悬架运动校核报告编写规范标准
基于某轻型载荷汽车的转向悬架系统dmu校核
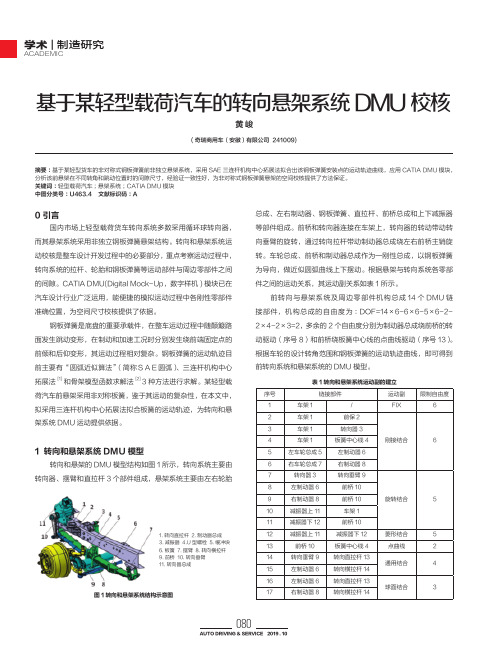
ACADEMIC
基于某轻型载荷汽车的转向悬架系统 DMU 校核
黄峻
( 奇瑞商用车(安徽)有限公司 241009)
摘要 :基于某轻型货车的非对称式钢板弹簧前非独立悬架系统,采用 SAE 三连杆机构中心拓展法拟合出该钢板弹簧安装点的运动轨迹曲线,应用 CATIA DMU 模块, 分析该前悬架在不同转角和跳动位置时的间隙尺寸,经验证一致性好,为非对称式钢板弹簧悬架的空间校核提供了方法保证。 关键词 :轻型载荷汽车 ;悬架系统 ;CATIA DMU 模块 中图分类号 :U463.4 文献标识码 :A
图 1 转向和悬架系统结构示意图
总成、左右制动器、钢板弹簧、直拉杆、前桥总成和上下减振器 等部件组成。前桥和转向器连接在车架上,转向器的转动带动转 向垂臂的旋转,通过转向拉杆带动制动器总成绕左右前桥主销旋 转。车轮总成、前桥和制动器总成作为一刚性总成,以钢板弹簧 为导向,做近似圆弧曲线上下摆动。根据悬架与转向系统各零部 件之间的运动关系,其运动副关系如表 1 所示。
序号 1 2 3 4 5 6 7 8 9 10 11 12 13 14 15 16 17
表 1 转向和悬架系统运动副的建立
链接部件
运动副
车架 1
/
FIX
车架 1
前保 2
车架 1
转向器 3
车架 1
板簧中心线 4
刚接结合
左车轮总成 5
左制动器 6
右车轮总成 7
右制动器 8
转向器 3
转向垂臂 9
左制动器 6
6
5
5 2 4 3
080
AUTO DRIVING & SERVICE 2019 . 10
学术 | 制造研究 ACADEMIC
F505-BM-DP-016标杆车悬架系统计算校核报告.
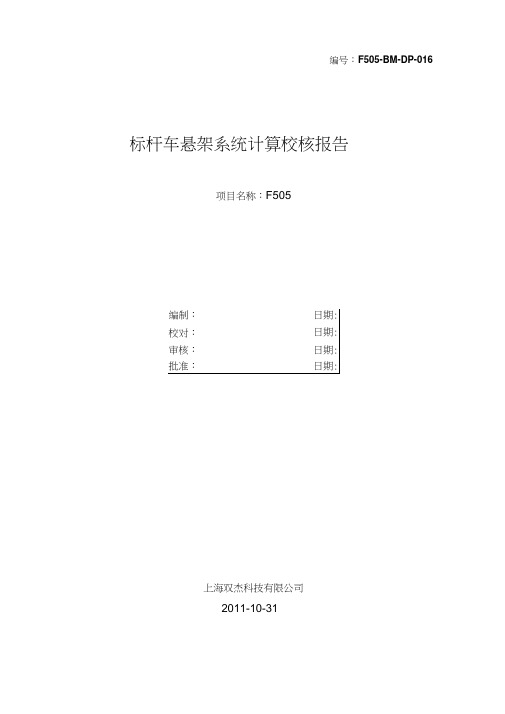
编号:F505-BM-DP-016标杆车悬架系统计算校核报告项目名称:F505编制:日期:校对:日期:审核:日期:批准:日期:上海双杰科技有限公司2011-10-311 •概述................................................................ 1.1.1 悬架系统基本介绍................................................ 1.1.2 计算目的.........................................................2.2 .悬架系统相关参数.................................................... 2.3 .悬架系统相关计算..................................................... 3.3.1 悬架偏频的计算................................................... 3.3.1.1 前悬架偏频的计算.............................................. 3.3.1.2 后悬架偏频的计算...............................................4.3.1.3 前后悬架偏频比.................................................4.3.2整车侧倾角计算..................................................... 5.3.2.1 前悬架的侧倾角刚度............................................ 5.3.2.2 后悬架的侧倾角刚度............................................. 8.3.2.3 侧倾角的计算.................................................. .9..3.3 整车的纵倾角刚度 (10)4. 悬架参数 (12)5. 总结 (12)参考文献........................................................ .131. 概述1.1 悬架系统基本介绍标杆车前悬架采用麦弗逊式独立悬架,下控制臂采用常见的“镰刀型”结构。
独立悬架导向机构设计及强度校核
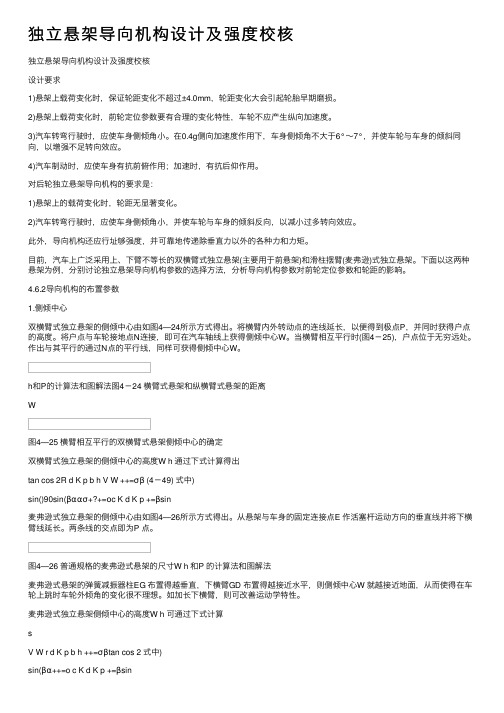
独⽴悬架导向机构设计及强度校核独⽴悬架导向机构设计及强度校核设计要求1)悬架上载荷变化时,保证轮距变化不超过±4.0mm,轮距变化⼤会引起轮胎早期磨损。
2)悬架上载荷变化时,前轮定位参数要有合理的变化特性,车轮不应产⽣纵向加速度。
3)汽车转弯⾏驶时,应使车⾝侧倾⾓⼩。
在0.4g侧向加速度作⽤下,车⾝侧倾⾓不⼤于6°~7°,并使车轮与车⾝的倾斜同向,以增强不⾜转向效应。
4)汽车制动时,应使车⾝有抗前俯作⽤;加速时,有抗后仰作⽤。
对后轮独⽴悬架导向机构的要求是:1)悬架上的载荷变化时,轮距⽆显著变化。
2)汽车转弯⾏驶时,应使车⾝侧倾⾓⼩,并使车轮与车⾝的倾斜反向,以减⼩过多转向效应。
此外,导向机构还应⾏址够强度,并可靠地传递除垂直⼒以外的各种⼒和⼒矩。
⽬前,汽车上⼴泛采⽤上、下臂不等长的双横臂式独⽴悬架(主要⽤于前悬架)和滑柱摆臂(麦弗逊)式独⽴悬架。
下⾯以这两种悬架为例,分别讨论独⽴悬架导向机构参数的选择⽅法,分析导向机构参数对前轮定位参数和轮距的影响。
4.6.2导向机构的布置参数1.侧倾中⼼双横臂式独⽴悬架的侧倾中⼼由如图4—24所⽰⽅式得出。
将横臂内外转动点的连线延长,以便得到极点P,并同时获得户点的⾼度。
将户点与车轮接地点N连接,即可在汽车轴线上获得侧倾中⼼W。
当横臂相互平⾏时(图4-25),户点位于⽆穷远处。
