alinco dr635 维修手册 英文版
InRow RC维修手册

设置常规配置 . . . . . . . . . . . . . . . . . . . . . . . . . . . . . . . . . . . . . . . . . . . . 11
制冷单元配置 . . . . . . . . . . . . . . . . . . . . . . . . . . . . . . . . . . . . . . . 11
运行和维护
InRow®RC
ACRC100 ACRC103
This manual is available in English on the enclosed CD. Dieses Handbuch ist in Deutsch auf der beiliegenden CD-ROM verfügbar. Deze handleiding staat in het Nederlands op de bijgevoegde cd. Este manual está disponible en español en el CD-ROM adjunto. Ce manuel est disponible en français sur le CD-ROM ci-inclus. Questo manuale è disponibile in italiano nel CD-ROM allegato. 本マニュアルの日本語版は同梱の CD-ROM からご覧になれます。 Instrukcja Obsługi w jezyku polskim jest dostepna na CD. O manual em Português está disponível no CD-ROM em anexo. Данное руководство на русском языке имеется на прилагаемом компакт-диске. 您可以从包含的 CD 上获得本手册的中文版本。 您可以从附属的CD上获得本手册的中文版本。
维修手册英文版
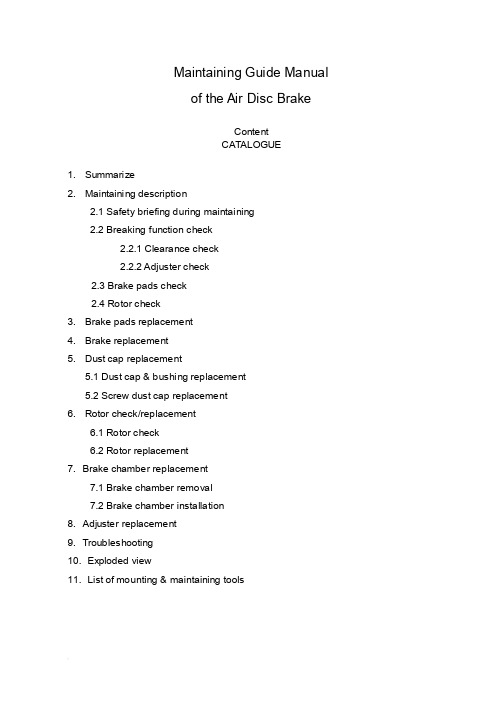
Maintaining Guide Manualof the Air Disc BrakeContentCATALOGUE1. Summarize2. Maintaining description2.1 Safety briefing during maintaining2.2 Breaking function check2.2.1 Clearance check2.2.2 Adjuster check2.3 Brake pads check2.4 Rotor check3. Brake pads replacement4. Brake replacement5. Dust cap replacement5.1 Dust cap & bushing replacement5.2 Screw dust cap replacement6. Rotor check/replacement6.1 Rotor check6.2 Rotor replacement7. Brake chamber replacement7.1 Brake chamber removal7.2 Brake chamber installation8. Adjuster replacement9. Troubleshooting10. Exploded view11. List of mounting & maintaining toolsBrief introduction of YOUFINYOUFIN was established on May 20th, 1998. It is a Sino-Foreign joint-venture enterprise registered in Wuhan Economic and T echnological Development Zone with multi-investors among which private investors dominate. It is a professional company engaged in manufacturing disc brakes and serving the principal automobile manufacturers by providing modularized supply. The main prod ucts cover hydraulic disc brakes and air disk brakes in close to thirty sizes.YOUFIN developed the air disc brake autonomously and patented the product. So far we are the only manufacturer in China that can mass produce air discs to be used in long distance coaches and inner city buses. It is evaluated that the quality of our products is close to the advanced international level in field use. The product development is part of the National T orch Plan and is also sponsored by the Small and Medium-sized Enterprise T echnical Innovation Foundation of Chinese Ministry of S&T.Our Air Disc Brake products are on an absolute leading position in China and the same international level as far as the key technology is concerned.1. SummarizeYOUFIN Air Disc Brake has four sizes (16’’, 17.5’’19.5’’, 22.5’’). It can satisfy different vehicles. The brakes have compact structure; automatically wear compensation and can easily changing the brake pad.2. Maintaining descriptionSafety briefing during maintainingIt’s most important to ensure safety driving and breaking by goodcharacteristics of the brake.Observe brake pad and rotor wear limits. When they warned already to assigned smallest thickness, it need replace immediately, otherwise, it may cause the accident. The pads scorches, grinds or greases must replace immediately.Every pad on each bridge must replace at the same time.When services the brake, the vehicle must park in smooth gound and the wheel withstand with the block/ stone prevent rolls.Note:●Must guarantee it does not occur with careless brake. When replace brakepad don’t make the brake, otherwise, it will hurts the body!●Do not use the compressed air or other cleaning up equipment clean thebrake, in order to avoid injures the body.●Be sure your hands and fingers place outside the caliper, in order to avoidinjures the body.●When moves and installs the brake should have some assistance, avoids ittoo heavy to hurts the body.●When take off the brake to make maintenance, it must fix on the clamp withhigh strength bolt, in order to avoid hurts the body.●Only allowed genuine YOUFIN kits and pads permitted by YOUFIN. Duringthe first 50 miles driving after new pad replacement, should avoid promptlybrake and brake at a long distance, Prevent overhigh temperature.●Allowed genuine YOUFIN kits and brake pads permitted by YOUFIN.●Only can use the recommendation kits in service. Screws the bolt/nutaccording to the request moment of force.Brake Function checkClearance checkProcess:●T ake off the hexagon bolt (39), loosen the pad retainer (38).●Remove pad retainer (38) from caliper.●Remove 3pcs of pad clip (37).●Move the cable (40) to the side.●Push the caliper towards the wheel and check the clearance with tune-upgauge.0.5mm ≤ clearance ≤ 1.2mmNote: Insert tune-up gauge between the caliper (1) and the brake pad (35). Should check the adjuster while the clearance is out of standard.Adjuster checkProcess:●Remove the rubber cap (12).●Turn hexagon head (22) clockwise by wrench to ensure clearance larger than3mm. (Or remove the brake pad and the push board)Note:a. Need enough room (3mm<clearance) for turn adjuster preventing un-fit.b. Never force to adjust the hexagon head (22) and/or the adjuster!Push the pressure arm 5 times in small increments and observe the hexagon head (22). While the adjuster is in good condition, hexagon head (22) must rotate clockwise.c. As the regulated quantity increase, rotation angle decreases.If the adjuster hexagon head (22):a) Not running at allb) Only running at first pushc) Running, but stopped in the middleWhile considers adjuster failed. Y ou should replace the brake on the basis of section 4 or change the adjuster in accordance with section 8.●Keep the clearances at 1mm (section 3) after adjuster check is finished.●Reinstall the rubber cap (12).Brake pads wearing check●Scorches, grinds and greased brake pad must replaces immediately.●Brake pads at the same bridge must replace at the same time.●Brake pad and pad clip must replace at the same time.Rotor checkProcess:●Remove the brake pad according to section 3.●T est thickness of the rotor.Note: Observe the brake pads and the rotor attrition situation. Excessive attrition of the rotor and the brake pads will reduce their potency and causes the brake fail!CAUTION: Rotors on the same bridge must replace at the same time. Single side rotor replacement is unacceptable. Recommend installs new brake pads whilereplace the new rotors.Rotor Dimension limitsRotor jumpiness (↗) check:2.4.1 Process:●Installs division indicator on the bracket (dial guage).●Measure jumpiness (↗) through turns the wheel. Jumpiness (↗) should lessthan 0.15.●Replaces the rotor to satisfy the request of section 6.●Modified brake pad should fulfil the specific requirements in section 3.2.4.2 Rotor test:At each change of Pads check the Rotor for grooves and cracks.The diagram at the right shows possible conditions of the surface.A = Small cracks spread over the surface are allowedB = Cracks less than 0.02in. (0.5mm) wide, running in a Radial direction, are allowedC = Grooves (circumferential) less than 0.06in. (1.5mm) wide are allowedD = Cracks in the vanes are not allowed and the Rotor MUST BE REPLACED.a = Pad contact area3. Brake Pad replacementNote: Do not use the pipe spanner/ board die! Keep your hands and fingers outside the caliper avoid the hurts of body!Brake Pad dismantle process:●T ake off hexagon bolt (39) from the Pad Retainer with spanner.●Remove the pad retainer from caliper (1).●T ake off the pad clip (37), which is above the pads (35,36) and push board (19).●Remove the sensor on brake pad.●T ake off the push board (19) & the brake pads (35,36).●Adjust hexagon head to make tappet back to the initial position.●Clean the pad groove & push board and anchor surface with brush.Note: Don’t hurt the dust cap (5 & 10). Be sure of no grease on installation surface!●Check the adjuster on the basis of section 2.2.2.Note: Fix the key while checking & turning the adjuster cap to avoid screw rotate.●Check the rotor according to section 2.4.3.2 Brake pad installing process:●Need enough room between the caliper & the rotor to insert brake pad.●Insert push board (19) at the place the caliper combine with the adjust screw.Note: Push board must on the bracket supporting surface. Adjust screw pin must in groove. Otherwise it will do harm to Adjuster mechanism. Ensure the dust cap untwisted by rotate the adjust screw.●Insert the cable sensor to pad groove. Fix cable on bearing (40).Note: The sensor contactor must face the brake disc and installs at the correctposition. Attention the wire trend to prevents the friction.●Insert new pad (36) at side of the push board.●Push caliper toward the wheel until the pad touch the rotor.Insert the brake padat wheel side.Note: Don’t adjust hexagon head violently.Note: Turn the adjuster counter-clockwise to decrease the clearance between pads.Don’t install the retainer before adjustment.Note: Check the rubber cap (12), be sure it is correctly seated.4. Brake replacementNote: Don’t use pipe wrench. Ensure your hands and fingers outside the caliperavoid hurt your body!Note: The Brake will supplies in assembly.CAUTION: The left brake and the right brake cannot exchange. Arrow direction on the brake is same as the forward direction of the wheel.4.1 Brake removal process:●Remove brake pad (see Section 3).●Release nut on the caliper, take of brake chamber.●Remove brake assessment from the bridge.●Check brake pad on the basis of section 2.3.●Check rotor on the basis of section 2.4.4.2 Brake installing process:●Install the new brake over rotor on the bridge. Screwed bolt with the spanner.Note: The right install order of the bolt is screwed both side symmetry.●T ake down the flange protection cap on the brake chamber.Note:Air chamber installment position. Open the scupper faces the ground, and stops other mouths.●Install brake pad and push board on the basis of section 3.●Install the air chamber and tighten with spanner.●Adjust the clearance.5. Guide Pin dust cap replacementNote: Do not use the pipe spanner/ board die! Keep your hand & finger outside the caliper, in order to avoid injuries.Note: When replaces all dust cap of guide bushing, section 5.1 & 5.2 should unify to avoids repetitive work. Single bushing replacement according to 5.1 and 5.2 corresponding work orders.5.1. Dust cap & bushing replacement●T ake off the brake pad according to section 3.●Loosen the chamber bolt and remove the brake chamber from caliper.●Remove the caliper assessment from bridge.●T ake off the steel cap (11) from guide bushing (8 & 9) by suitable tools.Dismantle caliper (1) from the bracket (2).Note: Don’t hurt the hole, the lid while open the steel cap with tools.●Loosen the bolt (6 & 7); separate the caliper (1) from the bracket (2).Note: When caliper moves, it may hurt body.●Cleaning up the bracket bonding plane●Take off the guide pin (8&9) on caliper (1). Then remove the dust cap (5).●Presses out bushing 4 with mandril from caliper1.●Cleans up the guide pin hole of caliper.Installing process:●Long guide pin hole must press in two new bushings. Short guide pin holepress in one.●Guarantee the size in drawing.●Greases between them and the bushing●Install new dust cap in the guide pin hole.Note: Cleans up the guide pin hole and grease the edge of dust cap before install for easy installation. Ensure the dust cap installs steadily, without crease and inside the ring groove of the caliper.●Install long/short guide pin to each hole and dust cap upside set in guide pinring groove.●Put the caliper (1) on the bracket (2) and plug guide pin (8&9) in guide hole.●Plug new bolt (6&7) (long one for pin 8, short one for pin 9) and screwed onbracket (2) with spanner.Note: Assembly must be careful, don’t damage the dust cap (5). First, screws bolt on long pin (8), and then screws bolt on short pin (9).When service maintenance, remove the guide pin (8&9) and replace by new bolt (6&7)!●Move the caliper on guide pin (8,9) forward and backward to check whether thecaliper can move freely.●Put on new copper cap on caliper (1) hole and push it in with correct kits. Note: Avoids the hurts of surface.●Raising the guide pin dust cap (5) carefully for cancel the air pressure.●Install brake across the rotor on bridge. Screwed bolt with the spanner.Note: Correct install process of the hexagon bolt.●Install brake pads and adjust clearance. Implemented section 3, notice theexplanation.●Cleaning the install flange on caliper and grease inside the pressure arm ballsocket before reinstall the brake chamber.●Install the brake chamber and screwed with spanner.Note: After the installation of brake chamber, the lowest chamber hole face theground must open, other mouths stop up.5.2. Screw dust cap replacementNote: If only replace the screw dust cap, does not need to remove the caliper andthe air chamber.Process:●Remove brake pad and push board according to section 3.●Push the caliper towards to brake chamber.●T ake off screw dust cap (10) from the ring groove on adjust screw (21).●T ake down from dust cap base with screwdriver.●Check screw thread.●Turning the adjust bolt for 30mm clockwise with the spanner.●Inspection thread corrosion and whether is damaged.●Turning it clockwise, feeling its lubrication and check the adjust screw thread.●Clean the base of caliper dust cap (10). (Arrow pointed)●Push new dust cap (10) on adjust screw. Install it on the base with kits. Observes itinstalls whether arrived.●Grease on the edge of dust cap (10) and install it on the base of adjust screw (21).Note: Guarantees the dust cap steadily in place and does not have the corrugation in the adjust screw ring groove.Installation process:●Install the brake pad and adjust the clearance (see Section 3).6. Rotor check/replacement6.1 Rotor check Check the rotor (Section 2.4) If the rotor reached the minimumthickness, it must be replaced.6.2 Rotor replacementNote: Generally recommend use new brake pad while install new/machined rotor.6.2.1 Uninstall the rotor:●R emove the brake pad. (see section 3)●T ake off the brake chamber. (see section 7)●T ake down brake from bridge. (see section 4)●T ake off the wheel and the rotor.(Refer to V ehicle Manufacture’srecommendations)6.2.2 Rotor installation:●I nstall the wheel and rotor. (refer to V ehicle Manufacture’s recommendations)●D egrease the rotor.●T urn the wheel and check the installed rotor (Section 2.4).●A djust ABS sensor refer to V ehicle Manufacture’s recommendations.●I nstall the brake (see Section 4).●I nsert pad (see Section 3).●I nstall brake chamber (see Section 7).7. Brake chamber replacementNote: Don’t use pipe wrench! Ensure your hands and fingers outside the caliperavoid hurts body!Note: Can only use the chamber assigned by the Vehicle Manufacture.7.1. Brake chamber removal:●Bleeds off the compressed air.●Remove the upper air pipe of brake chamber.●Remove the chamber from caliper.7.2. Brake chamber installation:Note: According to the brake installment position, only can open the scupperunderneath.●Cleans the sealing plane of the pressure are ball socket (arrow) and caliper beforethe brake chamber installation.●Screwed the chamber mounting nut alternately with spanner in torque ratingrequired by the air chamber supplier.●Connection the air pipe.Note: Never twist the braking line, place it originally avoid fiction with other sets.While exist air leak, finds the leakage and check the connection.●Function and performance examination.8. A djuster replacement8.1 A djuster removal●Remove brake pad (see Section 3).●Remove brake chamber (see Section 7).●T ake off brake (see Section 4).●T ake off upper bolt by hexagon wrench.●Remove adjuster and other parts in the caliper.Note: Don’t hurt the screw dust cap.8.2 A djuster installation●Grease inside the caliper.●Put the return spring (18) at each side.●Install the needle assembly and the adjuster.●Puts the washer and top head, screwed the bolt with spanner according to theopposite angle principle.Note: Guarantee the bolt tighted the moment of force.9. Troubleshooting11. List of mounting & maintaining toolsYOUFIN is in the process of logo replacement, new logo will put into practice gradually. It with the original logo is still the YOUFIN’s product. Final interpret right for the logo belongs to YOUFIN.。
美国艾美特(Amerex)便携式灭火器维修手册说明书

All fire extinguishers shall be installed, inspected and maintained in accordance with the National Fire Protection Association standard titled "Portable Fire Extinguishers", NFPA 10, or the National Fire Code of Canada and the requirements of local authorities having jurisdiction.When maintenance is indicated, it shall be performed by trained persons having proper equipment. Fire extinguishers are pressure vessels and must be treated with respect and handled with care. They are mechanical devices and require periodic maintenance to be sure that they are ready to operate properly and safely. Amerex strongly recommends that the maintenance of portable fire extinguishers be done by a trained professional – your local authorized Amerex Distributor.Amerex Corporation makes original factory parts available to insure proper maintenance – USE OF SUBSTITUTE PARTS RELEASES AMEREX OF ITS WARRANTY OBLIGATIONS. Amerex parts have machined surfaces and threads that are manufactured to exacting tolerances. All parts meet precise specifications and are subjected to multiple in -house inspections and tests for acceptability. There are substitute parts available which are incorrectly labeled as UL component parts, some are advertised as Amerex type. None of these meet UL requirements and all of them voids the Amerex extinguisher warranty and UL listing. DO NOT SUBSTITUTE.RECHARGE FIRE EXTINGUISHERS IMMEDIATELY AFTER ANY USEOWNER ’S SERVICE MANUALINSTALLATION, OPERATING & SERVICING INSTRUCTIONSMANUAL PN 05604PORTABLE HALON 1211 EXTINGUISHERSMODELS A344, C352, C354, B355, 361, B369, B371, 372AMEREX CORPORATION DOES NOT SERVICE, MAINTAIN OR RECHARGE FIRE EXTINGUISHERS. THIS MANUAL IS PUBLISHED AS A GUIDE TO ASSIST QUALIFIED SERVICE PERSONNEL IN THE INSPECTION, MAINTENANCE AND RECHARGE OF AMEREX FIRE EXTINGUISHERS ONLY. NO INSTRUCTION MANUAL CAN ANTICIPATE ALL POSSIBLE MALFUNCTIONS THAT MAY BE ENCOUNTERED IN THE SERVICE OF FIRE EXTINGUISHERS. DUE TO THE POSSIBILITY THAT PRIOR SERVICE PERFORMED ON THIS EQUIPMENT MAY HAVE BEEN IMPROPERLY DONE, IT IS EXTREMELY IMPORTANT THAT ALL WARNINGS, CAUTIONS AND NOTES IN THIS MANUAL BE CAREFULLY OBSERVED. FAILURE TO HEED THESE INSTRUCTIONS COULD RESULT IN SERIOUS INJURY. AMEREX ASSUMES NO LIABILITY FOR SERVICE, MAINTENANCE OR RECHARGE OF FIRE EXTINGUISHERS BY PUBLISHING THIS MANUALAMEREX CORPORATION – P.O. BOX 81 – TRUSSVILLE, ALABAMA 35173-0081Phone: 205/655-3271 Fax: 800/654-5980e -mail: sales@amerex Web Page: http://www.amerex REFERENCES IN THIS MAUNUAL: NFPA 10 Portable Fire ExtinguishersCGA C -1 Methods for Pressure Testing Compressed GasCylindersCGA C -6 Standard for Visual Inspection of SteelCompressed Gas Cylinders.National Fire Code of Canada AVAILABLE FROM: National Fire Protection Association, 1 Batterymarch Park,Quincy, MA 02169-7471 Compressed Gas Association, 14501 George Carter Way, Chantilly, VA 20151-2923 Compressed Gas Association, 14501 George Carter Way, Chantilly, VA 20151-2923 National Research Council Canada, 1200 Montreal Road,Ottawa, ON K1A 0R6 CanadaINSPECTING THE EXTINGUISHERThis extinguisher must be inspected at regular intervals (monthly or more often if circumstances dictate) to insure that it is ready for use. Inspection is a "quick check" that a fire extinguisher is available and is in operating condition. It is intended to give reasonable assurance that the fire extinguisher is fully charged. This is done by verifying that it is in its designated place, that it has not been actuated or tampered with and that there is no obvious physical damage or condition to prevent its operation.PERIODIC INSPECTION PROCEDURES(Monthly or more often if circumstances dictate)NFPA 10 Periodic inspection of fire extinguishers shall include a check of at least the following items:1.Located in designated place.2.No obstruction to access or visibility.3.Pressure gauge reading or indicator in the operable range or position.4.Operating instructions on nameplate and facing outward.5.Tamper seal not broken or missing.6.Examination for obvious physical damage, corrosion, leakage or clogged nozzle.7.Fullness determined by weighing or hefting.MAINTENANCENFPA 10 Extinguishers shall be subjected to maintenance at intervals of not more than 1 year, at the time of hydrostatic test or when specifically indicated by an inspection or electronic notification. Maintenance procedures include a thorough examination of the basic elements of a fire extinguisher:1.Mechanical parts2.Extinguishing agent or cartridge of cylinder operated extinguishers, pump tanks and certain types ofstored pressure extinguishers3.Expelling meansNOTE: Stored pressure halon 1211 extinguishers do not require an internal examination of the cylinder or examination of the agent during annual maintenance, but shall receive athorough external examination.Maintenance is a thorough examination of the fire extinguisher. It is intended to give maximum assurance that a fire extinguisher will operate effectively and safely. It includes a thorough examination for physical damage or condition to prevent its operation and any necessary repair or replacement. It will normally reveal if hydrostatic testing or internal maintenance is required.MAINTENANCE –SERVICE PROCEDURE1.Clean extinguisher to remove dirt, grease or foreign material. Check to make sure that the instructionnameplate is securely attached and legible. Inspect the cylinders for corrosion, abrasion, dents or weld damage. If any of these conditions are found and you doubt the integrity of the cylinder, hydrostatically test to factory test pressure, using the proof pressure method in accordance with CGA C-1 and C-6 and NFPA 10. See proper method of depressurizing and reclaiming Halon 1211 in SIX-YEAR MAINTENANCE/RECHARGE PROCEDURE.Note: When cleaning, avoid use of solvents around the pressure gauge. They could seriously damage the plastic gauge face.2. Inspect the extinguisher for damaged, missing or substitute parts. Only factory replacement parts areapproved for use on Amerex fire extinguishers.3.Remove and check pull pin for freedom of movement. Replacement if bent or if removal appears difficult.4.Check the date of manufacture printed on the extinguisher label (nameplate). All stored pressure Halon1211 extinguishers must be hydrostatically (proof pressure) tested every 12 years.5.Visually inspect the pressure gauge:a.If bent, damaged or improper gauge, depressurize and replace.b.If pressure is low or high and temperature/pressure relationship has been ruled out:1.If pressure is low, check for leaks.2.If over pressurized (overcharged), depressurize the extinguisher and follow recharge instructions. 