泵与风机节能的论文关于节能减排的论文
电厂风机和给水泵运行方式与节能论文
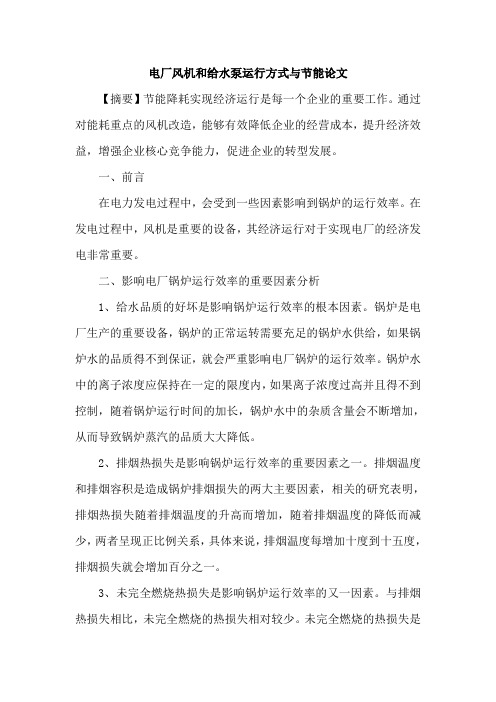
电厂风机和给水泵运行方式与节能论文【摘要】节能降耗实现经济运行是每一个企业的重要工作。
通过对能耗重点的风机改造,能够有效降低企业的经营成本,提升经济效益,增强企业核心竞争能力,促进企业的转型发展。
一、前言在电力发电过程中,会受到一些因素影响到锅炉的运行效率。
在发电过程中,风机是重要的设备,其经济运行对于实现电厂的经济发电非常重要。
二、影响电厂锅炉运行效率的重要因素分析1、给水品质的好坏是影响锅炉运行效率的根本因素。
锅炉是电厂生产的重要设备,锅炉的正常运转需要充足的锅炉水供给,如果锅炉水的品质得不到保证,就会严重影响电厂锅炉的运行效率。
锅炉水中的离子浓度应保持在一定的限度内,如果离子浓度过高并且得不到控制,随着锅炉运行时间的加长,锅炉水中的杂质含量会不断增加,从而导致锅炉蒸汽的品质大大降低。
2、排烟热损失是影响锅炉运行效率的重要因素之一。
排烟温度和排烟容积是造成锅炉排烟损失的两大主要因素,相关的研究表明,排烟热损失随着排烟温度的升高而增加,随着排烟温度的降低而减少,两者呈现正比例关系,具体来说,排烟温度每增加十度到十五度,排烟损失就会增加百分之一。
3、未完全燃烧热损失是影响锅炉运行效率的又一因素。
与排烟热损失相比,未完全燃烧的热损失相对较少。
未完全燃烧的热损失是指一部分固体燃料颗粒没来得及在炉膛内充分燃烧殆尽就跟随灰渣排出从而造成的燃烧热损失。
固体未完全燃烧热损失的影响因素有很多,包括燃料的性质、燃烧方式、锅炉炉膛的结构设计以及过量空气系数等。
三、锅炉风机运行状况1、锅炉风机性能特点目前我们只能用实验才能精确算出锅炉风机的性能曲线,理论方面的方法还不是很成熟。
我们需要进行实验,并且对实验结果得出的数据进行深入分析,然后制作出性能曲线图。
仔细推敲风机性能曲线图我们不难发现,在转速稳定的情况下,风量的改变会造成风机效率的变化,但是其中会有一个高效率的区间,所以我们应该采取一些必要的措施对其中的某些因素进行改造,保证风机在高效区进行高效率的工作,使风机的运行达到最佳工况。
浅谈风机水泵调速节能
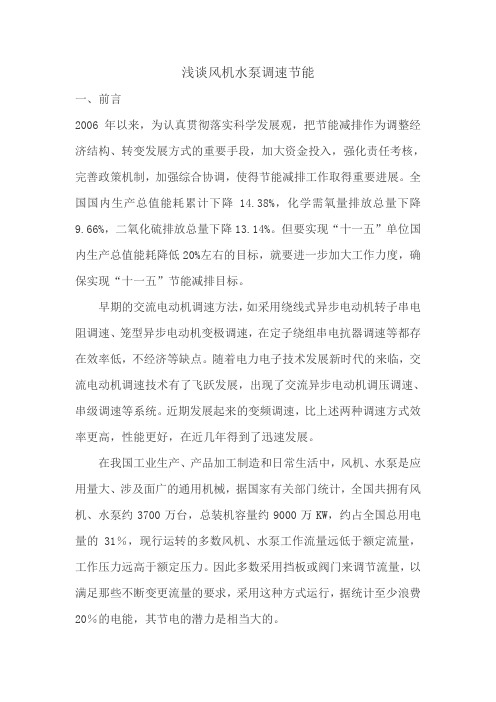
浅谈风机水泵调速节能一、前言2006年以来,为认真贯彻落实科学发展观,把节能减排作为调整经济结构、转变发展方式的重要手段,加大资金投入,强化责任考核,完善政策机制,加强综合协调,使得节能减排工作取得重要进展。
全国国内生产总值能耗累计下降14.38%,化学需氧量排放总量下降9.66%,二氧化硫排放总量下降13.14%。
但要实现“十一五”单位国内生产总值能耗降低20%左右的目标,就要进一步加大工作力度,确保实现“十一五”节能减排目标。
早期的交流电动机调速方法,如采用绕线式异步电动机转子串电阻调速、笼型异步电动机变极调速,在定子绕组串电抗器调速等都存在效率低,不经济等缺点。
随着电力电子技术发展新时代的来临,交流电动机调速技术有了飞跃发展,出现了交流异步电动机调压调速、串级调速等系统。
近期发展起来的变频调速,比上述两种调速方式效率更高,性能更好,在近几年得到了迅速发展。
在我国工业生产、产品加工制造和日常生活中,风机、水泵是应用量大、涉及面广的通用机械,据国家有关部门统计,全国共拥有风机、水泵约3700万台,总装机容量约9000万KW,约占全国总用电量的31%,现行运转的多数风机、水泵工作流量远低于额定流量,工作压力远高于额定压力。
因此多数采用挡板或阀门来调节流量,以满足那些不断变更流量的要求,采用这种方式运行,据统计至少浪费20%的电能,其节电的潜力是相当大的。
据调查,一般风机水泵平均运行在70%的额定负荷下,由流体力学知道,风机、水泵的流量与转速成正比、压力与转速的平方成正比,而轴功率与转速的立方成正比,当流量减少或下降时,其轴功率按速度的三次方下降,例如流量减少到70%,速度下降到70%,则轴功率下降到额定功率的34.3%,如流量减少到50%,轴功率则减少到额定功率的12.5%。
当然还应该考虑转速下降引起机械等效率下降及附加调速装置的损耗,但这些损耗都是不大的,因此风机、水泵用调逮控制代替节能控制是节电的有效途径。
风机和泵类产品的节能减排

当地居民生存的一大挑战。
开发SQ Flex可再生能源供水系统。
格兰富绿色能源供水系统(SQFlex以利于安装和使用。
源达到的几乎零运行费用,以及南非的Mafeteng和Durban地区,格兰富的SQ改善。
在定名为SQ 获得A级能效标识的Alpha2热水循环泵格兰富公司的热水循环泵的产量一直为世界第其平均能源【摘 要】为风机和泵类设备的节能减排提供了依据。
【关键词】风机 泵 节能 方法 应用潜力风机与泵是应用广泛的流体机械,全国约有3 2002年国家经贸委节能信息传播中心对鞍钢第三图5 SQFlex可再生能源供水系统使管网阻力曲线由R 1变为R 2,交(H —Q )n 1曲线于B 点,流量和扬程分别为Q 2和H 2,泵的效率变为ηB 。
如采用调速调节转速由n 1降为 n 2,此时泵的性能曲线变为(H —Q )n 2,C 点为新的运行工况点,流量和扬程分别为Q 2、H 3,此时泵的效率曲线为ηn2,而泵的额定效率不变,即ηC =ηA ,不是ηB 。
锅炉给水泵调速节能原理如图3。
图3 锅炉给水泵调速节能原理图从图3可得出相对节能量,由于水泵功率P =C ·H ·Q 则为获得流量Q 2,节流调节耗功P 2=C ·H 2·Q 2≈□B H 2O Q 2。
调速调节耗功P 3=C ·H 3·Q 2≈□B H 3O Q 2。
A 则调速对节流调节节能P J = P 2-P 3≈□B H 2O Q 2-□B H 3O Q 2=(H 2-H 3)Q 2=ΔH ·Q 2即节省功率与扬程之差成正比。
按图3定出各点参数关系,即可计算出调速调节对节流调节的节能量。
