PCB电镀工艺介绍
PCB电镀工艺介绍

可编写可更正PCB电镀工艺介绍线路板的电镀工艺, 大体可以分类 : 酸性光明铜电镀、电镀镍/金、电镀锡,文章介绍的是关于在线路板加工过程是, 电镀工艺的技术以及工艺流程, 以及详尽操作方法.二.工艺流程:浸酸→全板电镀铜→图形转移→酸性除油→二级逆流漂洗→微蚀→二级逆流漂洗→浸酸→镀锡→二级逆流漂洗→逆流漂洗→浸酸→图形电镀铜→二级逆流漂洗→镀镍→二级水洗→浸柠檬酸→镀金→回收→2-3 级纯水洗→烘干三.流程说明:(一)浸酸①作用与目的:除去板面氧化物, 活化板面 , 一般浓度在5%,有的保持在10%左右 , 主若是防范水分带入造成槽液硫酸含量不牢固;②酸浸时间不宜太长, 防范板面氧化; 在使用一段时间后, 酸液出现浑浊或铜含量太高时应及时更换 , 防范污染电镀铜缸和板件表面;③此处应使用级硫酸;( 二 ) 全板电镀铜:又叫一次铜, 板电 ,Panel-plating①作用与目的:保护方才积聚的薄薄的化学铜, 防范化学铜氧化后被酸浸蚀掉, 经过电镀将其加后到必然程度② 全板电镀铜相关工艺参数:槽液主要成分有硫酸铜和硫酸, 采用高酸低铜配方 , 保证电镀时板面厚度分布的均匀性和对深孔小孔的深镀能力; 硫酸含量多在180 克/ 升 , 多者到达240 克 / 升 ; 硫酸铜含量一般在75 克 / 升左右 , 另槽液中增加有微量的氯离子, 作为辅助光彩剂和铜光剂共同发挥光彩收效; 铜光剂的增加量或开缸量一般在3-5ml/L,铜光剂的增加一般依照千安小时的方法来补充也许依照实质生产板收效; 全板电镀的电流计算一般按 2 安/平方分米乘以板上可电镀面积, 对全板电来说 , 以即板长 dm×板宽 dm×2×2A/DM2;铜缸温度保持在室温状态 , 一般温度不高出 32 度 , 多控制在22 度 , 因此在夏季因温度太高, 铜缸建议加装冷却温控系统 ;1③工艺保护:每日依照千安小时来及时补充铜光剂, 按 100-150ml/KAH 补充增加 ; 检查过滤泵可否工作正常 , 有无漏气现象 ; 每隔 2-3 小时应用干净的湿抹布将阴极导电杆擦洗干净; 每周要如期解析铜缸硫酸铜〔 1 次/周〕, 硫酸〔 1次/ 周〕 , 氯离子〔 2次 / 周〕含量 , 并经过霍尔槽试验来调整光剂含量 , 并及时补充相关原料; 每周要冲刷阳极导电杆 , 槽体两端电接头 , 及时补充钛篮中的阳极铜球, 用低电流 0。
PCB电镀工艺介绍
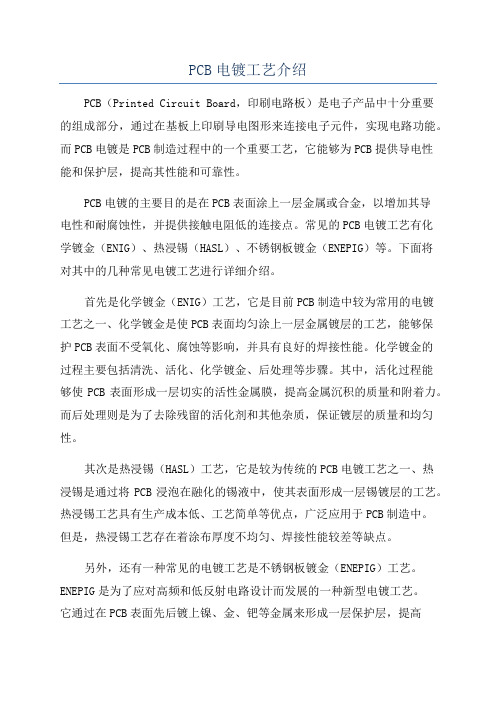
PCB电镀工艺介绍PCB(Printed Circuit Board,印刷电路板)是电子产品中十分重要的组成部分,通过在基板上印刷导电图形来连接电子元件,实现电路功能。
而PCB电镀是PCB制造过程中的一个重要工艺,它能够为PCB提供导电性能和保护层,提高其性能和可靠性。
PCB电镀的主要目的是在PCB表面涂上一层金属或合金,以增加其导电性和耐腐蚀性,并提供接触电阻低的连接点。
常见的PCB电镀工艺有化学镀金(ENIG)、热浸锡(HASL)、不锈钢板镀金(ENEPIG)等。
下面将对其中的几种常见电镀工艺进行详细介绍。
首先是化学镀金(ENIG)工艺,它是目前PCB制造中较为常用的电镀工艺之一、化学镀金是使PCB表面均匀涂上一层金属镀层的工艺,能够保护PCB表面不受氧化、腐蚀等影响,并具有良好的焊接性能。
化学镀金的过程主要包括清洗、活化、化学镀金、后处理等步骤。
