汽车车门拉延模具设计与成形模拟
汽车卧铺盖板拉延模设计(有cad图+文献翻译)

摘要本次设计做的是汽车车身覆盖件冲压模设计中的第一序拉延模的设计。
汽车模具在中国因为发展的时间比较短所以在很多方面现在比起一些机械工业发达的国家还有很大的差距。
但我国近年来在汽车模具方面也取得不少的发展与进步。
本次设计我做的是汽车盖板的拉延模设计。
在模具设计中主要是根据设计好的板件来用UG软件进行三维造型设计来完成模具的结构设计然后进行模具加工调试来最终生产出合格的模具。
在三维造型方面主要可以分为压边圈设计、上模设计、凸模设计和下模本体设计。
在进行各部分设计时要严格按照模具结构设计规范来进行设计。
在本次设计中我严格按照冲压模设计标准来进行模具设计,其中有一部分技术规范属于企业内部规范。
本设计经过反复检查没有发现大的纰漏,完全符合模具设计的要求。
关键词:汽车模具 UG 拉延模设计标准AbstractThe design do is auto body panel stamping die design sequence in the first drawing die design. Automotive die in China due to the development of a comparatively short time it is in many ways than some mechanical industrial developed countries there is a great gap. However, in recent years, China has also made the car a lot of mold development and progress. The design of the car I did the cover drawing die design. In the die design are mainly based on panels designed to use the UG software design to complete the three-dimensional structure of the mold and then mold design to final production of qualified commissioning of the mold. Main aspects of three-dimensional modeling can be divided into the blank holder design, the mold design, design and lower die punch body design. During the design of various parts of the structure to be in strict accordance with design specifications to the mold design.In this design I strictly in accordance with design standards for stamping die mold design, including technical specifications are part of the internal specification. After repeated checking of the design found no major flaws, in full compliance with the mold design.Keywords: car mold drawing die design standards UG目录前言 (1)1 设计前的准备工作 (5)1.1 技术协议 (5)1.1.1模具的材料及热处理 (5)1.1.2、模具结构 (5)1.1.3. 工艺、设计、制造要求 (7)1.2 查看工法图 (8)1.3查验对比 (9)1.4结构选择 (9)1.5材质选择 (9)2处理数模及分模线 (17)2.1片体缝合 (17)2.2拉伸实体 (17)2.3设计凸模退刀面 (18)2.4设计凸模主筋 (19)2.5压边圈退刀面的设计 (19)2.6压边圈主筋的设计 (20)2.7确定压边圈导向 (20)2.8导滑面的设计 (21)2.9导板数量的确定 (21)3压边圈的设计 (24)3.1压边圈强度 (24)3.2压边圈压力确定 (25)3.2压边圈让位及补强 (26)3.3气顶杆的设计 (27)3.4压边圈镶块设计 (28)3.5调压垫块与墩死垫块的设计 (28)3.6弹顶销的设计 (30)4上模的设计 (31)4.1上模型面及主筋 (31)4.2上模法兰面和辅筋 (31)4.3上模调压凸台的设计 (31)4.4上模起吊和反转结构的设计 (32)4.5压板槽的设计 (32)4.6导腿的设计 (32)4.7安全平台的设计 (32)4.8设计中心键槽及压板槽加强筋 (33)4.9上模弹顶销的设计 (33)4.10设计减轻空、流水孔及排气孔 (33)4.11定位板地设计 (34)5下模的设计 (41)5.1下模座的设计 (42)5.2设计墩死垫块 (42)5.3设计凸模安装固定法兰 (43)5.4设计安全螺钉 (43)5.5设计安全护板 (44)5.6运输连接的设计 (44)5.7导柱导向设计 (44)5.8下模导板窥视孔的设计 (44)5.9设计完成 (45)致谢 (46)参考文献 (47)前言汽车模具最主要的组成部分就是覆盖件模具。