作出与其平⾏的通过N点的平⾏线,同样可获得侧倾中⼼W。
h和P的计算法和图解法图4-24 横臂式悬架和纵横臂式悬架的距离W图4—25 横臂相互平⾏的双横臂式悬架侧倾中⼼的确定双横臂式独⽴悬架的侧倾中⼼的⾼度W h 通过下式计算得出tan cos 2R d K p b h V W ++=σβ (4-49) 式中)sin()90sin(βαασ+?+=οc K d K p +=βsin麦弗逊式独⽴悬架的侧倾中⼼由如图4—26所⽰⽅式得出。
从悬架与车⾝的固定连接点E 作活塞杆运动⽅向的垂直线并将下横臂线延长。
《乘用车悬架系统台架试验标准规范》编制说明范本
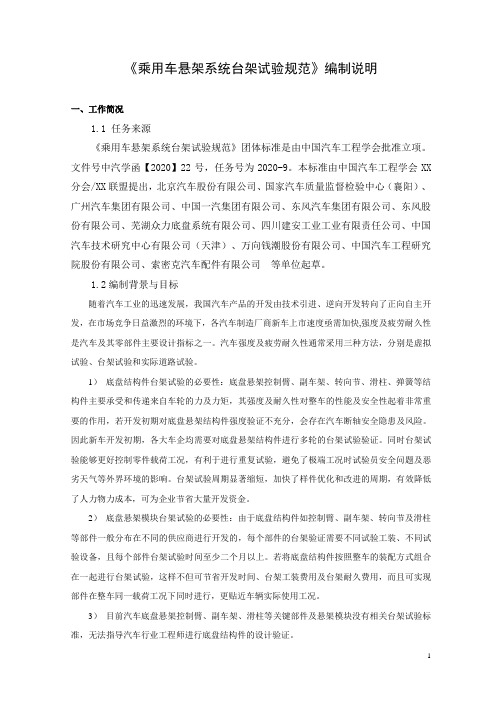
《乘用车悬架系统台架试验规范》编制说明一、工作简况1.1 任务来源《乘用车悬架系统台架试验规范》团体标准是由中国汽车工程学会批准立项。
文件号中汽学函【2020】22号,任务号为2020-9。
本标准由中国汽车工程学会XX 分会/XX联盟提出,北京汽车股份有限公司、国家汽车质量监督检验中心(襄阳)、广州汽车集团有限公司、中国一汽集团有限公司、东风汽车集团有限公司、东风股份有限公司、芜湖众力底盘系统有限公司、四川建安工业工业有限责任公司、中国汽车技术研究中心有限公司(天津)、万向钱潮股份有限公司、中国汽车工程研究院股份有限公司、索密克汽车配件有限公司等单位起草。
1.2编制背景与目标随着汽车工业的迅速发展,我国汽车产品的开发由技术引进、逆向开发转向了正向自主开发,在市场竞争日益激烈的环境下,各汽车制造厂商新车上市速度亟需加快,强度及疲劳耐久性是汽车及其零部件主要设计指标之一。
汽车强度及疲劳耐久性通常采用三种方法,分别是虚拟试验、台架试验和实际道路试验。
1)底盘结构件台架试验的必要性:底盘悬架控制臂、副车架、转向节、滑柱、弹簧等结构件主要承受和传递来自车轮的力及力矩,其强度及耐久性对整车的性能及安全性起着非常重要的作用,若开发初期对底盘悬架结构件强度验证不充分,会存在汽车断轴安全隐患及风险。
因此新车开发初期,各大车企均需要对底盘悬架结构件进行多轮的台架试验验证。
同时台架试验能够更好控制零件载荷工况,有利于进行重复试验,避免了极端工况时试验员安全问题及恶劣天气等外界环境的影响。
台架试验周期显著缩短,加快了样件优化和改进的周期,有效降低了人力物力成本,可为企业节省大量开发资金。
2)底盘悬架模块台架试验的必要性:由于底盘结构件如控制臂、副车架、转向节及滑柱等部件一般分布在不同的供应商进行开发的,每个部件的台架验证需要不同试验工装、不同试验设备,且每个部件台架试验时间至少二个月以上。
若将底盘结构件按照整车的装配方式组合在一起进行台架试验,这样不但可节省开发时间、台架工装费用及台架耐久费用,而且可实现部件在整车同一载荷工况下同时进行,更贴近车辆实际使用工况。
《乘用车悬架系统台架试验标准规范》编制说明范本
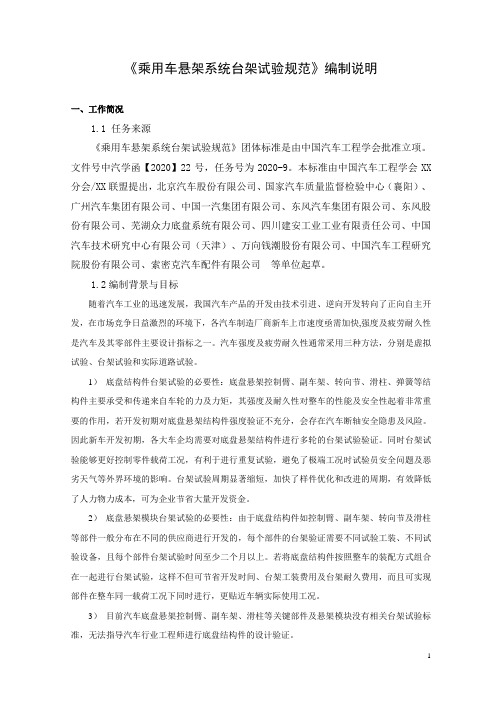
《乘用车悬架系统台架试验规范》编制说明一、工作简况1.1 任务来源《乘用车悬架系统台架试验规范》团体标准是由中国汽车工程学会批准立项。
文件号中汽学函【2020】22号,任务号为2020-9。
本标准由中国汽车工程学会XX 分会/XX联盟提出,北京汽车股份有限公司、国家汽车质量监督检验中心(襄阳)、广州汽车集团有限公司、中国一汽集团有限公司、东风汽车集团有限公司、东风股份有限公司、芜湖众力底盘系统有限公司、四川建安工业工业有限责任公司、中国汽车技术研究中心有限公司(天津)、万向钱潮股份有限公司、中国汽车工程研究院股份有限公司、索密克汽车配件有限公司等单位起草。
1.2编制背景与目标随着汽车工业的迅速发展,我国汽车产品的开发由技术引进、逆向开发转向了正向自主开发,在市场竞争日益激烈的环境下,各汽车制造厂商新车上市速度亟需加快,强度及疲劳耐久性是汽车及其零部件主要设计指标之一。
汽车强度及疲劳耐久性通常采用三种方法,分别是虚拟试验、台架试验和实际道路试验。
1)底盘结构件台架试验的必要性:底盘悬架控制臂、副车架、转向节、滑柱、弹簧等结构件主要承受和传递来自车轮的力及力矩,其强度及耐久性对整车的性能及安全性起着非常重要的作用,若开发初期对底盘悬架结构件强度验证不充分,会存在汽车断轴安全隐患及风险。
因此新车开发初期,各大车企均需要对底盘悬架结构件进行多轮的台架试验验证。
同时台架试验能够更好控制零件载荷工况,有利于进行重复试验,避免了极端工况时试验员安全问题及恶劣天气等外界环境的影响。
台架试验周期显著缩短,加快了样件优化和改进的周期,有效降低了人力物力成本,可为企业节省大量开发资金。
2)底盘悬架模块台架试验的必要性:由于底盘结构件如控制臂、副车架、转向节及滑柱等部件一般分布在不同的供应商进行开发的,每个部件的台架验证需要不同试验工装、不同试验设备,且每个部件台架试验时间至少二个月以上。
若将底盘结构件按照整车的装配方式组合在一起进行台架试验,这样不但可节省开发时间、台架工装费用及台架耐久费用,而且可实现部件在整车同一载荷工况下同时进行,更贴近车辆实际使用工况。
板簧悬架运动行程校核规范
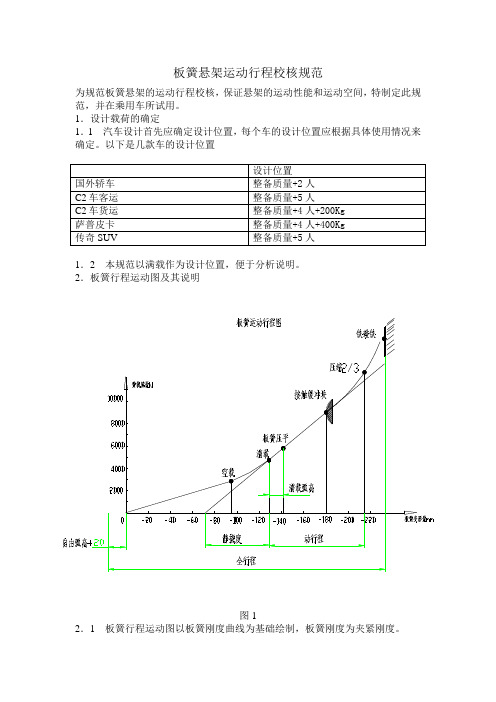
板簧悬架运动行程校核规范为规范板簧悬架的运动行程校核,保证悬架的运动性能和运动空间,特制定此规范,并在乘用车所试用。
1.设计载荷的确定1.1 汽车设计首先应确定设计位置,每个车的设计位置应根据具体使用情况来确定。
以下是几款车的设计位置1.2 本规范以满载作为设计位置,便于分析说明。
2.板簧行程运动图及其说明图12.1 板簧行程运动图以板簧刚度曲线为基础绘制,板簧刚度为夹紧刚度。
2.2 以满载位置为基准,至缓冲块压缩2/3时,为板簧悬架动行程,板簧悬架的动行程应保证3个g的动载荷冲击,悬架动行程不小于100 mm。
2.3 板簧刚度曲线在满载点的切线为悬架的满载刚度,由该切线沿伸至横轴交点,确定悬架静挠度,如图示,计算出的悬架动挠度应在悬架的动行程之内。
