设备5why分析表
5WHY_分析法培训(超经典)
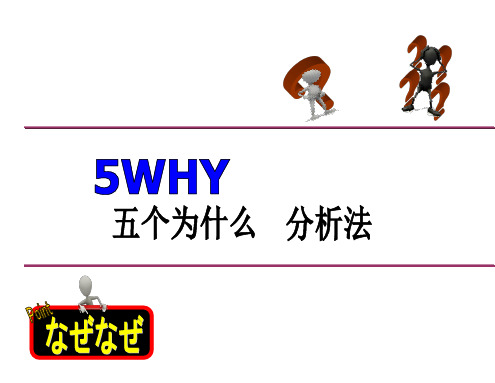
车间每天都有扫不完的油
Why16 为什么没有完整的图纸管理方法,没有人监督技术图纸的更改 — 因为没有人制定制度,也没有人执行监督制度
Why17 为什么没有人制定制度,也没有人执行监督制度 — 因为技术部负责人经常变换
Why18 为什么技术部负责人经常变换 — 因为企业留不住人才
Why19 企业为什么留不住人才 — 因为企业没有很好的管理管理者
Data Analysis Histograms 直方图
Scatter Diagrams
散布图
Control Chart 管制图
Problem Identification
Cause & Effect 鱼骨图
Prioritizations
Pareto 柏拉图
WHY-WHY
5WHY 链式图表
问题
1 – 为什 么?
著名案例2 为什么杰弗逊纪念馆大厦墙壁受腐蚀
(Why1)为什么大厦表面班驳陈旧? 专家发现,冲洗墙壁所用的清洁剂对建筑物有腐蚀作用 ,该大厦墙壁每年被冲洗的次数大大多余其他建筑,腐蚀 自然更加严重。 (Why2)为什么经常清洗呢? 因为大厦被大量的燕粪弄得很脏。 (Why3)为什么会有那么多的燕粪呢? 因为燕子喜欢聚集到这里。
真理诞生于一百个问号之后!
问题解决方法的基本步骤
>>>提取问题 >>>澄清问题 >>>分析问题 >>>查找原因要点 >>>把握问题趋势
>>>识别/确认直接原因 >>>问5个为什么以识别根本原因 >>>问5个为什么以查找为什么问题没有被发现 >>>问5个问什么查找为什么自身体系会允许问题发生
001反省会记录表(5WHY分析表)

问题点
why2
why3
why4
why5
根本原因
对策
更换主轴同步皮带 后,在设置主轴定位 角度过程中发现系统 参数确认按键坏、主 轴不能定位及定位角 度不准确等问题。
检查主轴定位一转信 号接近开关及线路; 正常
主轴不能定位,系统报警9081;无法 正确检测到电机传感器一转信号。
系统参数确认按键坏
5why分析树图展示系统参数确认按键坏更换主轴同步皮带后在设置主轴定位角度过程中发现系统参数确认按键坏主轴不能定位及定位角度不准确等问题
关于加工中心300-501主轴维修问题的5Why分析
时间: 2017 年 9 月 13 日 提出人: 梁广才 单501在加工过程中,主轴同步皮带断裂,周良华等人进行主轴同步皮带更换;更换后在设置主轴定位角度过程中发现系统参数确认按键坏、主轴不能定位及定位角度不准确等问题。 5Why分析树图展示
6M、5Why、鱼骨图分析法等大汇总
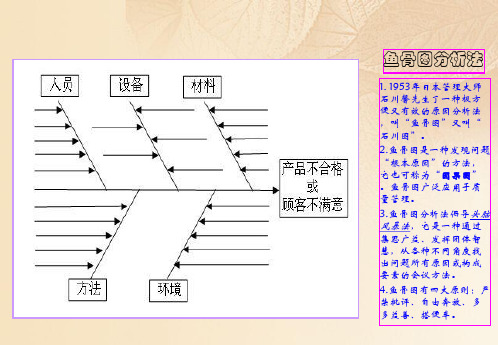
方法 不良过多是为什么
为什么开了 为什打的方法不好 为什么身体倾斜 为什么反手拉设备
枪的打点方法不好 反手拉设备 皮坐椅上有褶皱
打时身体倾斜 区别针开了
中骨【事实】
区别针开了 枪的打点方法不好 打时身体倾斜 反手拉设备 皮坐椅上有褶皱
所以 所以 所以 所以 所以
鱼骨图的三种类型
鱼骨图分析法
