{设备管理}设备使用管理维护管理与维修管理
设备管理及维护制度

设备管理及维护制度简介设备管理及维护制度是企业内部规定设备管理和维护的标准和流程,旨在保障企业设备安全、高效运转,延长设备使用寿命,降低维修成本,提高企业生产力和经济效益。
设备管理管理职责设备管理要明确职责分工,确定设备使用、保管、维护和维修等职责。
企业设备管理人员要认真履行职责,确保平稳、高效的设备运行。
购置和验收企业购置设备时,应制定统一的设备采购标准,进行严格的验收,确保设备符合国家、安全标准和企业的需要。
验收合格后,设备管理人员应开立设备档案,记录设备的型号、来源、价格、保修期、供应商、使用日期等相关信息。
同时,财务部门要将设备纳入固定资产管理中,定期更新设备信息。
使用和保管设备管理人员要确保设备的正常使用和保管,制定设备使用标准,规定设备使用场所、使用方法、操作注意事项等,确保设备使用安全,避免人为损坏和设备故障。
同时,设备管理人员要负责设备的保管,定期检查设备的保存状态,确保设备干净整洁,防止设备遭受损坏和盗窃。
设备管理人员要对设备进行保养和维护,定期对设备进行检查、维修和清洁,确保设备的良好使用状态。
备件管理备件管理是设备管理的重要组成部分。
备件管理人员要确定标准备件、常常备件和必备备件等备件种类和数量,确保备件充足,能够及时替换和维修设备。
备件管理人员要根据设备档案,建立设备备件清单,进行分类管理,定期更新备件资料,及时处理备件报废和更新问题。
设备维护维护制度设备维护是保障设备正常运转的一项重要工作。
设备管理人员要制定设备维护制度,对设备进行分类管理,确定维护周期和维护方式,确保设备的良好使用状态。
维护流程设备维护流程包括设备维护申请、维护部门审核、维护计划制定、维护执行和维护记录等环节。
设备管理人员要确保维护流程严格执行,对设备进行及时、科学的维修,防止因维护不及时而影响设备正常运转。
维护标准设备管理人员要根据设备的使用情况和使用需求,制定科学合理的设备维护标准,包括保养、清洗、检测和更换配件等内容。
设备使用和维护保养管理规定
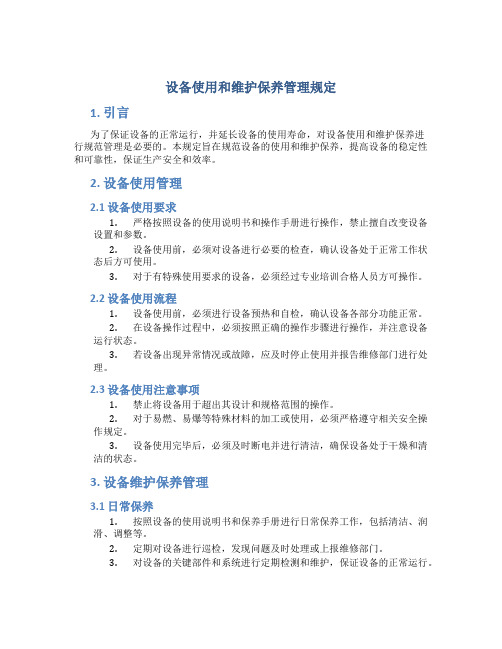
设备使用和维护保养管理规定1. 引言为了保证设备的正常运行,并延长设备的使用寿命,对设备使用和维护保养进行规范管理是必要的。
本规定旨在规范设备的使用和维护保养,提高设备的稳定性和可靠性,保证生产安全和效率。
2. 设备使用管理2.1 设备使用要求1.严格按照设备的使用说明书和操作手册进行操作,禁止擅自改变设备设置和参数。
2.设备使用前,必须对设备进行必要的检查,确认设备处于正常工作状态后方可使用。
3.对于有特殊使用要求的设备,必须经过专业培训合格人员方可操作。
2.2 设备使用流程1.设备使用前,必须进行设备预热和自检,确认设备各部分功能正常。
2.在设备操作过程中,必须按照正确的操作步骤进行操作,并注意设备运行状态。
3.若设备出现异常情况或故障,应及时停止使用并报告维修部门进行处理。
2.3 设备使用注意事项1.禁止将设备用于超出其设计和规格范围的操作。
2.对于易燃、易爆等特殊材料的加工或使用,必须严格遵守相关安全操作规定。
3.设备使用完毕后,必须及时断电并进行清洁,确保设备处于干燥和清洁的状态。
3. 设备维护保养管理3.1 日常保养1.按照设备的使用说明书和保养手册进行日常保养工作,包括清洁、润滑、调整等。
2.定期对设备进行巡检,发现问题及时处理或上报维修部门。
3.对设备的关键部件和系统进行定期检测和维护,保证设备的正常运行。
3.2 定期保养1.根据设备的使用情况和维护要求,制定定期保养计划,并按计划执行。
2.定期更换设备的易损件和耗材,确保设备的正常运行。
3.定期对设备进行检修和调试,保证设备的性能和稳定性。
3.3 维修管理1.当设备出现故障时,应及时停止使用,并上报维修部门进行处理。
2.维修过程中,必须按照维修规程进行操作,维修完成后进行测试和确认。
3.4 设备报废处理当设备达到使用寿命,或经济效益不再符合要求时,需要进行设备报废。
1.设备报废前,必须进行设备的清理、归档和备份等工作。
2.对于涉及环境保护的设备,必须按照相关法律法规进行处理。
设备使用与维护管理制度范本

设备使用与维护管理制度范本一、概述本制度旨在规范设备的使用与维护管理,确保设备的正常运行和延长设备的使用寿命,保证工作的顺利进行。
二、适用范围本制度适用于公司内部所有设备的使用与维护管理。
三、设备的使用规定1. 使用人员应按照设备的操作手册进行正确操作,熟悉设备的使用方法和注意事项;2. 在使用设备前,应检查设备的电源接头、电源开关等是否正常,确保电源接地可靠;3. 使用设备时应穿戴合适的劳动防护用品,避免因操作不当导致的伤害;4. 设备的操作台面应保持整洁,不得放置杂物,以免影响操作效果;5. 使用设备时,应保持机器周围的环境清洁,并保持通风良好,以防止设备过热;6. 在设备异常情况下,应立即停止使用,并及时通知维修人员进行检修;7. 使用完毕后,应及时关闭设备的电源,清理设备表面的污垢,保持设备整洁。
四、设备的维护管理规定1. 设备维护人员应定期检查设备的各项功能和性能指标,并记录检查结果;2. 设备维护人员应定期清洁设备的内部结构,以确保设备的正常运行;3. 维护人员应及时更换设备的易损件,延长设备的使用寿命;4. 维护人员应定期对设备进行润滑保养,并保持记录;5. 维护人员应定期检查设备的电源接线和电气元件,确保设备的电气安全;6. 维护人员应按照设备的维护计划进行维护和保养工作,并记录维护情况。
五、设备故障处理规定1. 在设备发生故障时,使用人员应立即停止使用,并及时通知维修人员进行处理;2. 维修人员应及时到达故障现场,进行故障诊断和维修;3. 维修人员应按照操作规程进行维修工作,确保设备的正常使用;4. 维修人员应及时向使用人员反馈故障原因和维修结果,并提出设备维护的建议;5. 经常出现故障的设备,应及时进行彻底维修或更换。
六、安全注意事项1. 使用人员应注意设备的周围环境,防止设备与水或其他液体接触,以避免电气事故的发生;2. 在设备运行过程中,严禁用湿手或带有金属饰品的手触摸设备,以防触电事故发生;3. 使用人员应定期参加安全操作培训,并熟悉设备的紧急停止按钮位置;4. 在设备维护过程中,维修人员应使用绝缘工具和穿戴绝缘手套,确保安全;5. 维修人员应随身携带维修工具和安全防护用品,并定期检查其可用性。
设备使用与维护管理办法
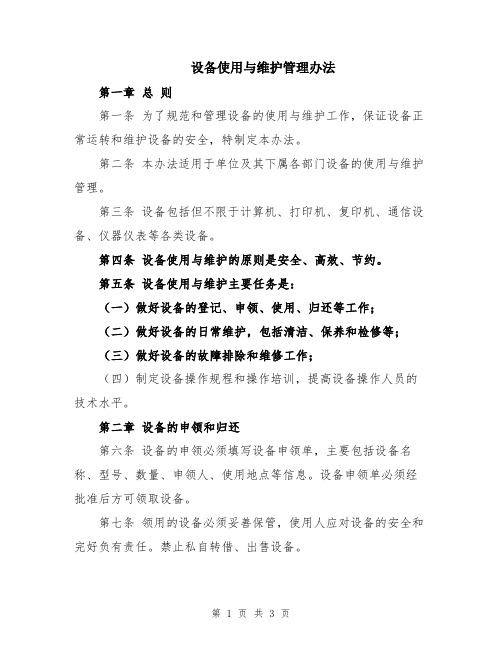
