质量管理五大工具
质量管理五大核心工具
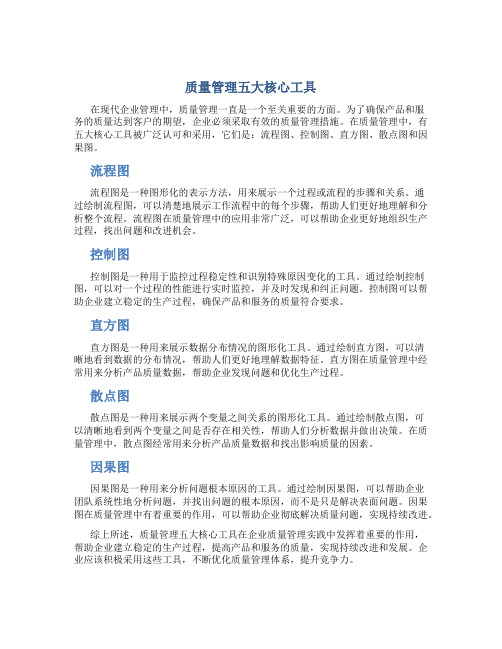
质量管理五大核心工具在现代企业管理中,质量管理一直是一个至关重要的方面。
为了确保产品和服务的质量达到客户的期望,企业必须采取有效的质量管理措施。
在质量管理中,有五大核心工具被广泛认可和采用,它们是:流程图、控制图、直方图、散点图和因果图。
流程图流程图是一种图形化的表示方法,用来展示一个过程或流程的步骤和关系。
通过绘制流程图,可以清楚地展示工作流程中的每个步骤,帮助人们更好地理解和分析整个流程。
流程图在质量管理中的应用非常广泛,可以帮助企业更好地组织生产过程,找出问题和改进机会。
控制图控制图是一种用于监控过程稳定性和识别特殊原因变化的工具。
通过绘制控制图,可以对一个过程的性能进行实时监控,并及时发现和纠正问题。
控制图可以帮助企业建立稳定的生产过程,确保产品和服务的质量符合要求。
直方图直方图是一种用来展示数据分布情况的图形化工具。
通过绘制直方图,可以清晰地看到数据的分布情况,帮助人们更好地理解数据特征。
直方图在质量管理中经常用来分析产品质量数据,帮助企业发现问题和优化生产过程。
散点图散点图是一种用来展示两个变量之间关系的图形化工具。
通过绘制散点图,可以清晰地看到两个变量之间是否存在相关性,帮助人们分析数据并做出决策。
在质量管理中,散点图经常用来分析产品质量数据和找出影响质量的因素。
因果图因果图是一种用来分析问题根本原因的工具。
通过绘制因果图,可以帮助企业团队系统性地分析问题,并找出问题的根本原因,而不是只是解决表面问题。
因果图在质量管理中有着重要的作用,可以帮助企业彻底解决质量问题,实现持续改进。
综上所述,质量管理五大核心工具在企业质量管理实践中发挥着重要的作用,帮助企业建立稳定的生产过程,提高产品和服务的质量,实现持续改进和发展。
企业应该积极采用这些工具,不断优化质量管理体系,提升竞争力。
质量管理的五大工具和七大方法

质量管理的五大工具和七大方法一、质量管理的五大工具:1.流程分析图:流程分析图也称为流程图,用于展示一个过程从开始到结束的步骤和关系。
通过分析流程分析图,可以识别出流程中的关键节点,并找出流程中存在的问题和不必要的环节,以便进行改进。
2.帕累托图:帕累托图也称为80/20法则图,用于识别导致问题的主要原因。
通过对问题进行分类并按照其重要性进行排序,可以确定要优先解决的问题和改进措施。
3.控制图:控制图用于监控和控制过程的稳定性和可靠性。
通过对过程数据进行统计分析和对比,可以及时发现过程中的异常和变化,以便采取相应的控制措施。
4.散点图:散点图用于分析两个变量之间的关系。
通过将两个变量的值绘制在坐标系中,并观察其分布情况和趋势,可以判断两个变量之间是否存在关联,并进行进一步的分析和处理。
5.直方图:直方图用于展示数据的分布情况。
通过将数据根据其取值范围进行分组,并绘制为垂直矩形条形图,可以直观地显示数据的集中趋势和离散程度,以便进行合理的判断和决策。
二、质量管理的七大方法:1.设计实验法:设计实验法用于确定影响产品质量的关键因素和最佳工艺参数。
通过制定合理的实验方案,对关键因素进行系统性的测试和调整,以找出最佳的工艺参数,从而提高产品的质量。
2.问题解决法:问题解决法用于解决质量问题和缺陷的产生。
通过采用系统性的方法和工具,如5W1H、鱼骨图、因果分析等,找出问题的根本原因,并制定相应的解决方案,以避免问题再次发生。
3.技术审查法:技术审查法用于评估和审核产品或项目的技术要求和技术能力。
通过对技术文件和工艺流程的审查,可以发现不符合要求的地方,并提出相应的建议和改进措施,以提高产品或项目的质量。
4.过程审核法:过程审核法用于评估和审核生产过程的执行情况。
通过对生产过程的现场观察和数据分析,可以发现过程中存在的问题和风险,并提出相应的改进和控制措施,以确保过程的稳定性和可靠性。
5.样品检验法:样品检验法用于评估产品的合格性和产品质量的稳定性。
