5WHY分析报告模板-改进版
5w报告范文

5w报告范⽂5w报告范⽂5w报告范⽂ 篇⼀:报告5W写法 报告:5W写法 when:什么时间发⽣的事情 where:在什么地点发⽣的事情 why:为什么发⽣,主要阐述事情发⽣的原因。
Who:由谁负责 How:怎样来处理 Result:结果 报告内容应包括:某个事情,在什么时间发⽣,发⽣地点,发⽣原因,由谁负责。
同时要提出解决办法,并把处理结果描述出来。
篇⼆:5W分析法 ⼀种根本系统解决问题的办法——5W分析法 5W分析法 —— 连问五次为什么?丰⽥汽车公司前副社长⼤野耐⼀曾举了⼀个例⼦来找出停机的真正原因。
有⼀次,⼤野耐⼀在⽣产线上的机器总是停转,虽然修过多次但仍不见好转。
于是,⼤野耐⼀与⼯⼈进⾏了以下的问答: 问“为什么机器停了”答“因为超过了负荷,保险丝就断了。
” 问“为什么超负荷呢”答“因为轴承的润滑不够。
” 问“为什么润滑不够” 答“因为润滑泵吸不上油来。
” 问“为什么吸不上油来”答“因为油泵轴磨损、松动了。
” 问“为什么磨损了呢”再答“因为没有安装过滤器,混进了铁屑等杂质。
” 经过连续五次不停地问“为什么”,才找到问题的真正原因和解决的⽅法,在油泵轴上安装过滤器。
如果我们没有这种追根究底的精神来发掘问题,我们很可能只是换根保险丝草草了事,真正的问题还是没有解决。
车间地上有⼀滩油----------------------为什么?把它清理掉 因为机器漏油--------------------------为什么? 因为垫圈劣化了------------------------为什么?换垫圈 因为所购的垫圈原料为次品-------- -----为什么?买更好的垫圈 因为它的价码不错----------------------为什么?改变采购政策,因为采购⼈员的绩效是依其与正常价格的节余⽽定 其实由于我们视⽽不见,缺乏改善意识,或未能刨根问底,错失了许多改善的机会,以⾄问题越解决越多,同样的问题接⽽连三的发⽣,我们整天疲于奔命,四处救⽕。
(完整版)5WHY分析报告
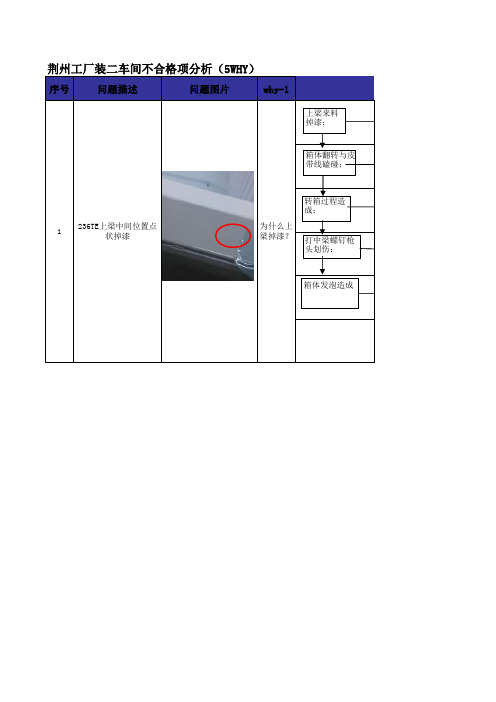
序号问题描述问题图片why-1荆州工厂装二车间不合格项分析(5WHY)
1236TE上梁中间位置点
状掉漆
为什么上
梁掉漆?
上梁来料
掉漆;
箱体翻转与皮
带线磕碰;
转箱过程造
成;
打中梁螺钉枪
头划伤;
箱体发泡造成
why-2
为什么掉漆位置相同?
分析
对上梁来料进行检查,挑选20个,无掉漆现象;(假因)
在箱胆拼装岗位进行工程观察,观察30台箱体,无上梁掉漆现象;(假因)
在转箱岗位进行工程观察,观察30台箱体,无上梁掉漆现象;(假因)
对中梁固定螺钉岗位进行工程观察,观察20台箱体,无上梁掉漆现象;(假因)
对出箱口的箱体进行观察,上梁掉漆位置均距离箱体左侧板230mm ,且型号为236TE 电脑冰箱;(真因)
分析why-3分析why-4
经过对掉漆箱体模具号进行检查,均为I线1#模具所生产为什么1#模
具上梁掉
漆?
