轿车精密塑料件成型模具的设计要点
汽车模具结构设计标准有哪些

汽车模具结构设计标准有哪些
汽车模具的结构设计标准主要包括以下几个方面:
1. 制造材料选择:汽车模具需要选择高强度、耐磨损、耐腐蚀的材料,如优质合金钢、工具钢或工程塑料等。
2. 结构稳定性:模具在工作过程中需要承受较大的压力和冲击,因此需要保证其结构具有足够的刚性和稳定性,以确保模具的精度和寿命。
3. 表面质量要求:模具的表面质量直接影响到汽车零部件的外观和功能,因此需要保证模具加工的表面光洁度、平整度和精度满足要求。
4. 模具尺寸精度:对于汽车模具而言,尺寸精度是非常重要的指标之一,因为模具的精度直接决定了汽车零部件的装配性能和使用寿命。
5. 模具生产工艺要求:模具的生产工艺应该合理,方便制造、安装和维修。
同时,还需要考虑到模具的耐磨耐蚀性能和容易修复性。
6. 模具使用寿命要求:汽车模具在使用过程中需要经受大量的工作循环和冲击,因此要求具有较长的使用寿命,一般应能够达到百万次以上的冲击寿命。
7. 安全性要求:汽车模具的设计应考虑到安全因素,防止意外
发生。
例如,模具中应该设置防护装置,确保操作员的安全。
8. 维修与更换要求:汽车模具在使用过程中可能会发生磨损或损坏,因此需要设计方便的维修和更换方式,以减少停机时间和成本。
9. 环境保护:汽车模具的制造和使用应符合环保要求,尽量减少对环境的污染。
总结来说,汽车模具的结构设计标准涵盖了材料选择、结构稳定性、表面质量、尺寸精度、生产工艺、使用寿命、安全性、维修与更换以及环境保护等多个方面,以确保模具的质量和性能符合汽车制造的要求。
(整理)精密模具设计要点

精密注射模具设计要点随着电子、电信、医疗、汽车等行业的迅速发展,对塑件的精度、性能要求也越来越高、精密注射成型要求塑件不仅具有较高的尺寸精度、较低的翘曲变形,而且还要有优异的光学性能。
注射成型是最重要的塑料成型方法之一,如何提高注射成型技术水平,生产出高精度的塑件,创造高附加值的产品,模具设计是重要环节。
在精密注射成型模设计中,除了应考虑一般模具设计事项外,还要特别考虑如下事项。
2 适当的模具尺寸精度2.1 塑件尺寸精度与模具尺寸精度的关联根据塑件图考虑模具设计、模具制作和塑件成型过程。
首先从塑件图面尺寸求得模具图面尺寸,然后按模具图面尺寸制作模具,得到模具实际尺寸,再由模具得到成型塑件。
但问题是如何保证塑件实际尺寸在图面所要求尺寸公差内。
2.2适当的收缩率即使同一树脂收缩率也会因成型条件不同而不同,精密成型要求收缩率变化小,预计收缩率和实际收缩率尽可能无差异。
当前收缩率的确定主要是通过整理以往类似塑件的实际收缩率来推定,也有用实验模求实际收缩率,再经修正,设计制作生产模。
但完全恰当地推定收缩率几乎是不可能的,不可避免地要在试模后修正模具。
为便于模具修正,在设计模具凹部尺寸时应将收缩率取小值,设计凸部尺寸时将收缩率取小值,设计凸部尺寸时将收缩率取大值。
3 防止产生收缩率波动精密注射成型必须以确定的尺寸作为制怍模具的前提。
然而,即使模具尺寸一定,塑件实际尺寸也会因实际收缩率不同而不同,所以在精密注射成型中,收缩率控制十分重要。
3.1 影响收缩率的主要因素模具尺寸可由塑件尺寸加上收缩率求得,所以在模具设计时需考虑影响收缩率的主要因素。
影响收缩率的主要因素有:①注射压力;②树脂温度;③模具温度;④浇口截面积;⑤注射时间;⑥冷却时间;⑦塑件壁厚;⑧增强材料含量;⑨定向性;⑩注射速度。
但塑件成型后仍然存在收缩,影响成型后收缩的主要因素有内部应力、结晶度、温度、湿度等。
(1)注射压力的影响。
注射压力对收缩率影响很大,注射压力大,收缩率小,塑件实际尺寸较大。
汽车模具设计标准与要求
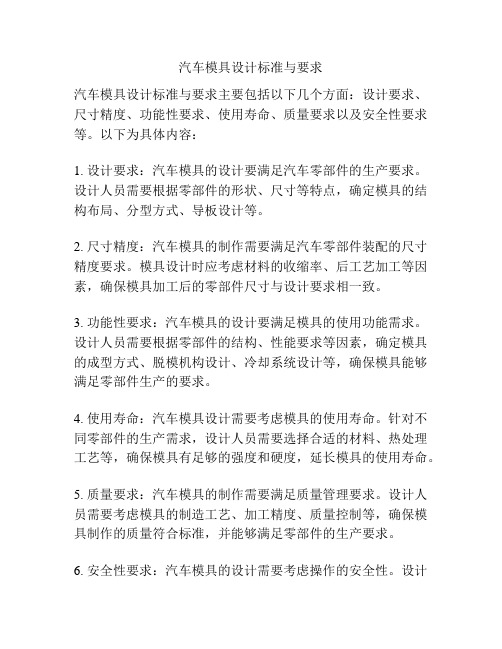
汽车模具设计标准与要求
汽车模具设计标准与要求主要包括以下几个方面:设计要求、尺寸精度、功能性要求、使用寿命、质量要求以及安全性要求等。
以下为具体内容:
1. 设计要求:汽车模具的设计要满足汽车零部件的生产要求。
设计人员需要根据零部件的形状、尺寸等特点,确定模具的结构布局、分型方式、导板设计等。
2. 尺寸精度:汽车模具的制作需要满足汽车零部件装配的尺寸精度要求。
模具设计时应考虑材料的收缩率、后工艺加工等因素,确保模具加工后的零部件尺寸与设计要求相一致。
3. 功能性要求:汽车模具的设计要满足模具的使用功能需求。
设计人员需要根据零部件的结构、性能要求等因素,确定模具的成型方式、脱模机构设计、冷却系统设计等,确保模具能够满足零部件生产的要求。
