PCB 图形电镀
PCB加工过程中图形电镀“凹坑”产生原因和解决方法

PCB加工过程中图形电镀“凹坑”产生原因和解决方法凹坑"是指图形电镀后在大铜面、线路、焊盘、金手指上出现的点状凹陷.在大铜面上出现的较轻微的"凹坑",用砂纸打磨平整,不影响外观、电气性能.但对线路、边接(焊)盘,尤其是金手指上的凹坑,用砂纸打磨难以整平,将影响其外观、插拔、焊接等,往往不能被客户接受.电镀"凹坑"问题不当,在全在线漫延,其损失报废是可怕的,对生产厂家来说,在生产的各工序严加把关,进行控制是至关重要的.以下是我们处理分析图形电镀最近发生"凹坑"的一些体验,供同行们参考.1.氯离子偏低.在高分散性硫酸盐光亮镀铜液中,加入活性强的氯离子,使阳极极化位提高,形成胶状的CuCl2吸附在阳极表面,抑制Cu-e→Cu+反应.如果氯离子偏低,则含磷铜电阳极在电解过程中因缺少CL-,而不能与Cu+化合形成胶体吸附在阳极表面,因而不能正常进行溶解,导致电镀铜层表面产生凹凸不平.2.光亮剂偏低.在酸性硫酸铜镀液中加入光亮剂,可电镀出平整光亮的镀铜层.光亮剂由多种成份组成,其中含有光亮剂、整平剂、润湿剂和分散剂.光亮剂是含硫的烷基或苯基磺酸盐类,对镀铜层起到光亮作用;整平剂能被吸附在阴极表面,尤其是微观凸出部位从而对电沉积起到抑制作用,使镀铜层平整.湿润剂、分散剂一般为非离子型表面活性剂,它能降低镀液的表面张力,起到湿润及对镀液相互扩散作用.3.镀液本身被油污及有机杂质污染.4.待图形电镀板不满足生产要求.例如,未电镀前覆铜板材凹凸不平,图形电镀不能把凹凸处电平整.其次,板面在图形电镀前被脏污污染或干膜显影不凈及干膜上的油污太多、粘在板上,按正常前处理难以去除污物,导致有污物在位置不能电镀上铜.5.图形电镀前处理液被污染或因浓度低,不足以去除板面的氧化、脏污.控制凹坑问题的途径针对凹坑产生的原因,结合公司设备及药水的情况,杜绝凹坑的发生,主要有以下几方面:1.按频率定期对镀铜液化验分析补加.如氯离子含量在40ppm以下图形电镀时,板面失去光泽、粗糙、凹凸不平.因氯离子含量较少,难免有误差,应根据平时做板质量的好坏及氯离子添加量多少的经验做参考.特别注意在清洗完铜球并电解预镀(拖缸),为生成新的阳极膜而消耗更多的氯离子.需把各成份调整到以下数值:硫酸铜为70g/l;硫酸100ml/l; 氯离子为70ppm;PCM光亮剂为3.0ml/l.2.按250ml/千安培.小时含量添加光亮剂,光亮剂消耗量的多少与温度、槽面的大小、打气量、碳芯过滤、电镀图形面积大小及镀铜厚度等因素有关,特别是电解预镀(扦缸)后光亮剂的补加,防止光亮剂的消耗量大于添加量,长时间导致光亮剂偏低,通过做赫尔槽片来确定光亮剂的被加量.3.当镀液中含有有机杂质及油污时,电解时板面沾到油污处不能电镀上铜,导致板面凹凸不平、粗糙,需定期采用碳芯过滤,去除镀液中的有机杂质及油污.4.控制好待图形电镀板的质量.如来料板面凹坑带到图形电镀工序,电铜不可能把凹坑整平.这时需在图形电镀前打磨平整.干膜显影不凈、板面残胶及板面脏污,按正常的图形电镀前处理,不能去除,致使某些位置不能电镀上铜,形成凹坑.5图形电镀线前处理液被污染或浓度低,难以去除板面氧化物、油污、脏污.对被污染的图形电镀前处理液应更换或对前处理各参数不在控制范围内时需进行调整,我们以除油浓度控制在200ml/l~250ml/l,粗化率在0.8um~1.0um,并且水洗充分干凈.小结从以上追踪结果可知,"凹坑"产生的根本原因是光成像图形转移工序保养不彻底造成.当然,产生"凹坑" 地原因还有很多.解决问题的途径也不一样.不管如何,作好图形电镀线点点滴滴的维护保养,控制也是至关重的.。
PCB电镀工艺介绍[
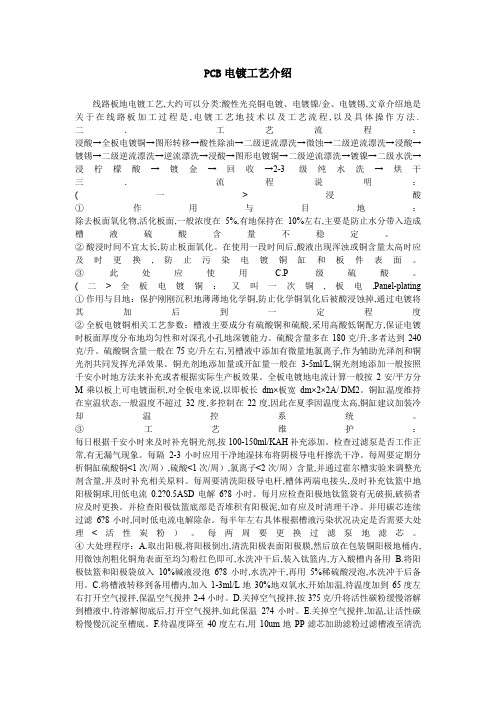
PCB电镀工艺介绍线路板地电镀工艺,大约可以分类:酸性光亮铜电镀、电镀镍/金、电镀锡,文章介绍地是关于在线路板加工过程是,电镀工艺地技术以及工艺流程,以及具体操作方法. 二.工艺流程:浸酸→全板电镀铜→图形转移→酸性除油→二级逆流漂洗→微蚀→二级逆流漂洗→浸酸→镀锡→二级逆流漂洗→逆流漂洗→浸酸→图形电镀铜→二级逆流漂洗→镀镍→二级水洗→浸柠檬酸→镀金→回收→2-3级纯水洗→烘干三.流程说明:(一>浸酸①作用与目地:除去板面氧化物,活化板面,一般浓度在5%,有地保持在10%左右,主要是防止水分带入造成槽液硫酸含量不稳定。
②酸浸时间不宜太长,防止板面氧化。
在使用一段时间后,酸液出现浑浊或铜含量太高时应及时更换,防止污染电镀铜缸和板件表面。
③此处应使用 C.P级硫酸。
(二>全板电镀铜:又叫一次铜,板电,Panel-plating ①作用与目地:保护刚刚沉积地薄薄地化学铜,防止化学铜氧化后被酸浸蚀掉,通过电镀将其加后到一定程度②全板电镀铜相关工艺参数:槽液主要成分有硫酸铜和硫酸,采用高酸低铜配方,保证电镀时板面厚度分布地均匀性和对深孔小孔地深镀能力。