6.Inspect discharge lever for any dirt or corrosion which might impair freedom of movement. Inspectcarrying handle for proper installation. If lever, handle or rivets are damaged, replace with proper Amerex part(s).7.Check weight of extinguisher and compare to proper weight specified on extinguisher nameplate. Ifdiscrepancy is noted, remove nozzle or hose assembly and follow Complete Maintenance/Recharge Procedure for recharging.8.Remove nozzle or hose and horn assembly. Inspect nozzle, hose gasket (o-ring), hose and hornassembly for damage –replace as necessary. Blow air through hose and horn or nozzle to insure passage is clear of foreign material and replace component parts as necessary.9.Inspect the valve assembly for corrosion or damage to hose thread connection. Replace valve assemblyor component parts as necessary following the proper recovery and recharge procedures. If valve removal is necessary, complete all steps in the Complete Maintenance/Recharge Procedure.10.Install nozzle or hose and horn assembly.11.Install new tamper seal and record service data on the extinguisher inspection tag.12.Replace the extinguisher on the wall hanger making sure that it fits the bracket properly –replace thebracket if necessary.COMPLETE MAINTENANCE –SIX YEAR TEARDOWNNFPA 10 Every six years, stored pressure extinguishers shall be emptied and subjected to the applicable maintenance procedures. When the applicable maintenance procedures are performed during periodic recharging, the six year requirement shall begin from that date.WARNING:a. Before attempting to devalve the extinguisher for Maintenance, Hydrotest or Recharging be sure that itis completely depressurized. Halon 1211 generates a vapor pressure of 22 psi @70°F. NEVER VENT TO THE ATMOSPHERE. Recover agent and vapor according to the instructions below.b. Never have any part of your body over the extinguisher while removing the valve assembly.c. Halon 1211 shall not be mixed with even the slightest amount of moisture. Prolonged exposure of adevalved cylinder to ambient air shall be avoided to prevent moisture contamination and cylinder rusting.plete items 1 through 9 in Maintenance/Service Procedure above.2.Attach the appropriate recharge adapter to the extinguisher operating valve. Empty the extinguisher of allpressure and Halon 1211 using a Halon 1211 recovery/recharge system and a bulk Halon 1211 supply cylinder with sufficient empty capacity to accept the contents of the extinguisher.NOTE: Every effort shall be made to halt unnecessary escape of Halon 1211 to the atmosphere to prevent detrimental environmental effect. High efficiency Halon 1211 Recovery/RechargeVacuum Pump Type Systems (UL Standard 2006) are commercially available. The Getz FireEquipment HR-1L or other UL Approved Recharge/Recovery system assures a minimum of 99%recovery efficiency. It allows a means of checking for and removing moisture or contaminationduring the recovery process.3. When the extinguisher is empty of all agent and pressure, remove valve assembly and disassemble byremoving downtube, spring and valve stem assembly. Discard valve stem assembly and collar o-ring.NOTE: Keep cylinder opening covered while devalved to minimize interior corrosion.4.Thoroughly clean all parts of the disassembled valve with a soft bristle brush or soft cloth. Blow the valveout with dry nitrogen.5.Install a new Amerex valve stem assembly after lightly lubricating the valve stem o-ring with V-711 (do notlubricate the valve stem seal). Reassemble the spring and downtube. Carefully install a new collar o-ring which has been lightly lubricated with V-711. Set the valve assembly aside.6.Inspect the cylinder interior following CGA Visual Inspection Standard C-6 and current NFPA 10guidelines. If a hydrotest has been performed or any moisture is evident, the cylinder shall be immediately warm air dried.7.Clean the o-ring seating groove in the cylinder neck. If any rust is evident, remove by using a fine emerycloth (200 grit). Clean the surface and lubricate the entire sealing area with a thin film of V-711. Install the valve assembly in extinguisher cylinder. Hand tighten firmly.e the Getz HR-1L or other UL Approved Recharge/Recovery system to purge the residual air from theextinguisher cylinder.9.Stand the extinguisher upright on a scale of sufficient size and capacity. Tare weight extinguisher orrecord empty weight.10.Follow all recharging instructions on Getz HR-1L or other UL Approved Recharge/Recovery system.11.Remove the recharge adapter. Some residual Halon vapor may remain in the valve outlet as a result ofthe charging procedure. Before attempting to leak detect, vacuum or blow the vapor away from the areas to be checked. Check extinguisher for leaks at the valve outlet, around the collar seal, cylinder welds and gauge using a Halogen Leak Detector (Preferred Method). The alternate method is to apply leak detecting fluid or a solution of soapy water to these areas. Use dry nitrogen to blow all liquid residue out of the valve and wipe the extinguisher to dry the exterior. DO NOT LEAVE ANY LIQUID INSIDE THE VALVE BODY.12.Install pull pin, new tamper seal, nozzle or hose and horn assembly to the extinguisher discharge valve.13.Weigh extinguisher to confirm that the total weight is within the tolerances indicated in the Maintenancesection on the extinguisher nameplate.14.Record service date and attach new tag in accordance with the requirements of the "Authority HavingJurisdiction".TROUBLESHOOTING GUIDEWARNING: ANY HALON 1211 EXTINGUISHER MUST BE COMPLETELY DEPRESSURIZED BEFORE ANY ATTEMPT IS MADE TO REMOVE THE VALVE AND CORRECT A LEAKAGEPROBLEM.To depressurize, see instructions in the Complete Maintenance section. Halon 1211 is a liquid under nitrogen pressure. Variations in the temperature may affect gauge readings. The gauge dial has been calibrated to reflect the tested extinguisher temperature extremes (-65°F to +120°F). When in doubt about a gauge reading, place the extinguisher at room temperature (70°F) for several hours to obtain a true reading.FOR REPLACEMENT PARTS SEE THE AMEREX PORTABLE AND WHEELED PARTS BOOK PN 27277 AVAILABLE AT UNDER MANUALS OF THE RESOURCE SELECTION.。
佳能某型号打印机维修手册(英文版)

佳能某型号打印机维修手册(英文版)IntroductionThank you for choosing a Canon printer. This maintenance manual will provide you with information and guidance on how to properly maintain and troubleshoot your Canon printer. Regular maintenance and proper handling of the printer will help ensure that it operates at optimal performance and has a longer lifespan.Safety PrecautionsBefore performing any maintenance or troubleshooting procedures on the printer, it's important to keep the following safety precautions in mind:- Always turn off the printer and unplug it from the power source before performing any maintenance procedures.- Do not attempt to disassemble the printer unless you are a qualified technician.- Use only genuine Canon printer parts and supplies.- Keep the printer in a well-ventilated area and away from direct sunlight and heat sources.Maintenance ProceduresRegular maintenance of the printer is important to ensure its smooth operation. Here are some maintenance procedures that should be performed regularly:- Clean the printer: Use a soft lint-free cloth and mild detergent to clean the printer exterior and paper trays. Clean the print head and ink cartridges using the printer's cleaning feature.- Replace ink cartridges: When the ink levels are low, replace the ink cartridges with genuine Canon cartridges to ensure high-quality prints.- Check paper feed: Remove any paper jams and ensure that the paper feed is smooth and unrestricted.TroubleshootingIf your printer is not functioning properly, here are some troubleshooting steps you can take:- Check for paper jams: Open the printer cover and remove any jammed paper from the paper feed.- Check ink levels: If the prints are coming out faded or incomplete, check the ink levels and replace the cartridges if necessary.- Restart the printer: Turn off the printer, unplug it, and wait for a few minutes before plugging it back in and turning it on again.ConclusionProper maintenance and regular troubleshooting are essential for ensuring the smooth operation of your Canon printer. By following the guidelines provided in this manual, you can keep your printer in good working condition and avoid costly repairs. If you encounter any issues that cannot be resolved through these procedures, please contact a qualified technician for assistance.Certainly! Let's delve further into various aspects of Canon printer maintenance and troubleshooting, and provide more detailed information on how to keep your Canon printer in optimal working condition.1. Printer Cleaning and MaintenanceRegular cleaning of your Canon printer is crucial for maintaining its performance and extending its lifespan. Here's a more in-depth look at the steps involved in cleaning and maintaining your printer:a. Cleaning the Exterior: Use a soft, lint-free cloth slightly dampened with water to wipe down the exterior of the printer. Avoid using harsh chemicals or abrasives, as they may damage the printer's surface.b. Cleaning the Paper Trays: Remove all paper from the trays and wipe them with a dry cloth to remove any dust or debris. Check for any paper remnants that may be stuck in the trays and remove them carefully.c. Cleaning the Print Head: The print head is a critical component of the printer that can get clogged with dried ink. Most Canon printers have a built-in function to clean the print head. Refer to your printer's manual to locate and perform the print head cleaning process.d. Inspecting for Wear and Tear: Periodically check for any signs of wear or damage to the printer, such as frayed cables, loose parts, or worn-out rollers. Address any issues promptly to prevent further damage.2. Ink Cartridge ReplacementWhen the ink levels in your Canon printer are low, it's essential to replace the ink cartridges with genuine Canon cartridges. Using non-genuine or refilled cartridges can compromise print quality and potentially damage the printer. Here's a step-by-step guide on how to replace ink cartridges in your Canon printer:a. Turn off the printer and unplug it from the power source.b. Open the printer cover to access the ink cartridge compartment.c. Carefully remove the empty ink cartridge by gently pressing down on it and then pulling it out from its slot.d. Take the new genuine Canon ink cartridge out of its packaging and remove the protective tape.e. Insert the new ink cartridge into the appropriate slot, ensuring it is securely in place.f. Close the printer cover and plug the printer back in.After replacing the ink cartridges, the printer may perform an ink charging process to prepare the new cartridges for printing. Follow any on-screen instructions or notifications to complete this process.3. Paper Feed and HandlingSmooth paper feed is essential for avoiding paper jams and ensuring high-quality prints. Here are some tips for maintaining proper paper feed in your Canon printer:a. Use High-Quality Paper: Ensure that you are using high-quality, compatible paper that meets the specifications recommended by Canon for your printer model.b. Load Paper Correctly: When loading paper into the tray, make sure it is properly aligned and not overloaded. Adjust the paper guides according to the paper size to prevent misfeeds.c. Clear Paper Jams: If a paper jam occurs, follow the printer's manual to safely remove the jammed paper. Avoid using excessive force, as it may cause damage to the printer's internal components.d. Regular Paper Tray Maintenance: Clean the paper trays regularly to remove any dust, debris, or paper fragments that can interfere with the paper feed mechanism.4. Troubleshooting Common Printer IssuesDespite regular maintenance, you may encounter occasional issues with your Canon printer. Here are some common problems and their troubleshooting steps:a. Print Quality Issues: If the prints appear faded, streaked, or distorted, it may indicate clogged nozzles or low ink levels. Run the printer's cleaning function to clear any clogged nozzles, and replace the ink cartridges if necessary.b. Paper Jams: If the printer is experiencing frequent paper jams, check for any obstructions in the paper path and ensure the paper is loaded correctly. Clear any jammed paper and follow the printer's manual for specific instructions.c. Connectivity Problems: If the printer is not responding to print commands, ensure that it is correctly connected to the computer or network. Check cables, wireless connections, and network settings to resolve connectivity issues.d. Error Messages: If the printer displays error messages, refer to the printer's manual for guidance on troubleshooting specific error codes. Restart the printer and follow any suggested troubleshooting steps.5. Additional Care and ConsiderationsIn addition to the maintenance and troubleshooting procedures mentioned above, here are some additional tips to keep your Canon printer in top condition:a. Firmware Updates: Check for and install firmware updates for your printer, as these updates often include enhancements and fixes that can improve performance and reliability.b. Environmental Considerations: Keep the printer in a clean, well-ventilated area, away from direct sunlight, excessive heat, or humidity. Environmental factors can affect the printer's performance and longevity.c. Professional Servicing: If you encounter persistent or complex issues with your printer that cannot be resolved through standard maintenance and troubleshooting, consider seeking professional servicing from a qualified Canon technician.In conclusion, regular maintenance, proper handling, and timely troubleshooting are essential for maximizing the performance and longevity of your Canon printer. By following the guidelines and best practices outlined in this manual, you can ensure that your Canon printer consistently delivers high-quality prints and reliable operation. Remember that proper maintenance not only saves you time and money, but also contributes to a better printing experience and overall satisfaction with your Canon printer.。
林肯电子焊接和切割产品说明书

Copyright © Lincoln Global Inc.LN ™- 25 PIPEIM10056April, 2011For use with machines having Code Number:11693Safety Depends on YouLincoln arc welding and cutting equipment is designed and built with safety in mind. However, your overall safety can be increased by proper installation ... and thoughtful operation on your part. DO NOT INSTALL, OPERATE OR REPAIR THIS EQUIPMENT WITHOUT READING THIS MANUAL AND THE SAFETY PRECAUTIONS CONTAINED THROUGHOUT.And, most importantly, think beforeyou act and be careful.IP23IEC 60974-5SECTION A:WARNINGSC ALIFORNIA PROPOSITION 65 WARNINGSWARNING: This product, when used for welding or cutting, produces fumes or gases which contain chemicals known to the State of California to cause birth defects and, in some cases, cancer. (California Health & Safety Code § 25249.5 et seq.)ARC WELDING CAN BE HAZARDOUS. PROTECTYOURSELF AND OTHERS FROM POSSIBLE SERIOUS INJURY OR DEATH. KEEP CHILDREN AWAY.PACEMAKER WEARERS SHOULD CONSULT WITH THEIR DOCTOR BEFORE OPERATING.Read and understand the following safety highlights. For additional safety information, it is strongly recommended that you purchase a copy of “Safety in Welding & Cutting - ANSI Standard Z49.1” from the American Welding Society, P.O. Box 351040, Miami, Florida 33135 or CSA Standard W117.2-1974. A Free copy of “Arc Welding Safety” booklet E205 is available from the Lincoln Electric Company, 22801 St. Clair Avenue, Cleveland, Ohio 44117-1199.BE SURE THAT ALL INSTALLATION, OPERATION,MAINTENANCE AND REPAIR PROCEDURES ARE PERFORMED ONLY BY QUALIFIED INDIVIDUALS.FOR ENGINE POWERED EQUIPMENT.1.a.Turn the engine off before troubleshootingand maintenance work unless themaintenance work requires it to be running.1.b.Operate engines in open, well-ventilated areas or vent the engineexhaust fumes outdoors. 1.c.Do not add the fuel near an open flame weldingwith hot engine parts and igniting. Do not spill fuel when filling tank. If fuel is spilled, wipe it up and do not start engine until fumes have been eliminated.1.d. Keep all equipment safety guards, coversand devices in position and in good repair.Keep hands, hair, clothing and tools away from V-belts, gears, fans and all other moving parts when starting, operating or repairing equipment.1.e.In some cases it may be necessary to remove safety guards toperform required maintenance. Remove guards only when necessary and replace them when the maintenance requiring their removal is complete. Always use the greatest care when working near moving parts. 1.f. Do not put your hands near the engine fan. Do not attempt tooverride the governor or idler by pushing on the throttle control rods while the engine is running. 1.g.To prevent accidentally starting gasoline engines while turningthe engine or welding generator during maintenance work,disconnect the spark plug wires, distributor cap or magneto wire as appropriate. 1.h.To avoid scalding, do not remove the radiatorpressure cap when the engine is hot.ELECTRIC ANDMAGNETIC FIELDS MAY BE DANGEROUS2.a.Electric current flowing through any conductorcauses localized Electric and Magnetic Fields (EMF).Welding current creates EMF fields around welding cables and welding machines 2.b.EMF fields may interfere with some pacemakers, andwelders having a pacemaker should consult their physician before welding. 2.c.Exposure to EMF fields in welding may have other health effectswhich are now not known. 