液压伺服系统设计参考
液压伺服系统
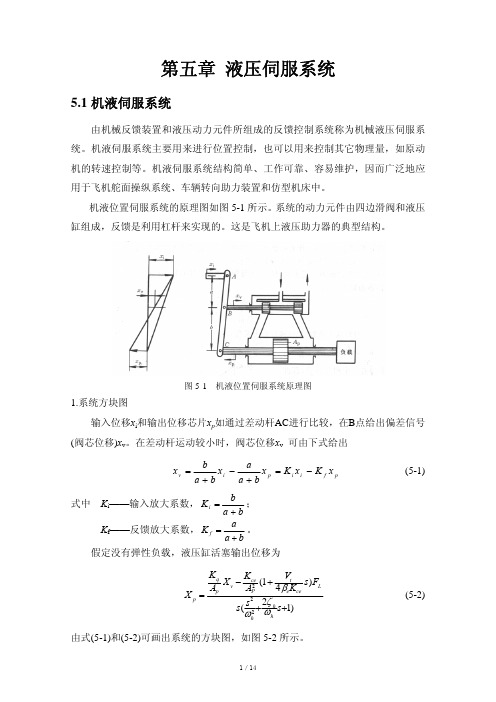
块图可得系统开环传递函数为
G(s)H
(s)
=
Kv s(ωs2h2 +2ωζhh
s+1)
(5-3)
式中
Kv——开环放大系数(也称速度放大系数), K v
=
KqK f Ap
式(5-3)中含有一个积分环节,因此系统是 I 型伺服系统。 由式(5-3)可画出开环系统伯德图,如图 5-3 所示。在ω < ωh 时,低频渐近线是
3.机液位置伺服系统举例 液压仿形刀架是机械液压位置控制系统的典型应用实例,它适用于车、铣、刨、
磨的机械加工。液压仿形刀架工作原理图如图 5-4 所示。
图 5-4 液压仿形刀架工作原理图
在仿形车床上,它可以仿照模板的形状自动加工出各种形状的轴类或旋转体
4/14
工件。它在机械制造业中得到广泛的应用。 (1)液压仿形刀架的结构及其工作原理
由此可知,仿形刀架是一个典型的机械液压位置控制系统。它的输入量是触头 的位移xi,输出量(即被控制量)是液压缸缸体的位移y,伺服阀在该系统中起到了比 较、放大和控制作用,液压缸是系统的执行元件,反馈、检测由杠杆完成。该系 统的工作原理可用图 5-5 职能方框图描述。
图 5-5 液压仿形刀架职能方框图
(5-6)
在设计液压位置伺服系统时,可以把它作为一个经验法则。 由图 5-3 所示的伯德图可以看出,穿越频率近似等于开环放大系数,即
ωc ≈ Kv
(5-7)
实际上ωc 稍大于Kv,而系统的频宽又稍大于ωc 。所以开环放大系数愈大,系统的
响应速度愈快。另外,开环放大系数越大,系统的控制精度也越高。所以要提高
仿生液压四足机器人电液伺服控制系统的设计与研究共3篇
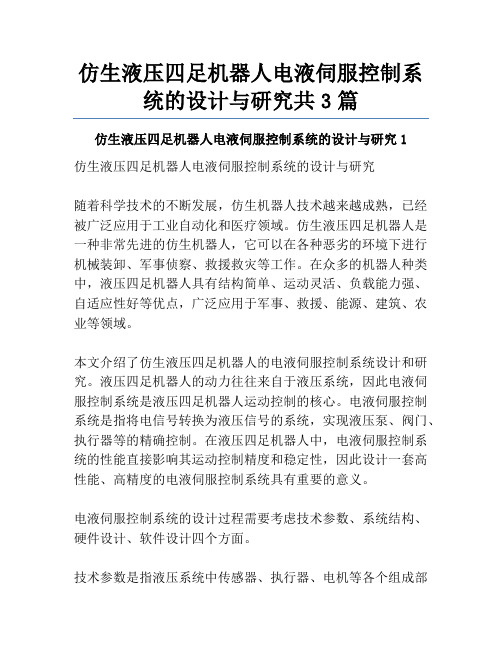
仿生液压四足机器人电液伺服控制系统的设计与研究共3篇仿生液压四足机器人电液伺服控制系统的设计与研究1仿生液压四足机器人电液伺服控制系统的设计与研究随着科学技术的不断发展,仿生机器人技术越来越成熟,已经被广泛应用于工业自动化和医疗领域。
仿生液压四足机器人是一种非常先进的仿生机器人,它可以在各种恶劣的环境下进行机械装卸、军事侦察、救援救灾等工作。
在众多的机器人种类中,液压四足机器人具有结构简单、运动灵活、负载能力强、自适应性好等优点,广泛应用于军事、救援、能源、建筑、农业等领域。
本文介绍了仿生液压四足机器人的电液伺服控制系统设计和研究。
液压四足机器人的动力往往来自于液压系统,因此电液伺服控制系统是液压四足机器人运动控制的核心。
电液伺服控制系统是指将电信号转换为液压信号的系统,实现液压泵、阀门、执行器等的精确控制。
在液压四足机器人中,电液伺服控制系统的性能直接影响其运动控制精度和稳定性,因此设计一套高性能、高精度的电液伺服控制系统具有重要的意义。
电液伺服控制系统的设计过程需要考虑技术参数、系统结构、硬件设计、软件设计四个方面。
技术参数是指液压系统中传感器、执行器、电机等各个组成部分的规格参数。
在该机器人的设计过程中,需要根据机器人运动的需求和工作环境,综合设计机器人的各项技术参数。
其中,执行器的大小、电机的功率、传感器的灵敏度都需要精确计算和匹配,以保证机器人运动控制的稳定性和精度。
系统结构是指电液伺服控制系统中各个组成部分的排布方式,包括电液伺服控制器、液压泵、阀门、执行器、传感器等。
在设计中,需要考虑系统结构的简洁性、紧凑性、功耗等因素,以便于整机的使用和维护。
硬件设计包括电路设计和机械结构设计。
机械结构设计需要考虑机器人的形状、尺寸和材料等,以便于机器人的运动和受载能力。
电路设计则需要根据机器人的应用环境和技术参数,设计控制器、传感器、执行器等电路电子元器件。
软件设计包括程序设计和算法设计。
程序设计是指通过编写程序来实现机器人各种功能的控制,算法设计则是指通过算法来实现机器人的各种自适应控制功能。
电液伺服阀静态特性试验台液压系统设计开题报告2word1

电液伺服阀静态特性实验台液压系统设计一、本课题的项目背景及研究意义电液伺服阀是闭环控制系统中最重要的一种伺服控制元件,它能将微弱的电信号转换成大功率的液压信号(流量和压力)。
用它作转换元件组成的闭环系统称为电液伺服系统。
电液伺服系统用电信号作为控制信号和反馈信号,灵活、快速、方便;用液压元件作执行机构,重量轻、惯量小、响应快、精度高。
对整个系统来说,电液伺服阀是信号转换和功率放大元件;对系统中的液压执行机构来说,电液伺服阀是控制元件;阀本身也是个多级放大的闭环电液伺服系统,提高了伺服阀的控制性能。
因此其性能直接决定和制约着整个电液伺服控制系统的控制精度、响应特性、工作可靠性及寿命。
电液伺服系统是液压伺服系统和电子技术相结合的产物,由于它具有更快的响应速度,更高的控制精度,在军事、航空、航天、机床等领域中得到广泛的应用。
目前,液压伺服系统特别是电液伺服系统己经成为武器自动化和工业自动化的一个重要方面,应用十分广泛。
按照国家有关规定,电液伺服阀出厂或维修以后必须进行性能测试和参数调节,以检验它的质量好坏。
伺服阀用量大的使用单位或重要使用场合,用户应设有伺服阀试验台,以便对新阀性能进行复检,并对使用中的伺服阎定期复检或比较试验。
目前,电液伺服阀性能测试试验台主要有两种类型:一种是传统的手工测试、记录类型;另一种是计算机辅助测试(ComputerAided Test简称CAT)类型。
传统手工测试系统利用按钮、信号发生器、记录仪、示波器等来实现,测试成本高、结构复杂,测试时受人为因素影响大,测试精度低。
随着信号处理技术和计算机技术的发展,出现了一种新型的测试系统,即CAT系统,是建立一套计算机数据采集和数字控制系统,与试验台连接起来,由计算机对各试验参数,如压力、流量、转速、温度等参数进行数据采集、量化和处理并输出测试结果。
