石川法求啮合刚度
考虑时变啮合刚度的齿轮动态啮合力分析
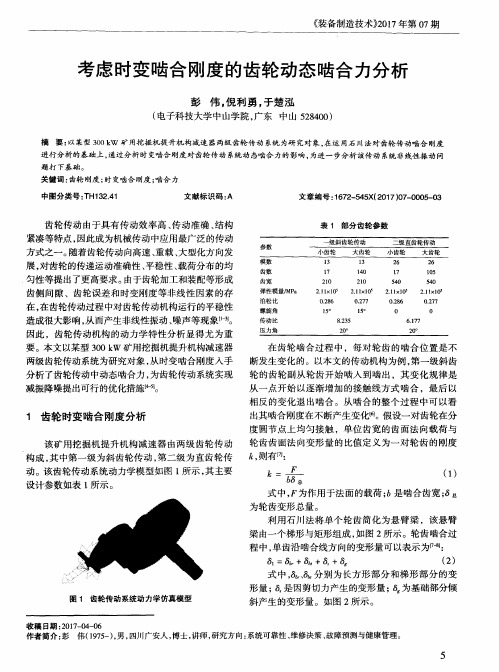
中图分类号 : T H 1 3 2 . 4 1
文献标识码 : A
文章编号 : 1 6 7 2 — 5 4 5 X( 2 0 1 7 ) 0 7 — 0 0 0 5 — 0 3
齿轮传 动由于具有传动效率高 、 传动准确 、 结构 紧凑等特点 , 因此成为机械传动 中应用最广泛 的传动
表 2 修 改 后 的 齿 轮模 数 和 齿 数
代 人 表 1的齿 轮 参数 ,采 用 接触 有 限元 法 可计
算得到第一级齿轮传动 的啮合刚度 , 如图3 所示 。
结合表 1 、 表 2的齿 轮参 数 , 三 种 情 况 下 第 一 级
齿轮传动的啮合刚度如图 4 所示。
啮 合 时 间/ s
相反 的变化退 出啮合 。从啮合的整个过程 中可以看 出其 啮合 刚 度在 不 断产生 变化 问 。假 设一 对 齿轮 在分
度圆节点上均匀接触 ,单位齿宽的齿面法 向载荷与 该矿用挖掘机提升机构减速器 由两级齿轮传动 轮齿 齿 面 法 向变 形 量 的 比值 定 义 为一 对 轮 齿 的 刚 度 , 则有用: 构成 , 其 中第 一级 为 斜 齿 轮传 动 , 第 二级 为直 齿 轮传 后 F 动 。该齿 轮传 动 系统 动力 学模 型如 图 l 所示 , 其 主要
1 = + + + ( 2 )
式 中, 、 分别 为长方形部分和梯 形部分的变 形量 ; 是因剪切力产生的变形量 ; 6 为基础部分倾
图 1 齿轮传 动系统动 力学仿真模型
斜产生的变形量 。如图 2 所示 。
收 稿 日期 : 2 0 1 7 — 0 4 — 0 6
石川法求啮合刚度
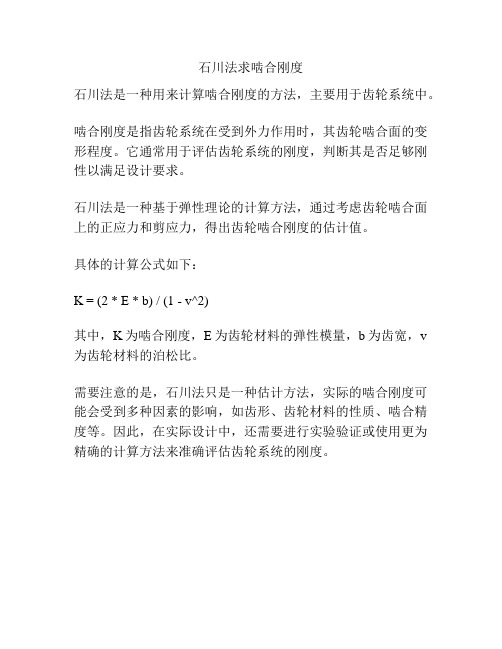
石川法求啮合刚度
石川法是一种用来计算啮合刚度的方法,主要用于齿轮系统中。
啮合刚度是指齿轮系统在受到外力作用时,其齿轮啮合面的变形程度。
它通常用于评估齿轮系统的刚度,判断其是否足够刚性以满足设计要求。
石川法是一种基于弹性理论的计算方法,通过考虑齿轮啮合面上的正应力和剪应力,得出齿轮啮合刚度的估计值。
具体的计算公式如下:
K = (2 * E * b) / (1 - v^2)
其中,K为啮合刚度,E为齿轮材料的弹性模量,b为齿宽,v 为齿轮材料的泊松比。
需要注意的是,石川法只是一种估计方法,实际的啮合刚度可能会受到多种因素的影响,如齿形、齿轮材料的性质、啮合精度等。
因此,在实际设计中,还需要进行实验验证或使用更为精确的计算方法来准确评估齿轮系统的刚度。
基于Workbench的齿轮啮合振动分析
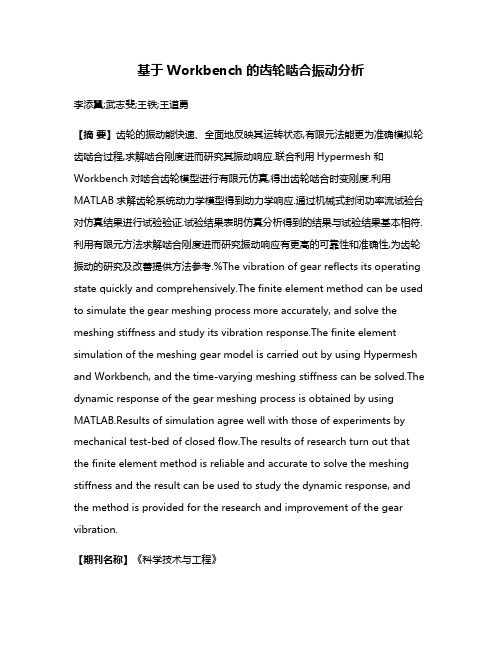
基于Workbench的齿轮啮合振动分析李添翼;武志斐;王铁;王道勇【摘要】齿轮的振动能快速、全面地反映其运转状态,有限元法能更为准确模拟轮齿啮合过程,求解啮合刚度进而研究其振动响应.联合利用Hypermesh 和Workbench对啮合齿轮模型进行有限元仿真,得出齿轮啮合时变刚度.利用MATLAB求解齿轮系统动力学模型得到动力学响应.通过机械式封闭功率流试验台对仿真结果进行试验验证.试验结果表明仿真分析得到的结果与试验结果基本相符.利用有限元方法求解啮合刚度进而研究振动响应有更高的可靠性和准确性,为齿轮振动的研究及改善提供方法参考.%The vibration of gear reflects its operating state quickly and comprehensively.The finite element method can be used to simulate the gear meshing process more accurately, and solve the meshing stiffness and study its vibration response.The finite element simulation of the meshing gear model is carried out by using Hypermesh and Workbench, and the time-varying meshing stiffness can be solved.The dynamic response of the gear meshing process is obtained by using MATLAB.Results of simulation agree well with those of experiments by mechanical test-bed of closed flow.The results of research turn out that the finite element method is reliable and accurate to solve the meshing stiffness and the result can be used to study the dynamic response, and the method is provided for the research and improvement of the gear vibration.