液压爬模法、滑模法、翻模法的优劣点比较
滑模、爬模、翻模施工技术对比

施工方法
爬模
翻模
爬模是综合大模板与滑升 翻模是大模板施工方法 模板工艺特点的一种施工 ,以混凝土结构作为支 方法。爬模主要由爬升装 承主体,上层模板支承 置、外组合模板、移动模 在下层模板上,循环交 板支架、上爬架、下吊架 替上升。分为塔吊翻模 、内爬架、模板及电器、 和液压翻模两种,前者 液压控制系统等部分构成 工作平台支撑于钢模板 。液压自爬模板工艺原理 的牛腿支架或横竖肋背 为自爬模的顶升运动通过 带上,通过塔吊提升模 液压油缸对导轨和爬架交 板及工作平台;后者工 替顶升来实现,导轨和爬 作平台与模板是分离的 模架互不关联,二者之间 ,工作平台支撑于提升 可进行相互运动.当爬模 架上,模板的提升靠固 架工作时,导轨和爬模架 定于混凝土结构主筋上 都支撑在埋件支座上,两 的手动葫芦来完成。 者之间无相对运动。
相对较慢。不便于在 不便于在施工和养护 施工和养护期间对混 期间对混凝土进行保 凝土进行保温和蒸汽 温和蒸汽养护。
养护。
三种施工方法对比分析表
序 号
项目
滑模
一般混凝土的浇筑及滑升
速度为平均0.2m/h,模板
5
施工 高度为0.9-1.5m。 效率
6
经济 较大 投入
因脱模时间早,所以滑模
混凝土外观需经过涂抹才
喷洒混凝土专用养护 剂(外模)与蓄水养 护(内模)相结合。
全站仪、铅垂仪、垂 全站仪、铅直垂仪、
线
垂线
二、滑模、爬模及翻模施工
2.1 滑模施工
2.1.1工艺原理及结构体系
滑模装置由模板系统、操作平
台系统、液压提升系统和垂直运输
系统等四大系统组成。滑模施工工
艺原理是预先在混凝土结构中埋置
钢管(称之为支承杆),利用千斤顶
爬模与滑模的主要区别

爬模与滑模的主要区别(简易区分,详细区分见下段):
滑模:是在模板与混凝土保持接触互相摩擦的情况下逐步整体上升的。
滑模上升时,模板高度范围内上部的混凝土刚浇灌,下部的混凝土接近初凝状态,而刚脱模的混凝土强度仅为0.2~0.4Mpa。
爬模:上升时,模板已脱开混凝土,此时混凝土强度已大于1.2Mpa,模板不与混凝土磨擦。
详细区分:
滑模:水泥混凝土浇筑时所用模板中的一种,它可以沿着水平方向、斜坡方向或垂直方向渐渐滑动,做到边浇捣,边脱模,是一种经济的先进方法,称为滑模施工。
其使用的混凝土是硬稠性混凝土,否则当模板滑移后,混凝土的边缘容易塌陷损坏。
高层建筑物,如果现场堆放条件受到限制,采用滑模比较好,而且施工速度快,降低模板损耗率。
但是对于异型墙体较多的建筑就不太适合了。
爬模:爬升模板是依附在建筑结构上,随着结构施工而逐层上升的一种模板,当结构凝土达到拆模强度而脱模后,模板不落地,依靠机械设备和支承体将模板和爬模装置向上爬升一层,定位紧固,反复循环施工。
爬模是适用于高层建筑或高耸构造物现浇钢筋混凝土结构的先进模板施工工艺。
翻模
翻模是指三角架翻模施工工艺,在电厂的冷却塔塔筒施工中经常遇到。
该种模板下部用架杆支成三角架做支撑,滑模用在电厂的烟囱筒壁施工中,需要一个顶升液压装置做为提升模板的机具。
爬模、滑模、翻模施工技术优劣对比

爬模、滑模、翻模施工技术优劣对比作者:张燕来源:《锋绘》2019年第07期摘要:爬模、滑模与翻模是框架混凝土结构中较为常用的几种施工方法。
在进行施工时,如何根据工程类型、特点以及工程所在地地质条件等因素科学合理地选择施工方法,以此来缩短工期,获得经济效益,具有重要的现实意义。
本文对爬模、滑模、翻模的施工方法的优劣以及安全质量控制措施进行了对比,希望为施工方法的选择提供参考。
关键词:爬模;滑模;翻模;优劣对比;质量安全控制模板在混凝土施工中至關重要,不同的模板形式决定了混凝土浇筑所采用的施工工艺也不同,对工期以及工程效益也有不同程度的影响。
现有的框架混凝土结构主要采用的模板有爬模、滑模与翻模,为了正确的选择模板施工方法,对各种模板的优缺点进行了解就显得尤为必要。
1 爬模施工爬模是爬升模板的简称,国外也叫跳模,爬模由爬架、爬升模板及爬升设备三部分组成,常用于桥墩、剪力墙体系、筒体体系等高耸结构的施工。
由于爬模具有自爬的能力,且脚手架可直接悬挂在自爬模板上,所以可以减少吊运作量以及节省外脚手架。
1.1 优点(1)一般的爬模架在组装之后,除了由于建筑结构的突变而需要对模板进行改装之外,其余情况下可以跟随施工的进程一直上升到顶部而不落地,所以可以节省施工场地的占用面积,减少由于在施工过程中的碰撞而造成的模板损坏。
(2)由于怕爬模可以提供全方位的操作平台,所以能够在保障施工人员的安全的前提下为施工人员的操作提供便利,而且不需要再额外搭设操作平台,节省了一部分的人力和物力。
(3)相对翻模而言,爬升速度快,模板标准化程度高,整个结构仅用一个液压油泵提升,一次组装;爬升过程中不用再支模、拆模、搭设脚手架和运输等工作,施工安全度高。
1.2 缺点(1)考虑到经济型、合理性,适用于公路桥梁中高度超过40米的矩形空心墩,而本项目主桥墩身高度约为20m。
(2)系统模板造价高,使用过程中保养、维护费用高,模板配件标准化高,损坏后需要从厂家定做。
高层建筑滑模法与爬模法施工技术研究
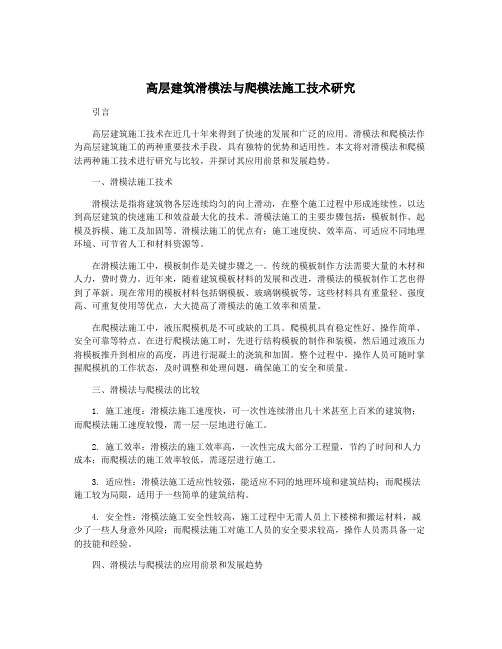
高层建筑滑模法与爬模法施工技术研究引言高层建筑施工技术在近几十年来得到了快速的发展和广泛的应用。
滑模法和爬模法作为高层建筑施工的两种重要技术手段,具有独特的优势和适用性。
本文将对滑模法和爬模法两种施工技术进行研究与比较,并探讨其应用前景和发展趋势。
