精确成型技术 第四讲- 铸造工艺设计1
合集下载
《铸造工艺》PPT课件

1.拔长。使金属坯料的横截面积减少,长度增加的工序。如图 4.13所示,得到具有长轴线的锻件,如光轴、曲轴、台阶轴、拉杆、 连杆等。
2.镦粗。使金属坯料的横截面积增大,高度减小的工序。用来锻 齿轮坯、圆盘等;也可以作为环、套类空心件冲孔前的预备工序; 还可以增加拔长的锻造比。见图4.14。
第4章
• 4.1.4 铸件的质量检验与缺陷分析 • 常见铸件缺陷的特征及缺陷产生原因见下表:
第4章
第4章
第4章
• 4.2 特种铸造简介 • 特种铸造指有别于砂型铸造的其他铸造方法,如金属型铸造、熔模
铸造、离心铸造、压力铸造、磁型铸造等。
• 4.2.1 金属型铸造 • 将金属液浇入到金属铸型中,依靠重力作用而获得铸件的铸造方法
第4章
• 4.3 锻造 • 锻造是利用外力,通过工具或模具使金属材料发生塑性变形,获得
一定形状、尺寸和性能的毛坯或零件的加工方法。根据所用设备和 工具的不同,锻造分为自由锻造、模型锻造、胎模锻造和特种锻造 四类。与其他加工方法相比,锻造具有以下特点: • (1)改善金属的组织,提高力学性能。 • (2)生产率较高。 • (3)节省材料和加工工时。。 • (4)适用范围广。 • 锻造的不足之处是不能获得形状很复杂的锻件。 • 4.3.1 金属的锻造性能 • 金属的锻造性能是指金属材料锻造的难易程度。锻造性常用金属的 塑性和变形抗力来综合衡量。塑性越好,变形抗力越小,则金属的 锻造性越好;反之则差。 • 影响金属锻造性能的因素有以下几方面。 • 1.金属的化学成分和组织 • 一般纯金属及其固溶体的锻造性最好,化合物的锻造性最差。钢中 的Cr、W、Mo、V等碳化物形成元素,会降低锻造性,而S、Cu、 Sn、Pb等元素分布于晶界,也降低锻造性。铸态的粗晶结构比细 晶粒组织的锻造性差。
2.镦粗。使金属坯料的横截面积增大,高度减小的工序。用来锻 齿轮坯、圆盘等;也可以作为环、套类空心件冲孔前的预备工序; 还可以增加拔长的锻造比。见图4.14。
第4章
• 4.1.4 铸件的质量检验与缺陷分析 • 常见铸件缺陷的特征及缺陷产生原因见下表:
第4章
第4章
第4章
• 4.2 特种铸造简介 • 特种铸造指有别于砂型铸造的其他铸造方法,如金属型铸造、熔模
铸造、离心铸造、压力铸造、磁型铸造等。
• 4.2.1 金属型铸造 • 将金属液浇入到金属铸型中,依靠重力作用而获得铸件的铸造方法
第4章
• 4.3 锻造 • 锻造是利用外力,通过工具或模具使金属材料发生塑性变形,获得
一定形状、尺寸和性能的毛坯或零件的加工方法。根据所用设备和 工具的不同,锻造分为自由锻造、模型锻造、胎模锻造和特种锻造 四类。与其他加工方法相比,锻造具有以下特点: • (1)改善金属的组织,提高力学性能。 • (2)生产率较高。 • (3)节省材料和加工工时。。 • (4)适用范围广。 • 锻造的不足之处是不能获得形状很复杂的锻件。 • 4.3.1 金属的锻造性能 • 金属的锻造性能是指金属材料锻造的难易程度。锻造性常用金属的 塑性和变形抗力来综合衡量。塑性越好,变形抗力越小,则金属的 锻造性越好;反之则差。 • 影响金属锻造性能的因素有以下几方面。 • 1.金属的化学成分和组织 • 一般纯金属及其固溶体的锻造性最好,化合物的锻造性最差。钢中 的Cr、W、Mo、V等碳化物形成元素,会降低锻造性,而S、Cu、 Sn、Pb等元素分布于晶界,也降低锻造性。铸态的粗晶结构比细 晶粒组织的锻造性差。
铸造工艺学课程设计案例

提交格式
成果报告需以PDF格式提交,同时附上所有相关数据和图表。
报告内容
报告需包含设计思路、工艺流程、数据分析及结论等部分,要求 内容详实、逻辑清晰。
成果展示形式和内容安排建议
展示形式
鼓励采用多媒体形式进行展示,如PPT、视频等。
内容安排
建议按照设计背景、设计思路、工艺流程、数据 分析、结论与展望等顺序进行展示。
