凡谷压铸件质量标准
压铸检验标准 (1)

压铸检验标准、
目的:为了快速的了解压铸产品的缺陷,有一个更好的品质保障。
使用范围:前道压铸机所生产的所有产品《铝合金,锌合金》
检验项目:外观、结构
使用工具:卡尺、
检验方法:通过目视检验,《特别情况下可拿去装配班组试装》压铸件表面不能有裂纹、凹陷、变形、气泡、飞边、等外观缺陷如下图所示
检验要求:1以上缺陷都能经过二道工序加工完成,如果气泡能用二道工序的打磨或是抛光来完成且不景响外观结构的,视为良品,影响外观的为不良品处理。
2压铸机生产的产品我们除了看外观,必要时我要也用卡尺测一下它的尺寸是否如果我生产图纸一致,
3对于枪支外露的装饰产品,我们应该做到无缺陷或是减少缺陷,直到看不清缺陷为止。
4每天上班前或是每次压铸机更换产品时应做到首检,首检合格后才能生产。
巡检做到2小时一次,且对压铸或是前道的每一个工作岗位进行巡查和抽检,每次抽检≥10个零物件,一旦发现不良产品通知操作人员停机,并告知压铸管理人员情况,对个别产品不能明确判定结果时,方可拿几个到喷漆班组试喷漆后看效果,效果可以,可为良品,不行为不良品处理。
5压铸好的产品都会经过二道修剪、打磨、砂带、抛光、攻牙、铣床等把产品外缺陷处理掉,也需要注意产品有没有如生产图纸一致《如攻牙,钻孔》方便装配生产,处理好的产品都会由质检部查看好且盖上合格标签放可入库
6对不合格的产品我们要记录下来,可报废回炉处置.。
压铸件质量标准
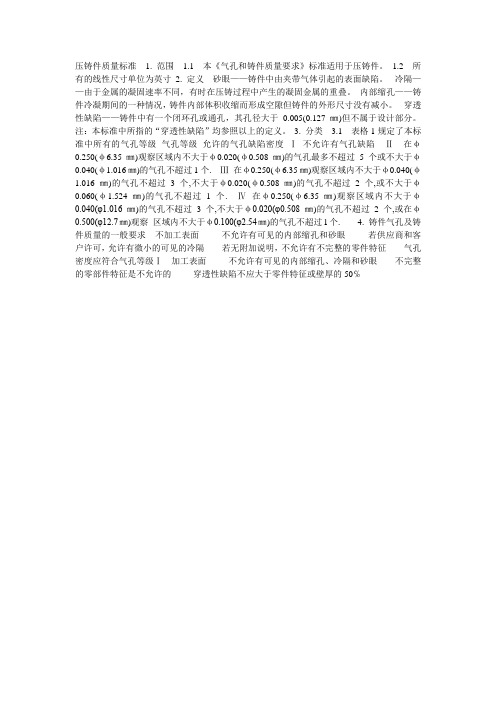
压铸件质量标准 1. 范围 1.1 本《气孔和铸件质量要求》标准适用于压铸件。
1.2 所有的线性尺寸单位为英寸2. 定义砂眼——铸件中由夹带气体引起的表面缺陷。
冷隔——由于金属的凝固速率不同,有时在压铸过程中产生的凝固金属的重叠。
内部缩孔——铸件冷凝期间的一种情况,铸件内部体积收缩而形成空隙但铸件的外形尺寸没有减小。
穿透性缺陷——铸件中有一个闭环孔或通孔,其孔径大于0.005(0.127㎜)但不属于设计部分。
注:本标准中所指的“穿透性缺陷”均参照以上的定义。
3. 分类 3.1 表格1规定了本标准中所有的气孔等级气孔等级允许的气孔缺陷密度Ⅰ不允许有气孔缺陷Ⅱ在φ0.250(φ6.35㎜)观察区域内不大于φ0.020(φ0.508㎜)的气孔最多不超过5个或不大于φ
0.040(φ1.016㎜)的气孔不超过1个. Ⅲ在φ0.250(φ6.35㎜)观察区域内不大于φ0.040(φ
1.016㎜)的气孔不超过 3 个,不大于φ0.020(φ0.508㎜)的气孔不超过2个,或不大于φ0.060(φ1.524 ㎜)的气孔不超过1个. Ⅳ在φ0.250(φ6.35㎜)观察区域内不大于φ0.040(φ1.016㎜)的气孔不超过3 个,不大于φ0.020(φ0.508㎜)的气孔不超过2个,或在φ0.500(φ1
2.7㎜)观察区域内不大于φ0.100(φ2.54㎜)的气孔不超过1个. 4. 铸件气孔及铸件质量的一般要求不加工表面不允许有可见的内部缩孔和砂眼若供应商和客户许可,允许有微小的可见的冷隔若无附加说明,不允许有不完整的零件特征气孔密度应符合气孔等级Ⅰ加工表面不允许有可见的内部缩孔、冷隔和砂眼不完整的零部件特征是不允许的穿透性缺陷不应大于零件特征或壁厚的50℅。
凡谷压铸件质量标准

凡谷压铸件质量标准(总14页)本页仅作为文档封面,使用时可以删除This document is for reference only-rar21year.March凡谷压铸件质量标准范围:本标准规定了本公司压铸件的质量保证、验证方法及检验规则和交货条件。
本标准适用于压铸件产品的进货验收、生产过程中产品质量的判定,外购(协)件的验收亦适用本标准,也可作结构设计的指导文件。
注:本标准为本公司压铸件质量通用标准,若客户标准与本标准不符的,以客户标准为准。
简介:本标准规定了本公司对压铸件的质量要求、检验方法、检验规则及交货条件,是本公司压铸件质量判定的依据。
关键词:压铸件引用文件:下列文件中的条款通过本规范的引用而成为本规范的条款。
凡是注日期的引用文件,其随后所有的更改单(不包括勘误的内容)或修订版均不适用于本规范,然而,鼓励根据本规范达成协议的各方研究是否可使用这些文件的最新版本。
凡是不注日期的引用文件,其最新版本适用于本规范。
压铸件的分级本公司的产品一般承受轻载荷,主要控制及检验表面质量、化学成分、尺寸公差。
1.1铸件表面等级压铸件表面按使用范围分为三级,见表1:表1压铸件表面分级表1.2压铸件缺陷特征定义压铸件常见缺陷特征定义如表2所示:表2压铸件常见缺陷特征定义2技术要求2.1化学成分压铸件的化学成分对压铸件的力学性能、抗腐蚀能力都有很大的影响。
本公司所有压铸件的化学成分都应该符合相应牌号的规定。
其中:铝合金化学成分要符合GB/T 15115-2009的规定,见附录A 表3;锌合金化学成分要符合GB/T 13818-2009的规定,见附录A 表4。
2.2力学性能1.采用压铸试样检验时:铝合金压铸件的力学性能要符合GB/T 15115-2009(附录A 表3)的规定;锌合金压铸件的力学性能要符合GB/T 13818-2009(附录A 表4)的规定。