汽车侧围拉延成型的数值模拟分析及运用
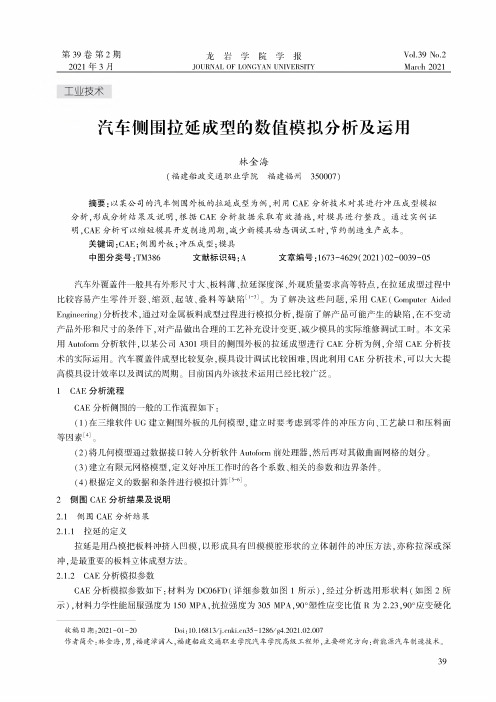
Vol.39 No.2March 2021第 39 卷 第 2 期2021年3月龙 岩 学 院 学 报J0URNAL 0F L0NGYAN UNIVERSITY 工业技术汽车侧围拉延成型的数值模拟分析及运用林金海(福建船政交通职业学院 福建福州350007)摘要:以某公司的汽车侧围外板的拉延成型为例,利用CAE 分析技术对其进行冲压成型模拟 分析,形成分析结果及说明,根据CAE 分析数据采取有效措施,对模具进行整改。
通过实例证 明,CAE 分析可以缩短模具开发制造周期,减少新模具动态调试工时,节约制造生产成本。
关键词:CAE ;侧围外板;冲压成型;模具中图分类号:TM386 文献标识码:A 文章编号:1673-4629( 2021) 02-0039-05汽车外覆盖件一般具有外形尺寸大、板料薄、拉延深度深、外观质量要求高等特点,在拉延成型过程中 比较容易产生零件开裂、缩颈、起皱、叠料等缺陷[1却。
为了解决这些问题,采用CAE ( Computer Aided Engineering)分析技术,通过对金属板料成型过程进行模拟分析,提前了解产品可能产生的缺陷,在不变动 产品外形和尺寸的条件下,对产品做出合理的工艺补充设计变更、减少模具的实际维修调试工时。
本文采 用Autoform 分析软件,以某公司A301项目的侧围外板的拉延成型进行CAE 分析为例,介绍CAE 分析技 术的实际运用。
汽车覆盖件成型比较复杂,模具设计调试比较困难,因此利用CAE 分析技术,可以大大提 高模具设计效率以及调试的周期。
目前国内外该技术运用已经比较广泛。
1 CAE 分析流程CAE 分析侧围的一般的工作流程如下:(1) 在三维软件UG 建立侧围外板的几何模型,建立时要考虑到零件的冲压方向、工艺缺口和压料面 等因素[4]o(2) 将几何模型通过数据接口转入分析软件Autoform 前处理器,然后再对其做曲面网格的划分。
(3) 建立有限元网格模型,定义好冲压工作时的各个系数、相关的参数和边界条件。
基于显式有限元方法的汽车顶盖拉延成形仿真与模具优化
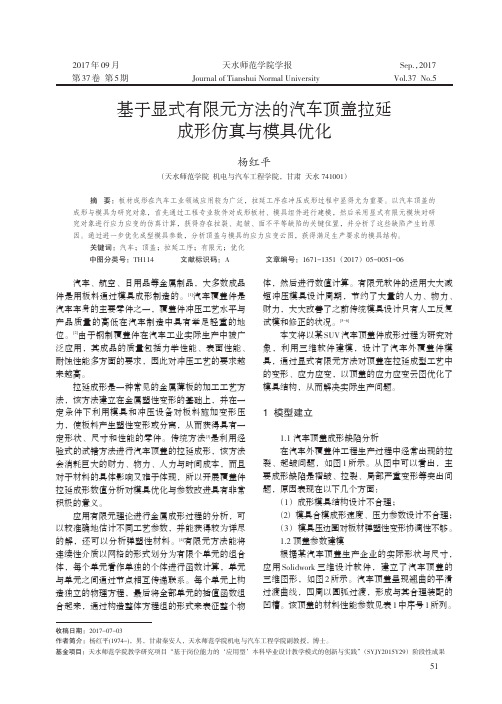
收稿日期:2017-07-03作者简介:杨红平(1974-),男,甘肃秦安人,天水师范学院机电与汽车工程学院副教授,博士。
基金项目:天水师范学院教学研究项目“基于岗位能力的‘应用型’本科毕业设计教学模式的创新与实践”(SYJY2015Y29)阶段性成果汽车、航空、日用品等金属制品,大多数成品件是用板料通过模具成形制造的。
[1]汽车覆盖件是汽车车身的主要零件之一,覆盖件冲压工艺水平与产品质量的高低在汽车制造中具有举足轻重的地位。
[2]由于钢制覆盖件在汽车工业实际生产中被广泛应用,其成品的质量包括力学性能、表面性能、耐蚀性能多方面的要求,因此对冲压工艺的要求越来越高。
拉延成形是一种常见的金属薄板的加工工艺方法,该方法建立在金属塑性变形的基础上,并在一定条件下利用模具和冲压设备对板料施加变形压力,使板料产生塑性变形或分离,从而获得具有一定形状、尺寸和性能的零件。
传统方法[3]是利用经验式的试错方法进行汽车顶盖的拉延成形,该方法会消耗巨大的财力、物力、人力与时间成本,而且对于材料的具体影响又难于体现,所以开展覆盖件拉延成形数值分析对模具优化与参数改进具有非常积极的意义。
应用有限元理论进行金属成形过程的分析,可以较准确地估计不同工艺参数,并能获得较为详尽的解,还可以分析弹塑性材料。
[4]有限元方法能将连续性介质以网格的形式划分为有限个单元的组合体,每个单元看作单独的个体进行函数计算,单元与单元之间通过节点相互传递联系。
每个单元上构造独立的物理方程,最后将全部单元的插值函数组合起来,通过构造整体方程组的形式来表征整个物体,然后进行数值计算。
有限元软件的运用大大减短冲压模具设计周期,节约了大量的人力、物力、财力,大大改善了之前传统模具设计只有人工反复试模和修正的状况。
[5-6]本文将以某SUV 汽车顶盖件成形过程为研究对象,利用三维软件建模,设计了汽车外覆盖件模具,通过显式有限元方法对顶盖在拉延成型工艺中的变形、应力应变,以顶盖的应力应变云图优化了模具结构,从而解决实际生产问题。
基于CAE技术的汽车覆盖件拉延模具设计

242机械设计与制造MachineryDesign&Manufacture第4期2010年4月文章编号:1001—3997(2010)04-0242—03基于CAE技术的汽车覆盖件拉延模具设计(1广西工学院机械工程系,柳州545006)(2柳州六合方盛机械有限公司,柳州545006)(3辽宁省机械研究院有限公司,沈阳110032)DiedesignofdrawingfortheautomobilepaneIbasedonCAEtechnologyL[UXi-fenl,HUANGHua-Yan2,ZHANGHong-mi3(1GuangxiUniversityofTechnology,Liuzhou545006,China)(2LiuzhouLiuhefangshengMachineCo.,Liuzhou545006,China)(3LiaoningProvincialMachineryResearchInstituteCo.,Ltd,Shenyang110032,China):【摘要】介绍了在CAE技术基础上进行的汽车覆盖件模具设计过程,利用板料成形有限元分析软;÷件Autoform实现了模具压料面、工艺补充面以及拉伸筋设计和覆盖件成形过程模拟。
