装配线精益改善ppt课件
合集下载
精益改善小知识ppt课件
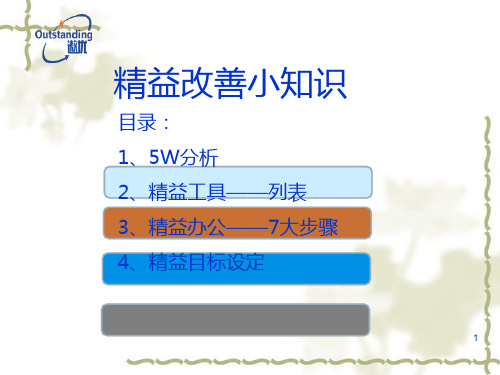
9
精益名词解释
QC旧七大手法
1、鱼骨图:鱼骨追原因. (寻找因果关系) 2、柏拉图:柏拉抓重点. (找出“重要的少数”) 3、层别法:层别作解析. (按层分类,分别统计分析) 4、查检表:查检集数据. (调查记录数据用以分析) 5、散布图:散布看相关. (找出两者的关系) 6、直方图:直方显分布. (了解数据分布与制程能力) 7、管制图:管制找异常. (了解制程变异)
14
精益名词解释
QA(QUALITY ASSURANCE)矩阵 一种实用而有效的质量保证工具,尤其在甄别、
因果矩阵 (Cause & Effect Matrix, CE矩阵)
发现潜在质量风险方面有一定优势,和其他质
量改进工具整合运用,尤其能发挥它的作用。
QM(Quality Maintence)矩阵
Error proof FMEA
2
精益工具——列表
IE改善工具列表
工时分析
时间研究
标准工时
绩效分析
工作抽样
操作模拟
视频分析
员工负荷
工作简化
干涉分析
损失分解
动作研究
物流工具列表
Kanban 看板
库存管理
可视化 管理
ABC分析
流程图
PQ分析
线平衡
面条图
PFEP
物料路径 与计划
牛奶送货 水蜘蛛 每日计划 均衡化
10
精益名词解释
PQ&PR分析 PQ分析:产品数量分析是一个很简单但 是非常有用的工具。它可以用来对生产的 产品按照数量进行分类,然后根据分类结 果对生产车间进行布局优化。 PR分析:产品工序流程分析是一个很简 单但是非常有用的工具。它可以用来对生 产的产品按照工序流程进行分类,然后根 据分类结果对生产车间进行布局优化。
改善精益生产案例PPT课件
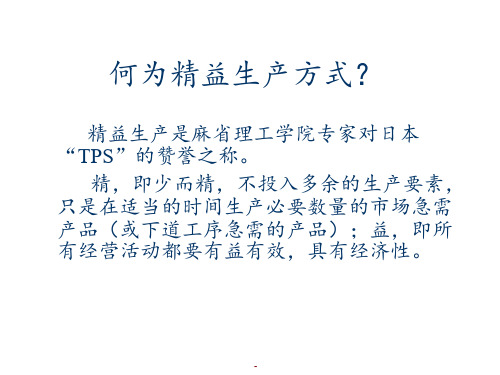
4
场所、位置 什么地方(where)
5
时间
什么时候(when)
6
方法
怎样(how)
⑵定量分析
-
进行的?
举例:根本原因的找出(5W1H) 清洗后,主销表面有锈迹,原因是注销表面与 器具接触处有积水
接触面积过大
减小接触面 积
改进
但效果不是很好
-
表面完全无接触
改变方式
-
改善四原则
原则 目标
例子
取消 简化 合并 重排
调查重点
1
生产量、 你们的生产量是否有所下降、你们是否能提高生产量、
生产率 是否因工作人员过多影响生产效率
2 质量
你们的产品质量是否有所下降、不合格率是否变得高了、 合格率是否能提高、产品缺点是否太多
3 成本
成本是否有所提高、原材料燃料单耗是否增加
4
交货期 你们的生产周期是多少?是否出现了赶不上交货期、生
何为精益生产方式?
精益生产是麻省理工学院专家对日本 “TPS”的赞誉之称。
精,即少而精,不投入多余的生产要素, 只是在适当的时间生产必要数量的市场急需 产品(或下道工序急需的产品);益,即所 有经营活动都要有益有效,具有经济性。
-
精益生产的特点:
w 消除一切浪费,追求精益求精和不断改善。 精简并消除一切不增值的岗位。精简产品 开发设计,生产,管理中一切不产生附加 值的工作,以最优品质,最低成本和最高 效率对市场需求作出最迅速的响应。
不能取消吗? 取消又会变成如何? 不能更为简单吗?
能否把两种以上的工程 合而为一?
能否重排工程?
