压铸压铸件设计规范
压铸件结构设计规范
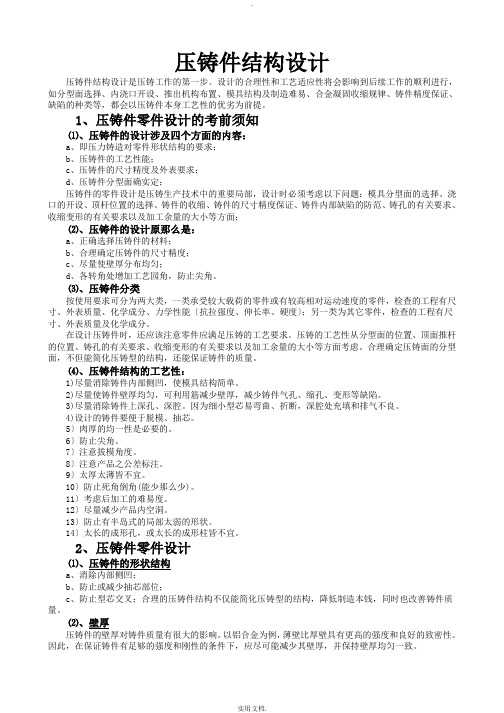
压铸件结构设计压铸件结构设计是压铸工作的第一步。
设计的合理性和工艺适应性将会影响到后续工作的顺利进行,如分型面选择、内浇口开设、推出机构布置、模具结构及制造难易、合金凝固收缩规律、铸件精度保证、缺陷的种类等,都会以压铸件本身工艺性的优劣为前提。
1、压铸件零件设计的考前须知⑴、压铸件的设计涉及四个方面的内容:a、即压力铸造对零件形状结构的要求;b、压铸件的工艺性能;c、压铸件的尺寸精度及外表要求;d、压铸件分型面确实定;压铸件的零件设计是压铸生产技术中的重要局部,设计时必须考虑以下问题:模具分型面的选择、浇口的开设、顶杆位置的选择、铸件的收缩、铸件的尺寸精度保证、铸件内部缺陷的防范、铸孔的有关要求、收缩变形的有关要求以及加工余量的大小等方面;⑵、压铸件的设计原那么是:a、正确选择压铸件的材料;b、合理确定压铸件的尺寸精度;c、尽量使壁厚分布均匀;d、各转角处增加工艺园角,防止尖角。
⑶、压铸件分类按使用要求可分为两大类,一类承受较大载荷的零件或有较高相对运动速度的零件,检查的工程有尺寸、外表质量、化学成分、力学性能〔抗拉强度、伸长率、硬度〕;另一类为其它零件,检查的工程有尺寸、外表质量及化学成分。
在设计压铸件时,还应该注意零件应满足压铸的工艺要求。
压铸的工艺性从分型面的位置、顶面推杆的位置、铸孔的有关要求、收缩变形的有关要求以及加工余量的大小等方面考虑。
合理确定压铸面的分型面,不但能简化压铸型的结构,还能保证铸件的质量。
⑷、压铸件结构的工艺性:1)尽量消除铸件内部侧凹,使模具结构简单。
2)尽量使铸件壁厚均匀,可利用筋减少壁厚,减少铸件气孔、缩孔、变形等缺陷。
3)尽量消除铸件上深孔、深腔。
因为细小型芯易弯曲、折断,深腔处充填和排气不良。
4)设计的铸件要便于脱模、抽芯。
5〕肉厚的均一性是必要的。
6〕防止尖角。
7〕注意拔模角度。
8〕注意产品之公差标注。
9〕太厚太薄皆不宜。
10〕防止死角倒角(能少那么少)。
压铸件结构设计规范
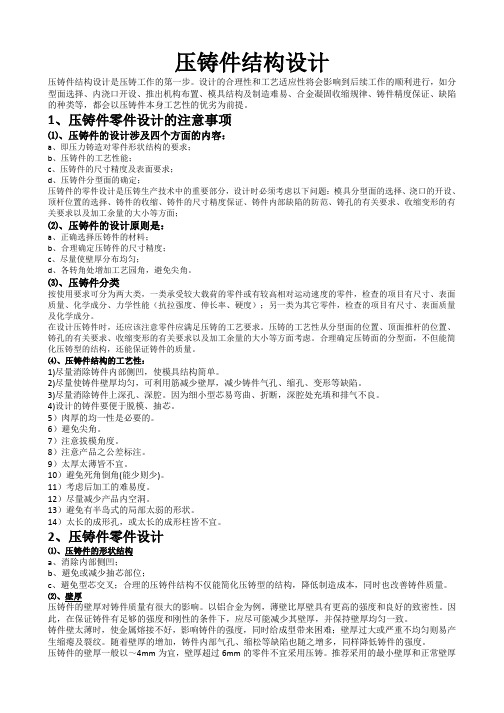
压铸件结构设计压铸件结构设计是压铸工作的第一步。
设计的合理性和工艺适应性将会影响到后续工作的顺利进行,如分型面选择、内浇口开设、推出机构布置、模具结构及制造难易、合金凝固收缩规律、铸件精度保证、缺陷的种类等,都会以压铸件本身工艺性的优劣为前提。
1、压铸件零件设计的注意事项⑴、压铸件的设计涉及四个方面的内容:a、即压力铸造对零件形状结构的要求;b、压铸件的工艺性能;c、压铸件的尺寸精度及表面要求;d、压铸件分型面的确定;压铸件的零件设计是压铸生产技术中的重要部分,设计时必须考虑以下问题:模具分型面的选择、浇口的开设、顶杆位置的选择、铸件的收缩、铸件的尺寸精度保证、铸件内部缺陷的防范、铸孔的有关要求、收缩变形的有关要求以及加工余量的大小等方面;⑵、压铸件的设计原则是:a、正确选择压铸件的材料;b、合理确定压铸件的尺寸精度;c、尽量使壁厚分布均匀;d、各转角处增加工艺园角,避免尖角。
