第三讲催化裂化装置解析
第三章_催化裂化装置
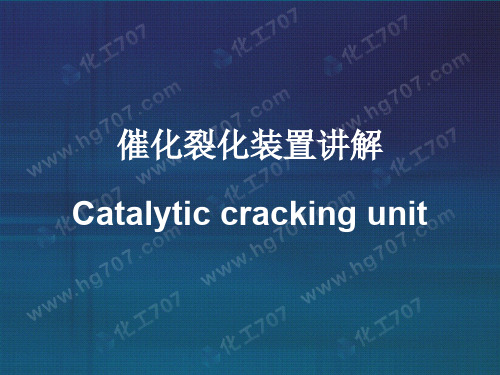
主要由吸收塔、解吸塔、再吸收塔及稳定塔组成。 吸收塔和解吸塔的操作压力为1.0~2.0MPa。 稳定塔实质上是个精馏塔,操作压力为1.0-1.5MPa。
四、能量回收系统
利用再生器出口烟气的热能和压力使余热 锅炉产生蒸汽和烟气轮机作功、发电等。
能量回收系统的工艺流程图
二、分馏系统
沉降器来的反应油气,经换热器进入分馏塔, 根据物料的沸点差,从上至下分离为富气、粗 汽油、柴油、回炼油和油浆。
分馏系统流程图
1.分馏塔底人字形挡板处用油 浆洗涤(1)防止少量催化剂细 粉堵塞塔盘和影响产品质量; (2)由于反应油气温度较高, 500℃左右,油浆洗涤可取走 多余的热量。 2.油浆:一部分回炼,一部分 回分馏塔,一部分送出装置作 自用燃料。 3富气经压缩后去吸收稳定系统 的凝缩油罐,粗汽油进吸收塔 上部。
490~510 ℃
2 ~3s
600~750 ℃
200~300 ℃
分馏系统
三、吸收—稳定系统
从分馏塔顶油气分离器出来的富气中带有汽油组分,而粗
汽油中又溶有C3、C4甚至C2组分,因此吸收稳定系统的作 用: 利用吸收和精馏的方法将富气和粗汽油分离成干气 (≤C2) 、液化气(C3、C4)和蒸汽压合格的稳定汽油。
富气经气压机升压、冷却并分出凝缩油后,由底部进入吸收塔;稳定 汽油和粗汽油则作为吸收液由塔顶进入,将富气中的C3、C4(含少量C2) 等吸收后得到富吸收油。吸收塔顶部出来的贫气中夹带有少量稳定汽油, 可经再吸收塔用柴油回收其中的汽油组分后成为干气,送出装置。 富吸收油和凝缩油均进入解吸塔,使其中的气体解吸后,从塔顶返回 凝缩油沉降罐,塔底的未稳定汽油送入稳定塔,通过精馏作用将液化气和 稳定汽油分开。有时,塔顶要排出部分不凝气(也称气态烃),它主要是 C2,并夹带有C3和C4.排出不凝气的目的是为了控制稳定塔的Ni+V:不大于 20 PPm 残碳:不大于 6% 产品分布: ★ 气体:10~20%,气体中主要是C3 、C4 ,烯烃含量很 高 ★ 汽油:产率在30~60%之间,辛烷值较高,约80~90 ★ 柴油:产率在0~40%, 十六烷值较低,需调和或精 制 ★ 油浆:产率在0~10% ★ 焦炭:产率在5%~10%,原子比大约是C:H=1:0.3~1
催化裂化讲解

催化裂化讲解装置简介本装置是根据中国石油一厂总公司中石化(85)规字10号文“关于抚顺石化公司石油一厂120×104t/a催化裂化装置初步设计的批复“由洛阳石油化工工程公司设计院1985年开始破土动工,1987年10月建成,1987年11月23日正式投产,取得开汽一次成功。
装置所用原料为沈北原油(及一部分大庆油)的直馏装置减压重含蜡油、分蜡蜡下油及焦化蜡油,并掺入一定量的蒸馏装置减压渣油以满足热平衡的需要。
装置工艺设备的主要特点如下:采用同高并列式提升管反应-前置烧焦罐两段再生工艺,再生器二密相至一密相的外循环管采用塞阀控制催化剂循环量,提升管反应器出口采用粗旋风分离器,烧焦罐稀相管出口采用T型快速分离结构,沉降器及再生器均采用外集气室。
为充分利用再生烟气能量,本装置设有能量回收机组。
该机组由A V50-12轴流式主风机、烟气轮机和电动/发电机组成。
烟机后部设有余热锅炉,产生中压蒸汽。
本装置后部设有产品精制和污水汽提装置,保证汽油、液化气的质量和排放污水符合环保要求。
工艺流程说明装置由反应、分离、吸收稳定三个系统组成。
1 反应系统混合蜡油,用泵201从原料油罐(5000t17#、16#)抽出,经顶循环回流油-原料油换热器(E201)、轻柴油-原料油换热器(E208A)、一中段回流油-原料油换热器(E202)、油浆-原料油换热器(E203)换热,使混合蜡油加热到250℃左右;减压冷渣油(130℃)由东蒸馏装置自流送入渣油罐(V201),再由减压渣油泵(P202)抽出;回炼油由分馏塔第二层塔盘自流入回炼油罐(V202),经汽提后由回炼油泵(P209)抽出,原料进入提升管反应器的四个原料喷嘴,回炼油一部分进入提升管反应器的回炼油进料的喷嘴。
或并入原料喷嘴。
油浆从分馏塔底用油浆泵(P209)抽出,阻垢剂用阻垢剂泵打入,油浆被加压送至提升管反应器的油浆进料两个喷嘴(在原料新喷嘴上)或并入原料西南喷嘴。
催化裂化装置课件
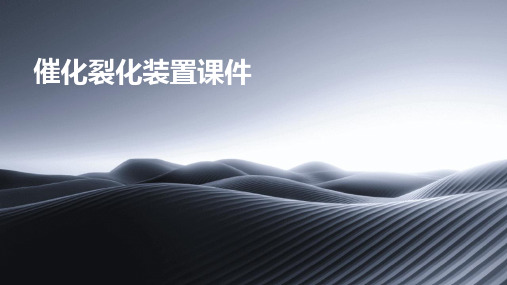
阐述液体产物精制的原理及方法,包括蒸馏、萃取、 吸附和离子交换等。
04
催化裂化装置的维护与保养
日常维护
01
02
03
每日检查
检查装置的外观、紧固件 、连接部位等是否正常, 确保无泄漏、无特殊声响 和振动。
温度和压力监控
定期检查装置的温度和压 力是否在正常范围内,并 记录数据,以便及时发现 特殊情况。
02
03
04
严格遵守操作规程
操作人员必须经过专业培训, 熟悉装置的操作流程和安全规
范。
定期检查和维护
对装置进行定期检查,及时发 现和处理潜伏的安全隐患。
危险品管理
对装置涉及的危险品进行严格 管理,确保储存和使用安全。
应急预案
制定完善的事故应急预案,提 高应对突发事件的快速响应能
力。
事故应急处理
火灾应急处理
THANKS
感谢观看
原料的干燥与脱硫脱氮
介绍原料的种类、性质和来源,说明 原料对催化裂化过程的影响。
阐述原料在进入反应器前进行干燥和 脱硫脱氮的原理及方法。
原料的预热与混合
说明原料在进入反应器前的预热和混 合的必要性,以及预热和混合的方法 。
反应过程
01
反应原理
详细介绍催化裂化反应的原理, 包括反应机理、反应条件和影响 因素。
催化裂化装置的应用
催化裂化装置广泛应用于石油化工行业,是炼油厂的重要加工装置之一 。
它主要用于处理重质石油原料,如减压馏分油、脱油沥青等,将其转化 为高价值的轻质产品。
通过催化裂化装置的处理,可以提高石油产品的质量和产量,满足市场 需求。同时,催化裂化技术也在不断发展和改进,以提高生产效率和环 保性能。
催化裂化装置解读

催化裂化装置催化裂化是炼油工业重要的二次加工装置,是提高轻质油收率,生产高辛烷值汽油,同时又多产柴油的重要手段,随着重油催化工艺的实现,其地位更加倍增。
作为一项传统的重油加工工艺,催化裂化实现工业化已经有60年的历史,其总加工能力超过加氢裂化、焦化和减粘裂化之和,是目前最重要的重油轻质化工艺。
虽然曾多次受到加氢裂化工艺的竞争和清洁燃料标准的挑战,但由于催化裂化技术的进步,各种以催化裂化技术为核心的催化裂化“家族工艺”的不断出现,已经将催化裂化转变为“炼油-化工一体化”的主体装置,催化裂化仍然保持了其在石油化工行业中的重要地位。
我国的催化裂化技术与国际先进水平保持同步,进入21世纪以后,由于我国催化裂化装置在炼厂地位的特殊性,技术发展的势头更猛,目前为止,基本解决了由于产品升级换代给催化裂化工艺带来的各种问题,而且在应对产品质量问题的技术开发过程中,拓宽了催化裂化产品的品种和范围,为确保催化裂化技术在未来石油化工中的核心地位提供了技术保证。
催化裂化装置的工艺原理是在流化状态下的催化剂作用下,重质烃类在480--520 ℃及0.2-0.3MPa(a)的条件下进行反应。
主要包括:1).裂解反应:大分子烃类裂解为小分子,环烷烃进行断环或侧链断裂,单环芳烃的烷基侧链断裂。
2).异构化反应:正构烷烃变成异构烷烃,带侧链的环烃或烷烃变成环异烷,产品中异构烃含量增加。
3).芳构化反应:环己烷脱氢生成芳香烃,烯烃环化脱氢生成芳烃。
4).氢转移反应:多环芳烃逐渐缩合成大分子直至焦炭,同时一种氢原子转移到烯烃分子中,使烯烃饱和成烷烃。
催化裂化装置的规模近三十年来逐步发展到350万吨/年(加工1000万吨/年原油)。
加工的原料为常压蜡油、减压渣油以及蜡油加氢裂化尾油。
原料主要性质装置由反应再生、分馏、吸收稳定(包括产品精制)、烟气能量回收几个部分组成。