其中,活化过程能够使PCB表面形成一层切实的活性金属膜,提高金属沉积的质量和附着力。
而后处理则是为了去除残留的活化剂和其他杂质,保证镀层的质量和均匀性。
其次是热浸锡(HASL)工艺,它是较为传统的PCB电镀工艺之一、热浸锡是通过将PCB浸泡在融化的锡液中,使其表面形成一层锡镀层的工艺。
热浸锡工艺具有生产成本低、工艺简单等优点,广泛应用于PCB制造中。
但是,热浸锡工艺存在着涂布厚度不均匀、焊接性能较差等缺点。
另外,还有一种常见的电镀工艺是不锈钢板镀金(ENEPIG)工艺。
ENEPIG是为了应对高频和低反射电路设计而发展的一种新型电镀工艺。
它通过在PCB表面先后镀上镍、金、钯等金属来形成一层保护层,提高PCB的可靠性和耐腐蚀性。
ENEPIG工艺具有良好的焊接性能、热稳定性和阻焊层附着力,非常适合于高频电路和复杂设计的PCB。
除了上述介绍的几种电镀工艺外,还有很多其他的电镀工艺,例如有机覆盖层镀金(OSIG)、沉金(ENIG)等。
每种电镀工艺都有各自的特点和适用范围,根据PCB设计的要求和产品的特性选择合适的电镀工艺非常关键。
PCB电镀铜锡工艺资料
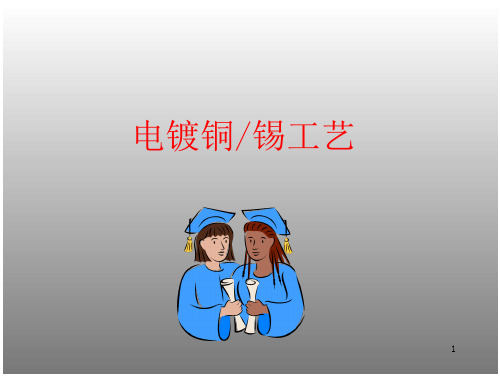
34
电镀铜溶液的控制
n 赫尔槽试验(Hull Cell Test)
n仅高电流密度区烧焦,试片的其它区域仍然正常----Copper Gleam 125T-2(CH) Additive 低 n改正方法:添加1ml/l Copper Gleam 125T-2(CH) Additive
: 濃度太低,Байду номын сангаас液導電性差,鍍液分 散能力差。
濃度太高,降低Cu2+的遷移率,電流 效率反而降低,❹對銅鍍層的延伸 率不利。
: 濃度太低,鍍層出現台階狀的粗糙 鍍層,易出現針孔和燒焦;濃度太 高,導致陽極鈍化,鍍層失去光澤 。
: (後面專題介紹)
11
操作條件對酸性鍍銅效果的影響
溫度
溫度升高,電極反應速度加快,允許電流密度提高,鍍 層沉積速度加快,但加速添加劑分解會增加添加劑消耗,鍍層結 晶粗糙,亮度降低。
31
电镀铜溶液的控制
n 赫尔槽试验 (Hull Cell Test)
阴极-
阳极+
32
电镀铜溶液的控制
n 赫尔槽试验(Hull Cell Test)参数
n — 电流: 2A n — 时间: 10分钟 n — 搅拌: 空气搅拌 n — 温度: 室温
33
电镀铜溶液的控制
n 赫尔槽试验(Hull Cell Test)
28
电镀铜溶液和电镀线的评价
n 热冲击测试
测试步骤
(1) 裁板16""x18"’ (2) 进行钻孔; (3) 经电镀前处理磨刷; (4) Desmear + PTH + 电镀; (5) 经电镀后处理的板清洗烘干; (6) 每片板裁上、中、下3小片100mm x 100mm测试板;
pcb电镀锡工艺
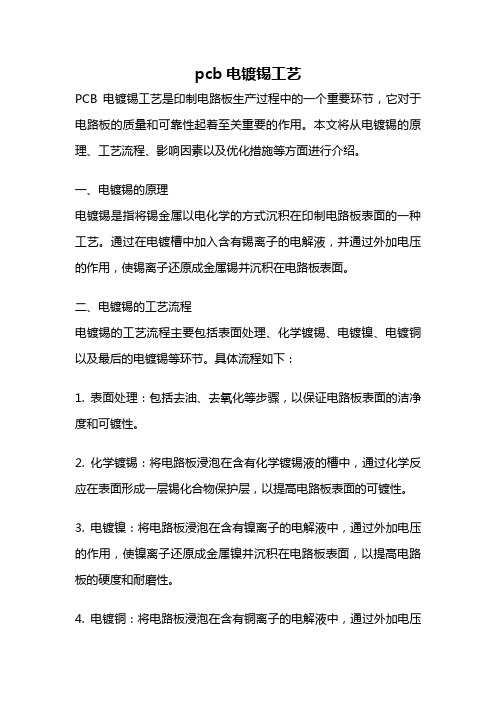
pcb电镀锡工艺PCB电镀锡工艺是印制电路板生产过程中的一个重要环节,它对于电路板的质量和可靠性起着至关重要的作用。
本文将从电镀锡的原理、工艺流程、影响因素以及优化措施等方面进行介绍。
一、电镀锡的原理电镀锡是指将锡金属以电化学的方式沉积在印制电路板表面的一种工艺。
通过在电镀槽中加入含有锡离子的电解液,并通过外加电压的作用,使锡离子还原成金属锡并沉积在电路板表面。
