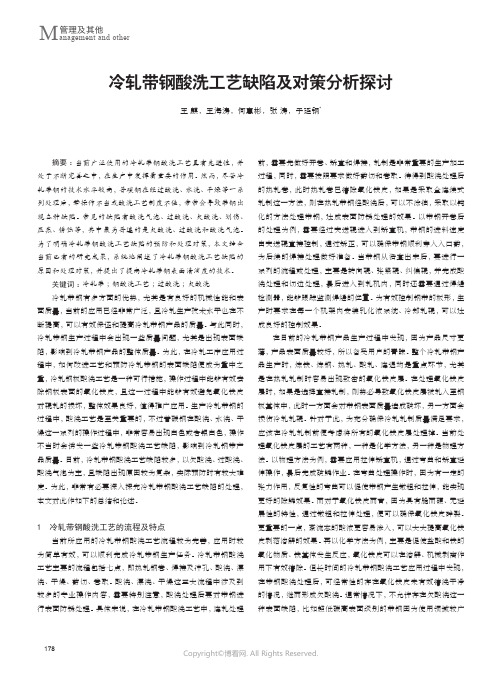
管理及其他M anagement and other冷轧带钢酸洗工艺缺陷及对策分析探讨王 麒,王海涛,何惠彬,张 涛,于延钢*摘要:当前广泛使用的冷轧带钢酸洗工艺具有先进性,并处于不断完善之中,在生产中发挥着重要的作用。
然而,尽管冷轧带钢的技术水平较高,普碳钢在经过酸洗、水洗、干燥等一系列处理后,若操作不当或酸洗工艺制度不佳,常常会导致带钢出现各种缺陷。
常见的缺陷有酸洗气泡、过酸洗、欠酸洗、划伤、压痕、锈蚀等,其中最为普遍的是欠酸洗、过酸洗和酸洗气泡。
为了明确冷轧带钢酸洗工艺缺陷的预防和处理对策,本文结合当前已有的研究成果,系统地阐述了冷轧带钢酸洗工艺缺陷的原因和处理对策,并提出了提高冷轧带钢表面清洁度的技术。
关键词:冷轧带;钢酸洗工艺;过酸洗;欠酸洗冷轧带钢有多方面的优势,尤其是有良好的机械性能和表面质量,当前的应用已经非常广泛,且冷轧生产技术水平也在不断提高,可以有效保证和提高冷轧带钢产品的质量。
与此同时,冷轧带钢生产过程中会出现一些质量问题,尤其是出现表面缺陷,影响到冷轧带钢产品的整体质量。
为此,在冷轧工序应用过程中,如何改进工艺和预防冷轧带钢的表面缺陷便成为重中之重,冷轧钢板酸洗工艺是一种可行措施,操作过程中能够有效去除钢板表面的氧化铁皮,且这一过程中能够有效避免氧化铁皮对辊轧的损坏,整体效果良好,值得推广应用。
生产冷轧带钢的过程中,酸洗工艺是至关重要的,不过普碳钢在酸洗、水洗、干燥这一系列的操作过程中,非常容易出现白色或者银白色,操作不当时会诱发一些冷轧带钢酸洗工艺缺陷,影响到冷轧钢带产品质量。
目前,冷轧带钢酸洗工艺缺陷较多,以欠酸洗、过酸洗、酸洗气泡为主,且缺陷出现原因较为复杂,实际预防时有较大难度。
为此,非常有必要深入探究冷轧带钢酸洗工艺缺陷的处理,本文对此作如下的总结和论述。
1 冷轧带钢酸洗工艺的流程及特点当前所应用的冷轧带钢酸洗工艺流程较为完善,应用时较为简单有效,可以顺利完成冷轧带钢生产任务。
探析冷轧厂酸洗工艺阶段的常见故障及优化

探析冷轧厂酸洗工艺阶段的常见故障及优化目前,为了提高国内钢材生产企业的生产能力,国内生产基地都采用酸洗-冷轧联合机组的设计,联合机组的采用能使工厂年产量达到百万吨以上。
其中酸洗阶段的主要任务是洗掉带钢表面的氧化铁,为冷轧工艺阶段提供合适的加工材料。
所以,维护好酸洗工艺段的设备对于整个加工过程都有重要意义。
本文以德国公司SMS DEMAGG 公司设计的机组为例,通过对酸洗工艺段常见故障进行分析,优化酸洗工艺流程。
1 酸洗工艺阶段的具体生产流程经过酸洗技术的不断改进,目前酸洗阶段采用的工艺都是浅槽紊流酸洗技术。
与传统的深槽酸洗和浅槽酸洗相比,紊流酸洗具有许多优势。
例如带钢以高张力通过酸洗工艺段,省去了张力单元和张力控制系统,设备得到精简;整个机组张力均匀,带钢在机组的运行状况较之前更加流畅;酸洗通道内使用较少的酸液,有利于酸液的工作循环;酸洗时间大大缩短。
整个酸洗工艺段一般分为浅槽紊流式酸洗,带钢平直通过。
酸洗段由3个酸洗槽构成。
酸洗槽的入口和出口上都安装有喷杆,侧喷嘴安装在酸洗槽的侧面,喷嘴的安装调整了酸液的紊流速度,也确定了酸槽中的工艺速度是满负荷的。
每个酸洗槽之间都有安装有一堆挤干辊,并且都连接着拍酸槽。
每个酸洗槽都配套安装有一个循环罐。
循环管路上安装着卧式离心泵,离心泵将酸液通过热交换器和管道运送到酸洗槽。
酸洗槽内的钢都具有特殊涂层并且附加耐酸砖衬保护。
酸洗槽盖放置在水封槽上。
外槽盖主要是由玻璃钢做成,内槽盖是采用浸入式设计,材料是PP材料。
内槽盖在外槽盖的卡槽内安装。
内槽盖在耐酸砖上形成紊流酸洗腔,槽盖由液压缸通过铰链驱动实现开启和关闭功能。
2 酸洗工艺段常见故障2.1 耐酸泵故障耐酸泵是在酸洗阶段为工艺进行提供酸液的主要设备,耐酸泵的正常运转才能为酸液紊流提供足够的动力。
经过在循环罐内的加压,酸液通过热交换器进入到酸洗槽的喷杆和侧面喷嘴处。
该联合机组采用的耐酸泵是来自于MUNSCH公司的单机械密封耐酸泵。
冷拔管常见缺陷、产生原因及预防和消除方法

[选取日期]冷拔无缝钢管常见的缺陷特征产生的原因及预防和消除方法2010年10月08日孟相欣冷拔无缝钢管常见的缺陷特征产生的原因及预防和消除方法一、折迭拔制后,钢管内外表面呈现直线或螺旋方向的折迭,局部或通长的出现在钢管上。
产生的原因:管料表面有折迭或夹杂物,有严重擦伤和裂纹,管料磨修处有棱角或深宽比(H/b)不够。
预防和消除方法:严格把好穿孔热轧质量关。
二、尺寸超差(包括壁厚超差,壁厚不均,直径超差,椭圆偏心)直径超过了标准的偏差,在同一截面上管壁一边薄,一边厚,直径不等,长短轴之差超出标准规定。
产生的原因:1、拔制模具选择不当,或芯棒(内模)调整不当。
2、内外模设计制造不合理或磨损严重,或硬度不够造成变形磨损。
3、热处理时间长,温度高,或热处理性能不均匀。
4、增减壁的规律控制不当。
5、拔制表编制不合格。
6、钢管矫直时被压扁,造成误差较大。