在试验过程中,计算机还可以根据数字反馈或人工输入要求,对测试过程进行控制,达到计算机密切跟踪和控制试验台及试件状态的目的,从而高速、高精度地完成对液压产品的性能测试。
液压伺服系统的计算

APC系统的操纵模式及工作参数的运算项目内容
操纵模式
由于压下力专门大,且精度和稳固性要求专门高,因此APC系统一样采纳三通阀—不对称缸操纵模式,即用标准四通伺服阀当三通阀用,压下缸活塞腔受控,活塞杆腔通恒定低压。
低压Pr的作用是轧制时Pr=0.5MPa左右,防止活塞杆腔空吸并吸入灰尘;换辊时使Pr=3MPa左右用于快速提升压下缸。
压下缸放在上支承辊轴承座与压下螺丝(或牌坊顶面)之间时,压下缸倒置,即活塞杆不动,缸体运动。
系统供油压
力Ps
因压下力专门大,为幸免压下缸尺寸、伺服阀流量和供油系统
参数尺寸过大,拟取经济压力;考虑液压元件及伺服阀的额定
压力系列,并考虑到可靠性和爱护水平,取Ps=28MPa
负载压力PL
考虑到压下力专门大,那个地点不可能按常规即最大功率传输
条件取P
L
=(2/3)Ps;但PL也不应过大,
应保证伺服阀阀口上有足够压降,以确保伺服阀的操纵能力,
那个地点取P
L
=23MPa
背压Pr 压下操纵状态取Pr=0.5MPa。
液压伺服、比例控制
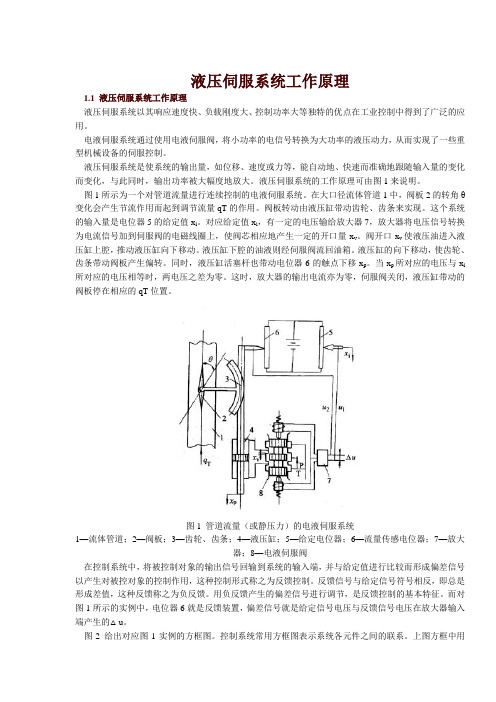
液压伺服系统工作原理1.1 液压伺服系统工作原理液压伺服系统以其响应速度快、负载刚度大、控制功率大等独特的优点在工业控制中得到了广泛的应用。
电液伺服系统通过使用电液伺服阀,将小功率的电信号转换为大功率的液压动力,从而实现了一些重型机械设备的伺服控制。
液压伺服系统是使系统的输出量,如位移、速度或力等,能自动地、快速而准确地跟随输入量的变化而变化,与此同时,输出功率被大幅度地放大。
液压伺服系统的工作原理可由图1来说明。
图1所示为一个对管道流量进行连续控制的电液伺服系统。
在大口径流体管道1中,阀板2的转角θ变化会产生节流作用而起到调节流量qT的作用。
阀板转动由液压缸带动齿轮、齿条来实现。
这个系统的输入量是电位器5的给定值x i。
对应给定值x i,有一定的电压输给放大器7,放大器将电压信号转换为电流信号加到伺服阀的电磁线圈上,使阀芯相应地产生一定的开口量x v。
阀开口x v使液压油进入液压缸上腔,推动液压缸向下移动。
液压缸下腔的油液则经伺服阀流回油箱。
液压缸的向下移动,使齿轮、齿条带动阀板产生偏转。
同时,液压缸活塞杆也带动电位器6的触点下移x p。
当x p所对应的电压与x i 所对应的电压相等时,两电压之差为零。
这时,放大器的输出电流亦为零,伺服阀关闭,液压缸带动的阀板停在相应的qT位置。
图1 管道流量(或静压力)的电液伺服系统1—流体管道;2—阀板;3—齿轮、齿条;4—液压缸;5—给定电位器;6—流量传感电位器;7—放大器;8—电液伺服阀在控制系统中,将被控制对象的输出信号回输到系统的输入端,并与给定值进行比较而形成偏差信号以产生对被控对象的控制作用,这种控制形式称之为反馈控制。
反馈信号与给定信号符号相反,即总是形成差值,这种反馈称之为负反馈。
用负反馈产生的偏差信号进行调节,是反馈控制的基本特征。
而对图1所示的实例中,电位器6就是反馈装置,偏差信号就是给定信号电压与反馈信号电压在放大器输入端产生的△u。
电液控制-机液伺服系统

四、液压转矩放大器
Hale Waihona Puke 反馈机构为 螺杆、螺母 液压马达轴完全跟 踪阀芯输入转角而 转动。但输出力矩 比输入力矩要大得 多,故称液压转矩 放大器。
电液步进马达
以惯性负载为主时,可分析得
方框图为:
则系统方框图为:
§系统稳定性分析
液压伺服系统的动态分析和设计一般都是以稳定性要求为 中心进行的。
令G(s)为前向通道的传递函数,H(s)为反馈通道的传递函 数,由以上的方框图可得系统的开环传递函数为:
含有一个积分环节,故系统为Ⅰ型系统。
可绘制开环系统伯德图,如下图所示:
对伯德图的分析
幅值穿越频率ωc≈Kv 相位穿越频率ωc=ωg 为了使系统稳定, 必须有足够的相位裕 量和增益裕量。 由图可见,相位裕 度已为正值,为使幅 值裕度为正值,可计 算求得要求: K 2
与全闭环系统相比,半闭环系统的稳定性好得多,但精度较低。
综上所述,由于结构柔度的影响,产生了结构谐振和液压谐 振的耦合,使系统出现了频率低、阻尼比小的综合谐振,综合谐 振频率ωn和综合阻尼比ξn常常成为影响系统稳定性和限制系统频 宽的主要因素,因此提高具有重要意义。 提高ωn 就需要提高结构谐振频率ωs,就要求负载惯量减小 (但已由负载特性决定),结构刚度增大(提高安装固定刚度和 传动机构刚度,尤其是靠近负载处的传动机构的结构刚度)。 增大执行元件到负载的传动比,可提高液压固有频率;提高 液压弹簧刚度的方法也可提高液压固有频率,从而提高综合谐振 频率。
反馈从活塞输出端Xp取出时,构成为半闭环系统,其方框图 为:
此时系统开环传函中含有二阶微分环节,当ωs2和ωn靠得很 近时,会有零极点相消现象,使综合谐振峰值减小,从而改善 系统稳定性,如曲线b所示。 系统闭环传函为:
卡特6018AC FS液压电铲电液伺服系统分析

数字应用55产 城卡特6018AC FS 液压电铲电液伺服系统分析袁嘉摘要:液压控制技术是以流体力学、液压传动和液力传动为基础,应用现代控制理论、模糊控制理论,将计算机技术、集成传感器技术应用到液压技术和电子技术中,为实现机械工程自动化或生产现代化而发展起来的一门技术,它广泛的应用于国民经济的各行各业,在农业、化工、轻纺、交通运输、机械制造中都有广泛的应用,尤其在高、新、尖装备中更为突出。