质量管理五大工具七大手法主要用途是什么
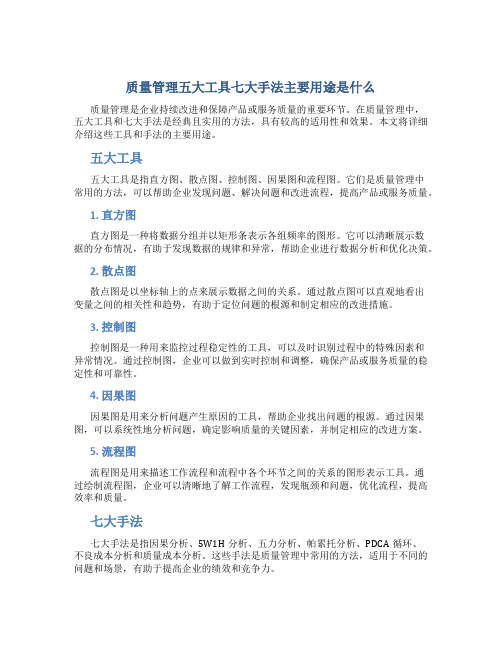
质量管理五大工具七大手法主要用途是什么质量管理是企业持续改进和保障产品或服务质量的重要环节。
在质量管理中,五大工具和七大手法是经典且实用的方法,具有较高的适用性和效果。
本文将详细介绍这些工具和手法的主要用途。
五大工具五大工具是指直方图、散点图、控制图、因果图和流程图。
它们是质量管理中常用的方法,可以帮助企业发现问题、解决问题和改进流程,提高产品或服务质量。
1. 直方图直方图是一种将数据分组并以矩形条表示各组频率的图形。
它可以清晰展示数据的分布情况,有助于发现数据的规律和异常,帮助企业进行数据分析和优化决策。
2. 散点图散点图是以坐标轴上的点来展示数据之间的关系。
通过散点图可以直观地看出变量之间的相关性和趋势,有助于定位问题的根源和制定相应的改进措施。
3. 控制图控制图是一种用来监控过程稳定性的工具,可以及时识别过程中的特殊因素和异常情况。
通过控制图,企业可以做到实时控制和调整,确保产品或服务质量的稳定性和可靠性。
4. 因果图因果图是用来分析问题产生原因的工具,帮助企业找出问题的根源。
通过因果图,可以系统性地分析问题,确定影响质量的关键因素,并制定相应的改进方案。
5. 流程图流程图是用来描述工作流程和流程中各个环节之间的关系的图形表示工具。
通过绘制流程图,企业可以清晰地了解工作流程,发现瓶颈和问题,优化流程,提高效率和质量。
七大手法七大手法是指因果分析、5W1H分析、五力分析、帕累托分析、PDCA循环、不良成本分析和质量成本分析。
这些手法是质量管理中常用的方法,适用于不同的问题和场景,有助于提高企业的绩效和竞争力。
1. 因果分析因果分析是通过分析问题的因果关系,找出问题的根本原因。
通过因果分析,企业可以避免只见树木不见森林的情况,深入挖掘问题的本质,实现从表面到根本的问题解决。
2. 5W1H分析5W1H分析是通过回答问题的5W(what、why、when、where、who)和1H (how)来全面了解问题的背景和原因。
质量管理五大工具和七大手法
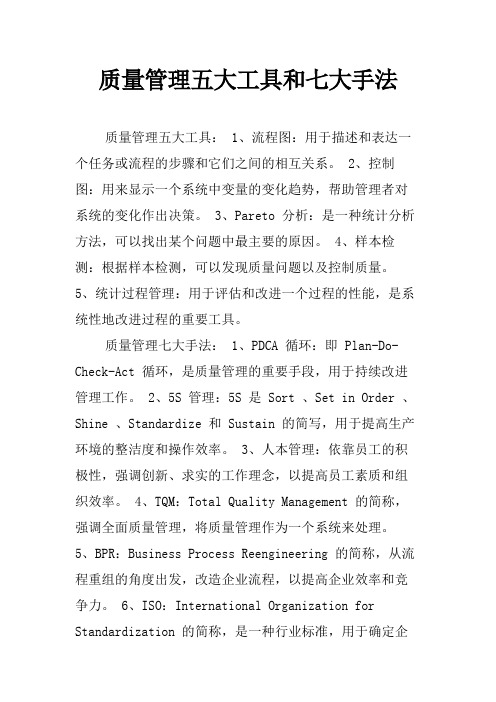
质量管理五大工具和七大手法
质量管理五大工具: 1、流程图:用于描述和表达一个任务或流程的步骤和它们之间的相互关系。
2、控制图:用来显示一个系统中变量的变化趋势,帮助管理者对系统的变化作出决策。
3、Pareto 分析:是一种统计分析方法,可以找出某个问题中最主要的原因。
4、样本检测:根据样本检测,可以发现质量问题以及控制质量。
5、统计过程管理:用于评估和改进一个过程的性能,是系统性地改进过程的重要工具。
质量管理七大手法: 1、PDCA 循环:即 Plan-Do-Check-Act 循环,是质量管理的重要手段,用于持续改进管理工作。
2、5S 管理:5S 是 Sort 、Set in Order 、Shine 、Standardize 和 Sustain 的简写,用于提高生产环境的整洁度和操作效率。
3、人本管理:依靠员工的积极性,强调创新、求实的工作理念,以提高员工素质和组织效率。
4、TQM:Total Quality Management 的简称,强调全面质量管理,将质量管理作为一个系统来处理。
5、BPR:Business Process Reengineering 的简称,从流程重组的角度出发,改造企业流程,以提高企业效率和竞争力。
6、ISO:International Organization for Standardization 的简称,是一种行业标准,用于确定企
业质量管理体系的组织形式和管理体制。
7、Kanban:是一种库存管理方式,用于控制物料的流动和消耗,是提高生产效率的有效工具。
质量管理五大工具
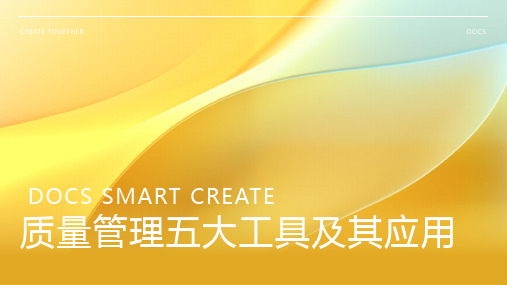