预防和消除方法:1、正确设计和选配拔管模具。
2、正确执行热处理制度,均匀加热。
3、正确调制矫直机,经常校对拔管机各部件和量具。
4、掌握不同钢种、不同规格钢管的增减壁规律。
5、正确合理编制拔制表。
6、椭圆度出格可重新矫直,局部椭圆度出格可切除。
三、划道钢管表面上呈现纵向直线的划痕称为划道,划道长短不一,宽窄不等,多为沟状,可见沟底。
产生的原因:1、拔模表面不光滑,有裂纹或粘结金属。
2、锤头过度部分有棱角,工具磨损。
3、欠酸洗或毛管上残存氧化铁皮。
4、磷化、皂化工序操作不当。
5、内外模以损坏或磨损严重。
6、中间退火不均,变形量不足。
预防和消除方法:1、提高拔管模具的表面质量。
2、钢管酸洗后,氧化铁皮要冲洗干净。
3、锤头过度部分要圆滑无棱角。
4勤检查模具和钢管的表面,发现问题及时处理。
四、斗纹钢管表面沿长度方向呈高低不平的环形波浪或波浪逐个相同排列,局部或通长出现在钢管内外表面上。
产生的原因:1、热处理后的性能不均,热轧时低温钢造成性能不均。
2、酸洗后冲洗不干净,磷化不良导致皂化不均。
常见酸洗缺陷及对策

(4)锈蚀 ) 酸洗后表面重新出现锈层的现象称为锈蚀 锈蚀形成的原因是 锈层的现象称为锈蚀。 形成的原因是: 原料酸洗后表面重新出现锈层的现象称为锈蚀。锈蚀形成的原因是: 带钢(钢板)酸洗后表面残留少许的酸溶液,或带钢清 少许的酸溶液 带钢(钢板)酸洗后表面残留少许的酸溶液,或带钢清洗后没有达到 完全干燥而使表面重新 干燥而使表面重 此外,带钢在酸洗后于高温的清 于高温的 完全干燥而使表面重新生锈。此外,带钢在酸洗后于高温的清洗水中 停留时间过长, 产生锈蚀现象。 锈蚀现象 停留时间过长,也会产生锈蚀现象。 带钢锈蚀处的钢板表面在轧制之后呈暗色 使成品在库存 库存时 带钢锈蚀处的钢板表面在轧制之后呈暗色,它促使成品在库存时再次 锈蚀处的钢板表面在轧制之后呈暗色, 锈蚀, 降低成品材的表面质 严重时使产品报 锈蚀,从而降低成品材的表面质量,严重时使产品报废。 防止锈蚀的措施是严格执行酸洗、清洗操作规程,及时给表面涂油, 及时给表面涂油 涂油, 防止锈蚀的措施是严格 行酸洗、 洗操作规 锈蚀的措施是严格执 并应堆放 干燥的地 堆放在 的地方 并应堆放在干燥的地方。 (5)夹杂 ) 带钢在酸洗后表面出现深陷的星罗棋布的黑点疵病称为夹杂。它是由 星罗棋布的黑点疵病称为夹杂 带钢在酸洗后表面出现深陷的星罗棋布的黑点疵病称为夹杂。它是由 于热轧时氧化铁皮被压入 形成的。这样的缺陷不可能采取酸洗 轧时氧化铁皮被压入所 的缺陷不可能采取酸洗法除 于热轧时氧化铁皮被压入所形成的。这样的缺陷不可能采取酸洗法除 轧后, 点便扩 延伸呈黑色条 去。当它经过冷轧后,黑点便扩展延伸呈黑色条状,大大降低了成品 钢板的冲击性能。 冲击性能 钢板的冲击性能。
6. 酸洗段经常出现的缺陷
(1)酸洗气泡 ) 酸洗气泡产生的机理是:金属和酸产生化学反应时, 酸洗气泡产生的机理是:金属和酸产生化学反应时,生成了部分氢 原子,它渗透到金属的结晶格子中,并使其变形, 原子,它渗透到金属的结晶格子中,并使其变形,变形后使氢更向 金属内扩散,其中一部分氢原子穿过金属并分子化,从酸液中逸出, 金属内扩散,其中一部分氢原子穿过金属并分子化,从酸液中逸出, 部分氢原子的分子化在晶格变形产生的“显微空孔”边界上, 部分氢原子的分子化在晶格变形产生的“显微空孔”边界上,或金 属的夹杂及孔隙中进行,氢在空孔中的压力可达到很大值( 属的夹杂及孔隙中进行,氢在空孔中的压力可达到很大值(几十兆 使金属中产生了引起氢脆的内应力。 帕),使金属中产生了引起氢脆的内应力。 防止产生气泡的措施是:调整酸液的浓度; 防止产生气泡的措施是:调整酸液的浓度;控制酸洗时溶液的温度 和带钢表面平直状态等。 和带钢表面平直状态等。
冷轧带钢酸洗工艺缺陷及对策分析

冷轧带钢酸洗工艺缺陷及对策分析摘要:在日常的工作中,工作人员需要通过酸洗工艺的工艺模式,将钢材料上所覆盖的氧化铁进行清洗,保障好后续工作可以顺利地开展。
在酸洗工艺的使用中仍旧存在一些缺陷,这些缺陷影响了整个加工工作的质量,因此应当针对冷轧带钢酸洗工艺进行升级,在保障钢材质量的基础上,提升钢材生产的效率。
关键词:酸洗工艺;工艺应用;对策;缺陷引言:冷轧带钢酸洗工艺是钢材生产加工中常见的一种工艺类型,主要是针对原料钢卷表面的氧化铁进行清洗,避免原料表面受到氧化铁的影响,导致原料本身的质量受损。
从目前的酸洗工艺应用现状进行分析,发现在工艺应用的过程中,出现了许多的问题,严重影响到了酸洗工艺的应用质量,氧化铁的处理也没有达到对应的要求。
根据实际的情况以及工作的现状进行了解,工作人员的专业水平、设备的使用、现场的监管等,这些对于工艺的开展产生了直接的影响。
一、氧化铁皮结构在城市发展建设过程中,对于钢材的需求量逐渐较大,为了能够平衡市场的需求,在当下的钢材生产加工工作中,采用酸洗-冷轧联合机组的设计,全面提升钢材的生产效率,以便于满足了目前城市建设中对于钢材的需求。
