第五章 吹塑成型
塑料成形工艺-吹塑成型

04 优缺点分析 Analysis of advantages and disadvantages
优点分析
03 02
01
1、成型设备简 单,适用材料 范围广;
2、型坯从挤出机 头流出后可直接引 入吹塑模内成型, 无须再二次加热。 生产效率高;
3、型坯温度均匀, 在吹塑过程中变形 能力一致,制品内 应力小,强度高。
零件;
请替换5.文修字整内容飞边 得到成品。
4
4
03 注意事项 Matters needing attention
注意事项
1、生产时要把 料斗处(上盖处) 一切杂物清除, 避免掉入料斗内 随料进入机筒。
2、如果机筒 内无料,不 允许螺杆长 时间空运转。
3、中空吹塑正常生产 中出现注射料量不均 匀或成型制品外形尺 寸不稳定时,可能是 由于机筒内有异物堵 塞或机筒加料段温度 过高所致,应及时拆 卸螺杆,清理机筒内
06 典型案例 classic case
典型案例 1、汽油桶
典型案例 2、浇花壶
典型案例 3.桶装水桶
典型案例 4、塑料隔离墩
典型案例 5、瓶装矿泉水
典型案例 6、灯罩
典型案例 7、儿童玩具
吹塑成型
Blow molding
演示完毕 谢谢欣赏
并且开模取出塑件。
经过注射吹塑成形的塑件壁厚均匀,无飞边,不需后加工, 由干注射型坯有底,因此底部没有拼和缝,强度高,生产效率 高。
但是设备与模具的价格昂贵,多用于小型塑件的大批量生 产。
典型模具 2、注射吹塑成形
1-注塑机喷嘴
2-注塑型坯 5-吹塑模
3-空心凸模 6-塑件
4-加热器
典型模具
3、注射拉伸吹塑成形
高分子成型工艺学第五章中空吹塑-

合 物
5.5 拉伸吹塑
新
型
成 型 装
2、拉伸吹塑方法
备 国
3)冷坯法挤出-拉伸-吹塑
家
工
程
研
究
中
心
聚
合 物
5.5 拉伸吹塑
新
型
成 型 装
2、拉伸吹塑方法
备 国
3)冷坯法挤出-拉伸-吹塑
家
工
程
研
究
中
心
聚
合 物
5.5 拉伸吹塑
新
型
成 型 装
2、拉伸吹塑方法
备 国
4)冷坯法注塑-拉伸-吹塑
家
工
程
研
究
中
5.5 拉伸吹塑
新
型
成 型 装
2、拉伸吹塑方法
备 国
2)热坯法注塑-拉伸-吹塑
家
工
程
研
究
中
心
聚
合 物
5.5 拉伸吹塑
新
型
成 型 装
2、拉伸吹塑方法
备 国
3)冷坯法挤出-拉伸-吹塑
家
工
程
研
究
中
心
聚
合 物
5.5 拉伸吹塑
新
型
成 型 装
2、拉伸吹塑方法
备 国
3)冷坯法挤出-拉伸-吹塑
家
工
程
研
究
中
心
聚
新
型
成 型 装
4、连接吹塑成型
备
国
家
工
程
研
究
中
心
聚
合 物
5.6 新型的中空吹塑成型
新
型
第五章挤出吹塑薄膜
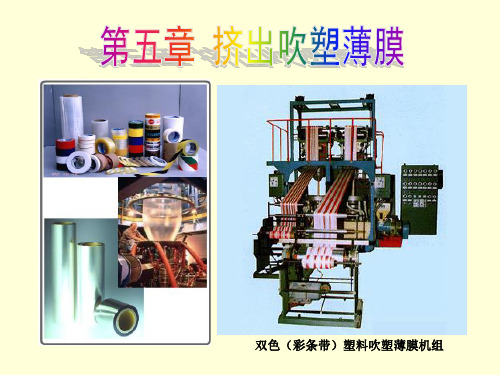
汇合处
缺点:会 产生“偏 中”现象, 薄膜厚度 不易控制 。
也可用于PE、
PP等大多数塑
料。应用最广。 工作过程:物料由机颈到达芯棒后分割为两股,绕芯
棒轴斜面流动至芯棒尖处重新融合,之后经分流锥扩
展成管坯从口模均匀挤出,再由压缩空气吹胀成薄。
2.螺旋式机头
工作过程:中心进料后经过芯棒上3~8个斜槽进入 各自的螺旋槽,螺槽由深变浅,最终消失;物料 流动过程中逐渐熔合,可有效消除熔接痕。
• 可以用吹塑法生产薄膜的塑料有:PVC、PE、 PP、PA、PS等。还发展了乙烯一醋酸乙烯 (EVA)薄膜。我国以PVC和聚烯烃薄膜居多。
挤出吹塑薄膜:
把物料加入到挤出机的机筒后,经螺杆 的转动、挤压和搅拌,物料在一定温度作用 下熔融塑化,并在螺杆推动下,经过滤网、 分流板后通过机头环形口模间隙挤出成薄壁 管,然后在流动状态下趁热用压缩空气将其 吹胀,再经风环冷却定型,进入人字板后夹 平,由导辊压紧牵引入卷取辊,最后制得薄 膜制品。
一、挤出吹塑薄膜工艺流程
熔挤
薄
加 融 出 吹定夹牵卷 膜
料 塑 膜 胀型平引取 制
化管
品
1.平挤上吹法 2.平挤下吹法 3.平挤平吹法
1.平挤上吹法:
特点:整个膜管挂在上部已冷却的坚韧段上,
牵引稳定,可得到厚度范围和幅宽范围较大
(D=10m)的薄膜;设备占地面积小,但厂房
要高;热空气向上, 影响冷却效果。
• 现在被广泛采用的复合薄膜有LDPE/PA/LDPE、 LDPE/PVDC、PA/离子型聚合物、 HDPE/LDPE/HDPE、LLDPE/HDPE/LLDPE等。
• 共挤吹膜法的技术难点在于复合机头的流道设 计,流道设计应保证各层熔料的流速均匀、结 合层剪切应力一致,各层机头的料温应能独立 控制。
吹塑成型工艺及吹塑制品设计
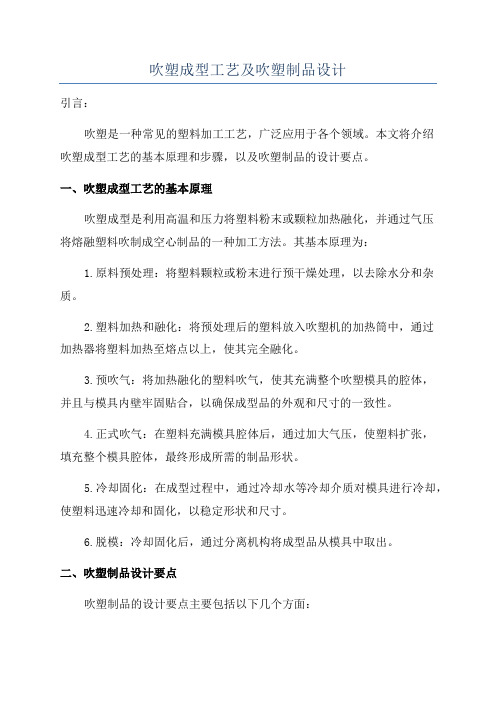
吹塑成型工艺及吹塑制品设计引言:吹塑是一种常见的塑料加工工艺,广泛应用于各个领域。
本文将介绍吹塑成型工艺的基本原理和步骤,以及吹塑制品的设计要点。
一、吹塑成型工艺的基本原理吹塑成型是利用高温和压力将塑料粉末或颗粒加热融化,并通过气压将熔融塑料吹制成空心制品的一种加工方法。
其基本原理为:1.原料预处理:将塑料颗粒或粉末进行预干燥处理,以去除水分和杂质。
2.塑料加热和融化:将预处理后的塑料放入吹塑机的加热筒中,通过加热器将塑料加热至熔点以上,使其完全融化。
3.预吹气:将加热融化的塑料吹气,使其充满整个吹塑模具的腔体,并且与模具内壁牢固贴合,以确保成型品的外观和尺寸的一致性。