实现了在有限元软÷:件内部进行模具的参数化设计,既缩短了模具设计时间,又提高了模具设计可靠性。
?i关键词:汽车覆盖件;拉延模具设计;Autoformi÷【Abstract】Theprocessofdie如s咖加rtheautomobilepanelbasedonCAEtechnologyisintro-;?duced.Thedesignofthebindersu币。
配e,addendumsu咖aceanddrawbead,andthesimulationsofthefo册一?:ingprocessfortheaut。
mobilepaneloreimplementedwiththeshee£metalformingsoJ2wal-eAut。
基于Dynaform的汽车覆盖件成形中拉延筋的设置与数值模拟_图文

基于Dynaform的汽车覆盖件成形中拉延筋的设置与数值模拟_图文模具技术2020 . No. 639文章编号:100124934(2020 0620039203基于Dynaform 的汽车覆盖件成形中拉延筋的设置与数值模拟郭敏杰, 曾珊琪(陕西科技大学机电工程学院, 陕西西安710021摘要:使用 ETA 公司的CA E 软件Dynaform , 通过求解器L S 2Dyna 计算, 利用E TA/Po st 2p rocessor 来模拟某轿车引擎盖内板的拉深成形。
通过模拟结果的比较, 最终确定拉延筋的最佳布置方案及拉延筋的优化形式等。
缩短了模具设计周期, 降低了设计成本, 提高车身质量。
关键词:Dynaform ; 拉延筋; 汽车覆盖件; 中图分类号:TP391. 9Abstract :By i si twa re ETA/Dynaf or m , t he f or mi ng p rocess of aca r e ngine i calculated by LS 2Dyna a nd si mulated by ETA/Post 2p rocessor. The op ti mal a nd s hap e of draw bea d were deter mi ned by comp a ri ng t he si mulation re 2sults. The i mp roved design could shorte n t he develop me nt cycle of die , reduce design cost a nd i mp rove t he quality of ca r body.K eyw ords :Dynaf or m ; drawbea d ; aut omobile cover ; numerical si mulation0引言拉深件的质量在很大程度上受材料流动的影响。
拉延模结构设计
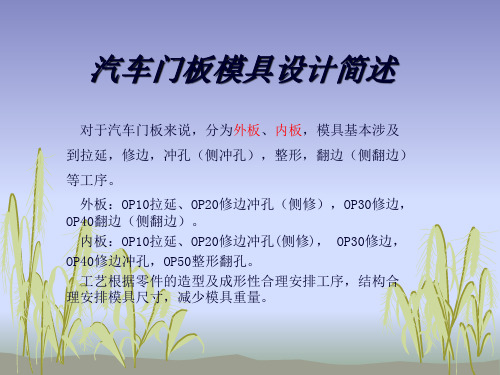
拉延模结构设计
(6)平衡块间距一般在350-400之间,周圈布置,靠近型面,靠近尽量布 置在顶杆上面,下面有筋支撑,保证受力到底。 (7)顶杆腿设计:高度最高150mm,加上顶杆冲击块,满足压边圈行程 (根据客户需求而定,必须满足受力到底,相连顶杆腿应考虑强度)。 (8)素材定位器根据客户要求来定(托料素材定位器用于幅度比较大的 外板),感应器在送料方向L型布置(2个)。 (9)壁厚、筋距、减重孔等按照客户要求设计(压边圈局部最少宽度为 250mm,保证强度)。 (10)四周穿线孔要贯穿,检查与凸模干涉情况。
拉延m,导板与导滑 面至少有2/3的接触
拉延模结构设计
2.3下模座设计 (1)根据项目经理给定的模具尺寸以及模具端头整体布局(考虑全顶杆 避让)。 (2)壁厚、筋距、减重孔等按照客户设计要求设计。 (3)根据压边圈、凸模、顶杆顶出高度、凸模安装面等关系设计下模座 底板(应还考虑底板与压边圈顶杆腿干涉)。 (4)模座筋条避让顶杆(筋刚好在U沟槽上时,要考虑设计马蹄筋,保证 受力到底),U沟锁付必须按客户要求设计。 (5)上下模具防呆(箱跟加导板防呆,一边箱根往Y正负方向偏10mm)。 (6)闭合块合理分布,压边圈与闭合块间留2mm的间隙。 (6)其它标准件按照客户标准设计。
(2)壁厚、筋距、减重孔等按照客户设计要求设计。 (3)凸模里面的筋必须受力到底,而且下模座的 筋要与顶杆避开(设计时先把顶杆拉出来,把下模座、凸模局部的筋画
出来)。 (4) 锁付考虑实际情况采用内锁或者外锁销钉 对角布置,大头销也对角布置,尽量与销钉分开, 保证凸模安装精度。 (5) 拉延凸模没有起吊,只有翻转。 (6) 凸模周圈定位根据客户要求设计。
拉延模结构设计
