三工位正负压成型工艺流程说明
负压真空铸造操作规程(3篇)
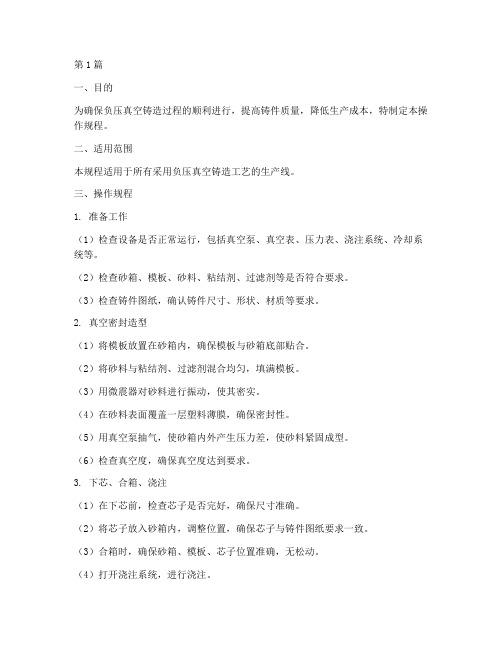
第1篇一、目的为确保负压真空铸造过程的顺利进行,提高铸件质量,降低生产成本,特制定本操作规程。
二、适用范围本规程适用于所有采用负压真空铸造工艺的生产线。
三、操作规程1. 准备工作(1)检查设备是否正常运行,包括真空泵、真空表、压力表、浇注系统、冷却系统等。
(2)检查砂箱、模板、砂料、粘结剂、过滤剂等是否符合要求。
(3)检查铸件图纸,确认铸件尺寸、形状、材质等要求。
2. 真空密封造型(1)将模板放置在砂箱内,确保模板与砂箱底部贴合。
(2)将砂料与粘结剂、过滤剂混合均匀,填满模板。
(3)用微震器对砂料进行振动,使其密实。
(4)在砂料表面覆盖一层塑料薄膜,确保密封性。
(5)用真空泵抽气,使砂箱内外产生压力差,使砂料紧固成型。
(6)检查真空度,确保真空度达到要求。
3. 下芯、合箱、浇注(1)在下芯前,检查芯子是否完好,确保尺寸准确。
(2)将芯子放入砂箱内,调整位置,确保芯子与铸件图纸要求一致。
(3)合箱时,确保砂箱、模板、芯子位置准确,无松动。
(4)打开浇注系统,进行浇注。
4. 真空浇注(1)在浇注过程中,保持真空度稳定。
(2)观察浇注过程,确保浇注正常进行。
(3)浇注结束后,关闭浇注系统。
5. 冷却、脱模(1)铸件凝固后,进行冷却。
(2)冷却至室温后,停止真空泵抽气。
(3)解除模板内的真空,进行脱模。
6. 铸件清理(1)检查铸件表面质量,去除毛刺、飞边等。
(2)检查铸件内部质量,确保无气孔、砂眼等缺陷。
(3)对铸件进行喷丸、抛丸等表面处理。
7. 检验(1)对铸件进行尺寸、形状、材质等检验。
(2)确认铸件符合要求后,进行包装、入库。
四、注意事项1. 操作人员应熟悉设备性能和操作规程,确保操作正确。
2. 操作过程中,注意观察设备运行状态,发现异常情况及时处理。
3. 真空泵、真空表、压力表等设备应定期检查、校准,确保其准确可靠。
4. 砂箱、模板、砂料、粘结剂、过滤剂等应符合要求,确保铸件质量。
5. 操作过程中,注意安全,防止意外伤害。
三工位正负压成型工艺流程说明
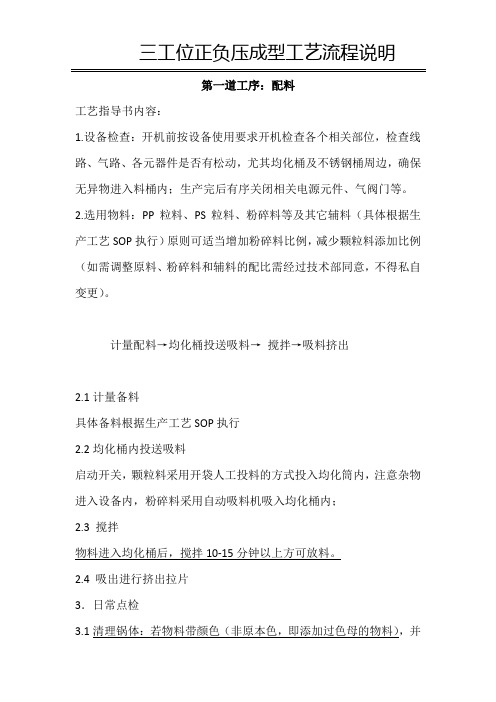
第一道工序:配料工艺指导书内容:1.设备检查:开机前按设备使用要求开机检查各个相关部位,检查线路、气路、各元器件是否有松动,尤其均化桶及不锈钢桶周边,确保无异物进入料桶内;生产完后有序关闭相关电源元件、气阀门等。
2.选用物料:PP粒料、PS粒料、粉碎料等及其它辅料(具体根据生产工艺SOP执行)原则可适当增加粉碎料比例,减少颗粒料添加比例(如需调整原料、粉碎料和辅料的配比需经过技术部同意,不得私自变更)。
计量配料→均化桶投送吸料→搅拌→吸料挤出2.1计量备料具体备料根据生产工艺SOP执行2.2均化桶内投送吸料启动开关,颗粒料采用开袋人工投料的方式投入均化筒内,注意杂物进入设备内,粉碎料采用自动吸料机吸入均化桶内;2.3 搅拌物料进入均化桶后,搅拌10-15分钟以上方可放料。
2.4 吸出进行挤出拉片3.日常点检3.1清理锅体:若物料带颜色(非原本色,即添加过色母的物料),并与下批次生产用物料颜色不同,应关闭机组和均化筒,及时清理残留物料;3.2生产时应注意检查物料颜色,当选择的物料与需求存在色差或夹杂色,应及时停止生产,调整后方可开机;3.3粉碎回收料工位注意料色回收的一致性,回收满袋后及时将吨袋封口,入库做好吨袋标识登记卡。
第二道工序:挤出压片挤出:物料通过挤出机料筒和螺杆间的作用,边受热塑化,边被螺杆向前推送,连续通过机头而制成各种截面制品或半制品的一种加工方法。
工艺指导书内容:1.设备检查:开机前按设备使用要求开机检查各个相关部位,检查线路、气路、各元器件是否有松动;生产完后有序关闭相关电源开关、气和水路阀门。
2.适用物料:PP粒料,PS粒料和边角料等。
3.工艺流程加热→输送吸料→喂料→设置工艺参数→出料→三辊压片→牵引→收卷→检测尺寸4.生产工艺要求4.1加热4.1.1打开电柜合上电源控制总闸,打开操作频点击加热启动;4.1.2预热时设定各区加热温度为220℃,加热时间一般约为2-3小时左右,当各区加热温度达到设定数值后,可继续恒温30分钟,同时确认各区段温控仪表和电磁阀工作状态。
压铸工艺及操作规程(3篇)

第1篇一、压铸工艺概述压铸是一种将金属熔体在高压下注入到铸模中,冷却凝固后得到所需的铸件的金属成型方法。
压铸工艺具有生产效率高、尺寸精度好、表面光洁度高等优点,广泛应用于汽车、家电、电子等行业。
二、压铸工艺流程1. 铝合金熔炼:将铝锭或铝合金锭放入熔炼炉中,通过加热熔化成铝液。
2. 模具准备:根据产品图纸制作或选用合适的模具,并对模具进行预热。
3. 铝液准备:将熔化的铝液过滤、除气、去除杂质,使其达到压铸要求。
4. 压射成型:将铝液注入到预热的模具中,在高压下使铝液充满模具型腔。
5. 冷却凝固:铝液在模具中冷却凝固,形成铸件。
6. 取件:将铸件从模具中取出。
7. 清理:对铸件进行去毛刺、抛光等表面处理。
8. 检验:对铸件进行尺寸、表面质量、机械性能等检验。
三、压铸操作规程1. 安全操作:操作者必须穿戴好劳保用品,如工作服、手套、眼镜等,确保人身安全。
2. 设备检查:开机前,检查设备是否正常运行,如油压、冷却系统、控制系统等。
3. 模具准备:根据产品图纸制作或选用合适的模具,并对模具进行预热。
4. 铝液准备:将熔化的铝液过滤、除气、去除杂质,使其达到压铸要求。
5. 压射成型:将铝液注入到预热的模具中,在高压下使铝液充满模具型腔。
6. 冷却凝固:铝液在模具中冷却凝固,形成铸件。
7. 取件:将铸件从模具中取出。
8. 清理:对铸件进行去毛刺、抛光等表面处理。
9. 检验:对铸件进行尺寸、表面质量、机械性能等检验。
10. 设备维护:定期对设备进行保养、检修,确保设备正常运行。
四、注意事项1. 铝液温度:铝液温度应控制在合适的范围内,过高或过低都会影响铸件质量。
2. 压射压力:压射压力应根据产品材质、厚度等因素进行调整,确保铸件成型质量。
3. 模具预热:模具预热温度应控制在合适的范围内,过高或过低都会影响铸件质量。
4. 铝液过滤:铝液过滤可有效去除杂质,提高铸件质量。
5. 模具维护:定期对模具进行检查、清洗、维护,确保模具使用寿命。
三工位正负压一体机操作说明书

三工位正负压一体机操作说明书三工位正负压一体机是一种用于医院、实验室等场合的设备,它可以同时实现正压、负压和平衡压力三种模式的切换。
该设备的操作说明书如下:一、产品概述三工位正负压一体机是一种能够快速调整空气压力的设备,可广泛应用于医院病房、ICU、实验室等场合。
该设备具有多种工作模式,包括正压、负压和平衡压力等,以满足不同的使用需求。
二、操作步骤1. 设备连接:将三工位正负压一体机接通电源并连接到所需的空气处理系统中。
2. 切换模式:按下设备面板上的切换按钮,选择需要的正压、负压或平衡压力模式,并按照设备要求进行调整。
3. 调整参数:根据需要调整设备的相关参数,如风量、温度、湿度等,以确保设备正常运转。
4. 开始运行:按下设备面板上的启动按钮,开始运行设备。
在运行过程中,应注意观察设备的运行情况,并及时调整参数以保证压力稳定。