4. 使用寿命:汽车模具设计需要考虑模具的使用寿命。
针对不同零部件的生产需求,设计人员需要选择合适的材料、热处理工艺等,确保模具有足够的强度和硬度,延长模具的使用寿命。
5. 质量要求:汽车模具的制作需要满足质量管理要求。
设计人员需要考虑模具的制造工艺、加工精度、质量控制等,确保模具制作的质量符合标准,并能够满足零部件的生产要求。
6. 安全性要求:汽车模具的设计需要考虑操作的安全性。
设计
人员需要合理设置模具的安全装置、警示标识等,确保操作人员的人身安全。
总之,汽车模具设计标准与要求是为了保证模具能够满足汽车生产的需求,并达到高质量、高效率的生产目标。
模具设计人员应严格按照标准要求进行设计,确保模具的质量和安全性。
汽车注塑件(塑料件)设计时需要遵循的14个基本原则

(2)拔模角和高度 通常,筋的拔模角在1-1.5度,最小不能小于0.5度,否则会导致零件脱模困
难。越高的筋顶部往往很薄,导致注塑过程中难以充满也就失去了筋的意义。筋 的顶端厚度一般不低于1毫米,高度一般为零件壁厚的2.5-3倍。当然也会有例外, 需要具体分析。
0.5 deg min 筋厚
Байду номын сангаас
1 min 壁厚
D min D min
塑料件中的柱销也是我们常用到的结构,主要用于提供连接和定位。 • 设计要点:
(1)像筋的设计一样要考虑拔模角度、出模方向、根部厚度与基本壁厚的比 例等。
(2)另外,我们还有一个相互矛盾的问题需要考虑。一方面,我们希望销柱 的厚度(B)尽量薄些,以防止表面出现缩痕。另一方面,我们希望其厚度能厚 一些,以增加结构强度。最终,我们要根据产品结构和材料等综合分析确定。
塑料件翻边结构十分重要,它能够明显提高制件的结构刚度控制变形,是很 有用的结构,我们设计时必须尽量考虑增加翻边结构。 • 设计要点:
(1)翻边的厚度应该与基本壁厚一致。 (2)考虑到零件花纹,我们对翻边的拔模角度有特殊的要求,一般在3-6度之 间。但是不同的花纹会有不同的要求,设计时应根据花纹要求及制造和质量要求 选择适当的拔模角。
P/L P/L
8 有许多种类型的花纹可以用于零件表面的装饰。我们设计时需要针对不同的
花纹选择合适的设计结构。 • 设计要点:
(1)拔模角—总的规则是每增加0.025毫米的花纹深度,需要增加至少1度的拔 模角。关于花纹和拔模角需要设计者和花纹供应商共同检查和确认,并得到 OEM的认可。
(2)翻边—对于翻边结构,花纹和拔模角的关系是最突出的。翻边结构就需 要一定的脱摸角度,以便零件从模具内移出。越长的翻边需要越大的脱模角度, 越深的花纹,也需要越大的脱模角度。如果不注意这点就会产生零件脱模困难, 甚至擦伤零件花纹表面。
塑料模成形件结构与尺寸设计
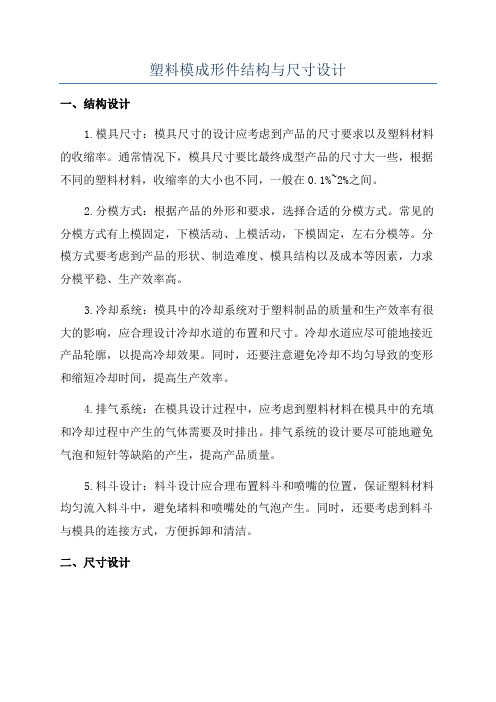
塑料模成形件结构与尺寸设计一、结构设计1.模具尺寸:模具尺寸的设计应考虑到产品的尺寸要求以及塑料材料的收缩率。
通常情况下,模具尺寸要比最终成型产品的尺寸大一些,根据不同的塑料材料,收缩率的大小也不同,一般在0.1%~2%之间。
2.分模方式:根据产品的外形和要求,选择合适的分模方式。
常见的分模方式有上模固定,下模活动、上模活动,下模固定,左右分模等。
分模方式要考虑到产品的形状、制造难度、模具结构以及成本等因素,力求分模平稳、生产效率高。
3.冷却系统:模具中的冷却系统对于塑料制品的质量和生产效率有很大的影响,应合理设计冷却水道的布置和尺寸。
冷却水道应尽可能地接近产品轮廓,以提高冷却效果。
同时,还要注意避免冷却不均匀导致的变形和缩短冷却时间,提高生产效率。
4.排气系统:在模具设计过程中,应考虑到塑料材料在模具中的充填和冷却过程中产生的气体需要及时排出。
排气系统的设计要尽可能地避免气泡和短针等缺陷的产生,提高产品质量。
5.料斗设计:料斗设计应合理布置料斗和喷嘴的位置,保证塑料材料均匀流入料斗中,避免堵料和喷嘴处的气泡产生。
同时,还要考虑到料斗与模具的连接方式,方便拆卸和清洁。
二、尺寸设计1.壁厚设计:产品的壁厚直接影响到成型产品的质量和性能。
壁厚过大会导致成型缩短和变形,壁厚过薄会导致产品强度不足。
在设计过程中,应根据产品的用途和要求,合理控制壁厚,提高产品的质量。
2.锁模力设计:锁模力是模具分模过程中所需的力量,应根据产品的大小、结构和材料的性质来确定。
锁模力过大会增加设备的负荷,锁模力过小会导致模具分模不完全。
3.滑动件设计:针对有滑动结构的成型件,应合理设计滑块的位置和形状,保证滑块流动灵活,防止在使用过程中卡死或损坏。