一、滑模法施工技术滑模法是指将建筑物各层连续均匀的向上滑动,在整个施工过程中形成连续性,以达到高层建筑的快速施工和效益最大化的技术。
滑模法施工的主要步骤包括:模板制作、起模及拆模、施工及加固等。
滑模法施工的优点有:施工速度快、效率高、可适应不同地理环境、可节省人工和材料资源等。
在滑模法施工中,模板制作是关键步骤之一。
传统的模板制作方法需要大量的木材和人力,费时费力。
近年来,随着建筑模板材料的发展和改进,滑模法的模板制作工艺也得到了革新。
现在常用的模板材料包括钢模板、玻璃钢模板等,这些材料具有重量轻、强度高、可重复使用等优点,大大提高了滑模法的施工效率和质量。
在爬模法施工中,液压爬模机是不可或缺的工具。
爬模机具有稳定性好、操作简单、安全可靠等特点。
在进行爬模法施工时,先进行结构模板的制作和装模,然后通过液压力将模板推升到相应的高度,再进行混凝土的浇筑和加固。
整个过程中,操作人员可随时掌握爬模机的工作状态,及时调整和处理问题,确保施工的安全和质量。
三、滑模法与爬模法的比较1. 施工速度:滑模法施工速度快,可一次性连续滑出几十米甚至上百米的建筑物;而爬模法施工速度较慢,需一层一层地进行施工。
2. 施工效率:滑模法的施工效率高,一次性完成大部分工程量,节约了时间和人力成本;而爬模法的施工效率较低,需逐层进行施工。
3. 适应性:滑模法施工适应性较强,能适应不同的地理环境和建筑结构;而爬模法施工较为局限,适用于一些简单的建筑结构。
4. 安全性:滑模法施工安全性较高,施工过程中无需人员上下楼梯和搬运材料,减少了一些人身意外风险;而爬模法施工对施工人员的安全要求较高,操作人员需具备一定的技能和经验。
超高层施工三种模板系统
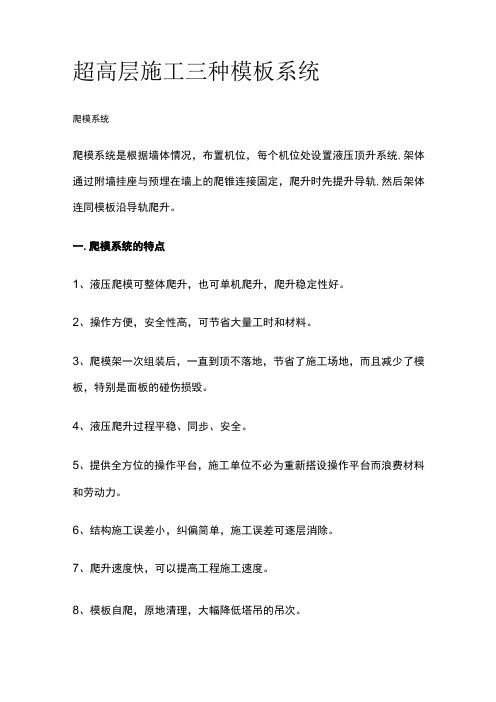
超高层施工三种模板系统爬模系统爬模系统是根据墙体情况,布置机位,每个机位处设置液压顶升系统,架体通过附墙挂座与预埋在墙上的爬锥连接固定,爬升时先提升导轨,然后架体连同模板沿导轨爬升。
一.爬模系统的特点1、液压爬模可整体爬升,也可单机爬升,爬升稳定性好。
2、操作方便,安全性高,可节省大量工时和材料。
3、爬模架一次组装后,一直到顶不落地,节省了施工场地,而且减少了模板,特别是面板的碰伤损毁。
4、液压爬升过程平稳、同步、安全。
5、提供全方位的操作平台,施工单位不必为重新搭设操作平台而浪费材料和劳动力。
6、结构施工误差小,纠偏简单,施工误差可逐层消除。
7、爬升速度快,可以提高工程施工速度。
8、模板自爬,原地清理,大幅降低塔吊的吊次。
9、爬模系统具有操作简便灵活,爬升安全平稳,速度快,模板定位精度高,施工过程中无需其他辅助起重设备的特点。
但一般机位较多,整体性不够好,承载力也不大。
爬模能容易适应较薄的墙厚变化,但墙体突变时适应困难。
二、施工要点每次浇筑混凝土面距模板顶面不应少于5cm o浇筑混凝土时,应用插入式振捣器捣固,并应避免接触模板、对拉螺栓、钢筋或空心支撑。
混凝土浇筑后,强度达到2.5MPa以上方可拆模翻倒。
每一节模板安装前均应清除表面灰浆污垢,整修变形部位并涂刷脱模剂。
模板沿墩身周边方向应始终保持顺向搭接。
爬模施工过程中,应经常检查中线、水平,发现问题及时纠正。
混凝土可采用洒水养护,当桥墩过高供水困难时,可采用混凝土养护液养护。
墩身混凝土脱模部分应及时用水泥砂浆堵塞对拉螺栓孔及修补表面缺陷。
爬模的接料平台、脚手平台、拆模吊篮的荷载,应平衡,不得超载,严禁混凝土吊斗碰撞爬模系统。
滑模系统滑模施工工艺广泛应用于钢筋混凝土的筒壁结构、框架结构、墙板结构。
对于高耸筒壁结构和高层建筑的施工,效果尤为显著。
一、滑模系统的特点1.滑模施工技术是混凝土工程中机械化程度高,施工速度快,场地占用少,安全作业有保障,综合效益显著的一种施工方法。
滑模、爬模和翻模

2主要施工工艺和流程2.1模板设计与制作空心薄壁高墩施工重点是解决模板模型、模板安装及拆除方法、混凝土运输等。
空心薄壁高墩施工一般采用的施工方法有落地支架提升模板、滑升模板及翻转模板施工方案。
落地支架提升模板方案支架材料用量较大,施工速度较慢;滑升模板方案施工速度快,但滑模工艺要求严格,质量难以控制,管理难度较大;翻转模板施工方案工艺较简单,施工过于连续,速度较快。
一般均需配备塔吊、电梯等设备。
经过详细比较,决定采用优化传统翻转模板施工方案。
采用此种施工方案,能够充分利用常备构件,材料用量少,施工速度较快,且工艺相对较简单。
2.1.1前期设计与制作为保证墩身混凝土的外观质量,加快施工进度,根据本标段墩身设计特点(空心、多室、内外截面尺寸较大、墩身较高)等,进行方案设计。
2.1.1.1 正面模板空心薄壁墩正面外模按照每块高1.5m、宽6m进行制作(即将6块1×1.5m的模板立起拼装而成),高度方向分3块进行拼装。
2.1.1.2 侧面模板空心薄壁墩侧面外模按照每块高1.5m,宽2.5m进行制作(即将2块1×1.5m的模板和1块0.5×1.5m的模板立起拼装而成),高度方向分3块进行拼装。
2.1.1.3模板连接及加固模板在同一平面连接处采用螺杆连接牢靠。
为保证混凝土浇注时不漏浆,成型美观,在模板连接处贴双面密封胶带。
为加强模板刚度和稳定性,保证空心薄壁墩浇注时不跑模,并为操作人员提供方便,在第一排模板沿1.5m高度方向,上、中、下部位水平向各设置一根(共3根)加强槽钢,每两根槽钢的间距为50cm。
上一排模板沿1.5m高度方向,上、下部位水平向各设置一根(共2根)加强槽钢,设置时以1.5m高度对称进行,间距为50cm。
