供应商质量评价制度
食堂供应商的质量评定和退出机制

食堂供应商的质量评定和退出机制一、质量评定目的为了确保食堂供应食品的安全、卫生、营养和口味,提高食堂服务质量,满足师生员工的就餐需求,特制定食堂供应商的质量评定和退出机制。
二、质量评定原则1. 公平、公正、公开:评定过程应保证各供应商公平竞争,结果公正、透明。
2. 综合评价:从食品质量、服务水平、价格等多个方面对供应商进行评价。
3. 持续改进:通过评定发现供应商存在的问题,促使供应商改进,提高服务质量。
三、质量评定内容1. 食品质量:包括食品的新鲜度、口感、营养价值、品种多样性等。
2. 服务水平:包括供应商的送餐速度、服务质量、态度、食堂卫生状况等。
3. 价格:供应商提供的食品价格应合理,性价比高。
4. 管理制度:供应商应具备完善的管理制度,包括食品安全管理、员工培训管理等。
5. 投诉处理:对师生员工的投诉,供应商应及时处理并采取改进措施。
四、质量评定流程1. 成立评定小组:由学校相关部门组成评定小组,负责食堂供应商的质量评定工作。
2. 数据收集:评定小组收集供应商在食品质量、服务水平、价格等方面的数据。
3. 现场考察:评定小组对供应商进行现场考察,了解其食堂卫生状况、管理制度等。
4. 综合评价:评定小组根据收集的数据和现场考察情况,对供应商进行综合评价。
5. 结果公示:将评定结果进行公示,接受师生员工的监督。
6. 反馈与改进:对评定结果进行分析,向供应商反馈存在的问题,督促其改进。
五、退出机制1. 供应商在质量评定过程中得分低于规定标准,给予警告并督促其改进。
2. 供应商在规定期限内未能改进或问题严重,暂停合作直至整改合格。
3. 供应商出现食品安全事故或重大服务质量问题,立即终止合作。
4. 供应商主动申请退出,经学校同意后终止合作。
5. 供应商因故无法继续提供服务,如破产、营业执照被吊销等,终止合作。
六、评定周期与有效期限1. 食堂供应商的质量评定周期为一年,定期进行。
2. 评定结果的有效期限为一年,过期需重新进行评定。
合格供应商评价管理制度

合格供应商评价管理制度一、引言供应商是企业运作中不可或缺的一环,合格供应商评价管理制度的建立和落地对于企业的供应链管理和产品质量控制至关重要。
本文旨在介绍一个较为完整的合格供应商评价管理制度。
二、评价标准的制定1.供应商注册根据企业的需求和要求,设定供应商应具备的基本要求,包括注册条件、供应能力、质量认证等。
2.供应商信用评价通过定期对供应商进行信用评价,评估供应商的经济状况、对合同的履约能力和信誉等。
根据评价结果,分级管理供应商,确保经济合作的安全性和可靠性。
3.供应商质量评价对供应商的产品质量进行评估,考察供应商的质量管理系统、生产工艺和检测能力等。
通过抽样检验、产品评估和用户反馈等方式,定期对供应商的产品质量进行监控和评价。
4.供应商交货准时率评价评估供应商的交货准时率,考察供应商的交货能力和生产计划管理水平。
及时了解供应商的交货情况,确保企业的生产计划能够按时进行。
三、评价方法的选择1.定性评价方法根据对供应商的实地考察、面谈和文件资料的评估,对供应商的综合能力和信誉进行评价。
此方法侧重于对供应商进行全面的综合评估,不仅考察供应商的产品质量水平,还考虑了供应商的可靠性和服务水平。
2.定量评价方法通过数据统计和分析的方法,对供应商的性能指标进行评估。
此方法侧重于通过客观的数据来评价供应商的性能,如交货准时率、产品质量合格率等。
四、评价周期和频率根据企业的需求和供应商的特点,确定评价周期和频率。
一般来说,供应商评价应定期进行,每年至少进行一次综合评价。
对于关键供应商和重要物资的供应商,可以加大评价频率。
五、评价结果应用1.供应商分类管理根据供应商的评价结果,将供应商进行分类管理,分为优秀供应商、合格供应商和不合格供应商等。
对于优秀供应商应及时给予奖励和激励;对于不合格供应商应采取相应的措施或进行整改。
2.供应商发展计划根据供应商的评价结果,制定相应的供应商发展计划,对于有潜力的供应商,可以给予相关资源和支持,帮助其提升能力和水平。
供应商质量评价制度
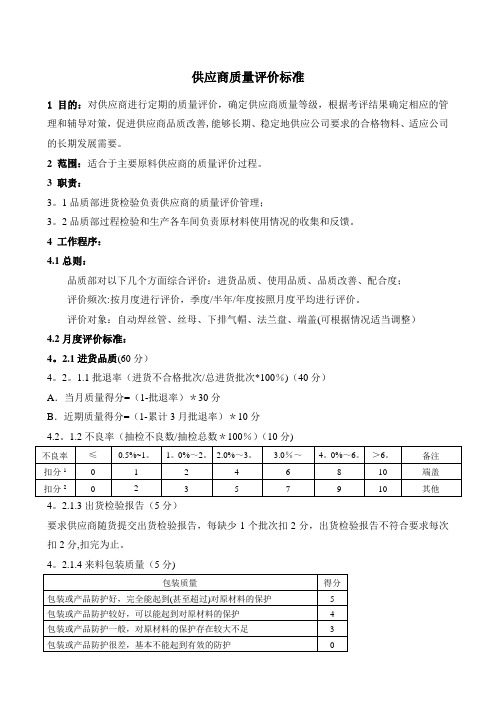
供应商质量评价标准1 目的:对供应商进行定期的质量评价,确定供应商质量等级,根据考评结果确定相应的管理和辅导对策,促进供应商品质改善,能够长期、稳定地供应公司要求的合格物料、适应公司的长期发展需要。
2 范围:适合于主要原料供应商的质量评价过程。
3 职责:3。
1品质部进货检验负责供应商的质量评价管理;3。
2品质部过程检验和生产各车间负责原材料使用情况的收集和反馈。
4 工作程序:4.1总则:品质部对以下几个方面综合评价:进货品质、使用品质、品质改善、配合度;评价频次:按月度进行评价,季度/半年/年度按照月度平均进行评价。
评价对象:自动焊丝管、丝母、下排气帽、法兰盘、端盖(可根据情况适当调整)4.2月度评价标准:4。
2.1进货品质(60分)4。
2。
1.1批退率(进货不合格批次/总进货批次*100%)(40分)A.当月质量得分=(1-批退率)*30分B.近期质量得分=(1-累计3月批退率)*10分4.2。
1.2不良率(抽检不良数/抽检总数*100%)(10分)4。
2.1.3出货检验报告(5分)要求供应商随货提交出货检验报告,每缺少1个批次扣2分,出货检验报告不符合要求每次扣2分,扣完为止。
4。
2.1.4来料包装质量(5分)4。
2。
2使用品质(20分)4.2.2。
1过程批不良(10分)在生产使用中,因原材料问题导致批量不良(一般外观缺陷>5%;严重外观缺陷、尺寸不良>3%;功能方面>2%),每出现一次过程投诉经确认批退的分别扣2、3、5分,扣完为止。
4.2。
2.1月使用个例不良(10分)根据生产过程中出现的不良情况,对同类供应商进行排名,按照9,7,5,3,1计算得分.4.2。
3品质改善效果(10分)对反馈品质问题的改善情况跟踪验证,根据问题出现的频次和改善效果,给出评分.4。
2.4配合度(10分)4。
2。
4。
1投诉处理配合度(7分)注:收到投诉报告或电话投诉1天内,及时向投诉人沟通并经其同意延时回复的不纳入评分范围。
供应商质量考核规定

供应商质量考核规定1. 背景为了确保供应商提供的商品和服务的质量符合公司要求,进一步提高供应链管理和产品质量标准,制定本供应商质量考核规定。
2. 目的本规定旨在建立供应商质量考核的制度和流程,确保供应商按照公司要求提供高质量的商品和服务,以保证公司产品质量和客户满意度。
3. 考核指标3.1 商品质量:供应商提供的商品应符合公司规定的质量标准和要求。