2.2压边圈设计 2.2.1压边圈设计要点: (1)压边圈的行程是CAE理论,安全侧销行程为压边圈的行程CAE理论+安 全量(10-20mm)。 (2)一个压边圈基本是四个安全侧销(根据客户要求选择有压板、侧销、 安全螺栓)。 (3)导板设计:导板设计时要过导10mm,压边圈顶出时,导板与导滑面 至少有2/3的接触(一体式压边圈10块导板,单独压边圈基本是8个)。 (4)起吊分别布置在压边圈四个角上,起吊高度尽量一致,翻转合理设 计(考虑压边圈重量,选择合适的起吊、翻转螺纹)。 (5)防侧键、防侧导板合理布置(防侧键四周分布,防侧导板送料方向布 置)。
汽车车门拉延模具设计

汽车车门拉延模具设计汽车车门拉延模具设计是汽车制造中极为重要的一个环节。
汽车车门作为车辆的进入和出入通道,直接关乎汽车舒适度和安全性。
而车门拉延模具设计,就决定了车门的质量和外观,影响汽车的整体品质。
下面将从汽车车门拉延模具所需的条件、设计流程、常见问题等方面进行详细阐述。
一、汽车车门拉延模具的条件1. 材料汽车车门拉延模具材料必须耐热、耐磨耗、寿命长、易加工等特点,常用的材料有合金钢、硬质合金等。
2. 设计汽车车门拉延模具设计应具备制造过程简单、加工成本低等特点,同时还需要考虑车门的质量和外观。
3. 技术汽车车门拉延模具制作技术要求较高,需要采用精密的加工技术和高质量的治具,以确保模具的精度和稳定性。
二、汽车车门拉延模具设计流程1. 方案设计汽车车门拉延模具设计的第一步是方案设计。
方案设计是一个非常关键的环节,需要根据车门的结构和需求,确定模具的摆放方式、模具尺寸、模具数量等方面的设计。
2. 3D建模在方案设计确定后,需要进行3D建模。
通过3D 建模,可以对模具的设计进行更加精细的设计和调整,并进行检查和修改。
3. 选择材料选择材料是汽车车门拉延模具设计中的一个重要环节,需要根据模具的使用环境和车门的要求选择适合的材料。
4. 制造模具制造模具是汽车车门拉延模具设计的最后一步。
制造模具需要选择高精度的机械设备和优质的治具,以确保模具的精度和稳定性。
制造完成后,需要进行检验和调整,以确保模具的质量和性能。
三、汽车车门拉延模具设计常见问题1. 模具表面质量不佳模具表面质量不佳是汽车车门拉延模具设计中经常出现的问题之一。
主要原因是模具加工精度不够高以及模具表面处理不当。
解决方法是优化加工工艺和表面处理过程。
2. 模具磨损严重由于汽车车门拉延模具使用频繁,容易引起模具磨损。
特别是在大批量生产时,模具的使用寿命会受到很大的影响。
使用合适的材料、加强模具的表面硬度、进行模具的定期保养等方法可以降低模具的磨损。
汽车车门拉延模具设计与成形模拟
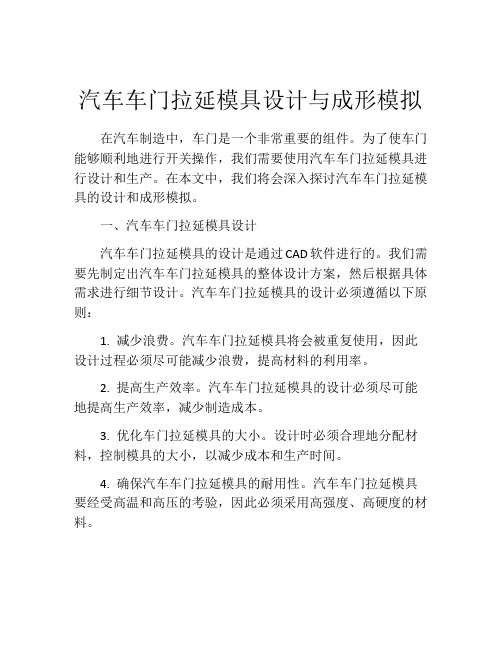
汽车车门拉延模具设计与成形模拟在汽车制造中,车门是一个非常重要的组件。
为了使车门能够顺利地进行开关操作,我们需要使用汽车车门拉延模具进行设计和生产。
在本文中,我们将会深入探讨汽车车门拉延模具的设计和成形模拟。
一、汽车车门拉延模具设计汽车车门拉延模具的设计是通过CAD软件进行的。
我们需要先制定出汽车车门拉延模具的整体设计方案,然后根据具体需求进行细节设计。
汽车车门拉延模具的设计必须遵循以下原则:1. 减少浪费。
汽车车门拉延模具将会被重复使用,因此设计过程必须尽可能减少浪费,提高材料的利用率。
2. 提高生产效率。
汽车车门拉延模具的设计必须尽可能地提高生产效率,减少制造成本。
3. 优化车门拉延模具的大小。
设计时必须合理地分配材料,控制模具的大小,以减少成本和生产时间。
4. 确保汽车车门拉延模具的耐用性。
汽车车门拉延模具要经受高温和高压的考验,因此必须采用高强度、高硬度的材料。
5. 考虑汽车的安全性。
汽车车门是车内的关键部件,设计时必须考虑汽车的安全性,确保车门经过模具成形后符合安全规范。
二、汽车车门拉延模具成形模拟通过汽车车门拉延模具的成形模拟,可以预测成形过程中的变形和应力,并优化汽车车门拉延模具的设计。
在汽车车门拉延模具的成形模拟过程中,需要进行以下步骤:1. 建立数学模型。
建立数学模型是进行模拟的第一步,必须精确描述汽车车门拉延模具的几何形状,包括模具内部和外部的形状,以及汽车车门的形状。
2. 设定模拟参数。
模拟参数是指成形过程中的各种条件和工艺参数,如材料的弹性模量,屈服强度,温度等。
这些参数必须根据实际情况进行设定,以使模拟结果尽可能地接近真实情况。
3. 实施模拟分析。
进行模拟分析是对模拟参数和数学模型的检验和确定。
这一步是模拟过程中最关键的一步,必须进行充分的对比和修正,以获得满意的模拟结果。
为了进行模拟分析,可以使用专业的模拟软件,如ABAQUS、LS-DYNA等。
这些软件可以通过数值方法和计算机模拟分析汽车车门拉延模具的成形过程,预测模具材料的受力情况、变形情况以及汽车车门的成形情况。
汽车顶盖后横梁拉延成形与模具设计

汽车顶盖后横梁拉延成形与模具设计[摘要]汽车顶盖后横梁是汽车中的重要部件,属于覆盖件,其有较高的要求,因此,对汽车后顶盖横梁拉延成形分析及模具设计进行研究有着非常重要的现实意义。
本篇文章,首先对汽车顶盖后横梁拉延成形作了分析,然后对其的拉延模具设计作了简析。
[关键词]汽车顶盖后横梁;拉延成形工艺;模具设计引言汽车顶盖后横梁属于较大的覆盖件且其构成也比较复杂,对其有较高的质量要求,因此,分析其拉延成形和模具设计有着重要的现实意义。
1汽车顶盖后横梁拉延成形分析1.1汽车顶盖后横梁成形工艺简析汽车顶盖后横梁的尺寸一般为九百毫米乘二百毫米乘八十毫米。
应用的材料一般为BLC冷轧钢板。
其经三道工序:拉延、冲孔修边以及整形冲孔成形,适中的深度、较小的尺寸是拉延件结构的特点,仅采用单动拉延模具就可满足拉延件的成形要求。