时间安排
每个小组展示时间不超过20分钟,需提前做好时 间规划。
课程设计评价标准及成绩评定方法
01
评价标准
将从设计创新性、实用性、技术 难度、报告质量等方面进行综合 评价。
02
成绩评定方法
03
优秀作品选拔
采用百分制评分,其中设计创新 性占30%、实用性占20%、技术 难度占20%、报告质量占30%。
铸造材料选择
根据零件使用要求、生产批量和成本 等因素,选择合适的铸造合金,如铸 铁、铸钢、铝合金等。
性能要求
铸造合金应具有良好的流动性、收缩 性、偏析倾向小等性能,以保证铸件 质量。同时,合金成分和性能应符合 相关标准或技术条件的规定。
03
案例分析:典型铸件生产工艺设计
铸件结构分析与设计优化建议
根据评分结果,选拔出优秀作品 进行表彰和奖励。
THANKS
感谢观看
推广新技术和新材料
积极推广先进的铸造技术和新材料,如3D打印技术、高性能铸造合 金等,提高铸件的精度和性能。
加强人才培养
加强铸造领域的人才培养和引进,提高从业人员的专业素质和技能水 平,为铸造行业的发展提供有力的人才保障。
06
课程设计成果展示与评价标准
课程设计成果提交要求说明
提交时间
所有成果需在课程结束前一周内提交,逾期将不予受理。
成果报告需以PDF格式提交,同时附上所有相关数据和图表。
报告内容
报告需包含设计思路、工艺流程、数据分析及结论等部分,要求 内容详实、逻辑清晰。
成果展示形式和内容安排建议
展示形式
鼓励采用多媒体形式进行展示,如PPT、视频等。
内容安排
建议按照设计背景、设计思路、工艺流程、数据 分析、结论与展望等顺序进行展示。
时间安排
每个小组展示时间不超过20分钟,需提前做好时 间规划。
课程设计评价标准及成绩评定方法
01
评价标准
将从设计创新性、实用性、技术 难度、报告质量等方面进行综合 评价。
02
成绩评定方法
03
优秀作品选拔
采用百分制评分,其中设计创新 性占30%、实用性占20%、技术 难度占20%、报告质量占30%。
铸造材料选择
根据零件使用要求、生产批量和成本 等因素,选择合适的铸造合金,如铸 铁、铸钢、铝合金等。
性能要求
铸造合金应具有良好的流动性、收缩 性、偏析倾向小等性能,以保证铸件 质量。同时,合金成分和性能应符合 相关标准或技术条件的规定。
03
案例分析:典型铸件生产工艺设计
铸件结构分析与设计优化建议
根据评分结果,选拔出优秀作品 进行表彰和奖励。
THANKS
感谢观看
推广新技术和新材料
积极推广先进的铸造技术和新材料,如3D打印技术、高性能铸造合 金等,提高铸件的精度和性能。
加强人才培养
加强铸造领域的人才培养和引进,提高从业人员的专业素质和技能水 平,为铸造行业的发展提供有力的人才保障。
06
课程设计成果展示与评价标准
课程设计成果提交要求说明
提交时间
所有成果需在课程结束前一周内提交,逾期将不予受理。
1铸造-铸造工艺基础.ppt-铸造

防止措施:
(1)铸件壁厚要尽量均匀,并使之
形状对称。 (2)尽量采用同时凝固原则。 (3)反变形法。 (4)时效处理。
三、铸件的裂纹与防止
1、热裂:高温下形成的裂纹。 形状特征:缝隙宽、形状曲折、缝内呈 氧化色。 主要影响因素: 合金性质 凝固时期受到阻碍
⑵ 冷裂:低温下形成的裂纹。 形状特征:裂纹细小、呈连续直线 状,有时缝内呈轻微氧化色。
灰铸铁、硅黄铜流
动性最好; 铸钢流动性最差。 影响合金流动性的 主要因素:化学成分
二、浇注条件
1、浇注温度 2、充型压力
三、铸型填充条件
1、铸型材料:导热系数、比热容
2、铸型温度
3、铸型中气体 4、铸件结构
第二节 铸件的凝固与收缩
一、铸件的凝固方式
逐层凝固方式:纯金属或共晶合金 糊状凝固方式:合金的结晶温度范围宽 中间凝固方式:介于上述二者之间。
三、铸件中的缩孔与缩松
1. 缩孔和缩松的形成
缩孔:集中在铸件上部或最后凝固部位容积较大的孔洞.