整理问题型
放空箱的架子和工程分离
中骨【事实】 放空箱的架子和工程分离 不能放到作业工程内 放空箱架子尺寸大 从工程下来的空箱比较多 需要箱子的组装零件种类多
所以 所以 所以 所以 所以
特性:例3
毛刺流向后工程
没有检查毛刺的时间 作业不适应
训练时间短 竭尽全力完成计划台数
不知道是不良品,所以放任自流
事实 推定 推定 推定 推定
鱼骨图分析方法培训
案例:8、产品开发失败
案例:8、客户流失
(嵌套式鱼骨图)
降低客户流失率是个非常庞大的系统工程。 需要涉及人事、IT、产品、风险、 市场、销售、服务等业务运营的各个层面。 降低流失率首先需要知道的关键问题是:客 户为什么流失?是哪些原因在导致客户流失 ?其中哪些是主要原因,哪些是次要原因? 这些原因之间有没有交互作用?应该怎样改
例2设备放空箱架子尺寸大不能放到作业工程内从工程下来的空箱多放空箱架子尺寸大不能放到作业工程内从工程下来的空箱多放空箱的架子和工程分离中骨事实所以需要箱子组装的零件种类较多x事实推定推定推定推定分离是为什么不能放是为什么大是为什么多是为什么所以所以所以所以放空箱的架子和工程分离不能放到作业工程内放空箱架子尺寸大从工程下来的空箱比较多需要箱子的组装零件种类多流向后工程是为什么毛刺流向后工程特性
提案件数少
5why分析举例
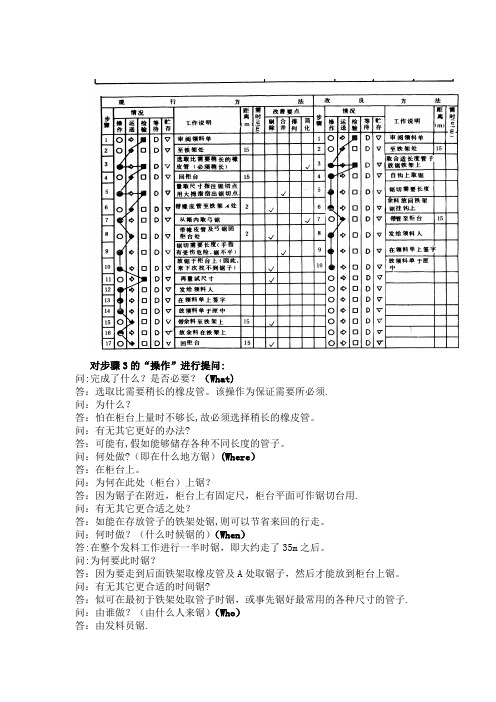
对步骤3的“操作”进行提问:问:完成了什么?是否必要?(What)答:选取比需要稍长的橡皮管。
该操作为保证需要所必须.问:为什么?答:怕在柜台上量时不够长,故必须选择稍长的橡皮管。
问:有无其它更好的办法?答:可能有,假如能够储存各种不同长度的管子。
问:何处做?(即在什么地方锯)(Where)答:在柜台上。
问:为何在此处(柜台)上锯?答:因为锯子在附近,柜台上有固定尺,柜台平面可作锯切台用.问:有无其它更合适之处?答:如能在存放管子的铁架处锯,则可以节省来回的行走。
问:何时做?(什么时候锯的)(When)答:在整个发料工作进行一半时锯,即大约走了35m之后。
问:为何要此时锯?答:因为要走到后面铁架取橡皮管及A处取锯子,然后才能放到柜台上锯。
问:有无其它更合适的时间锯?答:似可在最初于铁架处取管子时锯,或事先锯好最常用的各种尺寸的管子. 问:由谁做?(由什么人来锯)(Who)答:由发料员锯.问:为何要发料员锯?答:仓库没有其他人。
问:有无其他更合适的人锯?答:如果由具有锯切经验的专人来锯可能更好.问:如何做?(他是如何锯的)(How)答:用左手握住管子,以大拇指按住锯切的地方作为锯切点。
问:为何要如此锯?答:因为在锯切的过程中,并无其它专用夹具。
问:有无其它更合适的办法?答:如果使用一个简单的夹具夹住管子,则既可保持平整的锯缝,又不锯伤手指.对步骤5的“检验"进行提问:问:完成了什么?是否必要?(What)答:找出了锯切点,并用拇指按住。
有必要。
问:为什么?答:因为这样可以保证锯出所需的长度。
问:有无其它更好的办法?答:如果仓库存储有所需长度的管子则可取消此动作。
问:何处做?(Where)答:在柜台上做。
