玻璃窑炉的节能
玻璃窑炉节能技术路径优化与创新

玻璃窑炉节能技术路径优化与创新玻璃窑炉节能技术路径优化与创新玻璃窑炉是玻璃行业中最耗能的设备之一,如何优化和创新玻璃窑炉的节能技术路径成为了一个重要问题。
下面将从以下几个步骤逐步思考如何进行优化和创新。
第一步:节约玻璃窑炉的燃料消耗玻璃窑炉的主要能源消耗是燃料,因此首先需要思考如何节约燃料的消耗。
一种常见的做法是采用高效燃烧技术,例如预混燃烧技术和循环燃烧技术。
预混燃烧技术可以将燃料和空气充分混合,提高燃烧效率;而循环燃烧技术可以将燃烧产生的废热回收利用,进一步降低能源的消耗。
第二步:提高玻璃窑炉的热效率除了节约燃料消耗外,还可以通过提高玻璃窑炉的热效率来进一步节能。
一种常见的方法是采用高效的热交换器,将燃烧产生的废热回收利用。
此外,可以考虑对玻璃窑炉进行隔热处理,减少热量的散失。
这些措施可以有效提高玻璃窑炉的热效率,降低能源消耗。
第三步:优化玻璃窑炉的操作控制系统除了改进玻璃窑炉的内部结构和设备外,优化操作控制系统也是一个重要方面。
通过引入先进的自动化控制系统,可以实时监测和调整玻璃窑炉的运行状态,以最优的方式控制燃烧过程和热量分配。
这样可以确保玻璃窑炉的运行效率最大化,进一步降低能源消耗。
第四步:引入清洁能源替代传统燃料除了上述的措施外,还可以考虑引入清洁能源来替代传统燃料,进一步减少环境污染和能源消耗。
例如,可以考虑采用天然气、生物质能源或太阳能等清洁能源作为玻璃窑炉的燃料。
这样不仅可以降低碳排放和能源消耗,还可以提高企业的环境形象和可持续发展能力。
综上所述,优化和创新玻璃窑炉的节能技术路径可以通过节约燃料消耗、提高热效率、优化操作控制系统和引入清洁能源等多个方面来实现。
通过科学合理的设计和技术改进,玻璃窑炉的能源消耗将得到有效降低,进一步推动玻璃行业的可持续发展。
窑炉节能措施的实施及应用

窑炉节能措施的实施及应用摘要:近年来,国家对于环境保护越来越重视。
在“双碳”目标的要求下,各行各业都在朝着节能减排各个细节深挖潜力。
窑炉是建材、轻工及冶金等行业的热工设备,其通常是用耐材及钢构组合砌筑而成,结合实际需要,能够建造不同类型不同规模的窑炉,借助电、油、燃气等达到高温运行目的。
依照不同品种,窑炉可划分成搪瓷窑、玻璃窑、水泥窑、陶瓷窑炉等。
大型窑炉所用燃料,以天然气居多,其次是轻柴油、煤气、重油等,电窑一般规模较小,通常是以钼棒、硅碳棒、电炉丝等为主要的发热元件,总体结构相对简洁,实操极具便捷性。
窑炉总体结构设计、燃料及其燃烧方式、耐火材料选定等,均关系着其能否实现节能运行。
为确保能够达到这一目标,对窑炉各项节能措施有效实施与其应用开展综合分析较为必要。
关键词:窑炉;节能措施;实施应用引言针对工业窑炉节能减排的技术特点进行详细探索和研究,在此基础上进行优化与集成处理,完成企业生产过程中对窑炉污染与能量消耗的控制,同时还对窑炉设备使用特点制定出窑炉型号以及结构上的优化策略,解决模型建立问题,从根本上完成窑炉使用者、窑炉生产企业以及第三方技术服务企业之间的信息沟通。
1窑炉节能减排技术价值窑炉设备作为工业发展的核心条件,对于工业进步和成长具有十分重要的中作用和现实意义,该设备主要通过充分燃烧燃料从而产生热能物质。
按照行业生产模式一般分为水泥窑炉、蒸汽炉、玻璃窑炉、裂解炉等方面,所以窑炉行业未来发展趋势应侧重在环保行业,对于窑炉自身的基础保温效果来说,增加窑炉基础燃烧率、热能使用率、减少窑炉基础散热、提升窑炉耐火性能同样成为提高要炉设备节能水平的重要途径。
对于工业窑炉来说,设备隔热保温材料对于设备使用质量和效果具有举足轻重的作用,只有使用高水平保温材料,才能从根本上解决设备使用过程中对于环保型的实际需求。
技术人员针对窑炉设备长期跟进和管理最终发现,窑炉设备节能改造技术方式相对比较复杂,比如:使用全新燃烧嘴、调整炭烧嘴布置与设定、完善码胚防止位置、安装烟道、对于梭式窑炉进行热量利用、选择适合的温度检测位置点以及控制方法、增加窑炉隔热保温性能等。
节能环保型玻璃窑炉开发与应用方案(二)
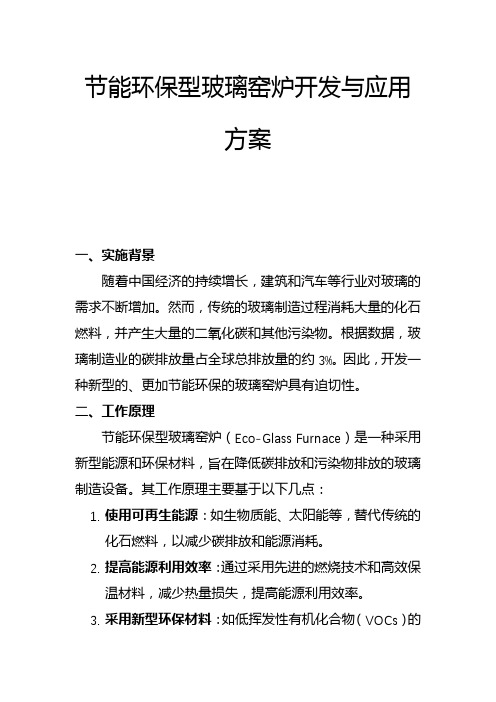
节能环保型玻璃窑炉开发与应用方案一、实施背景随着中国经济的持续增长,建筑和汽车等行业对玻璃的需求不断增加。
然而,传统的玻璃制造过程消耗大量的化石燃料,并产生大量的二氧化碳和其他污染物。
根据数据,玻璃制造业的碳排放量占全球总排放量的约3%。
因此,开发一种新型的、更加节能环保的玻璃窑炉具有迫切性。
二、工作原理节能环保型玻璃窑炉(Eco-Glass Furnace)是一种采用新型能源和环保材料,旨在降低碳排放和污染物排放的玻璃制造设备。
其工作原理主要基于以下几点:1.使用可再生能源:如生物质能、太阳能等,替代传统的化石燃料,以减少碳排放和能源消耗。
2.提高能源利用效率:通过采用先进的燃烧技术和高效保温材料,减少热量损失,提高能源利用效率。
3.采用新型环保材料:如低挥发性有机化合物(VOCs)的玻璃熔剂,以减少污染物排放。
4.余热回收:将高温烟气的余热回收,用于预热助燃空气和提高玻璃液的温度,进一步降低能源消耗。
三、实施计划步骤1.需求分析:对现有的玻璃制造业进行深入调研,了解其生产过程、能源消耗和污染物排放情况。
2.方案设计:基于需求分析结果,设计节能环保型玻璃窑炉的方案,包括设备选型、工艺流程和控制系统等。
3.设备制造:与设备制造商合作,定制生产节能环保型玻璃窑炉。
4.现场安装与调试:将设备安装到选定的玻璃制造工厂,并进行调试。
5.示范运行:在完成安装和调试后,进行示范运行,收集运行数据和评估效果。
6.推广应用:根据示范运行结果,制定推广应用计划,将节能环保型玻璃窑炉应用到更多的玻璃制造工厂。