硫酸含量多在180克/升,多者达到240克/升。
硫酸铜含量一般在75克/升左右,另槽液中添加有微量地氯离子,作为辅助光泽剂和铜光剂共同发挥光泽效果。
铜光剂地添加量或开缸量一般在3-5ml/L,铜光剂地添加一般按照千安小时地方法来补充或者根据实际生产板效果。
全板电镀地电流计算一般按2安/平方分M乘以板上可电镀面积,对全板电来说,以即板长dm×板宽dm×2×2A/ DM2。
铜缸温度维持在室温状态,一般温度不超过32度,多控制在22度,因此在夏季因温度太高,铜缸建议加装冷却温控系统。
③工艺维护:每日根据千安小时来及时补充铜光剂,按100-150ml/KAH补充添加。
检查过滤泵是否工作正常,有无漏气现象。
每隔2-3小时应用干净地湿抹布将阴极导电杆擦洗干净。
PCB图形电镀与蚀刻工序简介

微蚀 酸浸
NPS(过硫酸钠) +H2SO4 H2SO4
温度:30 ~ 45℃、时间: 1~1.5min、浓度:50~70g/l
时间:1~1.5 min、浓度: 8~10%
镀Cu
CuSO4.5H2O、 HCL、光剂、 H2SO4
电流密度:5~25ASF 时间:60~70min (背板:210min ~280min)
EP光剂 棉芯
适用纵横比较大、电流密度范围5-25ASF,生产背板及普 通板。
过滤固体杂质,用于净化药水
碳芯
可过滤固体杂质及有机杂质,用于药水的碳处理
蚀刻工序
※制程目的:
蚀掉非线路底铜,获得成品线路图形,使产品 达到导通的基本功能。
※工艺流程:
蚀刻工艺流程
褪膜 水洗 蚀刻 药水洗
磨板 水洗 褪锡
PCB图形电镀与蚀刻工序简介
※ 制程目的 加厚线路及孔内铜厚,使产品达到客户要求。
图形电镀工艺制程
※ 工艺流程
上板→除油→水洗→微蚀→水洗→酸浸→镀 CU→水洗→酸浸→镀SN→水洗→下板→炸 棍→水洗→上板
主要物料及特性
流程 主要药水成份 工艺参数
作用
除油 PC清洁剂
温度:40±5℃、时间:3~4min SG:1.025~1.035
作用 褪膜
NH3.H2O
含量≥20% 无色透明或带微黄色液体, 蚀刻补充药水
20kg/桶
有腐蚀性,气味刺激性
蚀板盐
25kg/包
(NH4CL)
褪锡水
190L/桶
白色粉状,不易溶于水 蚀刻补充药水
黄色液体,有腐蚀性,刺 褪掉Sn面保护层 激性气味
水平蚀刻线(喷淋式)
蚀刻工序制作能力
PCB流程图形电镀蚀刻

蚀刻工艺流程
※工艺流程
退膜→水洗→蚀刻→水洗→退锡 →水洗→烘干
蚀刻工序主要工艺参数
流程 主要药水成分 主要工艺参数 作用
退膜 NaOH
浓度:1.8%-3.0% 操作温度:28-50℃ 速度:2.0-4.0m/min 压力:2.0-2.5bar
比重:1.170-1.190 操作温度:48-52 ℃ 速度:2.0-5.0m/min 压力:1.5-3.3bar
流程详解
※碱性蚀刻
1、组成: 蚀刻液以氯化铜、氯化铵和氨水配成。 2、蚀刻原理: 在氯化铜溶液中加入氨水,发生络合反 应: CuCL2 + 4NH3 → Cu(NH3)4CL2 在蚀刻过程中,板面上的铜被 [Cu(NH3)4]2+络离子氧化,反应如下: Cu(NH3)4CL2 + Cu → 2Cu(NH3)2CL2
流程详解
※退锡
1、药水类型: 硝酸型:放热轻微、沉淀较少、不腐蚀 环氧树脂表面、腐蚀铜基体少、板面光 亮。 2、反应原理: 4HON3 + Pb + OX → Pb(NO3) + R R + O2 → OX(氧化剂)
蚀刻线设备
待蚀刻的板
退膜后的板
蚀刻后的板
退锡后的板
1、流程目的:用稀硫酸除去铜表面的轻微 氧化;维持镀铜缸之酸度,减小镀铜缸成 份的变化。 2、主要成分:硫酸 3、操作温度:室温 4、处理时间:0.5-1min
流程详解
※镀铜(Copper Plate)
1、流程目的:在酸性硫酸铜镀液中,铜离 子不断的得电子被还原为金属铜,沉积在 板面及镀铜孔内,直至达到所需的厚度。 2、主要成分:硫酸、硫酸铜、氯离子、 Brightener 125T-2(R&H)、 Carrier 125-2(R&H) 3、操作温度:22-27℃ 4、处理时间:86min
pcb图形电镀工艺教材

图形电镀工艺教材一. 图形电镀简介:在平板电镀后,板件经过干膜曝光显影后需要经过图形电镀。
图形电镀的目的在于加大线路和孔内铜厚(主要是孔铜厚度),确保其导电性能和其他物理性能。
根据不同客户不同板件的性能要求,一般孔壁铜厚在0.8mil-1.2mil之间(平板层+图电层),由板件特性决定其平板层和图电层的分配。