【期刊名称】《科学技术与工程》【年(卷),期】2017(017)024【总页数】6页(P49-54)【关键词】有限元方法;时变啮合刚度;动力学模型;齿轮振动特性【作者】李添翼;武志斐;王铁;王道勇【作者单位】太原理工大学齿轮研究所,太原 030024;太原理工大学齿轮研究所,太原 030024;太原理工大学齿轮研究所,太原 030024;太原理工大学齿轮研究所,太原030024【正文语种】中文【中图分类】TH132.41齿轮系统是各种机器和机械装备中应用最为广泛的动力和运动传递装置,其力学行为和工作性能对整个机器有重要的影响[1]。
齿轮刚度的计算
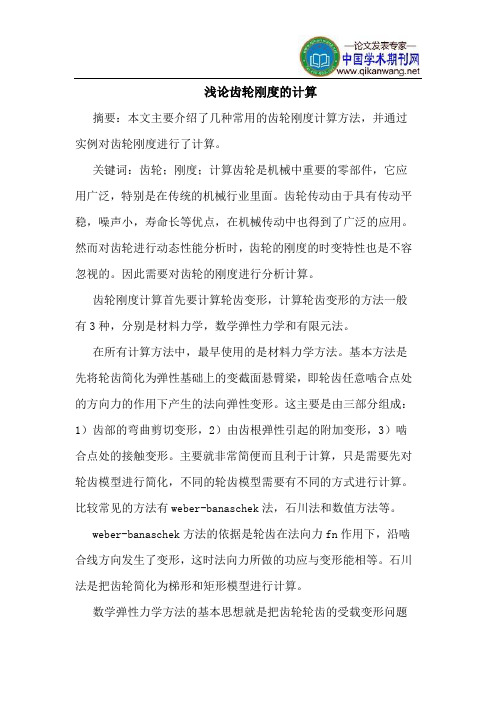
浅论齿轮刚度的计算摘要:本文主要介绍了几种常用的齿轮刚度计算方法,并通过实例对齿轮刚度进行了计算。
关键词:齿轮;刚度;计算齿轮是机械中重要的零部件,它应用广泛,特别是在传统的机械行业里面。
齿轮传动由于具有传动平稳,噪声小,寿命长等优点,在机械传动中也得到了广泛的应用。
然而对齿轮进行动态性能分析时,齿轮的刚度的时变特性也是不容忽视的。
因此需要对齿轮的刚度进行分析计算。
齿轮刚度计算首先要计算轮齿变形,计算轮齿变形的方法一般有3种,分别是材料力学,数学弹性力学和有限元法。
在所有计算方法中,最早使用的是材料力学方法。
基本方法是先将轮齿简化为弹性基础上的变截面悬臂梁,即轮齿任意啮合点处的方向力的作用下产生的法向弹性变形。
这主要是由三部分组成:1)齿部的弯曲剪切变形,2)由齿根弹性引起的附加变形,3)啮合点处的接触变形。
主要就非常简便而且利于计算,只是需要先对轮齿模型进行简化,不同的轮齿模型需要有不同的方式进行计算。
比较常见的方法有weber-banaschek法,石川法和数值方法等。
weber-banaschek方法的依据是轮齿在法向力fn作用下,沿啮合线方向发生了变形,这时法向力所做的功应与变形能相等。
石川法是把齿轮简化为梯形和矩形模型进行计算。
数学弹性力学方法的基本思想就是把齿轮轮齿的受载变形问题简化为一个半无限体的受载变形,利用保角映射函数把轮齿的曲线边界c映射为直边边界场。
这样可以应用弹性力学中平面问题的复变函数解答求解集中力作用下的半无限体的位移场,再由此确定受载轮齿的位移场。
康焱用有限元方法计算了渐开线直齿内齿轮的轮齿刚度,其最后得到的渐开线直齿内齿轮的载荷作用点的轮齿刚度的计算公式为[2-3]:c=(e/a)(λx+1)b(x+1)c×10-9(3)式中:a=0.0011z2-0.1381z+12.8587b=-0.0056z+1.0483c=-0.0002z+0.0376计算出轮齿任意啮合点k处的法向弹性变形δk以后,单个轮齿的啮合刚度即可求出kk=fkδk,应该说明的是轮齿在不同的啮合点啮合时δk是不同的,因此轮齿的啮合刚度也是啮合点位置的函数。
混合动力轿车传动系的扭转振动与噪声分析

混合动力轿车传动系的扭转振动与噪声分析邹良;唐小林;于海生;张彤;张建武【摘要】针对某深度混合动力轿车的传动系振动与噪声问题,对传动系统进行了扭转振动分析和噪声测试,识别出了噪声源。
在考虑啮合刚度的齿轮副等效轴系模型基础上,建立了复合行星轮系和整车传动系统的扭转振动力学模型。
对传动系的固有频率和模态振型进行了研究,并与噪声测试结果进行了对比。
结果表明,齿轮副啮合是该传动系的主要噪声源,而扭转振动是引起传动系噪声的重要原因。
%Aiming at the vibration and noise problem of transmission system in a deep hybrid electric vehi-cle, the torsional vibration analysis and noise test of its transmission system are carried out with noise source identi-fied. Based on the equivalent shafts model for gear pairs with consideration of engagement stiffness, dynamic models for the