1#模具为新式涨模,胎具
与上梁接触位置未用铁氟
龙进行防护,且有毛刺
整改措施责任人完成时
间
整改效果
验证
1、临时措施:对毛刺进行打磨后用铁
氟龙进行防护;2、根治措施:新模具
批产前必须由厂家对模具进行全面防
护后才能验收;
肖莎莎 3.21。
5WHY分析报告

5WHY分析报告标题:5WHY分析报告——解决问题的有效途径引言:在日常生活和工作中,我们常常会遇到各种问题和困难。
为了能够解决这些问题,提高工作效率和生活质量,人们提出了许多问题解决的方法和工具。
其中,5WHY分析方法作为一种简单而有效的工具,广泛应用于问题解决和质量改进领域。
本文将详细介绍5WHY分析的原理和应用,并通过案例分析说明其实践价值。
一、5WHY分析的原理1.1 5WHY分析的定义5WHY分析是一种追问问题根本原因的方法。
通过连续提出“为什么”问题,直至找到问题的真正原因,从而采取相应的措施来解决问题。
1.2 5WHY分析的核心思想5WHY分析的核心思想是“追根溯源”。
它认为导致问题发生的原因很少是一个单一因素,更多的是由多个因素相互作用所致。
通过逐步追问问题的根本原因,可以准确找到问题的发生原因,从而针对性地采取措施。
二、5WHY分析的应用2.1 5WHY分析在工作中的应用在工作中,5WHY分析可以用于解决各种问题,如生产线出现故障、客户投诉、项目延期等。
通过深入追问,可以确定问题出现的真正原因,并采取相应的措施来进行改进。
例如,当生产线出现故障时,通过进行5WHY分析,可以发现故障原因是由于设备维护不当,进而制定完善的设备维护计划,以提高生产效率。
2.2 5WHY分析在个人生活中的应用除了在工作中,5WHY分析也可以应用于个人生活的问题解决中。
例如,当我们感到疲倦和精神不振时,通过进行5WHY分析,可能发现原因是由于缺乏充足的睡眠。
进而,制定合理的作息时间表,改善睡眠质量,提高个人生活质量。
三、5WHY分析的案例分析3.1 案例一:生产线故障某公司的生产线经常出现故障,导致生产进度延误。
通过5WHY分析,工程师们发现故障的根本原因是设备维护不当。
随后,他们制定了规范的设备维护计划,并加强员工培训,最终解决了生产线故障问题。
3.2 案例二:客户投诉某餐厅连续几天接到客户投诉,称所提供的食物口感不佳。
事故调查改善报告-5-why分析法
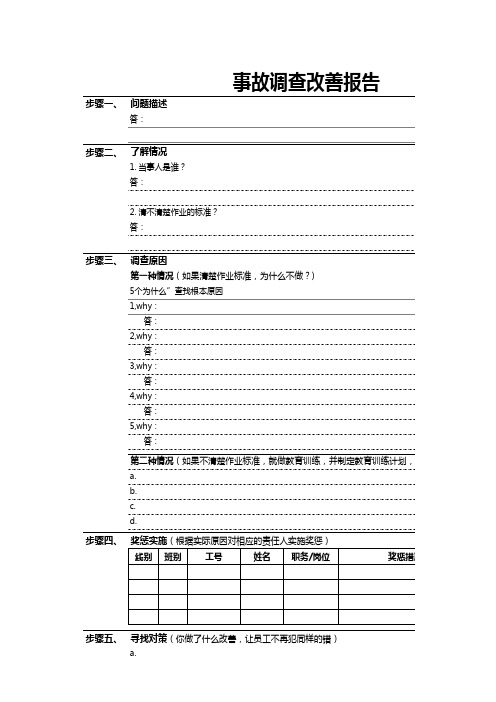
报告者: 年 月
_ 日
告
育训练计划,让其清楚标准)
奖惩措施
备注
者: 年 月
_ 日
事故调查改善报告
步骤一、 问题描述
答:
步骤二、 了解情况
1. 当事人是谁? 答: 2. 清不清楚作业的标准? 答:
步骤三、 调查原因
第一种情况(如果清楚作业标准,为什么不做?)
5个为什么”查找根本原因 1,why: 答: 2,why: 答: 3,why: 答: 4,why: 答: 5,why: 答:
第二种情况(如果不清楚作业标准,就做教育训练,并制定教育训练计划,让其清楚标准)
a. b. c. d.