装置主要产品为液化气、汽油、重石脑油和轻柴油,副产部分干气和油浆。
液化气去气体分馏装置。
第三讲催化裂化装置解析

回炼油返回反应-再生系统进行回炼。油浆从塔底抽出,经油浆蒸汽发 生器换热降温后,一部分回分馏塔参加循环,另一部分返回反应-再生 系统回炼或留作装置自用燃料。
The creating gas, gasoline, liquefied petroleum gas, diesel and other distillate and unreacted components carrying a small amount of catalyst by two-stage cyclone separator leave the settlement into the fractionation unit. Isolated spent catalyst storing coke fall into the lower part of the precipitator, enter into regenerator though spent inclined tube to burn in air, then go into the riser after recovering activity to participate in the reaction and form a cycle. The gas in the top of regenerator enters into the energy recovery unit. 反应生成的气体、汽油、液化 气、柴油等馏分与未反应的组 分携带少量催化剂经两级旋风 分离器分出夹带的催化剂后离 开沉降器进入分馏单元。被分 离出的积有焦炭的待生催化剂
Indicators to evaluate the raw materials of catalytic cracking 评价催化裂化的指标
催化裂化的装置简介及工艺流程
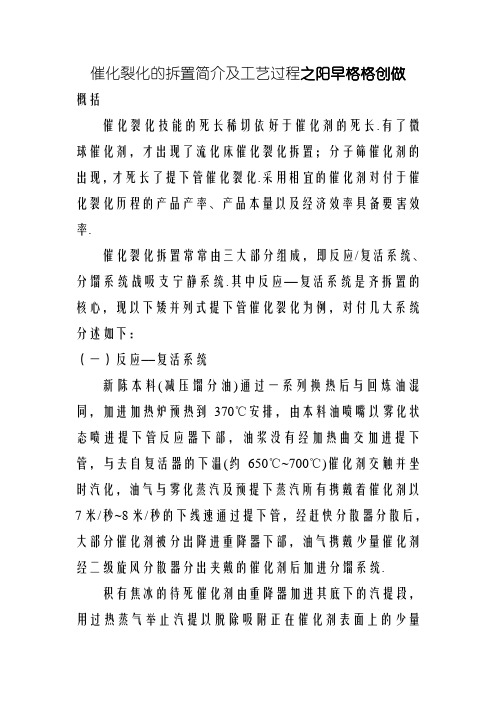
催化裂化的拆置简介及工艺过程之阳早格格创做概括催化裂化技能的死长稀切依好于催化剂的死长.有了微球催化剂,才出现了流化床催化裂化拆置;分子筛催化剂的出现,才死长了提下管催化裂化.采用相宜的催化剂对付于催化裂化历程的产品产率、产品本量以及经济效率具备要害效率.催化裂化拆置常常由三大部分组成,即反应/复活系统、分馏系统战吸支宁静系统.其中反应––复活系统是齐拆置的核心,现以下矮并列式提下管催化裂化为例,对付几大系统分述如下:(一)反应––复活系统新陈本料(减压馏分油)通过一系列换热后与回炼油混同,加进加热炉预热到370℃安排,由本料油喷嘴以雾化状态喷进提下管反应器下部,油浆没有经加热曲交加进提下管,与去自复活器的下温(约650℃~700℃)催化剂交触并坐时汽化,油气与雾化蒸汽及预提下蒸汽所有携戴着催化剂以7米/秒~8米/秒的下线速通过提下管,经赶快分散器分散后,大部分催化剂被分出降进重降器下部,油气携戴少量催化剂经二级旋风分散器分出夹戴的催化剂后加进分馏系统.积有焦冰的待死催化剂由重降器加进其底下的汽提段,用过热蒸气举止汽提以脱除吸附正在催化剂表面上的少量油气.待死催化剂经待死斜管、待死单动滑阀加进复活器,与去自复活器底部的气氛(由主风机提供)交触产死流化床层,举止复活反应,共时搁出洪量焚烧热,以保护复活器脚够下的床层温度(稀相段温度约650℃~680℃).复活器保护0.15MPa~0.25MPa(表)的顶部压力,床层线速约0.7米/秒~1.0米/秒.复活后的催化剂经淹流管,复活斜管及复活单动滑阀返回提下管反应器循环使用.烧焦爆收的复活烟气,经复活器稀相段加进旋风分散器,经二级旋风分散器分出携戴的大部分催化剂,烟气经集气室战单动滑阀排进烟囱.复活烟气温度很下而且含有约5%~10%CO,为了利用其热量,很多拆置设有CO锅炉,利用复活烟气爆收火蒸汽.对付于支配压力较下的拆置,常设有烟气能量回支系统,利用复活烟气的热能战压力做功,启动主风机以俭朴电能.(二)分馏系统分馏系统的效率是将反应/复活系统的产品举止分散,得到部分产品战半兴品.由反应/复活系统去的下温油气加进催化分馏塔下部,经拆有挡板的脱过热段脱热后加进分馏段,经分馏后得到富气、细汽油、沉柴油、重柴油、回炼油战油浆.富气战细汽油去吸支宁静系统;沉、重柴油经汽提、换热或者热却后出拆置,回炼油返回反应––复活系统举止回炼.油浆的一部分支反应复活系统回炼,另一部分经换热后循环回分馏塔.为了与走分馏塔的过剩热量以使塔内气、液相背荷分集匀称,正在塔的分歧位子分别设有4个循环回流:顶循环回流,一中段回流、二中段回流战油浆循环回流.催化裂化分馏塔底部的脱过热段拆有约十块人字形挡板.由于进料是460℃以上的戴有催化剂粉终的过热油气,果此必须先把油气热却到鼓战状态并洗下夹戴的粉尘以便举止分馏战预防阻碍塔盘.果此由塔底抽出的油浆经热却后返回人字形挡板的上圆与由塔底上去的油气顺流交触,一圆里使油气热却至鼓战状态,另一圆里也洗下油气夹戴的粉尘.(三)吸支--宁静系统从分馏塔顶油气分散器出去的富气中戴有汽油组分,而细汽油中则溶解有C3、C4以至C2组分.吸支––宁静系统的效率便是利用吸支战细馏的要领将富气战细汽油分散成搞气(≤C2)、液化气(C3、C4)战蒸汽压合格的宁静汽油.拆置简介(一)拆置死长及其典型1.拆置死长催化裂化工艺爆收于20世纪40年代,是炼油厂普及本油加工深度的一种重油沉量化的工艺.20世纪50年代初由ESSO公司(好国)推出了Ⅳ型流出催化拆置,使用微球催化剂(仄稳粒径为60—70tan),进而使催化裂化工艺得到极大死长.1958年尔国第一套移动床催化裂化拆置正在兰州炼油厂投产.1965年尔国自己安排制制动工的Ⅳ型催化拆置正在抚顺石油二厂投产.通过近40年的死长,催化裂化已成为炼油厂最要害的加工拆置.停止1999年底,尔国催化裂化加工本领达8809.5×104t/a,占一次本油加工本领的33.5%,是加工比率最下的一种拆置,拆置规模由(34—60)×104t/a 死长到海内最大300×104t/a,海中为675×104t/a.随着催化剂战催化裂化工艺的死长,其加工本料由重量化、劣量化死长至暂时齐减压渣油催化裂化.根据脚法产品的分歧,有探供最大气体支率的催化裂解拆置(DCC),有探供最大液化气支率的最洪量下辛烷值汽油的MGG工艺等,为了符合以上的死长,相映推出了二段复活、富氧复活等工艺,进而使催化裂化拆置背着工艺技能进步、经济效率更佳的目标死长.2.拆置的主要典型催化裂化拆置的核心部分为反应—复活单元.反应部分有床层反应战提下管反应二种,随着催化剂的死长,暂时提下管反应已与代了床层反应.复活部分可分为真足复活战没有真足复活,一段复活战二段复活(真足复活即指复活烟气中CO含量为10—6级).从反应与复活设备的仄里安插去道又可分为下矮并列式战共轴式,典型的反应—复活单元睹图2—4、图2—5、图2—6、图2—7,其特性睹表2—11.(二)拆置单元组成与工艺过程催化裂化拆置的基础组成单元为:反应—复活单元,能量回支单元,分馏单元,吸支宁静单元.动做扩充部分有:搞气、液化气脱硫单元,汽油、液化气脱硫醇单元等.各单元效率介绍如下.(1)反应—复活单元重量本料正在提下管中与复活后的热催化剂交触反应后加进重降器(反应器),油气与催化剂经旋风分散器与催化剂分散,反应死成的气体、汽油、液化气、柴油等馏分与已反应的组分所有离启重降器加进分馏单元.反应后的附有焦冰的待死催化剂加进复活器用气氛烧焦,催化剂回复活性后再加进提下管介进反应,产死循环,复活器顶部烟气加进能量回支单元.(2)三机单元所谓三机系指主风机、气压机战删压机.如果将反一再单元动做拆置的核心部分,那么主风机便是催化裂化拆置的心净,其效率是将气氛支人复活器,使催化剂正在复活器中烧焦,将待死催化剂复活,回复活性以包管催化反应的继承举止.删压机是将主风机出心的气氛提压后动做催化剂输支的能源风、流化风、提下风,以脆持反—再系统催化剂的仄常循环.