考核指标包括产品功能性能、外观质量、可靠性等。
3.2 交货准时率:供应商应按照合同约定的交货时间交付商品。
考核指标为供应商按时交货的比例。
3.3 服务质量:供应商提供的售前、售中和售后服务应满足公司要求。
考核指标包括服务响应速度、解决问题的能力等。
3.4 成本管理:供应商应合理控制成本,确保价格和费用的合理性。
考核指标包括商品价格、运输费用、售后服务成本等。
4. 考核周期和频率4.1 考核周期:供应商质量考核按季度进行,每个季度为一个考核周期。
4.2 考核频率:每个季度对所有供应商进行一次质量考核。
5. 考核方法5.1 数据收集:公司将收集供应商的相关数据,包括商品质量报告、交货准时情况、客户反馈等。
5.2 考核评分:根据考核指标对供应商进行评分,评分细则由公司根据实际情况制定。
5.3 绩效反馈:供应商将获得考核结果及评分反馈,公司将与供应商共同讨论改进措施,并制定改进计划。
6. 考核结果与处理6.1 考核结果:根据供应商的考核评分,公司将对供应商进行分类,分为合格、待改进和淘汰三类。
6.2 处理措施:针对不同分类的供应商,公司将采取相应的处理措施,包括奖励合格供应商、与待改进供应商制定改进计划、淘汰不合格供应商等。
7. 考核结果的监督和跟踪公司将对供应商的改进计划进行监督和跟踪,确保供应商的质量改进措施得到有效执行和落实。
8. 附则为了保障供应商质量考核的公平、公正,本规定在执行过程中应遵循公开透明、客观公正、严格执行的原则。
以上为供应商质量考核规定的主要内容,供相关部门和供应商参考和执行。
供应商质量评估与认证制度
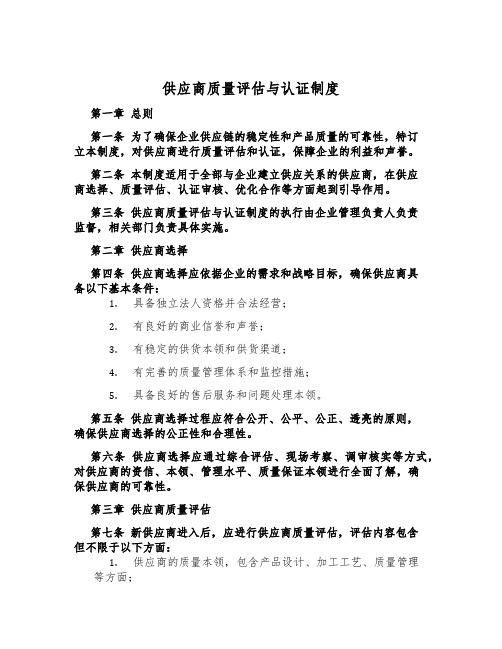
供应商质量评估与认证制度第一章总则第一条为了确保企业供应链的稳定性和产品质量的可靠性,特订立本制度,对供应商进行质量评估和认证,保障企业的利益和声誉。
第二条本制度适用于全部与企业建立供应关系的供应商,在供应商选择、质量评估、认证审核、优化合作等方面起到引导作用。
第三条供应商质量评估与认证制度的执行由企业管理负责人负责监督,相关部门负责具体实施。
第二章供应商选择第四条供应商选择应依据企业的需求和战略目标,确保供应商具备以下基本条件:1.具备独立法人资格并合法经营;2.有良好的商业信誉和声誉;3.有稳定的供货本领和供货渠道;4.有完善的质量管理体系和监控措施;5.具备良好的售后服务和问题处理本领。
第五条供应商选择过程应符合公开、公平、公正、透亮的原则,确保供应商选择的公正性和合理性。
第六条供应商选择应通过综合评估、现场考察、调审核实等方式,对供应商的资信、本领、管理水平、质量保证本领进行全面了解,确保供应商的可靠性。
第三章供应商质量评估第七条新供应商进入后,应进行供应商质量评估,评估内容包含但不限于以下方面:1.供应商的质量本领,包含产品设计、加工工艺、质量管理等方面;2.供应商的生产设备和技术水平,包含设备齐全程度、技术人员配备等方面;3.供应商的质量掌控管理体系,包含质量检测设备、质量文件、流程管理等方面;4.供应商的供货本领和供货稳定性,包含供货周期、交货按时率、库存管理等方面;5.供应商的售后服务和问题处理本领,包含产品质量问题的解决速度、售后服务支持等方面。
第八条供应商质量评估应设立评估小组,由各相关部门的专业人员构成,对供应商进行实地考察和数据收集,评估结果由评估小组汇总并形成评估报告。
第九条供应商质量评估结果分为优秀、合格、不合格三个等级,评估结果作为供应商绩效评价和后续合作决策的紧要依据。
第四章供应商认证审核第十条对已评估合格的供应商进行认证审核,确认其具备合作的本领和条件。
第十一条供应商认证审核由认证小组负责,由企业管理负责人组织,包含但不限于以下内容:1.对供应商的组织结构和管理体系进行审核,确认其质量管理体系的有效性和健全性;2.对供应商的生产设备进行审核,确认其设备的完善程度和技术水平;3.对供应商的质量管理流程进行审核,确认其质量管理流程的科学性和合理性;4.对供应商的质量掌控记录和文件进行审核,确认其质量记录的真实性和准确性。
供应商评价和再评价制度范文(3篇)

供应商评价和再评价制度范文评价部门:供应链管理部一、评价目的供应商评价和再评价制度的目的是为了确保与公司合作的供应商能够持续提供优质的产品和服务,以满足公司各部门的需求,并保证供应链的高效运作。
通过对供应商的评价和再评价,不断优化供应链管理,提高供应商的整体质量水平和服务水平,以促进公司的可持续发展。
二、评价范围评价范围包括所有与公司有业务往来的供应商,无论是直接供应材料和产品的一级供应商,还是间接供应支持材料和服务的二级供应商。
评价将涵盖供应商的质量管理体系、交货能力、服务质量、成本效益等方面。
三、评价方法1. 评价内容(1)质量管理体系评价:评估供应商是否具备完善的质量管理体系,并有效执行。
包括但不限于供应商是否有ISO9001等相关认证,是否有完善的质量管理流程和制度,是否有充足的技术力量和质量检测设备等。
(2)交货能力评价:评估供应商是否能够按时、足量地交货,并能够满足公司的要求。
评价内容包括供应商的生产能力、物流能力、仓储能力等。
(3)服务质量评价:评估供应商在售前、售中和售后服务方面的表现。
包括供应商的响应速度、技术支持能力、售后服务质量等。
(4)成本效益评价:综合评估供应商的价格水平与产品和服务的性价比,以确保公司获得合理的成本效益。
2. 评价周期(1)初次评价:对与公司新合作的供应商进行初次评价,以确定是否符合公司的要求,是否有资格为公司提供产品和服务。
初次评价将在与供应商签订合作协议之前进行。
(2)定期评价:对与公司有业务往来的供应商进行定期评价,周期为一年。
定期评价将对供应商的整体表现进行评估,以确定是否继续合作。
(3)不定期评价:对于供应商的严重质量问题或服务问题,以及公司内部发生重大变革时,将进行不定期评价,以确定是否需要对供应商进行再评价。
3. 评价指标(1)质量管理体系评价指标:包括认证情况、流程管理、技术力量、质量控制、不良率等。
(2)交货能力评价指标:包括交货准时率、交货完整率、交货及时性、仓储管理等。
供应商评价管理制度

供应商评价管理制度是企业日常运营中非常重要的一项工作。
通过评价供应商,可以确保企业获取高质量的原材料和产品,降低采购成本,提高产品质量,增强供应链稳定性。
本文将介绍供应商评价管理制度的概念、目的、内容和流程,并讨论如何建立和改进供应商评价管理制度。
一、概念和目的供应商评价管理制度是企业为了规范和提高供应商管理水平而制定的一系列规章制度和方法。
