@上汽通用五菱-供应商质量管理16步程序
通用汽车供应商管理16步法【最新版】

通用汽车供应商管理16步法1.初级评估广告积分制管理全新的管理方法,打破传统管理思维,一切以人为本,员工乐于接受.^^积分制管理被国内越来越多的单位引进实施,在国...定义:在进行潜在供应商评估之前,对新的潜在的供应商做一个初步的现场评估,或让供应商自我评估以确定供应商是否具有基本的质量体系,合适的技术能力和良好的管理水平。
目的:通过评估以确认一个新的潜在供应商是否有资格至少能进行潜在供应商评估范围:这个初步评估的过程适用于所有被认作是潜在来源的新的供应商。
程序:a.通用汽车公司的采购人员,经理或工程师进行现场评估b.供应商自我评估只能在通用汽车公司的要求下进行所有要素与现场评估的要素一致。
评分体系用以确定供应商是否有资格至少能进行潜在供应商评估。
2.潜在供应商评估定义:现场评估供应商是否能达到对管理体系的最基本要求目的:进行为期一至二天的评估以验证新的潜在供应商是否有能力达到与上汽通用五菱公司开展业务的最基本要求范围:在推荐某一供应商来开拓新的业务之前,如果该供应商未具备QS-9000认证,并且在以下任一状况成立的情形下,必须进行潜在供应商评审:1.潜在供应商的制造场所不是上海GM的现有供货源。
2.该项技术/零部件对此供应商的制造场所而言是全新的。
另外,当采购部门认为具有高度风险时,也将进行潜在供应商评审。
程序:1.采取根据QS-9000制定的潜在供应商评审文件形式。
2.必须在选定供应商只之前完成。
3.选定供应商定义:供应商评选委员会批准合格厂商的程序。
目的:选定在质量,服务及价格方面都具有竞争力的厂商来提供产品范围:全球范围内的供应商。
程序:由上海GM的供应商开发几供应商质量部门来:1.审核潜在供应商评审结果2.评估各候选供货来源3.批准或否决建议4.在必要的情形下批准整改计划5.签署决议文本4.产品质量先期策划和控制计划定义:为确保产品能满足客户的要求而建立一套完整的质量计划。
目的:此程序要求供应商开发并实施产品质量计划来:•利用资源,满足客户要求•近早发现所需的更改•保证全部必要步骤按期完成•促进双方信息交流•以具有竞争性的价格按时提供合格产品适用范围:所有为GM供货的供应商都必须针对每一个新零部件执行“产品质量先期策划和控制计划”程序。
供应商质量培训课程-供应商质量管理16步程序
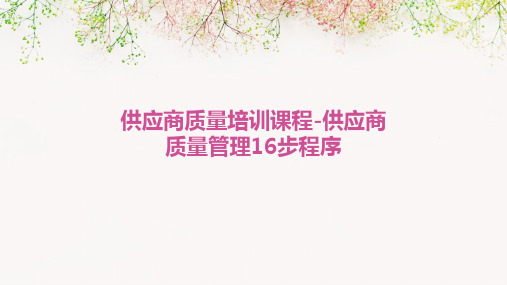
目
CONTENCT
录
• 供应商质量管理的概述 • 供应商质量管理的16步程序 • 供应商质量管理案例分析 • 总结与展望
01
供应商质量管理的概述
供应商质量管理的重要性
01
确保产品质量
供应商质量管理是确保产品质量的关健环节,通过严格控制供应商的产
品质量,可以避免因质量问题导致的生产中断和客户投诉。
01
02
03
04
全面性
供应商质量管理应涵盖所有供 应商和所有供应的产品,不应 有任何例外。
预防为主
应注重预防措施,通过在供应 商选择、产品开发、生产过程 控制等环节采取有效的管理措 施,避免质量问题的发生。
科学性
供应商质量管理应遵循科学的 方法和工具,如统计过程控制 、抽样检验等,以确保管理工 作的有效性和准确性。
展望2
数字化和智能化技术的应用将推动供应商质量管 理向更高效、更精准的方向发展。
展望3
可持续性将成为供应商质量管理的重要考量因素 ,企业将更加注重与环保、社会责任等相关的供 应商质量标准。
展望4
未来供应商质量管理将更加注重长期合作关系和 战略合作,而不仅仅是短期交易关系。
THANK YOU
感谢聆听
100%
总结2
供应商质量管理面临着诸多挑战 ,如供应商质量不稳定、交货期 延误、价格波动等。
80%
总结3
通过有效的供应商质量管理,可 以降低企业生产成本、提高产品 质量、增强企业竞争力,从而获 得更多的市场份额。
展望:未来供应商质量管理的发展趋势和方向
展望1
随着全球化和市场竞争的加剧,未来供应商质量 管理将更加注重跨文化交流和合作。
汽配供应商质量改进16步程序

爛间囲励飴16徵P
产品开始
SAICTWL
1引入世界上先进的经营理念和管理系统。
2培育适应全球经济一体化进程的企业文
化。
3有能力、有特点和合作精神的员工。
4以客户为导向,造百姓喜爱的车。
5打造在微车领域国内领先. 际有竞争力的汽车公
司。
SAIC GM WL \
国内最强,国际上一流的汽车企业。
米2010年在微车和小型车年产30—40万辆。
琳从生产资料型微车向乘用型的微车和其他小型车发展。
面对机遇和挑
供应商朋友,1屋备了
吗?