⑶、压铸件分类按使用要求可分为两大类,一类承受较大载荷的零件或有较高相对运动速度的零件,检查的项目有尺寸、表面质量、化学成分、力学性能(抗拉强度、伸长率、硬度);另一类为其它零件,检查的项目有尺寸、表面质量及化学成分。
在设计压铸件时,还应该注意零件应满足压铸的工艺要求。
压铸的工艺性从分型面的位置、顶面推杆的位置、铸孔的有关要求、收缩变形的有关要求以及加工余量的大小等方面考虑。
合理确定压铸面的分型面,不但能简化压铸型的结构,还能保证铸件的质量。
⑷、压铸件结构的工艺性:1)尽量消除铸件内部侧凹,使模具结构简单。
2)尽量使铸件壁厚均匀,可利用筋减少壁厚,减少铸件气孔、缩孔、变形等缺陷。
3)尽量消除铸件上深孔、深腔。
因为细小型芯易弯曲、折断,深腔处充填和排气不良。
4)设计的铸件要便于脱模、抽芯。
5)肉厚的均一性是必要的。
6)避免尖角。
7)注意拔模角度。
8)注意产品之公差标注。
9)太厚太薄皆不宜。
10)避免死角倒角(能少则少)。
11)考虑后加工的难易度。
压铸件设计规范详解

压铸件设计规范详解压铸件是指利用压铸工艺将熔融金属注入模具中,经过凝固和冷却后得到的零件。
由于该工艺具有生产效率高、成本低、制造精度高等优点,被广泛应用于汽车、航空航天、电子等领域。
为了保证压铸件质量和安全性,需要遵循一系列的设计规范。
下面将详细介绍压铸件设计规范。
一、材料选择1.铝合金:常用的有A380、A383、A360等。
根据使用条件和要求,选择合适的铝合金材料,确保压铸件具有良好的强度和塑性。
2.压铸型腔材料:常用的有铜合金、热处理工具钢等。
要选择适当的材料,以耐高温和磨损。
二、模具设计1.模具设计必须满足压铸件的要求,保证铸件的尺寸精度和表面质量。
2.模腔设计要考虑到铸件收缩率、冷却速度等因素,以避免产生缺陷和变形。
3.合理安排模具冷却系统,保证压铸件内部和表面的冷却均匀。
三、尺寸设计1.压铸件的尺寸设计应符合产品技术要求和工艺要求,确保功能和安装的需要。
2.避免设计尺寸太小或太薄,以免产生破裂和变形。
3.设计保证良好的表面质量,避免设计中出现接触不良、挤压不足等问题。
四、壁厚设计1.壁厚不应过薄,以免影响产品的强度和刚性。
2.避免壁厚过大,以减少成本和缩短冷却时间。
3.边缘和角部应注意壁厚过渡,避免产生应力集中。
五、设计角度和半径1.设计时应根据铝合金的流动性选择合适的角度和半径。
2.避免设计尖锐角度和太小的半径,以免产生气孔和挤压不足。
3.设计角度和半径应保持一定的一致性,避免因设计不当导致铸件变形和收缩不均匀。
六、设计放射状构件1.当压铸件具有放射状构件时,要合理设计放射状梁的位置和数量,以充分利用材料,并减少成本。
2.注意放射状构件的设计不应影响整体结构的强度。