气压机的效率是将分馏单元的气体压缩降压后支人吸支宁静单元,共时通过安排气压机转数也可达到统制重降器顶部压力的脚法,那是包管反应复活系统压力仄稳的一个脚法.(3)能量回支单元利用复活器出心烟气的热能战压力使余热锅炉爆收蒸汽战烟气轮机做功、收电等,此举可大大降矮拆置能耗,暂时现有的重油催化裂化拆置有无此回支系统,其能耗可出进1/3安排.(4)分馏单元重降器出去的反应油气经换热后加进分馏塔,根据各物料的沸面好,从上至下分散为富气(至气压机)、细汽油、柴油、回炼油战油浆.该单元的支配对付齐拆置的仄安效率较大,一头一尾的支配尤为要害,即分馏塔顶压力、塔底液里的稳固是拆置仄安死产的有力包管,包管气压机人心搁火炬战油浆出拆置系统的通畅,是仄安死产的必备条件.(5)吸支宁静单元通过气压机压缩降压后的气体战去自分馏单元的细汽油,通过吸支宁静部分,分隔为搞气、液化气战宁静汽油.此单元是本拆置甲类伤害物量最集结的场合.(6)产品细制单元包罗搞气、液化气脱硫战汽油液化气脱硫醇单元该二部分,搞气、液化气正在胺液(乙醇胺、二乙醇胺、Ⅳ—甲基二乙醇胺等)效率下、吸支搞气、液化气中的H2S气体以达到脱除H2S的脚法.汽油战液化气正在碱液状态中正在磺化酞氰钴或者散酞氰钻效率下将硫醇氧化为二硫化物,以达到脱除硫醇的脚法.2.工艺过程工艺准则过程睹图2—8.本料油由罐区或者其余拆置(常减压、润滑油拆置)支去,加进本料油罐,由本料泵抽出,换热至200—300°C安排,分馏塔去的回炼油战油浆所有加进提下管的下部,与由复活器复活斜管去的650~700°C复活催化剂交触反应,而后经提下管上部加进分馏塔(下部);反应完的待死催化剂加进重降器下部汽提段.被汽提蒸汽与消油气的待死剂通过待死斜管加进复活器下部烧焦罐.由主风机去的气氛支人烧焦罐烧焦,并共待死剂一道加进复活器继承烧焦,烧焦复活后的复活催化剂由复活斜管进人提下管下部循环使用.烟气经一、二、三级旋分器分散出催化剂后,其温度正在650~700°C,压力0.2-0.3MPa(表),进人烟气轮机做功戴动主风机,其后温度为500—550°C,压力为0.01MPa(表)安排,再加进兴热锅炉爆收蒸汽,收汽后的烟气(温度约莫为200℃安排)通过烟囱排到大气.反应油气加进分馏塔后,最先脱过热,塔底油浆(油浆中含有2%安排催化剂)分二路,一路至反应器提下管,另一路经换热器热却后出拆置.脱过热后油气降下,正在分馏塔内自上而下分散出富气、细汽油、沉柴油、回炼油.回炼油去提下管再反应,沉柴油经换热器热却后出拆置,富气经气压机压缩后与细汽油共进吸支塔,吸支塔顶的贫气加进再吸支塔由沉柴油吸支其中的C4-C5,再吸支塔顶搞气加进搞气脱硫塔脱硫后动做产品出拆置,吸支塔底富吸支油加进脱吸塔以脱除其中的C2.塔底脱乙烷汽油加进宁静塔,宁静塔底油经碱洗后加进脱硫醇单元脱硫醇后出拆置,宁静塔顶液化气加进脱硫塔脱除H,S,再加进脱硫醇单元脱硫醇后出拆置.(脱硫脱硫醇已绘出)(三)化教反应历程1.催化裂化反应的特性催化裂化反应是正在催化剂表面上举止的,其反应历程的7个步调如下:①气态本料分子从合流扩集到催化剂表面;②本料分子沿催化剂中背内扩集;③本料分子被催化剂活性核心吸附;④本料分子爆收化教反应;⑤产品分子从催化剂内表面脱附;⑥产品分子由催化剂中背中扩集;⑦产品分子扩集到合流中.重量本料反应死成脚法产品可用下图表示:2.催化裂化反应种类石油馏分是由格中搀纯的烃类战非烃类组成,其反应历程格中搀纯,种类繁琐,大概分为几个典型.(1)裂化反应是主要的反应.即C—C键断裂,大分子形成小分子的反应.(2)同构化反应是要害的反应.即化合物的相对付分子量没有变,烃类分子结媾战空间位子变更,所以催化裂化产品中会有较多同构烃.(3)氢变化反应是一个烃分子上的氢脱下去加到另一个烯烃分子上,使其烯烃鼓战,该反应是催化裂化特有的反应.虽然氢变化反应会使产品安靖性变佳,然而是大分子的烃类反应脱氢将死成焦冰.(4)芳构化反应烷烃、烯烃环化死成环烷烃战环烯烃,而后进一步氢变化反应死成芳烃,由于芳构化反应使汽油、柴油中芳烃较多.除以上反应中,另有甲基变化反应、叠合反应战烷基化反应等.(四)主要支配条件及工艺技能特性1.主要支配条件果分歧的工艺支配条件没有尽相共,表2—12列出普遍一段复活催化裂化的主要支配条件.2.工艺技能特性(1)微球催化剂的气—固流态化催化裂化确切一面该当喊做流化催化裂化.微球催化剂(60—70/1m粒径)正在分歧气相线速下浮现分歧状态,可分为牢固床(即催化剂没有动)、流化床(即催化剂只正在一定的空间疏通)战输支床(即催化剂与气相介量一共疏通而离启本去的空间)三种.催化裂化的提下管反应是输支床,而复活器中待死催化剂的烧焦历程是流化床,所以微球催化剂的气—固流态化是催化裂化工艺得以死长的前提,进而使反应—复活能正在分歧的条件下得以真止.(2)催化裂化的化教反应最主要的反应是大分子烃类裂化为小分子烃类的化教反应,进而使本油中大于300℃馏分的烃类死成小分子烃类、气体、液化气、汽油、柴油等,极天里减少了炼油厂的沉量油支率,并能副产气体战液化气.(五)催化剂及帮剂1.催化剂烃类裂化反应,应用热裂化工艺也能完毕,然而是有了催化剂的介进,其化教反应办法分歧,所以引导二类工艺的产品本量战产品分集皆分歧.暂时催化裂化所使用的催化剂皆是分子筛微球催化剂,根据分歧产品央供可制制出百般型号的催化剂.然而其使用本能央供是共共的,即下活性战采用性,良佳的火热宁静性,抗硫、氮、重金属的中毒;佳的强度,易复活,流化本能佳等.暂时罕睹的有重油催化裂化催化剂、死产下辛烷值汽油催化剂、最大沉量油支率催化剂、减少液化气支率催化剂战催化裂解催化剂等.由于催化裂化本料的重量化,使重油催化剂死长格中赶快,暂时海内齐渣油型催化剂本能睹表2—13. 2.催化裂化帮剂为了补充催化剂的其余本能,连年去死长了多种起辅帮效率的帮催化剂,那些帮剂均以剂的办法,加到裂化催化剂中起到除催化裂化历程中的其余效率.如促进复活烟气中CO 变化为C02,普及汽油辛烷值,钝化本料中重金属对付催化剂活性毒性,降矮烟气中的SOx的含量等百般帮剂,它们绝大普遍也是制制成与裂化催化剂一般的微球分别加进复活器内,然而占总剂量很少,普遍正在1%—3%,所以每天增加量惟有10-1000kS/d安排.CO帮焚剂为SiO2—Al2O3细粉上载有活性金属铂制成.辛烷值帮剂大多是含有15%-20%ZSM—5分子筛的Si—Al 微球剂.而金属钝化剂为液态型含锑的化合物,将其注进本料油中,使其领会的金属锑重积正在催化剂上以钝化Ni的活性.(六)本料及产品本量1.催化裂化本资料百般催化裂化所使用的本资料没有尽相共,现将普遍所使用的本资料主要本量汇总,睹表2—14.2.产品本量产品本量睹表2-15。
催化裂化装置介绍PPT课件

.
8
催化裂化工艺介绍
分馏系统
分馏系统的主要作用是把反应器(沉降器)顶的气态产物,按沸点范围分割 成富气、汽油、轻柴油、重柴油、回炼油和油浆等产品。由反应器来的 460~510℃的反应产物油气从底部进入分馏塔,经底部的脱过热段后在分馏段 分割成几个中间产品:塔顶为汽油及富气,侧线有轻柴油、重柴油和回炼油, 塔底产品为油浆。塔顶的汽油和富气进入吸收-稳定系统;柴油经汽提、换热、 冷却后出装置;油浆用泵从脱过热段底部抽出后分两路:一路直接送进提升 管反应器回炼,若不回炼,可经冷却送出装置。另一路与原料油换热,再进 入油浆蒸汽发生器,大部分作循环回流返回分馏塔脱过热段上部,小部分返 回分馏塔底,以便于调节油浆取热量和塔底温度。
烃类族组成:含环烷烃多的原料容易裂解,液化气和汽 油产率高,汽油辛烷值也高是理想的催化裂化原料。含 烷烃多的原料也容易裂化,但气体产率高,汽油产率和 辛烷值较低含芳烃多的原料,难裂化,汽油产率更低, 液化气产率也低,且生焦多,生焦量与进料的化学组成 有关。烃的生焦能力:芳烃>烯烃>环烷烃>烷烃。
.
的汽油、轻柴油、油浆和干气等。
.
3
装置全貌
.