• 定期检查:按照检查表的周期和要求,进行定期检查 • 记录检查结果:将检查结果记录下来,便于分析 • 分析检查结果:通过检查结果,分析质量问题,制定改进措施
检查表在质量管理中的应用实例
检查表在质量管理中的应用实例
• 某企业提高产品合格率 • 设计检查表,包括产品外观、尺寸、功能等方面的检查项目 • 定期进行检查,记录检查结果 • 分析检查结果,发现问题,制定并实施改进措施
五大工具综合运用的局限性
• 过于依赖数据:忽略非量化因素,可能导致问题被忽视 • 循环周期较长:需要较长时间才能看到改进效果
CREATE TOGETHER
DOCS
谢谢观看
THANK YOU FOR WATCHING
• 收集质量数据:收集需要监控的质量数据 • 整理数据:对数据进行整理,满足控制图设计要求 • 分析控制图:通过控制图分析数据点,发现质量问题
控制图在质量管理中的应用实例
控制图在质量管理中的应用实例
• 某企业提高产品合格率 • 收集生产工艺参数的数据,绘制控制图 • 分析控制图,发现异常数据点 • 针对异常数据点,制定并实施改进措施
CREATE TOGETHER
DOCS
DOCS SMART CREATE
质量管理五大工具及其应用
01
质量管理五大工具简介
五大工具的定义与作用
五大工具是指广泛应用于质量管理的五个方法
• PDCA循环:计划、执行、检查、处理四个阶段的循环过程 • 检查表:用于记录和检查质量问题的工具 • 直方图:用于显示质量数据分布的图形工具 • 散布图:用于分析两个质量变量之间关系的图形工具 • 控制图:用于监控质量过程稳定性的图形工具
20世纪中后期,五大工具逐渐被全球企业广泛应用
质量管理五大工具培训

质量管理五大工具培训质量管理五大工具是指流程控制图、因果图、直方图、散点图和Pareto图。
这些工具在质量管理方面起着至关重要的作用,具体体现在实现流程控制、防范问题、确定失误根源、制定优先处理措施等方面。
流程控制图流程控制图是其中一项重要的控制工具,旨在帮助质量管理人员实现过程的控制和优化。
该图常常被用来解决一些常见的问题,例如:1. 过程变异: 判断数据是否在偏离了平均值的情况下保持一定的范围内。
2. 特殊原因:判定哪些变异是由于非正常的原因产生的,比如材料质量问题或操作失误等。
3. 设置控制限:帮助质量管理人员识别出过程应该掌控的极限范围,从而在限制内保持生产的稳定性。
通过在质量管理过程中使用流程控制图,公司可以有效地进行过程控制,及时发现过程变异和非正常变异,并且了解到数据是否在处理时合乎标准,因此推动了质量和生产能力的大幅提高。
因果图因果图也叫鱼骨图,常常被用来识别不同问题产生的原因,从而帮助解决方案的制定。
它通常包含了五大要素:人员、设备、材料、方法和环境。
鱼骨图有助于团队理解给定问题的不同方面,例如:人员掌握度、工艺影响、材料质量、设备状况和环境影响等。
这些因素直接影响着产品质量。
通过因果图,质量管理人员可以更直观地了解质量问题的基本原因。
直方图直方图通常被用在质量管理中的统计学分析方面。
它能够通过收集连续性数据,展示数据的分布,从而更深入地理解数据的差异性和变异性。
直方图通常具有一个垂直的柱形图,每个柱子代表不同数值的出现频率,并且柱形图通常被用于比较两个或更多数据集之间的差异性。
通过统计分析、精炼、汇总及排除极值的方式,质量管理人员可以更加清楚地了解数据的分布,籍此发现潜在问题,从而制定对应策略,推动生产质量。
散点图散点图是另一个工具,用于分析来自不同变量组合的数据。
这样做就可以帮助质量管理人员确认因果关系,发现数据之间的统计学差异。
散点图可以清楚地显示数据之间的关系,例如:正相关、负相关或者无相关关系。
五大核心工具

质量管理五大工具质量管理五大工具,也称品管五大工具。
包括:1.统计过程控制(SPC,Statistical Process Control);2.测量系统分析(MSA,Measurement System Analyse);3.失效模式和效果分析(FMEA,Failure Mode & Effect Analyse);4.产品质量先期策划(APQP,Advanced Product Quality Planning);5.生产件批准程序(PPAP,Production Part Approval Process)。
