浇注系统浇口尺寸计算[优质ppt]
浇口与尺寸计算

已知求步骤解制造偏差尺寸公差(δz)(△)x 收缩率模具型腔径向尺寸(L m )50.320.210.640.750.0061模具型腔深度尺寸(H M )180.070.20.750.0061计算项目塑件基本尺寸塑件内径 Φ45+0.36→Φ45 +0.36 → Δ= 0.36塑件内孔高度 18+0.20→18 +0.20 → Δ= 0.20塑件高度 21± 0.22 →21.22 - 0.44 → Δ= 0.44小型芯内径 Φ8± 0.14→Φ7.86 +0.28→ Δ= 0.28(1)塑件外形的基本尺寸是最大尺寸,其公差为负偏差;型腔的的基本尺寸是最小尺寸,其公差为正偏差(2)塑件孔的径向基本尺寸 是最小尺寸,其公差 为正偏差;型芯的基本尺寸 是最大尺寸为名义尺寸 ,制造偏差 为负值(3)塑件孔的深度基本尺寸 是最小尺寸,其公差 为正偏差;型芯高度的基本尺寸 是最大尺寸 ,制造偏差 为负值;(4)模具上型芯的中心距与塑件上成型孔的中心距对应模具上成型孔的中心距与塑件上突起部分中心距对应 。
小型芯中心距30±0.14 →30 → Δ= 0.28(2)明确制品尺寸公差等级,并将尺寸换算为规定的形式由表3-9和表3-10知;有公差尺寸的公差等级为MT3级,对ABS 塑件属 “一般精度”;级。
允许偏差为双向偏差形式;故按照尺寸形式的规定(塑件外形的最大尺寸是基本塑件内形的最小尺寸是基本尺寸,其公差为正偏差 ) ,做如下转换:确定模具凹模内径和深度、型芯直径和高度以及两小孔的中心塑件外径 Φ50±0.32→Φ50.32 -0.64 → Δ= 0.64制品如图 所示,材料为ABS 。
(1)定模塑收缩率 (2)明确制品尺寸公差等级,并将尺寸换算为规定的形式 (3)成型尺寸计算(1)定模塑收缩率 从有关手册查知,ABS 的收缩率为0.4~0.7%。
在此取平均收缩率作为模塑收缩率,模具型芯高度尺寸21.220.070.20.750.0061(hs)模具型芯径向尺寸计450.170.50.750.0061算(ls)小型芯内径(ls)7.860.090.280.750.0061两小孔的中心距尺寸300.090.280.750.0061(C S)50.1450.14+0.2117.9617.96+0.07计算公式计算结论计算结论偏差;差为正偏差;偏差 为负值为正偏差;为负值;对应距对应 。
浇注系统浇口尺寸计算 ppt课件
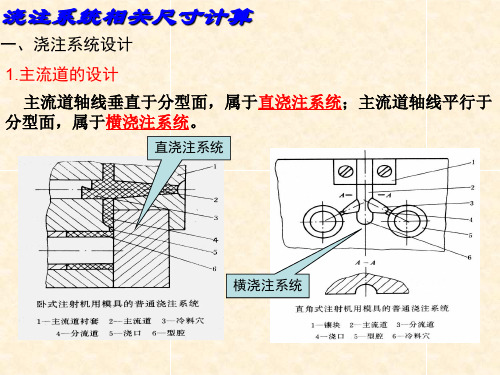
或圆形浇口,浇口截面积 AG与分流道的截面积 AR 的比值取:
AG : AR 0.07 ~ 0.09
矩形浇口的截面的宽度b与厚度t的比值常取:
b:t 3:1
注意:求解时,一般取浇口长度为定值,通过调 节浇口的宽度和厚度来谋求浇口的平衡。
浇注系统相关尺寸计算
浇注系统相关尺寸计算
浇口的平衡例题
浇注系统相关尺寸计算
主流道小端直径d一般取3~6mm,主流道的长度由定模座厚 度确定,一般L不超过60mm,主流道大端与分流道相接处应有 过渡圆角(通常r′取1~3mm)以减少料流转向时的阻力。
浇注系统相关尺寸计算
正确情况:主流道小端直径d比注射机喷嘴直径d0大0.5~1mm, R≥r+(0.5~1)mm。