5. 结束运行:在设备使用完毕后,按下面板上的停止按钮,使设备停止运行,并根据设备要求进行清理和维护。
三、注意事项1. 在使用三工位正负压一体机之前,请先仔细阅读使用说明书,并对设备进行检查和测试,确保设备处于良好状态。
2. 在操作过程中,应遵循设备的安全规范和操作流程,并严格按照设备要求进行参数调整和操作。
3. 在设备运行过程中,应注意观察设备的运行情况,并及时调整参数以确保设备的稳定性和安全性。
4. 在使用完毕后,应及时清理设备,并进行必要的维护和保养,以延长设备的使用寿命。
总之,三工位正负压一体机是一种重要的医疗设备,使用时需严格遵守相关规范和操作流程。
希望以上操作说明书能够为您提供帮助并指导您正确地使用该设备。
三工位母线加工机安全操作规程(2篇)
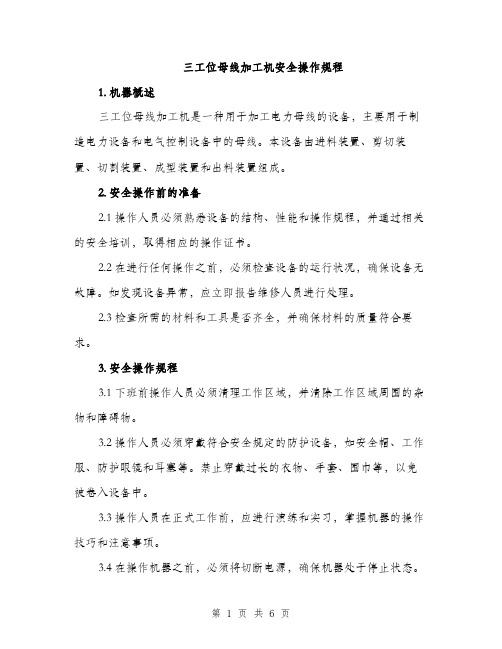
三工位母线加工机安全操作规程1. 机器概述三工位母线加工机是一种用于加工电力母线的设备,主要用于制造电力设备和电气控制设备中的母线。
本设备由进料装置、剪切装置、切割装置、成型装置和出料装置组成。
2. 安全操作前的准备2.1 操作人员必须熟悉设备的结构、性能和操作规程,并通过相关的安全培训,取得相应的操作证书。
2.2 在进行任何操作之前,必须检查设备的运行状况,确保设备无故障。
如发现设备异常,应立即报告维修人员进行处理。
2.3 检查所需的材料和工具是否齐全,并确保材料的质量符合要求。
3. 安全操作规程3.1 下班前操作人员必须清理工作区域,并清除工作区域周围的杂物和障碍物。
3.2 操作人员必须穿戴符合安全规定的防护设备,如安全帽、工作服、防护眼镜和耳塞等。
禁止穿戴过长的衣物、手套、围巾等,以免被卷入设备中。
3.3 操作人员在正式工作前,应进行演练和实习,掌握机器的操作技巧和注意事项。
3.4 在操作机器之前,必须将切断电源,确保机器处于停止状态。
3.5 严禁在设备运行时进行任何拆卸、维修或调整等操作。
3.6 操作人员必须按照操作规程中的要求进行操作,严禁超负荷操作或强行启动设备。
3.7 在进行设备加工时,应保持专注,严禁操作人员离开工作岗位或做其他事情干扰注意力。
3.8 在操作过程中,要注意观察设备的运行情况,如发现异常或异常声音,应立即停机并报告维修人员进行处理。
3.9 在设备操作过程中,禁止随意触碰或翻动设备上的受电部分,以免触电。
3.10 操作完成后,必须切断电源,清理设备上的杂物和残留物,保持设备的整洁。
4. 紧急情况处理4.1 在发生紧急情况时,操作人员必须立即停止设备运行,并按指定的逃生路线撤离现场,确保人身安全。
4.2 在设备发生故障或异常时,操作人员必须立即停止设备运行,并按照故障处理程序中的要求进行处理。
5. 安全检查与维护5.1 在设备日常运行中,应定期进行安全检查,并按照安全检查表进行记录。
成型工艺流程及条件介绍中英文对照

成型工艺流程及条件介绍Molding technique procedure and parameter introduction第一節成型工艺Section 1 molding technique.1.成型工艺参数类型Sorts of molding parameter.(1). 注塑参数Injection parameter.a.注射量Injection rate.b.计量行程Screw back positionc.余料量Cushiond.防诞量Sucking back ratee.螺杆转速Screw speedf.塑化量Plastic0 rateg.预塑背压Screw back pressureh.注射压力和保压压力Injection pressure and holding pressurei.注射速度Injection speed(2)合模参数Clamping parametera.合模力Clamping forceb.合模速度Clamping speedc.合模行程.Clamping stroked.开模力Opening forcee.开模速度Opening speedf.开模行程Opening positiong.顶出压力Ejector advance pressureh.顶出速度Ejector advance speedi.顶出行程Ejector advance position2.温控参数Temperature parametera.烘料温度Dry resin material temperatureb.料向与喷嘴温度Cylinder temperature and nozzle temperaturec.模具温度Mold temperatured.油温Oil temperature3.成型周期Molding cyclea.循环周期Cycle timeb.冷却时间Cool timec.注射时间Injection timed.保压时间Holding pressure timee.塑化时间Plant timef.顶出及停留时间Knocking out and delay timeg.低压保护时间Mold protect time成型工艺参数的设定须根据产品的不同设置.Molding technique parameter setting differs depending on type of product第二节成型条件设定Section 2 Molding parameter Setting按成型步骤:可分为开锁模,加热,射出,顶出四个过程.Molding steps: mold opening/closing, heating injection and knocking out.开锁模条件:Mold opening parameter:快速段中速度低压高压速度High-speedmid-speedLow pressure high pressure speed锁模条件设定:Mold closing parameter setting1锁模一般分: 快速→中速→低压→高压Mold closing: high-speed →low-speed →low pressure→high pressure2.快锁模一般按模具情况分,如果是平面二板模具,快速锁模段可用较快速度,甚至于用到特快,当用到一般快速时,速度设到55-75%,完全平面模可设定到80-90%,如果用到特快就只能设定在45-55%,压力则可设定于50-75%,位置段视产品的深浅(或长短)不同,一般是开模宽度的1/3.In high-speed section, Mold closing speed depends on type of mold. For two –pla te mold it can set quick and even especially quick usually, it set speed within 55-75%. For full-plate mold it set speed within80-90% while using especially high sp eed it set speed within 45-55% and pressure within 50-75% position distance setti ng differs depending on the volume of product and usually it can be set 1/3 of m old opening position.3.