torsional vibration of compound planetary gear sets and transmission system are established. The natural fre-quencies and mode shapes of transmission system are analyzed and compared with the results of noise test. The re-sults demonstrate that the source of noise in transmission system is the engagement of gear pairs while its important cause is torsional vibration.【期刊名称】《汽车工程》【年(卷),期】2014(000)006【总页数】6页(P709-714)【关键词】混合动力轿车;扭转振动;噪声测试;固有频率【作者】邹良;唐小林;于海生;张彤;张建武【作者单位】上海交通大学机械与动力工程学院,上海 200240;上海交通大学机械与动力工程学院,上海 200240;上海交通大学机械与动力工程学院,上海200240; 上海华普汽车有限公司,上海 201501;上海华普汽车有限公司,上海201501;上海交通大学机械与动力工程学院,上海 200240【正文语种】中文前言混合动力车辆(HEV)的动力复合装置一直是各研究机构和厂商的研发重点。
线外啮合齿轮传动啮合刚度计算_唐进元

(27) (28)
啮合 齿对 在 D 点 的变形 沿理
论啮合线方向的分量 。 式(24) 由等式 rb1 θP =rb2 θG +e 演化 而来 , 该等式是沿理论啮合线
方向的一个几何恒等式 。 方程
式(28)中实际上只有 θG 一个 变量 , 它是一个非线性方程 , 可 通过迭代方 法求解 , 迭代时需 图 3 啮出点计算示意图
许多文献1116在进行齿轮动力学分析时都取无误差的啮合刚度作为刚度模型线外啮合齿轮传动啮合刚度计算2312wjlicosdsigai2kj1j16wjsinjlidci3eeai与节圆齿厚sp之比bsp5时轮齿为宽齿处于平面应变状态此时有ee42若bspeee剪切弹性模量gee21齿根基础的弹性变形引起的啮合点的附加变形dfj对于窄齿bspf2fjj530621dfjhfhfbe04167tan2啮出终点线外啮合变形计算示意10图因此沿wj作用线方向齿部总的弹性变形为线外啮合刚度计算无加工制造误差时由式1式16可计算啮合刚度若计算有误差的线外啮合刚度则必须要知道啮合点位置与载荷作用角为啮合终点处线外啮合示意图图2中虚线为理论啮合终点位置转过的角度为p轮齿2对应转过的角度为为啮合角由三心定理知p为两齿廓退g出线外啮合时的节点位置
伸 , 主要给出一种轮齿上任一点在载荷作用下的变形
计算方法 。假设轮齿为一弹性基础上的变截面悬臂梁
(如图 1), Wj 为作用在轮齿表面 j 点的载荷 , 其引起的 总的弹性变形由下述 3 部分组成
(1)变截 面悬臂梁(齿部)的弯曲 、剪 切和压缩变
形;
(2)基础(齿根)的弹性变形引起的附加变形 ;
从图 5 可见考虑线外啮合时 , 啮合起点的刚度值 较图 4 中的理论啮合起点值要大 , 同时刚度曲线出现 一次从大到小的变化 。 计算表明 , 当同时考虑变形和 误差时 , 实际啮合起点刚度值较图 5 中的值还要大 , 刚 度曲线的变化更显著 , 载荷越大 , 误差越大 , 变化越显 著 。刚度的变化会引起系统动态响应的变化 , 进一步 使系统产生振动和噪声 。 因此 , 齿轮动力学分析中应 考虑线外啮合的实际的齿轮传动刚度 , 本文提出的线 外啮合刚度计算方法能把线外啮合与实际的刚度计算 有机结合起来 , 是一种十分有效的实用方法 。
求解齿轮刚度

% hxi1(i)=rxi1(i)*cos(gamai1(i))-sqrt(rf1^2-(sf1/2)^2);
N2Bi(i)=N2B2-i*step;
O2Bi(i)=sqrt(N2Bi(i)^2+rb2^2);
sigmabti1(i)=6*Fn*cos(miui1(i))^2*((hi1-hxi1(i))/(hi1-hr1)*(4-(hi1-hxi1(i))/(hi1-hr1))-2*log((hi1-hxi1(i))/(hi1-hr1))-3)*(hi1-hr1)^3/b/E/sf1^3;
sigmabti2(i)=6*Fn*cos(miui2(i))^2*((hi2-hxi2(i))/(hi2-hr2)*(4-(hi2-hxi2(i))/(hi2-hr2))-2*log((hi2-hxi2(i))/(hi2-hr2))-3)*(hi2-hr2)^3/b/E/sf2^3;