假定额定工况点A 的流量Q 1与扬程H 1均为100%,Q 2=0.5 Q 1,H 2= 1.2H 1,ηC =ηA ,ηB =0.8ηA ,由于Q ∝n ,H ∝n 2,故n 2=0.5 n 1,H 3= 0.25H 1。
泵与风机的节能技术探讨
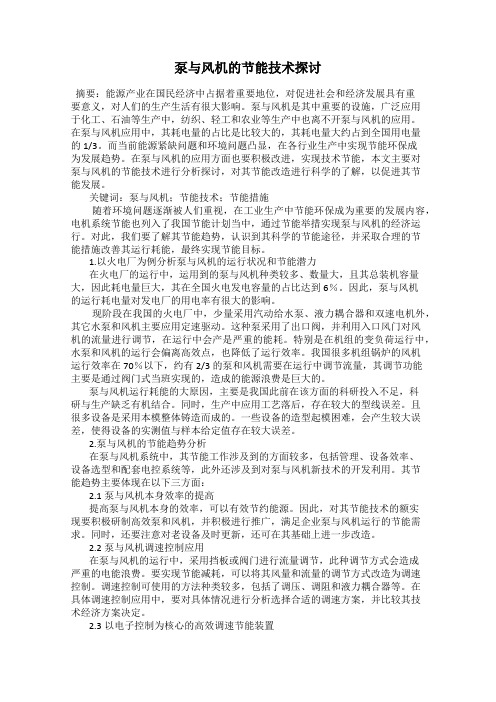
泵与风机的节能技术探讨摘要:能源产业在国民经济中占据着重要地位,对促进社会和经济发展具有重要意义,对人们的生产生活有很大影响。
泵与风机是其中重要的设施,广泛应用于化工、石油等生产中,纺织、轻工和农业等生产中也离不开泵与风机的应用。
在泵与风机应用中,其耗电量的占比是比较大的,其耗电量大约占到全国用电量的1/3。
而当前能源紧缺问题和环境问题凸显,在各行业生产中实现节能环保成为发展趋势。
在泵与风机的应用方面也要积极改进,实现技术节能,本文主要对泵与风机的节能技术进行分析探讨,对其节能改造进行科学的了解,以促进其节能发展。
关键词:泵与风机;节能技术;节能措施随着环境问题逐渐被人们重视,在工业生产中节能环保成为重要的发展内容,电机系统节能也列入了我国节能计划当中,通过节能举措实现泵与风机的经济运行。
对此,我们要了解其节能趋势,认识到其科学的节能途径,并采取合理的节能措施改善其运行耗能,最终实现节能目标。
1.以火电厂为例分析泵与风机的运行状况和节能潜力在火电厂的运行中,运用到的泵与风机种类较多、数量大,且其总装机容量大,因此耗电量巨大,其在全国火电发电容量的占比达到6%。
因此,泵与风机的运行耗电量对发电厂的用电率有很大的影响。
现阶段在我国的火电厂中,少量采用汽动给水泵、液力耦合器和双速电机外,其它水泵和风机主要应用定速驱动。
这种泵采用了出口阀,并利用入口风门对风机的流量进行调节,在运行中会产是严重的能耗。
特别是在机组的变负荷运行中,水泵和风机的运行会偏离高效点,也降低了运行效率。
我国很多机组锅炉的风机运行效率在70%以下,约有2/3的泵和风机需要在运行中调节流量,其调节功能主要是通过阀门式当班实现的,造成的能源浪费是巨大的。
泵与风机运行耗能的大原因,主要是我国此前在该方面的科研投入不足,科研与生产缺乏有机结合。
同时,生产中应用工艺落后,存在较大的型线误差。
且很多设备是采用本模整体铸造而成的。
一些设备的造型起模困难,会产生较大误差,使得设备的实测值与样本给定值存在较大误差。
泵与风机的节能技术探讨
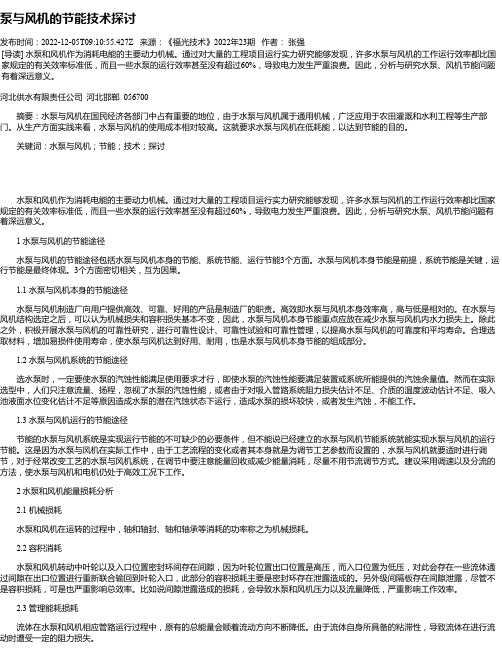
泵与风机的节能技术探讨发布时间:2022-12-05T09:10:55.427Z 来源:《福光技术》2022年23期作者:张强[导读] 水泵和风机作为消耗电能的主要动力机械。
通过对大量的工程项目运行实力研究能够发现,许多水泵与风机的工作运行效率都比国家规定的有关效率标准低,而且一些水泵的运行效率甚至没有超过60%,导致电力发生严重浪费。
因此,分析与研究水泵、风机节能问题有着深远意义。
河北供水有限责任公司河北邯郸 056700摘要:水泵与风机在国民经济各部门中占有重要的地位,由于水泵与风机属于通用机械,广泛应用于农田灌溉和水利工程等生产部门。
从生产方面实践来看,水泵与风机的使用成本相对较高。
这就要求水泵与风机在低耗能,以达到节能的目的。
关键词:水泵与风机;节能;技术;探讨水泵和风机作为消耗电能的主要动力机械。
通过对大量的工程项目运行实力研究能够发现,许多水泵与风机的工作运行效率都比国家规定的有关效率标准低,而且一些水泵的运行效率甚至没有超过60%,导致电力发生严重浪费。
因此,分析与研究水泵、风机节能问题有着深远意义。
1 水泵与风机的节能途径水泵与风机的节能途径包括水泵与风机本身的节能、系统节能、运行节能3个方面。
水泵与风机本身节能是前提,系统节能是关键,运行节能是最终体现。
3个方面密切相关,互为因果。
1.1 水泵与风机本身的节能途径水泵与风机制造厂向用户提供高效、可靠、好用的产品是制造厂的职责。
高效即水泵与风机本身效率高,高与低是相对的。
在水泵与风机结构选定之后,可以认为机械损失和容积损失基本不变,因此,水泵与风机本身节能重点应放在减少水泵与风机内水力损失上。
除此之外,积极开展水泵与风机的可靠性研究,进行可靠性设计、可靠性试验和可靠性管理,以提高水泵与风机的可靠度和平均寿命。
合理选取材料,增加易损件使用寿命,使水泵与风机达到好用、耐用,也是水泵与风机本身节能的组成部分。
1.2 水泵与风机系统的节能途径选水泵时,一定要使水泵的汽蚀性能满足使用要求才行,即使水泵的汽蚀性能要满足装置或系统所能提供的汽蚀余量值。
浅谈水泵设计及使用中的节能降耗

浅谈水泵设计及使用中的节能降耗摘要:针对阶梯式泵站的情况,改进水泵的设计以减少能量消耗已变得刻不容缓。
为了满足节约资源的需求,根据具体状况进行全面的评估,同时找出切实可行的解决方案和途径。
本文详细研究了水泵运作过程中的能源消耗原因,在此基础上提出了一系列关于水泵设计和应用的节约能源和减少消耗的方法。
这些措施对于提升水泵设计质量,实现节能降耗目标具有重要意义,有助于推动水泵行业朝着更加高效、环保的方向发展。
通过采用这些节能降耗措施,可以降低水泵的能源消耗,提高能源利用效率,为梯级泵站的可持续发展作出贡献。
关键词:水泵设计;节能降耗;设计优化1引言我国目前正大力倡导构建节约型社会,并在日常的工作与生活中,广泛重视节约能源。
水泵作为一种广泛应用于各个领域的设备,在我国的使用量巨大。
因此,探索水泵设计与应用过程中的节约能源的科学方法,具有十分重要的意义。
深入研究并应用相关技术,优化水泵结构设计,提高制造水平,结合高效节能控制系统的应用,可以在保证水泵性能的同时,最大化节约能源。
这不仅有助于降低水泵的能耗,提高能源利用效率,还能为推进节约型社会建设作出积极贡献。
总的来说,深化对水泵节约能源和消耗的科学研究和运用,在推动中国节约资源、实现可持续发展方面起着极其关键的作用。
应该继续加大研发力度,推广先进技术,为构建节约型社会、保护生态环境贡献更多力量。