其目的是通过对供应商的定期评估和监控,筛选出合格的供应商,并为企业选择有竞争力的供应商提供依据。
同时,通过评价,企业可以及时发现供应商存在的问题,并采取相应的改进措施,确保企业供应链的稳定性和可靠性。
二、内容供应商评价管理制度主要包括以下内容:1. 评价指标:根据企业自身情况和业务特点,确定适合的评价指标,如供应商的交货准时率、产品质量、服务水平等。
2. 评价方法:制定评价的具体方法和步骤,如采用问卷调查、现场考察、产品抽检等方式进行评价。
3. 评价周期:确定评价的周期,例如每季度、半年度或年度进行一次评价。
4. 评价标准:制定评价的标准,如交货准时率达到90%以上为合格,产品质量合格率达到95%以上为合格等。
5. 结果处理:根据评价结果,对供应商进行分类管理,如合格供应商、待改进供应商、淘汰供应商等。
6. 改进措施:对于评价不合格的供应商,制定相应的改进措施,并跟踪改进的进展。
三、流程供应商评价管理制度的流程如下:1. 确定评价指标:企业根据业务特点和需求,确定适合的评价指标。
2. 收集评价数据:采用问卷调查、现场考察、产品抽检等方式,收集供应商的相关数据。
3. 分析评价数据:对收集到的数据进行分析和统计,得出评价结果。
4. 评估供应商:根据评价结果,对供应商进行评估和分类管理。
5. 制定改进计划:对于评价不合格的供应商,制定改进计划,并跟踪改进的进展。
6. 定期评估:根据评估周期,定期对供应商进行评估和监控。
7. 持续改进:根据评估结果和改进计划的执行情况,不断改进和完善评价管理制度。
食品供应商检查评价制度范本
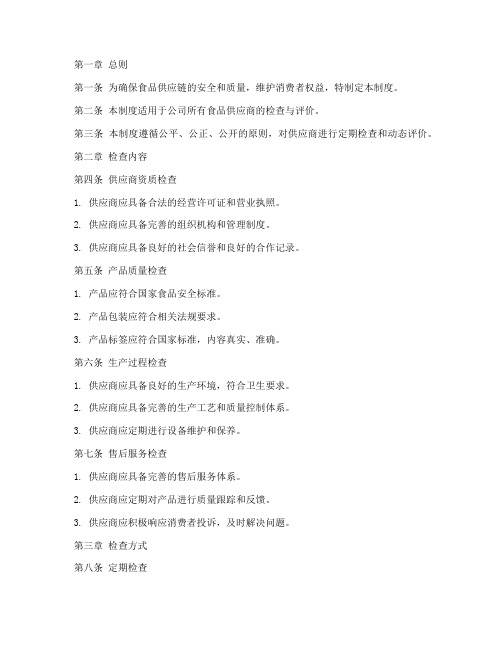
第一章总则第一条为确保食品供应链的安全和质量,维护消费者权益,特制定本制度。
第二条本制度适用于公司所有食品供应商的检查与评价。
第三条本制度遵循公平、公正、公开的原则,对供应商进行定期检查和动态评价。
第二章检查内容第四条供应商资质检查1. 供应商应具备合法的经营许可证和营业执照。
2. 供应商应具备完善的组织机构和管理制度。
3. 供应商应具备良好的社会信誉和良好的合作记录。
第五条产品质量检查1. 产品应符合国家食品安全标准。
2. 产品包装应符合相关法规要求。
3. 产品标签应符合国家标准,内容真实、准确。
第六条生产过程检查1. 供应商应具备良好的生产环境,符合卫生要求。
2. 供应商应具备完善的生产工艺和质量控制体系。
3. 供应商应定期进行设备维护和保养。
第七条售后服务检查1. 供应商应具备完善的售后服务体系。
2. 供应商应定期对产品进行质量跟踪和反馈。
3. 供应商应积极响应消费者投诉,及时解决问题。
第三章检查方式第八条定期检查1. 公司每年对供应商进行一次全面检查。
2. 供应商发生重大质量事故或投诉时,应立即进行检查。
第九条随机抽查1. 公司每月对供应商进行一次随机抽查。
2. 检查内容包括产品质量、生产环境、售后服务等方面。
第四章评价标准第十条供应商得分1. 供应商得分由资质检查、产品质量检查、生产过程检查和售后服务检查四部分组成。
2. 每部分满分为100分,总分满分为400分。
第十一条评价等级1. 供应商得分90分(含)以上为优秀供应商。
2. 供应商得分80分(含)至89分为良好供应商。
3. 供应商得分60分(含)至79分为合格供应商。
4. 供应商得分60分以下为不合格供应商。
第五章管理与监督第十二条公司设立食品供应商检查评价小组,负责实施本制度。
第十三条检查评价小组定期召开会议,分析供应商检查评价结果,对不合格供应商提出整改要求。
第十四条公司对供应商检查评价结果进行公示,接受各方监督。
第六章附则第十五条本制度自发布之日起施行,由公司负责解释。
供应商质量体系评估管理制度
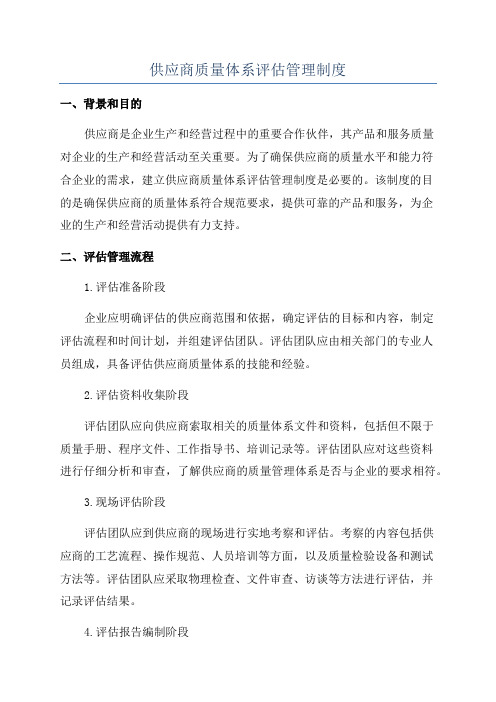
供应商质量体系评估管理制度一、背景和目的供应商是企业生产和经营过程中的重要合作伙伴,其产品和服务质量对企业的生产和经营活动至关重要。
为了确保供应商的质量水平和能力符合企业的需求,建立供应商质量体系评估管理制度是必要的。
该制度的目的是确保供应商的质量体系符合规范要求,提供可靠的产品和服务,为企业的生产和经营活动提供有力支持。
二、评估管理流程1.评估准备阶段企业应明确评估的供应商范围和依据,确定评估的目标和内容,制定评估流程和时间计划,并组建评估团队。
评估团队应由相关部门的专业人员组成,具备评估供应商质量体系的技能和经验。
2.评估资料收集阶段评估团队应向供应商索取相关的质量体系文件和资料,包括但不限于质量手册、程序文件、工作指导书、培训记录等。
评估团队应对这些资料进行仔细分析和审查,了解供应商的质量管理体系是否与企业的要求相符。
3.现场评估阶段评估团队应到供应商的现场进行实地考察和评估。
考察的内容包括供应商的工艺流程、操作规范、人员培训等方面,以及质量检验设备和测试方法等。
评估团队应采取物理检查、文件审查、访谈等方法进行评估,并记录评估结果。
4.评估报告编制阶段评估团队应根据评估结果编写评估报告,报告内容应包括供应商的优点和不足之处,并提供改进建议。
评估报告应由相关部门的主管审核,并在一定的时间内通报给供应商。
5.改进跟踪反馈阶段评估团队应与供应商共同制定改进计划,并定期跟踪和评估改进的效果,及时调整和完善供应商的质量体系。
评估团队应与供应商保持良好的沟通和合作关系,建立长期的合作伙伴关系。
三、评估标准和指标评估标准和指标应根据企业的需求和行业的特点进行制定,可以参考相关的国家和行业标准。
评估标准和指标应包括但不限于以下几个方面:1.管理体系评估供应商的质量管理体系是否完善,是否符合国家和行业的要求。
2.产品质量评估供应商的产品质量控制能力,包括原材料的采购、生产过程的控制、成品的检验等。
3.交付能力评估供应商的交付能力,包括交货时间的准确性和交货数量的准确性。
供应商质量评价及合格供方管理规章制度细则
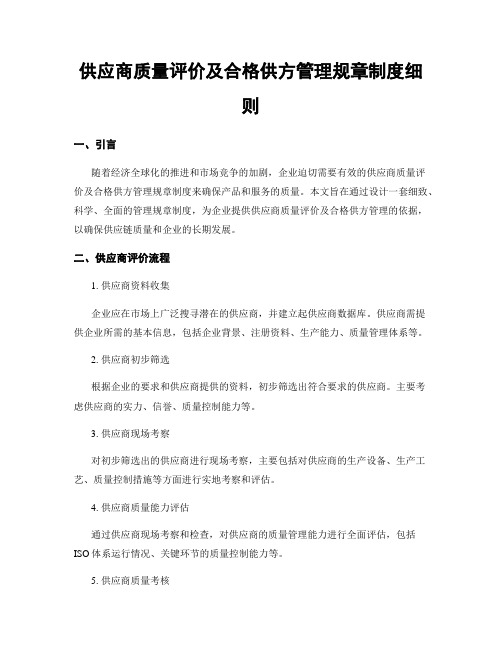
供应商质量评价及合格供方管理规章制度细则一、引言随着经济全球化的推进和市场竞争的加剧,企业迫切需要有效的供应商质量评价及合格供方管理规章制度来确保产品和服务的质量。
本文旨在通过设计一套细致、科学、全面的管理规章制度,为企业提供供应商质量评价及合格供方管理的依据,以确保供应链质量和企业的长期发展。
二、供应商评价流程1. 供应商资料收集企业应在市场上广泛搜寻潜在的供应商,并建立起供应商数据库。
供应商需提供企业所需的基本信息,包括企业背景、注册资料、生产能力、质量管理体系等。