检查的省略 配置变更的搬运省略
作业的重新估计 自動化
装配快速换线-流程改善分析ppt课件.pptx
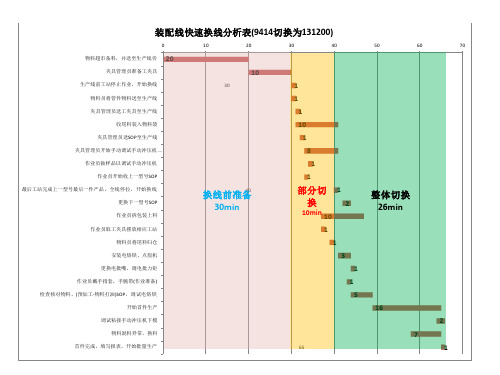
岗位: 职责:
① ② ③ ④
物料员/水蜘蛛
物料员提前30分钟按工位备料至物料车 水蜘蛛将物料送至生产线 水蜘蛛按工位顺序上料 换线后将生产余料归仓
岗位: 职责:
① ② ③
IPQC
按SOP核对物料 按SOP要求设定/点检电烙铁温度、电批扭力参数等 首件检验
岗位: 职责:
① ② ③ ④
多能工
按快速换线要求监督/管理换线过程 协助夹具管理员进行工夹具定位/安装 协助水蜘蛛上料工作(仅换线时)
装配线快速换线分析表(9414切换为131200)
0
10
20
30
40
物料超市备料,并送至生产线旁 20
夹具管理员准备工夹具 生产线前工站停止作业,开始换线
物料员将管件物料送至生产线 夹具管理员送工夹具至生产线
收尾料装入物料袋 夹具管理员送SOP至生产线 夹具管理员开始手动调试手动冲压机 … 作业员做样品以调试手动冲压机 作业员开始收上一型号SOP 最后工站完成上一型号最后一件产品 ,全线 停拉, 开始换 线
30
1
物料员将物料(管件/配件/注塑)送至生 产线
1
夹具管理员送工夹具至生产线工位
2
前段作业员收余料装入物料袋
3
夹具管理员更换SOP
2
中段停止作业,作业员收余料装入物 料袋 物料员按工位顺序给前段上料 物料员按工序给中段上料
后段完成,停止作业,作业员收余料 装入物 料袋 前段作业员进行作业准备
换线前准备 30min
更换下一型号SOP 作业员拆包装上料 作业员取工夹具摆放相应工站 物料员将尾料归仓 安装电烙铁、点胶机 更换电批嘴,调电批力矩 作业员戴手指套,手腕带(作业准备) 检查核对物料、(预加工-物料打油)SOP,调 试电烙 铁
装配线精益改善 PPT

Motion
Correction & Defect
After Kaizen 改善中
Remarks: 備考
减少空间浪费,创造有秩序的工作环境。
Name
新技術研究所(Shingijutsu Co., Ltd)
11
团队编号 编号
Kaizen Newspaper
问题
改善构想
负责人
团队名称前段突破 日期2010.11.12
Name 名前
张帝/沈婧/李剑
9
Kaizen title: 改善項目
正面总检改善
Operator number
Problem 問題
Measure taken 方法
Results 結果
总检正面检查工位提片次数的减少 1多层2、.,压正容后检面易不查检造良人查成员工硅太位片多提受4片个损次人,数导过致12的 次 3、 、 .清检制 增洁查定 加频只提 前率需片 面,要取 装变2杂 饰个更物 板人为的 与4小标 桌时准 面/12、 、数 已据 在1收B集线中使用
装配线精益改善
工艺 & 生产线:装配段/装配3线
KAIZEN的需求:
•降低装配段产能过剩 •减少人员等待 •减少流水线长度,提高空间利用率
TAKT TIME:
=3600/(76*33/4/20) =112.5S
当前问题:
备注:
•每条装配线UPH35大于层压机需求
UPH32 •绝缘,EL,工序等待时间太长,均大于
▪ 2.在3线人员数量减少了共4人(焊接1人,绝缘1人,VOC测试2人)
▪ 3.在3线流水线长度减少了3.3M;
▪ 4.在3线WID在线库存减少2块待层压板,
▪ 待层压架子减少2个(20块待层压板)
装配质量培训课件PPT(共 56张)

标
不得提前拆包装、准备
准 化
确认来件是否合格
作 业
以作业指导书作为装配标准
做好自检及点检标记
批量问题及时反馈、控制
培训
工装、工具的维护保养
• 操作者对使用的工装、工具有维护、修 整的责任,每日开线前要做好工装的点 检工作,发现问题及时修整确保生产, 并及时反馈报修。
培训
现场安全
• 劳保穿戴整齐,消灭一切划伤源。 • 吸烟有专门吸烟室,不允许流动吸烟。 • 不允许坐卧商品车,没有厂内颁发的驾
培训
推动质量意识的11种动力
• 能力 -承诺在实现质量目标上起到一个精神上的推
动作用,而能力却在行动上决定着质量目标 的实现。 -人的潜能是无限的 。
培训
推动质量意识的11种动力
• 沟通 -沟通对于工作质量的好坏有着重要的影响。
培训
推动质量意识的11种动力
• 教育培训 -品质识的四个陷阱
• 陷阱四:“这不关我的事!”
遇到企业问题--“不关我的事”
设计不佳
唤醒
生产技术模具不良
领导交待不清 管理不善
“我也有责任的意识!”