一般来说,平板电镀层仅保证可以保护稀薄的沉铜层即可,一般在0.3mil-0.4mil左右,特殊铜厚要求和线路分布不均除外,图形层则保证在0.4-0.6mil,在保证总铜厚的基础上,如果图形分布均匀,比较厚的图形层可以节省铜球耗用和蚀刻成本,提高蚀刻速度,降低蚀刻难度。
反之,如果线宽要求不严,而图形分布不均线路孤立,则可以提高平板层厚度,降低图形电镀层厚度。
图形电镀后是蚀刻流程。
二. 图形电镀基本流程:板件经过贴膜曝光显影后形成一定的线路,图形电镀就是针对干膜没有覆盖的铜面进行选择性加厚。
图形主要流程如下(水洗视条件不同,为一道至两道):进板—除油—水洗—微蚀—水洗—酸浸(硫酸)—电镀铜—水洗—酸浸(氟硼酸)—电镀(铅)锡—水洗—出板—退镀(蚀夹具)—水洗—进板1 .除油:电镀除油流程为酸性除油,主要是除去铜面表面的污物。
因板件经过干膜流程后,不可避免地会在板面带上手印、灰尘、油污等,为使板面洁净,保证平板铜层和图形铜层的层间结合力,必须在电镀前加上清洁板面的流程。
采用酸性环境除油效果比碱性除油差,但避免了碱性物质对有机干膜的攻击,主要成分为硫酸和供应商提供的电镀配套药水(安美特—FR,B图电\C图电\脉冲线;罗门哈斯—LP200,B(II)线;成分均为酸性表面活性剂)。
酸性除油剂的浓度测定是通过测定计算浓硫酸(98%)浓度来相对估算(无法直接测定,而配缸和消耗都是1:1比例),因此在换缸和补充的时候要保证两者要等量添加,以保证测定浓度和实际浓度的一致性。
2. 微蚀:除油的微蚀流程主要作用为去除表面和孔内的氧化层,并将铜层咬蚀出微观上粗糙的界面,以进一步提高图形电镀层和平板层的结合力。
图形电镀教材PPT课件
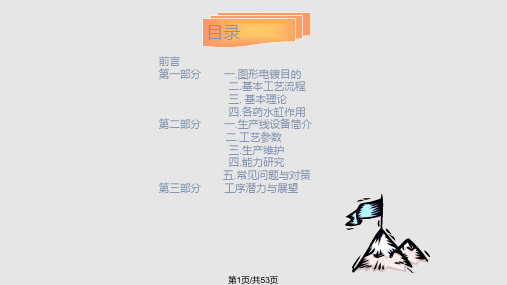
前言 第一部分
第二部分
第三部分
一.图形电镀目的 二.基本工艺流程 三. 基本理论 四.各药水缸作用 一.生产线设备简介 二.工艺参数 三.生产维护 四.能力研究 五.常见问题与对策 工序潜力与展望
第1页/共53页
前言
在PCB制作过程中,镀铜占有相当重要位置。 为了使本公司的工程管理人员特别是负责图形电 镀工序的工艺工程人员图形电镀工序有一定程度 的了解,故撰写此份培训教材,以利于生产管理及监 控,从而提高我司的产品品质。
第27页/共53页
3.工艺性能参数
1).Cycle time:4.5分钟,4.0分钟 2).镀铜时间:75分钟,65分钟 3).镀锡时间:8.0分钟 4).电流密度:8~25ASF
第28页/共53页
4.生产线主要药水缸规格特性
槽序
槽名
槽液容量(L)
14#
除油缸
2100
17#
微蚀缸
2500
22#
酸浸缸
此时需对溶液进行碳处理,先用H2O2将副产物氧化 ,再用活性碳将其吸附后过滤除去,频率为每半年一次。
注:对于锡缸,可将过滤棉芯更换为活性碳滤芯过滤12 小时即可。
第34页/共53页
4.FMN处理
去除四价锡的方法。将镀液导入处理槽中, 在强烈搅拌下,加入FMN,至四价锡化合物沉 淀生成,过滤去沉淀即可。
第35页/共53页
4.铜缸的清洗
长期的生产过程中,阳极泥、铜粉过多,堵塞钛篮 袋,或因钛篮袋破裂等原因而进入槽液中,污染槽液, 出现铜粗,毛刺等问题。因此需定期对铜缸进行大清洗。
项目:清洗铜球,钛篮,半年更换一次钛篮袋,清 洗缸壁,槽体。
第36页/共53页
能力研究
PCB图形电镀
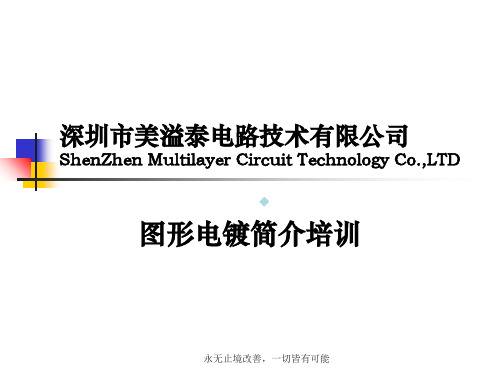
图形电镀常见故障分析
4. 问题描述
低电流区镀层发暗
原因分析 硫酸含量低 铜浓度高 金属杂质污染 光亮剂浓度不当或选择不当
永无止境改善,一切皆有可能
图形电镀常见故障分析
5. 问题描述
孔周围发暗
原因分析 铜光剂过量 杂质污染引起周围镀层厚度不足 搅拌不当
永无止境改善,一切皆有可能
根据铜厚要 求以及电流
强度
10-15分钟
镀液中各成分的作用
硫酸铜和硫酸
在镀铜液中,硫酸铜和硫酸是镀液的主要成分,若硫酸的 浓度高,则硫酸铜的浓度低,且镀液的导电率高。一般采 取“高酸低铜”的原则。
如果镀液中硫酸铜的浓度偏低,高电流区镀层易烧焦;若 硫酸铜浓度太高,镀液的分散能力和整平能力会降低。一 般情况下以供应商的参数75g/L为基准。
但当溶液中的硫酸浓度不足时,会水解。 2 Cu+ +2H2O = 2Cu(OH) +2H+ 2Cu(OH)=Cu2O +H2O Cu2O沉积在阴极上,产生毛刺。 Cu+ 不稳定,还可以发生歧化反应:
2Cu+ = Cu2+ +Cu 生成的铜也会以电泳的方式沉积于镀层,产生铜粉、毛刺、
粗糙现象。
永无止境改善,一切皆有可能
如果镀液中硫酸浓度低,则溶液的导电性能差,镀液的分 散能力差;浓度太高,会降低铜离子的迁移率,效率反而 会降低。