设备使用与维护管理办法第一章总则第一条为了规范和管理设备的使用与维护工作,保证设备正常运转和维护设备的安全,特制定本办法。
第二条本办法适用于单位及其下属各部门设备的使用与维护管理。
第三条设备包括但不限于计算机、打印机、复印机、通信设备、仪器仪表等各类设备。
第四条设备使用与维护的原则是安全、高效、节约。
第五条设备使用与维护主要任务是:(一)做好设备的登记、申领、使用、归还等工作;(二)做好设备的日常维护,包括清洁、保养和检修等;(三)做好设备的故障排除和维修工作;(四)制定设备操作规程和操作培训,提高设备操作人员的技术水平。
第二章设备的申领和归还第六条设备的申领必须填写设备申领单,主要包括设备名称、型号、数量、申领人、使用地点等信息。
设备申领单必须经批准后方可领取设备。
第七条领用的设备必须妥善保管,使用人应对设备的安全和完好负有责任。
禁止私自转借、出售设备。
第八条设备使用期限届满或者不再使用的,应当及时归还,归还时应当做好设备的清理并经过验收。
第三章设备的维护和保养第九条设备的日常维护主要包括清洁、保养和检修等。
第十条设备的清洁应定期进行,清除设备表面的灰尘和污渍,保持设备的整洁,并注意保护设备的屏幕和外壳不受损坏。
第十一条设备的保养应根据设备的使用情况和维修记录进行,定期更换设备的耗材和易损件,保证设备的正常运转。
第十二条设备的检修应根据设备的运行情况和维修记录进行,定期对设备进行全面检查和维护,及时发现和排除设备的故障。
第十三条设备的保养和检修工作必须由经过培训和资格认证的人员来完成,禁止未经授权的人员私自进行维护和修理工作。
第四章设备的故障排除和维修第十四条设备发生故障时,使用人应当及时停止使用,并向设备维修人员报告故障情况,维修人员应迅速排除故障。
第十五条设备维修人员应按照设备的维修规范来进行维修工作,禁止擅自更换设备的内部零部件,必要时可以与设备供应商或厂家联系,协助解决更复杂的故障。
第十六条设备维修完成后,维修人员应当向使用人交代维修情况,并进行设备的测试和验收,确保设备正常运转。
设备管理及维护制度
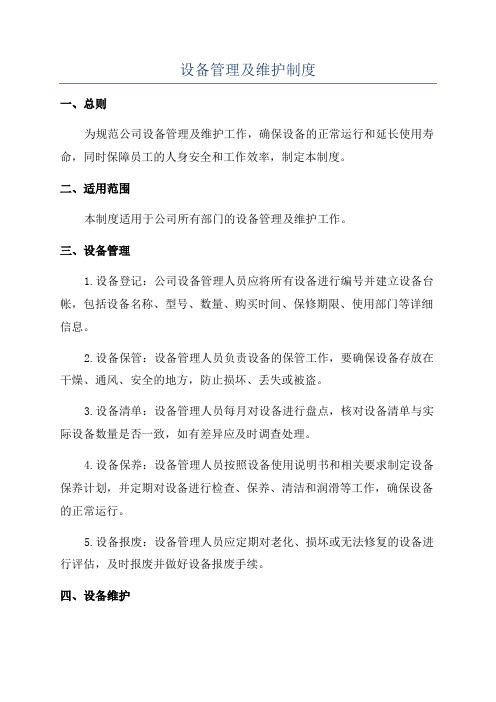
设备管理及维护制度一、总则为规范公司设备管理及维护工作,确保设备的正常运行和延长使用寿命,同时保障员工的人身安全和工作效率,制定本制度。
二、适用范围本制度适用于公司所有部门的设备管理及维护工作。
三、设备管理1.设备登记:公司设备管理人员应将所有设备进行编号并建立设备台帐,包括设备名称、型号、数量、购买时间、保修期限、使用部门等详细信息。
2.设备保管:设备管理人员负责设备的保管工作,要确保设备存放在干燥、通风、安全的地方,防止损坏、丢失或被盗。
3.设备清单:设备管理人员每月对设备进行盘点,核对设备清单与实际设备数量是否一致,如有差异应及时调查处理。
4.设备保养:设备管理人员按照设备使用说明书和相关要求制定设备保养计划,并定期对设备进行检查、保养、清洁和润滑等工作,确保设备的正常运行。
5.设备报废:设备管理人员应定期对老化、损坏或无法修复的设备进行评估,及时报废并做好设备报废手续。
四、设备维护1.设备故障报告:员工在使用设备中发现故障或异常现象应及时向设备管理人员进行报告,设备管理人员应及时处理故障或安排专业人员进行维修。
2.设备维修记录:设备管理人员应建立设备维修记录,对每次设备维修进行详细记录,包括维修日期、维修人员、故障原因、维修措施和费用等信息。
3.设备维修费用核算:设备管理人员应对设备维修费用进行核算,包括维修人员的工时费用、零配件费用等,并将费用纳入公司财务管理范畴。
4.设备维护计划:设备管理人员应根据设备的使用情况和维修记录制定设备维护计划,对设备进行定期维护和检修,以减少设备故障率和提高设备的工作效率。
五、责任分工1.设备管理人员负责设备的登记、保管、清单盘点、保养和报废等工作。
2.员工负责设备的正确使用和定期检查,发现故障及时报告。
3.财务部门负责设备维修费用的核算,信息技术部门负责设备维护计划的制定。
4.公司领导负责对设备管理及维护工作的监督和检查,确保制度的有效执行。
六、违纪处分对违反设备管理及维护制度的员工,将按照公司规定进行相应处分,包括扣工资、停职、辞退等。
设备安全管理和检修、维修制度范本

设备安全管理和检修、维修制度范本一、概述本制度的目的是为了保障设备的安全运行,维护设备的正常使用和延长设备的使用寿命。
本制度适用于公司内部所有设备的安全管理和检修、维修工作。
二、设备安全管理1.设立设备管理部门,负责设备的日常管理、维护和维修工作。
2.制定设备使用管理规定,明确设备的使用范围、使用条件和使用方法,并向相关人员进行培训。
3.建立设备使用台账,记录设备的基本信息、运行情况和维护情况,并定期进行检查和更新。
4.建立设备故障报修制度,及时处理设备故障,确保设备能够正常运行。
5.定期对设备进行检查和维护,发现问题及时修复,确保设备的正常运行。
6.明确设备的保养方法和周期,定期进行设备保养工作,延长设备的使用寿命。
7.建立设备的安全标识,提示相关人员注意设备的安全使用和维护。
三、设备检修制度1.设备检修周期按照设备的使用情况和维护要求进行制定,同时设备检修计划要提前布置,并向相关人员进行通知。
2.设备检修工作必须由经过培训合格的工作人员进行,不得擅自开展检修工作。
3.设备检修前,必须对设备进行停机并断电,并采取必要的安全措施,确保工作人员的人身安全。
4.检修作业过程中,必须按照检修规程进行操作,并及时记录检修情况和发现的问题。
5.设备检修结束后,必须对设备进行试运行和检查,确保设备的安全和正常运行。
四、设备维修制度1.设备维修工作必须由经过培训合格的维修人员进行,不得擅自开展维修工作。
2.维修前,必须对设备进行停机并断电,并采取必要的安全措施,确保维修人员的人身安全。
3.维修过程中,必须按照维修规程进行操作,并及时记录维修情况和使用的材料和工具。
4.维修结束后,必须对设备进行试运行和检查,确保设备的安全和正常运行,并修复维修时发现的问题。
5.对于需要外部维修的设备,必须选择经过认证的维修单位进行维修,并保持相应的维修记录和报告。
五、设备事故处置制度1.设备事故发生后,必须立即停机并断电,并采取必要的安全措施,防止事故进一步扩大。
设备管理及维护制度

设备管理及维护制度1. 引言设备管理及维护制度是为了保障公司设备的正常运行和延长设备的使用寿命,确保生产和工作的顺利进行而制定的。
2. 目的本制度的目的是明确设备管理和维护的责任、义务和流程,提高设备的可靠性和可用性,降低设备故障率,减少生产事故和停工损失。