培训
推动质量意识的11种动力
• 质量意识的第一个动 力来源就是期望
老板的期望 老师的期望 父母的期望
培训
推动质量意识的11种动力
• 质量意识的第二个动力来源就是诚信 -对商品的诚信-按设计的模样和性能设计出
培训
-个人素质的提高能在很大程
度上影响一个人的工作态度。
-通过培训,使公司上下形成一种统一的认识,每个 人都明确质量的含义,明确自己工作标准,明白自 己在造就企业完美质量体系中不可缺少的位置,明 白质量改进运动不是一个人的事,达成共识,才能 凝聚全体员工对质量的关心。
精益持续改善PPT课件
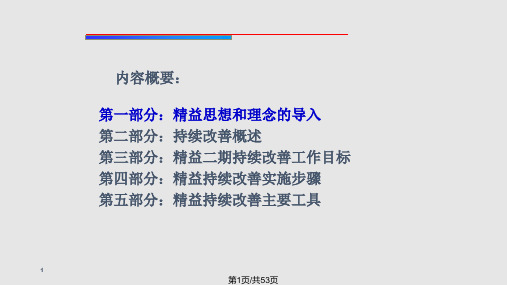
2.创造易于劳动的工作场所 不断发现问题点 不断进行改善 使劳动场所趋于完美
3.提高工作场所的活力 提案活动加强上下沟通 (上司与下属
提案者之间)
4.创造出成果 通过改善使企业直接获得效益
第14页/共53页
15
第二部分:持续改善概述
7、“改善提案” 作用和意义
(1)改善效果 改善作业方法 创造易于劳动的场所 降低成本 提高安全意识 提高品质 事务的合理化,高效率化
30
第30页/共53页
第四部分:持续改善活动实施步骤
2、持续改善工作要点
改善重在观念建立 改善重在全员参与 改善重在过程管理 改善重在持续不断
持续改善是以上模块内部能力的提升,是 模块之间交互的加强,可以说持续改善决定精 益总体推进的成败。
22
第22页/共53页
3、持续改善专项方案
持续改善
改善手法运用
目标设定
培养员工的改善意识 消除浪费、降低成本 持续改善、提高生产 效率 改善环境
培训工作开展
■改善意识培训 ■员工能力开发
现场改善
■生产现场改善 ■物流改善 ■交货期改善
20
第20页/共53页
第三部分:精益二期持续改善专项工作目标
2、持续改善在精益推进中的作用和地位
实现精益
生产管理 TPM
物流
5S/目视化 品质管理
21
第21页/共53页
第三部分:精益二期持续改善专项工作目标
2、持续改善在精益推进中的作用和地位 精益是体系建设,是系统工程,涉及生产、
工艺、设备、品质、物流、现场、成本、人力 资源、5S与目视化等方面。
27
第27页/共53页
第四部分:持续改善活动实施步骤
装配线的平衡ppt课件.ppt

(1)画出装配图; (2)计算节拍; (3)最小工作地数目; (4)进行装配线平衡。
第五章 生产与服务设施布置
解: (1)画出装配图
第五章 生产与服务设施布置
(2)计算节拍
节拍 2280(601+23%0 ) 2.0
第五章 生产与服务设施布置
(3)最小工作地数目
Smin
8.7 2.0
4.4
Smin 5
第五章 生产与服务设施布置
流水生产线的种类
1.按流水线的连续程度 ——连续流水线和间断流水线
2.按在流水线上加工对象的数目 ——单一对象流水线和多对象流水线
3.按流水线上的劳动对象是否移动 ——制件固定流水线和制件移动流水线
4.按流水线的节拍 ——强制节拍流水线和自由节拍流水线
5,按流水线的机械化程度 ——手工流水线和机械化流水线
三、 装配线平衡
(一)、为什么要进行生产线平衡?
你看到了什么?
★ 浪费时间资源 ★ 忙闲不均,引起矛盾 ★ 浪费人力资源
第五章 生产与服务设施布置
(二)生产线平衡的目的
物流快速﹐缩短生周期 减少或消除物料或半成品周转场所 消除生产瓶颈﹐提高作业效率 提升工作士气﹐改善作业秩序 稳定产品质量
首先: 安排后续工艺最多的工艺 其次: 安排加工时间最长的工艺
第五章 生产与服务设施布置
2
1.2
1
A
B
G
C
D
E
3.25
1
.5
工作站 1
1.4 H
F 1
工艺 A C D B E F G H
工作站 2
后续工艺数 时间 (Mins)
6
2
4
3.25
第五章 生产与服务设施布置
解: (1)画出装配图
第五章 生产与服务设施布置
(2)计算节拍
节拍 2280(601+23%0 ) 2.0
第五章 生产与服务设施布置
(3)最小工作地数目
Smin
8.7 2.0
4.4
Smin 5
第五章 生产与服务设施布置
流水生产线的种类
1.按流水线的连续程度 ——连续流水线和间断流水线
2.按在流水线上加工对象的数目 ——单一对象流水线和多对象流水线
3.按流水线上的劳动对象是否移动 ——制件固定流水线和制件移动流水线
4.按流水线的节拍 ——强制节拍流水线和自由节拍流水线
5,按流水线的机械化程度 ——手工流水线和机械化流水线
三、 装配线平衡
(一)、为什么要进行生产线平衡?