中速段,在快速段结束后即转换成中速,中速的位置一般是到模板(包括三板模,二板模)合在一块为止,具体长度应视模板板间隔,速度一般设置在30%-50%间,压力则是2 0%-45%间.In mid-speed section: Mold closing speed changes into mid-speed after high-speed section finish. Mid-speed start position is where two plates meet (include three-plat e mold and two-plate mold ) Distance of mid-speed is up to distance of two plate s plate it speed within 30-50% and pressure 20-45%.4.低压设定,低速设定一般是在模板接触的一瞬间,具体位置就设在机台显示屏显示的一瞬间的数字为准,这个数字一般是以这点为标准,,即于此点则起不了高压,高于此点则大,轻易起高压.设定的速度一般是15%-25%,视乎不同机种而定,压力一般设定于1-2%,有些机则可设于5-15%,也是视乎不同机种不同.Low-pressure section: Mold closing sets low-pressure when plates meeting. This po sition is set to the data of machine screen on this time. This point is the gage of the data. Data lower the point there is no high-pressure. Data higher the point th ere is high-pressure easily. It set speed within 15-25% and pressure within 1-2% d epending on type within 1-2% depending on type of injection molding machine. 5.高压设定,按一般机台而言,高压位置机台在出厂时都已作了设定,相对来讲,是不可以随便更改的,比如震雄机在50P.速度相对低压略高,大约在30-35%左右,而压力则视乎模具而定,可在55-85%中取,比如完全平面之新模,模具排气良好,甚至于设在55%即可,如果是滑块较多,原来生产时毛边也较多,甚至于可设在90%还略显不足.High-pressure section: To normal injection molding machine, high-pressure position had been set before they were sent to customer. It can not be modified. For exa mple high-pressure position of CHENHSONG machine is 50P.The speed of high-pr essure section is about 30-35% and higher than that of low-pressure. The pressure is up to mold, it can set within 55-85% For full-plate mold, it’s eject air well, it can set pressure 55% .If mold has a lot of slides and flash rate high in producti on, pressure can set 90%.加热工艺条件设定Heating technique parameter setting1.加热段温度设定必须按照产品所使用的原料的不同而不同,但却必须遵循一个这样的规则,即由射口筒到进科段温度是逐步递减的.且递减温度是以10.度为单位.The proper temperature setting differs depending on type of resin material, but it must be abide by a rule that temperature setting should diminish in step 10.C fr om nozzle to feeding resin material position.2特殊情况下.如料头抽丝,则射口筒温度应降低,如果是比较特殊的原料冷凝比较快的.则射口筒温度则不止比第二节法兰温度高10度.比如PPS. 尼龙等.Nozzle temperature setting should low if product line. If resin material such as PP S, PA, cool very soon , Nozzle temperature should higher more 10.C than the sec ond cylinder temperature.3.机台马达启动温度视乎机台不同而不同,一般出于对机台油路中的油封保护需要,油温最好能控制在40度-60度,以免油封长期高压而变化,缩短使用寿命,造成成型不稳定.Pump turning on temperature is different depending on type of injection molding machine. To protect oil seal of machine it set oil temperature within 40.C-60.C, Ifoil seal work on condition that high pressure and damaged It’s work time will be shorter, it can cause molding stable.第三节注射及熔胶(加料)工艺条件设定Injection and plastic Technique parameter setting一.注射Injection第四节常见塑料原料的有关温度值.原料Resin名称Name熔点℃Melt’s成型温度℃Molding Temperature(’c)分解温度℃Decomposing Temperature(‘C)模具温度℃Mold Temperature(‘c)干燥温度℃Resin dry temperature(‘c)注射是把塑料原料经加热后射进模腔的过程,它一般可分为第一级,第二级,第三级,第四级及保压几段:Injection is a step which inject melt resin material into mold. It consists of stepl,s tep2 ,step3,step4 and holding pressure step:1.第一级注射一般是注射料头段.