注塑机工作原理及成型工艺 (1)
注塑机的工作原理

注塑机的工作原理
注塑机,是一种广泛应用于塑料制品生产的设备,它通过将塑料加热熔化后注
入模具中,经冷却后形成所需的塑料制品。
那么,注塑机的工作原理是怎样的呢?
首先,注塑机的工作原理可以分为以下几个步骤,加料、熔化、注射、冷却、
开模等。
在加料阶段,注塑机会将塑料颗粒或粉末加入到料斗中,然后通过螺杆推进装
置将塑料颗粒或粉末送入加热筒中。
接下来是熔化阶段,加热筒中的塑料颗粒或粉末会被加热螺杆加热,使其熔化
成液态塑料,然后通过螺杆的旋转将熔化的塑料向前推送。
随后是注射阶段,熔化的塑料会被注入到模具中,填充整个模腔,形成所需的
塑料制品的外形。
然后是冷却阶段,模具中的塑料会在一定的时间内进行冷却,使其固化成型。
最后是开模阶段,经过冷却固化的塑料制品会被取出模具,完成整个注塑成型
的过程。
在整个工作过程中,注塑机会通过控制系统对加热、注射、冷却等过程进行精
确控制,以确保塑料制品的质量和生产效率。
总的来说,注塑机的工作原理是通过加热熔化塑料,注射到模具中,经冷却固
化成型,最终取出塑料制品的整个过程。
这种工作原理使得注塑机成为塑料制品生产中不可或缺的设备,广泛应用于日常生活用品、工业制品、汽车零部件等领域。
通过了解注塑机的工作原理,我们可以更好地理解其在塑料制品生产中的作用,为生产过程的优化和改进提供更多的思路和可能性。
注塑工艺流程及原理【免费下载】

注塑工艺流程:注塑成型工艺过程主要包括填充——保压——冷却——脱模等四个阶段,这四个阶段直接决定着制品的成型质量,而且这四个阶段是一个完整的连续过程。
注塑机工作原理:在注塑机工作中,在螺杆旋转时,塑料对于机筒内壁,螺杆螺槽底面,螺棱推进面以及塑料与塑料之间在都会产生摩擦及相互运动。
塑料的向前推进就是这种运动组合的结果,而摩擦产生的热量也被吸收用来提高塑料温度及熔化塑料。
螺杆的设计结构将直接影响到这些作用的程度同时,螺杆的旋转使固体床和机筒内壁之间的熔膜产生剪切作用,从而使熔膜和固体床分界面间的固体熔化。
随着固体床的螺旋形向前推移,固体床的体积逐渐缩小,而熔池的体积逐渐增大。
如果固体床厚度减小的速度低于螺槽深度变浅的速度,则固体床就可能部分或完全堵塞螺槽,使塑化产生波动,或者由于局部压由于各种塑料的熔融速度,熔体粘度,熔融温度范围,粘度对温度及剪切速率的敏感程度,高温分解气体的腐蚀性,塑料颗粒间的摩擦系数差异很大。
一般螺杆式注塑机的成型工艺过程是:首先将粒状或粉状塑料加入机筒内,并通过螺杆的旋转和机筒外壁加热使塑料成为熔融状态,然后机器进行合模和注射座前移,接着向注射缸通人压力油。
使螺杆向前推进,从而以很高的压力和较快的速度将熔料注入温度较低的闭合模具内,经过一定时间和压力保持(又称保压)、冷却,使其固化成型,便可开模取出制品。
扩展资料:注塑成型的优缺点:1、优点:成形周期时间短、生产制造高效率、易完成自动化技术;能成型形状复杂、规格精准、含有金属材料或非金属材料镶件的塑胶制品;产品品质稳定;应用范围广泛。
2、缺点:注塑设备价格成本较高;注塑模具结构复杂;生产成本高、生产周期长、不适合于单件小批量的塑件生产。
