轧制车间设计
年产万吨热轧带钢车间设计
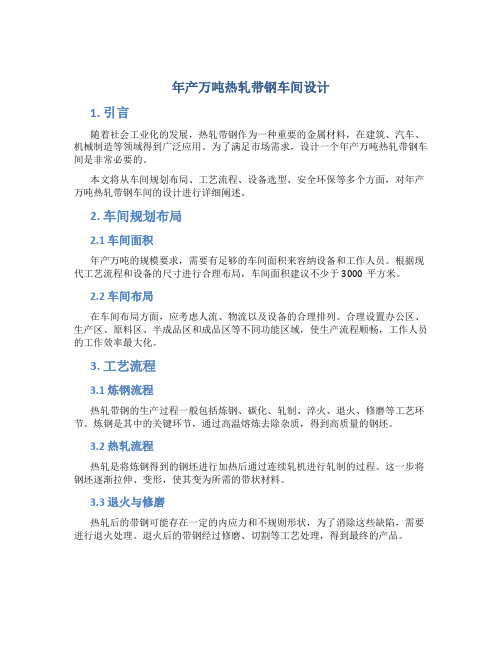
年产万吨热轧带钢车间设计1. 引言随着社会工业化的发展,热轧带钢作为一种重要的金属材料,在建筑、汽车、机械制造等领域得到广泛应用。
为了满足市场需求,设计一个年产万吨热轧带钢车间是非常必要的。
本文将从车间规划布局、工艺流程、设备选型、安全环保等多个方面,对年产万吨热轧带钢车间的设计进行详细阐述。
2. 车间规划布局2.1 车间面积年产万吨的规模要求,需要有足够的车间面积来容纳设备和工作人员。
根据现代工艺流程和设备的尺寸进行合理布局,车间面积建议不少于3000平方米。
2.2 车间布局在车间布局方面,应考虑人流、物流以及设备的合理排列。
合理设置办公区、生产区、原料区、半成品区和成品区等不同功能区域,使生产流程顺畅,工作人员的工作效率最大化。
3. 工艺流程3.1 炼钢流程热轧带钢的生产过程一般包括炼钢、碳化、轧制、淬火、退火、修磨等工艺环节。
炼钢是其中的关键环节,通过高温熔炼去除杂质,得到高质量的钢坯。
3.2 热轧流程热轧是将炼钢得到的钢坯进行加热后通过连续轧机进行轧制的过程。
这一步将钢坯逐渐拉伸、变形,使其变为所需的带状材料。
3.3 退火与修磨热轧后的带钢可能存在一定的内应力和不规则形状,为了消除这些缺陷,需要进行退火处理。
退火后的带钢经过修磨、切割等工艺处理,得到最终的产品。
4. 设备选型4.1 炼钢设备炼钢设备是热轧带钢车间中的核心设备,包括炉子、转炉、炼钢机等。
选购时应考虑设备的稳定性、生产能力以及能耗方面的因素。
4.2 轧机设备轧机设备是热轧过程中的关键设备,主要包括脱碳设备、轧机机组和辊道设备等。
选型时需综合考虑轧制能力、稳定性以及安全工作性能。
4.3 退火设备退火设备用于对经过轧制后的钢带进行退火处理,消除内应力和恢复材料的塑性。
选择设备时需考虑工艺要求、退火温度和速度的控制以及能耗方面的因素。
5. 安全环保在车间设计中,安全环保是至关重要的。
应设计合理的消防设施,安装可靠的烟雾和气体检测系统,确保生产过程中的安全。
轧钢车间设计

车间设计任务书是依据,由有关上级部门下达。设计任务书的基本内容包 括:
1. 车间的生产规模、品种 2. 生产方案 3. 建厂地址,厂区范围,资源利用状况、各种材料供应、运输等 4. 要求达到的技术水平,经济及社会效益 5. 投资及劳动定员的控制数字。 6. 环保要求
6
2 生产方案与产品方案制定
8
一. 板带钢生产:~0.2 薄带箔材,0.2~0.4 薄板,4~中厚板 1. 中厚板生产:单机四辊可逆式,双机架(2+4 或 4+4)可逆式;半连 轧连轧 2. 热轧薄板带钢:全连续式,半连续式、3/4 连续式 2.0~12mm→0.8mm 3. 冷轧带钢:单机可逆、连轧(3 机架 4 机架 5 机架 6 机架)0.1~2.0mm 二. 型钢生产 1. 横列布置普通轧法 2. 万能轧法 3. 型钢连轧 4. 热及冷弯型钢 5. 挤压法 三. 管材生产 1. 热轧法:自动轧管机、连轧管机、两辊斜轧穿孔、三辊斜轧穿孔、菌 式穿孔机、张力减径机、皮格尔轧管、狭舍尔轧管机 2. 热挤压 3. 焊接:直缝焊、螺旋焊 4. 冷加工:冷轧 冷拔、冷旋压 四. 线材生产 以下成卷交货 一般断面为圆形 1. 横列式(二辊轧机) 2. 半连续式(三辊轧机) 3. 连续式(二辊+45°无钮式或二辊+Y 型无钮)(单线或三线)
影响产品的产量、质量,因此选择轧机时应以生产方案和产品方案为依据进行
52.5
普通及深冲用低碳
0.2~0.3 600~1500
卷
钢带
22.5 22.5
7
镀锌钢板
0.25~0.55 700~1500 1000~6000 13.5 13.5
镀锌钢带
0.25~0.55 700~1500
热轧H型钢轧钢车间设计

热轧H型钢轧钢车间设计(design of hot H-beam mill)以连铸坯、热轧坯为原料,经加热和万能轧机轧制,生产热轧H型钢产品的车间设计。
H型钢过去称为宽边工字钢,属于经济断面型钢。
它与工字钢相比,其断面特点是翼缘(腿)可更宽、腹板(腰)可更高,而壁较薄;在相同断面面积时,H型钢的截面抵抗矩、惯性矩等力学性能都比工字钢高,可获得优良的抗弯能力和稳定性;腿部内外侧平行,呈直角,故拼装连接方便;形状美观。
H型钢主要用于制作高层民用建筑的构件,工业厂房的梁、柱和桩,桥梁钢结构件,重型车辆桥架及各种机械的构件和机座等。
H型钢用在建筑结构上可减轻重量30%~40%,做拼装组合构件可减少焊接、铆接工作量达25%。
在工业发达国家,目前热轧H型钢产量约占热轧钢材产量的2%~6%,占型钢产量的30%~60%。
H型钢产品按翼缘宽度分为宽翼缘H型钢(HK)、窄翼缘H型钢(HZ)和H型钢桩(HU)三大类。
中国国家标准规定的H型钢产品规格范围见表1。
目前国外生产的H型钢断面最大高度达1200mm,最大翼缘宽度达530mm。
H型钢的材质,主要有碳素钢和低合金结构钢,少量为含低镍、低铬的低温用钢和海洋用钢。
热轧H型钢轧钢车间设计的原则和方法见轧钢厂设计。
简史 1867年德国哈哥•萨克(Huge Sack)发明带立辊的万能轧机,1901年卢森堡阿尔贝德一迪弗当日(Arbed-Differdange)厂建成了由万能机架和轧边机架组成的格雷式(Grey)H型钢轧机,德国和美国等国也相继建成了此类轧机,但在20世纪前半个世纪建成甚少。
直至20世纪60年代,由于建筑业的高速发展,市场对H型钢的需求量增加,加快了H型钢轧机的发展,特别是轧钢技术和电控技术的进步,使其向多品种、自动化、中型轧机的连续化方向发展。
1985年联邦德国西马克(SMS)公司开发了由两架万能机架和一架二辊轧边机架组成的串列式万能轧机,轧出了H型钢,使串列式万能轧机向经济型方向发展。
线材轧钢工程车间平面布置

线材轧钢工程车间平面布置
一、一般规定
1、总图布置应考虑轧钢车间与上游连铸车间的衔接,宜采用辊道运输的方式输送连铸坯,紧凑布置。
2、车间工艺布置应满足生产工艺要求,流程畅通,布局合理,操作方便;对预留发展的车间,应预留设备、设施的布置场地。
二、主车间布置
1、设备布置宜紧凑,应留有设备安装、操作、检修空间和安全通道等。
2、主轧线设备应采用高架平台布置。
高架平台布置相对于车间±0.0m地坪,平台标高宜为+5.0m。
平台下应用于设置液压润滑站等设施。
3、主厂房起重机的轨面标高及起重量应按设备高度、设备检修要求、坯料成品的堆放能力和运输条件等确定。
起重机数量应根据车间生产能力确定。
4、单线轧制的线材车间主轧跨跨度宜为24m,双线轧制的线材车间主轧跨跨度宜为27m~30m。
5、坯料库、中间库和成品库的面积应保证正常生产需要。
坯料库存放量根据车间的热装热送率宜为2d~5d,没有全厂性成品仓库的线材车间,成品库存放量不宜少于7d。
三、辅助设施布置
1、主电室宜布置在轧机传动侧,生产线较长或设施分散时,可分区布置若干电气室。
2、轧辊间应靠近主轧跨,宜布置在轧机操作侧。
3、水处理设施应靠近车间集中布置。
轧钢车间设计3
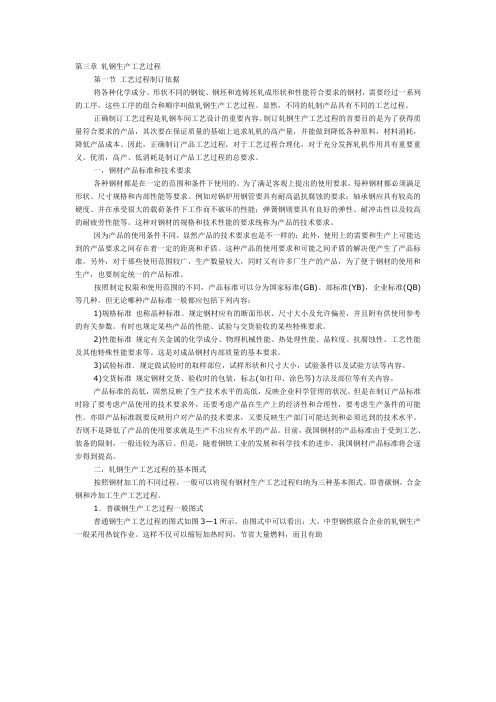
第三章轧钢生产工艺过程第一节工艺过程制订依据将各种化学成分、形状不同的钢锭、钢坯和连铸坯轧成形状和性能符合要求的钢材,需要经过一系列的工序,这些工序的组合和顺序叫做轧钢生产工艺过程。
显然,不同的轧制产品具有不同的工艺过程。
正确制订工艺过程是轧钢车间工艺设计的重要内容。
制订轧钢生产工艺过程的首要目的是为了获得质量符合要求的产品,其次要在保证质量的基础上追求轧机的高产量,并能做到降低各种原料,材料消耗,降低产品成本。
因此,正确制订产品工艺过程,对于工艺过程合理化,对于充分发挥轧机作用具有重要童义。
优质,高产、低消耗是制订产品工艺过程的总要求。
一,钢材产品标准和技术要求各种钢材都是在一定的范围和条件下使用的。