3. 适用范围本制度适用于公司所有的设备管理和维护工作,包括但不限于生产设备、办公设备、仪器仪表等。
4. 设备管理责任4.1 设备管理部门公司设备管理部门负责全面管理设备,包括设备的购置、调拨、维护、保养等工作。
设备管理部门应制定设备管理计划,并定期进行设备台账和维护记录的更新和审核。
4.2 设备使用部门设备使用部门是设备的直接使用者,负责设备的日常操作和保养工作。
设备使用部门应按照设备管理部门的要求,合理使用设备,定期进行设备的清洁、保养和检查,并及时向设备管理部门报告设备的异常情况。
5. 设备购置和调拨5.1 设备购置设备购置需要经过设备管理部门的审批,并按照公司的采购流程进行采购。
设备购置应根据公司的实际需求和设备的质量要求,选择合适的设备供应商,并签订合同进行购买。
5.2 设备调拨设备调拨需要经过设备管理部门和相关部门的协商和审批,确保设备调拨符合公司的实际需求和部门之间的合作关系。
设备调拨前应清楚设备的使用状态和维护记录,确保设备的可靠性和适用性。
6. 设备维护和保养6.1 设备维护计划设备管理部门应制定设备维护计划,包括定期维护、预防性维护和故障维修等内容。
设备维护计划应根据设备的类型、使用情况和制造商的要求进行制定,并按照计划进行实施。
6.2 设备保养设备使用部门应按照设备管理部门的要求,对设备进行日常保养工作。
设备保养包括设备的清洁、润滑、调整和更换易损件等工作。
设备保养应按照设备维护计划和操作规程进行,并及时记录和上报设备的保养情况。
6.3 故障维修设备故障需要及时维修,保证设备的正常运行。
设备故障维修应由设备管理部门负责,并与设备使用部门进行配合。
设备使用与维护管理制度(3篇)

设备使用与维护管理制度旨在确保企业或组织内部的设备能够安全地运行并使用,并提供维护保养和故障处理的准则和流程。
以下是一个可能的设备使用与维护管理制度的范本:1. 设备管理责任1.1. 设备管理员被指定为设备管理的负责人,并负责设备的日常维护、保养和监管。
1.2. 设备的具体使用责任由使用部门或个人承担。
2. 设备的合理使用2.1. 设备的使用应符合相关的法律法规和企业内部规定,不得用于非法活动。
2.2. 设备的使用应遵守设备的操作手册和使用指南,避免错误操作导致设备损坏或事故。
2.3. 设备的使用时间应合理安排,避免过度使用导致设备损耗加速。
3. 设备维护保养3.1. 设备管理员应按照设备的维护手册或要求,制定设备的定期维护计划,并按计划进行维护保养。
3.2. 设备管理员应定期检查设备的运行情况,及时发现和处理设备的故障或异常情况。
3.3. 设备使用部门或个人在发现设备故障时应及时向设备管理员报告,并配合进行维修。
4. 设备故障处理与维修4.1. 设备管理员应及时响应设备故障报告,并尽快确定故障原因并采取相应的维修措施。
4.2. 设备故障处理过程中应记录故障处理过程和维修结果,并及时向相关部门或个人汇报故障处理情况。
4.3. 严重故障或无法修复的设备应及时报废,并根据相关程序进行报废处理。
5. 设备备份与数据保护5.1. 设备使用部门或个人应定期备份设备中的重要数据,并妥善保管备份数据。
5.2. 设备管理员应定期检查备份数据的完整性和可读性,确保备份数据可以在需要时恢复或使用。
6. 设备报废与更新6.1. 设备管理员应定期评估设备的使用寿命和性能,提前制定设备更新计划,确保设备能够按时更新和替换。
6.2. 设备报废时应按照相关法律法规和企业内部规定进行报废处理,并妥善处理设备中的数据和敏感信息。
以上是一个可能的设备使用与维护管理制度的范本,具体的制度内容和要求可根据实际情况进行调整和完善。
设备使用与维护管理制度(2)第一章总则第一条为规范设备的使用与维护管理行为,提高设备的利用率和工作效率,有效延长设备的使用寿命,制定本制度。
设备管理与维修保养措施

设备管理与维修保养措施设备管理和维修保养措施是保障设备正常运行的关键环节,能够提高设备的使用寿命,降低设备故障率,以及提高设备的生产效率。
以下是一些建议的设备管理和维修保养措施:1.设备清单管理:建立设备清单,包括设备的型号、编号、购置日期、使用寿命等信息,并定期更新。
可以使用电子设备管理系统,使设备的信息更加清晰可见。
2.设备登记和使用规范:制定设备登记制度,确保设备购置、调拨、领用等环节都有明确的流程和记录,防止设备流失和错乱。
同时,制定设备使用规范,明确设备的操作流程、安全注意事项等,提高设备使用效率和安全性。
3.设备保养计划:根据设备的使用寿命和保养要求,制定设备保养计划。
计划包括设备的定期保养和维修保养等内容,可以根据设备的不同部位和重要性,设置不同的保养周期和要求。
4.设备保养记录:设备保养过程中,要及时记录设备的保养情况,包括保养的内容、时间、保养人员等。
可以使用设备保养表格或电子记录系统,方便查阅和管理。
5.设备故障处理:制定设备故障处理流程,包括故障报修、检修和维修等环节。
及时处理设备故障,可以避免故障扩大和影响生产。
6.设备定期检查:对设备进行定期检查,包括设备的外观、传动系统、电气系统等。
及时发现设备的潜在故障,采取预防性维护措施,防止设备因故障而停机。
7.设备培训和技术支持:对设备使用人员进行培训,使其熟悉设备的操作流程、维护要点等。
并提供专业的技术支持,解答设备使用中的问题,提高设备的使用效率和安全性。
8.备品备件管理:建立备品备件的管理制度,包括备品备件的采购、库存和使用等。
根据设备的使用情况和保养计划,合理配置备品备件,确保设备故障时能够及时更换和修复。
9.设备更新和淘汰:根据设备的使用寿命和技术要求,及时更新设备或淘汰老化设备。
定期评估设备的使用状态和性能,制定设备更新和淘汰计划,提高设备的生产效率和质量。
以上是一些设备管理和维修保养的措施,通过有效的设备管理和维修保养措施,可以确保设备的正常运行,提高设备的使用寿命和生产效率,降低设备故障率,为企业的发展和生产提供良好的保障。
设备日常维护管理制度 设备管理与维护制度

设备日常维护管理制度设备管理与维护制度1. 引言设备是企业正常运转的重要支撑,良好的设备日常维护管理制度对于保障设备正常运行、延长设备寿命、提高生产效率具有重要意义。
为了规范设备的管理与维护,制定本制度,以确保设备的正常运转和安全。
2. 适用范围本制度适用于本企业的所有设备,包括生产设备、办公设备以及其他相关设备。
3. 设备管理责任3.1 设备管理员由企业确定专人负责设备管理与维护,包括设备的日常巡检、故障排除、记录设备运行情况、及时向上级报告设备情况以及设备维护计划的编制。