同时,在设计过程中要注意滑动件与模具的配合尺寸,以确保分模顺利。
4.拉伸设计:对于有需求的拉伸结构的成型件,应合理设置拉伸杆的位置和形状,保证拉伸过程平稳,防止拉伸不均匀导致的变形或拉断现象的发生。
塑料注塑成型中的模具设计与优化
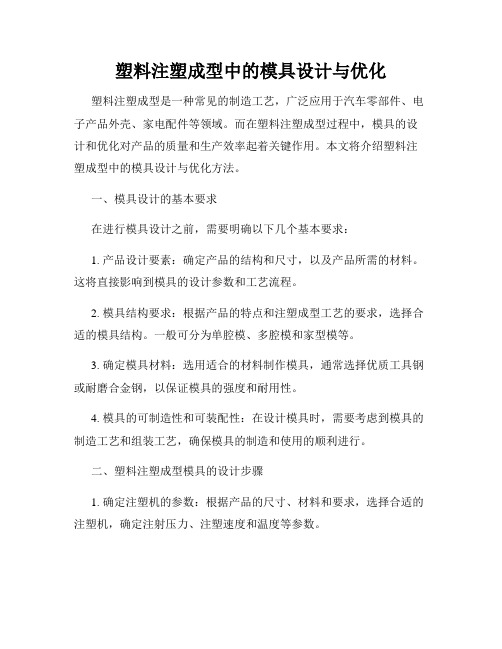
塑料注塑成型中的模具设计与优化塑料注塑成型是一种常见的制造工艺,广泛应用于汽车零部件、电子产品外壳、家电配件等领域。
而在塑料注塑成型过程中,模具的设计和优化对产品的质量和生产效率起着关键作用。
本文将介绍塑料注塑成型中的模具设计与优化方法。
一、模具设计的基本要求在进行模具设计之前,需要明确以下几个基本要求:1. 产品设计要素:确定产品的结构和尺寸,以及产品所需的材料。
这将直接影响到模具的设计参数和工艺流程。
2. 模具结构要求:根据产品的特点和注塑成型工艺的要求,选择合适的模具结构。
一般可分为单腔模、多腔模和家型模等。
3. 确定模具材料:选用适合的材料制作模具,通常选择优质工具钢或耐磨合金钢,以保证模具的强度和耐用性。
4. 模具的可制造性和可装配性:在设计模具时,需要考虑到模具的制造工艺和组装工艺,确保模具的制造和使用的顺利进行。
二、塑料注塑成型模具的设计步骤1. 确定注塑机的参数:根据产品的尺寸、材料和要求,选择合适的注塑机,确定注射压力、注塑速度和温度等参数。
2. 模具整体结构设计:根据产品的结构和尺寸,设计模具的整体结构,包括模具的型腔、型芯、导向机构等,并保证模具的生产效率和质量要求。
3. 流道系统设计:流道系统是模具中传递熔融塑料的管道系统,需要根据产品的结构和注塑工艺的要求进行设计,确保熔融塑料能够顺利注入模腔中。
4. 冷却系统设计:冷却系统是模具中的关键部分,可以通过冷却系统的设计合理调节模具温度,确保产品的质量和生产效率。
一般采用水冷却方式,需要在模具设计中合理布置冷却水路。
5. 塑料料斗和顶出机构设计:根据注塑成型的要求,设计合适的塑料料斗和顶出机构,以保证熔融塑料能够顺利注塑和产品能够从模具中顺利脱模。
三、模具设计的优化方法在塑料注塑成型过程中,模具设计的优化可以提高产品的质量和生产效率,降低生产成本。
以下是一些常用的模具设计优化方法:1. 流道长度和直径优化:流道的长度和直径对产品的注塑过程有着重要影响,应根据产品的尺寸和注塑机的要求进行合理设计,以减少产品的缩水和留痕。
汽车塑料产品结构设计的一般原则及精度

②模具
• 对于小尺寸的塑料件,模具的制造误差占塑料公 差的1/3。
• 与模具上运动的零件有关的塑件尺寸,其精度较 低。
• 模具上浇注系统和冷却系统设计不当,会使成型 塑件的收缩不均匀。
• 脱模系统的作用力不当,会使被顶出塑件变形。
a
43
③塑件结构
• 塑料件壁厚均匀一致,形体又对称,可使 塑件收缩均衡。提高塑料件的刚性,如加 强筋的合理设置或采用金属嵌件,能减小 塑件翘曲变形,都有利于提高塑件精度。
a
44
④工艺
• 注射周期各阶段的温度、压力和时间会影 响塑件的收缩、取向和残余应力,存在对 于塑件精度要求的最佳工艺。保证注塑件 精度更重要的是工艺参数的稳定性。成型 条件波动所造成的误差占塑件公差的1/3。
a
45
⑤使用
• 塑料材料对时间、温度、湿度和环境条件 的敏感性,在注射成型制品长期使用后, 会有显现。注塑件的尺寸和形位精度的稳 定性差。
形、瓦楞形、拱形、球形、抛物面,其刚 性比同样重量的平板要高得多
a
22
(2)加强筋的设计和运用
通过加强筋提高轴套扭转刚 性和弯曲刚性
a
23
容器沿口部位的设计起到了边缘增强
的作用,实质上这种突变的边缘可以 看作是加强筋的变异。
a
24(3)嵌ຫໍສະໝຸດ 的加强作用• 在制件中设置金属嵌件,可以提高塑料制件局部 或整体的强度。
a
38
a
39
1、影响因素
a
40
① 材料
• 注塑模塑的塑料在高温高压的熔融状态下充模流 动。常见的各种熔体温度为170-300℃。然后被冷 却固化,通常脱模温度在20-100℃。
• 下表 列出了常用的注射塑料的成型收缩率。 • 用无机填料填充、用玻璃纤维增强的塑料有较低
汽车塑料件结构设计的一般原则及精度

3 6
0.08 0.16 0.12 0.22 0.14 0.34 0.18 0.38 0.24 0.44 0.32 0.52 0.48 0.68
±0.12 ±0.22 ±0.16 ±0.26 ±0.24 ±0.34
6 10