T o H T O
圖®
瞼
一
初级评估(PA/IA)
定义:在潜在供应商评估之前,对新的潜在供应商作一个初步评估,或让供应商自我评估以确定其是否具备基本的质量体系、合适的技术能力和良好的管理水平。
目的:通过半天的评估以确认新的潜在供应商是否有资格进行潜在供应商评估。
范围:适用于所有被认作是潜在来源的新的供应商。
程序:A采购员、经理或工程师进行现场评估
——质量方面有12个要素——技术方面有7个要素
——管理方面有6个要素
B供应商自我评估(只能在客户的要求下进行,所有要素与现场评估的要素一致。
评分体系用以确定新的潜在供应商是否有资格进行潜在供应商评估。
上汽通用五菱-TS16949交流培训-2——采购流程及供应商质量开发流程全文

采购流程及供应商质量/开发流程12内容此次培训的目的和意义采购流程零件开发和批准流程新产品投放质量保证流程供应商质量改进12对SGMW的采购流程和供应商质量/开发流程和要求有一个进一步的了解使供应商了解SGMW的零件开发和批准流程帮助供应商的管理层认识和了解质量及相应策略了解在质量开发和改进过程中的重要环节使供应商了解SGMW对供应商体系的要求和期望此次培训的目的和意义:12采购流程12采购流程确定供应商入围技术评审主要相关方会议完善报价要求(SOR)目标设泄价格谈判采购推荐输出意向书签订潜在供应商的确定平衡报价内容125610111214潜在供应商的评审3采购决泄13供应商研讨会(如适用)4发放报价要求书7 报价9></a>8912采购流程确定供应商入围技术评审主要相关方会议完善报价要求(SOR) 目标设左价格谈判采购推荐输出意向书签订潜在供应商的确定平衡报价内容125612 14潜在供应商的评审3采购决左13供应商研讨会(如适用)4发放报价要求书1011报价8912潜在供应商确左和评审采购策略:-由SGMW采购委员会根拯不同项目制左、在不同零件采购过程中予以遵循确泄潜在供应商的原则:-符合采购策略-除非特殊情况并经采购委员会批准不允许单一供应商采购-符合对现有供应商体系整合的策略-供应商必须在同行业具有优势并且对采购的QSTP有贡献潜在供应商评审:-对供应商是否具有满足SGMW最低要求的能力的现场评审-对现有供应商可以不进行评审,供应商质量开发经理根据需要可要求进行PCPA -对新供应商,或现有供应商新的生产设施或新技术、新工艺,如没有获得QS或TS16949的认证,则须进行PSA评审:否则应进行PCPASGMW采购小组由SGMW采购员、供应商质量工程师、产品工程师组成12上汽通用五菱采购流程确泄供应商入围技术评审主要相关方会议完善报价要求(SOR)目标设立价格谈判采购推荐输出意向书签订潜在供应商的确定平衡报价内容1256101112潜在供应商的评审3采购决左13供应商研讨会(如适用)4发放报价要求书7报价8912供应商入围和报价供应商表现记录:-对现有供应商的质疑、价格、服务和技术表现的记录供应商入围:-只有通过评审的供应商才能入围-对现有供应商,其表现记录为红色或黄色的不能入弗I,除非得到采购委员会的特殊批准报价要求书:-只能向批准入围的供应商发放SGMW报价要求书-报价要求书包括工程SOR、质量SOR以及物流、包装等英它要求*以往常见问题:-供应商的报价不能够反映出SGMW的全部的要求12采购流程确定供应商入围技术评审主要相关方会议完善报价要求(SOR)目标设左价格谈判采购推荐输出意向书签订潜在供应商的确定平衡报价内容25610111214潜在供应商的评审3采购决左13供应商研讨会(如适用)4发放报价要求书7报价8912技术评审技术评审目的:-确认供应商具有完整的技术、质量、项目进度等的解决方案供应商在技术评审中应提供:-项目机构和时间进度计划-质量计划-制造计划-设施和设备计划-产品设计(SOR没有包括的部分)-商务方案(如适用)技术评审的输出:-风险评估:由采购员、SQ工程师和PE工程师共同完成-根据技术能力和质量能力评估决定可以进行下一步采购活动的供应商名单对最初报价要求的修改:-发现有技术或商务问题-SOR内容的更改12采购流程确泄供应商入围技术评审主要相关方会议完善报价要求(SOR)目标设立价格谈判采购推荐输出意向书签订潜在供应商的确定平衡报价内容125610111214潜在供应商的评审3采购决左13供应商研讨会(如适用)4发放报价要求书7报价8912采购推荐和采购决立采购推荐:-综合平衡项目在时间进度、质量、商务和技术方而的需要采购决定:-确立在QSTP最具优势的供应商-采购委员会批准推荐的供应商供应商质量工程师:-审阅和评估推荐堀单-同意/否决推荐意见-批准整改措施(如需要)-会签采购决定文件12供应商质量/开发16步流程12生产计划生产开始持续改进发运控制-一级发运控制-二级高级改进会议全球采购质量研讨会问题解决(PR/R)质量表现监控潜在供应商评审生产前会议样件批准按报价节拍生产初期生产控制生产件批准程序先期产品质量策划采购决定全球采购供应商质量开发16步质量策划设计质量质量管理/保持持续改进12生产计划生产开始持续改进发运控制-一级发运控制-二级高级改进会议全球采购质量研讨会问题解决(PR/R) 质量表现监控潜在供应商评审生产前会议样件批准按报价节拍生产初期生产控制生产件批准程序先期产品质量策划采购决定全球采购供应商质量开发16步SGMW采购流程12生产计划生产开始持续改进发运控制-一级发运控制-二级高级改进会议全球采购质量研讨会问题解决(PR/R) 质量表现监控潜在供应商评审生产前会议样件批准按报价肖拍生产初期生产控制生产件批准程序先期产品质量策划采购决定全球采购供应商质量开发16步SGMW零件开发和批准流程12生产计划生产开始持续改进发运控制-一级发运控制-二级高级改进会议全球采购质量研讨会问题解决(PR/R)质量表现监控潜在供应商评审生产前会议样件批准按报价盯拍生产初期生产控制生产件批准程序先期产品质量策划采购决宦全球采购供应商质量开发16步APQP先期产品质量策划12APQP先期产品质量策划供应商在确认和建立如何为保证产品满足顾客要求而需采取步骤的具体方法新产品投放之前进行的策划,制定具体的要求和掌握必要的信息识别早期更改,避免晚期更改,确保新产品的设计质量与制造质量保证按时、按疑交付满足质量要求的低成本的产品要求应用于所有新零件、供应商负责实施来自管理层的支持-供应商管理层的支持是APQP成功的关键12APQP先期产品质量策划12APQP先期产品质量策划概念设计/批准项目批准样件试生产投放规划产品设计和开发l></a>. 过程设计和开发产品和过程验证牛产计划反馈、评估和改进计划和确定项目产品设计和开发产品和过程验证过程设计和开发反馈评估和改进产品质量先期策划(APQP)的五个阶段1.计划和确定项目2.产品设计和开发3.工艺过程设计和开发4.产品和工艺过程确认5.