再上一排设置3根槽钢,最上面一排设置2根槽钢。
则所有槽钢的间距均为50cm,槽钢采用10号槽钢。
拉杆均设置在槽钢上,在槽钢上打孔穿设拉杆。
拉杆水平方向的间距为60cm,两端第一根拉杆应设置在距边30cm的位置。
滑膜、爬模、翻模施工特点

1、爬模施工爬模是现浇竖向钢筋混凝土结构的一项较为先进的施工工艺,在山区铁路施工中被普通采用。
它是在建筑物或构筑物的基础上,按照平面图,沿结构周边一次装设一段模板,随着模板内不断浇筑混凝土和绑扎钢筋,不断提升模板来完成整个建(构)筑物的浇筑和成型。
它的特点是:整个结构仅用一个液压滑动模板,一次组装;爬升过程中不用再支模、拆模、搭设脚手和运输等工作,混凝土保持连续浇筑,施工速度快,可避免施工缝,同时具有节省大量模板、脚手材料和劳力,减轻劳动强度,降低施工成本,施工安全等优点。
广泛应用于烟囱、贮仓、水塔、油罐、竖井、沉井、电梯井、电视塔和桥梁高墩等工程上;对民用高层、多层框架、框剪结构、亦可应用。
2、滑模施工滑模工程技术是我国现浇混凝土结构工程施工中机械化程度高、施工速度快、现场场地占用少、结构整体性强、抗震性能好、安全作业有保障、环境与经济综合效益显著的一种施工技术,通常简称为“滑模”。
但滑模不仅包含普通的模板或专用模板等工具式模板,还包括动力滑升设备和配套施工工艺等综合技术,目前主要以液压千斤顶为滑升动力,在成组千斤顶的同步作用下,带动1米多高的工具式模板或滑框沿着刚成型的混凝土表面或模板表面滑动,混凝土由模板的上口分层向套槽内浇灌,每层一般不超过30cm厚,当模板内最下层的混凝土达到一定强度后,模板套槽依靠提升机具的作用,沿着已浇灌的混凝土表面滑动或是滑框沿着模板外表面滑动,向上再滑动约30cm左右,这样如此连续循环作业,直到达到设计高度,完成整个施工。
滑模工艺是竖向混凝土工程的最好选择!3、翻模施工翻模施工是指:翻升模板由叁节大块钢模板与支架、钢管脚手架工作平台组合而成(施工中随着墩柱高度的增加将支架与已浇墩柱相连接,以增加支架的稳定性)。
模板高度施工时第一节模板支立于基顶,第二节模板支立于第一节段模板上。
当第二节混凝土强度达到3MPa以上、第一节混凝土强度达到10MPa以上时,拆除第一节模板并将模板表面清理干净、涂上脱模剂后,用吊车和手动葫芦将其翻升至第二节模板上,第三节模板置于第一节模板上。
高层建筑滑模法与爬模法施工技术研究
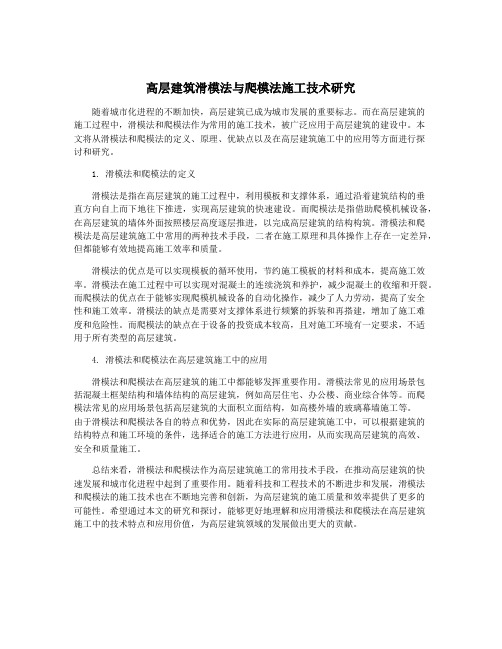
高层建筑滑模法与爬模法施工技术研究随着城市化进程的不断加快,高层建筑已成为城市发展的重要标志。
而在高层建筑的施工过程中,滑模法和爬模法作为常用的施工技术,被广泛应用于高层建筑的建设中。
本文将从滑模法和爬模法的定义、原理、优缺点以及在高层建筑施工中的应用等方面进行探讨和研究。
1. 滑模法和爬模法的定义滑模法是指在高层建筑的施工过程中,利用模板和支撑体系,通过沿着建筑结构的垂直方向自上而下地往下推进,实现高层建筑的快速建设。
而爬模法是指借助爬模机械设备,在高层建筑的墙体外面按照楼层高度逐层推进,以完成高层建筑的结构构筑。
滑模法和爬模法是高层建筑施工中常用的两种技术手段,二者在施工原理和具体操作上存在一定差异,但都能够有效地提高施工效率和质量。
滑模法的优点是可以实现模板的循环使用,节约施工模板的材料和成本,提高施工效率。
滑模法在施工过程中可以实现对混凝土的连续浇筑和养护,减少混凝土的收缩和开裂。
而爬模法的优点在于能够实现爬模机械设备的自动化操作,减少了人力劳动,提高了安全性和施工效率。
滑模法的缺点是需要对支撑体系进行频繁的拆装和再搭建,增加了施工难度和危险性。
而爬模法的缺点在于设备的投资成本较高,且对施工环境有一定要求,不适用于所有类型的高层建筑。
4. 滑模法和爬模法在高层建筑施工中的应用滑模法和爬模法在高层建筑的施工中都能够发挥重要作用。
滑模法常见的应用场景包括混凝土框架结构和墙体结构的高层建筑,例如高层住宅、办公楼、商业综合体等。
而爬模法常见的应用场景包括高层建筑的大面积立面结构,如高楼外墙的玻璃幕墙施工等。
由于滑模法和爬模法各自的特点和优势,因此在实际的高层建筑施工中,可以根据建筑的结构特点和施工环境的条件,选择适合的施工方法进行应用,从而实现高层建筑的高效、安全和质量施工。
总结来看,滑模法和爬模法作为高层建筑施工的常用技术手段,在推动高层建筑的快速发展和城市化进程中起到了重要作用。
随着科技和工程技术的不断进步和发展,滑模法和爬模法的施工技术也在不断地完善和创新,为高层建筑的施工质量和效率提供了更多的可能性。
高层建筑滑模法与爬模法施工技术研究
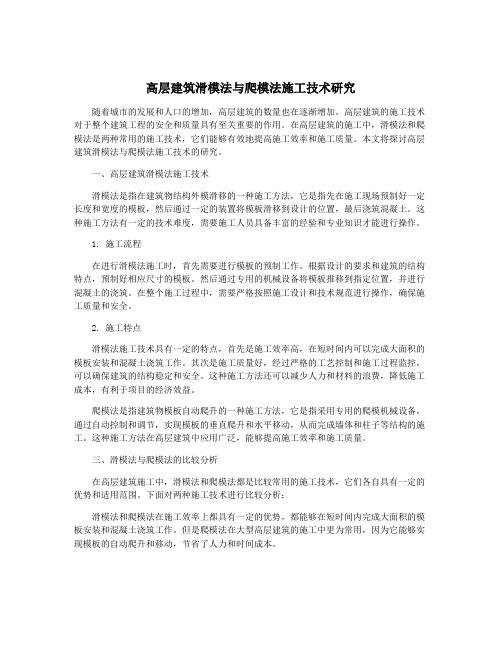
高层建筑滑模法与爬模法施工技术研究随着城市的发展和人口的增加,高层建筑的数量也在逐渐增加。
高层建筑的施工技术对于整个建筑工程的安全和质量具有至关重要的作用。
在高层建筑的施工中,滑模法和爬模法是两种常用的施工技术,它们能够有效地提高施工效率和施工质量。
本文将探讨高层建筑滑模法与爬模法施工技术的研究。
一、高层建筑滑模法施工技术滑模法是指在建筑物结构外模滑移的一种施工方法,它是指先在施工现场预制好一定长度和宽度的模板,然后通过一定的装置将模板滑移到设计的位置,最后浇筑混凝土。
这种施工方法有一定的技术难度,需要施工人员具备丰富的经验和专业知识才能进行操作。
1. 施工流程在进行滑模法施工时,首先需要进行模板的预制工作。