0.09 0.18 0.14 0.24 0.16 0.36 0.20 0.40 0.28 0.48 0.38 0.58 0.58 0.78
下表 列出了常用的注射塑料的成型收缩率。 用无机填料填充、用玻璃纤维增强的塑料有较低的成型收 缩率。
41
6、注塑件的精度
42
②模具
6、注塑件的精度
对于小尺寸的塑料件,模具的制造误差占塑料公差的1/3。 与模具上运动的零件有关的塑件尺寸,其精度较低。 模具上浇注系统和冷却系统设计不当,会使成型塑件的 收缩不均匀。 脱模系统的作用力不当,会使被顶出塑件变形。
30
5、抗变形设计 防止变形的措施
前述的避免应力集中以及刚性设计的一些措施,也都有 助于防止或者降低制件的变形。此外,设计时考虑防止产品 变形,在形状上进行规避。
31
5、抗变形设计
矩形的薄壁容器的侧壁容易发生内凹变 形,为此可将侧壁设计得稍微外凸一些
32
5、抗变形设计
深度较浅的盒类制品,为避免翘曲变形, 可将其底边设计成倒角形状
后果:塑料是对缺口和尖角之类比较敏感的材料,在应 力作用下,这些部位会逐渐产生微细裂纹,随后逐步扩展到 大的裂纹,而裂纹的不断延伸终将导致制件的损坏。
17
3、避免应力集中原则
避免应力集中应作为一条基本的准则
避免应力集中最直接最有效的方法就是在拐角、棱边、 凹槽灯等轮廓过渡与厚薄交接处采用圆弧过渡。
5、抗变形设计
汽车塑料件设计要求方案
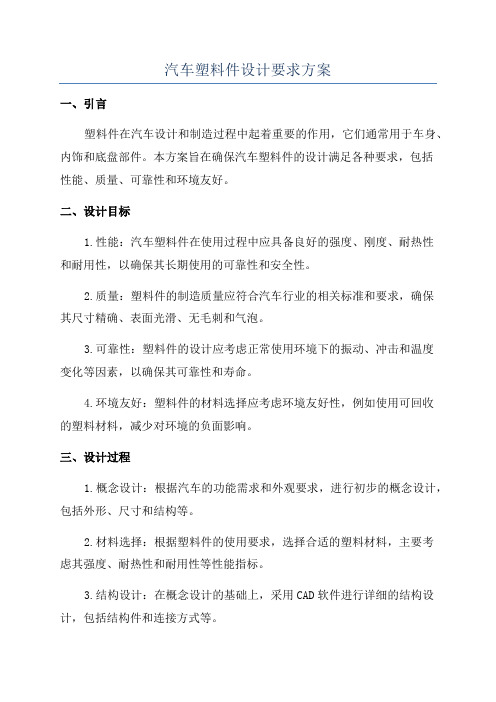
汽车塑料件设计要求方案一、引言塑料件在汽车设计和制造过程中起着重要的作用,它们通常用于车身、内饰和底盘部件。
本方案旨在确保汽车塑料件的设计满足各种要求,包括性能、质量、可靠性和环境友好。
二、设计目标1.性能:汽车塑料件在使用过程中应具备良好的强度、刚度、耐热性和耐用性,以确保其长期使用的可靠性和安全性。
2.质量:塑料件的制造质量应符合汽车行业的相关标准和要求,确保其尺寸精确、表面光滑、无毛刺和气泡。
3.可靠性:塑料件的设计应考虑正常使用环境下的振动、冲击和温度变化等因素,以确保其可靠性和寿命。
4.环境友好:塑料件的材料选择应考虑环境友好性,例如使用可回收的塑料材料,减少对环境的负面影响。
三、设计过程1.概念设计:根据汽车的功能需求和外观要求,进行初步的概念设计,包括外形、尺寸和结构等。
2.材料选择:根据塑料件的使用要求,选择合适的塑料材料,主要考虑其强度、耐热性和耐用性等性能指标。
3.结构设计:在概念设计的基础上,采用CAD软件进行详细的结构设计,包括结构件和连接方式等。
4.模具设计:根据结构设计的CAD模型,进行模具的设计和制造,确保塑料件的生产过程中能够精确复制设计要求。
5.实验验证:利用模具制备出样品进行实验验证,包括强度测试、耐热性测试和可靠性测试等,以确保设计要求的满足。
6.优化改进:根据实验结果,对设计进行优化改进,以提高塑料件的性能和可靠性。
四、质量控制1.原材料检验:对进货的塑料材料进行检验,包括外观、尺寸和性能测试等,确保原材料的质量符合设计要求。
2.生产过程控制:在塑料件生产过程中,采用严格的控制措施,确保良品率和尺寸精度的控制。
3.产品验收:对塑料件进行全面的验收,包括外观、尺寸和功能测试等,确保产品质量符合客户的要求。
4.售后服务:建立健全的售后跟踪服务体系,及时解决客户的问题和反馈,确保客户满意度。
五、环境友好1.材料选择:优先选择可回收的塑料材料,减少对环境的污染。
2.工艺改进:改进生产工艺,减少废料产生和能源消耗,提高生产效率。
塑料件成型模具设计

塑料件成型模具设计塑料件成型模具设计是塑料制品生产过程中不可缺少的环节。
因为模具的设计和制造直接关系到最终产品的形态、尺寸精度和产品的质量,影响着整个生产的质量和效益。
本文主要就塑料件成型模具设计进行详细的介绍和分析。
一、概述塑料件成型模具是在塑料注射成型过程中起着关键作用的工具,成型模具设计是塑料制品生产的最基本和最重要的环节之一,关系着塑料制品生产的质量和效益,是决定产品性能的重要因素之一。
所以,塑料件成型模具的设计和制造至关重要。
二、塑料件成型模具设计的流程1、确定产品设计图纸。
包括产品的形状、尺寸、重量等数据,并按照产品的使用要求制定出产品的性能指标。
2、进行模型设计。
包括产品的三维模型设计,根据产品的形状和尺寸,绘制出产品的三维模型。
3、确定模具结构。
根据产品的三维模型,确定模具的结构形式和零件加工方案,并进行结构设计和计算,以确定模具的各个组成部分的大小、材料、精度和工艺要求。
4、进行模具的毛胚铣削。