2. 供应商初步筛选根据企业的要求和供应商提供的资料,初步筛选出符合要求的供应商。
主要考虑供应商的实力、信誉、质量控制能力等。
3. 供应商现场考察对初步筛选出的供应商进行现场考察,主要包括对供应商的生产设备、生产工艺、质量控制措施等方面进行实地考察和评估。
4. 供应商质量能力评估通过供应商现场考察和检查,对供应商的质量管理能力进行全面评估,包括ISO体系运行情况、关键环节的质量控制能力等。
5. 供应商质量考核建立科学的供应商质量考核体系,对供应商的交货及时性、产品质量、售后服务等方面进行定期考核,评估供应商的综合质量表现。
三、合格供方管理规范1. 合同签订与合格供方签订合同,并确保合同的合法性和有效性。
合同中明确约定产品规格、质量要求、售后服务等内容,以确保供方的责任和义务。
2. 定期审核和监督定期对合格供方进行审核和监督,检查供方是否按照合同的要求进行生产和质量控制,及时发现并解决问题。
3. 不合格供方的处理对于经过多次审核仍不能达到合格标准的供方,企业应考虑终止合作关系,并寻找替代供应商,以确保产品和服务的质量。
4. 合格供方奖励机制建立合格供方奖励机制,对表现优秀的供应商给予奖励和激励,以激发供应商的积极性和持续改进的动力。
四、问题与建议在供应商质量评价及合格供方管理过程中,可能会遇到一些问题。
为此,建议企业应积极解决以下问题:1. 信息不对称问题供应商所提供的信息可能存在虚假、夸大等情况,企业应通过严格的审核和考核程序,加强对供应商的调查和验证,降低信息不对称的风险。
供应商评价和再评价制度范文(三篇)

供应商评价和再评价制度范文一、制度目的及依据供应商评价和再评价制度的目的在于确保供应商的稳定性和可靠性,为企业的采购和供应链管理提供参考依据,保证供应商和企业的长期合作关系,并促进供应链的健康发展。
本制度以企业的采购管理政策为依据,结合供应商管理的实际情况制定。
二、制度适用范围本制度适用于所有与企业有合作关系的供应商,包括原材料、零部件、设备等供应商。
三、供应商评价标准1. 供应商的质量管理体系是否符合国家和行业相关标准和规定;2. 供应商的质量水平是否能满足企业的质量要求;3. 供应商的交货准时率和交货完成率是否稳定;4. 供应商的服务质量是否能满足企业的要求,包括售后服务和技术支持等;5. 供应商的价格水平是否合理;6. 供应商的信誉是否良好,是否有违法违规行为记录。
四、供应商评价流程1. 采购部门制定供应商评价计划,包括评价指标及权重;2. 采购部门收集供应商相关信息,包括材料、设备、产品质量证明等;3. 采购部门对供应商进行评价,分析供应商的质量水平、交货能力、服务质量等;4. 根据评价结果,采购部门将供应商分为A、B、C三个等级,并制定不同的管理措施;5. 采购部门将评价结果及供应商等级通知供应商,并召开供应商评价结果反馈会议;6. 供应商通过改进措施提升自身供应能力,以提高供应商等级。
五、供应商再评价制度1. 采购部门根据供应商的表现进行再评价,主要包括以下方面:(1)供应商的质量水平是否有提升;(2)供应商的交货准时率和交货完成率是否有改善;(3)供应商的服务质量是否有提升;(4)供应商的价格是否有调整;2. 采购部门将再评价结果通知供应商,并召开供应商再评价结果反馈会议;3. 供应商通过改进措施进一步提升供应能力,以获得更好的供应商等级。
六、供应商等级管理1. A类供应商:质量管理体系符合标准,质量水平满足要求,交货准时率和交货完成率高,服务质量好,价格合理,信誉良好;2. B类供应商:质量管理体系基本符合标准,质量水平基本满足要求,交货准时率和交货完成率一般,服务质量一般,价格较合理,信誉尚好;3. C类供应商:质量管理体系有待改进,质量水平不满足要求,交货准时率和交货完成率低,服务质量差,价格偏高,信誉较差;4. 采购部门将不同等级的供应商建立档案,并定期进行跟踪管理。
药企供应商质量评估制度
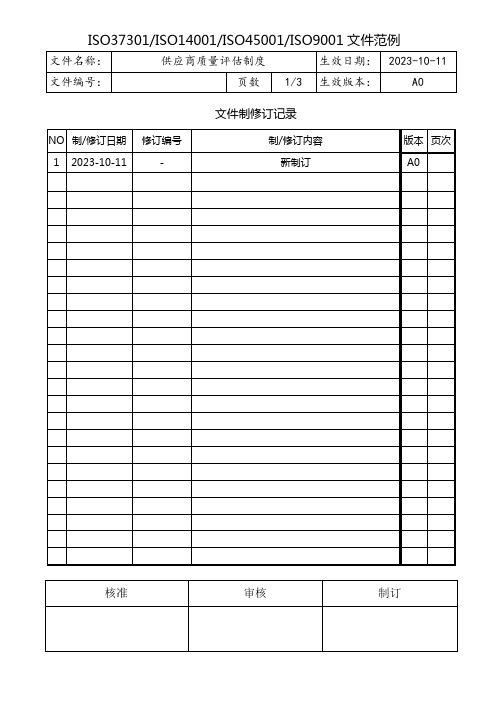
文件制修订记录一、目的:建立物料供应商质量评估制度,保证所采购物料的质量。
二、适用范围:适用于公司物料采购供应。
三、责任者:物料供应部、质控部。
四、正文:为了保证物料采购工作的顺利进行,确保物料的质量水平,必须对物料供货单位进行质量评估,这项工作由质控部、生产技术部和物料供应部共同完成。
供应商质量评估工作程序如下:1初步选择兽药生产所用的物料,应符合兽药各项标准,不得对兽药的质量产生不良影响,物料采购部门以企业起草的原辅料及包装材料标准作为寻求供货单位的依据,同时注意收集供货单位的质量标准及检验方法,以便进行比较和核对,再进一步了解供货单位的情况,并根据这些基本情况对供货单位进行初步选择。
2索样检验向初选合格的工厂索取小样,送质量管理部门检验。
同时,将本企业的质量标准交给对方,让对方按标准进行检验,看是否能够达到质量标准要求。
3质量审计小样检验合格后,初选过程中收集的资料又表明供货单位很可能成为本企业值得依赖的供应商时,质量管理部门会同供应部门按质量审计的要求对供货单位进行正式的调查,即质量审计。
3.1证照齐全,并且有主管部门批准的允许生产该产品的法律文件。
3.2厂房设施与设备能符合物料生产质量要求。
3.3其生产过程与质量保证体系完善。
3.4产品包装符合要求,质量安全,信誉良好。
3.5各种文件及记录规范、科学、合理。
3.6人员素质高,技术力量雄厚。
4工艺验证从质量审计结果满意的单位采购少量物料,生产技术部进行工艺验证,注意观察生产过程中可能出现的偏差,然后将成品与正常生产的产品进行对照检查,并比较结果。
物料采购部门从质量管理审计合格证的单位采购原辅料和包装材料。
4.1供货单位再审查供货单位的质量审查应定期进行,通常为1~2年审查一次。
当供货单位与产品质量有关的重要因素发生变动,有可能对本企业的产品造成影响时,可随时进行再审查。
4.2供货单位的更换每种物料均应选择2~3家质量审计合格的供货单位。
供应商确定后,一般不轻易更换,但如果对供货单位提供的物料出现两次以下的投诉或者市场变化有更合适的供货单位出现时,质量管理部门或物料采购部门可以提出更换供货单位的要求,中药饮片的产地要相对固定。
供应商评价制度

供应商评价制度目标这份文档的目标是建立一个供应商评价制度,以确保我们与供应商的合作始终保持高质量和高效率。
评价标准我们将使用以下标准评估供应商的绩效:1. 产品质量:供应商提供的产品应符合质量标准,并经过严格的测试和检查。
2. 交付准时度:供应商应按时交付产品,并确保供应链顺畅,避免延误。