根据设计的要求和建筑的结构特点,预制好相应尺寸的模板。
然后通过专用的机械设备将模板推移到指定位置,并进行混凝土的浇筑。
在整个施工过程中,需要严格按照施工设计和技术规范进行操作,确保施工质量和安全。
2. 施工特点滑模法施工技术具有一定的特点,首先是施工效率高,在短时间内可以完成大面积的模板安装和混凝土浇筑工作。
其次是施工质量好,经过严格的工艺控制和施工过程监控,可以确保建筑的结构稳定和安全。
这种施工方法还可以减少人力和材料的浪费,降低施工成本,有利于项目的经济效益。
爬模法是指建筑物模板自动爬升的一种施工方法,它是指采用专用的爬模机械设备,通过自动控制和调节,实现模板的垂直爬升和水平移动,从而完成墙体和柱子等结构的施工。
这种施工方法在高层建筑中应用广泛,能够提高施工效率和施工质量。
三、滑模法与爬模法的比较分析在高层建筑施工中,滑模法和爬模法都是比较常用的施工技术,它们各自具有一定的优势和适用范围。
下面对两种施工技术进行比较分析:滑模法和爬模法在施工效率上都具有一定的优势,都能够在短时间内完成大面积的模板安装和混凝土浇筑工作。
但是爬模法在大型高层建筑的施工中更为常用,因为它能够实现模板的自动爬升和移动,节省了人力和时间成本。
桥梁高墩滑模、爬模、翻模施工

桥梁高墩滑模、爬模、翻模施工随着我国现在桥梁高度的不断提升,高墩施工也成为了一个制约工程进展的关键节点,,为了区分滑模、爬模以及翻模这三种施工,介绍高墩施工中常见的滑模施工全过程一、滑模装置整个滑模装置由:模板系统、提升系统、操作平台、液压系统、辅助系统五大部分组成。
模板面板采用δ6mm钢板制作而成,模板高1.26米,用10号角钢作为加筋肋,间隔30cm,通过上下两道围圈定位支撑,围圈焊接于桁架梁上。
围圈采用10号角钢加工。
二、提升系统:提升架是滑模与混凝土间的联系构件,主要用于模板体、桁架、滑模工作盘,夹固桁架梁,避免变形,并且通过安装在顶部的千斤顶支撑在爬杆上,整个滑升荷载将通过提升架传递给爬杆,爬杆由φ48*3.5mm的钢管制成,根据施工经验和常规设计,采用“F”型提升架。
“F”型提升架主梁采用[18a槽钢,千斤顶底座为12mm厚钢板,筋板为8mm钢板。
爬杆在每一个墩位设置12根,外模侧设置8根,内模侧设置4根,采用壁厚精度较高的φ48*3.5mm无缝钢管,爬杆连接采用焊接连接,钢管在连接处焊接后,采用磨光机进行打磨,使钢管表面光滑,让千斤顶能顺利通过,焊接处要饱满, 爬杆表面不得有油漆和铁锈。
三、操作平台:操作平台分为主操作平台和辅助工作平台。
主操作平台作为施工的操作平台,承受施工人员、物料等荷载,主操作平台框架采用桁架梁结构,上部满铺5cm 厚脚手板。
辅助工作平台为混凝土养护修面的工作平台,采用钢木结构悬吊布置,沿混凝土面布置一周宽70cm平台,其上满铺5cm厚脚手板,用φ20mm圆钢间隔2米悬挂在提升桁架梁上,并搭设护栏。
四、液压系统:液压提升系统主要由液压千斤顶、液压控制台、油路和支承杆等部分组成。
1、液压千斤顶滑模液压千斤顶型号为:100型楔块式千斤顶,每个千斤顶上安装针型阀,以控制进油。
2、液压控制台液压控制台是液压传动系统的控制中心,是液压滑模的心脏。
主要由电动机、齿轮油泵、换向阀、液压分配器和油箱组成。
高层建筑滑模法与爬模法施工技术研究

高层建筑滑模法与爬模法施工技术研究随着经济的发展和城市化的进程,高层建筑的建设日益增多,其施工难度和安全风险也不断提高。
为此,建筑施工技术得到了广泛的研究和应用,其中滑模法和爬模法是目前比较先进的高层建筑施工技术之一。
本文将对这两种技术进行介绍和比较分析。
一、滑模法施工技术滑模法施工技术是指使用将建筑结构整体化的钢丝绳绕在建筑外壳表面,使钢丝绳相互拉扯,从而拉动建筑整体向上移动的一种技术。
滑模法施工技术具有以下优点:1.施工速度快。
采用滑模法施工技术,可以大幅度提高工期,最大限度地缩短施工周期,且可根据建筑高度和结构等要素进行调整。
2.施工成本低。
相比传统的建筑施工技术,滑模法施工技术人力、物力和材料成本都较低。
此外,滑模法施工技术可以较好地适应多种建筑形式和变化,这为建筑设计和施工方案提供了更多的选择。
3.工序简单。
滑模法施工技术是一种比较简单的施工方式,施工过程中不需要脚手架等辅助结构,减少了工序和材料的使用量,降低了建筑施工人员的劳动强度。
但是,滑模法施工技术也存在一些缺点,例如,需要较高的技术和专业知识,建筑施工人员必须具有一定的技术素质和实践经验,才能够保证施工质量和安全。
爬模法施工技术是指使用爬升机械装置,按建筑轮廓线进行连续升降的一种技术。
爬模法施工技术具有以下优点:1.安全性高。
采用爬模法施工技术可以大幅度提高施工作业的安全性,减少施工中对人员和机具的伤害,并有效保证施工过程中的安全。
2.施工效率高。
采用爬模法施工技术,无需脚手架,施工现场的垃圾清理等环节较为简便,可以大幅度提高施工效率,缩短施工周期。
3.操作简单。
相较于滑模法施工技术,爬模法施工技术操作性较简单,建筑施工人员可以很快掌握,并保证施工质量和效率。
但是,爬模法施工技术也存在一些缺点,例如,施工过程中产生的噪音和振动较大,可能会影响到周围居民的生活。
此外,由于爬升机械装置的高度限制,对于高层建筑的施工效果有一定的影响。
高层建筑滑模法与爬模法施工技术研究

高层建筑滑模法与爬模法施工技术研究高层建筑是城市中的地标性建筑,随着城市化进程的加快,高层建筑的数量和高度也在不断增加。
在高层建筑的施工中,滑模法和爬模法是两种常用的施工技术。