为了满足客观上提出的使用要求,每种钢材都必须满足形状、尺寸规格和内部性能等要求。
例如对锅炉用钢管要具有耐高温抗腐蚀的要求;轴承钢应具有较高的硬度、并在承受很大的载荷条件下工作而不破坏的性能;弹簧钢则要具有良好的弹性、耐冲击性以及较高的耐疲劳性能等。
这种对钢材的规格和技术性能的要求统称为产品的技术要求。
因为产品的使用条件不同,显然产品的技术要求也是不一样的;此外,使用上的需要和生产上可能达到的产品要求之间存在着一定的距离和矛盾。
这种产品的使用要求和可能之间矛盾的解决便产生了产品标准。
另外,对于那些使用范围较广,生产数量较大,同时又有许多厂生产的产品,为了便于钢材的使用和生产,也要制定统一的产品标准。
按照制定权限和使用范围的不同,产品标准可以分为国家标准(GB)、部标准(YB),企业标准(QB)等几种。
但无论哪种产品标准一般都应包括下列内容:1)规格标准也称晶种标准。
规定钢材应有的断面形状、尺寸大小及允许偏差,并且附有供使用参考的有关参数。
有时也规定某些产品的性能、试验与交货验收的某些特殊要求。
2)性能标准规定有关金属的化学成分、物理机械性能、热处理性能、晶粒度、抗腐蚀性、工艺性能及其他特殊性能要求等。
年产300万吨中厚板轧钢车间设计
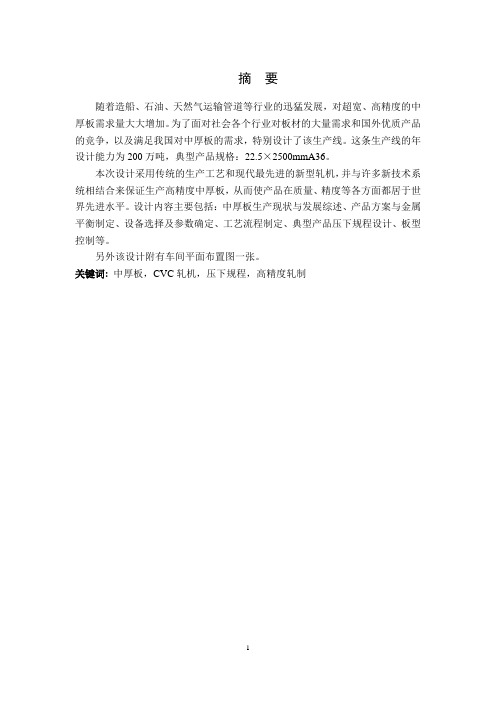
摘要随着造船、石油、天然气运输管道等行业的迅猛发展,对超宽、高精度的中厚板需求量大大增加。
为了面对社会各个行业对板材的大量需求和国外优质产品的竞争,以及满足我国对中厚板的需求,特别设计了该生产线。
这条生产线的年设计能力为200万吨,典型产品规格:22.5×2500mmA36。
本次设计采用传统的生产工艺和现代最先进的新型轧机,并与许多新技术系统相结合来保证生产高精度中厚板,从而使产品在质量、精度等各方面都居于世界先进水平。
设计内容主要包括:中厚板生产现状与发展综述、产品方案与金属平衡制定、设备选择及参数确定、工艺流程制定、典型产品压下规程设计、板型控制等。
另外该设计附有车间平面布置图一张。
关键词: 中厚板,CVC轧机,压下规程,高精度轧制目录摘要 (1)目录 (2)1 绪论 (5)1.1国内中厚板生产的发展历史 (5)1.2中厚钢板生产的发展趋势 (6)1.3本设计目的与内容 (7)2 产品大纲与金属平衡 (8)2.1产品大纲 (8)2.1.1 产品大纲 (8)2.1.2 技术要求 (9)2.2.金属平衡 (10)3 设备选择及参数确定 (12)3.1宽厚板轧机选择 (12)3.1.1 新型轧机 (12)3.1.2 轧机选择 (14)3.2辅助设备选择 (15)3.2.1 加热设备选择 (15)3.2.2 炉型确定 (15)3.2.3 产量计算 (16)3.2.4 炉子尺寸确定 (16)3.3斜刃剪的选择 (17)3.3.1 斜刃剪的形式 (17)3.3.2 主要技术参数 (17)3.4矫直设备选择 (18)3.5冷床的选择 (20)3.5.1 冷床结构和形式 (20)3.5.2 冷床主要技术参数 (21)3.6起重运输设备选择 (22)3.6.1 辊道形式 (22)3.6.2 辊道主要技术参数 (22)3.6.3 起重机的选择 (22)3.6.4 起重机的主要参数 (23)3.7热处理设备选择 (23)4 生产工艺流程与轧制规程制定 (24)4.1坯料选择 (24)4.1.1 原料的种类 (24)4.1.2 原料的材质 (24)4.1.3 原料的设计 (24)4.1.4 原料表面的缺陷清理 (25)4.2坯料加热 (25)4.2.1 加热的目的 (25)4.2.2 钢的加热温度 (25)4.2.3 钢的加热速度 (26)4.2.4 钢的加热制度 (26)4.3钢的轧制 (26)4.4钢板精整 (28)4.5板形控制 (28)4.6轧制规程设计 (29)4.6.1 轧制道次 (29)4.6.2 各道次压下量分配 (29)4.6.3 速度制度 (32)4.6.4 温度制度 (33)4.6.5 力能参数计算 (33)4.7典型产品22.5×2500MM A36厚板生产压下规程设计 (35)5 轧制图表和年产量计算 (39)5.1轧制图表 (39)5.1.1 研究轧机工作图表的意义 (39)5.1.2 轧制图表的基本形式及其特征 (39)5.2年产量的计算 (40)5.2.1 轧机小时产量计算 (40)5.2.2轧钢机平均小时产量 (41)5.2.3 年产量的计算 (43)5.2.4 影响轧机产量的因素 (44)结论 (45)致谢 (47)参考文献 (49)1 绪论中厚板的需求主要集中在建筑、锅炉、机械、造船、石油、电力等行业,产品类别有汽车板、锅炉板、合金结构板、造船及采油平台钢板、油气输送管线用钢板等。
年产125万吨1700冷轧带钢车间设计
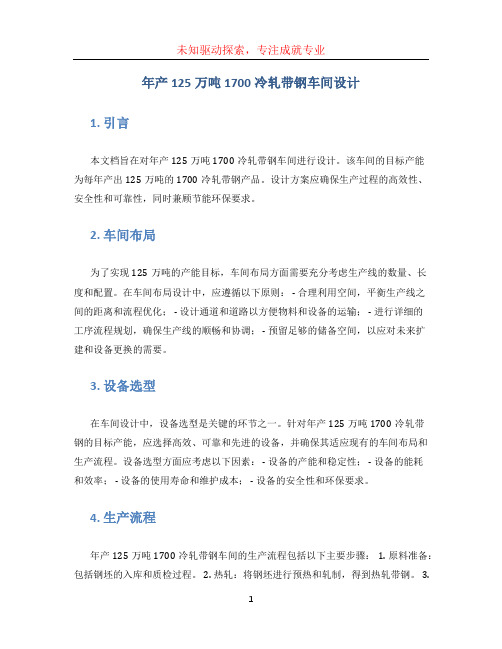
年产125万吨1700冷轧带钢车间设计1. 引言本文档旨在对年产125万吨1700冷轧带钢车间进行设计。
该车间的目标产能为每年产出125万吨的1700冷轧带钢产品。
设计方案应确保生产过程的高效性、安全性和可靠性,同时兼顾节能环保要求。
2. 车间布局为了实现125万吨的产能目标,车间布局方面需要充分考虑生产线的数量、长度和配置。
在车间布局设计中,应遵循以下原则: - 合理利用空间,平衡生产线之间的距离和流程优化; - 设计通道和道路以方便物料和设备的运输; - 进行详细的工序流程规划,确保生产线的顺畅和协调; - 预留足够的储备空间,以应对未来扩建和设备更换的需要。
3. 设备选型在车间设计中,设备选型是关键的环节之一。
针对年产125万吨1700冷轧带钢的目标产能,应选择高效、可靠和先进的设备,并确保其适应现有的车间布局和生产流程。
设备选型方面应考虑以下因素: - 设备的产能和稳定性; - 设备的能耗和效率; - 设备的使用寿命和维护成本; - 设备的安全性和环保要求。
4. 生产流程年产125万吨1700冷轧带钢车间的生产流程包括以下主要步骤: 1. 原料准备:包括钢坯的入库和质检过程。
2. 热轧:将钢坯进行预热和轧制,得到热轧带钢。
3.酸洗:对热轧带钢进行酸洗处理,以去除表面氧化物和杂质。
4. 退火:对酸洗后的带钢进行退火处理,以改善材料的力学性能。
5. 冷轧:将退火后的带钢进行冷轧,得到最终的冷轧带钢产品。
6. 表面处理:对冷轧带钢进行表面处理,以提高表面质量和防锈性能。
7. 包装和出货:对成品冷轧带钢进行包装和出货。
5. 厂区环境与设施除了车间设计,厂区环境和设施也需要考虑。
厂区环境和设施应具备以下要求:- 具备充足的生产用电和供水能力; - 配备有效的废水和废气处理设施,确保符合环保要求; - 考虑员工的生活设施,如员工宿舍、餐厅、停车场等; - 安全设施齐备,包括消防设备、通风设备等。
1700热轧280万吨车间设计
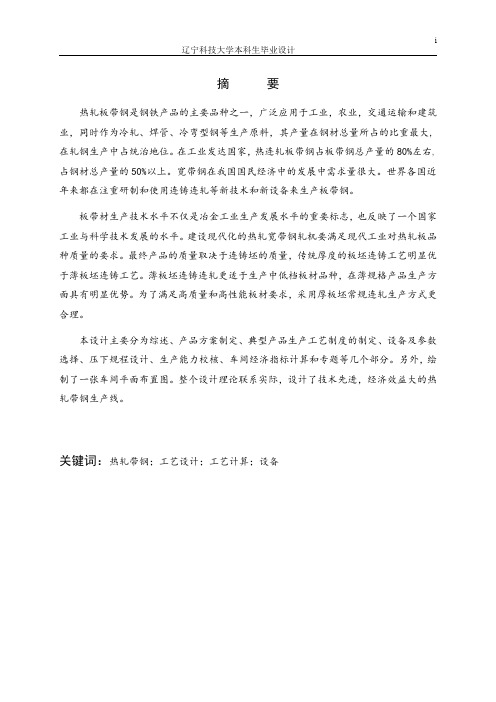
辽宁科技大学本科生毕业设计摘要热轧板带钢是钢铁产品的主要品种之一,广泛应用于工业,农业,交通运输和建筑业,同时作为冷轧、焊管、冷弯型钢等生产原料,其产量在钢材总量所占的比重最大,在轧钢生产中占统治地位。
在工业发达国家,热连轧板带钢占板带钢总产量的80%左右,占钢材总产量的50%以上。
宽带钢在我国国民经济中的发展中需求量很大。
世界各国近年来都在注重研制和使用连铸连轧等新技术和新设备来生产板带钢。
板带材生产技术水平不仅是冶金工业生产发展水平的重要标志,也反映了一个国家工业与科学技术发展的水平。
建设现代化的热轧宽带钢轧机要满足现代工业对热轧板品种质量的要求。
最终产品的质量取决于连铸坯的质量,传统厚度的板坯连铸工艺明显优于薄板坯连铸工艺。
薄板坯连铸连轧更适于生产中低档板材品种,在薄规格产品生产方面具有明显优势。
为了满足高质量和高性能板材要求,采用厚板坯常规连轧生产方式更合理。