二、电镀锡的工艺流程电镀锡的工艺流程主要包括表面处理、化学镀锡、电镀镍、电镀铜以及最后的电镀锡等环节。
具体流程如下:1. 表面处理:包括去油、去氧化等步骤,以保证电路板表面的洁净度和可镀性。
2. 化学镀锡:将电路板浸泡在含有化学镀锡液的槽中,通过化学反应在表面形成一层锡化合物保护层,以提高电路板表面的可镀性。
3. 电镀镍:将电路板浸泡在含有镍离子的电解液中,通过外加电压的作用,使镍离子还原成金属镍并沉积在电路板表面,以提高电路板的硬度和耐磨性。
4. 电镀铜:将电路板浸泡在含有铜离子的电解液中,通过外加电压的作用,使铜离子还原成金属铜并沉积在电路板表面,以增加电路板的导电性和连接性。
5. 电镀锡:最后一步是将电路板浸泡在含有锡离子的电解液中,通过外加电压的作用,使锡离子还原成金属锡并沉积在电路板表面,以形成一层保护层,提高电路板的耐腐蚀性和可焊性。
三、电镀锡的影响因素电镀锡的质量和效果受到多种因素的影响,主要包括电解液的成分和浓度、电镀温度、电镀时间、电流密度以及电解液的搅拌等。
1. 电解液的成分和浓度:电解液的成分和浓度直接影响着电镀锡的质量和均匀性。
合理选择电解液的成分和浓度可以提高电镀锡的质量。
2. 电镀温度:电镀温度对电镀锡的速度和均匀性有着重要的影响。
通常情况下,较高的温度可以加快电镀速度,但过高的温度会导致锡离子的过度扩散,影响电镀锡的均匀性。
3. 电镀时间:电镀时间决定了电镀锡的厚度,过长或过短的电镀时间都会影响电镀锡的质量。
PCB电镀焊料(锡铅合金)工艺介绍

1.作用和特性焊料(60%)的锡和40%的铅)镀层应具有双重目的。
它既用来作为金属抗蚀层,也用来作为以后要焊接元、器件的可焊性基体。
因为这种镀出的合金近于锡/铅的低共熔点(63的锡/37的铅,熔点为367℉);因此它是很容易热熔的,这就使得它很可焊。
大多数PCB制造厂商,要电镀金属化孔。
当为了保证焊接一致而要求合金成分不变时,就采用焊料镀层。
美国军用技术规范"MIL-P-81728,电镀锡-铅"指出:除非另有规定,电子元、器件(PCB,尤其是那些用金属化孔互连的、接线柱和空心铆钉的)用的锡/铅镀层的厚度,当以至少相隔0.1 英寸的四点测量时,平均最小厚度应为0.0003英寸(0.3毫英寸)MIL-STD-202的方法208叙述了一个用来确定镀层可焊性的机理。
要得到认可,测试时,镀层应很容易和完全被焊料所覆盖。
电镀锡铅金一般采用氟硼酸盐镀液,这与镀液具有的成份简单、阴极和阳极电流效率高,可以获得含锡、铅为任何比例的合金镀层有关。
锡铅合金电镀镀液主要由氟硼酸锡、氟硼酸铅、氟硼酸和添加剂所组成。
金属的氟硼酸盐可以买到浓液,然后再用水稀释到所要求的金属含量。
下表列出了可以买到的浓缩液的金属含量,配成镀液的各种含量列在下表中,其中有金属化孔电镀用的高分散性镀液配方。
1)镀液各组分的作用:氟硼酸亚锡和氟硼酸铅是金属的来源。
镀液金属组分的变化,将会影响合金淀积层的成分。
锡和铅金属浓液的组成焊料(60%Sn,40%Pb)电镀槽液的技术规范配制100加仑标准槽液先在热水中溶解硼酸,再加到镀槽中。
在冷水中先使胨溶胀,然后将水加热,同时强力搅拌。
应先将氟硼酸加到水中,然后再加入硼酸和金属盐浓液。
标准槽液的组成配制高分散性槽液配方操作条件高分散性槽液配方:这种镀液具有分散能力高、覆盖能力好、镀液成份简单、维护方便,成本低,热熔时的润湿性能好等伏点。