中文名质量管理五大工具外文名Five tools of quality control又名品管五大工具包括SPC,MSA,FMEA,APQP,PPAP目录1. 1SPC2. ▪概念3. ▪目的1. ▪计算表2. 2MSA3. 3FMEASPC概念SPC(Statistical Process Control)是一种制造控制方法,是将制造中的控制项目,依其特性所收集的数据,通过过程能力的分析与过程标准化,发掘过程中的异常,并立即采取改善措施,使过程恢复正常的方法。
利用统计的方法来监控制造过程的状态,确定生产过程在管制的状态下,以降低产品品质的变异SPC能解决之问题1.经济性:有效的抽样管制,不用全数检验,不良率,得以控制成本。
使制程稳定,能掌握品质、成本与交期。
2.预警性:制程的异常趋势可即时对策,预防整批不良,以减少浪费。
3.分辨特殊原因:作为局部问题对策或管理阶层系统改进之参考。
4.善用机器设备:估计机器能力,可妥善安排适当机器生产适当零件。
5.改善的评估:制程能力可作为改善前後比较之指标。
目的对过程做出可靠有效的评估;确定过程的统计控制界限,判断过程是否失控和过程是否有能力;为过程提供一个早期报警系统,及时监控过程的情况以防止废品的发生;减少对常规检验的依赖性,定时的观察以及系统的测量方法替代了大量的检测和验证工作MAS测量系统分析(MSA)是对每个零件能够重复读数的测量系统进行分析,评定测量系统的质量,判断测量系统产生的数据可接受性。
质量管理工具与方法
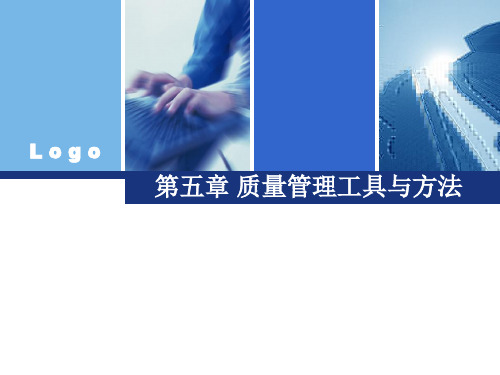
❖PPAP的目的 1)确定供方是否已经正确理解了顾客工程设计记录和规范的所有要求。 2)并且在执行所要求的生产节拍条件下的实际生产过程中,具有持续满足
Logo
第五章 质量管理工具与方法
本文档后面有精心整理的常用PPT编辑图标,以提高工作效率
Contents
1 2 3
Logo
5.1质量管理体系五大核心工具 5.2质量管理新旧七种工具 5.3 质量管理方法
Logo
5.1质量管理五大核心工具
❖ 质量管理五大工具,也称品管五大工具。包括: 1.统计过程控制(SPC,Statistical Process Control); 2.测量系统分析(MSA,Measure System Analyse); 3.失效模式和效果分析(FMEA,Failure Mode & Effct Analyse); 4.产品质量先期策划(APQP,Advanced Product Quality Planning); 5.生产件批准程序(PPAP,Production Part Approval Process)。
❖特点
1)目标明确:满足顾客要求,不断改进。 2)按规定的方法和组织形式进行策划。 3)应用各类分析工具:FMEA,MSA,SPC、流程图,QFD等。 4)保证跨职能活动的效率:横向协调小组。
5.1.5生产件批准程序(PPAP)
Logo
❖概念 生产件批准程序(PPAP)规定了包括生产件和散装材料在内的生产件批准的
❖ 在使用散布图调查两个因素之间的关系时,应尽可能固定对这两个因素有影响的其他因素 ,才能使通过散布图得到的结果比较准确。
质量管理五大工具、七大手法知识点总结

质量管理五大工具、七大手法知识点总结在质量管理领域,有一系列的工具和手法被广泛应用,以帮助企业提高产品和服务的质量,降低成本,增强竞争力。
其中,质量管理的五大工具和七大手法是最为常见和重要的。
接下来,让我们详细了解一下这些工具和手法的具体内容和应用。
一、质量管理五大工具1、统计过程控制(SPC)SPC 是一种借助统计方法对过程进行控制的工具。
它通过收集和分析过程中的数据,如产品的尺寸、重量、强度等,来监测过程是否处于稳定状态。