3.2 项目经理项目经理负责设备管理工作的协调与指导,监督设备管理员的工作执行情况,并向上级汇报设备管理的进展情况。
3.3 部门经理部门经理负责设备的采购、维护和保养工作,及时向上级反馈设备使用情况和所需资源。
4. 设备日常维护管理流程4.1 日常巡检设备管理员定期进行设备的日常巡检工作,检查设备的运行状况、设备周围的环境是否符合要求,并记录巡检情况。
4.2 设备保养设备管理员根据设备保养手册或生产设备生产周期,进行设备的定期保养,包括设备的清洁、润滑、紧固等维护工作,确保设备的正常运行。
4.3 设备维修设备管理员在巡检或保养过程中发现设备故障,应及时排除故障或报告上级,并跟踪维修进展情况,直至设备得到修复。
4.4 设备更换设备管理员根据设备的寿命、维修成本以及生产需求,定期评估设备是否需要更换,并提出更换申请,经上级批准后进行更换。
5. 设备运行记录与报告设备管理员应建立设备运行记录,按要求记录设备的运行参数、故障情况、维护与保养工作,并及时向上级报告设备运行情况与维护修理情况。
6. 设备维护培训企业应定期对设备管理员进行设备维护培训,包括操作技能、维护方法和应急处理等,提高设备管理员的维护能力和应急处理能力。
7. 引进设备与验收企业引进新设备时,应按照相关规定进行设备验收和鉴定,确保新设备符合规定要求,设备管理员参与设备验收工作并记录验收情况。
设备使用管理、维护管理与维修管理

设备使用管理、维护管理与维修管理简介设备使用管理、维护管理与维修管理是一个组织内确保设备正常运行和提高设备可靠性的重要环节。
这些管理活动涵盖了设备的采购、配置、部署、维护、修复和更替等方面。
本文档将介绍设备使用管理、维护管理与维修管理的基本原则和最佳实践,以帮助组织高效地管理设备。
设备使用管理设备使用管理是指有效地管理和控制设备的使用过程,以保证设备运行的高效性和稳定性。
以下是设备使用管理的基本原则和最佳实践:1. 设备登记与分类为了对设备进行有效管理,组织应该建立设备登记制度,并对设备按照类型、性能、用途等分类进行管理。
设备登记应包括设备的基本信息,如设备名称、型号、序列号、所属部门、责任人等。
2. 设备规范与标准制定设备的使用规范和标准,明确设备的使用流程和操作要求。
这些规范和标准应该包括设备的开启与关闭操作、设备的安全使用要求、设备的维护保养流程等。
通过规范设备的使用,可以提高设备的可靠性和使用寿命。
3. 设备维护与保养设备维护与保养是确保设备正常运行的重要环节。
组织应该制定设备维护与保养计划,并按照计划对设备进行定期维护和保养。
维护工作应包括设备的清洁、调校、润滑等工作,并记录维护的时间和内容。
4. 设备故障与问题处理当设备发生故障或问题时,组织应及时处理并解决。
维修人员应对设备故障进行排查和修复,并记录维修过程和结果。
对于频繁发生故障的设备,应该进行深入分析和调查,找出原因并采取措施进行改进。
维护管理维护管理是指对设备的维护活动进行有效管理和控制,以保证设备的正常运行和延长设备的使用寿命。
以下是维护管理的基本原则和最佳实践:1. 维护计划与策略组织应制定适当的维护计划和策略。
维护计划应考虑设备的使用频率、环境条件和制造商的建议等因素,制定适当的维护周期和维护内容。
维护策略应明确维护的重点和优先级。
2. 维护记录与跟踪对于每次维护活动,组织应该记录维护的时间、内容和结果。
这些维护记录有助于管理人员掌握设备的维护情况,及时发现并解决存在的问题。
{设备管理}设备使用与维护保养管理规定
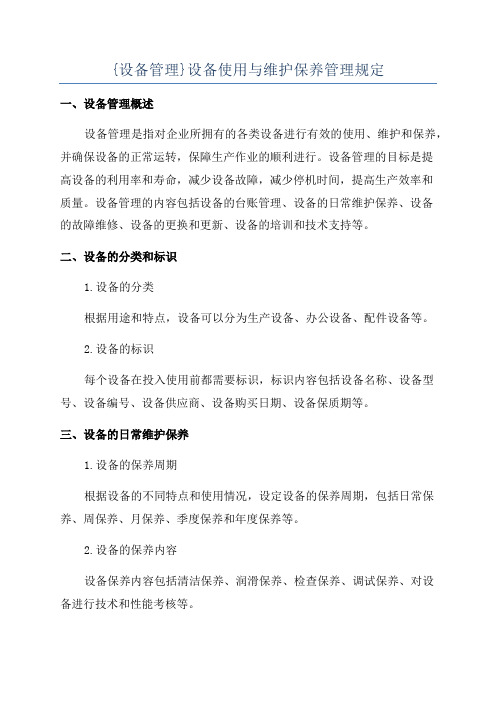
{设备管理}设备使用与维护保养管理规定一、设备管理概述设备管理是指对企业所拥有的各类设备进行有效的使用、维护和保养,并确保设备的正常运转,保障生产作业的顺利进行。
设备管理的目标是提高设备的利用率和寿命,减少设备故障,减少停机时间,提高生产效率和质量。
设备管理的内容包括设备的台账管理、设备的日常维护保养、设备的故障维修、设备的更换和更新、设备的培训和技术支持等。
二、设备的分类和标识1.设备的分类根据用途和特点,设备可以分为生产设备、办公设备、配件设备等。
2.设备的标识每个设备在投入使用前都需要标识,标识内容包括设备名称、设备型号、设备编号、设备供应商、设备购买日期、设备保质期等。
三、设备的日常维护保养1.设备的保养周期根据设备的不同特点和使用情况,设定设备的保养周期,包括日常保养、周保养、月保养、季度保养和年度保养等。
2.设备的保养内容设备保养内容包括清洁保养、润滑保养、检查保养、调试保养、对设备进行技术和性能考核等。
3.设备保养记录对每次设备保养的具体内容和结果进行记录,包括保养日期、保养人员、保养内容、设备状况等。
四、设备故障维修1.设备故障的诊断一旦设备出现故障,需要及时进行故障诊断,明确故障原因和范围。
2.设备故障的修复根据故障的性质和程度,确定维修的方法和措施,及时修复设备故障。
3.设备故障的记录和分析对设备故障进行记录和分析,包括故障原因、故障处理方法、修复时间等,为后续设备管理提供参考。
五、设备的更换和更新1.设备更换的判断标准根据设备的使用年限、故障频次、维修费用等因素,判断是否需要更换设备。
2.设备更换的流程设备更换需要经过申请、审批、采购、验收等多个环节,确保更换的设备能够满足生产需求。
3.设备更新的计划根据科技的发展和企业的需求,制定设备更新的计划,确保设备始终保持良好的工作状态。
六、设备的培训和技术支持1.设备操作培训对设备操作人员进行操作培训,让其熟悉设备的使用方法和注意事项。
设备使用与维护管理办法范本
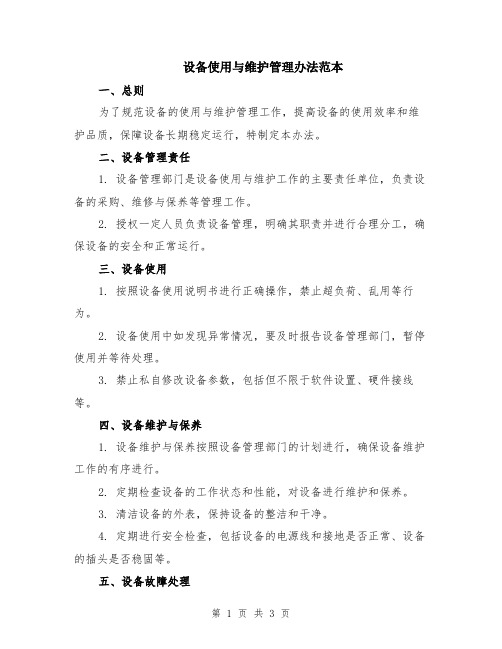
设备使用与维护管理办法范本一、总则为了规范设备的使用与维护管理工作,提高设备的使用效率和维护品质,保障设备长期稳定运行,特制定本办法。
二、设备管理责任1. 设备管理部门是设备使用与维护工作的主要责任单位,负责设备的采购、维修与保养等管理工作。
2. 授权一定人员负责设备管理,明确其职责并进行合理分工,确保设备的安全和正常运行。
三、设备使用1. 按照设备使用说明书进行正确操作,禁止超负荷、乱用等行为。
2. 设备使用中如发现异常情况,要及时报告设备管理部门,暂停使用并等待处理。
3. 禁止私自修改设备参数,包括但不限于软件设置、硬件接线等。
四、设备维护与保养1. 设备维护与保养按照设备管理部门的计划进行,确保设备维护工作的有序进行。
2. 定期检查设备的工作状态和性能,对设备进行维护和保养。
3. 清洁设备的外表,保持设备的整洁和干净。
