邹伟斌中国水泥工业水泥粉磨系统现状调查分析(连载二)
水泥联合粉磨系统调试中出现的问题及处理措施
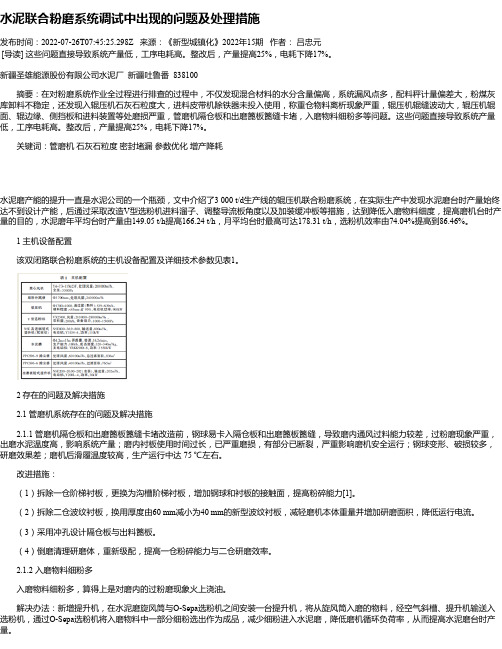
水泥联合粉磨系统调试中出现的问题及处理措施发布时间:2022-07-26T07:45:25.298Z 来源:《新型城镇化》2022年15期作者:吕忠元[导读] 这些问题直接导致系统产量低,工序电耗高。
整改后,产量提高25%,电耗下降17%。
新疆圣雄能源股份有限公司水泥厂新疆吐鲁番 838100摘要:在对粉磨系统作业全过程进行排查的过程中,不仅发现混合材料的水分含量偏高,系统漏风点多,配料秤计量偏差大,粉煤灰库卸料不稳定,还发现入辊压机石灰石粒度大,进料皮带机除铁器未投入使用,称重仓物料离析现象严重,辊压机辊缝波动大,辊压机辊面、辊边缘、侧挡板和进料装置等处磨损严重,管磨机隔仓板和出磨篦板篦缝卡堵,入磨物料细粉多等问题。
这些问题直接导致系统产量低,工序电耗高。
整改后,产量提高25%,电耗下降17%。
关键词:管磨机石灰石粒度密封堵漏参数优化增产降耗水泥磨产能的提升一直是水泥公司的一个瓶颈,文中介绍了3 000 t/d生产线的辊压机联合粉磨系统,在实际生产中发现水泥磨台时产量始终达不到设计产能,后通过采取改造V型选粉机进料溜子、调整导流板角度以及加装缓冲板等措施,达到降低入磨物料细度,提高磨机台时产量的目的,水泥磨年平均台时产量由149.05 t/h提高166.24 t/h,月平均台时最高可达178.31 t/h,选粉机效率由74.04%提高到86.46%。
1 主机设备配置该双闭路联合粉磨系统的主机设备配置及详细技术参数见表1。
2 存在的问题及解决措施 2.1 管磨机系统存在的问题及解决措施2.1.1 管磨机隔仓板和出磨篦板篦缝卡堵改造前,钢球易卡入隔仓板和出磨篦板篦缝,导致磨内通风过料能力较差,过粉磨现象严重,出磨水泥温度高,影响系统产量;磨内衬板使用时间过长,已严重磨损,有部分已断裂,严重影响磨机安全运行;钢球变形、破损较多,研磨效果差;磨机后滑履温度较高,生产运行中达 75 ℃左右。
改进措施:(1)拆除一仓阶梯衬板,更换为沟槽阶梯衬板,增加钢球和衬板的接触面,提高粉碎能力[1]。
磨内隔仓板改造失误后粉磨系统的再改进

21中图分类号:TQ172.632.9 文献标识码:B 文章编号:1008-0473(2019)01-0021-04 DOI 编码:10.16008/ki.1008-0473.2019.01.003磨内隔仓板改造失误后粉磨系统的再改进邹伟斌1 邹 健21. 中国建材工业经济研究会水泥专业委员会,北京 100024;2. 浙江鸿盛化工有限公司,浙江 绍兴 312300摘 要 RS公司在管磨机筛分隔仓板改造过程中,采用了篦缝宽度尺寸偏小的内筛板,导致磨内一仓(粗磨仓)至二仓(细磨仓)之间通风与过料能力明显下降,随之出现了系统产量降低、粉磨电耗增加的异常状况。
结合现场实际工况,首先解决管磨机筛分隔仓板的内筛板过料与通风能力;其次改造打散分级机下锥体筛板,然后调整研磨体级配。
改造后,系统产量提高,电耗明显降低。
关键词 管磨机 隔仓板 内筛板 下锥体筛板 研磨体级配 产量 电耗0 引言RS公司建有一套辊压机双闭路水泥联合粉磨系统,在Φ3.8 m×13 m双仓管磨机筛分隔仓板的改造过程中,选用了内筛板,投产后系统产量降低、粉磨电耗增加。
经过现场技术诊断分析,导致该不良现象产生的主要原因是:筛分隔仓板配置的内筛板篦缝小,过料能力不足。
结合现场实际工况分三步对粉磨系统实施改进:第一步,重点解决管磨机筛分隔仓板的内筛板过料与通风能力;第二步,改造辊压机预粉磨系统中打散分级机下锥体筛板,大幅度降低了入磨物料最大颗粒的比例以及颗粒群的整体粒径,为系统增产、降耗创造先决条件;第三步,根据入磨物料粒径与综合水分,对磨内研磨体级配进行针对性调整。
改造后,管磨机产量稳定提高,粉磨系统电耗明显降低。
本文对这次磨内隔仓板改造失误后粉磨系统的再改进进行总结。
1 系统配置与基本状况RS公司水泥制成工序配置RP120-80辊压机(物料处理能力180~230 t/h,主电机功率500 kW×2)+600/140打散分级机(物料处理能力≥380 t/h,打散电机功率55 kW+分级电机功率45 kW)+Φ3.8 m×13 m双仓管磨机(主电机功率2 500 kW-10 kV-额定电流185 A,主减速机型号JS130C,速比i =44.588∶1;磨机筒体工作转速16. 6r/min;磨机一仓有效长度3.75 m,仓长比例30%;二仓有效长度8.75 m,仓长比例70%;设计研磨体总装载量175 t)+O-Sepa N-3000高效涡流选粉机(主轴电机功率132 kW,最大喂料能力540 t/h,最大选粉能力180 t/h;配置系统风机风量210 000 m 3/h,风压5 600 Pa,风机电机功率500 kW-10 kV-额定电流35A)+磨尾收尘风机(风机风量45 000 m 3/h,风压3 500 Pa,风机电机功率90kW)组成的双闭路联合粉磨系统(见图1)。
水泥联合粉磨系统故障原因与解决措施
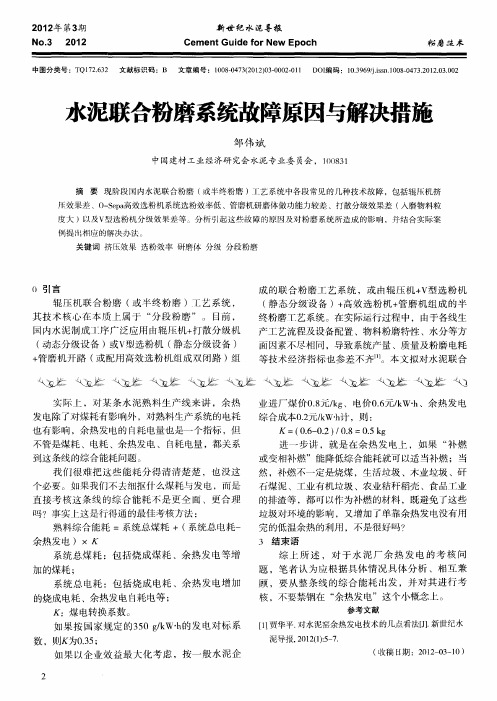
熟料 综合 能耗 =系统 总煤 耗 +( 系统 总 电耗一
余 热发 电 )× K
系统总煤耗 :包括烧成煤耗 、余热发 电等增 加 的煤耗 ; 系统总 电耗 :包括烧成 电耗 、余 热发电增加
综 上 所 述 ,对 于 水 泥 厂 余 热 发 电 的 考 核 问
题 ,笔者认为应根据具体情况具体分析 、相互兼
个 必要 。如 果我 们不 去细抠 什 么煤耗 与 发 电 ,而 是
进一步讲 ,就是在余热发 电上 ,如果 “ 补燃
或变 相补 燃 ”能 降低综 合能 耗就 可 以适 当补燃 ;当 然 ,补燃 不一 定是烧 煤 ,生 活垃圾 、木 业垃 圾 、矸
石煤 泥 、工业 有机 垃圾 、农业 秸秆 稻壳 、食品 工业
边 缘漏 料 。
1 . 响 分析 . 1影 2
磨丝木
粉 磨 单 闭路 ( 管磨 机 为开 路 ) 双 闭路 系统 ( 及 或半 终 粉 磨 系统 )中各 段 常 出现 的工艺 技术 与设 备故 障 模式 进行 探讨 分 析 ,并提 出相 应 的解 决办 法 。
1 辊压 机挤 压效 果 差 11 故 障原 因之 一 .