缩松:分散在铸件某区域内的细小缩孔。
宏观缩松 显微缩松
逐层凝固合金:缩孔倾向大; 糊状凝固合金:缩松倾向大。
2、 缩孔和缩松的防止
顺序凝固(定向凝固)原则: 在铸件上可能出现缩孔的厚 大部位通过安放冒口等工 艺措施,使铸件远离冒口 的部位先凝固,而后是靠 近冒口的部位凝固,最后 才是冒口本身的凝固。
⑴ 热应力:由于铸件
壁厚不均匀、各部分冷却速度 不同,以至在同一时期内铸件 各部分收缩不一致而引起的。
1杆:拉应力
2杆:压应力:
温 度 (℃) 浇口
同时凝固温度曲线铸件源自冷铁 ⅢⅠ Ⅱ 距离
铸件实现同时凝固示意图
精确成型技术 第四讲- 铸造工艺设计3

最小铸出孔槽
孔和槽尽量铸出,特别对于难加工的合 金材料。铸件上最小铸出孔和槽的尺寸,不 仅与其自身的尺寸大小有关,而且与孔所在 处壁厚有关。
铸件公差
GB/T 6414-1999《铸件尺寸公差与 机械加工余量》
非加工壁厚的负余量
在手工造型和造芯时,由于起模 敲动及木模因吸潮引起膨胀等原因, 使型腔尺寸扩大,为了保证铸件尺寸、 壁厚的准确性和避免铸件超重而采用 的负余量。
⑵在工艺说明中写出上、 侧、下字样,注明加工 余量数值。特殊要求的 加工余量可将数值标在 加工符号附近,凡带斜 度的加工余量应注明斜 度。
不铸出的孔和槽
用红色线打叉。
冒口
各种冒口都 用红色线表 示,注明斜 度和各尺寸, 并用序号1#、 2#区分。
补贴
用红色 线表示, 并注明 各部尺 寸。
工艺补正量
影响因数
⑴合金种类 ⑵铸造方法和生产批量 ⑶铸件大小和加工精度要求 ⑷浇注时加工面的位置
工艺补正量
3 2
2
1
补贴
1
工艺 余量
工艺补正量
为了防止铸件局部尺寸由于铸造收缩 率选用不当或其它工艺上的原因而超 差,在相应的非加工面上增厚的金属 层。
工艺补正量
工艺补正量
用工艺补正量保 证加工后的尺寸
铸造斜度(拔模斜度)
铸造工艺符号及表示方法
➢ 分型线 ➢ 分模面 ➢ 机械加工余量 ➢ 不铸出的孔和槽 ➢ 冒口
➢ 补贴 ➢ 工艺补正量 ➢ 砂芯冷铁 ➢ 浇注系统
分型线
用红色线表示,并用红色写出“上、中、 下”字样。
分模面
用红色线表 示,在任一 端画“<” 符号。
分型分模面
用红色线表示。
机械加工余量
铸造工艺课件

加工变形。防止铸件变形有以下几种方法: a) 采用反变形法 可在模样上做出与铸件变形量相等而方 向相反的预变形量来抵消铸件的变形,此种方法称为反变 形法。 b) 进行去应力退火 铸件机加工之前应先进行去应力退火, 以稳定铸件尺寸,降低切削加工变形程度。 c) 设置工艺肋 为了防止铸件的铸态变形,可在容易变形 的部位设置工艺肋。
(2)铸造应力的防止和消除措施 a)采用同时凝固的原则 同时凝固是指通过设置冷铁、布置浇口位置 等工艺措施,使铸件温差尽量变小,基本实现铸件各部分在同一时间 凝固。如图9-9所示。 b)提高铸型温度 c)改善铸型和型芯的退让性 d)进行去应力退火
图9-9 同时凝固原则
(3)铸件的变形和防止
铸件的变形包括铸件凝固后所发生的变形以及随后的切削
图9-8 定向凝固原则
b)合理确定铸件的浇注位置、内浇道位置及浇注工艺 浇 注位置的选择应服从定向凝固原则;内浇道应开设在铸件 的厚壁处或靠近冒口;要合理选择浇注温度和浇注速度,
在不增加其它缺陷的前提下,应尽量降低浇注温度和浇注 速度。
2. 铸造应力、变形和裂纹 在铸件的凝固以及以后的冷却过程中,随温度的不断降低,收缩 不断发生,如果这种收缩受到阻碍,就会在铸件内产生应力,引 起变形或开裂,这种缺陷的产生,将严重影响铸件的质量。 (1) 铸造应力的产生 铸造应力按其产生的原因可分为三种: a)热应力 铸件在凝固和冷却过程中,不同部位由于不均衡的收 缩而引起的应力。 b)固态相变应力 铸件由于固态相变,各部分体积发生不均衡变 化而引起的应力。 c)收缩应力 铸件在固态收缩时,因受到铸型、型芯、浇冒口、 箱挡等外力的阻碍而产生的应力。 铸件铸出后存在于铸件不同部位的内应力称为残留应力。