随着机电一体化的进程不断加快,技术装备的工作精度、响应速度和自动化程度的要求不断提高,对液压控制技术的要求也越来越高。
关键词:电液伺服控制系统、 液压传动卡特6018液压电铲是电动马达驱动,各液压泵、液压马达、液压油缸、液压控制阀等组成的大型先进采掘设备。
它主要由电液伺服控制系统、独立液压油冷却系统、独立回转系统、自动集中润滑系统、主泵控制系统等组成,下面重点介绍电液伺服控制系统。
1 电液伺服控制系统原理电液伺服控制系统是以液压动力元件作为驱动装置,采用电子反馈方式实现信号传输和控制的自动控制系统。
在这种系统中,输出量(位移、速度、力等)能够自动地、快速而准确地复现输入量的变化规律。
电液伺服控制系统具有以下优点:功率大、尺寸小、重量轻、加速性能好、控制精度高、响应速度快、稳定性好、使用寿命长等优点。
1、电液伺服控制系统的工作特点:(1)在系统的输出和输入之间存在电子反馈连接,从而组成闭环控制系统。
(2)系统的主反馈是负反馈,即反馈信号与输入信号相反,两者相比较得偏差信号控制液压系统流量,从而输入到液压元件中,使其向减小偏差的方向移动,既以偏差反馈来减小偏差。
(3)系统的输入信号的功率很小,而系统的输出功率可以达到很大。
因此它是一个功率放大装置,功率放大所需的能量由液压能源供给,供给能量的控制是根据伺服系统偏差大小自动进行的。
2、电液伺服控制系统的组成(1)输入元件——也称指令元件,它给出输入信号(指令信号)加于系统的输入端。
液压缸位置伺服控制系统的设计与优化

液压缸位置伺服控制系统的设计与优化液压是一种广泛应用于工业领域的技术,而液压缸作为其中的重要组成部分,起到了控制和传动力的关键作用。
液压缸的位置伺服控制系统设计与优化是一个不断发展的领域,本文将从控制原理、设计方法和优化策略三个方面探讨液压缸位置伺服控制系统的发展和应用。
一、控制原理液压缸的位置伺服控制系统是基于反馈控制原理的。
该系统的目标是通过对液压油的控制,使液压缸的位置达到期望值。
控制器根据外部的输入信号和反馈信息,对液压系统进行控制和调节,以实现位置的精确控制。
在液压缸位置伺服控制系统中,主要采用的控制方式有比例控制、积分控制和微分控制。
比例控制通过调节控制信号与反馈信号之间的比例关系,使系统的响应更为迅速。
积分控制通过积分控制器对误差进行积分,以消除系统的稳态误差。
微分控制则通过微分控制器对误差的变化率进行调节,以提高系统的动态响应性能。
二、设计方法液压缸位置伺服控制系统的设计方法主要包括系统分析、参数选取、控制器设计和系统仿真等步骤。
在系统分析中,需要确定系统的目标、输入和输出,并对系统进行建模和分析。
参数选取则是根据系统的要求和性能指标,选择合适的液压元件和参数数值。
控制器设计是根据系统的特点和需求,设计出合适的控制算法和参数。
系统仿真则是通过软件模拟系统的运行和反馈信息,以评估系统的性能和稳定性。
在液压缸位置伺服控制系统的设计中,还需要考虑到系统的非线性和动态特性。
液压系统的非线性主要体现在油液的粘性、压力和温度对系统性能的影响等方面。
为了解决这些非线性问题,可以采用模糊控制、神经网络控制等方法来调节系统的响应。
而系统的动态特性则需要通过对控制系统的参数进行调节和优化,以提高系统的动态性能和稳定性。
三、优化策略液压缸位置伺服控制系统的优化策略主要包括参数优化、结构优化和控制策略优化。
参数优化是根据系统的性能指标和要求,通过试验和仿真等方法对系统的参数进行调整和优化。
结构优化是通过改变系统的结构和组件,以提高系统的性能和效率。
电液伺服控制课程设计

电液伺服控制课程设计一、课程目标知识目标:1. 理解电液伺服系统的基本原理,掌握其主要组成部分及功能;2. 掌握电液伺服系统的数学模型,了解其动态特性和稳态特性;3. 学会分析电液伺服系统的性能指标,了解影响性能的主要因素;4. 掌握电液伺服系统的控制策略,了解不同控制算法的优缺点。
技能目标:1. 能够运用所学知识对电液伺服系统进行数学建模;2. 能够设计简单的电液伺服控制系统,并进行性能分析;3. 能够运用仿真软件对电液伺服系统进行仿真实验,验证控制策略的有效性;4. 能够对实际电液伺服系统进行调试和优化,提高系统性能。
情感态度价值观目标:1. 培养学生对电液伺服控制系统及其应用的兴趣,激发创新意识;2. 培养学生严谨的科学态度,注重理论与实践相结合;3. 培养学生团队协作精神,提高沟通与交流能力;4. 增强学生对我国液压事业的认同感,树立为国家和民族工业发展贡献力量的信念。
课程性质:本课程为专业技术课程,以理论教学与实践操作相结合的方式展开。
学生特点:学生具备一定的电工电子基础,具有较强的学习能力和动手能力。
教学要求:注重理论联系实际,强化实践教学,提高学生的实际操作能力。
将课程目标分解为具体的学习成果,以便在教学过程中进行有效评估和调整。
二、教学内容1. 电液伺服系统原理及组成部分- 液压基础知识回顾- 电液伺服系统的定义、分类及应用- 主要组成部分(液压泵、液压缸、伺服阀、传感器等)及其功能2. 电液伺服系统的数学建模- 系统的动态方程建立- 系统的稳态方程建立- 模型参数的识别与验证3. 电液伺服系统性能分析- 系统稳定性分析- 系统快速性分析- 系统精确性分析4. 电液伺服控制策略- 常用控制算法(PID控制、模糊控制、自适应控制等)- 控制算法的优缺点分析- 控制策略的设计与优化5. 电液伺服系统仿真与实验- 仿真软件的使用方法- 搭建仿真模型与实验平台- 仿真与实验结果的对比分析6. 电液伺服系统调试与优化- 系统调试方法与技巧- 常见故障分析与处理- 系统性能优化方案教学内容安排与进度:根据课程目标和教材章节,分阶段进行教学,确保内容的系统性和连贯性。
液压伺服与比例控制系统第四章 机液伺服系统