( 静态分级 设备 ) 高效选粉机+ + 管磨机组成 的半
终粉磨 T 艺 系统 。在实 际运行 过程 中 ,由于各 线生
产工艺流程及设备配置 、物料粉磨特性 、 水分等方 面 因素不尽 相 同 ,导致 系统 产量 、质 量及粉 磨 电耗 等技 术 经 济指 标也 参 差 不齐 Ⅲ 。本 文 拟对 水 泥联 合
K =f .- . / . 6 021 08:05k 0 . g
也 有影 响 ,余热 发 电的 自耗 电量也是 一 个指标 ,但 不 管是 煤耗 、电耗 、余 热 发 电 、 白耗 电量 ,都 关 系 到这条 线 的综合 能耗 问题 。 我 们 很 难 把 这 些 能耗 分 得 清 清楚 楚 ,也 没这
邹伟斌半终端粉磨系统新工艺新技术的应用

半终粉磨系统新工艺及其应用总结何活权新疆屯河水泥有限责任公司(831100)邹伟斌中国建材工业经济研究会水泥专业委员会(100024)提要:本文介绍了一种新型半终粉磨系统及其在生产中的应用,探讨了该粉磨系统节电效果;关键词:半终粉磨系统多级分选分段粉磨水泥粉磨工艺、设备的配置对水泥生产效率及经济效益影响极大,为提高水泥粉磨工艺水平,该公司和选粉机制造企业共同探讨,结合现有条件制订由联合粉磨改造成半终粉磨系统的新工艺技术。
重点是采用“多级分选、分段粉磨”的新工艺,将一台成品分离专用选粉机设置在辊压机预粉磨系统中的v 型选粉机出风口处,将辊压机系统挤压预粉磨过程中产生的合格品及时分选出来。
通过安装调试与生产运行证明:P • 042.5级水泥由技改前的200~220t/h提高到目前的280t/h,成品比表面积在370m2/kg以上,粉磨系统电耗由35.2kwh/t 降至27kWh/t,为公司水泥粉磨系统的节能降耗探索了一条新路子。
1 新工艺新技术探讨研究与启示1.1 通过对球破磨--管磨机粉磨系统研究得到的启示:在物料粗破碎阶段的效率最高,采用大钢球破碎大块物料,小钢球粉磨小颗粒物料。
若在粗破碎过程中采用风选原理,把细小颗粒及时带走,实现“边粉磨、边分选”,大大降低由细颗粒物料导致缓冲垫层所产生的无用功浪费,同时能够显著减少“过粉磨” 。
使其集破碎、研磨、分级功能为一体,提高了系统的破碎效率及后续细磨设备的粉磨能力,而且具有自动粗、细分级功能,分级精度较高,可不再单独配套分级设备。
1.2 配套预粉磨系统成品分离专用选粉机对辊压机+V 型静态选粉机+双仓管磨机+O-SePa 选粉机组成的联合粉磨闭路系统进行改造。
运用“多级分选、能选早选、分段粉磨”理论及系统工程方法为指导依据,并对粉磨系统中各段存在的技术问题进行了诊断分析,进而充分挖掘粉磨系统中每一段生产潜力,以求取得理想的效果。
在伊犁天山公司技改的基础上,经过与选粉机制造厂家技术人员共同努力,在现有水泥成品制备系统辊压机+V 型选粉机至管磨机之间增设一台专用成品选粉机,即形成:由180-120辊压机+V型静态分级机(V型选粉机)+预粉磨系统成品分离专用选粉机+①4.2X 13m双仓管磨机组成的新型半终粉磨闭路工艺系统,P • O42.5级水泥产量由技改前200~220 t/h提高到280t/h,水泥比表面积》370m2//kg,粉磨系统电耗由35.2kWh/1降低到27 kWh/1,吨水泥粉磨电耗降低8.2kwh/t,增产节电效果显著。
邹伟斌单传动辊压机在水泥、矿渣预粉磨应用(1)

DG单传动辊压机-----一种新型高效低能耗预粉磨设备在水泥、矿渣联合粉磨系统中的应用邹伟斌中国建材工业经济研究会水泥专业委员会摘要:据调查了解,国内水泥制成有20多种粉磨工艺系统,均各有其特点,但以采用辊压机+分级机+管磨机(或带选粉机)联合粉磨工艺系统为多,本文介绍了一种新型高效、低能耗的预粉磨设备----DG单传动辊压机及其与动态或静态分级机+管磨机组成的联合粉磨系统,在水泥粉磨与矿渣微粉制备中的应用及其取得的显著增产和节电效果;关键词:DG单传动辊压机联合粉磨粒度效应裂纹效应1.前言实施磨前物料预处理工艺,缩小入磨粒度、改善易磨性,是提高水泥粉磨系统产、质量,降低粉磨电耗最直接、最有效的技术途径。
在世界能源日趋危机、追求低碳及循环经济发展的今天,如何使水泥粉磨系统进一步节能降耗,是摆在我们粉磨工程技术人员面前的迫切任务。
国内水泥制成工序普遍使用管磨机终粉磨,其粉磨机理系利用研磨体的集群冲击、破碎与研磨效应完成水泥粉磨过程。
由于磨机一仓球形研磨体与物料之间为点接触,空隙较大,加之磨内四周空间不限,难以形成料床粉磨,即研磨体对物料做功具有随机性,电能大部分转换为热量与噪声、电能利用率低、粉磨效率低、电耗较高。
在材料水份受控的前提下,其生产能力与入磨物料粒度尺寸密切相关,磨机产量对物料粒度的变化非常敏感:入磨粒度越大,系统产量越低、粉磨电耗越高,反之亦然。