4.正式吹气:在塑料充满模具腔体后,通过加大气压,使塑料扩张,填充整个模具腔体,最终形成所需的制品形状。
5.冷却固化:在成型过程中,通过冷却水等冷却介质对模具进行冷却,使塑料迅速冷却和固化,以稳定形状和尺寸。
6.脱模:冷却固化后,通过分离机构将成型品从模具中取出。
二、吹塑制品设计要点吹塑制品的设计要点主要包括以下几个方面:1.材料选择:吹塑制品的设计要根据实际使用需求选择合适的塑料材料。
常见的吹塑材料有聚乙烯(PE)、聚丙烯(PP)、聚氯乙烯(PVC)等,每种材料在耐热性、机械性能等方面有所不同,需要根据具体需求进行选择。
2.成型品形状设计:吹塑制品的形状设计应考虑到塑料在膨胀过程中的变形情况,避免设计过于复杂的凸凹面以及壁厚不均匀的部分,以确保成型品的一致性和稳定性。
3.模具设计:模具的设计应根据成型品的形状和尺寸进行,考虑到成型件的缩水率和模具的缩水率,以保持成型品的尺寸准确度。
4.壁厚设计:吹塑制品的壁厚直接影响成型品的质量和性能,壁厚过薄容易变形,壁厚过厚则会增加成本和加工难度。
因此,需要根据制品的实际使用需求进行合理的壁厚设计。
5.强度设计:吹塑制品在使用过程中需要承受一定的载荷和压力,因此需要考虑制品的强度设计,确保其能够满足使用要求。
中空吹塑成型技术

g=
d+
d
(1 -
-
e
t t*
)
+
dt
(1)
E1 E2
h
在聚合物的玻璃化温度以上,普弹形变 在总形变中所占比例很小,可忽略。于是
g=
d+
d
(1 -
-
e
t t*
)
(2)
E1 E2
其中,t* 为松驰时间,随温度升高而减小。 η为粘度,随温度升高而降低。
(2)式也可写成
g=
g 2¥ (1 -
-
e
t t*
4.多层吹塑
以多层管坯复合,并 在同一条件下进行吹胀, 冷却。
5.2中空成型工艺过程
• 第一是制造型坯; • 第二是型坯定位; • 第三是吹塑; • 第四是冷却。
一.型坯的的制造
• 型坯的注射成型 • 型坯的挤出成型
1.型坯的注射成型
• ①一步法:注射型坯一经成型,还在塑性 状态模具开启;进入成型的第二阶段,即 把芯轴连同型坯迅速送到吹塑模具中,打 开压缩空气阀门,经芯轴吹入压缩空气, 使还处于熔融状态的型坯吹胀至模腔的形 状,在模具内冷却后打开模具,取出制品。
第五章 中空吹塑成型
• 中空成型的原理及分类 • 中空成型过程 • 中空吹塑过程的影响因素
5.1中空成型的原理及分类
• 中空成型的粘弹性原理 • 根据中空成型原理的两点推论 • 中空吹塑成型的分类及工艺特点
一.中空成型的粘弹性原理
• 数学描述 ห้องสมุดไป่ตู้ 文字叙述
一.数学描述
聚合物由于其长链结构及分子链的柔 顺性。一般情况下,将聚合物置于一定温 度下,从受外力作用开始,大分子的形复 经历一系列中间状态过渡到与外力相适应 的平衡状态是一个松驰过程,其形变随时 间的变化为:
中空吹塑成型方式概述课件

关键:控制各层树脂间的熔接。 混入黏结性树脂
可采用 添设黏结材料层
分为共挤出吹塑和多层注坯吹塑两种。
27
28
1 多层共挤出吹塑
多层共挤出吹塑是选用两台以上的挤出机,将同种或异 种塑料在不同的挤出机内熔融塑化后,在机头内复合、 挤出、形成多层同心的复合型坯,经吹塑制造中空容器 的技术。
1.多层结构的材质选择
14
2 注射吹塑要点
1.管坯温度与吹塑温度
注射成型时:温度高,粘度低,易变形,转移过程中 壁厚不均匀。 温度低,内应力高,变形,开裂。
依靠模具油温调节器或水冷机调节。 2.注射吹塑树脂 应具有高的相对分子量 熔融粘度,受剪切速率和加工温度影响小。
15
16
拉伸吹塑
拉伸吹塑:经双轴定向拉伸的一种吹塑成型工艺。
l
16、提出一个问题往往比解决一个更重要。因为 解决问 题也许 仅是一 个数学 上或实 验上的 技能而 已,而 提出新 的问题 ,却需 要有创 造性的 想像力 ,而且 标志着 科学的 真正进 步。 2023/10/17 13:48:3123:48:3217 October 2023
17、儿童是中心,教育的措施 便围绕 他们而 组织起 来。 1:48:32下午1:48下午13:48:3210月-23
按照制品容量范围及性能要求,可生产3—6层的层结
构。层结构及树质选择原则如下:阻隔层塑料可选用
聚酰胺(PA)、聚丙烯晴(PAN)或乙烯/乙烯醇共聚物
(EVOH);内壳层塑料可选用聚乙烯(PE)、聚丙烯
(PP)或聚碳酸酯(PC);再生层可选用型坯的飞边
和余料。其中内壳层、再生层或外表层的厚度应大于
粘结层和阻隔层。
此法生产能力每小时可达到3000只,容量为一公升的瓶子。
吹塑成型原理
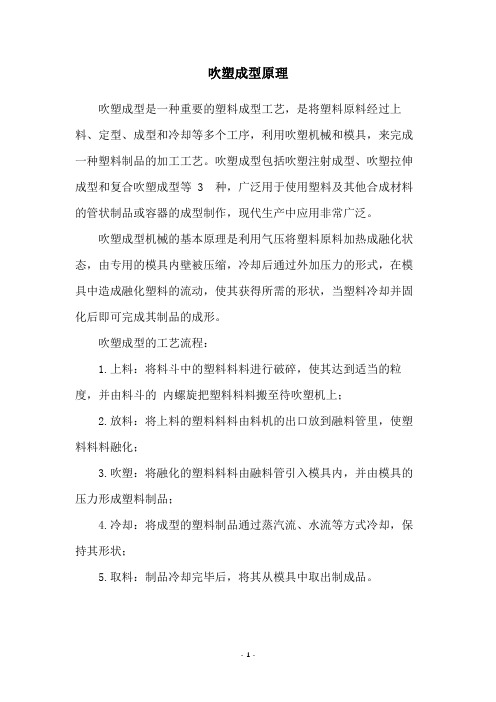
吹塑成型原理
吹塑成型是一种重要的塑料成型工艺,是将塑料原料经过上料、定型、成型和冷却等多个工序,利用吹塑机械和模具,来完成一种塑料制品的加工工艺。
吹塑成型包括吹塑注射成型、吹塑拉伸成型和复合吹塑成型等 3 种,广泛用于使用塑料及其他合成材料的管状制品或容器的成型制作,现代生产中应用非常广泛。
吹塑成型机械的基本原理是利用气压将塑料原料加热成融化状态,由专用的模具内壁被压缩,冷却后通过外加压力的形式,在模具中造成融化塑料的流动,使其获得所需的形状,当塑料冷却并固化后即可完成其制品的成形。
吹塑成型的工艺流程:
1.上料:将料斗中的塑料料料进行破碎,使其达到适当的粒度,并由料斗的内螺旋把塑料料料搬至待吹塑机上;
2.放料:将上料的塑料料料由料机的出口放到融料管里,使塑料料料融化;
3.吹塑:将融化的塑料料料由融料管引入模具内,并由模具的压力形成塑料制品;
4.冷却:将成型的塑料制品通过蒸汽流、水流等方式冷却,保持其形状;
5.取料:制品冷却完毕后,将其从模具中取出制成品。
- 1 -。
吹塑成型

现代吹塑技术源于上世纪三十年代,经过多年的发展,已发展成为继注塑和挤出之外的第三大塑料加工方法,吹塑技术与注塑相比较,设备造价低,可成型复杂的中空制品,广泛应用于包装,软料业及玩具、汽业制造等行业。
本文主要从以下四个方面为大家讲解吹塑技术的要点及特性。
一、吹塑技术概论1. 注射拉伸吹塑2. 挤出吹塑3. 注射吹塑二、吹塑件设计及吹塑材料1. 吹塑件设计要点2. 吹塑材料三、吹塑模具设计四、吹塑缺陷及排除方法一、吹塑技术概论1.注塑拉伸吹塑目前,注塑拉伸吹塑技术应用比注吹更为广泛,这种吹塑方法实际也是注射吹塑,只不过增加了轴向拉伸,便吹塑更加容易及能耗降低。
注拉吹可以加工制品的体积比注吹要大一些,吹制的容器体积在0.2~20L,其工作过程如下:①先注塑型坯,原理同普通注塑;②再将型坯转至加热调温工序,使型坯变软;③转至拉—吹工位,合模。
型芯内推杆沿轴向拉伸型坯,同时吹气使型坯贴紧模壁并冷却;④转至脱模工位取件。
注—拉—吹过程:注塑型坯→加热型坯→合模拉伸并吹起→冷却并取件注拉吹机械结构示意图2.挤出吹塑挤出吹塑是吹塑成型中应用最多的一种吹塑料方法,其可以加工的范围很广,从小型制品到大型容器及汽车配件,航天化工制品等,加工过程如下:①先将胶料熔融,混炼,熔体进入机头成为管况型坯;②型坯达到预定长度后,吹塑模具闭合,将型坯夹在两半模具之间;③吹气,将空气吹入型坯内,将型坯吹胀,便之贴紧模具型腔成型;④冷却制品;⑤开模,取走已冷硬的制品。
挤出吹塑加工过程:熔料→挤出型坯→合模吹塑→开模取件挤出吹塑原理示意图(1—挤出机头; 2—吹塑模; 3—型坯; 4—压缩空气吹管; 5—塑件)3.注射吹塑注塑吹塑是综合了注射成型与吹塑特性的成型方法,目前主要应用于吹制精度要求较高的饮料瓶及药瓶及一些小型的结构零件等。
①在注塑工位,先注塑出型胚,加工方法同普通注塑。
②注塑模开模后,芯棒连同型坯移动到吹塑工位。
③芯棒把型坯置于吹塑模之间,合模。
吹塑成型技术
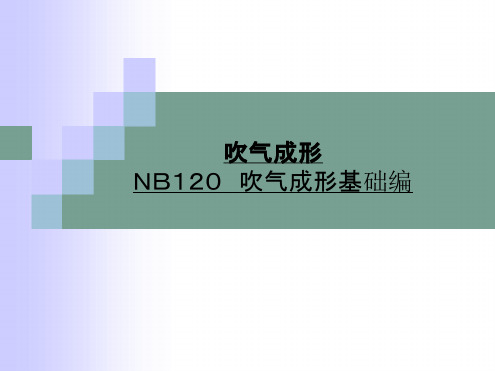
吹针
吹气气缸内部构造 排气管
冷空气
排气管 要点:前端及刀刃部分非常 锋利!
3、夹合
从模具来看的 话,是将型坯切断的部分。另外,如果是从制品来看的 话, 是把成形品和 边角料切断的部分叫 夹合
夹合部
上边角料
切割部分 (夹合)
夹合部 起点
边角料切割范围
(切割范围)
切割斜线部
MAX
边
(
角 料 側 )
8mm
NO.1R/B
№1 №2
《教材化完成 样板》
? 学习成形技术的前提(理解成形的基本动作) ? 模式图27 入子旋转延迟 (螺丝形状的入子下切割开始) D-21
NO.1R/B
《教材化完成 样板》
? 学习成形技术的前提(理解成形的基本动作) ? 模式图28 模具打开暂时停止 (螺丝形状的入子下切割) D-22
? 学习成形技术的前提(理解成形的基本动作) ? 模式图16 №1吹针打入 D-12
《教材化完成 样板》
№1 №2
? 学习成形技术的前提(理解成形的基本动作) ? 模式图17 №1吹气开始 (吹气延迟) D-13
《教材化完成 样板》
№1 №2
? 学习成形技术的前提(理解成形的基本动作) ? 模式图吹18气模具 吹き込み金型転写 D-14
《教材化完成 样板》
? 学习成形技术的前提(理解成形的基本动作) ? 模式图8 上面预吹气(延迟时间?時間定时) D-6
《教材化完成 样板》
? 学习成形技术的前提(理解成形的基本动作) ? 模式图9 模具闭合开发始 D-7
《教材化完成 样板》
? 学习成形技术的前提(理解成形的基本动作) ? 模式图10 上面急速排气 (时间延迟?时间定时) D-8
吹塑成型原理
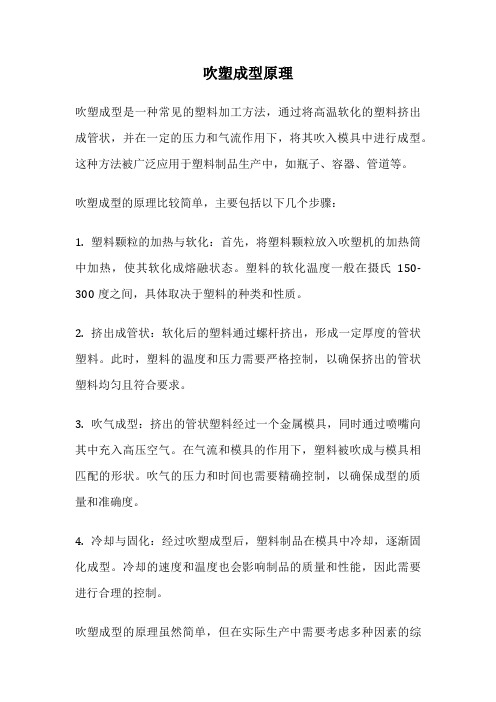
吹塑成型原理吹塑成型是一种常见的塑料加工方法,通过将高温软化的塑料挤出成管状,并在一定的压力和气流作用下,将其吹入模具中进行成型。
这种方法被广泛应用于塑料制品生产中,如瓶子、容器、管道等。
吹塑成型的原理比较简单,主要包括以下几个步骤:1. 塑料颗粒的加热与软化:首先,将塑料颗粒放入吹塑机的加热筒中加热,使其软化成熔融状态。
塑料的软化温度一般在摄氏150-300度之间,具体取决于塑料的种类和性质。
2. 挤出成管状:软化后的塑料通过螺杆挤出,形成一定厚度的管状塑料。
此时,塑料的温度和压力需要严格控制,以确保挤出的管状塑料均匀且符合要求。
3. 吹气成型:挤出的管状塑料经过一个金属模具,同时通过喷嘴向其中充入高压空气。
在气流和模具的作用下,塑料被吹成与模具相匹配的形状。
吹气的压力和时间也需要精确控制,以确保成型的质量和准确度。
4. 冷却与固化:经过吹塑成型后,塑料制品在模具中冷却,逐渐固化成型。
冷却的速度和温度也会影响制品的质量和性能,因此需要进行合理的控制。
吹塑成型的原理虽然简单,但在实际生产中需要考虑多种因素的综合作用。