问:为何要在此处做?答:因为尺固定在柜台的边缘.问:有无其它更合适的地方?答:有,在最后面的铁架B处。
问:何时做?(When)答:在柜台与铁架间行走约35m后,在A出锯前做。
问:为什么要在那时候?答:因为尺子在柜台上,所以必须将管子携至柜台处后才可做.问:有无其它更合适的时候做?答:有。
5Why分析表(案例)

XX电子有限公司5Why分析表(案例)产品名称A型针车型问题描述针变形分析日期2018.3.9 不良数量55000PCS/180PCS/4PCS 不良率 2.2000% 发生场所进料检验生产批号2018.3.2a.过程工艺、检验、零部件状况追踪检查说明1、是否遵循SOP的工艺条件、作业流程?☐是□否 4、是否使用了经验证合格的零件?☐是□否2、是否使用正确的设备(含条件)及工具?☐是□否 5、技术规范是否符合、验证且培训?☐是□否3、人员是否培训并鉴定?□是☐否6、生产期间的环境状况是否有区别?□是☐否7、运输包装是否符合标准书要求?☐是□否 8、其它,说明:说明:进行5WHY分析时,参与人员应尽量全面,如设计开发、工程(生产技术)、生产、品保、采购、业务、班组长、作业人员;过程中应采取开放式的以事实为原则,并结合采用脑力激荡法等方式进行。
b、根本原因分析(5个为什么):发生原因:第1个为什么?直接原因①为什么会发生电镀变形答:电镀卡槽内卡住撞击变形流出原因:第1个为什么?直接原因①为什么OQC没有管控到答:未尽职责第2个为什么?直接原因②为什么品质监控没有终止不良发生答:已发现不良实行全检,未能追踪第2个为什么?直接原因②为什么全检员工没有管控到答:技术培训不达标第3个为什么?直接原因③为什么电镀之后发现问题不能完全解决答全检过程中QC没能对全检之后的产品进行仔细抽检第3个为什么?直接原因③为什么发现不良没有严格管控答:监督不足第4个为什么?直接原因④为什么决定全检还不能控制不良答:控制不到位,OQC没能管控到第4个为什么?直接原因④为什么新进员工对产品认知不够规范答:经验不足第5个为什么?根本原因⑤为什么QC未跟踪追查不良答:不够细心第5个为什么?根本原因⑤为什么发现问题对策不够彻底答:包装人员不够认真负责c、问题点无法再现,根本原因查找1、现品分析(可采用环境试验、老化验证、模拟试验、客户或供应商场所验证、对手件上试验、实车验证等):机器运行正常,生产模具一次成型下落不会发生变形,电镀之后发现不良变形。
5why分析法案例

5why分析法案例
5why分析法是一种用于根本原因分析的问题解决技术,它通过问“为什么”五次来揭示问题背后的深层原因。
这种方法可以帮助我们超越表面问题,找到并解决真正的问题根源。
下面是一个5why分析法的案例:
在一家制造工厂中,一台机器突然停止工作。
为了找出停止工作的根本原因,团队决定使用5why分析法。
1. 为什么机器停止工作了?
- 因为机器的电源线断了。
2. 为什么电源线断了?
- 因为电源线被机器的移动部件挤压。
3. 为什么电源线会被挤压?
- 因为机器的移动部件没有正确地固定在位。
4. 为什么移动部件没有正确地固定在位?
- 因为固定部件的螺丝松动了。
5. 为什么螺丝会松动?