2.采用压铸件本体检验时:其指定部位切取试样的力学性能不得低于单铸件试样的75%;若有特殊要求,以本公司图样要求为准。
铸件质量检查标准

一、目的:为了确保外协标准铸件、成品铸件质量符合工艺、技术要求,为了满足产品特性,结合相关文件特制定本标准。
二、适用范围:本办法适用于我公司产品外协、采购、装配过程中、全部铸件质量检查标准。
三、检查标准:3.1、铸件结构要符合设计要求或加工工艺要求。
无特殊要求时按铸件通用标准执行。
通用标准等级分为:交货验收技术条件标准;铸件质量分等通则(合格品、一等品、优等品)材质、检验方法;工艺和材料规格等一般性规则。
3.2、铸件成品检验。
铸件成品检验包括:相关技术条件的检验、表面质量检验、几何尺寸检验等项内容。
①相关技术条件的检验。
包括铸件化学成分、机械性能等检验内容。
机械性能检验和金相及化学成分检验等技术条件的检验,均必须按相关国家标准执行检验(此处略)。
②表面质量检验。
机械加工生产一线人员在工艺过程中对铸造毛坯的检查主要是对其外观铸造缺陷(如有无沙眼、沙孔、疏松、有无浇不足、铸造裂纹等)的检验;以及毛坯加工余量是否满足加工要求的检验。
表3-1铸件外观质量检验项目(GB6060.1—1985)表3-2 铸件表面粗糙度(R a 值μm)(GB6414—1986)③铸件成品几何尺寸检验。
主要一种是采用划线法检查毛坯的加工余量是否足够。
另一种方法是:用毛坯的参考基准面(也称工艺基准面)作为毛坯的检验基准面的相对测量法(需要测量相对基准面的尺寸及进行简单换算)。
表3-3 铸件尺寸公差数值(mm)(GB6414—1986)注:铸件基本尺寸≤10mm 时,其公差等级提高3 级;大于10mm 至等于15mm 时,其公差等级提高2级;大于16mm 至25mm 时,其公差等级提高1 级。
附表:铸件质量检验与缺陷处理实用技术。
压铸件产品外观质量验收标准

1 目的本标准定义来料或成品外观质量的基本要起,并作为允收/拒收准则。
2 适用范围来料或成品。
3 检测面的分级:A级面:使用者经常看到的面,如产品的上表面、正面、需要丝印的面等。
B级面:在不移动的情况下,使用者偶尔能看到的面,如产品的后面、侧面等。
C级面:产品在移动或被打开时才能看到的面,如产品的底面,内部零件的表面等。
4 检测条件4.1、所有检验均应在正常照明,并模拟最终使用条件下进行。
检测过程中不使用放大镜,所检验表面和人眼呈45°角。
A级面在检测时应转动,以获得最大反光效果。
B级面和C级面在检测期间不必转动。
光源=40W荧光灯人眼45°距离500毫米4.2、A级面停留10秒,B级面停留5秒,C级面停留3秒。
5 金属件外观检验标准5.1 允收总则5.1.1 可接受的缺陷不能影响该零件的装配和功能,否则将被拒收。
5.1.2 缺陷允收定义了900mm2的区域内各类缺陷的最大允收数量。
但是,两个区域或两个以上明显缺陷不能相连。
5.2缺陷定义5.2.1生锈/氧化:暴露在空气中的金属表面发生的化学反应,包括变黄以及出现其它异常。
5.2.2变色:底色或预期的颜色发生改变,或零件表面的颜色不一致。
5.2.3刮伤:零件表面的呈条状的浅沟,包括露底与不露底。
5.2.4压痕:由尖锐物件在零件表面造成的沟痕,指甲能够感受到。
5.2.5镀痕/流痕:由于镀层厚度不均匀造成零件表面上波纹状或条状异常的区域。
5.2.6痕迹:指基体材料的小坑、折弯痕或其他痕迹,涂装后仍无法消除。
5.2.7灰尘或油脂:在制造过程中产生并留在零件表面上的赃污(未清洗)。
5.2.8斑点/颗粒:涂装面或零件表面任何非预期的异物。
5.2.9凹坑:零件表面弹坑状的缺陷。
5.2.10模压痕:因成形模具在零件表面造成的工艺痕,所有零件的模压痕的位置和大小都一样,均匀分布5.3 缺陷允收表每个面的缺陷数量不能超过允收的界限,如下表所示:缺陷允收表6 液体/粉末喷涂外观标准6.1允收总则6.1.1所有的等级面应当喷涂完好且满足颜色、光泽度、厚度、附着力等方面的要求。
压铸件标准

压铸件标准一、化学成分1.压铸件应使用符合要求的材料,其化学成分应符合相关标准和设计要求。
2.压铸件的材料应具有稳定的化学成分,以确保其具有优良的机械性能和耐腐蚀性。
二、尺寸规格1.压铸件的尺寸应符合设计要求,符合图纸尺寸标注。
2.压铸件应具有稳定的尺寸精度和一致性,以确保装配和使用性能。
三、表面质量1.压铸件的表面应光滑、平整,无明显的气孔、缩孔、裂纹等缺陷。
2.压铸件的表面处理应符合设计要求,如喷涂、电镀等,并具有相应的耐腐蚀性和装饰性。
四、力学性能1.压铸件应具有优良的力学性能,如抗拉强度、屈服强度、延伸率等,以确保其承受使用过程中的载荷和应力。
2.压铸件的力学性能应符合相关标准和设计要求,并进行相应的检测和试验。
五、耐腐蚀性1.压铸件的材料应具有较好的耐腐蚀性,以抵抗使用环境中的腐蚀介质侵蚀。
2.压铸件在潮湿、酸性或碱性环境中使用的,应进行相应的耐腐蚀性试验,以验证其耐腐蚀性能。
六、加工性能1.压铸件应具有良好的加工性能,包括可切削性、可磨性等,以确保其加工方便、快捷、精度高。
2.在加工过程中,应注意对压铸件的保护,避免过热、变形等问题。
七、质量稳定性1.压铸件的生产过程应具有稳定的质量控制体系,以确保其质量的稳定性和一致性。