根据模具的结构和工艺要求,进行各个零件的粗加工和精密加工,为模具的组装提供必要的条件。
5、模具组装和调试。
根据设计和加工完成的模具零件,进行组装,并进行模具的调试和磨合,以达到规定的要求和精度。
6、模具试模。
将模具安装到注塑机上,进行试模生产,检验模具的结构、性能和加工精度是否符合要求,直至达到优化效果。
三、设计注意事项1、产品设计要合理。
一款塑料件成型模具的设计首先要考虑的是产品的形态和尺寸,唯有确定好产品的形态和尺寸才能更好地进行模具设计。
2、材料的选择要考虑塑料件的特性。
模具的材料主要是热处理后的合金钢,但是在选材时也需要考虑塑料件的特性,如塑料件的尺寸、形态、温度等,不同的塑料件需要选用不同的模具材料,才能更好地完成注塑成型工作。
3、模具加工精度要高。
由于塑料件成型模具涉及到高要求的计量精度问题,故要求加工设备必须是精密性高、稳定性好的设备,并配备高精度的测量设备来控制加工精度。
精密塑料件成型模具的设计要点

冷却 时问
5 卜于取 向
结 1 V 热 CCc。 晶 : 0 收 i 化 缩 ● :
。 ● ●
压缩性 弹性 恢复
注 : 相 差性 ; ● O一一帔 捕关性
因此 , 工艺 因素 与聚台 物 的性 能 、 构形 态和 塑料 制 结 品之间 的 内在联 系 会通过 塑料 制品 表现 出米 ,分 析清 楚 这 些 内在的 联系 , 刊合 理拟 定 注塑 N TT艺 、 _ _ 合理 设计 制 造模具、 合理 选择 注塑加 工设 备都 有重 要意 艾。 3 合理确 定横 具的 尺寸及 公差
式 、 口位置 与分 布有 关 . 浇 而且 与工程 塑料 的结 晶取 向胜
制品 还是 对注 塑设 备都 提 出了 “ 密成 型 ”的概 念 和理 精 论 东芝 机械 公司 , 日本 制钢所 等许 多一 流的企 业相继 制
订 精密 注塑 制品 的公 差等 级企业 标 准 .有 的公 差 仅 相 当于 S/ 0 2 —9 5标准 I J T168 19 级精 度的 1 ~ /。E本 著名 / 13 l 2
一
而不一 致 。 因此 . 效地控 制塑 料制 品的 收缩 率在精 密注 有 塑技 术中就 显得 十分重 要 模 具 设 计 的 合理 与否 会 直接 影 响 塑 料 制 品 的收 缩 率 .由于摸 具型 腔 尺寸 是 塑料制 t 尺寸 加 J所 葬的 5 7 1 二 收缩 率求 得 的 ,而收缩 率 是由 塑料 生产 厂家 或 工程塑 料 手册 推 荐 的 ・ 个范 围内 的数值 .’ 不仅 与摸 具 的浇 r形 l = ]
『 1先选定 丁程塑料 利 料 .而 能进 行 精密 注塑 的T程 塑 姐i " 料 叉必 须选 用那 些 力学性 能高 、尺 寸稳 定 、抗蠕 变性 能 好 、耐 环境 膻 力开裂 的材 剌 其次 墟根 据所 选 的塑料 材
塑料模具设计结构5大要素
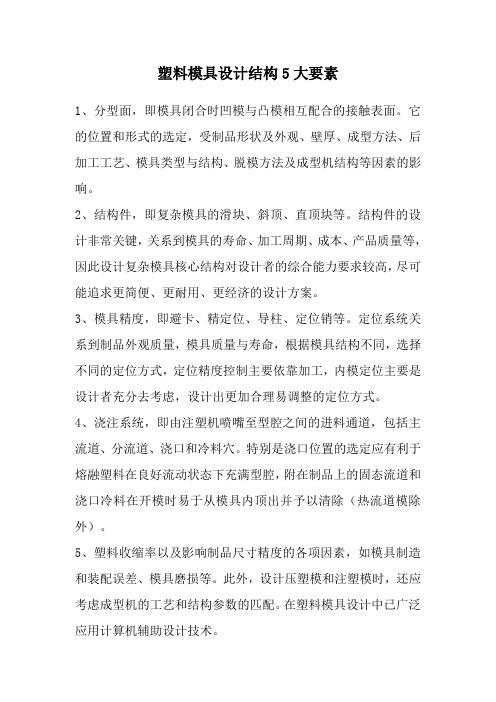
塑料模具设计结构5大要素
1、分型面,即模具闭合时凹模与凸模相互配合的接触表面。
它的位置和形式的选定,受制品形状及外观、壁厚、成型方法、后加工工艺、模具类型与结构、脱模方法及成型机结构等因素的影响。
2、结构件,即复杂模具的滑块、斜顶、直顶块等。
结构件的设计非常关键,关系到模具的寿命、加工周期、成本、产品质量等,因此设计复杂模具核心结构对设计者的综合能力要求较高,尽可能追求更简便、更耐用、更经济的设计方案。
3、模具精度,即避卡、精定位、导柱、定位销等。
定位系统关系到制品外观质量,模具质量与寿命,根据模具结构不同,选择不同的定位方式,定位精度控制主要依靠加工,内模定位主要是设计者充分去考虑,设计出更加合理易调整的定位方式。
4、浇注系统,即由注塑机喷嘴至型腔之间的进料通道,包括主流道、分流道、浇口和冷料穴。
特别是浇口位置的选定应有利于熔融塑料在良好流动状态下充满型腔,附在制品上的固态流道和浇口冷料在开模时易于从模具内顶出并予以清除(热流道模除外)。
5、塑料收缩率以及影响制品尺寸精度的各项因素,如模具制造和装配误差、模具磨损等。
此外,设计压塑模和注塑模时,还应考虑成型机的工艺和结构参数的匹配。
在塑料模具设计中已广泛应用计算机辅助设计技术。
模具设计标准汽车某汽车
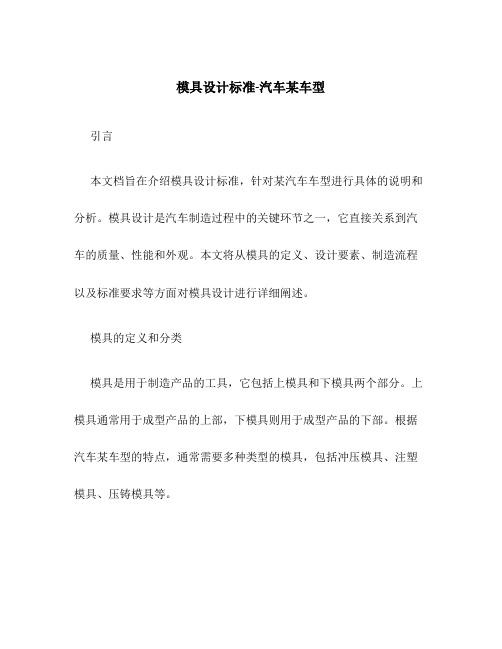
模具设计标准-汽车某车型引言本文档旨在介绍模具设计标准,针对某汽车车型进行具体的说明和分析。
模具设计是汽车制造过程中的关键环节之一,它直接关系到汽车的质量、性能和外观。