步骤四、 奖惩实施(根据实际原因对相应的责任人实施奖惩)
线别 班别 工号 姓名 职务/岗位 奖惩措施
备
步骤五、 寻找对策(你做了什么改善,让员工不再犯同样的错)
善,让员工不再犯同样的错)
5 Why 标准模板
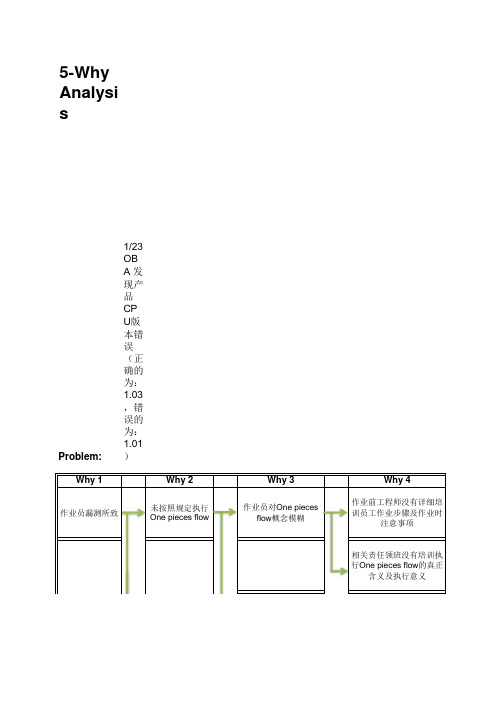
5-Why AnalysisProblem:1/23 OBA 发现产品CPU版本错误(正确的为:1.03,错误的为:1.01)Why 1Why 2Why 3Why 4作业员漏测所致未按照规定执行One pieces flow作业员对One piecesflow概念模糊作业前工程师没有详细培训员工作业步骤及作业时注意事项相关责任领班没有培训执行One pieces flow的真正含义及执行意义产品积压过多,导致升级OK产品与没有升级的产品混在了一起.临时接到客户通知,升级F/W。
工程师要求off lineupdate F/W(测试OK,待包装状态的产品)TCN中没有明确作业流程PE未提供测试流程的TCNPE认为TE的TCN中已经对流程作出说明;TE认为作业流程需要PE提供;PD没有检查确认包装站别产品上传时没有发现版本错误产品上传时,只要求对比ATIS&CSM是否一致TE W/I中没有要求检查确认软件版本信息的内容Why 5Root Cause Recurrence Prevention Status工程师认为作业步骤简单,无需在做更加详尽的培训工程师的自我假定,导致同作业员的交流不充分。
相关部门工程师制订的TCN,备注或培训时,着重强调作业步骤及作业时的注意事项。
Owner:TomClose我们高估作业员的理解能力,认为全部掌握,无需解释执行的意义我们的自我意识,没有同作业员做更加详尽的交流。
班会或培训时,我们要站在作业员的角度去理解问题;并适时的提问,让作业员真正理解培训内容。
Owner:TomClose出货紧急,作业员偏向了产量,而未对品质要求上面注意作业分配上面不充足,先期策划没有做好。
制定计划,协调资源,实施《重工排配表》。
做好先期准备工作,明确分工后方可开始作业。
Owner:TomCloseTE的TCN中只是阐述了测试步骤,没有作业流程;我们认为TE已经提供TCN,PE无需再作提供部门之间缺乏交流,没有明确责任分工。
5Why报告

与其它产品同时喷涂作业
检验员工作不认真
生产现场有自然风流动
岑南松
改善作业场所,试喷5-10PCS 试油墨。
A
15.7.23
分析系统的 根本原因
订单号 G20150702-21011
客户名称
迈科
客户地点 珠海
作业场所没有防尘保护
供应商(如需要)
艾美
制造地点 东莞长安
现其它的产品同时喷涂作业 检验人员不够了解客户标准
系统变更实施 责任人/日期
遏制计划实施 责任人/日期
预防类似问题产生的日期(如需要)
小组成员:
岑南松 曹坤 王小叶 邱树钊 胡杰 李后林 蓝文艳
问题解决时间 2015.7.23
问题处理过程记录
与顾客联系解决问题 责任人/日期
开始进行问题解决 责任人/日期
过程变更实施 责任人/日期
检验员误判
再培训检验员的ห้องสมุดไป่ตู้验手法增强
了解客户标准。对检验员的工
B
作进行奖惩制度
检验员工作不认真
改善作业场所自然风不得流动,
喷涂作业时不得同时多人作业,
C
严格要求检验员了解客户标准。
问题描述
水印不良