如果过程出现异常波动,就能及时发现并采取措施进行纠正。
例如,在汽车制造中,通过对零部件生产过程中的尺寸数据进行 SPC 分析,可以确保零部件的质量一致性,减少废品和返工。
2、测量系统分析(MSA)MSA 用于评估测量系统的准确性和可靠性。
在质量管理中,准确的测量是至关重要的,因为错误的测量结果可能导致错误的决策。
MSA 可以确定测量设备、测量人员、测量方法等因素对测量结果的影响,并采取措施来改进测量系统,提高测量的精度和可信度。
3、失效模式及后果分析(FMEA)FMEA 是一种前瞻性的风险评估工具。
它通过分析产品或过程可能出现的失效模式,评估其后果的严重程度、发生的可能性以及可检测性,从而提前采取预防措施,降低失效的风险。
在航空航天、医疗设备等对安全性要求极高的行业,FMEA 被广泛应用。
4、产品质量先期策划(APQP)APQP 是一种结构化的产品开发方法,旨在确保产品在开发过程中满足客户的需求和期望。
它涵盖了从产品概念设计到量产的整个过程,包括项目计划、设计开发、过程设计、产品和过程确认等阶段。
通过APQP,可以有效地整合各部门的资源和工作,缩短产品开发周期,提高产品质量。
5、生产件批准程序(PPAP)PPAP 是用来确定供应商是否已经正确理解了顾客工程设计记录和规范的所有要求,并且在生产过程中,在实际生产条件下,在规定的生产节拍下,具有持续生产满足顾客要求产品的潜在能力。
质量管理五大工具七大手法知识点总结

质量管理五大工具七大手法知识点总结质量管理在现代企业中起着至关重要的作用,有效的质量管理能够提高产品和服务的质量,降低成本,提高客户满意度,从而带来持续的竞争优势。
在质量管理中,五大工具和七大手法是常用的工具和方法,有助于组织实现质量目标并不断改进。
一、质量管理五大工具1.控制图:控制图是质量管理中常用的工具,通过分析数据的变化趋势,及时发现问题,采取行动进行改进,确保过程稳定。
2.直方图:直方图是一种用柱状图表示数据频率分布的图表,可以帮助分析数据的分布情况,识别问题根源并制定改进方案。
3.散点图:散点图是用点表示数据的散布情况,可以帮助找出数据中的关联性,有助于识别可能存在的模式和异常情况。
4.因果图:因果图(鱼骨图)是一种用来分析问题根本原因的工具,通过挖掘问题产生的各种可能性,有助于找出根本原因并解决问题。
5.Pareto图:Pareto图是依据帕累托原则绘制的图表,帮助确定问题的关键因素,有助于确定改进的重点。
二、质量管理七大手法1.质量目标的设定:明确质量目标是质量管理的首要步骤,只有设定明确的目标才能使团队明确方向,有针对性地开展工作。
2.质量数据收集:收集质量数据是了解生产过程和产品质量状况的必要手段,有助于发现问题和制定改进措施。
3.质量数据分析:对质量数据进行分析可以帮助识别问题的根源,找出改进机会,提高生产质量。
4.质量改进方案制定:根据质量数据分析的结果,制定适合的改进方案,并明确实施计划,有利于持续改进。
5.质量管理实施:质量管理实施是将改进方案付诸实施的过程,需要全员参与,确保达到预期效果。
6.质量管理控制:质量管理控制是对实施效果进行监控和调整的过程,随时根据数据和情况做出决策,确保质量持续改进。
7.质量管理评估:定期对质量管理工作进行评估,检验目标是否达成、工作是否有效,及时调整和优化工作方法。
以上是质量管理中常用的五大工具和七大手法,通过灵活应用这些工具和手法,企业可以更好地管理质量,提升竞争力,实现可持续发展。
质量管理五大工具书
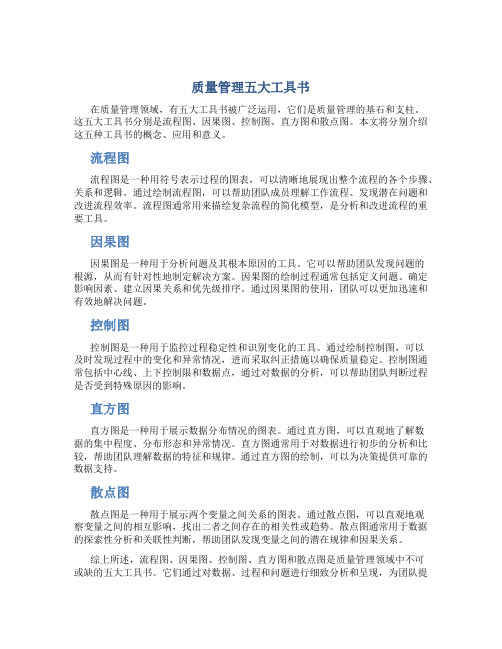
质量管理五大工具书在质量管理领域,有五大工具书被广泛运用,它们是质量管理的基石和支柱。
这五大工具书分别是流程图、因果图、控制图、直方图和散点图。
本文将分别介绍这五种工具书的概念、应用和意义。
流程图流程图是一种用符号表示过程的图表,可以清晰地展现出整个流程的各个步骤、关系和逻辑。
通过绘制流程图,可以帮助团队成员理解工作流程、发现潜在问题和改进流程效率。