在钢材的加工过程中,酸洗阶段十分的关键,由于钢材料的表面会存在有一层氧化铁,这一层氧化铁需要在酸洗阶段去除。
为了能够保障氧化铁的清洗工作可以顺利地开展,且达到实际的工作标准,当下必须针对工艺应用的情况,进行缺陷的弥补,保障工作人员的专业水平,提高现场的监督力度,促使工艺的使用更加符合规范。
氧化铁皮事实上是一种化学物质,在钢材料的生产过程中,附着于钢表面,对于钢材料本身具有一定的危害性。
为此,在钢材料生产的过程当中,酸洗工艺的应用十分的重要。
在工艺应用之前,工作人员必须对氧化铁皮的结构以及反应情况有较深的了解,这样才能在酸洗工艺的应用过程中。
按照规范进行氧化铁皮的清洗,保障工作的质量[1]。
氧化铁皮的实际结构分为三层,在这三层结构的划分过程中,主要是根据铁的氧化程度、致密度、硬度等因素进行明显的区别。
酸洗与冷轧缺陷

第二章酸洗一、酸洗线的目的酸洗线的目的有四个:1、除去热轧板卷表面氧化铁皮热轧板卷系在终轧温度800—900℃高温下经受热轧,因此,在带钢表面生成大量氧化铁皮。
这种氧化铁皮给冷轧操作带来了障碍,损坏了产品表面的美观,同时,也妨碍镀层性能、喷涂性能。
为除去这种氧化铁皮通常采用机械法和化学法相结合的方法。
所谓机械法是采用除鳞机进行弯曲加工使氧化铁皮中发生龟裂,容易和酸接触而除掉氧化铁皮的方法。
所谓化学法是使氧化铁皮和酸发生反应而除去氧化铁皮的方法。
所使用的酸通常是硫酸或盐酸。
盐酸和硫酸相比较,具有与氧化铁皮反应快、生成的铁盐在盐酸中溶解度大等优点,因此,可加快酸洗线的速度,提高了生产效率。
2、板卷的连接(焊接)为提高后部工序的作业率和收得率,把几个热轧板卷接头焊接起来,形成一个大板卷。
3、侧剪边热轧板卷的板宽全长未必均匀,并且由于边缘存在有龟裂的情况,故通常进行侧剪边。
4、涂油为防止板卷在卷取运输中产生伤痕,防锈或作为轧制顶涂敷,依照以上不同用途涂敷各种油(把这种操作总称预涂油)。
二、酸洗原理1、氧化层构成氧化铁皮是钢在高温下与氧反应而形成的,外层与氧接触更充分,金属与氧反应更彻底。
由金属基体向外依次为氧化亚铁FeO、四氧化三铁Fe3O4、三氧化二铁Fe2O3,其中氧化亚铁层最厚,如图。
影响带钢氧化层厚度的主要因素:带钢终轧和卷取温度;带钢冷却时间;氧化气氛;钢的化学成分。
2、与盐酸的反应在使用盐酸进行酸洗时,由于盐酸和Fe2O3发生反应最快。
基体铁(Fe)比氧化铁皮更容易溶解,容易形成所谓的过酸洗状态,所以,为防止产生过酸洗,添加少量的控制剂,在铁表面形成保护膜,起防止基体铁受酸腐蚀作用。
酸洗槽中,酸液浓度、温度、控制剂量都要严格掌握。
三种氧化铁均能很好地溶于盐酸,各种化学反应中,以氧化亚铁FeO为主,生成氯化亚铁和水。
FeO+2HCl=FeCl2+H2O影响反应进行的主要因素:盐酸浓度高有利于反应进行,但过高会增加酸挥发,使酸耗增加,一般控制在10%-20%;酸液温度高有利于反应进行,但过高也会增加酸挥发,使酸耗增加,一般控制在80℃-90℃;氯化亚铁FeCl2浓度高不有利于反应进行,过高时应更换酸液和冲洗酸槽,一般不超过28 0g/l。
酸洗板常见缺陷及控制措施

酸洗板常见缺陷及控制措施1、酸洗产品概述酸洗板带是以热轧钢卷带为原料,经酸洗后,表面质量和使用要求介于热轧板和冷轧板之间的中间产品。
与热轧板相比,酸洗板的优势主要在于:表面质量好、尺寸精度高、表面光洁度的提高、外观效果的增强以及减少用户分散酸洗造成的环境污染。
另外酸洗产品跟热轧产品相比较,由于表面氧化铁皮已经去除,因而焊接较容易,也利于涂油、上漆等表面处理。
一般热轧产品的表面质量等级是FA,酸洗产品是FB,冷轧产品是FB/FC/FD。
酸洗产品可以代替冷轧产品做一些结构件,也就是以热代冷。
2、酸洗板常见缺陷酸洗板在其生产过程中常见的缺陷主要有:氧化铁皮压入、氧斑(表面山水画)、腰折(横折印)、擦划伤、黄斑、欠酸洗、过酸洗等。
(注:缺陷是和标准或协议要求挂钩的,不符合的才叫缺陷,这里为了方便表达,用缺陷来代之某一类形貌。
)2.1 氧化铁皮压入氧化铁皮压入是热轧轧制过程中形成的一种表面缺陷。
经酸洗后,往往呈黑色点状、长条状压入,表面粗糙,一般有手感,且零星或密集出现。
氧化铁皮产生的原因,与多方面因素有关,主要的有以下几个方面:加热炉加热、除鳞过程、轧制工艺、轧辊材质及状态、辊道状态及轧制计划等。
控制措施:优化加热工艺,增加除鳞道次,定期检查维护辊道及轧辊,使轧制线保持良好的状态。
2.2 氧斑(表面山水画缺陷)氧斑缺陷是指热卷表面氧化铁皮洗掉后,留下的点状、线状或凹坑状形貌,目视呈无规律色差斑迹,由于形状类似山水画,所以也叫山水画缺陷。
目视像高低起伏的山峰状深色图案,在带钢板面呈现整体或者局部分布。
其本质上是氧化铁皮斑迹,氧化铁皮斑迹是浮在表面的一层东西,没有手感,可能颜色会深一点、浅一点。
深色部位相对粗糙,电泳后对外观有一定影响,但是不影响使用性能。
氧斑(山水画缺陷)产生原因:该缺陷本质是热轧带钢表面的氧化铁皮未被除净,经随后的轧制被压入基体,在酸洗后凸显出来。
