减速器壳体旋转钻夹具毕业设计
毕业设计(论文)开题报告涡轮减速器箱体机械加工工艺规程及钻床夹具设计
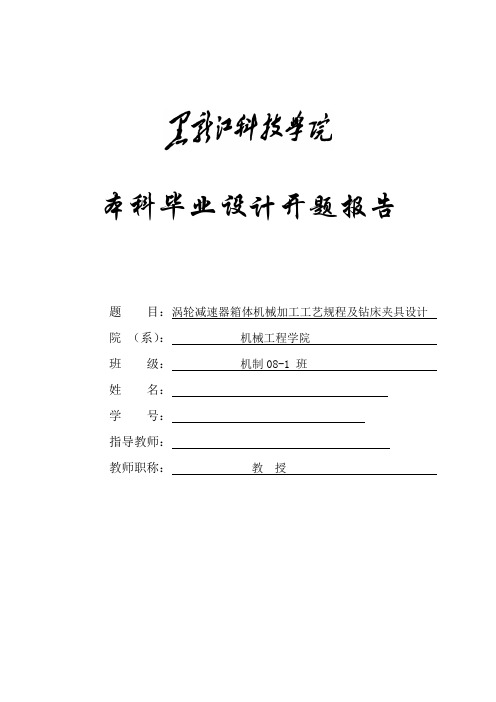
本科毕业设计开题报告
题目:涡轮减速器箱体机械加工工艺规程及钻床夹具设计院(系):机械工程学院
班级:机制08-1 班
姓名:
学号:
指导教师:
教师职称:教授
黑龙江科技学院本科毕业设计开题报告
华大学开发了计算机辅助组合夹具夹具设计系统。
随着CAFD技术的进一步发展和现代生产的需求,对组合夹具的设计和构形自动化、智能化提出了更高的要求[16]。
3、研究/设计的目标:
3.1涡轮减速器箱体加工工艺设计的目标
涡轮减速器箱体的主要技术要求是对孔和平面的精度和表面粗糙度的要求,支撑孔的尺寸精度、几何形状精度和表面粗糙度,孔与孔的轴线之间的相互位置精度(平行度、垂直度),装配基准面与加工时的定位基准面的平面度和表面粗糙度,各支承孔轴线和平面基准面的尺寸精度、平行度和垂直度。
加工时,按照先粗后精,加工面再加工孔的原则进行加工,这样才能加工出质量合格、符合技术要求的零件。
3.2钻床夹具设计的目标
夹具的设计则应在满足基本使用功能的基础上,尽量保证涡轮减速器箱体各部分的加工精度。
尽量优化、简化夹具结构,降低生产成本。
对夹具体以下有几点要求:1)有适当的精度和尺寸稳定性
2)有足够的强度和刚度
3)结构工艺性好
4)在机床上安装稳定可靠。
4、设计方案(研究/设计方法、理论分析、计算、实验方法和步骤等):
4.1涡轮减速器箱体机械加工工艺的设计方案
本题目加工涡轮减速器箱体零件如图1所示:
图1 零件图。
机械工艺夹具毕业设计143减速箱体工艺设计与工装设计
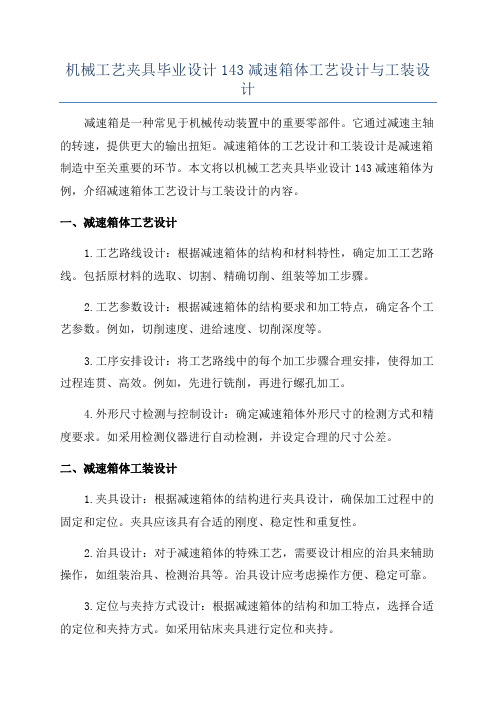
机械工艺夹具毕业设计143减速箱体工艺设计与工装设计减速箱是一种常见于机械传动装置中的重要零部件。
它通过减速主轴的转速,提供更大的输出扭矩。
减速箱体的工艺设计和工装设计是减速箱制造中至关重要的环节。
本文将以机械工艺夹具毕业设计143减速箱体为例,介绍减速箱体工艺设计与工装设计的内容。
一、减速箱体工艺设计1.工艺路线设计:根据减速箱体的结构和材料特性,确定加工工艺路线。
包括原材料的选取、切割、精确切削、组装等加工步骤。
2.工艺参数设计:根据减速箱体的结构要求和加工特点,确定各个工艺参数。
例如,切削速度、进给速度、切削深度等。
3.工序安排设计:将工艺路线中的每个加工步骤合理安排,使得加工过程连贯、高效。
例如,先进行铣削,再进行螺孔加工。
4.外形尺寸检测与控制设计:确定减速箱体外形尺寸的检测方式和精度要求。
如采用检测仪器进行自动检测,并设定合理的尺寸公差。
二、减速箱体工装设计1.夹具设计:根据减速箱体的结构进行夹具设计,确保加工过程中的固定和定位。
夹具应该具有合适的刚度、稳定性和重复性。
2.治具设计:对于减速箱体的特殊工艺,需要设计相应的治具来辅助操作,如组装治具、检测治具等。
治具设计应考虑操作方便、稳定可靠。
3.定位与夹持方式设计:根据减速箱体的结构和加工特点,选择合适的定位和夹持方式。
如采用钻床夹具进行定位和夹持。
4.工装加工设计:根据工装的结构和材料特性,确定加工工艺和加工路线。
工装应具有合适的刚度和精度。
总结起来,减速箱体工艺设计和工装设计是减速箱制造中的重要环节,对于保证减速箱体的加工质量和生产效率起着至关重要的作用。
通过合理设计工艺路线、工艺参数、工序安排以及夹具、治具的设计,可以实现减速箱体的高效加工和质量控制。
减速器箱盖钻孔组合机床的夹具设计
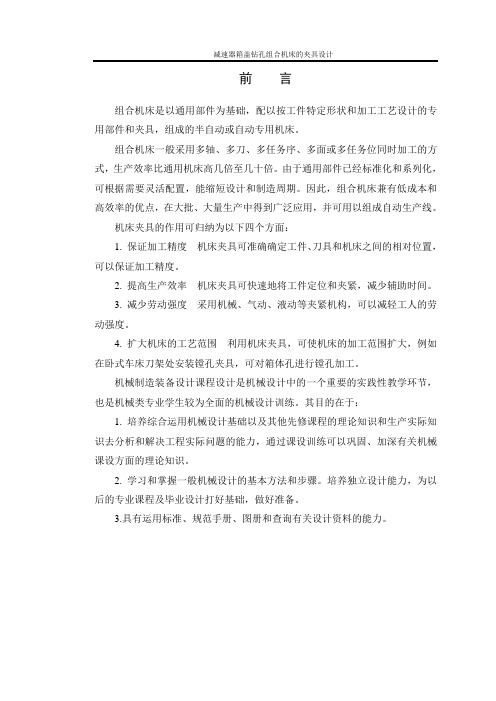
前言组合机床是以通用部件为基础,配以按工件特定形状和加工工艺设计的专用部件和夹具,组成的半自动或自动专用机床。
组合机床一般采用多轴、多刀、多任务序、多面或多任务位同时加工的方式,生产效率比通用机床高几倍至几十倍。
由于通用部件已经标准化和系列化,可根据需要灵活配置,能缩短设计和制造周期。
因此,组合机床兼有低成本和高效率的优点,在大批、大量生产中得到广泛应用,并可用以组成自动生产线。
机床夹具的作用可归纳为以下四个方面:1. 保证加工精度机床夹具可准确确定工件、刀具和机床之间的相对位置,可以保证加工精度。
2. 提高生产效率机床夹具可快速地将工件定位和夹紧,减少辅助时间。
3. 减少劳动强度采用机械、气动、液动等夹紧机构,可以减轻工人的劳动强度。
4. 扩大机床的工艺范围利用机床夹具,可使机床的加工范围扩大,例如在卧式车床刀架处安装镗孔夹具,可对箱体孔进行镗孔加工。
机械制造装备设计课程设计是机械设计中的一个重要的实践性教学环节,也是机械类专业学生较为全面的机械设计训练。
其目的在于:1. 培养综合运用机械设计基础以及其他先修课程的理论知识和生产实际知识去分析和解决工程实际问题的能力,通过课设训练可以巩固、加深有关机械课设方面的理论知识。
2. 学习和掌握一般机械设计的基本方法和步骤。
培养独立设计能力,为以后的专业课程及毕业设计打好基础,做好准备。
3.具有运用标准、规范手册、图册和查询有关设计资料的能力。
目录摘要 (I)ABSTRACT ....................................................................................... I I 1 绪论.. (1)1.1 组合机床概述 (1)1.2 该课题研究的目的和意义 (1)1.3 组合机床夹具发展史 (1)1.4 现代机床夹具的发展方向 (1)2 零件分析 (3)2.1 零件结构特点 (3)2.2 技术要求 (3)2.3 结构方案分析和方案的选择 (3)2.4 选择定位基准的原则及应注意的问题 (3)2.5 确定夹压位置应注意的问题 (3)2.6 工艺分析 (4)3 工艺参数的确定 (5)3.1 切削用量的确定 (5)3.2 确定切削力、切削扭矩、切削功率 (5)3.3 选择刀具结构 (6)3.4 导向结构的选择 (7)3.5 工作进给长度的确定 (8)3.6 快进长度的确定 (8)4 夹具设计 (9)4.1 夹具概述 (9)4.1.1 夹具分类 (9)4.1.2 机床夹具的现状 (9)4.2 夹具设计任务 (10)4.3 零件分析 (10)4.4 定位机构 (10)4.4.1 支撑板 (11)4.4.2 伸缩式定位销 (12)4.5 夹紧机构 (13)4.6 导向装置的选择 (15)4.7 机床夹具的总体形式 (16)4.7.1 确定工作台 (16)4.7.2 确定夹具体 (17)4.7.3 确定联接体 (17)4.7.4 夹具体的总体设计图 (17)4.8 绘制夹具装配图 (17)4.9 定位误差计算 (20)4.9.1 定位误差 (20)4.9.2 产生定位误差的原因 (20)4.9.3 定位误差的计算 (20)4.10 夹紧力计算 (21)4.11 夹具精度分析计算 (21)4.12 夹具的性能及优点 (23)结论 (24)谢辞 (25)参考文献 (26)减速器箱盖钻孔组合机床的夹具设计摘要本课题设计任务是:减速器箱盖双面钻孔组合钻床的夹具设计。
减速机壳加工工艺及夹具设计毕业设计论文

内容摘要:在生产过程中,使生产对象(原材料,毛坯,零件或总成等)的质和量的状态发生直接变化的过程叫工艺过程,如毛坯制造,机械加工,热处理,装配等都称之为工艺过程。
在制定工艺过程中,要确定各工序的安装工位和该工序需要的工步,加工该工序的机车及机床的进给量,切削深度,主轴转速和切削速度,该工序的夹具,刀具及量具,还有走刀次数和走刀长度,最后计算该工序的基本时间,辅助时间和工作地服务时间。