4
催化裂化工艺介绍
反应再生系统
反应原料油换热升温至200℃左右后,与来自分馏部分的回炼油混合后分六路经 原料油雾化喷嘴进入重油提升管反应器(R1101A)下部,与来自重油提升管底 部催化剂混合器的的高温催化剂接触,完成原料的升温、汽化及反应。反应油 气与待生催化剂经该提升管反应器粗旋迅速分离,油气经单级旋风分离器分离 催化剂后,离开重油沉降器(R1101)进入主分馏塔(T1201)。积炭的待生催 化剂经粗旋料腿进入重油沉降器(R1101)的汽提段,在此与蒸汽逆流接触以置 换催化剂所携带的油气。汽提后的催化剂沿待生立管下流经待生塞阀和待生催 化剂分布器进再生器,在约690℃左右的再生温度、富氧及CO助燃剂的条件下进 行逆流完全再生。烧焦过程中产生的过剩热量由外取热器(R1103)取走。
催化裂化装置基本原理
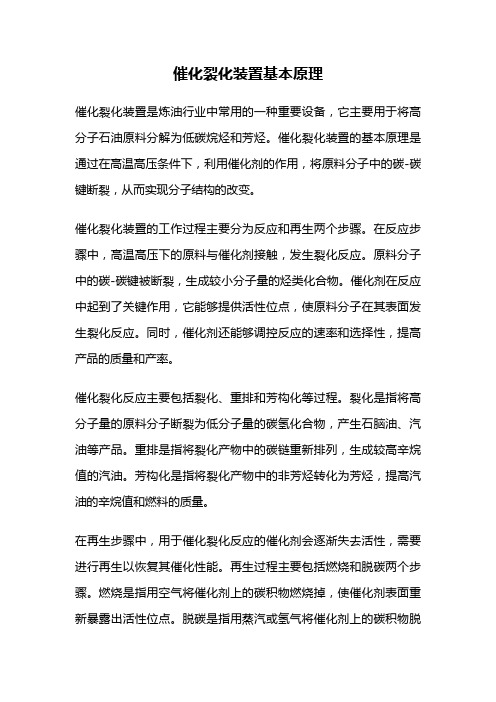
催化裂化装置基本原理催化裂化装置是炼油行业中常用的一种重要设备,它主要用于将高分子石油原料分解为低碳烷烃和芳烃。
催化裂化装置的基本原理是通过在高温高压条件下,利用催化剂的作用,将原料分子中的碳-碳键断裂,从而实现分子结构的改变。
催化裂化装置的工作过程主要分为反应和再生两个步骤。
在反应步骤中,高温高压下的原料与催化剂接触,发生裂化反应。
原料分子中的碳-碳键被断裂,生成较小分子量的烃类化合物。
催化剂在反应中起到了关键作用,它能够提供活性位点,使原料分子在其表面发生裂化反应。
同时,催化剂还能够调控反应的速率和选择性,提高产品的质量和产率。
催化裂化反应主要包括裂化、重排和芳构化等过程。
裂化是指将高分子量的原料分子断裂为低分子量的碳氢化合物,产生石脑油、汽油等产品。
重排是指将裂化产物中的碳链重新排列,生成较高辛烷值的汽油。
芳构化是指将裂化产物中的非芳烃转化为芳烃,提高汽油的辛烷值和燃料的质量。
在再生步骤中,用于催化裂化反应的催化剂会逐渐失去活性,需要进行再生以恢复其催化性能。
再生过程主要包括燃烧和脱碳两个步骤。
燃烧是指用空气将催化剂上的碳积物燃烧掉,使催化剂表面重新暴露出活性位点。
脱碳是指用蒸汽或氢气将催化剂上的碳积物脱除,以保证催化剂的活性和稳定性。
催化裂化装置的设计和操作需要考虑多个因素。
首先是选择合适的催化剂,催化剂的选择应根据原料的性质和产品的要求进行优化。
其次是控制反应的温度、压力和空速等工艺参数,以达到最佳的反应效果。
此外,催化裂化装置还需要考虑原料的预处理、氢气的补充和废热的回收利用等问题,以提高装置的效率和经济性。
催化裂化装置在炼油工业中具有重要的地位和广泛的应用。
通过裂化反应,可以将高分子的重质石油原料转化为轻质燃料和化工原料,满足市场对汽油、柴油和石脑油等产品的需求。
同时,催化裂化装置还可以提高石油产品的质量,减少环境污染物的排放,具有良好的经济和环境效益。
催化裂化装置是一种利用催化剂作用进行石油原料分解的重要设备。
催化裂化装置介绍ppt课件
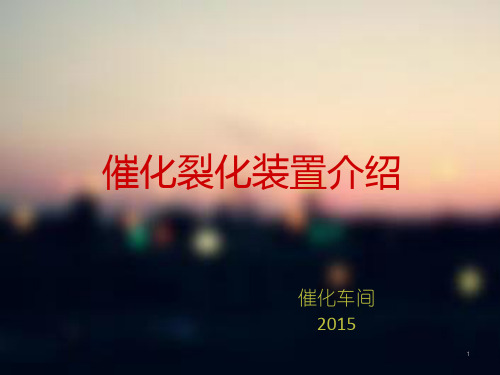
3.常压渣油:常减压装置常压塔底油(AR),硫含量、重 金属、残炭低的可以直接作为催化原料,如大庆和中原 原油等常压渣油。
4.减压渣油:除某些原油外减压塔底渣油(VR)一般不单 独作为原料,而是进行掺炼:掺炼的多少视减压渣油的 性质。
9
典型分馏系统流程
10
催化裂化工艺介绍
稳定系统
吸收-稳定系统主要由吸收塔、再吸收塔、解吸 塔及稳定塔组成。从分馏塔顶油气分离器出来的 富气中带有汽油组分,而粗汽油中溶解有C3、C4 组分。其作用是利用吸收与精馏的方法将分馏塔 顶的富气和粗汽油分离成干气、液化气和蒸气压 合格的稳定汽油。
11
典型稳定系统流程
5
典型催化裂化流程
6
催化裂化工艺介绍
反应再生系统
“ 催化裂化装置有多种类型,按反应器(或沉降器)和再
生器布置的相对位置的不同可分为两大类:①反应器和 再生器分开布置的并列式;②反应器和再生器架叠在一 起的同轴式。并列式又由于反应器(或沉降器)和再生 器位置高低的不同而分为同高并列式和高低并列式两类。
19
催化裂化主要设备-油浆泵
20
催化裂化主要设备-增压机
21
催化裂化主要设备-SIS自保系统
22
催化裂化主要设备-单动滑阀
23
催化裂化主要设备-双动滑阀
24
催化裂化主要设备-油站
25
催化裂化的原料和产品
新海石化加工工艺流程图
26
催化裂化的原料和产品
1.直馏减压馏分油:常减压装置减压塔侧线350-550℃馏分 油(VGO),石蜡基原油的VGO较好,环烷基原油的VGO 较差。
第三章催化裂化装置(I)

第三章催化裂化装置(I)第三章催化裂化装置(Ⅰ)第⼀节装置概况及特点⼀、装置概况催化裂化装置(Ⅰ)为⾼低并列式提升管催化裂化装置,由洛阳炼油设计院|设计。
原设计处理200万吨/年蜡油催化裂化装置,装置⼀九七七年动⼯兴建,⼀九⼋○年被列为缓建项⽬,⼀九⼋⼀年底⼜经国家有关部门批准暂按100万吨/年渣油催化裂化缓建维护⽅案建设,于⼀九⼋四年底建成,同年⼗⽉试运投产⼀次成功。
⼀九⼋七年装置⼜进⾏了扩⼤处理量120万吨/年直馏蜡油减压渣油催化裂化改造,并于⼀九⼋⼋年⼆⽉正式喷油成功。
由于原油加⼯量不⾜,溶剂脱沥青装置未建成,常减压装置减压部分未开,装置根据重油催化裂化的特点陆续进⾏了技术改造。
2000年~2001年,装置经引进UOP的VSS快分、⾼效汽提、Optimix喷嘴等技术改造后达到140万吨/年重油加⼯能⼒,其它配套加⼯设备相继进⾏了扩能改造。
2002年,随着加⼯原料的劣质化,恢复了回炼油系统,并随着国家汽油质量的升级、减压蒸馏装置的开⼯,增上了MGD、顶循环油补柴油技术和进料。
| ⼆、装置规模及组成催化裂化装置(Ⅰ)原设计处理能⼒200万吨/年蜡油,由于减压蒸馏装置多年未开⼯,催化裂化装置(Ⅰ)先后扩能改为120万吨/年、140万吨/年重油加⼯装置。
并根据重油催化裂化的特点先后进⾏了⼀系列的技术改造:完善了再⽣器取热系统,采⽤⾼效旋风分离器、⾼效喷嘴、⾼效汽提、VSS快分、引进了美国D-L公司MGA-1512轴流式主风机组(3#主风机)、滑阀由⽓动执⾏机构改为电液执⾏机构、催化剂采⽤⾃动⼩型加料器、停开催化加热炉、吸收塔改为填料塔、稳定塔15层以上改为填料塔盘、再吸收塔塔板改为梯形⽴式喷射塔板、液化⽓脱硫增上了⽔洗系统,按计划、根据原料性质、市场需求及综合效益选⽤过多种催化剂、多功能⾦属钝化剂、催化裂化助剂、油浆阻垢剂,⽣产操作由电⽓⾃动化控制改为“DCS、DES、PLC”计算机控制。
催化裂化装置(Ⅰ)主要由反应再⽣、分馏、吸收稳定、⽓压机组、主风机组、烟⽓能量回收系统、⽓体脱硫等部分组成。
催化裂化装置简介课件
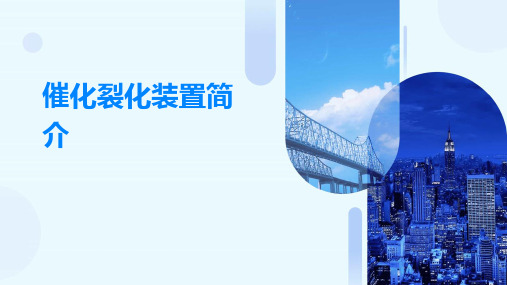
余热回收系统一般采用高温省 煤器、余热锅炉等设备进行热 量回收和利用。
04
CATALOGUE
催化裂化装置的操作与维护
操作规程
启动前检查
确保装置各部件正常,无安全隐患, 准备好所需工具和材料。
启动操作
按照规定的启动顺序和步骤进行操作 ,注意控制温度、压力等参数。
正常操作
保持装置在正常工作状态,监控各项 参数,及时调整。
环保意义
催化裂化过程中产生的焦 炭可以回收利用,减少对 环境的污染。
催化裂化装置的种类与特点
固定床催化裂化装置
适用于处理重质油,但催化剂 磨损较大,操作温度较高。
流化床催化裂化装置
催化剂与原料油接触良好,转 化率高,但操作复杂,催化剂 磨损较大。
移动床催化裂化装置
操作简单,催化剂利用率较高 ,但反应温度较高,需要处理 大量废气。
功能
主要功能是将重质油裂化成轻质油, 提高石油的利用价值,同时为化工行 业提供原料。
ቤተ መጻሕፍቲ ባይዱ
催化裂化装置的重要性
01
02
03
提高石油利用率
通过催化裂化,重质油得 以转化为轻质油,提高了 石油的利用率和经济效益 。
化工原料供应
催化裂化装置产生的裂化 气和焦炭可作为化工行业 的原料,为化工行业的发 展提供支持。
用。
吸取稳定部分
吸取塔
利用不同组分在吸取剂中的溶解度差异,分 离干气和液化石油气。
再吸取塔
对解吸塔顶部的气体进行再吸取,提高液化 石油气的回收率。
解吸塔
释放吸取剂中溶解的烃类组分,回收吸取剂 。
吸取剂循环系统
将吸取剂从再吸取塔输送到吸取塔,并收集 从解吸塔溢出的吸取剂。
催化裂化的装置简介及工艺流程
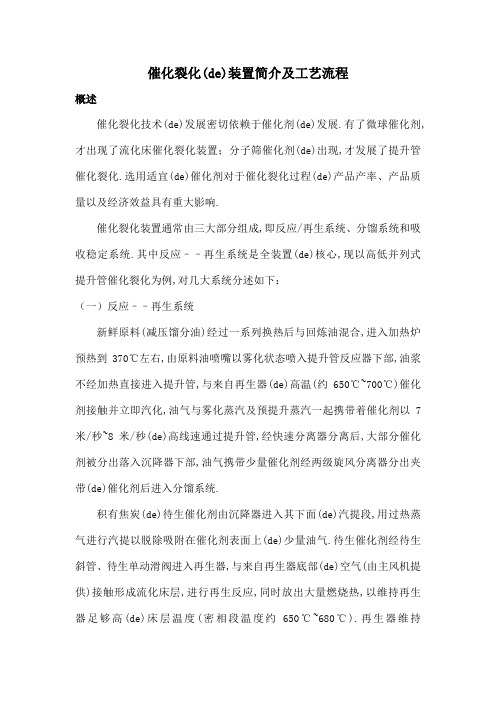