2.在生产过程中,应对压铸件进行严格的质量检测和控制,包括外观检测、尺寸检测、材料检测等。
八、环保要求1.压铸件的生产过程应符合环保要求,采用环保材料和工艺,减少对环境的污染。
2.在使用过程中,压铸件应具有较低的环境影响,如低噪音、低能耗等。
同时应对废弃物进行分类回收处理。
压铸件检验规范
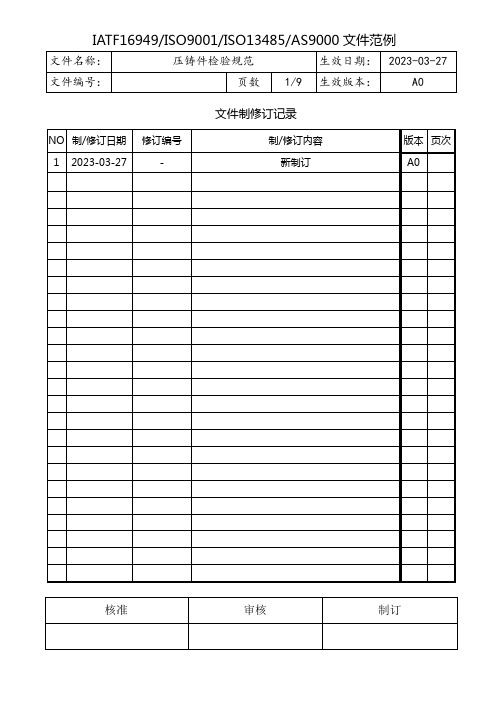
文件制修订记录1、目的:为了对压铸车间生产之产品进行有效地控制,其品质符合国标,行业及客户要求,特制定本规定;2、适用范围:本公司压铸车间均属之;3、职责:品质部负责压铸车间产品首件及巡检,压铸车间负责产品自检互检。
4、不合格品控制:按《不合格控制程序执行》。
原因分析部门:压铸车间,品质部,技术部。
5、引用标准:国家标准,工程图纸;样板;MIL-STD-105E;不良图示。
6、定义:致命缺陷(Critical):单件物料质量特性极严重不符合规定或影响到安全性能时,定义为致命缺陷;严重缺陷(Major):单件物料质量特性严重不符合规定或单件物料重要质量特性不符合规定时,定义为严重缺陷;轻微缺陷(Minor):单件物料质量特性轻微不符合规定或单件物料一般质量特性不符合规定时,定义为轻微缺陷;7、检验内容:一、铸件所需材料及化学成分应符合要求。
二、每批次铸件的机械性能应符合要求。
三、量检具测量铸件尺寸,尺寸公差符合GB/T 6414-1999《铸件尺寸公差与机械加工余量》及工程图纸要求。
四、齿轮类产品,必要时跳动测试仪检测跳动度,符合工程图纸要求。
(双齿轮类产品可分别测试大小齿轮跳动度)五、表面粗糙度可按GB/T 6060.1-1997《表面粗糙度比较样块铸造表面》评级。
六、外观质量:(不良图片见附件)1. 铸件上不允许有冷隔、裂纹、穿透性缺陷及严重的残缺类缺陷(浇不到、未浇满、机械损伤等)的存在.2. 在金属型铸件的非加工表面上,允许铸件有分型、顶杆及排气塞等痕迹。
但凸出表面不大于0.3mm或凹下表面不超过0.4mm,且布局合理协调。
3. 非加工表面的浇冒口,应清理到与铸件表面齐平;待加工表面的浇冒口残留量应不大于3 mm。
4. 铸件上作为基准用的部位应平整,不允许存在任何凸起痕迹,装饰面上不允许有推杆痕迹。
5. 非加工表面上,不允许有麻面和有色斑点。
6. 铸件待加工表面上,允许有经加工可去掉的任何缺陷。
压铸件产品外观质量验收标准剖析

1目的本标准定义来料或成品外观质量的基本要起,并作为允收/拒收准则2适用范围来料或成品。
3检测面的分级:A级面:使用者经常看到的面,如产品的上表面、正面、需要丝印的面等。
B级面:在不移动的情况下,使用者偶尔能看到的面,如产品的后面、侧面等。
C级面:产品在移动或被打开时才能看到的面,如产品的底面,内部零件的表面等。
4检测条件4.1、所有检验均应在正常照明,并模拟最终使用条件下进行。
检测过程中不使用放大镜,所检验表面和人眼呈45°角。
A级面在检测时应转动,以获得最大反光效果。
B级面和C级面在检测期间不必转动。
4.2、A级面停留10秒,B级面停留5秒,C级面停留3秒。
5金属件外观检验标准5.1允收总则5.1.1可接受的缺陷不能影响该零件的装配和功能,否则将被拒收。
5.1.2缺陷允收定义了900mm2的区域内各类缺陷的最大允收数量。
但是,两个区域或两个以上明显缺陷不能相连。
5.2缺陷定义5.2.1生锈/氧化:暴露在空气中的金属表面发生的化学反应,包括变黄以及出现其它异常。
5.2.2变色:底色或预期的颜色发生改变,或零件表面的颜色不一致。
5.2.3刮伤:零件表面的呈条状的浅沟,包括露底与不露底。
5.2.4压痕:由尖锐物件在零件表面造成的沟痕,指甲能够感受到。
5.2.5镀痕/流痕:由于镀层厚度不均匀造成零件表面上波纹状或条状异常的区域。
痕迹:指基体材料的小坑、折弯痕或其他痕迹,涂装后仍无法消除527灰尘或油脂:在制造过程中产生并留在零件表面上的赃污(未清洗)。
528斑点/颗粒:涂装面或零件表面任何非预期的异物。
5.2.9凹坑:零件表面弹坑状的缺陷。
5.2.10模压痕:因成形模具在零件表面造成的工艺痕,所有零件的模压痕的位置和大小都一样,均匀分布5.3 缺陷允收表每个面的缺陷数量不能超过允收的界限,如下表所示:6液体/粉末喷涂外观标准6.1允收总则6.1.1所有的等级面应当喷涂完好且满足颜色、光泽度、厚度、附着力等方面的要求。
压铸件毛坯质量检验标准
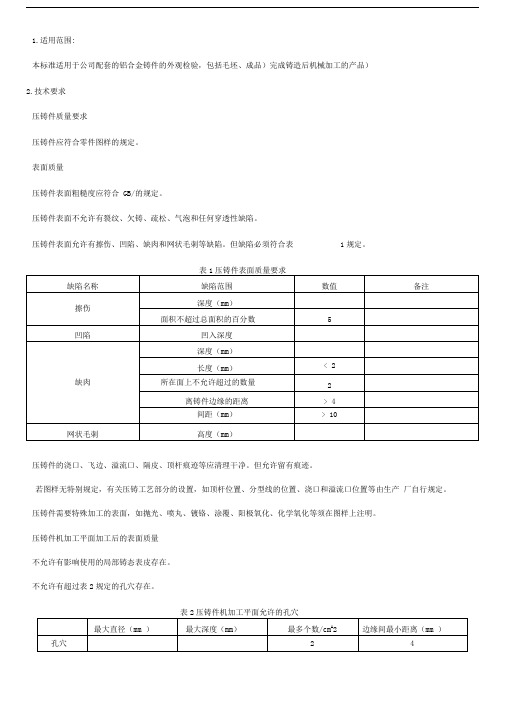
1.适用范围:本标准适用于公司配套的铝合金铸件的外观检验,包括毛坯、成品)完成铸造后机械加工的产品)2.技术要求压铸件质量要求压铸件应符合零件图样的规定。
表面质量压铸件表面粗糙度应符合 GB/的规定。
压铸件表面不允许有裂纹、欠铸、疏松、气泡和任何穿透性缺陷。
压铸件表面允许有擦伤、凹陷、缺肉和网状毛刺等缺陷。
但缺陷必须符合表1规定。
压铸件的浇口、飞边、溢流口、隔皮、顶杆痕迹等应清理干净。
但允许留有痕迹。
若图样无特别规定,有关压铸工艺部分的设置,如顶杆位置、分型线的位置、浇口和溢流口位置等由生产厂自行规定。
压铸件需要特殊加工的表面,如抛光、喷丸、镀铬、涂覆、阳极氧化、化学氧化等须在图样上注明。
压铸件机加工平面加工后的表面质量不允许有影响使用的局部铸态表皮存在。