浇注系统相关尺寸计算
2.分流道的设计 分流道是主流道末端与浇口之间的通道。用于一模多腔或单型腔
多浇口(塑件尺寸大)的场合。
浇注系统相关尺寸计算
分流道的截面形状及尺寸 为便于机械加工及凝料脱模,分流道一般设置在分型面上。
浇注系统相关尺寸计算
3.浇口的设计 浇口亦称进料口,是连接分流道与型腔的最短通道。
铸造浇注系统设计-课件(1)
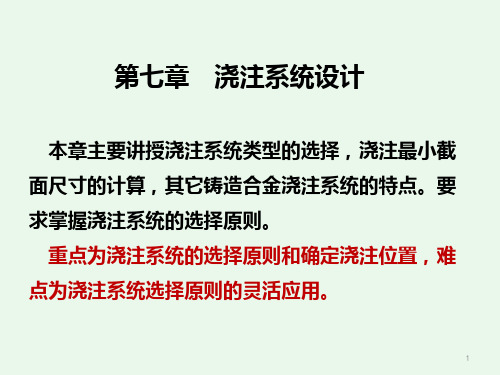
池盆形浇口杯
特点:挡渣作用明显,但是制作程序复杂,消耗 的金属较多 应用:主要用于中大型铸铁件。 结构:浇口盆 的深度应该大 于直浇道上端 直径的5倍。
12
浇口杯中应避免出现水平涡流
液态金属在平底的浇口杯中 流动 时易出现水平涡流。 流量分布不均匀造成流速方 向偏 斜。水平分速度对直浇 道中心线 偏斜,形成水平涡 流运动。在涡 流中心区形成 一个漏斗形充满空 气的等压 自由液面的空穴。容易 将空 气和渣子带入直浇道。
第七章 浇注系统设计
本章主要讲授浇注系统类型的选择,浇注最小截 面尺寸的计算,其它铸造合金浇注系统的特点。要 求掌握浇注系统的选择原则。
重点为浇注系统的选择原则和确定浇注位置,难 点为浇注系统选择原则的灵活应用。
1
概述
浇注系统:铸型中液态金属流入型腔的通道之总称 组成:浇口杯、直浇道、直浇道窝、横浇道、内浇道
2)采用纵向逆浇,设置底坎、挡板和闸门等; 3)采用特殊结构的浇口杯:拔塞式、浮塞式、铁隔 片式、闸门式等; 4)浇口杯与直浇道相连的边缘做成凸起状。
22
三、直浇道中的流动
直浇道的功用: 引导金属液进入横浇道、内绕道或直接导入型腔; 提供足够的压力头,使金属液克服各种流动阻力,
在规定时间内充满型腔。
型壁的多孔性、透气性和合金液的不相润湿性,给合金液的 运动以特殊边界条件
在充型过程中,合金液和铸型之间有着激烈的热作用、机 械作用和化学作用;合金液冲刷型壁,粘度增大,体积收 缩,吸收气体、使金属氧化等;
浇注过程是不稳定流动过程 ✓ 在型内合金液淹没了内浇道之后,随着合金液面上升,
充型的有效压力头渐渐变小 ✓ 型腔内气体的压力并非恒定 ✓ 浇注操作不可能保持浇口杯内液面的绝对稳定
模具设计之浇口设计PPT课件

常用于扁平而较薄的塑件,如盖板、托盘
第38页/共130页
§3.3 单分型面注射模普通浇注系统设计
平缝浇口(薄片浇口)
b取塑件长度的 25﹪~100﹪ t=0.2~1.5㎜ l=1.2~1.5㎜
用于成型面积较小、尺寸较大的扁平塑件
第39页/共130页
§3.3 单分型面注射模普通浇注系统设计
环形浇口
作用:改变熔体流向,使其以平稳的流态均衡
地分配到各个型腔。
分流道的形状与尺寸 b 0.2564 m4 L
h 2b 3
L=1~2.5倍的大端直径,一般取8~30㎜ α=5°~10 °
第27页/共130页
§3.3 单分型面注射模普通浇注系统设 计
分流道的表面粗糙度
Ra值1.25~2.5 m ,一般取1.6 m
型腔一般在模具中心
塑件在定模 塑件在动模 塑件分别在动、定模
第二节 浇注系统设计ppt课件
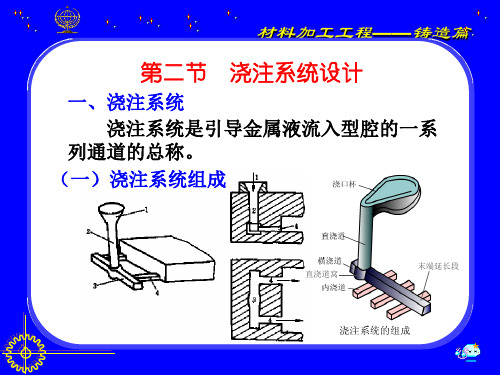