例如,塑料的选择、加热温度、挤出压力、吹气压力、模具设计等都会直接影响制品的质量和产能。
因此,生产厂家需要根据具体产品的要求和生产规模,合理调整各项参数,以达到最佳的生产效果。
吹塑成型作为一种高效、经济的塑料加工方法,已经成为塑料制品生产中不可或缺的一环。
通过不断的技术改进和创新,吹塑成型在生产效率、产品质量和环保方面都有了显著提升,为塑料制品行业的发展做出了重要贡献。
希望未来能够进一步完善吹塑成型技术,推动行业的持续发展和进步。
塑料瓶的注塑吹塑成型介绍(五篇)
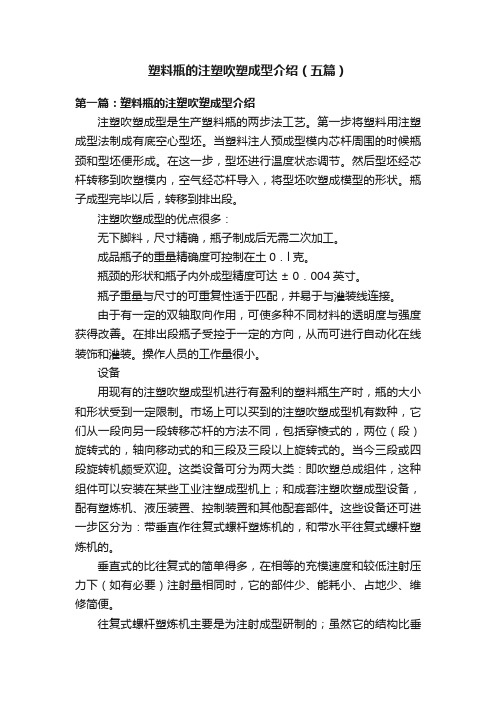
塑料瓶的注塑吹塑成型介绍(五篇)第一篇:塑料瓶的注塑吹塑成型介绍注塑吹塑成型是生产塑料瓶的两步法工艺。
第一步将塑料用注塑成型法制成有底空心型坯。
当塑料注人预成型模内芯杆周围的时候瓶颈和型坯便形成。
在这一步,型坯进行温度状态调节。
然后型坯经芯杆转移到吹塑模内,空气经芯杆导入,将型坯吹塑成模型的形状。
瓶子成型完毕以后,转移到排出段。
注塑吹塑成型的优点很多:无下脚料,尺寸精确,瓶子制成后无需二次加工。
成品瓶子的重量精确度可控制在土0.l克。
瓶颈的形状和瓶子内外成型精度可达± 0.004英寸。
瓶子重量与尺寸的可重复性适于匹配,并易于与灌装线连接。
由于有一定的双轴取向作用,可使多种不同材料的透明度与强度获得改善。
在排出段瓶子受控于一定的方向,从而可进行自动化在线装饰和灌装。
操作人员的工作量很小。
设备用现有的注塑吹塑成型机进行有盈利的塑料瓶生产时,瓶的大小和形状受到一定限制。
市场上可以买到的注塑吹塑成型机有数种,它们从一段向另一段转移芯杆的方法不同,包括穿棱式的,两位(段)旋转式的,轴向移动式的和三段及三段以上旋转式的。
当今三段或四段旋转机颇受欢迎。
这类设备可分为两大类:即吹塑总成组件,这种组件可以安装在某些工业注塑成型机上;和成套注塑吹塑成型设备,配有塑炼机、液压装置、控制装置和其他配套部件。
这些设备还可进一步区分为:带垂直作往复式螺杆塑炼机的,和带水平往复式螺杆塑炼机的。
垂直式的比往复式的简单得多,在相等的充模速度和较低注射压力下(如有必要)注射量相同时,它的部件少、能耗小、占地少、维修简便。
往复式螺杆塑炼机主要是为注射成型研制的;虽然它的结构比垂直式的复杂,但操作的可靠性较好。
当前的成型机械,包括大型的标准生产装置,可在较高的生产速度下生产出较大的瓶子来;注射装置的完善使聚氯乙烯和含丙烯睛的树脂更易于加工;增加工段(位)的开发工作正在继续进行。
通常,医药工业和化妆品工业是16央司和更小的注塑吹塑成型塑料瓶的市场。
《塑料成型工艺与模具设计》(上册)电子教案完全版

《塑料成型工艺与模具设计》(上册)电子教案完全版第一章:塑料成型工艺概述1.1 塑料成型的基本概念塑料的定义与特性塑料成型的定义与分类1.2 塑料成型工艺流程塑料原料的准备塑料的加热与塑化塑料的冷却与固化塑料的脱模与后处理1.3 塑料成型工艺参数温度压力速度时间第二章:塑料模具概述2.1 模具的分类与结构模具的分类模具的基本结构2.2 模具的设计原则模具设计的要求与步骤模具设计中的关键参数2.3 模具的材料与制造模具材料的选用原则模具的制造工艺第三章:塑料注射成型工艺与模具设计3.1 注射成型工艺概述注射成型原理与特点注射成型工艺参数3.2 注射模具的结构设计模具的型腔与型芯设计模具的冷却系统设计模具的加热系统设计3.3 注射模具的导向与定位模具的导向设计模具的定位设计第四章:塑料挤出成型工艺与模具设计4.1 挤出成型工艺概述挤出成型的原理与特点挤出成型工艺参数4.2 挤出模具的结构设计模具的口模设计模具的定径套设计模具的切割装置设计模具的导向设计模具的调整方法第五章:塑料吹塑成型工艺与模具设计5.1 吹塑成型工艺概述吹塑成型的原理与特点吹塑成型工艺参数5.2 吹塑模具的结构设计模具的型腔设计模具的吹气系统设计模具的后处理设计5.3 吹塑模具的导向与定位模具的导向设计模具的定位设计第六章:塑料压缩成型工艺与模具设计6.1 压缩成型工艺概述压缩成型的原理与特点压缩成型工艺参数6.2 压缩模具的结构设计模具的型腔设计模具的压柱设计模具的冷却系统设计模具的导向设计模具的定位设计第七章:塑料压注成型工艺与模具设计7.1 压注成型工艺概述压注成型的原理与特点压注成型工艺参数7.2 压注模具的结构设计模具的型腔设计模具的压注系统设计模具的冷却系统设计7.3 压注模具的导向与定位模具的导向设计模具的定位设计第八章:塑料传递成型工艺与模具设计8.1 传递成型工艺概述传递成型的原理与特点传递成型工艺参数8.2 传递模具的结构设计模具的型腔设计模具的传递系统设计模具的冷却系统设计模具的导向设计模具的定位设计第九章:塑料成型工艺与模具设计的计算与模拟9.1 模具设计计算塑料收缩率的计算模具尺寸的计算模具强度的计算9.2 模具设计模拟模具流动分析模具冷却分析模具翘曲分析9.3 模具设计软件介绍模具设计软件的功能与特点模具设计软件的应用实例第十章:塑料成型工艺与模具设计的实践与应用10.1 塑料成型工艺实践成型工艺的操作步骤与注意事项成型过程中的常见问题与解决方法10.2 模具设计应用实例典型模具设计案例分析模具设计在实际生产中的应用10.3 塑料成型工艺与模具设计的未来发展塑料成型技术的发展趋势模具设计技术的创新与突破重点和难点解析重点环节1:塑料成型的基本概念与特性补充和说明:塑料成型的基本概念和特性是理解后续成型工艺与模具设计的基础。