流程图通常用来描绘复杂流程的简化模型,是分析和改进流程的重要工具。
因果图因果图是一种用于分析问题及其根本原因的工具。
它可以帮助团队发现问题的根源,从而有针对性地制定解决方案。
因果图的绘制过程通常包括定义问题、确定影响因素、建立因果关系和优先级排序。
通过因果图的使用,团队可以更加迅速和有效地解决问题。
控制图控制图是一种用于监控过程稳定性和识别变化的工具。
通过绘制控制图,可以及时发现过程中的变化和异常情况,进而采取纠正措施以确保质量稳定。
控制图通常包括中心线、上下控制限和数据点,通过对数据的分析,可以帮助团队判断过程是否受到特殊原因的影响。
直方图直方图是一种用于展示数据分布情况的图表。
通过直方图,可以直观地了解数据的集中程度、分布形态和异常情况。
直方图通常用于对数据进行初步的分析和比较,帮助团队理解数据的特征和规律。
通过直方图的绘制,可以为决策提供可靠的数据支持。
散点图散点图是一种用于展示两个变量之间关系的图表。
通过散点图,可以直观地观察变量之间的相互影响,找出二者之间存在的相关性或趋势。
散点图通常用于数据的探索性分析和关联性判断,帮助团队发现变量之间的潜在规律和因果关系。
综上所述,流程图、因果图、控制图、直方图和散点图是质量管理领域中不可或缺的五大工具书。
它们通过对数据、过程和问题进行细致分析和呈现,为团队提供了重要的支撑和指导,帮助团队发现问题、改进流程和提升质量,实现持续的质量管理和优化。
质量管理的五大工具和八大手法
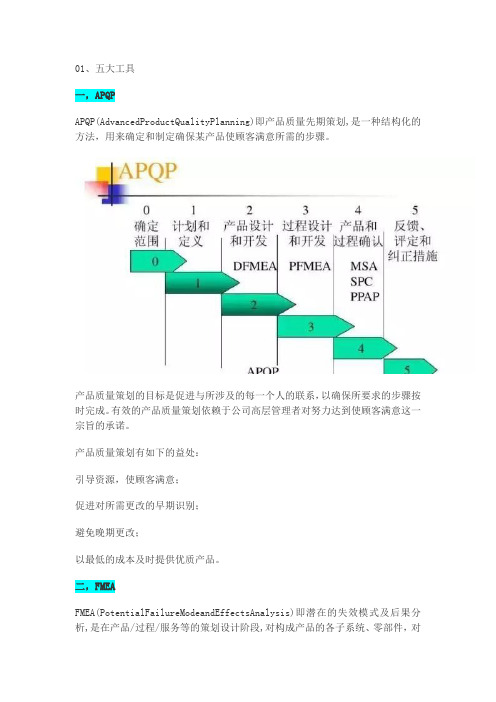
01、五大工具一,APQPAPQP(AdvancedProductQualityPlanning)即产品质量先期策划,是一种结构化的方法,用来确定和制定确保某产品使顾客满意所需的步骤。
产品质量策划的目标是促进与所涉及的每一个人的联系,以确保所要求的步骤按时完成。
有效的产品质量策划依赖于公司高层管理者对努力达到使顾客满意这一宗旨的承诺。
产品质量策划有如下的益处:引导资源,使顾客满意;促进对所需更改的早期识别;避免晚期更改;以最低的成本及时提供优质产品。
二,FMEAFMEA(PotentialFailureModeandEffectsAnalysis)即潜在的失效模式及后果分析,是在产品/过程/服务等的策划设计阶段,对构成产品的各子系统、零部件,对构成过程,服务的各个程序逐一进行分析,找出潜在的失效模式,分析其可能的后果,评估其风险,从而预先采取措施,减少失效模式的严重程序,降低其可能发生的概率,以有效地提高质量与可靠性,确保顾客满意的系统化活动。
FMEA种类:按其应用领域常见FMEA有设计FMEA(DFMEA)和过程FMEA(PFMEA),其它还有系统FMEA,应用FMEA,采购FMEA,服务FMEA。
三,MSAMSA(MeasurementSystemAnalysis)即MSA测量系统分析,它使用数理统计和图表的方法对测量系统的误差进行分析,以评估测量系统对于被测量的参数来说是否合适,并确定测量系统误差的主要成份。
四,PPAPPPAP(Productionpartapprovalprocess)即生产件批准程序,是对生产件的控制程序,也是对质量的一种管理方法。
PPAP生产件提交保证书:主要有生产件尺寸检验报告、外观检验报告、功能检验报告,、材料检验报告、外加一些零件控制方法和供应商控制方法;制造型企业要求供应商在提交产品时做PPAP文件及首件,只有当PPAP文件全部合格后才能提交;当工程变更后还须提交报告。
16949质量管理体系工具

16949质量管理体系五大工具分别是:测量系统分析(MSA)、产品质量先期策划(APQP)、潜在失效模式与后果分析(FMEA)、统计过程控制(SPC)和生产件批准(PPAP)。
1.**测量系统分析(MSA)**是对每个零件能够重复读数的测量系统进行分析,评定测量系统的质量,判断测量系统产生的数据可接受性。