2.4 以满载位置为基准,至铁碰铁时的悬架行程作为车轮与轮罩的校核依据,缓冲块压缩2/3至铁碰铁的距离不小于20 mm。
2.5 以满载位置为基准,至板簧压平段为板簧满载弧高,满载弧高控制在15-30mm。
2.6 板簧悬空时处于自由弧高+20的状态为悬架行程下极限,铁碰铁为悬架行程上极限,悬架从上极限至下极限为悬架的全行程,悬架的全行程应不小于220 mm,2.7 在空载与满载之间,可根据具体情况增加载荷点,如:2人状态、5人状态。
3.板簧运动行程校核板簧行程运动图(图1)作为设计计算及总布置评审的说明图。
板簧的实际运动行程校核可在二维或三维图上进行,见图2。
3.1 板簧主片的中性面A点的运动中心为O1,O1点由L1/4和e/2来决定,L1/4为1/4板簧前半部分的长度(即:1/4半长),e为板簧卷耳中心至板簧主片的中性面的距离。
3.2 桥中心的运动规迹按图2中的平行四边形确定,O2桥中心B点的运动中心。
图24.板簧前倾角的确定4.1 板簧前倾角考虑车辆的不足转向,应有适度的不足转向度。
4.2 从图2中可以看出车辆是否有不足转向的倾向,方法是以满载为平衡位置,桥中心分别上下跳动50,作水平线,分别量出图2中的x1和x2,(规定桥往前走为正)只要x1大于x2则车辆有不足转向。
悬架特性参数实验报告(3篇)

第1篇一、实验目的本实验旨在通过实际测试和数据分析,了解汽车悬架系统的特性参数,包括弹簧刚度、阻尼系数、悬挂行程等,并分析这些参数对汽车行驶性能的影响。
通过实验,我们可以优化悬架系统设计,提高汽车的舒适性和操控稳定性。
二、实验原理汽车悬架系统是连接车轮与车架的部件,其主要功能是吸收和缓解道路不平引起的冲击,保证车身平稳,提高乘坐舒适性。
悬架系统的特性参数主要包括弹簧刚度、阻尼系数和悬挂行程等。
1. 弹簧刚度(k):弹簧刚度是指弹簧单位变形量所需的力。
刚度越大,弹簧越难以变形,对冲击的吸收能力越强。
2. 阻尼系数(c):阻尼系数是指阻尼器吸收能量的能力。
阻尼系数越大,阻尼器吸收能量越多,车身振动越小。
3. 悬挂行程(x):悬挂行程是指车轮跳动时,悬挂系统相对车架的位移。
三、实验设备1. 汽车悬架测试台2. 力传感器3. 位移传感器4. 数据采集系统5. 计算机及软件四、实验步骤1. 搭建实验平台:将汽车悬架系统固定在测试台上,确保测试过程中的稳定。
2. 安装传感器:将力传感器和位移传感器分别安装在弹簧和悬挂行程上,用于测量弹簧刚度和悬挂行程。
3. 测试弹簧刚度:在汽车静止状态下,逐渐施加力,记录力传感器输出的力值和位移传感器输出的位移值,利用胡克定律计算弹簧刚度。
4. 测试阻尼系数:在汽车静止状态下,施加一定的频率和振幅的振动,记录力传感器输出的力值和位移传感器输出的位移值,利用阻尼比公式计算阻尼系数。
5. 测试悬挂行程:在汽车静止状态下,逐渐增加车轮跳动高度,记录悬挂行程。
五、实验结果与分析1. 弹簧刚度:实验结果表明,汽车悬架系统的弹簧刚度在1.5×10^5 N/m左右,符合一般汽车悬架系统的设计要求。
2. 阻尼系数:实验结果表明,汽车悬架系统的阻尼系数在0.1左右,符合一般汽车悬架系统的设计要求。
3. 悬挂行程:实验结果表明,汽车悬架系统的悬挂行程在20cm左右,符合一般汽车悬架系统的设计要求。
汽车悬架试验报告
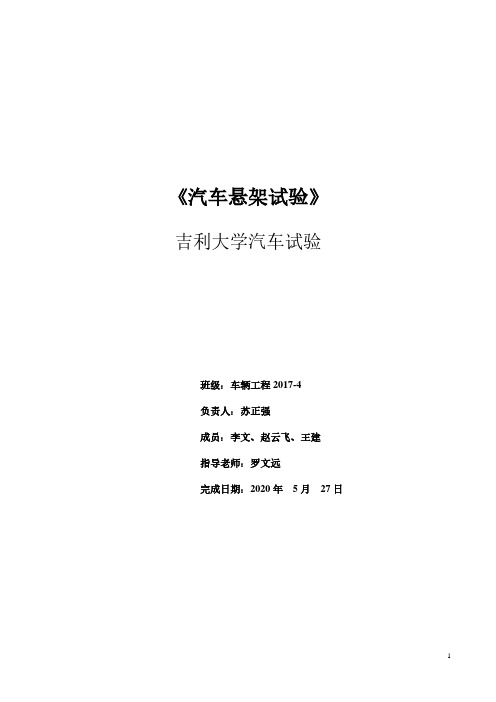
0, 4151
后
0, 02411 0^ 03386
0^ 02898
2+⑻⑻ 前
11.8064 后
1. 5898 10.1214
1. 7949 10. 9630
7
则可由以上数据计算平均值: 车身的固有频率为 f 0 = 2.1874,车轮的固有频率为
f = 2.5479 ,平均阻尼比为 = 0.2472
《汽车悬架试验》
吉利大学汽车试验
班级:车辆工程 2017-4 负责人:苏正强 成员:李文、赵云飞、王建 指导老师:罗文远 完成日期:2020 年 5 月 27 日
1
目录
一、试验概述(时间、地点、背景)........................................................................ 3 二、试验目的................................................................................................................ 3 三、试验所依据的标准................................................................................................ 3 四、试验项目................................................................................................................ 3 五、试验测试条件........................................................................................................ 4 六、试验仪器与设备.................................................................................................... 4 七、试验操作程序与具体方法.................................................................................... 4 八、人员组织与计划进度............................................................................................ 4 九、计划外事件的应对预案........................................................................................ 4 十、试验结果记录与分析............................................................................................ 5 参考资料........................................................................................................................ 8