- 因为机器在运行过程中振动过大,导致螺丝逐渐松动。
通过这一系列的“为什么”,团队发现,虽然电源线断裂是机器停止工作的直接原因,但根本原因在于机器的振动过大,导致固定部件的
螺丝松动。
因此,为了彻底解决问题,团队需要采取措施减少机器的振动,比如加强固定部件的稳定性,或者对机器的移动部件进行定期检查和维护,以确保螺丝不会松动。
通过这个案例,我们可以看到5why分析法如何帮助我们从表面问题深入到根本原因,从而采取有效的措施解决问题。
这种方法不仅适用于制造业,也适用于各种行业和领域的问题解决过程。
故障分析方法与工具(5Why和鱼骨图分析法)
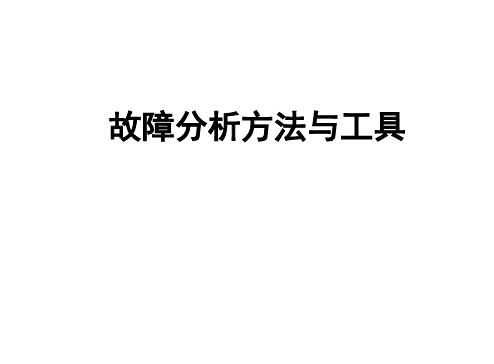
根
因
原因
关
4Why?
系
原因/影响关系
链
5Why?
原因
根本原因
2.5Why问题解决方 式
若问题答案有一个以上的原因,则应找出每个原因的根源。
注意原因的细分:
问题
直接原因 原因 原因
根本原因
直接原因
原因
原因
原因 根本原因
原因 根本原因
3.经典案例(1)
丰田汽车公司前副社长大野耐一先生曾举了一个例子来找出停机的真 正原因。 有一次,大野耐一在生产线上的机器总是停转,虽然修过多 次但仍不见好转。于是,大野耐一与工人进行了以下的问答:
2.鱼骨图类型
整理问题型
各要素与特性值间不存在原因关 系,而是结构构成团系。
原因型
鱼头在右,特性值通常以“ 为什么……”来写。
对策型
鱼头在左,特性值通常以“如 何提高/改善……”来写。
3.鱼骨图分析法步骤
(1)决定问题的特性。 简单说特性就是“工作的结果”。首先,对团队成员讲解目的, 然
后,认清、阐明需要解决的问题,并就此达成一致意见。
故障分析方法与工具
一、5Why分析法
丰田生产方式创始人大野耐一总爱在车 间走来走去,停下来向工人发问。他反复 就一个问题,问“为什么”,直到回答令 他满意,被他问到的人也心里明白为止— —这就是后来著名的“五个为什么”。
5Why分析法简单说就是深度分析法,也被称作 为什么-为什么分析,它是一种诊断性技术,被用来 识别和说明因果关系链。它的根源会引起恰当地定 义问题。
在必须处理以防止再发生的原因处停止,问: 我已经找到问题的根本原因了吗? 我能通过处理这个原因来防止再发生吗? 这个原因能通过以事实为依据的原因/效果关系链与问 题联系起来吗? 这个链通过了“因此”检验了吗? 如果我再问“为什么”会进入另一个问题吗? 确认你已经使用“5个为什么”调查方法来回答这些 问题,问: 为什么我们有了这个问题? 为什么问题会到达顾客处? 为什么我们的系统允许问题发生?
PSG(问题解决小组)5why分析标准表格

P D C A
A P C D
1 2 3 4 5 6 7
A P C D A P C DA P C DA P C D A P C D
A P C D
KPI 数据追踪
PSG
PROBLEM SOLVING GROUP
计划:问题定义,验证原因,确定解决方案(解决方案是什么,什 么时间做,谁来做) 检验:在实施后进行检验,如果问题点不在发生,则说明这个解决 方案是有效的
开始日期 : 机器 : Page 2
解决方案
做:行动执行,解决方案的执行
推行:及时生效执行(约2周内)将解决方案推广的其他区域
日期确认 N° 日期 原因 解决方案 /行动 预计完成时间 实际完成时间
备注
P D C A
A P C D
1
2
A P C D
3
A P C D
4
A P C D
5
A P C D
6
A P C D
7
A P C D
8
A P C D
9
A P C D
长期解决方案
日期确认 N° 日期 原因 解决方案 /行动 预计完成时间 实际完成时间
5why实例讲解

5Why分析法是一种系统地解决问题的方法,通过反复提问,探究问题的根本原因。
下面是一个实例来解释5Why分析法的应用。
假设我们遇到了一个问题:一个工厂的机器总是停机。
我们可以使用5Why分析法来探究根本原因。
1.第一个问题:为什么机器会停机?