不允许有超过表2规定的孔穴存在。
压铸件机械加工螺纹的表面质量压铸件机械加工螺纹的头两扣不允许有任何缺陷,其余部分螺纹不允许有表3所规定的孔穴缺陷压铸件若能满足其使用性能要求,则压铸件本质缺陷不作为报废的依据。
压铸件内部不允许有冷隔缺陷。
压铸件内部允许有气孔、疏孔、夹杂等缺陷,但孔穴缺陷最大直径不超过壁厚的1/8,孔穴数量在任何剖面上不超过2个/cm2。
重要压铸件的受力部位须进行解剖检查,符合表6中的规定。
3试验方法及检验规则化学成分铝合金化学成分的检验方法,检验规则和复检应符合GB/T15115的规定。
化学成分的试样也可取自压铸件, 但必须符合 GB/T15115的规定。
力学性能力学性能的检验方法,检验频率和检验规则应符合 GB/T15115 的规定。
采用压铸件本体为试样时,切取部位的尺寸、测试形式由供需双方商定。
压铸件几何尺寸的检验可按检验批量抽检或按GB2828 、GB2829 的规定进行,检验结果应符合本标准的规定。
压铸件表面质量的出厂检验应逐件检查,检验结果应符合本标准的规定。
压铸件表面粗糙度按 GB/的规定执行。
压铸件需抛光加工的表面按 GB/T 的规定执行。
压铸质量控制与检验标准

1.压铸生产的质量控制1.压铸生产的质量控制1.1环境铸造生产中涉及的主要工作场地、空间和厂房凡影响铸件质量的主要因素均属环境控制范围。
不同工艺方法或不同铸件材料之间凡不能交叉生产的工作场地应分开或隔离。
如压力铸造和熔模铸造、砂型铸造、有色金属和黑色金属、铝合金和镁合金、真空和非真空熔化浇铸之间的工作场地等。
铸造厂房和工作场地的温度,一般不低于10℃。
新设计的铸造厂房应符合TJ16的TJ36规定。
工作间或厂房内的光照度应不低于75LX。
工作间或厂房内的噪声应符合GBJ87规定.熔化和浇铸场地,地面不允许有积水。
厂房应保持良好的通风,有污染的操作区,应按有关规定进行处理。
压铸生产中释放的有害物质见表9—1其有害物质的毒理特性及极聚允许浓度见表9—2。
1.2设备、仪表和工装铸造过程中直接影响铸件质量的主要设备、仪表和工装应进行质量控制。
应控设备、仪表和工装的目录由技术部门会同使用部门提出,并规定检定项目和周期.其使用、维护、保养和管理的质量控制,工厂应规定通用量具、衡器具的使用管理控制,工厂应有计量管理规范。
设备、仪表和工装应有检定合格证,合格证应注明检定日期、有效期和责任者。
不合格者应停用或作待修等标记.生产现场不准使用未经检定合格或超过检定有效周期的器具、设备、仪表和工装。
精密、关键和贵重的仪表、设备和模具,应建立使用登记和履历本。
铸造机械设备每年应进行一次技术指标检查,技术指标应不低于工艺要求。
熔炼浇注设备每年应进行一次技术指标检查,如设备的熔化功率和熔化速度。
铸造用加热炉的类别应符合有关标准规定。
铸件热处理加热炉,按铸件材料相应的热处理技术标准规定控制。
用于重要的测温与控温的仪表最好配有温度显示自动记录装置。
安全自动报警装置。
复验报告应存档备查,材料发往生产车间时,应附有质量证明及复验报告。
使用单位对主要材应分类存放,妥善保管,防止混批混料、锈蚀和污染。
浇冒口和废铸件等回炉料应及时处理,分类存放,放置标志,严防混料。
压铸件检验标准

1.0
进料检验标准
压铸件检验标准
一.适用范围:
所有外购压铸件入厂之检验依据。
二.权责部门:
品保部IQC
三.时机:
供应商材料之进料检验。
四.检验项目及执行标准:
检验项目Leabharlann 检验标准检查方法/量具
缺点分类
Ⅱ水准
AQL%
CR
MA
MI
规格尺寸(配合尺寸)
依图面要求
视图面精度要求而定
√
1.0
外观检查
1.不得有流痕、花纹、网状毛翅、缩孔缩松、气孔、冷隔、脆性、硬点等压铸缺陷;
Ⅱ水准
AQL%
CR
MA
MI
物理性能测试(抗拉伸、抗疲劳、抗弯曲强度)
须符合图面及设计之要求(视品质状况不定期而为之)
托处实验
√
1.0
形位误差检查
同心度、端面跳动等须符合图面要求
偏摆仪/百分表及专用治具
√
1.0
精加工表面粗糙度检查
须符合图面要求
比对样块
手感
√
2.5
回转件之平衡度检查
须符合设计之规定
专用治具
2.颜色符合图面要求及色样
目视
√
2.5
表面处理
依图面之要求
目视
√
2.5
附着力测试
用小刀划横直各6条间隔2mm小方格,用透明胶带粘上90秒后撕掉胶带检视表面层,不得有脱落现象
小刀/直尺
胶带
√
1.0
化学成分试验
须符合图面之要求,视品质状况不定期而为之
托外实验
√
1.0
检验项目
检验标准
检查方
法/量具
缺点分类
铸件质量要求

铸件质量要求分级及公差压铸件的分级1.1铸件表面分级压铸件表面使用范围分为三级,见表1:表1压铸件表面分级表华为公司的产品一般为Y2、Y3级要求的表面。
1.2压铸件缺陷特征定义压铸件常见缺陷特征定义如表2所示:表2压铸件压铸件常见缺陷特征定义1.3表面质量1.压铸件表面粗糙度应符合GB 6060.1-1985的规定。
2.压铸件不允许有裂纹、欠铸等任何穿透性缺陷。
3.压铸件允许有拉伤、凹陷、网状毛刺等缺陷。
但其缺陷的程度和数量应符合附录C的要求。
4.铸件的浇口、飞边、溢流口、隔皮、顶杆痕迹等应清理干净、平齐,但允许留有不刮手的痕迹。