2.d.All welders should use the following procedures in order tominimize exposure to EMF fields from the welding circuit:2.d.1.Route the electrode and work cables together - Securethem with tape when possible.2.d.2.Never coil the electrode lead around your body.2.d.3.Do not place your body between the electrode and workcables. If the electrode cable is on your right side, the work cable should also be on your right side.2.d.4.Connect the work cable to the workpiece as close as pos-sible to the area being welded.2.d.5.Do not work next to welding power source.SAFETYConformanceProducts displaying the CE mark are in conformity with European Community Council Directive of 15 Dec 2004 on the approximation of the laws of the Member States relating to electromagnetic compatibility,2004/108/EC. It was manufactured in conformity with a national standard that implements a harmonized standard: EN 60974-10 Electromagnetic Compatibility (EMC) Product Standard for Arc Welding Equipment. It is for use with other Lincoln Electric equipment. It is designed for industrial and professional use. IntroductionAll electrical equipment generates small amounts of electromagnetic emission. Electrical emission may be transmitted through power lines or radiated through space, similar to a radio transmitter. When emissions are received by other equipment, electrical interference may result. Electrical emissions may affect many kinds of electrical equipment; other nearby welding equipment, radio and TV reception, numerical controlled machines, telephone systems, computers, etc. Be aware that interference may result and extra precautions may be required when a welding power source is used in a domestic establishment.Installation and UseThe user is responsible for installing and using the welding equipment according to the manufacturer’s instructions. If electromagnetic disturbances are detected then it shall be the responsibility of the user of the welding equipment to resolve the situation with the technical assistance of the manufacturer. In some cases this remedial action may be as simple as earthing (grounding) the welding circuit, see Note. In other cases it could involve construction of an electromagnetic screen enclosing the power source and the work complete with associated input filters. In all cases electromagnetic disturbances must be reduced to the point where they are no longer troublesome.Note: The welding circuit may or may not be earthed for safety reasons according to national codes.Changing the earthing arrangements should only be authorized by a person who is compe-tent to access whether the changes will increase the risk of injury, e.g., by allowing parallelwelding current return paths which may damage the earth circuits of other equipment. Assessment of AreaBefore installing welding equipment the user shall make an assessment of potential electromagnetic prob-lems in the surrounding area. The following shall be taken into account:a) other supply cables, control cables, signaling and telephone cables; above, below and adjacent to thewelding equipment;b) radio and television transmitters and receivers;c) computer and other control equipment;d) safety critical equipment, e.g., guarding of industrial equipment;e) the health of the people around, e.g., the use of pacemakers and hearing aids;f) equipment used for calibration or measurementg) the immunity of other equipment in the environment. The user shall ensure that other equipment beingused in the environment is compatible. This may require additional protection measures;h) the time of day that welding or other activities are to be carried out.The size of the surrounding area to be considered will depend on the structure of the building and other activities that are taking place. The surrounding area may extend beyond the boundaries of the premises. Methods of Reducing EmissionsMains SupplyWelding equipment should be connected to the mains supply according to the manufacturer’s recommenda-tions. If interference occurs, it may be necessary to take additional precautions such as filtering of the mains supply. Consideration should be given to shielding the supply cable of permanently installed welding equip-ment, in metallic conduit or equivalent. Shielding should be electrically continuous throughout its length. The shielding should be connected to the welding power source so that good electrical contact is maintained between the conduit and the welding power source enclosure.Maintenance of the Welding EquipmentThe welding equipment should be routinely maintained according to the manufacturer’s recommendations. All access and service doors and covers should be closed and properly fastened when the welding equip-ment is in operation. The welding equipment should not be modified in any way except for those changes and adjustments covered in the manufacturers instructions. In particular, the spark gaps of arc striking and stabilizing devices should be adjusted and maintained according to the manufacturer’s recommendations. Welding CablesThe welding cables should be kept as short as possible and should be positioned close together, running at or close to floor level.Equipotential BondingBonding of all metallic components in the welding installation and adjacent to it should be considered. However, metallic components bonded to the work piece will increase the risk that the operator could receive a shock by touching these metallic components and the electrode at the same time. The operator should be insulated from all such bonded metallic components.Earthing of the WorkpieceWhere the workpiece is not bonded to earth for electrical safety, not connected to earth because of its size and position, e.g., ships hull or building steelwork, a connection bonding the workpiece to earth may reduce emissions in some, but not all instances. Care should be taken to prevent the earthing of the workpiece increasing the risk of injury to users, or damage to other electrical equipment. Where necessary, the connec-tion of the workpiece to earth should be made by a direct connection to the workpiece, but in some countries where direct connection is not permitted, the bonding should be achieved by suitable capacitance, selected according to national regulations.Screening and ShieldingSelective screening and shielding of other cables and equipment in the surrounding area may alleviate prob-lems of interference. Screening of the entire welding installation may be considered for special applications1._________________________1 Portions of the preceding text are contained in EN 60974-10: “Electromagnetic Compatibility (EMC) prod-uct standard for arc welding equipment.”TECHNICAL SPECIFICATIONS – LN™-25 PIPE (K2614-5)Thermal tests have been performed at ambient temperature. The Duty Cycle (duty factor) @ 40ºC (104°F) has been determined by simulation.WELD CAbLE SIzETable A.1 located below are copper cable sizes rec-ommended for different currents and duty cycles.Lengths stipulated are the distance from the welder to work and back to the welder again. Cable sizes are increased for greater lengths primarily for the purpose of minimizing cable drop.** Tabled values are for operation at ambient temperatures of 104°F(40°C) and below. Applications above 104°F(40°C) may require cables larger than recommended, or cables rated higher than 167°F(75°C).CV Power Sources with Stud Connectors and no Remote/Local Switch. (See Figure A.7)Place CV/CC switch in the feeder in the "CV" position.Work clipWorkElectrodeJumperLN™-25 PIPERanger 250, 250 LPG Ranger 305G, 305D Ranger 10,000Ranger 3 Phase Ranger 225GXT Ranger 225Commander 300Vantage 300, 400, 500Air Vantage 500FIGURE A.7POWER SOURCE TO LN™-25 PIPE CAbLE CONNECTION DIAGRAMS*If Power Source has a 14-Pin Cable connector and no“Output Terminal” switch.• ELECTRIC SHOCK CAN KILL. Unless using COLD FEED fea-ture, when feeding with gun trig-ger, the electrode anddrivemechanism are always electri-cally energized and could remain energized several sec-onds after the welding ceases..• Do not touch electrically live partor electrodewith skin or wet clothing.• Insulate yourself from work and ground.• Always wear dry insulating gloves.• Do not operate with covers, panels or guards removed or open.AND GASSES can bedangerous.ventilation or exhaust toremove fumes from breathingzone.SPARKS can causefire or explosion.eye, ear and body protec-tion.SEE ADDITIONAL WARNING INFORMATIONUNDER ARC WELDING SAFETY PRECAUTIONSAND IN THE FRONT OF THIS OPERATING MAN-UAL.---------------------------------------------------------------------READ AND UNDERSTAND ENTIRE SECTIONbEFORE OPERATING MACHINE.INPUT POWERONOFFWIRE FEEDERPOSITIVE OUTPUTNEGATIVE OUTPUTINPUT POWERDIRECT CURRENTOPEN CIRCUITVOLTAGEINPUT VOLTAGEOUTPUT VOLTAGEINPUT CURRENTOUTPUT CURRENTPROTECTIVEGROUNDWARNING ORCAUTIONU0U1U2I1I2GRAPHIC SYMbOLS THAT APPEAR ONTHIS MACHINE OR IN THIS MANUALDEFINITION OF WELDING TERMSWFS• Wire Feed SpeedCC• Constant CurrentCV• Constant VoltageGMAW• Gas Metal Arc weldingSMAW• Shielded Metal Arc weldingFCAW• Flux Core Arc WeldingGENERAL DESCRIPTIONGeneral Physical DescriptionThe LN™-25 PIPE is specially engineered to be the most rugged portable wire feeder available and meets the individual welder needs. This model includes a gas solenoid for flexibility to run most wire processes.The plastic case is molded from a high impact, flame retardant plastic for durability and low weight. The patent pending design keeps the internal components protected and dry.The heart of the LN™-25 PIPE is the 2 roll MAX-TRAC™ drive. The patented features on the wire drive offer tool-less changing of the drive rolls and wire guides for quick spool changes. A tachometer controlled motor powers the patent pending drive rolls for smooth, steady feeding without slippage.The LN™-25 PIPE has only two p.c. boards that are designed to be simple, reliable and easy to service. General Functional DescriptionThe LN™-25 PIPE as designed is a simple, robust feeder. Standard features include a calibrated wire feed speed dial, 2 step/trigger interlock switch, Gas Purge and Cold Feed.RECOMMENDED PROCESSES• GMAW• FCAWPROCESS LIMITATIONS• GMAW-P procedures must be qualified by the cus-tomer.• Across-the-Arc models are not recommended for stitch or spot welding.EQUIPMENT LIMITATIONS• The duty cycle of the wire feeder is 450A, 60%. Duty cycle is based upon the amount of welding performed in a 10 minute period.• The maximum spool size is 45 lb, 12" diameter.• Maximum FCAW gun length is 15 ft.• Maximum GMAW gun length is 25 ft.• K2330-1 Timer Kits do not work with the feeder. Use K2330-2 kits.• Push-pull guns do not work with the wire feeder.• The digital displays do not show preset voltage RECOMMENDED POWER SOURCES• CV-250• CV-300• CV-305• CV-400• CV-655• DC-400• DC-600• DC-655• Invertec V-350 PRO• Invertec V-450 PRO• Multi-Weld 350• Ranger 10,000• Ranger 3 Phase• Ranger 225• Ranger 225 GXT• Ranger 250• Ranger 250 GXT• Ranger 305• SAE-400• Pipeliner 200G• Classic 300• Vantage 300• Vantage 400• Vantage 500• Air Vantage 500Big Red’sEagle 10,000 PlusClassic’sWIRE FEED SPEED KNObWire Feed Speed, CV OperationWhen Across the Arc models are operated with CV power sources, the wire feed speed will remain a con-stant value, independent of arc voltage changes, as along as the arc voltage does not drop below the val-ues per the following table.83% Wire Feed SpeedThe 83% wire feed speed reduces the wire feed speed to 83% of the original set value when activated.For example, if the original wfs = 200 in/min, the feed-er will regulate to 0.83 x 200 = 166 in/min.The 83% trigger requires a gun with a dual procedure switch.This feature is often useful when welding pipe, and a “cooler” procedure is required on the bottom portion.The thermal light illuminates when the wiredrive motor draws too much current. If thewill automatically shutdown for up to 30 seconds to allowWFSA VWeldingvalue in the left display will be either ampsAMPS VOLTAGEA VAfter WeldingThe display continues to hold the value of theWFS and arc voltage for five secondsINTERNAL CONTROLSGAS PURGE PUSHbUTTONThe gas solenoid valve will energize but neither the power source output nor the drive motor will be turned on. The Gas Purge switch is useful for setting the proper flow rate of shielding gas. Flow meters should always be adjusted while the shielding gas is flowing.FACTORY INSTALLED EQUIPMENT • K1500-2 Gun Receiver Bushing.DRIVE ROLL KITS (See Parts Pages)ing with hose nipple, set screw ing with hose nipple, set screwing with hose nipple, set screwELECTRIC SHOCK can kill.• Turnthe input power OFF at the welding power source before installation or changing drive rolls and/or guides.•Do not touch electrically live parts.• When inching with the gun trigger, electrode and drive mechanism are "hot" to work and ground and could remain energized several seconds after the gun trigger is released.• Do not operate with covers, panels or guards removed or open.• Only qualified personnel should perform mainte-nance work.-----------------------------------------------------------------------ROUTINE MAINTENANCE• Check weld cables, control cables and gas hoses for cuts.• Clean and tighten all weld terminals.PERIODIC MAINTENANCE• Clean drive rolls and inner wire guide and replace if worn.• Blow out or vacuum the inside of the feeder.This Troubleshooting Guide is provided to help you locate and repair possible machine malfunctions.Simply follow the three-step procedure listed below.Step 1.LOCATE PROBLEM (SYMPTOM).Look under the column labeled “PROBLEM (SYMP-TOMS)”. This column describes possible symptoms that the machine may exhibit. Find the listing that best describes the symptom that the machine is exhibiting.Step 2.POSSIBLE CAUSE.The second column labeled “POSSIBLE CAUSE” lists the obviousexternal possibilities that may contribute to the machine symptom.Step 3.RECOMMENDED COURSE OF ACTIONThis column provides a course of action for the Possible Cause, generally it states to contact your local Lincoln Authorized Field Service Facility.If you do not understand or are unable to perform theRecommended Course of Action safely, contact your local Lincoln Authorized Field Service Facility.HOW TO USE TROUbLESHOOTING GUIDEService and Repair should only be performed by Lincoln Electric Factory Trained Personnel.Unauthorized repairs performed on this equipment may result in danger to the technician and machine operator and will invalidate your factory warranty. For your safety and to avoid Electrical Shock, please observe all safety notes and precautions detailed throughout this manual.__________________________________________________________________________JapaneseChineseKoreanArabicREAD AND UNDERSTAND THE MANUFACTURER’S INSTRUCTION FOR THIS EQUIPMENT AND THE CONSUMABLES TO BE USED AND FOLLOW YOUR EMPLOYER’S SAFETY PRACTICES.SE RECOMIENDA LEER Y ENTENDER LAS INSTRUCCIONES DEL FABRICANTE PARA EL USO DE ESTE EQUIPO Y LOS CONSUMIBLES QUE VA A UTILIZAR, SIGA LAS MEDIDAS DE SEGURIDAD DE SU SUPERVISOR.LISEZ ET COMPRENEZ LES INSTRUCTIONS DU FABRICANT EN CE QUI REGARDE CET EQUIPMENT ET LES PRODUITS A ETRE EMPLOYES ET SUIVEZ LES PROCEDURES DE SECURITE DE VOTRE EMPLOYEUR.LESEN SIE UND BEFOLGEN SIE DIE BETRIEBSANLEITUNG DER ANLAGE UND DEN ELEKTRO-DENEINSATZ DES HERSTELLERS. DIE UNFALLVERHÜTUNGSVORSCHRIFTEN DES ARBEITGEBERS SIND EBENFALLS ZU BEACHTEN.JapaneseChineseKoreanArabicLEIA E COMPREENDA AS INSTRUÇÕES DO FABRICANTE PARA ESTE EQUIPAMENTO E AS PARTES DE USO, E SIGA AS PRÁTICAS DE SEGURANÇA DO EMPREGADOR.。
款丰田卡罗拉自动变速器系统维修手册(英文版)

2004款丰田卡罗拉自动变速器系统维修手册(英文版) 40–1AUTOMATIC TRANSMISSION TRANS –AUTOMATIC TRANSAXLE ASSY ATMAUTOMATIC TRANSAXLE ASSY ATM400LF–01PRECAUTION1 The automatic transaxle is composed of highly precision–finished parts necessitating carefulinspection before reassembly because even a small nick could cause fluid leakage or affectthe performance The instructions here are organized so that youwork on only one componentgroup at a time This will help avoid confusion from similar–looking parts of different sub–as-semblies being on your workbench at the same time The component groups are inspected andrepaired from the converter housing side As much as possible complete the inspection repairand reassembly before proceeding to the next component group If a defect is found in a certaincomponent group during reassembly inspect and repair this group immediately If a compo-nent group cannot be assembled because parts are being ordered be sure to keep all parts ofthe group in a separate container while proceeding with disassembly inspection repair andreassembly of other component groupsRecommended ATF T–IV2 All disassembled parts should be washed clean and any fluid passages and holes should beblown through with compressed air3 Dry all parts with compressed air–never use shop rags4 When using compressed air always aim away from yourself to prevent accidentally sprayingATF or kerosene on your face5 The recommended automatic transaxle fluid or kerosene should be used for cleaning6 After cleaning the parts should be arranged in the correct order for efficient inspection repairsand reassembly7 When disassembling a valve body be sure to match each valve together with the correspond-ing spring8 New discs for the brakes and clutches that are to be used for replacement must be soaked inATF for at least 15 minutes before reassembly9 All oil seal rings clutch discs clutch plates rotating parts and sliding surfaces should becoated with ATF prior to reassembly10 All gaskets and rubber O–rings should be replaced11 Do not apply adhesive cements to gaskets and similar parts12 Make sure that the ends of a snap ring are not aligned with one of the cutouts and are installedin the groove correctly13 If a worn bushing is to be replaced the sub–assembly containing the bushing must also be re-placed14 Check thrust bearings and races for wear or damage Replace if necessary15 Use petroleum jelly to keep parts in place16 When working with FIPG material you must observe the followingUsing a razor blade and a gasket scraper remove all the old packing FIPG material from thegasket surfaceThoroughly clean all components to remove all the loose materialClean both sealing surfaces with a non–residue solventParts must be reassembled within 10 minutes of application Otherwise the packing FIPG ma-terial must be removed and reapplied2004 COROLLA RM1037U135140–2AUTOMATIC TRANSMISSION TRANS –AUTOMATIC TRANSAXLE FLUID ATMAUTOMATIC TRANSAXLE FLUID ATM400LG–01ON–VEHICLE INSPECTION1 CHECK THE FLUID LEVELHINTDrive the vehicle so that the engine and transaxle are at normaloperating temperatureFluid temperature 70 – 80 C 158 – 176 FOK if hot a Park the vehicle on a level surface and set the parkingAdd if hot b With the engine idling and the brake pedal depressedshift the shift lever into all ranges from P to L position andreturn to P positionc Pull out the dipstick and wipe it cleand Push it back fully into the pipee Pull it out and check that the fluid level is in the HOT posi-D25120 tionleaks it is necessary to repair or replace O–ringsFIPGs oil seals plugs or other parts2004 COROLLA RM1037U135240–3AUTOMATIC TRANSMISSION TRANS –PARKNEUTRAL POSITION SWITCH ASSY ATMPARKNEUTRAL POSITION SWITCH ASSY ATM400LH–01REPLACEMENT1 REMOVE BATTERY2 REMOVE BATTERY CARRIERa Remove the 4 bolts and battery carrierC801593 DISCONNECT FLOOR SHIFT CABLE TRANSMISSIONCONTROL SHIFTa Remove the nut from the control shaft leverbDisconnect the control cable from the control shaft leverc Remove the clip and disconnect the control cable fromthe control cable bracketC961474 REMOVE PARKNEUTRAL POSITION SWITCH ASSYa Disconnect the parkneutral position switch connectorb Remove the nut washer and control shaft leverc Pry out the lock plate and remove the manual valve shaftnutd Remove the 2 bolts and pull out the parkneutral positionswitchD251245 INSTALL PARKNEUTRAL POSITION SWITCH ASSYa Install the parkneutral position switch to the manual valveshaftb Temporarily install the 2 boltsc Place a new lock plate and tighten the nutTorque55 Nm 56 kgfcm 49 inlbfdTemporarily install the control shaft leverD099572004 COROLLA RM1037U135340–4AUTOMATIC TRANSMISSION TRANS – PARKNEUTRAL POSITION SWITCH ASSY ATMeTurn the lever counterclockwise until it stops then turn itclockwise 2 notchesf Remove the control shaft leverD25126g Align the groove with neutral basic lineNeutralh Hold the switch in position and tighten the 2 boltsBasic LineTorque 55 Nm 56 kgfcm 49 inlbfGrooveD08584i Using a screwdriver stake the nut with the lock plateD08585j Install the control shaft lever washer and nutTorque 125 Nm 127 kgfcm 9 ftlbfk Connect the parkneutral position switch connectorD251256 INSTALL FLOOR SHIFT CABLE TRANSMISSIONCONTROL SHIFTa Temporarily install the control cable to the control shaft le-ver with nutb Install the control cable and clip to the bracketC961472004 COROLLA RM1037U135440–5AUTOMATIC TRANSMISSION TRANS –PARKNEUTRAL POSITION SWITCH ASSY ATM7 INSTALL BATTERY CARRIERa Install the battery carrier and 4 boltsTorque 13 Nm 132 kgfcm 10 ftlbfC801598 ADJUST SHIFT LEVER POSITION See page 40–449 INSPECT SHIFT LEVER POSITION See page 40–4410 INSPECT PARKNEUTRAL POSITION SWITCH ASSY See page 40–62004 COROLLA RM1037U135540–6AUTOMATIC TRANSMISSION TRANS –PARKNEUTRAL POSITION SWITCH ASSY ATM400LI–01ADJUSTMENT1 INSPECT PARKNEUTRAL POSITION SWITCH ASSYa Apply the parking brake and turn the ignition switch ONb Depress the brake pedal and check that the engine starts only when the shift lever is set in N or P posi-tion and it does not start in the other positionc Check that the back–up light comes on and the reverse warning buzzer sounds only when the shiftlever is set in R position and these do not function in the other positionsIf a failure is found check the park neutral position switch for continuity2 ADJUST PARKNEUTRAL POSITION SWITCH ASSYa Loosen the 2 bolts of park neutral position switch and setNeutralBasic Line the shift lever to the N positionb Align the groove and neutral basic linec Hold the switch in position and tighten the 2 boltsTorque 55 Nm 56 kgfcm 49 inlbfd After adjustment