吹塑成型
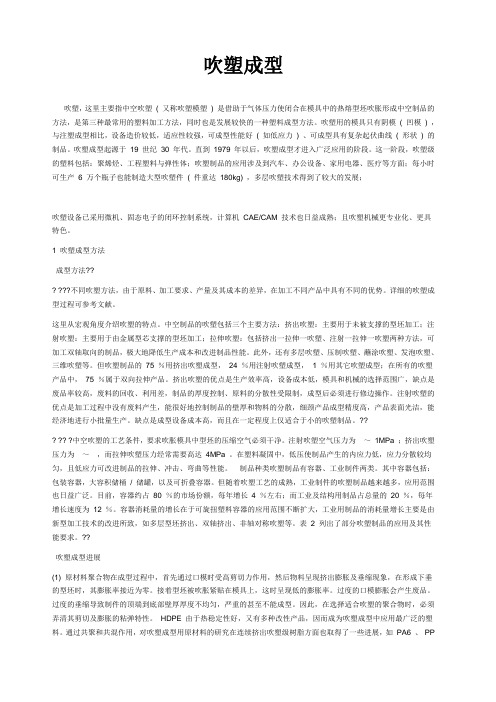
吹塑成型吹塑,这里主要指中空吹塑( 又称吹塑模塑) 是借助于气体压力使闭合在模具中的热熔型坯吹胀形成中空制品的方法,是第三种最常用的塑料加工方法,同时也是发展较快的一种塑料成型方法。
吹塑用的模具只有阴模( 凹模) ,与注塑成型相比,设备造价较低,适应性较强,可成型性能好( 如低应力) 、可成型具有复杂起伏曲线( 形状) 的制品。
吹塑成型起源于19 世纪30 年代。
直到1979 年以后,吹塑成型才进入广泛应用的阶段。
这一阶段,吹塑级的塑料包括:聚烯烃、工程塑料与弹性体;吹塑制品的应用涉及到汽车、办公设备、家用电器、医疗等方面;每小时可生产 6 万个瓶子也能制造大型吹塑件( 件重达180kg) ,多层吹塑技术得到了较大的发展;吹塑设备已采用微机、固态电子的闭环控制系统,计算机CAE/CAM 技术也日益成熟;且吹塑机械更专业化、更具特色。
1 吹塑成型方法成型方法??? ???不同吹塑方法,由于原料、加工要求、产量及其成本的差异,在加工不同产品中具有不同的优势。
详细的吹塑成型过程可参考文献。
这里从宏观角度介绍吹塑的特点。
中空制品的吹塑包括三个主要方法:挤出吹塑:主要用于未被支撑的型坯加工;注射吹塑:主要用于由金属型芯支撑的型坯加工;拉伸吹塑:包括挤出一拉伸一吹塑、注射一拉伸一吹塑两种方法,可加工双轴取向的制品,极大地降低生产成本和改进制品性能。
此外,还有多层吹塑、压制吹塑、蘸涂吹塑、发泡吹塑、三维吹塑等。
但吹塑制品的75 %用挤出吹塑成型,24 %用注射吹塑成型, 1 %用其它吹塑成型;在所有的吹塑产品中,75 %属于双向拉伸产品。
挤出吹塑的优点是生产效率高,设备成本低,模具和机械的选择范围广,缺点是废品率较高,废料的回收、利用差,制品的厚度控制、原料的分散性受限制,成型后必须进行修边操作。
注射吹塑的优点是加工过程中没有废料产生,能很好地控制制品的壁厚和物料的分散,细颈产品成型精度高,产品表面光洁,能经济地进行小批量生产。
吹塑成型技术

第1章吹塑成型基础1.1定义塑料吹塑成型是一种生产中空塑料制品的加工过程,它仅适用于热塑性塑料,例如聚乙烯、聚氯乙烯、聚对苯二甲酸乙二醇酯,及工程塑料如聚碳酸酯等。
吹塑成型加工的三种主要方法是:挤出吹塑成型、注塑吹塑成型和拉伸吹塑成型。
1.2基本加工过程吹塑成型加工过程可分为三个阶段:1)熔融塑化利用挤出机或注塑机使原料熔融;2)型坯成型利用挤出机机头和口模或注塑模具成型型坯;3)吹塑成型利用辅助的空气压缩机提供压缩空气并用液压夹紧装置夹紧模具成型制品。
上述成型加工过程中,首先是需要生产管坯,通常称为型坯,此术语来源于玻璃工业。
可以用挤出机或注塑机生产型坯,常将注塑机生产的型坯称为预成型。
吹塑过程是将热的型坯或坯料送入吹塑模具内,模具闭合的同时夹紧型坯,然后将热的管坯吹到冷的模具壁上,冷却定型后顶出制品。
多数情况下,中空制品需要后加工,例如去除飞边、印刷、贴标签、灌入产品等。
一些制品上的钻孔、研磨操作等可用自动操作设备完成,基本的吹塑加工过程见图1.1。
1.3吹塑历史玻璃、塑料、铝是现今吹塑制品的三种原材料。
现代的塑料吹塑成型技术是从玻璃吹塑制品中发展起来的,如图1.2所示。
这种方法是公元前1世纪由叙利来玻璃工人首先发明的。
他们把吹管末端的玻璃泡吹成许多带有手柄、底座并随意附加一些装饰物的制品。
在中世纪,由英国和欧洲的一些地方将这种加工技术进行了改进和完善并使之成为一种重要的商品工业。
1.4发展史简介现代塑料吹塑成型加工(图1.1)起源于20世纪30年代。
当时的Plax公司和Illinois的Owens公司发明了第一个专利。
它是以玻璃吹塑技术为基础的自动化设备,如图1.3所示。
但由于当时塑料材料价格高、性能差而阻碍了塑料吹塑成型的发展,使塑料瓶优点不及玻璃瓶。
然而在40年代中期,由于低密度聚乙烯的采用(英国ICI研制),提供了玻璃所不能比拟的耐挤压的优点。
1950年,Elmer Mill发明了一个连续挤出旋转吹塑机的专利并由Continental Can公司使用。
吹塑成型原理

吹塑成型原理
吹塑成型是一种常用的塑料加工方法,主要用于制作中空容器和管道等产品。
其原理是通过将高温熔化的塑料挤出到模具中,然后利用气压或真空将塑料挤压成模具的形状。
具体来说,吹塑成型通常分为两个步骤:挤出和吹气。
在挤出过程中,将加热至熔融状态的塑料注入到挤出机的螺杆中。
螺杆加热和旋转,将塑料推送到模具中的挤出头部。
挤出头部附近有一个空气进气孔,通过调节气压来控制空气进入的速度和压力。
在挤出头部出口处,有一个圆形成型腔。
当塑料从挤出头部挤出时,空气通过进气孔进入模具,将热塑性塑料按照模具的形状吹膨胀。
形成薄壁中空形状的塑料制品。
在吹塑成型过程中,气压、温度和模具的形状等参数都会影响最终产品的质量。
通过控制这些参数,可以生产出各种不同形状和尺寸的塑料制品。
总的来说,吹塑成型是一种通过挤出塑料并利用气压将其形成成型的方法。
它在制造塑料容器和管道等产品时具有广泛的应用。
吹塑成型工艺流程

吹塑成型工艺流程吹塑成型,这可是个挺有趣的制造工艺呢。
就像吹气球似的,不过这气球吹出来可就不是简单玩玩,而是变成各种各样有用的东西。
咱先说说原料吧。