但当入磨物料粒度较小或大部分呈粉状时,则可显著弥补一仓粗碎能力不足的缺陷,充分发挥管磨机细磨能力有余、对水泥颗粒整形的粉磨技术优势。
自二十世纪八十年代中期,高效率料床粉磨设备—辊压机在德国问世以来,我国通过技术引进与自主研发制造的辊压机已广泛应用于水泥、化工、金属矿山及其他行业,国内新型干法水泥生产线生料制备采用辊压机终粉磨工艺系统,与中卸风扫烘干磨及立磨工艺相比,据保守测算吨生料可节电5-8kwh/t甚至以上,节能空间大;但在水泥制成工序中,由于辊压机终粉磨工艺制备的水泥颗粒级配分布较窄、颗粒形貌球形度差、标准稠度需水量大、凝结时间不正常、使用性能不良等因素影响,辊压机及分级设备只承担预粉磨功能。
我国水泥粉磨技术现状调查分析(一)
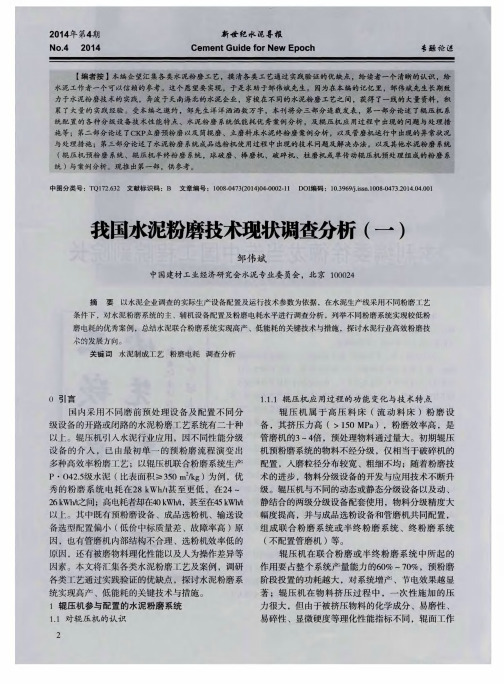
细、软 、绵 、湿的物料挤压效果相对较差 )。辊压 机动辊脱离中间架挡板作往复运动 , 标志着液压力 完全 通过 物料 传递 ;两 台主 电机 运行 电流 不大 于额
定 电流 ,在额 定 电流允 许范 围 内 ( 至少 应 达到额 定
焊 ( 相 当于连 续 运行 一 年时 间 )。 当辊压 机所 处 的
辊 压机辊面磨损 ,不仅造成工作辊缝变化 , 同时 ,辊面磨损或剥落严重出现凹槽以后 ( 主要是 辊面 中间部分 ),辊面花纹磨损后辊面光滑 ,对物 料的牵制 、啮合能力也会 明显削弱 ,挤压粉碎效果 大打 折 扣 。与花 纹完 整 的平 整辊 面相 比 ,严 重磨损 或剥 落后 的辊 面对物 料施 加 的挤 压力 不均 匀 、局部 漏料 ( 边 部 或 中部 )、出机 料饼 中粗 颗粒 ( 甚 至 未 经挤压 ) 增多 ,影响后续管磨机潜在粉磨能力 的发 挥 的 同时还 会加 剧分 级设 备磨 损 ,损 坏后 的 辊面对 物料 的牵制能力降低 、辊面剥落及凹槽处填充的物 料逃逸挤压 、加剧边缘漏料 ,挤压效果显著下降, 导致联合 ( 预粉磨 、半终粉磨 ) 粉磨系统生产能力 明显降低 、粉磨 电耗 增加 。辊压机辊 面耐磨层 一
造的防磨侧挡板 ,两辊之间铸有防磨凸块 , 工作寿命 挤 压 效果 。个 别 大 块也 不 宜 大 于辊 径 尺 寸 的5 %。 显著提高;当使用的侧挡板磨损严重,就要及时进行 即有 “ 挤 粗不 挤 细 、挤 硬不 挤软 、挤 脆不 挤绵 、挤 干不挤湿”的料床粉磨特性 ( 并非不挤压 ,只是对 更换, 然后再将退下的侧挡板进行耐磨处理备用。 辊 压机挤 压后的水泥颗粒形貌多数 为片状 、 针 状 、多 角 状 ,由 于磨 辊 结 构 方 面 固有 的粉 磨 特 性 ,其 自身对 水 泥颗粒 形 貌 的修正 能力 较 差 ,加之
浅析我国水泥粉磨技术的现状及改善策略

浅析我国水泥粉磨技术的现状及改善策略【摘要】水泥粉磨技术是水泥生产过程中一道提升水泥质量的重要工艺,在我国已经有较久的应用历史。
本文对我国现有的水泥粉磨技术进行总结分析,研究了水泥粉磨技术的现状,并根据技术现状中所存在的不足,提出了几点对应的改善措施,力图从粉磨技术工艺上对我国水泥生产水平的提升做出微薄贡献。
【关键词】水泥粉磨;水泥生产;技术改进【中图分类号】TU525【文献标识码】A【文章编号】1002-8544(2017)06-0182-02在水泥的生产流程中,粉磨技术是影响水泥质量的关键,一吨水泥的产出往往需要应用粉磨技术处理数十种物料,生产过程中的主要人工、能源消耗以及污染便是在这一环节产生。
针对于目前水泥生产中粉磨物料环节所带来的各种问题,如何采取切实有效的解决、改善措施,是有关部门以及学术界多次会议中提到的话题。
1.水泥粉磨技术现状1.1 发展潜力巨大在改革开放近四十年来,我国的基础设施建设得到了十分迅猛的发展。
在建筑、路桥、土工、给排水等建设领域,均离不开水泥的使用。
因此,我国一直以来,乃至于今后相当长的时期内仍将是水泥消耗的大国,对优质水泥的需求量与日俱增。
特别是在“十二五”期间,我国的高铁、高速、房地产建设再一次进入建设的新阶段,我国也在目前环境问题日益严重的情况下提出了新一轮的建材生产标准与政策。
在此背景下,水泥粉磨技术的发展潜力十分巨大,通常水泥生产成本中有40%左右的成本来自于粉磨环节或者与之相关的环节,粉磨技术上的一点微小调整与改进,便能够对水泥生产起到足够显著的影响。
1.2 设备能耗较高目前的水泥粉磨工艺所存在的普遍问题是能耗较高,就现有设备而言,水泥生产中所产生的最主要的能耗便来自于粉磨环节。
如生料、煤粉的制备以及水泥粉磨的过程都需要消耗大量的电能,目前的设备水平相比于多年以前有了巨大的提升,如辊压式预粉磨系统,相比最传统的粉磨工艺在能耗上节省了近一半,但对于目前的水泥市场需求来说仍显不足。
水泥联合(半终)粉磨系统管磨机一仓仓长的探讨
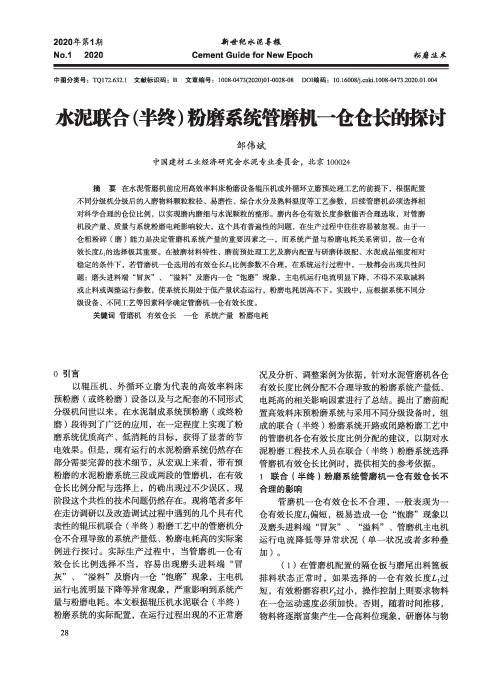