具注射量一般可根据料头的轻重来估计其行程,当然也可以依据公式来计算,如公式:Step l injects usually tunnel material, Injection V olume can be estimated accordingto the weight of course it can be calculated by formula:L=Si=Vi/0.785Ds2L:注射行程; Si: 注射行程;L: injection stroke Si: injection strokeVi:理论注射容积; Ds:螺杆直径;Vi: injection volume of theoretical Ds: diameter of screw0.785:是Ω/4的值.0. 785: value of Ω/4.当然,如果我们在成型时每设定一个参数都要计算一次,要成型出一个产品就要几个小时才能完成了.But it cost a lot of time to produce one product if every time molding parameter is setting by calculation.2.第二级是注塑产品约2/3的阶段,当然,根据产品特殊需要,也允许成型不到2/3阶段,比如避免结合线问题,这一阶段的成型速度及压力一般是整个成型段的最大值段,如果排的产品与机台基本是相吻合的.模具结构合理,排气良好,这一段的压力一般也不会超过80%.速度侧视产品需变,可能大到95%也可,自然一般都是在55%-80%间. Step 2 inject 2/3 of product. It can lower 2/3 of product according to requirement of product. For example to prevent weld line. Molding speed and pressure on thi s step is the maximum of whole molding section. If Mold suit the injection moldi ng machine and mold structure reasonable and eject air well, pressure of this step should lower 80%. Molding speed setting within 55-80% but it may setting 95% for especial product.3.第三段是注射余下的1/3段,其速度和压力根据产品的需要,一般是小于第二段,速度和压力存在于一个往下降的过程.主要是为了防止产品毛边的产生,但同时又必须把产品充填饱满.Step3 inject remain 1/3 of product. According to product molding speed and press ure lower than that of step2 To prevent flash speed and pressure should decrease but it can’t shot short.4.第四段:一般有机台还有第五,第六段,这段的成型速度和压力相同前,都存在两段一个递减过程.其作用都是起到一个再次充满的作用.Step4 section: Some injection machines have step5,step6 which are same as former molding speed and pressure this step should diminish and inject once more.5.保压段:不论成型什么产品,都存在一个保压过程.任何产品都不同程度的存在一个厚薄不一的问题,正常情况下,较厚的部分都可能存在一个收缩凹陷的现象,为了解决这种现象,就应应用到保压,保压一般来讲都应用较慢的射速,而压力的设置则应看缩水的情况如何,小到25%,大到80%都有可能.Holding pressure step: No matter what product there is a holding pressure step. A ny product can’t molding a same thickness. Usually the deeper section may sink mark . To prevent this defect it should set holding pressure, The injection speed o f holding pressure step is slow but holding pressure setting within 25-80% dependi ng on sink mark.二.熔胶段工艺Plastic Technique1.再复杂的熔胶旋转过程最多不会超过三段,因为熔胶本身就是存在于把胶熔进料筒的过程,如果原料粘度大,熔胶压力则大,但速度则应取决于原料的分解温度,熔胶速度越快,原料中的剪切力则会越大,料管温度则越高,局部原料产生分解的可能性则会越大,故一般熔胶会采用中速为宜,如45%-75%,熔胶同时会碰到一个比较重要的环节,那就是背压的使用,产品精度要求越大,背压的使用则更大,背压可使原料分子间结构更紧密,成型出的产品则尺寸更稳定,外观越好.当然,背压太大,则会产生流涎,所以背压的使用又应考虙到其它原因.Plastic should lower 3 steps, because plastic is a step to add melt resin material t o cyclinder , Higher stick of resin material ,higher screw back pressure. Screw sp eed differs depending on decomposing temperature of resin material ,Higher screw speed ,Higher trim force of resin, higher cyclinder temperature. Some resin mater ial may decomposes so it set screw speed in mid-speed such as 45-75%, In plasti c step setting screw back pressure is very important, Higher screw back pressure , higher quality of product screw back pressure make resin structure order, Molding product is beautiful and volume stable. But ,it maybe flow if screw back pressure too high . So all factors should be considered when using screw back pressure.2.