perform the inspection described inGroovestep1D255142004 COROLLA RM1037U135640–7AUTOMATIC TRANSMISSION TRANS – AUTOMATIC TRANSAXLE ASSY ATMAUTOMATIC TRANSAXLE ASSY ATM400LJ–01COMPONENTSHood Sub–assyAir Cleaner Assy13 132 1070 71 62 inlbf70 71 62 inlbfBatteryCylinder HeadCover No2 12 122 91275 130 913 132 1010 102 7Control Cable Support255 260 19StarterAssy39 400 2913 132 10 wo ABSOil Cooler Inlet Tube No1Oil Cooler OutletTube No1 39 400 29 13 132 10Floor ShiftCable Transmission345 350 25Control Shift55 56 49 inlbfClipSpeedometer sensorTransmission Oil Filler connectorTube Sub–assy55 56 49 inlbf Battery Carrier12 1229 Automatic Transaxle AssyO–ringATF Level Gauge12 122 9 Transmission Control CableNm kgfcm ftlbf Specified torque Bracket No1Non–reusable part C953482004 COROLLA RM1037U135740–8AUTOMATIC TRANSMISSION TRANS– AUTOMATIC TRANSAXLE ASSY ATM80 815 59Front Drive Shaft Assy RH52 530 3852 530 38Snap Ring Engine MountingBracket LHTorque Converter Clutch Assy64 65047 Engine Mounting52 530 38Insulator LHx 646 470 3428 285 20Snap Ring23 235 17 Front Drive Shaft Assy LHFlywheel Housing Under CoverTransmission Case Protector18 182 14Automatic Transaxle AssyEngine Mounting Insulator RREngine Mounting 87 887 64Bracket RR 64 652 47Engine Mounting Bracket FR64 652 47Engine Under Cover RH52530 3852 530 38Engine Under Cover LH 64 652 4764 652 4752 530 38FrontSuspension Member DynamicDamper52 530 38Engine Mounting MemberSub–assy CenterNm kgfcm ftlbf Specified torque 39 398 29Non–reusable part C953492004 COROLLA RM1037U135840–9AUTOMATIC TRANSMISSION TRANS –AUTOMATIC TRANSAXLE ASSY ATM400LK–02REPLACEMENT1 REMOVE HOOD SUB–ASSY2 REMOVE CYLINDER HEAD COVER NO23 REMOVE BATTERY4 REMOVE BATTERY CARRIERa Remove the4 bolts and battery carrierC801595 REMOVE AIR CLEANER ASSEMBLY WITH HOSE6 REMOVE FLOOR SHIFT CABLE TRANSMISSIONCONTROL SHIFTa Remove the nut from the control shaft leverb Disconnect the control cable from the control shaft leverc Remove the clip and disconnect the control cable fromthecontrol cable bracketC961477 REMOVE TRANSMISSION CONTROL CABLESUPPORTa Disconnectthe wire harness clamp and control cablefrom thecontrol cable supportb Remove thebolt and control cable supportC957508 REMOVE TRANSMISSION CONTROL CABLE BRACKET NO1a Remove the 2 bolts and control cable bracket2004 COROLLA RM1037U135940–10AUTOMATIC TRANSMISSION TRANS –AUTOMATIC TRANSAXLE ASSY ATM9 DISCONNECT WIRE HARNESSa Remove the2 bolts and disconnect the 2 wire harnessesb Remove the bolt and disconnect the wire harness clampbracketC93666c Remove thebolt and disconnect the wire harness clampbracketC9364310 DISCONNECT CONNECTORa Disconnect the transmission wire connectorb Disconnect the parkneutral position switch connectorc wo ABSDisconnect the speedometer sensor connector11 REMOVE TRANSMISSION OIL FILLER TUBESUB–ASSYa Remove the ATF lever gaugeb Remove the 2 bolts oil cooler tube clamp and oil fillertubec Remove theO–ring from the oil filler tubeD0996112 DISCONNECT OIL COOLER INLET TUBE NO1a Using SST disconnect the oil cooler inlet tube No 1SST 09023–12700SSTC9364613 DISCONNECT OIL COOLER OUTLET TUBE NO1a Using SST disconnect the oil cooler outlet tube No 1SST 09023–127002004 COROLLA RM1037U136040–11AUTOMATIC TRANSMISSION TRANS –AUTOMATIC TRANSAXLE ASSY ATM14 DISCONNECT OXYGEN SENSOR CONNECTORa Remove the foot restb Pull up the floor carpetc Disconnect the oxygen sensor connectorNo 1 No 2 15 SUSPEND ENGINE ASSYEngine Hanger Engine Hanger a Disconnect the 2 PCV hosesb Install the No1 and No2 engine hangers in the correctdirectionParts NoNo1 engine hanger 12281–22021No2 engine hanger 12281–15040Bolt91512–B1016Front Rear D25372 Torque 38 Nm 387 kgfcm 28 ftlbfc Attach the engine chain hoist to the engine hangersCAUTIONDo not attempt to hang the engine by hooking the chain toany other parts16 REMOVE FRONT WHEELS17 REMOVE ENGINE UNDER COVER RH18 REMOVE ENGINE UNDER COVER LH19 DRAIN AUTOMATIC TRANSAXLE FLUIDa Remove the drain plug and gasket and drain ATFb Install a new gasket and drain plugTorque 175 Nm 178 kgfcm 13 ftlbf20 REMOVE EXHAUST PIPE ASSY FRONT See page 15–221 REMOVE FRONT DRIVE SHAFT ASSY RH See page 30–6SST 09520–01010 09520–24010 09520–32040 22 REMOVE FRONT DRIVE SHAFT ASSY LH See page 30–6SST 09520–01010 09520–24010 09520–3204023 REMOVE AUTOMATIC TRANSMISSION CASE PROTECTORa Remove the 2 bolts and case protector24 REMOVE STARTER ASSYa Remove the nut and disconnect the starter wireb Disconnect the connectorc Remove the 2 bolts and starter25 SUPPORT AUTOMATIC TRANSAXLE ASSYa Support the automatic transaxle with a transmission jack26 REMOVE TRANSVERSE ENGINE ENGINEMOUNTINGINSULATORa Remove the 5bolts nut and engine mounting insulatorLHD099642004 COROLLA RM1037U136140–12AUTOMATIC TRANSMISSION TRANS –AUTOMATIC TRANSAXLE ASSY ATM27 REMOVE TRANSVERSE ENGINE ENGINEMOUNTINGBRACKETa Remove the3 bolts and engine mounting bracket LHD0996528 REMOVE TRANSVERSE ENGINE ENGINEMOUNTING INSULATORa Remove thebolt from the engine mounting bracket RRC80192b Remove the3 nuts bolt and engine mounting insulatorRR from the suspension memberC8016729 REMOVE TRANSVERSE ENGINE ENGINEMOUNTING INSULATORa Remove thebolt and nut from the engine mounting brack-et FRC8016630 REMOVEENGINE MOUNTING MEMBER SUB–ASSYCENTERa Remove the4 bolts dynamic damper and member sub–assycenter with engine mounting insulator FRC953542004 COROLLA RM1037U136240–13AUTOMATIC TRANSMISSION TRANS –AUTOMATIC TRANSAXLE ASSY ATM31 REMOVETRANSVERSE ENGINE ENGINEMOUNTINGBRACKETa Remove the 2bolts and engine mounting bracket FRC8017232 REMOVE TRANSVERSE ENGINE ENGINEMOUNTINGBRACKETa Remove the 3bolts and engine mounting bracket RRC9364533 REMOVE FLYWHEEL HOUSING UNDER COVER34 REMOVE AUTOMATIC TRANSAXLE ASSYa Turn the crankshaft to gain access and remove the 6 boltswhile holding the crankshaft pulley bolt with a wrenchF00478b Remove the 6 boltsc Separate and remove the automatic transaxleD0996635 REMOVE TORQUE CONVERTER CLUTCH ASSY36 INSPECT TORQUE CONVERTER CLUTCH ASSY See page 40–20SST 09350–32014 09351–32010 09351–320202004 COROLLA RM1037U136340–14AUTOMATIC TRANSMISSION TRANS –AUTOMATIC TRANSAXLE ASSY ATM37 INSTALL TORQUE CONVERTER CLUTCH ASSYa Install the torque converter clutch to the automatic trans-axleb Using vernier calipers measure the dimension A be-tweenthe transaxle fitting part and the converter fittingpart of the drive plateC63993c Using vernier calipers and a straight edge measure thedimension B shown in the illustration and check that Bisgreater than A measured in bStandardA 1 mm or moreNOTICEDo not add the thickness of straight edgeC6591138 INSTALL AUTOMATIC TRANSAXLE ASSYa Install the automatic transaxle and 6 bolts to the engineTorqueABolt A 64 Nm 650 kgfcm 47 ftlbfB Bolt B。
美国汽车品牌的车辆维修手册说明书
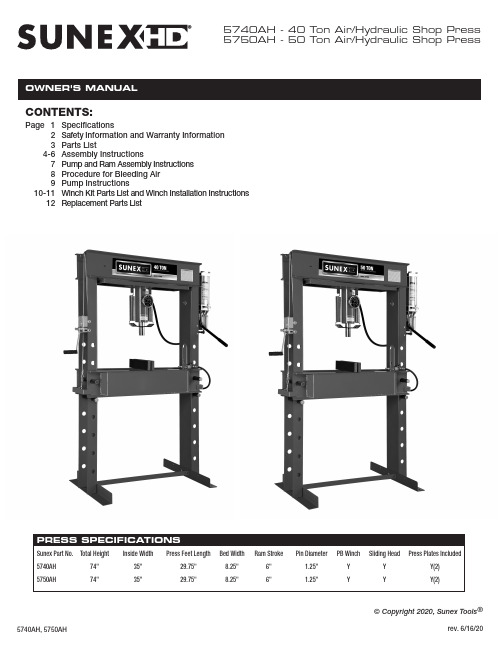
5740AH - 40 Ton Air/Hydraulic Shop Press 5750AH - 50 Ton Air/Hydraulic Shop PressCONTENTS:Page 1Specifications2Safety Information and Warranty Information 3Parts List4-6Assembly Instructions789Pump and Ram Assembly Instructions Procedure for Bleeding Air Pump Instructions10-11Winch Kit Parts List and Winch Installation Instructions 12Replacement Parts List© Copyright 2020, Sunex Tools ®SAFETY INFORMATIONThis symbol alerts you to the possibility of serious injury or death if instructions are not followed.This symbol alerts you to the possibility of damage to or destruction of equipment if instructions are not followed.Failure to heed these warnings may result in lossof load, damage to the press and/or failure resulting in property damage, personal or fatal injury. Thisoperating manual contains important details concern-ing the safe operation of this tool. The user must read and understand these details before any use of the tool. This manual must be retained for future reference.• Read, study, understand and follow all instructions before operating this press.• Always wear safety goggles, (users and bystanders).•Parts being pressed may splinter, shatter, or be ejected from the press at a dangerous rate of speed. Because there are a variety of press applications, it is the responsibility of the press owner to provide adequate guards, eye protection and protective clothing to the press operator.• Visual inspection of the press should be made before use, checking for signs of cracked welds, bent bed pins, loose or missing bolts, leaks, or any other structural damage. Corrections must be made before using the press.•Do not go near leaks. High pressure hydraulic uid can puncture skin and cause serious injury,gangrene, or death. If injured, seek emergency medical help as immediate surgery is required to remove the uid.• Prior to use make sure the press is securely anchored to a concrete oor.•Keep hands, arms, feet, and legs out of work area. Accidental slippage can result in personal injury.• Always use an accurate force gauge to measure pressing force.• Do not exceed the rated capacity or tamper with the pressure/force settings. When attachments and adapters are used the rated capacity of the system shall be no greater than the rated capacity of the lowest rated component or combination of components that make up the system. • Avoid off-center loads. Offset loads can damage ram and may cause load to eject at a dangerous rate of speed. Do not use any spacer or extender between the press ram plunger and the item being pressed. If there is not enough ram stroke, adjust the height of the movable bolster.•Remove all loads from movable bolster before attempting to adjust bolster height. Beware of possible falling bolster.•Press only on loads supported by movable bolster and press plates included. Do not support loads on oor or press frame legs.• When using any accessories such as press plates or arbor plates, be certain they are centered on the movable bolster and in full contact with both sides of the bolster.• Before applying load, be certain all movable bolster supporting pins are fully engaged. Verify lift cables (if equipped) are slack before pressing on the bolster.• Always use a bearing shield when pressing bearings.•Use caution when positioning work to be pressed to ensure the item to be pressed cannot be ejected at a dangerous rate of speed.• Release hydraulic pressure before loosening any ttings.• Maintain proper hydraulic uid levels.• Do not make any alterations or modi cations to the press.•This product may contain one or more chemicals known to the State of California to cause cancer and birth defects or other reproductive harm. Wash hands thoroughly after handling.•Failure to heed and understand these markings may result in serious or fatal personal injury and/or property damage.OWNER/USER RESPONSIBILITYThe owner and/or user must have an understanding of the manufacturer'soperating instructions and warnings before using this press. Personnel involvedin the use and operation of equipment shall be careful, competent, trained,and quali ed in the safe operation of the equipment and its proper use whenservicing motor vehicles and their components. Warning information shouldbe emphasized and understood.If the operator is not uent in English, the manufacturer's instructions andwarnings shall be read to and discussed with the operator in the operator'snative language by the purchaser/owner, making sure that the operatorcomprehends its contents.Owner and/or user must study and maintain for future reference the manufactur-er’s instructions. Owner and/or user is responsible for keeping all warning labels and instruction manuals legible and intact. Replacement labels and literature are available from the manufacturers.INSPECTIONVisual inspection of the shop press should be made before each use of the press, checking for damaged, loose or missing parts. Each press must be inspected by a manufacturer’s repair facility immediately, if subjected to an abnormal load or shock. Any press which appears to be damaged in any way, is found to be badly worn, or operates abnormally must be removed fromservice until necessary repairs are made by a manufacturers's authorized repair facility. It is recommended that an annual inspection of the press be made by a manufacturer’s authorized repair facility and that any defective parts, decals or warning labels be replaced with manufacturer’s speci ed parts. A list of authorized repair facilities is available from the manufacturer.SAFETY INSTRUCTIONS•CHECK YOUR LOCAL, STATE AND FEDERAL REGULATIONSREGARDING THE SAFE USE OF THIS EQUIPMENT.•Your safety is top priority. Please handle equipment with care.•Fully retract unit and remove all items from the press bed frame.•Support the press bed, and remove the pins.•Raise or lower bed to desired height and reinstall press pins. Be certainpins are fully engaged in the parallel anges of the upright columns.•Position press on a at, level, hard surface, preferably concrete.Make sure all nuts and bolts are tight.•Clear the area of bystanders, especially small children, before using.•Set the press bed to the required height. The press is most effectivewhen the work piece is located 1 inch below the ram’s retracted position.The compression stroke can include the entire 5 inch working range.•The press is designed to exert a force on anything which is positionedbeneath its ram. The work piece can pop out from under the ram at a high rate of speed and injure someone.•Pressing Bearings: It is essential that you use the bearing shield whenpressing bearings on or off.LIMITED WARRANTY:SUNEX INTERNATIONAL, INC. WARRANTS TO ITS CUSTOMERS THAT THE COMPANY’S SUNEX TOOLS ® BRANDED PRODUCTS ARE FREE FROM DEFECTS IN WORKMANSHIP AND MATERIALS.Sunex International, Inc. will repair or replace its Sunex T ools ® branded products which fail to give satisfactory service due to defective workmanship or materials, based upon the terms and conditions of the following described warranty plans attributed to that speci c product. This product carries a ONE-YEAR warranty. During this warranty period, Sunex T ools ® will repair or replace at our option any part or unit which proves to be defective in material or workmanship. Other important warranty information....This warranty does not cover damage to equipment or tools arising fromalteration, abuse, misuse, damage and does not cover any repairs or replace-ment made by anyone other than Sunex Tools ® or its authorized warranty service centers. The foregoing obligation is Sunex Tools ®’ sole liability under this or any implied warranty and under no circumstances shall we be liable for any incidental or consequential damages. Note: Some states do not allow the exclusion or limitation of incidental or consequential damages, so the abovelimitation or exclusion may not apply to you. Return equipment or parts to Sunex Tools ®, transportation prepaid. Be certain to include your name and address, evidence of the purchase date, and description of the suspected defect.If you have any questions about warranty service, please write to Sunex Tools ®.This warranty gives you speci c legal rights and you may also have other rightswhich vary from state to state. Repair kits and replacement parts are available for many of Sunex Tools ® products regardless of whether or not the product is still covered by a warranty plan.SHIPPING ADDRESS: MAILING ADDRESS:Sunex Tools Sunex Tools 315 Hawkins Rd. P .O. Box 4215Travelers Rest, South Carolina 29690 Greenville, South Carolina 29608THIS OPERATING MANUAL CONTAINS IMPORTANT SAFETY INFORMATION. READ CAREFULLY AND UNDERSTAND ALL INFORMATION BEFORE OPERATING THIS TOOL. SAVE THIS MANUAL FOR FUTURE USE.WARNING: This product can expose you to chemicals including nickel, which is known to the State of California to cause cancer and birth defects or other reproductive harm.For more information go to .Press Frame - 1Press Bed - 1Press Feet - 2Z Bar - 11/2"-13 x 1-1/2" Hex Head Bolts - 101/2" Nuts - 10Air MotorPump and Ram - 1Pump Extension Handle - 11" x 3" x 14"Press Plates - 2Accessory only -Not needed for assemblyPushing Adapter - 1Accessory only -Not needed for assemblyBearing Shield - 1Accessory only -Not needed for assemblyESTIMATED ASSEMBLY TIME: 30 MINUTESACCESSORIESASSEMBL CONTINUEDPUMP AND RAM ASSEMBL Y INSTRUCTIONSPROCEDURE FOR BLEEDING AIRPUMP INSTRUCTIONSWINCH INSTALLATION INSTRUCTIONS CONTINUED。
Auto Clean Rotisserie ACR 维修手册说明书

INSTALLATION MANUALAuto Clean RotisserieACR on underframe- NOTICE -This manual is prepared for the use of trained Service Technicians and should not be used by those not properly qualified. If you have attended a training for this product, you may be qualified to perform all the procedures in thismanual.This manual is not intended to be all encompassing. If you have not attended a training for this product, you should read, in its entirety, the repair procedure you wish to perform to determine if you have the necessary tools, instru-ments and skills required to perform the procedure. Procedures for which you do not have the necessary tools, instruments and skills should be performedby a trained technician.Reproduction or other use of this Manual, without the express written consent ofFri-Jado, is prohibited.VersionsVersion Issue dateRemarks dd/mm/yy130627/06/2013First releaseINDEXIndex (4)General technical data (5)Technical Data ACR on Stand (5)Installation procedures (6)Introduction (6)Unpacking the unit (6)Location (7)Electrical supply (7)Factory default ! (7)Legs / Castors (8)Tethering of the unit (8)Water supply and filter connection (9)Placing of detergent (10)Placing of bucket (10)Connecting the drain tube (10)Test run (11)Extraction of the rotisserie (11)Instructions for operators (11)Placing and connecting (12)GENERAL TECHNICAL DATAThis manual covers the ACR rotisserie.All of the information, illustrations and specifications contained in this manual are based on the latest product information available at the time of printing.DimensionsWidth mm 1440Depth mm 950 [SB], 1065 [PT]Height mm 1810WeightGross kg 445Netkg 380Maximum ambient temperature °C 35Sound pressuredB (A)< 70Electrical installationVoltage V 3N~ 400/230FrequencyHz 50/60Required powerkW 12Max. nominal current A 18PlugCEE-form A 32lengthm approx. 2.2DrainOpen connection mm min. 40Water connection Aerated inch ¾WaterpressurekPa 200 – 500flowing at 15 ltr/min Acidity pH 7.0-8.0Chloridesppm < 30Water hardness KH< 7°(0° = recommended !)DrainOpen connectioninch min. 40 mm inside Cleaning agentJohnson diversey, Suma D9mLapprox. 1000 per cycleEcolab, Greasecutter Plus Ecolab, 158Dr Becher. UN1824 NL-B Oven and grill cleaner Wesca. LP052-09INSTALLATION PROCEDURES• Unpacking of the unit.• Remove the pallet under the unit with the help of a fork lift.• Put the unit on his location.• Check if there is enough free space around the unit (see installation drawing).• Tethering of the unit.• Check the electrical supply.• Connect the water. Measure water hardness. Connect the lime filter.• Place detergent. Place bucket. Connect drain.• Make a test run on 250°C.• Give instructions to the operator.Immediately after unpacking the oven, check for possible shipping damage. If the oven is found to be damaged, save the packaging material and contact the carrier within 15 days of delivery.The standard way to remove the oven from a pallet is with a fork lift.INSTALLATION PROCEDURESPrior to installation, test the electrical service to assure that it agrees with the specifications on the machine data plate located on the right side panel near the controls. The connecting cable for the unit must be equipped with an approved plug connection. If use is to be made of a permanent connection, the connecting cable must be connected to a manual on/off switch that is installed near the unit in a clear visible manner.IMPORTANT: Make sure you lea-ve sufficient space around therotisserie or warmer to easily remove or insert the rotor. If the base has (rotating) wheels, the floor on which it rests must be level.The oven must be installed on a level surface. The installation location must allow adequate clearances for servicing and proper operation.The unit must be connected according to one of the the figures below.910 mm 36”123456NL1123456L2L1L3N 123456L2L1L3400 V, 3N ~ 50...60 Hz200 V or 230 V, 1N ~ 50...60 Hz200 V or 230 V, 3 ~ 50...60 HzFACTORY DEFAULT !INSTALLATION PROCEDURESThe ACR is placed on a stand with 2 swivel and 2 locking swivel castors.Warning: Safety standards require that, when this appliance is properly connected to the electrical power supply using flexible conduit, adequate means be provided to limit move-ment of the appliance without depending on or transmitting stress to the electrical conduit. This means that, as part of the installation, the base or bottom unit of stacked models must be secured to the building structure (typically either wall or floor) to limit the movement of the appliance and, thus, helping to prevent damage to the conduit during cleaning, main-tenance and service operations.A tether bracket, as shown on the drawing below, is provided with the stand. Based on the routing of the flexible conduit, the bracket must be installed along with the caster to one corner of the base using the hardware provided. The remaining open hole in the center of the tether bracket is to be used to secure one end of the tether (locally supplied chain, cable, etc.). The other end of the tether is to be secured to an anchoring point in the building struc-ture.Note: Length of tether must be shorter than the flexible conduit to make sure that duringappliance movement, no stress is transmitted to the conduit.INSTALLATION PROCEDURESOn the backside of the stand, 2 water inlets can be found with 3/4” connection. As shown, the outmost is meant for filtered (descaled) water. The other connection has to be used for normal tap water.2 hoses with 3/4” straight to 3/4” angled, lenght 1,5mtr (60”) are supplied with the unit.A water filter, in case applicable, can be connected on the inside or on the outside of the stand.Note that on the inside of the stand, a hose can be disconnected from the 3/4”socket in or-der to put the filter in between.Both connections need to be connected!!In case one connection is left open, the water from the other one will come out.In case one connection is blocked, the cleaning program will not function properly.The by-pass of the descaling filter, if applicable, needs to be adjusted to zero.Refer to the filters manual to determine the filter capacity. This filter capacity needs to be adjusted in the manager parameters.supplied with the unit.INSTALLATION PROCEDURESPlace the bottle of detergent inside the side of the stand. Place the tube with cap inside the bottle. Be sure that the tube sticks inside the bottle until the bottom.There are 6 different approved detergents suitable for the ACR. These are:1. Diversey, Suma D9.2. Ecolab. Grease Cutter Plus.3. Ecolab. 