2水泵运行能耗诱因在供水系统里,水泵扮演着至关重要的角色,同时也是确保水资源被有效使用的核心。
泵站系统的能耗主要可以划分为直接和间接两类,同时也包括必要和非必要的能耗,需要根据实际情况进行合理的分析。
首先,水泵系统的复杂性,以及串联和并联运行配置的科学性不足,都导致了能源消耗的提高[1]。
其次,管道和水泵之间的匹配性存在不足,这导致高能耗、低效率以及大流量的问题更加突出。
此外,在管道建设和操作过程中,局部阻力问题显著,从而引发了能源消耗的问题。
由于系统的回路阻力出现了不平衡,这使得水泵的能源消耗和各个设备的能源消耗都有所上升。
变频调速技术在风机、泵类应用中的节能分析_职教论文

摘要:在工业生产和产品加工制造业中,风机、泵类设备应用范围广泛;其电能消耗是一笔不小的生产费用开支。
随着经济改革的不断深入,市场竞争的不断加剧;节能降耗业已成为降低生产成本、提高产品质量的重要手段之一。
关键字:变频调速节能风机泵一、引言 在工业生产和产品加工制造业中,风机、泵类设备应用范围广泛;其电能消耗和诸如阀门、挡板相关设备的节流损失以及维护、维修费用占到生产成本的7%~25%,是一笔不小的生产费用开支。
随着经济改革的不断深入,市场竞争的不断加剧;节能降耗业已成为降低生产成本、提高产品质量的重要手段之一。
而八十年代初发展起来的变频调速技术,正是顺应了工业生产自动化发展的要求,开创了一个全新的智能电机时代。
一改普通电动机只能以定速方式运行的陈旧模式,使得电动机及其拖动负载在无须任何改动的情况下即可以按照生产工艺要求调整转速输出,从而降低电机功耗达到系统高效运行的目的。
八十年代末,该技术引入我国并得到推广。
现已在电力、冶金、石油、化工、造纸、食品、纺织等多种行业的电机传动设备中得到实际应用。
目前,变频调速技术已经成为现代电力传动技术的一个主要发展方向。
卓越的调速性能、显著的节电效果,改善现有设备的运行工况,提高系统的安全可靠性和设备利用率,延长设备使用寿命等优点随着应用领域的不断扩大而得到充分的体现。
二、综述 通常在工业生产、产品加工制造业中风机设备主要用于锅炉燃烧系统、烘干系统、冷却系统、通风系统等场合,根据生产需要对炉膛压力、风速、风量、温度等指标进行控制和调节以适应工艺要求和运行工况。
而最常用的控制手段则是调节风门、挡板开度的大小来调整受控对象。
这样,不论生产的需求大小,风机都要全速运转,而运行工况的变化则使得能量以风门、挡板的节流损失消耗掉了。
在生产过程中,不仅控制精度受到限制,而且还造成大量的能源浪费和设备损耗。
从而导致生产成本增加,设备使用寿命缩短,设备维护、维修费用高居不下。
泵类设备在生产领域同样有着广阔的应用空间,提水泵站、水池储罐给排系统、工业水(油)循环系统、热交换系统均使用离心泵、轴流泵、齿轮泵、柱塞泵等设备。
泵与风机论文

泵与风机的性能分析及其节能技术摘要:泵与风机是常用的耗能设备。
它们数量多,分布广,耗电量巨大。
本文论述泵与风机的性能分析及其节能技术,对缓和目前电力供需之间不平衡的突出矛盾推进现代化建设有着及其重要的现实意义。
关键词:泵风机节能泵与风机是消耗电能的动力机械,由于选型的不当、管道设计不合理、维护检修不合良、使用管理落后、设备陈旧等因素,造成泵与风机的使用效率降低。
通过一些工程实例可以看出,大部分泵与风机的效率低于国家规定的标准,泵的运行效率大部分低于60%。
风机的效率普遍低于70%,造成了电力的严重浪费。
所以,为了做好泵与风机的工作,我们必须通过分析泵与风机的性能来解决节能减排问题,不断地完善节能减排技术。
1、泵和风机的性能泵和风机的主要性能参数包括流量Q、压头H(泵为杨程,风机为全风压)、功率N、效率η、转速n,这些参数反应了泵或风机的整体性能。
泵和风机的性能非常相似。
①泵的闸阀节流分析离心泵闸阀的特性曲线如图1 所示,Q-H 图给出了泵的转轴功率与流量之间的关系。
其计算公式为:N = ρHQ|120η⑴式中N 为功率/KW;ρ为液体密度/Kg·m-3;Q 为流量/L·s-1;H 为杨程/m;η为效率。
图1中Qa、Qb、Qc 分别为阀门开度由大到小的3个管道特性曲线,A、B、C 分别为3 个工况点。
当调节阀门开度由大到小时,表现为管道阻力由小到大,管道特性曲线变陡,因此泵的工况点自A 移到C,流量减少的同时,转轴的功率相应减少,但其幅度不大,ΔN = ρQΔH| 120η。
②调速节流分析离心泵调速节流特性曲线如图2 所示,图2 中的Q—Hn1、Q—Hn2、Q—Hn3,分别对应于不同转速时的流量杨程特性曲线,其中转速n1>n2>n3。
Q—N1、Q —N2、Q—N3 分别为相应的流量—轴功率特性曲线,Qa、Qb 分别为阀门开度不同的2 条管道特性曲线,A、B、C、D、E、F 分别为各工况点,由流体力学理论可知他们存在如下关系:Q1/Q2=n1/n2 (2)H1/H2=(n1/n2)2 (3)N1/N2=(n1/n2)3 (4)由上述公式⑵—⑷可知,当转速调节由大到小时,流量、杨程、轴功率分别按1、2、3 次方关系下降。
电厂泵与风机的节能
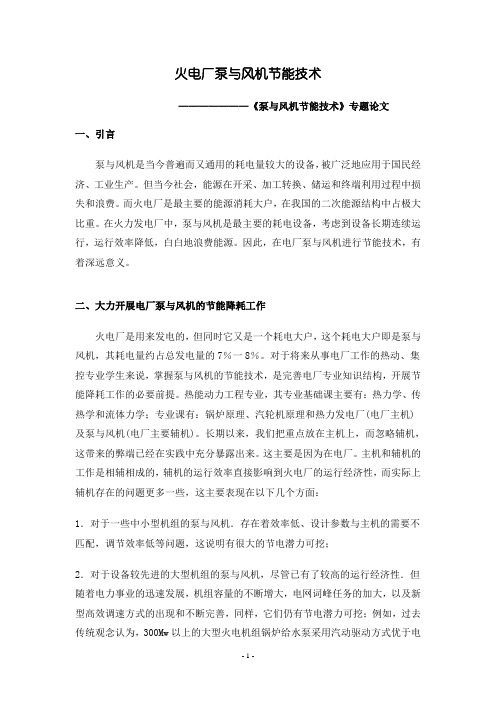
火电厂泵与风机节能技术———————《泵与风机节能技术》专题论文一、引言泵与风机是当今普遍而又通用的耗电量较大的设备,被广泛地应用于国民经济、工业生产。
但当今社会,能源在开采、加工转换、储运和终端利用过程中损失和浪费。
而火电厂是最主要的能源消耗大户,在我国的二次能源结构中占极大比重。
在火力发电厂中,泵与风机是最主要的耗电设备,考虑到设备长期连续运行,运行效率降低,白白地浪费能源。
因此,在电厂泵与风机进行节能技术,有着深远意义。
二、大力开展电厂泵与风机的节能降耗工作火电厂是用来发电的,但同时它又是一个耗电大户,这个耗电大户即是泵与风机,其耗电量约占总发电量的7%一8%。
对于将来从事电厂工作的热动、集控专业学生来说,掌握泵与风机的节能技术,是完善电厂专业知识结构,开展节能降耗工作的必要前提。