滑模法是将整个楼层的模板和钢筋一起浇筑混凝土,然后利用复合模板衔接,逐步向上推进的一种连续浇筑工艺。
爬模法是在施工过程中,通过升降机将支模系统由下向上架设,然后再浇筑混凝土的一种施工工艺。
本文将详细介绍这两种方法的施工原理,技术要点和应用范围,以及两种方法的优缺点和发展趋势。
一、高层建筑滑模法施工技术1. 施工原理滑模法是将整个楼层的模板和钢筋一起浇筑混凝土,然后利用复合模板衔接,逐步向上推进的一种连续浇筑工艺。
在施工过程中,首先要在地面上拼装好一定长度的支模,然后将模板和钢筋吊装至支模上,进行混凝土浇筑。
当混凝土达到规定强度后,就可以将支模向上推进一定距离,继续进行下一段的浇筑,直到整个楼层的混凝土浇筑完成。
2. 技术要点在滑模法的施工过程中,要严格控制混凝土的配合比和浇筑质量,确保每段混凝土的强度达到要求。
由于滑模法是连续浇筑的工艺,需要采取一系列措施确保混凝土的温度和收缩变形得到有效控制,避免出现裂缝和变形等问题。
还需要对模板和支模系统进行精细的设计和施工,确保施工安全和浇筑质量。
3. 应用范围滑模法适用于高层建筑的整体结构施工,尤其是在高层建筑的主体结构和核心筒的施工中应用较为广泛。
由于滑模法可以实现连续浇筑,更适合高层建筑结构的大体量浇筑,可以提高施工效率和质量。
4. 优缺点和发展趋势滑模法的优点是可以实现连续浇筑,提高施工效率,减少人力、物力和时间成本。
滑模法可以保证混凝土浇筑的质量和一致性,减少因为多次拼装和拆卸而带来的施工质量问题。
但是滑模法也存在一些问题,比如需要更高的技术要求和设备投入,需要进行严格的施工管理和质量控制。
未来,随着高层建筑的数量和高度的不断增加,滑模法将得到更广泛的应用,并且在技术和设备方面将继续得到改进和完善。
2024版滑模爬模翻模施工技术ppt课件
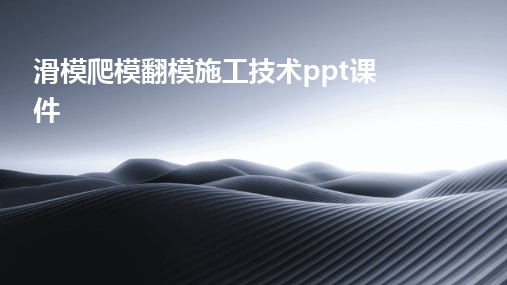
•滑模施工技术概述•爬模施工技术介绍•翻模施工技术讲解•三种施工技术比较与选择目录•施工现场管理与安全措施•质量控制与验收标准解读01滑模施工技术概述滑模施工原理及特点原理特点滑模系统组成与功能由模板、围圈、提升架等组成,用于形成混凝土结构形状。
由油泵、油管、千斤顶等组成,提供滑升动力。
由内外吊架、脚手架等组成,提供施工操作空间。
由传感器、控制台等组成,实现滑模施工的自动化和智能化控制。
模板系统液压系统操作平台系统控制系统适用范围与优势分析适用范围优势分析发展趋势及前景展望发展趋势前景展望未来滑模施工技术将在超高层建筑、大型公共设施等领域得到更广泛的应用,同时还将推动相关产业的发展和进步。
02爬模施工技术介绍爬模基本原理及特点爬模基本原理爬模特点爬升装置控制系统模板系统030201爬升系统组成与功能适用范围与优势分析适用范围适用于高层或超高层建筑的剪力墙、框架柱等竖向结构的施工。
优势分析与传统翻模相比,爬模施工速度更快、安全性更高、质量更易保证;与滑模相比,爬模的模板自爬能力更强,适用范围更广。
发展趋势及前景展望发展趋势前景展望03翻模施工技术讲解翻模基本原理及特点翻模基本原理翻模特点翻转系统组成与功能翻转系统组成由翻转模板、翻转油缸、导向装置、悬挂装置等组成。
翻转系统功能实现模板的快速、准确翻转,提高施工效率和质量。
适用范围与优势分析适用范围优势分析随着科技的不断进步,翻模施工技术将向自动化、智能化方向发展,提高施工效率和质量。
前景展望随着基础设施建设的不断推进和建筑市场的不断扩大,翻模施工技术将在未来得到更广泛的应用和推广。
同时,随着新材料、新工艺的不断涌现,翻模施工技术也将不断创新和发展,为建筑行业带来更多的便利和效益。
发展趋势发展趋势及前景展望VS04三种施工技术比较与选择原理特点原理特点原理在已浇筑的混凝土上安装模板,然后翻转模板进行下一层的施工。
要点一要点二特点模板可重复利用,节约成本,但施工速度相对较慢。
高层建筑滑模法与爬模法施工技术研究

高层建筑滑模法与爬模法施工技术研究高层建筑滑模法和爬模法是现代建筑施工中常用的施工技术,它们在高层建筑的施工过程中发挥着重要的作用。
本文将对高层建筑滑模法和爬模法进行研究,分析其特点、优缺点和适用范围。
高层建筑滑模法是一种以滑模板为基础的施工技术。
它的原理是将预制混凝土板通过液压系统和滑板机构,由远端滑移至近端,使结构不断延伸和增高。
滑模法具有施工效率高、质量稳定、安全可靠等优点。
由于采用了预制混凝土板,施工期间对周边环境的影响较小。
滑模法施工时需要较大的场地和专业设备,而且对施工工序和工期的安排要求较高,施工过程中难以及时进行修正和调整。
爬模法是另一种高层建筑施工技术,它利用爬模架等设备由下往上逐层施工。
爬模法可以根据建筑高度的增加而自动调整,适用于各种高度和形状的建筑物。
它也具有施工速度快、操作方便等优点。
爬模法的设备较为灵活,可以根据施工需求进行调整和改造。
爬模法施工需要密切协调多个施工工序,对施工人员的技术要求较高。
高层建筑滑模法和爬模法的适用范围各有特点。
滑模法适用于结构较为规则、平面形状简单的建筑物,例如高层住宅、办公楼等。
而爬模法则适用于结构形状复杂、高度较大的建筑物,例如塔楼、桥梁等。
根据实际工程需求和施工条件,选择合适的施工技术对于提高施工效率和质量具有重要意义。
高层建筑滑模法和爬模法是现代建筑施工中常用的技术。
它们各具特点,适用范围不同。
在实际施工过程中,需要根据建筑结构、施工条件和工期等因素选择合适的施工技术,以确保施工的顺利进行。