这原料就好比是做饭的食材,得精心挑选。
一般都是用塑料颗粒,这些小颗粒就像一个个等待变身的小精灵。
它们得是那种适合吹塑的材料,比如说聚乙烯或者聚丙烯。
把这些塑料颗粒放进料斗里,就像把米放进米缸准备做饭一样。
然后呢,有个很关键的步骤,就是加热。
这加热就像是给那些塑料颗粒做桑拿浴。
通过螺杆的转动,把塑料颗粒慢慢往前送,这螺杆就像一个勤劳的小搬运工。
在往前送的过程中,周围的加热装置就开始发挥作用了,温度一点点升高,塑料颗粒开始变软,就像冰化成水一样,从一颗颗硬邦邦的小颗粒变成了软软的、黏黏的一团。
这时候的塑料就像一团软软的泥巴,可塑性很强。
接着就是挤出了。
这就好比是把那团软泥巴从一个特殊的模具里挤出来。
这个模具的形状可就决定了以后吹塑出来产品的基本形状。
比如说,如果模具是个圆形的,那挤出来的就是个圆形的塑料管模样的东西。
这个塑料管呢,就像一条长长的、软软的蛇,不过是空心的哦。
再接下来就是吹塑这个神奇的环节啦。
往这个刚刚挤出来的塑料管里吹气,这就真的像吹气球一样了。
空气就像一个神奇的魔法力量,把这个软软的塑料管给吹得鼓起来。
不过这吹气可不能乱来,得控制好气压,就像吹气球的时候不能太用力,不然就爆了。
这时候,塑料管在气压的作用下,就按照模具的形状一点点膨胀起来,从一根简单的管子变成了想要的形状,可能是个瓶子,可能是个桶之类的东西。
在吹塑的过程中,模具就像一个严格的塑形老师。
它把吹起来的塑料紧紧地包裹住,让塑料按照它的样子成型。
而且这个模具的温度也很有讲究呢,不能太热也不能太冷。
太热了,塑料可能会粘在模具上,就像糖粘在手上一样,不好取下来;太冷了呢,塑料可能就不能很好地贴合模具,形状就不那么完美了。
等吹塑完成了,还有个冷却的过程。
这就像刚出锅的馒头得晾凉一样。
让成型的塑料制品慢慢冷却下来,这样它才能保持住形状。
吹塑的成型工艺

吹塑的成型工艺哎呀,说起吹塑成型工艺,这玩意儿可真是个技术活儿,不是随便哪个人都能玩得转的。
记得上次去工厂参观,亲眼见识了这门手艺,那叫一个震撼啊!那天,我穿着一身工作服,戴着安全帽,跟着师傅走进了车间。
一进去,那机器轰鸣声震得我耳朵嗡嗡响,空气中还弥漫着一股塑料的味道。
师傅指着一台巨大的机器说:“看,这就是吹塑机,我们今天的主角。
”我凑近一看,那机器真不小,像个钢铁巨兽似的。
师傅开始给我讲解,说吹塑成型啊,就是先把塑料加热融化,然后通过一个模具,吹成各种形状的塑料制品。
听起来简单,但实际操作起来,那可是门大学问。
师傅带我走到一台正在工作的机器前,只见那机器的一端,有个大铁管子,里面装满了融化的塑料。
师傅说,这塑料得加热到一定的温度,太热了不行,太冷了也不行,得恰到好处。
我心想,这跟炒菜差不多,火候得掌握好。
接着,师傅让我看那模具,模具里面是空心的,形状各异,有的像瓶子,有的像桶。
他说,这模具可是关键,形状得精确,不然吹出来的塑料制品就不合格。
我看着那模具,心想,这得有多精细的手艺才能做得出来啊。
然后,师傅打开了机器,那大铁管子里的塑料就开始流动,通过模具,慢慢吹成了一个塑料桶。
我看着那塑料一点点成型,心里那个激动啊,就像看魔术一样。
师傅说,这速度得控制好,太快了塑料会变形,太慢了又影响效率。
我看着那塑料桶一点点成型,心里那个佩服啊。
这吹塑成型工艺,真是个技术活儿,得有经验,有耐心,还得有手艺。
我看着师傅熟练地操作着机器,心想,这手艺得练多少年才能这么熟练啊。
参观完车间,我走出工厂,心里感慨万千。
这吹塑成型工艺,看似简单,实则复杂,每一个细节都至关重要。
就像人生一样,看似平淡无奇,实则充满了学问和挑战。
这一趟工厂之旅,让我对吹塑成型工艺有了新的认识,也让我对生活有了新的感悟。
所以啊,下次你看到那些塑料制品,不妨想想,这背后可是有着一群手艺人的辛勤付出和智慧结晶呢。
吹塑成型工艺,不仅仅是制造塑料制品那么简单,它更是人类智慧和创造力的体现。
第五章 吹塑成型

c. 分子量分布 分子量分布宽,有利于得到高质量的管坯,但过宽,可能导致制品强度下降。 d.拉伸粘度 拉伸粘度随拉伸应力增加而增大的物料有利于吹塑加工。 另外,原料在加工过程中应具有阻止氧气、二氧化碳、氮气及水蒸气等向容器内外透散的 特性。
第12页
第五章
不连续旋转往复式挤出机的工作原理与连续旋转往复式螺杆挤出机基本相似,主要差别在于其螺杆 在往复过程中停止旋转,机筒内固体物料不能连续地变为熔体,因而,熔体的挤出是不连续的。吹塑成 型工艺中常见的挤出机为单螺杆挤出机,其组成和结构和普通单螺杆挤出机并无特殊之处,由机筒、螺 杆、加热元件、温控元件与传动装置等部分组成。普通挤出机在满足如下要求后也可用于吹塑成型: ① 其驱动装置须是无极调速的,以确保挤出速率与最佳吹塑周期相匹配; ② 其螺杆须具有适当的长径比,以确保物料能被均匀、充分地塑化,提高制品的精度和均匀性; ③ 可在较低温度下挤出管坯,以利于缩短生产周期,提高生产效率。
第8页
第五章
(3)把压缩空气通过模具分型面上的吹气管头注入型坯,利用压缩空气力将型坯不断 向模腔的冷壁进行吹胀,使尚处于可塑状态的管坯被吹胀而紧贴于模具型腔的内壁上,形 成与型腔形状一致的制品;
(4)调整开口,冷却吹塑制品,并在保持一定的充气压力的前提下进行第一次冷却定 型,以确保冷却在紧贴模具的情况下进行;
第13页
第五章