反馈、评估和改进12APQP先期产品质量策划12成立一个横向职能小组-工程、生产、质量、销售、成本核算、制造、营销、采购等-横向职能小组并不意味着由一个人来做所有的事情项目管理-项目经理负责项目,并对项目的成功和失败承担责任-项目管理是为了满足或超越相关各方需求和期望,将%种知识、 在项目活动中应用的过程APQP 先期产品质量策划12项目管理一般情况下越接近项目投放日期人们才开始关注项目12QS9000要求建立和实施先期产品质量策划并运用APQP 手册中 适当的技术几何尺寸与公差(GD&T)质量功能展开(QFD)制造设计/装配设计(DFM/DFA)价值工程(VE)实验设计(DOE)失效模式及后果分析一设计和过程FMEA有限元方法(FEM)实体建模仿真技术计算机辅助设计/工程(CAD/CAE)可靠性工程计划APQP 先期产品质量策划12APQP 先期产品质量策划充分完整的理解顾客的要求-顾客完整的工程规范要求-顾客装配线的装配、配合和质量要求-不同阶段顾客不同的交样要求-与顾客充分的沟通-以往不同顾客反馈问题产品特性和过程特性的识别-产品特性:是指工程文件上标明的零件的特征(比如尺寸、特性、功能、 性、外观或表而要求)-产品特性分为特殊或一般特性并且可以测量-关键产品特性:在公差范用内的合理的变差会严重影响顾客的满意 巧、工具和技术 化学特-产品质量特性:只要变差在公差范用内,则不会造成顾客的不满意但是一旦超出工程规范限则会引起顾客的不满意-一般产品特性:只要变差在公差范用内,则不会造成顾客的不满意而超出工程规范限顾客的不满意也不是很明显12产品特性和过程特性的识别-过程特性指过程参数-影响KPC/PQC的过程特性为关键过程特性KCC12PFD/PFMEA/PCP/作业指导书/操作者培训APQP先期产品质量策划过程流程图PFD关键特性识别KCDS过程失效模式PFMEA顾客要求过程控制计划PCP历史经验教训质量问题数据作业指导书操作者/检验员培训分级检查经验教训积累质量数据/不断改进12FMEA的定义是使用识别和帮助消除产品和过程的潜在失效模式的技术的分析工具历史最初源于二十世纪四十年代在上世纪六十年代广泛应用于NASA APOLLO项目由从事APOLLO项目的工程师带到其它行业在上世纪八十年代由福特工程技术部门所使用被美国汽车工业协会AIAG所使用被通用汽车应用于整车开发流程和PPAP 失效模式和后果分析FMEA12风险优先顺序数(RPN)简单的乘法对三项因素风险的评估:严重度X 频度数X 不易探测度RPN每个潜在的原因都有RPN对每个问题的发生可能性进行风险评估立足于发现根本原因失效模式和后果分析FMEA12零件开发和批准流程12供应商第二次项目会议生产设计发放供应商选立会议技术规范分析(TSA)供应商第三次项目会议生产件批准生产试运行GP12初期生产控制供应商第一次项目会议125611121315工装设计发放3GP9按报价节拍生产14供应商工装设讣和制造4实验室批准7工装样件生产和提交8零件开发和批准流程供应商第四次项目会议16样件批准91012零件开发和批准流程供应商第二次项目会议生产设计发放供应商选定会议技术规范分析(TSA)供应商第三次项目会议生产件批准生产试运行GP12初期生产控制供应商第一次项目会议125611121315工装设计发放3GP9按报价节拍生产14供应商工装设计和制造4实验室批准7工装样件生产和提交8供应商第四次项目会议16样件批准91012供应商项目第一次会议在供应商选泄的2周内召开SGMW的采购小组应进一步明确:-时间进度的要求-非工装样件和工装样件的要求-PPAP和GP9的要求供应商在会议上应提供:-供应商APQP横向协调小组名单-APQP时间进度表及未决问题淸单-初始的PFD/PFMEA/PCP-分供方管理计划-售后质量问题降低计划12零件开发和批准流程供应商第二次项目会议生产设计发放供应商选定会议技术规范分析(TSA)供应商第三次项目会议生产件批准生产试运行GP12初期生产控制供应商第一次项目会议125611121315工装设计发放3GP9按报价节拍生产14供应商工装设计和制造4实验室批准7工装样件生产和提交8供应商第四次项目会议16样件批准91012工装设计发放和设计/制造工装:包括模具、夹具和检具非正式工装样件-手工/简易/非完全工装/快速样件-用于验证外观、装配和配合尺寸工装设计发放-用于开发工装的设计规范的确认-T1/T2设计发放工装的设计和制造-制定工装设计和制造的时间进度计划-明确OTS交样的要求和零件检测要求12零件开发和批准流程供应商第二次项目会议生产设计发放供应商选定会议技术规范分析(TSA)供应商第三次项目会议生产件批准生产试运行GP12初期生产控制供应商第一次项目会议125611121315工装设计发放3GP9按报价节拍生产14供应商工装设计和制造4实验室批准7工装样件生产和提交8供应商第四次项目会议16样件批准91012技术规范分析TSA图纸的理解工程规范和标准的确认和理解顾客要求的确认特殊特性的确认材料和分供方淸单零件试制和试验计划12零件开发和批准流程供应商第二次项目会议生产设计发放供应商选定会议技术规范分析(TSA)供应商第三次项目会议生产件批准生产试运行GP12初期生产控制供应商第一次项目会议125611121315工装设计发放3GP9按报价节柏生产14供应商工装设计和制造4实验室批准7工装样件生产和提交8供应商第四次项目会议16样件批准91012生产计划生产开始发运控制-一级发运控制-二级高级改进会议全球采购问题解决(PR/R)质量表现监控潜在供应商评审生产前会议样件批准按报价节拍生产初期生产控制生产件批准程序先期产品质量策划采购决定生产前会议12生产前会议项目时间进度讣划的跟踪和问题的解决OTS提交计划和要求OTS尺寸测量和材料/性能试验计划的确认和批准-OTS零件尺寸检测方法的确认-SGMWPE工程师批准-SGMWSQ工程师和供应商签字确认FE功能评估计划和要求12零件开发和批准流程供应商第二次项目会议生产设计发放供应商选定会议技术规范分析(TSA)供应商第三次项目会议生产件批准生产试运行GP12初期生产控制供应商第一次项目会议1256111312 1315工装设计发放3GP9按报价节拍生产14供应商工装设讣和制造4实验室批准7工装样件生产和提交8供应商第四次项目会议16样件批准9 1012实验室批准和工装样件生产/提交实验室批准-所有试验的地点和设施必须得到SGMW SQ工程师的批准工装样件OTS生产-必须使用生产用模具和生产用夹具-检具按照OTS尺寸测量计划中确定的测量工具/方法工装样件OTS提交按照SGMW的OTS程序要求提交(数量、交付地点、时间、标签要求等) -材料报告、试验报告、尺寸测量报告、-提交前供应商有责任确认满足SGMW的所有要求-零件提交以及检验/测屋报告提交-提交前需得到SGMW