氧斑的控制措施:降低加热炉出钢温度,增加粗轧除鳞道次,同时优化精轧冷却水工艺。
酸洗资料

酸洗理论资料大纲Ø氧化皮产生原理Ø酸洗理论基础Ø影响酸洗的因素ØH2SO4酸洗理论ØMixed Acid 酸洗理论Ø酸洗引起的带钢缺陷Ø氧化铁皮是金属在加热、热处理或在热状态进行加工时形成的一层附着在金属表面上的金属氧化物。
是热轧带钢时在终轧、卷曲及冷却时产生的。
Ø在从精轧末机架出来的带钢表面上,铁原子首先与空气中的氧原子结合形成第一层氧化物,这层氧化物可能是致密的Fe3O4,或者是疏松的FeO。
在第一种情况下,氧化铁皮的进一步增长过程可能只靠氧和铁的离子扩散来进行的;在第二种情况下,空气中的氧可自由地通过多孔、疏松的氧化铁皮,而使氧化铁皮加厚和致密化。
无论上述哪种情况,最终结果就是形成了我们通常所看到的带钢表面的氧化铁皮。
Fe αFe+Fe 3O 4αFe+FeO3O 4+Fe 2O 3FeO+Fe 3O 4γFe+FeOFeOFe3O4Fe2O3氧化皮与退火炉内氧含量关系FeO+HF→FeF2+H2OFe3O4+HF→FeF3+FeF2+H2OFe2O3+HF →FeF3+H2OFeO+H2SO4→FeSO4+H2OFe3O4+H2SO4→Fe2(SO4)3+FeSO4+H2O Fe2O3+H2SO4→Fe2(SO4)3+H2OH2SO4酸洗理论硫酸(H2SO4)的作用Fe+H2SO4→FeSO4+H2FeO+H2SO4→FeSO4+H2OFe3O4+H2SO4→Fe2(SO4)3+FeSO4+H2OFe2O3+H2SO4→Fe2(SO4)3+H2Oü硫酸在酸洗中与Fe 、FeO 反应较快,与表层的Fe2O3、Fe3O4反应非常慢,所以在之前使用Scale Breaker 与Shot Blaster 使scale 表面龟裂,方便H2SO4流入与FeO 反应,通过FeO 层,使Fe2O3、Fe3O4从基体上脱离,扩大龟裂,后续混酸HF 从龟裂中渗透,与FeO 反应,快速除去氧化皮反应方程式主要有:氢氟酸不仅对scale 而且对金属材料自身也有侵蚀作用,所以这种酸单独使用的情况非常少,通常是与硝酸混合使用,但是硝酸和氢氟酸的混酸比起氢氟酸单独使用效果不是很显著,但F-对不锈钢有强烈的点蚀作用,硝酸与氢氟酸的混酸酸洗效果最优,短时间即能获得良好的表面质量,目前得到普遍使用。
冷轧各工序质量缺陷汇

冷轧各工序质量缺陷汇总冷轧带钢的生产工序流程主要包括:热轧来料、推拉式盐酸酸洗、单机可逆冷轧、电解脱脂清洗、全氢(或氮氢)退火炉、单机平整、重卷纵切(或横切)、拉伸弯曲矫直、包装储存和运输等。
为使全体干部职工对各生产工序有可能造成的产品质量缺陷有一全面了解,以达到全员、全过程控制的目的,现将冷轧各工序有可能产生或存在的质量缺陷汇总如下:一、酸洗工序在酸洗过程中由于工艺参数控制不当,操作不认真或操作失误,将影响酸洗质量,产生各种缺陷,归纳起来缺陷的品种有:酸洗气泡(氢气病),过酸洗,欠酸洗,锈蚀,夹杂,划伤,压痕等,占冷轧产品缺陷的2%左右。
1、酸洗气泡由于酸与裸露的金属作用,生成氢所造成的,外观特征是条状的小鼓泡,破裂后呈黑色细裂缝,冷轧时气泡破裂及延伸扩大,降低产品的冲击韧性。
2、过酸洗金属在酸液中停留时间过长,使金属表面在酸液作用下变得粗糙麻面的现象。
产生的主要原因:开卷、焊接时间过长,穿带时间过长,机械故障停机,调配酸液浓度时停机等,使金属在酸液中滞留时间过长所致,一旦出现过酸洗,将严重影响带材质量,也给轧制生产带来困难:延伸性降低,容易断带、粘轻,很难轧出成品。
3、欠酸洗带钢酸洗后,表面残留局部未酸洗掉的氧化铁皮时称为欠酸洗。
产生的原因:带钢表面严重氧化,氧化皮厚薄不均,较厚的氧化皮需较长的酸洗时间。
酸液的温度低,浓度低,运行速度快,铁盐含量过高等,另外矫直不彻底,波浪大,酸洗时局部未浸泡在酸液中,也容易产生欠酸洗。
一旦出现欠酸洗,在轧制时使产品表面出现暗色,严重时氧化皮压入,形成条状照斑。
4、锈蚀带钢酸洗后表面重新出现锈层的现象叫锈蚀。
产生的原因:清洗槽水中的酸含量超标,带钢清洗后没有完全干燥,表面上还残留有酸和水而使表面重新生锈。
另外,酸洗后在清洗槽中停留时间过长,也将导致锈蚀。
1防止措施:严格执行酸洗、清洗、烘干操作规程,及时进行钝化或涂油处理,并堆放到干燥的地方。
5、窝边、划伤、压痕等由于设备问题、操作不认真引起,上卷时夹盘未对正,运行时跑偏易造成窝边。
冷轧厂酸洗工艺段常见表面缺陷及预防

冷轧厂酸洗工艺段常见表面缺陷及预防摘要:冷轧钢板酸洗的目的是为了去除带钢在生产过程中表面产生的氧化铁皮。
防止在后续加工工艺中氧化铁皮对轧件造成的损坏。
如果未将氧化铁皮清洗干净,则会造成一系列的工艺段表面缺陷,本文简要介绍了酸洗板产生的表面缺陷产生的原因以及如何纠正预防缺陷的发生。
关键词:酸洗线;酸洗;缺陷引言目前,为了提高国内钢材生产企业的生产能力,国内生产基地都采用酸洗-冷轧联合机组的设计,联合机组的采用能使工厂年产量达到百万吨以上。