假是中间部分和边缘部分有高度差存在,且在其试制中拉延件边缘会有不足拉深以及皱起的现象出现的拉深浅覆盖制件。
这就要求在进行模具工艺的优化工作时,要对其参数、润滑以及压边力这三方面的因素有较深层次的考虑。
应该对严重影响模具皱起效果的拉严筋对材料的流动现象加以关注。
1.2汽车顶盖后横梁拉延方向确定冲压工序的后续方案、产品的最终质量以及利用材料效率的高低都是由拉延的方向所决定的。
选择冲压负角最小的方向作为拉深的方向,这可最好的保障:第一,可使毛坯状的板料在与凸模最初始接触中保持最小的相对滑动幅度;第二,拉深板料的时候,可保持板料变形在最大程度上的均匀分布;第三,结束拉延之后,可保持凹摸和凸模的完全贴合[1]。
1.3汽车顶盖后横梁压面料与工艺补充部分的设计采用钣金内部填充工艺与拉深补充工艺将过渡性的材料添加到产品的翻边部分,才能成功拉深出合乎规格的零件,这主要是进行了工艺补充。
进行对存在于拉延部件和压料面间起过渡作用的工艺补充面的设计时,根据产品的具体形状,可对展开翻边的位置和预留切边的空间进行综合性的考虑,为了达到使毛坯拉深条件增大的目的,最终使成形的效果更好,可把零件整体轮廓的修边线向外延展三十毫米到五十毫米不等的距离。
基于Dynaform的汽车覆盖件成形中拉延筋的设置与数值模拟.
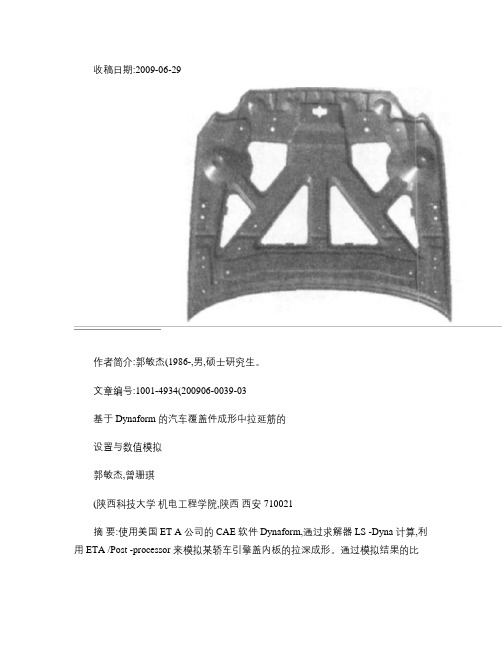
收稿日期:2009-06-29作者简介:郭敏杰(1986-,男,硕士研究生。
文章编号:1001-4934(200906-0039-03基于Dynaform 的汽车覆盖件成形中拉延筋的设置与数值模拟郭敏杰,曾珊琪(陕西科技大学机电工程学院,陕西西安 710021摘要:使用美国ET A 公司的CAE 软件Dynaform,通过求解器LS -Dyna 计算,利用ETA /Post -processor 来模拟某轿车引擎盖内板的拉深成形。
通过模拟结果的比较,最终确定拉延筋的最佳布置方案及拉延筋的优化形式等。
缩短了模具设计周期,降低了设计成本,提高车身质量。
关键词:Dynaform;拉延筋;汽车覆盖件;数值模拟中图分类号:T P391.9 文献标识码:BAbstract:By using increment simulation sof tware ETA/Dynafor m,the forming process of a car engine inner panal w as calculated by LS -Dyn a and simulated byETA/Post -pr ocessor.The optimal setting and sh ape of draw bead w ere deter mined by comparing the simulation r e -sults.T he impr oved design could shorten the development cycle of die,reduce design cost and improve the quality of car body.Keywords:Dynafor m;dr awbead;automobile cover;numerical simulation0 引言拉深件的质量在很大程度上受材料流动的影响。
汽车覆盖件冲压模具毕业设计-拉延-修边冲孔-侧整形
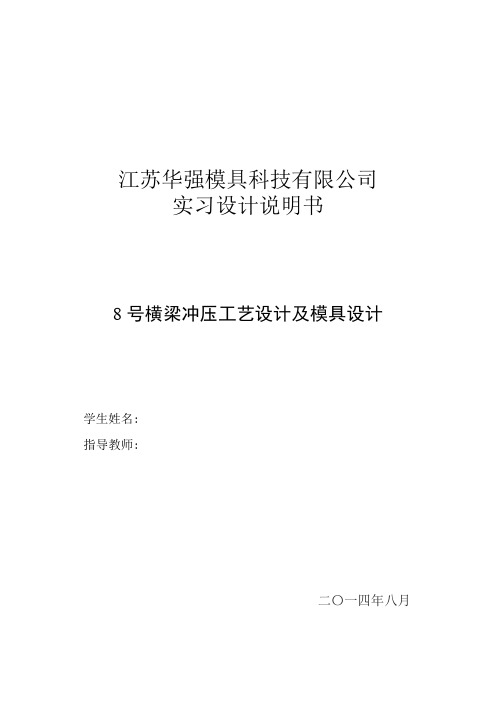
江苏华强模具科技有限公司实习设计说明书8号横梁冲压工艺设计及模具设计学生姓名:指导教师:二〇一四年八月摘要本设计说明书介绍了上汽集团某型号商用车8号横梁加强板的冲压模具设计过程。
首先根据该覆盖件的结构特点,利用CAD和CAE技术,对该零件进行了全面的冲压工艺分析,接着制定了合理的工艺方案,在设计工艺方案的过程中重点介绍了拉深工艺的设计过程,其中主要包括拉深方向的选择、工艺补充面的设计、压料面的设计和拉深筋的设计。
最后根据已定的工艺方案,利用UG软件完成了拉延模、修边冲孔模和侧整形模这三套模具的结构设计。
关键词:汽车覆盖件,CAD,CAE,工艺补充,拉延模。
AbstractThe design specification describes a model number of commercial vehicles SAIC 8 beam stiffeners stamping die design process. Firstly, according to the structural characteristics of the cover, the use of CAD and CAE technology, the components of a comprehensive analysis of the stamping process, and then developed a reasonable process solutions. In the course of the program's design process focuses on the process of drawing the design process, which mainly include the drawing direction of choice addendum design, design and design drawbead binder surface. Finally, according to the process scheme has been set, using UG software to complete the drawing die, punching die design and side trimming plastic mold co three mold.Keywords: auto cover, CAD, CAE, addendum, drawing die.