158.4. Dr. Bechaer. UNI824 NL-B Oven and Grill Cleaner.5. Wesca. LP052-09.The first 2 products are highly recommended.PLACING OF BUCKETPlace the bucket, which is delivered with the unit, inside the stand under the drain valve.It is also possible to put other containers in the underframe to collect the grease.Note1: In one run, 5 liters ( 1,3 gallon) grease can come out.Note 2: The temperature of the grease can go up to 80°C (176°F).Make sure that the container meets the above requirements.CONNECTING THE DRAIN TUBEAn open draining system with a 110 mm (4 1/2”) funnel is recommended (see installation drawing). The drain tube has an outside diameter of 33 mm (1 1/3 inch).• It is not allowed to make a closed connection!• Make sure that the tube is not kinked and is sloping downwards to the drain funnel. • The minimum inside diameter of the sewer pipe needs to be 40mm (1 1/2”).• A siphon in the customers sewer is highly recommended to prevent odors from coming out of the sewer.INSTALLATION PROCEDURESThe oven must be burned in to release any odours that might result from heating the new oven surfaces. Operate the oven at maximum temperature setting of 250°C for 30 minutes. Smoke with an unpleasant odour will normally be given off during this burn-in period.An extraction hood is prescribed. The ACR produces about 10 m³ vapour during a cooking cycle. When placing the rotisserie under an extraction hood, the following guide lines have to be considered (see also the installation drawing):• The minimum capacity of the extraction hood has to be 800 m³/h.• The extraction hood has to extend minimum by 20 cm on all sides of the rotisserie.• The extraction hood has to have a free hight, above the rotisserie, of a minimum of 30 cm.• The rotisserie has to be accessible for service purposes.• The extraction hood has to have facilities to drain any condensation, down to a drain.After installation of the rotisserie the operator of the unit has to be instructed.The instruction has to cover the following subjects:• Programming and options.• Working of the unit.• Free space of unit for cooling of drive motor and blowers.• Run through the user manual.• How to check and change detergent.• Periodical maintenance:o Cleaning of fan plate every month.o Cleaning of top plate every month.o Changing lime filter when saturated.• How to react for information or service calls.PLACING AND CONNECTINGDESCRIPTION OF THE LABELS1 Exit of power cable. 1,5mtr3 Watersupply inlet “G”¾”4 Drain hose 32mm , lenght 1,5mtr5 Fume outlet (vent) oven.6a Space between the oven and a wall. 6b Space between the back and a wall. 7 Space between top and hood.8 Capture funnel for drain water 10 Suction pipe, air.bFri-Jado B.V. • P.O.Box560•4870AN•Etten-Leur•TheNetherlands•tel+31765085400•fax+31765085444•****************•。
Cascade 20D Razorback Clamp 的维修手册说明书
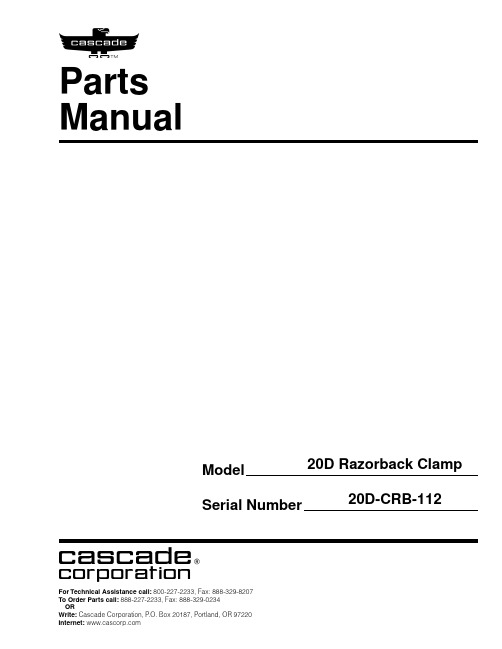
Parts Manual cFor Technical Assistance call: 800-227-2233, Fax: 888-329-8207 To Order Parts call: 888-227-2233, Fax: 888-329-023420D R azorback Clamp20D-CRB-112ModelSerial Number cascadeாcorporationPART NO.DESCRIPTION669224Service Manual 672944Operators Guide668987Installation Instructions680664Servicing Cascade Cylinders-VHS 679929Tool Catalog673964Literature Index Order FormPublicationsREF QTY PART NO.DESCRIPTION 11679150No Step Decal22665595No Hand Hold Decal31679059Quick Change Hook Decal123Base Unit GroupREF QTY PART NO.DESCRIPTION353771Base Unit Group 12207425Hose, 24.00 in.22675055Hose, 17.50 in.31601377Fitting, 8-842601377Fitting, 8-856601377Fitting, 8-863671222Capscrew, 3/8 NC x .75724071Capscrew82671570Cylinder v927861Roll Pin - Inner1027962Roll Pin - Outer 111671549Frame - Upperv See Cylinder page for parts breakdown.q Not included in Base Unit Group.See Restrictor Cartridge page for parts breakdown. Reference: SK-5299.REF QTY PART NO.DESCRIPTION 128667910Washer138667909Capscrew141682098Bumper152665707Nut, 1/2 in. ID1623659Capscrew174668910Bearing184667663Bearing194668911Bearing201680620Mounting Plate - RH211680619Mounting Plate - LH221674168Frame - Lower232667609Restrictor Cartridge q20D25DREF QTY PART NO.DESCRIPTION671570Cylinder Assembly 126510Cotter Pin s 22667624Nut Retainer s 32667625Nut s41671572Shell 51602580Fitting 61558200Piston 712716O-Ring v 81662452Seal v 912785O-Ring v101615128Back-Up Ring v 111563906Retainer 121662448Seal v131638243Nylon Ring v 141636853Wiper v 151667623Nut 161667623Rod 171667626Washer 181—Spacer191671047Seal Loader, Piston v 201671051Seal Loader, Retainer v 668021Service Kitv Included in Service Kit 668021.s Included in Nut Service Kit 668926.Reference: S-7605, S-7658CylinderRestrictor CartridgeREF QTY PART NO.DESCRIPTION667609Restrictor Cartridge 112701O-Ring21667611Plunger312841O-Ring41667610Plug – Special515716Jam NutREF QTY PART NO.DESCRIPTION344388Valve Group 343684Valve Group v 11667490Special Fitting 212841O-Ring q 31667471Spool 42609453Fitting, 1052667487Spring 67604510Fitting, 671678270Check Valve – VPO 82659058Check Valve – PO 92667516Service Kit q101679846Low Flow Spool Kit 112667494Fittingq Included in Service Kit 667513.v Items 1–22 only.Valve GroupREF QTY PART NO.DESCRIPTION1222840O-Ring q 132673098Spring 142667492Poppet151673089Spool Assembly 162667491Sleeve 171343685Valve Body 181661347Service Kit q 191334615Relief Valve 201684625Service Kit 211343687Relief Valve 221667510Service Kit 231334808Valve Bracket 667513Service KitArm Groupq Includes items 1 thru 7 only.Quick-Change Mounting GroupClass IIREF QTY PART NO.DESCRIPTION678833Lower Hook Group12675514Hook24678942Capscrew, 5/8 NC x 1.2532675515Guide42678832PinReference: S-3197.Mounting Plates with Bolt-On Upper HooksREF QTY PART NO.DESCRIPTION1 1 680619 Mounting Plate Assembly–LH q2 1 680620 Mounting Plate Assembly–RH s 316002330Upper Hook–LH 41210491Upper Hook–RH 54768577Capscrew, M20 x 35q Includes items3 and 5.sIncludes items 4 and 5.Do you have questions you need answered right now? Call your nearest Cascade Parts Department.Cascade (UK) Ltd.15, Orgreave Crescent Dore House Industrial Estate HandsworthSheffield S13 9NQ EnglandTel: 742-697524FAX: 742-695121Cascade Scandinavia AB Box 124Hammarvägen 10567 23 Vaggeryd SwedenTel: 42-0-393-36950 FAX: 46-0-393-36959Cascade N.V. European Headquarters P.O. Box 30091300 El Almere Damsluisweg 561332 ED AlmereThe NetherlandsTel: 31-36-5492911 FAX: 31-36-5492964Cascade Norway Østerliveien 37A 1153 Oslo NorwayTel: 47-22-743160 FAX: 47-22-743157Cascade France S.A.R.L.1D Rue De CharaintruBP 18, 91360 Epinay-Sur-OrgeMorangis Cedex, FranceTel: 33-1- 64547500FAX: 33-1-64547501Cascade Hispania S.A.Carrer 5 Sector CZona Franca DuaneraPoligono de la Zon Franca08040 Barcelona, SpainOffice No. 256Tel: 93-264-07-30FAX: 93-264-07-31Cascade Canada Inc.5570 Timberlea Blvd.Mississauga, OntarioCanada L4W-4M6Tel: 905-629-7777FAX: 905-629-7785Cascade GmbHD-41199 MonchengladbachKlosterhofweg 52GermanyTel: 49-216-668230FAX: 49-216-6682323Cascade N.V.Benelux Sales and ServiceP.O. Box 30091300 El AlmereDamsluisweg 561332 ED AlmereThe NetherlandsTel: 31-36-5492950FAX: 31-36-5492974Cascade FinlandAlbert Petreliuksenkatu 301370 VantaaFinlandTel: 358-9-836-1925FAX: 358-9-836-1935Cascade Corporation2501 Sheridan AvenueSpringfield, OH 45505Tel:888-CASCADE (227-2233)FAX: 888-329-0234Cascade Japan Ltd.5-5-41,Torikai KamiSettsu, OsakaJapan, 566Tel: 81-726-53-3490FAX: 81-726-53-3497Cascade Korea108B, Namdong Ind Complex 658-3 Gojan-Dong Namdong-GuInchon, 405-310 KoreaTel: 82-32-821-2051FAX: 82-32-821-2055Cascade Australia1445 Ipswich RoadRocklea, QLD 4106AustraliaTel: 1-800227-223FAX: (07) 3373-7333Cascade New Zealand15 Ra Ora DriveEast Tamaki, AucklandNew ZealandTel: 9-273-9136FAX: 9-273-9137Cascade (Africa) Pty. Ltd.P.O. Box 625, Isando 160060A Steel RoadSparton, Kempton ParkSouth AfricaTel: 27-11-975-9240FAX: 27-11-394-1147Cascade-Xiamen No. 668 Yangguant Rd. Xinyang Industry Zone Haicant, Xiamen City Fujian ProvinceP.R. China 361026 Tel: 86-592-651-2500 FAX: 86-592-651-2571Cascade (Singapore) Trading Co.Four Seasons Park Autumn Block - Apt. 1802 12 Cuscaden Walk SingaporeTel: 65-834-1935FAX: 65-834-1936c。
莫瑞德独立悬挂系统维修手册说明书
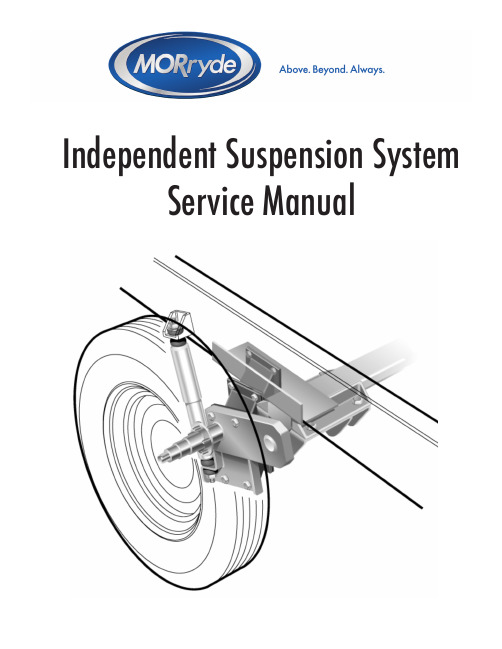
Independent Suspension SystemService ManualIndependent Suspension SystemCONTENTSINTRODUCTION (2)MAINTENANCE (3)SERVICE..............................................................................................................................3-5SUSPENSION ALIGNMENT (5)TROUBLE SHOOTING AND TORQUE CHART..........................................................6-7INTRODUCTIONDESCRIPTIONThe MORryde “IS” Independent Rubber Suspension System uses 100% Natural Rubber Springs to support the trailer weight and absorb road shock. By absorbing the shock, the rubber provides a much smoother towing experience than steel leaf springs. With the new MORryde “IS” Independent Rubber Suspension System, there are no more broken leaf springs! The towing is virtually hassle-free with the smoothest towing available for fifth wheels and travel trailers.The Primary benefits that you can expect from the MORryde ”IS” suspension are:SMOOTHER TOWING - the MORryde suspension has up to 2 1/2 times the suspension travel of leaf springs or rubber axles, allowing the MORryde suspension to absorb road shock much better.IMPROVED TOWABILITY - the MORryde suspension is designed to “block” body roll, improving the cornering and stability of the tow vehicle and trailer combination.AUTOMOTIVE STYLE ALIGNMENT - a MORryde first! You can manage your tire wear through toe and camber adjustments, a feature no other towable suspension offers!HEIGHT ADJUSTABILITY - the MORryde suspension can be adjusted easily to accommodate different tow heights and to compensate for side-to-side load variations.PROVEN DURABILITY - the MORryde suspension has undergone strenuous testing to prove it’s durability. The result? No more broken leaf springs!U.S. PAT. NO. 5,899,470MAINTENANCEMaintenance to the MORryde “IS” suspension system is minimal. For service information regarding bearing options or braking systems on your trailer, please consult the appropriate brake/axle manufacturer.LUBRICATIONAfter November of 2001, the “IS” journal shaft will have a grease zerk on the under side of the “IS” torque bracket. It should be greased every 12 months or 6000 miles.SHOCK ABSORBER MAINTENANCEThe shock absorbers used on the MORryde “IS” rubber suspension are sealed, hydraulic type and require no periodic maintenance. Shock absorbers of this type should be checked every 10,000 miles to make sure they are functioning satisfactorily, bushings are not worn, and the dust cover has not been damaged by flying stones or debris from the road. If a shock absorber is leaking, fails to operate, or develops an unusual noise, the shock absorber should be replaced.SERVICENOTE: ALL SERVICE PROCEDURES MUST BE PERFORMED WITH THE VEHICLE SUPPORTED AT THE FRAME WITH APPROPRIATELY RATED SAFETY STANDS AND JACKS.PROCEDURES FOR JACKING UP UNITIt is permissible to jack up a unit equipped with a MORryde Independent Rubber Suspension System only on the Beam Assembly under the Rubber Springs or the frame of the trailer. The most efficient location to raise a trailer is at the frame. Jacks and safety stands should be positioned towards the front and rear portion of the trailer frame. To perform suspension work tires should be approximately 4” above the ground.INSPECTION/REPLACEMENT OF RUBBER SPRINGSMORryde rubber springs are made of a special formulation of natural rubber. The rubber springs are vulcanized (bonded) to steel plates. There are two unlikely problems that may occur with MORryde rubber springs:1. The first type is bond failure. This condition is apparent when the rubber separates from the metalplate.2. The second type is a rubber failure. This condition is apparent when the rubber tears ordelaminates and generally occurs in the middle of the rubber spring between the metal plates. Either of the conditions described above would not always necessitate replacement of the rubber spring. If there is a question about the integrity of a marginal rubber spring, a 3” wide object (such as a 3” putty knife) can be used to probe the rubber spring in the affected area. (If the probe penetrates the crack or separation .75” or more, the spring should be replaced). Rubber Springs should be inspected when supporting the trailer.REPLACEMENT OF A RUBBER SPRING ASSEMBLY1. Raise the unit until the tires are approximately 4” off the ground, the frame is supported with safety stands and the suspension is hanging unsupported.2. Remove both tires on the side of the unit the Rubber Springs are to be replaced.3. Loosen or cut loose brake wires to obtain slack.4. Remove 3/8” bolts securing Rubber Springs to Hanger Assembly and Beam Assembly.5. Pry rubber springs out from between the Beam Assembly and the Hanger Assembly.6. Align and bolt the rubber spring assembly to the Hanger Assembly. Drift pins can be used to align the bolt holes on the Beam Assembly with the Rubber Spring bolt holes (a bottle or floor jack may be needed to raise the Beam Assembly and the bolt holes of the Rubber Spring).7. Reinstall the shocks.8. Use heat-shrink connectors to reconnect brake wires. Use tie straps to secure brake wires out of harms way of Beam Assembly, Rubber Springs and Shock Absorbers.9. Reinstall tires, torque all bolts and remove jack standREPLACEMENT OF SHOCK ABSORBERThere are two (2) shock absorbers utilized on the MORryde Independent Rubber Suspension System, per axle. These shock absorbers are made by Monroe. They have special valving and stroke length specifically designed for the MORryde suspension. They are rarely available through Monroe after market dealers. Consult with MORryde directly for replacements. Refer to figure below.1. Fastener Nut2. Washer3. Rubber Bushing To replace a shock absorber:1. Remove fasteners.2. Remove shock absorber.3. Install new bushings on new shock absorber per exploded illustration above.4. Install new shock absorber.5. Torque fasteners per Torque Chart in Specification section.4. Clip welded to trailer frame5. Shock Absorber6. Clip welded to Beam AssemblyREPLACEMENT OF BEAM ASSEMBLYThe Beam Assembly attaches the wheel and rubber suspension to the Hanger Assembly, which is welded to the frame of the coach. Should a beam and or spindle become damaged and need to be replaced follow the steps below.1. Jack up the unit (see procedure for jacking up unit).2. Remove tires.3. Remove wheel drum and backing plate, which contains the brakes.4. Remove Rubber Shear Springs from the Beam Assembly.5. Remove shock at the lower end.6. Remove nuts and washer at the end of the journal bar (toward inside of frame).7. Pull out the Beam Assembly.8. Slide in new Beam Assembly. Bearings should be replaced if damaged or worn.9. Reinstall nuts in the journal bar, then the shock, spring, backing plate and wheel drum.10. Appropriately torque all nuts and bolts (see torque chart)11. Reinstall the tires and wheels.SUSPENSION ALIGNMENTThe MORryde independent suspension system allows for automotive style toe and camber wheel alignment. This allows you to manage your RV’s tire wear as effectively as you manage yourtow vehicle. There are four bolts per wheel, which allow for these adjustments. Always adjust the CAMBER first, followed by the TOE.ADJUSTING THE CAMBER1. Connect the alignment machine and level the unit on the alignment turntables.2. If camber is negative, add a shim to the outside of the Torque Bracket.3. If camber is positive, add a shim to the inside of the Torque Bracket.4. Shims are available in three sizes - 1/4”, 1/8”, and 1/16”.25”5. A 1⁄4” shim will change the camber approximately 1 degree.6. To decrease camber, loosen the four Torque Bracket bolts and remove the 3⁄4” bolts one at a timeto install shims.7. Unit will need to be raised to add camber.8. Appropriately torque all bolts.ADJUSTING THE TOE1. Connect the alignment machine and level the unit on the alignment turn tables.2. Loosen the four bolts holding the Torque Bracket to the Hanger Assembly.3. Move the Torque Bracket Assembly to obtain the correct toe readings on the alignment machine.4. Tighten the Torque Bracket bolts.5. Raising the coach is not required to adjust the toe.6. Toe adjustment can be accomplished with a “port-a-power” or large alignment bar.7. Appropriately torque all bolts.The following list covers the most frequent cause for concern, which may arise with the MORryde Independent Suspension System. If a problem occurs that is not addressed here, please contact MORryde International direct for further service information at 574- 293-1581.Problem / Symptom CorrectionCause• Excessive tire wear• Shock absorbers are worn • Tires not aligned• Worn torque bracket bearing• Worn shock absorbers• Improper tire pressure• Improper rubber springdeflection• Worn shock absorbers• Tires rubber on wheel wellor the suspension bottomingout• Improper tire pressure• Torn rubber shear spring• Improper hitch weight• Call MORryde for differentdensity of rubber spring• Replace shock absorber• If spring deflection is correctand height adjustment isnot sufficient, a spacertube needs to be weldedbetween the frame and the“IS” system.• Adjust air pressure• Replace rubber shear spring• Travel trailers should have10%-12% height weight. Fifthwheel trailers should have20%-25% height weight.• Have tires re-aligned• Have the bearings replaced• Replace shock absorber• Adjust air pressure• Rough ride• Excessive swayTROUBLE SHOOTINGTORQUE CHARTBolt Size Grade 8Grade 51/4-20 5/16-18 3/8-16 7/16-14 1/2-13 5/8-11 5/8-18 3/4-107142540601151251901020355590170185280Torque values must be verified with a torque wrench. A calibrated pneumatic impact wrench is not acceptable substitute.AXLE BRAKE INFORMATIONThe MORryde “IS” can utilize several different sizes of brakes. Systems that are factory installed may have different brake components than those systems that are installed after market. In an aftermarket installation, it is possible to upgrade braking systems to use a larger brake such as 12-1⁄/4” x 2-1⁄/2”or 12-1⁄/4” x 3-3/8” brakes or to disc brakes. If after market customers are not upgrading their braking system at the time of installation, the existing braking system on the trailer or fifth wheel will be used. For more brake information, consult your owner’s manual of your trailer or contact MORryde for a more detailed discussion on brake options.PLEASE DIRECT ALL CORRESPONDENCE TO:MORryde International1966 Sterling Ave.Elkhart, IN 46516Phone: (574) 293-1581Fax: (574) 294-4936Email:*******************。
DR635说明书
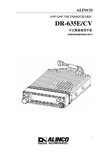