4. 定期进行安全检查,包括设备的电源线和接地是否正常、设备的插头是否稳固等。
五、设备故障处理1. 设备故障发生后,应及时报告设备管理部门,并提供详细的故障描述。
2. 临时处理故障时,要保证自身安全,并按照设备管理部门的指导进行操作。
3. 设备故障处理需遵循故障排除原则,排查问题原因并修复故障。
六、设备备品备件管理1. 设备备品备件采购应按照设备管理部门的计划进行,确保备品备件的数量和质量满足使用需求。
2. 设备备品备件的存放要规范、整齐,避免损坏或混乱。
3. 设备备品备件使用完毕或损坏后,要及时报告设备管理部门,并进行及时补充或更换。
七、设备报废管理1. 设备达到报废标准后,由设备管理部门进行评估并决定是否报废。
2. 设备报废前,要进行设备的清理和备案,确保设备资料的完整性。
3. 设备报废后,要进行相应的处理,包括但不限于设备的拆解、销毁和废物分类处理。
八、设备管理档案1. 设备管理部门应建立设备管理档案,记录设备的采购、维修和保养等详细信息。
2. 设备使用部门要按照规定提交设备使用信息,保证设备管理档案的完整和准确。
生产设备的使用、维护保养与安全管理办法(4篇)
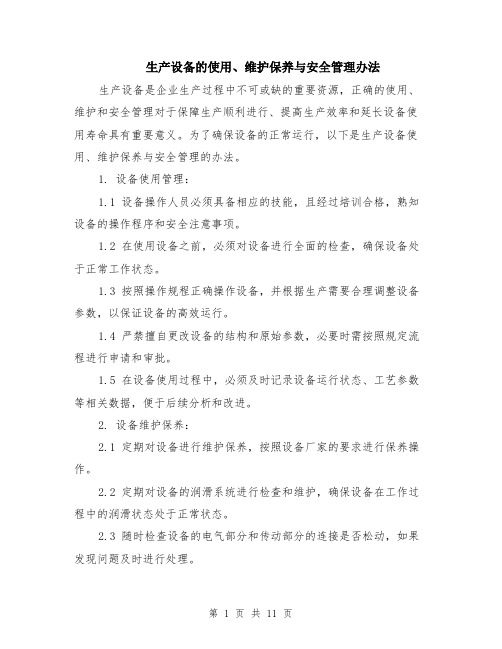
生产设备的使用、维护保养与安全管理办法生产设备是企业生产过程中不可或缺的重要资源,正确的使用、维护和安全管理对于保障生产顺利进行、提高生产效率和延长设备使用寿命具有重要意义。
为了确保设备的正常运行,以下是生产设备使用、维护保养与安全管理的办法。
1. 设备使用管理:1.1 设备操作人员必须具备相应的技能,且经过培训合格,熟知设备的操作程序和安全注意事项。
1.2 在使用设备之前,必须对设备进行全面的检查,确保设备处于正常工作状态。
1.3 按照操作规程正确操作设备,并根据生产需要合理调整设备参数,以保证设备的高效运行。
1.4 严禁擅自更改设备的结构和原始参数,必要时需按照规定流程进行申请和审批。
1.5 在设备使用过程中,必须及时记录设备运行状态、工艺参数等相关数据,便于后续分析和改进。
2. 设备维护保养:2.1 定期对设备进行维护保养,按照设备厂家的要求进行保养操作。
2.2 定期对设备的润滑系统进行检查和维护,确保设备在工作过程中的润滑状态处于正常状态。
2.3 随时检查设备的电气部分和传动部分的连接是否松动,如果发现问题及时进行处理。
2.4 定期清洁设备的各个部位,将设备内部的杂物和灰尘清除干净,以确保设备的正常运行。
2.5 对设备的关键零部件进行定期检修和更换,以确保设备的稳定性和安全性。
3. 设备安全管理:3.1 在生产过程中,设备必须经过严格的安全检查和测试,确保设备符合安全标准。
3.2 操作人员必须佩戴符合要求的个人防护用品,严禁穿戴过大或过松的衣物或饰品。
3.3 维护人员必须具备相应的安全知识和技能,且必须遵守安全操作规程。
3.4 在设备维护过程中,必须切断设备的电源,并采取正确的安全措施,确保人身安全。
3.5 对设备进行定期的安全检查和维护,对设备存在的安全隐患及时进行处理。
总结:生产设备的使用、维护保养与安全管理对于企业的生产运行具有重要意义。
通过合理的使用管理、维护保养和安全管理措施,可以提高设备的运行效率,延长设备的使用寿命,保障生产安全。
设备管理及维护制度

设备管理及维护制度一、引言设备管理及维护是保障生产运行的重要环节,需要建立一套科学、规范、高效的管理制度。
本文将介绍设备管理及维护制度的相关内容,以确保设备正常运行、延长设备寿命、提高生产效率。
二、设备管理制度1. 设备资料管理设备管理始于设备资料的建立和完善。
每个设备都应建立详细的资料档案,包括设备名称、型号、规格、制造商、购买日期、保修期限等信息,并进行分类、编码、标识,便于管理和查找。
2. 设备投资决策设备投资应根据实际需要和经济效益进行决策,包括设备采购、更新、报废等决策。
决策过程应经过充分的论证和评估,确保投资的合理性和可行性。
3. 设备验收管理设备验收是确保设备质量合格的重要环节。
验收应按照规定的程序进行,包括设备检验、试运行、技术验收等环节,确保设备符合要求并具备正常运行的能力。
4. 设备领用管理设备的领用应按照一定的流程进行,包括设备出库、签收、使用登记等环节。
领用人应对设备进行细致的检查,如有问题应及时反馈给设备管理部门。
5. 设备保养管理设备保养是保障设备正常运行的重要措施。
每台设备应有保养计划,定期进行检修、清洁、润滑等工作,延长设备寿命,减少故障发生的可能性。
6. 设备维修管理设备维修是在设备故障时进行的修复工作。
维修工作应有专门的维修人员进行,按照维修流程进行操作,确保设备能够尽快恢复正常运行。
7. 设备更新管理设备更新是为了跟上科技发展和市场需求而进行的设备替换工作。
更新应根据设备状况和需求进行决策,包括设备更新时机、设备选型、设备采购等环节。
8. 设备报废管理设备报废是设备寿命到期或无法修复时进行的处理工作。
报废应按照规定的程序进行,包括设备评估、报废审批、设备处置等环节,确保设备报废的合法性和安全性。
三、设备维护制度1. 定期维护设备维护应按照一定的周期进行,包括设备检查、清洁、润滑、调试等工作。
维护人员应按照维护计划进行操作,确保设备的正常运行和稳定性。
2. 预防性维护预防性维护是为了防止设备故障而进行的维护工作。
设备管理及维护制度

设备管理及维护制度一、总则为了加强设备管理,保证设备的正常运行,提高设备的利用率和完好率,延长设备的使用寿命,降低设备维修成本,保障生产的顺利进行,特制定本制度。
二、设备管理的职责划分(一)设备管理部门1、负责制定设备管理的规章制度和技术标准,并监督执行。
2、负责设备的选型、采购、验收、安装、调试、报废等全过程管理。
3、建立设备档案,包括设备的技术资料、运行记录、维修记录等。
4、制定设备的维修计划和保养计划,并组织实施。
5、负责设备的技术改造和更新工作,提高设备的性能和效率。
(二)设备使用部门1、负责设备的日常使用和维护,严格按照操作规程进行操作。
2、做好设备的日常保养工作,如清洁、润滑、紧固等。
3、发现设备故障及时报告设备管理部门,并协助维修人员进行维修。
4、负责设备的安全管理,防止发生安全事故。
(三)维修部门1、负责设备的维修工作,及时排除设备故障,保证设备的正常运行。
2、做好设备维修记录,分析设备故障原因,提出改进措施。
3、协助设备管理部门做好设备的预防性维护工作。
三、设备的选型与采购(一)设备选型1、根据生产工艺和生产任务的要求,结合设备的性能、质量、价格等因素,选择合适的设备型号。