你看到了什么?
★ 浪费时间资源 ★ 忙闲不均,引起矛盾 ★ 浪费人力资源
第五章 生产与服务设施布置
(二)生产线平衡的目的
物流快速﹐缩短生周期 减少或消除物料或半成品周转场所 消除生产瓶颈﹐提高作业效率 提升工作士气﹐改善作业秩序 稳定产品质量
首先: 安排后续工艺最多的工艺 其次: 安排加工时间最长的工艺
第五章 生产与服务设施布置
2
1.2
1
A
B
G
C
D
E
3.25
1
.5
工作站 1
1.4 H
F 1
工艺 A C D B E F G H
工作站 2
后续工艺数 时间 (Mins)
6
2
4
3.25
精益生产现场管理和改善ppt课件
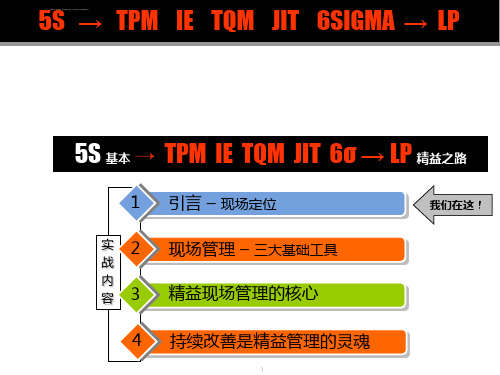
目视工作现场的建立
讨论 目视化工作现场的建立
现在有哪些目视管理
识别哪些地方需要建立目视管理
讨论确定如何和怎样去建立目视管理
实施和跟踪
5S 基本 → TPM IE TQM JIT 6σ → LP 精益之路
实 战 内 容
看板是如何提升管理的精度?
1
看板有哪些,如何确定?
2
围绕看板,构建目标管理运作平台
3
管理看板是发现问题、解决问题的非常有效且直观的手段
确定谁将要做什么 使之目视控制 在适当的位置进行目视控制
目视化工作现场的建立
制订目视化控制计划
协调和标准化目视控制
创建和实施目视控制
检验和修正目视控制
建立目视化控制持续改进计划
在流程中自己进行检查控制 邀请另外一个团队审计目视控制 邀请参与各方审计控制设备 按要求休整目视控制设备
目视化工作现场的建立
人
机
料
法
环
目视管理常用工具及制作要领 (二)、目视管理工具的基本要素
1、提高工作环境的改善 2、提高安全管理的措施 3、提高品质管理的水准 4、提高设备TPM的水准 5、提高现物管理精度
通过彻底5S的实施 安全、舒适的工作环境,人人都按标准办 大家都来做改善
目视管理5项直接效果及其常见措施
制订目视化控制计划
协调和标准化目视控制
创建和实施目视控制
检验和修正目视控制
建立目视化控制持续改进计划
确定后续活动 确定谁在什么时候将要做什么 决定谁将得到信息及如何的到 实施改进计划
目视工作现场的建立
必须取得高层领导的支持
要从流程和人/机/料/法/环方面综合考虑
要坚持用同一个标准
讨论 目视化工作现场的建立
现在有哪些目视管理
识别哪些地方需要建立目视管理
讨论确定如何和怎样去建立目视管理
实施和跟踪
5S 基本 → TPM IE TQM JIT 6σ → LP 精益之路
实 战 内 容
看板是如何提升管理的精度?
1
看板有哪些,如何确定?