本设计主要分为综述、产品方案制定、典型产品生产工艺制度的制定、设备及参数选择、压下规程设计、生产能力校核、车间经济指标计算和专题等几个部分。
另外,绘制了一张车间平面布置图。
整个设计理论联系实际,设计了技术先进,经济效益大的热轧带钢生产线。
关键词:热轧带钢;工艺设计;工艺计算;设备ABSTRACTHot Strip is one of the main varieties of steel products,widely used in industry, agriculture,transport and construction sectors,as both cold-rolled,welded,cold-formed steel and other raw materials,and its share of total steel production in the the largest proportion in the steel rolling production dominate.In industrialized countries,hot rolling plate steel plate steel production accounted for about80%,accounting for more than50%of total production of steel.Wide strip in the development of our national economy in great demand.In recent years,countries in the world are in the focus on the development and use of new technologies such as continuous casting and rolling,and new equipment to produce flat steel.Plate and strip production technology level is not only the production of metallurgical industry an important indicator of the level of development,but also reflects a country's industrial and scientific and technological development level.Building a modern hot-rolled wide strip mills to meet modern industry hot-rolled plate variety and quality requirements. The quality of the final product depends on the quality of the billet,the traditional thick slab casting process significantly better than the thin slab continuous casting process.Thin slab casting and rolling plate varieties better suited to middle and low production,the production of thin gauge has obvious advantages.To meet the requirements of high quality and high performance laminates,using conventional thick slab rolling production more reasonable way.The design is divided into overview,product program development,typical system has been developed production processes,equipment and parameter selection,draft schedule design,production capacity check,calculate economic indicators and thematic workshops and several other parts.The whole design theory with practice,the design of technologically advanced,cost-effective large hot strip production line.Keywords:hot rolled strip;process design;process calculation;equipment目录1综述 (1)1.1热轧板带钢发展史 (1)1.1.1国外热轧板带的发展 (1)1.1.2国内热轧板带钢的发展 (2)1.2热轧板带钢产品概述 (3)1.2.1热轧板带钢的种类、规格及用途 (3)1.2.2板带产品的使用特点、生产特点及技术要求 (4)1.3热轧带钢生产工艺概述 (4)1.3.11700ASP工艺流程及其先进技术 (4)1.3.21780工艺流程及其先进技术 (5)1.4热轧工艺装备关键技术 (6)1.4.1无头轧制 (6)1.4.2ASR技术 (7)1.4.3CVC技术 (8)1.4.4在线制造 (9)1.4.5现代建模方法 (9)1.5热轧宽带钢的发展趋势 (10)2产品方案 (11)2.1产品方案的编制 (11)2.1.1产品方案简介 (11)2.1.2选择计算产品 (11)2.2坯料 (12)2.2.1钢种 (12)2.2.2坯料规格 (12)2.3产品特点 (12)2.3.1产品质量标准 (12)2.3.2产品性能 (13)2.3.3产品规格 (13)2.3.4产品目标值 (14)2.4产品方案和金属平衡 (14)2.4.1产品方案 (14)3生产工艺过程和设备的选择 (16)3.11700生产工艺流程及其概述 (16)3.2生产方案的选择 (16)3.3工艺布置特点和设备的选择 (17)3.3.1机组配置 (17)3.3.2加热炉的选择 (17)3.3.3粗轧机组的选择 (18)3.3.4立辊轧机的选择 (18)3.3.5保温装置的选择 (20)3.3.6飞剪机的选择 (20)3.3.7高压水除鳞设备的选择 (21)3.3.8精轧机组的选择 (22)3.3.9层流冷却 (23)3.3.10卷取机的选择 (24)4生产工艺流程图和典型产品 (27)4.1确定轧制方法 (27)4.2根据产品选择原料 (27)4.3工艺流程图 (27)5压下规程设计 (28)5.1粗轧机压下规程的制度 (28)5.1.1粗轧机组各道次的压下量分配 (28)5.1.2根据成品板宽确定精轧坯宽度 (28)5.1.3计算粗轧机组轧制时的宽展量 (29)5.1.4计算坯料轧前的膨胀宽度 (29)5.2精轧机压下规程的制定 (30)6校核咬入能力 (32)7轧制时间制度 (33)7.1粗轧轧制时间计算 (33)7.2精轧轧制时间计算 (35)8温度制度 (40)8.1粗轧时各道次的温降 (40)8.2精轧温度制度 (41)9速度制度 (43)9.1粗轧机速度制度 (43)9.2精轧机速度制度 (43)10计算各道的平均变形速度 (47)10.1粗轧各道次的平均变形速度 (47)10.2精轧各道次的平均变形速度 (48)11轧制力及轧制力矩的计算 (49)11.1粗轧机轧制力和轧制力矩的计算 (50)11.2精轧机轧制力和轧制力矩的计算 (52)12生产设备的校核 (55)12.1轧辊的校核 (55)12.2粗轧机轧辊强度校核 (55)12.3精轧轧辊强度的校核 (59)12.4接触应力的计算 (64)13轧机生产能力校核 (67)13.1年产量计算 (67)13.2工作制度与工作时间 (67)13.3轧机生产能力校核 (67)专题:钛及钛合金性能及应用 (71)1钛的性能及应用 (72)1.1概述 (72)1.2钛的资源和它的战略地位 (72)1.3我国钛工业基础 (73)1.4钛的性能和应用 (74)1.5研究和发展 (75)2钛合金的性能及应用 (77)2.1钛合金发展史 (77)2.2钛合金性能 (77)2.2.1热强度高 (77)2.2.2抗蚀性好 (77)2.2.3低温性能好 (78)2.3典型钛合金性能 (78)2.4钛合金应用 (78)参考文献 (79)致谢 (81)1综述1.1热轧板带钢发展史热轧板带钢轧机的发展已有70多年历史,汽车工业、建筑工业、交通运输业等的发展,使得热轧及冷轧薄钢板的需求量不断增加,从而促使热轧板带钢轧机的建设获得了迅速和稳定的发展。