其中酸洗阶段的主要任务是洗掉带钢表面的氧化铁,为冷轧工艺阶段提供合适的加工材料。
所以,维护好酸洗工艺段的设备对于整个加工过程都有重要意义。
1.酸洗工艺质量缺陷酸洗工艺缺陷主要包括:(1)工艺控制不当造成的缺陷:欠酸洗、过酸洗、停车斑;(2)机械作用造成的缺陷:擦划伤、边丝和毛边、卷边、折皱、缝合;(3)其它水印、边锈、漏涂等。
2.工艺控制不当造成的缺陷及预防纠正措施2.1欠酸洗欠酸洗是带钢表面氧化铁皮与盐酸反应不充分仍残留在带钢表面,其主要成分是Fe304,Fe0。
缺陷特征及判定方法:带钢表面有条纹状或鳞片状黑印.用纸巾擦拭有粘附现象。
多出现于带钢的边部和头尾部,严重时遍布整个带钢表面。
造成的主要原因:酸液的浓度、温度低,酸洗速度过快,或Fe2+浓度过高;另外原料板形、热轧卷取温度等因素也可产生欠酸洗。
边部欠酸洗的产生原因有两方面:1.热轧时带钢边部冷却较快达到570℃以下:Fe0-4Fe304 +Fe并能长时间保持在400-500℃,形成致密的Fe304保护层,给酸洗造成了较大的困难。
2.板形不好导致峰部与酸接触时间短,出现欠酸洗。
头尾部欠酸洗是因为带刚尾部在酸槽垂度太小,酸洗时间不够。
纠正预防措施:首先降低运行速度,到出口活套坑处跟踪观察质量;其次适当将6#槽酸液温度升高1-2℃;进一步查看各酸槽自由酸浓度和Fe2+浓度,如有必要,修改注酸系数,增加注酸量。
另外操作工要及时按产品的不同规格控制酸洗时间。
冷拔无缝钢管缺陷分类与产生原因基本知识

冷拔无缝钢管缺陷分类与产生原因基本知识一. 擦伤:特征:钢管表面呈现长短不一,方向不定的无规则的擦痕,一般呈直线形,均能看到其底。
产生原因:1)退火时操作不当;2)在吊运中划伤;3)在矫直过程中,钢管在套筒处擦伤。
二.划道(又称拉丝、拉毛、直道包括青线)特征:钢管内外表面上呈现纵向直线形的长短不一划道,外为沟状,可见底,表面有损伤内划道,表面无损伤直线。
产生原因:1)毛管上划道;2)毛管上残存有氧化铁皮;3)润滑剂涂层不良,引起摩擦力增加,致使模具发热焊接金属;4)内外模具硬度不够或不均,光洁度差;5)锤头不良,过渡部分产生尖锐的棱角,模具磨损,造成划道。
三.抖纹:特征:在钢管内外表面上,沿长度方向呈高低不平的整圈或半圈波形的环痕,逐个相间排列,有连续的,也有断续的。
一般由拉拔动时抖动(称“打机枪”)所造成。
产生原因:1)酸洗过程未冲净,润滑不良,涂层不均;2)退火性能不均匀,抗拉强度过大,含碳量较高的热轧钢管冷却速度过大,造成钢质较硬,加工硬化;3)管子过大,头部无空隙,皂化不良;4)芯棒细,拔制时芯棒产生弹性变形,引起抖动; 5)拉拔时启动速度过快,或开拉时链条振动;6)配模不合理,入口锥角太大,管与模孔接触面积小,或模具定径位置不当,拔制时变形不稳,定面抖动。
四.凹坑(包括压痕):特征:钢管表面呈面积不一的局部凹陷,有的呈周期性,也有的无规律。
缺陷表面有破伤为凹坑,表面无破伤的为压痕。
产生原因:1)由于氧化铁皮或其他质硬的污物粘附在钢管表面,在拔制或矫直中压入钢管表面后剥落而留下压痕;2)矫直辊粘附了异物,在矫直过程中钢管表面压成凹坑;3)原先存在于钢管表面的翘皮剥落。
五.麻点:特征:钢管表面成片的点状细小凹坑。
产生原因:1)酸洗时产生点状腐蚀;2)退火后氧化铁皮过厚矫直后压入了钢管表面;3)钢管保存不好产生锈蚀;4)氧化皮未清洗干净,拉拔压入管面,产生麻点;5)管面有油污,退火时局部烧成麻面。
酸洗资料及冷拔常用缺陷

酸洗资料及冷拔常用缺陷冷拔钢管中常见的缺陷及其处理方法1、折迭:拔制后,钢管内外表面呈现直线或螺旋方向的折迭,局部或通长的出现在钢管上。
产生的原因:管料表面有折迭或平杂物,有严重擦伤和裂纹,管料磨修处有棱角或深宽比(H/b)不够。
预防和消除方法:严格按照规程要求对管料进行修磨。
不合格管料不投产,防患于未然。
严格把好穿孔热序的质量关。
2、尺寸超差(包括壁厚超差,壁厚不均,直径超差,椭圆)直径超过了标准的偏差范围,在同一截面上管壁一边薄,厚,直径不等,长短轴之差超出标准规定。
产生的原因:1、拔制模具选择不光,或蕊棒(内模)调整不当。
2、拔模内模设计制造不合理或磨损严重,或硬度不够造成变形磨损。
3、热处理时间长,温度高。
或热处理性能不均匀。
4、空拔时增减壁的规律控制不当,拔制表编制不合理。
5、钢管矫直时被压扁,工卡量具未校零,误差大。
预防和消除方法:1、正确设计制造和选配拔管模具。
2、正确执行热处理制度,均匀加热。
3、正确调整矫直机,经常校对拔管机各部件位置和量具。
4、正确合理编制拔制表,掌握不同钢种、不同规格钢管的增减壁规律。
5、椭圆度不出格,判为合格品,椭圆度出格可重新矫直,局部椭圆度出格可切除。
3、划道:钢管表面上呈现纵向直线形的划痕称为划道。
划道长短不一,宽穿窄不等,多为沟状,可见沟底。
产生的原因:1、拔模内表不光滑,有裂纹或结金属。
2、锤头过渡部分有棱角,磨损工具。
3欠酸洗或毛管上残存氧化铁皮。
4、在涂润滑油时,磷化、皂化工序操作不当。