七、设计排气系统1.设计时要考虑到铸件内部的气孔、气泡等气体排出问题。
2.合理安排和设计排气道,以保证良好的注模效果和铸件质量。
八、设计孔和螺纹1.设计孔和螺纹时应遵循标准规范,确保质量和安装的可靠性。
2.孔和螺纹的位置和尺寸应符合产品要求,保证压铸件的功能和使用要求。
压铸件产品技术标准规范

螺纹代号——螺纹公差带代号(中径、顶径)——旋合长度
l)公差带代号由数字加字母表示(内螺纹用大写字母,外螺纹用小写字母),如 7H、6g等,应特别指出,7H,6g等代表螺纹公差,而H7,g6代表圆柱体公差代号。
2)旋合长度规定为短(用S表示)、中(用N表示)、长(用L表示)三种。一般情况下,不标注螺纹旋合长度,其螺纹公差带按中等旋合长度(N)确定。必要时,可加注旋合长度代号S或L,如“ M20-5g6g-L”。特殊需要时,可注明旋合长度的数值,如“M20-5g6g-30”。
Rcl/2表示英制螺纹密封锥管螺纹,尺寸代号1/2in,右旋。
2.5
2.5.1公制螺纹
公制细牙内螺纹
公制粗牙内螺纹
规格
标准径
6H精度
规格
标准径
6H精度
Dmax
Dmin
ax
Dmin
M2.5*0.35
2.15
2.184
2.121
M1.4*0.3
1.10
1.16
1.075
M3.0*0.35
2.65
2.684
6.25
6.378
6.188
M4.0*0.7
3.30
3.422
3.242
M8*0.75
7.25
7.378
7.188
M4.5*0.75
3.75
3.878
3.688
M8*1.00
7.00
7.153
6.917
M5.0*0.8
4.20
4.334
细牙
管螺纹
非螺纹密封
G
管道联接中的常用螺纹,螺距及牙型均较小,其尺寸代号以in为单位,近似地等于管子的孔径。螺纹的大径应从有关标准中查出,代号R表示圆锥外螺纹,Rc表示圆锥内螺纹,Rp表示圆柱内螺纹
压铸件产品技术规范标准

压铸件产品技术规范标准1. 引言压铸件是一种具有高精度、高强度和高复杂性的金属铸件,广泛应用于汽车、电子、航空航天等行业。
为了确保压铸件产品质量的稳定和一致性,制定了一系列的技术规范标准,以规范压铸件的生产和质量控制过程。
本文将介绍压铸件产品技术规范标准的主要内容,包括材料要求、尺寸和形状公差、表面处理、硬度要求、力学性能要求等方面。
2. 材料要求压铸件的材料选择对产品的质量和性能具有重要影响。
根据不同的应用领域和要求,压铸件常用的材料包括铝合金、锌合金、镁合金等。
2.1 铝合金铝合金是最常用的压铸件材料之一,具有良好的流动性、加工性能和机械性能。
常用的铝合金包括ADC12、A380等,其化学成分和物理性能应符合相应的标准。
2.2 锌合金锌合金是另一种常用的压铸件材料,具有良好的液态流动性和冷却收缩性能。
常用的锌合金有Zamak 3、Zamak 5等,其化学成分和物理性能应符合相应的标准。
2.3 镁合金镁合金具有重量轻、比强度高等特点,适用于要求重量轻、高强度的产品。