对高层建筑滑模法和爬模法进行进一步的研究和探索,有助于提高施工效率和质量,推动建筑施工技术的创新和发展。
滑模法与爬模法施工技术在超高层建筑中的运用

滑模法与爬模法施工技术在超高层建筑中的运用滑模法与爬模法是一种综合效益高、场地占用少、施工速度快、机械化程度高且安全作业有保障的施工技术,因此被广泛应用于超高层、高层建筑中。
在本案,笔者结合实践经验,分别浅析滑模法与爬模法在超高层建筑中的应用。
标签:滑模法;爬模法;超高层建筑引言超高层建筑主要采用框架梁、框柱梁、剪力墙和核心筒等竖向结构,且上述结构的施工进度与施工质量直接关乎到工程的整体进度和质量,理应加以重视。
在实际施工中,常用的施工技术包括滑模法和爬模法。
滑模法与爬模法施工技术在超高层建筑中的应用均表现出以下优越性:机械化程度高、结构整体性好、施工进度快、节约劳动和模板等。
据此,下文分别介绍滑模法与爬模法在超高层建筑中的应用,以供同行参考。
一、滑模法在超高层建筑中的应用所谓滑模法,是指沿梁、柱、墙等构件在建筑底部组装高约1.2m的滑升模板,并通过液压提升设备,紧随模板内混凝土的分层浇筑高度向上滑升支撑杆,直至达到要求的浇筑高度。
滑模装置通常由模板系统、平台系统和液压提升系统组成。
(一)滑模施工工序滑模法的主要施工工序为:组装滑模、绑模板内筋→插支撑杆→浇初升混凝土→检查和调整相关参数→绑钢筋、浇墙体混凝土、正常滑升→绑墙筋、吊活动平台、空提→支模板→绑钢筋→浇筑混凝土→上一层墙体滑模→拆除模板。
(二)滑模滑升滑模滑升主要分为初升阶段、正常滑升阶段和末升阶段组成。
在初升之前,应按要求进行试升。
在混凝土浇筑完毕约3-4h之后,所有千斤顶一并试升5cm 左右。
若混凝土在出模之初便出现塌落,则可判定混凝土的出模强度不达标;若模板与混凝土粘接,混凝土出现水平裂纹且滑升困难,则说明滑升时间被推迟。
用手按试升滑出的混凝土时,若有指纹,指甲划过留有痕迹,但不粘手,则可进行初升,即上升模板15-24cm,并全面检查模板系统,同时按需进行调整。
在正常滑升模板时,模板的初期提速应比混凝土的灌注速度稍慢,直至混凝土表面与模板上口之间的间距达到10cm左右时,方才按常速滑升,即混凝土浇筑一层,模板滑升一层。
高桥墩施工方法

高桥墩施工方法
高桥墩的施工方法包括液压滑升模板法、翻模施工等。
液压滑升模板法是现浇混凝土结构施工中机械化程度比较高的
活动连续成型施工工艺,具有施工整体性强、施工速度较快等优点。
但由于滑模法施工对连续性要求过高造成施工人员疲劳、不可预见性多的缺点,同时多台千斤顶升同步困难造成偏位控制难度大、滑升设备复杂、对构件截面同一性要求较高及施工投入过大等因素决定不适合在本工程中施工。
翻模施工的主要危险源为拆模、吊装模板和施工人员设置安全围栏。
一般来说,当主跨距L≤ 80m,不对称浇筑混凝土量不超过5立方米。
总的来说,具体采用哪种方法要根据桥墩的高度、设计要求、施工条件等多方面因素进行选择。
爬模、滑模、翻模施工技术优劣对比

锋绘2019年第4期148㊀㊀评价因子权重子因子子因子权重复合权重交通便捷性0.28㊀㊀0.28景观要素0.47人文遗迹0.210.098公园绿地0.220.103绿规规划绿地0.10.047滨水环境0.470.221基础服务设施0.15㊀㊀0.15生态本底0.1㊀㊀0.13㊀总结利用层次分析法得出各因子权重后,利用G I S 软件,对各因子进行权重叠加,得出绿道选线适宜度分析图,由图可以看出霸州绿道选线以及敏感区主要受生态斑块分布影响,分布在中亭河及其支渠㊁市域内植被覆盖区域附近;二级敏感区为人文景观资源分布区;三级敏感区为农田内机耕路㊁农村服务点附近;不敏感区为工矿区和高压线廊等危险区域.参考文献[1]许树柏.实用决策方法:层次分析法原理[M ].天津大学出版社,1988.[2]俞孔坚.«城市绿道规划与设计»[D ].江苏科学技术出版社,2015.[3]蔡眉.滨水绿道地域文化景观设计研究[D ].湖南农业大学,2014.[4]孙帅.都市型绿道规划设计研究[D ].北京林业大学,2013.爬模㊁滑模㊁翻模施工技术优劣对比张㊀燕(重庆交通大学经济与管理学院,重庆400000)摘㊀要:爬模㊁滑模与翻模是框架混凝土结构中较为常用的几种施工方法.在进行施工时,如何根据工程类型㊁特点以及工程所在地地质条件等因素科学合理地选择施工方法,以此来缩短工期,获得经济效益,具有重要的现实意义.本文对爬模㊁滑模㊁翻模的施工方法的优劣以及安全质量控制措施进行了对比,希望为施工方法的选择提供参考.关键词:爬模;滑模;翻模;优劣对比;质量安全控制㊀㊀模板在混凝土施工中至关重要,不同的模板形式决定了混凝土浇筑所采用的施工工艺也不同,对工期以及工程效益也有不同程度的影响.现有的框架混凝土结构主要采用的模板有爬模㊁滑模与翻模,为了正确的选择模板施工方法,对各种模板的优缺点进行了解就显得尤为必要.1㊀爬模施工爬模是爬升模板的简称,国外也叫跳模,爬模由爬架㊁爬升模板及爬升设备三部分组成,常用于桥墩㊁剪力墙体系㊁筒体体系等高耸结构的施工.由于爬模具有自爬的能力,且脚手架可直接悬挂在自爬模板上,所以可以减少吊运作量以及节省外脚手架.1.1㊀优点(1)一般的爬模架在组装之后,除了由于建筑结构的突变而需要对模板进行改装之外,其余情况下可以跟随施工的进程一直上升到顶部而不落地,所以可以节省施工场地的占用面积,减少由于在施工过程中的碰撞而造成的模板损坏.(2)由于怕爬模可以提供全方位的操作平台,所以能够在保障施工人员的安全的前提下为施工人员的操作提供便利,而且不需要再额外搭设操作平台,节省了一部分的人力和物力.