熔胶过程还有一个比较重要的环节,那就是松退,松退分前松退和后松退,其作用一般是为了防止流涎和抽丝,设定值速度和压力都在20%-50%间,设定的行程一般在2-5cm间,太长的行程可能会使料筒里面贮存空气,导致下一模出现不期望的气泡.In plastic step sucking back is very important too. Sucking back include front suc king back and back sucking back It setting sucking back to prevent flow and line. It sets sucking back speed and pressure within 20-50% and distance within 2-5c m. TOO long distance make cyclinder reserve air and cause bubble at next moldin g.顶出的工艺设定knocking out technique setting产品经冷却定型后则有一个开模的过程,开模基本上是合模的反过程.开模的未段则有一个慢速设置,开模完成后,产品必须顶出的过程.There is a mold opening step after product cooling taking shape. Mold opening is a reverse step of mold closing. The last step of mold opening speed set slow. Pr oduct should be knocked out after mold opened.一.顶前:Knocking out顶前最好分两个阶级,第一阶可分为中压慢速,即是把产品轻轻顶出一部分,然后是中压中速顶,中压中速一般指的是35%-55%,而低速则有可能低到5%,这需视产品不同而言,顶出行程设定是顶出长度稍比产品垂直深度大1-2cm即可.Knocking out includes two steps, Step1 section setting mid-speed, knocks product out partly step2 section setting mid-pressure and mid-speed . Depending on differe nt product, mid-pressure and mid-speed sets within 35-55% but low-speed can set 5%. Distance of knocking out longer 1-2cm than the vertical thickness of product.二.退针Back顶退包括两个过程与顶落的过程基本一致,顶退的终点应预留1-3cm的空间,以保护顶针油管不被顶坏.The same as knocking out, ejector back includes 2 steps. To protect the ejector oi l jar, it should make a 1-3mm distance in the ending point of ejector back.三.顶针方式还包括一个多次顶,单次顶及顶针停留的选择,机械手取产品,脱模顺利的情况都采取多项,为了顶针油缸寿命的延长,多次顶就以不超过三次为宜,顶针停留一般用在顶针带着产品退回有可能对增品产生损伤的模具,同时为配合机械手使用,有时也需要较短的顶针停留.The way of knocking out includes knocking out once, Knocking out repeat and ej ector delay. Take product by manipulator or take product easy, it should select kn ocking out once. To longer the work time of ejector oiljar, times of knocking out lower 3 times. Ejector delay used when product will be damaged if ejector back or suit manipulator.成型时间的设定Molding time setting在保证产品质量的前提下,周期时间是越短越好,周期时间又包括如下几项:射胶时间,保压时间,熔胶时间,冷却时间,顶出时间,锁模低压时间,甚至乎关系到时间因素的还有还开模与锁模,及顶出的快慢.Cycle time should shorter on condition that product quality well. Cycle time inclu des: injection time , holding pressure time, plastic time, cure time, knocking out ti me and mold protect time. Even mold opening closing sopeed and knocking out s peed affect cycle.1. 射胶时间包含保压时间,一般看起来,射胶时间越长,产品越饱和,但我们在讲求质量时,同时也须考虑产能,更何况,射胶时间过长,有可能会造成产品过于饱满而寻致粘模顶的变形呎寸偏大等一系列问题,故我们在设置射胶时间时应综合考虑,尽量在合乎质量要求时缩短射胶时间.Injection time consists holding pressure time. Longer injection time, fuller product, we should consider production quantity when we suit for quality. If injection tim e too long, it may cause a series of defects suck as flash strain. So all sorts of f actors should be considered, injection time should be shout if quality suit for requ irement.2. 熔胶时间的长短取决于熔胶速度设定的快慢,背压设定的大小,但有一点,熔胶时间控制的长短一定要比冷却时间短.Plastic time depends on plastic speed and screw back pressure, but plastic time m ust shorter than cure time.3. 冷却时间:冷却时间的长短直接影响到成型的周期,冷却时间越长,成型时间就越长,造成产能就越低,故我们在设定高压冷却时间时,只要能保证到产品成型顺利,不会直接影响到变形等问题,设定的时间也是越短越好.Cure time: Cure time affects molding cycle. Longer cure time, longer molding cyc le, lower production quantity. So it sets cure time short on condition that product molding succed and can’t deformation..4. 