关键词:工序,工位,工步,加工余量,定位方案,夹紧力Abstract :Enable producing the target in process of production (raw materials, the blank , state of quality and quantity on part become always ) take place direct course of change ask craft course, if the blank is made, machining, heat treatment , assemble etc. and call it the craft course. In the course of making the craft , is it confirm every erector location and worker step that process need this of process to want, the locomotive of processing , this process , and the entering the giving amount of the lathe, cut depth , the rotational speed of the main shaft and speed of cutting, the jig of this process, the cutter and measuring tool, a one hundred sheets ofnumber of times still leaves and a one hundred sheets of length leaves, calculate basic time of this process , auxiliary time and service time of place of working finally.Keyword:The process, worker one, worker's step , the surplus of processing, orient the scheme , clamp strength目录摘要Abstract第一章绪论 (5)第二章零件的工艺分析 (5)2.1零件的工艺分析 (5)2.2确定毛坯的制造形式 (5)2.3箱体零件的工艺性 (5)第三章拟定箱体加工的工艺路线 (6)3.1 定位基准的选择 (6)3.2 加工路线的拟定 (6)第四章加工余量,工序尺寸及毛坯尺寸的确定 (9)4.1 机盖 (9)4.2 机座 (10)4.3 机体 (11)第五章确定切削用量及基本工时 (11)5.1 机盖 (11)5.2机座 (17)5.3机体 (26)参考文献 (39)结论 (40)第一章:绪论箱体零件是机器或部件的基础零件,它把有关零件联结成一个整体,使这些零件保持正确的相对位置,彼此能协调地工作.因此,箱体零件的制造精度将直接影响机器或部件的装配质量,进而影响机器的使用性能和寿命.因而箱体一般具有较高的技术要求.由于机器的结构特点和箱体在机器中的不同功用,箱体零件具有多种不同的结构型式,其共同特点是:结构形状复杂,箱壁薄而不均匀,内部呈腔型;有若干精度要求较高的平面和孔系,还有较多的紧固螺纹孔等.箱体零件的毛坯通常采用铸铁件.因为灰铸铁具有较好的耐磨性,减震性以及良好的铸造性能和切削性能,价格也比较便宜.有时为了减轻重量,用有色金属合金铸造箱体毛坯(如航空发动机上的箱体等).在单件小批生产中,为了缩短生产周期有时也采用焊接毛坯.毛坯的铸造方法,取决于生产类型和毛坯尺寸.在单件小批生产中,多采用木模手工造型;在大批量生产中广泛采用金属模机器造型,毛坯的精度较高.箱体上大于30—50mm的孔,一般都铸造出顶孔,以减少加工余量.第二章:零件工艺的分析2.1零件的工艺分析2.1.1要加工孔的孔轴配合度为H7,表面粗糙度为Ra小于1.6um,圆度为0.0175mm,垂直度为0.08mm,同轴度为0.02mm。
减速器箱体的加工工艺及夹具毕业设计论文
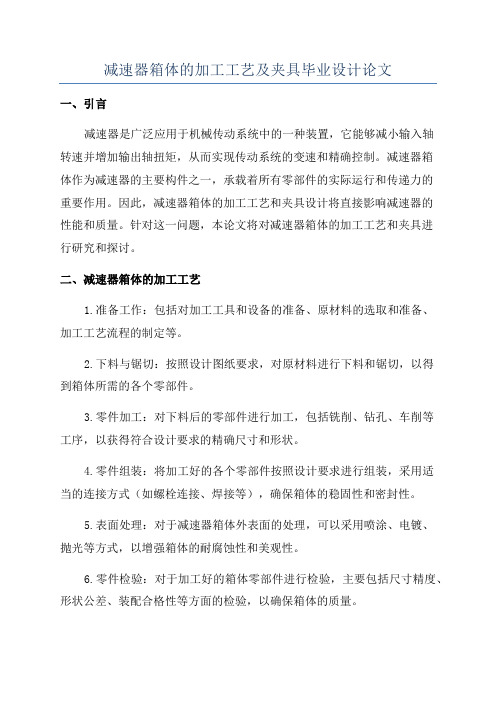
减速器箱体的加工工艺及夹具毕业设计论文一、引言减速器是广泛应用于机械传动系统中的一种装置,它能够减小输入轴转速并增加输出轴扭矩,从而实现传动系统的变速和精确控制。
减速器箱体作为减速器的主要构件之一,承载着所有零部件的实际运行和传递力的重要作用。
因此,减速器箱体的加工工艺和夹具设计将直接影响减速器的性能和质量。
针对这一问题,本论文将对减速器箱体的加工工艺和夹具进行研究和探讨。
二、减速器箱体的加工工艺1.准备工作:包括对加工工具和设备的准备、原材料的选取和准备、加工工艺流程的制定等。
2.下料与锯切:按照设计图纸要求,对原材料进行下料和锯切,以得到箱体所需的各个零部件。
3.零件加工:对下料后的零部件进行加工,包括铣削、钻孔、车削等工序,以获得符合设计要求的精确尺寸和形状。
4.零件组装:将加工好的各个零部件按照设计要求进行组装,采用适当的连接方式(如螺栓连接、焊接等),确保箱体的稳固性和密封性。
5.表面处理:对于减速器箱体外表面的处理,可以采用喷涂、电镀、抛光等方式,以增强箱体的耐腐蚀性和美观性。
6.零件检验:对于加工好的箱体零部件进行检验,主要包括尺寸精度、形状公差、装配合格性等方面的检验,以确保箱体的质量。
7.最终组装和调试:将经过检验合格的零部件进行最终组装,并进行调试和测试,确保减速器箱体的性能和功能达到设计要求。
三、减速器箱体加工工艺中的夹具设计夹具是加工工艺中的重要辅助工具,它能够固定工件、定位、限制运动和提高加工稳定性。
在减速器箱体加工过程中,夹具的设计对于保证加工质量和提高生产效率起到关键作用。
以下是减速器箱体加工工艺中常用的夹具设计方法:1.定位夹具:定位夹具主要用于将待加工的零部件正确的位置上,确保加工精度和减小误差。
常用的定位夹具有平行销、固定块、定位板等。
2.夹持夹具:夹持夹具用于将工件固定在加工设备上,以保证加工过程的稳定性和安全性。
常用的夹持夹具有机械夹具、液压夹具、气动夹具等。
减速机壳体加工工艺及其夹具设计
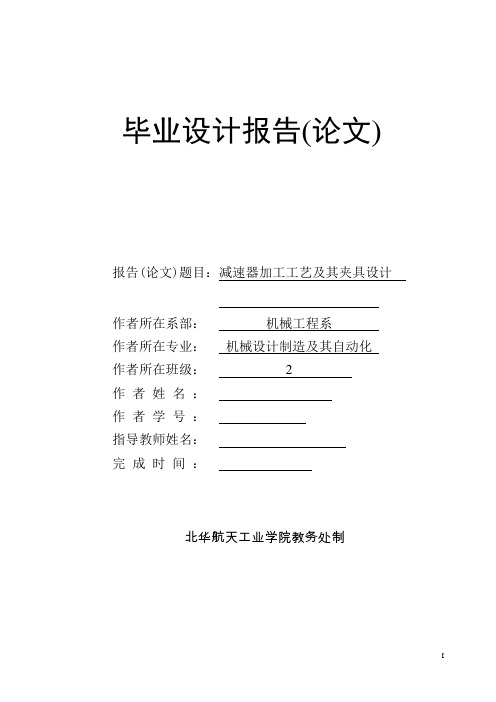
毛坯的尺寸等于零件的尺寸加上(对于外型尺寸)或减去(对内腔尺寸)加工余量。毛坯的形状尽可能与零件相适应。在确定,毛坯的形状时,为了方便加工,有时还要考虑下列问题:
(1)为了装夹稳定、加工方便,对于形状不易装夹稳固或不易加工的零件要考虑增加工艺搭子。
(2)为了提高机械加工的生产率,有些小零件可以作成一坯多件。
>1.8
1.0~1.8
0.5~0.8
0.1~0.3
0.1~0.55
0.04~0.2
0.2~0.3
0.2~0.5
0.1~0.2
0.01~0.02
指孔径在180以下,铸件直径的余量.L/d<2
L/d=2~10时,加工误差增加1.2~2倍
平
面
粗刨,粗铣
精刨,精铣
细刨,细铣
粗磨
半精磨
精磨
研磨
25
6.3
0.8
二.箱体的材料、毛坯及热处理
1、毛坯种类的确定。
常用毛坯种类有:铸件、锻件、焊件、冲压件。各种型材和工程塑料件等。在确定毛坯时,一般要综合考虑以下几个因素:
(1)依据零件的材料及机械性能要求确定毛坯。例如,零件材料为铸铁,须用铸造毛坯;强度要求高而形状不太复杂的钢制品零件一般采用锻件。
(2)依据零件的结构形状和外形尺寸确定毛坯,例如结构比较的零件采用铸件比锻件合理;结构简单的零件宜选用型材,锻件;大型轴类零件一般都采用锻件。
减速器箱体的机械加工过程取决于精度要求、批量大小、结构特点、尺寸重量、大小等因素。此处还应考虑车间的条件,中间有无热处理工序。
由图可知,减速器箱体整个加工工艺过程分为两大阶段,先对箱盖和机体分别进行加工,而后合箱对整体箱进行加工。第一阶段主要完成平面、紧固孔、油塞孔和油标的加工,为整体合箱做准备。第二阶段为合装好的箱体上加工轴承孔及其端面,第二阶段加工完成后,还应拆箱,为了保证轴承孔加工精度和拆装后的重复精度,应在两阶段之间安排钳工工序,钻铰二定位销孔,并打入定位销。