5、内外模已损伤或磨损严重。
6、中间退火不均,变形量不足。
预防和消除方法:1、提高拔管模具的表面质量。
2、氧化皮要酸洗,冲洗干净,涂层要均匀牢固。
3、锤头过渡部分要圆滑无棱角。
4、勤检查模具和钢管表面,发现问题及时处理。
4、抖纹:钢管表面沿长度方向呈高低不平的环形波浪或波浪逐个相同排列,局部的或通长的出现在钢管内外表面上。
产生的原因:1、热处理后的性能不均,润滑不良,皂化不均。
冷轧酸洗常见问题及预防

冷轧酸洗常见问题及预防
冷轧酸洗较易出现的问题有:欠酸洗、过酸洗、宽窄印、停车斑。
相关的原因及预防措施为:
1、欠酸洗
钢带表面残留未酸洗的氧化铁皮,呈横向的黑色条纹。
原因:
拉矫机运行状态不良,使氧化铁皮未经充分疏松剥离;带钢表面的氧化铁皮薄膜未洗干净;酸洗工艺不适当,酸浓度偏低;温度低,酸液中亚铁成分高或速度太快所致;酸槽喷嘴堵塞。
措施:
按酸洗工艺规程控制好酸洗液的浓度、温度和运行速度;降低带钢张力;检查拉矫机,确保其运行状态良好,定时更换上新辊;检查酸洗段喷嘴。
2、过酸洗
带钢表面粗糙,颜色呈现黑暗色或棕黑色。
原因:
酸洗机组工艺速度太低,带钢在酸洗工艺段停留时间过长;酸洗温度过高;酸洗浓度过高;设备故障,被迫停车。
措施:
缩短设备故障排除时间;严格控制酸洗工艺,按酸洗技术规程要求控制好酸液浓度,温度和工艺段速度;出现大的设备事故时要将酸液放到罐内。
3、宽窄印
板带边部出现一明显条痕。
原因:
宽度规格变化时,拉矫机换辊不及时;宽度规格变化时,轧机工作辊换辊不及时。
措施:
发现时及时停车;及时更换拉矫机或轧机工作辊。
4、停车斑
停车时,钢带表面出现大片斑迹。
呈黄色、严重时呈黑色。
原因:
带钢在酸槽中停留时间过长,酸液与带钢长时间接触,酸洗液化合物在带钢表面沉积。
措施:
尽量减少因设备故障引起的酸洗工艺段停机。
冷拔管常见缺陷产生原因及预防和消除方法
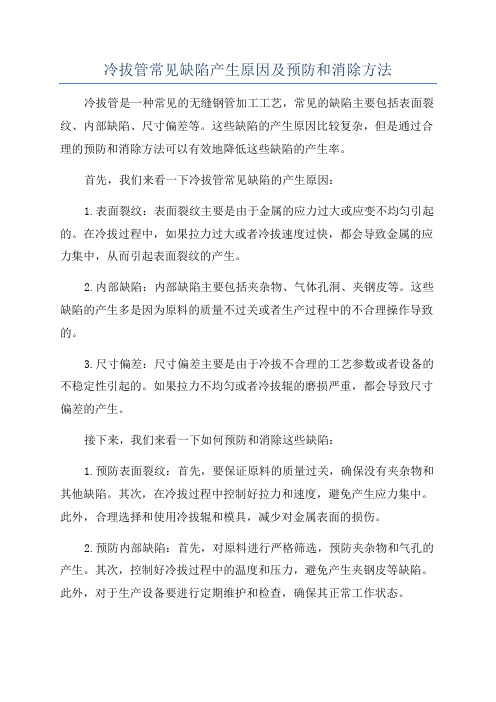
冷拔管常见缺陷产生原因及预防和消除方法冷拔管是一种常见的无缝钢管加工工艺,常见的缺陷主要包括表面裂纹、内部缺陷、尺寸偏差等。
这些缺陷的产生原因比较复杂,但是通过合理的预防和消除方法可以有效地降低这些缺陷的产生率。
首先,我们来看一下冷拔管常见缺陷的产生原因:1.表面裂纹:表面裂纹主要是由于金属的应力过大或应变不均匀引起的。
在冷拔过程中,如果拉力过大或者冷拔速度过快,都会导致金属的应力集中,从而引起表面裂纹的产生。
2.内部缺陷:内部缺陷主要包括夹杂物、气体孔洞、夹钢皮等。
这些缺陷的产生多是因为原料的质量不过关或者生产过程中的不合理操作导致的。
3.尺寸偏差:尺寸偏差主要是由于冷拔不合理的工艺参数或者设备的不稳定性引起的。
如果拉力不均匀或者冷拔辊的磨损严重,都会导致尺寸偏差的产生。
接下来,我们来看一下如何预防和消除这些缺陷:1.预防表面裂纹:首先,要保证原料的质量过关,确保没有夹杂物和其他缺陷。
其次,在冷拔过程中控制好拉力和速度,避免产生应力集中。
此外,合理选择和使用冷拔辊和模具,减少对金属表面的损伤。
2.预防内部缺陷:首先,对原料进行严格筛选,预防夹杂物和气孔的产生。
其次,控制好冷拔过程中的温度和压力,避免产生夹钢皮等缺陷。
此外,对于生产设备要进行定期维护和检查,确保其正常工作状态。
3.预防尺寸偏差:首先,要合理选择冷拔工艺参数,尽量保证拉力的均匀分布。
其次,定期检查和更换冷拔辊和模具,减少磨损对尺寸的影响。
此外,对于冷拔设备要进行定期维护和校准,确保其稳定性。
除了以上措施外,还可以通过加热退火、自动控制系统、成品质量检测等方法来预防和消除冷拔管的常见缺陷。
加热退火可以降低冷拔过程中的应力,提高内部结构的均匀性;自动控制系统可以实时监测冷拔过程中的各项参数,并进行调整;成品质量检测可以及时发现和修复缺陷,确保产品的合格率。
综上所述,冷拔管常见缺陷的产生原因比较复杂,但是通过合理的预防和消除方法可以有效地降低这些缺陷的产生率。
- 1、下载文档前请自行甄别文档内容的完整性,平台不提供额外的编辑、内容补充、找答案等附加服务。
- 2、"仅部分预览"的文档,不可在线预览部分如存在完整性等问题,可反馈申请退款(可完整预览的文档不适用该条件!)。
- 3、如文档侵犯您的权益,请联系客服反馈,我们会尽快为您处理(人工客服工作时间:9:00-18:30)。
冷拔钢管中常见的缺陷及其处理方法1、折迭:拔制后,钢管内外表面呈现直线或螺旋方向的折迭,局部或通长的出现在钢管上。
产生的原因:管料表面有折迭或平杂物,有严重擦伤和裂纹,管料磨修处有棱角或深宽比(H/b)不够。
预防和消除方法:严格按照规程要求对管料进行修磨。
不合格管料不投产,防患于未然。
严格把好穿孔热序的质量关。
2、尺寸超差(包括壁厚超差,壁厚不均,直径超差,椭圆)直径超过了标准的偏差范围,在同一截面上管壁一边薄,厚,直径不等,长短轴之差超出标准规定。
产生的原因:1、拔制模具选择不光,或蕊棒(内模)调整不当。
2、拔模内模设计制造不合理或磨损严重,或硬度不够造成变形磨损。