p
c
t
h' =Cc e mt c s = Kd c s
Ap Vt 1 + c s
1 + cs
注:1.稳态情况下,动压反馈环节传递函数趋近于零,对稳态
性能不产生影响。 2.动态过程中,随着负载变化而产生附加阻尼作用,而且
负载压力变化率越大,阻尼作用越明显。
四、动压反馈装置的参数选择问题
附加阻尼比:
经拉氏变换可解得:
V0 s
Qd
1
=
1
p0 + V0
P1 s
Cc p0
同理可解得:
V0 s
Qd
2
=
1
p0 + V0
P2 s
Cc p0
则:
V0 s
( ) Qd 1
Qd
2
= 1
p0 + V0
P1 s
P2
Cc p0
设一个管道的压力升高值等于另一个管道的压力降
低值,则有: Qd 1 = Qd 2 = Qd
原式可写成:
小结
比较元件要求:
1)与指令元件相连;2)与被控对象相连;3)与放大元件相连。
机液伺服系统工作可靠。但是,对参数设计要求较 高,一旦加工完成不易更改 。另外,机械元件有惯 性,时间常数较大 ;机械运动件间总有间隙、摩擦, 工作久了总有磨损,这些都会降低系统的精度。
由于液压动力元件的传递函数式是积分环节加振 荡环节。因此,可以说机液系统的开环传递函数基本 上都是积分加振荡。
影响机液伺服系统稳定性的主要因素: 1 系统开环增益 2 积分环节 3 系统固有频率和阻尼比 4 延时环节和非最小相位环节
4.2 结构柔度对系统稳定性的影响
机电一体化第六章伺服驱动控制系统设计
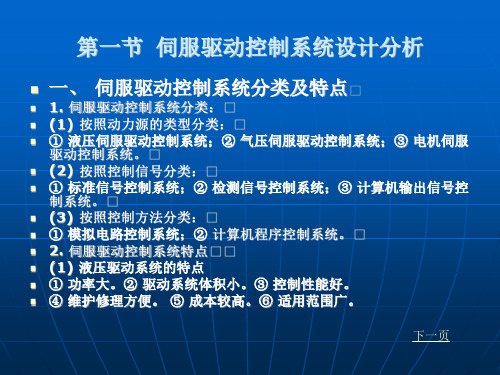
钟。 F.体积小、自定位和价格低是步进电动机驱动控制的三大优势。 G. 步进电机控制系统抗干扰性好
上一页 下一页
二、 伺服驱动控制系统设计的基本要求
1. 高精度控制 2. 3. 调速范围宽、低速稳定性好 4. 快速的应变能力和过载能力强 5. 6.
闭环调节系统。
(4) ①
② 调节方法。
(5) ① 使用仪器。用整定电流环的仪器记录或观察转速实际值波形,电
② 调节方法。
上一页 下一页
六、 晶体管脉宽(PWN)直流调速系统
晶体管脉宽直流调速系统与用频率信号作开关的晶闸管系统相比,具 (1) 由于系统主电源采用整流滤波,因而对电网波形影响小,几乎不 (2) 由于晶体管开关工作频率很高(在2 kHz左右),因此系统的 (3) 电枢电流的脉动量小,容易连续,不必外加滤波电抗器也可平稳 (4) 系统的调速范围很宽,并使传动装置具有较好的线性,采用Z2
上一页 下一页
(2) ① A. 步进电动机型号:130BYG3100D (其他型号干扰大) B. 静转矩15 N·m C. 步距角0.3°/0 6°
D. 空载工作频率40 kHz E. 负载工作频率16 kHz ② A. 驱动器型号ZD-HB30810 B. 输出功率500 W C. 工作电压85~110 V D. 工作电流8 A E. 控制信号,方波电压5~9 V,正弦信号6~15 V ③ 控制信号源。
(3) ① 标准信号控制系统(如图6-16) ②检测信号控制系统 (如图6-17)
③ 计算机控制系统(如图6-18)
上一页 返 回
图6-16 标准信号控制系统图 图6-17 检测信号控制系统图 图6-18 计算机控制系统图
液压伺服系统设计及其性能分析
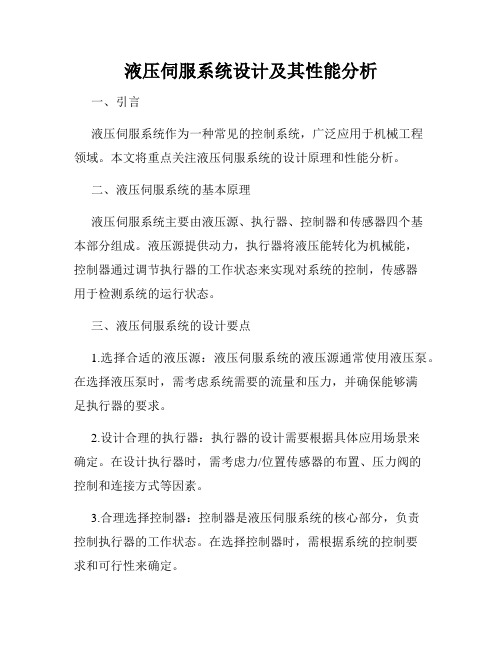
液压伺服系统设计及其性能分析一、引言液压伺服系统作为一种常见的控制系统,广泛应用于机械工程领域。
本文将重点关注液压伺服系统的设计原理和性能分析。
二、液压伺服系统的基本原理液压伺服系统主要由液压源、执行器、控制器和传感器四个基本部分组成。
液压源提供动力,执行器将液压能转化为机械能,控制器通过调节执行器的工作状态来实现对系统的控制,传感器用于检测系统的运行状态。
三、液压伺服系统的设计要点1.选择合适的液压源:液压伺服系统的液压源通常使用液压泵。
在选择液压泵时,需考虑系统需要的流量和压力,并确保能够满足执行器的要求。
2.设计合理的执行器:执行器的设计需要根据具体应用场景来确定。
在设计执行器时,需考虑力/位置传感器的布置、压力阀的控制和连接方式等因素。
3.合理选择控制器:控制器是液压伺服系统的核心部分,负责控制执行器的工作状态。
在选择控制器时,需根据系统的控制要求和可行性来确定。
4.传感器的选择与布置:传感器用于检测系统的运行状态,根据不同的应用场景选择合适的传感器,并合理布置以提高系统的控制精度。
四、液压伺服系统性能分析1.系统的动态响应性能:液压伺服系统的动态响应性能是指系统对外界输入信号的响应速度。
通过理论计算和实验测试,可以评估系统的响应时间、过渡过程和稳态性能等指标。
2.系统的稳态精度:液压伺服系统的稳态精度是指系统在稳定工作状态下输出信号与输入信号之间的偏差。
通常通过分析系统应力平衡和输出信号的稳定性来评估系统的稳态精度。
3.系统的稳定性分析:液压伺服系统的稳定性是指系统在各种工况下能够保持稳定工作状态的能力。
通过分析系统的传递函数和伯努利方程等理论,可以评估系统的稳定性。
4.系统的能效分析:液压伺服系统的能效是指系统在输入输出之间的能量转换效率。
通过分析系统的功率损失和效率等指标,可以评估系统的能效。
五、结论液压伺服系统的设计和性能分析是提高系统运行效率和工作质量的重要步骤。
通过合理选择液压源、设计合理的执行器、选择合适的控制器和传感器,并对系统的动态响应性能、稳态精度、稳定性和能效进行全面分析,可以有效提升液压伺服系统的性能。
液压伺服系统电液伺服系统课件
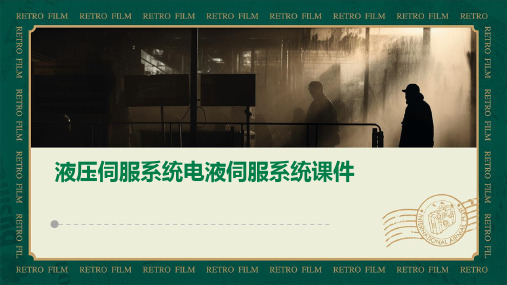