轻合金的特点是密度小、熔点低、导热 系数大、质量定容热容量小、化学性质活泼、 极易氧化和吸收气体等,因此易氧化生成氧 化膜,在紊流情况下卷入液流中而产生夹杂 缺陷。
1.轻合金要求平稳、无涡流、无喷溅地充满 型腔。
2. 浇注时间要短,以避免出现浇不到等缺陷。 3. 一般采用开放式底注式浇注系统,广泛应 用垂直缝隙式和带立缝的底注式浇注系统 (除高度小于100mm的不重要的小件外)。
3.具有良好撇渣能力,防止夹渣和气孔缺陷。 4.保证型内金属液面有足够的上升速度,以 免形成夹砂结疤、皱皮、冷隔等缺陷。
5.金属液进入型腔时线速度不可过高,避免 飞溅、冲刷型壁或砂芯。 6.浇注系统结构力求简单,简化造型,减少 清理工作量和液态金属的消耗。
材料加工工程——铸造篇
二、液态金属在浇注系统基本组元中的流动 (一)液态金属在铸型中流动过程的特点:
材料加工工程——铸造篇
继续充填内浇道出口处以上的型腔部分时:
H02vg2 h总损 hh型损
对于作用在内浇道中金属液上的实际压头
的平均值H均: 设:H均H0h
内浇道出口处以上的型腔 内金属液的平均静压头
H均2vg2( 1浇型 )
S阻 m 2/2 2 H 均
其中:2
1
1浇型
材料加工工程——铸造篇
材料加工工程铸造篇四浇注系统的计算一浇注系统的计算步骤二按流体力学公式计算浇注系统三按经验公式计算非铁合金的阻流截面积积四缝隙式浇注系统的尺寸计算材料加工工程铸造篇确定浇注系统各基本组元的尺寸结构开始确定浇注系统类型确定浇注系统引入位置计算浇注系统阻流面积选择浇道比计算各组元的截面尺寸浇注试验浇注材料加工工程铸造篇二按流体力学公式计算浇注系统适用于转包浇注的封闭式浇注系统
浇口的设计PPT课件

缺点:是去除浇道后﹐将在成型品表面 留下痕迹。
22.11.2020
第四章 塑料注射模的设计和制造
§4.3 普通浇注系统的设计及制造
七、浇口的设计及制造
2.浇口的类型及特点
22.11.2020
问题 目的与要求 重点和难点 浇口的设计制造 排气系统设计 思考与练习
侧浇口
一般开设在分型面上,适合于一 模多腔,浇口去除方便;但压力 损失大、壳形件排气不便、易产 生熔接痕。
22.11.2020
典型的浇口厚度是0.25至1.27mm。
第四章 塑料注射模的设计和制造
§4.3 普通浇注系统的设计及制造
七、浇口的设计及制造
2.浇口的类型及特点
问题 目的与要求
环状浇口
重点和难点 浇口的设计制造 排气系统设计
思考与练习
使用环状浇口﹐熔料自由地沿 著环状浇口中心部分流动﹐然 后熔料向下流动充填模具。 典型的浇口厚度是0.25至1.6mm。
典型的浇口尺寸为:厚度0.4至 6.4mm﹐宽度为1.6至12.7mm。
22.11.2020
第四章 塑料注射模的设计和制造
§4.3 普通浇注系统的设计及制造
七、浇口的设计及制造
2.浇口的类型及特点
问题 目的与要求 重点和难点 浇口的设计制造
扇形浇口
典型的浇口尺寸为﹕厚度0.25至1.6mm﹐宽度 6.4至25%的型腔侧壁的长度。
22.11.2020
第四章 塑料注射模的设计和制造
§4.3 普通浇注系统的设计及制造
七、浇口的设计及制造
2.浇口的类型及特点
22.11.2020
问题 目的与要求 重点和难点 浇口的设计制造 排气系统设计 思考与练习
《浇口的设计》课件