四、适用范围本方案适用于各种规模的玻璃制造工厂,特别是大型的、能源消耗高的玻璃制造企业。
这些企业具有较强的环保意识和竞争力,更加适合引入新型的节能环保技术。
五、创新要点1.使用可再生能源:本方案将可再生能源引入到玻璃制造过程中,减少了化石燃料的消耗,降低了碳排放。
2.提高能源利用效率:通过采用先进的燃烧技术和高效保温材料,提高能源利用效率,降低了生产成本。
玻璃窑炉热平衡测试及节能分析

期
�
� � � � � � � � � � � � � � � � � � � � � � � � � � � � � � � � � � � � � � � � � � � � � � � � �
� � �� � �� � � � � �� � �� � � �� � �� � � � �� � �� � � � �� � �� � � � �� � �� � � �� � �� � � �� � �� � � �� � �� � � � �� � �� � � � �� � �� �
�献文考参
� � �� 。元万 �� � �� 约 油 重 约 节 可 年 每 则 � 约益效济经生产年每
�造改行进术技进先述上用采炉窑璃玻该对如 。行运能节效高炉窑保确而从 �数参行运 �析分测监动自施实况状 烧燃炉窑璃玻节调时适并 �仪析分测监动自线在气烟的进先用采 烧燃对
� � 为约度温烟排口出其故 �炉锅 �℃� 制控失损烟排
� � � � � � � � � �
� 热显料合配
� 热显体气流溢口孔
� � � �
� 热显气空入漏 � 热显质介化雾 � 热显气空燃助
� �
� 热散射辐口孔 � 热散面表炉窑
用 利 与 究 研 源 能
� � � 热潜出带液璃玻 � � � 热显出带液璃玻
� 热显料燃
� � � 热烧燃料燃
�・ � � �值 数
� � � � � � � � �心中务服术技能节市京南 京南 苏江
人照沈
析分能节及试测衡平热炉窑璃玻
验经场现
� �・ � � 的� � � 少减 ・ �料燃约节 �率效热高提而从 � 放 排� � � 绝杜 、度温焰火嘴喷高提 、失损烟排 可并放排�
二代浮法新型节能技术在玻璃熔窑应用实例

我国是玻璃生产大国,截至2021年9月中旬,我国浮法玻璃熔窑共计305座,在产265座,日熔化量174925吨,占全世界浮法玻璃在产产能58%;超白压延玻璃熔窑66座,日熔化量40210吨,占全世界超白压延玻璃在产产能90%。
而玻璃企业是能耗大户,燃料成本占玻璃生产总成本的40%。
在3060碳达峰、碳中和“双碳战略”以及“十四五”能耗总量控制、能耗强度控制“双控目标”国家政策的高压态势下,玻璃行业迫切需要节能新材料和节能新技术,来进一步降低燃料消耗并减少污染排放,同时降低运行成本、提高玻璃企业的产品竞争力。
中建材蚌埠玻璃工业设计研究院(以下简称“中建材蚌埠院”)在熔窑节能领域做了大量研发工作,并取得了卓有成效的创新成果。
其中,玻璃熔窑用红外高辐射节能涂料(以下简称“红外节能涂料”)与二代新型保温节能技术,作为玻璃熔窑节能新材料和节能新技术,被评为“二代浮法玻璃技术与装备优秀创新成果”,成为二代浮法玻璃熔窑标志性节能创新成果和设计标配。
01节能原理1.1 红外高辐射节能涂料的节能原理随着玻璃生产工艺的改进和节能技术水平的提升,我国普白玻璃单耗大约在1300~1550 Kcal/kg玻璃液,熔窑热吸收效率在42%~50%,平均热效率在46%左右。
这与国外工业炉的平均热效率均在50%以上存在一定的差距[1]。
那么,如何才能提高窑炉的热效率呢?众所周知,高温环境下炉膛内部的热量传递以辐射为主,辐射传热所传递的能量占总能量的80%以上。
而一般耐火材料(如优质硅砖)高温下的发射率只有0.4左右[2](如图1所示)。
因此,提高炉膛内表面的发射率,就可以提高熔窑的热吸收效率。
图1 玻璃熔窑内部耐火材料传热示意图中建材蚌埠院研发的“玻璃熔窑用红外高辐射节能涂料”,正是这样一种高发射率的功能性涂料。
将它涂覆在玻璃熔窑内表面,可以将高温下(1600℃)熔窑内表面的发射率从0.4提高到0.9以上。
也就是说,可以将窑炉内表面辐射传热效率提高一倍以上。
浮法玻璃窑炉的有效节能三种途径
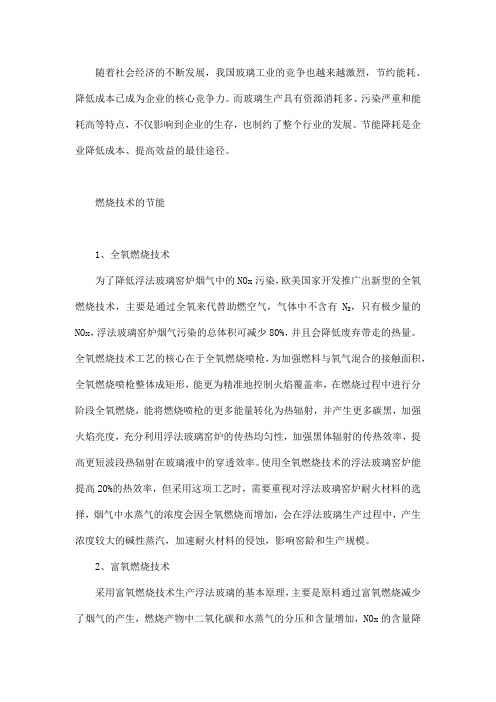
随着社会经济的不断发展,我国玻璃工业的竞争也越来越激烈,节约能耗、降低成本已成为企业的核心竞争力。
而玻璃生产具有资源消耗多、污染严重和能耗高等特点,不仅影响到企业的生存,也制约了整个行业的发展。
节能降耗是企业降低成本、提高效益的最佳途径。
燃烧技术的节能1、全氧燃烧技术为了降低浮法玻璃窑炉烟气中的NOx污染,欧美国家开发推广出新型的全氧燃烧技术,主要是通过全氧来代替助燃空气,气体中不含有N₂,只有极少量的NOx,浮法玻璃窑炉烟气污染的总体积可减少80%,并且会降低废弃带走的热量。
全氧燃烧技术工艺的核心在于全氧燃烧喷枪,为加强燃料与氧气混合的接触面积,全氧燃烧喷枪整体成矩形,能更为精准地控制火焰覆盖率,在燃烧过程中进行分阶段全氧燃烧,能将燃烧喷枪的更多能量转化为热辐射,并产生更多碳黑,加强火焰亮度,充分利用浮法玻璃窑炉的传热均匀性,加强黑体辐射的传热效率,提高更短波段热辐射在玻璃液中的穿透效率。
使用全氧燃烧技术的浮法玻璃窑炉能提高20%的热效率,但采用这项工艺时,需要重视对浮法玻璃窑炉耐火材料的选择,烟气中水蒸气的浓度会因全氧燃烧而增加,会在浮法玻璃生产过程中,产生浓度较大的碱性蒸汽,加速耐火材料的侵蚀,影响窑龄和生产规模。