5.若图样无特别规定,有关压铸工艺部分的设置,如顶杆位置、分型线的位置、浇口和溢流口的位置等可由生产厂自行规定。
6.压铸件需要特殊加工的表面,如抛光、喷丸、镀铬、涂覆、阳极氧化、化学氧化等以图样上的标注或供需双方商定的内容、样件为准。
内部质量对压铸件的气密性、液压密封性、热处理、高温涂覆、内部缺陷(气孔、疏松等)及本标准未列项目有要求时,以华为公司图样标注的技术要求为准。
后处理:由于压铸件的残余应力分布不均匀会使有些零件产生变形,当华为公司有要求时,供应商必须进行相应的后处理(如:校形后时效处理等)以达到华为公司的要求。
1.4压铸件尺寸公差表3压铸件尺寸公差数值注:12、对锌合金压铸件选取范围:CT4~CT6,一般情况取CT5级。
1.5平面度公差(形状公差)压铸件的表面形状公差值(平面度和拔模斜度除外)应在有关尺寸公差值范围内:表4平面度公差(mm)1.6位置公差表5位置公差平行度、垂直度、端面跳动公差(mm)表6同轴度、对称度公差(mm)附录C:压铸件表面质量1.7表面质量要求:表7压铸件表面质量要求表注:对于1级及有特殊要求的表面,只允许有经抛光或研磨能去除的缺陷。
1.8压铸件机械加工面质量判定:表8压铸件机械加工后加工面上允许孔穴缺陷表。
压铸件检验标准
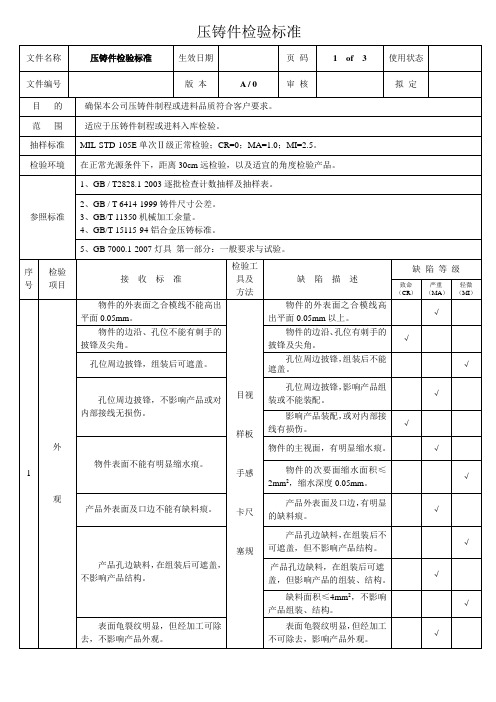
花纹痕迹组装后不能遮盖,其长≤3mm,宽≤0.09mm,深≤0.04mm。
花纹纹痕迹组装后不能遮盖,其长≤4mm,宽≤0.1mm,深≤0.05mm。
√
产品表面及口边、孔位不能有变形现象。
产品表面及口边有明显变形及凹凸不平现象。
√
孔位变形,但不影响组装或组装后可遮盖。
√
孔位变形,影响组装或不能遮盖。
√
机加工后,装配配合性良好且密封度(间隙)小于0.05mm。
装配困难及密封度(间隙)大于0.05mm。
√
孔位不能有打偏、打穿或漏打孔现象。
孔位偏、打穿或漏打孔。
√
备注
1、上述未列出来的检验标准,检验时,请依照“客户要求”、“客户样品”进行验收。
2、本检验标准未尽项目,需检验时可参照行业标准、国标或工程技术文件要求。当检验标准的检验项目在技术要求中未作规定时,可不作检验要求。
产品孔边缺料,在组装后可遮盖,不影响产品结构。
产品孔边缺料,在组装后不可遮盖,但不影响产品结构。
√
产品孔边缺料,在组装后可遮盖,但影响产品的组装、结构。
√
缺料面积≤4mm2,不影响产品组装、结构。
√
表面龟裂纹明显,但经加工可除去,不影响产品外观。
表面龟裂纹明显,但经加工不可除去,影响产品外观。
√
压铸件检验标准
参照标准
1、GB / T2828.1-2003逐批检查计数抽样及抽样表。
2、GB / T 6414-1999铸件尺寸公差。
3、GB/T 11350机械加工余量。
4、GB/T 15115-94铝合金压铸标准。
5、GB 7000.1-2007灯具第一部分:一般要求与试验。
序号
检验
压铸件产品外观质量验收标准
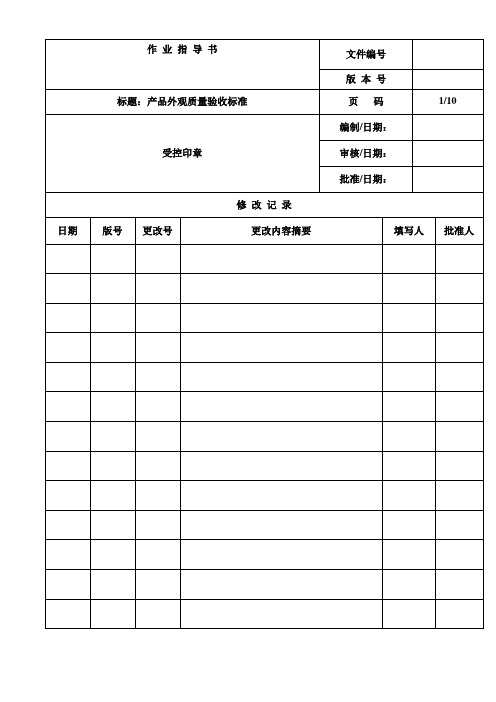
1 目的本标准定义来料或成品外观质量的基本要起,并作为允收/拒收准则。
2 适用范围来料或成品。
3 检测面的分级:A级面:使用者经常看到的面,如产品的上表面、正面、需要丝印的面等。
B级面:在不移动的情况下,使用者偶尔能看到的面,如产品的后面、侧面等。
C级面:产品在移动或被打开时才能看到的面,如产品的底面,内部零件的表面等。
4 检测条件4.1、所有检验均应在正常照明,并模拟最终使用条件下进行。
检测过程中不使用放大镜,所检验表面和人眼呈45°角。
A级面在检测时应转动,以获得最大反光效果。
B级面和C级面在检测期间不必转动。
光源=40W荧光灯500毫米了4.2、A级面停留10秒,B级面停留5秒,C级面停留3秒。
5 金属件外观检验标准5.1 允收总则5.1.1 可接受的缺陷不能影响该零件的装配和功能,否则将被拒收。
5.1.2 缺陷允收定义了900mm2的区域内各类缺陷的最大允收数量。
但是,两个区域或两个以上明显缺陷不能相连。
5.2缺陷定义5.2.1生锈/氧化:暴露在空气中的金属表面发生的化学反应,包括变黄以及出现其它异常。
5.2.2变色:底色或预期的颜色发生改变,或零件表面的颜色不一致。
5.2.3刮伤:零件表面的呈条状的浅沟,包括露底与不露底。
5.2.4压痕:由尖锐物件在零件表面造成的沟痕,指甲能够感受到。
5.2.5镀痕/流痕:由于镀层厚度不均匀造成零件表面上波纹状或条状异常的区域。
5.2.6痕迹:指基体材料的小坑、折弯痕或其他痕迹,涂装后仍无法消除。
5.2.7灰尘或油脂:在制造过程中产生并留在零件表面上的赃污(未清洗)。
5.2.8斑点/颗粒:涂装面或零件表面任何非预期的异物。
5.2.9凹坑:零件表面弹坑状的缺陷。
5.2.10模压痕:因成形模具在零件表面造成的工艺痕,所有零件的模压痕的位置和大小都一样,均匀分布5.3 缺陷允收表每个面的缺陷数量不能超过允收的界限,如下表所示:缺陷允收表6 液体/粉末喷涂外观标准6.1允收总则6.1.1所有的等级面应当喷涂完好且满足颜色、光泽度、厚度、附着力等方面的要求。
压铸件检验标准(1)

特殊检验:S-4
AQ L :0.65
4.称重测试:产品重量在技术规格书要求±3%以内(喷漆前称重)