环保理念:通过优化浇口设计,减 少废料,降低对环境的影响
添加标题
添加标题
添加标题
添加标题
提高产品质量:通过优化浇口设计, 提高产品质量,减少废品率
智能化设计:通过优化浇口设计, 实现智能化生产,提高生产自动化 程度
智能化:采用先进的智能技术,提高浇口设计的准确性和效率 环保化:采用环保材料和工艺,减少对环境的污染和破坏 轻量化:采用轻质材料和结构,降低浇口设计的重量和成本 集成化:将浇口设计与其他工艺环节相结合,提高生产效率和产品质量
浇口设计影响产品的成型质量 浇口设计影响产品的力学性能 浇口设计影响产品的外观质量 浇口设计影响产品的生产效率
浇口位置:选择合适的浇口 位置,避免影响产品外观和 性能
浇口尺寸:根据产品尺寸和 形状选择合适的浇口尺寸, 保证产品成型质量
浇口数量:根据产品结构和 生产效率选择合适的浇口数 量,避免产品缺陷
感谢您的观看
汇报人:
浇口形状:选择合适的浇口 形状,提高产品成型质量和 生产效率
浇口冷却:合理设计浇口冷 却系统,保证产品成型质量 和生产效率
浇口清理:定期清理浇口, 保证产品成型质量和生产效 率
浇口设计的优化
提高浇口质量:优化浇口设计,提高浇口质量,减少缺陷 降低浇口成本:优化浇口设计,降低浇口成本,提高生产效率 提高浇口效率:优化浇口设计,提高浇口效率,减少废品率 提高浇口稳定性:优化浇口设计,提高浇口稳定性,减少波动性
浇口的设计
汇报人:
目录
添加目录标题
浇口的基Байду номын сангаас概念
浇口的设计原则
浇口设计的实际 应用
浇口设计的优化
浇口设计的新趋 势
添加章节标题
浇注系统的计算和设计PPT课件
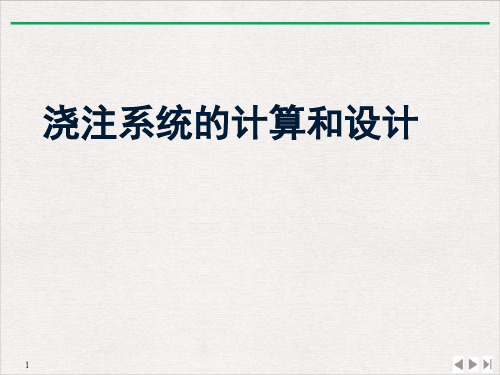
合适的浇注时间与铸件结构、铸型工艺条件、合 金种类及选用的浇注系统类型等有关。每种铸件, 在已确定的铸造工艺条件下,都对应有适宜的浇 注时间范围。由于近年来普遍认识到快浇对铸件 的益处,因此浇注时间比过去普遍缩短,特别是
灰铸铁和球墨铸铁件更是如此。浇注系统的流量系数通 常是指阻流截面的 流 量系数。
快浇的优点: 金属的温度和流动性降低幅度小,易充满型腔。 减小皮下气孔倾向。充型期间对砂型上表面的热作用时间短, 可减少夹砂结疤类缺陷。对灰铸铁、球墨铸铁件,快浇可以 充分利用共晶膨胀消除缩孔缩松缺陷。
快浇的缺点: 对型壁有较大的冲击作用,容易造成涨砂、冲 砂、抬箱等缺陷。浇注系统的重量稍大,工艺出品率略低
用底注浇包浇注时,浇注系统必须是开放式的,直 浇道不被充满,保证钢液不会溢出浇道以外。为快 速而平稳地充型,对一般中小铸件多用底注式,高 大铸件常采用阶梯式浇注系统。
(一)底注包浇注系统的经验计算法
铸钢车间的浇包容量和熔炉吨位一致,一般只有一种 或几种容量的浇包和数种直径的包孔。生产中先确定 浇包容量和包孔直径,依经验的浇口比确定浇注系统 各组元尺寸。 1、浇包容量及包孔选择 浇包总容量应大于铸型内金属需要量。小浇包只设一 个包孔,大于30t的浇包可设两个包孔。每个包孔的钢 液流量——浇注速度,不仅决定于包孔直径,还与包 内钢液深度有关。但实践中为方便起见,给出了包孔 直径和平均浇注速度的关系。 2、浇注时间和液面上升速度
3、其他组元截面积