减速器机盖加工工艺及顶面孔钻夹具设计—毕业设计(论文)-说明书-张颖超

减速器机盖加工工艺及顶面孔钻夹具设计—毕业设计(论文)-说明书-张颖超本科毕业设计(论文)减速器机盖加工工艺及顶面孔钻夹具设计学院名称:机械工程学院专业:机械设计制造及其自动化班级:11机制1学号:11321108减速器机盖加工工艺及顶面孔钻夹具设计摘要:蜗杆减速器箱体零件是箱体类零件的一种。
它把减速器箱体中的轴和齿轮等有关零件和机构联接为一整体,使这些齿轮等零件和机构保持正确的相对位置,以便其上各个机构和零件能正确、协调一致地工作,减速器箱体的加工精度直接影响减速器的装配质量,进而影响机器的使用性能和寿命。
因此研究使用适合的夹具对该类型零件进行加工是一个值得深入探讨的问题。
在本次设计中,对蜗杆减速器箱体机盖的加工工艺路线进行了编制和方案优选,对钻夹具的钻模板类型进行了深入研究以使所加工零件易于装夹,计算了采用一面两孔制的定位方法所引起的定位误差,从而论证了该套设计方案的可行性和经济性。
关键词:蜗杆减速器,箱体,钻夹具,工艺The Design of Reducer’s Cover machining process and Design ofTop Face Drill FixtureAbstract:Worm gear reducer box body parts is one of the box body parts. The shaft of the reducer housing and gear and related parts and joined into a whole, make these gear and other parts and kept the correct relative position, so that its various agencies and parts can correct, the coordinated work, reducer box directly influences the machining accuracy of gear reducer assembly quality, will affect the use of machine performance and service life. Therefore research using suitable fixture for processing of the types of parts was a problem worthy of in-depth discussion.In the design, processing technology route of worm reducer box machine cover compilation and scheme optimization, the drilling template type of drill jigs were studied in order to make the processing parts easy clamping, were calculated by using a two hole system caused by the positioning method of positioning error, which demonstrates the feasibility and economy of this set of design scheme.Keywords:Worm gear reducer; Box body; Drill jig; Process目录序言 (1)第1章零件分析与方案论证 (2)1.1减速器零件的作用 (2)1.1.1减速器零件的作用及分类 (2)1.1.2箱体类零件的分析 (3)1.2零件的分析 (3)1.2.1零件的技术要求 (3)1.2.2零件的加工分析方法 (5)1.3设计任务书 (5)第2章工艺规程设计 (7)2.1确定毛坯的制造形式 (7)2.2生产类型及工艺特征 (7)2.3定位基准的选择 (8)2.3.1粗基准的选择 (8)2.3.2 精基准的选择 (9)2.4制定工艺路线 (9)2.4.1常见传动形式的对比 (10)2.5机械加工余量、工序尺寸及毛坯尺寸的确定 (10)2.5.1毛坯尺寸确定及毛坯图的绘制 (10)2.5.2工序尺寸确定 (12)2.6确定切削用量及基本工时 (12)第3章专用夹具设计 (26)3.1设计概述 (26)3.2 钻孔夹具方案设计 (26)3.2.1 了解夹具总体设计的要求 (26)3.2.2夹具的类型与钻模的类型 (27)3.3夹具设计 (28)3.3.1工件定位分析 (28)3.3.2 夹紧机构的确定 (30)3.3.3 定位误差分析 (31)3.3.4 夹紧力计算 (32)3.3.5 夹具设计装配图 (33)3.4 夹具体零件的设计 (34)3.4.1 夹具体毛坯的类型 (35)3.4.2夹具体零件图的绘制 (35)第4章专用夹具三维造 (37)4.1 夹具三维造型 (37)参考文献 (42)致谢 (43)序言在工业化程度非常高的当今社会,各式各样、大大小小的减速器无处不在,应用十分广泛,尤其是在汽车等各种交通工具和大型机械中。
通用减速机壳体连接孔钻削加工工艺装备设计——组合机床、夹具设计_毕业设计 推荐

学号保密了额毕业设计(论文)通用减速机壳体连接孔钻削加工工艺装备设计——组合机床、夹具设计教学系:机电工程系指导教师:专业班级:机自1094班学生姓名:二零一三年六月毕业设计(论文)任务书学生姓名专业班级机自1094班指导教师工作单位机电工程系设计(论文)题目通用减速机壳体连接孔钻削加工工艺装备设计——组合机床、夹具设计设计(论文)主要内容:1、通用减速机壳体8×Φ13连接孔钻削加工工艺方案设计;2、通用减速机壳体8×Φ13连接孔钻削加工组合机床设计;3、通用减速机壳体8×Φ13连接孔钻削加工多轴箱设计;4、编写设计说明书要求完成的主要任务及其时间安排:主要任务:1、通用减速机壳体8×Φ13连接孔钻削加工工艺方案;2、绘制机床联系尺寸图、加工示意图、工序图等;3、绘制加工多轴箱总图;4、进行必要的设计计算;5、编写设计说明书;时间安排:第1~3周:接受毕业设计课题,根据课题内容了解课题研究的现状,并进行查找资料,完成开题报告;第4~5周:通用减速机壳体8×Φ13连接孔钻削加工工艺方案设计;第6~8周:绘制机床联系尺寸图、加工示意图、工序图等;第9周:绘制加工多轴箱总图;第10~11周:进行必要的设计计算;第12周:编写毕业设计说明书第13周:对设计进行检查、纠正、整理、综合;最后打印,交指导老师复查。
必读参考资料:《组合机床简明设计手册》机械工业出版社《机械制造装备设计》机械工业出版社指导教师签名:教研室主任签名:毕业设计(论文)开题报告题目通用减速机壳体连接孔钻削加工工艺装备设计——组合机床、夹具设计1.目的及意义:本次的毕业设计的目的在于让我们在设计之中得到构思设计,设计方案的分析,工艺方案的设计,零件的有必要的计算,CAD机械制图和查阅相关资料文献的综合训练。
通过此次设计来达到对以前所学知识的巩固和对所学相关知识的综合应用,以达到对于所学知识相关的设计的熟练应用。
毕业设计(论文)-减速箱体机械加工工艺及夹具设计-2套夹具(全套图纸)[管理资料]
![毕业设计(论文)-减速箱体机械加工工艺及夹具设计-2套夹具(全套图纸)[管理资料]](https://img.taocdn.com/s3/m/10c191a177232f60dccca19d.png)
减速箱体机械加工工艺及夹具设计全套CAD图纸,加153893706学生姓名:学生学号:院(系):机电工程学院年级专业:2004级机械设计制造及其自动化指导教师:二〇〇八年六月摘要箱体零件是一种典型零件,其加工工艺规程和工装设计具有典型性。