3、热处理时间长,温度高。
或热处理性能不均匀。
4、空拔时增减壁的规律控制不当,拔制表编制不合理。
5、钢管矫直时被压扁,工卡量具未校零,误差大。
预防和消除方法:1、正确设计制造和选配拔管模具。
2、正确执行热处理制度,均匀加热。
3、正确调整矫直机,经常校对拔管机各部件位置和量具。
4、正确合理编制拔制表,掌握不同钢种、不同规格钢管的增减壁规律。
5、椭圆度不出格,判为合格品,椭圆度出格可重新矫直,局部椭圆度出格可切除。
3、划道:钢管表面上呈现纵向直线形的划痕称为划道。
划道长短不一,宽穿窄不等,多为沟状,可见沟底。
产生的原因:1、拔模内表不光滑,有裂纹或结金属。
2、锤头过渡部分有棱角,磨损工具。
3欠酸洗或毛管上残存氧化铁皮。
4、在涂润滑油时,磷化、皂化工序操作不当。
5、内外模已损伤或磨损严重。
6、中间退火不均,变形量不足。
预防和消除方法:1、提高拔管模具的表面质量。
2、氧化皮要酸洗,冲洗干净,涂层要均匀牢固。
3、锤头过渡部分要圆滑无棱角。
4、勤检查模具和钢管表面,发现问题及时处理。
4、抖纹:钢管表面沿长度方向呈高低不平的环形波浪或波浪逐个相同排列,局部的或通长的出现在钢管内外表面上。
产生的原因:1、热处理后的性能不均,润滑不良,皂化不均。
3、蕊杆细,拔制时蕊杆产生弹性变形引起抖动。
4、拔模形状不合理,入口锥角太大,使钢管与模孔的接触面积过小,使拔制变形不稳定面抖动。
预防和消除方法:1、按规程要求进行处理达到软化,性能均匀。
2、要把好酸洗、磷化、皂化的质量关。
3、按规定的变霰量拔制。
4正确选用蕊杆尺寸。
5、拔凹:在钢管纵向上,管壁向内呈条状凹陷,其长短无规则。
产生的原因:1、无蕊棒拔制(空拔)薄钢管时,减径量过大。
2、钢管锤头端部有棱角,过渡部分有皱折。
3、管料局部薄壁(如磨修点)。
预防和消除方法:1、空拔薄壁管时,要合理分配减经量。
2、锤头端部应无棱角和皱折。
3、对管料表面的局部缺陷,清理,深宽比要合理。
6、开裂(纵裂):钢管呈现穿透管壁的纵向裂开,有通长局部开裂。
产生的原因:1、压下量过大,连拔道次过多,管料加工硬化严重,空拔尤甚。
2、热处理不当,造面管料塑性不一至功加工硬化未全部消除。
3、钢管拔制后未及时热处理。
4、塑性低的钢种较易开裂。
预防和消除方法:1、合理编制拔制表。
2、合金钢管和连拔钢管拔后要及时热处理。
3、按工艺要求进行热处理,冷却速度要合理控制,使其性能均匀,消除加工硬化。
7、过酸洗:钢管表面呈现孔状、芝麻状裂口,轻重程度不同一般外表面比内表严重。
产生的原因:1、钢管表面氧化皮厚薄不均,疏松与牢固不同。
2、酸洗时间过长。
3、酸洗浓度低,硫酸亚铁含量高,在酸洗温度高的情况下,容易过酸洗。
4、酸液浓度不均,溶液不流动,腐蚀不均。
预防和消除方法:1、正确执行酸洗技术操作规程。
2、掌握好热处理操作,防止钢管表面氧化铁皮厚薄不均。
3、严格贯彻勤吊勤看、勤检查,防止过酸洗。
8、麻点:(麻面、麻坑)钢管表面成片的细点状凹坑,局部或连续的出现在钢管表面上。
产生的原因:1、热处理造成氧化铁皮过厚,在矫直时氧化铁皮压入剥落后产生麻点。
2、酸洗后残留氧化铁皮或皂化液中有脏物,拔后产生麻点。
3、管子酸洗后,停放时间过长生锈造成麻面。
4、管子表面有油污,热处理时聚结成油点在加热时烧成麻面。
预防和消除方法:装炉时正确执行热处理制度。
2、坚持快速周转。
3、酸洗做不到过洗、不欠洗,酸洗后及时拔制。
9、拉拔断裂:拉拔产生怪叫声,缺少润滑效果,模蕊拉毛,管内拉伤,拉拔机负荷增大,成品率降低等。
产生原因:1、前道工序不符合操作规程,在某一环节上出现问题,如酸洗碳化(氢脆)、钢管拉拔时造成断裂。
2、磷化不达标,过渡(太老)造成拉拔时磷化膜脱落,未完成皂化目的,即产生冷拔时怪叫声不断。
3、皂化温度太低或太高,浓度不足,皂化吸附量不足或皂液被酸化失去润滑效果。
4、磷化不足造成模蕊和管内壁损伤,拉拔时负荷增大。
预防和消除方法:1、各道工序严格把关,控制酸洗浓度、温度、时间,勤冲洗、换水。
2、经常检查磷化液的总酸度,游离酸度,形成足量的磷化膜。
3、控制皂化温度、浓度,保持槽内皂液清洁,免除酸化。
4、检查变形量模具、模蕊是否达标。
要想提高质量,只有严格把关,按工序要求操作,在生产中寻找规律,总结经验,解除磷化质量控制及检测方法2磷化后的工件,根据其用途,对其质量指标进行分项检验。
主要质量控制指标,包括磷化膜外观、磷化膜厚度或膜重、磷化膜或后处理以后的耐蚀性三大共性指标。
根据磷化用途有时还要检测:磷化与漆膜配套性、磷化膜硬度、摩擦系数、抗擦伤性等指标。
关于磷化的三共性指标,可参照如下标准及方法。
磷化膜外观:采用目测法,相关标准G B11376-89《金属的磷酸盐转化膜》和G B6807-86《钢铁工件涂漆前磷化处理技术条件》。
磷化膜厚度或膜重:膜厚度测量采用G B6462《金属的氧化覆盖层横断面厚度显微镜测量法》,也可采用测厚仪,按照G B4956《磁性金属基体上非磁性覆盖层厚度测量磁性方法》或G B4957《非磁性金属基体上非导电覆盖层测量涡流方法》。