以包孔截面积为基准,参照下述浇口比确定浇注系统各组元截面积 S包孔:S 直:S横:S内 =1:(1.8~2.0): (1.8~2.0) :(2.0~2.5)
指出图51所示二种横浇道形式的优劣
指出图51所示二种横浇道形式的优劣 5、计算阻流截面积S阻 采用顶注法的体收缩大的合金铸件。 若A-A水平面低于铸件最高点 (一)底注包浇注系统的经验计算法 充型期间对砂型上表面的热作用时间短,可减少夹砂结疤类缺陷。 充型期间对砂型上表面的热作用时间短,可减少夹砂结疤类缺陷。 3、每层内浇道的总截面积 计算阻流截面的水力学公式 充型期间对砂型上表面的热作用时间短,可减少夹砂结疤类缺陷。 合箱偏差及浇注时的涨砂等 采用顶注法的体收缩大的合金铸件。 铸钢车间的浇包容量和熔炉吨位一致,一般只有一种或几种容量的浇包和数种直径的包孔。 2) 假定铸件(型腔)的横截面积S沿高度方向不变 铸型及砂芯干燥过程中的尺寸变化 浇注系统的流量系数通常是指阻流截面的 流量系数。 采用顶注法的体收缩大的合金铸件。 浇注期间金属对型腔上表面烘烤时间长,促成夹砂结疤和粘砂类缺陷。 充型期间对砂型上表面的热作用时间短,可减少夹砂结疤类缺陷。 每种铸件,在已确定的铸造工艺条件下,都对应有适宜的浇注时间范围。
浇注系统浇口尺寸计算

若不满足上述条件,需要通过调节浇口尺寸使各浇口 的流量及成型工艺条件达到一致,这就是浇注系统的平衡。
浇注系统相关尺寸计算
分流道的布置 在多型腔模具中分流道的布置中有平衡式和非平衡式两类: 平衡式布置:
③扇形浇口 成型大平面板状及薄壁塑件时,宜采用扇形浇口。在扇形浇口的
整个长度上,沿进料方向截面宽度逐渐变大,为保持断面积处处相 等,浇口的截面厚度逐渐减小。
浇注系统相关尺寸计算
④点浇口 又称针点浇口或橄榄形浇口,是一种在塑件中央开设浇口时使
用的圆形限制性浇口,用于成型壳类、盒类的热塑性塑件。
优点: 浇口残留痕迹小,易取
浇注系统相关尺寸计算
浇口的平衡 当采用非平衡式布置的浇注系统或者同模生产不同塑件时,需
对浇口的尺寸加以调整,以达到浇注系统的平衡。
浇口平衡的计算思路: 通过计算各个浇口的BGV值(Balanced Gate Value)来判断和 设计。 浇口平衡时满足下述要求:
①相同塑件多型腔,各浇口BGV值必须相等 ②不同塑件多型腔,各剪口BGV值必须与其塑件的填充量成正比
由上式可得:
AG1 3t12 0.73mm2,t1 0.49mm,b1 3t1 1.47mm AG3 3t32 1.87mm2, t3 0.79mm,b3 3t3 2.37mm
浇注系统相关尺寸计算
3.浇口的设计 浇口亦称进料口,是连接分流道与型腔的最短通道。
浇注系统相关尺寸计算
浇口的尺寸一般根据经验确定,截面积为分流道断面积的 3%~9%,截面形状常为矩形或圆形,浇口的长度为1~1.5mm。
- 1、下载文档前请自行甄别文档内容的完整性,平台不提供额外的编辑、内容补充、找答案等附加服务。
- 2、"仅部分预览"的文档,不可在线预览部分如存在完整性等问题,可反馈申请退款(可完整预览的文档不适用该条件!)。
- 3、如文档侵犯您的权益,请联系客服反馈,我们会尽快为您处理(人工客服工作时间:9:00-18:30)。
浇注系统相关尺寸计算
浇口的平衡例题
解:由排列位置知2A2B4A4B相同,3A3B5A5B相同,1A1B相同,