随着科技的不断发展,液压伺服系统也在不断创新和完善。未来,液压伺服系统将朝着智能化、数字 化、网络化方向发展,实现更高效、更精准的控制。同时,液压伺服系统还将更加注重环保和节能, 推动绿色制造和可持续发展。
02 电液伺服系统基础知识
电液转换元件
01
02
03
伺服阀
将电气信号转换为液压流 量或压力,实现液压执行 机构的精确控制。
速度同步
采用液压伺服系统实现多工位、多执行机构的速 度同步,优化生产流程。
航空航天领域中的应用
飞机起落架收放系统
通过电液伺服系统实现飞机起落架的平稳收放,确保飞行安全。
发动机推力控制
利用液压伺服系统对航空发动机进行精确的推力控制,提高飞行 性能。
飞行姿态调整
采用电液伺服系统实现飞行姿态的快速、精确调整,满足复杂飞 行需求。
仿真分析
在系统模型的基础上,进行仿真分析,包括系统动态响应、控制精度、稳定性等方面的评估,以验证设计的合理性。
优化设计
根据仿真分析结果,对系统进行优化设计,包括调整元件参数、改进控制策略等,以提高系统性能。
04 电液伺服系统实现技术
硬件平台搭建
控制器选择
根据系统需求,选用合适的控制器,如PLC、DSP等,确保控制精 度和实时性。
元件选型与计算
元件选型
根据规格书要求,选择合适的液压泵 、马达、阀等元件,确保系统性能达 标。
元件计算
对所选元件进行详细的计算和分析, 包括流量、压力、功率等参数,确保 元件之间的匹配性和系统的稳定性。
系统仿真与优化
系统建模
利用AMESim、MATLAB/Simulink等仿真软件,建立液压伺服系统的数学模型,为后续仿真分析提供基础。
液压系统技术方案

(4.12) (4.13 )
第 5 页 共 32 页
QL—阀的负载流量 W—功放级滑阀的面积梯度或面积增益
—油液密度
Cd—流量系数 xv—阀芯位移 Ps—供油压力
从上面的分析可知,由于阀的压力――流量特性方程 QL f ( pL , xv ) 是一个非线
性方程,所以阀控液压控制系统实际上是一个高度非线性系统。对于高度非线性系统
来说,线性化分析方法是工程上一种行之有效的方法。
考虑到闭环系统工作时,伺服阀总是工作在平衡点(例如零点)附近,因此,我们
采用传统的小增量线性化分析方法,得线性增量方程:
QL K q xv K c pL
(4.14)
式中:流量放大系数 K q
QL xv
A
流量一压力放大系数 K c
QL pL
A
压力放大系数 K p
pL xv
A
KQ Kc
4.4.2 振动缸的特性分析
4.4.2.1 振动缸的流量连续方程
振动缸是把液体的压力能转换成机械能,用来驱动焊件作直线运动的液压执行元
件,其输入参量为液体压力和液体流量,输出参数为液压缸的运动速度、力和输出功
率等。
本系统中,缸体固定,活塞运动。当液压缸输出力与负载相等,且输入的液体流
本系统选用的 MOOG 阀,基本结构如图 6 所示。
图 6 高频电液伺服阀的基本结构 该阀为三级阀,先导阀为二级喷嘴挡板阀,功率阀由先导阀驱动,其阀芯上装有 位移传感器,用来检测阀芯位置,实行外部电反馈。 4.4.1.2 电液伺服阀的动态特性 在液压伺服系统中,输入输出信号一般常为变化的信号,伺服阀一般也并不工作 在静态,因此,其动态特性非常重要。 从自动控制的观点来看,伺服阀是一个高度复杂的装置,具有高阶的非线性动态 特性。因此,用一阶、二阶、甚至三阶传递函数描述伺服阀的动态特性,也仅仅是对 伺服阀实际动态特性的一个近似等效。 在大多数电液伺服阀系统中,伺服阀的动态响应往往高于系统负载的动态响应。 因此,在分析系统动态特性时,只需要知道在一个适当的低频段内的伺服阀动态特性,
带钢卷曲机纠偏液压伺服控制系统设计共27页
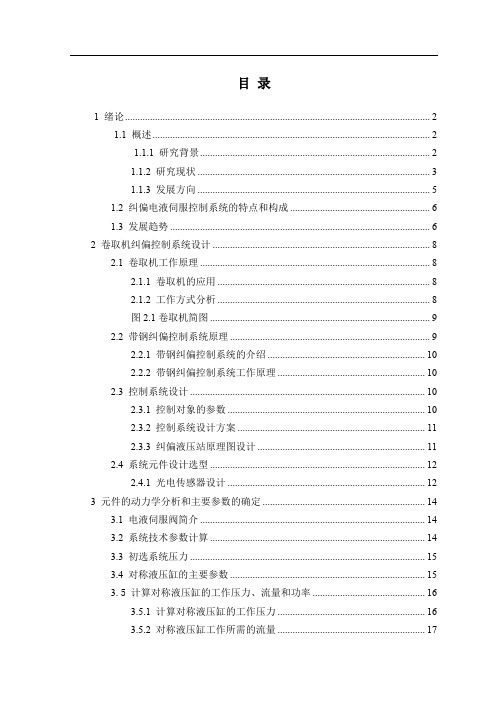
目录1 绪论 (2)1.1 概述 (2)1.1.1 研究背景 (2)1.1.2 研究现状 (3)1.1.3 发展方向 (5)1.2 纠偏电液伺服控制系统的特点和构成 (6)1.3 发展趋势 (6)2 卷取机纠偏控制系统设计 (8)2.1 卷取机工作原理 (8)2.1.1 卷取机的应用 (8)2.1.2 工作方式分析 (8)图2.1卷取机简图 (9)2.2 带钢纠偏控制系统原理 (9)2.2.1 带钢纠偏控制系统的介绍 (10)2.2.2 带钢纠偏控制系统工作原理 (10)2.3 控制系统设计 (10)2.3.1 控制对象的参数 (10)2.3.2 控制系统设计方案 (11)2.3.3 纠偏液压站原理图设计 (11)2.4 系统元件设计选型 (12)2.4.1 光电传感器设计 (12)3 元件的动力学分析和主要参数的确定 (14)3.1 电液伺服阀简介 (14)3.2 系统技术参数计算 (14)3.3 初选系统压力 (15)3.4 对称液压缸的主要参数 (15)3.5 计算对称液压缸的工作压力、流量和功率 (16)3.5.1 计算对称液压缸的工作压力 (16)3.5.2 对称液压缸工作所需的流量 (17)3.5.3 计算对称液压缸的输出功率 (17)3.6 液压控制系统动力元件参数的确定 (17)3.6.1 确定动力元件(伺服阀)参数 (17)3.6.2 动力元件(伺服阀)的选择 (18)3.6.3 液压泵及电机的选型 (18)3.6.4 液压阀的选型 (18)3.7 液压辅件的设计计算与选型 (19)3.7.1 油箱的设计 (19)3.7.2 阀块的设计 (20)3.7.3 管道尺寸的确定 (21)3.7.4 其它元件的选型 (22)3.7.5 液压油的选用 (22)参考文献 (24)1绪论1.1概述电液伺服阀是闭环控制系统中最重要的一种伺服控制元件,它能将微弱的电信号转换成大功率的液压信号(流量和压力)。
液压伺服千斤顶系统设计

摘要:所设计的四顶顶升系统的主要参数是每只千斤顶高约1000mm,最大行程为400mm,最大载荷为20t。