PE工程师和SQ工程师的批准12工装样件定义12供应商第二次项目会议生产设计发放供应商选立会议技术规范分析(TSA)供应商第三次项目会议生产件批准生产试运行GP12初期生产控制供应商第一次项目会议125611121315工装设计发放3GP9按报价节拍生产14供应商工装设讣和制造4实验室批准7工装样件生产和提交8供应商第四次项目会议16样件批准91012供应商第三次项目会议在OTS得到批准之后、准备试生产之前进行项目时间进度计划的跟踪和问题的解决明确PPAP的要求-PPAP授权书-PPAP尺寸测量计划/材料和性能试验计划-PPAP提交等级和生产数量/时间的确认明确GP9按报价节拍生产的要求-GP9的方式和时间计划明确GP12初期生产控制的要求12供应商第二次项目会议生产设计发放供应商选定会议技术规范分析(TSA)供应商第三次项目会议生产件批准生产试运行GP12初期生产控制供应商第一次项目会议1256121315工装设计发放3GP9按报价节拍生产14供应商工装设计和制造4实验室批准7工装样件生产和提交8供应商第四次项目会议16样件批准91012生产计划生产开始持续改进发运控制-一级发运控制-二级高级改进会议全球采购 质量研讨会 问题解决(PR/R) 质量表现监控 潜在供应商评审 生产前会议 样件批准 按报价节舶生产 初期生产控制 生产件批准程序先期产品质量策划采购决定PPAP12PPAP 生产件批准目的:来验证供应商的生产过程具有能力来生产满足顾客要求的产品 适用范围:-新零件-工程更改-工艺过程的更改-分供方的更改-生产场地和生产工装/设备的更换或调整-试验和检测方法的改变-已得到批准但是工装闲置已超过12个月-苴它:此种情况供应商应书而通知顾客代表(SQ 工程师)12PPAP 生产件批准流程批量试生产-供应商按照实现的计划完成试生产的准备工作-1-8小时的生产,最低连续生产数量为300件,除非得到SQ 工程师的书而 -在正式生产场地,使用正式生产条件的工装、工艺、检具、材料和操作者 -每个单独的生产过程,如多个相同的生产线/操作工位、一模多腔的不同 等均应进行零件的检查和试验 -按照得到批准的控制计划进行试生产零件的测量和试验-按照PPAP 授权时顾客批准的零件测量和试验计划进行,所有图纸和工程 要求中的性能试验均应进行-每个单独生产过程的零件均应进行测量和试验-供应商保留上述测量和试验记录-检测和试验报告中无数据,只有“合格”、“符合”字样是不可接受的12PPAP 生产件批准流程初始过程能力分析-对每个特殊特性均要求进行初始过程能力分析且结果满足顾客要求 过程能力指数>1.67 =过程满足顾客要求1.33 <过程能力指数< 1.67之间=可接受,但是需要改进并得到顾客认可 过程能力指数&t; 1.33 =不可接受 批准位置规范-初始过程能力分析只能在过程稳立且正常的条件下进行测量系统分析MSA-了解测量系统变差的来源以及这些来源对测量结果的影响-测量系统分析不应仅在PPAP阶段进行,而应该在控制计划中左期规左-R&R分析结果:特殊特性必须小于10%, 10%-30%Z间需改进测量系统变差的类型(测量系统的组成)测量数据相对于参考值或标准值位置的特性:偏移稳迫性线性关于测疑数据分布范囤的特性:重复性再现性12PPAP生产件批准流程PPAP提交类型:等级1—只提交保证书(对指宦的外观项目,还应提供一份外观批准报告)等级2—提交保证书、样件、图纸、尺寸检验报告、台架和功能试验报告、外观批准报告等级3—到顾客所在地,除等级2要求内容外,过程能力结果、能力分析、过程控制计划、测量系统分析报告、FMEA等级4—同等级3,但是不包括零件等级5—在供应商现场,内容同等级3PPAP提交之前必须得到SQ工程师的批准SGMW可要求提交分供方2-3件样件所有提交的样件必须有标签,注明零件号码、名称、生产日期等信息PPAP零件提交得到批准后的问题的整改和问题零件的处理12供应商第二次项目会议生产设计发放供应商选立会议技术规范分析(TSA)供应商第三次项目会议生产件批准生产试运行GP12初期生产控制供应商第一次项目会议25611121315工装设计发放GP9按报价节拍生产14供应商工装设计和制造4实验室批准7工装样件生产和提交8供应商第四次项目会议16样件批准91012生产计划生产开始持续改进发运控制-一级发运控制-二级髙级改进会议全球采购质量研讨会问题解决(PR/R) 质量表现监控潜在供应商评审生产前会议样件批准按报价节拍生产初期生产控制生产件批准程序先期产品质量策划采购决定GP9按报价节拍生产12GP9按报价节拍生产验证供应商生产过程是否有能力按照报价肖拍生产满足质量要求的产品目的是在批量生产开始和加速阶段事先降低问题发生的风险所有新零件均应进行GP9•除非得到SQ经理的批准流程:-项目启动时由供应商完成供应商基本信息调查-第二次项目会议时由SQ工程师确认GP9的方式:顾客还是供应商监控-供应商监控的由供应商按照事先计划日期自行完成并提交报告-顾客监控的由SQ工程师到供应商现场监督整个生产过程并完成报告-SQ经理对GP9的批准GP9与现场生产能力分析与改进供应商第二次项目会议生产设计发放供应商选左会议技术规范分析(TSA)供应商第三次项目会议生产件批准生产试运行GP12初期生产控制供应商第一次项目会议125611121315工装设计发放3GP9按报价节拍生产14供应商工装设计和制造4实验室批准7工装样件生产和提交8供应商第四次项目会议16样件批准91012生产计划生产开始持续改进发运控制-一级发运控制-二级高级改进会议全球采购质量研讨会问题解决(PR/R)质量表现监控潜在供应商评审生产前会议样件批准按报价节舶生产初期生产控制生产件批准程序先期产品质量策划采购决能GP12初期生产控制12GP12初期生产控制GP12初期生产控制是对PPAP控制讣划的补充支持供应商来验证过程的控制,以便在供应商现场能迅速发现和纠正问题,而不是在顾客所在地供应商需按照GP12控制讣划对每批生产的零件进行检测和试验SGMWSQI程师可能采取以下方式进行验证: -到现场监督生产过程和检测/试验过程 -要求供应商随每批发货提供以上记录 -安排第三方检测或试验12新产品投放质量保证流程12新产品投放质量要求紧迫感整车质量很大程度上取决于投放时的质量有效的配合暴需问题不要隐藏问题有力的跟踪必须有力的跟踪所有零件质量问题零件准备状态满足质量要求及时交付生产系统准备状态生产系统、质量系统、分供方系统项目管理层核心小组问题解决小组工厂问题小组12新产品投放质量保证成立专门新产品投放小组特殊行动小组投放阶段问题升级流程WW P高层供应商访问日边界样件批准过程控制计划审核生产能力确认发运控制策略和实施GP12审核问题解决流程二级发运控制12生产计划生产开始GPS持续改进发运控制-一级发运控制-二级高级改进会议全球采购质量研讨会问题解决(PR/R)质量表现监控潜在供应商评审生产前会议样件批准按报价节舶生产初期生产控制生产件批准程序先期产品质量策划采购决定GP8持续不断改进12GP8持续不断改进供应商在获得PPAP批准和GP12完成之后,有责任持续不断的改进质量目的是继续降低制造过程中的变差以提髙产品的质量供应商应建立跟踪流程来跟踪所有厂内和顾客反馈的问题即使顾客没有要求供应商也应进行的工作RPN的持续不断降低PPM的持续不断降低124.