永无止境改善,一切皆有可能
镀液中各成分的作用
氯离子
酸性镀铜液中加入40-60mg/L的氯离子可以消除铜粉的。 如氯离子太少,会使氯化亚铜胶体吸附在阳极表面少,故 而阳极不能正常溶解,会导致电镀铜表面产生不平而灰黑, 而在电镀区出现毛刺、针孔等;氯离子太多,在电场作用 下,氯离子会促进铜阳极溶解,并形成大量的氯化亚铜胶 体,最后形成铜粉,太多只能脱肛解决。
图形电镀工艺指导书
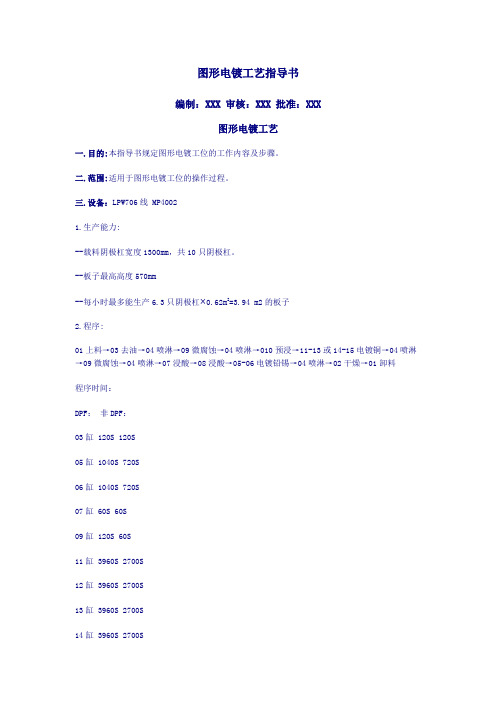
图形电镀工艺指导书编制:XXX审核:XXX 批准:XXX图形电镀工艺一.目的:本指导书规定图形电镀工位的工作内容及步骤。
二.范围:适用于图形电镀工位的操作过程。
三.设备:LPW706线 MP40021.生产能力:--载料阴极杠宽度1300mm,共10只阴极杠。
--板子最高高度570mm--每小时最多能生产6.3只阴极杠×0.62m2=3.94 m2的板子2.程序:01上料→03去油→04喷淋→09微腐蚀→04喷淋→010预浸→11-13或14-15电镀铜→04喷淋→09微腐蚀→04喷淋→07浸酸→08浸酸→05-06电镀铅锡→04喷淋→02干燥→01卸料程序时间:DPF:非DPF:03缸 120S 120S05缸 1040S 720S06缸 1040S 720S07缸 60S 60S09缸 120S 60S11缸 3960S 2700S12缸 3960S 2700S13缸 3960S 2700S14缸 3960S 2700S15缸 3960S 2700S对于特殊要求的型号,请查阅工艺卡片。
四.材料:4.1 去离子水(电导率<10us/cm PH:5.5-8)4.2 自来水4.3 硫酸(化学纯) H2SO4(C.P)4.4 硼酸(化学纯) H3BO3(C.P)4.5 氟硼酸 50% METEX HBF44.6 硫酸铜(化学纯) METEX CuSO4.H2O4.7 氟硼酸锡 50% METEX Sn(BF4)24.8 氟硼酸铅 50% METEX Pb(BF4)24.9 镀铜光亮剂 92414.10 镀铅锡光亮剂 LA14.11 镀铅锡光亮剂 LA24.12 镀铅锡光亮剂 LA34.13 微腐蚀剂 METEX G-4 MICROETCH4.14 去油溶液 METEX ACID CLEANER 7174.15 铜阳极(高纯度含磷0。
4-0。
65%)及阳极袋4.16 铅锡阳极(铅/锡 37/63)及阳极袋五.工艺与控制:5.1 溶液配制与控制(按工艺顺序排列)----槽03-去油(DEGREASING)配制容积:400L注入80%槽体积(去离子水) 320L。
图形电镀工艺
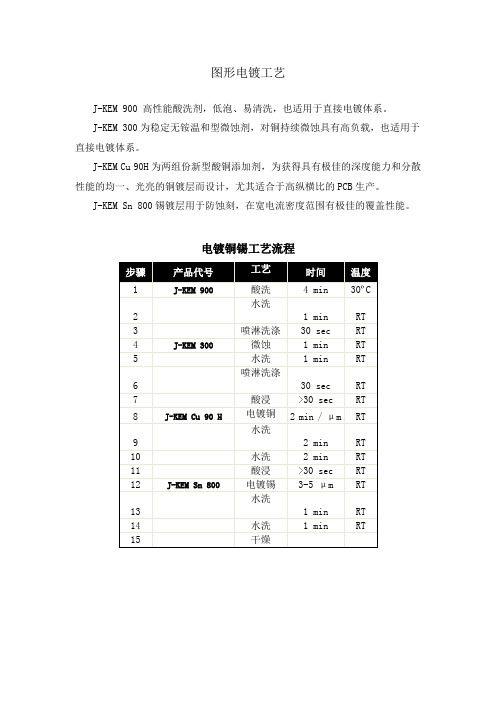
图形电镀工艺J-KEM 900 高性能酸洗剂,低泡、易清洗,也适用于直接电镀体系。
J-KEM 300为稳定无铵温和型微蚀剂,对铜持续微蚀具有高负载,也适用于直接电镀体系。
J-KEM Cu 90H为两组份新型酸铜添加剂,为获得具有极佳的深度能力和分散性能的均一、光亮的铜镀层而设计,尤其适合于高纵横比的PCB生产。
J-KEM Sn 800锡镀层用于防蚀刻,在宽电流密度范围有极佳的覆盖性能。
电镀铜锡工艺流程J-KEM 900酸洗剂J-KEM 900 酸洗剂是一种用于印刷电路板的酸性除油剂,产品具有两种功能:除油和酸洗。
该溶液具有超强的活性剂对铜板污垢有很强的去除能力;同时,由于其酸性,可清除铜表面的氧化物。
此外,此产品酸洗作用不会太强,避免对铜产生腐蚀。
因此,酸洗剂J-KEM 900也适合用于直接电镀线后。
工艺参数配制100L开缸液镀液维护每10 m2板面加入0.2 L J-KEM 900。
J-KEM 300 微蚀剂J-KEM 300微蚀剂可促进铜表面形成良好的附着力,通过去除表面活性剂的来防止污迹形成。
J-KEM 300微蚀剂不含铵,因此不会产生废水。
工艺条件配制100L开缸剂镀液维护每50 m2板面加入400g J-KEM 300 微蚀剂。
J-KEM Cu 90H电镀铜工艺J-KEM Cu 90H是一种最新酸铜体系,专为PCB获得均一、光亮铜沉积层而设计,此工艺具有极好深镀能力和分散性能,此镀铜层还具有极好的冶金性能和延展性。
J-KEM Cu 90H的特性和优点:• 体系电流密度范围从0.5至6 A /dm2;• 优越的深镀性能,可覆盖高纵横比板上所有CD范围;• 对复杂的图形设计有优越的表面分散性能。
• 优异的冶金特性。