常用的镁合金有AZ91D、AM60B等,其化学成分和物理性能应符合相应的标准。
3. 尺寸和形状公差为了保证压铸件的尺寸精度和形状一致性,对其尺寸和形状设定了公差要求。
公差的选择应根据产品的具体要求和应用领域来确定。
4. 表面处理压铸件在生产过程中常常需要进行表面处理,以提高其耐腐蚀性、耐磨性和装饰性。
常见的表面处理方法包括喷漆、电镀、阳极氧化等。
5. 硬度要求压铸件的硬度是其材料和工艺的重要指标之一,对产品的强度、耐磨性、耐腐蚀性等性能有直接影响。
硬度测试应按照相应的标准进行,测试结果应符合规定的要求。
6. 力学性能要求压铸件的力学性能包括抗拉强度、屈服强度、延伸率等指标。
根据产品的具体要求和应用领域,制定了相应的力学性能要求。
力学性能测试应按照相应的标准进行,测试结果应符合规定的要求。
7. 检验和质量控制为了确保压铸件产品的质量稳定和一致性,需要进行严格的检验和质量控制。
压铸产品结构设计的工艺要求

压铸类产品结构设计的工艺要求
压力铸造是将熔融状态或者(半)熔融状态合金浇入压铸机的压室,以极高的速度在高压的作用下充填在压铸模的型腔内,使熔融合金在高压下冷却凝固成型的方法。
常见的压铸材料包括:铝合金、锌合金、镁合金、铜合金等,铝合金又分为铝镁合金、铝铜合金、铝锌合金、铝硅合金等。
压铸类产品在结构设计时的工艺要求注意的几个方面。
①压铸件的厚度
压铸件产品的厚度一般指料厚,料的厚薄直接影响压铸的难易,一般情况下,压铸产品的料厚≥0.8mm,具体料厚根据产品设计。
压铸产品不会因为局部料厚产生缩水的现象,相反,在一些尖钢薄钢处要加料填充,避免模具强度低而损坏。
压铸产品的外观面局部最小料厚≥0.7mm,非外观面局部最小料厚度建议≥0.4mm,太薄会导致填充不良、无法成型,薄的区域面积也不能太大,否则无法成型。
②压铸件的拔模角
压铸件与塑胶件一样,内外表面都需要拔模角,压铸件外表面的
拔模角一般在1°~3°,内表面拔模角比外表面拔模角大一点,方便产品出模。
③压铸件的后续加工
压铸件有时达不到设计的要求,需要后续加工。
其中螺丝柱中的螺纹就是后续加工的,在设计产品时只需留出底孔就可以。
压铸件有深孔时,压铸件需要做出孔位置,再通过后续机械钻孔加工完成。
压铸件有些表面要求较高的精度,一般也需要后续加工,在设计时可在需要后续加工的地方留出加工余量,加工余量一般在0.5mm 左右。
④压铸件产品不能变形,一般是螺丝连接,在做扣位连接,连接的对应产品必须能变形,如塑胶产品等。
⑤压铸件产品加强筋不能太多,对于薄壁类零件,需适当设计加强筋,以增加产品的抗弯强度,防止产品变形损坏。
铸造件压铸件尺寸公差标准规范
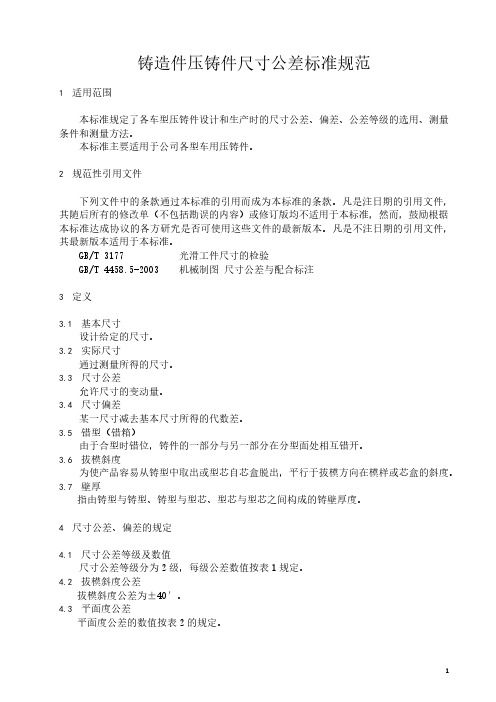
铸造件压铸件尺寸公差标准规范1 适用范围本标准规定了各车型压铸件设计和生产时的尺寸公差、偏差、公差等级的选用、测量条件和测量方法。
本标准主要适用于公司各型车用压铸件。