因此只需求1A2A3A尺寸即可。先求2A尺寸,并以此为基准求2A3A
的尺寸。
2
2
1)分流道圆形截面积 AR :ARd2R5.2 08m2m 2.02m 7 2m
Wa、Wb ----分别为a、b型腔的填充量(熔体质量或体积) AGa、AGb----分别为a、b型腔的浇口截面积( mm2)
LRa、LRb----分别为主流道中心到达a、b型腔的流动通道的长度 ( mm)
LGa、LGb----分别为a、b型腔的浇口长度( mm)
浇注系统相关尺寸计算
浇口的平衡 无论是相同塑件还是不同塑件多型腔,一般在设计时取矩形浇口
致因浇口痕迹而影响塑件的表面美观效果。
浇注系统相关尺寸计算
浇注系统的平衡问题
中小塑件的注射模广泛采用一模多腔形式,设计时应保证所 有型腔同时充填和成型。
一般在塑件形状及模具结构允许的情况下,主流道到各型腔的分 流道设计成长度相等、形状及截面尺寸相同的形式(型腔布局为对 称式布局)。
若不满足上述条件,需要通过调节浇口尺寸使各浇口 的流量及成型工艺条件达到一致,这就是浇注系统的平衡。
浇注系统相关尺寸计算
浇口的尺寸一般根据经验确定,截面积为分流道断面积的 3%~9%,截面形状常为矩形或圆形,浇口的长度为1~1.5mm。
注意: 在设计浇口时,往往先取较小的尺寸值,以便在试模时
逐步加以修正。
浇注系统相关尺寸计算
(2)浇口的类型
①直接浇口 直接浇口又称中心浇口、主流道浇口,这种浇口由主流道直接进
2)基准浇口2A的截面尺寸:
由:AG20.0A 7R1.4m 2 2m 得:t2 0 .6m 9 ,b 2 m 3 t2 2 .0m 7m
3)求其他两组浇口的截面尺寸,由BGV相等得:
BG V A G 1
A G 3
1 .42 0 .0
浇注系统相关尺寸计算
一、浇注系统设计 1.主流道的设计 主流道轴线垂直于分型面,属于直浇注系统;主流道轴线平行于分 型面,属于横浇注系统。
直浇注系统
横浇注系统
浇注系统相关尺寸计算
为便于流道凝料的脱出,内壁粗糙度Ra小于0.4μm,主流道 设计成圆锥形,其锥度α=2°~6°,如果锥度过大,易发生涡 流,锥度过小则流道凝料脱出困难
料,常用于成型大而深的塑件。
浇注系统相关尺寸计算
②侧浇口 侧浇口又称边缘浇口,一般开设在分型面上,调整其截面的厚
度和宽度可以调节熔体充模时的剪切速率及浇口固化时间,主要用 于中小型塑件的多型腔模具。
浇注系统相关尺寸计算
③扇形浇口 成型大平面板状及薄壁塑件时,宜采用扇形浇口。在扇形浇口的
整个长度上,沿进料方向截面宽度逐渐变大,为保持断面积处处相 等,浇口的截面厚度逐渐减小。
或圆形浇口,浇口截面积 AG 与分流道的截面积 AR 的比值取:
AG:AR0.0~ 70.09
矩形浇口的截面的宽度b与厚度t的比值常取:
b:t3:1
注意:求解时,一般取浇口长度为定值,通过调 节浇口的宽度和厚度来谋求浇口的平衡。
浇注系统相关尺寸计算
浇注系统相关尺寸计算
浇口的平衡例题
下图为相同10个型腔的模具流道分布图,各浇口均为矩形狭缝,且 各段分流道直径(d R =5.08mm)相等,各浇口长度 LG =1.27mm, 各相邻型腔中心相距143mm,上下型腔分流道长度为102mm。为 保证浇注系统平衡,试确定浇口尺寸?