回答:因为机器超载,保险丝烧断了。
2.第二个问题:为什么机器会超载?
回答:因为轴承的润滑不足。
3.第三个问题:为什么轴承会润滑不足?
回答:因为润滑泵失灵了。
4.第四个问题:为什么润滑泵会失灵?
回答:因为它的轮轴耗损了。
5.第五个问题:为什么润滑泵的轮轴会耗损?
回答:因为杂质跑到里面去了。
通过5Why分析法,我们找到了问题的根本原因是杂质进入了润滑泵,导致轮轴磨损和润滑泵失灵,进而导致机器超载和保险丝烧断。
为了解决这个问题,我们可以采取措施来防止杂质进入润滑泵,例如在润滑泵上加装滤网。
有效的管理工具之一----5WHY
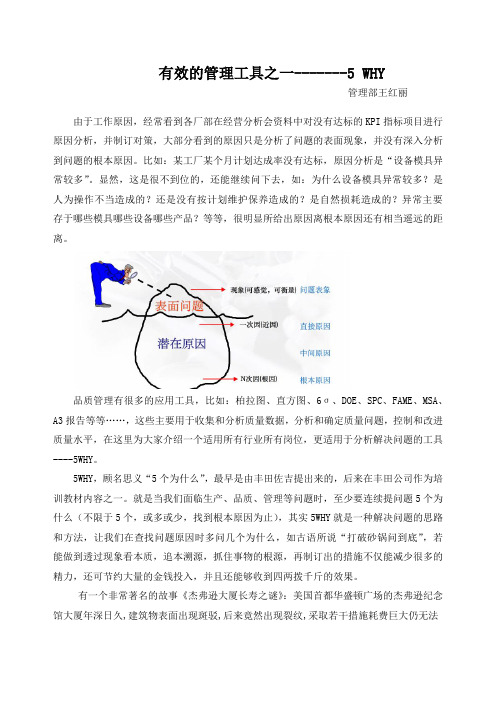
有效的管理工具之一-------5 WHY管理部王红丽由于工作原因,经常看到各厂部在经营分析会资料中对没有达标的KPI指标项目进行原因分析,并制订对策,大部分看到的原因只是分析了问题的表面现象,并没有深入分析到问题的根本原因。
比如:某工厂某个月计划达成率没有达标,原因分析是“设备模具异常较多”。
显然,这是很不到位的,还能继续问下去,如:为什么设备模具异常较多?是人为操作不当造成的?还是没有按计划维护保养造成的?是自然损耗造成的?异常主要存于哪些模具哪些设备哪些产品?等等,很明显所给出原因离根本原因还有相当遥远的距离。
品质管理有很多的应用工具,比如:柏拉图、直方图、6σ、DOE、SPC、FAME、MSA、A3报告等等……,这些主要用于收集和分析质量数据,分析和确定质量问题,控制和改进质量水平,在这里为大家介绍一个适用所有行业所有岗位,更适用于分析解决问题的工具----5WHY。
5WHY,顾名思义“5个为什么”,最早是由丰田佐吉提出来的,后来在丰田公司作为培训教材内容之一。
就是当我们面临生产、品质、管理等问题时,至少要连续提问题5个为什么(不限于5个,或多或少,找到根本原因为止),其实5WHY就是一种解决问题的思路和方法,让我们在查找问题原因时多问几个为什么,如古语所说“打破砂锅问到底”,若能做到透过现象看本质,追本溯源,抓住事物的根源,再制订出的措施不仅能减少很多的精力,还可节约大量的金钱投入,并且还能够收到四两拨千斤的效果。
有一个非常著名的故事《杰弗逊大厦长寿之谜》:美国首都华盛顿广场的杰弗逊纪念馆大厦年深日久,建筑物表面出现斑驳,后来竟然出现裂纹,采取若干措施耗费巨大仍无法遏止。
政府非常担忧,派专家们调查原因,拿出办法。
后来报告交上来写明调查结果:最初以为蚀损建筑物的原因是酸雨。
研究表明,原因是冲洗墙壁所含的清洁剂对建筑物有酸蚀的作用,而该大厦墙壁每日被冲洗,大大频于其他建筑,受酸蚀损害严重。
5W2H分析报告模版-设备故障