该箱体零件结构复杂,零件毛坯采用铸造成形。
在加工过程中,采用先面后孔的加工路线,以保证工件的定位基准统一、准确。
为了消除切削力、夹紧力、切削热和因粗加工所造成的内应力对加工精度的影响,整个工艺过程分为粗、精两个阶段。
通过被加工零件的分析完成了机械加工工艺的设计及各加工工序机动时间的计算。
根据箱体零件的结构及其功能,运用定位夹紧的知识完成了夹具设计。
关键词箱体,工艺,夹具ABSTRACTThis box machine element is typical, the manufacturing process and tooling design of it is structure of this box machine element is complicated, the machine element’s blank adopt casting shape. In the process of manufacture, in order to ensure th -e location datum accurate and unity, I adopt the manufacturing line from face to order to clear away the influence for machining accurate of internal stress, cutting force, clamping force, heat in cutting from coarse manufacturing, the whole manufacturing pro -cess is made of coarse and accurate manufacturing. Parts were processed through the a -nalysis of the complete machining process design and the manufacturing processes for mobile time calculations. According to the box components and the function and structu -re, the use of the knowledge positioning clamp completed the fixture design.Key words Box machine,Processing,Jig目录摘要 (I)ABSTRACT (II)1 绪论 (1)课题背景 (1)制订工艺规程的意义与作用及其基本要求 (1)夹具的设计 (1)2 零件的分析 (2)箱体零件的功用和结构特点 (2)箱体零件图样分析 (2)箱体零件工艺分析 (3)箱体零件的主要技术要求 (4)主要设计内容 (5)3 工艺规程设计 (7)箱体的材料及毛坯 (7)减速箱箱体加工的主要问题和加工工艺过程设计所应采取的相应措施 (8)减速箱体加工定位基准的选择 (8)制定箱体的工艺路线 (9)机械加工余量、工序尺寸及毛坯尺寸的确定 (13)确定切削用量及基本工时(机动时间) (15)时间定额计算及生产安排 (28)4 夹具设计 (35)镗床夹具设计 (35)工件加工工艺分析 (35)定位方案及定位元件设计 (35)夹紧方案及夹紧元件设计 (35)镗杆的直径与长度 (36)夹具体的设计 (36)镗套的设计 (36) (38)夹具精度分析计算 (40)镗孔夹具的装配说明 (41)钻床夹具设计 (42)工件结构特点分析 (42)工件定位方案和定位元件的设计 (42)夹紧方案和夹紧元件的设计 (42)夹具体的设计 (43)钻模板的设计 (43)钻套的选择与设计 (44)切削力及夹紧计算 (45)夹具精度分析计算 (46)钻床夹具的装配说明 (48)结论 (49)参考文献 (50)致谢 (51)1 绪论课题背景毕业设计(论文)是我们在学校学习的最后一门课程,也是对自己在大学中所学知识的一个全面的检验。
(完整版)减速器箱盖钻孔加工组合机床设计毕业设计论文
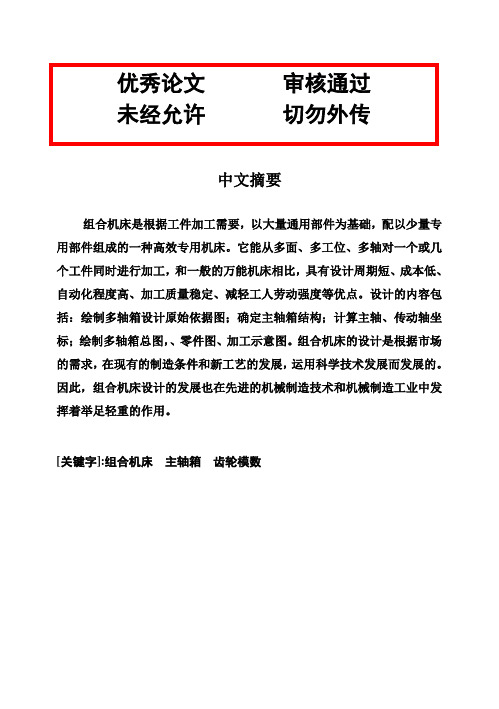
优秀论文审核通过未经允许切勿外传中文摘要组合机床是根据工件加工需要,以大量通用部件为基础,配以少量专用部件组成的一种高效专用机床。
它能从多面、多工位、多轴对一个或几个工件同时进行加工,和一般的万能机床相比,具有设计周期短、成本低、自动化程度高、加工质量稳定、减轻工人劳动强度等优点。
设计的内容包括:绘制多轴箱设计原始依据图;确定主轴箱结构;计算主轴、传动轴坐标;绘制多轴箱总图,、零件图、加工示意图。
组合机床的设计是根据市场的需求,在现有的制造条件和新工艺的发展,运用科学技术发展而发展的。
因此,组合机床设计的发展也在先进的机械制造技术和机械制造工业中发挥着举足轻重的作用。
[关键字]:组合机床主轴箱齿轮模数AbstractCombination Machine Tool is required under the workpiece to alarge number of common components, based on a few specific components together with an efficient machine tools.It from the multi-faceted, multi-site, multi-axis workpiece on one or several simultaneous processing. Compared with the general multi-function machines, with shorter design cycles, low cost, , process quality, reduce labor intensity and so on.Design include: multi-axle design drawing; to determine the structure of the spindle box; calculate the spindle, drive shaft coordinates; draw more axle box of the map part of the diagram, schematic processing.According to market demand, the existing manufacturing conditions and on the development of new technology, the use of science and technology to development.Therefore, the development of Combination Machine Tool design are advanced machinery manufacturing technology and machinery manufacturing industry played a pivotal role.