% % % %hr=sqrt(rb^2-(sf/2)^2)-sqrt(rf^2-(sf/2)^2);
sf1=2*rF1*sin(pi/2/z1+invalpha-tan(alpha_F1)+alpha_F1);%危险截面长度
sf2=2*rF2*sin(pi/2/z2+invalpha-tan(alpha_F2)+alpha_F2);
miuj1(i)=aj1(i)-gamaj1(i);
rxj1(i)=O1Bj(i);
hxj1(i)=rxj1(i)*cos(alpha-miuj1(i))-sqrt(rf1^2-(sf1/2)^2);
齿轮时变啮合刚度改进计算方法_李亚鹏

文章编号:1004-2539(2010)05-0022-05齿轮时变啮合刚度改进计算方法李亚鹏 孙 伟 魏 静 陈 涛(大连理工大学机械工程学院, 辽宁大连 116024)摘要 齿轮时变啮合刚度是齿轮系统动力方程的重要基础参数,针对目前时变啮合刚度主要利用有限元方式计算,效率偏低的问题,以及解析法石川公式仅考虑齿轮轮齿刚度,未考虑齿轮轮体刚度,容易在齿轮动力学分析中引入高次谐波激励的不足,本文在详细介绍解析算法石川公式中重要参数算法的基础上提出改进的石川公式,为齿轮动力方程提供一个整体意义上的时变啮合刚度计算方法。
同时介绍了多齿啮合时齿轮综合时变啮合刚度的计算方法。
关键词 时变啮合刚度 改进石川公式 有效齿根圆 内啮合传动Study on the Improved Algorithm of the Time-varying Meshing Sti ffness of G earLi Y apeng Sun Wei Wei Jing Chen T ao(School of M echanical Engineering,Dalian University of T echnology,Dalian116024,China)Abstract The time-varying meshing stiffness of gear is the m ost im portant parameter in the dynamic equation of the gear systems,but now the m ost usually way of obtaining the parameter is the finite element methods and it’s very low efficiency.The Ishikawa formula is the analytical method which was used to calculate the time-varying meshing stiffness,it’s high efficiency but it only considers the deformation of the tooth of the gear,what’s m ore, s ome parameter which was referred in the Ishikawa formula don’t have a certain way to get now.Aiming at these prob2 lems,in this paper,the calculation method of the unclear parameters and an im proved formula of the time-varying meshing stiffness are presented.C om pared with the Ishikawa formula,the im proved formula consider the deformation of the gear web plate and bring less high harm onic excitation.And this paper introduces the calculation principle of multi-tooth time-varying meshing stiffness.K ey w ords T ime-varying meshing stiffness Im proved ishikawa formula E ffective root diameter Internal meshing transmission0 引言齿轮传动是目前机械系统中的最重要的传动方式,随着齿轮传动系统向高速、重载、大型化方向发展,单纯依赖传统静力学模型所进行的齿廓修形、螺旋角修形等方式已经远远不能满足当前使用要求。
小模数齿轮传动的时变啮合刚度计算方法

Te
chno
l
ogy,
Changsha,
410114
2.