2 规范性引用文件下列文件中的条款通过本标准的引用而成为本标准的条款。
凡是注日期的引用文件,其随后所有的修改单(不包括勘误的内容)或修订版均不适用于本标准,然而,鼓励根据本标准达成协议的各方研究是否可使用这些文件的最新版本。
凡是不注日期的引用文件,其最新版本适用于本标准。
GB/T 3177 光滑工件尺寸的检验GB/T 4458.5-2003 机械制图尺寸公差与配合标注3 定义3.1 基本尺寸设计给定的尺寸。
3.2 实际尺寸通过测量所得的尺寸。
3.3 尺寸公差允许尺寸的变动量。
3.4 尺寸偏差某一尺寸减去基本尺寸所得的代数差。
3.5 错型(错箱)由于合型时错位,铸件的一部分与另一部分在分型面处相互错开。
3.6 拔模斜度为使产品容易从铸型中取出或型芯自芯盒脱出,平行于拔模方向在模样或芯盒的斜度。
3.7 壁厚指由铸型与铸型、铸型与型芯、型芯与型芯之间构成的铸壁厚度。
4 尺寸公差、偏差的规定4.1 尺寸公差等级及数值尺寸公差等级分为2级,每级公差数值按表1规定。
4.2 拔模斜度公差拔模斜度公差为±40′。
4.3 平面度公差平面度公差的数值按表2的规定。
表 1 (mm)注:(基本尺寸-25)÷25,取整数。
表2(mm)注:(基本尺寸-75)÷25,取整数。
4.4 位置度公差位置度公差的数值按表3的规定。
4.5 同轴度公差同轴度公差的数值按表4的规定。
(mm)注:(基本尺寸-75)÷25,取整数。
4.6 角度尺寸公差对于两个面之间有角度要求的,角度尺寸公差为±20′。
4.7 公差带的位置一般情况下,公差带应相对于基本尺寸对称分布,即一半在基本尺寸之上,一半在基本尺寸之下。
根据实际需要,公差带也可以不对称分布,在此情况下,公差应单独标注在基本尺寸的后面。
压铸件结构设计规范
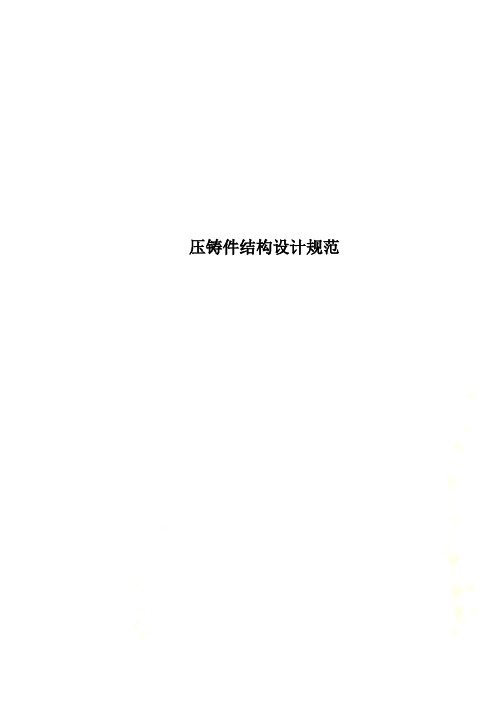
压铸件结构设计规范压铸件结构设计压铸件结构设计是压铸工作的第一步。
设计的合理性和工艺适应性将会影响到后续工作的顺利进行,如分型面选择、内浇口开设、推出机构布置、模具结构及制造难易、合金凝固收缩规律、铸件精度保证、缺陷的种类等,都会以压铸件本身工艺性的优劣为前提。
1、压铸件零件设计的注意事项⑴、压铸件的设计涉及四个方面的内容:a、即压力铸造对零件形状结构的要求;b、压铸件的工艺性能;c、压铸件的尺寸精度及表面要求;d、压铸件分型面的确定;压铸件的零件设计是压铸生产技术中的重要部分,设计时必须考虑以下问题:模具分型面的选择、浇口的开设、顶杆位置的选择、铸件的收缩、铸件的尺寸精度保证、铸件内部缺陷的防范、铸孔的有关要求、收缩变形的有关要求以及加工余量的大小等方面;⑵、压铸件的设计原则是:a、正确选择压铸件的材料;b、合理确定压铸件的尺寸精度;c、尽量使壁厚分布均匀;d、各转角处增加工艺园角,避免尖角。
⑶、压铸件分类按使用要求可分为两大类,一类承受较大载荷的零件或有较高相对运动速度的零件,检查的项目有尺寸、表面质量、化学成分、力学性能(抗拉强度、伸长率、硬度);另一类为其它零件,检查的项目有尺寸、表面质量及化学成分。