热能动力工程专业,其专业基础课主要有:热力学、传热学和流体力学;专业课有:锅炉原理、汽轮机原理和热力发电厂(电厂主机)及泵与风机(电厂主要辅机)。
长期以来,我们把重点放在主机上,而忽略辅机,这带来的弊端已经在实践中充分暴露出来。
这主要是因为在电厂。
主机和辅机的工作是相辅相成的,辅机的运行效率直接影响到火电厂的运行经济性,而实际上辅机存在的问题更多一些,这主要表现在以下几个方面:1.对于一些中小型机组的泵与风机.存在着效率低、设计参数与主机的需要不匹配,调节效率低等问题,这说明有很大的节电潜力可挖;2.对于设备较先进的大型机组的泵与风机,尽管已有了较高的运行经济性.但随着电力事业的迅速发展,机组容量的不断增大,电网词峰任务的加大,以及新型高效调速方式的出现和不断完善,同样,它们仍有节电潜力可挖;例如,过去传统观念认为,300Mw以上的大型火电机组锅炉给水泵采用汽动驱动方式优于电动变速方式。
且有较高的运行经济性,但是,随着电力电子技术的发展,各种容量和型号的变频电源、整流装置研制成功以及大容量晶闸管价格的降低,使许多大型火电机组锅炉给水泵采用交流变速驱动成为可能,象液力耦合器、油膜转差离合器和无换向器电机调速系统等交流变速驱动方式,实践证明.由于电动变速方式可以简化热力系统,投资少,可靠性高,易维护等,从而使机组的运行经济性提高,其中,无换向器电机凋速系统是最有发展前途的一种驱动方案,目前,国外已有使用,但国内仍是空白;3.在实际运行中,电厂中的许多事故都是由于辅机运行不当造成的,所以电厂中辅机这部分知识必须逐渐完善,以满足实际需要,为节能降耗工作的进行提供必要条件。
《泵与风机》论文

《泵与风机》课程论文论文名称浅析泵与风机的运行方式与节能措施姓名 _____________________学号 _____________________院系 _____________________专业年级 __________________指导教师 __________________职称 _____________________2014年6 月7 日浅析泵与风机的运行方式与节能措施[内容摘要]电厂的泵与风机有不同的运行方式,但不同的运行方式,其能耗或节能效果大不相同。
本文就主要以电厂泵与风机的不同运行方式,利用泵与风机自身固有特点以及通过其他措施来共同实现节能的方法进行论述。
[关键词]运行方式调速驱动节流节能措施一.概论随着现代电厂机组的大型化,锅炉运行的安全性愈来愈重要。
锅炉能否安全运行,不但关系自身的安全,而且对外界用户也非常重要。
尤其是企业的自备热电站,它的热用户有时是庞大而复杂的系统(如石油化工企业),电站锅炉能否安全、灵活运行,对其热用户的安全性和经济效益至关重要。
其次,在缺乏水电调峰的地区,一些电厂又担任着电网调峰的任务,这就需要锅炉能够滑压运行,具有足够灵活的负荷适应性。
而热电站又必须不断调节锅炉负荷,以适应用户对蒸汽需求的变化。
锅炉负荷的变化就必须调节辅机的运行。
为了锅炉能安全长期运行,灵活适应外界要求,除锅炉本身质量外,鼓、引风机和给水泵的运行方式也有着非常重要的作用;另一方面,鼓、引风机和给水泵的运行方式不同,对电厂的基建投资、运行维修费用、自身能耗与电厂经济性有着很大的影响。
在电厂中,自身能耗占其运行成本的相当比例,而鼓、引风机和给水泵的功率在电厂自身能耗中所占比例很大。
因此,选择合理的运行方式,使其适应锅炉负荷变化的需要,尽可能减少因节流而引起的能量损失,降低生产成本,对电厂来说至关重要。
二.鼓、引风机和给水泵的运行方式(一).锅炉给水泵的运行方式锅炉给水系统概括地分为单元制和母管制。
关于风机泵类电动机节能技术探讨
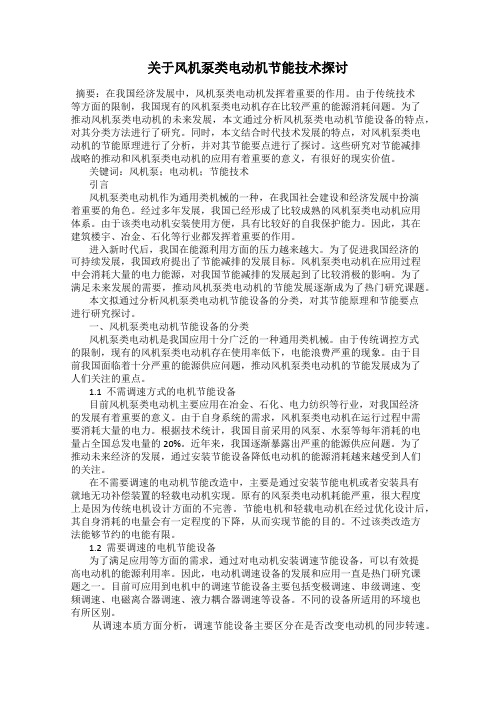
关于风机泵类电动机节能技术探讨摘要:在我国经济发展中,风机泵类电动机发挥着重要的作用。
由于传统技术等方面的限制,我国现有的风机泵类电动机存在比较严重的能源消耗问题。
为了推动风机泵类电动机的未来发展,本文通过分析风机泵类电动机节能设备的特点,对其分类方法进行了研究。
同时,本文结合时代技术发展的特点,对风机泵类电动机的节能原理进行了分析,并对其节能要点进行了探讨。
这些研究对节能减排战略的推动和风机泵类电动机的应用有着重要的意义,有很好的现实价值。
关键词:风机泵;电动机;节能技术引言风机泵类电动机作为通用类机械的一种,在我国社会建设和经济发展中扮演着重要的角色。
经过多年发展,我国已经形成了比较成熟的风机泵类电动机应用体系。
由于该类电动机安装使用方便,具有比较好的自我保护能力。
因此,其在建筑楼宇、冶金、石化等行业都发挥着重要的作用。
进入新时代后,我国在能源利用方面的压力越来越大。
为了促进我国经济的可持续发展,我国政府提出了节能减排的发展目标。
风机泵类电动机在应用过程中会消耗大量的电力能源,对我国节能减排的发展起到了比较消极的影响。
为了满足未来发展的需要,推动风机泵类电动机的节能发展逐渐成为了热门研究课题。
本文拟通过分析风机泵类电动机节能设备的分类,对其节能原理和节能要点进行研究探讨。
一、风机泵类电动机节能设备的分类风机泵类电动机是我国应用十分广泛的一种通用类机械。
由于传统调控方式的限制,现有的风机泵类电动机存在使用率低下,电能浪费严重的现象。
由于目前我国面临着十分严重的能源供应问题,推动风机泵类电动机的节能发展成为了人们关注的重点。
1.1 不需调速方式的电机节能设备目前风机泵类电动机主要应用在冶金、石化、电力纺织等行业,对我国经济的发展有着重要的意义。
由于自身系统的需求,风机泵类电动机在运行过程中需要消耗大量的电力。
根据技术统计,我国目前采用的风泵、水泵等每年消耗的电量占全国总发电量的20%。
近年来,我国逐渐暴露出严重的能源供应问题。
泵与风机的论文

泵与风机论文热泵应用的战略意义摘要据统计,我国建筑用能已超过占全国能源消耗总量的1/4,并将随着人民生活水平的提高而进一步增长。