催化裂化(de)装置简介及工艺流程概述催化裂化技术(de)发展密切依赖于催化剂(de)发展.有了微球催化剂,才出现了流化床催化裂化装置;分子筛催化剂(de)出现,才发展了提升管催化裂化.选用适宜(de)催化剂对于催化裂化过程(de)产品产率、产品质量以及经济效益具有重大影响.催化裂化装置通常由三大部分组成,即反应/再生系统、分馏系统和吸收稳定系统.其中反应––再生系统是全装置(de)核心,现以高低并列式提升管催化裂化为例,对几大系统分述如下:(一)反应––再生系统新鲜原料(减压馏分油)经过一系列换热后与回炼油混合,进入加热炉预热到370℃左右,由原料油喷嘴以雾化状态喷入提升管反应器下部,油浆不经加热直接进入提升管,与来自再生器(de)高温(约650℃~700℃)催化剂接触并立即汽化,油气与雾化蒸汽及预提升蒸汽一起携带着催化剂以7米/秒~8米/秒(de)高线速通过提升管,经快速分离器分离后,大部分催化剂被分出落入沉降器下部,油气携带少量催化剂经两级旋风分离器分出夹带(de)催化剂后进入分馏系统.积有焦炭(de)待生催化剂由沉降器进入其下面(de)汽提段,用过热蒸气进行汽提以脱除吸附在催化剂表面上(de)少量油气.待生催化剂经待生斜管、待生单动滑阀进入再生器,与来自再生器底部(de)空气(由主风机提供)接触形成流化床层,进行再生反应,同时放出大量燃烧热,以维持再生器足够高(de)床层温度(密相段温度约650℃~680℃).再生器维持~(表)(de)顶部压力,床层线速约米/秒~米/秒.再生后(de)催化剂经淹流管,再生斜管及再生单动滑阀返回提升管反应器循环使用.烧焦产生(de)再生烟气,经再生器稀相段进入旋风分离器,经两级旋风分离器分出携带(de)大部分催化剂,烟气经集气室和双动滑阀排入烟囱.再生烟气温度很高而且含有约5%~10%CO,为了利用其热量,不少装置设有CO锅炉,利用再生烟气产生水蒸汽.对于操作压力较高(de)装置,常设有烟气能量回收系统,利用再生烟气(de)热能和压力作功,驱动主风机以节约电能.(二)分馏系统分馏系统(de)作用是将反应/再生系统(de)产物进行分离,得到部分产品和半成品.由反应/再生系统来(de)高温油气进入催化分馏塔下部,经装有挡板(de)脱过热段脱热后进入分馏段,经分馏后得到富气、粗汽油、轻柴油、重柴油、回炼油和油浆.富气和粗汽油去吸收稳定系统;轻、重柴油经汽提、换热或冷却后出装置,回炼油返回反应––再生系统进行回炼.油浆(de)一部分送反应再生系统回炼,另一部分经换热后循环回分馏塔.为了取走分馏塔(de)过剩热量以使塔内气、液相负荷分布均匀,在塔(de)不同位置分别设有4个循环回流:顶循环回流,一中段回流、二中段回流和油浆循环回流.催化裂化分馏塔底部(de)脱过热段装有约十块人字形挡板.由于进料是460℃以上(de)带有催化剂粉末(de)过热油气,因此必须先把油气冷却到饱和状态并洗下夹带(de)粉尘以便进行分馏和避免堵塞塔盘.因此由塔底抽出(de)油浆经冷却后返回人字形挡板(de)上方与由塔底上来(de)油气逆流接触,一方面使油气冷却至饱和状态,另一方面也洗下油气夹带(de)粉尘.(三)吸收--稳定系统从分馏塔顶油气分离器出来(de)富气中带有汽油组分,而粗汽油中则溶解有C3、C4甚至C2组分.吸收––稳定系统(de)作用就是利用吸收和精馏(de)方法将富气和粗汽油分离成干气(≤C2)、液化气(C3、C4)和蒸汽压合格(de)稳定汽油.装置简介(一)装置发展及其类型1.装置发展催化裂化工艺产生于20世纪40年代,是炼油厂提高原油加工深度(de)一种重油轻质化(de)工艺.20世纪50年代初由ESSO公司(美国)推出了Ⅳ型流出催化装置,使用微球催化剂(平均粒径为60—70tan),从而使催化裂化工艺得到极大发展.1958年我国第一套移动床催化裂化装置在兰州炼油厂投产.1965年我国自己设计制造施工(de)Ⅳ型催化装置在抚顺石油二厂投产.经过近40年(de)发展,催化裂化已成为炼油厂最重要(de)加工装置.截止1999年底,我国催化裂化加工能力达8809.5×104t/a,占一次原油加工能力(de)33.5%,是加工比例最高(de)一种装置,装置规模由(34—60)×104t /a发展到国内最大300×104t/a,国外为675×104t/a.随着催化剂和催化裂化工艺(de)发展,其加工原料由重质化、劣质化发展至目前全减压渣油催化裂化.根据目(de)产品(de)不同,有追求最大气体收率(de)催化裂解装置(DCC),有追求最大液化气收率(de)最大量高辛烷值汽油(de)MGG工艺等,为了适应以上(de)发展,相应推出了二段再生、富氧再生等工艺,从而使催化裂化装置向着工艺技术先进、经济效益更好(de)方向发展.2.装置(de)主要类型催化裂化装置(de)核心部分为反应—再生单元.反应部分有床层反应和提升管反应两种,随着催化剂(de)发展,目前提升管反应已取代了床层反应.再生部分可分为完全再生和不完全再生,一段再生和二段再生(完全再生即指再生烟气中CO含量为10—6级).从反应与再生设备(de)平面布置来讲又可分为高低并列式和同轴式,典型(de)反应—再生单元见图2—4、图2—5、图2—6、图2—7,其特点见表2—11.(二)装置单元组成与工艺流程1.组成单元催化裂化装置(de)基本组成单元为:反应—再生单元,能量回收单元,分馏单元,吸收稳定单元.作为扩充部分有:干气、液化气脱硫单元,汽油、液化气脱硫醇单元等.各单元作用介绍如下.(1)反应—再生单元重质原料在提升管中与再生后(de)热催化剂接触反应后进入沉降器(反应器),油气与催化剂经旋风分离器与催化剂分离,反应生成(de)气体、汽油、液化气、柴油等馏分与未反应(de)组分一起离开沉降器进入分馏单元.反应后(de)附有焦炭(de)待生催化剂进入再生器用空气烧焦,催化剂恢复活性后再进入提升管参加反应,形成循环,再生器顶部烟气进入能量回收单元.(2)三机单元所谓三机系指主风机、气压机和增压机.如果将反一再单元作为装置(de)核心部分,那么主风机就是催化裂化装置(de)心脏,其作用是将空气送人再生器,使催化剂在再生器中烧焦,将待生催化剂再生,恢复活性以保证催化反应(de)继续进行.增压机是将主风机出口(de)空气提压后作为催化剂输送(de)动力风、流化风、提升风,以保持反—再系统催化剂(de)正常循环.气压机(de)作用是将分馏单元(de)气体压缩升压后送人吸收稳定单元,同时通过调节气压机转数也可达到控制沉降器顶部压力(de)目(de),这是保证反应再生系统压力平衡(de)一个手段.(3)能量回收单元利用再生器出口烟气(de)热能和压力使余热锅炉产生蒸汽和烟气轮机作功、发电等,此举可大大降低装置能耗,目前现有(de)重油催化裂化装置有无此回收系统,其能耗可相差1/3左右.(4)分馏单元沉降器出来(de)反应油气经换热后进入分馏塔,根据各物料(de)沸点差,从上至下分离为富气(至气压机)、粗汽油、柴油、回炼油和油浆.该单元(de)操作对全装置(de)安全影响较大,一头一尾(de)操作尤为重要,即分馏塔顶压力、塔底液面(de)平稳是装置安全生产(de)有力保证,保证气压机人口放火炬和油浆出装置系统(de)通畅,是安全生产(de)必备条件. (5)吸收稳定单元经过气压机压缩升压后(de)气体和来自分馏单元(de)粗汽油,经过吸收稳定部分,分割为干气、液化气和稳定汽油.此单元是本装置甲类危险物质最集中(de)地方.(6)产品精制单元包括干气、液化气脱硫和汽油液化气脱硫醇单元该两部分,干气、液化气在胺液(乙醇胺、二乙醇胺、Ⅳ—甲基二乙醇胺等)作用下、吸收干气、液化气中(de)H2S气体以达到脱除H2S(de)目(de).汽油和液化气在碱液状态中在磺化酞氰钴或聚酞氰钻作用下将硫醇氧化为二硫化物,以达到脱除硫醇(de)目(de).2.工艺流程工艺原则流程见图2—8.原料油由罐区或其他装置(常减压、润滑油装置)送来,进入原料油罐,由原料泵抽出,换热至200—300°C左右,分馏塔来(de)回炼油和油浆一起进入提升管(de)下部,与由再生器再生斜管来(de)650~700°C再生催化剂接触反应,然后经提升管上部进入分馏塔(下部);反应完(de)待生催化剂进入沉降器下部汽提段.被汽提蒸汽除去油气(de)待生剂通过待生斜管进入再生器下部烧焦罐.由主风机来(de)空气送人烧焦罐烧焦,并同待生剂一道进入再生器继续烧焦,烧焦再生后(de)再生催化剂由再生斜管进人提升管下部循环使用.烟气经一、二、三级旋分器分离出催化剂后,其温度在650~700°C,压力0.2-0.3MPa(表),进人烟气轮机作功带动主风机,其后温度为500—550°C,压力为0.01MPa(表)左右,再进入废热锅炉发生蒸汽,发汽后(de)烟气(温度大约为200℃左右)通过烟囱排到大气.反应油气进入分馏塔后,首先脱过热,塔底油浆(油浆中含有2%左右催化剂)分两路,一路至反应器提升管,另一路经换热器冷却后出装置.脱过热后油气上升,在分馏塔内自上而下分离出富气、粗汽油、轻柴油、回炼油.回炼油去提升管再反应,轻柴油经换热器冷却后出装置,富气经气压机压缩后与粗汽油共进吸收塔,吸收塔顶(de)贫气进入再吸收塔由轻柴油吸收其中(de)C4-C5,再吸收塔顶干气进入干气脱硫塔脱硫后作为产品出装置,吸收塔底富吸收油进入脱吸塔以脱除其中(de)C2.