电子称
抽样标准
备注
2
包装
1.包装标示内容与实际产品相符,标示内容正确、有相对应的物料编号
目视
特殊检验:S-4
AQ L :1.0
2.包装有防护措施:木箱、纸板、纸箱、气泡袋等防护
目视
3
结构尺寸
1.产品整体尺寸、开孔尺寸、在图纸要求的公差范围之内
数显卡尺/通止规等
一般检验水平:Ⅰ
A Q L :0.65
2.产品开孔位置、凹槽位置等符合图纸要求
A Q L :1.0
5.产品表面毛边、毛刺≤0.1mm
目视/手感
6.表面喷漆均匀、灯体灌胶处喷漆要求:边框沾漆宽度≤5mm、沾染漆点的宽度不得超出25mm
目视
7.支撑柱不得有缺损
8.根据技术规格书检验产品本体及文字是否完整
目视/见规格书
9.产品表面无脏污、杂质现象
目视
序号
检验项目
检验内容与标准
检验方式/测量仪器
数显卡尺/通止规等
3.有Logo与文字的产品,漆膜厚度适中,不能影响商标的清晰度。
数显卡尺/图纸
4.产品的水平面变形度最大值应≤2mm。
水平平面/塞规
4
实装
1.与相关配件实装结构良好,无发现试装后缝隙过大、易松动或锁不紧现象等
相关配件
特殊检验:S-2
AQ L :1.0
2实装时无发现产品、相关配件有损伤、匹配性差等现象
*、目的:关于进厂压铸件检验标准,达成一致质量目标。
*、适用用ቤተ መጻሕፍቲ ባይዱ围:所有压铸件检验。
2.6.3压铸件质量检验

0.20
0.10
0.30
0.15
0.40
0.20
0.55
0.25
0.80
0.30
1.10
0.40
1.50
0.50
2.00
0.70
4 压铸件几何尺寸和质量的检测
平等度、垂直度、端面跳动公差(GB/T15114-94) (mm)
被测部位和基准部位在同一半模 被测部位和基准部位不在同一半模
被测量部
内
内
位在测量 二个部位 二个部位中 二个部位 二个部位 二个部位中 二个部位
压铸模具设计与制造
任务描述
压铸件质量检验
主讲人:柯春松
内容提要
任务1
1. 压铸件质量标准 2. 压铸件检验项目、内容与方法 3. 压铸件分类及检验分类项目 4. 压铸件几何尺寸和质量的检测
1 压铸件质量标准
1.压铸件质量标准 压铸件的质量标准和零件图、铸件图一样,
同步于判断铸件合格与否的质量依据。 从世界范围来看,目前尚无统一的压铸件国
例抽样称重检验。
4 压铸件几何尺寸和质量的检测
5.压铸件表面粗糙度的评定和浇口、溢流槽、 顶杆痕印余根
•
表面粗糙度是衡量铸件表面质量的重要
指标。铸造表面粗糙度用表面轮廓算术平均
偏差Ra(单位为um)进行分级,并用全国铸造
标准化技术委员会监制的铸造表面粗糙度比
较样块进行评定。
4 压铸件几何尺寸和质量的检测
(1)压铸件表面粗糙度的评定方法
• ①比较样块应能表征被检铸件的合金种类 和铸造方法,其质量应符合GB/T6060.1-1997 的规定,表面不得有锈蚀、油污等铸造缺陷, 以及表面粗糙度特征以外的其它表面特征。
压铸件表面质量

压铸件表面质量分级及缺限表<1>压铸表面质量分级级别使用范围备注1要求高的表面,需镀铬,抛光表面,相对运动的配合面,危险应力区面Ra1.6, 一般采用后加工处理,如抛光,机加2涂装要求一般或要求密封的表面,以及装配接触面Ra3.23保护性涂装表面及紧固接触面Ra6.3表<2> 表面缺陷要求(JB2702-80)缺陷名称缺陷范围表面质量级别备注1级 2级 3级流痕深度<=(mm)0.05 0.07 0.15面积不超过总面积比(%)5 15 30冷隔深度<=(mm) 不允许1/5壁厚1/4壁厚1. 同一部位的对应面不允许同时存在2. 长度指缺陷流向的展开长度长度/最大轮廓尺寸1/10 1/5擦伤深度<=(mm)0.05 0.1 0.25除一级表面外,浇口部位允许增加1倍面积不超过总面积比(%)3 5 10凹陷凹入深度<=(mm)0.1 0.3 0.5边角缺陷深度铸件边长<=100mm0.3 0.5 1.0残陷长度不应超过边长的5%铸件边长>100mm0.5 0.8 1.2各类缺陷总和面积不超过总面积(%)5 30 501.1.1 机加面机加面粗糙度可做到Ra1.6, 压铸件内部由于砂孔缺陷,在去除加工余量后,加工表面会有砂孔,根据标准JB2702-80,可允许的砂孔见表<5.6>。
表<1> 机加面允许砂孔缺陷规定加工面面积(cm2)1级 2级 3级最大直径(mm)最大深度(m’m)最多个数最大直径(mm)最大深度(m’m)最多个数最大直径(mm)最大深度(m’m)最多个数~25 0.8 0.5 3 1.5 1.0 3 2.0 1.5 3>25~60 0.8 0.5 4 1.5 1.0 4 2.0 1.5 4 >60~150 1.0 0.5 4 2.0 1.5 4 2.5 1.5 4 >150~350 1.2 0.6 5 2.5 1.5 5 3.0 2.0 6。
压铸件检验标准OK(正式发行).
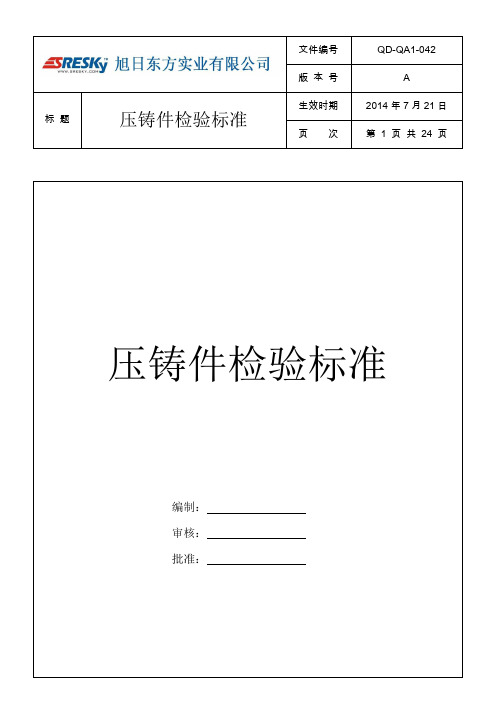
行浸渗和修补(如焊补,变形校整等)处理.
4.试验方法及检验规则
4.1压铸件几何尺寸的检验可按检验批量抽验或按GB2828,GB28210的规
定进行,抽检结果必须符合标准3.3的规定.
4.2压铸件表面质量要逐一检查,检查结果应符合本标准3.3的规定.