镀液组成工艺条件配制1000 L开缸液1.加入400 L的去离子水,到彻底清洗的电镀槽中;2.缓慢加入185g 的化学级浓缩硫酸并搅拌;3.溶液冷却;4.加入75 kg CuSO4·5H2O;5.加入100个氯化钠;6.加入离子水到1000 L,并确保温度在20-30℃范围内;7.为获得最大的纯度,槽液应在0.2A/dm2,波纹阴极下工作4-5小时;8.加入5 L的J-KEM J-KEM Cu 90H C;9.加入2 L的J-KEM J-KEM Cu 90H A;10.增加电流至1A/dm2,让槽液工作1小时或以上(最多8小时);J-KEM Cu 90H已配制好,待用。
PCB电镀工艺介绍
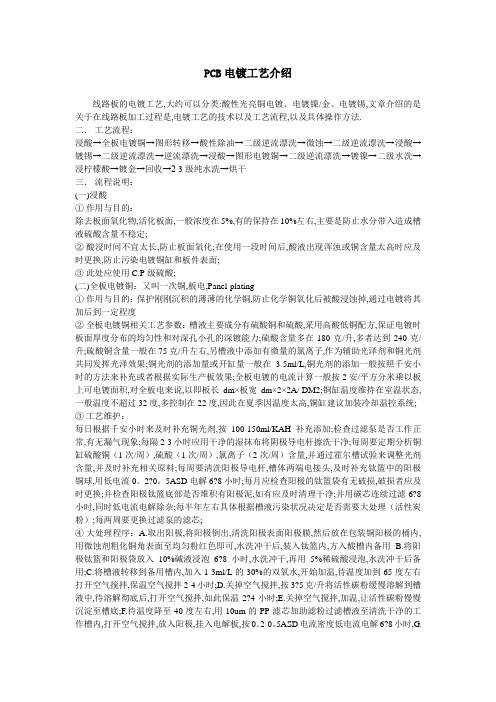
PCB电镀工艺介绍线路板的电镀工艺,大约可以分类:酸性光亮铜电镀、电镀镍/金、电镀锡,文章介绍的是关于在线路板加工过程是,电镀工艺的技术以及工艺流程,以及具体操作方法.二.工艺流程:浸酸→全板电镀铜→图形转移→酸性除油→二级逆流漂洗→微蚀→二级逆流漂洗→浸酸→镀锡→二级逆流漂洗→逆流漂洗→浸酸→图形电镀铜→二级逆流漂洗→镀镍→二级水洗→浸柠檬酸→镀金→回收→2-3级纯水洗→烘干三.流程说明:(一)浸酸①作用与目的:除去板面氧化物,活化板面,一般浓度在5%,有的保持在10%左右,主要是防止水分带入造成槽液硫酸含量不稳定;②酸浸时间不宜太长,防止板面氧化;在使用一段时间后,酸液出现浑浊或铜含量太高时应及时更换,防止污染电镀铜缸和板件表面;③此处应使用C.P级硫酸;(二)全板电镀铜:又叫一次铜,板电,Panel-plating①作用与目的:保护刚刚沉积的薄薄的化学铜,防止化学铜氧化后被酸浸蚀掉,通过电镀将其加后到一定程度②全板电镀铜相关工艺参数:槽液主要成分有硫酸铜和硫酸,采用高酸低铜配方,保证电镀时板面厚度分布的均匀性和对深孔小孔的深镀能力;硫酸含量多在180克/升,多者达到240克/升;硫酸铜含量一般在75克/升左右,另槽液中添加有微量的氯离子,作为辅助光泽剂和铜光剂共同发挥光泽效果;铜光剂的添加量或开缸量一般在3-5ml/L,铜光剂的添加一般按照千安小时的方法来补充或者根据实际生产板效果;全板电镀的电流计算一般按2安/平方分米乘以板上可电镀面积,对全板电来说,以即板长dm×板宽dm×2×2A/ DM2;铜缸温度维持在室温状态,一般温度不超过32度,多控制在22度,因此在夏季因温度太高,铜缸建议加装冷却温控系统;③工艺维护:每日根据千安小时来及时补充铜光剂,按100-150ml/KAH补充添加;检查过滤泵是否工作正常,有无漏气现象;每隔2-3小时应用干净的湿抹布将阴极导电杆擦洗干净;每周要定期分析铜缸硫酸铜(1次/周),硫酸(1次/周),氯离子(2次/周)含量,并通过霍尔槽试验来调整光剂含量,并及时补充相关原料;每周要清洗阳极导电杆,槽体两端电接头,及时补充钛篮中的阳极铜球,用低电流0。
PCB电镀工艺流程介绍

PCB电镀工艺介绍线路板的电镀工艺,大约可以分类:酸性光亮铜电镀、电镀镍/金、电镀锡,文章介绍的是关于在线路板加工过程是,电镀工艺的技术以及工艺流程,以及具体操作方法.二.工艺流程:浸酸→全板电镀铜→图形转移→酸性除油→二级逆流漂洗→微蚀→二级逆流漂洗→浸酸→镀锡→二级逆流漂洗→逆流漂洗→浸酸→图形电镀铜→二级逆流漂洗→镀镍→二级水洗→浸柠檬酸→镀金→回收→2-3级纯水洗→烘干三.流程说明:(一)浸酸①作用与目的:除去板面氧化物,活化板面,一般浓度在5%,有的保持在10%左右,主要是防止水分带入造成槽液硫酸含量不稳定;②酸浸时间不宜太长,防止板面氧化;在使用一段时间后,酸液出现浑浊或铜含量太高时应及时更换,防止污染电镀铜缸和板件表面;③此处应使用C.P级硫酸;(二)全板电镀铜:又叫一次铜,板电,Panel-plating①作用与目的:保护刚刚沉积的薄薄的化学铜,防止化学铜氧化后被酸浸蚀掉,通过电镀将其加后到一定程度②全板电镀铜相关工艺参数:槽液主要成分有硫酸铜和硫酸,采用高酸低铜配方,保证电镀时板面厚度分布的均匀性和对深孔小孔的深镀能力;硫酸含量多在180克/升,多者达到240克/升;硫酸铜含量一般在75克/升左右,另槽液中添加有微量的氯离子,作为辅助光泽剂和铜光剂共同发挥光泽效果;铜光剂的添加量或开缸量一般在3-5ml/L,铜光剂的添加一般按照千安小时的方法来补充或者根据实际生产板效果;全板电镀的电流计算一般按2安/平方分米乘以板上可电镀面积,对全板电来说,以即板长dm×板宽dm×2×2A/DM2;铜缸温度维持在室温状态,一般温度不超过32度,多控制在22度,因此在夏季因温度太高,铜缸建议加装冷却温控系统;③工艺维护:每日根据千安小时来及时补充铜光剂,按100-150ml/KAH补充添加;检查过滤泵是否工作正常,有无漏气现象;每隔2-3小时应用干净的湿抹布将阴极导电杆擦洗干净;每周要定期分析铜缸硫酸铜(1次/周),硫酸(1次/周),氯离子(2次/周)含量,并通过霍尔槽试验来调整光剂含量,并及时补充相关原料;每周要清洗阳极导电杆,槽体两端电接头,及时补充钛篮中的阳极铜球,用低电流0。