轧制车间设计

名词解释1.可行性研究是对所拟建工程项目从有关的各方面进行调查和综合论证,为拟建项目提供科学依据,从而保证所建项目在技术上先进可行,经济上合理有利。
2.初步设计是按设计任务书给定条件,在可行性研究基础上进行的;3.施工设计是按已经批准的初步设计绘制施工图,把设计内容变成施工文件和图纸,据此进行车间建设。
4.成材率——是成品重量与投入的原料重量之比的百分数,成材率是一项重要的技术经济指标,其高低反映了生产组织管理及生产技术水平的高低。
5.轧制图表——轧制图表也称轧制进程表和轧制工作图表,表示和反映了轧制道次和轧制时间之关系的图表。
6.轧机负荷率——轧机的全年实际轧制时间与全年计划轧制时间之比,反映了轧机的是否被充分利用以及设备间的平衡情况7.总图——总平面布置——车间相互位置的关系。
8.生产车间:生产主线;指直接生产各种加工产品的车间. 如型材,管材,板带,棒线生产车间,锻造件及模压件生产车间等9.辅助车间:指为主要生产车间服务的车间。
动力、机修、电修、工模具、计器、中心实验室等10.企业内运——原辅材料、燃料、半成品、成品、废料、废渣等。
(内运主要有辊道、行车、运输小车、升降设备等,运输周转是否灵活可靠,直接影响车间效率)11.产品方案工厂或车间拟生产产品名称,品种,规格,状态以及年计划产量。
由设计任务书规定或设计者调研提出经主管部门批准。
12.金属平衡表是反映某一定时期(一年),制品金属材料的收支情况,是编制工厂或车间生产预算与制定计划、内部与外部运输、以及平面布置的重要数据。
基于成品率及损失率编制。
13.钢轨:一般情况下,30kg/m以下称为轻轨,否则为重轨。
14.经济断面型材:断面形状类似于普通型材,而断面各部分的金属分布更加合理,使用时经济效益高于普通型材。
15.生产工艺流程的共同性:坯料准备⇨加热⇨轧制⇨冷却⇨热处理⇨精整⇨入库16.竖炉(炉身直立,炉内大部装满物料的冶金炉,炉气在炉内向上运动,与炉料之间呈逆流换热。
年产万吨热轧线材车间设计
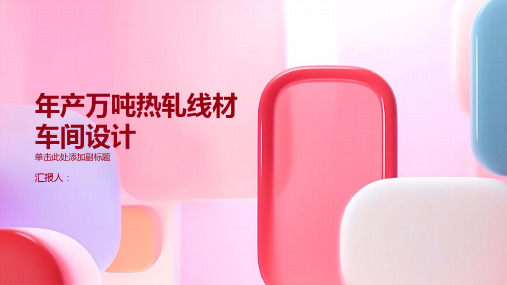
照明设计:采 用节能型照明 设备,保证车 间内光线充足, 提高工作效率。
噪声控制:采 用隔音材料和 降噪设备,降 低车间内噪声, 保证员工身心
健康。
其他设施设计: 如消防设施、 安全设施等, 保证车间安全
运行。
安全与卫生设施规划
安全设施:包括消防设施、安全通道、安全警示标志等 卫生设施:包括卫生间、消毒设施、通风设施等 安全与卫生设施布局:合理规划,确保安全与卫生设施的布局合理、方便使用 安全与卫生设施维护:定期检查、维护安全与卫生设施,确保其正常运行
05
生产工艺与操作规 程制定
生产工艺流程描述
原料准备:包括原料的采购、运输、储 存等环节
冷却:将轧制后的线材进行冷却,使 其达到可加工状态
加热处理:将原料加热至一定温度, 使其达到可塑性状态
成品检验:对线材的尺寸、性能等进 行检验,确保产品质量
轧制:将加热后的原料通过轧辊进行轧 制,形成线材
包装运输:将检验合格的线材进行包 装、运输,交付客户
操作规程制定与培训计划
制定操作规程:根据生产工艺和设备特点,制定详细的操作规程,包括操作步骤、注意事项、 安全要求等。
培训计划制定:根据操作规程,制定培训计划,包括培训时间、培训内容、培训方式等。
培训实施:按照培训计划,组织员工进行培训,包括理论培训和实际操作培训。
考核与评估:培训结束后,对员工进行考核,评估培训效果,并根据考核结果调整培训计划。
年产万吨热轧线材 车间设计
单击此处添加副标题
汇报人:
目录
添加目录项标题 生产线规划与布局 生产工艺与操作规程制定 环境保护与废弃物处理方 案设计
设计背景与目标 车间环境与设施设计 能源消耗与节能措施设计 总结与展望
中厚板轧制车间设计

1.前言建国以来到2000年前后我国厚板轧机发展比较缓慢,这一时期我国共计拥有25套中厚板轧机,其原设计能力为1600万t/a 左右。
鞍钢1958年投产的半连续轧板厂和武钢1968年投产的轧板厂的2800/2800mm 厚板轧机,这两套厚板轧机均为原苏联设计和制造,是当时我国最大和比较完善的中厚板生产设备,设计产品规格为(计产品规格为(44~5050)×)×)×100010001000~~25002500×(×(×(400040004000~~1800018000))mm mm。
5050、、60年代大炼钢铁时期和其后,我国自行设计制造了一大批23002300~~2800mm 中厚板轧机并建于各省骨干钢铁企业中。
舞阳钢铁公司1978年建成投产一套4200mm 特厚板轧机,完全由国内自力更生进行设计和制造建设的。
特厚板轧机,完全由国内自力更生进行设计和制造建设的。
9090年代初期上海浦钢、鞍钢、邯钢、首钢(秦皇岛厂)引进的42004200、、43004300、、30003000、、3450mm 四套厚板轧机及生产线的二手设备,国内做必要改造并补齐相应配套设施而较快地建成投产。
地建成投产。
我国到2000年前后已有的25套中厚板轧机按辊身长度划分情况如下:套中厚板轧机按辊身长度划分情况如下:66套辊身长度辊身长度 3450 3450 ~4300mm 轧机;5套辊身长度套辊身长度 2800 2800~3000mm 轧机;14套辊身长度23002300~~2500mm 轧机。
轧机。
从以上轧机分析,有14套轧机的辊身长度为23002300~~ 2500mm ,从而在半个,从而在半个世纪以来我国所生产的宽度2000mm 及以下中厚钢板占据了市场的主导地位,钢板厚度主要是5(6)~)~ 25mm 25mm 。
这就是至今我们习惯于把中厚板、厚板、宽厚板。
这就是至今我们习惯于把中厚板、厚板、宽厚板轧机笼统地称为中厚板轧机的原因。
轧制车间设计 -回复
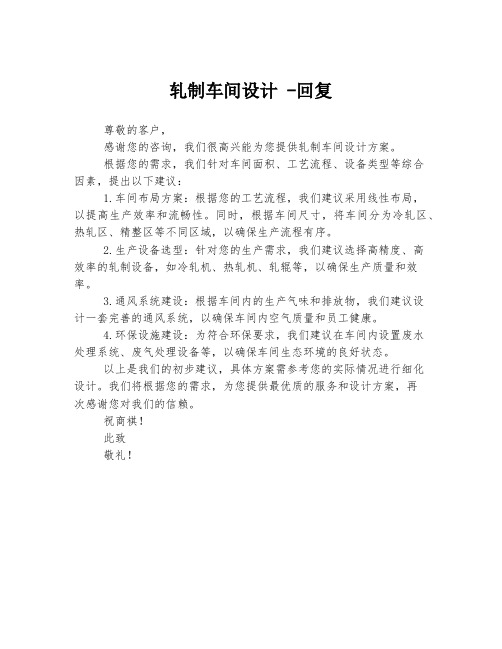
轧制车间设计 -回复
尊敬的客户,
感谢您的咨询,我们很高兴能为您提供轧制车间设计方案。
根据您的需求,我们针对车间面积、工艺流程、设备类型等综合
因素,提出以下建议:
1.车间布局方案:根据您的工艺流程,我们建议采用线性布局,
以提高生产效率和流畅性。
同时,根据车间尺寸,将车间分为冷轧区、热轧区、精整区等不同区域,以确保生产流程有序。
2.生产设备选型:针对您的生产需求,我们建议选择高精度、高
效率的轧制设备,如冷轧机、热轧机、轧辊等,以确保生产质量和效率。
3.通风系统建设:根据车间内的生产气味和排放物,我们建议设
计一套完善的通风系统,以确保车间内空气质量和员工健康。
4.环保设施建设:为符合环保要求,我们建议在车间内设置废水
处理系统、废气处理设备等,以确保车间生态环境的良好状态。
以上是我们的初步建议,具体方案需参考您的实际情况进行细化
设计。
我们将根据您的需求,为您提供最优质的服务和设计方案,再
次感谢您对我们的信赖。
祝商祺!