[Key words]:Combination machine tools; Spindle box ;Gear module目录中文摘要 (I)Abstract ........................................................................................................................ I I 第1章绪论 (1)1.1 毕业设计的目的 (1)1.2 组合机床的特点 (1)1.3 组合机床的发展前景 (2)1.3.1 组合机床产品结构的变化 (2)1.3.2 组合机床的快速转变 (2)1.3.3 组合机床技术装备现状与发展趋势 (4)1.3.4 组合机床行业的发展思考 (5)第2章拟定方案 (7)2.1 制定工艺方案要求 (7)2.2 确定机床配置形式及结构方案 (7)2.3 总体设计-三图一卡 (7)2.4 主要技术参数及要求 (7)第3章确定切削用量及选用刀具 (9)3.1 选择切削用量 (9)3.1.1 床切削用量选择的特点 (9)3.1.2 用量应注意的问题 (9)3.2 确定切削力,切削扭矩,切削功率 (9)第4章组合机床总体设计-三图一卡 (11)4.1 被加工零件工序图 (11)4.1.1 被加工零件工序图的作用及内容 (11)4.1.2 注意事项 (11)4.2 加工示意图 (11)4.2.1 加工示意图的作用及内容 (11)4.2.2 注意事项 (12)4.2.3 选择刀具结构 (12)4.2.4 初定主轴类型,尺寸 (13)4.2.5 加工示意图上的重要尺寸 (14)4.2.6 确定动力部件的工作循环及工作行程 (14)4.2.7.其它应注意的问题 (14)4.3 机床联系尺寸图 (14)4.3.1 联系尺寸图的作用及内容 (14)4.3.2 选择动力部件 (15)4.3.3 联系尺寸图应考虑的主要问题 (16)4.3.4 联系尺寸图的画法与步骤 (16)4.4 机床生产率计算卡 (17)4.4.1.理想生产率Q (17)4.4.2 实际生产率Q1 (17)4.4.3 机床生产率计算卡的一般格式 (18)第5章组合机床主轴箱设计 (20)5.1 概述 (20)5.2 通用钻孔主轴箱的组成 (20)5.3 主轴箱的设计步骤与内容 (20)5.4 主轴结构形式的选择及动力计算 (21)5.4.1 主轴结构形式的选择 (21)5.4.2 主轴直径和齿轮模数的初步确定 (21)5.4.3 主轴箱的动力计算 (22)5.5 传动系统的设计与计算 (23)5.5.1 对传动系统的一般要求 (23)5.5.2 拟定主轴箱传动系统的基本方法 (23)5.5.3 传动系统设计的一般要求 (23)5.6 传动系统的设计 (24)5.6.1 多轴箱传动路线拟定 (24)5.6.2 确定传动轴位置及齿轮齿数 (25)5.6.3 主轴箱传动轴坐标计算,绘制坐标检查图 (26)5.7 主轴的润滑、变速 (29)5.8 主轴箱总图设计 (29)5.8.1 主视图 (29)5.8.2 展开图 (30)5.8.3 主轴和传动轴装配图 (30)5.8.4 主轴箱技术条件 (30)总结 (31)参考文献 (32)致谢 (33)第1章绪论毕业设计是学生毕业前完成学习任务所必须的重要环节,它是我们机械制造及其自动化专业四年所学专业课的综合应用,更是培养我们独立思考和动手能力的重要过程。
机械毕业设计(论文)蜗轮蜗杆减速器壳体加工工艺及工装夹具设计【全套图纸】
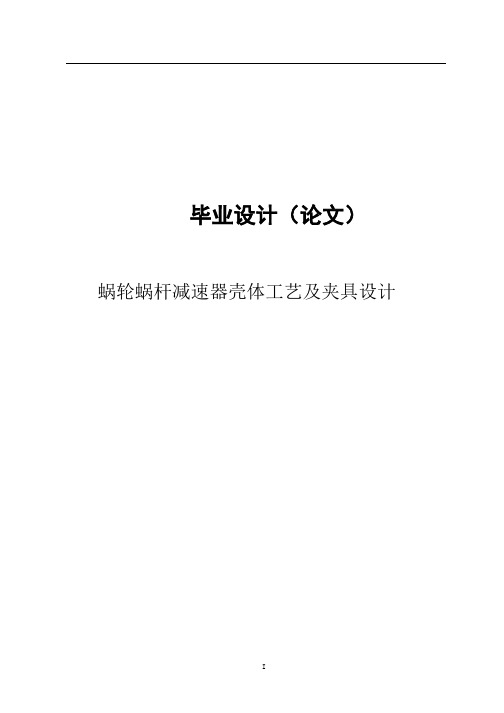
1 绪论 ··································································································· 1 1.1 机械加工工艺概述 ······································································· 1 1.2 机械加工工艺流程 ········································································1 1.3 夹具概述 ····················································································2 1.4 机床夹具的功能 ······················································夹具的发展趋势 ·····································································2 1.5.1 机床夹具的现状 ······································································2 1.5.2 现代机床夹具的发展方向 ························································· 3
汽车后桥减速器壳工艺规程设计及其夹具设计

汽车后桥减速器壳工艺规程设计及其夹具设计优秀设计引言毕业设计是学生的最后一个教学环节,我这次毕业设计的题目是某汽车后桥减速器壳工艺规程设计及其夹具设计。
汽车在正常行驶时,发动机的转速很高,只靠变速箱来降低,会使变速箱的尺寸增大。
同时,转速下降,扭矩必然增加,也就加大了变速箱与变速箱后一级传动机构的传动负荷。
因此,在动力向左右驱动轮分流的差速器之前需要设置一个主减速器。
而主减速器壳是汽车后桥主减速器的一部分。
主减速器壳体加工精度的高低直接影响着差速器壳及主、被动齿轮的配合精度,因而其加工工艺直接影响车桥和整车质量。
我此次毕业设计的任务是对汽车后桥减速器壳进行工艺分析并且设计其夹具。
经过查阅相关资料,并且结合所学的机械知识,对该零件进行工艺分析,确定出合理的加工工艺方案,并选择切削用量及其工艺装备。
了解零件的结构特点及技术要求,查阅相关书籍,例如夹具方面的教材及图册,经过反复的研究、设计、比较、试验,最终设计出一套合理的夹具,即车法兰止口的夹具。
最后在老师和同学的帮助下,经过不断地修改、检查,最终完成了汽车后桥减速器壳工艺规程及其夹具设计。
本次毕业设计使我在机械方面受益匪浅。
特别是刘老师在工作中对我的耐心辅导,他对学生强烈的责任感和严谨的治学态度,无不给我以深刻的影响。
由于类似的大型课题很少接触,经验能力方面的欠缺,错误之处一定存在,恳请各位老师给予批评指正,以便今后的工作尽善尽美。
目录目录 (2)第1章零件的分析 (4)1.1减速器壳在汽车上的位置及功用 (4)1.2减速器壳的结构特点及技术要求 (4)1.2.1结构特点 (4)1.2.2技术要求分析 (5)第2章工艺规程的设计 (7)2.1生产类型的确定 (7)2.1.1生产纲领的确定 (7)2.1.2零件年产量的确定 (7)2.1.3生产类型的确定 (7)2.1.4生产类型对应的工艺特征 (7)2.2毛坯的选择 (8)2.2.1铸件的精度等级选择: (8)2.2.2毛坯余量及偏差的选择 (8)2.3各加工表面的加工方法的选择 (10)2.3.1加工方法的确定 (10)2.3.2加工阶段的划分 (12)2.4制定加工工艺路线 (13)2.5工艺方案的分析 (17)2.6确定各工序的加工余量、工序尺寸、切削用量及工时定额 (18) 2.6.1确定各工序的加工余量 (18)2.6.2确定各工序的工序尺寸 (19)2.6.3确定各工序的切削用量 (20)2.6.4确定各工序的工时定额 (26)2.7确定各工序的工艺装备和机床的选择 (43)2.7.1刀具的选择 (43)2.7.2量具的选择: (44)2.7.3夹具的选择 (45)2.7.4机床设备的选择: (46)2.8选择定位基准的原则 (46)2.8.1粗基准的选择 (46)2.8.2精基准的选择 (47)2.9合理夹紧方法的确定 (48)2.9.1夹紧力的方向 (48)2.9.2夹紧力的作用点 (48)第3章夹具的设计 (50)3.1夹具设计的目的 (50)3.2所设计夹具的工序内容、工序所用的机床和刀具 (50)3.2.1 工序内容 (50)3.2.2 工序所用的机床和刀具 (51)3.3夹具设计满足的要求 (51)3.4定位基准及定位元件的选择 (51)3.5夹紧元件的选择 (52)3.6定位误差的计算 (53)3.6.1产生定位误差的原因 (53)3.6.2定位误差的计算 (53)3.7切削力及夹紧力计算 (55)结论 (57)致谢 (58)参考文献 (59)附录A (65)附录B (72)第1章零件的分析1.1减速器壳在汽车上的位置及功用汽车正常行驶时,发动机的转速通常在2000至3000r/min左右,如果将这么高的转速只靠变速箱来降低下来,那么变速箱内齿轮副的传动比则需很大,而齿轮副的传动比越大,两齿轮的半径比也越大,换句话说,也就是变速箱的尺寸会越大。