在设计压铸件时,还应该注意零件应满足压铸的工艺要求。
压铸的工艺性从分型面的位置、顶面推杆的位置、铸孔的有关要求、收缩变形的有关要求以及加工余量的大小等方面考虑。
合理确定压铸面的分型面,不但能简化压铸型的结构,还能保证铸件的质量。
⑷、压铸件结构的工艺性:1)尽量消除铸件内部侧凹,使模具结构简单。
2)尽量使铸件壁厚均匀,可利用筋减少壁厚,减少铸件气孔、缩孔、变形等缺陷。
3)尽量消除铸件上深孔、深腔。
因为细小型芯易弯曲、折断,深腔处充填和排气不良。
4)设计的铸件要便于脱模、抽芯。
5)肉厚的均一性是必要的。
6)避免尖角。
7)注意拔模角度。
8)注意产品之公差标注。
9)太厚太薄皆不宜。
10)避免死角倒角(能少则少)。
- 1、下载文档前请自行甄别文档内容的完整性,平台不提供额外的编辑、内容补充、找答案等附加服务。
- 2、"仅部分预览"的文档,不可在线预览部分如存在完整性等问题,可反馈申请退款(可完整预览的文档不适用该条件!)。
- 3、如文档侵犯您的权益,请联系客服反馈,我们会尽快为您处理(人工客服工作时间:9:00-18:30)。
表8 推荐机加工余量及其偏差(mm)
基本尺寸 每面余量
≤100
0.5
+0.4 -0.1
>100~250
0.75
+0.5 -0.2
> 250 ~400
1.0
+0.5 -0.3
> 400 ~630
1.5
+0.6 -0.4
> 630 ~1000
一般采用的加强筋的尺寸按图 1选取:
t1=2 t /3~t;t2=3 t /4~t;
R≥t/2~t;
h≤5t; r≤0.5mm
(t—压铸件壁厚,最大不超过
6~8mm)。
图1
四、铸孔和孔到边缘的最小距离
1)铸孔
压铸件的孔径和孔深,对要求不高的孔可 以直接压出,按表5。
表5 最小孔径和最大孔深
孔 合金 径
类别
锌合金 铝合金 镁合金 铜合金
最小孔径 d(mm)
技术上 一般的 可能的
1.5
0.8
2.5
2.0
2.0
1.5
4.0
2.5
最大孔深(mm)
盲孔
通孔
d>5 d<5 d>5 d<5
6d 4d 12d 8d
4d 3d 8d 6d
5d 4d 10d 8d
3d 2d 5d 3d
孔的最 小斜度
0~0.3% 0.5 % ~1%
我司现采用的脱模斜度一般取1.5°。
三、加强筋
加强筋的设置可以增加零件的强度和刚性,同时 改善了压铸的工艺性。 但须注意:
① 分布要均匀对称; ② 与铸件连接的根部要有圆角; ③ 避免多筋交叉; ④ 筋宽不应超过其相连的壁的厚度。当壁厚小 于 1.5mm时,不宜采用加强筋; ⑤ 加强筋的脱模斜度应大于铸件内腔所允许的 铸造斜度。
M8
2.30 2.75 3.18 3.63 4.70 5.58 7.45
d2
~
~
~
~
~
~
~
2.40 2.85 3.30 3.75 4.85 5.70 7.60