1DR-635E/CV中文简易使用手册更详细的说明请参考原英文说明书2安装和面板说明 (4)一:拆卸可分离的前面板.......................................................................................................4 二:扩展电源控制部分...........................................................................................................5 三:前面板使用说明简表.......................................................................................................5 四:背面接口..........................................................................................................................7 五:面板显示符号说明...........................................................................................................7 第二章:基本操作.. (8)一:打开/关闭设备.................................................................................................................8 二:切换主工作信道..............................................................................................................9 三:音量设置..........................................................................................................................9 四:静躁深度设置 (9)频率模式(VFO mode )...............................................................................................10 内存频道操作模式 (11)第三章:参数设置 (15)步进步长选择........................................................................................................................16 扫描类型................................................................................................................................16 按键响声................................................................................................................................16 超时控制................................................................................................................................16 超时处罚................................................................................................................................17 APO 电源管理.......................................................................................................................17 单音频脉冲频率....................................................................................................................18 蜂鸣音....................................................................................................................................18 繁忙信道锁定........................................................................................................................18 防盗功能................................................................................................................................19 发射状态屏幕颜色设置.........................................................................................................19 接收状态屏幕颜色设置.........................................................................................................20 待机状态屏幕颜色设置.........................................................................................................20 屏幕亮度调节........................................................................................................................20 呼叫ID 设置(数据通讯使用)..........................................................................................20 通讯速率选择(数据通讯使用).........................................................................................21 APRS 通信间隔时间设置......................................................................................................21 第四章:其他功能 (21)切换波段................................................................................................................................21 V-V/U-U 同时接收................................................................................................................22 单段模式................................................................................................................................22 扫描功能.. (22)Vfo sacn..........................................................................................................................22 Memory Scan..................................................................................................................23 跳跃频道设置.................................................................................................................23 编程扫描................................................................................................................................23 亚音扫描(CTCSS 连续音频编码静噪系统)...................................................................24 DCS 扫描(数字亚音)........................................................................................................24 锁定功能.. (25)3窄带模式................................................................................................................................25 AM (调幅)接收模式..........................................................................................................25 数字通讯................................................................................................................................26 防盗报警功能........................................................................................................................27 防盗操作................................................................................................................................28 数据包通讯............................................................................................................................30 APRS 自动位置报告系统......................................................................................................31 远程遥控(仅EMS-57手咪) (33)4安装和面板说明一:拆卸可分离的前面板1:将电台右侧的锁扣向前按下2:将面板向右推动3:小心拿下前面板,注意中间的连线5二:扩展电源控制部分三:前面板使用说明简表*主要功能(单按钮功能简表)序号 按钮名称 功能简述 1 PWR 按钮 打开或关闭电台电源 2 主波段音量旋钮 控制主波段的音量大小 3 副波段音量旋钮 控制副波段的音量大小4 主波段收发指示灯 指示主波段的工作情况,红色为正在发射,绿色为正在接收5 副波段接收指示灯 指示副波段的工作情况,绿色为正在接收6 V/.M/MW 内存信道模式/频率模式转换7 频率/频道旋钮 主要功能选择旋钮,可切换内存信道、工作频率及其他设置 8 波段按钮 选择主信道,可交换子信道和主信道 9 紧急呼叫 切换到紧急呼叫频率10 Mhz 按钮 在VFO 频率模式时,可按下,切换以M 为单位的频率步进 11 TSDCS/LOCK 设置TONE 和DCS 选项 12 HL/PACKET 切换高/中/低三档功率 13 SQL/DIAGTAL 设置静躁等级 14 FUNC/SET 进入功能菜单ALINCO615 MIC.CONNECTOR 车载电台话筒连接座 序号对应上图中的部件编号*组合按钮功能简表1(按下(F )功能键后再按其他功能键) 序号 按钮名称 功能6 V/M/MW 写入频率到内存信道8 BAND/VVUU 切换成VV 或者UU 显示工作模式(主副波段都必须在VFO 模式)9 CALL/RXBAND 在VFO 模式下,按F 再按CALL 键,可切换出隐藏频率 V 段可切换出77M (广播)12X (航空)U 段可切换出350M 10 MHZ/SHIFT 上下差频方向选择/差频范围选择 11 TSDCS/LOCK 锁定电台 12 HL/PACKET 进入复制/通讯模式 13 SQL/DIGITAL 进入数字语音通讯模式*组合功能简表2(需按下(F)功能键并同时按其他功能键) 序号 按钮名称 功能 1 PWR 恢复到出厂状态5 V/M/MW 清除所有记忆的存储信道 8 BAND/VVUU 切换单/双段模式 9 CALL/RXBAND 进入克隆模式 10 MHZ/SHIFT 切换宽频/窄频工作模式 11 TSDCS/LOCK 切换AM 调幅模式 12 HL/PACKET 设置信道字符命名功能 13 SQL/DIGITAL 进入电源显示模式*需要长按激活的功能 序号 按钮名称 功能13 SQL/DIGITAL 按下1秒后进入监听模式 14 FUNC/SET 按下2秒后进入设置菜单7四:背面接口序号 按钮名称 功能1 外部扬声器接口 可接入外接扬声器音箱(在CLONE 模式时插入复制电缆)2 电源接口 13.8V 输入3 温控风扇 当按下PTT 时风扇自动激活4 天线接口座 连接50欧馈线和外接天线5 9针RS232接口(选件) 连接计算机使用五:面板显示符号说明8序号 功能1 当按下FUNC 键时显示2 当激活调幅模式时显示3 中功率档指示 4 低功率档指示 5 窄带接收指示 6 差频指示 7 音频显示 8 数字亚音指示9 当副波段切换为主波段时指示 10 锁定指示 11 防盗功能指示 12 EJ-50U 附件插入指示13 当副波段为频道模式或CALL 模式时指示 14 差转功能指示 15 数字语音模式指示 16 寻呼模式指示17 副波段工作频率或命名字符显示 18 副波段收发信号强度表指示 19 当副波段接收到信号时指示 20 主波段工作频率或命名字符显示 21 主波段收发信号强度表指示 22 频率M 和HZ 间隔符号 23 当主波段收到信号时指示 24 静躁深度等级25 在内存信道模式时显示当前信道编号第二章:基本操作一:打开/关闭设备按下PWR 键可打开设备电源,再次按下可关闭设备电源9二:切换主工作信道按下BAND 键可切换VHF 或UHF 信道到主波段,在主波段显示的工作频率可以收发,在右侧副波段显示的频率仅可收听,主副波段可同时收听和显示。
黑鹰自动车辆维修工具指南说明书

Operating Instructions & Parts ManualSFA Companies10939 N. Pomona Ave. Kansas City, MO 64153******************************Magic Lift TMHydraulicService JacksModel Capacity BH6057 5 Ton TonSPECIFICATIONSSAFETY and GENERAL INFORMATIONSave these instructions. For your safety, read, understand, and follow the information provided with and on this jack before using. The owner and operator of this equipment shall have an understanding of this jack and safe operating procedures before attempting to use. The owner and operator shall be aware that use and repair of this product may require special skills and knowledge. Instructions and safety information shall be conveyed in the operator's native language before use of this jack is authorized. If any doubt exists as to the safe and proper use of this jack, remove from service immediately.Inspect before each use. Do not use if broken, bent, cracked or damaged parts are noted. Any jack that appears damaged in any way, or operates abnormally shall be removed from service immediately. If the jack has been or suspected to have been subjected to a shock load (a load dropped suddenly, unexpectedly upon it), immediately discontinue use until jack has been checked by a factory authorized service center (contact distributor or manufacturer for list of authorized service centers). It is recommended that an annual inspection be done by qualified personnel. Labels and Operator's Manuals are available from manufacturer.PRODUCT DESCRIPTIONThis Hydraulic Service Jack is designed to lift, but not support, one end of a vehicle. Immediately after lifting, loads must be supported by an identical pair of appropriately rated jack stands. This MagicLift™ service jack has a unique feature that provides fast, no load lifts to the jacking point, at which time it lifts in approximately 3/4" ~ 2" increments.WARNING : NEVER use hydraulic jack as stand-alone device. After lifting, immediately support the liftedvehicle with an identical pair of appropriately rated jack stands.Figure 1 - Model BH6057 & BH6107 ComponentsPREPARATIONAssemblyInsert handle into the handle sleeve. Tighten the bolt on handle sleeve to prevent accidental removal of handle while in use.Before Use1. Verify that the product and application are compatible, if in doubt call Blackhawk Technical Service (888) 332-6419.2. Before using this product, read the operator's manual completely and familiarize yourself thoroughly with theproduct, its components and recognize the hazards associated with its use.3. To familiarize yourself with basic operation, locate and turn the release valve (handle):a. Clockwise until firm resistance is felt to further turning. This is the ‘CLOSED’ release valve position used toraise the saddle.b. Counter-clockwise, but no more than 1/2 a turn from the closed position. This is the ‘OPEN’ release valveposition used to lower the saddle.4. With the saddle fully lowered and release valve closed, pump the operating handle. If lift arm responds immediately,jack is ready for use. If jack does not respond, open release valve and pump 6 ton 8 full strokes to purge air.Close release valve and recheck operation.5. Ensure that jack rolls freely. Raise and lower the unloaded saddle throughout the lifting range before putting intoservice to ensure the pump operates smoothly. Replace worn or damaged parts and assemblies with Blackhawk authorized replacement parts only.Bleeding / Venting Trapped AirReinstall the oil filler plug.OPERATIONNOTICE Only attachments and/or adapterson area of the vehicle as specified by the vehicle manufacturer.1. Follow the vehicle manufacturer’s recommended guidelines for lifting. Engage the emergency brake and chock each unlifted wheel in both directions to prevent inadvertent vehicle movement.2. Close the release valve by turning the handle clockwise until firm resistance is felt.3. Refer to the vehicle manufacturer owner’s manual to locate approved lifting points on the vehicle. Center jack saddle under lift point.4. Verify lift point, then pump handle to contact lift point. To lift, pump handle until load reaches desired height. Never use foot pedal to raise loads.5. Transfer the load immediately to appropriately rated jack stands.: NEVER use hydraulic jack as adevice! ALWAYS transfer the lifted load IMMEDIATELY to an identical pair of appropriately rated jack stands. Use one pair of jack stands per vehicle. Rated capacity is per pair only! Do not exceed rated capacity.NOTICE Be sure all tools and personnel are clear before owering load. Slowly open the release valve! The more you turn the handle counter-clockwise, the faster the load will come down. Maintain control of the rate of speed at which the load lowers at all times!1. Raise load high enough to clear the jack stands.2. Remove jack stands carefully. (always used in pairs).3. Slowly turn the handle counter-clockwise, but no more than 1/2 a turn. If the load fails to lower:a. Use another jack to raise the vehicle high enough to reinstall jack stands.b. Remove the malfunctioning jack and then the jack stands.c. Using the functioning jack to lower the vehicle. 4. After removing jack from under the vehicle, fully lower the saddle to reduce ram exposure to rust and contamination.MAINTENANCEImportant: Use ONLY premium grade hydraulic jack oil. Avoid mixing different types of fluid and Never use brake fluid, turbine oil, transmission fluid, m otor oil or glycerin. Improper fluid can cause failure of the jack and the potential for sudden and immediate loss of load. Adding oil1. With saddle fully lowered set jack in its upright, level position. Locate and remove oil filler screw.2. Fill with oil until ~3/16" above the inner cylinder as seen from the oil filler hole. Reinstall the oil filler screw. Changing oilFor best performance, replace the complete fluid supply at least once per year.1. With saddle fully lowered, remove oil filler plug.2. Lay the jack on its side and drain the fluid into a suitable container.Note: Dispose of hydraulic fluid in accordance with local regulations.3. Fill with oil until ~3/16" above the inner cylinder as seen from the oil filler hole. Reinstall oil filler screw.4. Perform bleeding/venting trapped air procedure.LubricationA periodic coating of light lubricating oil to pivot points, axles and hinges will help to prevent rust and assure that wheels, casters and pump assemblies move freely. CleaningPeriodically check the pump piston and ram for signs of rust or corrosion. Clean as needed and wipe with an oily cloth.Note: Never use sandpaper or abrasive material on these surfaces!StorageWhen not in use, store the jack with saddle fully lowered.REPLACEMENT PARTS(refer to page 5-9)Not all components of the jack are replacement items, but are illustrated as a convenient reference of location and position in the assembly sequence. When ordering parts, please give the Model number, part number and parts description. Call or write for current pricing: SFA Companies, 10939 N. Pomona Ave. Kansas City, MO 64153, U.S.A. Tel:(888)332-6419Fax:(816)891-6599E-Mail:******************************Replacement Parts Illustration for Model BH605712345678910111213141516181719202123222425 2627282929AC B DE FHI BC JKLU TS R QM N POB C FQReplacement Parts Illustration for Model BH6107123456789101112131415161817192021232224252627282929AC BDEF HI BC J KLU T SR QM N PO B C FQReplacement Parts List for Model BH6107ONE YEAR LIMITED WARRANTYFor a period of one (1) year from date of purchase, SFA Companies will repair or replace, at its option, without charge, any of its products which fails due to a defect in material or workmanship under normal usage. This limited warranty is a consumer’s exclusive remedy.Performance of any obligation under this warranty may be obtained by returning the warranted product, freight prepaid, to SFA Companies Warranty Service Department, 10939 N. Pomona Ave., Kansas city, MO 64153. Except where such limitations and exclusions are specifically prohibited by applicable law.(1) THE CONSUMER’S SOLE AND EXCLUSIVE REMEDY SHALL BE THE REPAIR OR REPLACEMENT OF DEFECTIVE PRODUCTS AS DESCRIBED ABOVE.(2) SFA COMPANIES SHALL NOT BE LIABLE FOR ANY CONSEQUENTIAL OR INCIDENTAL DAMAGE OR LOSS WHATSOEVER.(3) ANY IMPLIED WARRANTIES, INCLUDING WITHOUT LIMITATION THE IMPLIED WARRANTIES OF MERCHANTABILITY AND FITNESS FOR A PARTICULAR PURPOSE, SHALL BE LIMITED TO ONE YEAR, OTHERWISE THE REPAIR, REPLACEMENT OR REFUND AS PROVIDED UNDER THIS EXPRESS LIMITED WARRANTY IS THE EXCLUSIVE REMEDY OF THE CONSUMER, AND IS PROVIDED IN LIEU OF ALL OTHER WARRANTIES, EXPRESS OR IMPLIED.(4) ANY MODIFICATION, ALTERATION, ABUSE, UNAUTHORIZED SERVICE OR ORNAMENTAL DESIGN VOIDS THIS WARRANTY AND IS NOT COVERED BY THIS WARRANTY.Some states do not allow limitations on how long an implied warranty lasts, so the above limitation may not apply to you. Some states do not allow the exclusion or limitation of incidental or consequential damages, so the above limitation or exclusion may not apply to you. This warranty gives you specific legal rights, and you may also have other rights which vary from state to state.SFA Companies10939 N. Pomona Ave. Kansas City, MO 64153816-891-6390******************************。
林肯焊接和切割设备维修指南说明书

L T -7 TRACTOR TROUBLESHOOTINGIM279-TSJUNE 1995Safety Depends on YouLincoln arc welding and cutting equipment is designed and built with safety in mind. However, your overall safety can be increased by proper installation ... and thought-ful operation on your part.DO NOT INSTALL, OPERATE OR REPAIR THIS EQUIPMENT WITHOUT READING THIS MAN-UAL AND THE SAFETY PRE-CAUTIONS CONTAINED THROUGHOUT.And, most importantly, think before you act and be careful.Mar ‘95TABL E OF CONTENTSivivGENERAL DESCRIPTIONThe LT-7 tractor is a compact, lightweight, DC, single arc tractor.It is capable of operating with 3/32”through 3/16”electrode with a current carrying capacity of 1000 amps.The LT-7 has a travel range from 6 to 70 inches per minute.FIGURE E.1 - 115VAC INPUT POWER CIRCUITSINPUT POWER CIRCUITSThe LT7 is powered by 115VAC which is usually sup-plied from the welding power source.The 115VAC isapplied to the travel board.This voltage is also coupledto the control box circuitry through the on/off powerswitch and a 3 amp circuit breaker.The input power isthen applied to the the variable voltage board and,through resistor R1, to the control board.The 115VACis rectified and regulated by the control board whichsupplies 24VDC to the logic board.Upon receiving commands from the user operated switches or potentiomenters the logic board sends the appropriate signal to the control board which then dri-ves the wire feed motor to the correct speed and direc-tion.When the start signal is received by the control board the power source contact relay(1CR) is ener-gized as well as the travel relay(2CR) and the wire drive motor.When weld current closes reed switch 3CR the logic board directs the control board to change the wire feed speed from the preset inch speed to the welding feed speed set by the wire speed control potentiome-ter.Reed switch 4CR protects the internal grounding wire circuitry.In the event that abnormally high currentwas to flow in the grounding lead system the 4CR reed switch would close, signaling the logic board to stop the welding procedure.The inch up switch, which is cou-pled directly to the control board, dictates that the wire drive motor reverse direction and back the electrode wire away from the work piece.T ravel speed, direction and mode (either manual or auto) are determined by the settings of the three con-trols connected to the travel board.The travel board then applies the correct voltage and polarity to the trav-el motor to satisfy the control settings.CONTROL,LOGIC AND TRAVEL BOARDSFIGURE E.2 - CONTROL LOGIC AND TRAVEL BOARDSArc voltage is monitored by the voltmeter and variable voltage board.When the LT7 tractor is being operated in the constant current mode the variable voltage board is essential in the control of the wire feed speed. As the arc length changes the arc voltage will also change.The variable voltage board recognizes this change and signals the logic board to either increase or decrease the wire feed speed.This function is neces-sary to maintain a constant electrode arc length and a stable and high quality weld.The variable voltage board also generates a low volt-age which is applied to the electrode during the inch down mode.When the electrode makes contact with the work piece this low voltage is “loaded down”thus signaling the control circuitry to stop the wire feed motor.This feature allows the operator to utilize “work touch sensing”.FIGURE E.3 - VARIABLE VOLT AGE BOARD VARIABLE VOL TAGE BOARDA-4NOTES A-4If for any reason you do not understand the test procedures or are unable to perform the tests/repairs safely, contact the Lincoln Electric Service Department for technical troubleshooting assistance before you proceed.Call 216-383-2531 or 1-800-833-9353.Service and Repair should only be performed by L incoln Electric Factory Trained Personnel.Unauthorized repairs performed on this equipment may result in danger to the technician and machine operator and will invalidate your factory warranty.For your safety and to avoid Electrical Shock,please observe all safety notes and precautions detailed throughout this manual.This Troubleshooting Guide is provided to help you locate and repair possible machine malfunctions.Simply follow the three step procedure below.Step 1.LOCATE PROBLEM (SYMPTOM).Look under the column labeled “PROBLEM (SYMPTOMS)”.This column describes possible symptoms that the machinery may exhibit.Find the listing that best describes the symptom that the machine is exhibiting.Symptoms are grouped according to:function problems and travel problems.Step 2.PERFORM EXTERNAL TESTS.The second column labeled “FIELD COURSE OF ACTION”lists the basic possibilities that may contribute to the machine symptom.Perform these tests/checks in the order listed.Step 3.PERFORM COMPONENT TESTS.The last column labeled “RECOMMENDED SHOP COURSE OF ACTION”lists the most likely components that may have failed in your machine.It also specifies the appropriate test procedure to verify that the subject component is either bad or good.If there are a number of possible components,check the components in the order listed to eliminate one possibility at a time until you locate the cause of your problem.All the necessary test specifications and repair procedures are described in detailfollowing the troubleshooting guide.All electrical test points, terminal strips,junctions, etc., can be found on the electrical wiring diagrams and schematicsin the Electrical Diagram Section.How To Use Troubleshooting GuideT able B.1 P.C.Board Status LightsON* INDICA TES LIGHT IS DIMT able B.2 P.C.Board Status Light DefinitionsB-22TROUBL ESHOOTING AND REPAIR B-22 ArrayFIGURE B.1 Logic P.C.Board LED LocationsFIGURE B.3 Control P.C.Board LED LocationsB-23NOTES B-231.Remove the wire feed motor connector from the LT7 control box.ing the ohmmeter measure the motor resistances per Table B.3.Also see Figure B.43.If the motor resistance test is good pro-ceed to the Motor Applied Voltage T est.MOTOR APPLIED VOLTAGE TEST 1.Carefully connect the 110VDC supply (SUPPL Y TURNED OFF) to pins C and D on the motor connector.2.Carefully connect the variable 0 to 90VDC supply (SUPPL Y TURNED OFF) to pins A and B on the motor connector.