(二) 铸造合金的收缩
铸造合金从液态冷却到室温的过程中,其体积和尺寸缩减的现 象称为收缩。它主要包括以下三个阶段: 1.液态收缩 金属在液态时由于温度降低而发生的体积收缩。 2.凝固收缩 熔融金属在凝固阶段的体积收缩。液态收缩和凝固 收缩是铸件产生缩孔和缩松的基本原因。 3.固态收缩 金属在固态时由于温度降低而发生的体积收缩。固 态收缩对铸件的形状和尺寸精度影响很大,是铸造应力、变形 和裂纹等缺陷产生的基本原因。
(2)铸造应力的防止和消除措施 a)采用同时凝固的原则 同时凝固是指通过设置冷铁、布置浇口位置 等工艺措施,使铸件温差尽量变小,基本实现铸件各部分在同一时间 凝固。如图9-9所示。 b)提高铸型温度 c)改善铸型和型芯的退让性 d)进行去应力退火
图9-9 同时凝固原则
(3)铸件的变形和防止
铸件的变形包括铸件凝固后所发生的变形以及随后的切削
图9-8 定向凝固原则
b)合理确定铸件的浇注位置、内浇道位置及浇注工艺 浇 注位置的选择应服从定向凝固原则;内浇道应开设在铸件 的厚壁处或靠近冒口;要合理选择浇注温度和浇注速度,
在不增加其它缺陷的前提下,应尽量降低浇注温度和浇注 速度。
2. 铸造应力、变形和裂纹 在铸件的凝固以及以后的冷却过程中,随温度的不断降低,收缩 不断发生,如果这种收缩受到阻碍,就会在铸件内产生应力,引 起变形或开裂,这种缺陷的产生,将严重影响铸件的质量。 (1) 铸造应力的产生 铸造应力按其产生的原因可分为三种: a)热应力 铸件在凝固和冷却过程中,不同部位由于不均衡的收 缩而引起的应力。 b)固态相变应力 铸件由于固态相变,各部分体积发生不均衡变 化而引起的应力。 c)收缩应力 铸件在固态收缩时,因受到铸型、型芯、浇冒口、 箱挡等外力的阻碍而产生的应力。 铸件铸出后存在于铸件不同部位的内应力称为残留应力。
(二) 铸造合金的收缩
铸造合金从液态冷却到室温的过程中,其体积和尺寸缩减的现 象称为收缩。它主要包括以下三个阶段: 1.液态收缩 金属在液态时由于温度降低而发生的体积收缩。 2.凝固收缩 熔融金属在凝固阶段的体积收缩。液态收缩和凝固 收缩是铸件产生缩孔和缩松的基本原因。 3.固态收缩 金属在固态时由于温度降低而发生的体积收缩。固 态收缩对铸件的形状和尺寸精度影响很大,是铸造应力、变形 和裂纹等缺陷产生的基本原因。
教学课件:第四节铸造工艺设计

化。
数字化技术可以帮助设计师快速 准确地预测铸造过程中可能出现 的问题,提高设计效率和产品质
量。
数字化技术还可以实现远程协作 和在线评审,提高工作效率和降
低沟通成本。
环保材料的使用
随着环保意识的提高,铸造行 业开始广泛使用环保材料,如 再生材料、低铅材料等。
使用环保材料可以降低生产过 程中的污染排放,提高企业的 环保意识和社会责任感。
提高铸造工艺设计水平的建议
培养专业人才
加强铸造工艺设计人才的培养和引进,建 立完善的人才激励机制,提高设计人员的
专业素质和创新能力。
A 加强科技创新
鼓励企业加大科技研发投入,引进 先进技术和设备,提高铸造工艺的
技术水平和生产效率。
B
C
D
加强行业合作与交流
加强企业间的合作与交流,共同推动铸造 工艺设计的进步和发展,实现资源共享和 优势互补。
推进数字化转型
利用数字化技术实现铸造工艺设计的智能 化和精细化,提高设计效率和产品质量。
THANKS
感谢观看
考虑浇注系统的排渣和排气性 能,以避免铸造缺陷的产生。
对浇注系统进行优化设计,降 低金属液的消耗和能源件的结构和工艺要求,合理设 置冒口的位置和大小。
考虑冒口和出气孔的散热性能,以避 免铸件产生缩孔和裂纹等缺陷。