2020年第4期No.1 2020韧磨抜术新世他水猊專报Cement Guide for New Epoch中图分类号:TQ172.632.1 文献标识码:B 文章编号:1008-0473(2020)01-0028-08 DOI 编码:10.16008/ki.l008-0473.2020.01.004水泥联合(半终)粉磨系统管磨机一仓仓长际讨邹伟斌中国建材工业经济研究会水泥专业委员会,北京100024摘要在水泥管磨机前应用高效率料床粉磨设备辐压机或外循环立磨预处理工艺的前提下,根据配置不同分级机分级后的入磨物料颗粒粒径、易磨性、综合水分及熟料温度等工艺参数,后续管磨机必须选择相对科学合理的仓位比例,以实现磨内磨细与水泥颗粒的整形。
磨内各仓有效长度参数能否合理选取,对管磨机段产量、质量与系统粉磨电耗影响较大,这个具有普遍性的问题,在生产过程中往往容易被忽视。
由于一仓粗粉碎(磨)能力是决定管磨机系统产量的重要因素之一,而系统产量与粉磨电耗关系密切,故一仓有效长度厶的选择极其重要。
在被磨材料特性、磨前预处理工艺及磨内配置与研磨体级配、水泥成品细度相对 稳定的条件下,若管磨机一仓选用的有效仓长厶比例参数不合理,在系统运行过程中,一般都会出现共性问题:磨头进料端“冒灰”、“溢料”及磨内一仓“饱磨”现象,主电机运行电流明显下降,不得不采取减料或止料或调整运行参数,使系统长期处于低产量状态运行,粉磨电耗居高不下。
实践中,应根据系统不同分级设备、不同工艺等因素科学确定管磨机一仓有效长度。
关键词管磨机有效仓长一仓系统产量粉磨电耗0引言以辐压机、外循环立磨为代表的高效率料床预粉磨(或终粉磨)设备以及与之配套的不同形式 分级机问世以来,在水泥制成系统预粉磨(或终粉 磨)段得到了广泛的应用,在一定程度上实现了粉磨系统优质高产、低消耗的目标,获得了显著的节 电效果。
但是,现有运行的水泥粉磨系统仍然存在部分需要完善的技术细节,从宏观上来看,带有预粉磨的水泥粉磨系统三段或两段的管磨机,在有效仓长比例分配与选择上,的确出现过不少误区,现阶段这个共性的技术问题仍然存在。
再论水泥粉磨工艺发展趋势及改造要点(下)

中图分类号:TQ 72.632 文献标识码:B 文章编号: 008-0473(20 8)06-00 9- 4 DOI编码: 0. 6008/ki. 008-0473.20 8.06.008再论水泥粉磨工艺发展趋势及改造要点(下)邹伟斌中国建材工业经济研究会水泥专业委员会,北京 100024摘 要 配置高效率料床粉磨设备辊压机(或三辊、四辊外循环预粉磨立磨)+V型静态气流分级机+(下进风或侧进风)高效涡流选粉机+管磨机+(侧进风或内循环风)高效涡流选粉机组成的新型双闭路三选粉半终粉磨系统以及大型辊压机(或大型三辊、四辊外循环预粉磨立磨)与动态、静态两级组合气流分级机组成的开路(或闭路)联合(或半终)粉磨系统,立磨水泥终粉磨系统、筒辊磨终粉磨系统以及辊压机终粉磨系统均具有良好的节电优势,是水泥粉磨系统节电改造的方向。
采用大型辊压机(或大型三辊、四辊外循环预粉磨立磨)水泥联合(或半终)粉磨系统实现优质、高产、低消耗的技术原则是:“磨前处理是关键、磨内磨细是根本、磨后选粉是保证”,这也是对水泥联合(或半终)粉磨系统实施改造的三个重要内容。
在这一原则指导下的优化改造技术,使水泥粉磨系统电耗一降再降,为提升水泥企业的经济效益提供了强有力的技术支撑。
关键词 料床预粉磨 辊压机 立磨 管磨机 筒辊磨 粉磨工艺(上接2018年第五期)2 水泥粉磨工艺改造要点粉磨理论与生产实践证明:采用“分段粉磨”的能耗明显低于一段粉磨。
由磨前配置的高效料床预粉磨设备与不同形式的分级机+管磨机+高效选粉机组成的水泥联合(或半终)粉磨系统实现了良好的“分段粉磨”,是目前国内广泛应用的粉磨工艺,其在“磨前处理是关键、磨内磨细是根本、磨后选粉是保证”的原则下实现了粉磨系统的优质、高产和低消耗。
这个原则也表明了水泥联合(或半终)粉磨系统优化改造的方向和“分段粉磨”的具体内容。
2.1 管磨机前采用大型辊压机(或大型外循环预粉磨立磨)预粉磨水泥工业生产中,管磨机仍占粉磨设备的主导地位。
邹伟斌:水泥粉磨实用技术案例
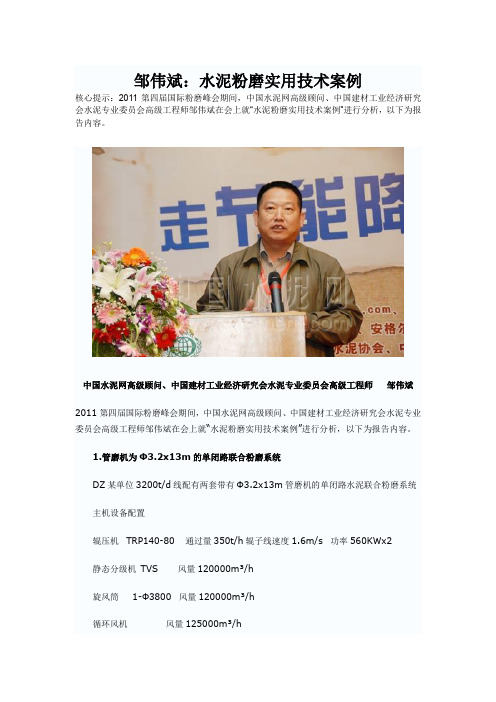
邹伟斌:水泥粉磨实用技术案例核心提示:2011第四届国际粉磨峰会期间,中国水泥网高级顾问、中国建材工业经济研究会水泥专业委员会高级工程师邹伟斌在会上就“水泥粉磨实用技术案例”进行分析,以下为报告内容。
中国水泥网高级顾问、中国建材工业经济研究会水泥专业委员会高级工程师邹伟斌2011第四届国际粉磨峰会期间,中国水泥网高级顾问、中国建材工业经济研究会水泥专业委员会高级工程师邹伟斌在会上就“水泥粉磨实用技术案例”进行分析,以下为报告内容。