3. 客户支持:供应商应提供良好的客户支持服务,快速响应问题,并积极解决任何潜在的问题。
4. 价格合理性:供应商的价格应与市场相符,并提供具有竞争力的报价。
5. 可靠性与稳定性:供应商应以可靠和稳定的方式提供产品,避免不可预见的供应中断。
评价过程供应商评价将包括以下步骤:1. 搜集数据:收集与供应商相关的数据,包括交付迟延、客户投诉和产品质量问题等。
这些数据将作为评估供应商绩效的依据。
2. 评估供应商:根据评价标准,对供应商的绩效进行评估,并给予相应的评分。
3. 反馈和改进:将评估结果与供应商分享,并提供改进意见。
供应商将有机会改进和纠正存在的问题。
4. 监督和复评:定期监督供应商的绩效,并进行复评。
如果供应商在复评中继续表现差,则将考虑终止合作关系。
评价结果基于供应商评估的结果,我们将采取相应的措施:1. 优秀供应商:对于具有优秀绩效的供应商,我们将加强与其的合作,并考虑增加订单或延长合作期限。
2. 合格供应商:对于达到合格水平的供应商,我们将继续合作,并提供必要的指导和反馈。
3. 不合格供应商:对于表现不佳的供应商,我们将采取纠正措施,并考虑中止合作关系。
复评和改进为了确保与供应商的持续合作,我们将定期进行复评,并向供应商提供改进意见。
供应商应针对我们提出的建议做出积极回应,并迅速采取必要的纠正措施。
结论供应商评价制度的建立旨在确保我们与供应商的合作始终保持高质量和高效率。
通过评估供应商的绩效,并采取适当的措施,我们将能够建立长期稳定的合作关系,并为客户提供优质产品和服务。
品质管理部门供应商质量评估与审核管理制度

品质管理部门供应商质量评估与审核管理制度一、引言在现代商业竞争中,供应商的选择和管理对于企业的发展和成功至关重要。
品质管理部门作为企业质量管理的重要组成部分,承担着供应商质量评估与审核的责任。
本文旨在介绍品质管理部门供应商质量评估与审核管理制度,以确保企业在供应链中获得高质量的产品和服务。
二、供应商质量评估的目的和原则为了确保供应链环节的可靠性和稳定性,品质管理部门对供应商的质量进行评估。
供应商质量评估的目的是验证供应商的质量管理能力和产品质量,以确保符合企业的要求和标准。
评估过程应遵守以下原则:1. 公正性:评估过程应公正、公平,不偏袒或歧视任何一家供应商。
2. 可靠性:评估结果应可靠,真实反映供应商的质量情况。
3. 系统性:评估应基于一套完整的质量评估体系,包括供应商文件审核、现场检查和样品测试等环节。
4. 动态性:供应商评估不应是一次性的,应定期进行,以确保评估结果的准确性和实时性。
三、供应商质量评估的实施流程供应商质量评估需要经过多个环节的审核和审查。
以下是供应商质量评估的实施流程:1. 提交材料:供应商需向品质管理部门提交相关材料,包括企业资质证书、产品质量认证证书等。
2. 文件审核:品质管理部门对供应商提交的文件进行审核,核查其合法性和真实性。
3. 现场检查:品质管理部门对供应商的生产现场进行实地检查,包括设备状况、生产流程和质量控制等。
4. 样品测试:品质管理部门对供应商提供的样品进行质量测试,以验证产品的合格性。
5. 反馈评估结果:品质管理部门根据评估结果向供应商提供反馈,包括评估等级和存在的问题。
6. 支持改进:如果供应商存在质量问题,品质管理部门将提供支持和指导,帮助供应商改进其质量管理体系和生产流程。
四、供应商质量审核的频率和标准供应商质量审核应定期进行,以确保供应商的质量管理能力和产品质量与企业要求相匹配。
审核频率和标准应根据供应商的重要性和过往表现进行确定。
1. 高风险供应商:对于那些在过去出现过质量问题或有较高质量风险的供应商,审核频率应更为频繁。
供应商质量评价制度

供应商质量评价制度供应商质量评价制度是指企业根据供应商的质量管理体系、产品质量、服务质量等方面的综合表现,对其进行评价和排名,并根据评价结果制定相应的管理措施和奖惩机制的一项制度。
这个制度的建立,旨在确保企业的商品或服务在供应链中的质量有所保障,以提高企业整体的竞争力和市场地位。
以下是一个关于供应商质量评价制度的详细介绍。
一、评价指标1.质量管理体系评价:评估供应商的质量管理体系是否完善、规范,并且是否取得了相关认证,如ISO9001等。
2.产品质量评价:对供应商所提供的产品进行全方位的质量评估,包括产品的设计、材料选用、加工工艺等方面。
3.交货时间评价:评估供应商的交货准确性和及时性,以保证企业生产计划的顺利进行。
二、评价方法1.定期评价:按照一定的评价周期,对供应商进行定期评价,如每半年或每年一次。
评价内容可以包括供应商的质量管理体系、产品质量、交货时间、服务水平等方面。
2.问题反馈:通过与供应商的密切沟通,获取并及时反馈问题和意见,并要求供应商采取具体的改进措施。
3.现场考察:不定期对供应商进行现场考察,了解其质量管理体系的具体运行情况,同时对其产品、仓储条件、生产设备等进行实地检查。
4.数据分析:根据供应商提供的相关数据和企业的实际情况,进行数据分析,以评估和排名供应商。
三、评价结果1.评级排名:根据各项评价指标的得分和权重,对供应商进行评级排名,将供应商分为A、B、C等等级,并根据评级结果确定相应的管理措施。
2.奖惩机制:根据供应商的得分,对各级供应商进行奖励和惩罚,并与供应商签订相应的协议和合同,明确奖惩措施。
3.合作发展:与评级较高的供应商建立长期合作关系,共同发展。
四、管理措施1.低分供应商淘汰:对评级为C级或得分较低的供应商,加强督促、督察和考核,若仍不能达到要求,则取消合作。
2.支持和培训:针对评级为B级或得分中等的供应商,加强支持和培训,提升其质量和服务水平。
3.奖励和合作:对评级为A级或得分较高的供应商,给予奖励和合作机会,共同发展。
供应商评价和再评价制度(5篇)
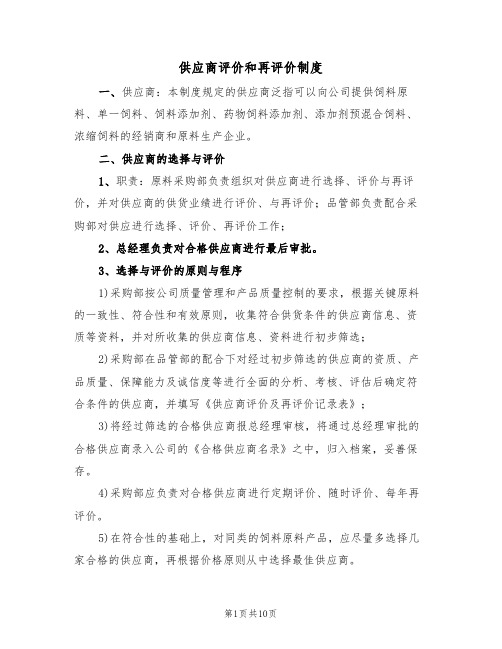
供应商评价和再评价制度一、供应商:本制度规定的供应商泛指可以向公司提供饲料原料、单一饲料、饲料添加剂、药物饲料添加剂、添加剂预混合饲料、浓缩饲料的经销商和原料生产企业。
二、供应商的选择与评价1、职责:原料采购部负责组织对供应商进行选择、评价与再评价,并对供应商的供货业绩进行评价、与再评价;品管部负责配合采购部对供应进行选择、评价、再评价工作;2、总经理负责对合格供应商进行最后审批。
3、选择与评价的原则与程序1)采购部按公司质量管理和产品质量控制的要求,根据关键原料的一致性、符合性和有效原则,收集符合供货条件的供应商信息、资质等资料,并对所收集的供应商信息、资料进行初步筛选;2)采购部在品管部的配合下对经过初步筛选的供应商的资质、产品质量、保障能力及诚信度等进行全面的分析、考核、评估后确定符合条件的供应商,并填写《供应商评价及再评价记录表》;3)将经过筛选的合格供应商报总经理审核,将通过总经理审批的合格供应商录入公司的《合格供应商名录》之中,归入档案,妥善保存。