缺点是镀层较软,易在生产过程中划痕。
通过热熔可以改变晶体结构,提高镀层的抗蚀性能。
pcb镀金常用工艺
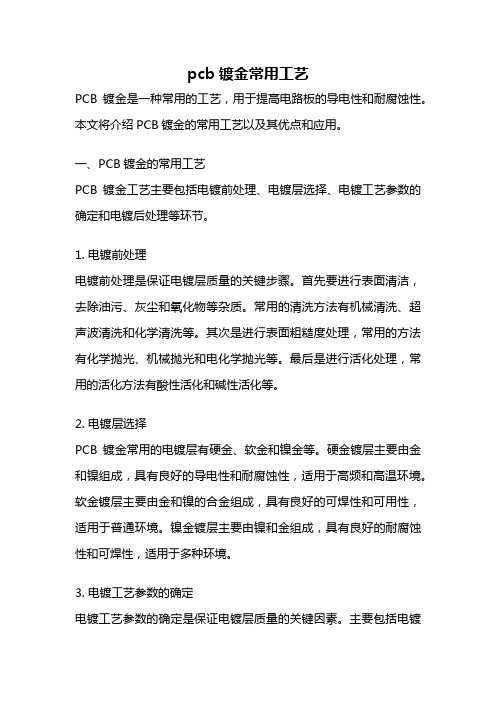
pcb镀金常用工艺PCB镀金是一种常用的工艺,用于提高电路板的导电性和耐腐蚀性。
本文将介绍PCB镀金的常用工艺以及其优点和应用。
一、PCB镀金的常用工艺PCB镀金工艺主要包括电镀前处理、电镀层选择、电镀工艺参数的确定和电镀后处理等环节。
1. 电镀前处理电镀前处理是保证电镀层质量的关键步骤。
首先要进行表面清洁,去除油污、灰尘和氧化物等杂质。
常用的清洗方法有机械清洗、超声波清洗和化学清洗等。
其次是进行表面粗糙度处理,常用的方法有化学抛光、机械抛光和电化学抛光等。
最后是进行活化处理,常用的活化方法有酸性活化和碱性活化等。
2. 电镀层选择PCB镀金常用的电镀层有硬金、软金和镍金等。
硬金镀层主要由金和镍组成,具有良好的导电性和耐腐蚀性,适用于高频和高温环境。
软金镀层主要由金和镍的合金组成,具有良好的可焊性和可用性,适用于普通环境。
镍金镀层主要由镍和金组成,具有良好的耐腐蚀性和可焊性,适用于多种环境。
3. 电镀工艺参数的确定电镀工艺参数的确定是保证电镀层质量的关键因素。
主要包括电镀液的成分和浓度、电流密度、电镀时间和温度等。
电镀液的成分和浓度应根据不同的电镀层选择确定。
电流密度和电镀时间应根据电镀层的厚度和均匀性要求确定。
温度的控制对电镀层的质量也有重要影响,通常要求在一定的范围内保持恒定。
4. 电镀后处理电镀后处理是保证电镀层质量的重要环节。
主要包括清洗、干燥和包装等。
清洗的目的是去除电镀液残留物和杂质,常用的方法有水洗、酸洗和碱洗等。
干燥的目的是除去水分,常用的方法有自然干燥、热风干燥和吸湿剂干燥等。
包装的目的是保护电镀层,常用的方法有真空包装、泡沫包装和气密包装等。
二、PCB镀金的优点PCB镀金具有以下优点:1. 提高导电性:金属电镀层能够提高电路板的导电性,降低导电阻抗,提高信号传输效率。
2. 增强耐腐蚀性:金属电镀层能够有效防止电路板受到氧化、腐蚀和污染等环境因素的侵蚀,延长电路板的使用寿命。
3. 增加可焊性:金属电镀层能够提高电路板与焊接材料之间的附着力,增加焊接的牢固度和可靠性。
PCB电镀工艺与流程

PCB电镀工艺与流程PCB(Printed Circuit Board)电镀工艺是指将金属薄膜通过一系列的化学和物理过程沉积在PCB上,来实现金属层的制备和保护。
PCB电镀工艺的主要流程可分为预处理、化学镀金、沉金镍、焊锡覆盖、化学抛光和后处理等环节。
首先,预处理是PCB板表面准备工作的开始。
主要包括去油污、去氧化、去除残留树脂、去除脱脂剂等。
这一步的目的是确保PCB表面干净,为后续的化学镀金提供良好的基础。
常用的处理方法包括碱性清洗、酸洗、水洗等。
接下来是化学镀金过程。
一般采用的金属有银、镍、金等。
在该过程中,通过电解法将金属离子沉积在PCB表面,形成金属涂层。
首先,在PCB表面加上一层薄膜以保护其他区域不被沉积金属。
然后,将PCB浸入金属离子溶液中,通过施加电压促进金属离子在PCB表面沉积成金属层。
镀金层的厚度可以通过控制电流密度和时间来调节。
沉金镍过程是为了提高PCB的耐腐蚀性和导电性能。
镀金层主要是金属镍和金。
镀金层能够提高PCB板的抗氧化能力,并增加PCB板与焊接材料的附着力。