减速器壳体旋转钻夹具毕业设计

减速器壳体旋转钻夹具毕业设计目录绪论 (1)1 工作台方案设计 (3)1.1 回转体系统方案设计 (3)1.1.1 回转体系统原理及总体框图 (3)1.1.2 回转体系统传动系统方案 (3)1.1.3 回转体系统控制系统方案 (4)1.2 夹具体系统方案设计 (5)1.2.1 夹具体系统原理及总体框图 (5)1.2.2 夹具体系统传动系统方案 (5)1.2.3 夹具体系统控制系统方案 (6)2 工作台传动系统设计 (8)2.1 工作台设计 (8)2.1.1 回转体设计 (8)2.1.2 夹具体设计 (9)2.2 传动比及参数确定 (9)2.2.1 传动比设定 (9)2.2.2 步进电机最大回转速度及频率 (10)2.2.3 步进电机分度精度 (10)2.3 步进电机选择 (10)2.3.1 步进电机启动力矩计算 (11)2.3.2 步进电机最大转速 (12)2.3.3 步进电机最大频率 (12)2.3.4 步进电机型号 (12)2.4 气缸选择 (12)2.4.1 气缸输出力计算 (13)2.4.2 气缸行程 (13)2.4.3 气缸活塞速度 (14)2.4.4 气缸型号 (14)2.5 齿轮传动设计 (14)2.5.1 齿轮的材料及类型 (14)2.5.2 按齿面接触疲劳强度设计尺寸 (14)2.5.3 确定齿轮的主要参数与主要尺寸 (15)2.5.4 校核齿根弯曲疲劳强度 (16)2.6 蜗杆传动设计 (17)2.6.1 蜗杆传动类型 (18)2.6.2 蜗轮蜗杆的材料 (18)2.6.3 按齿面接触疲劳强度设计 (18)2.6.4 蜗轮蜗杆主要参数与几何尺寸 (19)2.6.5 校核齿根弯曲疲劳强度 (20)2.7 轴的设计 (21)2.7.1 轴1的设计 (21)2.7.3 轴2的设计 (22)2.7.3 主轴的设计 (22)2.7.4 蜗杆轴的设计 (22)2.8 键的选择 (23)2.8.1 键联接类型 (23)2.8.2 键连接的尺寸 (23)2.9 轴承的选择 (24)2.9.1 轴承的类型 (24)2.9.2 轴承的尺寸 (24)2.9.3 滚动轴承的密封装置 (25)3 工作台控制系统设计 (26)3.1 控制系统元器件选择 (26)3.1.1 单片机选择 (26)3.1.2 I/O接口芯片选择 (27)3.1.3 存储器选择 (28)3.1.4 译码器选择 (29)3.1.5 地址锁存器选择 (30)3.2 控制系统电路设计 (31)3.2.1 主控电路设计 (31)3.2.2 I/O接口电路设计 (31)结论 (33)附录 (34)参考文献 (42)致谢 (43)绪论中国数控分度回转工作台产业发展出现的问题中,许多情况不是很乐观,如产业结构的不合理、产业集中于劳动力密集型的产品;技术密集型的产品明显落后于发达工业的国家;生产要素决定性作用正在被削弱;产业能源消耗较大、产出率较低、环境污染较严重、对自然资源的破坏力大;企业总体规模又偏小、技术创新能力的薄弱、管理水平较落后等。
机械制造专业毕业论文--汽车后桥减速器粗镗夹具设计

摘要组合机床是随着生产力的发展,由万能机床和专用机床发展而来的。
具有较高的加工效率、加工精度及加工工艺性能,工序高度集中等特点。
机床夹具是机械制造中一项重要的工艺装备。
工件在机床上加工时,为保证加工精度和提高生产效率,必须使工件在机床上相对刀具占有正确的位置,为克服切削过程中工件受外力的作用而破坏定位,还必须对工件施夹紧力。
与之相对应的专用夹具的设计—是根据加工表面的具体情况,选择合理的定位方案、定位基准、定位误差的分析计算、工序公差的计算、定位销高度的计算、定位元件材料及机械性能的选用、确定刀具的对刀或引导方式包括:夹紧装置的设计(铰链四杆机构的设计、偏心轮夹紧机构的设计)、夹紧力的作用点和方向、夹紧力的分析和计算、铰链夹紧机构夹紧力的原动力的计算、夹紧元件及传动装置的设计(动力部分的设计和选择、传动装置系统主要参数的计算、控制部分的设计与选择、执行部分的设计与选择、辅助装置的设计与选择)、确定夹具其他组成部分的结构形式、确定夹具体的形式和夹具的总体结构(夹具体毛坯结构的选择、夹具体的排屑结构、夹具体结构尺寸的确定、夹具体的吊装装置的设计)。
关键词:夹具,定位,铰链四杆机构,液压,夹紧力ABSTRACTThe assembly engine bed is along with the productivity's development, and be developed by all-powerful engine bed and appropriation engine bed . It is a kind of high-efficiency special machine tool, which according to the process need of workplace, on the basis of a large number general parts equipped with a few special parts.The tool machine tongs is an important craft to equip in the machine manufacturing.The work piece at tool machine up process, process the accuracy and exaltations to produce the efficiency for the assurance, must make the work piece is on the tool machine the opposite knife has the position of the occupancy exactitude, for overcome to slice to pare the process in a function but the breakage fixed positions that is subjected to the outside dint, must still to a Clip the tight dint of work.In the multiple station vertical modular machine tool, which is used to drilling 12 holes of the components. I select the design of working-holding part, which includes the integral design of working-holding mechanism; the base part design of the working-holding mechanism and the design of hanging drilling template. The working-holding part is made up of the design of orientation schema; the selection of orientation module ; the mistaking analysis of orientation calculating ; the