4)采购部应负责对合格供应商进行定期评价、随时评价、每年再评价。
5)在符合性的基础上,对同类的饲料原料产品,应尽量多选择几家合格的供应商,再根据价格原则从中选择最佳供应商。
三、对供应商的评价频次1、定期评价:公司每半年对合格供应商要进行定期评价;2、随时评价:对新人选供应商或已经入选但供应的原料质量不够稳定、或信誉、能力一般的供应商应该随时进行评价;3、年度再评价:公司每年年底对合格供应商进行一次再评价,对供应能力、质量信誉较差的供应商坚决剔除。
四、供应评价原则评价供应商主要针对其资质、诚信、产品质量、保障能力等;对影响程度不同的采购产品可采取不同的评价准则;公司在评价供应商时应全面考虑以下因素:1、供应商的产品中质量、价格、后续服务、历史业绩等;2、供应商的诚信度、保障能力;3、来自外部方面的信息(如同行的评价、主管部门的推荐、第三方认证等);4、满足规范要求的:营业执照、生产许可、产品检验报告等;5、若涉及采购产品中有强制性认证的,还应有认证的证书和质量证明等。
供应商分级评价制度模板

供应商分级评价制度模板一、目的为了优化供应商结构,规范供应商日常管理,提高产品质量,稳定供应商队伍,建立长期互惠供求关系,对供应商进行评估分级,特制定本制度。
二、适用范围1、本制度适用于经商品销售部审核并登记备案的供应商。
2、集团所属企业均可参照执行。
三、评价指标1、资质评定:包括供应商的营业执照、税务登记证、组织机构代码证等相关证件的齐全性。
2、合作情况评定:包括供应商的交货准时率、产品质量合格率、售后服务满意度等。
四、评价方法1、资质评定:对供应商的证件进行审核,确保其合法有效。
2、合作情况评定:采用量化评分方式,根据供应商的交货准时率、产品质量合格率、售后服务满意度等指标进行评估。
五、评价周期1、新进供应商:在合作前进行一次评价。
2、已合作供应商:每半年进行一次评价。
六、分级标准1、战略供应商:合作双方通过建立共同的利益机制,并在合作过程中能够起到整合行业的供应链的作用。
优化资源配置、增强彼此竞争优势、降低运行风险及成本,建立长期的相互学习、相互支持、共同发展的战略联盟关系。
2、重点供应商:供应商提供的产品或服务对于公司具有一定的重要性和独特性,双方具备长期合作的业务基础或长远合作的发展愿景。
在业务范围、产品质量、成本、服务、资源优化等方面需双方协同发展,逐步实现稳定的业务关系。
3、常规供应商:供应商处于市场充分竞争的行业中,采购物资的获取难度较小。
在实施程序化采购的过程中,重点评价成本、质量、供货保障、改善提升能力等绩效指标,择优选择合作供应商。
4、一般交易供应商:采取短期或订单合作方式达成的简单交易模式,满足采购业务需求的合作关系。
七、供应商分级管理1、根据评价结果,将供应商分为战略供应商、重点供应商、常规供应商和一般交易供应商。
2、针对不同级别的供应商,制定不同的采购策略和管理措施,确保供应商关系的稳定性和合作关系的长久性。
八、激励与惩罚1、对于评价优秀的供应商,给予一定的奖励,如优惠政策、订单增加等。
食材供应商质量评估管理制度
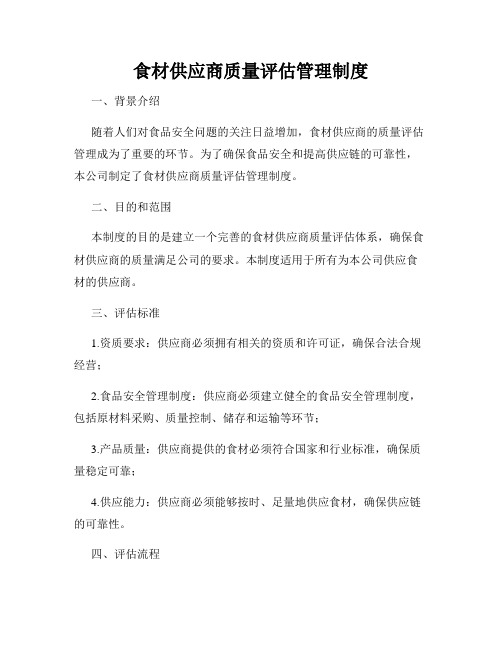
食材供应商质量评估管理制度一、背景介绍随着人们对食品安全问题的关注日益增加,食材供应商的质量评估管理成为了重要的环节。
为了确保食品安全和提高供应链的可靠性,本公司制定了食材供应商质量评估管理制度。
二、目的和范围本制度的目的是建立一个完善的食材供应商质量评估体系,确保食材供应商的质量满足公司的要求。
本制度适用于所有为本公司供应食材的供应商。
三、评估标准1.资质要求:供应商必须拥有相关的资质和许可证,确保合法合规经营;2.食品安全管理制度:供应商必须建立健全的食品安全管理制度,包括原材料采购、质量控制、储存和运输等环节;3.产品质量:供应商提供的食材必须符合国家和行业标准,确保质量稳定可靠;4.供应能力:供应商必须能够按时、足量地供应食材,确保供应链的可靠性。
四、评估流程1.供应商申请:供应商向本公司提交供应申请,并提供相关资质证明文件;2.初步评估:本公司对供应商进行初步评估,包括资质审核、现场考察等;3.签订合同:初步评估合格的供应商与本公司签订供应合同;4.正式评估:供应商按照约定的周期提供食材,并接受本公司的定期评估;5.评估结果:根据评估结果,本公司将供应商分为优秀、合格和不合格三个等级,以便后续管理和优化供应链;6.奖惩机制:对于评估等级为优秀的供应商,本公司将给予奖励;对于评估等级为不合格的供应商,本公司将采取相应的惩罚措施,甚至终止合作关系。
五、监督和整改本公司将建立监督机制,对供应商的食材质量进行随机抽检和监测,确保供应商在整个合作期间始终保持良好的质量水平。
若供应商出现质量问题,本公司将要求其进行整改,并进行相应的惩罚。
六、风险管理本公司将建立供应商风险管理制度,根据供应商的评估结果和质量情况,对风险供应商进行重点管理和监督。
七、培训和提升本公司将定期组织培训活动,提升供应商的食品安全意识和管理水平,促进供应商与本公司的共同成长。
八、制度的执行和修订本公司将确保制度的有效执行,并根据实际运行情况进行修订和优化,以不断提高供应商质量评估管理水平。
食堂供应商评价管理制度
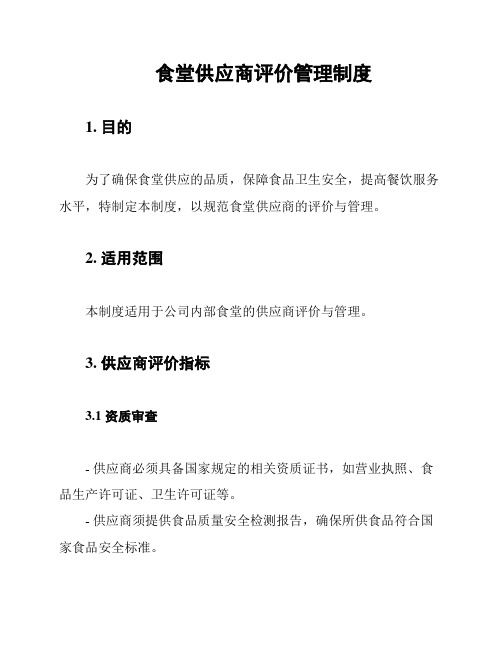
食堂供应商评价管理制度1. 目的为了确保食堂供应的品质,保障食品卫生安全,提高餐饮服务水平,特制定本制度,以规范食堂供应商的评价与管理。
2. 适用范围本制度适用于公司内部食堂的供应商评价与管理。
3. 供应商评价指标3.1 资质审查- 供应商必须具备国家规定的相关资质证书,如营业执照、食品生产许可证、卫生许可证等。
- 供应商须提供食品质量安全检测报告,确保所供食品符合国家食品安全标准。
3.2 质量控制- 供应商需提供稳定的产品质量,不得出现食品安全事故。
- 供应商应建立产品质量追溯体系,确保出现问题能迅速找到源头。
3.3 价格合理- 供应商提供的价格应具有竞争力,同时保证产品质量。
- 供应商需提供价格明细,以便于食堂进行成本控制。
3.4 服务满意度- 供应商需提供优质的售后服务,及时解决食堂在使用过程中遇到的问题。
- 供应商应定期与食堂沟通,了解食堂需求,持续改进服务质量。
3.5 交货信誉- 供应商需按照合同规定的时间、数量、质量提供货物。