Co
l
l
egeo
fMe
chan
i
c
a
landVeh
i
c
l
eEng
i
ne
e
r
i
ng,
HunanUn
i
ve
r
s
i
t
Changsha,
410082
y,
Ab
s
t
r
a
c
t:Duet
ot
hesma
l
lc
en
t
e
rd
i
s
t
anc
e,t
hedynami
c pe
ft
heme
sh
i
ngs
t
i
f
f
ne
s
si
nt
hewho
l
ec
l
e.Thei
n
f
l
uenc
e
so
fc
en
t
e
rd
i
s
G
yc
t
anc
ee
r
r
o
r
sandsha
f
tho
l
ef
i
tc
l
e
a
r
anc
e
sbo
t
hsupe
r
impo
s
edandwe
akenede
a
cho
t
he
法向啮合刚度和综合啮合刚度

法向啮合刚度和综合啮合刚度
法向啮合刚度是指在啮合过程中,啮合齿轮之间的法向刚度。
在齿轮传动中,齿轮齿面的啮合会受到受力,而法向啮合刚度则是描述了齿轮在法向上的刚度特性。
它是啮合齿轮在法向上受到外部载荷作用时,齿轮齿面的位移与受力之间的关系,通常用刚度系数来表示。
法向啮合刚度的大小会影响齿轮传动系统的动态特性和传动精度。
综合啮合刚度是指考虑了齿轮传动中齿轮啮合时的所有刚度因素后得到的综合刚度。
它包括了齿轮的法向啮合刚度、刚度变化系数、齿根刚度、齿顶刚度等因素。
综合啮合刚度的大小直接影响着齿轮传动系统的动态响应和传动精度。
综合啮合刚度越大,传动系统的刚度越高,传动精度也会相应提高。
从设计角度来看,法向啮合刚度和综合啮合刚度对于齿轮传动系统的设计至关重要。
合理选择和设计齿轮的啮合刚度,可以提高齿轮传动系统的动态性能和传动精度,减小齿轮啮合时的振动和噪音。
因此,在齿轮传动系统的设计和优化过程中,需要充分考虑和评估法向啮合刚度和综合啮合刚度,以确保齿轮传动系统具有良好的工作性能和可靠性。
总的来说,法向啮合刚度和综合啮合刚度是齿轮传动系统中重要的参数,它们直接影响着传动系统的性能和精度。
合理的设计和选择可以提高齿轮传动系统的工作效率和可靠性。
考虑时变啮合刚度的齿轮动态啮合力分析
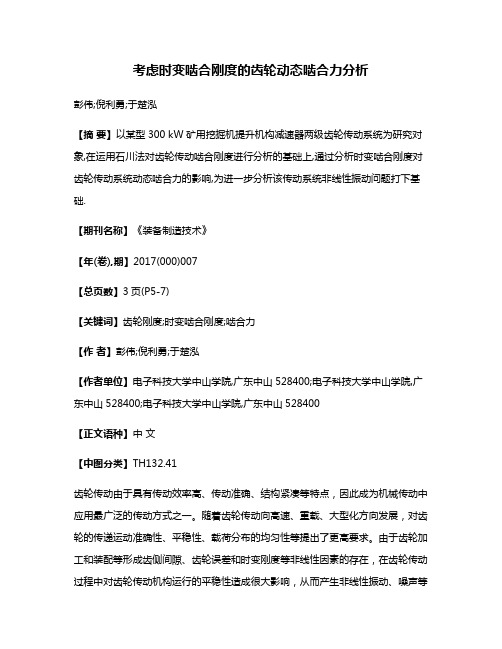
考虑时变啮合刚度的齿轮动态啮合力分析彭伟;倪利勇;于楚泓【摘要】以某型300 kW矿用挖掘机提升机构减速器两级齿轮传动系统为研究对象,在运用石川法对齿轮传动啮合刚度进行分析的基础上,通过分析时变啮合刚度对齿轮传动系统动态啮合力的影响,为进一步分析该传动系统非线性振动问题打下基础.【期刊名称】《装备制造技术》【年(卷),期】2017(000)007【总页数】3页(P5-7)【关键词】齿轮刚度;时变啮合刚度;啮合力【作者】彭伟;倪利勇;于楚泓【作者单位】电子科技大学中山学院,广东中山528400;电子科技大学中山学院,广东中山528400;电子科技大学中山学院,广东中山528400【正文语种】中文【中图分类】TH132.41齿轮传动由于具有传动效率高、传动准确、结构紧凑等特点,因此成为机械传动中应用最广泛的传动方式之一。
随着齿轮传动向高速、重载、大型化方向发展,对齿轮的传递运动准确性、平稳性、载荷分布的均匀性等提出了更高要求。
由于齿轮加工和装配等形成齿侧间隙、齿轮误差和时变刚度等非线性因素的存在,在齿轮传动过程中对齿轮传动机构运行的平稳性造成很大影响,从而产生非线性振动、噪声等现象[1-3]。
因此,齿轮传动机构的动力学特性分析显得尤为重要。
本文以某型300 kW矿用挖掘机提升机构减速器两级齿轮传动系统为研究对象,从时变啮合刚度入手分析了齿轮传动中动态啮合力,为齿轮传动系统实现减振降噪提出可行的优化措施[4-5]。
该矿用挖掘机提升机构减速器由两级齿轮传动构成,其中第一级为斜齿轮传动,第二级为直齿轮传动。