2
围绕看板,构建目标管理运作平台
3
管理看板是发现问题、解决问题的非常有效且直观的手段
确定谁将要做什么 使之目视控制 在适当的位置进行目视控制
目视化工作现场的建立
制订目视化控制计划
协调和标准化目视控制
创建和实施目视控制
检验和修正目视控制
建立目视化控制持续改进计划
在流程中自己进行检查控制 邀请另外一个团队审计目视控制 邀请参与各方审计控制设备 按要求休整目视控制设备
目视化工作现场的建立
人
机
料
法
环
目视管理常用工具及制作要领 (二)、目视管理工具的基本要素
1、提高工作环境的改善 2、提高安全管理的措施 3、提高品质管理的水准 4、提高设备TPM的水准 5、提高现物管理精度
通过彻底5S的实施 安全、舒适的工作环境,人人都按标准办 大家都来做改善
目视管理5项直接效果及其常见措施
制订目视化控制计划
协调和标准化目视控制
创建和实施目视控制
检验和修正目视控制
建立目视化控制持续改进计划
确定后续活动 确定谁在什么时候将要做什么 决定谁将得到信息及如何的到 实施改进计划
目视工作现场的建立
必须取得高层领导的支持
要从流程和人/机/料/法/环方面综合考虑
要坚持用同一个标准
精益改善项目案例生产效率提升PPT课件(42页)(2024版)

项目范围: 项目通过推进精益生产,减少生产制造全流程内的浪费,有效减少作业人员、提升产量,缩短交付周期,在降低制造成本的同时,快速满足客户的需求。以工厂为试点,三地工厂同步实施,在制冷集团各事业部推广。
变量
名称
CTQ
单位
Y
生产效率提升
月人均产出
套/人
Y1
生产组织模式变革
订单交付周期
天
Y2
制造技术提升
大线组长 柔性线组长 柔性线巡检
减少1人 两两合并 两两合并
15
Y2改善(节选)—管理优化减员
改善效果:计划减员101人,实际减员101人,计划达成率100%。
部门(分厂)
总一
总二
总三
部装
注塑
财务
品质
职能部
目标(人)
7
2
6
3
31
14
18
20
推进 方向
Y1的改善 摘录1
改善项目名称:订单下达规范性
改善类别
技术
管理
设备
材料
费用
其它
√
改善前
改善后
问题点
改善方案
1、针对计划下达准确率、计划完成及时性的责任划分不明晰,产销责权关系不清,存在管理真空; 2、相关流程时间节点不规范、不合理,且操作随意性较强; 3、产销信息传递不畅。经常出现生产计划与销售计划间的信息不对称;
1、以文件形式彻底固化尾数清理流程、明确激励考核要求; 2、计划管理建立专人监控机制,按周、月通报 3、物资管理监督车间生产过程物料损耗,并每日统计滚动输出; 4、供应商建立安全库存,保证欠产物料补缺的及时性,减少超期作业任务产生; 5、车间物料管护规范每周稽查不少于2次。
《装配线精益改善》课件
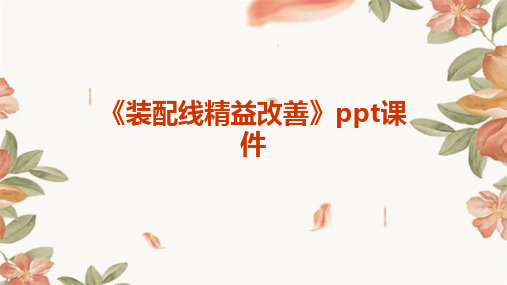
降低生产成本
减少原材料浪费
减少人工成本
通过精确计算和控制原材料消耗,降 低生产成本。
通过提高生产效率和自动化程度,降 低装配线人工成本。
降低能耗和资源消耗
通过改进设备和工艺,降低装配线能 耗和资源消耗。
提升产品质量
01
02
03
提高产品合格率
通过消除装配线上的缺陷 和错误,提高产品合格率 。
加强质量管理体系
02
03
拉动系统
采用拉动式生产方式,根据实际 需求调整生产,避免过量生产和 库存积压。
04
精益生产与传统生产的区别
目标不同
传统生产追求高产量,精益生产追求高效、 低成本。
方法不同
传统生产关注设备利用率、生产效率,精益 生产关注整个价值流的整体效率。
关注点不同
传统生产采用大批量、标准化生产,精益生 产注重灵活性、个性化生产。
单元化生产的步骤包括划分单元、优 化布局、标准化作业等。
通过单元化生产可以减少生产过程中 的等待和运输时间,提高生产效率。
04
装配线精益改善的实践案例
某汽车企业的精益改善实践
总结词:全面实施
详细描述:该汽车企业在生产线上全面实施精益改善,通过消除浪费、提高生产 效率和质量,实现了显著的成本降低和产能提升。
05
装配线精益改善的未来发展
数字化与智能化技术的应用
数字化技术
通过引入数字化技术,如物联网、大数据和云计算,实现装配线实时数据采集、分析和反馈,提高生产效率和 产品质量。
智能化技术
利用人工智能、机器学习等技术,实现装配线智能化控制、预测性维护和自动化决策,降低生产成本和减少人 工干预。