设计出气孔的位置和大小,以确保金 属液在充型过程中能够顺利排出气体。
铸造工艺设计的流程
确定浇注系统
设计合理的浇注系统,确保金 属液能够平稳、均匀地流入型
腔。
确定冒口和冷铁
根据铸件的要求和铸造方法, 设计合适的冒口和冷铁,控制 铸件的冷却速度和补缩效果。
确定工艺参数
根据铸件的要求和生产条件,选 择合适的工艺参数,如金属液的 成分、浇注温度、浇注速度等。
数字化技术可以帮助设计师快速 准确地预测铸造过程中可能出现 的问题,提高设计效率和产品质
量。
数字化技术还可以实现远程协作 和在线评审,提高工作效率和降
低沟通成本。
环保材料的使用
随着环保意识的提高,铸造行 业开始广泛使用环保材料,如 再生材料、低铅材料等。
使用环保材料可以降低生产过 程中的污染排放,提高企业的 环保意识和社会责任感。
提高铸造工艺设计水平的建议
培养专业人才
加强铸造工艺设计人才的培养和引进,建 立完善的人才激励机制,提高设计人员的
专业素质和创新能力。
A 加强科技创新
鼓励企业加大科技研发投入,引进 先进技术和设备,提高铸造工艺的
技术水平和生产效率。
B
C
D
加强行业合作与交流
加强企业间的合作与交流,共同推动铸造 工艺设计的进步和发展,实现资源共享和 优势互补。
推进数字化转型
利用数字化技术实现铸造工艺设计的智能 化和精细化,提高设计效率和产品质量。
THANKS
感谢观看
考虑浇注系统的排渣和排气性 能,以避免铸造缺陷的产生。
对浇注系统进行优化设计,降 低金属液的消耗和能源件的结构和工艺要求,合理设 置冒口的位置和大小。
考虑冒口和出气孔的散热性能,以避 免铸件产生缩孔和裂纹等缺陷。
设计出气孔的位置和大小,以确保金 属液在充型过程中能够顺利排出气体。
铸造工艺设计的流程
确定浇注系统
设计合理的浇注系统,确保金 属液能够平稳、均匀地流入型
腔。
确定冒口和冷铁
根据铸件的要求和铸造方法, 设计合适的冒口和冷铁,控制 铸件的冷却速度和补缩效果。
确定工艺参数
根据铸件的要求和生产条件,选 择合适的工艺参数,如金属液的 成分、浇注温度、浇注速度等。
最新1.3铸造工艺设计课件教学讲义ppt
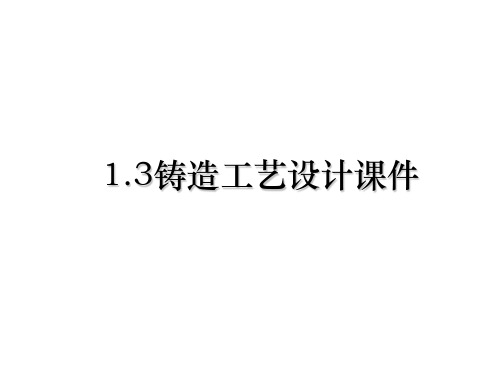
✓指合金液能充满型腔的最小厚度,小于最小壁 厚易产生浇不足、冷隔等缺陷。
✓铸件最小壁厚与 合金种类、铸件尺 寸等因素有关。
19
1.3 铸造工艺设计 铸件壁厚不易过厚 ✓ 过大的壁厚会引起铸件晶粒粗大,强度下降,
产生缩孔、缩松等缺陷
20
1.3 铸造工艺设计 ➢2、铸件壁厚尽量均匀 ✓壁厚不均易产生缩孔和缩松,内应力和变形、开 裂等缺陷。
30
1.3 铸造工艺设计
❖ 浇注位置选择原则 ➢ 重要面朝下 ➢ 大平面朝下 ➢ 薄壁部分置于铸型下部或使其处于垂直或 倾斜位置 ➢ 厚大部分朝上或侧面 ➢ 型芯少而稳定
31
1.3 铸造工艺设计 ➢ 重要面朝下 ✓ 铸件上部易产生砂眼、气孔、夹渣等缺陷,且晶
粒较粗大。重要加工面应朝下或位于侧面;重要 加工面有数个时,应将较大的平面朝下。
➢ 选择浇注系统类型。 ➢ 确定内交道在铸件上的位置、数目和金属液引入方
向。 ➢ 决定直浇道的位置和高度。 ➢ 计算浇注时间并核算金属上升速度。 ➢ 计算阻流截面积S阻。 ➢ 确定浇口比并计算各组员截面积。 ➢ 绘出浇注系统图。
42
1.3 铸造工艺设计 2.铸件分型面的选择 ✓ 指上、下、左、右砂型间的接触面,应能在保
简化内腔自带型芯
13
1.3 铸造工艺设计
框形与肋板结构
肋板与框架立体图
14
✓ 型芯在铸型中应支撑牢固
1.3 铸造工艺设计
内腔是否连通立体图 内腔连通不连通零件图
内腔连通不连通型芯放置
15
1.3 铸造工艺设计
✓ 增加型芯头或工艺孔,以固定型芯,同时便于 型芯固排清
封闭内腔立体图
封闭内腔零件图 封闭内腔型芯无法取出