因千斤顶载荷较大,位置精度要求较高,故顶升速度不宜过大,最大顶升速度应控制在60mm/min以内。
工作原理是,二位四通电磁换向阀的电磁铁的工作状态是由单片机控制的,当换向阀电磁铁通电时,换向阀左位接入系统,油液经电磁换向阀和平衡阀进入油缸下腔,使得千斤顶上升,再从油缸上腔流出,经电磁换向阀和滤油器流回到油箱内,这时平衡阀的作用相当于一个单向阀;反之,当换向阀电磁铁断电时,换向阀右位接入系统,油液经换向阀流入油缸上腔,当上腔压力达到一定值时,平衡阀上位接入系统,这时平衡阀的作用相当于一个节流阀,油液从油缸下腔流出,经平衡阀、电磁换向阀和滤油器流回到油箱。
从而实现了千斤顶升降换向功能,并具有过载保护和断电保护的功能。
为了适应复杂工作表面的工件,千斤顶的工作台与活塞杆应采用转动连接副相连当顶升系统工作时,液压千斤顶工作台可随工件表面形状进行自由转动调节,所以设计时将活塞杆顶部插入球头,与工作台形成转动副。
由于光栅尺的尺寸较长,将活塞和活塞杆做成中空状来放置光栅。
工作时发光元件与光敏元件随活塞作同步运动,光栅尺下端固定在底盖上不动,光源与光栅尺的相对位移量通过读数头转化为数字信号传递给单片机。
关键词:四顶同步顶升单片机光栅目录1. 引言 (3)1.1 选题的依据及课题的意义 (4)1.2 国内外的研究概况 (4)1.3 单片机控制系统的发展概况 (5)1.4 PID控制算法的发展概况 (7)1.5 设计要求及工作内容 (8)1.6 目标、主要特色及工作进度 (8)2.机械结构与液压传动系统设计 (8)2.1系统结构分析 (9)2.2 千斤顶零部件分析 (11)2.3 油缸与螺纹的校验 (14)2.3.1油缸的壁厚校验 (14)2.3.2 锁母螺纹牙剪切强度校验 (14)2.3.3锁母螺纹牙的弯曲强度校验 (15)2.4 液压系统分析 (16)2.5 液压泵与电动机的选择 (17)2.6 超高压泵站简介 (18)3 . 单片机控制系统设计 (19)3.1 单片机的选用及功能介绍 (19)3.2 片外存储器功能简介 (20)3.3 显示部分设计 (23)3.4 键盘部分设计 (26)3.5 交流异步电动机变频调速系统 (29)3.5.1 交流异步电动机变频调速原理 (29)3.5.2主电路和逆变电路工作原理 (30)3.5.3 变频与变压 (33)3.6 位移检测部分的设计 (40)3.6.1 位移检测传感器的选用 (40)3.6.2 光栅位移传感器与单片机的接口设计 (41)3.7 位移传感器部分的设计 (45)3.7.1 A/D转换器的选择 (45)3.7.2 压力传感器与单片机的接口设计 (49)4.系统的PID控制算法 (50)4.1 PID控制原理 (50)4.2 数字PID控制算法 (52)4.2.1 位置式PID控制算法 (52)4.2.2 增量式PID控制算法 (53)4.3 智能自适应PID控制器 (54)5. 系统模拟仿真 (59)5.1 SIMULINK概述 (60)5.2 SIMULINK的窗口和菜单 (60)5.3 用SIMUINK创建模型 (62)5.4 用SIMULINK进行系统仿真与分析 (63)5.4.1 建立控制系统模型 (63)5.4.2 系统模块参数设置与仿真参数设置 (64)5.4.3 系统仿真与分析 (66)6.结论 (69)7.致谢 (70)8. 参考文献 (70)1. 引言1.1 选题的依据及课题的意义随着现代社会的不断发展,工业化程度的不断深入,大尺寸、大重量、不规则表面的工件越来越多的成为工厂加工的对象。
基于ATmega16L的电液伺服控制系统设计

基于ATmega16L的电液伺服控制系统设计李禹萱;李云红【摘要】针对电液伺服闭环控制过程中,设定信号不断发生变化,电液阀门位置定位精确度较低的难题.采用AT-mega16L作为核心控制器,并配有高精度A/D、D/A 转换器,通过对阀门开度控制信号和位置反馈信号进行采集、转换、计算和比较,发出控制信号决定并执行换向阀的换向、交流伺服电动机的起停运转,推动液压缸推杆的伸缩,进而对阀门转角大小、开度百分比进行精确定位.%In the process of electro-hydraulic servo closed loop control, set signals are constantly changing and electro-hydraulic valve location accuracy is low. Through the acqusitiion, transformation, calculation and comparison of signals to control valve opening and position feedback signals, the system with ATmegal6L as the core controller, equipped with high-precision A/D and D/A converters, sends a control signal to determine and perform the reversing of reversing valve and the operation of AC servomotor, promote the stretching of hydraulic cylinder rod, and thus realizes the precise position of the valve angle size and the opening percentage.【期刊名称】《现代电子技术》【年(卷),期】2012(035)019【总页数】4页(P141-144)【关键词】单片机微处理器;伺服控制;阀门位置;RS 485通信【作者】李禹萱;李云红【作者单位】西安电子科技大学机电工程学院,陕西西安710126;西安工程大学电子信息学院,陕西西安710048【正文语种】中文【中图分类】TN911.7-34;TP2730 引言随着电力电子技术、电机控制技术、计算机技术和传感器技术的发展,交流伺服控制技术已逐步取代了传统的直流控制技术,越来越多地应用到各种工业控制领域中。