这一步的工艺较为复杂,包括化学沉积、电解沉积和后处理等。
然后是焊锡覆盖过程。
焊锡覆盖是为了在PCB表面形成一层锡层,用于焊接元件的连接。
常用的焊接方法有浪涂法、喷涂法和喷锡法等。
在这个过程中,需要在PCB表面形成一层均匀且可焊接的锡层,以提供良好的焊接条件。
化学抛光过程是为了提高PCB表面的光洁度和平整度。
主要通过机械研磨和化学蚀刻等方法,去除PCB表面的不均匀性和氧化层,以保证PCB板的光洁度,并提高PCB表面的附着力。
最后是后处理过程。
主要包括PCB板的清洗、干燥和包装等。
这一步是为了去除电镀过程中的残留物,保证PCB的质量和稳定性。
总结起来,PCB电镀工艺是将金属薄膜沉积在PCB板上的过程,通过一系列的化学和物理过程实现。
工艺流程包括预处理、化学镀金、沉金镍、焊锡覆盖、化学抛光和后处理等环节。
每个环节都是为了实现PCB板的保护和金属层的制备,以提高PCB的性能和可靠性。
PCB电镀镍工艺介绍及故障原因与排除
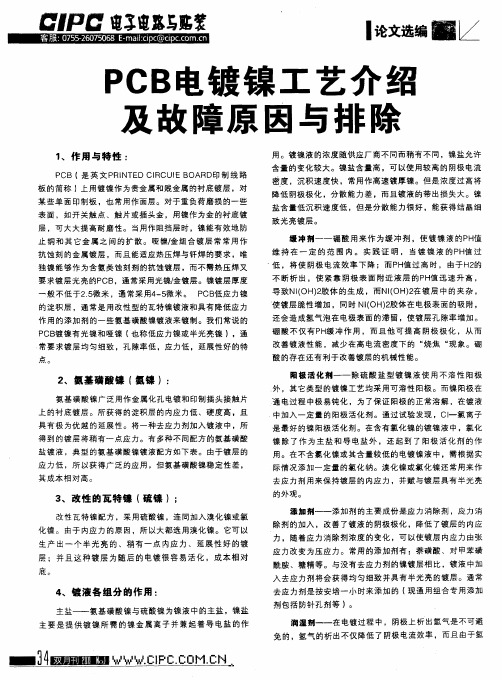
板 的简 称 】上 用镀 镍 作 为贵金 属 和贱金 属 的衬底 镀 层 ,对 某 些单 面 印制 板 ,也 常 用作 面层 。对 于重 负荷 磨损 的一 些
表 面 ,如 开关 触 点 、触 片或 插头 金 ,用镍作 为 金 的衬底 镀
密度 ,沉积速度快 。常用作高速镀厚镍。但是浓度过高将
降低 阴极极 化 ,分 散 能 力差 ,而 且镀 液 的带 出 损失 大 。镍 盐 含量 低沉 积 速 度低 ,但 是分 散 能 力很 好 ,能 获得 结 晶细
2 、氨 基 磺 酸镍 ( 氨镍 ):
氨 基磺 酸镍 广 泛 用作 金属 化孔 电镀 和 印制插 头 接触 片
阳 极 活 化 剂一 一 除 硫 酸 盐 型 镀 镍 液使 用 不 溶 性 阳极
外 ,其 它类 型 的镀 镍 工艺 均采 用可 溶 性 阳极 。而 镍 阳极 在 通 电过 程 中极 易钝 化 ,为 了保 证 阳极 的正 常溶解 。在 镀 液 中 加入 一定 量 的 阳极 活化 剂 。通 过试 验 发现 ,CI 氯 离 子 -
E分析一 一 镀 液应 该用 工艺 控 制所 规定 的工 艺规 程 的 )
要 点 ,定期 分析 镀 液组 分 与赫 尔槽试 验 ,根 据所 得参 数指 导 生产 部 门调节 镀 液各参 数 。 F 搅 拌一 一 镀 镍 过 程 与其 它 电镀 过 程 一 样 ,搅 拌 的 )
目的是 为 了加速 传 质过 程 ,以降低 浓度 变化 ,提 高允 许使
的淀积 层 ,通 常 是 用 改性型 的瓦 特镍 镀 液和具 有 降低 应 力 作 用 的添 加 剂 的一 些氨 基磺 酸 镍镀 液来 镀制 。我 们 常说 的 P 镀 镍 有光 镍 和 哑镍 ( 称低 应 力镍 或半 光亮 镍 ),通 CB 也 常要 求镀 层 均匀 细致 。孔 隙率低 。应 力低 。延展 性好 的 特
- 1、下载文档前请自行甄别文档内容的完整性,平台不提供额外的编辑、内容补充、找答案等附加服务。
- 2、"仅部分预览"的文档,不可在线预览部分如存在完整性等问题,可反馈申请退款(可完整预览的文档不适用该条件!)。
- 3、如文档侵犯您的权益,请联系客服反馈,我们会尽快为您处理(人工客服工作时间:9:00-18:30)。