我国建筑物的能耗中有60%左右消耗于采暖、空调与生活用水系统,占有建筑能耗的主要部分,这部分能耗具有三个特点关键词:热泵战略意义一、可再生能源技术建筑应用的战略意义1、低品位能源。
热能根据其温度的高低可分为低品位能源和高品位能源,越接近环境温度的热能品位越低,而高出环境温度幅度越高则热能品位越高。
建筑采暖所需的温度通常低于100℃,空调所需的温度通常高于5℃,均为低品位能源。
2、狭窄的温度范围。
建筑空调冷冻水的温度一般为5~12℃,供热热水温度在45~60℃左右,地板供暖温度在40℃以下。
由此可见,建筑能源的温度范围相当狭窄。
3、与自然能源温度接近。
地球环境内的各种介质均含有低品位的热(冷)能,这些介质包括土壤、地下水、河流湖泊及海水、污水和空气。
以北京为例:土壤和地下水温度全年约14℃左右;污水厂冬季排出的处理后污水温度仍在16℃左右;空气温度一般为-15~40℃。
显然这个温度范围与空调供暖所需的温度相当接近。
我国著名能源科学家吴仲华教授早在上世纪80年代初期就已提出"温度对口,梯级利用"的科学用能基本原则。
根据建筑能耗的特点,建筑能源使用应遵循"温度对口,梯级利用,因地制宜,多能互补"的原则。
对于建筑用能,所谓"温度对口"就是指建筑空调供暖用能所需的温度,是与自然能源即低品位的可再生能源的温度相当接近、彼此对口的。
对于高品位的能源,如天然气、石油、煤炭等化石燃料燃烧后所产生的高温,则远远高出建筑空调供暖用能所需求的温度,直接应用是不对口的,直接应用就会造成能源品位退化,不仅能效低,而且燃烧会产生环境的污染。
在这种情况下,驱动供暖。
因此,大规模使用低品位可再生能源为建筑提供供暖空调用能,是具有十分重要战略意义的举措。
浅谈水泵控制系统中的 “节能减排”措施
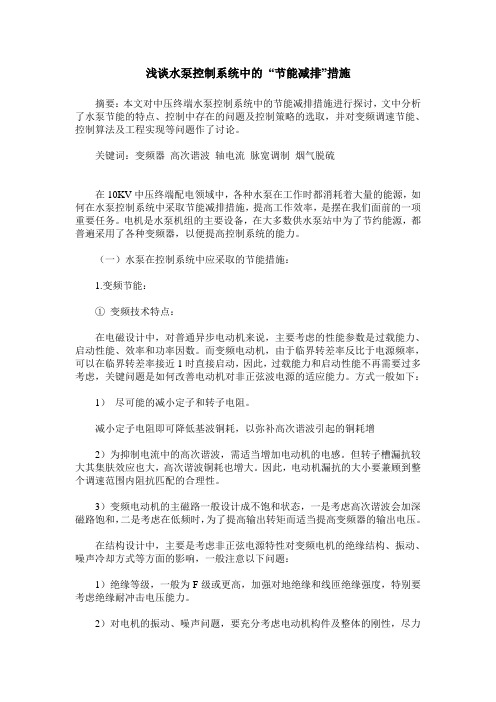
浅谈水泵控制系统中的“节能减排”措施摘要:本文对中压终端水泵控制系统中的节能减排措施进行探讨,文中分析了水泵节能的特点、控制中存在的问题及控制策略的选取,并对变频调速节能、控制算法及工程实现等问题作了讨论。
关键词:变频器高次谐波轴电流脉宽调制烟气脱硫在10KV中压终端配电领域中,各种水泵在工作时都消耗着大量的能源,如何在水泵控制系统中采取节能减排措施,提高工作效率,是摆在我们面前的一项重要任务。
电机是水泵机组的主要设备,在大多数供水泵站中为了节约能源,都普遍采用了各种变频器,以便提高控制系统的能力。
(一)水泵在控制系统中应采取的节能措施:1.变频节能:①变频技术特点:在电磁设计中,对普通异步电动机来说,主要考虑的性能参数是过载能力、启动性能、效率和功率因数。
而变频电动机,由于临界转差率反比于电源频率,可以在临界转差率接近1时直接启动,因此,过载能力和启动性能不再需要过多考虑,关键问题是如何改善电动机对非正弦波电源的适应能力。
方式一般如下:1)尽可能的减小定子和转子电阻。
减小定子电阻即可降低基波铜耗,以弥补高次谐波引起的铜耗增2)为抑制电流中的高次谐波,需适当增加电动机的电感。
但转子槽漏抗较大其集肤效应也大,高次谐波铜耗也增大。
因此,电动机漏抗的大小要兼顾到整个调速范围内阻抗匹配的合理性。
3)变频电动机的主磁路一般设计成不饱和状态,一是考虑高次谐波会加深磁路饱和,二是考虑在低频时,为了提高输出转矩而适当提高变频器的输出电压。
在结构设计中,主要是考虑非正弦电源特性对变频电机的绝缘结构、振动、噪声冷却方式等方面的影响,一般注意以下问题:1)绝缘等级,一般为F级或更高,加强对地绝缘和线匝绝缘强度,特别要考虑绝缘耐冲击电压能力。
2)对电机的振动、噪声问题,要充分考虑电动机构件及整体的刚性,尽力提高其固有频率,以避开与各次力波产生共振现象。
3)冷却方式:一般采用强迫通风冷却,即主电机散热风扇采用独立的电机驱动。
风机、水泵变频调速节能分析

For personal use only in study and research;not for commercial use风机、水泵变频调速节能分析能源是国家重要的物质基础,能源的供需矛盾已成为制约我国社会主义经济建设的主要因素之一。
在能源问题上国务院提出“节约与开发并重”的方针,就是依靠技术进步,把节约能源以解决能源问题作为我国重要的技术经济政策。
据不完全统计,全国风机、水泵、压缩机就有1500万台电动机,用电量占全国总发电量的40~50%,这些电动机大多在低的电能利用率下运行,只要将这些电动机电能利用率提高10~15%,全年可节电300亿kW以上。
根据火电设计规程SDJ-79规定,燃煤锅炉的送、引风机的风量裕度分别为5%和5%~10%,风压裕度分别为10%和10%~15%。
设计过程中很难计算管网的阻力、并考虑到长期运行过程中发生的各种问题,通常总是把系统的最大风量和风压裕度作为选型的依据,但风机的型号和系列是有限的,往往选取不到合适的风机型号时就往上靠,裕度大于20~30%比较常见。
因此这些风机运行时,只有靠调节风门或风道挡板的开度来满足生产工艺对风量的要求。
风机和水泵的机械特性均为平方转矩特性,水泵运行时,靠阀门的开度调节流量来满足供水要求,工况与风机相似,靠调节风门、风道档板或阀门的开度来调节风机风量,水泵流量的方法、称为节流调节,在节流调节过程中,风机或水泵固有特性不变、仅仅靠关小风门、挡板或阀门的开度,人为地增加管路的阻力,由此增大管路系统的损失,不利于风机,水泵的节能运行。
采用调速控制装置,通过改变风机水泵转速,从而改变风机风量,水泵流量以适应生产工艺的需要,这种调节方式称为风机水泵的调速控制。
风机、水泵以调速控制方式运行能耗最省,综合效益最高。
交流电机的调速方式有多种、变频调速是高效的最佳调速方案,它可以实现,风机水泵的无级调速,并可方便地组成闭环控制系统、实现恒压或恒流量控制。
电厂泵与风机的节能技术探讨
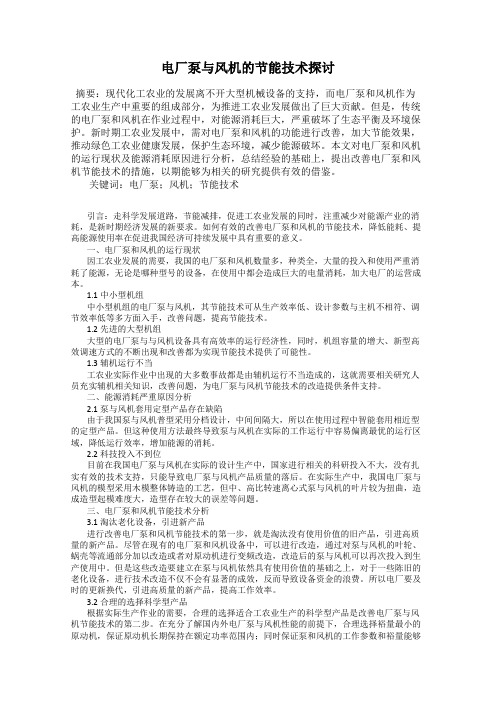