design of bulge-circle mechanism; the design of the four-pole mechanism and the calculating of the original power of the four-pole mechanism; the calculation of height dowel; the choice of the drilling set type, the calculating of the height of the drilling set type; the design and calculation of drilling accuracy ; the design of movable drilling the template; the design of the division control apparatus.KEY WORDS: The tongs, the fixed position,four pole organizations of pintle, the liquid press, Clip the tight dint目录前言 (1)第1章加工工件工艺 (2)§1.1加工工件 (2)§1.1.1工件的用途 (2)§1.1.2工件的毛坯制造方式 (2)§1.1.3工件的工艺分析 (2)§1.1.4工件定位基准的选择 (3)§1.2工件的定位方法和定位误差 (3)§1.2.2工件的定位误差及产生原因 (3)§1.2.3定位销的设计步骤 (4)§1.2.4设计定位销及分析定位误差 (5)§1.3加工工件应选用的机床类型及该机床的特点 (6)§1.3.1加工工件应选用的机床类型 (6)§1.3.2组合机床的特点 (6)第2章液压传动系统的设计与计算 (7)§2.1液压传动系统的设计步骤和内容 (7)§2.2明确液压系统的设计要求,进行负载特性分析 (7)§2.3 确定执行元件 (7)§2.4执行元件的工况分析及方案设计 (8)§2.5确定液压缸的主要参数 (10)§2.6选择液压元件 (12)§3.1 电动机的选择 (13)§3.2 液压集成块 (14)第4章专用夹具设计 (16)§4.1夹具及夹紧力的概念 (16)§4.2确定夹紧力时应当注意的几个问题 (17)§4.3计算切削力及切削合力作用的位置 (18)§4.4夹紧力的确定 (19)§4.5夹紧机构和夹紧动力机构的选择 (21)§4.5.1夹紧机构的选择 (21)§4.5.2夹紧动力机构的选择 (21)§4.5.3油缸的参数计算 (21)结论 (25)参考文献 (25)前言大学生活就要结束了,在过去的几年中,我们系统的学习了许多专业基础课和专业课,设计过机械机构、减速器、机床夹具等等。
减速器机体工艺规程及工装夹具设计说明书【优秀】

减速器机体工艺规程及工装夹具设计说明书【优秀】(文档可以直接使用,也可根据实际需要修订后使用,可编辑推荐下载)毕业设计(论文)说明书专业班次:姓名:毕业设计(论文)题目系(部)年级专业姓名设计(论文)题目:设计开始时间:年月日设计结束时间:年月日设计指导人:教研室主任:系主任:毕业设计(论文)评阅书题目:系(部)年级专业姓名评阅意见:成绩:指导教师:职务:年月日业设计(论文)答辩评定书年级专业班级:姓名:答辩过程记录员:成绩评定专业答辩组组长:年月日太毕业设计(论文)任务书第1页第2页第3页第4页目录摘要 (1)Abstract (2)绪论 (1)一、工艺部分 (2)(一)零件的分析 (2)1、零件的作用 (2)2、零件的工艺分析 (2)(二)工艺规程设计 (2)1、确定毛坯的制造形式 (2)2、基面的选择 (3)(三)制定工艺路线 (3)1、工艺路线方案一 (3)2、工艺路线方案二 (3)3、工艺方案的分析与比较 (4)(四)机械加工余量、工序尺寸及毛坯尺寸的确定 (5)1、机体结合面的尺寸公差及加工余量 (5)2、机体下底面的尺寸公差及加工余量 (5)3、各油孔端面的尺寸公差及加工余量 (5)4、8-Φ13孔的尺寸公差及加工余量 (6)5、齿轮孔端面的尺寸公差及加工余量 (6)6、齿轮孔的尺寸公差及加工余量 (6)(五)确定切削用量及基本工时 (6)二、夹具设计 (42)(一)钻床夹具设计 (43)1、问题的提出 (43)2、夹具设计 (43)参考文献 (46)结束语 (47)外文原文............................................. 错误!未定义书签。
中文翻译............................................. 错误!未定义书签。
致谢............................................... 错误!未定义书签。
- 1、下载文档前请自行甄别文档内容的完整性,平台不提供额外的编辑、内容补充、找答案等附加服务。
- 2、"仅部分预览"的文档,不可在线预览部分如存在完整性等问题,可反馈申请退款(可完整预览的文档不适用该条件!)。
- 3、如文档侵犯您的权益,请联系客服反馈,我们会尽快为您处理(人工客服工作时间:9:00-18:30)。
减速器壳体旋转钻夹具毕业设计目录绪论 (1)1 工作台方案设计 (3)1.1 回转体系统方案设计 (3)1.1.1 回转体系统原理及总体框图 (3)1.1.2 回转体系统传动系统方案 (3)1.1.3 回转体系统控制系统方案 (4)1.2 夹具体系统方案设计 (5)1.2.1 夹具体系统原理及总体框图 (5)1.2.2 夹具体系统传动系统方案 (5)1.2.3 夹具体系统控制系统方案 (6)2 工作台传动系统设计 (8)2.1 工作台设计 (8)2.1.1 回转体设计 (8)2.1.2 夹具体设计 (9)2.2 传动比及参数确定 (9)2.2.1 传动比设定 (9)2.2.2 步进电机最大回转速度及频率 (10)2.2.3 步进电机分度精度 (10)2.3 步进电机选择 (10)2.3.1 步进电机启动力矩计算 (11)2.3.2 步进电机最大转速 (12)2.3.3 步进电机最大频率 (12)2.3.4 步进电机型号 (12)2.4 气缸选择 (12)2.4.1 气缸输出力计算 (13)2.4.2 气缸行程 (13)2.4.3 气缸活塞速度 (14)2.4.4 气缸型号 (14)2.5 齿轮传动设计 (14)2.5.1 齿轮的材料及类型 (14)2.5.2 按齿面接触疲劳强度设计尺寸 (14)2.5.3 确定齿轮的主要参数与主要尺寸 (15)2.5.4 校核齿根弯曲疲劳强度 (16)2.6 蜗杆传动设计 (17)2.6.1 蜗杆传动类型 (18)2.6.2 蜗轮蜗杆的材料 (18)2.6.3 按齿面接触疲劳强度设计 (18)2.6.4 蜗轮蜗杆主要参数与几何尺寸 (19)2.6.5 校核齿根弯曲疲劳强度 (20)2.7 轴的设计 (21)2.7.1 轴1的设计 (21)2.7.3 轴2的设计 (22)2.7.3 主轴的设计 (22)2.7.4 蜗杆轴的设计 (22)2.8 键的选择 (23)2.8.1 键联接类型 (23)2.8.2 键连接的尺寸 (23)2.9 轴承的选择 (24)2.9.1 轴承的类型 (24)2.9.2 轴承的尺寸 (24)2.9.3 滚动轴承的密封装置 (25)3 工作台控制系统设计 (26)3.1 控制系统元器件选择 (26)3.1.1 单片机选择 (26)3.1.2 I/O接口芯片选择 (27)3.1.3 存储器选择 (28)3.1.4 译码器选择 (29)3.1.5 地址锁存器选择 (30)3.2 控制系统电路设计 (31)3.2.1 主控电路设计 (31)3.2.2 I/O接口电路设计 (31)结论 (33)附录 (34)参考文献 (42)致谢 (43)绪论中国数控分度回转工作台产业发展出现的问题中,许多情况不是很乐观,如产业结构的不合理、产业集中于劳动力密集型的产品;技术密集型的产品明显落后于发达工业的国家;生产要素决定性作用正在被削弱;产业能源消耗较大、产出率较低、环境污染较严重、对自然资源的破坏力大;企业总体规模又偏小、技术创新能力的薄弱、管理水平较落后等。