悬架动力学分析技术规范

上海同济同捷科技有限公司企业标准TJI/YJY·03·155-2005悬架动力学分析技术规范2005-09-28 发布2005-09-30 实施上海同济同捷科技有限公司发布前言为使本公司在悬架动力学分析时技术规范化和资料的积累,将本公司的经验给予总结,使之有普遍的指导作用,编制本标准并在实践中不断充实和完善。
内容包括:悬架动力学模型的建立的技术要求;模型检验要求;分析结果的评价原则和输出内容。
本标准于2005年9月30日实施。
本标准的附录A为规范性附录。
本标准由上海同济同捷科技有限公司提出。
本标准由上海同济同捷科技有限公司质量与项目管理中心负责归口管理。
本标准主要起草人:白冰悬架动力学分析技术规范1 范围:1.1 本标准适用于悬架动力学分析中的模型建立。
1.2 本标准适用于悬架动力学分析时对悬架分析过程进行质量控制及评价。
2悬架模型的建立2.1 悬架模型的建立的目的:悬架系统设计直接关系到整车的操纵稳定性、平顺性等主要性能,通过悬架的动力学仿真分析,达到满足整车性能匹配和系统优化的要求。
2.2悬架ADAMS几何模型的建立的方法;2.2.1通过输入各设计硬点或连接点的坐标;2.2.2通过直接导入悬架三维CAD模型数据的方式;2.2.3添加合适的运动副、弹性元件等,输入各零部件的相关参数;2.2.3.1运动副按照悬架上的实际连接方式进行进行添加,由较多的连接物体构成的运动副可根据实际情况简化,如减震器上支点,可合理简化为球铰;2.2.3.2弹性元件中弹簧根据实际的测量得到的数据输入,非线性弹簧根据非线性关系使用spline线定义,弹性衬套输入x、y、z 三个方向的平移刚度及扭转刚度的试验值,横向稳定杆根据试验值或分析值输入;2.2.3.3输入的各零部件必须与三维数模中的零件质量、质心、转动惯量保持一致;2.2.4 ADAMS模型,硬点坐标与三维数模误差精确到0.01mm;2.2.5采用各种技术方法,例如,导入UG数模,建立近似实物的模型,提高模型的外观质量,以增强模型与实物的符合性和直观性;2.2.6几何模型建立以后,按照待分析悬架的实际技术参数,检验或准确输入各零部件的物理指标;2.3 悬架动力学模型建立原则2.3.1 保证各弹性连接件的方向,并正确输入弹性连接件的各向刚度、各向阻尼等参数;2.3.2 悬架导向杆、转向梯形杆件、横向稳定杆等不同物体的约束方式应与待分析样车的物理状况一致;2.3.3 悬架自由度、悬架上下运动行程、转向器或齿条行程角输入数值、轮胎定位参数、初始设计位置轮心坐标应符合工程实际情况,满足仿真分析目标要求;2.4 悬架动力学模型建立原则2.4.1 满足2.2悬架动力学模型建立技术所有要求;2.4.2 准确输入下述参数:悬架非簧载质量、悬架各杆件质量及转动惯量、车轮质量及转动惯量、转向拉杆质量及转动惯量;2.4.3 准确输入弹簧刚度、弹簧预紧力、减震器特性曲线;2.4.4准确输入其它悬架动力学分析所需的相关零件质量、转动惯量;3 悬架模型检验及仿真分析技术要求3.1 模型检验仿真分析之前必须对模型进行检验,悬架模型符合要求:3.1.1无自由物体(part);3.1.2无没有质量及质心物体(part);3.1.3原则上不允许存在片体(sheet);3.1.4无多余约束;3.1.5悬架仿真模型自由度应与待分析样机实际状况相吻合;3.1.6仿真模型验证成功。
董伟佳-悬架运动校核
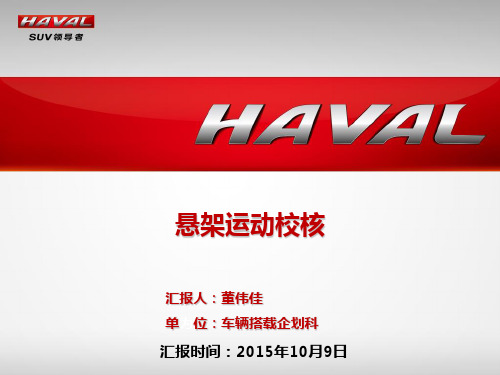
二、引用标准
Q/CC SY0082-2014 Q/CC SJ0647-2014 Q/CC SJ446-2013 Q/CC SJ447-2013
整车保安防灾评价 前悬架DMU仿真模型减震器行程计算规范 麦弗逊式前悬架DMU仿真模型建立规范 双横臂式前悬架DMU仿真模型建立规范
第10页/共27页
进行干涉检查时,对于两侧对称的情况一般只对左侧进行检查,下图为 CHB121车型前悬架DMU模型及运动副的表示,该模型还可应用于轮跳校核和传 动轴匹配。
第11页/共27页
4、悬架运动和转向运动的范围值添加;(此值计算过程在PPT第五页)
1 2
3
转向运动 悬架运动
第12页/共27页
度测量位置相对应),图纸最大行程如图1所示;减震器数模最大行程如图2所示。
图1、图纸最大行程
图2、数模最大行程 第5页/共27页
图3、减震器缸筒上端面到缓冲块下平面的距离测量位 图4、缓冲块最大压缩量
上极限行程=减震器缸筒上端面到缓冲块下平面的距离+2/3缓冲块最大压缩量, 减震器缸筒上端面到缓冲块下平面的距离测量位置如图3所示;缓冲块最大压缩量 选取如图4所示。
中文 前悬架运动模型
前悬固定 左前减振支柱上部 左前车轮及减振器下部
左前下摆臂 左转向拉杆
转向机 左前半轴 左前稳定杆连接杆 左前稳定杆 右前稳定杆 右前减振支柱上部 右前车轮及减振器下部 右前下摆臂 右转向拉杆 右前半轴 右前稳定杆连接杆
运动模型中的零部件需根据运动关系对零部件进行拆解,拆解组合后的零 部件如下表所示。
悬架运动校核
汇报人:董伟佳 单为位:车辆搭载企划科
悬架运动校核报告编写规范标准