(3)相对翻模而言,爬升速度快,模板标准化程度高,整个结构仅用一个液压油泵提升,一次组装;爬升过程中不用再支模㊁拆模㊁搭设脚手架和运输等工作,施工安全度高.1.2㊀缺点(1)考虑到经济型㊁合理性,适用于公路桥梁中高度超过40米的矩形空心墩,而本项目主桥墩身高度约为20m .(2)系统模板造价高,使用过程中保养㊁维护费用高,模板配件标准化高,损坏后需要从厂家定做.(3)对整个顶升系统的机械性能要求较为严格,损坏后需要专人维修.1.3㊀安全保证措施1.3.1㊀高空坠物控制措施为避免高空坠物的发生,模板临边及接缝处防护采取的措施为:采用镀锌钢板加工成 L 型焊接模板四周;模板倒角位置与塔身混凝土之间的空隙采取5m m 厚的钢板进行覆盖,此钢板必须依据倒角大小切割成弧状,固定方式同接缝处;购置成品防护网对爬模外侧进行全部封闭;在爬模上设置物料收纳箱,集中保管施工材料㊁工器具.1.3.2㊀起重伤害控制措施塔柱施工空间有限,施工材料㊁工具多,给作施工作业人员带来诸多不便.为减少起重伤害事故的发生,在进行吊装作业时配备合格的司索工㊁信号工,严格执行 十不吊 的操作规程,在吊装作业半径范围外设置警戒区域,设专人值守.吊装大型材料时停止相关及交叉作业.1.4㊀施工质量控制措施在对桥梁墩身混凝土施工以前,需检查模板㊁混凝土表面以及混凝土外表面的光滑度是否符合要求;此外,在保证各类预埋件的安装位置准确的基础上,进行爬模施工时不能将基础遗漏.2㊀滑模施工滑模也称滑动模板,是以滑模千斤顶㊁电动提升机等为提升动力,带动模板(或滑框)沿着混凝土(或模板)表面滑动而成型的现浇混凝土结构的施工方法的总称,预先在混凝土结构内埋置钢管(支承杆),以千斤顶㊁提升架将滑升模板施工荷载转至支承杆,待混凝土强度达到要求后,利用液压提升系统沿支承提升整个装置,完成循环作业.2.1㊀优点(1)采用滑模施工可以降低施工成本,常用于筒体结构㊁结构施工工艺有较多的重复以及上下层的竖向结构布置变化不大的高层建筑等工程的施工.(2)通过采用滑模施工的方法,可以解决材料堆放在施工过程中的场地限制问题.(3)通过液压滑模施工组装模板时,当模板的高度大于1m时,就可以连续浇筑混凝土成型,结构整体性好,提高工程质量;在进行筒仓施工时,可以一次性组装滑升,施工过程中不需采用脚手架,每天滑升的高度最高可达5m,与普通模板相比,施工速度快,模板损耗率低,可以节省大量的成本和工期.2.2㊀缺点在滑模的施工过程中,很难控制滑模滑动的时间,只能依靠经验进行判断,若滑动过早,则容易导致混凝土表面的不平整,若滑动的过晚,则容易使混凝土水平方向产生裂缝.此外,滑模对提升系统刚度的要求较高,若支撑杆有弯曲的现象,则墩身的竖直度就很难得到保证,该方法不适用于变截面以及设有中系梁的高墩施工.2.3㊀安全保证措施(1)在混凝土施工前,做好对施工人员的安全交底,提高施工人员的安全意识,保障施工人员的人身安全.(2)混凝土浇筑前须派专职安全人员进行安全隐患排查,若发现问题应及时通知班组进行整改工作.(3)考虑到滑模系统内均为钢结构,为保证操作平台施工人员的安全,所使用的照明电源必须采用36V 低压电源.2.4㊀施工质量控制措施(1)控制好台墩的垂直度.需要保证操作平台的垂直度,应该将材料均匀的放置在操作平台,在浇注混凝土时应该分层㊁分段㊁对称的浇筑.(2)要准确的安装模板.为了保证滑模组装后在后面的施工过程中不再进行拆装,在组装模板之前,应认真的检查起滑线以下已经完成的施工结构的尺寸和标高,并对设计轴线㊁结构边线以及提升架的位置进行标记.(3)控制好爬杆的弯度.对爬杆的弯度控制可以分为两种情况,当爬杆中弯度较小的时候,可以将爬杆与墩台的主筋焊接在一起;当爬杆中的弯度较大时,应该将弯曲程度较大的部分切除之后再焊接一根新的爬杆,并在新爬杆和混凝土接触的部分垫10m m左右厚的刚靴.3㊀翻模施工翻模即用两节或三节模板进行墩身浇筑,每次浇筑完成后,通过拆除下面一节或二节模板,始终预留上一节模板作为上部新装模板的支撑承重系统,上部模板主要靠下部预留模板和墩身之间的摩阻力和拉杆支撑力来支撑,从而实现交替上升,完成墩身浇筑.3.1㊀优点(1)施工工艺简单,模板的提升可以直接采用塔吊或吊车进行,不需配备专用的提升油泵,节省材料.(2)模板可以周转使用,节约成本,经济优势明显,可自由的调节浇筑高度.(3)模板拼装容易,内模可现场进行加工拼装,施工速度快,适用范围广.3.2㊀缺点(1)墩身平面位置难以控制,模板上下接头间的接缝若处理不好容易出现错台,抗风能力差(2)模板操作平台需单独设计,搭设拼装不好操作,模板的拆卸也比较麻烦,且容易导致安全事故.(3)墩身预埋件数量要少,对模板拉杆的质量要求要高,吊装作业次数较多.3.3㊀安全保证措施(1)施工前,应做好对每一个工序的风险分析,定期对机具进行检查㊁维修与保养,确保机具正常运行.(2)在高温天气进行混凝土浇筑时,应控制好混凝土的入模温度;如遇雷雨以及4级以上的大风天气,施工人员应及时撤离现场,并停止各种机械以及模板安拆作业.(3)操作平台上严禁堆放重物,对于易滑落的物体应采取临时固定措施;应按要求布设安全网,对于操作平台的转角处以及预留孔洞处应采用钢筋网片进行防护.3.4㊀施工质量控制措施空心薄壁墩的墩身钢筋主筋之间应采用螺纹套筒进行连接;在钢筋安装时,应提前埋设下一节墩身的预留钢筋;采用C50高强度混凝土垫块按照梅花形布置钢筋保护层.在混凝土浇筑前,应对混凝土接触面凿毛洗净,并检查模板的平整度㊁接缝是否符合规范,保证钢筋焊接平滑,无错台现象;混凝土的浇筑应对称同时进行,振捣应该及时.