(See T able B.3)3.Apply field voltage first(pins C and D) to the motor.Then slowly apply the arma-ture voltage on pins A and B.(See T able B.3)4.The motor should run and the speed should vary with changes to the armature voltage.5.If the motor does NOT run and change speed correctly the motor or gear box may be faulty.6.To stop motor REMOVE ARMATURE VOLT AGE FIRST .(Pins A and B)T ABLE B.3TEST PROCEDUREWIRE DRIVE MOTOR TEST (continued)FIGURE B.4 - Wire Drive Motor Connector PinsTEST PROCEDURE1.Remove the travel motor connector fromthe LT7 control box.ing the ohmmeter measure the motorresistances per Table B.4.Also see Figures B.5.and B.6*3.If the motor resistance test is good pro-ceed to the Motor Applied Voltage T est. MOTOR APPLIED VOLTAGE TEST1.*Carefully connect the 110VDC supply(SUPPL Y TURNED OFF) to pins C and D on the travel motor connector.See FigureB.62.Carefully connect the variable 0 to 90VDCsupply (SUPPL Y TURNED OFF) to pins A and B on the travel motor connector.3.*Apply field voltage first (pins C and D) tothe motor.See Figure B.6 and T able B.44.Slowly apply the armature voltage on pinsA and B.(See T able B.4)5.The motor should run and the speedshould vary with changes to the armature voltage.6.If the travel motor does NOT run andchange speed correctly the motor or gear box may be faulty.7.*To stop motor REMOVE ARMATUREVOLT AGE FIRST.(Pins A and B)*DENOTES OLDER UNITS WITH FIELD WINDING*DENOTES OLDER UNITS WITH FIELD WINDINGFIGURE B.5 T ravel Motor Connector PinsFIGURE B.6 T ravel Motor Connector Pins (OlderUnits with Powered Field.)B-29NOTES B-29MOTOR REMOVAL PROCEDURE:1.Remove the wire drive motor cable fromthe LT7 control box.ing the 1/2”wrench remove the boltholding the flux hopper(if used) to the bumper handle assembly.e the large slot head screwdriver toremove the two slot head screws holding the bumper handle assembly to the gear box housing.e the 5/32”Allen type wrench to removethe socket head cap screw from the gear box housing and motor end bracket.5.Locate and remove the four small slothead screws holding the inspection cover plate to the gear box housing.Note place-ment of rubber gasket and cable strain clamp.6.Locate and remove the two socket headcap screws mounting the motor to the gear box housing.Note:The inspection cover plate has to be remove (Step #5) to gain access to the two socket head cap screws.7.Carefully remove the motor(with piniongear) from the gear box assembly.MOTOR REPLACEMENT PROCEDURE: 1.Carefully install the replacement motor(with pinion gear) and mount to the gear box housing using the two socket head caps screws.ing the four small slot head screwsinstall the inspection cover plate along with the rubber gasket and cable clamp.3.Install the bumper handle assembly withthe socket head cap screw and the two larger slot head screws.4.Install the flux hopper (if used) to thebumper handle assembly and secure with the hex head bolt.5.Attach the wire drive motor cable to theLT7 control box receptacle.WIRE DRIVE MOTOR REMOVAL PROCEDURE (continued)CONNECTION SCHEMATIC - M15342T h i s d i a g r a m i s p r o v i d e d f o r r e f e r e n c e o n l y .I t m a y n o t b e t o t a l l y a p p l i c a b l e t o a l l m a c h i n e c o d e s .CONTROL BOX WIRING DIAGRAM- L7460It may not be totally applicable to all machine codes.C-3NOTES C-3World's Leader in Welding and Cutting Products Premier Manufacturer of Industrial Motors。
Lincoln Global NA-5 自动焊接器说明书
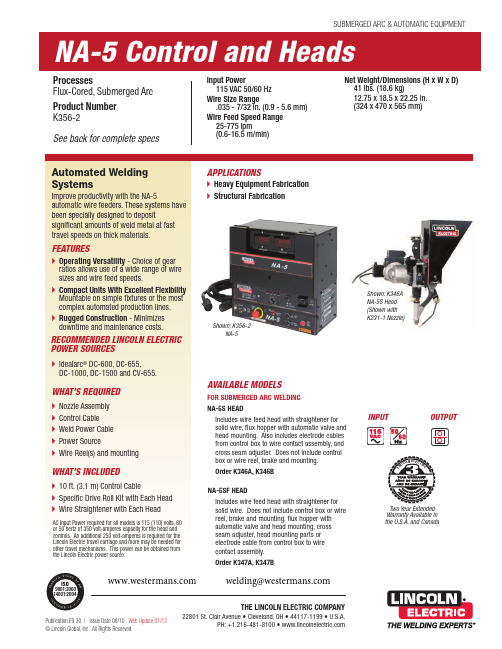
Publication E9.30 | Issue D a te 08/10 Web Update 01/12© Lincoln Global, Inc. All Rights Reserved.SUBMERGED ARC & AUTOMATIC EQUIPMENTProcessesFlux-Cored, Submerged Arc Product Number K356-2See back for complete specs Input Power115 VAC 50/60 Hz Wire Size Range.035 - 7/32 in. (0.9 - 5.6 mm)Wire Feed Speed Range 25-775 ipm(0.6-16.5 m/min)Net Weight/Dimensions (H x W x D)41 lbs. (18.6 kg)12.75 x 18.5 x 22.25 in.(324 x 470 x 565 mm)PH: +1.216-481-8100 • Shown: K356-2NA-5[ 2]|NA-51.Control Power Switch –Turns wire feeder input power on and off. Also serves as an emergency stop switch.2.Pilot Light –Shows when the electrode is "hot".3.Inch Pushbuttons –Feed electrode up and down when not welding.4.Start and Stop Pushbuttons –Control welding cycles.5.Meter Value Pushbutton –Monitor either the preset values or the actual values.6.Timer Control –For burnback and/or wire react time.7.Crater Module (optional) –Controls procedure for anadjustable period of time to regulate bead size or fill craters at the end of the weld.8.Weld Timer (optional) –Eliminates the need to press stop pushbutton.9.Lockable Cover –Lockout procedure controls when necessary.10.Digital Display –Monitor wire feed speed and voltage on separate meters.11.Start Module (optional) –Controls penetration, bead size, or other factors for an adjustable time at the start of the weld.12.WFS and Voltage Preset Controls –Preset wire feed speed and voltage prior to and during welding. These controlseliminate returning to the power source for routine procedure changes.13.Travel Switch –Controls the travel mechanism for automatic starting and stopping when welding, travel without welding during setup and travel off.12345678910111213K299 Reel and Mounting – Order separately.NA-5 Control K356-2DC Power Source –Constant Voltage type with on-off control of power source output.4 ft. (1.2 m) Motor Cord –Included with K346.4 ft. (1.2 m) Electrode CablesContact Nozzle (optional)K335-26 Extension – Motor, flux hopper and electrode cables. Optional when more than 4 ft. (1.2 m) is required.Work Cable – Two or more 4/0NA-5S and NA-5SFFor Submerged Arc WeldingTwo 4/0 electrode cables and the multi-conductor control cable.Flux Hopper –Included with K346.Solid Wire Straightener Head4 ft. (1.2 m) Flux Hopper Cord –Included with K346.REQUIRED EQUIPMENTSolenoid AssemblyValve to automatically control water flow when using cooling attachment on K148 contact assemblies. Can also be used to control gas. Order K223Starting or Crater Module Permits additional settings of wire feed speed and voltage for an adjustable period of time (10 seconds max). Can be used for either a starting procedure or a crater fill procedure. If both are required, two assemblies must be ordered.Order K334Remote Interface ModulePermits remote operation of theNA-5 Inch Up, Inch Down, Start andStop Functions by either of thefollowing user-supplied externalsignals and provides electricalisolation of the NA-5 control circuitryfrom these signals:-SwitchesMomentary closure of contactsrated for 24 volts,5 milliamperes, DC.-24 Volt SignalsMomentary application of 24volt ±10% AC or DC signalcapable of 5 milliamperessteady state. (.15 amp peakcapacitive in rush) per input.This module can be used withall codes of NA-5 Controls andreplaces the earlier K336Remote Pushbutton InterfaceModule, which provided for onlyexternal switch closure signals.Order K336Weld Timer ModulePermits setting of weld time for anadjustable period of time. Eliminatesneed to press stop pushbutton. Thetimer unit is adjustable from 0.00 -9.99 seconds.Order K337-10Control To Head ExtensionCable AssemblyThe standard head is equipped withcables which permit the head to bemounted up to four feet from thecontrols. "F" models, however, donot include electrode cables. Whenthe head is mounted further awayfrom the control, extension cableassemblies must be purchased. Forthe NA-5S head: Includes motor,tachometer, and flux valve leadextensions with polarized plugs andelectrode. 26 ft. length.Order K335-26Recommended for the NA-5N, andSF heads. It is the same as the K335without the flux valve lead extension.Available in 46 ft. lengths.Order K338-46Mounting KitFor use if the NA-5 control box is tobe mounted on the carriage.Order T14469SINGLE ELECTRODESubmerged Arc Contact NozzleAssembly for 3/32 in. (2.4 mm),1/8 in. (3.2 mm) and 5/32 in.(4.0 mm) electrodes.For 5/64 in. (2.0 mm), 3/16 in.(4.8 mm) or 7/32 in. (5.6 mm) sizes,order additional appropriate KP1962tips. Outer flux cone gives full fluxcoverage with minimumconsumption.(Rated up to 650 amps.)Order K231-1K231 nozzle tipsDesigned for long life.OrderKP1962-1B1for 1/8 in. (3.2mm) wireKP1962-2B1for 3/16 in. (4.8 mm) wireKP1962-3B1for 3/32 in. (2.4 mm) wireKP1962-4B1for 5/32 in. (4.0 mm) wireKP1962-5B1for 7/32 in. (5.6 mm) wireKP2082-2B1for 5/64 in. (2.0 mm) wireNarrow Gap Deep Grove NozzleFor single arc 3/32 in. (2.4 mm)diameter wire welding on thickwalled steel plate with nearlyparallel-sided, narrow gap jointpreparations.Order K386Contact Jaw AssemblySingle arc contact jawassembly for 1/8-7/32 in.(3.2-5.6 mm) diameter wire. Ruggedcontact jaws for maximum life atcurrents over 600 amps.Order K226RTWINARC®Tiny Twinarc®Wire StraightenerStraightens wire diameters .045 thru3/32 in. (1.2 thru 2.4 mm).Particularly valuable on longerelectrical stickout procedures.Order K281Tiny Twinarc®Feeds two 1/16, 5/64, or 3/32 in.(1.6, 2.0, or 2.4 mm) electrodes forhigh speed submerged arc welds onthin gauge (1.89 mm) to heavy plate.Includes contact nozzle, wire guides,drive rolls and guides, and a secondwire reel and mounting bracket.Order K129-1/16K129-5/64K129-3/32Large Wire Twinarc®Contact AssembliesFeeds two 5/64 in. (2.0 mm),3/32 in. (2.4 mm) or 1/8 in. (3.2 mm)wires for submerged arc weldingon "Fast-Fill" joints or hardfacingbeads.Order K225GENERAL OPTIONSConcentric FluxCone AssemblyFor use with K148B, Positive ContactNozzle Assembly. Gives concentricflux coverage around the electrode.Order K285Positive Contact AssemblyFor single arc welding at highcurrents (optional T12928 watercooling attachment recommendedwhen welding over 600 amps).Order K148A(for 3/32 to 1/8 in. wire)Order K148B(for 5/32 to 3/16 in. wire)ESO (Extended Stick-Out)ExtensionLinc-Fill long stickoutextension for K148A Single ArcPositive Contact Nozzle Assembly.Required for long stickout technique.Order K149-5/325 in. Nozzle ExtensionExtends the wire for subarc nozzlesby 5 inches [up to 1/4 in. (6.4 mm)diameter wire].Order KP2721-1Horizontal Head AdjusterProvides crank adjustment of headposition. Has 2 in. (51 mm)horizontal travel.Order K96Vertical Lift AdjusterProvides 4 in. (102 mm) hand crankadjustment of vertical head position.It also includes up to 3-3/4 in.(95.2 mm) in-and-out horizontaladjustment with stops that can bepreset for simple repetition of thesame adjustment.Order K29SpreadArc OscillatorOscillates head across the line oftravel. Calibrated dwell time andoscillation speed controls permit theSpreadArc to cover large areasquickly with smooth beads ofminimum admixture.Order K278-1TC-3 Self-PropelledTravel CarriageThe TC-3 travel carriage allows themounting of up to two feed heads/controllers and wire reels to a beamfor basic hard automationinstallations.Order K325 HCS(for 5-75 ipm)NA-5| [ 3]Automatic Flux Hopper Assembly Flux Hopper for MAXsa ™29 Heads (included standard on the MAXsa ™22 Heads). Order K219Wire Reel Assembly for 50-60 lb. CoilsAccommodates 50 lb. (22.7 kg) or 60 lb. (27.2 kg) coils of wire on automatic wire feeders. The unit includes a wire reel mountingspindle and braking system. Cannot be used with K2462-1.Order K299Tandem ReelsTwo Wire Reel Mounting for TC-3. Order K390Tandem Arc FrameworkProvides mountings with desired positioning adjustments for two standard Automatic Wire Feed Heads. Includes insulation and hardware to permit direct mounting to a high capacity TC-3 Carriage, or to the user's gantry or fixture for either direction of travel.Order K387Flux HopperTandem Arc Flux Hopper for K387 mountings. Order K389Wire Straightener (Subarc) up to 7/32 in. (5.6 mm)Includes a three roll wire straightener with adjustable pressure. (1 included with each tractor and MAXsa ™Feed Head.) Order K1733-5(1)For the K347 Head, order the K338 extension.(2)For gear ratios shown.C U S T O M E R A S S I S T A N C E P O L I C YThe business of The Lincoln Electric Company is manufacturing and selling high quality welding equipment, consumables, and cutting equipment. Our challenge is to meet the needs of our customers and to exceed their expectations. Onoccasion, purchasers may ask Lincoln Electric for information or advice about their use of our products. Our employees respond to inquiries to the best of their ability based on information provided to them by the customers and the knowledge they may have concerning the application. Our employees, however, are not in a position to verify the information provided or to evaluate the engineering requirements for the particular weldment. Accordingly, Lincoln Electric does not warrant or guarantee or assume any liability with respect to such information or advice. Moreover, the provision of such information or advice does not create, expand, or alter any warranty on our products. Any express or implied warranty that might arise from the information or advice, including any implied warranty of merchantability or any warranty of fitness for any customers’ particular purpose is specifically disclaimed.Lincoln Electric is a responsive manufacturer, but the selection and use of specific products sold by Lincoln Electric is solely within the control of, and remains the sole responsibility of the customer. Many variables beyond the control of Lincoln Electric affect the results obtained in applying these types of fabrication methods and service requirements.Subject to Change – This information is accurate to the best of our knowledge at the time of printing. Please refer to for any updated information.For best welding results with Lincoln Electric equipment, always use Lincoln Electric consumables. Visit for more details.。
Altronic AGV5 气体计量阀门维修手册说明书
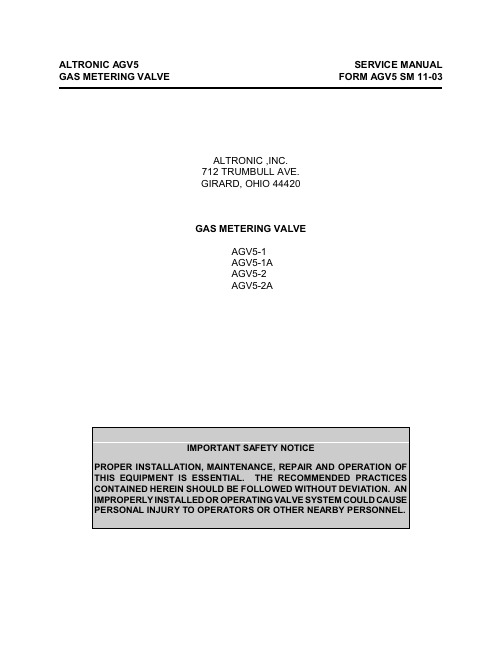
ALTRONIC AGV5SERVICE MANUAL GAS METERING VALVE FORM AGV5 SM 11-03ALTRONIC ,INC.712 TRUMBULL AVE.GIRARD, OHIO 44420GAS METERING VALVEAGV5-1AGV5-1AAGV5-2AGV5-2ATABLE OF CONTENTS ALTRONIC AGV5 SERVICE MANUALSECTION ITEM PAGE1.0VALVE SERVICE AND REPAIR MANUAL OVERVIEW32.0PARTS IDENTIFICATION53.0REPLACEMENT OR UPDATE OF PCB ASSEMBLY134.0REPLACEMENT OF THE PRESSURE TRANSDUCER175.0PRESSURE TESTING OF AGV5 VALVE181.0 AGV5 SERVICE AND REPAIR MANUAL OVERVIEWThe AGV5 Gas Metering Valve has been designed to provide reliable operation with a minimum amount of maintenance.To ensure optimum performance, periodic inspection and cleaning is necessary.Preventative maintenance issues can be integrated into the current maintenance schedule of the engine. Most maintenance requires little effort and no downtime of the AGV5 valve.Corrective maintenance is to be done when the AGV5 Gas Metering Valve begins to behave erratically. Procedures have been generated to troubleshoot and to repair most minor issues.•External Visual Inspection – Inspect the exterior of the valve for loose connections, frayed wires or major structural damage.•Cleaning –Exterior cleaning will aid in the visual inspection of the external casing and ensure good connections. Ethyl alcohol or mild soapy water can be used as cleaning agents.•Maintenance Log – To facilitate troubleshooting and to establish service schedules, a maintenance log should be kept on the valve.•Calibration – Calibration of the AGV5 is performed in a controlled environment before shipment. Since calibration of the valve requires equipment not normally available in the field, it is recommended that the device be returned to the Altronic distributor serving your area. Throughout this service manual service parts will be identified by the item number assigned to them in the parts list. For example, (1a) and its position inside the AGV5 device can be found by locating that item number on Fig.1A.AGV UPDATES•In addition to the standard procedures, older AGV5 units below S/N 1400 will require more items (such as the pressure transducer and transducer housing)to be changed. These items and procedures are identified by specific notes(“When Updating Units below S/N 1400") within the appropriate sections of the manual.•In addition to the repair of malfunctioning units, instructions are given in SECTION 3.0 which describe the process of updating an AGV5 to the current configuration of PCB assembly.2.0 PARTS IDENTIFICATION2.1PARTS LIST - AGV5Reference exploded view on 1A.ITEM NO.QUANTITY PART NO.DESCRIPTION 11881002-KT PC B Field Retrofit Kit1a1872005PC B Assem bly, Logic1b1810114Bushing, Magnet1c1810112Assembly, Magnet Holder 1d4801008W asher, Flat #41e4801009W asher, Lock #41f4801010Screw, 4-4011150301008Actuator Assembly12150303018Control Housing Assembly 206801058Bolt, 1/4-28 x 2"2.2PARTS LIST - AGV5Reference exploded view on 1B.ITEM NO.QUANTITY PART NO.DESCRIPTION 11881002-KT PC B Field Retrofit Kit1a1872005PC B Assem bly, Logic1b1810114Bushing, Magnet1c1810112Assembly, Magnet holder1d4801008W asher, Flat #41e4801009W asher, Lock #41f4801010Screw, 4-4021820020Valve Repair Kit2a1810033O-ring2b1810038O-ring2c1810035O-ring2d2810023O-ring2e1810024O-ring2f1810036O-ring2g1810037O-ring2h1810027O-ring2i1810025O-ring2j1810031O-ring2k1803020O-ring Lube33801018Screw, 10-324150303076Valve Seat, Primary5150303086Valve Seat, Secondary6350303066Spacer7150303056Poppet, Metering81801015Spring93801011Screw, 6-3210150303046Perch, Spring11150301008Assembly, Actuator12150303018Assembly, Control Housing136801014Bolt, 1/4-2814150303026Guide,Anti-rotation151********Piston, Balance16150301106Cap, Balance Piston171801002W asher181********Nut191820022Pressure Transducer Housing Kit 266 801006Screw, 8-32 x 1"2.3PARTS LIST - AGV5Reference exploded view on 1C.ITEM NO.QUANTITY PART NO.DESCRIPTION 11881002-KT PC B Field Retrofit Kit1a1872005PC B Assem bly, Logic1b1810114Bushing, Magnet1c1810112Assembly, Magnet Holder 1d4801008W asher, Flat #41e4801009W asher, Lock #41f4801010Screw, 4-4021820020Valve Repair Kit2a1810033O-ring2b1810038O-ring2c1810035O-ring2d2810023O-ring2e1810024O-ring2f1810036O-ring2g1810037O-ring2h1810027O-ring2i1810025O-ring2j1810031O-ring2k1803020O-ring Lube201 801002W asher, Flat 21150301106Cap, Balance Piston221810024O-ring23150301096Piston, Balance241810026Plug, Hex25150301166Nut, Balance Piston2.4PARTS LIST - AGV5Reference exploded view on FIG. 1D.ITEM NO.QUANTITY PART NO.DESCRIPTION 11881002-KT PC B Field Retrofit Kit1a1872005PC B Assem bly, Logic1b1810114Bushing, Magnet1c1810112Assembly, Magnet Holder1d4801008W asher, Flat #41e4801009W asher, Lock #41f4801010Screw, 4-4021820020Valve Repair Kit2a1810033O-ring2b1810038O-ring2c1810035O-ring2d2810023O-ring2e1810024O-ring2f1810036O-ring2g1810037O-ring2h1810027O-ring2i1810025O-ring2j1810031O-ring2k1803020O-ring Lube266801006Screw, 8-32 x 1"271820021AG V5 Transducer Kit27a1810116Assembly, Pressure Transducer 27b1801005Snap Ring27c1810031O-ring27d1803020O-ring Lube284801007Stand-off, 4-4029150302026Housing, Transducer3.0 REPLACEMENT OF PRINTED CIRCUIT BOARD ASSEMBLY USING 881002- KT3.1Retrofit installation of a new PCB assembly (1a) can only be done by a qualified repair facility.The valve must be removed from service and re-calibrated and retested prior to use.N OTE: When updating existing AGV5 units with S/N 1400 or lower, the obsolete pressure transducer and transducer housing (19) MUST be replaced in addition to the PCB assembly (1a). The obsolete pressure transducer is identified by the presence of four wires rather than three. The obsolete transducer has a white wire in addition to the normal black, red and green wires currently used. The new pressure transducer and housing assembly with all required hardware is available completely assembled under kit part number 820022.3.2Retain all removed parts in a small plastic bag. These parts should be returned to Altronic,Inc. for exchange credit.3.3The following tools are required for the removal and installation of