此致
敬礼!。
2030冷轧车间设计

摘要根据任务书要求,设计年产210万吨2030冷轧带钢车间设计。
按照车间设计的步骤,主要完成产品大纲制定、主辅设备选择、压下分配、轧制规程计算、轧制图表、轧制力计算、轧辊强度校核、电机能力验算、年产量计算、车间平面布置。
设计中参阅了国内外有关轧机的先进工艺、轧机的装备、技术及一些辅助设备的论述,特别参考了宝钢冷轧薄板厂生产线参数和现场数据,使本设计车间达到工艺合理、设备先进。
本设计车间能生产的带钢品种多,规格齐全。
产品规格为0.3~3.5mm冷轧板带,典型产品为Q215冷轧薄板带钢,产品规格0.8 1400mm。
设计附有车间平面图。
关键词:车间设计冷轧带钢轧制工艺五机架连轧机组ABSTRACTAccording to the task requirements, I designed this 2030mm cold-rolling workshop for an annual output of 2.1 million tons.Steps in accordance with the workshop design,I mainly complete the product outline of the development, main and auxiliary equipment options, press distribution, the calculation of order rolling, rolling chart, the calculation of rolling force and roll strength, motor ability checking, annual terms, workshop layout.Refer to the design of domestic and foreign advanced technology of the rolling mill, rolling mill equipment, technology and some discussion of auxiliary equipment, especially reference to the Baosteel and Steel cold-rolled sheet production line parameters ,making the design process to achieve a reasonable workshop, advanced equipment.The steel plant can produce more complete specifications.The product specifications range8.0 .0.3 to 3.5mm.the typical product is the Q215 1400There is a picture of the plan following the design workshop.Key words: Workshop design; Cold rolled strip; Rolling system; Rolling five-rack unit目录摘要 (Ⅰ)ABSTRACT (Ⅱ)1 绪论 (1)1.1 本设计的目的及意义 (1)1.2 本设计的主要内容 (1)1.3 2030mm冷连轧生产工艺介绍 (1)1.3.1 加工温度低,在轧制中将产生不同程度的加工硬化 (2)1.3.2 冷轧中要采用工艺冷却和润滑 (2)1.3.3 冷轧中要采用张力轧制 (2)1.4 冷轧薄板带钢产品的发展及重要地位 (3)2 产品方案及生产方案 (4)2.1 制定产品大纲 (4)2.2 生产方案 (5)2.3 金属平衡表 (6)3 制定工艺流程 (7)3.1 冷轧板带钢生产的工艺流程 (7)3.2 工艺流程介绍 (8)3.2.1 酸洗 (8)3.2.3 精整 (9)3.2.4 镀锌 (9)3.2.5 平整 (10)4 主辅设备选择 (11)4.1 设备组成 (11)4.2 设备参数 (11)4.2.1 连续酸洗机组 (11)4.2.2 全连续式冷轧机 (13)4.2.3 全氢罩式退火机组 (15)4.2.4 平整机组 (16)4.2.5 横剪机组 (17)4.2.6 纵剪机组 (18)4.2.7 重卷机组 (18)4.2.9 热镀锌机组 (20)5 轧制规程设计 (22)5.1 压下规程概述 (22)5.2 压下量的分配 (22)5.3 速度制度 (23)5.4 张力制度的制定 (24)5.5 轧制压力的计算 (24)5.6 压下规程的制定 (28)6 轧辊强度校核 (29)6.1 综述 (29)6.2 确定工作辊和支撑辊的各个重要尺寸 (30)6.3轧辊强度的校核 (31)6.3.1 支撑辊强度校核 (31)6.3.2 工作辊强度校核 (32)7 电机能力验算 (33)7.1 轧制力矩的确定 (33)7.1.1 轧制力矩的确定 (33)7.1.2 摩擦力矩的确定 (33)7.1.3 空转力矩的确定 (34)7.2 电机能力校核 (34)8 年产量计算 (37)8.1 轧机小时产量计算 (37)8.2 轧机平均小时产量 (39)8.3 轧机年产量的计算 (40)9 车间平面布置 (41)9.1 仓库面积计算 (41)9.1.1 原料仓库面积 (41)9.1.2 中间仓库面积 (42)9.1.3 成品仓库面积 (42)9.1.4 其它面积 (43)9.2 设备间距确定 (43)9.2.1 轧机机列间的距离 (43)9.2.2 轧机到切断设备的距离 (43)10 各项技术经济指标 (44)结论 (46)参考文献 (47)致谢 (48)附录:车间平面布置图 (49)1 绪论冷轧是指在再结晶温度以下的轧制。
年产200万吨冷轧厂车间设计(毕业设计)

0.50
4.50
10
93.55
10.69
超低碳合金钢 板 超低碳合金钢 卷
0.49
8.70
8
93.32
8.57
0.49
8.55
12
93.53
12.56
合计
200
213.54
• • • • • • • • • • • • • • • • •
年产200万吨的冷轧产品,年需要热轧钢卷213.54万吨。确定冷轧厂所需的热轧原料规格为: 带钢宽度:900~1900mm 带钢宽度:900~1900mm 带钢厚度:1.8~6.0mm 钢卷内径:φ760mm 钢卷外径:φ1200~2150mm 钢卷重量:最大42.1吨 2.1.2原料的技术条件 (1)热轧带钢原料不应有边缘裂口、裂缝或向上弯起90°以上的边缘,边缘整齐,内圈无舌头。 (2)热轧带钢原料不得有扁卷,内圈松≤3圈,外圈松≤1圈,层与层间隙≤10mm。 (3)热轧带钢表面不应有粗划痕及轧入外来杂质,必须脱油、脱脂、无漆。 (4)热轧带钢最大波浪度为: a)厚度1.8—3.0mm带长每2m最大到20mm; b)厚度3.1—4.5mm带长每2m最大到15mm; c)厚度4.6—6.0mm带长每2m最大到10mm。 (5)宽度偏差:0~+20mm。带钢表面不应有超过厚度偏差之半的麻点、凹面、划痕等轻微局部 缺陷,但应保证钢带允许的最小厚度。 (6)凸度:凸度是指垂直轧制方向横截面上,中点厚度与距带钢边部40mm处厚度的差值。
普通碳素钢板
0.47
4.55
30
93.51
32.08
优质碳素钢卷
0.49
4.70
40
93.34
42.85
优质碳素钢
年产150万吨冷轧薄板钢厂生产车间设计毕业设计

年产150万吨冷轧薄板钢厂生产车间设计摘要本设计说明书是参照鞍钢冷轧薄板厂工艺流程,结合现代化生产实际要求设计了年产150万吨冷轧薄板钢厂的生产车间。
该车间的主体设备包括:浅槽酸洗机组、五机架全连续冷轧机组、罩式退火炉、单机架四辊式平整机组、横切、纵切及重卷机组等。
设计时结合各产品的市场前景合理地分配了各产品产量,并且优化了冷轧薄板的生产工艺,绘制了车间平面图。
关键词:冷轧板;退火;车间设计;AbstractThe design specification is modeled Anshan Iron and Steel Cold Rolling Mill process, combined with the practical requirements of modern production design of the annual output of 1.5 million tons cold-rolled sheet steel production workshop.The workshop's main equipment includes: light tank pickling line, the five stand continuous rolling mill, hood-type annealing furnace, single stand four-roller temper mill, cross-cutting, slitting and recoiling unit, etc. Design of future products in the market combined with the rational allocation of production of various products, and optimizes the production process of cold-rolled sheet, draw a workshop plan.Keywords: cold rolled sheet; annealing; plant design目录摘要 ............................................................................................................. I謀荞抟箧飆鐸怼类蒋薔。