本文将从模具的定义、设计要素、制造流程以及标准要求等方面对模具设计进行详细阐述。
模具的定义和分类模具是用于制造产品的工具,它包括上模具和下模具两个部分。
上模具通常用于成型产品的上部,下模具则用于成型产品的下部。
根据汽车某车型的特点,通常需要多种类型的模具,包括冲压模具、注塑模具、压铸模具等。
冲压模具冲压模具是最常见的模具类型之一,用于汽车零部件的冷冲压成型。
它包括上下模板、导向装置、定位销、冲头、导柱等部件。
冲压模具的设计要素包括模具结构、材料选择、成形工艺等。
注塑模具注塑模具用于汽车塑料零部件的注塑成型。
它包括模仁、模板、模芯、顶针、喷嘴等部件。
注塑模具的设计要素包括模具材料、射出系统、冷却系统、顶出系统等。
压铸模具压铸模具用于汽车零部件的熔融金属压铸成型。
它包括模仁、模板、射杆、压铸腔等部件。
压铸模具的设计要素包括模具结构、冷却系统、压铸工艺参数等。
模具设计要素模具设计要素是模具设计的重要考虑因素,对于保证模具的质量和性能至关重要。
以下是一些模具设计要素的简要介绍。
精度要求模具的精度要求直接关系到成型产品的质量和尺寸精度。
根据汽车某车型的设计要求,模具的精度要求应满足相应的标准,如国家汽车工程研究中心制定的相关标准。
强度和刚性模具的强度和刚性对模具的使用寿命和稳定性有着重要影响。
模具的设计应考虑材料的选择、结构的合理性和加工工艺等因素,以确保模具具有足够的强度和刚性。
导向和定位模具的导向和定位是模具工作过程中的关键问题,它直接关系到产品的定位精度和尺寸一致性。
合理设计导向装置和定位销等部件,能够减小模具的运动误差,提高产品的一致性。
散热和冷却模具的散热和冷却系统对模具的寿命和成型效果有着重要影响。
合理设计冷却系统,能够有效降低模具的温度,提高模具的使用寿命和产品的表面质量。
玩具小车注塑模具设计

玩具小车注塑模具设计玩具小车注塑模具设计,是指设计适用于制造玩具小车的注塑模具。
注塑模具是一种用于生产塑料制品的工具,通过注塑机将熔化的塑料注入模具中,冷却固化后,最终得到所需的塑料制品。
以下是关于玩具小车注塑模具设计的一些详细内容。
首先,玩具小车注塑模具设计的第一步是确定设计需求。
根据客户提供的要求和需求,确定所需的模具规格、尺寸、材料等。
同时,还需要考虑到玩具小车的外观设计和功能特点,比如是否需要转向、是否有开合的部件等。
接下来,进行注塑模具的结构设计。
注塑模具通常包括模具座、模芯、模腔、冷却系统、顶出系统等部分。
模具座是模具的基础部分,用于支撑和安装模具。
模芯和模腔则是成型件的形状所依据的部分,冷却系统用于控制模具温度并加快冷却速度,顶出系统则用于将成型件从模具中排出。
在进行结构设计时,需要考虑到模具的可制造性和操作性。
模具的结构应该尽可能简单、稳定,以提高模具的寿命和生产效率。
同时,还需要保证模具的可维修性,方便进行模具维护和更换部件。
在设计模具结构时,还需要进行模具的流动分析。
通过流动分析,可以预测塑料在注塑过程中的流动情况、充填时间和充填压力,从而优化模具结构,提高注塑质量和生产效率。
另外,玩具小车注塑模具设计还需要考虑到材料的选择。
模具常用的材料包括钢材和铝合金。
钢材具有高强度和耐磨性,适用于生产大批量的塑料制品。
铝合金则具有良好的导热性和加工性能,适用于生产小批量的塑料制品。
最后,进行模具的制造和试模。
根据设计图纸,选择合适的加工设备和工艺,进行模具的制造。
制造完成后,进行试模,验证模具的性能和稳定性。
总结起来,玩具小车注塑模具设计是一个综合性的工程,需要对结构、流动分析、材料等进行全面考虑。
通过设计合理的注塑模具,可以高效地生产出符合要求的玩具小车。
精密塑胶件注塑模具顶出结构及加工成型工艺研发

精密塑胶件注塑模具顶出结构及加工成型工艺研发一、导言随着工业技术的发展,精密塑胶件在各个行业中得到了广泛的应用。
注塑模具是生产精密塑胶件的重要成型工具,包括模具结构设计、加工成型工艺研发等方面,都对精密塑胶件的质量和生产效率有着重要的影响。
本文将重点探讨精密塑胶件注塑模具顶出结构及加工成型工艺的研发。
二、模具顶出结构设计模具的顶出结构是指在注塑过程中,塑料熔料在充模过程中,通过顶出装置使塑料零件从模具中弹出的一种结构。
对于精密塑胶件的顶出结构设计,应综合考虑以下几个方面的因素:1.模具材料的选择。
模具材料的选择应根据精密塑胶件的材料性质和生产工艺要求进行选择,一般常用的模具材料有P20、45#、718等。
同时,模具材料的硬度和耐磨性也是影响顶出结构设计的重要因素。
2.顶出方式的选择。