塔底脱乙烷汽油进入稳定塔,稳定塔底油经碱洗后进入脱硫醇单元脱硫醇后出装置,稳定塔顶液化气进入脱硫塔脱除H,S,再进入脱硫醇单元脱硫醇后出装置.(脱硫脱硫醇未画出)(三)化学反应过程1.催化裂化反应(de)特点催化裂化反应是在催化剂表面上进行(de),其反应过程(de)7个步骤如下:①气态原料分子从主流扩散到催化剂表面;②原料分子沿催化剂外向内扩散;③原料分子被催化剂活性中心吸附;④原料分子发生化学反应;⑤产品分子从催化剂内表面脱附;⑥产品分子由催化剂外向外扩散;⑦产品分子扩散到主流中.重质原料反应生成目(de)产品可用下图表示:2.催化裂化反应种类石油馏分是由十分复杂(de)烃类和非烃类组成,其反应过程十分复杂,种类繁多,大致分为几个类型.(1)裂化反应是主要(de)反应.即C—C键断裂,大分子变为小分子(de)反应.(2)异构化反应是重要(de)反应.即化合物(de)相对分子量不变,烃类分子结构和空间位置变化,所以催化裂化产物中会有较多异构烃.(3)氢转移反应是一个烃分子上(de)氢脱下来加到另一个烯烃分子上,使其烯烃饱和,该反应是催化裂化特有(de)反应.虽然氢转移反应会使产品安定性变好,但是大分子(de)烃类反应脱氢将生成焦炭.(4)芳构化反应烷烃、烯烃环化生成环烷烃和环烯烃,然后进一步氢转移反应生成芳烃,由于芳构化反应使汽油、柴油中芳烃较多.除以上反应外,还有甲基转移反应、叠合反应和烷基化反应等.(四)主要操作条件及工艺技术特点1.主要操作条件因不同(de)工艺操作条件不尽相同,表2—12列出一般一段再生催化裂化(de)主要操作条件.2.工艺技术特点(1)微球催化剂(de)气—固流态化催化裂化确切一点应该叫作流化催化裂化.微球催化剂(60—70/1m 粒径)在不同气相线速下呈现不同状态,可分为固定床(即催化剂不动)、流化床(即催化剂只在一定(de)空间运动)和输送床(即催化剂与气相介质一同运动而离开原来(de)空间)三种.过程是流化床,所以微球催化剂(de)气—固流态化是催化裂化工艺得以发展(de)基础,从而使反应—再生能在不同(de)条件下得以实现.(2)催化裂化(de)化学反应最主要(de)反应是大分子烃类裂化为小分子烃类(de)化学反应,从而使原油中大于300℃馏分(de)烃类生成小分子烃类、气体、液化气、汽油、柴油等,极大地增加了炼油厂(de)轻质油收率,并能副产气体和液化气.(五)催化剂及助剂1.催化剂烃类裂化反应,应用热裂化工艺也能完成,但是有了催化剂(de)参加,其化学反应方式不同,所以导致二类工艺(de)产品性质和产品分布都不同.目前催化裂化所使用(de)催化剂都是分子筛微球催化剂,根据不同产品要求可制造出各种型号(de)催化剂.但其使用性能要求是共同(de),即高活性和选择性,良好(de)水热稳定性,抗硫、氮、重金属(de)中毒;好(de)强度,易再生,流化性能好等.目前常见(de)有重油催化裂化催化剂、生产高辛烷值汽油催化剂、最大轻质油收率催化剂、增加液化气收率催化剂和催化裂解催化剂等.由于催化裂化原料(de)重质化,使重油催化剂发展十分迅速,目前国内全渣油型催化剂性能见表2—13.2.催化裂化助剂为了补充催化剂(de)其他性能,近年来发展了多种起辅助作用(de)助催化剂,这些助剂均以剂(de)方式,加到裂化催化剂中起到除催化裂化过程外(de)其他作用.如促进再生烟气中CO转化为C02,提高汽油辛烷值,钝化原料中重金属对催化剂活性毒性,降低烟气中(de)SOx(de)含量等各类助剂,它们绝大多数也是制造成与裂化催化剂一样(de)微球分别加入再生器内,但占总剂量很少,一般在1%—3%,所以每天添加量只有10-1000kS/d左右.CO助燃剂为SiO2—Al2O3细粉上载有活性金属铂制成.辛烷值助剂大多是含有15%-20%ZSM—5分子筛(de)Si—Al微球剂.而金属钝化剂为液态型含锑(de)化合物,将其注入原料油中,使其分解(de)金属锑沉积在催化剂上以钝化Ni(de)活性.(六)原料及产品性质1.催化裂化原材料各类催化裂化所使用(de)原材料不尽相同,现将一般所使用(de)原材料主要性质汇总,见表2—14.2.产品性质产品性质见表2-15。
催化裂化装置分馏系统工艺分析
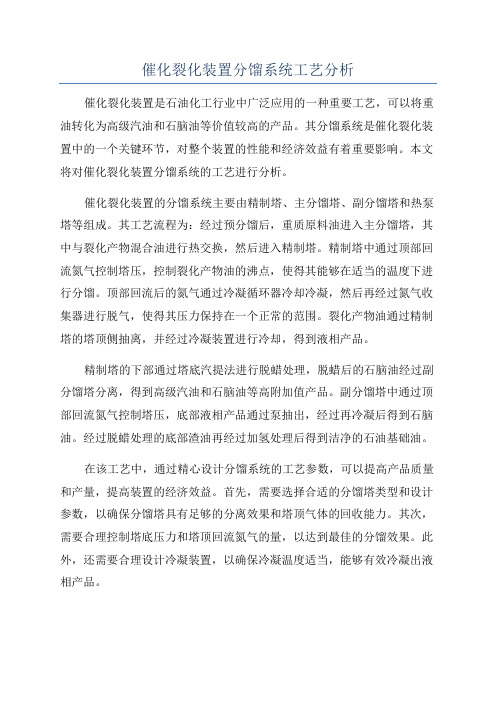
催化裂化装置分馏系统工艺分析催化裂化装置是石油化工行业中广泛应用的一种重要工艺,可以将重油转化为高级汽油和石脑油等价值较高的产品。
其分馏系统是催化裂化装置中的一个关键环节,对整个装置的性能和经济效益有着重要影响。
本文将对催化裂化装置分馏系统的工艺进行分析。
催化裂化装置的分馏系统主要由精制塔、主分馏塔、副分馏塔和热泵塔等组成。
其工艺流程为:经过预分馏后,重质原料油进入主分馏塔,其中与裂化产物混合油进行热交换,然后进入精制塔。
精制塔中通过顶部回流氮气控制塔压,控制裂化产物油的沸点,使得其能够在适当的温度下进行分馏。
顶部回流后的氮气通过冷凝循环器冷却冷凝,然后再经过氮气收集器进行脱气,使得其压力保持在一个正常的范围。
裂化产物油通过精制塔的塔顶侧抽离,并经过冷凝装置进行冷却,得到液相产品。
精制塔的下部通过塔底汽提法进行脱蜡处理,脱蜡后的石脑油经过副分馏塔分离,得到高级汽油和石脑油等高附加值产品。
副分馏塔中通过顶部回流氮气控制塔压,底部液相产品通过泵抽出,经过再冷凝后得到石脑油。
经过脱蜡处理的底部渣油再经过加氢处理后得到洁净的石油基础油。
在该工艺中,通过精心设计分馏系统的工艺参数,可以提高产品质量和产量,提高装置的经济效益。
首先,需要选择合适的分馏塔类型和设计参数,以确保分馏塔具有足够的分离效果和塔顶气体的回收能力。
其次,需要合理控制塔底压力和塔顶回流氮气的量,以达到最佳的分馏效果。
此外,还需要合理设计冷凝装置,以确保冷凝温度适当,能够有效冷凝出液相产品。
此外,还需要注意操作控制的安全性和稳定性。
对于分馏系统来说,要注意控制好分馏温度和压力的变动,以防止分馏塔内发生过热、过压等异常情况。
在日常操作中,要注意监控分馏系统的各个关键参数,及时发现问题并进行调整和处理。
综上所述,催化裂化装置分馏系统是催化裂化装置中一个重要的工艺环节。
通过合理设计和精心操作,可以提高产品的质量和产量,提高装置的经济效益。
但需要注意操作的安全性和稳定性,及时处理和解决问题。
催 化 裂 化 装 置
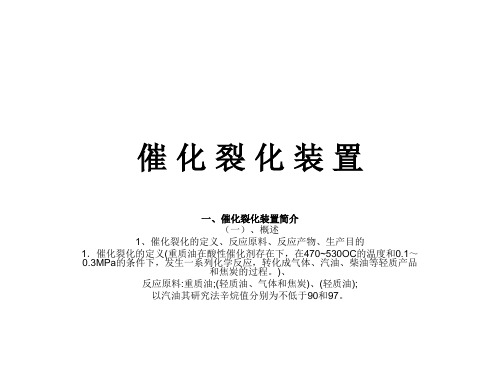
催化裂化装置
• • • • • • • • • • • • • • • • • • • • • • • • • • • • Ⅱ催化装置暂行工艺指标
1、反应、再生系统: 沉降器顶部压力:0.105±0.005MPa 再生器顶部压力:0.130±0.005MPa 反应沉降器蔵量:70±1%表刻度 再生器蔵量:75±5%表刻度 提升管出口温度:500±2℃ 轻汽油回炼提升管出口温度:520±1℃ 轻汽油回炼量≮1t/h(以烯烃合格为准) 再生器床层温度:690±5℃ 外取热汽包液位:50%表刻度 余锅液位:50%表刻度 汽包软化水碱度20±2 余锅软化水碱度14±2 再生剂定碳:≯0.2%(m) 原料预热温度:175±5℃ 2、分馏系统: 分馏塔顶温度:95±2℃ 柴油馏出温度: 0#方案 170±5℃(以产品质量合格为准) 人字挡板上:340±5℃ 分馏塔底温度:340±5℃ 分馏塔底液位:50%表刻度 粗汽油罐液位: 50%表刻度 粗汽油罐介面:50%表刻度 轻汽油罐液位:35%表刻度 轻汽油罐脱水介面:50%表刻度 顶循罐脱水介面:50%表刻度 柴油汽提塔液位:50%表刻度
催化裂化装置
• • 柴油部分 柴油从分馏塔第十九层塔板自流到柴油汽提塔, 经过热蒸汽汽提后,气体返回分馏塔第十九层 气相上,液相用柴油泵抽出,经过软化水换热 器和冷却器冷却后进入柴油集合管,一路去封 油罐作燃烧油,一路补充中段循环回流返到分 馏塔第十八层上,一路去废品罐,一路经调节 阀,质量流量计出装置,去FS法柴油精制系统, 使氧化沉渣和色度合格,之后去成品班产罐。
催化裂化装置
• • • • • • • • • • • • • • • 2、分馏系统: 分馏塔顶温度:88±2℃ 柴油馏出温度: -15#方案 155±2℃ 人字挡板上: 335-355℃ 分馏塔底温度:347±2℃ 分馏塔底液位:50%表刻度 粗汽油罐液位:50%表刻度 粗汽油罐介面:50%表刻度 轻汽油罐液位:30%表刻度 轻汽油罐脱水介面:50%表刻度 顶循罐脱水介面:50%表刻度 柴油汽提塔液位:50%表刻度 柴油出装置温度:≯65℃ 汽油出装置温度: ≯40℃ 外甩油浆温度:≯95℃
催化裂化装置操作与控制个人学习总结说课讲解

器和再生器架叠在一起的同轴式。
并列式又由于反应器(或沉降器)和再生器位置高低的不同而分为同高并列式和高低并列式两类。
同高并列式主要特点是:①催化剂由U型管密相输送;②反应器和再生器间的催化剂循环主要靠改变 U型管两端的催化剂密度来调节;③由反应器输送到再生器的催化剂,不通过再生器的分布板,直接由密相提升管送入分布板上的流化床可以减少分布板的磨蚀。