该齿轮传动系统动力学模型如图1所示,其主要设计参数如表1所示。
在齿轮啮合过程中,每对轮齿的啮合位置是不断发生变化的。
以本文的传动机构为例,第一级斜齿轮的齿轮副从轮齿开始啮入到啮出,其变化规律是从一点开始以逐渐增加的接触线方式啮合,最后以相反的变化退出啮合。
从啮合的整个过程中可以看出其啮合刚度在不断产生变化[6]。
齿轮时变啮合刚度计算研究 杨雄威 夏宗朝

齿轮时变啮合刚度计算研究杨雄威夏宗朝摘要:本文分析总结了齿轮啮合刚度的常见计算方法。
提出了一种接触有限元法计算时变啮合刚度且验证了其准确性,并分析了齿轮产生冲击振动的缘由。
关键词:齿轮;时变啮合刚度;接触有限元;冲击振动0.引言齿轮刚度的精确计算是轮齿修形、动态特性、故障诊断、寿命预测以及齿轮参数优化设计等研究的前提条件。
有必要对圆柱齿轮刚度的计算作进一步的探讨和研究。
日本机械学会[1]上齿轮的刚度定义为如下:齿轮刚度为使一对或几对同时啮合的精确齿轮在1mm齿宽上产生1um绕度所需的啮合线上的载荷。
设齿轮宽度为b(mm),齿轮所受的作用于齿廓的法向载荷为Fn(N),齿轮的总变形为δ(um),齿轮上的载荷集度,即齿轮单位齿宽的载荷ω为:ω=Fn/b;齿轮的柔度为:q=δ/ω; 则齿轮的刚度为:c=1/q= Fn/b/δ。
齿轮的单齿刚度的定义为单齿在外载荷的作用下,接触力与位移的比例系数,其表达式为:Kn=Fn/un;其中Fn为作用于轮齿齿廓曲面的接触力;un为齿轮的综合弹性变形量,其中包括了弯曲变形、剪切变形和接触变形等。
单齿对啮合刚度的定义为两个齿轮啮合过程中的综合刚度,两个齿轮以串联的方式耦合形成的单齿接触对,通过单齿刚度可以计算出啮合刚度为:K=K1*K2/(K1+ K2);其中1,2分别为小齿轮和大齿轮。
齿轮啮合综合刚度定义为多对齿轮接触时,各对齿轮间形成并联的耦合关系,所以齿轮啮合综合刚度的表达式为:Km=K1+K2+…+Kn所以齿轮啮合综合刚度主要与单齿的弹性变形、单齿对齿轮的综合弹性变形以及齿轮重合度有关。
因此只要求得齿轮的弹性变形,即可确定齿轮啮合综合刚度。
1.几种常用齿轮刚度计算方法的比较目前关于齿轮轮齿啮合变形的计算方法大致有三种,即材料力学方法、弹性力学方法和数值方法。
材料力学方法中又分为韦伯公式和石川公式。
本文将主要采用ISO方法(B法)回归公式,半经验回归公式,材料力学(石川公式)及有限元方法对相同参数齿轮的刚度进行计算比较。
基于参数反求的齿轮裂纹时变啮合刚度计算方法
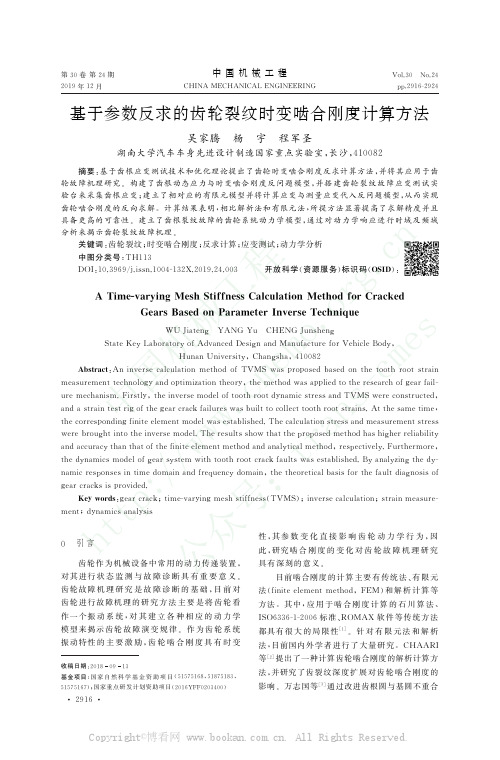
me
s
的力包含法向 载 荷 N 和 垂 直 于 法 向 载 荷 的 摩 擦
限元法虽 然 能 够 通 过 计 算 得 到 齿 轮 时 变 啮 合 刚
量大、建模困难且无法验证等.
(
4)
号
ht
tp
的基础上,采用优化方法反向求解时变啮合刚度.
将计算结果与其他方法对比来验证该方法的有效
公
众
性.同时构建多 自 由 度 齿 轮 系 统 动 力 学 模 型,将
N(
t)-Cmδn)
δn
[
4]
运用有限元分析
(
1)
其中,
N 为法 向 载 荷,
Cm 为 齿 轮 啮 合 黏 性 阻 尼,
方法和赫兹接触理论分析方法描述了齿轮啮合传
动 过 程 中 齿 轮 啮 合 刚 度 的 变 化 过 程.LIANG
δn 为法向 综 合 弹 性 形 变. 根 据 轮 齿 传 递 误 差 原
械
如图 1 所示,啮合齿接触时,实际作用于齿面
o.
次的齿轮故 障 进 行 定 量 诊 断.然 而,解 析 法 和 有
ww
w.
现代测试方法、优化方法与有限元法相结合,提出
Nx =N (
c
o
s
α+μs
i
n
α)
:
动态应力发生相应的变化 [10],该 方 法 通 过 对 各 种
tr
关系,即啮合刚度 的 变 化 会 引 起 裂 纹 部 位 的 齿 根
o.