常见的顶出方式有机械顶出、气动顶出和液压顶出等。
对于精密塑胶件而言,要考虑到产品的表面光洁度和尺寸精度等因素,通常采用气动顶出或液压顶出方式较为合适。
3.顶出装置的设计。
顶出装置通常包括顶出销和顶出板两部分。
其中,顶出销的材料应与模具材料相匹配,以保证顶出销的刚性和耐磨性,同时辅助顶出板的设计要合理,以保证塑料零件能够完整且顺利地脱模。
1.模具加工工艺研发。
模具加工工艺主要包括模具加工序列的确定、工艺参数的选择和加工精度控制等。
通过合理的模具加工工艺研发,可以提高模具的加工效率和加工精度。
2.塑料熔融流道设计。
塑料熔融流道设计的好坏直接影响着塑胶件的质量和生产效率。
对于精密塑胶件而言,流道应尽可能短而粗,以保证塑料熔料的快速流动和顺畅充模。
3.注塑工艺参数的优化。
注塑工艺参数的优化包括注射速度、保压时间、保压压力和注射温度等方面的考虑。
通过调整这些参数,可以获得更好的塑胶件成型品质和缩短生产周期。
4.模具温度控制。
模具温度对于塑胶件的收缩率和表面光洁度有着重要的影响。
通过合理的模具温度控制,可以避免塑胶件的变形和表面瑕疵。
汽车研发:塑料件的工艺设计要求及注意事项!

汽车研发:塑料件的工艺设计要求及注意事项!小姐姐的“美”是由颜值、身材和才华组成,而才华又占了很大的比例!就像汽车由不同的零件组成,每个零件根据自身性能及功能的需求,又由不同的材料组成,其中塑料就是汽车上十分重要的材料,塑料件占了很大的比例!今天漫谈君就带你一起来看看塑料件的工艺设计要求及注意事项漫谈君说一、漫谈君为大家准备了如下干货:1、56集CATIA基础教程,在公众号后台回复“56”,即可领取!2、全套汽车标准,在公众号后台回复“标准”,即可领取!3、特斯拉专利,在公众号后台回复“特斯拉专利”,即可领取!4、《Model X及Model 3中文用户手册》,在公众号后台回复“中文用户手册”,即可领取!二、汽车大漫谈汽车研发技术群加群:汽车大漫谈7群已满员,专注探索汽车研发技术,有需要进群的工程师童鞋,请加漫谈君微信:autotechstudy01,备注名称+专业哟,方便邀请进群!一前言本文主要介绍的是塑料件的分模线、拔模方向、拔模角度的选择以及塑料件B面结构设计时加强筋的布置、滑块斜顶行程的校核等,本文介绍的只适合注塑成型的塑料件,可能对其他成型工艺不具备参考意义。
二拔模方向拔模方向是塑料件从模具中被顶出的方向。
可以简单地把它理解为一个杯形蛋糕远离杯形蛋糕盘的方向。
这个盘的顶部平面的方向就是拔模方向。
拔模方向也可以比作“最小阻力方向”。
1内孔脱模内孔脱模以尺寸小的一端为准,以保证与内孔配合零件的尺寸及配合间隙,脱模方向为尺寸扩大的方向取得,同时也保证分型线不外露,如下图所示:2外形尺寸外形尺寸以大端为准,脱模斜度向尺寸缩小的方向取得,保证零件与周围的配合间隙,同时要保证零件的工艺美观要求,如下图所示:三拔模角度要求由于塑料冷却时出现收缩,会使塑件紧包在成型芯上。
为了便于脱模,与脱模方向平行的塑件表面,都应设计合理的拔模角度。
塑料件设计中的拔模角度要求如下:1皮纹外表面及零件翻边和配合边•无皮纹的外表面及零件的翻边和配合边,-般要3°以上的拔模角度,如果实现困难,最小1.5°但翻边宽度要窄;•细皮纹一般要3°拔模角。
汽车塑料件设计要求
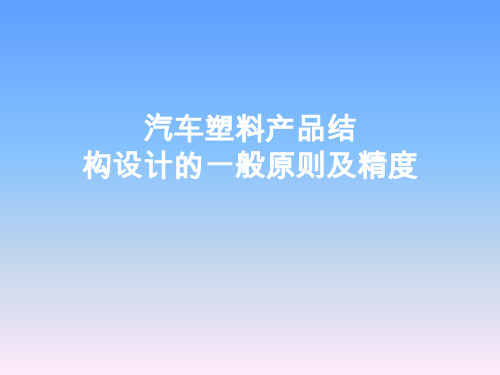
矩形的薄壁容器的侧壁容易发生内凹变 形,为此可将侧壁设计得稍微外凸一些
深度较浅的盒类制品,为避免翘曲变形, 可将其底边设计成倒角形状
因壁厚不同,壁厚处的塑料完全固化后, 会对先行固化的薄壁部位施以拉力,导 致制件出现变形
(a)采用均匀壁厚的办法;
(b)采用增加筋的高度的 办法。
采用加强筋来防止框形结构变形
避免受热部位过热导致变 形的几种设计方案
① 使产品中的零部件与热源保持有一段距离。
② 在塑料部件与发热体之间,设置像铝箔之类反射性 能好的反射体,可以减少热量的吸收。
③ 可采用对流的设计。在适当部位设计格栅或开设不同 形状的散热窗口,也有利于热量的散发。
④ 在用于温度过高的部位时,应采用热导率低的隔热材 料进行隔热。
(3) 尺寸设计要考虑成型的可能性,不同的 成型工艺对制件的尺寸设计,包括尺寸大 小,尺寸变化会有一定的限制。
二、壁厚均一的设计原则
• 在确定壁厚尺寸时,壁厚均一是一个重要原则。 该原则主要是从工艺角度以及由工艺导致的质量 方面的问题而提出来的。均匀的壁厚可使制件在 成型过程中,熔体流动性均衡,冷却均衡。壁薄 部位在冷却收缩上的差异,会产生一定的收缩应 力,内应力会导致制件在短期之内或经过一个较 长时期之后发生翘曲变形。