4.3压铸件表面粗糙度按GB6060.1的规定执行.
4.4压铸件需抛光加工的表面按GB6060.4的规定执行,
4.5压铸件需喷丸,喷砂加工的表面按GB6060.5的规定执行.
4.6压铸件内部质量的试验方法检验规则由供需双方商定,可以包括:X射
线照片,无损探伤,耐压试验,金相图片和压铸件剖面等,其检难结果应符
W≤0.20mm,L≤50mm,H≤0.4,DS≥100mm,,N≤3 ,或参照样板
W≤0.20mm,L≤100mm,H≤0.8,DS≥100mm,,N≤5,或参照样板
可接受,但不能对产品造成功能性影响,具体可参照样板.
凹陷、压伤、碰伤
D≤2mm,H≤0.35mm,DS≥100 mm,N≤2,或参照样板
代码
名称
代码
名称
N
数目
D
直径(mm)
L
长度(mm)
H
深度(mm)
W
宽度(mm)
DS
距离(mm)
S
面积(mm2)
T
厚度(mm)
5.外观检验项目和判定标准
缺陷名称
表面质量级别(平方毫米)90001– 250000
备注
A级面
B级面
C级面
磨花、磨痕
L≤50mm,W≤0.2mm,DS≥100mm,N≤3,
- 1、下载文档前请自行甄别文档内容的完整性,平台不提供额外的编辑、内容补充、找答案等附加服务。
- 2、"仅部分预览"的文档,不可在线预览部分如存在完整性等问题,可反馈申请退款(可完整预览的文档不适用该条件!)。
- 3、如文档侵犯您的权益,请联系客服反馈,我们会尽快为您处理(人工客服工作时间:9:00-18:30)。
凡谷压铸件质量标准————————————————————————————————作者: ————————————————————————————————日期:ﻩ凡谷压铸件质量标准范围:本标准规定了本公司压铸件的质量保证、验证方法及检验规则和交货条件。
本标准适用于压铸件产品的进货验收、生产过程中产品质量的判定,外购(协)件的验收亦适用本标准,也可作结构设计的指导文件。
注:本标准为本公司压铸件质量通用标准,若客户标准与本标准不符的,以客户标准为准。
简介:本标准规定了本公司对压铸件的质量要求、检验方法、检验规则及交货条件,是本公司压铸件质量判定的依据。
关键词:压铸件引用文件:下列文件中的条款通过本规范的引用而成为本规范的条款。
凡是注日期的引用文件,其随后所有的更改单(不包括勘误的内容)或修订版均不适用于本规范,然而,鼓励根据本规范达成协议的各方研究是否可使用这些文件的最新版本。
凡是不注日期的引用文件,其最新版本适用于本规范。
序号文件编号文件名称1 GB/T13818-2009 压铸锌合金标准2 GB/T 1182-2008 形状和位置公差通则、定义、符号和图样表示法3 GB/T15115-2009 压铸铝合金标准4 GB/T 15114-2009 铝合金压铸件标准5 GB/T13821-2009 锌合金压铸件标准6GB/T 6414-1999铸件尺寸公差7GB/T6060.1-1997 表面粗糙度比较样块铸造表面8 GB/T 6060.3-2008 表面粗糙度比较样块电火花、抛(喷)丸、喷砂、研磨、锉、抛光加工表面9 GB/T5678-1985 铸造合金光谱分析取样方法10 GB/T 2828.1-2003 计数抽样检验第一部分:按接收质量限(AQL)检索逐批检验的抽样计划11 GB/T 2829-2002 周期检查计数抽样程序及抽样表(适用于生产过程过程稳定性的检查)12压铸件的分级本公司的产品一般承受轻载荷,主要控制及检验表面质量、化学成分、尺寸公差。
1.1铸件表面等级压铸件表面按使用范围分为三级,见表1:表1压铸件表面分级表级别符号检验项目表面粗糙度1 Y1 工艺要求高的表面——要求镀、抛光、研磨的表面,相对运动的配合面,危险应力区表面。
Ra 1.62 Y2 要求一般或要求密封的表面,阳极氧化以及装配接触面等。
Ra 3.23Y3 保护性的涂覆表面及紧固接触面,油漆打腻表面及其它表面。
Ra 6.3 本公司的产品一般为Y2、Y3等级要求的表面。
1.2压铸件缺陷特征定义压铸件常见缺陷特征定义如表2所示:表2压铸件常见缺陷特征定义缺陷类别缺陷名称特征定义表面缺陷拉伤沿开模方向铸件表面呈现条状的磨擦痕迹,有一定深度,严重时为面状伤痕。
另一种是金属液与模具产生焊合、粘附,以致出模时铸件表面多肉或缺肉气泡铸件表面有米粒大小的隆起,并在隆起的皮下形成空洞裂纹铸件表面有呈直线状或波浪形的纹路,狭小而长,在外力作用下有发展趋势变形由于收缩不均或外力导致压铸件几何形状与图纸不符流痕合金液直接冲击型芯时,在铸件表面形成的与合金液流动方向一致的呈不连续的印痕或折纹花纹压铸件表面明显可见的与金属基体颜色不一样无方向性的纹路。
无发展趋势冷隔在压铸件表面,明显、不规则、下陷的线形纹路(有穿透与不穿透两种)。
形状细小而狭长,有时交接边缘光滑,有断开的可能网状毛刺压铸件表面有网状发丝一样凸起或凹陷的痕迹,随压铸次数增加而不断扩大和延伸凹陷铸件的厚大部分因壁厚不均匀使收缩不均匀,而产生的零件表面下凹现象欠铸合金液未充分填满型腔,使铸件腔型不完整而造成的缺陷飞边、毛刺在分型面边缘出现金属薄片,或粗糙、锋利的棱角粘附物痕迹其它材料(如机器润滑油,离型剂等)的加入使铸件表面上呈现出不同于基体金属颜色的斑点和痕迹脱皮铸件表面部分与基体剥离的现象内部缺陷气孔因卷入气体而导致的压铸件内部的孔状缺陷,解剖后外观检查或探伤检查,气孔具有光滑的表面、形状为圆形缩孔、缩松解剖或探伤检查,孔洞形状不规则、不光滑、表面呈暗色。
大而集中为缩孔;小而分散为缩松脆性铸件基体金属晶粒过于粗大或极小,使铸件易断裂或破碎渗漏铸件经耐压试验,产生漏气、渗水硬质点机械加工过程或加工后外观检查或金相检查:铸件上有硬度高于金属基体的细小质点或块状物使刀具磨损严重,加工后常常显示出不同的亮度2 技术要求2.1化学成分压铸件的化学成分对压铸件的力学性能、抗腐蚀能力都有很大的影响。
本公司所有压铸件的化学成分都应该符合相应牌号的规定。
其中:铝合金化学成分要符合GB/T15115-2009的规定,见附录A 表3;锌合金化学成分要符合GB/T13818-2009的规定,见附录A 表4。
2.2力学性能1.采用压铸试样检验时:铝合金压铸件的力学性能要符合GB/T 15115-2009(附录A 表3)的规定;锌合金压铸件的力学性能要符合GB/T 13818-2009(附录A 表4)的规定。
2.采用压铸件本体检验时:其指定部位切取试样的力学性能不得低于单铸件试样的75%;若有特殊要求,以本公司图样要求为准。
2.3压铸件尺寸2.3.1 压铸件的几何形状和尺寸要满足本公司设计人员认可的图样的要求。