标题:立式加工中心主轴故障分析报告发生时间(When):2010.1.1 发生工序(Where):车削发现人(Who):张三设备名称(Which):立式加工中问题描述:(what)1、不能正常启动2、有杂音原因分析:(可参考人/机/料/法/环)五个方面进行分析(Why)人:人员技能不足机:设备年限已久老化法:使用方法有误环:现场温度过低测:测量工具不行临时解决办法: 1)技能问题? 2)制度是否影响人的工作? 3)是选人的问题吗? 4)是培训不够吗? 5)是技能不对口吗? 6)是人员对公司心猿意马吗? 7)有责任人吗? 8)人会操作机器?人适应环境吗?人明白方法吗?人认识料吗?造成的损失、影响程度(How much)1)技能问题? 2)制度是否影响人的工作? 3)是选人的问题吗? 4)是培训不够吗? 5)是技能不对口吗? 6)是人员对公司心猿意马吗? 7)有责任人吗? 8)人会操作机器?人适应环境吗?人明白方法吗?人认识料吗?预防措施(How to)1)技能问题? 2)制度是否影响人的工作? 3)是选人的问题吗? 4)是培训不够吗? 5)是技能不对口吗? 6)是人员对公司心猿意马吗? 7)有责任人吗? 8)人会操作机器?人适应环境吗?人明白方法吗?人认识料吗?5M1E问题分析法-概念a) 人(Man):操作者对质量的认识、技术熟练程度、身体状况等;b) 机器(Machine):机器设备、测量仪器的精度和维护保养状况等;c) 材料(Material):材料的成分、物理性能和化学性能等;d) 方法(Method):这里包括生产工艺、设备选择、操作规程等;e) 环境(Environment):工作地的温度、湿度、照明和清洁条件等;f) 测量(Measurement):主要指测量时采取的方法是否标准、正确;5M1E问题分析法—应用举例一.人的分析: 1)技能问题? 2)制度是否影响人的工作? 3)是选人的问题吗? 4)是培训不够吗? 5)是技能不对口吗? 6)是人员对公司心猿意马吗? 7)有责任人吗? 8)人会操作机器?人适应环境吗?人明白方法吗?人认识料吗?二.机器的分析 1)设备选型对吗? 2)保养问题吗? 3)给机器的配套对应吗? 4)作机器的人对吗?机器的操作方法对吗?机器放的环境适应吗?三.材料的分析1)材料规格对么 2)材料材质对么? 3)材料是否有缺陷?4)用的符合规范吗?四.法的分析: 1:是按法做的吗? 2:看的明白吗? 3:写的明白吗? 4:法适合吗? 5:有法吗? 6:方法是给对应的人吗?方法在这个环境下行吗?五.环的分析: 1)在时间轴上环境变了吗? 2)光线、温度、湿度、污染度考虑了吗? 3)环境是安全的吗? 4)生产环境。
8D根本原因分析之5WHY与鱼骨图完整版
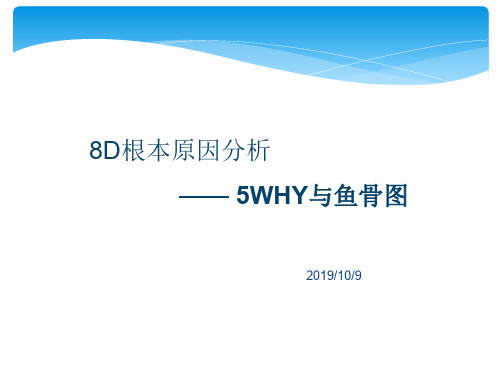
直接原因 原因 原因 根本原因
直接原因
原因
原因
原因 根本原因
原因 根本原因
2.4 推导的同时进行验证
异常的发生
为什么? (原因/后果 关系)
CCCC
直接原因
为什么? (原因/后果 关系)
CCC C
为什么? 原因x
(原因/后果 关系)
CCC
原因xx
为什么? (原因/后果 关系)
CCC
原因xxx
为什么? (原因/后果 关系)
5WHY分析法的运用①
5WHY分析法的运用②
异常现象 为什么?