2.**产品质量先期策划(APQP)**是一种结构化的方法,用来确定和制定确保某产品使顾客满意所需的步骤。
它的目标是促进与所涉及的每一个
人的联系,以确保所要求的步骤按时完成。
3.**潜在失效模式与后果分析(FMEA)**是产品设计或生产早期阶段就开始进行的一组系列化活动。
及早地指出根据经验判断出的弱点和可能产
生的缺陷及其造成的后果和风险,并在决策中采取措施加以消除。
4.**统计过程控制(SPC)**分析生产过程的质量控制是保证产品质量的重要环节,稳定的生产过程会带来质量上的飞跃。
统计过程控制图用于记
录与质量有关的工序参数或不同时间的产品参数。
5.**生产件批准程序(PPAP)**的目的是用来确定供方是否已经正确理解了顾客工程设计记录和规范的所有要求,并且在执行所要求的生产节拍
条件下的实际生产过程中,具有持续满足这些要求的潜能,是目前最完善的供应商选择与控制系统。
- 1、下载文档前请自行甄别文档内容的完整性,平台不提供额外的编辑、内容补充、找答案等附加服务。
- 2、"仅部分预览"的文档,不可在线预览部分如存在完整性等问题,可反馈申请退款(可完整预览的文档不适用该条件!)。
- 3、如文档侵犯您的权益,请联系客服反馈,我们会尽快为您处理(人工客服工作时间:9:00-18:30)。
目录
质量管理五大工具................................................................... 错误!未定义书签。
一、1SPC .............................................................................. 错误!未定义书签。
二、MSA............................................................................... 错误!未定义书签。
三、FMEA............................................................................. 错误!未定义书签。
四、APQP ............................................................................. 错误!未定义书签。
五、PPAP.............................................................................. 错误!未定义书签。
质量管理五大工具
质量管理五大工具,也称品管五大工具。
包括:1.统计过程控制(SPC,Statistical Process Control);2.测量系统分析(MSA,Measurement System Analyse);3.失效模式和效果分析(FMEA,Failure Mode & Effect Analyse);4.产品质量先期策划(APQP,Advanced Product Quality Planning);5.生产件批准程序(PPAP,Production Part Approval Process)。
一、1SPC
概念
SPC是一种制造控制方法,是将制造中的控制项目,依其特性所收集的数据,通过过程能力的分析与过程标准化,发掘过程中的异常,并立即采取改善措施,使过程恢复正常的方法[1]。
利用统计的方法来监控制程的状态,确定生产过程在管制的状态下,以降低产品品质的变异 SPC能解决之问题 1.经济性:有效的抽样管制,不用全数检验,不良率,得以控制成本。
使制程稳定,能掌握品质、成本与交期。
2.预警性:制程的异常趋势可即时对策,预防整批不良,以减少浪费。
3.分辨特殊原因:作为局部问题对策或管理阶层系统改进之参考。
4.善用机器设备:估计机器能力,可妥善安排适当机器生产适当零件。
5.改善的评估:制程能力可作为改善前後比较之指标。
目的
·对过程做出可靠有效的评估;