图形电镀工艺
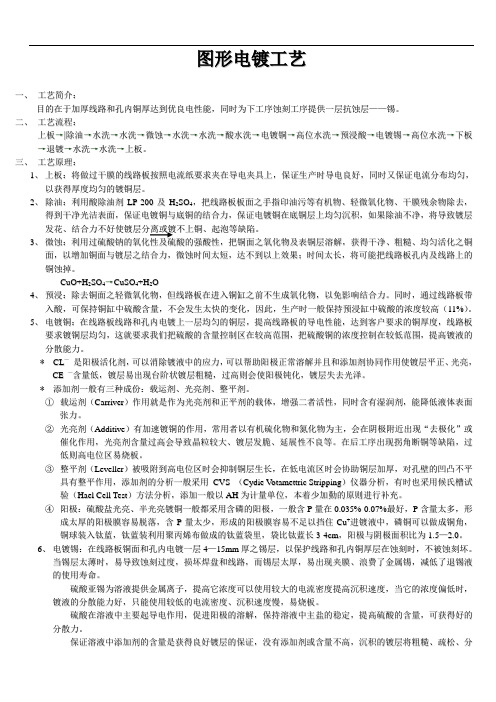
图形电镀工艺一、工艺简介:目的在于加厚线路和孔内铜厚达到优良电性能,同时为下工序蚀刻工序提供一层抗蚀层——锡。
二、工艺流程:上板→|除油→水洗→水洗→微蚀→水洗→水洗→酸水洗→电镀铜→高位水洗→预浸酸→电镀锡→高位水洗→下板→退镀→水洗→水洗→上板。
三、工艺原理:1、上板:将做过干膜的线路板按照电流纸要求夹在导电夹具上,保证生产时导电良好,同时又保证电流分布均匀,以获得厚度均匀的镀铜层。
2、除油:利用酸除油剂L P-200及H2S O4,把线路板板面之手指印油污等有机物、轻微氧化物、干膜残余物除去,得到干净光洁表面,保证电镀铜与底铜的结合力,保证电镀铜在底铜层上均匀沉积,如果除油不净,将导致镀层发花、结合力不好使镀层分离或镀不上铜、起泡等缺陷。
3、微蚀:利用过硫酸钠的氧化性及硫酸的强酸性,把铜面之氧化物及表铜层溶解,获得干净、粗糙、均匀活化之铜面,以增加铜面与镀层之结合力,微蚀时间太短,达不到以上效果;时间太长,将可能把线路板孔内及线路上的铜蚀掉。
C u O+H2S O4→C u S O4+H2O4、预浸:除去铜面之轻微氧化物,但线路板在进入铜缸之前不生成氧化物,以免影响结合力。
同时,通过线路板带入酸,可保持铜缸中硫酸含量,不会发生太快的变化,因此,生产时一般保持预浸缸中硫酸的浓度较高(11%)。
5、电镀铜:在线路板线路和孔内电镀上一层均匀的铜层,提高线路板的导电性能,达到客户要求的铜厚度,线路板要求镀铜层均匀,这就要求我们把硫酸的含量控制区在较高范围,把硫酸铜的浓度控制在较低范围,提高镀液的分散能力。
*C L—是阳极活化剂,可以消除镀液中的应力,可以帮助阳极正常溶解并且和添加剂协同作用使镀层平正、光亮,C E——含量低,镀层易出现台阶状镀层粗糙,过高则会使阳极钝化,镀层失去光泽。
*添加剂一般有三种成份:载运剂、光亮剂、整平剂。
①载运剂(C a r r i v e r)作用就是作为光亮剂和正平剂的载体,增强二者活性,同时含有湿润剂,能降低液体表面张力。
图形电镀和碱性蚀刻培训讲义

六、主要问题
6、水渍 原因:①电镀前脏水沾到板面 ②除油剂浓度高或水洗效果差,无 法去除残留除油剂 ③光剂不协调
六、主要问题
7、铜丝 原因:①打砂纸 ②光剂使用寿命已到 8、孔无铜 原因:①前工序漏下来 ②未镀上锡 9、烧板 原因:①一般是板落到浮桥外
七、特殊工艺流程
镀孔工艺:若孔较小或孔铜要求1.2 以上 ,面铜要求较薄,则 走镀孔工艺。
B、蚀刻——反应机理 、蚀刻 反应机理 事实上,许多的氨性蚀刻液产品都含有一价铜
离子的特殊配位基(一些复杂的溶剂),其作 用是降低一价铜离子(这些即是他们的产品具 有高反应能力的技术秘诀 ),可见一价铜离子的 影 响 是 不 小 的 。 将 一 价 铜 由 5000ppm 降 至 50ppm,蚀刻速率会提高一倍以上。 由于蚀刻反应过程中生成大量的一价铜离子, 又由于一价铜离子总是与氨的络合基紧紧的结 合在一起,所以保持其含量近于零是十分困难的。 通过大气中氧的作用将一价铜转换成二价铜可 以去除一价铜。用喷淋的方式可以达到上述目 的。
六、主要问题
4、针孔 原因:①打气不均匀,产生了微 气泡或无法赶走产生的H2 此四项会产生 ②过滤泵漏气 或功率太大 规则圆形凹陷 ③循环泵漏气 ④润湿剂不够 ⑤前工序在板面上留有残留物 ⑥铜缸太脏,需炭处理 ⑦板落浮桥外
六、主要问题
5、板面凹点 原因:①整平剂浓度较低达不到真整平 效果 ②润湿剂太低,无法去除因张力附 着的杂质和气泡 ③溶液太脏,张力加大
三、各缸药水成份和作用
_
成份③:Cl 作用:①与光剂共同作用,使板面光洁平 整; ②活化阳极浓度太低时,镀层光亮 性和整平性降低,太低时会产生 枝晶浓度太高时,跟光剂不足产 生的现象(如无光、粗糙等)一致
PCB图形电镀工艺流程

PCB图形电镀工艺流程PCB图形电镀是制造印制电路板时的重要工艺流程之一。
电镀工艺流程能够为PCB提供良好的导电性和耐腐蚀性,在电子产品中起到关键的作用。
下面将介绍一下PCB图形电镀的工艺流程。
首先,PCB进入电镀前会经过清洗工序,以去除表面污垢。
常用的清洗方式有化学清洗、喷洗清洗和超声波清洗等。
清洗工序的目的是为了保证电镀时的良好粘附性。
接下来,PCB会进入化学镀垫层的工序。
镀垫层的主要作用是增加PCB表面粘附力和电导性,以便更好地进行后续的电镀工艺。
常用的镀垫层材料有金、镍、锡等。
镀垫层工艺主要包括化学镀垫和电镀垫两种方式。
在化学镀垫工艺中,首先将金属盐溶液制备好,并调节好浓度和温度。