- 供应商应具备一定的抗风险能力,确保在紧急情况下仍能稳定供应。
4. 供应商评价流程4.1 初选- 食堂根据供应商的资质、实力、价格等因素进行初步筛选。
- 对初选合格的供应商进行进一步的实地考察和综合评估。
4.2 评估- 食堂成立评估小组,对供应商进行综合评估,包括产品质量、服务、信誉等方面。
- 评估结果作为供应商筛选的重要依据。
4.3 签订合同- 根据评估结果,与合格供应商签订供应合同。
- 合同中应明确供应商的义务、责任以及违约处理办法。
4.4 定期考核- 食堂应定期对供应商进行考核,了解供应商的经营状况、产品质量等。
- 对考核不合格的供应商,食堂有权暂停或终止合同。
5. 保密条款- 供应商和食堂应签订保密协议,确保双方的商业秘密得到保护。
- 违反保密条款的供应商将承担相应的法律责任。
6. 附则- 本制度自发布之日起实施。
- 本制度的解释权归公司食堂所有。
7. 联系方式- 食堂联系人:XXX - 联系电话:XXX - 邮箱地址:XXX{content}。
供应商评价制度

供应商评价制度一、背景介绍随着供应链管理的发展,供应商评价制度逐渐成为企业进行供应商管理的重要工具。
供应商评价制度通过对供应商的能力、绩效和风险进行评估,帮助企业选取合适的供应商、优化供应链并确保供应链的稳定性和可持续发展。
二、评价指标体系1. 能力评价指标供应商的能力评价是评估供应商在核心业务和关键能力方面的表现。
包括但不限于:(1)供应商的技术能力:供应商的技术实力是否满足企业的需求,包括研发能力、产品质量等。
(2)供应商的生产能力:供应商的生产规模、生产线设备是否能够满足企业的需求,是否具备扩产能力等。
(3)供应商的供货能力:供应商的供货能力是否稳定,供货周期是否可控等。
2. 绩效评价指标供应商的绩效评价是评估供应商在合作过程中的表现。
包括但不限于:(1)供应商的交货准时率:供应商是否按时交货,是否存在延迟交货的情况。
(2)供应商的产品质量:供应商提供的产品是否符合企业的质量要求,是否存在质量问题。
(3)供应商的售后服务:供应商在售后服务方面的表现,包括及时响应、快速解决问题等。
3. 风险评价指标供应商的风险评价是评估供应商在供应链中潜在的风险情况。
包括但不限于:(1)供应商的财务状况:供应商的财务健康状况,是否存在债务风险或经营不善等情况。
(2)供应商的供应链风险:供应商在自身供应链中可能存在的风险,包括原材料供应不稳定、环境风险等。
(3)供应商的可持续性:供应商的发展前景和可持续发展策略,是否具备长期合作的基础。
三、评价方法与流程1. 数据收集企业可以通过内部数据、供应商提供的数据以及第三方数据等方式收集评价所需的数据。
2. 数据分析企业可以根据评价指标体系对收集到的数据进行分析,制定相应的评价标准和权重。
3. 评价结果反馈对供应商进行评价后,企业应当及时将评价结果反馈给供应商,并与供应商进行沟通和讨论。
4. 持续改进根据供应商的评价结果,企业应当与供应商共同制定改进措施,并进行跟踪和监督,持续改进供应商的能力和绩效。
- 1、下载文档前请自行甄别文档内容的完整性,平台不提供额外的编辑、内容补充、找答案等附加服务。
- 2、"仅部分预览"的文档,不可在线预览部分如存在完整性等问题,可反馈申请退款(可完整预览的文档不适用该条件!)。
- 3、如文档侵犯您的权益,请联系客服反馈,我们会尽快为您处理(人工客服工作时间:9:00-18:30)。
供应商质量评价标准1 目的:对供应商进行定期的质量评价,确定供应商质量等级,根据考评结果确定相应的管理和辅导对策,促进供应商品质改善,能够长期、稳定地供应公司要求的合格物料、适应公司的长期发展需要。
2 围:适合于主要原料供应商的质量评价过程。
3 职责:3.1品质部进货检验负责供应商的质量评价管理;3.2品质部过程检验和生产各车间负责原材料使用情况的收集和反馈。
4 工作程序:4.1总则:品质部对以下几个方面综合评价:进货品质、使用品质、品质改善、配合度;评价频次:按月度进行评价,季度/半年/年度按照月度平均进行评价。
评价对象:自动焊丝管、丝母、下排气帽、法兰盘、端盖(可根据情况适当调整)4.2月度评价标准:4.2.1进货品质(60分)4.2.1.1批退率(进货不合格批次/总进货批次*100%)(40分)A.当月质量得分=(1-批退率)*30分B.近期质量得分=(1-累计3月批退率)*10分4.2.1.2不良率(抽检不良数/抽检总数*100%)(10分)4.2.1.3出货检验报告(5分)要求供应商随货提交出货检验报告,每缺少1个批次扣2分,出货检验报告不符合要求每次扣2分,扣完为止。
4.2.1.4来料包装质量(5分)4.2.2使用品质(20分)4.2.2.1过程批不良(10分)在生产使用中,因原材料问题导致批量不良(一般外观缺陷>5%;严重外观缺陷、尺寸不良>3%;功能方面>2%),每出现一次过程投诉经确认批退的分别扣2、3、5分,扣完为止。
4.2.2.1月使用个例不良(10分)根据生产过程中出现的不良情况,对同类供应商进行排名,按照9,7,5,3,1计算得分。
4.2.3品质改善效果(10分)对反馈品质问题的改善情况跟踪验证,根据问题出现的频次和改善效果,给出评分。
4.2.4配合度(10分)4.2.4.1投诉处理配合度(7分)注:收到投诉报告或投诉1天,及时向投诉人沟通并经其同意延时回复的不纳入评分围。
4.2.4.2服务配合度(3分)对品质要求提供的其他资料(如材质报告等)或服务要求,不能如期提供的,每次扣1分,未提供的扣3分。
4.3质量评价等级提供改善措施并由品质在后续供货中监督。
2)D级发生一次时,一个月必须改善不良点;D级发生两次时,限期整改,予以警告;若连续三个月被评为D级,则取消该供应商资格。
4.3季度/半年/年度评价:取供应商月度平均值作为该供应商季度/半年/年度评分,评分=累计总得分/月数。
4.4来料质量异常及过程异常的反馈处理4.4.1 SCAR报告《Supplier Corrective Action Request Report》4.4.1.1发放条件:a)来料抽检时,功能不良超出AQL;b)来料抽检时,尺寸不良影响装配,并且不良率超过3%;c)来料抽检时,外观缺陷的不良率大于5%;d)生产线投诉时,与a)、b)、c)相同;e)客户投诉并要求书面回复时。