当混凝土达到一定强度在进行脱模,脱模后应及时覆盖并进行养生.4㊀结语爬模㊁滑模与翻模都各具特点,可分别用于不同的混凝土结构类型.采用爬模浇筑的混凝土实体及外观质量较好,适用于钢筋混凝土竖直或倾斜结构,范围较广.滑模具有施工速度快,安全性高的特点,适用于等截面或变截面薄壁空心混凝土等结构,应用范围较窄;而翻模在滑模的基础之上可广泛适用于各种结构,但其施工进度相对较慢.在实际的施工过程中,可根据施工条件以及工期质量等的要求合理的选择适用的模板.参考文献[1]张磊.核心筒液压爬模在包头金融文化中心工程I标段项目中的应用.建筑工程技术与设计[J],2016,(32):253.[2]蒋晓磊.滑模法在桥梁墩柱建设中的应用及施工要点[J].山西建筑,2016,42(12):173G174.[3]张群,张林刚.浅谈公路软土地基处理现状[J].中国科技纵横,2011,(12):275,72.锋绘2019年第4期149㊀。
- 1、下载文档前请自行甄别文档内容的完整性,平台不提供额外的编辑、内容补充、找答案等附加服务。
- 2、"仅部分预览"的文档,不可在线预览部分如存在完整性等问题,可反馈申请退款(可完整预览的文档不适用该条件!)。
- 3、如文档侵犯您的权益,请联系客服反馈,我们会尽快为您处理(人工客服工作时间:9:00-18:30)。
液压爬模系统
投入较大,施工质量相对较差 施工进度快、施工安全度高、劳动强度 。不便于在施工和养护期间对 低、便于操作 桥墩混凝土进行保温和养护。
千斤顶顶升系统
1、材料投入少,工艺简单,可直接使用 塔吊或吊车提升,不需要再安装专用提 升油泵。 2、投资少,经济优势明显,模板可周转 使用,每次浇筑高度可随时调节。 3、模板拼装简单,通用性强,内模可现 场加工拼装,施工速度较快。
1、模板上下节段间接缝控制不 好容易出现错台,墩身平面位 置不好控制,抗风能力差。 2、模板周围的操作平台不好搭 设,需单独设计,人工拼装和 拆卸模板时不好操作,易发生 安全事故。 3、模板拆除后,脱模剂涂抹不 便。 4、墩身预埋件数量要少,对模 板拉杆的质量要求要高。吊装 作业次数较多。
塔吊、吊车
方案二
滑模法
滑模装置由模板系统、操作平台系统、 液压提升系统和垂直运输系统等四大系 统组成。滑模施工工艺原理是预先在墩 身混凝土结构中埋置钢管(称之为支承 杆),利用千斤顶与提升架将滑升模板 的全部施工荷载转至支承杆上,待混凝 土具备规定强度后,通过自身液压提升 系统将整个装置沿支承杆上滑,模板定 位后又继续浇筑混凝土并不断循环的一 种施工工艺。
1、考虑到经济型、合理性,适 用于公路桥梁中高度超过40米 的矩形空心墩,而本项目主桥 墩身高度约为20m。 2、系统模板造价高,使用过程 中保养、维护费用高,模板配 件标准化高,损坏后需要从厂 家定做。 3、浇筑高度不能调节,一次只 能浇筑4.5/6米。 4、对整个顶升系统的机械性能 要求较为严格,损坏后需要专 人维修。
较
施工效率 经济投入 外观质量 备注
每次混凝土浇筑高度 约为4.5m-6m,约5-6 天一个循环。
较大
较好
一般混凝土的浇筑及 提升速度为平均 0.2m/h,模板高度为 0.9-1.5m。
较大
较差
翻模模板分2-3节, 每次浇筑高度约为4- 塔吊较大,吊 6m,约5-6天一个循 车较小 环。
较好
液压爬模法、滑模
项目 施工方法 简介
方案一
液压爬模法
自爬模的顶升运动通过液压油缸对导轨 和爬架交替顶升来实现。导轨和爬模架 二者之间可进行相对运动。在爬模架处 于工作状态时,导轨和爬模架都支撑在 埋件支座上,两者之间无相对运动。退 模后就可在退模留下的爬锥上安装受力 螺栓、挂座体及埋件支座,调整上下换 向盒舌体方向来顶升导轨。待导轨顶升 到位,就位于该埋件支座上后,操作人 员可转到下平台去拆除导轨提升后露出 的下部埋件支座、爬锥等。在解除爬模 架上所有拉杆之后就可以开始顶升爬模 架,这时候导轨保持不动,调整上下舌 体方向后启动油缸,爬模架就相对于导 轨向上运动。通过导轨和爬模架这种交 替附墙,提升对方,爬模架沿着墙体上 升,直到坐落于预留爬锥上,就这样实 现逐层提升。
方案三
ห้องสมุดไป่ตู้
翻模法
翻模即用两节或三节模板进行墩身浇 筑,每次浇筑完成后,通过拆除下面一 节或二节模板,始终预留上一节模板作 为上部新装模板的支撑承重系统,上部 模板主要靠下部预留模板和墩身之间的 摩阻力和拉杆支撑力来支撑,从而实现 交替上升,完成墩身浇筑。
液压爬模法、滑模法、翻模法的优劣点比较
优点 1、液压爬模可整体爬升,也可单榀爬 升,爬升稳定性好。 2、自重较轻,利用预埋在墩身的高强螺 栓支撑,操作方便,安全性高,可节省 大量工时和材料,模板抗风能力很好。 3、除了因为建筑结构的要求(如墙面突 然缩进或形状突变)需要对模架改造之 外,一般情况下爬模架一次组装后,一 直到顶不落地,节省了施工场地,而且 减少了模板(特别是面板)的碰伤损毁。 4、液压爬升过程平稳、同步、安全。 5、提供全方位的操作平台,施工单位不 必为重新搭设操作平台而浪费材料和劳 动力,施工人员易操作,安全系数较高 。 6、墩身垂直度和平整度易调控,结构施 工误差小,纠偏简单,施工误差可逐层 消除,避免施工误差的积累。 7、相对翻模而言,爬升速度快,模板标 准化程度高,整个结构仅用一个液压油 泵提升,一次组装;爬升过程中不用再支 模、 拆模、 搭设脚手架和运输等工作, 施工安全度高。 缺点 模板提升方式