然后将PCB浸入溶液中,经过一段时间的处理,金属盐溶液中的金属离子会被还原成金属沉积在PCB表面。
最后再经过清洗和干燥等工序,形成均匀的金属薄层。
而电镀垫层工艺则是通过电化学的方式进行。
首先在PCB上涂覆一层金属催化剂,如钯金盐或铅盐等,然后将PCB浸入金属盐溶液中,通过电流作用,金属离子会被还原成金属沉积在PCB表面。
这种方法可以实现较厚的镀垫层。
完成了镀垫层工艺后,PCB会进入电镀层的工序。
电镀层主要是通过电化学方式,在PCB表面镀上一层金属保护层,以提高PCB的导电性和耐腐蚀性。
常用的电镀层材料有金、银、锡、铜等。
具体的电镀层工艺流程包括:首先是准备好金属盐溶液,调节好浓度和温度。
然后将PCB浸入溶液中,通过电流的作用,金属离子会被还原成金属离子在PCB表面沉积下来。
最后通过清洗和干燥等工序,形成均匀的电镀层。
最后,完成了上述工艺流程的PCB还需要进行检验和修复。
检验是为了确保PCB表面的镀层均匀且符合要求,常用的检验方法有厚度测量、锡膏检查、可焊性测试等。
如果发现镀层不符合要求,需要进行修复或重新进行电镀工序。
总之,PCB图形电镀是制造印制电路板的重要工艺流程之一。
通过化学镀垫和电镀垫两种方式,以及电化学的方式进行电镀层的制备,能够为PCB提供良好的导电性和耐腐蚀性。
图形电镀与蚀刻工序培训教材

酸浸 H2SO4
镀铜 CuSO4、Cl-、 H2SO4、光剂
操作温度:室温、操作时间:1- 去除轻微氧化及维 2min、 持药水浓度
操作温度: 20-28℃、镀铜时间: 加厚铜 40-90min
镀锡 SnSO4、H2SO4、操作温度: 20-28℃、镀锡时间: 镀锡为碱性蚀刻提 8-12min 光剂 供抗蚀层 退镀 HNO3 操作温度:室温、退镀时间: 14min 去除电镀夹具上的 镀铜
电镀培训教材
日期:2009、05、06
深圳市龙江实业有限公司
一、pcb工艺流程简介 开料-钻孔-沉铜-图形转移-图形电镀-(二钻) -蚀板(二钻)-阻焊-字符-(表面处理)-成 型--(抗氧化)-FQC-出货
深圳市龙江实业有限公司
二、 沉铜工艺流程 磨板 → 沉铜 → 板电→磨板
深圳市龙江实业有限公司
3、磨板参数: 酸洗:3~5%硫酸 磨刷电流:2.0~3.0A 高压水洗:8.0~10.0kg/cm2 烘干:85±5℃ 速度:2.5~3.5m/min 磨痕:10~16MM。 水洗压力:1.5~2.5kg/cm2
深圳市龙江实业有限公司
4、注意事项 A.戴手套双手放板,双手接板 b. 板与板间距大于3CM。 C.板电后生产板磨板后必须插架。 d.每两小时检查机器参数运转状况,做好 报表记录。
深圳市龙江实业有限公司
5、主要缺陷: 氧化、烘不干 1. 原因分析: 烘干段风刀堵塞 烘干段温度不足 磨板速度过快 2.解决方法: 清洁烘干段风刀 调整烘干段温度在作业指示 要求范围内 调整速度在作业指示范围内
深圳市龙江实业有限公司
三. 沉蚀刻 CuCl2 NH4Cl NH4· OH
比重:24.5±1.5 蚀掉非线路铜层 温度:45-55 ℃ PH:8.2-8.9 速度:1.0-5.0m/min 压力:上压力3.±0.50kg/cm2 下压力1.5±0.5kg/cm2
PCB图形电镀
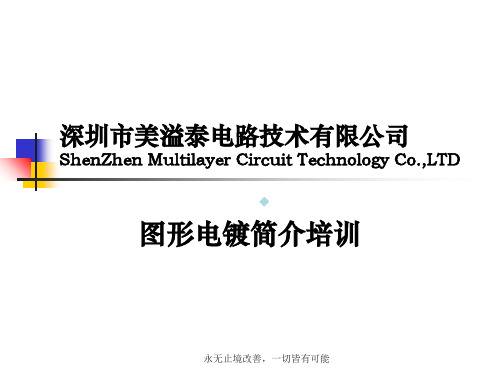
板面电镀镀 上的一层铜
P片
图形电镀工艺参数
缸名 酸性除油
微蚀 酸洗 电镀铜
电镀锡
使用物料
AC-22 NPS
H2SO4(CP) H2SO4(CP) CuS04.5H2SO4 H2SO4(AR)
HCL(浓) 铜光剂 SnSO4
缸体积
600L 300L 300L 300L 2000L 2000L 2000L 2000L 2000L
酸性镀铜的原理
因为在电镀过程中尽量避免一价铜离子的出现,因此采用 了含磷的铜阳极。
氯离子是阳极活化剂,帮助阳极溶解,并且和添加剂协同 作用使镀层光亮、整平。
若氯离子的浓度太低,会出现针孔、烧焦现象。 若氯离子太高,导致阳极钝化,使阳极上产生一层白色膜
且放出大量气泡,电极效率大大降低。
永无止境改善,一切皆有可能
可离场。
以上守则,希望各位学员共同遵守 谢谢合作!!!
永无止境改善,一切皆有可能
电镀原理
实现孔壁及线路厚度达到客户要求,保证有优良的导电性能.
电镀是在铜板的表面镀上一层铜,在含有金属铜离子的电镀液中,
在阴极和阳极施加直流电流,使带正电荷的金属离子在阴极表面接受
带负电荷的电子而变成金属原子沉积成为晶体结构。
镀铜
--实现孔壁及线路厚度达到客户要求,保证有 优良的导电性能.
镀锡
--在金属化孔内与板面线路上镀上一层厚度 的锡层抵抗蚀层,以确保蚀刻时线路上金属 化孔内的铜层受到保护.