➢ 浇口杯 ➢ 直浇道 ➢ 横浇道 ➢ 内浇道
✓铸件最小壁厚与 合金种类、铸件尺 寸等因素有关。
19
1.3 铸造工艺设计 铸件壁厚不易过厚 ✓ 过大的壁厚会引起铸件晶粒粗大,强度下降,
产生缩孔、缩松等缺陷
20
1.3 铸造工艺设计 ➢2、铸件壁厚尽量均匀 ✓壁厚不均易产生缩孔和缩松,内应力和变形、开 裂等缺陷。
30
1.3 铸造工艺设计
❖ 浇注位置选择原则 ➢ 重要面朝下 ➢ 大平面朝下 ➢ 薄壁部分置于铸型下部或使其处于垂直或 倾斜位置 ➢ 厚大部分朝上或侧面 ➢ 型芯少而稳定
31
1.3 铸造工艺设计 ➢ 重要面朝下 ✓ 铸件上部易产生砂眼、气孔、夹渣等缺陷,且晶
粒较粗大。重要加工面应朝下或位于侧面;重要 加工面有数个时,应将较大的平面朝下。
➢ 选择浇注系统类型。 ➢ 确定内交道在铸件上的位置、数目和金属液引入方
向。 ➢ 决定直浇道的位置和高度。 ➢ 计算浇注时间并核算金属上升速度。 ➢ 计算阻流截面积S阻。 ➢ 确定浇口比并计算各组员截面积。 ➢ 绘出浇注系统图。
42
1.3 铸造工艺设计 2.铸件分型面的选择 ✓ 指上、下、左、右砂型间的接触面,应能在保
简化内腔自带型芯
13
1.3 铸造工艺设计
框形与肋板结构
肋板与框架立体图
14
✓ 型芯在铸型中应支撑牢固
1.3 铸造工艺设计
内腔是否连通立体图 内腔连通不连通零件图
内腔连通不连通型芯放置
15
1.3 铸造工艺设计
✓ 增加型芯头或工艺孔,以固定型芯,同时便于 型芯固排清
封闭内腔立体图
封闭内腔零件图 封闭内腔型芯无法取出
➢ 浇口杯 ➢ 直浇道 ➢ 横浇道 ➢ 内浇道
铸造工艺设计.正式版PPT文档

未延伸凸台
延伸凸台
如图 (a)所示的铸钢梁,由于受较大热应力,产生了变形,改成(b)工字截面后,虽然壁厚仍不均匀,但变形减小。
工等工序复杂化。分型面的选择应在保证铸件质 机械造型的铸件比手工造型的精度高,故加工余量要小些;
铸件上垂直于分型面的不加工表面,最好具有结构斜度,这样起模省力,铸件精度高。
首先要考虑这个零件有 几种可能的分型方案
方案Ⅰ 沿底版中心分型。轴孔 下芯方便,但底版上四个 凸台必须采用活块且铸件 在上、下箱各半。
轮形铸件在批量不大 的生产条件下,多采用三 箱造型;但在大批量生产 条件下,采用机器造型时, 需采用环状型芯。
避免使用活块
未延伸凸台
延伸凸台
如图(a)所示凸台均妨碍起模,必须采用活块或增
加型芯来克服。改成图(b)的结构避免了活块和砂芯,
起摸方便,简化造型。
机械加工余量---应根据生产批量、合金种类、铸件尺 寸、加工面的位置、浇注位置等确定。
最小铸出孔及槽---铸件的孔、槽是否铸出,应从工 艺、质量及经济上考虑。较大的孔、槽应当铸出, 以减少切削加工工时,节约金属材料,同时也可减 小铸件上的热节;孔、槽较小而壁较厚,则不易铸 出,直接加工。
实例分析
支座
方案Ⅱ 沿底面分型,铸件全部在 下箱,不会产生错箱,铸 件易清理。但轴孔内凸台 必须采用活块或下芯且轴 孔难以铸出。
床身铸件的分型方案
应尽量减少分型面的数量
铸件图所示的三通铸件 其内腔必须采用一个T字 型芯来形成;
当中心线ab呈垂直时, 铸型必须有三个分型面;
当中心线cd呈垂直时, 铸型有两个分型面,
当中心线ab与cd都呈水 平位置时,铸型只有一个 分型面。
分型面应尽量平直
相关主题
- 1、下载文档前请自行甄别文档内容的完整性,平台不提供额外的编辑、内容补充、找答案等附加服务。
- 2、"仅部分预览"的文档,不可在线预览部分如存在完整性等问题,可反馈申请退款(可完整预览的文档不适用该条件!)。
- 3、如文档侵犯您的权益,请联系客服反馈,我们会尽快为您处理(人工客服工作时间:9:00-18:30)。
➢ 为什么要规定铸件的最小厚度?灰铸铁 件的壁厚过大或局部过薄会出现哪些问 题?