目录第一章概论 (1)1.1课题背景 (1)1.2课题的意义 (1)第二章产品工艺方案的确定 (2)2.1产品的结构分析 (2)2.2产品的成形可行性分析 (2)2.3工艺方案的提出 (2)2.4工艺方案的选择 (3)第三章拉延模的工艺设计 (5)3.1拉延工艺的设计原则 (5)3.2拉延制件的设计 (6)3.2.1拉深方向的选择 (6)3.2.2工艺补充部分的设计 (7)3.2.3压料面的设计 (9)3.2.4拉延筋的设计 (10)3.2.5拉深制件的创建 (13)第四章拉延模的设计 (15)4.1拉延模的类型 (15)4.2拉延模类型的选择 (15)4.3拉延模工艺参数的计算 (15)4.3.1压力中心的确定 (15)4.3.2拉伸力的计算 (16)4.3.3压边力的计算 (16)4.3.4冲压设备的选择 (17)4.5拉延模主要零件的结构设计 (18)4.5.1拉延凹模的设计 (18)4.5.2拉延凸模的设计 (20)4.5.3压料装置的设计 (20)4.5.4顶件装置的设计 (21)4.5.5导向装置的设计 (22)4.5.6限位和起吊装置的设计 (22)4.4.7模架铸件结构的设计 (23)4.4.8拉延模的整体设计 (24)第五章修边模的设计 (26)5.1修边模工艺参数的计算 (26)5.1.1修边凸、凹模刃口尺寸计算 (26)5.1.2压边力的计算 (26)5.1.3冲裁力的计算 (27)5.1.4卸料力的计算 (27)5.1.5顶件力的计算 (27)5.1.6冲裁工艺力的计算 (27)5.1.7冲裁设备的选择 (27)5.2修边模主要零件的结构设计 (29)5.2.1修边模结构设计原则 (29)5.2.2修边模类型的选择 (29)5.2.3修边模结构方案设计 (30)5.2.4修边模主要零件的设计 (30)5.2.5修边冲孔模的整体设计 (32)第六章侧整形模的设计 (33)6.1整形 (33)6.2斜楔机构 (33)6.2.1斜楔机构的组成 (33)6.2.2斜楔机构的类型 (33)6.2.3斜楔机构的运动分析 (34)6.2.4斜楔机构的受力分析 (35)6.2.5滑块的工作效率 (35)6.2.5斜楔机构的选择原则 (35)6.3侧整形模工艺参数的计算 (36)6.3.1整形力的计算 (36)6.3.2冲压设备的选择 (36)6.4侧整形模主要零件的结构设计 (38)6.4.1整形刀块的设计 (38)6.4.2压料装置的设计 (39)6.4.3顶件装置的设计 (39)6.4.4侧整形模整体的设计 (40)结论 (41)参考文献 (42)致谢 (43)第一章概论1.1课题背景此次设计产品依托所在江苏华强模具科技有限公司的“无锡振华SV71项目”,产品名称8号横梁加强版,产品编号C00018679。
汽车车门内板冲压成形工艺分析

汽车车门内板冲压成形工艺分析•该文分析了某轿车车门内板的成形工艺及易产生的缺陷,并据此制定了其合理的冲压工艺方案。
文章通过对拉延成形过程的模拟与分析,得出了合理的工艺方案,目的是为类似零件工艺方案的制定提供参考。
汽车覆盖件具有尺寸大、相对厚度小、形状复杂等特点,决定了在冲压成形中板料变形的复杂性,变形规律不易被掌握,不能定量地对主要工艺参数和模具参数进行计算,在工程实践中还主要运用经验类比来进行冲压工艺设计。
一、冲压工艺制定1.零件工艺分析图1所示为某轿车车门内板零件图,材料为St14,料厚0.8mm。
从图可以看出,该零件形状复杂,高差较大,局部成形较多,板料的变形不是单纯的拉延成形,而是存在一定程度的胀形变形,是典型的汽车覆盖件。
图1中的a和b处,由于窗框部分进行内工艺补充后,形成了零件的反成形形状,这部分形状的成形一般不能靠外部材料进行补充,只能靠该部分板料的胀形成形来实现,胀形成形深度较深,a和b处大约有20mm左右,且转角部R较小,因此在拉延成形过程中很容易出现破裂。
在零件的c处,存在大约12mm高的台阶,此部分若在第一次拉延过程中直接成形,则压料面可能有以下两种分法:(1)将c部分作为压边面的一部分,即将分模线分在零件侧壁圆角处,这样由于台阶对板料的进料阻力较大,易导致零件在拉延过程中可能产生破裂;(2)将c部分作为凸模的一部分,即将分模线分在c部分外侧的法兰上,则在拉延过程中该区域的板料是悬空的,在径向拉应力和切向压应力的作用下,材料集中收缩到此处,可能导致零件的该部分起皱,甚至有迭料的可能。
由上面的工艺分析可知,该覆盖件成形难度大,成形工艺较复杂。
图1 某轿车车门内板零件图2.工艺方案的制定产品冲压成形工艺的确定过程,就是分析和预测板料在变形过程中可能产生的缺陷,并采取一定的措施,以消除和防止冲压缺陷,同时考虑制造能力、冲压设备、投资成本等因素。