分析为什么 会发生这样 的问题
零件名称
H21上盖
作业场所有灰尘
分析为什么 没有发现这 样的问题
不够了解客要求标准
5-Why 分析表
零件编号
编号: AM20150722-001
问题发生时间
15.7.19
问题处理时间
15.7.22
制单号: 0001
纠正措施及责任人
日期
油墨没有虑好 检验员不够熟练
5WHY分析报告样本

5WHY分析报告样本1. 背景本次5WHY分析旨在深入挖掘导致某产品生产过程中出现质量问题的根本原因。
通过该分析,我们希望能够找出问题的源头,并采取针对性的措施以提高产品质量和生产效率。
2. 问题描述在某次产品生产过程中,发现有20%的产品存在质量问题,影响了生产进度和产品质量。
问题主要表现为产品尺寸不准确,偏差超过允许范围。
3. 问题分解3.1 为什么会出现尺寸偏差?•原因1:生产线上的机器磨损严重,导致加工精度降低。
•原因2:原料质量不稳定,造成产品尺寸的不准确。
3.2 为什么机器磨损严重?•原因1:缺乏定期的机器维护和检修。
•原因2:机器使用频率过高,超出其承受范围。
3.3 为什么原料质量不稳定?•原因1:供应商提供的原料质量参差不齐。
•原因2:原料的储存和处理过程不符合要求,导致质量下降。
3.4 为什么缺乏维护和检修?•原因1:公司对设备维护和检修的重视程度不够。
•原因2:缺乏专业的维护和检修团队。
3.5 为什么机器使用频率过高?•原因1:生产计划不合理,导致机器长时间连续运行。
•原因2:缺乏对生产过程的实时监控和调度。
4. 根本原因分析通过上述问题分解,我们可以发现,导致产品尺寸偏差的根本原因为:公司对设备维护和检修的重视程度不够,缺乏定期的机器维护和检修;以及生产计划不合理,导致机器长时间连续运行。
5. 改进措施针对上述根本原因,我们提出以下改进措施:1.增加对设备维护和检修的投入,定期对机器进行维护和检修,提高加工精度。
2.对供应商进行严格筛选,确保提供的原料质量稳定。
3.优化生产计划,合理安排机器运行时间,避免长时间连续运行。
4.建立实时监控和调度系统,对生产过程进行有效管理。
6. 总结通过本次5WHY分析,我们深入挖掘了导致产品尺寸偏差的根本原因,并提出了相应的改进措施。
希望通过实施这些措施,提高产品质量和生产效率,减少类似问题的发生。
7. 后续行动计划为确保改进措施的有效实施,特制定以下行动计划:7.1 设备维护和检修•短期目标:在接下来的一个月内,完成对所有关键设备的维护和检修工作。
完整5个why报告模板
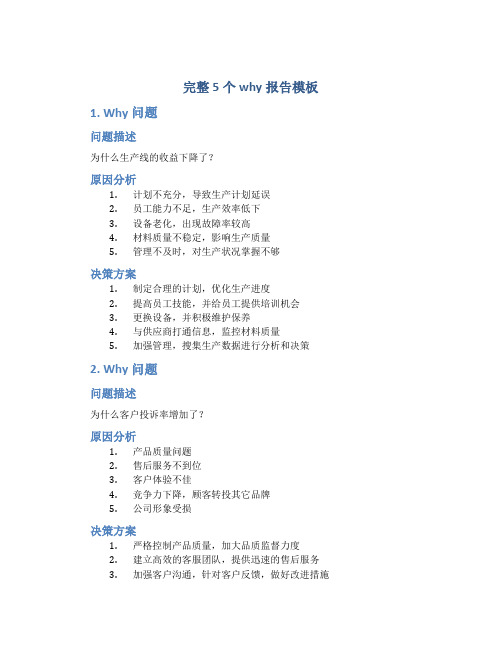
完整5个why报告模板1. Why 问题问题描述为什么生产线的收益下降了?原因分析1.计划不充分,导致生产计划延误2.员工能力不足,生产效率低下3.设备老化,出现故障率较高4.材料质量不稳定,影响生产质量5.管理不及时,对生产状况掌握不够决策方案1.制定合理的计划,优化生产进度2.提高员工技能,并给员工提供培训机会3.更换设备,并积极维护保养4.与供应商打通信息,监控材料质量5.加强管理,搜集生产数据进行分析和决策2. Why 问题问题描述为什么客户投诉率增加了?原因分析1.产品质量问题2.售后服务不到位3.客户体验不佳4.竞争力下降,顾客转投其它品牌5.公司形象受损决策方案1.严格控制产品质量,加大品质监督力度2.建立高效的客服团队,提供迅速的售后服务3.