注塑工艺的应用:在工业制品中,注射成型的制品有:厨房用具(垃圾桶、碗、塑料水桶、壶、厨具及其各种各样器皿),电气设备的机壳(电吹风、吸尘机、食品类搅拌装置等),小玩具与手机游戏,汽车产业的各种各样商品,其他很多商品的零件等。
注塑原理及成型工艺

注塑原理及成型工艺注塑是一种广泛应用于制造业的成型工艺,通过将熔化的塑料注入模具中,经过冷却固化形成所需的形状。
注塑成型工艺被广泛应用于塑料制品的生产,如塑料零件、容器、玩具等。
注塑的原理是利用注塑机将塑料原料加热熔化后,通过螺杆将熔化的塑料推入模具腔室中,经过冷却后得到所需的产品形状。
注塑机是注塑成型的核心设备,它由注射装置、锁模装置、压力调节系统、温度控制系统等部分组成。
在注塑成型工艺中,首先将塑料原料投入到注塑机的料斗中,通过螺杆转动将塑料原料推入加热筒中加热熔化。
加热筒中设置有加热器,通过加热器对塑料原料进行加热,使其熔化成熔融状态。
螺杆转动时,熔化的塑料被推入注射器中,注射器前端连接着模具。
接下来,注塑机通过液压系统将螺杆向前推送,将熔融状态的塑料注入模具腔室中。
模具腔室是根据产品的形状设计的,它通常由两个模具组成,上模和下模。
模具上有所需产品的空腔,当注射器将塑料注入模具腔室中后,模具迅速闭合,形成闭合的模具腔室。
在模具腔室中,熔融的塑料通过冷却系统进行快速冷却,使其固化成型。
冷却系统通常由冷却水或冷却油组成,通过循环流动的方式将热量带走,加速塑料的冷却固化过程。
冷却时间根据产品的要求进行控制,过短会导致产品未完全固化,过长则会延长生产周期。
当塑料完全冷却后,模具打开,成型的塑料制品从模具中取出。
取出的制品可以通过割台、取出机械手等方式进行。
割台通常用于切割产品与模具之间的连接部分,使产品与模具分离。
取出机械手则可以自动将产品从模具中取出,提高生产效率。
注塑成型工艺具有成本低、生产效率高、产品质量稳定等优点,因此被广泛应用于塑料制品生产领域。
注塑原理及成型工艺的掌握对于塑料制品的设计与生产至关重要,只有深入了解注塑原理,掌握成型工艺,才能生产出高质量、符合要求的塑料制品。
注塑机工艺流程注塑成型工艺过程详解
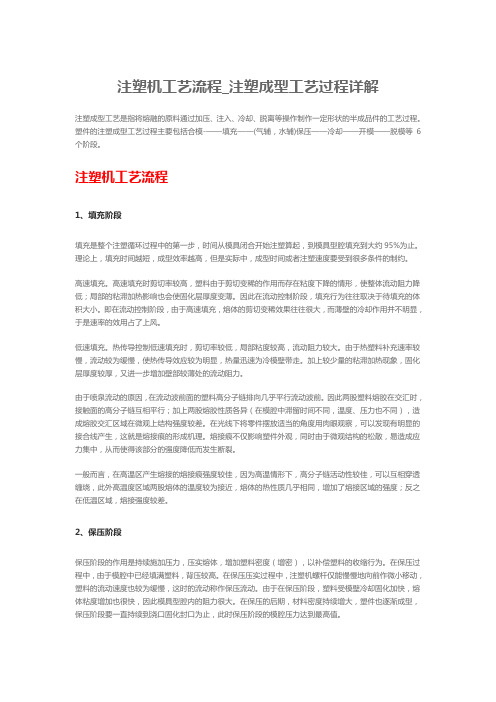
注塑机工艺流程_注塑成型工艺过程详解注塑成型工艺是指将熔融的原料通过加压、注入、冷却、脱离等操作制作一定形状的半成品件的工艺过程。
塑件的注塑成型工艺过程主要包括合模-——填充——(气辅,水辅)保压——冷却——开模——脱模等6个阶段。
注塑机工艺流程1、填充阶段填充是整个注塑循环过程中的第一步,时间从模具闭合开始注塑算起,到模具型腔填充到大约95%为止。
理论上,填充时间越短,成型效率越高,但是实际中,成型时间或者注塑速度要受到很多条件的制约。
高速填充。
高速填充时剪切率较高,塑料由于剪切变稀的作用而存在粘度下降的情形,使整体流动阻力降低;局部的粘滞加热影响也会使固化层厚度变薄。
因此在流动控制阶段,填充行为往往取决于待填充的体积大小。
即在流动控制阶段,由于高速填充,熔体的剪切变稀效果往往很大,而薄壁的冷却作用并不明显,于是速率的效用占了上风。
低速填充。
热传导控制低速填充时,剪切率较低,局部粘度较高,流动阻力较大。