➢ 铸件为何会产生变形和开裂,如何防止 变形和开裂?
(A a)
A 2 ; R a; r 0.1(A a) a
直 角 相 交 的 两 壁
A a ; c 3 A a, a c A, h 4c a
成
T
型
相
交
的 c 1.5 A a
三
a 2c A
壁
h 8c
c 3 Aa ac A
外圆角
上
上
下
下
不必要的圆角给生产带来困难
尽量少用砂芯
原结构
修改后 结构
以砂台代替砂芯
有利于砂芯的固定与排气
芯撑
1
2
整体砂 芯易于 固定和 排气
改变结构利于 固定和排气
芯撑
工艺凸台 及孔
加强筋
原结构
修改后 结构
利用加强筋减小铸件壁厚
利用铸造筋改善铸件充填条件
原 结 构
修 改 后
结
构
作业题
铸件的最小壁厚
砂型铸造的最小壁厚(mm)
铸件大小
小件 < 200×200mm 中件 200×200~ 500×500mm
大件 > 500×500mm
铸 灰铸 孕育 青 铝合 镁 钢 铁 铸铁 铜 金 合
金
4~5 3~5 2.5~4 2~3 2~3 3~4
10~ 12
15~ 20
8~10
12~ 15
6~8
10~ 12
5~7 4~6 4~6
10~ 8~10 8~
12
10
铸件的临界壁厚
➢临界壁厚指铸件一般容许的最大壁厚。厚壁铸 件容易产生缩孔、缩松、结晶组织粗大等缺 陷,从而使铸件的力学性能下降。
➢临界壁厚通常可按其最小壁厚的三倍来确定。 ➢最小壁厚和临界壁厚之间就是适宜的壁厚。
铸件的内壁厚
外壁铸件
《材料精确成形技术》 第四讲
铸造工艺设计
➢铸件结构设计 ➢造型工艺设计
铸件结构设计
➢铸件结构设计的合理性 ➢铸件结构的工艺性
铸件结构设计的合理性
➢ 合理设计铸件壁厚 ➢ 合理设计壁的连接与过渡 ➢ 采用结构圆角 ➢ 避免水平方向的大平面 ➢ 防止变形、裂纹等缺陷
铸件壁厚
三个方面要求:
➢保证铸件达到所需要的强度和刚度; ➢尽可能节约金属; ➢铸造时没有太大的困难。
h 4c
铸件的结构圆角
R (1 5
~
1 10)(T1 T2 )
避免水平方向的大平面
a) 存在薄的大平面, 不合理
b) 平面改成斜面, 合理
c) 结构不能变时,可 用倾斜铸型的方法进 行浇注
防止变形
利用 加强 筋防 止铸 件变 形
防止收缩受阻而产生裂纹
辐条
对 称 辐
设计 成弯 曲状
条
和 带
铸件内壁
铸件种类
铸件内壁厚度比外壁 的相对减少值(%)
铸钢 铸铁 铸铜 铸铝 铸镁
10~ 20~ 15~ 10~ 10~
20
30
20
20
20
壁的连接与过渡
均匀壁厚, 避免热节
改变连接壁的角度,防止形成尖砂
筋条错 开,防 止形成 大热节
厚壁与薄壁的过渡
铸件各部分的壁厚有一定的差 异时,壁的相互连接处一定要采取 渐变的方式,以防止出现变形、裂 纹等缺陷
应用 单数
辐条
铸件结构的工艺性
铸件结构不仅要求设计合理,而 且能容易地实现其铸造生产,这 就是铸件结构的工艺性。
铸件结构的工艺性要求
➢ 有利于简化铸造工艺 ➢ 减少不必要的外圆角 ➢ 尽量少用砂芯 ➢ 有利于砂芯的固定与排气 ➢ 合理设置加强筋
简化铸造工艺
外壁内凹的框形件
上 中
中
上
下
下
带不易起模凸台的铸件
➢ 铸件为何会产生变形和开裂,如何防止 变形和开裂?