①有利于成型 加工;
②节约原材料, 降低成本;
③简洁、美观;
简化设计的一些建议和提示
(1) 结构简单,形状对称,避免不规则的几 何图形;
结 构 简 单 容 易 成 型
对 称 设 计
(2) 产品侧孔和侧壁内表面的凹凸形状成型 困难,需要在产品成型后进行二次加工, 设计时应避免。
设 计 改 进 避 免 侧 向 抽 芯
① 不受模具活动部分影响的尺寸a,如图所示,它 是指在同一动模或定模的零件中成型的尺寸。
- 1、下载文档前请自行甄别文档内容的完整性,平台不提供额外的编辑、内容补充、找答案等附加服务。
- 2、"仅部分预览"的文档,不可在线预览部分如存在完整性等问题,可反馈申请退款(可完整预览的文档不适用该条件!)。
- 3、如文档侵犯您的权益,请联系客服反馈,我们会尽快为您处理(人工客服工作时间:9:00-18:30)。
轿车精密塑料件成型模具的设计要点
轿车精密塑料件成型模具的设计要点
为了保证轿车精密塑料件的性能、质量与可靠性,注射成型出质量较高、符合产品设计要求的塑料制品,必须对塑料材料、注塑设
备与模具及注塑工艺不断进行改进。
一.影响精密注塑的主要因素
判定精密注塑的依据是注塑制品的精度,即制品的尺寸公差、形位公差和表面粗糙度。
要进行精密注塑,必须有许多相关的条件,而最本质的是塑料材料、注塑模具、注塑工艺和注塑设备这四项基本因素。
设计塑料制品时,应首先选定工程塑料材料,而能进行精密注塑的工程塑料又必须选用那些力学性能高、尺寸稳定、抗蠕变性能好、耐环境应力开裂的材料。
其次应根据所选择的塑料材料、成品尺寸
精度、件重、质量要求以及预想的模具结构选用适用的注塑机。
在
加工过程中,影响精密注塑制品的因素主要来自模具的精度、注塑
收缩,以及制品的环境温度和湿度变化幅度等方面。
在精密注塑中,模具是用以取得符合质量要求的精密塑料制品的关键之一,精密注塑用的模具应切实符合制品尺寸、精度及形状的
要求。
但即使模具的精度、尺寸一致,其模塑的塑料制品之实际尺
寸也会因收缩量差异而不一致。
因此,有效地控制塑料制品的收缩
率在精密注塑技术中就显得十分重要。
影响塑料收缩率的主要有热收缩、相变收缩、取向收缩、压缩收缩与弹性回复等因素,而这些影响因素与精密注塑制品的成型条件
或操作条件有关。
因此,在设计模具时必须考虑这些影响因素与注
塑条件的关系及其表观因素,如注塑压力与模腔压力及充模速度、
注射熔体温度与模具温度、模具结构及浇口形式与分布,以及浇口
截面积、制品壁厚、塑料材料中增强填料的含量、塑料材料的结晶
度与取向性等因素的影响。
上述因素的影响也因塑料材料不同,其它成型条件如温度、湿度、继续结晶化、成型后的内应力、注塑机的变化而不同。
由于注塑过程是把塑料从固态粉料或粒料向液态熔体、又向固态制品转变的过程。
从粒料到熔体,再由熔体到制品,中间要经过温
度场、应力场、流场以及密度场等的作用,在这些场的共同作用下,不同的塑料热固性或热塑性、结晶性或非结晶性、增强型或非增强
型等具有不同的聚合物结构形态和流变性能。
凡是影响到上述场的
因素,必将会影响到塑料制品的'物理力学性能、尺寸、形状、精度
与外观质量。
这样,工艺因素与聚合物的性能、结构形态和塑料制品之间的内在联系会通过塑料制品表现出来。
分析清楚这些内在的联系,对合
理地拟定注塑加工工艺、合理地设计并按图纸制造模具、乃至合理
选择注塑加工设备都有重要意义。
精密注塑与普通注塑在注塑压力和注射速率上也有区别。
精密注塑常采用高压或超高压注射、高速注射以获得较小的成型收缩率。
综合上述各种原因,设计精密注塑模具时,除考虑一般模具的设计要素外,还须考虑以下几点:①采用适当的模具尺寸公差;②防止
产生成型收缩率误差;③防止发生注塑变形;④防止发生脱模变形;⑤
使模具制造误差降至最小;⑥防止模具精度的误差;⑦保持模具精度。
二.防止产生成型收缩率误差
由于收缩率会因注塑压力而发生变化,因此,对于单型腔模具,型腔内的模腔压力应尽量一致;至于多型腔模具,型腔之间的模腔压
力应相差很小。
在单型腔多浇口或多型腔多浇口的情况下,必须以相同的注塑压力注射,使型腔压力一致。
为此,必须确保使浇口位置均衡。
为了
使型腔内的模腔压力一致,最好使浇口入口处的压力保持一致。
浇
口处压力的均衡与流道中的流动阻力有关。
所以,在浇口压力达到均衡之前,应先使流道均衡。
由于熔体温度和模具温度对实际收缩率产生影响,因此,在设计精密注塑模具型腔时,为了便于确定成型条件,必须注意型腔的排列。