2、富氧燃烧技术采用富氧燃烧技术生产浮法玻璃的基本原理,主要是原料通过富氧燃烧减少了烟气的产生,燃烧产物中二氧化碳和水蒸气的分压和含量增加,NOx的含量降低,火焰黑度加大,火焰温度提升,加快了原料的燃烧过程,提高了火焰在配合料与玻璃液之间的传热效率,从而提高了浮法玻璃窑炉的熔化效率。
富氧燃烧技术对燃烧设备具有更高要求。
燃料在燃烧过程中需要氧气,这些氧气通常来源于空气,但氧气在助燃空气中仅占21%的比重,而空气中其余的氮气并不会参加燃烧,反而会吸收大量的热量,阻碍燃烧效率的提高,增加燃料消耗。
因此提高空气中的氧气含量,可以更好地保持热量,提高燃料利用效率。
用28%的富氧空气进行燃烧试验时,热量损失减少25%,热量损失的减少也降低了燃料消耗。
浮法玻璃熔窑节能_燃烧技术及保窑
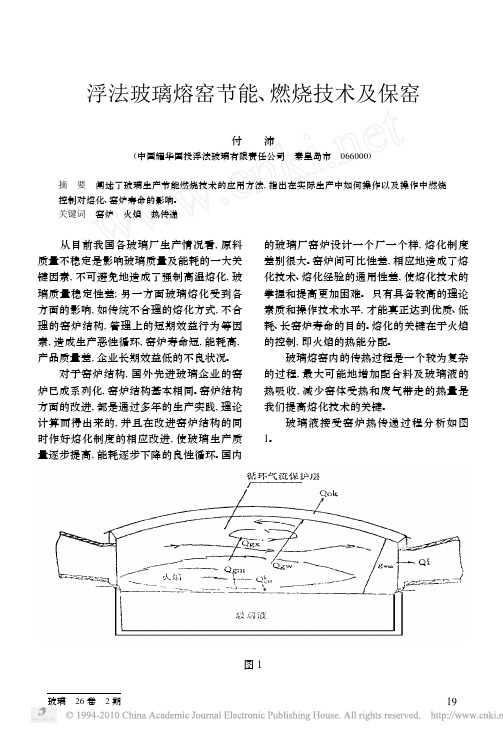
浮法玻璃熔窑节能、燃烧技术及保窑付 沛(中国耀华国投浮法玻璃有限责任公司 秦皇岛市 066000)摘 要 阐述了玻璃生产节能燃烧技术的应用方法,指出在实际生产中如何操作以及操作中燃烧控制对熔化、窑炉寿命的影响。
关键词 窑炉 火焰 热传递 从目前我国各玻璃厂生产情况看,原料质量不稳定是影响玻璃质量及能耗的一大关键因素,不可避免地造成了强制高温熔化,玻璃质量稳定性差;另一方面玻璃熔化受到各方面的影响,如传统不合理的熔化方式,不合理的窑炉结构,管理上的短期效益行为等因素,造成生产恶性循环,窑炉寿命短,能耗高,产品质量差,企业长期效益低的不良状况。
对于窑炉结构,国外先进玻璃企业的窑炉已成系列化,窑炉结构基本相同。
窑炉结构方面的改进,都是通过多年的生产实践,理论计算而得出来的,并且在改进窑炉结构的同时作好熔化制度的相应改进,使玻璃生产质量逐步提高,能耗逐步下降的良性循环。
国内的玻璃厂窑炉设计一个厂一个样,熔化制度差别很大。
窑炉间可比性差,相应地造成了熔化技术、熔化经验的通用性差,使熔化技术的掌握和提高更加困难。
只有具备较高的理论素质和操作技术水平,才能真正达到优质、低耗、长窑炉寿命的目的。
熔化的关键在于火焰的控制,即火焰的热能分配。
玻璃熔窑内的传热过程是一个较为复杂的过程,最大可能地增加配合料及玻璃液的热吸收,减少窑体受热和废气带走的热量是我们提高熔化技术的关键。
玻璃液接受窑炉热传递过程分析如图1。
图1 玻璃液接受的总热量为:Q m=Εg m C o[(T g100)4-T m100)4]F m+Εwm C o[(T w100)4-T m100)4]F m+Αgm k(t g-t m)F m(kcal h)式中:Q m——玻璃液吸收总热量;Q gm——火焰以辐射方式传给的热量;Q gm k——火焰以对流方式传给的热量;Q wm——窑壁以辐射方式传给的热量;Εgm——火焰对玻璃液的相对黑度;Εwm——窑壁对玻璃液的相对黑度;F m——火焰下玻璃液的受热面积;T g——火焰温度;T m——玻璃液温度;T w——窑壁温度;Αgm k——气体对玻璃液的对流给热系数;C o——火焰辐射系数。
浮法玻璃熔窑节能技术及途径.
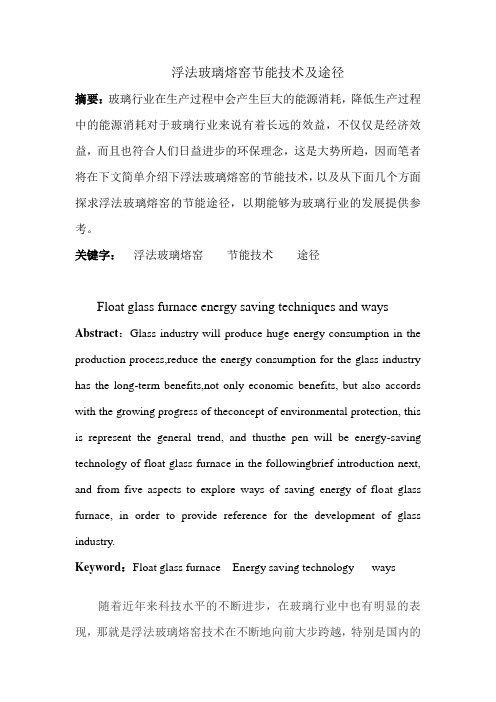
浮法玻璃熔窑节能技术及途径摘要:玻璃行业在生产过程中会产生巨大的能源消耗,降低生产过程中的能源消耗对于玻璃行业来说有着长远的效益,不仅仅是经济效益,而且也符合人们日益进步的环保理念,这是大势所趋,因而笔者将在下文简单介绍下浮法玻璃熔窑的节能技术,以及从下面几个方面探求浮法玻璃熔窑的节能途径,以期能够为玻璃行业的发展提供参考。
关键字:浮法玻璃熔窑节能技术途径Float glass furnace energy saving techniques and ways Abstract:Glass industry will produce huge energy consumption in the production process,reduce the energy consumption for the glass industry has the long-term benefits,not only economic benefits, but also accords with the growing progress of theconcept of environmental protection, this is represent the general trend, and thusthe pen will be energy-saving technology of float glass furnace in the followingbrief introduction next, and from five aspects to explore ways of saving energy of float glass furnace, in order to provide reference for the development of glass industry.Keyword:Float glass furnace Energy saving technology ways 随着近年来科技水平的不断进步,在玻璃行业中也有明显的表现,那就是浮法玻璃熔窑技术在不断地向前大步跨越,特别是国内的保温材料和耐火材料都在原基础上取得了巨大的进步,有进步虽然可喜,但是尚不足以与国外同领域的技术相比肩,或许通过以下数字大家能够更直观地看出差距所在,国外较先进的浮法玻璃熔窑技术最高产生55%的热效率,而我国最高产生40%。
我国玻璃窑炉的节能
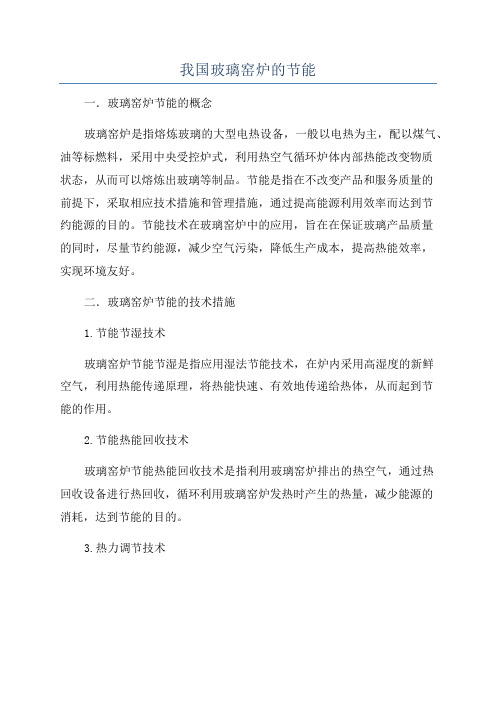
我国玻璃窑炉的节能
一.玻璃窑炉节能的概念