个性化与定制化生产的发展
装配车间效率提升报告 共23页PPT资料
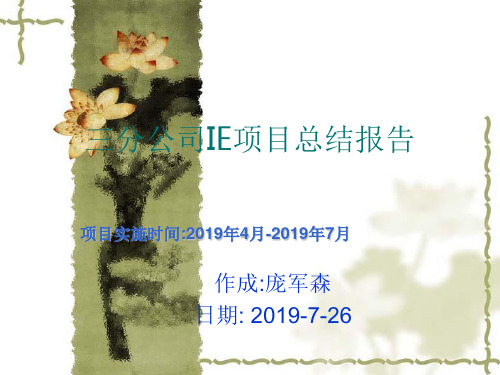
展开内容之生产方式改变后流水线平面图
流程工程现状分析:生产线的布局为L+H型作业
改善后:采用L+H型生产线(拉动式):
通
小包装物料暂放 支架 漏斗暂放
道
水箱盖暂放
包装物料暂放
成品暂放
电源/控制板 发热管 压条
水箱暂放 主体暂放
隔热圈/保温板
电源线暂放
通
工具櫃
底盖暂放
玻璃杯暂放
道
包装物料暂放
三分公司IE项目总结报告
项目实施时间:2019年4月-2019年7月
作成:庞军森 日期: 2019-7-26
展开内容之生产方式改变
由直线Line方式W型改为L+H型
新型生产方 式5月23日试
运行
更高质量 更高效率 更低劳动强度 更低生产成本
展开内容之生产方式改变前流水线平面图
流程工程现状分析:生产线的布局为直线Line对前三项不良分析并制定解决方案
4月不良前三项包括了底脚不平、奶嘴飞线、显示不良、杂色。4个月三项不良中底脚不平一直占 据第一位;奶嘴飞线得到很好的控制由10.52%降到4.59%
分析方案如下
不良项 原因分析
底脚不 包装不良 底板变形 平
解决方案 1.生产线煲水压形 2.改善包装工艺
1. 改善前:物料摆放混乱,标示不清晰,
经常导致物料混用现象。
2. 改善后:现场改善后现场干净整齐,一目了然。
作业现场改善 前
更高质量 更高效率 更低劳动强度 更低生产成本
作业现场改善 后
展开内容之现场5S打造
5S活动不仅能够改善生产环境,还能提高生产效率、产品品质、员工 士气……牵一而动百,是其他管理活动有效展开的基石之一。
装配线精益改善
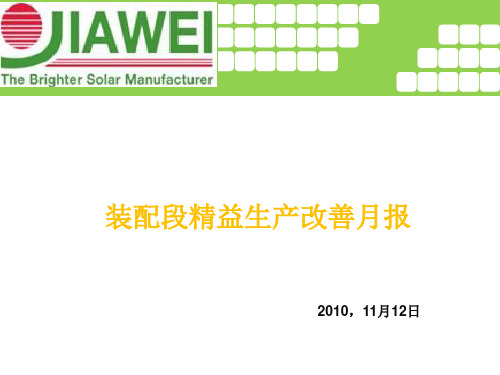
12人
焊接…
写流 程卡
80
正面检查
40
排版 glass 量间距
6
X X 电路连接
2
绝缘
XVOC
EL
X正面检查
8 100
300
准备涂 锡带
20
切割 胶纸
100
100
桌子
两个工 位配合
合计571S
86S
90.59S
90.47S
92.82S
45.30S
82.96S
52.56S
88.84S
改善前的流程图
每个子工艺的Cycle Time(改善前)
Name
新技術研究所(Shingijutsu Co., Ltd)
11
Kaizen title: 改善項目
待层压区改善
Operator number 待层压区改善
Problem
Measure taken
Results
問題
方法
結果
1、周转架多出60%,造成空间
浪费
2、待层板放置混乱,浪费周 转时间
3、放置混乱,周转时引起
批准人
将来 Being, Jeanette
安全
0
0
0
0
0
0
0
排版后工序人员数量 15
10
15
14
14
14
12
10
人员
单串焊接人员数量
12
11
12
12
12
12
11
组别小时产能
35
32
35
35
35
35
32
排版玻璃库存
40
超实用精益改善案例PPT幻灯片课件

• 所做的工作:
– 1.现场时间的观测 – 2.确定了存在的浪费 – 3.分析内部时间,外部时间 – 4.工位工刀具盒的制做 – 5.文件架的制做 – 6.建立快速换模工作站
41
珠海市俊凯机械有限公司
改善前
改善后
刀具无标志,使用时需寻找,测量, 这样会增加工人劳动强度,影响工 作效率,也不便刀具寿命的统计
序号 工序
机器
人标准工时 机器标准工时 序号 工序
机器
人标准工时 机器标准工时
1 下料
卧铣
15
5
1 下料
卧铣
10
3
2 飞底面
立铣
35
15
2 飞底面
立铣
30
15
3 铣长度
哈斯机
15
60
3 铣长度
哈斯机
10
64
4 铣内腔
起亚机
15
270
4 铣内腔
起亚机
10
110
5 铣外宽
哈斯机
15
80
5 铣外宽及沉孔 哈斯机
U型布局 定岗定人
已建立 已建立
407m 24/h2人
提高了51.8% 提高了100%
22
珠海市俊凯机械有限公司 活动目标:
一、生产效率提升50% 二、建立小批量生产线,岗位及人员的确定。
活动时间:6月3日-6月10日
23
珠海市俊凯机械有限公司
• 改善范围:
– 观测小批量产品族的生产过程.