根据本零件的工艺性和本身的结构特点,结合实际生产情况,车门内板的工艺过程如下:拉延+切角;二次拉延+切边+冲孔;切边+冲孔;侧切+侧冲孔翻孔+冲孔+整形;整形+冲孔。
某车型尾门内板拉深成形模具型面设计及成形性数值模拟
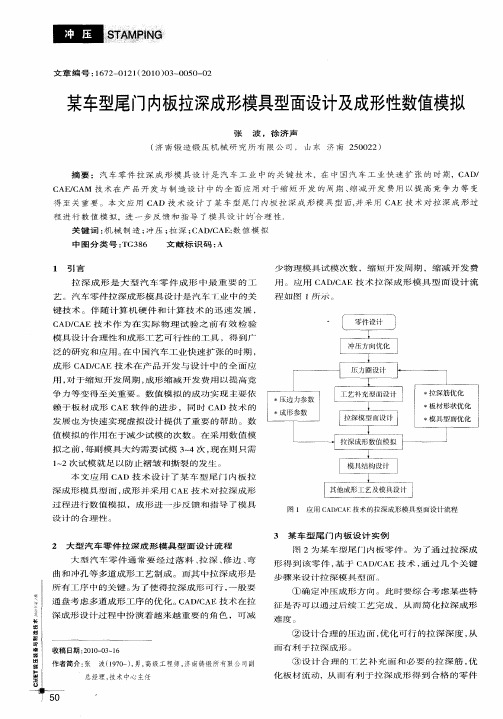
赖 于板 材成 形 C AE软 件 的 进 步 , 同 时 CAD技 术 的
发 展 也 为 快 速 实 现 虚 拟 设 计 提 供 了 重 要 的 帮 助 。数 值 模 拟 的 作 用 在 于 减 O' - ̄模 的 次 数 。 在 采 用 数 值 模 i
拟 之 前 , 副 模 具 大 约 需 要 试 模 就 足 以 防 止 褶 皱 和 撕 裂 的 发 生 。 ~ 本 文应 用 C AD 技 术 设 计 了 某 车 型 尾 门 内 板 拉
深成 形模 具型 面 , 形 并采 用 C 成 AE 技 术 对 拉 深 成 形 过 程 进 行 数 值 模 拟 ,成 形 进 一 步 反 馈 和 指 导 了 模 具 设计 的合理 性 。 3 某 车 型 尾 门 内板 设 计 实 例 2 大 型 汽 车 零 件 拉 深 成 形 模 具 型 面 设 计 流 程
质量。
④ 运 用 初 步 设 计 好 的 拉 深 成 形 模 具 型 面 进 行
C AE数 值 模 拟 , 定 成 形 可 行 性 。 如 有 必 要 进 行 优 确 化 修正拉 深 模 型面 。
图 4 拉深成形数值模拟板 材厚度变化
⑤ 在 可 行 的 拉 深 模 具 型 面 E进 行 工 艺 参 数 优
摘 要 :汽 车 零 件 拉 深 成 形 模 具 设 计 是 汽 车 工 业 中 的 关 键 技 术 ,在 中 国 汽 车 工 业 快 速 扩 张 的 时 期 ,C / AD C / AE CAM 技 术 在 产 品 开 发 与 制 造 设 计 中 的全 面 应 用 对 于 缩 短 开 发 的 周 期 、 减 开 发 费用 以提 高 竞 争 力 等 变 缩 得 至 关 重 要 。本 文 应 用 CAD 技 术 设 计 了某 车 型 尾 门 内板 拉 深 成 形 模 具 型 面 , 采 用 C 并 AE 技 术 对 拉 深 成 形 过 程 进 行 数 值 模 拟 ,进 一 步 反 馈 和 指 导 了模 具 设 计 的 理 性 . 合
某车型车门内板试制工艺及模具设计
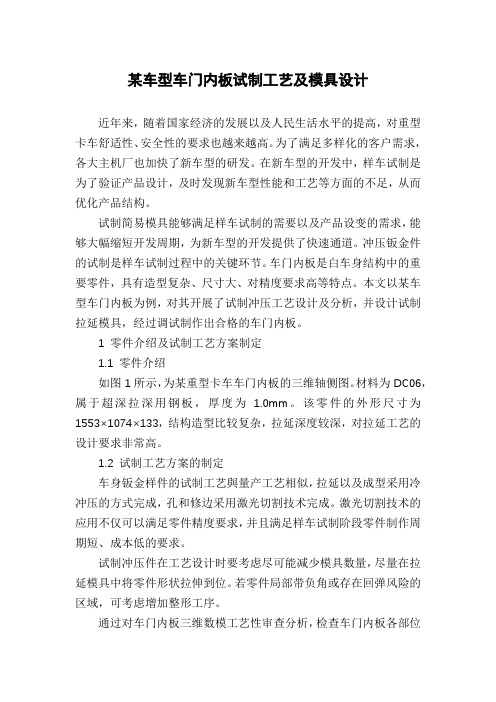
某车型车门内板试制工艺及模具设计近年来,随着国家经济的发展以及人民生活水平的提高,对重型卡车舒适性、安全性的要求也越来越高。
为了满足多样化的客户需求,各大主机厂也加快了新车型的研发。
在新车型的开发中,样车试制是为了验证产品设计,及时发现新车型性能和工艺等方面的不足,从而优化产品结构。
试制简易模具能够满足样车试制的需要以及产品设变的需求,能够大幅缩短开发周期,为新车型的开发提供了快速通道。
冲压钣金件的试制是样车试制过程中的关键环节。
车门内板是白车身结构中的重要零件,具有造型复杂、尺寸大、对精度要求高等特点。
本文以某车型车门内板为例,对其开展了试制冲压工艺设计及分析,并设计试制拉延模具,经过调试制作出合格的车门内板。
1 零件介绍及试制工艺方案制定1.1 零件介绍如图1所示,为某重型卡车车门内板的三维轴侧图。
材料为DC06,属于超深拉深用钢板,厚度为 1.0mm。
该零件的外形尺寸为1553×1074×133,结构造型比较复杂,拉延深度较深,对拉延工艺的设计要求非常高。
1.2 试制工艺方案的制定车身钣金样件的试制工艺與量产工艺相似,拉延以及成型采用冷冲压的方式完成,孔和修边采用激光切割技术完成。
激光切割技术的应用不仅可以满足零件精度要求,并且满足样车试制阶段零件制作周期短、成本低的要求。
试制冲压件在工艺设计时要考虑尽可能减少模具数量,尽量在拉延模具中将零件形状拉伸到位。
若零件局部带负角或存在回弹风险的区域,可考虑增加整形工序。
通过对车门内板三维数模工艺性审查分析,检查车门内板各部位均无冲压负角,因此无需增加整形工序。
该车门内板存在翻边结构,一般情况下的试制工艺方案为OP10拉延,OP20修边侧修边冲孔侧冲孔(激光切割完成),OP30翻边。
车门内板的翻边结构如图2所示:翻边高度为2.2 mm,高度较小。
我们本着减少模具数量、降低试制成本的原则,考虑是否可以将此处翻边结构集成在拉延工序全部成型。
- 1、下载文档前请自行甄别文档内容的完整性,平台不提供额外的编辑、内容补充、找答案等附加服务。
- 2、"仅部分预览"的文档,不可在线预览部分如存在完整性等问题,可反馈申请退款(可完整预览的文档不适用该条件!)。
- 3、如文档侵犯您的权益,请联系客服反馈,我们会尽快为您处理(人工客服工作时间:9:00-18:30)。
毕业设计(论文)
专业:机械设计制造及其自动化
题目:汽车车门拉延模具设计
与成形模拟
作 者 姓 名:
导师及职称:
导师所在单位Байду номын сангаас机械与汽车工程学院
汽车车门拉延模具设计与成形模拟
摘 要
本课题把汽车覆盖件车门内板作为研究的对象,以常见的板料成形分析软件Dynaform作为工具对拉延成形工艺参数进行研究。本课题设计的意义是拉延成形CAE分析可以提前预测冲压产品的缺陷,帮助工程技术人员对拉延成形工艺进行优化,以减少反复试模修模的次数,缩短产品的设计和生产周期。完成的主要工作有通过UG对汽车车门进行拉延模具的设计,再根据零件的结构特点制定合理的成形工序,采用Dynaform软件对拉深成形过程进行数值模拟,查看模拟结果中的板料流入量,根据经验和反复对试验结果的验证与分析后,重新设定相关系数,找到最合适的参数设置。