(A a)
A 2 ; R a; r 0.1(A a) a
直 角 相 交 的 两 壁
A a ; c 3 A a, a c A, h 4c a
成
T
型
相
交
的 c 1.5 A a
三
a 2c A
壁
h 8c
c 3 Aa ac A
外圆角
上
上
下
下
不必要的圆角给生产带来困难
尽量少用砂芯
原结构
修改后 结构
以砂台代替砂芯
有利于砂芯的固定与排气
芯撑
1
2
整体砂 芯易于 固定和 排气
改变结构利于 固定和排气
芯撑
工艺凸台 及孔
加强筋
原结构
修改后 结构
利用加强筋减小铸件壁厚
利用铸造筋改善铸件充填条件
原 结 构
修 改 后
结
构
作业题
铸件的最小壁厚
砂型铸造的最小壁厚(mm)
铸件大小
小件 < 200×200mm 中件 200×200~ 500×500mm
大件 > 500×500mm
铸 灰铸 孕育 青 铝合 镁 钢 铁 铸铁 铜 金 合
金
4~5 3~5 2.5~4 2~3 2~3 3~4
10~ 12
15~ 20
8~10
12~ 15
6~8
10~ 12
5~7 4~6 4~6
10~ 8~10 8~
12
10
铸件的临界壁厚
➢临界壁厚指铸件一般容许的最大壁厚。厚壁铸 件容易产生缩孔、缩松、结晶组织粗大等缺 陷,从而使铸件的力学性能下降。
➢临界壁厚通常可按其最小壁厚的三倍来确定。 ➢最小壁厚和临界壁厚之间就是适宜的壁厚。
铸件的内壁厚
外壁铸件
《材料精确成形技术》 第四讲
铸造工艺设计
➢铸件结构设计 ➢造型工艺设计
铸件结构设计
➢铸件结构设计的合理性 ➢铸件结构的工艺性
铸件结构设计的合理性
➢ 合理设计铸件壁厚 ➢ 合理设计壁的连接与过渡 ➢ 采用结构圆角 ➢ 避免水平方向的大平面 ➢ 防止变形、裂纹等缺陷
铸件壁厚
三个方面要求:
➢保证铸件达到所需要的强度和刚度; ➢尽可能节约金属; ➢铸造时没有太大的困难。
h 4c
铸件的结构圆角
R (1 5
~
1 10)(T1 T2 )
避免水平方向的大平面
a) 存在薄的大平面, 不合理
b) 平面改成斜面, 合理
c) 结构不能变时,可 用倾斜铸型的方法进 行浇注
防止变形
利用 加强 筋防 止铸 件变 形
防止收缩受阻而产生裂纹
辐条
对 称 辐
设计 成弯 曲状
条
和 带
铸件内壁
铸件种类
铸件内壁厚度比外壁 的相对减少值(%)
铸钢 铸铁 铸铜 铸铝 铸镁
10~ 20~ 15~ 10~ 10~
20
30
20
20
20
壁的连接与过渡
均匀壁厚, 避免热节
改变连接壁的角度,防止形成尖砂
筋条错 开,防 止形成 大热节
厚壁与薄壁的过渡
铸件各部分的壁厚有一定的差 异时,壁的相互连接处一定要采取 渐变的方式,以防止出现变形、裂 纹等缺陷
应用 单数
辐条
铸件结构的工艺性
铸件结构不仅要求设计合理,而 且能容易地实现其铸造生产,这 就是铸件结构的工艺性。
铸件结构的工艺性要求
➢ 有利于简化铸造工艺 ➢ 减少不必要的外圆角 ➢ 尽量少用砂芯 ➢ 有利于砂芯的固定与排气 ➢ 合理设置加强筋
简化铸造工艺
外壁内凹的框形件
上 中
中
上
下
下
带不易起模凸台的铸件