• 所做的工作:
工具摆放混乱,没有标示,经常用工 具时需要到处寻找工具浪费时间
工具摆放整齐、标示清楚明了, 员工不需要再寻找工具。
33
珠海市俊凯机械有限公司
– 1.现场时间的观测 – 2.确定了存在的浪费 – 3.分析内部时间,外部时间 – 4.工位工刀具盒的制做 – 5.文件架的制做 – 6.建立快速换模工作站
41
珠海市俊凯机械有限公司
改善前
改善后
刀具无标志,使用时需寻找,测量, 这样会增加工人劳动强度,影响工 作效率,也不便刀具寿命的统计
序号 工序
机器
人标准工时 机器标准工时 序号 工序
机器
人标准工时 机器标准工时
1 下料
卧铣
15
5
1 下料
卧铣
10
3
2 飞底面
立铣
35
15
2 飞底面
立铣
30
15
3 铣长度
哈斯机
15
60
3 铣长度
哈斯机
10
64
4 铣内腔
起亚机
15
270
4 铣内腔
起亚机
10
110
5 铣外宽
哈斯机
15
80
5 铣外宽及沉孔 哈斯机
U型布局 定岗定人
已建立 已建立
407m 24/h2人
提高了51.8% 提高了100%
22
珠海市俊凯机械有限公司 活动目标:
一、生产效率提升50% 二、建立小批量生产线,岗位及人员的确定。
活动时间:6月3日-6月10日
23
珠海市俊凯机械有限公司
• 改善范围:
– 观测小批量产品族的生产过程.
• 所做的工作:
工具摆放混乱,没有标示,经常用工 具时需要到处寻找工具浪费时间
工具摆放整齐、标示清楚明了, 员工不需要再寻找工具。
33
珠海市俊凯机械有限公司
《装配线精益改善》课件
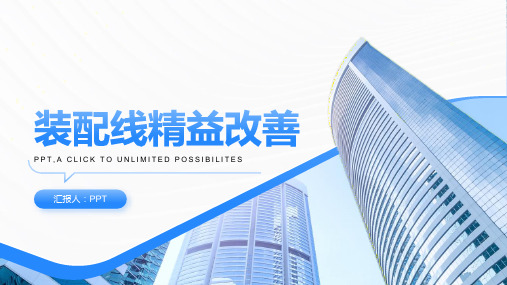
培训员工:对员工进行持续培训,提高 员工技能和素质
加强管理:加强装配线管理,提高生 产效率和生产质量
工业4.0:智能化、数字化、网络化、个性化生产 精益生产:消除浪费、提高效率、降低成本 结合展望:实现智能制造,提高生产效率和产品质量 持续改进:不断优化生产流程,提高生产效率和产品质量 应用案例:介绍成功案例,展示精益生产与工业4.0结合的效果
整理:区分必要和不必要 的物品,只留下必要的物 品
整顿:将必要的物品按照 规定位置摆放整齐
清扫:保持工作场所的清 洁,防止灰尘和污垢的积 累
清洁:保持工作场所的整 洁,防止灰尘和污垢的积 累
素养:培养员工良好的工 作习惯和素养,提高工作 效率和质量
目的:提高生产效率,降低成本 方法:通过颜色、形状、位置等视觉信号进行管理 应用:生产现场、仓库、办公室等 效果:提高员工工作效率,减少错误率,降低库存成本
企业背景:某机械制造企业,生产汽车零部件 改善目标:提高装配线效率,降低成本 改善措施:引入精益生产理念,优化生产流程,提高自动化程度 改善效果:装配线效率提高20%,成本降低15%,产品质量得到提升
企业背景:某家具制造企业,生 产各类家具产品
改善措施:引入精益生产理念, 优化生产流程,提高员工技能
和废品率
背景:某汽车制造企业面临生产效率低下、质量问题频发的问题 改善措施:引入精益生产理念,优化装配线布局,提高生产效率 效果:生产效率提高20%,质量问题减少50% 启示:精益生产理念在装配线改善中的重要性,以及持续改进的必要性
企业背景:某电子产品制造企业,生产手机、电脑等电子产品 改善目标:提高生产效率,降低成本 改善措施:引入精益生产理念,优化生产线布局,提高自动化程度 改善效果:生产效率提高20%,成本降低15%,产品质量得到提升
- 1、下载文档前请自行甄别文档内容的完整性,平台不提供额外的编辑、内容补充、找答案等附加服务。
- 2、"仅部分预览"的文档,不可在线预览部分如存在完整性等问题,可反馈申请退款(可完整预览的文档不适用该条件!)。
- 3、如文档侵犯您的权益,请联系客服反馈,我们会尽快为您处理(人工客服工作时间:9:00-18:30)。
KAIZEN TARGETS
目标
组别 项目
如果每天有持续作用,在右上角标注 ●
线别:装配3线
日期 Ww44.1-ww44.5
日期
2010.11.12
名称:排版到正面检查
起始
目标
第一天
节拍时间
112.5
第二天 第三天 第四天 第五天
批准人
将来 Being, Jeanette
安全
0
0
0
0
0
0
0
排版后工序人员数量 15
7 Types of Muda Overproduction
待层压板 电脑
11人
40
6
焊接…
排版 glass 量间距
电路连接
EL
正面检查
100
写流 程卡
8
300
20
准备涂 切割 锡带 胶纸
桌子
100
100
50
两个工 位配合
合计465.3S
93.3S
90.59S
sunenergy
90.47S
92.82S
110.56S
KAIZEN KICK-OFF MEETING
17.63
10.5 17.63 15.6 15.6 15.6 10.6
KAIZEN KICK-OFF MEETING
.