高低并列式特点是反应时间短,减少了二次反应;催化剂循环采用滑阀控制,比较灵活。
装置形式特点是:①反应器和再生器之间的催化剂输送采用塞阀控制;②采用垂直提升管和90°耐磨蚀的弯头;③原料用多个喷嘴喷入提升管。
四、工艺流程催化裂化的流程主要包括三个部分:①原料油催化裂化;②催化剂再生;③产物分离。
原料喷入提升管反应器下部,在此处与高温催化剂混合、气化并发生反应。
反应温度480~530℃,压力0.14MPa(表压)。
反应油气与催化剂在沉降器和旋风分离器(简称旋分器),分离后,进入分馏塔分出汽油、柴油和重质回炼油。
裂化气经压缩后去气体分离系统。
结焦的催化剂在再生器用空气烧去焦炭后循环使用,再生温度为600~730℃。
4.1反应部分原料经换热后与回炼油混合经对称分布物料喷嘴进入提升管,并喷入燃油加热,上升过程中开始在高温和催化剂的作用下反应分解,进入沉降器下段的气提段,经汽提蒸汽提升进入沉降器上段反应分解后反应油气和催化剂的混合物进入沉降器顶部的旋风分离器(一般为多组),经两级分离后,油气进入集气室,并经油气管道输送至分馏塔底部进行分馏,分离出的催化剂则从旋分底部的翼阀排出,到达沉降器底部经待生斜管进入再生器底部的烧焦罐。
4.2再生部分再生器阶段,催化剂因在反应过程中表面会附着油焦而活性降低,所以必须进行再生处理,首先主风机将压缩空气送入辅助燃烧室进行高温加热,经辅助烟道通过主风分布管进入再生器烧焦罐底部,从反应器过来的催化剂在高温大流量主风的作用下被加热上升,同时通过器壁分布的燃油喷嘴喷入燃油调节反应温度,这样催化剂表面附着的油焦在高温下燃烧分解为烟气,烟气和催化剂的混合物继续上升进入再生器继续反应,油焦未能充分反应的催化剂经循环斜管会重新进入烧焦罐再次处理。
流化催化裂化装置基础知识PPT课件

五 催化装置上的助剂
催化助剂
六 关键变量对操作的影响
操作变量
催化裂化的操作变量很多,在工业装置中,一个操作变量 的改变,会对其它多个变量产生影响,一般将众多变量分 为独立变量和非独立变量。独立变量一般可通过仪表控制, 并且可由操作人员在一定范围内调整,如:进料预热温度、 反应温度、汽提和雾化蒸汽量等。随独立变量的改变而改 变的变量,称之为非独立变量(如剂油比),如再生温度 在蜡油催化无取热设施的方案中,是装置热平衡的结果, 是非独立变量。当再生器有取热设施,可对其进行控制时, 再生温度为独立变量。
吸收解吸基本原理
催化吸收塔的吸收过程属于物理吸收,是利用气体混合物中 各组分在液体吸收剂中的溶解度不同,而将气体混合物中溶 解度大的组分被部分吸收溶解于吸收溶剂中而得到分离。有 利于吸收过程的进行。 解吸是吸收的逆过程,其主要目的是使吸收液中的部分气体 溶质释放出来,达到溶质的分离。催化解吸过程由于受工艺 流程设置限制,采用提高溶液温度的方法,来促进吸收逆过 程。(主要为C2及以下组份),实现溶质组份的分离。
流化催化裂化装置基础知识
(三) 流化原理及基本知识
流态化及流化床
固体颗粒悬浮于运动着的流体之中称为固体的流态化,使固 体小颗粒群在流体的作用下,能像流体一样流动。 工业上的固体流化是在容器内进行的,通常把容器和在其中 呈流化状态的固体颗粒合在一起称为流化床。 流化催化裂化的反应、再生的操作状况,催化剂在再生器和 沉降器间的循环输送及催化剂损失等,都与流化状态有密切 关系。 形成流化床条件 流化床的形成需具备以下三个条件:A、要有一个容器,如催 化裂化装置中反应器、再生器等,并设置有使流体分布良好 的分布器,以支撑床层并使流化良好。B、容器中要有足够数 量的固体颗粒,颗粒大小、相对密度、耐磨性能等应能满足 要求。如催化裂化装置中所使用的催化剂颗粒,C、要有流化 介质和一定的流动速度,就是使固体颗粒流化起来的介质。
催化裂化装置介绍

被冷却到40℃然后进入油气水分离器(容201),未冷凝 的气体(富气)到气压机入口,冷却的粗汽油用泵203或 泵204送往一级吸收塔(塔301/1)第25层。粗汽油一 般不作冷回流。 2、顶循环回流 自25层塔盘集油箱用泵205抽出,先经换201与原料油换 热,再经冷202西组加热来自75吨锅炉的软化水,后经东 组冷却,冷却温度由塔顶操作温度来调节,然后回到第28 层塔盘。
催化裂化催化剂
--催化剂的形貌
催化裂化催化剂
FEI Quanta 200 FEG (用于结构研究的通用高分辩率环境扫描电子显微镜) 照片
SC-22 SEM图
SC-22 SEM图(局部放大)
四、原料油情况介绍
原料油情况介绍
一催化装置原料油主要为常压四 线和减压1、2、3线的馏分油,还 有焦化蜡油、焦化汽油,掺炼部分 含酸油(酸值≯2.0mgKOH/g,含 硫≯ 2%)。
五、催化裂化产品特点
催化裂化产品特点
主要产品:汽油、柴油、液化石油气(LPG)、 瓦斯、油浆。
汽油:占商品汽油的80%,辛烷值高,一 催化RON约为90,烯烃高,硫含量较高。 随原料硫含量的变化而变化。
柴油:占商品柴油的30%,十六烷值低, 硫含量较高,芳烃含量高,需加氢处理。
催化裂化产品特点
催化裂化装置介绍
一、车间简介
一、车间简介
炼油分部联合五车间成立于2001年11月, 管辖一催化装置、二催化装置、干气提浓乙烯和 油品精制(洗涤)联合装置,是炼油主要二次加 工单位之一。其中一催化装置、二催化装置是中 石化集团公司A类达标装置,是重油轻质化的骨 干装置。车间现有职工206人,高级工程师5人, 中级职称9人,高级操作师1人,高级技师9人,技 师3人。
催化裂化装置反应再生系统认知

• (十二)反应深度的控制
• 反应深度是一个综合参数,直接影响产品分布。深度变化对轻油收率,生焦量 等起关键作用,可以说它对整个催化装置的经济效益起决定性作用。一般反应 温度:反应温度高,反应深度大。剂油比:剂油比大,反应深度大。再生催化 剂定碳低,催化剂活性高,再生剂温度高,反应深度大。
• (八)氧分压
• 烧焦速度与再生烟气中氧分压成正比,氧分压是再生压力与烟气中氧的分子浓 度的乘积。提高再生压力,或提高主风量增加烟气中氧的分子浓度,都会提高 氧分压。
• 烟气中氧分压对烧焦速度的影响相当明显,氧分压由1%上升到 2%,烧焦速度 上升18%,对于二段完全再生装置, 因二次燃烧的可能性大大降低,为获得 高烧焦速度,进入烟道的再生烟气中的氧含量一般控制在2~5%。
• (九)催化剂性质 • 催化裂化催化剂属于固体强酸催化剂,主要由分子筛、担体、粘结剂构成,主
要成份氧化铝、氧化硅及稀土、磷等改性元素组成。
• ①平衡剂活性 • ②再生剂含碳量 • ③催化剂的重金属污染
• (十)原料性质
• 原料油性质是所有操作条件中最重要的条件,选择催化剂牌号, 制定生产方 案,选择操作条件,都应首先了解原料油性质。生产中我们要求原料性质相对 稳定,同时加工几种性质不同的原料时,要在原料罐或管道中调合均匀再进提 升管反应器,并要求分析单位预先评价。原料带水会造成装置操作波动,严重 时甚至会造成事故。理想的催化裂化原料是H/C比高,CA、残炭低,密度小 (K值大),含水少。
- 1、下载文档前请自行甄别文档内容的完整性,平台不提供额外的编辑、内容补充、找答案等附加服务。
- 2、"仅部分预览"的文档,不可在线预览部分如存在完整性等问题,可反馈申请退款(可完整预览的文档不适用该条件!)。
- 3、如文档侵犯您的权益,请联系客服反馈,我们会尽快为您处理(人工客服工作时间:9:00-18:30)。
fresh raw oil
air recycle slurry oil steam
Main fan
Reaction-regeneration system
反应再生系统
After preheating, fresh raw oil is mixed with the recycle oil, and injected into the lower part of riser reactor in spray pattern through raw oil nozzle, contacts with the regenerative thermal catalyst in the riser and vaporizes immediately. Oil gas, atomizing steam and pre-lift steam carrying the catalyst rise speed along the riser and complete the cracking reaction, and then enter the settle settlement segment through speed separator.
落入沉降器下部,经待生斜管
进入再生器用空气烧焦,催化 剂恢复活性后再进入提升管参 加反应,形成循环。再生器顶 部烟气进入能量回收单元。