快速响应问题的最初反应5.不合格产品的控制(标识)6.风险(RPN)降低是否确左存在的风险?是否应用了防错?7.标准操作者培训操作者是否得到培训?&标准化作业操作者是否遵循标准化作业?9.分级检査不同层次的管理者是否进行检査?10.防错验证防错是否得到验证?顾客接受检查和评审C.A.R.E.是否具有C.A.R.E.?(100%检查髙风险项目)13.总结经验教训质量关键策略增加成功的机会,降低错误发生不合格品控制2.工厂生产会议每日生产会议1.管理层的质量管理活动泄期质疑管理会议。
上汽五菱汽车股份有限公司质量管理体系程序文件

上汽五菱汽车股份有限公司质量管理体系程序文件上汽通用五菱汽车股份有限公司质量管理体系程序文件SGMW Quality Management System ProcedureQP/SGMW 8。
5。
06-2005版本号Version#:A产品安全管理程序Product Safety Management Procedure2005—12-27发布 2005-12—30实施Issued on December27,2005 Implemented on December30,2005上汽通用五菱汽车股份有限公司发布Issued by SAIC GM Wuling Automobile Co。
Ltd前言Foreword本文件是上汽通用五菱汽车股份有限公司《质量手册》章节8。
5的支持性文件,目的在于通过对公司产品质量问题进行评估及产品追溯系统、问题预警系统的建设和维护,以确保产品安全问题得以快速、有效的解决和处理, 并满足国家关于缺陷汽车产品召回管理规定的要求.The procedure is the supporting file of SGMW “Qua lity Manual" Chapter 8.5 It is intended to ensure that the product safety issues are resolved fast and effectively and meet therequirements of national recall management regulations on defect automotive products, throughthe evaluations on the product quality issues as well as the development and maintenance of theproduct traceability system and pre—alarm system.本程序由上汽通用五菱汽车股份有限公司提出.This is put forward by SGMW。
GM供应商质量改进16步过程方法培训

GM供应商质量改进16步过程方法培训主题:通用供应商质量改进的16步过程方法(GM16)16步过程方法是通用全球选择供应商的一种战略方法,包含质量策划、质量设计、质量治理与保持、连续改善等内容。
GM16包含所有现行的通用程序,用于治理供应商产品质量,购买满足设计寿命和使用寿命的零部件。
以上为通用的供应商质量改进的16步程序方法。
其中前面8步是产品投产前应该解决的咨询题,后面8步是产品在使用过程中显现的相关咨询题的解决措施。
第二步:供应商选择1,对象:WWP定点委员会举荐和评估的对象。
2,缘故:基于质量、服务、成本和技术方面的降低风险;3,文件出处:通用全球采购(2);4,定义:定点委员会举荐的对象;5,目的:判定在质量、服务和价格方面有竞争力的产品供应商;6,范畴:全球;7,过程:审核举荐对象;评估候选对象;批准/否定举荐对象;假如需要,批准正确的行动方案;签署定点文件。
第三步:前期产品质量策划与操纵(APQP)1, 对象:APQP是在质量、最优化生产和最大顾客中意度的一种17时期的设计过程;2,缘故:提供给供应商一种质量策划和完成的途径。
整合资源满足通用要求及降低成本。
确保项目进度,便于协商沟通。
3,文件出处:GM采购部。
4,备注:关于所有新的供应商,APQP必须。
相关文件见GM1927P相关表式。
5,含义:一种正式的有组织的方法用于定义和建立必要的过程来确保产品满足客户要求。
6,目的:该过程要求供应商建立和完成产品质量打算来:指导供应商满足客户需要;当必要的改变时促进早期识不;确保所有需要的步骤及时完成;便于沟通要求;以有竞争力的成本及时提供合乎质量要求的产品。
7,范畴:所有GM的供应商都要求完成所有新零件的APQP。
8,过程:策划和定义项目;产品设计与开发;流程设计与开发;产品与流程的确认;质量;产能;进度。
第五步:样件认可(GP-11)1,对象:GP-11是一种常用的样件或前样件的认可要求程序。
上汽五菱:供应商质量管理16步程序

交流以对质量,生产能力和进度等要求进行研讨并取得认同。
样件审批或工装样品(OTS)认可(GP—11)
样件审批 定义: 上汽通用五菱汽车股分有限公司规定的样件审批规程。 目的: 提供上汽通用五菱汽车股分有限公司统一的对样件及其附带文件的最低要 求,协助识别并纠正部件上的问题以减少部件差异,评估设计、制造和装 配可能产生的影响,加速“正式生产件审批”程序的执行。 范围: 适用于需提供新样件的所有供应商。 程序:-由客户提供对样件的检验清单 -供应商得到有关提供样件要求的通知 -供应商得到GP-11中提出的要求 -供应商提交样件和按客户要求等级提供文件 -供应商会得到提交样件审理结果的通知: ―批准用于样车制造 ―可用于样车制造 ―不可用于样车制造
程序:采用根据QS9000制定的潜在供应商评审文件形式。 必须在选定供应商之前完成。
选定供应商—JPC会议
定义: 联合采购委员会批准合格厂商的程序。 目的: 选定在质量、服务及价格方面都具有竞争力的供应 商来提供产品。 范围: 全球范围内的供应商。 程序: 由上汽通用五菱的供应商开发及供应商质量部门来: -审核潜在供应商评审结果 -评估各候选供货来源 -批准或否决建议 -在必要的情形下批准整改计划 -签署决议文本
SAIC GM WL
国内最强、国际上一流的汽车企业。
OHT 0-1
* 2010年在微车和小型车年产30—40万辆。 * 从生产资料型微车向乘用型的微车和其他小型车发展。
面对机遇和挑战 供应商朋友,您做好准备了吗?