2、优先选择技术先进、性能可靠、节能高效、环保安全的设备。
3、考虑设备的通用性和互换性,便于设备的维修和保养。
(二)设备采购1、按照公司的采购程序,进行设备的采购。
2、与供应商签订采购合同,明确设备的规格、型号、技术参数、质量标准、交货期、价格、售后服务等条款。
3、设备到货后,由设备管理部门组织验收,验收合格后方可入库或投入使用。
四、设备的安装与调试(一)设备安装1、设备安装前,要制定详细的安装方案,包括安装工艺、安装进度、质量控制等。
2、安装人员要严格按照安装方案进行安装,确保安装质量。
3、安装过程中,要做好安全防护工作,防止发生安全事故。
(二)设备调试1、设备安装完成后,要进行调试,调试包括单机调试和联动调试。
设备、工器具保养及维修管理制度(4篇)

设备、工器具保养及维修管理制度第一章总则第一条为了保障设备、工器具的正常运转,提高设备利用率,延长设备使用寿命,确保生产安全和质量,制定本制度。
第二条本制度适用于本单位所有设备、工器具的保养和维修工作。
第三条设备、工器具的保养和维修应遵循“提前预防、综合管理、主动维修、完善检查”的原则。
第四条设备、工器具的保养和维修应具备规范性、周期性和系统性。
第五条设备、工器具的保养和维修工作由设备管理部门负责组织实施。
第六条本制度的修改和解释权归设备管理部门所有。
第二章设备、工器具的分类和标识第七条设备、工器具按照其使用性质和用途,分为生产设备、辅助设备和工器具。
第八条设备、工器具应按照统一标准进行分类和标识。
分类要准确、明确,标识要醒目、持久。
第九条设备、工器具的标识应包括设备编号、设备名称、型号、生产厂家、安装地点等信息。
第十条设备、工器具的标识应牢固固定,避免遗失或混淆。
第三章设备、工器具的保养管理第十一条设备、工器具保养管理包括计划性保养和日常保养。
第十二条计划性保养由设备管理部门根据设备、工器具的使用情况和生产需要制定。
第十三条计划性保养工作应提前编制计划、明确责任、分工合作、掌握时间节点。
第十四条计划性保养工作包括设备、工器具的检查、清洁、润滑、调整、更换。
第十五条日常保养由设备使用人负责,包括设备的日常巡检、清洁和保养。
第十六条设备使用人应对设备的状况进行日常观察和记录,及时发现问题并及时报修。
第四章设备、工器具的维修管理第十七条设备、工器具的维修分为日常维修和大修。
第十八条日常维修包括设备的小故障修理、部件更换、调整。
第十九条日常维修工作由设备管理部门负责安排和执行。
第二十条大修由设备管理部门根据设备的实际情况和维修需要进行安排。
第二十一条大修包括设备的主要部件更换、调整和整体修复。
第二十二条维修人员应具备相应的技术和资质,操作过程应符合安全操作规程。
第五章设备、工器具的报废管理第二十三条设备、工器具达到国家法律法规规定的报废标准或无法修复时,应及时报废。
设备管理和维护制度范文(三篇)
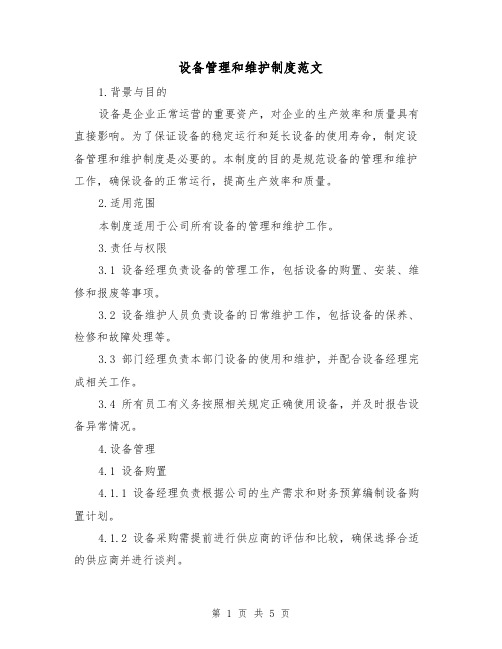
设备管理和维护制度范文1.背景与目的设备是企业正常运营的重要资产,对企业的生产效率和质量具有直接影响。
为了保证设备的稳定运行和延长设备的使用寿命,制定设备管理和维护制度是必要的。
本制度的目的是规范设备的管理和维护工作,确保设备的正常运行,提高生产效率和质量。
2.适用范围本制度适用于公司所有设备的管理和维护工作。
3.责任与权限3.1 设备经理负责设备的管理工作,包括设备的购置、安装、维修和报废等事项。
3.2 设备维护人员负责设备的日常维护工作,包括设备的保养、检修和故障处理等。
3.3 部门经理负责本部门设备的使用和维护,并配合设备经理完成相关工作。
3.4 所有员工有义务按照相关规定正确使用设备,并及时报告设备异常情况。
4.设备管理4.1 设备购置4.1.1 设备经理负责根据公司的生产需求和财务预算编制设备购置计划。
4.1.2 设备采购需提前进行供应商的评估和比较,确保选择合适的供应商并进行谈判。
4.1.3 设备经理负责设备的验收工作,确保设备符合规定要求,并填写验收报告。
4.1.4 设备验收合格后,设备经理将设备信息录入设备台账,登记设备的型号、数量、购置日期和供应商等信息。
4.2 设备安装与调试4.2.1 新设备安装前,设备经理要组织安装人员进行设备布置和安装工作,并保证设备安装符合相关标准和规定。
4.2.2 设备安装完成后,设备经理要组织调试人员进行设备的调试和试运行,确保设备能够正常运行。
4.2.3 设备安装和调试完成后,设备经理要对设备进行验收,填写验收报告,并将设备信息记录到设备台账中。
4.3 设备维修与保养4.3.1 设备维护人员要按照设备维护计划进行设备的定期保养工作,包括设备的清洁、润滑和紧固等。
4.3.2 设备维护人员要及时处理设备的故障,并记录故障处理情况和维护记录。
4.3.3 设备经理要监督设备维护人员的工作,确保设备的正常运行和维护工作的及时完成。
4.4 设备报废4.4.1 设备经理要定期对设备进行评估和检查,判断设备是否需要报废。
设备的使用和维护管理制度范本

设备的使用和维护管理制度范本一、目的与适用范围本制度旨在规范和管理公司内各类设备的使用和维护工作,保障设备的安全、稳定和有效运行。
适用于公司内所有设备的使用和维护管理工作。
二、责任与权限1. 公司设备管理部门负责设备的统一管理和维护工作,制定设备使用和维护标准,并监督各部门的执行情况。
2. 各部门负责自身所用设备的日常使用和维护,同时配合设备管理部门进行定期检查、保养和维修工作。
三、设备的使用管理1. 设备使用前,用户必须经过相关培训,并获得设备管理部门的授权。
2. 使用设备时,必须按照设备操作手册中的规定进行操作,不得随意更改设备设置。
3. 设备使用完毕,必须及时关机并拔掉电源插头,保证设备安全。
4. 设备使用人员要定期检查设备的工作状态和性能,如发现异常情况应及时报告设备管理部门。
5. 禁止未经授权拆卸、修理设备,发现设备故障或异常情况时,应立即报告设备管理部门。
四、设备的维护管理1. 设备使用部门应按照设备管理部门的安排,定期进行设备的保养和维修工作。
2. 定期对设备进行清洁、润滑和更换耗材等维护工作,确保设备的正常运行。
3. 设备管理部门要对设备进行定期的巡检和维护,定期检查设备状况,及时发现并处理设备故障和异常情况。
4. 设备故障或异常时,设备管理部门应及时组织维修人员进行维修或更换设备,确保设备的正常运行。
5. 设备报废后,设备管理部门负责安排设备的处置,确保环境和安全要求。
五、设备安全管理1. 设备使用人员在使用设备时要注意安全,遵守相关安全规定,确保自身和他人的安全。