(2)机头 机头包括多孔板、滤网连接管和型芯组件等。吹塑机常用的机头分直通式机头、转角机 头和带储料缸式机头三种,其中,直通式机头方向与螺杆轴线方向一致,熔体流经此机 头时,流向不变,此类机头可用于热敏性塑料的吹塑成型,硬PVC瓶往往是采用此机头 进行吹塑得到;转角机头由管式机头和连接管组成,两者彼此垂直;带储料缸式机头中 带有储料缸,熔体先在其中储存,当储存量达到一定值后,被一起挤压吹塑,由于储料 缸中可存储足量体积的熔体,故此类机头可用于生产啤酒桶等大型吹塑制品。
- 1、下载文档前请自行甄别文档内容的完整性,平台不提供额外的编辑、内容补充、找答案等附加服务。
- 2、"仅部分预览"的文档,不可在线预览部分如存在完整性等问题,可反馈申请退款(可完整预览的文档不适用该条件!)。
- 3、如文档侵犯您的权益,请联系客服反馈,我们会尽快为您处理(人工客服工作时间:9:00-18:30)。
热坯吹塑周期较短。在实际工业生产中最为常见;根据制造方法的不同,吹塑成型工艺
可分为挤出吹塑、注射吹塑和拉伸吹塑三个主要方法,加工不同产品时,可根据原料、 加工要求、产量及成本等具体情况选择适当的吹塑方法。
第5页
第五章
挤出吹塑是最主要的一种吹塑成型方法,主要用于未被支撑的型坯加工,约 的吹塑制 品是通过此法制造的。 根据坯料的供料方式,挤出吹塑分为连续挤出吹塑和不连续挤出吹塑两种,其中,连 续挤出吹塑是指挤出机连续地挤出管坯,当管坯达设定长度时,闭合模具,切断管坯,并 连同模具一起被移至下一工位进行吹胀、冷却、脱模,从时间上看,后一段管坯的挤出与 前一段管坯的吹胀、冷却、脱模是同步进行的,故连续挤出吹塑生产效率高,适合大批量 生产。
第20页
第五章
② 螺杆转速 螺杆转速是影响管坯质量的另一个重要的因素。螺杆转速快,挤出产量提高,可 得到更多的型坯,但过快可能导致熔体产生不稳定流动,型坯表面质量下降,严重时甚至 可能出现熔体破裂现象,而且,转速过快时,将产生大量摩擦热,增大了塑料发生瞬间降 解的危险。所以,在能够挤出均匀、光滑管坯且没有使挤出传动系统超负荷的前提下,螺 杆转速尽可能快,但不宜过快,一般应控制在70转/分以下,具体的螺杆转速大小取决于
第17页
第五章
图c为典型的下吹法模具结构示意图,使用 时,从挤出机口模出来的坯料套在底部以固定口颈的内外尺寸。由于型坯的下端壁厚比 较厚,采用下吹法可使容器口颈部位的壁厚较厚, 较适宜大、中型容器的吹胀成型。
第18页
第五章
影响挤出吹塑成型工艺和制品质量的因素主要有型坯的温度、吹气压力和吹气速度、 吹胀比、模温和冷却时间等。 (1)管坯制造过程中的影响因素 ① 原料 原料是影响管坯质量的一个非常重要的因素。除了性能上必须满足制品的使用要求之 外,原料的如下特性对型坯的质量存在较为明显的影响:
一般为三角形或梯形。由于吹塑压力较低,一般介于0.2~0.7MPa之间,模具结构比较简单,对模具
强度的要求比较低,故有多种材料可用于制作吹塑模具,如铝合金、锌合金、钢材、铍铜等,具体材质 可根据物料特性及制品数量进行选择。为了排除模具表面和管坯表面之间的空气,确保制品的外观质量,
模具上应设置排气孔或排气槽,排气孔或排气槽的位置、形状及数量主要取决于型腔的形状,但由于其
第9页
第五章
(7)修整制品,去除制品飞边,回收边角料,进行质量检测等。 多层复合吹塑成型工艺是在单层挤出吹塑成型工艺的基础上发展起来的一种新型工艺 过程,两者间并无实质性的不同,两者的差别主要表现在型坯的加工方法不同,另外,多 层挤出需采用能够挤出多层结构管状物的机头。多层复合吹塑成型工艺可用于成型不同物 料组成的吹塑制品。在多层吹塑成型工艺中,各层塑料间的相互熔合效果及彼此间粘结质 量的控制十分重要,如果塑料间熔合效果不好,粘结较差,则制品夹口区的强度将会显著 下降,从而影响制品质量。在实际生产中,可采用适当的方法来改善不同物料层间的熔合 和粘结性能,如往各层物料中混入粘性的组分,或在原料各层间增加有粘结功能的物料层 等。多层吹塑所用物料的种类及必要的层数应视具体要求确定,制品的层数越多,成型也
与制品直接接触,故需要具有较高的加工精度。
第15页
第五章
从模具的结构和成型工艺方法上看,吹塑模具可分为上吹 法(顶吹法)、下吹法(底吹法)和平吹法(气针法)三种, 图a为典型的上吹法模具结构示意图,模具的颈部朝上,闭模 时,管坯底部被夹紧,顶部开口,压缩空气从模具上端通过型
芯吹入模腔中。上吹法的优点是型芯和吹气芯轴合二为一,故
型坯将塑化不良,尺寸及质量不均匀,最终降低制品的强度。
第22页
第五章
① 型坯温度 型坯的温度直接影响其形状的稳定性、制品的表面光洁度、接缝强度及冷却时间等。
当型坯温度较高时,其强度将有所下降,制品虽然容易发生吹胀变形,但难于保证制品壁
厚的均匀性,尤其是管坯纵向厚度的均匀性。同时,吹胀物的冷却时间延长,成型设备的 生产效率下降。反之,降低型坯温度可确保其具有足够的强度,但吹塑成型将变得困难,
具体的物料。
第21页
第五章
③ 口模 口模是决定型坯尺寸及形状的重要装置,主要由两对半阴模构成,其内表面需具有足
够的光洁度,且尺寸必须按设计要求加工,口模定型段尺寸一般为口模芯棒之间隙数值的
8倍左右。 ④ 加工温度 加工温度升高,型坯下垂严重,型坯长度增加,但直径及壁厚将下降,严重时,甚至 可能导致型坯断裂;温度下降,型坯表面将变得粗糙,可能出现鲨鱼皮、流痕、竹节等,
第3页
第五章
吹塑成型分类
01
按型坯状态分类