械
or
AT
ime
G
va
r
i
ng Me
s
hS
t
i
f
f
石川法求啮合刚度
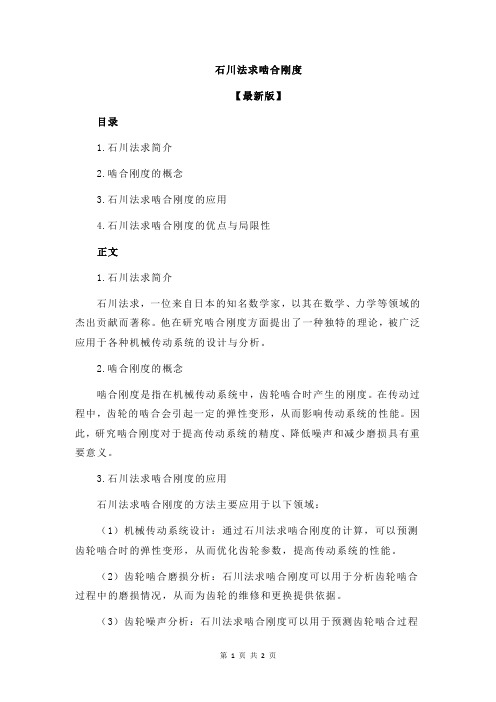
石川法求啮合刚度
【最新版】
目录
1.石川法求简介
2.啮合刚度的概念
3.石川法求啮合刚度的应用
4.石川法求啮合刚度的优点与局限性
正文
1.石川法求简介
石川法求,一位来自日本的知名数学家,以其在数学、力学等领域的杰出贡献而著称。
他在研究啮合刚度方面提出了一种独特的理论,被广泛应用于各种机械传动系统的设计与分析。
2.啮合刚度的概念
啮合刚度是指在机械传动系统中,齿轮啮合时产生的刚度。
在传动过程中,齿轮的啮合会引起一定的弹性变形,从而影响传动系统的性能。
因此,研究啮合刚度对于提高传动系统的精度、降低噪声和减少磨损具有重要意义。
3.石川法求啮合刚度的应用
石川法求啮合刚度的方法主要应用于以下领域:
(1)机械传动系统设计:通过石川法求啮合刚度的计算,可以预测齿轮啮合时的弹性变形,从而优化齿轮参数,提高传动系统的性能。
(2)齿轮啮合磨损分析:石川法求啮合刚度可以用于分析齿轮啮合过程中的磨损情况,从而为齿轮的维修和更换提供依据。
(3)齿轮噪声分析:石川法求啮合刚度可以用于预测齿轮啮合过程
中的噪声,从而为降噪设计提供参考。
4.石川法求啮合刚度的优点与局限性
优点:
(1)计算简便:石川法求啮合刚度的计算方法相对简单,易于工程技术人员掌握和应用。
(2)适用范围广:石川法求啮合刚度的方法适用于各种类型的齿轮啮合,具有较强的通用性。
局限性:
(1)精度受限:石川法求啮合刚度的计算方法基于一定的假设和简化,因此计算结果的精度受到一定限制。
石川法求啮合刚度
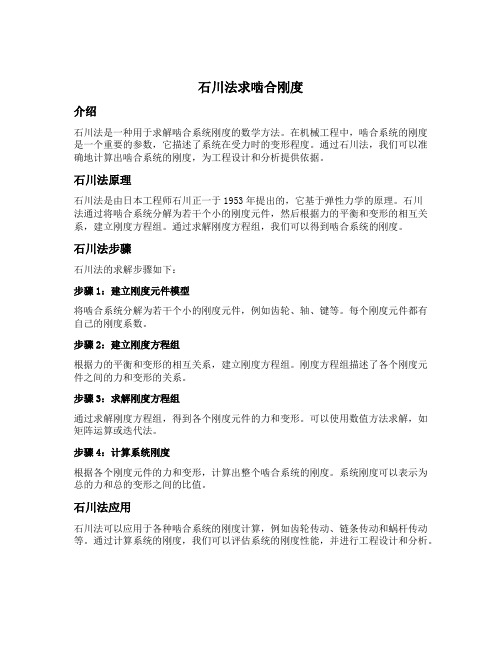
石川法求啮合刚度介绍石川法是一种用于求解啮合系统刚度的数学方法。
在机械工程中,啮合系统的刚度是一个重要的参数,它描述了系统在受力时的变形程度。
通过石川法,我们可以准确地计算出啮合系统的刚度,为工程设计和分析提供依据。
石川法原理石川法是由日本工程师石川正一于1953年提出的,它基于弹性力学的原理。
石川法通过将啮合系统分解为若干个小的刚度元件,然后根据力的平衡和变形的相互关系,建立刚度方程组。
通过求解刚度方程组,我们可以得到啮合系统的刚度。
石川法步骤石川法的求解步骤如下:步骤1:建立刚度元件模型将啮合系统分解为若干个小的刚度元件,例如齿轮、轴、键等。
每个刚度元件都有自己的刚度系数。
步骤2:建立刚度方程组根据力的平衡和变形的相互关系,建立刚度方程组。
刚度方程组描述了各个刚度元件之间的力和变形的关系。
步骤3:求解刚度方程组通过求解刚度方程组,得到各个刚度元件的力和变形。
可以使用数值方法求解,如矩阵运算或迭代法。
步骤4:计算系统刚度根据各个刚度元件的力和变形,计算出整个啮合系统的刚度。
系统刚度可以表示为总的力和总的变形之间的比值。
石川法应用石川法可以应用于各种啮合系统的刚度计算,例如齿轮传动、链条传动和蜗杆传动等。
通过计算系统的刚度,我们可以评估系统的刚度性能,并进行工程设计和分析。
石川法优势石川法具有以下优势:1.准确性:石川法基于弹性力学原理,可以准确地计算出啮合系统的刚度。
2.灵活性:石川法适用于各种啮合系统,可以灵活地应用于不同的工程问题。
3.可靠性:石川法已经在实际工程中得到了广泛的应用和验证,其计算结果具有一定的可靠性。
4.效率性:石川法的计算过程相对简单,可以通过计算机程序实现自动化计算,提高计算效率。
总结石川法是一种用于求解啮合系统刚度的数学方法。