2. 禁止在设备周围存放易燃易爆物品,确保设备的安全运行。
3. 设备管理部门要确保设备的安全性能和防护功能完好,及时修复损坏的安全设备。
4. 对于需进行检修、保养和维修的设备,设备管理部门应提前制定并遵守相关安全操作规程,确保人员操作安全。
六、违规与处罚对于违反设备使用和维护管理制度的行为,将进行相应的处罚和纪律处分,包括口头警告、书面警告、扣发奖金或清退等。
设备管理及维护制度
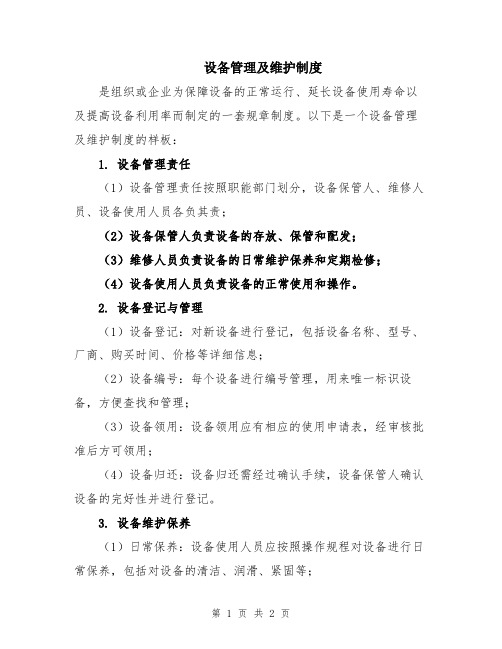
设备管理及维护制度是组织或企业为保障设备的正常运行、延长设备使用寿命以及提高设备利用率而制定的一套规章制度。
以下是一个设备管理及维护制度的样板:1. 设备管理责任(1)设备管理责任按照职能部门划分,设备保管人、维修人员、设备使用人员各负其责;(2)设备保管人负责设备的存放、保管和配发;(3)维修人员负责设备的日常维护保养和定期检修;(4)设备使用人员负责设备的正常使用和操作。
2. 设备登记与管理(1)设备登记:对新设备进行登记,包括设备名称、型号、厂商、购买时间、价格等详细信息;(2)设备编号:每个设备进行编号管理,用来唯一标识设备,方便查找和管理;(3)设备领用:设备领用应有相应的使用申请表,经审核批准后方可领用;(4)设备归还:设备归还需经过确认手续,设备保管人确认设备的完好性并进行登记。
3. 设备维护保养(1)日常保养:设备使用人员应按照操作规程对设备进行日常保养,包括对设备的清洁、润滑、紧固等;(2)定期保养:设备维护人员负责制定设备定期保养计划,并按照计划进行设备的定期保养,包括更换易损件、检查设备运行状态等;(3)保养记录:对设备的日常保养和定期保养都应进行记录,包括保养内容、保养时间等。
4. 设备维修与更换(1)设备故障报修:使用人员在发现设备故障时应及时向维修人员报修,并进行故障描述;(2)维修及时性:维修人员应及时进行维修,尽量减少设备停机时间;(3)设备更换:对于老化严重、维修无法解决的设备,应及时进行更换;(4)维修记录:对设备维修过程进行记录,包括故障原因、维修方法、维修时间等。
5. 设备更新与报废(1)设备更新:当设备技术落后、不适应生产需要时,应及时进行设备更新,购买新设备;(2)设备报废:对于无法修复或不再使用的设备,应及时进行设备报废处理,并进行相关的设备报废手续。
以上是一个设备管理及维护制度的基本框架,具体的实施和细节可以根据实际情况进行调整和完善。
- 1、下载文档前请自行甄别文档内容的完整性,平台不提供额外的编辑、内容补充、找答案等附加服务。
- 2、"仅部分预览"的文档,不可在线预览部分如存在完整性等问题,可反馈申请退款(可完整预览的文档不适用该条件!)。
- 3、如文档侵犯您的权益,请联系客服反馈,我们会尽快为您处理(人工客服工作时间:9:00-18:30)。
{设备管理}设备使用管理维护管理与维修管理岗前培训持证上岗定人定机定责2建章健制使用守则操作规程维护保养规程岗位责任3检查监督班组长设备员第三节设备维护管理一设备维护保养制度:三级维护保养制1日常维护保养(日保)保养人:操作工人要点:班前检查加油润滑随手清洁处理异常班后维护真实记录坚持不懈周末养护2一级保养(一保)保养人:操作工人(主)+维修工人(辅)要点:定期计划重点拆解清洗检查擦拭润滑间隙调整紧固复位行为规范记录检查3二级保养(二保)保养人:维修人员(主)+操作工人(辅)要点:定期计划系统检查校验仪表全部润滑修复缺陷调整精度损件更换恢复公差消除泄漏认真记录制订对策标准验查二设备点检制度1点检分类日常点检定期点检专项点检精密点检2点检作业表年月No.设备编号:设备名称:检查者:审核:检查项目允许状态月日月日月日月日月日冷观察镜破损无裂纹及破损水观察镜水锈无水锈装冷却水充足置冷却水管不泄漏3点检准备定点:确定点检设备关键部位,薄弱环节定项:确定点检项目即检查内容(技术水平匹配,仪器仪表配套)定标:确定点检检查项目的判定标准(设备技术要求、实践经验)定周期:确定点检周期(安全、耗损、工艺、负荷、经验、可调)定法:确定点检方法(解体,非解体,停机,非停机,五感,仪表)定人:确定点检人员(按照不同点检分类确定)定表:确定点检表格定记录:确定点检记录内容项目及相关分析4点检实施检查:按照点检规范对设备的点检部位进行检查;记录:将检查结果记录在案;处理:检查中间出现的异常及时处理,恢复设备正常状态,并将处理结果记录,不能处理的要报告传达给负责部门处理;分析:定期分析检查记录内容,找出设备薄弱环节或难以维护部位,提出改进意见;改进:组织实施对设备薄弱环节的改进工作。
5点检管理点检模型管理:点检工作模型包括:点检区域划分,点检路线图,点检业务流程(PDCA循环);点检计划模型包括:日点检作业卡,定期点检计划表,长期点检计划表,专业点检计划表和精密点检计划表;点检实绩管理:记录管理包括:日点检记录,给脂加油记录,定期检查记录,维修报告书,改进维修记录,MTBF 分析记录,维修费用记录等等;实绩分析包括:分析会议,故障分析,劣化倾向分析和管理,维修方案研究决策程序,分析方法的运用等等;点检人员技术素质管理:点检人员岗位职责,点检技术要求,点检人员培训,点检人员业务评价和业绩考评,点检人力资源管理。
第四节设备润滑管理一润滑管理的摩擦学基础1摩擦学的研究内容摩擦起因磨屑形成机理润滑理论机械运动副的摩擦学特性和失效机理摩擦磨损测试技术减摩耐磨材料及其表面处理技术润滑材料2指导润滑管理设备磨损曲线磨损量磨合正常磨损阶段剧烈磨损阶段磨损阶段T设备磨损曲线二润滑管理目的和内容1目的:防止机械摩擦副异常磨损防止润滑剂污染、泄漏防止润滑故障提高可靠性降低维修成本2内容:润滑技术管理润滑物资管理三润滑管理实施1建立组织,配备人员专业润滑技术人员专职润滑管理员日保操作人员润滑润滑站(配制、化验、供应、回收、再生)2建章定制岗位责任制度设备润滑制度润滑站管理制度设备清洗换油制度3实施有效管理技术支持管理:润滑卡片,图表,计算机辅助润滑管理软件设备润滑卡片设备名设备型号设备编号所在车间总贮油量kg制造厂设备用油脂换油部位润滑材料润滑周期油量(kg)清洗换油计划管理:年、季、月清洗换油计划,按质换油计划;油品质量管理:入库化验,在用品定期化验;润滑“五定”管理:定点,定质,定量,定人,定期;润滑“三过滤”管理:领油过滤,转桶过滤,加油过滤润滑技术管理:润滑故障解决,复杂设备润滑系统改造,旧油回收与再生技术,新润滑材料和技术实验推广;润滑设施管理:自动润滑系统诊断维护管理,润滑工具管理;四计算机辅助润滑管理1功能