- 1、下载文档前请自行甄别文档内容的完整性,平台不提供额外的编辑、内容补充、找答案等附加服务。
- 2、"仅部分预览"的文档,不可在线预览部分如存在完整性等问题,可反馈申请退款(可完整预览的文档不适用该条件!)。
- 3、如文档侵犯您的权益,请联系客服反馈,我们会尽快为您处理(人工客服工作时间:9:00-18:30)。
液压伺服系统设计液压伺服系统设计在液压伺服系统中采用液压伺服阀作为输入信号的转换与放大元件。
液压伺服系统能以小功率的电信号输入,控制大功率的液压能(流量与压力)输出,并能获得很高的控制精度和很快的响应速度。
位置控制、速度控制、力控制三类液压伺服系统一般的设计步骤如下:1)明确设计要求:充分了解设计任务提出的工艺、结构及时系统各项性能的要求,并应详细分析负载条件。
2)拟定控制方案,画出系统原理图。
3)静态计算:确定动力元件参数,选择反馈元件及其它电气元件。
4)动态计算:确定系统的传递函数,绘制开环波德图,分析稳定性,计算动态性能指标。
5)校核精度和性能指标,选择校正方式和设计校正元件。
6)选择液压能源及相应的附属元件。
7)完成执行元件及液压能源施工设计。
本章的内容主要是依照上述设计步骤,进一步说明液压伺服系统的设计原则和介绍具体设计计算方法。
由于位置控制系统是最基本和应用最广的系统,所以介绍将以阀控液压缸位置系统为主。
4.1 全面理解设计要求4.1.1 全面了解被控对象液压伺服控制系统是被控对象—主机的一个组成部分,它必须满足主机在工艺上和结构上对其提出的要求。
例如轧钢机液压压下位置控制系统,除了应能够承受最大轧制负载,满足轧钢机轧辊辊缝调节最大行程,调节速度和控制精度等要求外,执行机构—压下液压缸在外形尺寸上还受轧钢机牌坊窗口尺寸的约束,结构上还必须保证满足更换轧辊方便等要求。
要设计一个好的控制系统,必须充分重视这些问题的解决。
所以设计师应全面了解被控对象的工况,并综合运用电气、机械、液压、工艺等方面的理论知识,使设计的控制系统满足被控对象的各项要求。
4.1.2 明角设计系统的性能要求1)被控对象的物理量:位置、速度或是力。
2)静态极限:最大行程、最大速度、最大力或力矩、最大功率。
3)要求的控制精度:由给定信号、负载力、干扰信号、伺服阀及电控系统零飘、非线性环节(如摩擦力、死区等)以及传感器引起的系统误差,定位精度,分辨率以及允许的飘移量等。
4)动态特性:相对稳定性可用相位裕量和增益裕量、谐振峰值和超调量等来规定,响应的快速性可用载止频率或阶跃响应的上升时间和调整时间来规定;5)工作环境:主机的工作温度、工作介质的冷却、振动与冲击、电气的噪声干扰以及相应的耐高温、防水防腐蚀、防振等要求;6)特殊要求;设备重量、安全保护、工作的可靠性以及其它工艺要求。
4.1.3 负载特性分析正确确定系统的外负载是设计控制系统的一个基本问题。
它直接影响系统的组成和动力元件参数的选择,所以分析负载特性应尽量反映客观实际。
液压伺服系统的负载类型有惯性负载、弹性负载、粘性负载、各种摩擦负载(如静摩擦、动摩擦等)以及重力和其它不随时间、位置等参数变化的恒值负载等。
4.2 拟定控制方案、绘制系统原理图在全面了解设计要求之后,可根据不同的控制对象,按表6所列的基本类型选定控制方案并拟定控制系统的方块图。
如对直线位置控制系统一般采用阀控液压缸的方案,方块图如图36所示。
图36 阀控液压缸位置控制系统方块图4.3 动力元件参数选择动力元件是伺服系统的关键元件。
它的一个主要作用是在整个工作循环中使负载按要求的速度运动。
其次,它的主要性能参数能满足整个系统所要求的动态特性。
此外,动力元件参数的选择还必须考虑与负载参数的最佳匹配,以保证系统的功耗最小,效率高。
动力元件的主要参数包括系统的供油压力、液压缸的有效面积(或液压马达排量)、伺服阀的流量。
当选定液压马达作执行元件时,还应包括齿轮的传动比。
4.3.1 供油压力的选择选用较高的供油压力,在相同输出功率条件下,可减小执行元件——液压缸的活塞面积(或液压马达的排量),因而泵和动力元件尺寸小重量轻,设备结构紧凑,同时油腔的容积减小,容积弹性模数增大,有利于提高系统的响应速度。
但是随供油压力增加,由于受材料强度的限制,液压元件的尺寸和重量也有增加的趋势,元件的加工精度也要求提高,系统的造价也随之提高。
同时,高压时,泄漏大,发热高,系统功率损失增加,噪声加大,元件寿命降低,维护也较困难。
所以条件允许时,通常还是选用较低的供油压力。
常用的供油压力等级为7MPa到28MPa,可根据系统的要求和结构限制条件选择适当的供油压力。
4.3.2 伺服阀流量与执行元件尺寸的确定如上所述,动力元件参数选择除应满足拖动负载和系统性能两方面的要求外,还应考虑与负载的最佳匹配。
下面着重介绍与负载最佳匹配问题。
(1)动力元件的输出特性将伺服阀的流量——压力曲线经坐标变换绘于υ-F L平面上,所得的抛物线即为动力元件稳态时的输出特性,见图37。
图37 参数变化对动力机构输出特性的影响a)供油压力变化;b)伺服阀容量变化;c)液压缸面积变化图中 F L——负载力,F L=p L A;p L——伺服阀工作压力;A——液压缸有效面积;υ——;液压缸活塞速度,q L——伺服阀的流量;q0——伺服阀的空载流量;p s——供油压力。