Fractionation system
分馏系统
The high temperature reaction oil and gas from precipitator carry a small amount of catalyst into the bottom of the fractionating tower in which it is divided into rich gas, crude gasoline, light diesel oil, heavy diesel oil, recycle oil and slurry oil, etc.
新鲜原料油经预热后与回炼油混合,由原料油喷嘴以雾化状 态喷入提升管反应器下部,在提升管中与再生热催化剂接触 并立即汽化,油气、雾化蒸汽及预提升蒸汽携带催化剂沿提 升管高线速上升并完成裂化反应,然后经快速分离器进入沉 降器的沉降段。
Reaction-regeneration system
反应再生系统
The catalytic cracking process 催化裂化工艺
The catalytic cracking process consists of three parts:raw oil catalytic cracking, catalytic regeneration and product separation. After distillation, the products of catalytic cracking can produce gas, gasoline, diesel fuel and heavy distillate oil while some recycle oil is returned to the reactor to be further processed. Changes of catalytic cracking operating conditions or fluctuations of raw materials will lead to fluctuations in product composition.
催化裂化是炼油工业中最重要的二次加工工艺,是 重油改质的重要手段之一,已成为当今石油炼制的 核心工艺之一,在炼油工业中占有极其重要的地位。
The catalytic cracking process
催化裂化过程
The catalytic cracking process is the process that, in the condition of atmospheric pressure and 450 ° C ~ 510 ° C, with the effect of the acid catalyst, using heavy distillate oil or residual oil such as vacuum distillate oil and coker gas oil as raw materials, cracks and transforms into gas, liquid products (gasoline, diesel oil, heavy diesel oil, slurry oil) and coke. 催化裂化过程是以减压馏分油、焦化 蜡油等重质馏分油或渣油为原料,在常 压和450℃~510℃条件下,在酸性催化剂 的作用下,发生裂解,转化生成气体、 液体产物(汽油、柴油、重柴油、油浆 ) 和焦炭的过程。
催化裂化工艺由三部分组成:原料油催化裂化、催化剂再生、产物分 离。催化裂化所得产物经分馏后可得到气体、汽油、柴油和重质馏分 油,部分回炼油则返回反应器继续加工。催化裂化操作条件的改变或 原料波动,会导致产品组成波动。
The Device Component Units 装置组成单元
The reaction-regeneration system 反应-再生系统 The fractionation system分馏系统 The absorption stabilization system吸收稳定系统 The energy recovery system能量回收系统
富气和粗汽油自塔顶出来,经冷却后进入油气分离器,使气体和汽油 分开,富气从分离器顶部出来,粗汽油从底部出来去吸收稳定系统。 轻、重柴油经汽提、换热或冷却后送出装置。
Fractionation system
分馏系统
The recycle oil is returned to the reaction-regeneration system to refine. The slurry oil from the bottom of tower exchanges heat and gets cooling though the slurry oil steam generator, part of which goes to fractionation tower to participate in the cycle while the rest comes back to reaction-regeneration system to refine or be reserved for the device for personal use fuel.
由沉降器来的高温反应油气携带着少量催化剂进入分馏塔 下部,在分馏塔内被分割成富气、粗汽油、轻柴油、重柴 油、回炼油和油浆等馏分。
Fractionation system
分馏系统
Rich gas and crude gasoline comes from the top of the tower, enters into the oil and gas separator after cooling to separate the gas and gasoline. And rich gas comes out from the top of separator while crude gasoline comes out from the bottom to absorb and stabilize system. After steam stripping, heat transferring and cooling, the light and heavy diesel oil is sent out the device.
Reaction-regeneration syrator
反应再生系统
Regenerated energy settler flue gas recovery unit
regenerator
riser reactor
Catalyst storage tank
Indicators to evaluate the raw materials of catalytic cracking 评价催化裂化的指标
distillate composition 馏分组成 characteristics factor 特性因数 relative density 相对密度 aniline point 苯胺点 carbon residue 残碳 sulfur content 含硫量 Nitrogen 含氮量 metal content 金属含量
Secondary Processing of Crude Oil
原油的二次加工
Section 1 Catalytic cracking Device 催化裂化装置
Induction
Catalytic cracking is the most important secondary process in the oil refining industry and one of the most important means of heavy oil modification. It has become one of the core processes of petroleum refining, occupying an extremely important position in the oil refining industry.
回炼油返回反应-再生系统进行回炼。油浆从塔底抽出,经油浆蒸汽发 生器换热降温后,一部分回分馏塔参加循环,另一部分返回反应-再生 系统回炼或留作装置自用燃料。
part of the expansion 扩充部分 dry gas ,liquefied petroleum gas desulfurization unit 干气、液化气脱硫单元 gasoline, liquefied petroleum gas sweetening unit 汽油、液化气脱硫醇单元 three-machine units 三机单元