4.4.1.2 结案条件:a)来料连续3批无类似缺陷;b)一个月只有一批来料,且该批来料无类似缺陷或不良率有明显降低;c)一个半月无上货,其他同类产品无类似缺陷或不良率有明显降低;4.4.2 除4.4.1.1项之外发现的来料不良,可以通过或其它形式反馈给供应商改善、处理;4.5附表附表一《供应商品质改善通知单》附表二《来料不良改善通知单》附表三《供应商月度质量评价表》附表一供应商品质改善通知单附表二来料不良改善通知单3.6 来料质量异常的反馈及处理3.6.1 SCAR报告《Supplier Corrective Action Request Report》3.6.1.1发放条件:f)来料抽检时,功能不良超出AQL;g)来料抽检时,尺寸不良影响装配,并且不良率超过3%;h)来料抽检时,外观缺陷的不良率大于5%;i)生产线投诉时,与a)、b)、c)相同;j)客户投诉并要求书面回复时;3.6.1.2 结案条件:d)来料连续3批无类似缺陷;e)一个月只有一批来料,且该批来料无类似缺陷或不良率有明显降低;f)一个半月无上货,其他同类产品无类似缺陷或不良率有明显降低;3.6.2 除3.5.1.1项之外发现的来料不良,SQE都必须以或其它形式反馈给供应商改善、处理;• 5.1.3 考评标准• 5.1.3.1 现场质保体系等级考评本公司通过对供方现场审核,根据供方质保体系实际满足要求的程度,对附表1“供方评定评分表”中的项目,按标准逐项进行打分,并以得分高低按以下标准确定供方质保体系考评结论及等级:A级(合格):得分为90-100。
B级(合格):得分为80-89。
C级(合格需改进):得分为70-79。
D级(不合格):得分为70以下。
• 5.1.3.2 实物质量等级考评•A级(合格):经在本公司及供方现场实物质量抽查均无缺陷,且供方所供产品一次入库批次合格率为100%。
•B级(合格):经在本公司及供方现场实物质量抽查无缺陷,且供方所供产品一次入库批次合格率为98%以上。
•C级(合格需改进):经在本公司及供方现场实物质量抽查一般项存在缺陷且总项数小于2项(含),同时供方所供产品一次入库批次合格率为96%以上(含)。
•D级(不合格):经在本公司及供方现场实物质量抽查一般项存在缺陷且总项数大于2项,且供方所供产品一次入库批次合格率为96%以下。
• 5.1.3.3 供货业绩考评a. 供方交付产品的合格率(以本公司质量部的质量统计报表为准)在98%以上为合格,否则为不合格。
b. 供方产品交付及时率(以本公司采购部的供方供货业绩记录表为准)为100%者合格,否则不合格。
c. 供方服务到位率(以本公司发出的“质量问题信息反馈单”和要求供方前来处理质量问题或有关事宜的实现程度来评价)不低于95%者为合格,否则不合格。
• 5.1.3.4 综合考评为了更真实、客观、全面地反映供方的总体状况,分别从供方的质量保证能力、生产/交付能力、服务能力以及提供产品的价格水平等方面建立相应的供方综合评价指标,并根据各供方的实际供货情况,逐一予以评价打分,最后结合各指标重要度权数,得出其综合考评得分。
供方的综合考评得分由本公司采购部按季、按年予以统计,并及时向各供方通报。
其各评价指标的评价打分标准如下:A. 质量保证能力(得分围为0-100分;权数为0.35)a) 供方所供产品一次入库批次合格率×100作为得分基数。
b) 本公司生产过程中发现不合格,每次扣1分。
c) 供方事故(供方在交付产品时因延迟交付或交付后因质量问题造成本公司停产的)每发生一次扣5分。
d) 重复发生同类不合格问题的,每次扣2分。
B. 生产/交付能力(得分围为0-100分;权数为0.3)a) 供方产品交付及时率(以本公司采购部的供方供货业绩记录表为准)×100作为得分基数。
b) 供方事故(供方在交付产品时因延迟交付或交付后因质量问题造成本公司停产的)每发生一次扣5分。
c) 提供产品未按包装规包装的,每次扣3分。
C. 服务能力(得分围为0-100分;权数为0.15)a) 评价得分基数为100分。
b) 供方对本公司发出的“质量问题信息反馈单”,不能在规定的时间给予答复的,每次扣5分。
c) 因供方问题,未能及时到现场进行服务的或服务不解决问题的,每次扣5分。
D. 产品价格水平(得分围为80-100分;权数为0.2)a) 评价得分基数为100分。
b) 高于同行业同类产品市场平均价的为“偏高”,扣20分;c) 接近同行业同类产品市场平均价的为“平价”,扣10分;d) 低于同行业同类产品市场平均价的为“偏低”,不扣分。
E. 综合考评得分综合考评得分=质量保证能力评价得分×0.35+生产/交付能力评价得分×0.35+服务能力评价得分×0.15+产品价格水平评价得分×0.2• 5.2 供方年度奖惩• 5.2.1 奖惩原则• 5.2.1.1 为了更好地奖励先进、鞭策落后,自2004年开始,各供方需在本公司设立一定数额(按各供方年供货额大小和年度综合考评得分高低而定)的综合质量保证金。
• 5.2.1.2 供方在本公司设立的综合质量保证金,由本公司统一使用,并定期向各供方通报使用情况。
• 5.2.1.3 经各供方确认的各类质量损失赔偿款及本公司技术、质量和其他专业人员亲临供方现场的技术咨询、指导费,均在供方的综合质量保证金中列支,若综合质量保证金不足,则在本公司应付供方的货款中扣除。
• 5.2.1.4 经综合考评,被评为年度优秀供方的,本公司将给予一定的奖励,并在综合质量保证金中列支。
• 5.2.1.5 经综合考评,最终定为不合格的供方,本公司将没收该供方当年度的综合质量保证金。
若其质量赔偿额超过当年度综合质量保证金的,则在本公司应付该供方的货款中扣除。
• 5.2.2 奖惩标准• 5.2.2.1 经综合考评,评审合格的供方,将列入本公司合格分承包方名册。
• 5.2.2.2 经综合考评,评审不合格的供方,本公司给予拆点黄牌警告,且供方必须制定整改措施,并按本公司要求限期进行整改,整改措施需报本公司。
整改期间本公司暂停供方的供货。
限期整改仍不合格的,本公司有权中止与供方的供货关系。
• 5.2.2.3 经综合考评,供方质保体系考评等级和实物质量考评等级均为A级的供方,优先推荐为本公司当年度的优秀供方。
• 5.2.2.4 对过程控制好、产品质量稳定、服务到位、价格适宜、供货及时且质保体系考评等级和实物质量考评等级均为A级的供方,可评选为“优秀供方”,发给“优秀供方证书”,并在下年度给予以下奖励:a. 凡属两家配套的产品,优秀分供方所供产品份额可提升到60-80%。
b. 本公司应付该供方的货款可以根据规定的压款期减少一个月。
c. 本公司新产品开发时,该供方可享有优先研制和接受订单的待遇。
5.2.2.5 对于经综合考评,评审不合格且经限期整改后仍不合格的供方,本公司除没收其综合质量保证金外,将逐步予以淘汰,并重新选点。
. .. . 文章.。