1.管磨机为Ф3.2x13m的单闭路联合粉磨系统DZ某单位3200t/d线配有两套带有Ф3.2x13m管磨机的单闭路水泥联合粉磨系统主机设备配置辊压机TRP140-80 通过量350t/h辊子线速度1.6m/s 功率560KWx2静态分级机TVS 风量120000m³/h旋风筒1-Ф3800风量120000m³/h循环风机风量125000m³/h磨尾除尘风机风量44000 m³/h,风压4450Pa 功率75 KW选粉机K2000C 处理能力85-110 t/h 功率110 KW选粉机风机风量161647m³/h,风压4226Pa 功率280 KW该系统生产P.C32. 级水泥台时产量达120 t/h以上(成品细度R80<1.0%、R45<6.0%、R30<22%),粉磨电耗24 KWh/t。
主电机1600KW-10KV-额定电流118A,设计装载量125t,实装150t左右。
进相前电流114A,进相后电流98A。
磨机一仓长3.0m(24%)、装载量33t、平均球径27.35mm;二仓长9.5m(76%),装载量120t,平均球径16.69mm。
二仓内设有五道活化环。
3.管磨机为Ф3.8x13m的单闭路联合粉磨系统3.1 SD某单位采用两套HFCG140-70辊压机+SF600/140打散分级机+Ф3.8x13m开流高细磨生产水泥细度R80<3.0%、比表面积350m2/Kg、台时产量125 t/h x2、粉磨电耗28 KWh/t。
水泥粉磨系统异常案例分析及解决措施(二)
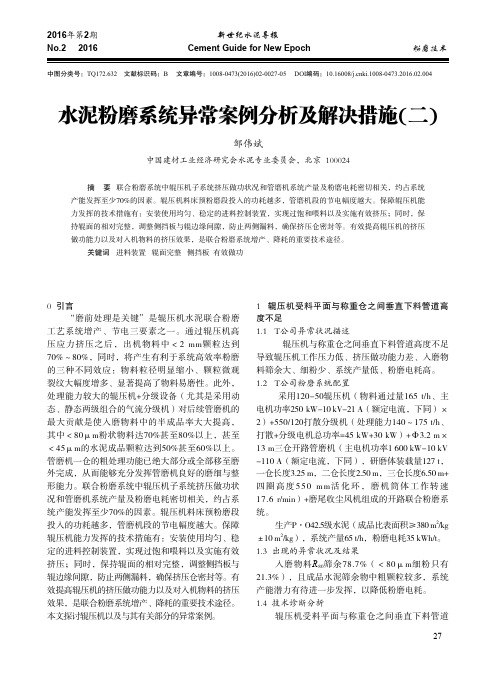
中图分类号:TQ 72.632 文献标识码:B 文章编号: 008-0473(20 6)02-0027-0 DOI编码: 0. 6008/ki. 008-0473.20 6.02.004水泥粉磨系统异常案例分析及解决措施(二)邹伟斌中国建材工业经济研究会水泥专业委员会,北京 100024摘 要 联合粉磨系统中辊压机子系统挤压做功状况和管磨机系统产量及粉磨电耗密切相关,约占系统产能发挥至少70%的因素。
辊压机料床预粉磨段投入的功耗越多,管磨机段的节电幅度越大。
保障辊压机能力发挥的技术措施有:安装使用均匀、稳定的进料控制装置,实现过饱和喂料以及实施有效挤压;同时,保持辊面的相对完整,调整侧挡板与辊边缘间隙,防止两侧漏料,确保挤压仓密封等。
有效提高辊压机的挤压做功能力以及对入机物料的挤压效果,是联合粉磨系统增产、降耗的重要技术途径。
关键词 进料装置 辊面完整 侧挡板 有效做功0 引言“磨前处理是关键”是辊压机水泥联合粉磨工艺系统增产、节电三要素之一。
通过辊压机高压应力挤压之后,出机物料中<2 mm颗粒达到70%~80%,同时,将产生有利于系统高效率粉磨的三种不同效应:物料粒径明显缩小、颗粒微观裂纹大幅度增多、显著提高了物料易磨性。
此外,处理能力较大的辊压机+分级设备(尤其是采用动态、静态两级组合的气流分级机)对后续管磨机的最大贡献是使入磨物料中的半成品率大大提高,其中<80μm粉状物料达70%甚至80%以上,甚至<45μm的水泥成品颗粒达到50%甚至60%以上。
管磨机一仓的粗处理功能已绝大部分或全部移至磨外完成,从而能够充分发挥管磨机良好的磨细与整形能力。
联合粉磨系统中辊压机子系统挤压做功状况和管磨机系统产量及粉磨电耗密切相关,约占系统产能发挥至少70%的因素。
辊压机料床预粉磨段投入的功耗越多,管磨机段的节电幅度越大。
保障辊压机能力发挥的技术措施有:安装使用均匀、稳定的进料控制装置,实现过饱和喂料以及实施有效挤压;同时,保持辊面的相对完整,调整侧挡板与辊边缘间隙,防止两侧漏料,确保挤压仓密封等。
水泥粉磨行业现状及发展趋势

水泥粉磨行业现状及发展趋势
水泥粉磨行业是水泥生产过程中的关键环节,直接影响到水泥品质和生产成本的控制。
以下是水泥粉磨行业的现状及发展趋势:
现状:
1.市场需求稳定增长:随着国民经济的发展,建筑业和基础设
施建设的需求不断增加,水泥粉磨行业的市场需求保持稳定增长的态势。
2.技术水平提升:水泥粉磨技术不断创新和改进,现代化水泥
粉磨装备的运行效率和产品质量得到提高。
3.环保标准要求提高:随着环保意识的增强,水泥粉磨企业需
要符合更高的环保标准,开展节能减排措施。
4.行业竞争加剧:水泥粉磨行业企业众多,市场竞争激烈,企
业间需要通过技术创新和降低生产成本来提高竞争力。
发展趋势:
1.装备自动化和智能化:随着工业自动化和人工智能技术的发展,水泥粉磨行业也趋向于装备自动化和智能化,提高生产效率和产品质量。
2.磨矿一体化发展:磨矿一体化是水泥粉磨行业发展的趋势,
通过磨矿一体化技术可以综合利用矿山资源和降低生产成本。
3.强调节能减排:水泥粉磨行业需要重视节能减排工作,减少
煤炭和电力等资源的消耗,降低对环境的影响。