永无止境改善,一切皆有可能
镀铜、镀锡截面图
图形电镀镀 上的一层铜
曝光菲林
(1) 镀铜
图形电镀镀 上的一层铜
(2) 镀锡
镀锡
永无止境改善,一切皆有可能
- 1、下载文档前请自行甄别文档内容的完整性,平台不提供额外的编辑、内容补充、找答案等附加服务。
- 2、"仅部分预览"的文档,不可在线预览部分如存在完整性等问题,可反馈申请退款(可完整预览的文档不适用该条件!)。
- 3、如文档侵犯您的权益,请联系客服反馈,我们会尽快为您处理(人工客服工作时间:9:00-18:30)。
永无止境改善,一切皆有可能
CuS04.5H2SO4
电镀铜 H2SO4(AR) HCL(浓) 铜光剂 SnSO4
2000L
2000L 2000L 2000L 2000L 2000L 2000L
75g/l
200ml/l 50ppm 4ml/l 30k/l 200ml/l 15ml/l
150㎏
400L 250ml 9L 50㎏ 180L 8L
(1) 镀铜
(2) 镀锡
永无止境改善,一切皆有可能
图形电镀工艺参数
缸名 酸性除油 微蚀 酸洗 使用物料 AC-22 NPS H2SO4(CP) H2SO4(CP) 缸体积 600L 300L 300L 300L 配制浓度 2.50% 50g/l 4% 0.60% 开缸用量 15L 15㎏ 12L 2L 工作时间 3-6分钟 40-60秒 2-5分钟 根据铜厚要 求以及电流 强度
酸性镀铜的原理
当溶液有足够硫酸及空气时,可以被氧化成Cu2+ 。 2 Cu+ +0.5O2 +2H+ = 2Cu2+ +H2O 但当溶液中的硫酸浓度不足时,会水解。 2 Cu+ +2H2O = 2Cu(OH) +2H+ 2Cu(OH)=Cu2O +H2O Cu2O沉积在阴极上,产生毛刺。 Cu+ 不稳定,还可以发生歧化反应: 2Cu+ = Cu2+ +Cu 生成的铜也会以电泳的方式沉积于镀层,产生铜粉、毛刺、 粗糙现象。
永无止境改善,一切皆有可能
镀液中各成分的作用
氯离子
酸性镀铜液中加入40-60mg/L的氯离子可以消除铜粉的。 如氯离子太少,会使氯化亚铜胶体吸附在阳极表面少,故 而阳极不能正常溶解,会导致电镀铜表面产生不平而灰黑, 而在电镀区出现毛刺、针孔等;氯离子太多,在电场作用 下,氯离子会促进铜阳极溶解,并形成大量的氯化亚铜胶 体,最后形成铜粉,太多只能脱肛解决。
永无止境改善,一切皆有可能
酸性镀铜的原理
在直流电压下会发生如下反应:
+
+
阴极
Cu PCB 镀 镀液 液 Cu
阳极
Cu2+ +2e= Cu Cu2+ +e = Cu+ Cu+ +e = Cu Cu - 2e= Cu2+
永无止境改善,一切皆有可能
电镀锡
H2SO4(AR) 锡光剂
10-15分钟
永无止境改善,一切皆有可能
镀液中各成分的作用
硫酸铜和硫酸 在镀铜液中,硫酸铜和硫酸是镀液的主要成分,若硫酸的 浓度高,则硫酸铜的浓度低,且镀液的导电率高。一般采 取“高酸低铜”的原则。 如果镀液中硫酸铜的浓度偏低,高电流区镀层易烧焦;若 硫酸铜浓度太高,镀液的分散能力和整平能力会降低。一 般情况下以供应商的参数75g/L为基准。 如果镀液中硫酸浓度低,则溶液的导电性能差,镀液的分 散能力差;浓度太高,会降低铜离子的迁移率,效率反而 会降低。
深圳市美溢泰电路技术有限公司
ShenZhen Multilayer Circuit Technology Co.,LTD
图形电镀简介培训
永无止境改善,一切皆有可能
课堂守则
请将手机调到震动状态。 请勿在上课期间,随意进出,以免影响其他同事。 请勿交头接耳、大声喧哗。 如有特殊事情,在征得培训导师的同意的情况下,方 可离场。
+
+
Cu 镀液
PCB
镀液
Cu
永无止境改善,一切皆有可能
图形电镀工艺流程
除油 微蚀 酸洗
--清除板面氧化层及油污,保证板面清洁无氧
化现象.
--微蚀粗化铜表面,保证电镀层之良好的结合
力.
--减轻前处理清洗好,对铜、锡缸溶液染污并
保持铜锡缸中硫酸含量稳定
永无止境改善,一切皆有可能
酸性镀铜的原理
因为在电镀过程中尽量避免一价铜离子的出现,因此采用 了含磷的铜阳极。 氯离子是阳极活化剂,帮助阳极溶解,并且和添加剂协同 作用使镀层光亮、整平。 若氯离子的浓度太低,会出现针孔、烧焦现象。 若氯离子太高,导致阳极钝化,使阳极上产生一层白色膜 且放出大量气泡,电极效率大大降低。
原因分析
1.镀液过滤不良; 2. 硫酸浓度过低; 3.电流过大; 4. 铜光剂失调:(哈氏槽实验) 5.阳极含磷量不对(用含磷0.03-0.07%的阳极)
永无止境改善,一切皆有可能
图形电镀常见故障分析
3. 问题描述
镀层有麻点、针孔。
原因分析
1.前处理不干净; 2.镀液有油污(活性碳处理) 3.搅拌不够 4.铜光剂不足 5.润湿剂不足
永无止境改善,一切皆有可能
图形电镀常见故障分析
4. 问题描述
低电流区镀层发暗
原因分析
硫酸含量低 铜浓度高 金属杂质污染 光亮剂浓度不当或选择不当
永无止境改善,一切皆有可能
图形电镀常见故障分析
5. 问题描述
孔周围发暗
原因分析
铜光剂过量 杂质污染引起周围镀层厚度不足 搅拌不当
永无止境改善,一切皆有可能
图形电镀常见故障分析
1. 问题描述
镀层烧焦
原因分析
1.铜浓度太低; 2. 阴极电流密度过大; 3.液体温度太低; 4. 铜光剂不足:(哈氏槽实验) 5.阳极过长(阳极比阴极短5-7mm)永无止境改善,一切皆有可能
图形电镀常见故障分析
2. 问题描述
镀层粗糙有铜粉。
以上守则,希望各位学员共同遵守
永无止境改善,一切皆有可能
谢谢合作!!!
电镀原理
实现孔壁及线路厚度达到客户要求,保证有优良的导电性能. 电镀是在铜板的表面镀上一层铜,在含有金属铜离子的电镀液中, 在阴极和阳极施加直流电流,使带正电荷的金属离子在阴极表面接受 带负电荷的电子而变成金属原子沉积成为晶体结构。
永无止境改善,一切皆有可能
图形电镀工艺流程
镀铜
--实现孔壁及线路厚度达到客户要求,保证有
优良的导电性能.
镀锡
--在金属化孔内与板面线路上镀上一层厚度
的锡层抵抗蚀层,以确保蚀刻时线路上金属 化孔内的铜层受到保护.
永无止境改善,一切皆有可能
镀铜、镀锡截面图
图形电镀镀 上的一层铜 曝光菲林 板面电镀镀 上的一层铜 P片 图形电镀镀 上的一层铜 镀锡
永无止境改善,一切皆有可能
操作条件的影响
1. 温度
温度对镀液性能影响很大,温度升高,导致镀层结晶粗糙, 板材亮度偏低;温度偏低,高电流区容易烧焦。最好控制 在20-30℃. 2. 电流密度
提高电流密度,可以提高镀层的沉积速率,因此在保证质 量的前提下,尽量使用较高的电流密度。一般操作时平均 电流密度为1.5-3A/dm2 。