:设备润滑档案油品质量管理润滑“五定”管理设备清洗换油计划管理油品需求计划管理润滑设施管理润滑工作检查评估润滑管理文件、卡片生成2计算机润滑管理逻辑流程设备润滑档案油品质量管理润滑“五定”管理润滑设施管理润滑管理文件、卡片生成系统设备清洗换油计划管理油品需求计划管理润滑工作检查评估第五节设备故障管理一设备故障及分类定义:设备丧失规定功能(不能工作,性能劣化,不安全)1产生过程分类:突发性故障渐进性故障2时间长短分类:间歇性故障永久性故障3宏观原因分类:固有故障操作维护不当故障磨损故障4功能劣化分类:潜在故障功能故障二故障原因和模式1宏观原因:设计缺陷材料缺陷制造缺陷操作维护环境不当2微观原因:弹性变形失效塑性变形(屈服)失效塑性断裂失效脆性断裂失效疲劳断裂失效腐蚀失效磨损失效蠕变失效三故障发生规律1浴盆曲线磨损量故障率初发偶发故障期耗损(劣化)故障期故障期T2故障渐变过程设P-F间隔在P-F备潜在故障发生线P间隔进行性功能故障发生线F预防维修tPtF时间劣化渐变过程如下:微缺陷中缺陷大缺陷故障不会产生会产生已发展到停机,暂时不小停机或影响故障边缘,置之影响功能设备功能不理后果严重3故障复合多重状况劣化原因劣化劣化劣化原因原因原因劣化劣化劣化原因原因原因原因单一因素多因素复合因素结构四设备故障全过程管理1故障信息收集设备使用、故障记录日志设备编号名称型号规格日使用故障故障检查排除换备件修理工时移交停机时间使维修理期时间发生现象原因措施名称数钳仪电生产用修费用时间量图号工工工时间等待修理人人(元)2故障信息储存统计采用计算机存储统计:信息输入-统计-查询-显示-打印内容:故障设备名-车间(厂)故障次数-停机总时间-平均无故障时间-平均修理时间-故障主次图3故障分析主次图分析故障累积频次92.5%99.9%百分81.4%数70.3%45.5%变速主轴溜板电器其他(主次排列的故障原因)鱼骨分析中骨中骨中骨小骨小骨小骨脊骨故障小骨小骨小骨细骨中骨中骨中骨PM分析透过现象,分析其物理本质的方法。
P:phenomenaphysicalproblempreventive现象物理的问题可预防的M:mechanismmaterialmachinemanpowermethod 机理材料设备人力方法连续问5个为什么。
假设检验方法阶段A:问题A假设1,2,…验证1,2…结论A;阶段B:问题B假设1,2,…验证1,2…结论B;阶段C:问题C假设1,2,…验证1,2…结论C;最终结论劣化趋势图分析设备性能t1t2t3t4t5时间故障树分析(顶事件)设备故障与部件故障1(中间事件)部件故障2与或元件1元件2元件3元件4失效失效失效失效(底事件)故障的集合优选搜寻f1f2f3f4f5故障集合表征集合s1s2s3s4s5s6s7s8三个原则:最大概率+最小费用+纯集优选4故障处理故障特征起因重复性多发性周期性耗损性先天性失误性修理性故障故障故障故障故障故障故障项修局改造定期纠正改造规范培训质部改造报废维修恢复再设计训练量控制5评价与反馈设备状态与维修经验反馈设计与制造厂商(设计制造)使用部门(选型)维修部门(维修改造)五设备事故管理1设备事故因非正常损坏造成的停产或效能降低,损失超限的称为事故。
分类:一般事故,重大事故,特大事故2调查分析切断电源,根除隐患保护现场,立即上报调查原因,分析处理制订方案,恢复抢修六设备状态监测管理1可行性分析决策有效经济合算2模式选择振动监测(离线、在线)油液分析红外成象其他3配备专人选人定则培训4倾向管理倾向监测确定报警阈值5维修决策数据化监测反馈机制快速反馈决策维修应变常备第五节设备维修管理一设备维修方式1事后修理(冗余、非主线设备)2定期修理(耗损周期明显设备)3强制性修理(安全性、故障后果严重型、流程设备)3检查后修理(无固定负荷、精、稀、关设备)4状态监测修理(实施状态监测和倾向管理设备)5机会修理(有生产空闲、节假日并周期不明显设备、项修设备)6针对性修理(项修、局部维修,负荷及运动不平均设备)7改造性修理(耗损严重、重复故障、先天不足设备)二设备维修的一般步骤1编制计划2修前预检3准备文件(工令、图纸、资料)4物料准备(备件、材料、工具、仪表准备)5组织准备(指挥、联络、协调)6现场准备(水、电、气、动、风)7维修实施8试车验收9总结反馈三维修策略选择1可靠性为中心的维修策略选择故障后果导向可行性导向有效性导向2利用率为中心的维修策略选择利用率影响评估排序故障特征分析维修方式选择3适应性维修的维修策略选择维修方式的生产损失评估维修成本综合费用评估4其他综合评估维修策略选择方式综合评估导向:后果+效益+维修资源四维修计划1编制维修计划的基本准则作业控制准则:工作量,优先级、维修资源工作量均衡准则:保养,计划维修,改造,随机抢修按照优先级均衡搭配集中与分散均衡准则:按照优先级从高到底向基层分散计划信息畅通准确准则:会议、通讯、E-mail2编制维修计划程序确定成套设备中关键设备和生产间隙时间设备层层分解到元件级确定各元件最佳维修措施编制作业计划编制作业进度计划3维修计划运行文件作业命令单预防维修作业说明书维修计划(举例见下面表)作业汇总表作业平衡图表派工牌维修计划表设备名称5t吊车地址仓库(66)周期工种序号作业内容每机1一般检查2检查大车驱动噪声,振动及温度异常周3检查小车驱动噪声,振动及温度异常4升降机运转情况检5检查电动机驱动噪声,振动及温度异常6仔细查看钢丝绳滑伦和吊钩是否损坏查7肯定限位装置是否工作可靠械8检查吊挂控制装置是否安全可靠及状态每1检查大车行走电机是否安全可靠2检查大车制动器安全性及垫衬磨损三机3检查大车驱动轴承是否可靠4检查大车减速齿轮箱状态个械5检查小车电动机是否安装可靠6检查小车制动器间隙、动作及衬垫磨损月部7检查升降机部件8负荷状态下检查制动器是否可靠的分9检查齿轮箱是否漏油10检查钢丝绳磨损和连接状况检11一般检查12报告润滑情况修13报告机器一般清洁状况1检查大车电动机线头和接地状况电2检查下垂的导线及时紧张,滑动磨损检查器3检查小车行走电机线头和接地部4检查升降机电气部分分5检查吊车总成有无损坏,看能否自由活动6检查电动机线头和接地是否安全7检查各限位开关的线路4维修计划的编制和执行准备:资料、说明、图纸、备件信息编制作业号和费用号编制预防维修说明书制订发放作业单作业进度计划和派工评估、反馈和数据整理归档五维修计划实施控制1进度控制:时间表的监督和调整2资金控制:费用统计和预算的比较对照3质量控制:修理合格证制度、验收制度感谢阅读多年企业管理咨询经验,专注为企业和个人提供精品管理方案,企业诊断方案,制度参考模板等欢迎您下载,均可自由编辑。