4.绿色环保产品发展:随着消费者对绿色环保产品的需求增加,水泥粉磨企业需要开发出更环保、高质量的产品,以适应市场需求。
综上所述,水泥粉磨行业目前面临着市场竞争加剧和环保要求提高等挑战,但通过技术创新、装备智能化和磨矿一体化等发展趋势的引领,水泥粉磨行业仍然具备较大的发展潜力。
水泥粉磨系统优化探讨二
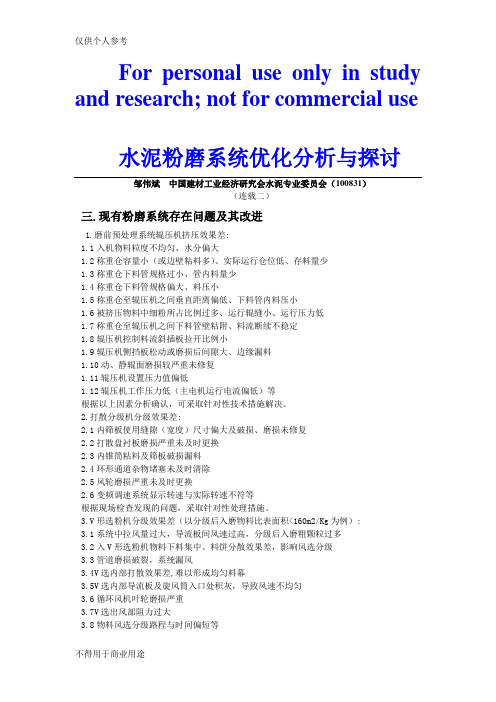
For personal use only in study and research; not for commercial use 水泥粉磨系统优化分析与探讨邹伟斌中国建材工业经济研究会水泥专业委员会(100831)(连载二)三.现有粉磨系统存在问题及其改进1.磨前预处理系统辊压机挤压效果差:1.1入机物料粒度不均匀、水分偏大1.2称重仓容量小(或边壁粘料多)、实际运行仓位低、存料量少1.3称重仓下料管规格过小、管内料量少1.4称重仓下料管规格偏大、料压小1.5称重仓至辊压机之间垂直距离偏低、下料管内料压小1.6被挤压物料中细粉所占比例过多、运行辊缝小、运行压力低1.7称重仓至辊压机之间下料管壁粘附、料流断续不稳定1.8辊压机控制料流斜插板拉开比例小1.9辊压机侧挡板松动或磨损后间隙大、边缘漏料1.10动、静辊面磨损较严重未修复1.11辊压机设置压力值偏低1.12辊压机工作压力低(主电机运行电流偏低)等根据以上因素分析确认,可采取针对性技术措施解决。
2.打散分级机分级效果差:2.1内筛板使用缝隙(宽度)尺寸偏大及破损、磨损未修复2.2打散盘衬板磨损严重未及时更换2.3内锥筒粘料及筛板破损漏料2.4环形通道杂物堵塞未及时清除2.5风轮磨损严重未及时更换2.6变频调速系统显示转速与实际转速不符等根据现场检查发现的问题,采取针对性处理措施。
3.V形选粉机分级效果差(以分级后入磨物料比表面积<160m2/Kg为例):3.1系统中拉风量过大,导流板间风速过高,分级后入磨粗颗粒过多3.2入V形选粉机物料下料集中、料饼分散效果差,影响风选分级3.3管道磨损破裂,系统漏风3.4V选内部打散效果差,难以形成均匀料幕3.5V选内部导流板及旋风筒入口处积灰,导致风速不均匀3.6循环风机叶轮磨损严重3.7V选出风部阻力过大3.8物料风选分级路程与时间偏短等检查系统采取相应技术处理措施。
VSK选粉机带有可调节旋转分离转子,其分级后的入磨物料粒径比V形选粉机分级粒径更小、颗粒更细、更均匀。
水泥粉磨工艺发展趋势及改造要点_邹伟斌
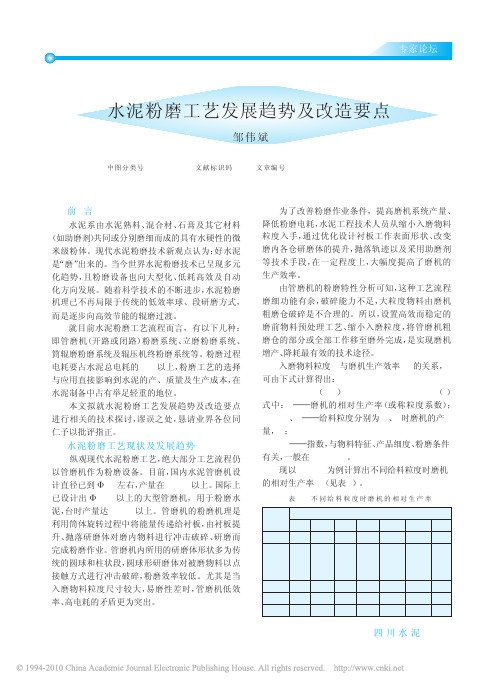
工艺磨细后的水泥颗粒级配中某一粒径的含量相 对集中,即通常所说的“窄级配水泥”。磨内隔仓板 及出料篦板篦缝一般≤6mm。
开路高细磨系统必须强化通风与收尘措施,磨 内风速保持 0.5 ̄0.8m/s,宜选择布袋收尘工艺。如果 出现研磨体表面因静电吸附细物料而影响粉磨效 率时,可考虑引入助磨剂解决,该工艺粉磨电耗一 般在 30 ̄33kWh/t。
2.2.1 预处理开路高细磨系统
众所周知,水泥成品中 30"m 以下颗粒所占比 例决定胶砂强度的发挥,特征粒径 16 ̄24#m的含量 越多越好。中小型磨机一般磨身较短,物料在磨内 停留被粉磨的时间也短,完全依靠磨内研磨体对物 料的破碎与粉磨,物料往往不易被磨细,导致成品 中粗颗粒含量偏多,严重制约水泥水化活性的发 挥。预处理工艺的设置对开路粉磨系统的增产、节 电及提高水泥的磨细程度意义重大。
综上所述,今后一段时间内,水泥工业高耗能 粉磨设备(如管磨机)的选用将会逐步减少,而具有 高效低耗的辊磨将成为水泥粉磨领域主机设备的
首选方向。
表 2 不同粉磨系统电耗比较
球磨Biblioteka 辊压机粉磨系统环辊磨
粉磨 联合粉磨 终粉磨 粉磨 辊磨 Horomill Cemax
Fuller 评价 6.4 7.7 1.7 8.4 7.1 7.4 5.3 4.7
采用开路高细磨技术磨制的矿渣水泥强度见表 3。
表 3 开路高细磨矿渣水泥强度( GB 法)
矿渣掺 比表面积 抗折强度 /MPa 量 /% (/ m2/kg) 3d 7d 28d
0
395 6.6 8.4 8.3
15
372 5.9 8.0 8.5
30
378 4.6 6.2 8.0
抗压强度 /MPa 3d 7d 28d 35.0 50.4 59.7 29.0 42.1 58.2 25.9 37.9 55.1
改造水泥粉磨工艺 提高产品实物质量
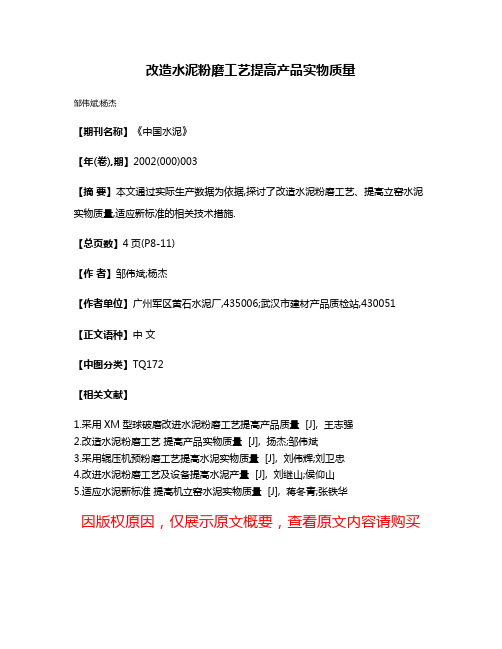
改造水泥粉磨工艺提高产品实物质量
邹伟斌;杨杰
【期刊名称】《中国水泥》
【年(卷),期】2002(000)003
【摘要】本文通过实际生产数据为依据,探讨了改造水泥粉磨工艺、提高立窑水泥实物质量,适应新标准的相关技术措施.