PCB电镀工艺介绍线路板的电镀工艺,大约可以分类:酸性光亮铜电镀、电镀镍/金、电镀锡,文章介绍的是关于在线路板加工过程是,电镀工艺的技术以及工艺流程,以及具体操作方法.二.工艺流程:浸酸→全板电镀铜→图形转移→酸性除油→二级逆流漂洗→微蚀→二级逆流漂洗→浸酸→镀锡→二级逆流漂洗→逆流漂洗→浸酸→图形电镀铜→二级逆流漂洗→镀镍→二级水洗→浸柠檬酸→镀金→回收→2-3级纯水洗→烘干三.流程说明:(一)浸酸①作用与目的:除去板面氧化物,活化板面,一般浓度在5%,有的保持在10%左右,主要是防止水分带入造成槽液硫酸含量不稳定;②酸浸时间不宜太长,防止板面氧化;在使用一段时间后,酸液出现浑浊或铜含量太高时应及时更换,防止污染电镀铜缸和板件表面;③此处应使用C.P级硫酸;(二)全板电镀铜:又叫一次铜,板电,Panel-plating①作用与目的:保护刚刚沉积的薄薄的化学铜,防止化学铜氧化后被酸浸蚀掉,通过电镀将其加后到一定程度②全板电镀铜相关工艺参数:槽液主要成分有硫酸铜和硫酸,采用高酸低铜配方,保证电镀时板面厚度分布的均匀性和对深孔小孔的深镀能力;硫酸含量多在180克/升,多者达到240克/升;硫酸铜含量一般在75克/升左右,另槽液中添加有微量的氯离子,作为辅助光泽剂和铜光剂共同发挥光泽效果;铜光剂的添加量或开缸量一般在3-5ml/L,铜光剂的添加一般按照千安小时的方法来补充或者根据实际生产板效果;全板电镀的电流计算一般按2安/平方分米乘以板上可电镀面积,对全板电来说,以即板长dm×板宽dm×2×2A/ DM2;铜缸温度维持在室温状态,一般温度不超过32度,多控制在22度,因此在夏季因温度太高,铜缸建议加装冷却温控系统;③工艺维护:每日根据千安小时来及时补充铜光剂,按100-150ml/KAH补充添加;检查过滤泵是否工作正常,有无漏气现象;每隔2-3小时应用干净的湿抹布将阴极导电杆擦洗干净;每周要定期分析铜缸硫酸铜(1次/周),硫酸(1次/周),氯离子(2次/周)含量,并通过霍尔槽试验来调整光剂含量,并及时补充相关原料;每周要清洗阳极导电杆,槽体两端电接头,及时补充钛篮中的阳极铜球,用低电流0。
2?0。
5ASD电解6?8小时;每月应检查阳极的钛篮袋有无破损,破损者应及时更换;并检查阳极钛篮底部是否堆积有阳极泥,如有应及时清理干净;并用碳芯连续过滤6?8小时,同时低电流电解除杂;每半年左右具体根据槽液污染状况决定是否需要大处理(活性炭粉);每两周要更换过滤泵的滤芯;④大处理程序:A.取出阳极,将阳极倒出,清洗阳极表面阳极膜,然后放在包装铜阳极的桶内,用微蚀剂粗化铜角表面至均匀粉红色即可,水洗冲干后,装入钛篮内,方入酸槽内备用 B.将阳极钛篮和阳极袋放入10%碱液浸泡6?8小时,水洗冲干,再用5%稀硫酸浸泡,水洗冲干后备用;C.将槽液转移到备用槽内,加入1-3ml/L的30%的双氧水,开始加温,待温度加到65度左右打开空气搅拌,保温空气搅拌2-4小时;D.关掉空气搅拌,按3?5克/升将活性碳粉缓慢溶解到槽液中,待溶解彻底后,打开空气搅拌,如此保温2?4小时;E.关掉空气搅拌,加温,让活性碳粉慢慢沉淀至槽底;F.待温度降至40度左右,用10um的PP滤芯加助滤粉过滤槽液至清洗干净的工作槽内,打开空气搅拌,放入阳极,挂入电解板,按0。
2-0。
5ASD电流密度低电流电解6?8小时,G.经化验分析,调整槽中的硫酸,硫酸铜,氯离子含量至正常操作范围内;根据霍尔槽试验结果补充光剂;H.待电解板板面颜色均匀后,即可停止电解,然后按1-1。