在大量使用机械手的塑胶公司,我们的顶出时间一般是与机械手配合为宜,全自动使用机械手时顶出停留时间一般保持1.5-2秒,半自动生产,如因顶针退回会导致产品掉落或卡紧,而取不下产品,停留时间则应保持5秒左右.In PCE company, for using manipulator in abundence , knocking out time suits m anipulator, Knocking out delay keeps 1.5-2 second when using manipulator full-ma nipulator, knocking out delay keeps about 5 second when using manipulator semi-manipulator and product will fall or can’t be taken off if ejector back.5. 低压保护时间对保护我们人身安全,模具安全起很大作用,配合好模具低压位置和低压压力的调整,低压保护的时间应取1-3秒,保护时间越短,可能造成的危害则越小. Low-pressure protect is very important for safety and protect mold, Mold protect t ime should adjust within 1-3 second suit low pressure and position of mold protect, shorter protect time, make damaged.。
三维印刷成型的基本流程

三维印刷成型的基本流程视频演讲稿本次课主要讲解,三维印刷成型的基本流程。
教学目标就是:通过这次课的学习,让你初步了解三维印刷成型的基本流程所有激光3D打印技术都有4个主要的步骤,三维印刷成型自然也不例外:首先要有一个三维模型,而且要把模型转换为快速成型通用的“STL”格式。
然后利用专业的成型软件把三维模型分成多个二维的轮廓薄片,通俗地说就是分层。
接着把已经分层的三维模型调入到成型机,从下往上一层层进行堆积打印,最后对打印出来的实物进行一定的后处理,就可以得到我们需要的产品。
基本流程就是这样。
接下来我们看第一个问题:如何得到三维模型?首先可以通过PRO/E、UG等三维设计软件,设计出三维模型。
比如这个鼠标模型,就是通过PRO/E三维软件,直接设计出来的。
还可以通过逆向工程,反求出三维模型。
比如可以通过这个光学三维扫描仪上面的摄像头,直接扫描下面这个实物,经过数拼接得到三维模型。
通过刚才的讲解,相信你对三维模型的获取已经有了初步的认识。
接下来,第二个问题:也是这次课的重点:如何将模型进行分层,分层以后又如何进行堆积打印?刚才已经提到,我们可以利用专业的成型软件把三维模型,比如这个圆柱按照一定的方向分成多个二维的薄片。
分层是一种离散的过程,计算非常复杂。
但好在我们有计算机,只需轻轻一按,软件就会自动地分层,无需我们操心。
分层以后,成型机就可以把二维薄片从下往上一层一层地进行堆积打印,最终形成一个三维的零件实体。
那么,“三维印刷”成型机又是如何进行打印的呢?这个问题是我们这次课的重中之重。
这是一台基于3DP技术的开源3D打印机。
我们以它为例,来看看“三维印刷”成型机是如何工作的?这就是刚才提到的那台3D打印机,这是利用这台打印机打印出来的各种模型。
首先,要进行装粉,装好以后,利用铺粉辊把粉末铺平并压实。
然后,喷头在计算机控制下,按照成型数据,有选择地喷射粘结剂建造层面。
然后继续送粉、铺粉和喷射粘结剂,如此周而复始地送粉、铺粉和喷射粘结剂,最终完成一个三维粉体的粘结。
一步法三工位注拉吹成型技术

一步法三工位注拉吹塑料中空成型技术一步法注拉吹塑料中空成型是当今世界先进的拉伸制瓶工艺技术,采用高压高速注射瓶坯、对瓶坯进行轴向拉伸和双向吹塑拉伸、冷却定型等工艺技术。
注射、拉伸、吹塑工序在一台设备上依次完成,即“一步法”制瓶工艺。
塑料瓶经拉伸后透明度、表面刚度、抗冲击性、阻气透性等综合机械性能得到了较大提高,生产效率高,制品内在质量及尺寸精度容易得到保证。
1、一步法注拉吹工艺设备简介一步法注拉吹工艺设备的主机是注拉吹塑料中空成型机及其注拉吹模具,主要由注射装置、升降转位装置、拉伸吹塑装置、脱模装置、液压系统、气路系统、电控系统、微机自动控制系统、机架、安全罩、注射瓶坯模、拉伸吹塑成型模等部分组成,集成了注拉吹专用控制电脑、变频控制器、电液比例控制系统、热流道模具等一些先进工艺装备。
一步法注拉吹设备的辅机主要有塑料除湿干燥机、空气压缩机、空气除湿机、模具冷却机等,是集“机、电、液、气、微机”的一体化高端技术装备,本项目创新性地综合运用了P ID 温控技术、变频技术、微机自动控制技术、热流道模具技术等一些先进的技术,与国内目前普遍使用的挤吹机、注吹机、注拉吹二步法设备相比,在自动化程度、成品率、节约能耗、减少废料等多方面都具有明显的技术优势。
适于生产带瓶颈、精度高、透明度好、无毒、对内容物保存效果好的高档塑料瓶,广泛用于加工医药、保健品、食品、化妆品及化工等行业的PET、PEN、PP 、PC 等高档包装瓶。
2、设备及技术特点2.1 三工位包括注射瓶坯工位、拉伸吹塑工位、脱模工位,参见图1 。
2.2 一步法工艺瓶坯注射成型、瓶坯拉伸、瓶子吹塑成型等工序在该机上依次完成。
2.3 变频与电液比例复合调速技术的应用变频与电液比例复合调速专利技术应用于注拉吹制瓶工艺在国际上尚属首次,并取得了很大实效,较以往采用变量泵供油、双泵供油或双联泵组供油具有很多优势。
主要体现在小流量高压工况时:(1 )双泵供油时,因为各工况之间的流量变化时间都在3 s 以内,而泵由零转速启动到额定转速的时间在3 s 左右,所以该机在高压小流量时不能停掉大泵,只能全流量供油、卸荷阀卸荷,造成能耗。
多工位级进模的排样设计

2.2.4双边载体排样
双边载体排样是在产品条料的两侧分别留出一定宽度的 材料,并在适当位置与产品两边相连接,实现对产品条料的 送进,它比单边载体排样送进更顺利,料带定位精度更高, 适合产品两端都有接口可连,特别适合送进强度较弱的薄板 料。但是,相对材料利用率较低,且通常需要采用双边导正。 图2-7所示为双边载体排样,共有16个工位,其中 (1)~(4) 工位为冲裁; (5)~(14) 工位为弯曲;(15) 工 位将制件从条料上分离;(16) 工位为将废料切断,这一步 根据实际情况而定,如果有自动收料装置时,可不设计。
2.2 多工位级进模排样的类型
多工位级进模排样中的搭边作用特殊,通常称为载体。载 体是运送坯件的物体,载体与坯件或坯件与坯件的连接部分称 搭口。载体的主要作用是将坯件传递到各工位进行各种冲裁和 成形加工。因此,要求载体能够在带料的动态送进中,使坯件 保持送进稳定、定位准确,才能顺利地加工出合格制件。根据 载体形式的不同将级进模排样分为无载体排样、边料载体排样、 单载体排样、双边载体排样、中心载体排样5种类型。