OHT 0-1
供应商质量管理16步程序
——供应商质量培训课程
上汽通用五菱采购部 供应商开发/质量室 OHT 0-1
通用汽车公司的供应商评估报告

三、范围: 建议对所有需要进行PPAP的新部件或新材料行使本
程序,依照其风险程度之不同来确定先后(这是前期 质量规划的一部分)
五、投产前会议(续)
四、程序 通过供应商与客户有关人员在产品开发小组会议上进 行密切交流对以下方面的要求进行研讨并取得认同:
一、初级评估(续)
四、程序: a、通用汽车公司的采购人员,经理或工程师进行现场 评估 ---质量方面有12个要素 ---技术方面有7个要素 ---管理方面有6个要素 b、供应商自我评估只能在通用汽车公司的要求下进行 所有要素与现场评估的要素一致。 评分体系用以确定供应商是否有资格至少能进行潜 在供应商评估。
七、正式生产件审批程序
一、定义: 关于正式生产件得以审批的一般产业程序。
二、目的: 验证某供应商的生产工艺是否具备生产满足客户要求 的产品的潜能。
三、范围: 在新产品投产前,或当现有产品在技术、工艺上有改 动,或供应商情况发生变化,都必须通过此“正式生 产件审批”程序
四、程序 供应商严格按照正式生产件审批程序(PPAP)中规
二、潜在供应商评估
一、定义: 现场评估供应商是否能达到对管理体系的最基本要求
二、目的: 进行为期一至二天的评估以验证新的潜在供应商是否 有能力达到与上汽通用五菱公司开展业务的最基本要求
三、范围: 在推荐某一供应商来开拓新的业务之前,如果该供应商 未具备QS-9000认证,并且在以下任一状况成立的情形 下,必须进行潜在供应商评审:
一、初级评估
一、定义: 在进行潜在供应商评估之前,对新的潜在的供应商做
一个初步的现场评估,或让供应商自我评估以确定供 应商是否具有基本的质量体系,合适的技术能力和良 好的管理水平。 二、目的:
供应商质量培训课程 -供应商质量管理16步程序
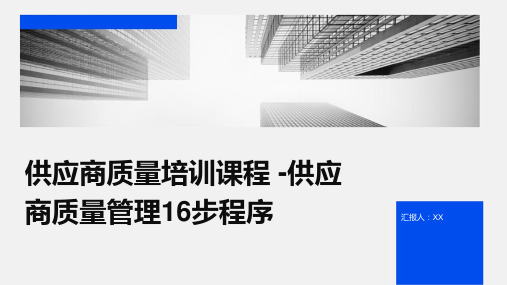
商质量管理16步程序
汇报人:XX
目录
• 引言 • 供应商选择与评估 • 供应商质量协议与合同 • 供应商过程监控 • 供应商质量改进 • 供应商审核与认证 • 供应商关系管理 • 总结与展望
01
引言
课程目的和背景
应对全球化采购挑战
随着全球化的发展,企业越来越多地 依赖外部供应商,供应商质量管理成 为确保产品质量和竞争优势的关键因 素。
04
供应商过程监控
过程监控的目的和内容
目的:确保供应商在生产过程中遵循质 量标准,及时发现并纠正潜在问题,以 确保最终产品符合质量要求。
跟踪供应商的质量绩效,包括产品合格 率、不良品率、客户投诉等。
评估供应商的质量管理体系,确保其有 效性和符合性。
内容
监控供应商的生产过程,包括原材料采 购、生产工艺、设备维护等。
产品。
降低质量成本
通过预防、鉴定和减少不合格 品,降低因质量问题引起的成 本增加,包括返工、退货、保 修等。
提升客户满意度
优质的产品有助于提高客户满 意度和忠诚度,进而促进业务 增长和市场份额提升。
强化供应链韧性
优质的供应商能够更好地应对 市场波动和不确定性,提高供
应链的稳定性和韧性。
02
供应商选择与评估
对企业的建议与启示
建立完善的供应商质量管理体系
企业应建立全面、系统的供应商质量管理体系,明确管理流程和责任 分工,确保供应商质量管理的有效实施。
加强供应商选择与评估
在选择供应商时,应注重其质量保障能力、技术实力、服务水平等方 面的评估,确保选择优质的供应商合作伙伴。
强化供应商培训与辅导
定期对供应商进行质量意识、技能等方面的培训与辅导,提高供应商 的整体素质和能力水平。
供应商管理16步

通用汽车公司潜在供应商评审流程
采购者提交潜在供应商
采购质量进行预评审 (If Need)
Purchase Dept. Base on Supplier's QE & Engineering Dept. Information do Risk Analysis
Register 注册QS9000?