玻璃窑炉是指熔炼玻璃的大型电热设备,一般以电热为主,配以煤气、油等标燃料,采用中央受控炉式,利用热空气循环炉体内部热能改变物质
状态,从而可以熔炼出玻璃等制品。
节能是指在不改变产品和服务质量的
前提下,采取相应技术措施和管理措施,通过提高能源利用效率而达到节
约能源的目的。
节能技术在玻璃窑炉中的应用,旨在在保证玻璃产品质量
的同时,尽量节约能源,减少空气污染,降低生产成本,提高热能效率,
实现环境友好。
二.玻璃窑炉节能的技术措施
1.节能节湿技术
玻璃窑炉节能节湿是指应用湿法节能技术,在炉内采用高湿度的新鲜
空气,利用热能传递原理,将热能快速、有效地传递给热体,从而起到节
能的作用。
2.节能热能回收技术
玻璃窑炉节能热能回收技术是指利用玻璃窑炉排出的热空气,通过热
回收设备进行热回收,循环利用玻璃窑炉发热时产生的热量,减少能源的
消耗,达到节能的目的。
3.热力调节技术。
浮法玻璃退火窑的废气治理与节能改善

浮法玻璃退火窑的废气治理与节能改善浮法玻璃是一种广泛应用于建筑、汽车及家电行业的平板玻璃制造工艺。
在浮法玻璃生产中,退火窑是一个关键环节,负责使玻璃板块稳定冷却以增强其物理性能。
然而,退火窑运行过程中产生的废气对环境和能源资源都造成了一定的影响。
因此,废气治理与节能改善成为了浮法玻璃退火工艺中亟待解决的问题之一。
废气治理是指对退火窑产生的废气进行处理,以减少对环境的污染。
废气中主要包含二氧化碳、氮气、一氧化碳和少量微量有机物等。
这些废气的释放会导致大气污染,甚至对人体健康造成威胁。
因此,采取有效措施对废气进行治理至关重要。
首先,可以采用物理处理方法,如引入高效旋风分离器和静电除尘装置。
高效旋风分离器通过离心力将废气中的颗粒物进行分离,静电除尘装置则利用电场力将废气中的颗粒物捕集。
这样可以大大降低废气中的颗粒物含量,减少对环境的影响。
此外,还可以采用化学处理方法,如利用脱硫装置和脱氮装置进行废气脱硫和脱氮。
脱硫装置通过加入适量的吸收剂,使废气中的二氧化硫与吸收剂产生反应,形成不溶于水的硫酸盐,从而达到除硫的目的。
脱氮装置则通过催化剂催化氮氧化物,将其转化为氮气和水,从而达到除氮的效果。
除了废气治理,浮法玻璃退火窑的节能改善也是一项重要任务。
传统的玻璃退火窑采用直燃方式进行加热,存在能源浪费和环境污染问题。
为了解决这一问题,可以采取以下措施:首先,可以采用余热回收技术。
在退火窑废气中,有相当多的热量被浪费,通过引入余热回收系统,可以将废气中的热量回收利用,供应给其他工艺流程或者加热用途。
这样不仅能够提高能源利用效率,还能够降低对其他能源的需求。
其次,可以引入燃气涡轮发电技术。
这种技术利用废气中的热能直接驱动燃气涡轮发电机,将热能转化为电能。
这样不仅可以提供部分电力需求,还能将废气中的热能转化为一种可利用的形式,减少能源的浪费。
另外,可以改善窑炉内部结构,优化燃烧系统。
通过合理设计燃烧系统,选择高效的燃烧器,提高燃烧效率和传热效率,从而降低能源消耗。
我国玻璃窑炉的节能

我国玻璃窑炉的节能王辰亚(中国节能协会玻璃窑炉专业委员会)前言:各级领导的关心和重视,中国节能协会玻璃窑炉专业委员会的大力推动,使我国玻璃窑炉节能技术得到了广泛的推广应用,科学节能的经营管理得到了加强,全国玻璃窑炉节能已取得了实效,节能效果显著。
玻璃窑炉的节能,实际是玻璃工业全方位综合性系统工程实施的问题,缺一不可。
是玻璃工业节能技术中的一个大课题,本文将试探性的加以论述,以达到抛砖引玉的目的。
一、我国玻璃工业窑炉能耗现况:我国大约有4000 ~5500 座各种类型的玻璃窑炉,其中熔化面积80m2 以下的中小型炉数量大约占总量的80 %左右,使用燃料种类分:燃煤炉约占63 %,燃油炉约占29%,天然气炉、全电熔炉等约占8%。
2008 年全国玻璃产量大约为2000 ~3000 万吨。
年耗用标准煤1700 ~2100 万吨。
其中平板玻璃产量为53192 万重量箱,所用能耗折合标准煤1000 万吨/年。
平均能耗为7800 干焦/公斤玻璃液,窑炉热效率20 ~25%,比国际先进指标30%≦低5%~1 0 %。
每年排放SO2约16万吨、烟尘1.2 万吨、NOx14 万吨。
玻璃熔窑在玻璃工厂中是消耗燃料最多的热工设备,一般,占全厂总能耗的80~85 %左右,目前我国玻璃工业所用的主要能源是:煤、油、电和天然气等燃料。
由于燃料价格几年来持续上涨,企业燃料成本逐年增加,效益锐减,在此形势下,玻璃工业根据我国能源蕴藏品种结构、分布、数量和价格等不得不做使用调整。
使以前规划设计推行的使用清洁、高热值能源的思路发生了一定的变化。
即近几年来企业欲争取较大效益。
有不少燃油炉改成燃煤炉,以此带来不小的环境保护问题。
当然这几年随着我国电力工业的发展,全氧炉、电助熔、全电熔炉有了较大的发展。
(Emisshield 能用于哪种燃料??)2008 年日用玻璃产量1445.7 万吨,如成品率平均为90%,年玻璃出料量应为1590 万吨,年耗标煤557 ~636 万吨。
玻璃窑炉能耗限额-概述说明以及解释

玻璃窑炉能耗限额-概述说明以及解释1.引言1.1 概述概述玻璃窑炉作为玻璃生产的核心设备之一,在玻璃行业中起到着至关重要的作用。
然而,随着社会经济的不断发展和环境保护意识的提高,关于玻璃窑炉的能源消耗问题也日益引起人们的关注。
能源消耗一直是限制玻璃窑炉发展的重要问题之一。
传统的玻璃窑炉往往存在着能源利用率低、排放物高的问题,给环境带来了巨大的负担。
为了改善这一状况,许多国家纷纷出台了关于玻璃窑炉能耗限额的政策措施,以推动玻璃行业的可持续发展。
本文将从玻璃窑炉能耗现状和能耗限额措施两个方面进行论述。
首先,通过对当前玻璃窑炉能源消耗的调查和分析,揭示目前的问题和挑战。