由图37可见,当伺服阀规格和液压缸面积不变,提高供油压力,曲线向外扩展,最大功率提高,最大功率点右移,如图37a。
当供油压力和液压缸面积不变,加大伺服阀规格,曲线变高,曲线的顶点A p s不变,最大功率提高,最大功率点不变,如图37b。
当供油压力和伺服阀规格不变,加大液压缸面积A,曲线变低,顶点右移,最大功率不变,最大功率点右移,如图37c。
(2)负载最佳匹配图解法在负载轨迹曲线υ-F L平面上,画出动力元件输出特性曲线,调整参数,使动力元件输出特性曲线从外侧完全包围负载轨迹曲线,即可保证动力元件能够拖动负载。
在图38中,曲线1、2、3代表三条动力元件的输出特性曲线。
曲线2与负载轨迹最大功率点c 相切,符合负载最佳匹配条件,而曲线1、3上的工作点α和b,虽能拖动负载,但效率都较低。
(3)负载最佳匹配的解析法参见液压动力元件的负载匹配。
(4)近似计算法在工程设计中,设计动力元件时常采用近似计算法,即按最大负载力F Lmax选择动力元件。
在动力元件输出特性曲线上,限定F Lmax≤p L A=,并认为负载力、最大速度和最大加速度是同时出现的,这样液压缸的有效面积可按下式计算:(37)图38 动力元件与负载匹配图形按式37求得A值后,可计算负载流量q L,即可根据阀的压降从伺服阀样本上选择合适的伺服阀。
近似计算法应用简便,然而是偏于保守的计算方法。
采用这种方法可以保证系统的性能,但传递效率稍低。
(5)按液压固有频率选择动力元件对功率和负载很小的液压伺服系统来说,功率损耗不是主要问题,可以根据系统要求的液压固有频率来确定动力元件。
四边滑阀控制的液压缸,其活塞的有效面积为(38)二边滑阀控制的液压缸,其活塞的有效面积为(39)液压固有频率ωh可以按系统要求频宽的(5~10)倍来确定。
对一些干扰力大,负载轨迹形状比较复杂的系统,不能按上述的几种方法计算动力元件,只能通过作图法来确定动力元件。
计算阀控液压马达组合的动力元件时,只要将上述计算方法中液压缸的有效面积A 换成液压马达的排量D,负载力F L换成负载力矩T L,负载速度换成液压马达的角速度,就可以得到相应的计算公式。
当系统采用了减速机构时,应注意把负载惯量、负载力、负载的位移、速度、加速度等参数都转换到液压马达的轴上才能作为计算的参数。
减速机构传动比选择的原则是:在满足液压固有频率的要求下,传动比最小,这就是最佳传动比。
4.3.3 伺服阀的选择根据所确定的供油压力p s和由负载流量q L(即要求伺服阀输出的流量)计算得到的伺服阀空载流量q0,即可由伺服阀样本确定伺服阀的规格。
因为伺服阀输出流量是限制系统频宽的一个重要因素,所以伺服阀流量应留有余量。
通常可取15%左右的负载流量作为伺服阀的流量储备。
除了流量参数外,在选择伺服阀时,还应考虑以下因素:1)伺服阀的流量增益线性好。
在位置控制系统中,一般选用零开口的流量阀,因为这类阀具有较高的压力增益,可使动力元件有较大的刚度,并可提高系统的快速性与控制精度。
2)伺服阀的频宽应满足系统频宽的要求。
一般伺服阀的频宽应大于系统频宽的5倍,以减小伺服阀对系统响应特性的影响。
3)伺服阀的零点漂移、温度漂移和不灵敏区应尽量小,保证由此引起的系统误差不超出设计要求。
4)其它要求,如对零位泄漏、抗污染能力、电功率、寿命和价格等,都有一定要求。
4.3.4 执行元件的选择液压伺服系统的执行元件是整个控制系统的关键部件,直接影响系统性能的好坏。
执行元件的选择与设计,除了按本节所述的方法确定液压缸有效面积A(或液压马达排量D)的最佳值外,还涉及密封、强度、摩擦阻力、安装结构等问题。
4.4 反馈传感器的选择根据所检测的物理量,反馈传感器可分为位移传感器、速度传感器、加速度传感器和力(或压力)传感器。
它们分别用于不同类型的液压伺服系统,作为系统的反馈元件。
闭环控制系统的控制精度主要决定于系统的给定元件和反馈元件的精度,因此合理选择反馈传感器十分重要。
传感器的频宽一般应选择为控制系统频宽的5~10倍,这是为了给系统提供被测量的瞬时真值,减少相位滞后。
传感器的频宽对一般系统都能满足要求,因此传感器的传递函数可近似按比例环节来考虑。
4.5 确定系统方块图根据系统原理图及系统各环节的传递函数,即可构成系统的方块图。
根据系统的方块图可直接写出系统开环传递函数。
阀控液压缸和阀控液压马达控制系统二者的传递函数具有相同的结构形式,只要把相应的符号变换一下即可。
4.6 绘制系统开环波德图并确定开环增益系统的动态计算与分析在这里是采用频率法。
首先根据系统的传递函数,求出波德图。
在绘制波德图时,需要确定系统的开环增益K。
改变系统的开环增益K时,开环波德图上幅频曲线只升高或降低一个常数,曲线的形状不变,其相频曲线也不变。
波德图上幅频曲线的低频段、穿越频率以及幅值增益裕量分别反映了闭环系统的稳态精度、截止频率及系统的稳定性。
所以可根据闭环系统所要求的稳态精度、频宽以及相对稳定性,在开环波德图上调整幅频曲线位置的高低,来获得与闭环系统要求相适应的K值。
4.6.1 由系统的稳态精度要求确定K由控制原理可知,不同类型控制系统的稳态精度决定于系统的开环增益。
因此,可以由系统对稳态精度的要求和系统的类型计算得到系统应具有的开环增益K。
4.6.2由系统的频宽要求确定K分析二阶或三阶系统特性与波德图的关系知道,当ζh和K/ωh都很小时,可近似认为系统的频宽等于开环对数幅值曲线的穿越频率,即ω-3dB≈ωc,所以可绘制对数幅频曲线,使ωc在数值上等于系统要求的ω-3dB值,如图39所示。
由此图可得K值。
图39 由ω-3dB绘制开环对数幅频特性a)0型系统;b)I型系统4.6.3 由系统相对稳定性确定K系统相对稳定性可用幅值裕量和相位裕量来表示。