⑩ 当级进成形工位数不是很多,制件的精度要求较高 时,可采用压回条料的技术,即将凸模切入料厚的后,模 具中的机构将被切制件反向压人条料内,再送到下一工位 加工,但不能将制件完全脱离带料后再压入。 ⑩ 在级进冲压过程中,各工位分段切除余料后,形成 完整的外形,此时一个重要的问题是如何使各段冲裁的连 接部位平直或圆滑,以免出现毛刺、错位、尖角等。因此 应考虑分断切除时的搭接方法。搭接方法如图2-1所示,图 2-1(a)为搭接,第一次冲出A、B两区,第二次冲出C区,搭 接区是冲载C区凸模的扩大部分,搭接量应大于0.5倍的材 料厚。图2-1(b)为平接,除了必须如此排样时,应尽量避 免使用此搭接方法。平接时在平接附近要设置导正销,如 果工件允许,第二次冲裁宽度应适当增加一些,凸模要修 出微小的斜角(一般取3°~5°)。
真空导入成型工艺工艺流程

THANK YOU
感谢聆听
原理
该工艺基于真空吸力原理,通过创建模具内部的负压环境,使得 液态或半固态材料在外部大气压力的作用下被吸入模具中,并在 模具内完成填充、流动和固化等过程,最终获得所需形状和性能 的制品。
工艺流程简介
01
02
03
04
准备阶段
包括模具设计、制造与装配, 以及材料的准备和预处理等。
真空导入阶段
将液态或半固态材料通过特定 的进料系统导入模具中,同时 启动真空系统以创建负压环境 。
设备调试
根据工艺参数和产品要求,对设备进行调试和优化,以确保生产过程的稳定性和 产品质量的一致性。
03
真空导入成型工艺详细流程
模具装配与密封
模具准备
选择适当的模具材料,并进行加工和抛光,确保模 具表面光滑、无缺陷。
模具装配
将模具各部分按照设计要求进行装配,确保模具的 准确性和稳定性。
密封处理
在模具的合模面上涂抹脱模剂,并放置密封条,以 防止树脂泄漏。真空Fra bibliotek统启动及参数设置
80%
真空泵启动
打开真空泵,检查真空系统的密 封性,确保无泄漏。
100%
参数设置
根据树脂的性质和工艺要求,设 置真空度、保持时间等参数。
80%
真空度检测
在树脂注入前,对真空度进行检 测,确保达到预设的真空度要求 。
树脂注入与固化过程控制
树脂准备
按照配比要求准备好树脂和固 化剂,并进行充分搅拌,确保 混合均匀。
05
设备维护与保养
设备日常保养项目
01
02
03
清洁设备
定期清理设备表面和内部 的灰尘、杂质,保持设备 干净整洁。
热压成型机操作规程
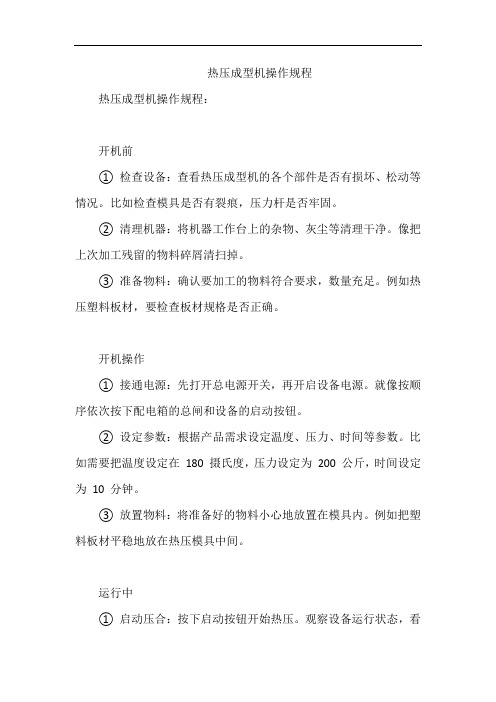
热压成型机操作规程热压成型机操作规程:开机前① 检查设备:查看热压成型机的各个部件是否有损坏、松动等情况。
比如检查模具是否有裂痕,压力杆是否牢固。
② 清理机器:将机器工作台上的杂物、灰尘等清理干净。
像把上次加工残留的物料碎屑清扫掉。
③ 准备物料:确认要加工的物料符合要求,数量充足。
例如热压塑料板材,要检查板材规格是否正确。
开机操作① 接通电源:先打开总电源开关,再开启设备电源。
就像按顺序依次按下配电箱的总闸和设备的启动按钮。
② 设定参数:根据产品需求设定温度、压力、时间等参数。
比如需要把温度设定在180 摄氏度,压力设定为200 公斤,时间设定为10 分钟。
③ 放置物料:将准备好的物料小心地放置在模具内。
例如把塑料板材平稳地放在热压模具中间。
运行中① 启动压合:按下启动按钮开始热压。
观察设备运行状态,看压力和温度是否稳定。
② 查看状况:注意观察物料的成型情况。
像查看塑料板材是否在逐渐成型,有无异常变形。
③ 避免干扰:运行过程中不要随意触碰设备和模具。
比如不要在热压过程中伸手去调整物料位置。
停机后① 停止加热:热压完成后先关闭加热系统。
例如把加热按钮按到关闭状态。
②泄压操作:按规定程序进行泄压。
像缓慢打开泄压阀门,让压力逐渐降低。
③ 取出产品:等压力完全释放后,小心地取出成型后的产品。
比如用工具把热压好的塑料件从模具中取出。
④ 关闭电源:最后关闭设备电源和总电源。
按顺序先关设备开关再关总闸。
⑤ 设备清洁:清理设备,把模具和工作台清理干净,为下次使用做准备。
像把模具上残留的物料清理掉。
正负压吸塑机工作流程
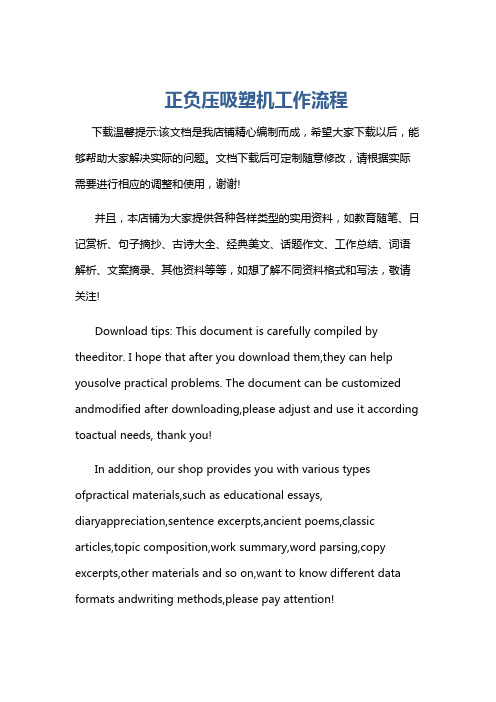
正负压吸塑机工作流程下载温馨提示:该文档是我店铺精心编制而成,希望大家下载以后,能够帮助大家解决实际的问题。
文档下载后可定制随意修改,请根据实际需要进行相应的调整和使用,谢谢!并且,本店铺为大家提供各种各样类型的实用资料,如教育随笔、日记赏析、句子摘抄、古诗大全、经典美文、话题作文、工作总结、词语解析、文案摘录、其他资料等等,如想了解不同资料格式和写法,敬请关注!Download tips: This document is carefully compiled by theeditor. I hope that after you download them,they can help yousolve practical problems. The document can be customized andmodified after downloading,please adjust and use it according toactual needs, thank you!In addition, our shop provides you with various types ofpractical materials,such as educational essays, diaryappreciation,sentence excerpts,ancient poems,classic articles,topic composition,work summary,word parsing,copy excerpts,other materials and so on,want to know different data formats andwriting methods,please pay attention!正负压吸塑机工作流程一、准备工作阶段。
在启动正负压吸塑机之前,需要进行全面细致的准备工作。
- 1、下载文档前请自行甄别文档内容的完整性,平台不提供额外的编辑、内容补充、找答案等附加服务。
- 2、"仅部分预览"的文档,不可在线预览部分如存在完整性等问题,可反馈申请退款(可完整预览的文档不适用该条件!)。
- 3、如文档侵犯您的权益,请联系客服反馈,我们会尽快为您处理(人工客服工作时间:9:00-18:30)。
第一道工序:配料
工艺指导书内容:
1.设备检查:开机前按设备使用要求开机检查各个相关部位,检查线路、气路、各元器件是否有松动,尤其均化桶及不锈钢桶周边,确保无异物进入料桶内;生产完后有序关闭相关电源元件、气阀门等。
2.选用物料:PP粒料、PS粒料、粉碎料等及其它辅料(具体根据生产工艺SOP执行)原则可适当增加粉碎料比例,减少颗粒料添加比例(如需调整原料、粉碎料和辅料的配比需经过技术部同意,不得私自变更)。
计量配料→均化桶投送吸料→搅拌→吸料挤出
2.1计量备料
具体备料根据生产工艺SOP执行
2.2均化桶内投送吸料
启动开关,颗粒料采用开袋人工投料的方式投入均化筒内,注意杂物进入设备内,粉碎料采用自动吸料机吸入均化桶内;
2.3 搅拌
物料进入均化桶后,搅拌10-15分钟以上方可放料。
2.4 吸出进行挤出拉片
3.日常点检
3.1清理锅体:若物料带颜色(非原本色,即添加过色母的物料),并
与下批次生产用物料颜色不同,应关闭机组和均化筒,及时清理残留物料;