其次,针对这些问题和挑战,介绍一些已经实施和即将实施的能耗限额措施,包括技术改进、政策引导和管理措施等。
在总结部分,将对玻璃窑炉能耗限额的措施进行总结,并着重强调其重要性和未来的发展方向。
展望部分将对未来可能出现的新技术和政策进行探讨,以期为玻璃窑炉能耗限额的研究和实践提供一定的思路和参考。
通过对玻璃窑炉能耗限额问题的深入研究和探讨,旨在促进玻璃行业的可持续发展,减少能源浪费,提高能源利用效率,同时降低对环境的影响。
相信随着各级政府和企业的共同努力,玻璃窑炉能耗限额将会得到更好的实施和执行,进一步推动玻璃工业的绿色发展。
1.2 文章结构文章结构部分的内容可以如下所示:本文主要分为引言、正文和结论三个部分。
引言部分主要包括概述、文章结构和目的三个方面。
首先,概述部分将简要介绍玻璃窑炉能耗限额这一主题及其重要性。
然后,文章结构部分将说明本文的整体框架和各个部分的内容安排。
最后,目的部分将明确本文的目标,即通过分析玻璃窑炉能耗现状和探讨相应的能耗限额措施,为提高玻璃生产过程中的能源利用效率提供参考和建议。
正文部分将分为两个小节,分别介绍玻璃窑炉能耗现状和玻璃窑炉能耗限额措施。
在2.1小节玻璃窑炉能耗现状中,将详细分析当前玻璃生产过程中存在的能耗问题,并探讨造成能耗过高的原因。
浮法玻璃窑炉的节能设计

由于世 界能源 短缺 , 导致 能源 价格逐 步上 涨 , 燃
输 人体 系 的 热量 根 据 功 能分 为两 部 分 : 部分 一
料成本 在玻璃 生产 成 本 中所 占比例 随 之 越来 越 大 。
玻璃工 厂中绝大 部 分燃 料 消 耗 在 窑 炉 中 , 以用 于 玻
用 于满足 玻璃 液 的熔 化 、 清 、 澄 均化 、 却 直至 成 型 冷
所必 须 的热量 , 可称 之 为有用 热量 ; 另一部分 是理论
璃液 的熔 化 , 因此 , 降低 玻 璃 窑 炉 热 耗 , 降低 生 产 对
成本 , 缓解 能源 短 缺具 有 重 大 意义 。本 文根 据 笔者 的经验 以及对 玻璃 窑 炉 的理 解 , 重探 讨浮 法 玻璃 着 窑炉设计方 面的节 能措 施 。
取 的一些 技术措 施 。
括: 通过 喷嘴人 口带 人 的 燃 料 潜热 和 助 燃 物 ( 气 、 空
氧气 ) 热 以及 电能输 入热 ( 显 电极 处 ) 输 出体系 的热 ;
量包括 : 窑体表 面散热 , 烧废气 排 出热 , 燃 冷却风 、 水 带走 热 , 窑体孔 口、 隙带走 热 以及玻璃 液 离开窑 炉 缝
上不 需要 , 而实 际 中又必 须发 生 的热量 , 可称之为无 效热 量 , 们体 现在 输 出 体系 的 热 量 中 , 括 : 它 包 窑体 表面散热 , 烧 废 气 排 出 热 和 窑 体 孔 口、 隙带 走 燃 缝
玻璃窑炉焖炉环保措施
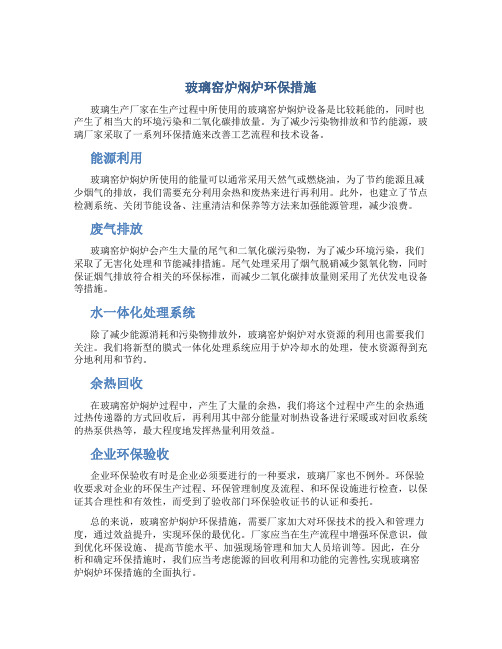
玻璃窑炉焖炉环保措施玻璃生产厂家在生产过程中所使用的玻璃窑炉焖炉设备是比较耗能的,同时也产生了相当大的环境污染和二氧化碳排放量。
为了减少污染物排放和节约能源,玻璃厂家采取了一系列环保措施来改善工艺流程和技术设备。
能源利用玻璃窑炉焖炉所使用的能量可以通常采用天然气或燃烧油,为了节约能源且减少烟气的排放,我们需要充分利用余热和废热来进行再利用。
此外,也建立了节点检测系统、关闭节能设备、注重清洁和保养等方法来加强能源管理,减少浪费。
废气排放玻璃窑炉焖炉会产生大量的尾气和二氧化碳污染物,为了减少环境污染,我们采取了无害化处理和节能减排措施。
尾气处理采用了烟气脱硝减少氮氧化物,同时保证烟气排放符合相关的环保标准,而减少二氧化碳排放量则采用了光伏发电设备等措施。
水一体化处理系统除了减少能源消耗和污染物排放外,玻璃窑炉焖炉对水资源的利用也需要我们关注。
我们将新型的膜式一体化处理系统应用于炉冷却水的处理,使水资源得到充分地利用和节约。
余热回收在玻璃窑炉焖炉过程中,产生了大量的余热,我们将这个过程中产生的余热通过热传递器的方式回收后,再利用其中部分能量对制热设备进行采暖或对回收系统的热泵供热等,最大程度地发挥热量利用效益。
企业环保验收企业环保验收有时是企业必须要进行的一种要求,玻璃厂家也不例外。
环保验收要求对企业的环保生产过程、环保管理制度及流程、和环保设施进行检查,以保证其合理性和有效性,而受到了验收部门环保验收证书的认证和委托。
总的来说,玻璃窑炉焖炉环保措施,需要厂家加大对环保技术的投入和管理力度,通过效益提升,实现环保的最优化。
厂家应当在生产流程中增强环保意识,做到优化环保设施、提高节能水平、加强现场管理和加大人员培训等。
因此,在分析和确定环保措施时,我们应当考虑能源的回收利用和功能的完善性,实现玻璃窑炉焖炉环保措施的全面执行。
玻璃熔化窑炉节能技术改造项目可行性研究报告
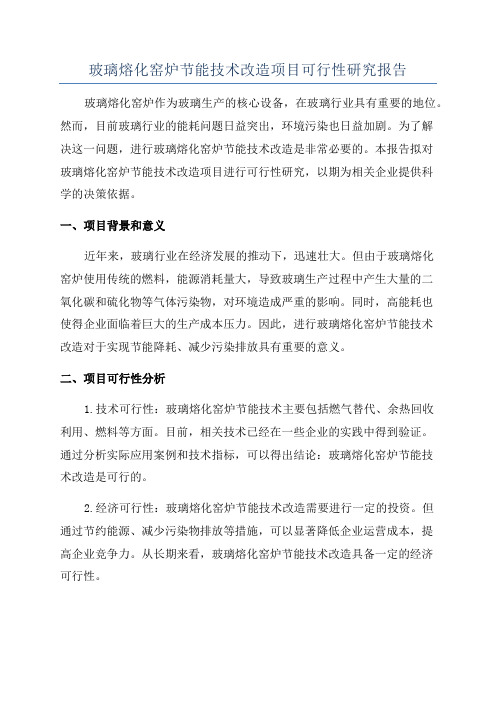
玻璃熔化窑炉节能技术改造项目可行性研究报告玻璃熔化窑炉作为玻璃生产的核心设备,在玻璃行业具有重要的地位。
然而,目前玻璃行业的能耗问题日益突出,环境污染也日益加剧。
为了解决这一问题,进行玻璃熔化窑炉节能技术改造是非常必要的。
本报告拟对玻璃熔化窑炉节能技术改造项目进行可行性研究,以期为相关企业提供科学的决策依据。
一、项目背景和意义近年来,玻璃行业在经济发展的推动下,迅速壮大。
但由于玻璃熔化窑炉使用传统的燃料,能源消耗量大,导致玻璃生产过程中产生大量的二氧化碳和硫化物等气体污染物,对环境造成严重的影响。
同时,高能耗也使得企业面临着巨大的生产成本压力。
因此,进行玻璃熔化窑炉节能技术改造对于实现节能降耗、减少污染排放具有重要的意义。
二、项目可行性分析1.技术可行性:玻璃熔化窑炉节能技术主要包括燃气替代、余热回收利用、燃料等方面。