ACTION 反馈、评审和改进行动
1.0 PLAN AND DEFINE PROGRAM 计划和确定项目
DESIGN GOALS 设计目标 RELIABILITY AND QUALITY GOALS 可靠性和质量目标 PRELIMINARY BILL OF MATERIAL 初始材料清单 PRELIMINARY PROCESS FLOW CHART 初始过程流程图 PRELIMINARY LISTING OF SPECIAL PRODUCT AND PROCESS CHARACTERISTICS 关键产品和关键过程特性初始清单 PRODUCT ASSURANCE PLAN 产品保证计划
是 Yes
否 No
是Yes
High Risk ?
否 No
Register 注册QS9000?
是 Yes
Supplier Engineering Capability Assessment
Supplier Engineering Capability Assessment &
Potential Supplier Assessment
1 级控制发货 CONTROLLED SHIPPING 1
问题报告 /解决 PROBLEM REPORT/RESOLUTION
供应商表现监控 PERFORMANCE MONITORING
- 1、下载文档前请自行甄别文档内容的完整性,平台不提供额外的编辑、内容补充、找答案等附加服务。
- 2、"仅部分预览"的文档,不可在线预览部分如存在完整性等问题,可反馈申请退款(可完整预览的文档不适用该条件!)。
- 3、如文档侵犯您的权益,请联系客服反馈,我们会尽快为您处理(人工客服工作时间:9:00-18:30)。
初期生产次品遏制程序(GP—12) 初期生产次品遏制程序(GP—12)
定义: 供应商正式生产件审批程序控制计划的加强措施, 定义 供应商正式生产件审批程序控制计划的加强措施,初期生产次 品遏制计划( 品遏制计划(GP-12)与产品先期质量策划及控制计划参考手 ) 册中的投产前控制计划是一致的。 册中的投产前控制计划是一致的。 目的: 帮助供应商验证对其工序的控制, 目的 帮助供应商验证对其工序的控制,使质量问题能迅速在供应商 现场被发现和纠正,而不影响到客户的生产线。 现场被发现和纠正,而不影响到客户的生产线。 范围:本程序适用于所有需要通过正式生产件审批程序的零件, 范围:本程序适用于所有需要通过正式生产件审批程序的零件,包括 所有小批量供货,加上采购部门指定的数量。 所有小批量供货,加上采购部门指定的数量。此程序不只限项 目的开始。 目的开始。 程序:作为质量先期策划之组成部分,供应商将制定 程序:作为质量先期策划之组成部分,供应商将制定GP-12投产前控 投产前控 制计划, 控制计划是PPAP正式生产件审批程序的要求 制计划,GP-12控制计划是 控制计划是 正式生产件审批程序的要求 之一,在达到此阶段放行标准之前必须按该计划执行。 之一,在达到此阶段放行标准之前必须按该计划执行。
投产前会议
定义:与供应商进行交流以明确零件质量合格及持续改进的要求。 定义:与供应商进行交流以明确零件质量合格及持续改进的要求。 目的: 目的:保证所有质量要求在供应商及客户负责供应商的部门之间得到 确切的交流。 确切的交流。 范围:建议对所有需要进行PPAP的新部件或新材料行使本程序,依 的新部件或新材料行使本程序, 范围:建议对所有需要进行 的新部件或新材料行使本程序 照其风险程度之不同来确定先后。 照其风险程度之不同来确定先后。(这是先期质量策划的一个部 分) 程序: 程序:通过供应商与客户有关人员在产品开发小组会议上进行密切的 交流以对质量,生产能力和进度等要求进行研讨并取得认同。 交流以对质量,生产能力和进度等要求进行研讨并取得认同。
生产件批准程序PPAP 生产件批准程序PPAP
定义: 关于正式生产件得以审批的一般产业程序。 定义 关于正式生产件得以审批的一般产业程序。 目的: 目的 验证某供应商的生产过程是否具备生产满足客户要求的产 品的潜能。 品的潜能。 范围:在新产品投产前,或当现有产品在技术、工艺上有改动或供 范围:在新产品投产前,或当现有产品在技术、 应商情况发生变化,都必须通过此“正式生产件审批” 应商情况发生变化,都必须通过此“正式生产件审批”程序 程序:供应商严格按照正式生产件审批程序( 程序:供应商严格按照正式生产件审批程序(PPAP)中规定的各项 ) 要求执行。 要求执行。
样件审批或工装样品(OTS)认可(GP—11) 样件审批或工装样品(OTS)认可(GP—11)
样件审批 定义: 上汽通用五菱汽车股分有限公司规定的样件审批规程。 定义 上汽通用五菱汽车股分有限公司规定的样件审批规程。 目的: 目的 提供上汽通用五菱汽车股分有限公司统一的对样件及其附带文件的最低要 协助识别并纠正部件上的问题以减少部件差异,评估设计、 求,协助识别并纠正部件上的问题以减少部件差异,评估设计、制造和装 配可能产生的影响,加速“正式生产件审批”程序的执行。 配可能产生的影响,加速“正式生产件审批”程序的执行。 范围: 适用于需提供新样件的所有供应商。 范围 适用于需提供新样件的所有供应商。 程序: 由客户提供对样件的检验清单 程序:-由客户提供对样件的检验清单 -供应商得到有关提供样件要求的通知 供应商得到有关提供样件要求的通知 -供应商得到 供应商得到GP-11中提出的要求 供应商得到 中提出的要求 -供应商提交样件和按客户要求等级提供文件 供应商提交样件和按客户要求等级提供文件 -供应商会得到提交样件审理结果的通知: 供应商会得到提交样件审理结果的通知: 供应商会得到提交样件审理结果的通知 ―批准用于样车制造 批准用于样车制造 ―可用于样车制造 可用于样车制造 ―不可用于样车制造 不可用于样车制造
时间线
零件寿命
产品开始
上汽通用五菱
OHT 0-1
ห้องสมุดไป่ตู้ 景: SAIC WL
1 引入世界上先进的经营理念和管理系统。 引入世界上先进的经营理念和管理系统。