加强客户沟通,针对客户反馈,做好改进措施4.提升品牌竞争力,争取更多的目标客户5.多参加社交活动,提高公司知名度3. Why 问题问题描述为什么销售目标没完成?原因分析1.销售团队精神不振,效率低下2.销售方式陈旧,无法适应市场变化3.产品价格过高,相比同行竞争劣势明显4.营销宣传不充分,潜在客户数量少5.经销商计划不合理,市场策略不明确决策方案1.提高销售员士气,组建激励机制2.推广新型销售方式,积极开展网络营销3.调整产品价格策略,提高市场竞争力4.加大广告宣传,拓宽潜在客户量5.与经销商密切合作,确定目标市场和营销策略4. Why 问题问题描述为什么员工流失率越来越高?原因分析1.薪资福利待遇不公平2.工作强度过大,工作环境恶劣3.晋升空间不足,员工无职业发展前景4.公司管理理念不合理,员工无归属感5.团队合作氛围不浓厚,个人荣誉感不足决策方案1.公平地制定薪资福利待遇体系,确保员工得到公正对待2.参照国际先进标准,改善工作环境,减轻工作强度3.制定员工晋升计划和职业规划,鼓励员工自我发展4.推行以人为本的公司管理理念,增强员工归属感5.强化团队合作,加强团队文化建设,提高企业凝聚力5. Why 问题问题描述为什么客户转化率日趋低?原因分析1.目标客户定位不准确2.营销活动策划不合理,无法引起客户兴趣3.价格策略不合理,客户不能承受高昂的价格4.销售流程复杂,让客户流失5.客户反馈问题未及时跟进处理决策方案1.精准定位目标客户,针对性制定营销策略2.设计优秀的营销活动,注重宣传传播,吸引客户3.制定针对性的价格策略,满足客户需求4.简洁明了的销售流程,留下良好的印象5.高效处理客户反馈问题,及时回复和解决客户问题。
- 1、下载文档前请自行甄别文档内容的完整性,平台不提供额外的编辑、内容补充、找答案等附加服务。
- 2、"仅部分预览"的文档,不可在线预览部分如存在完整性等问题,可反馈申请退款(可完整预览的文档不适用该条件!)。
- 3、如文档侵犯您的权益,请联系客服反馈,我们会尽快为您处理(人工客服工作时间:9:00-18:30)。
不适合内容在库品处理方案:
拉杆配装后,
1.工序步聚表
2.5WHY 分析序号12
重新设计冲棒
打导角的冲棒外径偏大
1
禁止二次回牙
端面导角圆直径过大,
超出上限
内牙纹端面2-3个牙磨损
严重
攻牙时排铁屑不顺畅
打导角的冲棒直径设计
不合理——
该批次产品实施了2次回
牙
拉杆组装后,MA寸法NG 组装后,拉杆拧入螺母
部分过深
先前为镀镍,改为镀锌
而实施了退镀,酸洗时
选成牙损伤
————端面倒角角度过小
3月25日
内牙纹磨损,导致小径偏大原因分析
改善对策
改善对策
修正冲棒设计图纸,将冲棒直径由¢11.0修改为¢10.5修正冲棒设计图纸,将冲棒角度由100°修改为 110°。
备注
改善确认担当部门安拓完成日期3月25日进料——冷打成型——攻牙——电镀——外观检查——包装——出货
不适合现象
根本原因再发防止对策
设计不合理
重新设计冲棒
冲棒未实施寿命管理
产品在冷打成型时,打
导角的冲棒磨损
对冲棒实施寿命管
理
品番
品名
发生日期2月1日拉杆螺母
MB80-13-C1251A
全数选别
序号试作品量产品
1WHY
2WHY
3WHY
4WHY
5WHY 安拓
已完成
5WHY分析报告书
SMC
已完成不良
信
息
不良分类
现品区分寸法
性能
外观
形状
他(
)
善。