悬架运动校核报告编写规范标准悬架运动校核报告是汽车设计过程中的重要内容,旨在评估汽车悬架系统在各种情况下的动态响应和耐久性,并指导悬架参数的优化设计。
正确编写悬架运动校核报告,对汽车的安全性、品质和性能具有重要影响。
下面介绍悬架运动校核报告编写的规范标准。
一、报告结构悬架运动校核报告应包括标题、正文、结论和参考文献等部分。
其中,标题应准确反映报告主题,正文应按照逻辑顺序叙述研究内容,结论应简明扼要,参考文献应列出所引用文献的详细信息。
二、报告内容1. 引言:介绍研究目的、背景和意义,阐述悬架系统的结构和工作原理,分析研究需要解决的问题和重点。
2. 悬架运动学分析:对悬架系统进行运动学分析,计算并绘制车辆在行驶过程中的运动规律。
包括车辆的悬架几何参数、车轮悬挂方式、悬架软硬度、悬架刚度等方面的分析。
3. 悬架动力学分析:对悬架系统进行动力学分析,计算并绘制车辆在行驶过程中的动力学响应。
涉及到车辆在路面上运动过程中受到的力的分类、大小及方向,以及悬架系统对这些力的响应情况等方面的分析。
4. 悬架材料、结构分析:对悬架系统的材料和结构进行分析,评估其中一些可能存在的问题,如应力集中、材料疲劳等。
5. 模拟与仿真:在对悬架系统进行分析后,用计算机模拟与仿真的方法,评估悬架系统的动态响应。
可以使用MATLAB、SIMULINK等硬件仿真软件。
6. 结论:根据上述分析,得出悬架系统的优点和不足之处,提出可能存在的问题和改进方案,并展望未来的研究方向。
三、技术要求1. 技术标准:编写悬架运动校核报告的过程中,需要参照相关的技术标准和规范,包括国家标准和行业标准等。
2. 严谨性和准确性:报告内容应严谨、准确、无误。
在编写报告前应对所使用的数据和统计信息进行认真核对,确保数据的正确性和准确性。
3. 细致和完整性:报告内容应细致、全面,不遗漏任何重要的信息和数据,并对数据的来源进行详细的说明。
4. 结论说服力:在结论部分,应明确、简明扼要地表达研究所得到的结论,对未来的发展方向进行分析与预测,以及提出有效的建议。
汽车悬架的实验报告(3篇)

第1篇一、实验目的1. 了解汽车悬架的结构和工作原理;2. 掌握汽车悬架的性能测试方法;3. 分析汽车悬架在不同工况下的性能表现;4. 提高汽车悬架的维修和调试能力。
二、实验原理汽车悬架系统是汽车底盘的重要组成部分,其主要作用是连接车架(或车身)与车轮,传递和缓冲各种路面冲击力,保证汽车行驶的平顺性和稳定性。
汽车悬架系统由弹性元件、导向机构、减振器和稳定杆等组成。
三、实验设备与材料1. 汽车悬架实验台;2. 汽车悬架系统;3. 传感器;4. 数据采集器;5. 计算机及软件。
四、实验步骤1. 汽车悬架系统安装:将汽车悬架系统安装到实验台上,确保安装牢固。
2. 测试准备:将传感器安装在汽车悬架系统上,连接数据采集器。
3. 性能测试:(1)垂直跳动测试:在汽车悬架系统上施加一定的垂直力,记录悬架系统的垂直跳动量。
(2)侧向跳动测试:在汽车悬架系统上施加一定的侧向力,记录悬架系统的侧向跳动量。
(3)俯仰跳动测试:在汽车悬架系统上施加一定的俯仰力,记录悬架系统的俯仰跳动量。
(4)扭力测试:在汽车悬架系统上施加一定的扭力,记录悬架系统的扭力传递性能。
(5)刚度测试:在汽车悬架系统上施加一定的载荷,记录悬架系统的刚度。
4. 数据采集与处理:将实验数据传输到计算机,利用软件进行分析和处理。
5. 结果分析:根据实验数据,分析汽车悬架系统在不同工况下的性能表现。
五、实验结果与分析1. 垂直跳动测试:汽车悬架系统的垂直跳动量较小,说明其具有良好的缓冲性能。
2. 侧向跳动测试:汽车悬架系统的侧向跳动量较小,说明其具有良好的稳定性。
3. 俯仰跳动测试:汽车悬架系统的俯仰跳动量较小,说明其具有良好的操控性能。
4. 扭力测试:汽车悬架系统在扭力作用下,能够有效地传递和缓冲扭力,保证汽车行驶的稳定性。
5. 刚度测试:汽车悬架系统的刚度适中,既能保证汽车的舒适性,又能满足操控性能。
六、实验结论1. 汽车悬架系统在垂直跳动、侧向跳动、俯仰跳动和扭力传递等方面均表现出良好的性能。
悬架运动校核报告编写规范标准

目录1.概述 (1)2.1号标杆车轿车前悬架跳动校核 (2)2.1前悬架运动校核的有关参数 (2)2.2 前悬架跳动包络图 (2)2.3 前悬架包络与轮罩等的间隙校核 (3)2.4 前悬架摆臂与副车架间隙校核 (4)3.1号标杆车轿车后悬架跳动校核 (5)3.1 1号标杆车轿车后悬架跳动量 (5)3.2 1号标杆车轿车后悬架跳动包络图 (5)3.3 1号标杆车轿车后悬架跳动包络与周边间隙 (5)4.前后悬架螺旋弹簧长度校核 (8)5.前、后减振器长度校核 (8)5.1 前减振器校核 (8)5.2 后减振器校核 (8)6.总结 (9)参考文献 (9)1.概述悬架是汽车上的重要总成,在汽车行驶过程中,悬架系统因载荷及路面变化总是处于不断的变化之中,因此在进行总布置设计时,必须对悬架的运动进行校核,防止发生运动干涉。
此校核的目的是确定悬架运动至极限位置时占用的空间(对于前悬架应同时考虑上跳、下跳及转向至极限位置时的情况),从而检查悬架与轮罩、纵梁、副车架等之间的间隙是否足够,同时检查悬架系统内部在变化过程中是否存在干涉现象。
下面分别对1号标杆车轿车前、后悬架跳动情况进行分析,对其空间布置情况进行校核。
2.1号标杆车前悬架跳动校核1号标杆车轿车前悬架为麦弗逊式独立悬架,驱动方式为发动机前横置、前驱动,前轮既是转向轮,又是驱动轮。
因此,在进行前悬架运动校核时,必须同时考虑转向、悬架变形两个方面的综合作用。
2.1前悬架运动校核的有关参数根据前悬架的空间位置及转向器的设计行程(设计行程为152mm),可得1号标杆车轿车的悬架运动包络图。
前悬架的上跳极限按橡胶限位块压缩1/2计算,得出1号标杆车轿车前悬架上跳最大行程38.7mm,即前悬架从满载状态向上最大跳动量;前悬架的下跳极限为前减振器活塞杆拉出最长位置时的状态,得出1号标杆车轿车前悬架下跳最大行程115.4mm,即前悬架从满载状态向下最大跳动量。