膜重测量采用重量法,可依照G B6807《钢铁工件涂漆前磷化处理技术条件》或G B9792《金属材料上的转化膜单位面积上膜层质量的测定》。
耐蚀性:检测磷化膜本身的耐蚀性可采用硫酸铜点滴法,氯化钠盐水浸泡法和盐雾试验法。
点滴法和盐水浸泡法可依照G B6807-86《钢铁件涂漆前磷化处理技术条件》,磷化膜经过后处理如涂油,涂蜡,涂漆后一般进行盐雾试验检验。
盐雾试验可依照G B1771-79《漆膜耐盐雾测定法》或G B6458《金属覆盖层中性盐雾性试验》。
1.涂漆前打底用磷化用于漆前打底的磷化处理,其主要目的是提高漆膜的附着力和涂层系统的耐蚀性,因此重点在于与漆膜的配合性能方面。
一般对磷化质量检测指标包括膜外观、膜厚度和与漆膜配套后的性能。
膜外观应为均匀细密完整的磷化膜,对轻铁系磷化,其外观应为均匀细密完整的磷化膜,对轻铁系磷化,其外观应为完整的红蓝彩色膜。
磷化膜不宜过厚,一般膜重应小于7.5g/m2,最佳为1.5~3.0g/m2,对于轻铁系磷化膜重0.5~1.0g/m2为宜,过厚和粗糙的磷化膜是不利涂漆的。
耐蚀性指标包括磷化膜本身的耐蚀性和涂漆前不应出现泛黄生锈现象。
磷化与漆配合后的耐蚀性是最为重要的,它体现了磷化膜与漆协同后的整体耐蚀能力。
磷化膜与涂漆配合后除检测耐蚀性外,一般还需测定其漆膜的机械物理性能,如:附着力、冲击强度、抗弯能力(柔韧性)等。
涂漆前打底用磷化的质量指标及检测方法一般应参照国家标准G B6807-86《钢铁工件涂漆前磷化处理技术条件》,该标准对磷化膜的各项质量指标及检测评价方法都有较详细的规定,其主要内容如下:(1)磷化膜外观应为结晶致密、连续均匀的浅灰到深灰色膜,对于轻铁系磷化应为连续彩色膜。
允许出现下述缺陷;轻微的水迹,铬酸盐痕迹、轻微挂灰现象,由于热处理焊接及加工等表面状态不同造成的磷化膜缺陷。
对于下述则是不允许出现的缺陷:磷化膜出现泛黄生锈、磷化膜疏松、磷化露底局部无膜,严重挂灰。
(2)涂漆用磷化膜重应低于7.5克/m2。
(3)磷化膜的耐蚀性采用盐水浸泡法,磷化工件在3%N a C l水溶液中,在15~25℃温度下,浸泡1h不应出现锈蚀。
磷化与漆膜配合后的耐蚀性检测是将磷化工件涂覆25~35μm的A04-9白氨基漆,划痕后进行盐雾试验(按G B1771-79)经24h盐雾试验(铁系磷化是8h盐雾试验)漆膜应无起泡、生锈、脱落现象。
G B6807-86对硫酸铜点滴法没有作为必须检测的项目,认为可作为工序间磷化质量的快速检验方法,而对磷化与涂漆配合后的耐蚀性作为必检项目。
对于漆前磷化的检验指标及方法也可参照G B11376-89《金属的磷酸盐转化膜》。
因此,从标准的规定检验项目看,漆前打底用磷化应该是致密、均匀、薄层磷化膜,应着重检验磷化与油漆配套后的耐蚀性及机械物理性能。
2.对防锈、耐蚀用磷化对于这类磷化,其主要目的是为了耐蚀防护,其耐蚀性是最为重要的指标。
一般的质量检测指标包硫酸铜点滴要大于1m i n,耐盐水大于2h,盐雾试验大于1.5h。
有关涂油或涂蜡后的耐蚀性检测,最好采用盐雾试验,具体应达到的耐盐雾时间,可由供需双方商定。
3.润滑、耐磨减摩磷化起润滑作用的磷化主要用在冷加工方面,一般是锌系。
耐磨减摩磷化是用于载荷摩擦运动的工件,常规的是锰系磷化。
对于起润滑作用的磷化,主要检验外观、膜重、耐蚀性以及皂化后的滑润性,有时要测定摩擦系数。
要求磷化膜外观应均匀完整,一般膜重大于5g/m2,以保证有一定的膜厚,经皂化后,明显降低摩擦力,减少模具损伤,减少工件冷作时的开裂。
对于耐磨减摩磷化,一般为锰系磷化,其磷化膜外观应为均匀完整深灰或黑色膜。
对于配合间隙小的零部件,其膜重应在1~3g/m2,动配合间隙大的工件,其膜重应在5g/m2以上。
要求这类磷化有较高的硬度和抗擦伤性能,具体指标可由供需双方商定。
同时耐磨减摩磷化应有较好的耐蚀性,通常耐盐雾应在1.5h以上。
对于润滑、耐磨减摩磷化同样可参照G B11976-89。
4.其它用途的磷化磷化除了用上述三个领域外,还可用于电绝缘方面,装饰性方面。
其常规质量检测指标为外观、膜重和耐蚀性。
对电绝缘磷化,要求检测单位面积上的表面电阻。
对装饰性磷化要根据不同的要求进行染色处理,要求不同的颜色色度和耐蚀性,这些指标的检测方法和控制范围一般由供需双方商定。
磷化质量指标的检测和控制,是根据其用途的不同要有各种不同的要求,除常规的外观、膜重,某些磷化的耐蚀性有标准可遵循外,大部分指标及检测方法都是由供需双方商定。
产品中心:钢管冷拔磷化润滑系列→ XL-2000钢管冷拔专用磷化剂一、特点及适用范围:X L-2000钢管冷拔磷化剂是一种磷酸锌系中温磷化处理剂。
磷化膜为深灰色,膜重4-8g/m2,膜层结晶致密、均匀与基体附着力强。
该磷化剂是较先进、具有高科技含量的磷化产品,使用该产品进行磷化处理,可使金属表面转换成非金属表面,生成磷酸锌膜结构,并且有吸附润滑剂性能,有利于金属塑性加工处理。