年产490万吨热轧板带钢车间设计
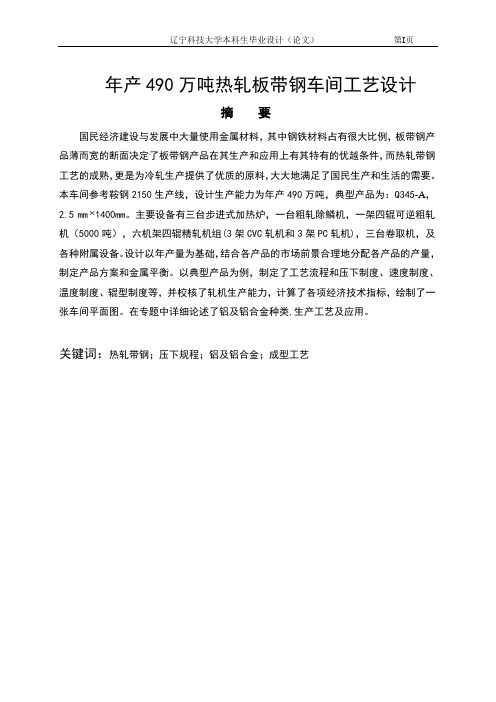
年产490万吨热轧板带钢车间工艺设计摘要国民经济建设与发展中大量使用金属材料,其中钢铁材料占有很大比例,板带钢产品薄而宽的断面决定了板带钢产品在其生产和应用上有其特有的优越条件,而热轧带钢工艺的成熟,更是为冷轧生产提供了优质的原料,大大地满足了国民生产和生活的需要。
本车间参考鞍钢2150生产线,设计生产能力为年产490万吨,典型产品为:Q345-A,2.5 mm 1400mm。
主要设备有三台步进式加热炉,一台粗轧除鳞机,一架四辊可逆粗轧机(5000吨),六机架四辊精轧机组(3架CVC轧机和3架PC轧机),三台卷取机,及各种附属设备。
设计以年产量为基础,结合各产品的市场前景合理地分配各产品的产量,制定产品方案和金属平衡。
以典型产品为例,制定了工艺流程和压下制度、速度制度、温度制度、辊型制度等,并校核了轧机生产能力,计算了各项经济技术指标,绘制了一张车间平面图。
在专题中详细论述了铝及铝合金种类,生产工艺及应用。
关键词:热轧带钢;压下规程;铝及铝合金;成型工艺Annual output of 4.90 million tons of hot rolled flat steelplant process designAbstractLots of metal materials are being used in country’s economic constructions, steel makes up a big proportion,The product of steel strip are widely produced and used because of its special superior function.As its industrial art get close to maturity and provide cold rolled steel strip with raw material of excellent quality,which satisfy requirements of people’s lives. Refering to the 2150 Hot Rolling Strip Steel Plant of An Steel, the designed plant has an annual capability of 4.90millions tons for typical product of Q345-A, 2.5 mm 1400 mm. The maojor facilities include: three walking beam furnaces, one descaling machine for rough rolling, one 4-roll reversing blooming mill (5000 tons), one 6-stand and 6-roll finishing mill group (3 Continuously Variable Crown rolling mills and 3 Pair Cross rolling mills), three coilers, and appurtenances. Considering market prospect, the yield, product scheme, and metal balance of each kind of product are appropriately designed based on the annual plant capacity. For the typical product, the process flow diagram, depressing systerm, velocity system, temperature system, and crown systerm, etc. are determined. Furthermore, the production capacity of the rolling mill is checked, the economic and technical norms are cauculated, and a plane figure for this workshop is drafted. In the chapter of special topic, The species,industrial arts and use of aluminum and its alloy are discussed in detail.Key words: hot rolled steel strip, depressing schedulel, aluminum and its alloy, species and use目录摘要 (I)Abstract....................................................................................................... I I 1综述 (1)1.1热轧板带的发展史 (1)1.2热轧及热轧的现状 (1)1.2.1热轧定义 (1)1.2.2热轧工艺优点 (2)1.2.3热轧工艺不足之处 (2)1.2.4热轧板带的分类 (2)1.2.5热轧板带钢的规格 (3)1.2.6热轧板带钢生产的大体工艺流程 (4)1.2.7 新型轧机简介 (5)1.2.8国内热轧板带的生产现状 (6)1.3热轧及热轧板带生产未来发展方向 (7)1.4 本设计的目的和意义 (8)2 产品方案和金属平衡 (9)2.1 产品方案的编制 (9)2.1.1 产品方案简介 (9)2.1.2 编制产品方案的原则及方法 (9)2.1.3 选择计算产品 (9)2.2产品特点 (10)2.2.1热轧产品品种及产品钢号标准 (10)2.2.2产品质量标准 (11)2.2.3产品性能 (12)2.3确定产品方案 (13)2.4编制金属平衡表 (14)3 主要设备及参数的确定 (16)3.1 加热炉 (16)3.1.1 加热炉的主要结构及特点 (16)3.1.2 加热炉的主要尺寸 (16)3.1.3 加热温度、时间及产量 (17)3.1.4 设备规格 (17)3.2 粗轧主要设备 (17)3.2.1粗轧除鳞装置 (18)3.2.2粗轧机 (18)3.3 精轧主要设备 (19)3.3.1 带坯边部加热器 (20)3.3.2 切头飞剪 (20)3.3.3 精轧除鳞装置 (21)3.3.4 精轧立辊轧机F1E (21)3.3.5 精轧机组轧机 (22)3.4保温装置的选择 (25)3.5层流冷却 (25)3.6卷取设备 (26)3.7生产方案的选择 (29)4 轧制工艺及轧制制度的确定 (30)4.1 生产工艺流程 (30)4.1.1 生产工艺简介 (30)4.1.2 生产工艺流程概述 (30)4.2 加热制度 (31)4.2.1 加热的目的 (31)4.2.2 加热的要求 (32)4.2.3 加热温度的确定 (32)4.2.4 加热时间的确定 (33)4.2.5 加热速度的确定 (33)4.3 压下规程制定 (33)4.3.1 根据产品选择原料 (34)4.3.2 粗轧机组压下制度的制定 (34)4.3.3 精轧机组压下制度的确定 (37)4.3.4 咬入条件校核 (38)4.4 轧制时间制度 (38)4.4.1 粗轧机轧制时间制度 (38)4.4.2 精轧机轧制时间制度 (40)4.4.3 轧机工作图表 (43)4.5 温度制度 (44)4.5.1 粗轧温度制度 (45)4.5.2 精轧温度制度 (46)4.5.3 卷取温度制度 (47)4.6 速度制度 (47)4.6.1粗轧机速度制度 (47)4.6.2精轧机速度制度 (48)4.6.3粗轧各道次的平均变形速度 (50)4.6.4精轧各道次的平均变形速度 (51)4.7 辊型制度 (52)5 生产设备校核 (55)5.1 轧制力与轧制力矩 (55)5.1.1 轧制力的计算 (55)5.1.2 轧制力矩的计算 (56)5.1.3 粗轧与精轧的轧制力和轧制力矩 (56)5.2设备能力参数校核 (57)5.2.1轧制力能参数 (57)5.2.2咬入角校核 (58)5.3 轧辊强度校核 (58)5.3.1 参数计算 (58)5.3.2 轧辊强度校核 (60)5.4 电机功率校核 (66)5.5 年产量计算 (69)5.5.1 工作制度与工作时间 (69)5.5.2 加热炉能力校核 (70)5.5.3轧机生产能力校核 (71)6车间技术经济指标 (74)6.1 概述 (74)6.2 车间各项技术经济指标制定 (75)7 结语 (76)专题:铝及铝合金产品成型工艺 (77)致谢 (88)参考文献 (89)附录A (90)1综述1.1热轧板带的发展史自1926年建成世界上第一台带钢热连轧机以来,它的发展大体上分成四个阶段。