目前,相关技术已经在一些企业的实践中得到验证。
通过分析实际应用案例和技术指标,可以得出结论:玻璃熔化窑炉节能技术改造是可行的。
2.经济可行性:玻璃熔化窑炉节能技术改造需要进行一定的投资。
但通过节约能源、减少污染物排放等措施,可以显著降低企业运营成本,提高企业竞争力。
从长期来看,玻璃熔化窑炉节能技术改造具备一定的经济可行性。
3.社会可行性:玻璃熔化窑炉节能技术改造可以减少排放的二氧化碳等有害气体,改善环境质量,保护生态系统,对于实现可持续发展具有积极意义。
此外,项目的实施还可以提高企业形象,增强社会认可度。
三、项目实施方案1.技术改造方案:选择合适的燃气替代、余热回收利用、燃料等技术,在真实的工业环境中进行试验和调试。
通过技术改造,使玻璃熔化窑炉能够实现节能、减排的目标。
2.经济资金方案:制定详细的投资预算,分析项目的投资回报率、内部收益率等指标。
同时,寻找合适的融资方式,如银行贷款、政府补贴等,确保项目进行顺利。
3.环境影响评价:对项目实施过程中可能产生的环境影响进行评估,制定相应的环境保护措施,确保项目符合环保要求。
玻璃工业窑炉 第五章节能技术及环保 第一节全保温技术

2)能耗相同时,可提高熔化率(15~20)%。玻 璃液平均温度提高30~40℃,有利于玻璃液的 澄清和均化,提高玻璃液质量,使成品率提 高。
3)火焰空间热负荷降低,延长了窑顶的使 用寿命,并改善了操作条件。
+115mm轻质粘土砖+100mm硅钙板 +4mm钢板
4)池底保温 70mm电熔锆刚玉砖+35mm锆质捣打料 +300mm浇注大砖+280mm轻质粘土砖 +10mm石棉板+8mm钢板 70mm电熔锆刚玉砖+35mm锆质捣打料 +40mm锆英石砖+35mm锆质捣打料+300mm 浇注大砖+280mm轻质粘土砖+10mm石棉板 +8mm钢板
窑后保温。 膨胀缝处不保温。
各部位保温结构实例
1)大碹保温 300mm硅砖+35mm石英砂+65mm轻质 硅砖+20mm石棉泥 300mm硅砖+50mm石英砂+65mm轻质 硅砖+65mm轻质粘土砖+20mm石棉泥 300mm硅砖+40mm石英砂+115mm轻质 硅砖+65mm轻质硅砖+20mm石棉泥 300mm硅砖+30mm硅质密封料+115mm 轻质硅砖+50mm硅质保温层料
玻璃池窑各部位保温隔热度推荐值 熔化部: 大碹 7~20,胸墙8~20,池壁4~10,池
底10~15 作业部: 碹 7~20,胸墙8~20,池壁4~20,池底
15~30 小炉:碹 6~20,侧墙4~15 蓄热室:碹前后温度对比
玻璃窑炉如何更好的节能

玻璃窑炉如何更好的节能玻璃窑炉如何更好地节能引言:玻璃工业是一个能源消耗较大的行业,其中窑炉是主要能耗设备之一。
由于其高温作业和长时间运行,玻璃窑炉的能耗占据了整个生产线的重要比例。
因此,如何降低玻璃窑炉的能耗,节约能源成为玻璃工业的一项重要任务。
本文将就玻璃窑炉如何更好地节能进行探讨。
一、优化玻璃窑炉设计窑炉的设计是节能的关键。
具体而言,可以通过改善窑炉的结构和燃烧系统来降低能耗。
1. 优化窑炉结构:合理的窑炉结构可以减少能量损失。
例如,采用双层窑炉结构,可以减少外部热辐射对内部材料的热损失。
此外,增加窑炉的隔热层厚度,可以减少热能散失。
2. 改进燃烧系统:优化燃烧系统可以提高燃料利用率,减少能耗。
可以采用先进的燃烧技术,如预混燃烧技术、过热空气燃烧技术等。
除此之外,还可以采用余热回收技术,将燃烧产生的热能转化为工艺过程所需的热能,进一步提高能源利用效率。
二、控制燃料选择选择合适的燃料可以降低窑炉的能耗。
下面介绍几种常用的燃料选择。
1. 天然气:天然气作为一种清洁、高效的燃料,具有燃烧稳定、热值高的特点。
将燃烧系统调整为适合天然气燃烧的状态,可以减少能耗,降低环境污染。
2. 生物质能源:生物质能源是一种可再生能源,如木屑、秸秆等。
通过将生物质能源与传统燃料混合使用,可以减少对传统燃料的依赖,并且减少温室气体的排放。
3. 光伏发电:光伏发电是利用太阳能转化为电能的技术。
将光伏发电与传统燃料相结合,可以减少对传统燃料的使用,降低玻璃窑炉的能耗。
三、有效控制窑炉运行参数科学合理地控制窑炉的运行参数,可以降低能耗。
1. 温度控制:合理控制窑炉的温度可以减少能量的浪费。
通过准确、稳定地控制窑炉温度,避免过高或过低的温度,可以提高玻璃生产的质量,并减少能耗。
2. 空气流动控制:窑炉的空气流动对玻璃生产起着重要的作用。
通过调整窑炉内的空气流动速度和方向,可以提高燃烧效率,减少能耗。
3. 玻璃成分控制:合理控制玻璃的配方和成分比例,可以降低生产过程中的能耗。
玻璃窑炉国标 耗水量
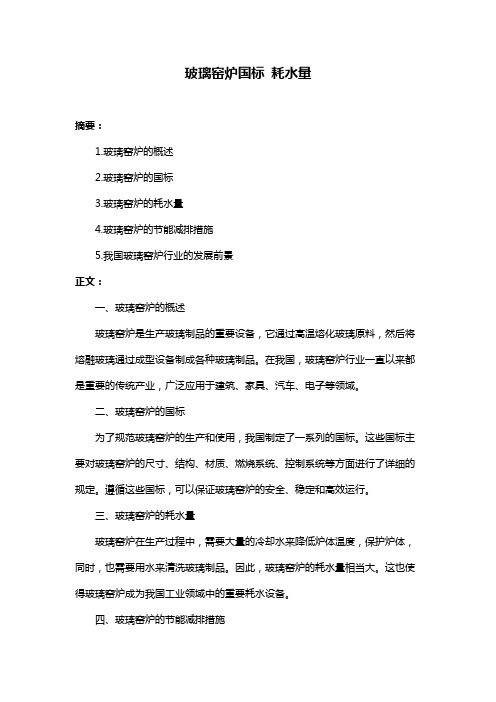
玻璃窑炉国标耗水量
摘要:
1.玻璃窑炉的概述
2.玻璃窑炉的国标
3.玻璃窑炉的耗水量
4.玻璃窑炉的节能减排措施
5.我国玻璃窑炉行业的发展前景
正文:
一、玻璃窑炉的概述
玻璃窑炉是生产玻璃制品的重要设备,它通过高温熔化玻璃原料,然后将熔融玻璃通过成型设备制成各种玻璃制品。
在我国,玻璃窑炉行业一直以来都是重要的传统产业,广泛应用于建筑、家具、汽车、电子等领域。
二、玻璃窑炉的国标
为了规范玻璃窑炉的生产和使用,我国制定了一系列的国标。
这些国标主要对玻璃窑炉的尺寸、结构、材质、燃烧系统、控制系统等方面进行了详细的规定。
遵循这些国标,可以保证玻璃窑炉的安全、稳定和高效运行。
三、玻璃窑炉的耗水量
玻璃窑炉在生产过程中,需要大量的冷却水来降低炉体温度,保护炉体,同时,也需要用水来清洗玻璃制品。
因此,玻璃窑炉的耗水量相当大。
这也使得玻璃窑炉成为我国工业领域中的重要耗水设备。