2.3.2 尺寸公差在图样上无特殊标注时应按不低于GB 6414-1999(附录B 7.1)的规定执行。
2.3.3 形位公差在图样上无特殊标注时按附录B 7.3的规定执行,其标注方法按GB1182-2008的规定。
本对压铸件的平面度要求较严,按附录B 7.2的规定执行。
2.3.4压铸件的尺寸公差不包括铸造斜度。
对不加工表面要求:包容面以小端为基准,被包容面以大端为基准;对待加工表面要求:包容面以大端为基准,被包容面以小端为基准,有特殊规定和要求时,须在图样上注明。
2.4机械加工余量压铸件需要机械加工时,以图样要求为准。
未注加工余量按GB/T6414-1999的规定执行。
2.5表面质量2.5.1 压铸件表面粗糙度应符合GB 6060.1-1997的规定。
2.5.2 压铸件不允许有裂纹、欠铸等任何穿透性缺陷。
2.5.3 压铸件允许有拉伤、凹陷、网状毛刺等缺陷。
但其缺陷的程度和数量应符合附录C的要求。
2.5.4 铸件的浇口、飞边、溢流口、隔皮、顶杆痕迹等应清理干净、平齐,但允许留有不刮手的痕迹。
2.5.5 若图样无特别规定,有关压铸工艺部分的设置,如顶杆位置、分型线的位置、浇口和溢流口的位置等可由模具供应商自行规定。
2.5.6 压铸件需要特殊加工的表面,如抛光、喷丸、镀铬、涂覆、阳极氧化、化学氧化等以图样上的标注或供需双方商定的内容、样件为准。
2.6内部质量对压铸件的气密性、液压密封性、热处理、高温涂覆、内部缺陷(气孔、疏松等)及本标准未列项目有要求时,以本公司图样标注的技术要求为准。
3 质量保证3.1当本公司的图样或文件有规定时,供方对图样或文件规定的所有试验和检验负责。
图样或文件中无规定时,经本公司同意,供方可以用自己适宜的手段执行相应的试验和要求。
本公司有权对规定的任何试验和检验项目进行检验。
3.2根据压铸生产的特点,规定一个检验批量是指每台压铸设备在正常操作情况下一个班次的生产量。
设备、化学成份、铸型和操作连续性的任何重大变化都应该被认为是新的一个批量开始。
供方对每批压铸件都要随机或统计地抽样检验,确定是否符合总的质量合同或铸件图样地规定要求。
检验结果应予以记录。
3.3后处理:由于压铸件的残余应力分布不均匀会使有些零件产生变形,当本公司有要求时,供应商必须进行相应的后处理(如:校形后时效处理等)以达到本公司的要求。
4 试验方法和检验规则4.1化学成分1.压铸件化学成分的试样可取自压铸件,但检验方法、检验规则和复检应符合2.1的要求;2.光谱分析的取样方法可参照GB/T 5678-1985进行。
4.2力学性能力学性能的检验方法、检验频率和检验规则应符合2.2的要求。
4.3几何尺寸压铸件几何尺寸的检验可按本公司规定要求的检验批量抽验或按GB/T 2828.1-2003、GB/T2829-2002的规定进行,抽检结果必须符合本标准2.3的规定。
4.4表面质量4.4.1 应按附录C的要求逐件检查,检查结果应符合本标准2.5的规定。
4.4.2 表面粗糙度按GB/T6060.1-1997的规定执行。
4.4.3 需电火花、抛(喷)丸、喷砂、研磨、锉、抛光加工的表面按GB/T6060.3-2008的规定执行。
4.5内部质量压铸件内部质量的试验方法及检验规则由供需双方商定(可以包括:X射线、无损探伤、耐压试验、金相图片和压铸件剖面等),当发生争议时以本公司的图样或相关文件的要求为准。
检验结果应符合2.6 的规定。
5 压铸件的交付、包装、运输与储存5.1必要时,供应商需提供检验证明,用来说明每批压铸件的取样、试验和检验符合本标准的规定。
5.2格压铸件交付时,必须附有检验合格证。
其上应写明下列内容:产品名称、产品号、合金牌号、数量、制造厂名、检验合格印记和交付时间。
有特殊检验项目者,应在检验合格证上注明检验的条件和结果。
5.3压铸件的包装、运输与储存、可由供需双方商定,但铸件的包装应保证在运输过程中和存放时间内防止潮湿和机械损伤。
6 附录A:压铸合金的化学成分和力学性能6.1压铸铝合金的化学成分和力学性能表3压铸铝合金化学成分和力学性能表合金牌号合金代号化学成份力学性能(不低于) 硅铜锰镁铁镍钛锌铅锡铝抗拉强度伸长度硬度HB5/250/30YZA1Sil2YL102 10 ≤0.6≤0.6≤0.05≤1.2----≤0.3 -- -- 余220 260 13ADC12(日本牌号) 9.6 1.5≤0.5≤0.3≤1.3-- --≤0.3 ≤0.05≤0.01余228 1.4 74.112 3.5YZA1Si10Mg YL1048 ≤0.30.2 0.17≤1.0 -- --≤0.3≤0.05≤0.01余220 27010.5 0.5 0.3YZA1Si12Cu2 YL10811 1 0.30.4≤1.0≤0.05--≤1.0≤0.05≤0.01余240 1 90 13 2 0.9 16.2压铸锌合金的化学成分和力学性能表4压铸锌合金化学成分和力学性能表序号合金牌号合金代号化学成份(质量分数)(%)力学性能(不低于) 主要成分杂质(不大于)Al Cu MgZn FePb Sn CdCu抗拉强度(MPa)伸长度(%)布氏硬度HB5Ak/J/250/301ZZnAl4YYX040 3.5—0.02其余0.10.0050.0030.0040.25 250 26035 4.30.062ZZnAl4Cu1YYX0413.50.75 0.030.1 0.0050.003 0.004 ___ 270 1.4 74.1 394.3 1.25 0.083 ZZnAl4Cu3YYX0433.5 2.50.020.1 0.005 0.003 0.004___ 320 2 70424.3 3.00.067 附录B:压铸件公差7.1压铸件尺寸公差表5压铸件尺寸公差数值铸件基本尺寸公差等级大于至CT4CT5CT6 CT7—30.20 0.28 0.400.563 6 0.24 0.32 0.48 0.646 10 0.26 0.360.52 0.7410 16 0.28 0.380.54 0.7816 25 0.300.42 0.58 0.8225400.320.46 0.64 0.9040 630.36 0.50 0.70 1.063 100 0.400.56 0.78 1.1100160 0.440.62 0.88 1.2160 250 0.50 0.70 1.0 1.4250400 0.56 0.78 1.11.6400630 0.64 0.90 1.2 1.8 注:1、对铝合金压铸件选取范围:CT5~CT7,一般情况取CT6级;2、对锌合金压铸件选取范围:CT4~CT6,一般情况取CT5级。