Through the analysis of Dynaform software simulation results, we can conclude that sheet thickness, drawing beads design, BHF size, the size of the design forming, stamping the number and intensity of such results has a significant impact on the sheet metal forming. Only through experience and constantly experiments can we find out the best solution and get the best simulation results.
通过Dynaform软件的模拟仿真结果的分析,板料的厚度,拉延筋的设计,压边力的大小,成形的尺寸设计,冲压的次数与力度等对板料的成形结果都有很大影响,要想获得最理想的仿真结果,只有通过经验和不断地实验才能找出最佳方案。
本毕业设计的有用结论主要是用Dynaform软件可以模拟板料成形的真实过程,从而避免生产过程耗费很大的人力物力财力去试验,很大程度上节约成本。CAE数值分析仿真结果也十分准确,在中国仿真率达到97%,在国外达到100%,它的应用将越来越广泛。
The main useful conclusions of graduation design is that the real process of sheet metal forming can be simulated by Dynaform software, in order to avoid labor-intensive production processes and material resources to test and to save the cost largely. CAE Numerical analysis and simulation results are also very accurate simulation in China reached 97% to 100% in a foreign country, its application will be more widely
Keywords: drawing forming; CAE analysis; Dynaform Software
插图清单
图1-1汽车门内板零件- - - - - - - - - - - - - - - - - - - - - - - - - - - - - - - - - - - - - - - - - - - - - - -4
关键词:拉延成形;CAE分析;Dynaform软件
Mold design and Forming Simulation of the Drawing of Car Door
Abstract
This topic do research on forming process parameters with the car door inner panel as the object of study, and common sheet metal forming analysis software Dynaform as a tool studied. Design of this project is the significance of drawing forming CAE analysis can predict in advance stamping product defects, helping engineers and technicians on the drawing forming process optimization to reduce repair mode repeatedly tryout times, shorten product design and production cycle. The main work completed through the car door for UG drawing die design, according to the structural characteristics of the part forming process to develop a reasonable, using software Dynaform deep drawing process is simulated view simulation results sheet inflows based on experience and repeated validation of the test results and analysis, re-set the correlation coefficient, to find the most suitable parameter settings.