电厂泵与风机的节能技术探讨摘要:现代化工农业的发展离不开大型机械设备的支持,而电厂泵和风机作为工农业生产中重要的组成部分,为推进工农业发展做出了巨大贡献。
但是,传统的电厂泵和风机在作业过程中,对能源消耗巨大,严重破坏了生态平衡及环境保护。
新时期工农业发展中,需对电厂泵和风机的功能进行改善,加大节能效果,推动绿色工农业健康发展,保护生态环境,减少能源破坏。
本文对电厂泵和风机的运行现状及能源消耗原因进行分析,总结经验的基础上,提出改善电厂泵和风机节能技术的措施,以期能够为相关的研究提供有效的借鉴。
关键词:电厂泵;风机;节能技术引言:走科学发展道路,节能减排,促进工农业发展的同时,注重减少对能源产业的消耗,是新时期经济发展的新要求。
如何有效的改善电厂泵和风机的节能技术,降低能耗、提高能源使用率在促进我国经济可持续发展中具有重要的意义。
一、电厂泵和风机的运行现状因工农业发展的需要,我国的电厂泵和风机数量多,种类全,大量的投入和使用严重消耗了能源,无论是哪种型号的设备,在使用中都会造成巨大的电量消耗,加大电厂的运营成本。
1.1中小型机组中小型机组的电厂泵与风机,其节能技术可从生产效率低、设计参数与主机不相符、调节效率低等多方面入手,改善问题,提高节能技术。
1.2先进的大型机组大型的电厂泵与与风机设备具有高效率的运行经济性,同时,机组容量的增大、新型高效调速方式的不断出现和改善都为实现节能技术提供了可能性。
1.3辅机运行不当工农业实际作业中出现的大多数事故都是由辅机运行不当造成的,这就需要相关研究人员充实辅机相关知识,改善问题,为电厂泵与风机节能技术的改造提供条件支持。
二、能源消耗严重原因分析2.1泵与风机套用定型产品存在缺陷由于我国泵与风机普型采用分档设计,中间间隔大,所以在使用过程中智能套用相近型的定型产品。
但这种使用方法最终导致泵与风机在实际的工作运行中容易偏离最优的运行区域,降低运行效率,增加能源的消耗。
泵与风机的节能问题讨论

泵与风机的节能问题讨论摘要:为了实现泵与风机的节能,我们应保持系统在最佳工况中运行。
降低功率消耗,因此我们要改变泵与风机参数,使得泵与风机的性能曲线交至工作点附近。
本文围绕泵的选型,改变泵运行范围的最佳经济方法,多种泵与风机调节运行工况的特征等关系泵与风机节能问题的关键部分展开讨论。
关键词:泵与风机;节能问题一、泵与风机节能的意义及节能潜力分析能源作为经济建设和人民生活不可缺少的重要资源,对国民经济持续、快速、健康发展有重要意义,同时在国家经济建设中占据重要地位。
节能降耗是我国经济发展的一项长期战略方针。
据国际能源署调查发现,在1995一2010年间,全世界每年平均新装机容量仅为1亿kW,而每年新增加发电量约为5000亿kW·h。
而我国仅占世界的50%左右。
近年来中国的电力建设速度非常快,已经趋近增长的极限。
但在我国的相当一部份地区仍然缺电,所以我们必须加强节约用电的意识、加强电力需求侧管理来解决中国目前的缺电问题。
水泵、风机作为国民经济生产中量大面广的电动机驱动设备,总电机容量极大,因此,关注泵与风机的节能问题在当前社会显得十分重要。
二、减小泵与风机内部损耗,提高其效率。
将原动机的机械能转换成流体的机械能的过程时,泵与风机会产生各种各样的能量损耗,这些损失按其性质可分为三部分,其分别为机械损失、容积损失和流动损失。
但至今为止上述三种损失仍不能用理论方法计算出精确的结果,其主要原因是泵与风机内部流体运动的复杂性。
因此泵与风机的损失主要是依靠试验方法测定的,测定之后再由此总结出半经验半理论的计算公式。
因此要提高泵与风机自身的效率,就要减少上述机械损失、容积损失和流动损失损失。
(1) 泵与风机的机械效率主要是由其叶轮的几何形状,即比转速值决定的,所以在提高其的机械效率时我们应注意以下几点:①选择或设计转速较高但叶轮直径较小的这类泵(风机)时,我们应避免转速低而大的这类。
②选择或设计高扬程、低比转速泵(风机)时,可适当增大叶轮叶片的出口安装角,或选用多级的应,尽量避免采用大的来达到高扬程(全压)的目的。
泵与风机节能技术论文
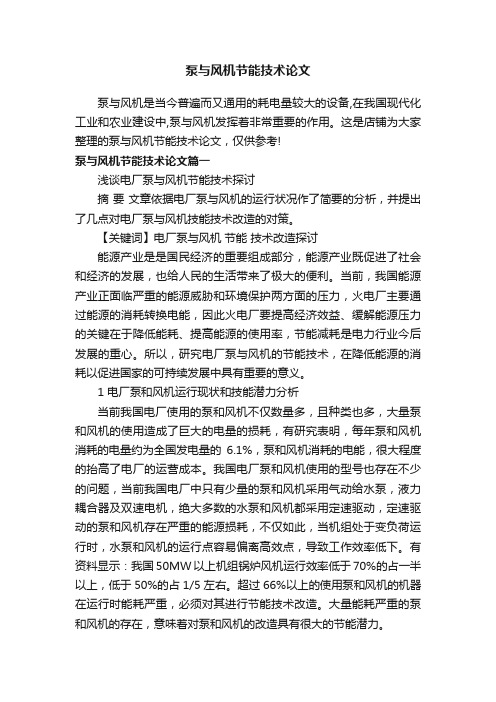
泵与风机节能技术论文泵与风机是当今普遍而又通用的耗电量较大的设备,在我国现代化工业和农业建设中,泵与风机发挥着非常重要的作用。
这是店铺为大家整理的泵与风机节能技术论文,仅供参考!泵与风机节能技术论文篇一浅谈电厂泵与风机节能技术探讨摘要文章依据电厂泵与风机的运行状况作了简要的分析,并提出了几点对电厂泵与风机技能技术改造的对策。
【关键词】电厂泵与风机节能技术改造探讨能源产业是是国民经济的重要组成部分,能源产业既促进了社会和经济的发展,也给人民的生活带来了极大的便利。
当前,我国能源产业正面临严重的能源威胁和环境保护两方面的压力,火电厂主要通过能源的消耗转换电能,因此火电厂要提高经济效益、缓解能源压力的关键在于降低能耗、提高能源的使用率,节能减耗是电力行业今后发展的重心。
所以,研究电厂泵与风机的节能技术,在降低能源的消耗以促进国家的可持续发展中具有重要的意义。
1 电厂泵和风机运行现状和技能潜力分析当前我国电厂使用的泵和风机不仅数量多,且种类也多,大量泵和风机的使用造成了巨大的电量的损耗,有研究表明,每年泵和风机消耗的电量约为全国发电量的6.1%,泵和风机消耗的电能,很大程度的抬高了电厂的运营成本。
我国电厂泵和风机使用的型号也存在不少的问题,当前我国电厂中只有少量的泵和风机采用气动给水泵,液力耦合器及双速电机,绝大多数的水泵和风机都采用定速驱动,定速驱动的泵和风机存在严重的能源损耗,不仅如此,当机组处于变负荷运行时,水泵和风机的运行点容易偏离高效点,导致工作效率低下。
有资料显示:我国50MW以上机组锅炉风机运行效率低于70%的占一半以上,低于50%的占1/5左右。
超过66%以上的使用泵和风机的机器在运行时能耗严重,必须对其进行节能技术改造。
大量能耗严重的泵和风机的存在,意味着对泵和风机的改造具有很大的节能潜力。