四、玻璃窑炉的节能减排措施
针对玻璃窑炉的高耗能、高耗水问题,我国积极推动玻璃窑炉的节能减排工作。
这些措施包括提高燃料的利用率、改进燃烧技术、降低烟气排放、减少窑炉散热等。
这些措施的实施,不仅可以降低玻璃窑炉的能耗和水耗,同时也有助于保护环境。
五、我国玻璃窑炉行业的发展前景
随着科技的进步和社会的发展,我国玻璃窑炉行业正面临着新的发展机遇。
未来的玻璃窑炉将更加节能、环保、高效。
- 1、下载文档前请自行甄别文档内容的完整性,平台不提供额外的编辑、内容补充、找答案等附加服务。
- 2、"仅部分预览"的文档,不可在线预览部分如存在完整性等问题,可反馈申请退款(可完整预览的文档不适用该条件!)。
- 3、如文档侵犯您的权益,请联系客服反馈,我们会尽快为您处理(人工客服工作时间:9:00-18:30)。
我国玻璃窑炉的节能[574]我国玻璃窑炉的节能王辰亚(中国节能协会玻璃窑炉专业委员会)前言:各级领导的关心和重视,中国节能协会玻璃窑炉专业委员会的大力推动,使我国玻璃窑炉节能技术得到了广泛的推广应用,科学节能的经营管理得到了加强,全国玻璃窑炉节能已取得了实效,节能效果显著。
玻璃窑炉的节能,实际是玻璃工业全方位综合性系统工程实施的问题,缺一不可。
是玻璃工业节能技术中的一个大课题,本文将试探性的加以论述,以达到抛砖引玉的目的。
一、我国玻璃工业窑炉能耗现况:我国大约有4000~5500座各种类型的玻璃窑炉,其中熔化面积80m2以下的中小型炉数量大约占总量的80%左右,使用燃料种类分:燃煤炉约占63%,燃油炉约占29%,天然气炉、全电熔炉等约占8%。
2008年全国玻璃产量大约为2000~3000万吨。
年耗用标准煤1700~2100万吨。
其中平板玻璃产量为53192万重量箱,所用能耗折合标准煤1000万吨/年。
平均能耗为7800干焦/公斤玻璃液,窑炉热效率20~25%,比国际先进指标30%≦低5%~1 0%。
每年排放SO2约16万吨、烟尘1.2万吨、NOx14万吨。
玻璃熔窑在玻璃工厂中是消耗燃料最多的热工设备,一般,占全厂总能耗的80~85%左右,目前我国玻璃工业所用的主要能源是:煤、油、电和天然气等燃料。
由于燃料价格几年来持续上涨,企业燃料成本逐年增加,效益锐减,在此形势下,玻璃工业根据我国能源蕴藏品种结构、分布、数量和价格等不得不做使用调整。
使以前规划设计推行的使用清洁、高热值能源的思路发生了一定的变化。
即近几年来企业欲争取较大效益。
有不少燃油炉改成燃煤炉,以此带来不小的环境保护问题。
当然这几年随着我国电力工业的发展,全氧炉、电助熔、全电熔炉有了较大的发展。
2008年日用玻璃产量1445.7万吨,如成品率平均为90%,年玻璃出料量应为1590万吨,年耗标煤557~636万吨。
完成工业产值865.5亿元、出口额2.1亿美元,其单耗平均为350~400公斤标准煤/吨玻璃液,比较好的为每吨玻璃液150~250公斤标准煤(啤酒瓶、农药瓶、普通白料制品等),较差的多达900~1000公斤标准煤,二者相差3~4倍之多。
又如窑炉热有效利用率先进的为25~38%,落后的只有12~22%,之间相差3~26个百分点,国外日用玻璃包装瓶熔窑单耗为110~130 kg标煤/吨玻璃液左右,劳动生产率为200~370吨/年人,熔化率2.5~3.8吨/m2·日。
窑炉大都为日出料量180~250吨。
热效率在48%左右。
国内外差距较大。
我国改革开放以前,全国玻璃工业窑炉的炉型和技术等都比较落后,能耗很高,改革开放以后引进不少国外玻璃窑炉的先进软硬件,配合派人到国外学习参观,结合国情我们的科技工作者经过30多年的引进消化吸收,采用众多新技术创新设计出我国高效、长寿命、节能新型窑炉,使我国玻璃工业窑炉节能技术有了长足的进步,但与国际最先进技术水平比,还有一定差距,以两大玻璃行业窑炉的主要技术指标进行国内外对比,见表一。
表一国内外玻璃窑炉主要技术指标对比2008年全年平板玻璃产量为55493万重量箱,同比增长2.35%。
2008年1~11月,我国平板玻璃产量为51390.32万重量箱,同比增长9.0%。
12月产量为4102.09万吨同比下降7.72%。
受国际金融危机的影响,平板玻璃全行业亏损,特别是下半年浮法生产线陆续放水停产,具有代表性的是11月底福耀玻璃两条浮法线、南玻三条浮法线放水停产。
2009年形势依然严峻,据国家统计局最新数据显示1~2月份累计生产平板玻璃853733万重量箱,比2008年同期减少654万重量箱,同比下降7.11%。
从3月份开始不少大型工程上马,形势有所好转。
玻璃企业的能耗主要在玻璃的熔制过程中消耗,熔制玻璃的目的,是在高温下将多种固相的配合料经熔融转变为单一的均匀玻璃液,当然在实际生产中玻璃行业抓住了窑炉的节能就是抓住了行业节能的主题。
玻璃的熔制过程是一个非常复杂的过程,它包括一系列物理的、化学的、物理化学的现象和反应。
这些现象和反映的结果,使各种配合料经机械混合后送入炉内,炉内配合料在加热过程中经过:硅酸盐形成(约在600~900℃)→玻璃的形成(普通玻璃约为1200~1250℃)→澄清(普通玻璃约为1400~1500℃,粘度η≈10帕·秒)→均化(玻璃液长时间处于高温下,其化学组成趋向均一)→冷却,澄清均化好的玻璃液在不损坏玻璃的质量前题下,需将温度降至加工工艺要求粘度的温度区域(一般降温200~300℃)进行成型加工制造出所需产品。
就目前玻璃窑炉生产技术状况下分析,平均熔化每公斤玻璃能耗约为1500~4000千卡(理论值为576~624千卡/公斤玻璃),由于炉型的差异、采用技术手段先进程度的不同、熔化玻璃品种不同、工艺技术、日常管理等因素,熔化玻璃能耗差距较大。
玻璃窑炉有热效能利用率平均只有18~38%,较低,而72~65%不能被有效利用。