通过分解啮合系统为若干个刚度元件,并建立刚度方程组,可以准确地计算出系统的刚度。
石川法具有准确性、灵活性、可靠性和效率性等优势,在工程设计和分析中有着重要的应用价值。
石川法求啮合刚度
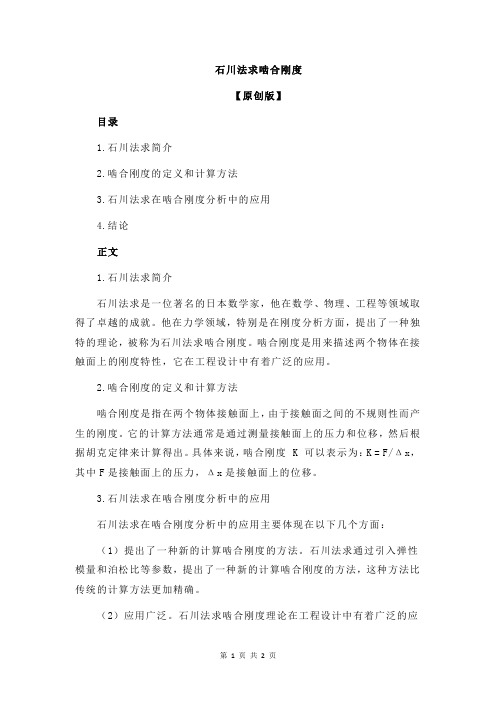
石川法求啮合刚度
【原创版】
目录
1.石川法求简介
2.啮合刚度的定义和计算方法
3.石川法求在啮合刚度分析中的应用
4.结论
正文
1.石川法求简介
石川法求是一位著名的日本数学家,他在数学、物理、工程等领域取得了卓越的成就。
他在力学领域,特别是在刚度分析方面,提出了一种独特的理论,被称为石川法求啮合刚度。
啮合刚度是用来描述两个物体在接触面上的刚度特性,它在工程设计中有着广泛的应用。
2.啮合刚度的定义和计算方法
啮合刚度是指在两个物体接触面上,由于接触面之间的不规则性而产生的刚度。
它的计算方法通常是通过测量接触面上的压力和位移,然后根据胡克定律来计算得出。
具体来说,啮合刚度 K 可以表示为:K = F/Δx,其中F是接触面上的压力,Δx是接触面上的位移。
3.石川法求在啮合刚度分析中的应用
石川法求在啮合刚度分析中的应用主要体现在以下几个方面:
(1)提出了一种新的计算啮合刚度的方法。
石川法求通过引入弹性模量和泊松比等参数,提出了一种新的计算啮合刚度的方法,这种方法比传统的计算方法更加精确。
(2)应用广泛。
石川法求啮合刚度理论在工程设计中有着广泛的应
用,例如在齿轮设计、轴承设计等领域都有应用。
(3)促进了啮合刚度理论的发展。
石川法求啮合刚度理论的提出,促进了啮合刚度理论的发展,为后来的研究者提供了重要的理论基础。
4.结论
石川法求啮合刚度理论在工程设计中有着广泛的应用,它提高了啮合刚度计算的精确度,促进了啮合刚度理论的发展。
- 1、下载文档前请自行甄别文档内容的完整性,平台不提供额外的编辑、内容补充、找答案等附加服务。
- 2、"仅部分预览"的文档,不可在线预览部分如存在完整性等问题,可反馈申请退款(可完整预览的文档不适用该条件!)。
- 3、如文档侵犯您的权益,请联系客服反馈,我们会尽快为您处理(人工客服工作时间:9:00-18:30)。
石川法求啮合刚度
摘要:
1.石川法简介
2.石川法求啮合刚度的基本原理
3.石川法求啮合刚度的具体步骤
4.石川法在实际工程中的应用及局限性
正文:
石川法是一种用于求解齿轮啮合刚度的方法,由日本学者石川武雄教授提出,因此得名。
该方法主要应用于齿轮传动系统,通过计算得到齿轮啮合刚度,从而分析齿轮传动系统的动力学性能。
石川法求啮合刚度的基本原理是:首先假设齿轮啮合刚度K 为常数,然后根据齿轮啮合的接触疲劳强度条件,求解齿轮的啮合刚度K。
具体来说,石川法将齿轮啮合刚度K 表示为:
K = f * β * γ
其中,f 为接触疲劳强度系数,β 为齿轮啮合系数,γ 为齿轮齿廓系数。
石川法求啮合刚度的具体步骤如下:
1.根据齿轮的材料、热处理状态和齿轮副的装配条件,确定接触疲劳强度系数f。
2.计算齿轮啮合系数β。
β的计算公式为:β = (1 + μ) / (1 - μ),其中μ为齿轮副的相对滑动量。
3.计算齿轮齿廓系数γ。
γ的计算公式为:γ = (1 + ε) / (1 - ε),其中ε为
齿轮副的相对错位量。
4.将f、β、γ代入公式K = f * β * γ,计算得到齿轮啮合刚度K。
石川法在实际工程中得到了广泛的应用,例如在齿轮传动系统的设计、分析和故障诊断中。
然而,石川法也存在一定的局限性,例如在处理高、低速传动系统和高精度传动系统时,石川法可能无法提供准确的结果。