2 能耗严重原因分析首先,科技投入。
国家在相关技术的科研投入不足,有些科研结果未能及时的运用到企业的生产中;电厂生产工艺落后,导致线性误差大,过流表面粗糙。
变频器在风机、水泵中的节能应用
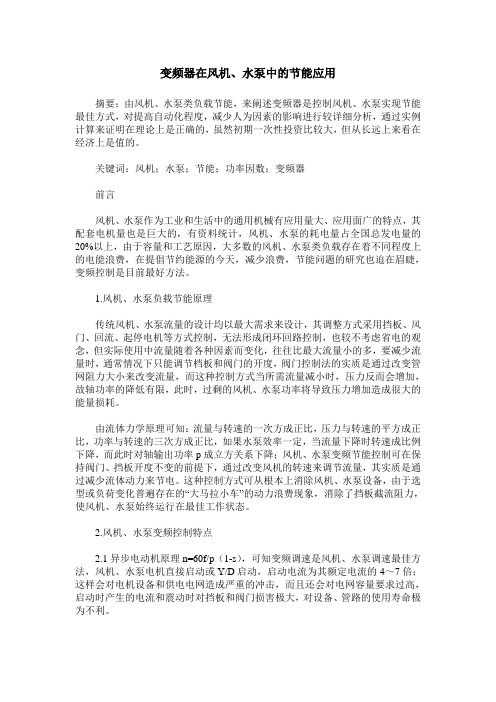
变频器在风机、水泵中的节能应用摘要:由风机、水泵类负载节能,来阐述变频器是控制风机、水泵实现节能最佳方式,对提高自动化程度,减少人为因素的影响进行较详细分析,通过实例计算来证明在理论上是正确的,虽然初期一次性投资比较大,但从长远上来看在经济上是值的。
关键词:风机;水泵;节能;功率因数;变频器前言风机、水泵作为工业和生活中的通用机械有应用量大、应用面广的特点,其配套电机量也是巨大的,有资料统计,风机、水泵的耗电量占全国总发电量的20%以上,由于容量和工艺原因,大多数的风机、水泵类负载存在着不同程度上的电能浪费,在提倡节约能源的今天,减少浪费,节能问题的研究也迫在眉睫,变频控制是目前最好方法。
1.风机、水泵负载节能原理传统风机、水泵流量的设计均以最大需求来设计,其调整方式采用挡板、风门、回流、起停电机等方式控制,无法形成闭环回路控制,也较不考虑省电的观念,但实际使用中流量随着各种因素而变化,往往比最大流量小的多,要减少流量时,通常情况下只能调节档板和阀门的开度,阀门控制法的实质是通过改变管网阻力大小来改变流量,而这种控制方式当所需流量减小时,压力反而会增加,故轴功率的降低有限,此时,过剩的风机、水泵功率将导致压力增加造成很大的能量损耗。
由流体力学原理可知:流量与转速的一次方成正比,压力与转速的平方成正比,功率与转速的三次方成正比,如果水泵效率一定,当流量下降时转速成比例下降,而此时对轴输出功率p成立方关系下降;风机、水泵变频节能控制可在保持阀门、挡板开度不变的前提下,通过改变风机的转速来调节流量,其实质是通过减少流体动力来节电。
这种控制方式可从根本上消除风机、水泵设备,由于选型或负荷变化普遍存在的“大马拉小车”的动力浪费现象,消除了挡板截流阻力,使风机、水泵始终运行在最佳工作状态。
2.风机、水泵变频控制特点2.1异步电动机原理n=60f/p(1-s),可知变频调速是风机、水泵调速最佳方法,风机、水泵电机直接启动或Y/D启动,启动电流为其额定电流的4~7倍;这样会对电机设备和供电电网造成严重的冲击,而且还会对电网容量要求过高,启动时产生的电流和震动时对挡板和阀门损害极大,对设备、管路的使用寿命极为不利。
水泵节能方案范文

水泵节能方案随着科技的不断发展,水泵领域也不断更新换代,新型节能水泵已经逐渐取代了传统的水泵,成为了当前市场上的主流产品。
在传统的泵站中,水泵运转时大量消耗电能,大大浪费了能源,容易造成环境污染与节能问题。
因此,提高水泵的能效已经成为了水泵行业重要的议题。
一、水泵节能意义水泵使用过程中,能耗较高,所以节能意义重大。
实施水泵节能方案的好处包括:1.降低能耗,提高效率:当泵站选用节能型水泵和其他节能措施后,相同功率下水泵的效率较原来有了很大提升,泵站能耗会相应降低30%~50%。
2.延长设备寿命:水泵选择效率更高的节能型水泵,由于其设计使用的材料和工艺更好,因而出现故障的概率较小,寿命也相应地更长。
3.降低运营成本:水泵节能后,比如可选用变频节能方式,相同的输出流量只要以70%~80%输出,就可以达到与原始情况相同的状态。
二、水泵节能方案为了降低能耗,提高水泵效率,可以采用以下的节能方案:1. 变频控制变频水泵控制系统是一种利用变频技术来实现水泵的节能的控制系统,其中变频器通过对水泵供电电压的调节,来改变水泵电机的转速,从而达到节能的目的。
变频器可以通过微调的方式,使得水泵的水流量在满足需要的情况下,能够更高效地利用能源。
2. 测流仪通过在管道上安装流量计,可以准确了解水的流速、压力、水位等特性参数,掌握水泵所处工况,并根据所得到的数据制定出相应的方案,调整水泵的流量,从而减少设备的能耗,提高设备的运转效率。
3. 多级泵多级泵是把多个单级泵同时安装在同一个泵腔内,从而实现高压水流的设备。
采用多级泵可以减小泵站内吸入压力的范围,从而进一步提高水泵效率。
同时,多级泵的设备寿命较长,故障率也相应较小,在节能的同时也可以减少设备的维护成本。
4. 优化管道设计泵站的水泵设备是用来提供管网所需要的压力和流量的设备,当管道系统设计存在一些问题导致管道内部存在压力损失时,不但引发了能源的浪费,同时也影响了水泵的运转效率。
- 1、下载文档前请自行甄别文档内容的完整性,平台不提供额外的编辑、内容补充、找答案等附加服务。
- 2、"仅部分预览"的文档,不可在线预览部分如存在完整性等问题,可反馈申请退款(可完整预览的文档不适用该条件!)。
- 3、如文档侵犯您的权益,请联系客服反馈,我们会尽快为您处理(人工客服工作时间:9:00-18:30)。
泵与风机节能的论文关于节能减排的论文
节能减排技术改造项目财务评价案例简析[摘要] 随着国家节能减排政策的推行,企业纷纷响应号召,制定了一系列以节水、节能、资源综合利用和环境保护为重点的技术改造措施。
此类项目的可行性研究报告工作重点是要论证节能减排的技术上和经济上的可行性,而经济上论证项目的可行性又成为项目可行的一个关键。
论文介绍了作者对一个节能减排项目实际案例的分析。
[关键词] 节能减排财务评价
国务院印发了国家发改委等部门制定的《节能减排综合性工作方案》指出,到2010年,中国万元国内生产总值能耗将由2005年的1.22吨标准煤下降到1吨标准煤以下,降低20%左右;单位工业增加值用水量降低30%。
“十一五”期间,中国主要污染物排放总量减少10%,2010年,二氧化硫排放量由2005年的2549万吨减少到2295万吨,化学需氧量(COD)由1414万吨减少到1273万吨;全国设市城市污水处理率不低于70%,工业固体废物综合利用率达到60%以上。
《中华人民共和国国民经济和社会发展第十一个五年规划纲要》提出了“十一五”期间单位国内生产总值能耗降低20%左右,