2.2 前悬架跳动包络图图1前悬架跳动包络图将前悬架数模导入ADAMS软件中,在悬架各铰接点处添加合适的运动副、弹性元件等连接部件,并输入相关参数,得到如图1所示的分析模型。
2汽车总布置_悬架运动校核
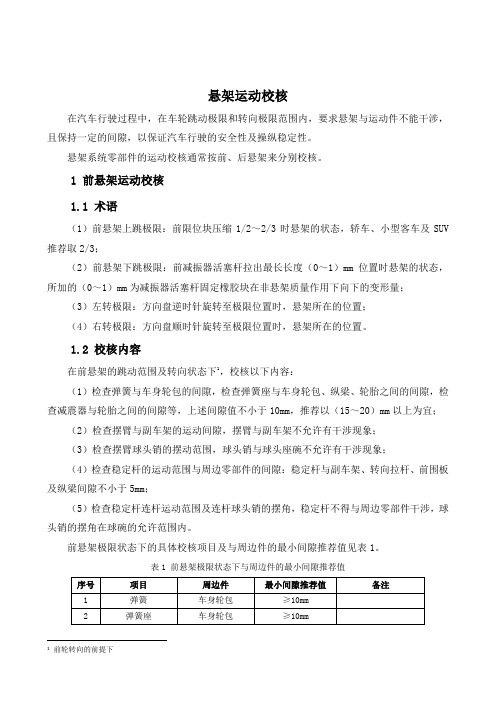
悬架运动校核在汽车行驶过程中,在车轮跳动极限和转向极限范围内,要求悬架与运动件不能干涉,且保持一定的间隙,以保证汽车行驶的安全性及操纵稳定性。
悬架系统零部件的运动校核通常按前、后悬架来分别校核。
1 前悬架运动校核1.1 术语(1)前悬架上跳极限:前限位块压缩1/2~2/3时悬架的状态,轿车、小型客车及SUV 推荐取2/3;(2)前悬架下跳极限:前减振器活塞杆拉出最长长度(0~1)mm位置时悬架的状态,所加的(0~1)mm为减振器活塞杆固定橡胶块在非悬架质量作用下向下的变形量;(3)左转极限:方向盘逆时针旋转至极限位置时,悬架所在的位置;(4)右转极限:方向盘顺时针旋转至极限位置时,悬架所在的位置。
1.2 校核内容在前悬架的跳动范围及转向状态下1,校核以下内容:(1)检查弹簧与车身轮包的间隙,检查弹簧座与车身轮包、纵梁、轮胎之间的间隙,检查减震器与轮胎之间的间隙等,上述间隙值不小于10mm,推荐以(15~20)mm以上为宜;(2)检查摆臂与副车架的运动间隙,摆臂与副车架不允许有干涉现象;(3)检查摆臂球头销的摆动范围,球头销与球头座碗不允许有干涉现象;(4)检查稳定杆的运动范围与周边零部件的间隙:稳定杆与副车架、转向拉杆、前围板及纵梁间隙不小于5mm;(5)检查稳定杆连杆运动范围及连杆球头销的摆角,稳定杆不得与周边零部件干涉,球头销的摆角在球碗的允许范围内。
前悬架极限状态下的具体校核项目及与周边件的最小间隙推荐值见表1。
表1 前悬架极限状态下与周边件的最小间隙推荐值1前轮转向的前提下2 后悬架运动校核2.1 术语(1)上跳极限:后限位块压缩1/2~2/3;轿车及小型客车非独立悬架推荐取1/2,轿车及小型客车独立悬架、SUV推荐取2/3;(2)下跳极限:后减振器活塞杆拉出最长长度(0~2)mm位置时悬架系统的状态,所加的(0~2)mm为减振器活塞杆固定橡胶块在非悬架质量作用下向下的变形量。
2.2 校核内容在后悬架跳动范围内,检查减振器、弹簧、弹簧座与车身轮包、纵梁等之间的间隙,间隙值不小于10mm,推荐(15~20)mm以上为宜,后悬架极限状态下各部件与周边件的最小间隙推荐值见表2。
悬架性能实验报告总结(3篇)

第1篇一、实验背景随着我国汽车工业的快速发展,汽车悬架系统作为汽车底盘的重要组成部分,其性能直接影响着车辆的乘坐舒适性、行驶安全性以及操控稳定性。
为了提高汽车悬架系统的性能,本研究对某型汽车悬架系统进行了性能实验,以期为悬架系统的优化设计提供理论依据。
二、实验目的1. 了解汽车悬架系统的基本原理和结构;2. 评估悬架系统的各项性能指标;3. 为悬架系统的优化设计提供理论依据。
三、实验方法1. 实验设备:汽车悬架系统、测力传感器、加速度传感器、计算机等;2. 实验步骤:(1)搭建实验平台,安装好汽车悬架系统;(2)对悬架系统进行标定,确保各传感器正常工作;(3)按照实验方案进行实验,记录实验数据;(4)对实验数据进行处理和分析。
四、实验结果与分析1. 悬架刚度实验(1)实验数据:通过对悬架系统施加不同频率的正弦载荷,记录悬架系统的振动响应,得到悬架刚度随频率的变化曲线。
(2)分析:从实验数据可以看出,悬架刚度随着频率的增加而逐渐减小,说明悬架系统具有较好的高频阻尼性能。
2. 悬架阻尼实验(1)实验数据:通过改变阻尼比,记录悬架系统的振动响应,得到悬架阻尼系数随阻尼比的变化曲线。
(2)分析:从实验数据可以看出,随着阻尼比的增大,悬架系统的阻尼系数逐渐增大,说明悬架系统具有较好的阻尼性能。
3. 悬架振动实验(1)实验数据:对悬架系统施加不同频率的正弦载荷,记录悬架系统的振动响应,得到悬架振动响应随频率的变化曲线。
(2)分析:从实验数据可以看出,悬架振动响应随着频率的增加而逐渐减小,说明悬架系统具有较好的高频振动抑制性能。
4. 悬架性能综合评价根据实验结果,对悬架系统进行综合评价,主要包括以下几个方面:(1)悬架刚度:悬架刚度应适中,以保证车辆在行驶过程中的稳定性和舒适性;(2)悬架阻尼:悬架阻尼应适中,以保证车辆在行驶过程中的平稳性和操控性;(3)悬架振动:悬架振动应较小,以保证车辆在行驶过程中的舒适性。
悬架系统运动校核.doc

第一章悬架系统运动校核第一节概述悬架是现代汽车上的重要的大总成之一,他把车身(或车架)与车轮(或车轴)弹性的连接起来。
它的主要作用是传递作用在车轮和车身(或车架)之间的力和力矩;缓和路面传递给车身(或车架)的冲击载荷。
衰减由此给乘员或货物的震动,提高汽车的平顺性;保证汽车在不平路面上或载荷变化时有良好的运动特性,保证汽车操纵稳定性,使汽车有良好的高速行驶能力。
发动机前置前轮驱动的乘用车(轿车或MPV),常采用麦弗逊式前悬架和拖曳臂或扭力梁后悬架。
发动机中置后轮驱动的微型客车或微型货车,常采用麦弗逊式前悬架,钢板弹簧和整体车桥式后悬架。
第二节悬架运动校核在汽车的行驶过程中,在车辆跳动极限和转向极限范围内,悬架运动件之间不能产生干涉,且保持一定的间隙,以保证汽车行驶的安全性及操纵稳定性。
悬架运动校核术语的定义:1、前悬架上跳极限前悬架上跳极限是指前限位块压缩1/2~2/3时的状态为准。
轿车、小型客车推荐取1/2,SUV推荐取2/3。
2、前悬架下跳极限前悬架下跳极限是指前减震器活塞杆拉出最长长度0~1mm位置时的状态,其中所加的0~1mm为减震器活塞杆固定橡胶块在非悬挂质量作用下向下的变形量。
3、后悬架上跳极限后悬架上跳极限是指后限位块压缩1/2~2/3时的状态为准。
轿车、小型客车推荐取1/2,SUV推荐取2/3。
4、后悬架下跳极限后悬架下跳极限是指后减震器活塞杆拉出最长长度0~2mm位置时的状态,其中所加的0~2mm为减震器活塞杆固定橡胶块在非悬挂质量作用下向下的变形量。