2.20 2.60 3.08 3.48 4.38 5.38 7.15
d3
~
~
~
~
~
~
~
2.30 2.70 3.20 3.60 4.50 5.50 7.30
设计带嵌件的压铸件的注意事项:
① 嵌件与压铸件的连接必须牢固,要求在嵌件上开槽、凸 起、滚 花等;
② 嵌件必须避免有尖角,以利安放并防止铸件应力集中; ③ 必须考虑嵌件在模具上定位的稳固性,满足模具内配合要求; ④ 外包嵌件的金属层不应小于1.5~2mm; ⑤ 铸件上的嵌件数量不宜太多; ⑥ 铸件和嵌件之间如有严重的电化腐蚀作用,则嵌件表面需要镀层保
外),使金属填充时流动平稳,气体容易 排出,并可避免因锐角而产生裂纹。对于 需要进行电镀和涂饰的压铸件,圆角可以 均匀镀层,防止尖角处涂料堆积。 压铸件的圆角半径R一般不宜小于1mm, 最小圆角半径为0.5 mm,见表2。铸造圆 角半径的计算见表3。
表2 压铸件的最小圆角半径(mm)
压铸合金 锌合金
压铸件的壁厚一般以2.5~4mm为宜,壁厚超过6mm的零 件不宜采用压铸。推荐采用的最小壁厚和正常壁厚见表1。
表1 压铸件的最小壁厚和正常壁厚
壁厚处的面积 a×b(cm2)
锌合金 最小 正常
铝合金
镁合金
壁 厚 h (mm)
最小 正常 最小 正常
铜合金 最小 正常
≤25 >25~100 >100~500
锌合金
0°10′ 0°15′ 0°15′ 0°45′
β
铝、镁合金 0°15′ 0°30′ 0°30′
1°
铜合金
0°30′ 0°45′
1°
1°30′
说明:①、由此斜度而引起的铸件尺寸偏差,不计入尺寸公差值内。 ②、表中数值仅适用型腔深度或型芯高度≤50mm,表面粗糙度在Ra0.1,大端 与小端尺寸的单面差的最小值为0.03mm。当深度或高度>50mm,或表面 粗糙 度超过Ra0.1时,则脱模斜度可适当增加。
②、计算后的最小圆角应符合表2的要求。
2) 脱模斜度
设计压铸件时,就应在结构上留有 结构斜度,无结构斜度时,在需要之处, 必须有脱模的工艺斜度。斜度的方向, 必须与铸件的脱模方向一致。推荐的脱 模斜度见表4。
表4 脱模斜度
合金
配合面的最小脱模 非配合面的最小脱
斜度
模斜度
α
外表面α 内表面β 外表面α 内表面β
>500
0.5
1.5
0.8
2.0
0.8
2.0
0.8
1.5
1.0
1.8
1.2
2.5
1.2
2.5
1.5
2.0
1.5
2.2
1.8
3.0
1.8
3.0
2.0
2.52.0ຫໍສະໝຸດ 2.52.54.0
2.5
4.0
2.5
3.0
我司现使用的绝大多数为铝压铸件,其壁厚一般控制在 2.0~2.5mm。
二、铸造圆角和脱模斜度
1)铸造圆角 压铸件各部分相交应有圆角(分型面处除
条件,铸孔到铸件边缘应保
持一定的壁厚,见图2。
b≥(1/4~1/3)t
图2
当t<4.5时,b≥1.5mm
五、压铸件上的长方形孔和槽
压铸件上的长方形孔和槽的设计推荐按表7 采用。
表7 长方形孔和槽(mm)