02 按制造方法不同分类
第4页
第五章
根据吹塑成型时型坯状态的不同,吹塑成型工艺可分为冷坯吹塑和热坯吹塑两种, 冷坯吹塑是将挤出或注射得到的坯料重新加热到类橡胶状态后,再放入吹塑模具内进行 吹塑成型,热坯吹塑是将所得的型坯直接在热状态下立即送入吹塑模具中进行吹胀成型,
进行吹塑得到;转角机头由管式机头和连接管组成,两者彼此垂直;带储料缸式机头中
带有储料缸,熔体先在其中储存,当储存量达到一定值后,被一起挤压吹塑,由于储料
缸中可存储足量体积的熔体,故此类机头可用于生产啤酒桶等大型吹塑制品。
第14页
第五章
(3)吹塑模具 吹塑模具常设计为以分型面为界的对开式两半模具,对形状不规则的瓶类或容器,模具的分型面也可能 设计为不规则,必要时,可使用三个或更多个移动部件组成分型面模具,一般没有冷却剂通道,但对于 大型吹塑模具,可设计冷却水道。模口部分一般做成较窄的锋利刀口状,以便快速切断型坯,刀口形状
③ 可在较低温度下挤出管坯,以利于缩短生产周期,提高生产效率。
第13页
第五章
(2)机头 机头包括多孔板、滤网连接管和型芯组件等。吹塑机常用的机头分直通式机头、转角机 头和带储料缸式机头三种,其中,直通式机头方向与螺杆轴线方向一致,熔体流经此机
头时,流向不变,此类机头可用于热敏性塑料的吹塑成型,硬PVC瓶往往是采用此机头
其结构简单,缺点是不能确定型坯内径和长度,需要另外增加 修饰工序,且由于借助型芯作为吹气芯轴,当通过压缩空气时, 将对机头产生影响,从而可能影响型坯的质量。
第16页
第五章
图b为平吹法模具结构示意图, 型坯进入模具后,上下端夹持,压缩 空气经横向气针注入型坯。平吹法的 优点是压缩空气可以容器的任何部位 注入,可用于吹塑成型非开口容器、 可折叠软容器等。
第7页
第五章
单层挤出吹塑成型工艺过程一般包括以下几个步骤: (1)利用挤出机完成对塑料的输送、压缩、熔化、塑化、排气等功能,并将熔体泵入 机头,按预先设定好的程序,在预定的时间,从管状机头挤出适当厚度和直径的型坯,垂 挂在安装于机头正下方的预先分开的吹塑模具的型腔中; (2)当下垂的型坯达到预定的长度时,立即闭合吹塑用的两半模具,利用模具的闭合 力,将型坯切断并夹持在两半模具之间,切断后移至另一工位,从型坯一端插入吹管头, 并确保吹管、型坯及吹胀模腔具有相同的中心轴线;
第19页
第五章
a.熔融指数 熔融指数低,管坯下垂容易,容易得到厚薄均匀的管坯,但如果熔融指数过低, 熔体产生不稳定流动的概率增大,而不稳定流动一旦发生,制品的外观质量将变差,甚至出现 不合格现象。所以,在吹塑成型前,应根据具体的制品性能及加工性能合理选择原料。一般情 况下,吹塑成型大中型尺寸的制品时,原料的熔融指数宜小些,反之,生产小型吹塑制品时,
熔融指数宜大些。
b. 分子量 原料分子量大,受应力作用时,防止出现龟裂的能力强,所以,一般采用分子量 较大的原料,但分子量过高,型坯的挤出及后续的吹塑将愈加困难,分子量的大小应综合考虑。 c. 分子量分布 分子量分布宽,有利于得到高质量的管坯,但过宽,可能导致制品强度下降。 d.拉伸粘度 拉伸粘度随拉伸应力增加而增大的物料有利于吹塑加工。 另外,原料在加工过程中应具有阻止氧气、二氧化碳、氮气及水蒸气等向容器内外透散的 特性。
第12页
第五章
不连续旋转往复式挤出机的工作原理与连续旋转往复式螺杆挤出机基本相似,主要差别在于其螺杆
在往复过程中停止旋转,机筒内固体物料不能连续地变为熔体,因而,熔体的挤出是不连续的。吹塑成
型工艺中常见的挤出机为单螺杆挤出机,其组成和结构和普通单螺杆挤出机并无特殊之处,由机筒、螺 杆、加热元件、温控元件与传动装置等部分组成。普通挤出机在满足如下要求后也可用于吹塑成型: ① 其驱动装置须是无极调速的,以确保挤出速率与最佳吹塑周期相匹配; ② 其螺杆须具有适当的长径比,以确保物料能被均匀、充分地塑化,提高制品的精度和均匀性;
就越困难。
第10页
第五章
典型的挤出吹塑设备如 图1所示。 1-机头, 2-夹坯块, 3-挤出机, 4-吹塑模具, 5-制品
第11页
第五章
(1) 挤出机 挤出吹塑成型设备中,挤出机的质量好坏在很大程度上决定了生产的可操作性、稳定性和安全性, 更决定了生产中空吹塑制品的力学性能、外观质量、各批制品间的均匀一致性、生产效率和成本高低等, 是吹塑装置中最主要的设备。挤出吹塑成型用挤出机分两类,一类是连续挤出熔体的连续旋转往复式螺
杆挤出机,一类是间歇挤出熔体的往复式挤出机,也即不连续旋转往复式挤出机。对于连续式螺杆挤出
机而言,通过螺杆的旋转使物料沿螺槽向前移动,并受热形成熔体,熔体储存于螺杆头前面的机筒内, 当熔体量达到一定值后,油缸工作,产生推力,使螺杆向前移动,熔体被连续挤出,柱塞油压逐渐下降, 螺杆后退,如此反复进行生产;
第6页
第五章
不连续挤出吹塑则是将熔融的物料挤出并储存起来,再用柱塞将熔体挤成管坯,并吹 塑成型。由于此法事先储存了较多的熔体,故可在较短时间内挤出大量的树脂,因而,可 由于生产储罐及其他大型制品。 根据挤出吹塑制品的结构,挤出吹塑分为单层挤出吹塑和多层挤出吹塑。 挤出吹塑的优点是设备简单,设备成本低,投资少,模具和机械的选择范围广,管坯 生产效率高,型坯温度比较均匀,熔接逢少,制品破裂程度低,吹塑制品强度较高,适合 不同形状、大小和壁厚的中空容器的生产,适合多种塑料的中空成型,能生产大型容器, 产品成本低、工艺简单、效益高。