【总页数】4页(P8-11)
【作者】邹伟斌;杨杰
【作者单位】广州军区黄石水泥厂,435006;武汉市建材产品质检站,430051【正文语种】中文
【中图分类】TQ172
【相关文献】
1.采用XM型球破磨改进水泥粉磨工艺提高产品质量 [J], 王志强
2.改造水泥粉磨工艺提高产品实物质量 [J], 扬杰;邹伟斌
3.采用辊压机预粉磨工艺提高水泥实物质量 [J], 刘伟辉;刘卫忠
4.改进水泥粉磨工艺及设备提高水泥产量 [J], 刘继山;侯仰山
5.适应水泥新标准提高机立窑水泥实物质量 [J], 蒋冬青;张铁华
因版权原因,仅展示原文概要,查看原文内容请购买。
水泥联合粉磨系统调试体会
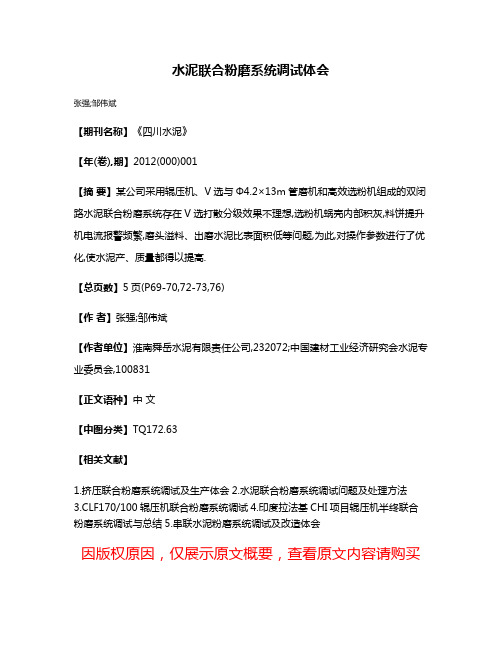
水泥联合粉磨系统调试体会
张强;邹伟斌
【期刊名称】《四川水泥》
【年(卷),期】2012(000)001
【摘要】某公司采用辊压机、V选与Φ4.2×13m管磨机和高效选粉机组成的双闭路水泥联合粉磨系统存在V选打散分级效果不理想,选粉机蜗壳内部积灰,料饼提升机电流报警频繁,磨头溢料、出磨水泥比表面积低等问题,为此,对操作参数进行了优化,使水泥产、质量都得以提高.
【总页数】5页(P69-70,72-73,76)
【作者】张强;邹伟斌
【作者单位】淮南舜岳水泥有限责任公司,232072;中国建材工业经济研究会水泥专业委员会,100831
【正文语种】中文
【中图分类】TQ172.63
【相关文献】
1.挤压联合粉磨系统调试及生产体会
2.水泥联合粉磨系统调试问题及处理方法
3.CLF170/100辊压机联合粉磨系统调试
4.印度拉法基CHI项目辊压机半终联合粉磨系统调试与总结
5.串联水泥粉磨系统调试及改造体会
因版权原因,仅展示原文概要,查看原文内容请购买。
- 1、下载文档前请自行甄别文档内容的完整性,平台不提供额外的编辑、内容补充、找答案等附加服务。
- 2、"仅部分预览"的文档,不可在线预览部分如存在完整性等问题,可反馈申请退款(可完整预览的文档不适用该条件!)。
- 3、如文档侵犯您的权益,请联系客服反馈,我们会尽快为您处理(人工客服工作时间:9:00-18:30)。
中国水泥工业水泥粉磨系统现状调查分析邹伟斌中国建材工业经济研究会水泥专业委员会(北京100024)(连载二)摘要:本文以水泥企业调查的实际生产设备配置及运行技术参数为依据,在水泥生产线采用不同粉磨工艺条件下,水泥粉磨系统的主、辅机设备配置及粉磨电耗水平进行了调查分析,列举了不同粉磨系统实现较低粉磨电耗的优秀案例,探讨了水泥行业高效粉磨技术的发展方向。
本文以连载方式刊发,第一部分论述了辊压机系统配置的各种分级设备技术性能特点、水泥粉磨系统低能耗优秀案例分析及辊压机应用过程中出现的问题与处理措施等。
第二部分论述了CKP立磨预粉磨以及筒辊磨、立磨料床水泥终粉磨案例分析以及管磨机运行中出现的异常状况与处理措施;第三部分论述了水泥粉磨系统成品选粉机使用过程中出现的技术问题及解决办法以及其他水泥粉磨系统(辊压机预粉磨系统、辊压机半终粉磨系统;球破磨、棒磨机、破碎机、柱磨机或单传动辊压机预处理组成的粉磨系统)与案例分析;总结了水泥联合粉磨系统实现高产、低能耗的技术关键与措施。
关键词:水泥制成工艺粉磨电耗调查分析(接上期)3.CKP立磨(料床)预粉磨机以及带有CKP立磨(料床)预粉磨的水泥粉磨系统(工艺流程见图15)由日本秩父小野田与川崎重工推出的CKP立磨(料床)预粉磨系统配套于管磨机,对入管磨机前水泥熟料进行连续碾压预粉磨,有效降低入磨物料粒度,可提高系统产量50%--100%、节电20%--30%。
用于预粉磨水泥生料,可使系统增产100%—200%,节电幅度达30%—40%。
CKP立磨和一般风扫立磨的主要区别是取消了顶部成品选粉机与风机及收尘器,系统装机功率低。
其主要功能是作为预粉磨,碾磨后的物料不经任何分级直接入磨,虽颗粒粒径分布较宽,但碾磨后的物料具有“晶格微裂纹”,易磨性显著改善。
与后续管磨机可以组成开路或闭路粉磨等系统;CKP立磨特点:顶部无选粉机、采用边部机械卸料(30%物料参与循环以密实料床、70%物料入管磨机)、固定料床粉磨、运行能耗低、工作性能稳定、磨辊与磨盘采用高性能耐磨材料,使用寿命达30000h以上,实现了长寿命、高效率运转。
图15 用于预粉磨的CKP 立磨(左) CKP 立磨预粉磨工艺流程(右)案例一:冀东水泥有限公司二线采用CKP240立磨(主电机功率功率2100kw )配置在Φ4.8×7.5m 闭路水泥磨(主电机功率2500kw )前,系统产量180t/h —200t/h 、粉磨电耗32kwh/t 左右;烟台冀东水泥公司采用CKP240立磨+Φ4.8×9.5m 闭路管磨机(主电机功率3550kw ),生产P.O42.5R 水泥,系统产量达208.45t/h ,粉磨电耗33.02kwh/t ;【1】案例二:江南小野田水泥有限公司4000t/d 生产线,水泥粉磨系统采用CKP170立磨作预粉磨(磨盘直径:1700mm 、磨辊直径1160mm 、宽度450mm 、磨辊数量:3个、主电机功率:950kw 、处理能力180t/h ); 后续管磨机:φ4.0 × 12.0 m (主电机功率2700kw );成品选粉机:0-Sepa N —2500(主轴电机功率132kw 、处理能力450t/h 、成品产量150t/h )组成的预粉磨闭路系统;生产P.ΙΙ52.5级硅酸盐水泥(成品比表面积365m2/kg —370m2/kg )、台时产量108t/h —110t/h 、系统粉磨电耗39.5kwh/t ;经CKP 立磨处理后的入磨粒径P80平均为1.7mm 、90μm 以下微粉含量达45%以上,CKP 投入功耗仅6.8kwh/t 左右;该粉磨系统中CKP 立磨有30%物料参与循环以密实料床、稳定碾磨效果。
【2】案例三:秦皇岛浅野水泥有限公司4000t/d 生产线,水泥粉磨系统采用CKP-170立磨(功率800kw )配置于Φ3.9×12m (主电机功率2400kw )闭路水泥磨前,系统产量115t/h 。
4.HOROmill3800(筒辊磨)水泥料床终粉磨系统(工艺流程见图16) 筒辊磨1993年由法国FCB 公司研发推出的高效率料床粉磨设备,并应用于水泥工业生产。