(原因/效果关系)
直接原因 为什么?
真正的解决问题 必须找出问题的 根本原因,而不 是问题本身,根 本原因总是隐藏 在问题的背后。
(原因/效果关系)
原因 为什么?
(原因/效果关系)
原因 为什么?
(原因/效果关系)
为什么?
真正 原因
根本原因
大野耐一总是爱在车间走来走去,停下来向工人发问。他反复地就一个问题, 问“为什么”,直到回答令他满意,被他问到的人也心里明白为止——这就是 后来著名的“五个为什么”。
千万别忽视第一步 5问法的关键所在为:鼓励解决问题的人要努力避开主观或自负的假设和逻辑陷 阱,从结果着手,沿着因果关系链条,顺藤摸瓜,穿越不同的抽象层面,直至 找出原有问题的根本原因.
昨晚深夜2点才睡着
为什么昨天失眠呢?
昨天下午喝了咖啡
3.1 案例1:迟到
对策:换个时间如何?换种饮料如何?
3.2 案例2:为什么杰弗逊纪念馆大厦墙壁受腐蚀
美国华盛顿广场的杰弗逊纪念馆大厦,1943年建立,之后因年 久失修,表面斑驳陈旧,政府非常担心,派专家调查原因。
5Y分析表

JY-8.5.2-01 A0 问题陈述:关键设备-No.15 全自动折弯机设备手册规定维护保养 规定,自动润滑器过滤器每年更换,对所有油缸主轴每半年进行检 查,不能提供实施维护检查活动的证据
1Y:为什么关键设备-No.15 全自动折弯机未按照设备手册规定维 护保养?
因为关键设备No.15 全自动折弯机的《设备检修计划》中未有对 过滤器每年更换,对所有油缸主轴每半年进行检查的相关要求 2Y:为什么《设备检修计划》中没有对No.15 全自动折弯机过滤 器每年更换,对所有油缸主轴每半年进行检查的相关要求?
因为《设备检修计划》只是按照设备常用易损、安全部位作检修 3Y:为什么《设备检修计划》只是按照设备常用易损、安全部位 作检修?
因为对《设备检修计划》无相关管理规定?
根本原因:《设备控制程序》中《设备检修计划》依据作管理要 求
How(对策): 1.资源科重新评审、修订和发布《设备控制程序》,并将依照设 备手册中检修、维护要求增加入《设备控制程序》中 2.按照设备手册重新评审、确认公司内所有设备的维修计划,并 对按照设备手册要求修订设备维修计划; 3.组织资源科设备检修人员、生产科设备操作人员对修订后的《 设备控制程序》、《设备检修计划》进行培训。
对策结果确认: 2014年6月23日由技术科郝静、张鹏现场抽查CNC-WS-10-2R-1弯管 机设备维修计划,未发现重复现象。 责任人:单连强 确认日期:2014.6.23
5why分析法详细范本

《出货检查指导书》文件编写 时,未对功能检测进行充分的 规定
为什么?
工程部、质量部对标准 8.2.4理解不深刻,培训不 到位
为什么?
无 为什么?
无
为什么?
根本原因
无 为什么?
1)QC检验时,对《出货检查 指导书》要求向电镀厂索取检 测报告、并对客户验货报告进 行跟进的规定不熟悉 2)对QC进行《出货检查指导 A 书》的培训不到位
为什么? 使用该路径分析为什么管理体系会允许该问题发生?
为什么?无为什么? Nhomakorabea无
为什么?
无
为什么?
无
为什么?
总结:经分析,此不符合项发生的根本的原因是: 1)QC检验时,对《出货检查书》要求向电镀厂索取检测报告、并对客户验货报告进行跟进的规定不熟悉 2)对QC进行《出货检查书》的培训不到位 3)《出货检查书》文件编写时,未对功能检测进行充分具体的规定 4)工程部、质量部对标准8.6理解不深刻,培训不到位
为什么?
无
无 C
根本原因
商和客户提供的检测报告 QC检验时,对《出货检查指导
进行确认
书》要求向电镀厂索取检测报
为什么?