5、左转极限左转极限是指方向盘逆时针旋转至极限位置时,悬架所在位置。
6、右转极限右转极限是指方向盘顺时针旋转至极限位置时,悬架所在位置。
下面已某轿车为例说明悬架运动校核的方法:麦弗逊式前悬架(如图1所示)运动校核主要是分析悬架在上跳左转极限、上跳右转极限、下跳左转极限、下跳右转极限四个状态下,悬架各运动件的干涉情况。
由于悬架与转向均具有对称性,本次对前悬架运动校核,采用左侧悬架校核分析,悬架左转极限和右转极限分别采用各自的最大值。
吊车悬架操作规程标准(3篇)
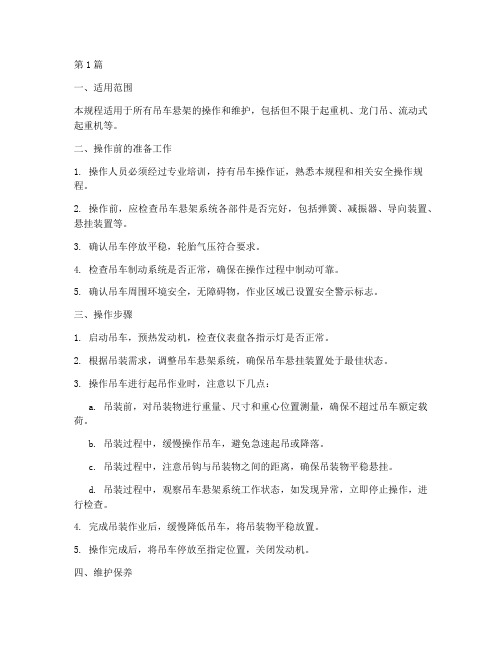
第1篇一、适用范围本规程适用于所有吊车悬架的操作和维护,包括但不限于起重机、龙门吊、流动式起重机等。
二、操作前的准备工作1. 操作人员必须经过专业培训,持有吊车操作证,熟悉本规程和相关安全操作规程。
2. 操作前,应检查吊车悬架系统各部件是否完好,包括弹簧、减振器、导向装置、悬挂装置等。
3. 确认吊车停放平稳,轮胎气压符合要求。
4. 检查吊车制动系统是否正常,确保在操作过程中制动可靠。
5. 确认吊车周围环境安全,无障碍物,作业区域已设置安全警示标志。
三、操作步骤1. 启动吊车,预热发动机,检查仪表盘各指示灯是否正常。
2. 根据吊装需求,调整吊车悬架系统,确保吊车悬挂装置处于最佳状态。
3. 操作吊车进行起吊作业时,注意以下几点:a. 吊装前,对吊装物进行重量、尺寸和重心位置测量,确保不超过吊车额定载荷。
b. 吊装过程中,缓慢操作吊车,避免急速起吊或降落。
c. 吊装过程中,注意吊钩与吊装物之间的距离,确保吊装物平稳悬挂。
d. 吊装过程中,观察吊车悬架系统工作状态,如发现异常,立即停止操作,进行检查。
4. 完成吊装作业后,缓慢降低吊车,将吊装物平稳放置。
5. 操作完成后,将吊车停放至指定位置,关闭发动机。
四、维护保养1. 定期检查悬架系统各部件,包括弹簧、减振器、导向装置、悬挂装置等,确保其完好。
2. 定期检查轮胎气压,确保符合要求。
3. 定期检查制动系统,确保制动可靠。
4. 定期进行润滑保养,包括悬挂装置、导向装置等。
五、安全注意事项1. 操作过程中,严禁超载、超速、急速起吊或降落。
2. 吊装作业时,严禁在吊车下方站人或通行。
3. 操作过程中,如发现异常情况,应立即停止操作,报告相关人员处理。
4. 操作人员应佩戴安全帽、安全带等防护用品。
5. 操作区域应设置安全警示标志,确保作业安全。
六、附则1. 本规程由吊车操作人员严格执行。
2. 本规程的解释权归企业安全管理部门。
3. 本规程自发布之日起实施。
第2篇一、概述为确保吊车悬架系统在操作过程中的安全性和可靠性,特制定本规程。
- 1、下载文档前请自行甄别文档内容的完整性,平台不提供额外的编辑、内容补充、找答案等附加服务。
- 2、"仅部分预览"的文档,不可在线预览部分如存在完整性等问题,可反馈申请退款(可完整预览的文档不适用该条件!)。
- 3、如文档侵犯您的权益,请联系客服反馈,我们会尽快为您处理(人工客服工作时间:9:00-18:30)。
悬架运动校核报告编写规范标准目录1.概述 (1)2.1号标杆车轿车前悬架跳动校核 (1)2.1前悬架运动校核的有关参数 (1)2.2 前悬架跳动包络图 (2)2.3 前悬架包络与轮罩等的间隙校核 (2)2.4 前悬架摆臂与副车架间隙校核 (3)3.1号标杆车轿车后悬架跳动校核 (4)3.1 1号标杆车轿车后悬架跳动量 (4)3.2 1号标杆车轿车后悬架跳动包络图 (4)3.3 1号标杆车轿车后悬架跳动包络与周边间隙 (5)4.前后悬架螺旋弹簧长度校核 (9)5.前、后减振器长度校核 (9)5.1 前减振器校核 (9)5.2 后减振器校核 (10)6.总结 (11)参考文献 (12)1.概述悬架是汽车上的重要总成,在汽车行驶过程中,悬架系统因载荷及路面变化总是处于不断的变化之中,因此在进行总布置设计时,必须对悬架的运动进行校核,防止发生运动干涉。
此校核的目的是确定悬架运动至极限位置时占用的空间(对于前悬架应同时考虑上跳、下跳及转向至极限位置时的情况),从而检查悬架与轮罩、纵梁、副车架等之间的间隙是否足够,同时检查悬架系统内部在变化过程中是否存在干涉现象。
下面分别对1号标杆车轿车前、后悬架跳动情况进行分析,对其空间布置情况进行校核。
2.1号标杆车前悬架跳动校核1号标杆车轿车前悬架为麦弗逊式独立悬架,驱动方式为发动机前横置、前驱动,前轮既是转向轮,又是驱动轮。
因此,在进行前悬架运动校核时,必须同时考虑转向、悬架变形两个方面的综合作用。
2.1前悬架运动校核的有关参数根据前悬架的空间位置及转向器的设计行程(设计行程为152mm),可得1号标杆车轿车的悬架运动包络图。
前悬架的上跳极限按橡胶限位块压缩1/2计算,得出1号标杆车轿车前悬架上跳最大行程38.7mm,即前悬架从满载状态向上最大跳动量;前悬架的下跳极限为前减振器活塞杆拉出最长位置时的状态,得出1号标杆车轿车前悬架下跳最大行程115.4mm,即前悬架从满载状态向下最大跳动量。
2.2 前悬架跳动包络图图1前悬架跳动包络图将前悬架数模导入ADAMS软件中,在悬架各铰接点处添加合适的运动副、弹性元件等连接部件,并输入相关参数,得到如图1所示的分析模型。
2.3 前悬架包络与轮罩等的间隙校核1)前悬架在上极限位置且前轮在左转向极限位置时与轮罩的空间位置关系如图2,此时弹簧托盘与轮罩钣金件内侧之间的最小间隙为11.0mm。
最小间隙图22)前悬架在上极限位置且前轮在左转向极限位置时与防溅垫的空间位置关系如图3,此时弹簧托盘与防溅垫的最小间隙为19.3mm。
最小间图33)前悬架在上极限位置且前轮在右转向极限时与纵梁的空间位置关系如图4,此时吊杆与纵梁钣金之间的最小间隙为15.6mm。
最小间隙图42.4 前悬架摆臂与副车架间隙校核1)前悬架在上极限左转极限位置时摆臂与副车架之间的位置关系如图5,摆臂前端与副车架上部钣金之间的最小间隙为5.3mm;图52)前悬架在下极限右转极限位置时摆臂与副车架之间的位置关系如图6,摆臂后端与副车架上部钣金之间的最小间隙为7.3mm 。