2 培育适应全球经济一体化进程的企业文化。 培育适应全球经济一体化进程的企业文化。 3 有能力、有特点和合作精神的员工。 有能力、有特点和合作精神的员工。 4 以客户为导向,造百姓喜爱的车。 以客户为导向,造百姓喜爱的车。 5 打造在微车领域国内领先、国际有竞争力的汽车公司。 打造在微车领域国内领先、国际有竞争力的汽车公司。
选定供应商—JPC会议 选定供应商—JPC会议
定义: 联合采购委员会批准合格厂商的程序。 定义 联合采购委员会批准合格厂商的程序。 目的: 选定在质量、 目的 选定在质量、服务及价格方面都具有竞争力的供应 商来提供产品。 商来提供产品。 范围: 全球范围内的供应商。 范围 全球范围内的供应商。 程序: 由上汽通用五菱的供应商开发及供应商质量部门来: 程序 由上汽通用五菱的供应商开发及供应商质量部门来: -审核潜在供应商评审结果 审核潜在供应商评审结果 -评估各候选供货来源 评估各候选供货来源 -批准或否决建议 批准或否决建议 -在必要的情形下批准整改计划 在必要的情形下批准整改计划 -签署决议文本 签署决议文本
SAIC GM WL
国内最强、国际上一流的汽车企业。 国内最强、国际上一流的汽车企业。
OHT 0-1
* 2010年在微车和小型车年产30—40万辆。 2010年在微车和小型车年产 —40万辆 年在微车和小型车年产30 万辆。 * 从生产资料型微车向乘用型的微车和其他小型车发展。 从生产资料型微车向乘用型的微车和其他小型车发展。
潜在供应商评估(PSA) 潜在供应商评估(PSA)
定义: 现场评估供应商是否能达到对管理体系的最基本要求。 定义 现场评估供应商是否能达到对管理体系的最基本要求。 目的: 目的 进行为期一至二天的评估以验证新的潜在供应商是否有能力达 到与上汽通用五菱汽车股分有限公司开展业务的最基本要求。 到与上汽通用五菱汽车股分有限公司开展业务的最基本要求。 范围: 在推荐某一供应商来开拓新的业务之前,如果该供应商未具备 范围 在推荐某一供应商来开拓新的业务之前, QS9000认证,并且在以下任一状态成立的情形之下,必须进 认证, 认证 并且在以下任一状态成立的情形之下, 行潜在供应商评审: 行潜在供应商评审: 1. 潜在供应商的制造场所不是上汽通用五菱的现有供货源。 . 潜在供应商的制造场所不是上汽通用五菱的现有供货源。 2. 该项技术 零部件对此供应商的制造场所而言是全新的。 . 该项技术/ 零部件对此供应商的制造场所而言是全新的。 此外,当采购部门认为具有较高风险时,也将进行潜在供应商评审。 此外,当采购部门认为具有较高风险时,也将进行潜在供应商评审。 程序:采用根据 制定的潜在供应商评审文件形式。 程序:采用根据QS9000制定的潜在供应商评审文件形式。 制定的潜在供应商评审文件形式 必须在选定供应商之前完成。 必须在选定供应商之前完成。
面对机遇和挑战 供应商朋友,您做好准备了吗? 供应商朋友,您做好准备了吗?
OHT 0-1
供应商质量管理16步程序 供应商质量管理16步程序
——供应商质量培训课程 供应商质量培训课程
上汽通用五菱采购部 供应商开发/ 供应商开发/质量室 OHT 0-1
初级评估(PA / TA) TA) 初级评估(
定义:在潜在供应商评估之前,对新的潜在供应商作一个初步评估, 定义:在潜在供应商评估之前,对新的潜在供应商作一个初步评估,或 让供应商自我评估以确定其是否具备基本的质量体系、 让供应商自我评估以确定其是否具备基本的质量体系、合适的技 术能力和良好的管理水平。 术能力和良好的管理水平。 目的: 目的:通过半天的评估以确认新的潜在供应商是否有资格进行潜在供应 商评估。 商评估。 范围:适用于所有被认作是潜在来源的新的供应商。 范围:适用于所有被认作是潜在来源的新的供应商。 程序: 采购员、 程序:A 采购员、经理或工程师进行现场评估 ——质量方面有 个要素 质量方面有12个要素 质量方面有 ——技术方面有 个要素 技术方面有7个要素 技术方面有 ——管理方面有 个要素 管理方面有6个要素 管理方面有 B 供应商自我评估(只能在客户的要求下进行,所有要素与现场 供应商自我评估(只能在客户的要求下进行, 评估的要素一致。 评估的要素一致。 评分体系用以确定新的潜在供应商是否有资格进行潜在供应商评估。 评分体系用以确定新的潜在供应商是否有资格进行潜在供应商评估。 任务: 任务:确定供应商是否有资格进行潜在供应商评估
先期产品质量策划APQP和控制计划 先期产品质量策划APQP和控制计划
定义: 为确保产品能满足客户的要求而建立一套完整的质量计划。 定义 为确保产品能满足客户的要求而建立一套完整的质量计划。 目的: 此程序要求供应商开发并实施产品质量计划: 目的 此程序要求供应商开发并实施产品质量计划: -利用资源,满足客户要求 利用资源, 利用资源 -尽早发现所需的更改 尽早发现所需的更改 -保证全部必要步骤按期完成 保证全部必要步骤按期完成 -促进双方信息交流 促进双方信息交流 -以具有竞争性的价格按时提供合格产品 以具有竞争性的价格按时提供合格产品 范围: 范围 所有为上汽五菱供货的供应商都必须针对每一个新零部件执行 产品质量先期策划和控制计划” “产品质量先期策划和控制计划”程序 程序: 根据客户的要求和意见,按以下各阶段进行: 程序 根据客户的要求和意见,按以下各阶段进行: -计划并制定项目 计划并制定项目 -产品设计与开发 产品设计与开发 -工艺设计与开发 工艺设计与开发 -产品及工艺验证 产品及工艺验证 -反馈,评估及整改措 反馈, 反馈
通 向 成 功 的16步 ! 步
全球采购 质量改进会 质量研讨会 二级发货控制 一级发货控制 问题通报与解决GP-5 问题通报与解决 成效监控 持续改进GP-8 持续改进 按预定能力运行GP-9 按预定能力运行 初期生产次品遏制GP-12 初期生产次品遏制 生产件审准PPAP 生产件审准 正式工装样件OTS审批 审批GP-11 正式工装样件 审批 投产前会议 产品质量先期策划和控制计划 确定供应商 潜在供应商评估PSA 潜在供应商评估 初级评估PA 初级评估