热轧板带轧制规程设计轧钢车间设计
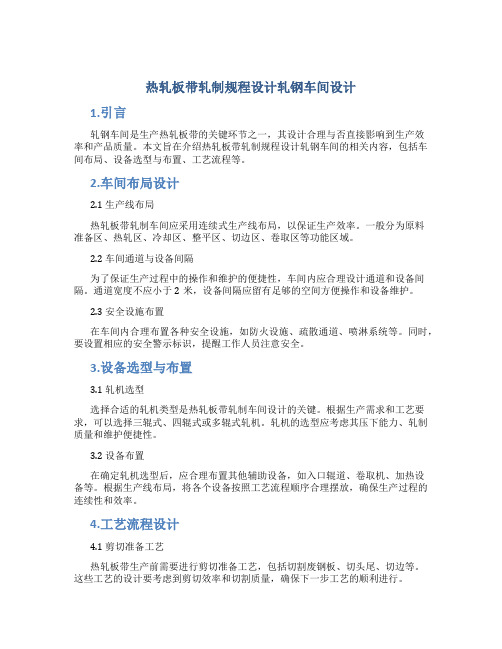
热轧板带轧制规程设计轧钢车间设计1.引言轧钢车间是生产热轧板带的关键环节之一,其设计合理与否直接影响到生产效率和产品质量。
本文旨在介绍热轧板带轧制规程设计轧钢车间的相关内容,包括车间布局、设备选型与布置、工艺流程等。
2.车间布局设计2.1 生产线布局热轧板带轧制车间应采用连续式生产线布局,以保证生产效率。
一般分为原料准备区、热轧区、冷却区、整平区、切边区、卷取区等功能区域。
2.2 车间通道与设备间隔为了保证生产过程中的操作和维护的便捷性,车间内应合理设计通道和设备间隔。
通道宽度不应小于2米,设备间隔应留有足够的空间方便操作和设备维护。
2.3 安全设施布置在车间内合理布置各种安全设施,如防火设施、疏散通道、喷淋系统等。
同时,要设置相应的安全警示标识,提醒工作人员注意安全。
3.设备选型与布置3.1 轧机选型选择合适的轧机类型是热轧板带轧制车间设计的关键。
根据生产需求和工艺要求,可以选择三辊式、四辊式或多辊式轧机。
轧机的选型应考虑其压下能力、轧制质量和维护便捷性。
3.2 设备布置在确定轧机选型后,应合理布置其他辅助设备,如入口辊道、卷取机、加热设备等。
根据生产线布局,将各个设备按照工艺流程顺序合理摆放,确保生产过程的连续性和效率。
4.工艺流程设计4.1 剪切准备工艺热轧板带生产前需要进行剪切准备工艺,包括切割废钢板、切头尾、切边等。
这些工艺的设计要考虑到剪切效率和切割质量,确保下一步工艺的顺利进行。
4.2 加热工艺在热轧过程中,板带需要经过加热设备进行加热处理。
加热工艺的设计要考虑到板带的厚度、材质和加热温度等因素,同时要控制加热时间和加热温度的精确度,以确保板带达到所需的热处理效果。
4.3 轧制工艺轧制工艺是热轧板带车间最关键的环节之一。
在轧制工艺中,要根据板带的厚度、材质和产品要求选择适当的轧辊间隙,控制轧制速度和轧制力度,以获得所需的轧制效果。
4.4 冷却工艺轧制后的板带需要进行冷却以固定产品形状和物理性能。
年产10万吨热轧无缝钢管车间设计

年产10万吨热轧无缝钢管车间设计摘要本设计以包头地区为依据,设计年产量为10万吨的小无缝钢管生产车间,其产品种类包括:油井管、套管、液压支柱用管、锅炉管、结构管等种类。
产品直径范围为Φ60.3mm~Φ159mm,以规格60.3*6.45*11500、139.7*7.72*11500,钢种N80为设计典型产品。
整个设计的重要内容有:原料的选择及产品大纲的制定;轧钢设备的选择及工艺流程的制定;计算部分有轧制表的计算、车间年产量的计算、轧辊力能参数的计算及其校核;车间平面布置与各设备间距的确定;最后根据设计参数绘制了车间平面布置图。
关键词无缝钢管;车间设计;生产工艺Abstract A seamless steel pipe production workshop with annual output 100,000 tons was designed based on Baotou areas.The kinds of profucts include: Oil pipe, casing, hydraulic prop pipe, boiler pipe, structural pipe and so on in this workshop.The diameter of the products range from Φ60.3mm~Φ159mm, and the typical product is N80 steel with the specification of 60.3*6.45*11500 and139.7*7.72*11500. The important content of the design involves: choosing stuff and making The plans of the products; Choosing Rolling mill equipment and making the process of formulation; The aspects of Calculation includes working out rolling Table、production workshop、Rolling force and intension verifying of the roll; planning dispose of the workshop, fixing the space between flown line and the equipment areas; At last, the layout of workshop was drawed according to designing parameters.Key words Seamless steel pipe; Workshop designing; Production technics前言本设计以包头地区为依据,设计年产量10万吨的热轧无缝钢管车间。
轧钢车间设计
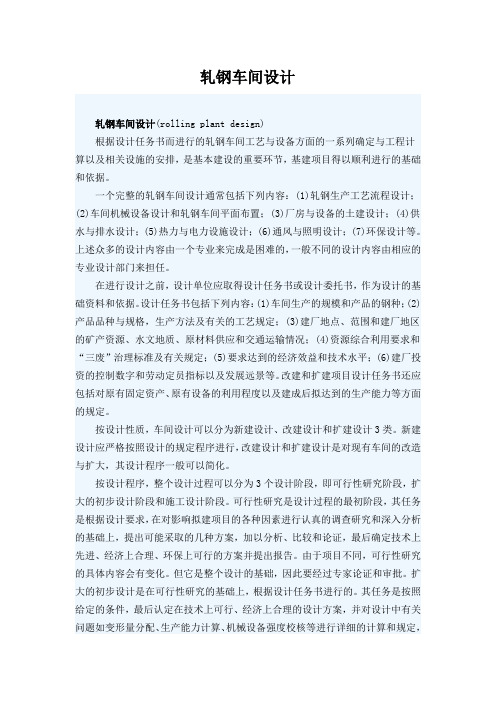
轧钢车间设计轧钢车间设计(rolling plant design)根据设计任务书而进行的轧钢车间工艺与设备方面的一系列确定与工程计算以及相关设施的安排,是基本建设的重要环节,基建项目得以顺利进行的基础和依据。
一个完整的轧钢车间设计通常包括下列内容:(1)轧钢生产工艺流程设计;(2)车间机械设备设计和轧钢车间平面布置;(3)厂房与设备的土建设计;(4)供水与排水设计;(5)热力与电力设施设计;(6)通风与照明设计;(7)环保设计等。
上述众多的设计内容由一个专业来完成是困难的,一般不同的设计内容由相应的专业设计部门来担任。
在进行设计之前,设计单位应取得设计任务书或设计委托书,作为设计的基础资料和依据。
设计任务书包括下列内容:(1)车间生产的规模和产品的钢种;(2)产品品种与规格,生产方法及有关的工艺规定;(3)建厂地点、范围和建厂地区的矿产资源、水文地质、原材料供应和交通运输情况;(4)资源综合利用要求和“三废”治理标准及有关规定;(5)要求达到的经济效益和技术水平;(6)建厂投资的控制数字和劳动定员指标以及发展远景等。
改建和扩建项目设计任务书还应包括对原有固定资产、原有设备的利用程度以及建成后拟达到的生产能力等方面的规定。
按设计性质,车间设计可以分为新建设计、改建设计和扩建设计3类。
新建设计应严格按照设计的规定程序进行,改建设计和扩建设计是对现有车间的改造与扩大,其设计程序一般可以简化。
按设计程序,整个设计过程可以分为3个设计阶段,即可行性研究阶段,扩大的初步设计阶段和施工设计阶段。
可行性研究是设计过程的最初阶段,其任务是根据设计要求,在对影响拟建项目的各种因素进行认真的调查研究和深入分析的基础上,提出可能采取的几种方案,加以分析、比较和论证,最后确定技术上先进、经济上合理、环保上可行的方案并提出报告。
由于项目不同,可行性研究的具体内容会有变化。
但它是整个设计的基础,因此要经过专家论证和审批。
扩大的初步设计是在可行性研究的基础上,根据设计任务书进行的。
- 1、下载文档前请自行甄别文档内容的完整性,平台不提供额外的编辑、内容补充、找答案等附加服务。
- 2、"仅部分预览"的文档,不可在线预览部分如存在完整性等问题,可反馈申请退款(可完整预览的文档不适用该条件!)。
- 3、如文档侵犯您的权益,请联系客服反馈,我们会尽快为您处理(人工客服工作时间:9:00-18:30)。
名词解释1.可行性研究是对所拟建工程项目从有关的各方面进行调查和综合论证,为拟建项目提供科学依据,从而保证所建项目在技术上先进可行,经济上合理有利。
2.初步设计是按设计任务书给定条件,在可行性研究基础上进行的;3.施工设计是按已经批准的初步设计绘制施工图,把设计内容变成施工文件和图纸,据此进行车间建设。
4.成材率——是成品重量与投入的原料重量之比的百分数,成材率是一项重要的技术经济指标,其高低反映了生产组织管理及生产技术水平的高低。
5.轧制图表——轧制图表也称轧制进程表和轧制工作图表,表示和反映了轧制道次和轧制时间之关系的图表。
6.轧机负荷率——轧机的全年实际轧制时间与全年计划轧制时间之比,反映了轧机的是否被充分利用以及设备间的平衡情况7.总图——总平面布置——车间相互位置的关系。
8.生产车间:生产主线;指直接生产各种加工产品的车间. 如型材,管材,板带,棒线生产车间,锻造件及模压件生产车间等9.辅助车间:指为主要生产车间服务的车间。
动力、机修、电修、工模具、计器、中心实验室等10.企业内运——原辅材料、燃料、半成品、成品、废料、废渣等。
(内运主要有辊道、行车、运输小车、升降设备等,运输周转是否灵活可靠,直接影响车间效率)11.产品方案工厂或车间拟生产产品名称,品种,规格,状态以及年计划产量。
由设计任务书规定或设计者调研提出经主管部门批准。
12.金属平衡表是反映某一定时期(一年),制品金属材料的收支情况,是编制工厂或车间生产预算与制定计划、内部与外部运输、以及平面布置的重要数据。
基于成品率及损失率编制。