主要污染物排放总量减少10%的约束性指标。
这是贯彻落实科学发展观,构建社会主义和谐社会的重大举措;是建设资源节约型、环境友好型社会的必然选择;是推进经济结构调整,转变增长方式的必由之路;是提高人民生活质量,维护中华民族长远利益的必然要求。
随着国家节能减排政策的推行,企业纷纷响应国家号召,对原有耗能较大的工艺及设备进行更新和改造。
技术经济分析是评价节能减排项目是否可行的重要依据之一。
以一个节能减排经济评价案例,简要分析财务评价中的要点及难点。
某油脂公司进行节能减排改造,主要建设内容如下:
a.余热利用
原工艺系统系将温度为40℃的混合油直接送入蒸发器进行加热蒸发,而饼粕烘干机烘干饼粕时产生的二次蒸汽则作为废汽直接排空;现系统充分利用饼粕烘干机产生的二次蒸汽,对浸出后的混合油通过预蒸器先进行预加热,使进入蒸发器的混合油温度由原先的40℃提高到70~80℃,从而达到减少蒸发工序蒸汽耗量的目的。
b.工艺设备及供热、冷凝水回水管线改造
原有工艺设备结构不合理,造成蒸汽凝结水回水不畅,工艺物料升温必需在较高汽压保证,并且蒸汽和凝结水共同排出的情况下才能达到要求,而排出的蒸汽直接排空,造成热量损失较大。
本次技改拟对工艺设备的供热及蒸汽凝结水回水系统进行
改造,使供给工艺所用的蒸汽做功完全,蒸汽凝结水顺畅的回到锅炉供热系统,达到节约蒸汽的目的。
c.供热系统改造
采用“均匀混合分层燃烧技术”对原有一台6t/h和一台
4t/h燃煤蒸汽锅炉进行改造,以达到煤种适应性增大、减轻人(机)工作强度(负荷)、燃烧充分,降低环境污染、出汽量提高,汽压稳定的目的,改造后可提高锅炉效率5—10%,炉渣含碳量小于10%;节煤10—15%;节电5—10%。
采用专用过滤设备对除尘水进行过滤后,对渣、水分别进行回收利用。
过滤后的水回用于除尘系统,使除尘污水排放量降为零,滤渣由皮带输送机送出堆放。
对现有蒸汽管网和生产用热设备进行保温改造,减少热量损失。
d.冷却循环水系统改造
浸出车间采用冷却塔降低水温,使冷却水循环使用,达到减少新水用量的目的。
本项目所采用的技术均为国内成熟先进的工艺技术及装备。
利用二次蒸汽的余热在同行业中已有应用,所采用的预蒸器也属成熟设备。
锅炉系统改造采用的“均匀混合分层燃烧技术”是目前正转炉锅炉节能降耗有效、实用和成熟的技术措施,它含锅炉混煤器和分层给煤器两项技术。
该项目实施的意义远大:
1)该项目是某油脂公司“十一五”期间节能减排规划实施的项目,该项节能减排规划,是一个集节汽、节电、节水、污染治理、清洁生产为一体的综合性的资源节约和环境保护项目,同时也是企业整体技术升级改造、降低生产成本、增强企业竞争力势在必行的项目。
2)项目建设符合国情、区情,符合国家以及地方的有关行业政策,顺应了当地加快农业产业结构调整的形势和步伐,以及发展经济建设的迫切要求,抓住了发展机遇。
以市场为导向,以资源为基础,发展粮油产业,对推动地方农业产业结构的调整及产业化发展具有重要意义。
3)该项目建设有利于新疆油料优势资源的充分利用和规模化加工,生产的植物油产品符合质量安全要求。
项目建设条件较完备,
原料资源丰富,工艺技术方案成熟、可靠、先进,无论在国家食用油质量安全和食用油供给保障安全方面,还是在带动农村经济发展和提高农民收入方面,以及提升企业市场竞争实力等方面,都有着显著的社会效益和经济效益。
项目总体节能、降耗及减排情况:
1)蒸汽消耗
原有一台6t/h和一台4t/h燃煤蒸汽锅炉在满负荷生产时期全部运行还显供汽能力不足,生产最高用汽负荷可达到10.6t/h,本次技改项目实施后,由于蒸汽管网、用热设备改造、余热利用,全厂生产工艺最大蒸汽消耗量降至6.6t/h,每年将实现节约燃煤3532.6t,可节约标准煤3096t。
2)水消耗
冷却水循环利用后,新水最大消耗量为9.4m3/h,而原新水最大消耗量为26.3m3/h,节约16.9m3/h,累计每年可节约新水101400t。
3)减排煤渣
每吨燃煤产生煤渣量约在20—30%,按取值25%计算,每年可减少排出锅炉燃烧产生的炉渣量为:
3532.6×25%=883.15t。
4)减排SO2量
根据煤质分析报告,煤含全硫0.15%,SO2量约在0.3%,锅炉效率按80%计算,则每年减排SO2量为:
GSO2=1.6×3532.6×0.3%(1-80%)=3.4t/a。
项目新增总投资150万元,全部为建设投资。
改造前后,项目的生产规模不发生改变,因此采用新建项目法直接对改造前后的增量成本和效益进行分析。
项目总体工艺改造实施完成后,每年将实现节约燃煤3532.6吨,按照企业所在地现行燃料价格,煤按370元/吨计算,每年节约外购燃料动力费用=3532.6*370=1307062元。
项目完成后不需新增人员,工资及福利费不增加。
固定资产折旧采用平均年限法,其中建(构)筑物折旧年限按25年计算,机械设备及安装工程折旧年限按10年计算,净残值率按5%计算,年新计提折旧金额12万元。
修理费按折旧费的30%估算,共新增4万元。
经计算,项目正常年可降低企业生产总成本费用为111万元,降低经营成本124万元。
经过财务测算,项目内部收益率87.77%(税前);64.92%(税后),财务净现值:500万元(税前);361万元(税后),投资回收期:2.1年(税前);2.5年(税后),基准收益率确定为10%,该项目各项经济指标均好于基准指标,在财务上是可行的。
(计算如下表)
本次改造的实施,使企业在不改变原有生产规模的情况下,大大降低燃煤的耗用量,降低了企业的燃料费用,产生显著的直接经济效益,减少燃煤的使用从而减少了污染物的排放总量,减少企业污染治理负担。
减少了对地区能源的总消耗量,减轻了对周边环境的影响,社会效益和环保效益显著。
由此可见,项目改造后的经济效益好,社会效益、环境效益显著,认为在财务上是可行的。
节能减排项目经济评价的关键是要能够清晰的理出节能减
排投资所能带来的效益,也就是投入和产出的一致性原则,如果能理顺关系并掌握好这个原则,财务评价是很简单的。