4
sunenergy
2.13M
合计:17.63M
2.5M
EVA/TPE裁切
2M
2M
玻璃清洗机
2.9M
2.4M
3.7M
TPE运输车 玻璃周转箱 EVA存放车
待层压板 电脑
12人
焊接…
Before : 工作区域2.9M,人员4名 After : 工作区域1.6M,人员2名
7 Types of Muda
Overproduction
Waiting
Before Kaizen 改善前
Conveyance Processing
Inventory
Motion
After Kaizen 改善後
Correction & Defect
.
88.84S
改善后的流程图
每个子工艺的Cycle Time(改善后预测)
KAIZEN KICK-OFF MEETING
.
sunenergy
8
Kaizen title: 改善項目
Operator number 作業者番号
Problem 問題
绝缘工位分解
Measure taken 方法
Results 結果
.
52.56S
88.84S
改善前的流程图
每个子工艺的Cycle Time(改善前)
TT:改善前生产前段的节拍
CT:改善前每个工位的周期
KAIZEN KICK-OFF MEETING
.
sunenergy
6
2.13M
合计:17.63M
2.5M
EVA/TPE裁切
2M
1.6M
玻璃清洗机
2.4M
7M
TPE运输车 玻璃周转箱 EVA存放车
=3600/(76*33/4/20) =112.5S
当前问题:
备注:
•每条装配线UPH35大于层压机需求
UPH32 •绝缘,EL,工序等待时间太长,均大于
20s • 排板后流水线17.6M太长
改善产能过剩,需要减少单串焊接人 员数量
KAIZEN KICK-OFF MEETING
.
3
sunenergy
10
15
14
14
14
12
10
人员
单串焊接人员数量
12
11
12
12
12
12
11
组别小时产能
35
32
35
35
35
35
32
排版玻璃库存
40
25
40
40
40
40
40
在线待层压板库存
2
0
2
0
0
0
0
物料 待层压板库存
160
80
150
130
ቤተ መጻሕፍቲ ባይዱ
100
80
80
待层压板搬运距离(M) 3
0
2
1
1
1
1
流水线长度(米) 其他
朱正
IE技术员 工程
王欲
改善组 生产
KAIZEN持续时间: 2010,10月20日~11月12日
KAIZEN KICK-OFF MEETING
.
2
sunenergy
工艺 & 生产线:装配段/装配3线
KAIZEN的需求:
•降低装配段产能过剩 •减少人员等待 •减少流水线长度,提高空间利用率
TAKT TIME:
sunenergy
装配段精益生产改善月报
2010,11月12日
.
KAIZEN KICK-OFF MEETING
装配段精益生产改善小组
领导人: 领导助理:
成员:
姓名
职位
戴学岗
生产中心
熊军明
IE主管 工程
张帝
经理 工程
李剑
设备经理 工程
刘丽丽
副主管 品质
沈婧
PE
工程
张彩霞
QE
品质
周爱萍、徐利平
生产经理 生产
Results 結果
总检正面检查工位提片次数的减少 1多层2、.,压正容后检面易不查检造良人查成员工硅太位片多提受4片个损次人,数导过致12的 次 3、 、 .清检制 增洁查定 加频只提 前率需片 面,要取 装变2杂 饰个更物 板人为的 与4小标 桌时准 面/12、 、数 已据 在1收B集线中使用
B
/
1.多于的桌子,堆积2pcs待层压板 2.绝缘SST太短,有长时间等待浪
费
1.移走一张多于桌子 2.绝缘工位合并到EL测试工位
Before : 工作区域4M,人员1名 After : 工作区域2M,减少人员1名
7 Types of Muda
Overproduction
Waiting
Before Kaizen 改善前
Conveyance Processing
Inventory
Motion
After Kaizen 改善後
Correction & Defect
Remarks: 備考
减少等待,缩短流水线2M,r 人员1名
KAIZEN KICK-OFF MEETINGN名am前e
张帝/李剑/熊军明
.
sunenergy
9
Remarks: 備考
取消使用无异常,EL增加的灯管能起到反面检查的作用
KAIZEN KICK-OFF MEETINGN名am前e
张帝/沈婧/李剑
.
sunenergy
10
Kaizen title: 改善項目
正面总检改善
Operator number
Problem 問題
Measure taken 方法
写流 程卡
80
正面检查
40
排版 glass 量间距
6
X X 电路连接
2
绝缘
XVOC
EL
X正面检查
8 100
300
准备涂 锡带
20
切割 胶纸
100
100
桌子
两个工 位配合
合计571S
86S
90.59S
sunenergy
90.47S
92.82S
45.30S
82.96S
KAIZEN KICK-OFF MEETING
Kaizen title: 改善項目
Operator number 作業者番号
Problem 問題
EL代替VOC测试
Measure taken 方法
Results 結果
/
1.VOC不能发现的问题EL都能检测
1.合并VOC测试于EL测试
出来
2.在EL测试仪器内壁装灯管,开灯在EL
2.多于的工序
测试仪器上检查杂物,等其他不良