PCB assembly (1a): aspanner or strap wrench, a small Phillips head screw driver, wire cutter/strippers and an Allen wrench set.3.4Removing and replacing the older style PCB assembly.A.Disconnect the power from the AGV5 system at the source. After power is off,disconnect all field wiring at junction box.B.Remove the cover from the AGV5 housing by unscrewing it. See FI G.1A. Use aspanner wrench or leather strap wrench to grip the cover.C.Remove the old PCB assembly (1a) by removing the four Phillips head screws (1f) whichsecure it to the pressure transducer housing base (19). With the PCB assembly (1a)loose, locate the three wires (black, red and green) coming from pressure transducer(27a) to the underside of the PCB assembly (1a). Cut the wires from the old style PCBassembly as closely as possible to the PCB. Locate the two wires coming from theactuator coil (green and white)and unplug the two pin connector coming from theunderside of the old PCB assembly. These five wires will be reused with the new PCBassembly (1a).D.Locate the wires coming from the existing LVDT assembly to the old style PCB assemblyand cut them off. Locate all of the tie wraps holding the old wiring harness to thehousing and remove them. Now remove the wiring harness and the old PCB assemblyby pulling the old wiring back through the conduit going to the junction box. These wireswill not be used with the new PCB assembly (1a).E.Remove the pressure transducer housing assembly (19) by removing the six Allen headmounting screws (26) holding it to the control housing assembly (12).The pressuretransducer housing (19) and the old LVDT coil can now be removed from the device.Use an Allen wrench to loosen the set screw in the clamping end of the pressuretransducer housing holding the LVDT coil and remove the LVDT coil. The LVDT coil willnot be reused. Replace the LVDT coil in the pressure transducer housing with themagnet guide (1b).See FI G. 1D. Tighten the Allen screw to hold the magnet guide (1b)in the housing (29) securely.F.Remove the LVDT core from the shaft attaching it to the poppet assembly by carefullyunscrewing the core from the 4-40 threaded stud (Allen head set screw)which holds it.See FIG.1C. The new magnet holder assembly (1c) is installed by threading onto the4-40 threaded stud.NOTE: When updating existing AGV5 units with S/N 1400 or lower,the obsoletepressure transducer and transducer housing assembly (19) MUST be replaced inaddition to the PCB assembly (1a).The obsolete pressure transducer is identifiedby the presence of four wires rather than three. The obsolete transducer has awhite wire in addition to the normal black, red and green wires currently used.The new pressure transducer and housing assembly with all required hardwareis available completely assembled under kit part number 820022. A specialmagnet holder assembly (1c) is supplied with this kit which will thread onto the10-32 stud used on these older valves.G.Replace the pressure transducer housing assembly (19) by sliding it over the newmagnet holder assembly (1c) and replacing the six Allen head mounting screws (26)holding it to the control housing assembly (12). Use the O-ring lubricant (2k) to helphold the O-rings (2c) and (2f) in place under the pressure transducer housing assembly(19). Tighten the six Allen screws (26) to 18-20 inch-pounds in order to hold thetransducer housing assembly (19) to the control housing assembly (12) securely. Seesection 5.0 for leak testing directions. Leak test the valve before proceeding to H.H.Place the new PCB assembly (1a) onto the 4-40 stand-offs (28) on the top of thepressure transducer housing assembly (19) oriented as shown in FI G. 1A and 1B.Secure the PCB assembly (1a) to the unit with the four Phillips head screws (1f), flatwashers (1d) and lock washers (1e) as shown. Before tightening the screws (1f), centerthe top of the magnet in the hole in the PCB as shown in FIG. 1A.I.Reconnect the wiring from the pressure transducer (27a) to the three position terminalstrip as shown in FI G. 1A.Cut off the plastic connector on the actuator leads andreconnect the actuator wires to the two-position terminal strip as shown in FIG. 1A.Dress the wires appropriately, taking care to not stress any connections or wires.3.5Calibrating the position sensor.A.The following items are required to calibrate the position sensor when a new PCBassembly is installed: a 24-volt power supply capable of supplying 5 amperes, a GOVDisplay Module P/N 891002-1 and a 4-20 milliampere simulator. See FIG.2 for theAGV5 test stand wiring diagram. Wire the components together as shown.B.Power up the AGV5 and the Display Module will go to the HOME screen of the AGV5program within 1 minute. The HOME screen is shown below. The first line of the display indicates the status of the valve; with the input control current set to 4 milliamperes or less, the valve is OFF or closed. The second line of the display indicates the position sensor (Hall Effect) output voltage at this position of the valve, 1.850 volts in this case.Read and record the actual voltage of the sensor. This value is the MIN POS value. The last characters XX.XX of the second line of the display show the position of the valve in terms of % open. The % open reading of the valve will not be correct until the valve is calibrated; disregard the XX.XX value shown at this time.C.Increase the current from the simulator to 20 milliamperes and observe the display; the proper display is shown below.NOTE: On valves below S/N 2001, if the magnet does not move and the position sensor voltage on the display does not change, reverse the green and white wires connecting to the actuator coil and retry. The top line of the display indicates that the valve is operating in the position control mode and the desired set point from the simulator is for a 100% open condition. The XXX.XX value is the valve position based on the position sensor signal; this value is incorrect until after the valve is calibrated. Read and record the value shown on the second line for the position sensor voltage in the place of the 3.750 value in the example.This value is the MAX POS value. At this time reduce the input current signal from the simulator to 4milliamperes or less before proceeding.D.I n order to program the position sensor calibration values into the AGV5 unit, the configuration password must be entered in sequence. When in the configuration mode all of the internal configuration values of the AGV5 are displayed. These values are never adjusted in normal use and should be accessed only by qualified personnel. The first configuration screen is shown below. After it appears, press the SETUP key until the HARDWARE CONFIG screen shown in section 3.5D appears, no other screen values will require adjustment from the factory default values.F1to enter configure mode pressF2then pressSETUPthen pressSETUPpress to move to the next groupE.Press the setup key until the display shown below appears. The sensor voltage value for the minimum open position can now be entered. Recall the value read and recorded in section 3.5, step B. This value plus 50 millivolts should be used for the MINPOS value. The +50 millivolt offset voltage allows for a 0.00% output reading from the valve to any user equipment when it is off, in spite of any thermal growth of the valve parts which mayoccur during normal use.+press to increase value-press to decrease valueThe right arrow always points to the adjustable value on the CONFIGURATION screen. Adjustments to CON FIG values are saved instantly and retained until changed again.F.Use the UP arrow key to select the screen for the entry of the sensor voltage representing the maximum open position of the valve or 100% open. Recall the value read and recorded in section 3.5 step C. This value minus 50 millivolts should be used for the MAXPOS value. The -50 millivolt offset voltage ensures that the valve will be able to reach its wide open position regardless of minor system variations.Epress to display nextvalue+press to increase value-press to decrease valueNORMpress to exit setup mode3.6After returning from the position sensor calibration screen, follow these instructions for testingthe calibration of the AGV5.A.The input simulator should still be set to 4 milliamperes or less and the HOME screen display should appear as shown below. The position sensor voltage should be about the same as read in section 3.5 step B, and the valve position shown in % open should now read close to the fully closed position of 0.00%.A reading of 0.00 +/- 0.50% would be inthe normal range.B.Adjust the input simulator to the values of current shown below and observe the display.The values shown for % open at each current input should now be calibrated to thoseshown in the table within a range of +/- 0.50 %.8 milliamperes25%12 milliamperes50%16 milliamperes75%20 milliamperes 100%C.Measure the 24 volt power supply current to the AGV5 valve with the valve100% open.The current from the power supply should be 2.25 amperes or less.4.0 REPLACEMENT OF THE PRESSURE TRANSDUCERS4.1Replacement of pressure transducer (27a) can be performed in the field under the directionof the distributor or Altronic personnel. The transducer (27a) is supplied in a kit (27) which includes all of the necessary parts.NOTE: When repairing or updating existing AGV5 units with S/N 1400 or lower, the obsolete pressure transducer and transducer housing as well as the PCB assembly MUST be replaced. The obsolete pressure transducer is identified by the presence of four wires rather than three. The obsolete transducer hasa white wire in addition to the normal black, red and green wires currently used. Thenew pressure transducer and housing assembly with all of the required hardware is available and comes completely assembled under kit part number 820022 (FIG.1B, 19).A.Remove the cover from the AGV5 housing by unscrewing it. See fig. 1A. Use a spannerwrench or leather strap wrench to grip the cover.B.Examine and make notes of the AGV electronic board assembly (1a) which show the wirerouting and orientations.C.Disconnect the transducer (27a) from the electronics board (1a) and remove the board(1a) from the transducer housing assembly (19).Do not remove more wires thannecessary.ing snap ring pliers,remove the snap ring (27b) holding the transducer (27a).E.With a small pry tool, remove the transducer (27a) from its housing.F.There is an O-ring (27c) placed on the underside of the transducer (27a).If this O-ring(27c) is damaged, it must be replaced.G.Insert the new transducer (27a) into position, taking care to have O-ring (27c) in placewithin the cavity. Use O-ring lubricant (27d) to help hold the O-ring (27c) in place.H.Re-insert the snap ring (27b) to hold the transducer in place. See section 5.0 for leaktesting directions. Leak test the pressure transducer before proceeding to step I.I.Route the three wires coming from the pressure sensor under the PCB assembly (1a) tothe terminal strip.J.Mount the PCB assembly(1a) to the pressure transducer housing.K.Attach the wiring to the PCB assembly (1a) in the proper orientation.5.0 AGV5 PRESSURE TEST5.1After repair and before returning an AGV5 valve to service, the valve assembly must bepressure tested for leaks. Using compressed air, pressurize the valve assembly to 100 PSIG by blocking both the input and output ports. Check for leaks using a solution of water and mild detergent.N OTE: Do not contaminate the electronics with the leak test solution.Remove the PCB assembly to test the pressure transducer interface. Leaks will be indicated by a steady stream of bubbles originating at the source. Pay special attention to the interfaces between the pressure transducer housing (19) and the control housing assembly (12), the pressure transducer (27a) and the pressure transducer housing (25), and the actuator assembly (11) and the port assembly. See FIG. 1A. If a leak is detected, remove all pressure before attempting to tighten fasteners to reduce leakage.5.2The AGV5 valve is not a shutoff valve. There may be some flow through the valve from theinput port to the output port when the valve is closed; this is normal.。
ALINCO-DR635E车载对讲机操作说明
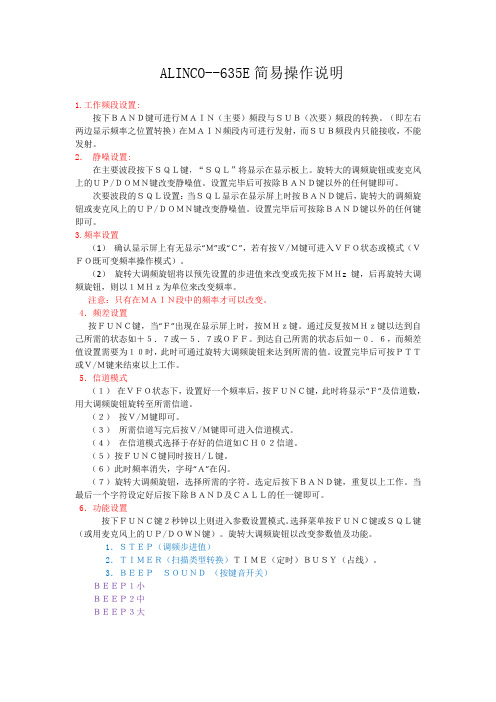
ALINCO--635E简易操作说明1.工作频段设置:按下BAND键可进行MAIN(主要)频段与SUB(次要)频段的转换。
(即左右两边显示频率之位置转换)在MAIN频段内可进行发射,而SUB频段内只能接收,不能发射。
2.静噪设置:在主要波段按下SQL键,“SQL”将显示在显示板上。
旋转大的调频旋钮或麦克风上的UP/DOMN键改变静噪值。
设置完毕后可按除BAND键以外的任何键即可。
次要波段的SQL设置:当SQL显示在显示屏上时按BAND键后,旋转大的调频旋钮或麦克风上的UP/DOMN键改变静噪值。
设置完毕后可按除BAND键以外的任何键即可。
3.频率设置(1)确认显示屏上有无显示“M”或“C”,若有按V/M键可进入VFO状态或模式(VFO既可变频率操作模式)。
(2)旋转大调频旋钮将以预先设置的步进值来改变或先按下MHz键,后再旋转大调频旋钮,则以1MHz为单位来改变频率。
注意:只有在MAIN段中的频率才可以改变。
4.频差设置按FUNC键,当“F”出现在显示屏上时,按MHz键。
通过反复按MHz键以达到自己所需的状态如+5.7或-5.7或OFF。
到达自己所需的状态后如-0.6,而频差值设置需要为10时,此时可通过旋转大调频旋钮来达到所需的值。
设置完毕后可按PTT或V/M键来结束以上工作。
5.信道模式(1)在VFO状态下,设置好一个频率后,按FUNC键,此时将显示“F”及信道数,用大调频旋钮旋转至所需信道。
(2)按V/M键即可。
(3)所需信道写完后按V/M键即可进入信道模式。
(4)在信道模式选择于存好的信道如CH02信道。
(5)按FUNC键同时按H/L键。
(6)此时频率消失,字母“A”在闪。
(7)旋转大调频旋钮,选择所需的字符。
选定后按下BAND键,重复以上工作。
当最后一个字符设定好后按下除BAND及CALL的任一键即可。
6.功能设置按下FUNC键2秒钟以上则进入参数设置模式。
选择菜单按FUNC键或SQL键(或用麦克风上的UP/DOWN键)。
欧里森和通用电气产品维修手册说明书
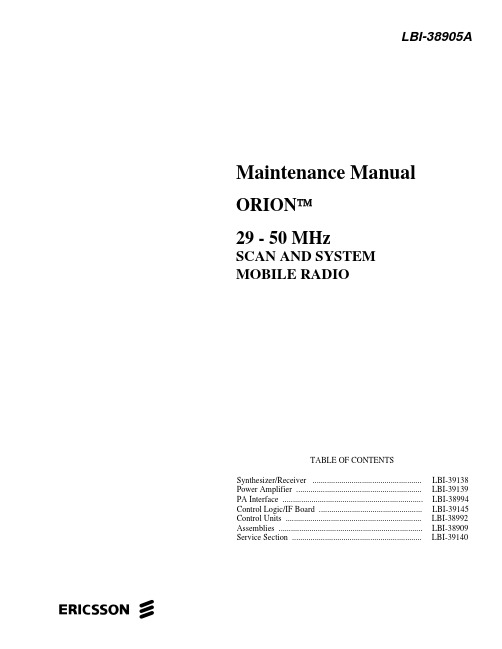
LBI-38905Aericssonz Maintenance Manual ORION™29 - 50 MHzSCAN AND SYSTEMMOBILE RADIOTABLE OF CONTENTSSynthesizer/Receiver .....................................................LBI-39138 Power Amplifier .............................................................LBI-39139 PA Interface ....................................................................LBI-38994 Control Logic/IF Board ..................................................LBI-39145 Control Units ..................................................................LBI-38992 Assemblies ......................................................................LBI-38909 Service Section ...............................................................LBI-39140NOTICE!This manual covers Ericsson and General Electric products manufactured and sold by Ericsson Inc.NOTICE!Repairs to this equipment should be made only by an authorized service technician or facility designated by the supplier. Any repairs, alterations or substitution of recommended parts made by the user to this equipment not approved by the manufacturer could void the user’s authority to operate the equipment in addition to the manufacturer’s warranty.NOTICE!The software contained in this device is copyrighted by Ericsson Inc. Unpublished rights are reserved under the copyright laws of the United States.This manual is published by Ericsson Inc., without any warranty. Improvements and changes to this manual necessitated by typographical errors, inaccuracies of current information, or improvements to programs and/or equipment, may be made by Ericsson Inc., at any time and without notice. Such changes will be incorporated into new editions of this manual. No part of this manual may be reproduced or transmitted in any form or by any means, electronic or mechanical, including photocopying and recording, for any purpose, without the express written permission of Ericsson Inc.Copyright © March, 1995, Ericsson Inc.2SPECIFICATIONS*Frequency Range:29-42 MHz, 35-50 MHzBattery Drain:ReceiveSquelched 1.1 Amperes at 13.8 VoltsUnsquelched 3.0 Amperes at 13.8 Volts (15 Watts Output) Transmitter:60 Watts16 Amperes at 13.2 Volts110 Watts28 Amperes at 13.6 VoltsFrequency Stability:0.0005% depending on modelTemperature Range:-30°C (-22°F) to +60°C (+140°F)Duty Cycle:100% Receive, 14% TransmitTransmitterTransmit Output Power:60/110 WattsConducted Spurious:-85 dBModulation:±5 kHzAudio Sensitivity:55 to 110 millivoltsAudio Frequency Characteristics:Within +1 dB to -3 dB of a 6 dB/octave pre-emphasis 300 Hzand within +1 dB to -4.5 dB of a 6 dB/octave pre-emphasis 3000 Hzper EIA standards. Post-limiter filter per FCC and EIA. Distortion:Less than 2% (1000 Hz)Less than 5% (3000 Hz)Deviation Symmetry:0.3 kHz maximumContinued3ContinuedSPECIFICATIONS*Maximum Frequency Separation:29-42 MHz, 35-50 MHzMicrophone Load Impedance:`600 OhmsPower Adjust Range:100% to 50% of rated power (U.S.A. Models)RF Output Impedance:50 OhmsFM Noise:-50 dBReceiverAudio Output:15 Watts with less than 3% distortion(To 4.0 ohm speaker)Sensitivity:0.35 µV (STD)/0.22 µV (PRE)12 dB SINAD (IEIA method)Selectivity:-85 dBEIA Two-Signal Method(20 kHz Channels)Spurious Response:-100 dBIntermodulation 20 kHz:-85 dBMaximum Frequency Separation:29-42 MHz, 35-50 MHzFrequency Response:Within +1, -3 dB of 6 dB/octave de-emphasis from 300 to 3000MHz (1000 Hz reference)RF Input Impedance:50 OhmsHum/Noise ratio:Unsquelched-50 dBSquelched-70 dBChannel Spacing:20 kHzRegulatory DataFrequency Range MHz RF Output (Watts)FCC ID DOC Type Number DOC Cert. Number287 194 318A 29-4260/30AXATR-337-A5(ORION 30W ONLY)TR-33729-42110AXATR-338-A5- - - -- - - -287 194 318A 35-5060/30AXATR-337-B5(ORION 30W ONLY)TR-33735-50110AXATR-338-A5* These specifications are typical values intended primarily for use of the service technician. Refer to the appropriate Specifications Sheet for the complete specifications.4DESCRIPTIONEricsson Inc.synthesized ORION mobile radio combinations are completely solid-state, utilizing microcomputer technology and integrated circuits to provide high-quality, high-reliability radios. Standard low band combinations are equipped with:• Microcomputer Controlled Frequency Synthesizer•0.0005% Frequency Stability• Noise Blanker• Other Structured OptionsThe basic radio consists of three printed wiring boards mounted in a cast aluminum frame. The three boards are:1. The Control Logic/IF board2. The Frequency Synthesizer/Receiver board3. The Power Amplifier/Exciter boardThe radio is of double-layer construction with tuning adjustments easily accessible.The Control Logic/IF Board is located on the top of the radio, while the Power Amplifier/Exciter and the Synthesizer/Receiver boards are located on the bottom of the radio.SYNTHESIZERThe synthesizer consists of a microcomputer, E lectrically E rasable R ead O nly M emory (EEPROM), a frequency synthesizer IC, transmit and receive V oltage Controlled O scillator's (VCO) and associated circuitry. The frequency synthesizer under control of the microcomputer generates all transmit and receive R adio F requencies (RF).The EEPROM stores binary data for all radio frequencies, Channel Guard tones/digital codes and the timing function of the C arrier C ontrol T imer (CCT). The microcomputer accesses the EEPROM and provides the correct WALSH bits to the Channel Guard circuitry to generate the correct Channel Guard tone or digital code on a per-channel basis.PROGRAMMINGThe EEPROM allows the radio to be programmed or reprogrammed as needed to adapt to changing system requirements. Radio Frequencies, Channel Guard tone and digital codes and the CCT function can be reprogrammed.The EEPROM can be reprogrammed through the radio front connector using a personal computer. This programmer allows all information to be loaded simultaneously.Programming instructions are provided in the respective Programmer Maintenance Manuals. TRANSMITTERThe transmitter consists of the frequency synthesizer, transmitter VCO and a P ower A mplifier (PA) assembly. The PA assembly consists of a PA board mounted on a heat sink assembly. The PA board also contains the exciter, low-pass filter and antenna switching diode.Audio and Channel Guard circuitry for the transmitter is located on the Control Logic/IF Board. RECEIVERThe receiver consists of the frequency synthesizer, RX VCO, injection amplifiers, front end, IF, limiter detector and noise blanker circuitry. Audio, squelch and Channel Guard circuitry for the receiver is located on the Control Logic/IF Board.SYSTEM CONTROL FUNCTIONA microprocessor on the Control Logic/IF board controls the frequency synthesizer, the TX ON/OFF, the decoding of CTCSS tones, the generation of CTCSS tones,. etc. The audio processor circuitry of the transmitter and the receiver are located on the Control Logic/IF board. Squelch circuitry and a connection to the digital AEGIS circuit is also located on the Control Logic/IF board.OPERATIONComplete operating instructions for the ORION two-way radio are provided in Operator's Manual LBI-38888 for the control unit used.MAINTENANCEThe Service Section in maintenance manual LBI-39140 contains the maintenance information to service this radio. The Service Section includes:• Disassembly Procedures5• Replacement of IC's, chip capacitors and resistors• Alignment procedures for the transmitter and receiver • Troubleshooting Procedures and wave forms • A mechanical layout for the radio is found in ORION Assemblies Maintenance Manual LBI-38909.RADIO UNIT344A4576P1/JHM-171S60A, 344A4576P2/JHM-171S60B344A4576P3/JHM-171S110A, 344A4576P4/JHM-171S110B6(DD00-JHM-171S)7Ericsson Inc.Private Radio SystemsMountain View RoadLynchburg, Virginia 245021-800-592-7711 (Outside USA, 804-592-7711)Printed in U.S.A.。
维修英语手册