浇注系统相关尺寸计算
浇口的平衡
相同塑件多型腔的BGV值
BGV AG LR LG
AG ----浇口的截面积( mm2) LR ----从主流道中心到浇口的流动通道的长度( mm2) LG ----浇口的长度( mm)
浇注系统相关尺寸计算
浇口的平衡
2)不同塑件多型腔的BGV值
Wa BGaVAGa LRbLGb Wb BGbV AGb LRaLGa
浇注系统相关尺寸计算
分流道的布置 在多型腔模具中分流道的布置中有平衡式和非平衡式两类: 平衡式布置:
特点:分流道到各型腔浇口的长度、断面形状、尺寸都相同。 优点:可均衡送料和同时充满型腔,塑件的力学性能基本一致。 缺点:分流道比较长。
浇注系统相关尺寸计算
非平衡式布置: 特点:分流道到各型腔浇口长度不相等的布置。 优点:适应于型腔数量较多的模具,使模具结构紧凑 缺点:不利于均衡送料。为同时充满型腔,各浇口的断面尺寸要 制作得不同,在试模中要多次修改才能实现。
浇注系统相关尺寸计算
主流道小端直径d一般取3~6mm,主流道的长度由定模座厚 度确定,一般L不超过60mm,主流道大端与分流道相接处应有 过渡圆角(通常r′取1~3mm)以减少料流转向时的阻力。
浇注系统相关尺寸计算
正确情况:主流道小端直径d比注射机喷嘴直径d0大0.5~1mm, R≥r+(0.5~1)mm。
浇注系统相关尺寸计算
2.分流道的设计 分流道是主流道末端与浇口之间的通道。用于一模多腔或单型腔
多浇口(塑件尺寸大)的场合。
浇注系统相关尺寸计算
分流道的截面形状及尺寸 为便于机械加工及凝料脱模,分流道一般设置在分型面上。
浇注系统相关尺寸计算
3.浇口的设计 浇口亦称进料口,是连接分流道与型腔的最短通道。
浇注系统相关尺寸计算
浇口的平衡 当采用非平衡式布置的浇注系统或者同模生产不同塑件时,需
对浇口的尺寸加以调整,以达到浇注系统的平衡。
浇口平衡的计算思路: 通过计算各个浇口的BGV值(Balanced Gate Value)来判断和 设计。 浇口平衡时满足下述要求:
①相同塑件多型腔,各浇口BGV值必须相等 ②不同塑件多型腔,各剪口BGV值必须与其塑件的填充量成正比
浇注系统相关尺寸计算
④点浇口 又称针点浇口或橄榄形浇口,是一种在塑件中央开设浇口时使
用的圆形限制性浇口,用于成型壳类、盒类的热塑性塑件。
优点: 浇口残留痕迹小,易取
得浇注系统的平衡,也利于 自动化操作。
缺点: 在模具结构上需增加一个
分型面,即双分型面,以便 浇口凝料取出。
浇注系统相关尺寸计算
⑤潜伏浇口 浇口的分流道位于分型面上,浇口本身设在模具内的隐蔽处,不