5ASD的电流密度进行电解生膜处理1-2小时,待阳极上生成一层均匀致密附着力良好的黑色磷膜即可;I.试镀OK.即可;⑤阳极铜球内含有0。
3?0。
6%的磷,主要目的是降低阳极溶解效率,减少铜粉的产生;⑥补充药品时,如添加量较大如硫酸铜,硫酸时;添加后应低电流电解一下;补加硫酸时应注意安全,补加量较大时(10升以上)应分几次缓慢补加;否则会造成槽液温度过高,光剂分解加快,污染槽液;⑦氯离子的补加应特别注意,因为氯离子含量特别低(30-90ppm),补加时一定要用量筒或量杯称量准确后方可添加;1ml盐酸含氯离子约385ppm,⑧药品添加计算公式:硫酸铜(单位:公斤)=(75-X)×槽体积(升)/1000硫酸(单位:升)=(10%-X)g/L×槽体积(升)或(单位:升)=(180-X)g/L×槽体积(升)/1840盐酸(单位:ml)=(60-X)ppm×槽体积(升)/385(三)酸性除油①目的与作用:除去线路铜面上的氧化物,油墨残膜余胶,保证一次铜与图形电镀铜或镍之间的结合力②记住此处使用酸性除油剂,为何不是用碱性除油剂且碱性除油剂除油效果较酸性除油剂更好?主要因为图形油墨不耐碱,会损坏图形线路,故图形电镀前只能使用酸性除油剂。
③生产时只需控制除油剂浓度和时间即可,除油剂浓度在10%左右,时间保证在6分钟,时间稍长不会有不良影响;槽液使用更换也是按照15平米/升工作液,补充添加按照100平米0。
5?0。
8L;(四)微蚀:①目的与作用:清洁粗化线路铜面,确保图形电镀铜与一次铜之间的结合力②微蚀剂多采用过硫酸钠,粗化速率稳定均匀,水洗性较好,过硫酸钠浓度一般控制在60克/升左右,时间控制在20秒左右,药品添加按100平米3-4公斤;铜含量控制在20克/升以下;其他维护换缸均同沉铜微蚀。
(五)浸酸①作用与目的:除去板面氧化物,活化板面,一般浓度在5%,有的保持在10%左右,主要是防止水分带入造成槽液硫酸含量不稳定;②酸浸时间不宜太长,防止板面氧化;在使用一段时间后,酸液出现浑浊或铜含量太高时应及时更换,防止污染电镀铜缸和板件表面;③此处应使用C.P级硫酸;(六)图形电镀铜:又叫二次铜,线路镀铜①目的与作用:为满足各线路额定的电流负载,各线路和孔铜铜后需要达到一定的厚度,线路镀铜的目的及时将孔铜和线路铜加厚到一定的厚度;②其它项目均同全板电镀(七)电镀锡①目的与作用:图形电镀纯锡目的主要使用纯锡单纯作为金属抗蚀层,保护线路蚀刻;②槽液主要由硫酸亚锡,硫酸和添加剂组成;硫酸亚锡含量控制在35克/升左右,硫酸控制在10%左右;镀锡添加剂的添加一般按照千安小时的方法来补充或者根据实际生产板效果;电镀锡的电流计算一般按1。
5安/平方分米乘以板上可电镀面积;锡缸温度维持在室温状态,一般温度不超过30度,多控制在22度,因此在夏季因温度太高,锡缸建议加装冷却温控系统;③工艺维护:每日根据千安小时来及时补充镀锡添加剂剂;检查过滤泵是否工作正常,有无漏气现象;每个2-3小时应用干净的湿抹布将阴极导电杆擦洗干净;每周要定期分析锡缸硫酸亚锡(1次/周),硫酸(1次/周),并通过霍尔槽试验来调整镀锡添加剂含量,并及时补充相关原料;每周要清洗阳极导电杆,槽体两端电接头;每周用低电流0。
2?0。