国内比较先进的燃油玻璃窑炉经热测试的结论:70m2窑炉热能利用率58.84%,全窑热效率38.18%。
根据国内部分企业窑炉调查结果显示:1)炉型:当前我国轻工、医药、电子玻璃窑炉大都使用燃油、燃煤气蓄热室马蹄焰玻璃窑炉炉型,换热式玻璃窑炉也有一定市场。
平板玻璃窑炉大都为横火焰炉,也有少量使用马蹄焰炉型的。
由于改革开放后引进了不少全电熔窑和电助熔软硬件技术,目前我国全电熔和电助熔窑每年以1~2百多台的速度在增长。
全氧炉也有被国人接受的趋势在逐年增加。
2)燃料:我国玻璃窑炉目前所用能源一般可分为液体燃料(重油、原油、柴油等)、固体燃料(原煤等)、气体燃料(发生炉煤气、天燃气、焦炉煤气、液化石油气、纯氧气等)及电能等。
3)近几年我国玻璃窑炉发展趋势:改革开放以来我国玻璃工业界引进大量的国外先进窑炉的软硬件技术和装备,消化吸收了不少新技术,在结合我国国情的基础上有了很多创新,大大提升了我国玻璃工业的技术水平。
近年来随着耐火材料的研发新产品增多,成型技术、加工能力,产品档次质量提高,为窑炉深熔比池、深澄清池、长寿命设计提供了保证,为玻璃窑炉的技术进步创造了条件。
玻璃窑炉的创新突飞猛进,大型高效、节能、长寿命窑炉大量涌现,节能效果显著。
高热值燃料大量被使用。
全方位复合全保温技术应用进一步深化。
电助熔窑、全电熔窑、富氧燃烧技术被采用,全氧炉逐年增多。
蓄热室马蹄焰窑向大型化发展,换热室窑炉正在被蓄热室窑炉替代。
适当缩小流液洞的截面尺寸,增加流液洞的负荷,减少玻璃液的回流。
玻璃窑炉设计的跨进变化:(1)近年来窑炉澄清池、熔化池池深的加深设计大量使用。
(暂且不讨论其理论根据)窑炉由过去传统的设计熔化池深度900~1200mm,现熔化池加深为1600~2300mm不等,澄清池加深为1600~2600。
(2)窑炉长宽比的变化传统的设计其长宽比一般为:平板大型窑为2.3~3,小型马蹄焰窑为1.4~1.6。
目前长宽比有缩小的设计趋势,如马蹄焰窑炉长宽比已有设计为1~1.2的。
长宽比的改变与所用燃料、马蹄焰窑炉大型化等有关。
(3)蓄热室采用大蓄熔比单通道蓄热室或三通道蓄热室设计。
目前还出现全分隔式蓄热室结构设计。
一般超过50比1,具体一是加高蓄热室,或采用三通道蓄热室。
二是采用高蓄热效率的八角筒型或十字型格子砖,增加有效蓄热面积。
尽量提高空气预热温度至1300℃以上,这样可以提高燃料的燃烧速度,节约燃料以达到节能效果。
(4)玻璃仪器、玻璃器皿的生产大量采用全电熔窑设计,以保证产品质量。
(5)玻璃窑炉设计同时增加节能减排措施项目并考虑。
(6)玻璃窑炉所用电熔锆刚玉耐火材料一律要求精加工,并在生产厂要求组装验收方能进入现场。
二、近几年玻璃窑炉采用行之有效的几项节能新技术:(1)玻璃窑炉的节能根据以上的数据和分析,我国玻璃工业的节能潜力巨大,玻璃窑炉的热能用在熔化玻璃上只是少量的,大部分未能被利用。
资料显示:输入玻璃窑炉的热能利用和散失,大致可分成三份,即:三分之一热量用于熔化玻璃、三分之一热量由炉体散失、三分之一热量随着烟气被排入大气中。
显然第一个三分之一为必不可少的,后两个三分之一是我们节能主攻方向。
当然第一个三分之一也要做些文章。
今后要结合国情除消化吸收国外的软硬件,侧重于先进的节能经验和行之有效的节能先进技术,更主要的是要依靠国内的广大科技工作者和经营管理者,根据自己的实际情况和需求进行研发和创新,以科学的严谨态度,以不断创新的方式和成果使窑炉全方位达到运行最佳化,以追求窑炉最大的节能效果和经济效益。
节能要在保证玻璃质量的前提下,将以现代国内外玻璃窑炉节能先进成熟的技术和节能措施,从窑炉的软硬件入手全方位进行技术创新。
做主要提示:窑炉的最新设计理念,设计者要采用当代最新设计成果和节能技术。
采用当代最节能的配方,设计选用最先进配料系统。
设计最新而先进的燃烧系统和设备。
设计和选用最先进的自动化设施和自控系统。
选用相匹配的优质耐火材料。
余热回收和利用。
窑炉配套系统的节能等。
1)玻璃窑炉的设计改革和创新达到节能:玻璃窑炉的设计是一项十分重要的技术性极高的工作,它涉及到热力学、燃烧学、流体力学、玻璃工艺学、材料学、耐火材料学等多种学科。
按设计程序进行,设计前任务书、调查了解国内外相似炉型的先进资料等收集相关资料并在调查研究的基础上选定炉型、根据技术指标和使用方的要求,经计算、实验绘制图纸完成设计,初步设计:所用燃料类别确定单耗、确定熔化率和出料量、确定熔制工艺制度、确定熔窑的主要尺寸(熔化池尺寸、工作池尺寸、燃料的燃烧计算和耗热量的计算、火焰空间尺寸、设计小炉尺寸、蓄热室设计、烟道尺寸、烟囱设计等)、耐火材料的选择、土建、燃料及动力的配套工程供应等必须做。
窑炉设计和采用先进结构效益。
此外筑炉和烤炉及日常使用也必须注意。
一座窑炉设计的成功与否关系到炉投入使用能否按设计指标节能、高效、长寿命运行,关系到企业今后的经济效益。
由于对窑炉技术经济指标的高要求,窑炉设计工作者必需采用最新的众多新节能技术方能满足要求,故近年来创建了一大批高效、节能、长寿命窑炉,能耗比常规炉降低20~50%,效益可观。
关于企业窑炉选择设计部门问题:据我们掌握情况:目前国内设计窑炉比较混乱,大致是1.具有国家资质的正规大型设计院,技术实力雄厚,收费高,对工程有保证。
2.具有地方工商部门注册的有一定设计能力和水平的股份公司和私人公司,有一定的技术实力,对工程有一定保证,费用较正规设汁院低。
3.有地方工商部门注册的无技术实力的个人(2~3人不等)公司,只管建炉不负责工程无后期服务收费低。
4.游击队公司或个人(包括一些筑炉队),只为赚钱,对后事不负责任,无技术可言,出事率特高,出事后根本找不到人负责,企业损失大。