依靠高速旋转过程中的筒与内部可加压的辊对物料实施反复碾压(筒体转速为临界转速1.6倍左右,物料在辊柱面与筒体内环面碾压通道多次碾压),物料啮入角在18°左右,料层厚度较薄,属于中等压力料床粉磨;与高效选粉机组成闭路粉磨系统,适宜于水泥、矿渣微粉、生料的制备,能量利用率高,系统粉磨电耗低;图16 HOROmill(筒辊磨)水泥料床终粉磨系统工艺流程我国牡丹江水泥厂2002年从法国FCB公司引进一台HOROmill3800筒辊磨,2003年6月13日正式投运,与其他粉磨系统相比,节电效果非常显著。
HOROmill3800筒辊磨技术参数见表2:【3】表2 HOROmill3800筒辊磨技术参数相同型号的HOROmill3800筒辊磨水泥终粉磨系统于2005年1月在陕西中材汉中水泥公司投运,磨机电机功率2500kw,粉磨P.O42.5级水泥(比表面积353m2/kg)产量87.9t/h、系统粉磨电耗为33.18kwh/t;【4】5.立磨水泥料床终粉磨系统(工艺流程见图17)1980年7月,德国非凡公司在汉诺威Teutonia水泥厂投产了世界上第一台正式用于生产水泥的立磨,型号为MPS3750C,磨盘中径Φ3750mm、磨辊直径Φ2700mm、装机功率1900KW、选粉机型号SLF6700(PZ45水泥产量78t/h),由此揭开了水泥立磨终粉磨的篇章;辊套和衬板净磨耗:粉磨快硬PZ45水泥6.5g/t、粉磨矿渣水泥(78%矿渣)38g/t。
【5】除上述非凡公司MPS水泥立磨案例,在国、内外运行的尚有以下知名公司的水泥立磨终粉磨系统:图17 水泥立磨料床终粉磨系统工艺流程5.1 LM56.3+3C/S水泥立磨料床终粉磨系统(见图18)图18 莱歇水泥立磨终粉磨系统案例一:湖北亚东水泥有限公司采用德国莱歇公司LM56.3+3C/S立磨终粉磨水泥(磨盘直径5600mm、磨机电机功率5300kw,配用LSKS 87选粉机(功率400 kw,工作转速50r/min--125r/min),生产P.O42.5水泥台时产量215t/h、粉磨电耗33kwh/t;磨制P.C32.5水泥台时产量255t/h、系统粉磨电耗30kwh/t;【6】案例二:CEMEX公司在阿联酋Jebel Ali 5000t/d线水泥制成系统,采用德国莱歇公司的LM56.3+3C/S大型水泥立磨(配套主电机功率5700kw),粉磨纯硅酸盐水泥(成品比表面积351 m2/Kg),磨机产量210 t/h --220 t/h,系统粉磨电耗34.6kwh/t。
【7】5.2 OK33-4水泥立磨终粉磨系统(见图19)图19 OK水泥立磨料床终粉磨系统案例一:2006年4月云南国资水泥东骏有限公司投用 F.L.S公司制造的OK33-4立磨(选粉机ROKS40.0)、磨盘转速25r/min、磨辊数量4只(轮胎形辊,中部带有排气凹槽)、磨盘直径Φ4760mm、磨辊直径Φ1950mm、主电机YRKK800-6、功率3000KW、主减速机MAAG-WPU142、额定功率2735KW;设计生产能力:矿渣粉84t/h(比表面积>420m2/kg)、熟料粉150t/h(比表面积>330m2/kg);实际生产运行数据如下:磨制熟料粉台时产量150t/h--160t/h、粉磨电耗28.82kwh/t、磨耗3.02g/t;磨制矿渣粉台时产量85t/h--95t/h、粉磨电耗49.54kwh/t、磨耗12.06g/t;由于矿渣显微硬度高(HV450--HV700)、玻璃体含量高、磨蚀性大,磨制矿渣微粉时磨盘及磨辊的磨耗量比粉磨水泥时大;【8】5.3TRMKS43.4立磨水泥终粉磨(见图20)天津院研制的TRMKS43.4立磨用于水泥终粉磨,以下是国内与国外两个实际案例:图20 TRMK水泥立磨案例一:武汉阳逻(娲石)水泥有限公司采用天津院研制的TRMKS43.41立磨(主电机功率3150kw、风机功率1400kw、风量410000m/h、风压8000Pa、选粉机功率250kw),设计能力:S75级矿渣微粉90t/h、比表面积≥420m2/kg;P.C32.5级水泥130t/h、成品比表面积≥350m2/kg;生产P.C32.5级水泥产量140t/h、成品比表面积≥350m2/kg、系统粉磨电耗29kwh/t;生产S75级矿渣微粉产量103t/h、成品比表面积>425m2/kg、系统粉磨电耗低于42kwh/t;【9】案例二:TRMSK43.4立磨成功用于哈萨克斯坦标准水泥有限公司,粉磨比表面积463.5m2/kg矿渣微粉,产量94.3t/h、系统粉磨电耗低于38kwh/t;粉磨比表面积352.3m2/kg的OPC水泥,产量112.6t/h、系统粉磨电耗低于28kwh/t;【10】5.4华新HXLM43.4水泥立磨终粉磨HXLM43.4立磨运行参数(主电机功率3150kw),磨机产量140t/h--160t/h (成品比表面积≥360m2/kg);生产P.O42.5级水泥,粉磨电耗35kwh/t--38kwh/t;生产P.C32.5级水泥,粉磨电耗30kwh/t--32kwh/t;立磨磨辊、磨盘堆焊材料:高铬碳铁基硬质合金,吨水泥金属磨耗量:磨盘:5.2g/t;磨辊:2.6g/t;【11】6.管磨机系统(双滑履中心传动管磨机见图21)6.1关于入磨物料粒径与管磨机产量的关系入磨物料粒径与管磨机产量的关系:管磨机内部四周空间不限,研磨体随机做功,对于粉磨片状及粉状料的效果较好,但不能形成料床,粗碎能力不足、磨细能力有余。
总的粉磨规律是:入磨物料粒径越小、细粉比例越大、管磨机产量越高、系统粉磨电耗越低。
关于磨机产量与入磨物料粒径之间的关系,可由下式表述:x (1)Kd=(G2/G1)=(d1/d2)式中:Kd--磨机的相对生产率或称粒径系数;G1、G2--分别代表入磨粒径为d1、d2时的磨机产量(t/h);X--指数,与物料特性、成品粒径、粉磨条件有关,一般X=0.15--0.35之间取值;现以X=0.20为例,以此推出不同入磨粒径时磨机的相对生产率Kd见表3:2.19倍,增产幅度达到219%,即实现了设计能力的翻番;以Φ4.2×13m水泥管磨机为例,以入磨物料粒径25mm计算,设计产量为90t/h;当采用预粉磨及高效分级设备将入磨物料粒径降至0.5mm时,磨机产量可达到197t/h,计算值与实际产量基本吻合。