5ASD电解6?8小时;每月应检查阳极袋有无破损,破损者应及时更换;并检查阳极袋底部是否堆积有阳极泥,如有应及时清理干净;每月用碳芯连续过滤6?8小时,同时低电流电解除杂;每半年左右具体根据槽液污染状况决定是否需要大处理(活性炭粉);每两周要更换过滤泵的滤芯;④大处理程序:A.取出阳极,取下阳极袋,用铜刷清洗阳极表面,水洗冲干后,装入阳极袋内,放入酸槽内备用B.将阳极袋放入10%碱液浸泡6?8小时,水洗冲干,再用5%稀硫酸浸泡,水洗冲干后备用;C.将槽液转移到备用槽内,按3?5克/升将活性碳粉缓慢溶解到槽液中,待溶解彻底后,吸附4-6小时候,用10um的PP滤芯加助滤粉过滤槽液至清洗干净的工作槽内,放入阳极,挂入电解板,按0。
2-0。
5ASD电流密度低电流电解6?8小时,D.经化验分析,调整槽中的硫酸,硫酸亚锡含量至正常操作范围内;根据霍尔槽试验结果补充镀锡添加剂;E.待电解板板面颜色均匀后,即停止电解;F.试镀OK.即可;⑤补充药品时,如添加量较大如硫酸亚锡,硫酸时;添加后应低电流电解一下;补加硫酸时应注意安全,补加量较大时(10升以上)应分几次缓慢补加;否则会造成槽液温度过高,亚锡氧化,加快槽液老化 ;⑥药品添加计算公式:硫酸亚锡(单位:公斤)=(40-X)×槽体积(升)/1000硫酸(单位:升)=(10%-X)g/L×槽体积(升)或(单位:升)=(180-X)g/L×槽体积(升)/1840(八)镀镍①目的与作用:镀镍层主要作为铜层和金层之间的阻隔层,防止金铜互相扩散,影响板子的可焊性和使用寿命;同时又镍层打底也大大增加了金层的机械强度;②全板电镀铜相关工艺参数:镀镍添加剂的添加一般按照千安小时的方法来补充或者根据实际生产板效果,添加量大约200ml/KAH;图形电镀镍的电流计算一般按2安/平方分米乘以板上可电镀面积 ;镍缸温度维持在40-55度,一般温度在50度左右,因此镍缸要加装加温,温控系统;③工艺维护:每日根据千安小时来及时补充镀镍添加剂 ;检查过滤泵是否工作正常,有无漏气现象;每个2-3小时应用干净的湿抹布将阴极导电杆擦洗干净;每周要定期分析铜缸硫酸镍(氨基磺酸镍)(1次/周),氯化镍(1次/周),硼酸(1次/周)含量,并通过霍尔槽试验来调整镀镍添加剂含量,并及时补充相关原料;每周要清洗阳极导电杆,槽体两端电接头,及时补充钛篮中的阳极镍角,用低电流0。
2?0。
5ASD电解6?8小时;每月应检查阳极的钛篮袋有无破损,破损者应及时更换;并检查阳极钛篮底部是否堆积有阳极泥,如有应及时清理干净;并用碳芯连续过滤6?8小时,同时低电流电解除杂;每半年左右具体根据槽液污染状况决定是否需要大处理(活性炭粉);每两周药更换过滤泵的滤芯;④大处理程序:A.取出阳极,将阳极倒出,清洗阳极,然后放在包装镍角的桶内,用微蚀剂粗化镍角表面至均匀粉红色即可,水洗冲干后,装入钛篮内,方入酸槽内备用 B.将阳极钛篮和阳极袋放入10%碱液浸泡6?8小时,水洗冲干,再用5%稀硫酸浸泡,水洗冲干后备用;C.将槽液转移到备用槽内,加入1-3ml/L的30%的双氧水,开始加温,待温度加到65度左右打开空气搅拌,保温空气搅拌2-4小时;D.关掉空气搅拌,按3?5克/升将活性碳粉缓慢溶解到槽液中,待溶解彻底后,打开空气搅拌,如此保温2?4小时;E.关掉空气搅拌,加温,让活性碳粉慢慢沉淀至槽底;F.待温度降至40度左右,用10um的PP滤芯加助滤粉过滤槽液至清洗干净的工作槽内,打开空气搅拌,放入阳极,挂入电解板,按0。
2-0。
5ASD电流密度低电流电解6?8小时,G.经化验分析,调整槽中的硫酸镍或氨基磺酸镍,氯化镍,硼酸含量至正常操作范围内;根据霍尔槽试验结果补充镀镍添加剂;H.待电解板板面颜色均匀后,即可停止电解,然后按1-1。