3.2生产时应注意检查物料颜色,当选择的物料与需求存在色差或夹杂色,应及时停止生产,调整后方可开机;
3.3粉碎回收料工位注意料色回收的一致性,回收满袋后及时将吨袋封口,入库做好吨袋标识登记卡。
第二道工序:挤出压片
挤出:物料通过挤出机料筒和螺杆间的作用,边受热塑化,边被螺杆向前推送,连续通过机头而制成各种截面制品或半制品的一种加工方法。
工艺指导书内容:
1.设备检查:开机前按设备使用要求开机检查各个相关部位,检查线路、气路、各元器件是否有松动;生产完后有序关闭相关电源开关、气和水路阀门。
2.适用物料:PP粒料,PS粒料和边角料等。
3.工艺流程
加热→输送吸料→喂料→设置工艺参数→出料→三辊压片→牵引→收卷→检测尺寸
4.生产工艺要求
4.1加热
4.1.1打开电柜合上电源控制总闸,打开操作频点击加热启动;
4.1.2预热时设定各区加热温度为220℃,加热时间一般约为2-3小时左右,当各区加热温度达到设定数值后,可继续恒温30分钟,同时确认各区段温控仪表和电磁阀工作状态。
4.1.3各区生产工艺温度设定;
4.2点击操作频开启油泵润滑和水泵冷却系统,检查系统油压和各区冷却管路,观察各区设定温度与实际数值是否存在差异,各温区控制温差以±3℃(调节各区段冷却管路节流水阀即可)。
4.3开启管道输送吸料,将物料依次吸入储料仓、料斗内,物料内不允许有杂物,并确保连续生产时料斗不得断料。
4.4设定相关工艺参数如下表:
4.5打开真空泵,将真空度控制在合理范围内。
4.6模头出料无碳化色,达到生产片材要求且出料稳定后,可调节模唇开口(模唇开口为生产片材的厚度1.4-1.6倍大小)。
4.7将三辊轻缓移动至模头下方待料沿着中底棍卷动进入依次穿过各个辅助辊道后,进入牵引辊,调节三辊得到所需片材生产厚度(±0.02mm),并将边角割刀调节所需生产片材宽度(±2mm),为防止片材宽度不一,割刀调整完成后将螺丝拧紧固定,将合格片材端引入收卷架,调节收卷装置,使得片材收卷均整。
4.8牵引力控制适当,片材不得出现横向拉伸纹,以及避免片材收卷过松或过紧,收卷松紧适当,侧面波动误差小于±2cm,人员操作应防止夹手。
4.9无特殊情况下,收卷要求尽可能整卷,收卷完成后为防止片材表面污染或划伤等,收卷外层应用收缩膜包装不少于三层,并用包装带收紧固定,附带填写流转卡标识后入库。
5.清机及防护
5.1生产中清理真空口堵料时,严禁使用坚硬金属工具,可以用木片、竹片等,防止损坏螺杆及筒体。
5.2设备使用结束,在停机前,待料喂料斗里料走完,加入聚丙烯(PP),开始清机,直至模头出料接近PP料颜色。
5.3对模头的模唇清洁干净,如模唇有杂质和焦黑料存在,操作员及时清理模头,清理模头如下:将铜刀或者竹刀深入模唇大约3cm 处,来回拉动铜刀三至五次,将模头内部残余熔料清出,用铜丝球或者铜刷以及纱布清洁模唇表面。
5.4设备使用结束停机后,为防止灰尘杂质粘附表面损伤三辊,应手动将三辊间距调开2cm以上,并使用防尘装置将三辊表面遮盖,使用时用干净的布条进行擦拭后开机生产。
5.5如需更换片材颜色料生产,应该及时清理粉碎机组管道、储料仓及料斗,原则上本色改其它颜色可不做要求,它色改纯色务必进行清理。
第三道工序:吸塑成型
吸塑成型:是一种将热塑性塑料片材加工成各种制品的较特殊的塑料加工方法。
片材夹在框架上加热到软化状态,采用真空吸附于模具表面,冷却后成型,并应用于各行各业的一种技术工艺。
热成型工艺概况-压力来源:真空、气压、机械辅助。
热成型生产线的基本流程:加热、成型、冷却、裁切、粉碎。
加热:目前塑料片板材的加热多采用电阻丝加热、红外线陶瓷发热砖加热和石英管加热器加热。
热成型设备上的加热站通常采用上下加热炉结构,对于不同塑料片材的成型温度,一般是通过温度控制器调节发热器温度实现片材的所需的成型温度。
根据成型材料与成型模具的接触面的不同,成型过程可分为阳模成型、阴模成型、对模成型和无模成型。
热成型设备加工工艺及过程关键控制
工艺指导书内容:
1.适用设备:三工位正负压热成型机。
2.适用产品:塑料盒、碗、盖、盘类等产品。
3.工艺流程
塑料片材→上料送片→加热软化→真空吸塑成型(正负压热成型机)→伺服电机裁切→计数堆叠→制品取出→检验→包装入库
3.1上料工艺要求
3.1.1根据成型产品选择对应的片材,上卷片时要检查片材的尺寸及外观是否符合生产要求,注意检查片材表面清洁防止粘附异物、沙尘污染,以免后道模具刃口受损;
3.1.2将片材移送至上料位置,将片材外端拉出依次穿过两边定位棍轴、压片橡胶棍轴、碰制端装置,按下点动送片,把片端部拉起引入导入架,使其穿过导片架上的压辊轮进入入片口的搭扣输送齿链,使片材平整进入导轨;
3.1.3对不同厚度的片材需调整压片轮的高度以降低送片电机的负载,
调整压片轮时应保证两边高度一致,以保证塑片不会偏边脱链;3.1.4根据模具尺寸、片材宽度调节送片链轨至合适宽度(一般单边距离较模具保持15~20mm);
3.1.5调节链轨宽度在引入端应比输出端窄10~25mm,具体可视片材在加热时下垂情况及制品成型而确定。
3.2加热工艺要求
3.2.1根据片材厚度,在控制屏温度控制页面上设置上下炉加热温度如下表:
3.2.2预热时间约10~20分钟,当温度控制页面的显示读数达到设置读数时,可以开始生产作业。
3.2.3根据成型面积尺寸,纵向调整电热炉和冷却板的位置去相适应。
3.2.4每区有相应温控微调操作,生产过程若出现某一区域温度偏高或偏低,轻触相应区域,上下炉各个区温度微调控制,值域0~100%。
3.2.5片材经炉加热后方可进入模具成型,具体见下表:
3.3 成型工艺要求
3.3.1根据片材厚度和产品类别,在控制屏温度控制页面上设置成型参数如下表:
3.3.2模腔成型真空负压力0.06~0.09Mpa,成型真空正压力
<0.40Mpa,根据成型制品的表面质量微调。
3.3.3打开模具冷水机,水温设置10~25℃,以控制成型制品脱模温度在10~25℃。
3.3.4生产停机时为防止异物掉入模腔,上下模要处于合模状态。
3.3.5设置送片长度、生产模次按相应产品SOP表规定。
3.3.6成型模具装配按《正负压成型模具装配作业指导书》要求。
3.4冲裁工艺要求
3.4.1根据片材厚度设置裁切力如下表所示:
3.4.2裁切刀模精准定位须依据实际成型效果来确定,模具的上、下模刀口重合要注意上、下刀口相互对正,保证无裁偏和冲破。
3.4.3为维护刀片,生产时应避免空裁切。
3.4.4模具刀模装配按《正负压成型模具装配作业指导书》要求。
3.5计数、堆叠
将整版裁切好的制品按设定的堆叠数在线升降堆叠。
3.6 检验
按成品检验标准执行。
3.7码垛入库
按相应产品SOP表包装规范进行码垛堆放。
3.8本工序产品触点点检如下表:
三工位正负压成型工艺流程说明
总结
原料控制:
要求:对原料的填充材料的配合比例(填充料不宜超30%),原料水分处理(≤2%)。
挤出片材:
要求:片材厚薄均匀一致,片材表观对成型制品的满足。
方法:调节相关螺杆挤出加工部位的挤出温度、模头温度、三辊温度、喂料、牵引参数和真空压力的控制。
成型制品:
要求:成型制品表观质量的满足(客户使用功能性、产品的符合性)。
方法:调节成型模温温度、加热上下炉温度、成型计时、成型压力等。
包装组件:
要求:按客户产品SOP表装袋入箱,区分箱体信息与内部实物的一致性。
方法:在线挑拣点数装袋,包装点袋装箱。