告、并对客户验货报告进行跟 进的规定不熟悉
为什么?
对QC进行《出货检查指导书 》的培训不到位
为什么?
为什么?
使用该路径分析为什么该问题没有被检测到?
《出货检查指导书》中未 明确规定:当不能进行功 能检测时,应向供应商索 取检测报告或向客户确认 出货的情况进行跟踪,并 对进行确认
1)《出货检查指导书》文件编 写时,未对功能检测进行充分 的规定 2)工程部、质量部对标准8.6 理解不深刻,培训不到位 B
无
5why分析法案例

5why分析法案例5W法是什么?5W法也被称为"5Why法",是一种通过反复追问为什么的方法,用于深入分析问题的根本原因。
它被广泛应用于质量管理、安全管理、故障分析和工作流程改进等领域。
本文将列举一个关于生产线停工的案例,并使用5Why法进行分析。
案例描述:某工厂的生产线经常发生停工现象,导致产品交付延迟和产品质量问题。
该工厂的管理团队希望通过5Why法找出根本原因,并制定相应的解决方案。
第一为什么 (Why 1):为什么生产线会停工?回答: 因为设备故障。
第二为什么 (Why 2):为什么设备会发生故障?回答: 因为没有进行定期维护。
第三为什么 (Why 3):为什么没有进行定期维护?回答: 因为维护人员不足。
第四为什么 (Why 4):为什么会出现维护人员不足的情况?回答: 因为没有足够的维护预算。
第五为什么 (Why 5):为什么没有足够的维护预算?回答: 因为管理团队没有意识到维护的重要性,把预算用于其他方面。
通过以上的5Why分析可以得出以下结论:生产线停工的根本原因是管理团队没有意识到维护的重要性,并且将维护预算用于其他方面。
解决这个问题需要管理团队重视维护工作,并为其提供足够的预算,以确保设备能够进行定期维护。
此外,还需要加强维护人员的培训和管理,以确保他们有能力和资源来执行维护工作。
解决方案:1. 建立维护意识: 管理团队应当认识到维护工作对生产线运作的重要性,并将其纳入管理指标中。
2. 调整预算分配: 管理团队应当为维护工作划拨足够的预算,确保维护人员能够有条件地进行定期维护。
3. 加强维护人员培训: 管理团队应当提供维护人员所需的培训和技能提升机会,以提高他们的执行能力。
4. 设备监控和维护计划: 建立设备监控系统,及时发现设备故障,并制定详细的维护计划,以确保设备的长期稳定运行。
总结:通过5Why分析,我们可以了解到生产线停工的根本原因,并提出相应的解决方案。
5Y分析表

对策结果确认: 2014年6月23日由技术科郝静、张鹏现场抽查CNC-WS-人:单连强 确认日期:2014.6.23
因为《设备检修计划》只是按照设备常用易损、安全部位作检修 3Y:为什么《设备检修计划》只是按照设备常用易损、安全部位 作检修?
因为对《设备检修计划》依据无相关管理规定 4Y:为什么对《设备检修计划》依据无相关管理规定?
根本原因:《设备控制程序》中《设备检修计划》依据作管理要 求
How(对策): 1.资源科重新评审、修订和发布《设备控制程序》,并将依照设 备手册中检修、维护要求增加入《设备控制程序》中 2.按照设备手册重新评审、确认公司内所有设备的维修计划,并 对按照设备手册要求修订设备维修计划; 3.组织资源科设备检修人员、生产科设备操作人员对修订后的《 设备控制程序》、《设备检修计划》进行培训。
5Y分析表
JY-8.5.2-01 A0 问题陈述:关键设备-No.15 全自动折弯机设备手册规定维护保养 规定,自动润滑器过滤器每年更换,对所有油缸主轴每半年进行检 查,不能提供实施维护检查活动的证据
1Y:为什么关键设备-No.15 全自动折弯机未按照设备手册规定维 护保养?
因为关键设备No.15 全自动折弯机的《设备检修计划》中未有对 过滤器每年更换,对所有油缸主轴每半年进行检查的相关要求 2Y:为什么《设备检修计划》中没有对No.15 全自动折弯机过滤 器每年更换,对所有油缸主轴每半年进行检查的相关要求?