从什么角度分析中国数控分度回转工作台产业的发展状况?以什么方式评价中国数控分度回转工作台产业的发展程度?中国数控分度回转工作台产业的发展定位和前景是什么?中国数控分度回转工作台产业发展与当前经济热点问题关联度如何……诸如此类,都是数控分度回转工作台产业发展必须面对和解决的问题——中国数控分度回转工作台产业发展已到了岔口;中国数控分度回转工作台产业生产企业急需选择发展方向。
中国数控分度回转工作台产业发展研究报告阐述了世界数控分度回转工作台产业的发展过程,分析了中国数控分度回转工作台产业发展的现状和差距,开创性的提出了“新型数控分度回转工作台产业”及替代品产业的概念,在这基础上,从四个方面即“以人为本”、“创新科技”、“友好环境”和“面向未来”准确地限定了“新型数控分度回转工作台产业”及替代性产品的涵。
根据“新型数控分度回转工作台产业”及替代产品的评价体系和量化指标体系,从全新的角度对中国数控分度回转工作台产业发展进行了推演和精准预测,在此基础上,对中国的行政区划和四大都市圈的数控分度回转工作台产业发展进行了全面的研究。
60 年代以来,跨国公司推动的产业全球化发展使得国际分工和国际贸易格局发生了改变,加工贸易成为全球化产业发展的本质要求。
在全球化背景下,对于发展中国家而言,产业升级成为在全球化产业链条中由劳动密集环节向资本和技术密集环节逐步提升的过程。
由跨国公司推动的加工贸易的发展,为发展中国家切入全球高新技术产业链条,实现产业升级提供了便捷路径。
其中分度回转工作台的运用得到了广泛推广,各种新型工作台不断被引进,同时我国也自主研制和开发了一批适用、高效性的分度回转工作台。
本次设计的意义是设计出一套结构简单、实用性强、精度系数比较高的自动分度回转工作台,并能满足生产和加工的需要。
分度回转工作台作为数控机床中的一个非常大的部分,研究其设计、制造过程是非常有实际的工程应用价值。
数控工作台的应用非常多,而数控工作台像自动分度回转工作台的研究必然有着其实际的意义。
本次设计主要容包括:1.旋转钻夹具工作台总体方案设计;2.旋转钻夹具工作台传动系统设计;3.旋转钻夹具工作台控制系统设计;4.总装加工动画模拟。
1 工作台方案设计1.1 回转体系统方案设计旋转钻夹具回转体系统部分主要实现精确分度,保证加工质量,所以对这部分的设计是本次设计的核心,下面来介绍一下这部分主要容。
1.1.1 回转体系统原理及总体框图回转体系统工作原理是采用单片机控制步进电机带动回转体系统回转,通过键盘和显示屏幕发送指令给单片机,控制脉冲分配器向步进电机发送脉冲,步进电机直接带小齿轮,经过蜗轮蜗杆运动传动后,将回转体系统分度到设定好的角度。
自动回转分度主要由两部分组成,回转体系统传动系统部分和控制系统部分。
传动系统部分主要由步进电机、齿轮副传动和蜗杆传动组成;回转体系统控制系统部分主要由单片机、键盘显示屏、I/O接口芯片和驱动器组成。
回转体系统总体框图见图1-1。
图1-1 回转体系统总体框图1.1.2 回转体系统传动系统方案分度回转工作台主要用于数控钻床、镗床和铣床,其外形和通用工作台几乎一样,但它的驱动是伺服系统的驱动方式。
它可以与其他伺服进给轴联动。
整个传动系统由,步进电机、轴、齿轮副、蜗轮蜗杆和工作台组成。
图1-2为自动分度回转体系统。
它的回转、分度转位和定位锁紧都是由给定的指令进行控制的。
工作台的运动是由伺服电动机,经齿轮减速后由蜗轮蜗杆带动回转体系统回转分度。
图1-2自动分度回转体系统图1)回转体;2)工作台箱体;3)齿轮;4)工作台底座;5)蜗轮;6)步进电机;7)圆锥滚子轴承;8)蜗杆。
工作台回转分度工作时候,由控制系统发送指令给步进电机,步进电机带动齿轮副转动,再带动蜗轮轴回转,并由蜗轮带动工作台回转分度;工作台停止时,通过蜗轮蜗杆的自锁和步进电机的自锁保证工作台的自锁。
1.1.3 回转体系统控制系统方案回转体系统控制系统电路由单片机主控电路、I/O扩展电路、步进电机接口电路和键盘显示电路组成。
回转体系统控制系统元件主要单片机,外部RAM、ROM、I/O接口、光电隔离、功率放大、键盘、显示屏和驱动器等组成。
由键盘输入参数,通过I/O接口芯片到进行单片机处理,然后一面通过I/O芯片输出到显示屏,另一面输出通过光电隔离与功率放大到驱动器,再由驱动器驱动步进电机。
控制系统硬件结构如图1-3。
图 1-3 控制系统硬件结构图1.2 夹具体系统方案设计1.2.1 夹具体系统原理及总体框图夹具体系统工作原理是采用一面两销,手动控制偏心轮带动压板夹紧零件定位部位。
由于要加工成90°的两个方向上的端面孔位,所以采用换向阀控制双作用气缸进行前进和后退的状态,采用手动分度摆杆带动分度销控制90°分度盘的准确定位和锁紧。
夹具体系统主要由两部分组成,夹具体系统传动系统部分和控制系统部分。
传动系统部分主要由齿轮齿条副、分度销和分度盘组成;夹具体系统控制系统部分主要由换向阀、进气管、出气管和控制回路组成。
夹具体系统总体框图见图1-4。
图1-4 夹具体系统总体框图1.2.2 夹具体系统传动系统方案夹具体的使用可以说是相当广泛,而采用合适的传动和控制系统可以使夹具体的效率和使用率增加,生产成本降低。
整个传动系统由气缸、分度销、分度盘、齿轮齿条副、手动摆杆和卡盘组成。
图1-5为手控半自动夹具体系统。
它的回转由气缸带动齿轮齿条副控制,分度转位和定位锁紧则是由分度销和分度盘进行手动控制的。
图1-5 夹具体传动系统图1)卡盘1;2)分度盘;3)分度销;4)手动摆杆;5)换向阀;6)分度齿轮;7)卡盘2;8)齿条;9)气缸。
本夹具体系统在工作时,需先通过手动摆杆将分度销拔出来,再利用换向阀控制气缸前进和后退实现夹具体两个方向的转位控制,转位过程手动摆杆处于自由状态,便于转位后的分度定位和锁紧。
1.2.3 夹具体系统控制系统方案夹具体系统控制系统回路由二位五通换向阀、进气口、出气口、气缸和控制电路组成。
通过按下按钮开关,使气缸的活塞杆向前推进,并带动齿轮齿条副实现90°转位,松开按钮开关,气缸活塞杆回到气缸末端,使夹具体回到初始位置。
控制系统硬件结构如图1-6。
图 1-6 控制系统硬件结构图2 工作台传动系统设计2.1 工作台设计工作台的设计主要包括下箱体和夹具体的设计,在保证加工需要的前提下,尽量设计出结构紧凑的零部件是本次设计的宗旨。
2.1.1 箱体设计自动分度回转工作台箱体起着支承并含有各种传动的零件,像齿轮、轴承、轴等,使它们能能保持正常得运动精度及运动关系。
箱体又可以存储润滑剂,能实现各种类运动零部件的润滑。
安全保护与密封作用,并使箱体部的零件不会受外界的环境影响,又保护了机器操作者他们的人生安全,并含有一定得隔热、隔振和隔音的作用。
使机器的各部分又分别由独立的箱体组成,各组成单元,便于加工、装配、修理和调整。
改善机器造型,协调机器的各部分比例,使整机造型美观。
自动分度回转工作台主要用于镗床,铣床,钻床等需要多面转位加工的工件,是机械加工中常用的机床附件,因此尺寸不易过大,要能配合机床的使用。
考虑箱体零件的布置及与机床上的工件关系,设计尺寸如图2-1示:图2-1 工作台箱体尺寸图2.1.2 夹具体设计手控半自动夹具体主要由夹具体主体、夹紧元件、定位元件、传动元件和控制元件组成。
为了便与加工、装配、调整和修理,各元件独立生产加工。
由于需要多面加工,在保证夹具体工作精度的同时,还要具有可旋转性,为了配合箱体和回转体的安装,夹具体尺寸在保证容得下零件的同时,不宜过大。
综合考虑,设计尺寸如图2-2所示:图2-2 夹具体尺寸图2.2 传动比及参数确定2.2.1 传动比设定系统要实现的参数:工作台回转速度最大为60度/秒,工作台分度精度为0.2度。