13.钢轨:一般情况下,30kg/m以下称为轻轨,否则为重轨。
14.经济断面型材:断面形状类似于普通型材,而断面各部分的金属分布更加合理,使用时经济效益高于普通型材。
15.生产工艺流程的共同性:坯料准备⇨加热⇨轧制⇨冷却⇨热处理⇨精整⇨入库16.竖炉(炉身直立,炉内大部装满物料的冶金炉,炉气在炉内向上运动,与炉料之间呈逆流换热。
17.电阻炉(电流通过导体所产生的焦耳热为热源的电炉,分为直接与间接电阻炉。
)18.感应炉(利用物料的感应电热效应而使物料加热或熔化的电炉。
)19.设备台时系数与设备运转系数的乘积称为设备利用系数。
20.轧制图表——表示和反映轧制道次和轧制时间之间的关系的图表。
也称轧制进程表和轧制工作图表21.炉底强度(炉子单位生产率):每平方米炉底布料面积上每小时生产(加热)的量。
22.飞剪——用于横切运行中的金属料23.金属流线——生产各类产品由原料到成品的工艺流程线。
24.跨度(跨距)——车间横向上两柱中心线间距离25.工时定额——完成单位产品所消耗的工时。
26.流动资金——用于购买劳动对象,支付职工工资和产品销售等保证生产经营活动所需要的资金——供、产、销所需资金。
27.储备资金——原、辅材料,燃料,备品备件,包装用品等占用的流动资金;生产资金——从原料投产到产品入库占用资金;成品资金——产品检验入库到产品发送并收到贷款时占用的资金28.C物化劳动——已耗费掉生产资料转移价值,如原、辅材料,燃料,动力,固定资产折旧等。
V 活化劳动——劳动者自身创造的价值(以工资形式分配给劳动者个人和集体消耗的部分。
29.投资回收期自项目正式投产之日起到提供收益总额达到建设投资总额之日所需要的时间(用资金平衡表测算)。
简答论述1.车间工艺设计的内容是什么?根据设计任务书,确定生产工艺过程、确定轧机组成、选择所需各种设备,画出车间工艺平面布置图、确定劳动组织与技术经济指标等。
对与本车间设计有关的所有其他专业设计提出要求以及所需要的资料。
(水、电、动力、热力、通风、照明、采暖、厂房建筑等)2.车间设计的程序是什么?一般分为三个阶段:可行性研究、初步设计和施工设计三个阶段。
(1) 可行性研究是对所拟建工程项目从有关方面进行综合调查和论证,为拟建项目提供科学决策依据;(2) 初步设计是按设计任务书给定条件,在可行性研究基础上进行的;(3) 施工设计是按已经批准的初步设计绘制施工图,把设计内容变成施工文件和图纸,据此进行车间建设。
3.车间设计的步骤是什么?车间设计的步骤:(1)车间设计总论;(2)制定产品方案和选择生产方案;(3)确定生产工艺流程及工艺制度;(4)年工作小时计算;(5)工艺规程设定计算;(6)轧机生产能力计算;(7)主要辅助设备选择和生产能力计算;(8)车间组成及平面布置;(9)环境保护;(10)劳动组织及技术经济指标。
4.可行性研究作用(1)确定建设项目,编制初步设计的基础。
(2)向银行贷款,筹措资金的依据。
(3)有关部门相互签约,互承责任,建立协作关系的依据。
(4)向当地政府申请建设执照的依据。
(5)安排科研和设备试制的依据。
5.可行性研究内容(1)市场需求的情况(有无销路、是否有利);(2)工程条件(原料,资源,厂址气象,水文地质等);(3)技术保障(工艺技术);(4)劳动组织,工程进度;(5)资金和成本;(6)经济效果(投资回收率、返本期及静现值)。
6.可行性研究步骤(1)调研收集资料——写出调查报告(生产工艺;产品品种、产量、规格;国内外市场;销售价格等)(2)资料分析提出方案;(3)方案比较;(4)编制可行性研究报告。
7.分析常见的材料损耗形式及损耗原因?金属消耗量:烧损(含熔损),溶损,切损(含残屑),工艺损失(轧废)等。
8.分析生产方案的选择依据以及比较内容?依据:(1) 材质,品种,规格,状态及质量要求:(2)年产量的大小(单机架或连轧)。
(3) 投资,建设速度,装备水平,劳动条件,定员,及发展规划等。
(4) 国家技术政策。
比较:(1) 生产能力;(2) 产品质量;(3) 维护、操作、装备水平;(4) 投资(设备投资,占地,厂房,辅助设施);(5) 综合效益(节能,降耗,安全,环保,达产周期等)。
9.中厚钢板的生产工艺流程:(板坯)坯料⇒加热⇒除磷⇒两辊粗轧⇒四辊精轧⇒热矫直⇒水冷却⇒冷床⇒矫直⇒分段(取样) ⇒切边⇒定尺剪切⇒检验⇒收集、打印⇒入库10.分析工艺制度的内容?(1) 坯料选择;(2) 坯料准备制度;(3) 加热制度:加热温度、加热速度、加热时间;(4) 变形制度(工艺设计的核心),主要是工艺规程设计——压下规程;孔型辊型设计;工模具设计;(5) 冷却制度:冷却速度和冷却温度制度;(6) 精整制度:矫直,剪切,热处理,平整,表面处理,机加工,检验等。
11.简述轧机布置形式及其特点(可绘图说明)?12.绘制典型钢材冷加工生产工艺流程?13.试确定年产50万吨棒材车间的生产工艺流程。
答:年产50万吨棒材车间的生产工艺流程如下:坯料→加热→粗轧轧制→中轧轧制→精轧轧制→水冷→飞剪剪切→冷却→冷剪→检查→包装→入库14.确定原料为1.0×1500mm,生产成品为0.5×1500 mm薄钢板生产工艺流程。
15.轧机的主要工艺参数是什么?轧辊尺寸、轧制力、轧制速度、轧制温度、轧件的厚度、宽度及压下量、主电机功率及转速等16.车间设计目的:建设新的企业,扩建或改建老企业。
任务:1. 对所设计的车间做出技术和经济的详细规划;2. 确定车间的生产经济状况,技术经济指标及施工组织方案等。
内容:工艺、设备(机械和电控)、土建、水处理、供气、供电、总图运输、采暖和通风、以及概预算和技术经济分析等。
17.设计任务书内容:(1)产品大纲(品种规格,生产规模);生产方案(2)建厂基础条件(厂址、厂区范围、资源、水文地质、燃料、动力、供水、供电、运输等);(3)要达到的经济效益和技术水平;(4)投资和劳动定员控制数字以及环保情况。
18.设计说明书主要内容是:一.总论(前言、综述、概况)(对该产品生产有一全面了解)二.产品方案与金属平衡计算三.生产方案制定及生产工艺流程制定四.工艺制度的制定五.设备选择(初选、精选、确定)六.工艺参数计算工艺规程制定与计算;温度制度;速度制度;张力制度;辊型制度;压力计算;冷却制度七.主要设备校核主要设备校核:轧辊校核;电机校核;机架强度校核等八.车间生产能力计算:轧机工作图表绘制、轧机小时产量计算、轧机年产量计算九.车间平面布置:仓库面积计算十.各项技术经济指标:包括金属消耗、燃料消耗、电耗、水耗、设备消耗、成本等附表附图:车间平面布置图、孔型图、程序、外文翻译、19.板带材产品的技术要求:(1)尺寸精度;(2)板带材版型好;(3)表面质量高;(4)性能要好。
20.生产工艺流程图:三种基本形式1 普碳钢生产工艺流程;2 合金钢生产工艺流程;3 冷加工生产工艺流程。
21.由于连铸坯具有金属消耗少,节能,工艺路线短,节省投资和质量好,成本低等优点22.预先热处理:作用是消除内应力,防止开裂;成分均匀,消除某些合金钢粗大树枝状结晶组织;防止白点产生等.23.提高设备产量的方法(1)合理增加铸锭的质量;(2)缩短轧制节凑(合理分配道次、提高自动化程度);(3)提高成品率。
24.辅助设备选择原则1. 满足生产工艺流程要求;2. 保证有较高的工作效率,充分发挥主设备的能力(大10%~20%);3. 节省投资(重量,占地面积,性能价格比)25.矫直的目的——长度方向矫直;横断面整形;表面氧化铁皮疏松26.车间劳动组织指生产劳动过程中科学地组织人们进行劳动,合理使用劳力,处理好工人之间,工人与领导、工人与劳动对象、工人与劳动手段间的关系而成为一个协调的统一体。
编制车间综合技术经济指标表的意义何在综合评述内容:1. 阐述本设计的优、缺点;2. 结合技术经济指标及现场实际和有关资料验证本设计的正确性,合理性,先进性。
3. 本设计实施后对国民经济所起的作用(国家,地方)。
4. 本设计实施后的经济效益(利润,企业发展),社会效益(税收,供需矛盾)。
5. 其它(如解决就业、下岗职工、资源配置、社会稳定等)技术经济评论是设计效果的总反映,既可表明该设计的优点,又可进一步找出差距,加以改进。
计算题1.计算产品的成材率?A = (Q-W)/Q×100%式中:Q—原料量t,W=金属消耗量(损失量)t。
2.新建300万吨/年热轧板带车间,其产品规格为1.2~12.7×1000~1550mm,精轧机拟采用四辊CVC轧机,最大横移量δ=100mm,试确定轧机组成方案及轧辊辊身长度?解:(1)轧机组成方案:粗轧机组采用两架粗轧机,一架二辊一架四辊,1/2连轧布置;精轧机组采用7机架四辊连轧,CVC轧机(2)工作辊辊身长度:L = Bmax + a,由于Bmax=1550 >1200mm, 所以a=200~400mm,取a =300mm,则求出:L = 1550+300=1850 mm(3)由于精轧机采用四辊CVC轧机工作辊辊身长应增加两倍之横移量,则L = 1850+200=2050 mm3.以热轧六机架连续轧制为例画图说明轧制图表的特点及特征时间?答:热轧六机架连续式轧机的轧制图表如右下图所示,其特点是:(1)通过各机架之金属秒体积流量相等;(2)各道次间的间隙时间随各机架轧机轧制速度的提高而递减,tj1>tj2>------>tjn(3)轧制节奏时间为:T = t zh+ Δt(4)轧制总延续时间为:Tz = t zh +式中t zh为一个道次的纯轧时间,Δt为上根轧完到下根开始轧制的间隙时间。