·确定过程的统计控制界限,判断过程是否失控和过程是否有能力;
·为过程提供一个早期报警系统,及时监控过程的情况以防止废品的发生;
·减少对常规检验的依赖性,定时的观察以及系统的测量方法替代了大量
的检测和验证工作[1]
计算表
Pp 和Ppk不合格率
质量管理五大工具
二、MSA
一是确保测量数据的准确性/质量,使用测量系统分析(MSA)方法对获得
测量数据的测量系统进行评估;二是确保使用了合适的数据分析方法,如使用SPC工具、试验设计、方差分析、回归分析等。
MSA (MeasurementSystemAnalysis)使用数理统计和图表的方法对测量系统的分辨率和误差进行分析。
测量系统分析(MSA)是对每个零件能够重复读数的测量系统进行分析,评定测量系统的质量,判断测量系统产生的数据可接受性。
MSA的目的:
了解测量过程,确定在测量过程中的误差总量,及评估用于生产和过程控
制中的测量系统的充分性。
MSA促进了解和改进(减少变差)。
在日常生产中,我们经常根据获得的过程加工部件的测量数据去分析过程
的状态、过程的能力和监控过程的变化;那么,怎么确保分析的结果是正确的呢?我们必须从两方面来保证:
1)是确保测量数据的准确性/质量,使用测量系统分析(MSA)方法对获得
测量数据的测量系统进行评估;
2)是确保使用了合适的数据分析方法,如使用SPC工具、试验设计、方差
分析、回归分析等。
MSA使用数理统计和图表的方法对测量系统的分辨率和误
差进行分析,以评估测量系统的分辨率和误差对于被测量的参数来说是否合适,并确定测量系统误差的主要成分。
[2]
三、FMEA
在设计和制造产品时,通常有三道控制缺陷的防线:避免或消除故障起因、预先确定或检测故障、减少故障的影响和后果。
FMEA正是帮助我们从第一道防
线就将缺陷消灭在摇篮之中的有效工具。
FMEA是一种可靠性设计的重要方法。
它实际上是FMA(故障模式分析)和FEA(故障影响分析)的组合。
它对各种可能的风险进行评价、分析,以便在现有技术的基础上消除这些风险或将这些风
第3页,共4页
险减小到可接受的水平。
及时性是成功实施FMEA的最重要因素之一,它是一个“事前的行为”,而不是“事后的行为”。
为达到最佳效益,FMEA必须在故障
模式被纳入产品之前进行。
FMEA实际是一组系列化的活动,其过程包括:找
出产品/过程中潜在的故障模式;根据相应的评价体系对找出的潜在故障模式进行风险量化评估;列出故障起因/机理,寻找预防或改进措施。
由于产品故障
可能与设计、制造过程、使用、承包商/供应商以及服务有关,因此FMEA又细
分为设计FMEA、过程FMEA、使用FMEA和服务FMEA四类。
其中设计FMEA和过
程FMEA最为常用。
FMEA的目的
1)能够容易、低成本地对产品或过程进行修改,从而减轻事后修改的危机。
2)找到能够避免或减少这些潜在失效发生的措施。
[2]
四、APQP
产品质量先期策划(或者产品质量先期策划和控制计划)是
QS9000/TS16949质量管理体系的一部分。
定义及其他知识点:产品质量策划
是一种结构化的方法,用来确定和制定确保某产品使顾客满意所需的步骤。
产品质量策划的目标是促进与所涉及每一个人的联系,以确保所要求的步骤按时
完成。
有效的产品质量策划依赖于高层管理者对努力达到使顾客满意这一宗旨的承诺。
五、PPAP
PPAP生产件批准程序(Production part approval process) PPAP生产件
提交保证书:主要有生产件尺寸检验报告,外观检验报告,功能检验报告,材料检验报告; 外加一些零件控制方法和供应商控制方法;主要是制造型企业要求供
应商在提交产品时做ppap文件及首件,只有当ppap文件全部合格后才能提交;当工程变更后还须提交报告。
PPAP是对生产件的控制程序,也是对质量的一
种管理方法
PPAP的目的
1)确定供方是否已经正确理解了顾客工程设计记录和规范的所有要求。
2)并且在执行所要求的生产节拍条件下的实际生产过程中,具有持续满足
这些要求的潜能。