合金类别
最小宽度b 最大深度H
厚度h
铅锡合金
0.8 ≈10 ≈10
锌合金
0.8 ≈12 ≈12
铝合金
1.2 ≈10 ≈10
镁合金
1.0 ≈12 ≈12
说明:宽度b在具有铸造斜度时,表内值为小端部位值。
铜合金
1.5 ≈10 ≈8
六、压铸件内的嵌件
压铸件内采用嵌件的目的: ① 改善和提高铸件上局部的工艺性能,如
强度、硬度、耐磨性等; ② 铸件的某些部分过于复杂,如孔深、内
侧凹等无法脱出型芯而采用嵌件; ③ 可以将几个部件铸成一体。
d4
≥4.2 ≥5.0 ≥5.8 ≥6.7 ≥8.3 ≥10 ≥13.3
旋入深度t
t≥1.5d
我司现较为常用的自攻螺钉规格为M4与M5, 其采用的底孔直径如下表:
d2
d3
t
M4
3.84 0
3.59 +0.1
10
-0.1
0
0
+0.1
M5
4.84
4.54
20
-0.1
0
2) 铸孔到边缘的最小距离
为了保证铸件有良好的成 型
铝锡合金
圆角半径R 0.5 0.5
压铸合金 圆角半径R
铝、镁合金
1.0
铜合金
1.5
我司现采用的圆角一般取R1.5。
表3 铸造圆角半径的计算(mm)
相连接两壁的厚度
图例
圆角半径
相等壁厚
rmin=Kh rmax=Kh R=r+h
不等壁厚
r≥(h+h1)/3 R= r+(h+h1)/2
说明:①、对锌合金铸件,K=1/4;对铝、镁、合金 铸件, K=1/2。
压铸件设计规范
一、 壁厚
压铸件的壁厚对铸件质量有很大的影响。以铝合金为例, 薄壁比厚壁具有更高的强度和良好的致密性。因此,在保 证铸件有足够的强度和刚性的条件下,应尽可能减少其壁 厚,并保持壁厚均匀一致。
铸件壁太薄时,使金属熔接不好,影响铸件的强度,同时 给成型带来困难;壁厚过大或严重不均匀则易产生缩瘪及 裂纹。随着壁厚的增加,铸件内部气孔、缩松等缺陷也随 之增多,同样降低铸件的强度。
0~0.3% 2 % ~4%
说明:①、表内深度系指固定型芯而言,,对于活动的单个型芯其深度还可以适当 增加。
②、对于较大的孔径,精度要求不高时,孔的深度亦可超出上述范围。
对于压铸件自攻螺钉用的底孔,推荐采用的底孔直 径见表6。
表6 自攻螺钉用底孔直径(mm)
螺纹规格d M2.5 M3 M3.5 M4 M5 M6
2.0
+1 -0.4
表9 推荐铰孔加工余量(mm)
公称孔径D
≤6
铰孔余量
0.05
>6~10 0.1
> 10 ~18 >18 ~30 >30 ~50 >50 ~60
0.15
0.2
0.25
0.3
我司现采用的机加工余量一般取0.3~0.5mm。
护; ⑦ 有嵌件的铸件应避免热处理,以免因两种金属的相变而引起体积变
化,使嵌件松动。
七、压铸件的加工余量
压铸件由于尺寸精度或形位公差达不到产品图纸 要求时,应首先考虑采用精整加工方法,如校正、 拉光、挤压、整形等。必须采用机加工时应考虑 选用较小的加工余量,并尽量以不受分型面及活 动成型影响的表面为毛坯基准面。