图63)前悬架在下极限右转极限位置时,摆臂与副车架之间的位置关系如图7。
摆臂前端与副车架下板之间的最小间隙为3.8mm 。
图73. 1号标杆车后悬架跳动校核由于后轮不是转向轮,后悬架跳动主要表现为悬架变形引起的悬架跳动。
下面校核后悬架跳动情况。
摆臂前端与副车架上摆臂后端与副车架上部摆臂前端与副车架摆臂后端与副车架3.1 1号标杆车轿车后悬架跳动量根据悬架的匹配及偏频、挠度的相关计算,1号标杆车轿车后悬架动挠度为61.4 mm,即后悬架从满载状态向上的最大跳动量为61.4mm。
3.2 1号标杆车轿车后悬架跳动包络图根据逆向得到的标杆车后悬架关键点数模,在ADAMS软件中建立后悬架运动学分析模型,在后悬架数模各铰接点处添加合适的运动副、弹性元件等连接部件,并输入相关参数,得到如图8所示的分析模型。
图8后悬架分析模型根据后悬架动挠度等参数,通过运动学分析,可以作出后悬架跳动至极限位置时的最大包络体。
3.3 1号标杆车后悬架跳动包络与周边间隙后悬架采用纵臂扭转梁复合式半独立悬架,后悬架在跳动过程中,主要在X方向和Z方向上发生位移。
1)后悬架位于上极限位置时,减振器与车身轮罩最小间隙为12.2mm,如图9。
最小间隙图92)后悬架处于上极限位置时,减振器防尘罩与加油管总成间隙最小,其最小间隙为24.5mm,如图10。
最小间隙图103)后悬架处于上极限位置时,减振器防尘罩与加油管总成间隙最小,其最小间隙为15.7mm,如图11。
最小间隙图114)后悬架处于上极限位置时,后扭转梁与燃油箱护板间隙最小,其最小间隙为14.5mm,如图12。
最小间隙图125)后悬架位于上极限位置时,后扭转梁与燃油箱加油软管间隙最小,其最小间隙为13.3mm ,如图13。
图136)后悬架位于上极限位置时,后扭转梁与燃油箱回气软管间隙最小,其最小间隙为14.5mm ,如图14。
图147)后悬架位于上极限位置时,后扭转梁与主消声器总成间隙最小,其最小间隙为16.7(9.7)mm ,如图15。
图158)后悬架位于上极限位置时,右螺旋弹簧支座与主消声器总成间隙最小,其最小间隙为16.7(23.9)mm ,如图16。
图169)后悬架位于上极限位置时后扭转梁上制动软管固定支架与后地板纵梁间隙最小,其最小间隙为18.2mm ,如图17。
图1710)后悬架位于上极限位置时,后扭转梁与中隔热板间隙最小,其最小间隙为18.3mm ,如图18。
图184. 前后悬架螺旋弹簧长度校核 悬架在运动过程中,必须验证螺旋弹簧在上下极限位置的长度是否满足使用要求,弹簧长度应该满足以下要求:1、 上极限位置时螺旋弹簧应该不能并圈。
2、 下极限位置时螺旋弹簧长度应该小于弹簧自由长度,以防止弹簧脱落 根据CAE 分析的悬架跳动结果可以确定螺旋弹簧的长度,见表1:镖1 螺旋弹簧长度列表最小间隙最小间隙最小间隙最小间隙最小间隙最小间隙悬架下极限长度(mm) 半载长度(mm)上极限长度(mm)并圈长度(mm)自由长度(mm)前悬261 157 106 70 365后悬286 192 107 84 316生并圈;悬架处于下极限位置时,其长度小于自由长度,故弹簧处于被压缩状态,不会脱落。
因此,螺旋弹簧长度符合整车设计要求。
5.前、后减振器长度校核悬架运动过程中必须校核减振器的工作行程,以判断悬架在运动过程中减振器推杆是否顶死。
5.1 前减振器校核a)根据厂家提供前减振器图纸可得前减振器极限尺寸,如图19所示。
图19 前减振器极限尺寸b)前悬架在上极限位置时,前减振器的长度为344.5mm,如图20所示,大于减振器极限最短尺寸,故减振器推杆不会顶死。
图20 上极限位置前减振器长度5.2 后减振器校核a)根据厂家提供后减振器图纸可得减振器极限尺寸,如图21所示;图21 后减振器行程范围b)悬架在上极限位置时,减振器的长度为454.3mm(大于440 mm),故满足后减振器行程要求,如图22所示。
图22 上极限位置后减振器长度6.总结前后悬架在上极限、满载、半载、空载、下极限几种状态下与车身及其相邻件之间的间隙值,见表2:表2 悬架运动间隙校核结果最小间隙悬架状态距离(mm) 样车值(mm)前悬弹簧托盘与轮罩钣金件内侧上极限左转极限11.0 11.1 弹簧托盘与防溅垫内侧上极限左转极限19.3 19.3 悬架(吊杆)与纵梁钣金上极限右转极限15.6 15.8长度最长686mm,最长491mm,最长度架校核摆臂前端与副车架上部钣金上极限左转极限 5.3 5.6 摆臂后端与副车架上部钣金下极限右转极限7.3 7.3 摆臂前端与副车架下部钣金下极限右转极限 3.8 1.5 摆臂后端与副车架下部钣金下极限右转极限7.2 9.2后悬架校核减振器与轮罩上极限12.2 12.2减振器防尘罩与加油管总成上极限24.5 22.7减振器防尘罩与加油管护板上极限15.7 10.0后扭转梁与燃油箱护板(样车无燃油箱护板)上极限14.513.8(与燃油箱最小间隙)后扭转梁与燃油箱加油软管上极限13.3 22.2后扭转梁与燃油箱回气软管上极限14.5 29.6后扭转梁与主消声器总成上极限16.7(9.7)30.1右螺旋簧支座与主消声器总成上极限16.7(23.9)16.2后扭转梁上制动软管固定支架与后地板纵梁上极限18.2 21.1后扭转梁与中隔热板上极限18.3 30.7根据企业标准:1、在前悬架的跳动范围内及转向状态检查减振器、弹簧座与车身轮包、纵梁、等的间隙,间隙值不小于12mm。
2、在前悬架的跳动范围内检查摆臂与副车架的运动间隙,摆臂与副车架不允许有干涉现象。
3、后悬架的跳动范围内检查减振器、弹簧和弹簧座与车身轮包、制动油管等的间隙,间隙值不小于12mm,与加油管的距离不小于6mm。
可以得出结论:悬架在运动过程中不会发生干涉,符合整车设计要求。
7.参考文献1. 汽车工程手册编写组编. 《汽车工程手册》(设计篇). 北京:机械工业出版社,20012. 刘惟信. 《汽车设计》. 北京:清华大学出版社,20022。