由于热塑料补充速率较慢,流动较为缓慢,使热传导效应较为明显,热量迅速为冷模壁带走。
加上较少量的粘滞加热现象,固化层厚度较厚,又进一步增加壁部较薄处的流动阻力。
由于喷泉流动的原因,在流动波前面的塑料高分子链排向几乎平行流动波前。
因此两股塑料熔胶在交汇时,接触面的高分子链互相平行;加上两股熔胶性质各异(在模腔中滞留时间不同,温度、压力也不同),造成熔胶交汇区域在微观上结构强度较差。
在光线下将零件摆放适当的角度用肉眼观察,可以发现有明显的接合线产生,这就是熔接痕的形成机理。
熔接痕不仅影响塑件外观,同时由于微观结构的松散,易造成应力集中,从而使得该部分的强度降低而发生断裂。
一般而言,在高温区产生熔接的熔接痕强度较佳,因为高温情形下,高分子链活动性较佳,可以互相穿透缠绕,此外高温度区域两股熔体的温度较为接近,熔体的热性质几乎相同,增加了熔接区域的强度;反之在低温区域,熔接强度较差。
2、保压阶段保压阶段的作用是持续施加压力,压实熔体,增加塑料密度(增密),以补偿塑料的收缩行为。
[整理]成型机工作原理
![[整理]成型机工作原理](https://img.taocdn.com/s3/m/c879413b2bf90242a8956bec0975f46527d3a7df.png)
1、注塑成型机的工作原理注塑机的工作原理与打针用的注射器相似,它是借助螺杆(或柱塞)的推力,将已塑化好的熔融状态(即粘流态)的塑料注射入闭合好的模腔内,经固化定型后取得制品的工艺过程。
注射成型是一个循环的过程,每一周期主要包括:定量加料--熔融塑化--施压注射--充模冷却--启模取件。
取出塑件后又再闭模,进行下一个循环。
2、注塑机的结构注塑机根据塑化方式分为柱塞式注塑机和螺杆式注塑机,按机器的传动方式又可分为液压式、机械式和液压--机械(连杆)式,按操作方式分为自动、半自动、手动注塑机。
(1)卧式注塑机:这是最常见的类型。
其合模部分和注射部分处于同一水平中心线上,且模具是沿水平方向打开的。
其特点是:机身矮,易于操作和维修;机器重心低,安装较平稳;制品顶出后可利用重力作用自动落下,易于实现全自动操作。
目前,市场上的注塑机多采用此种型式。
(2)立式注塑机:其合模部分和注射部分处于同一垂直中心线上,且模具是沿垂直方向打开的。
因此,其占地面积较小,容易安放嵌件,装卸模具较方便,自料斗落入的物料能较均匀地进行塑化。
但制品顶出后不易自动落下,必须用手取下,不易实现自动操作。
立式注塑机宜用于小型注塑机,一般是在60克以下的注塑机采用较多,大、中型机不宜采用。
(3)角式注塑机:其注射方向和模具分界面在同一个面上,它特别适合于加工中心部分不允许留有浇口痕迹的平面制品。
它占地面积比卧式注塑机小,但放入模具内的嵌件容易倾斜落下。
这种型式的注塑机宜用于小机。
(4)多模转盘式注塑机:它是一种多工位操作的特殊注塑机,其特点是合模装置采用了转盘式结构,模具围绕转轴转动。
这种型式的注塑机充分发挥了注射装置的塑化能力,可以缩短生产周期,提高机器的生产能力,因而特别适合于冷却定型时间长或因安放嵌件而需要较多辅助时间的大批量制品的生产。
但因合模系统庞大、复杂,合模装置的合模力往往较小,故这种注塑机在塑胶鞋底等制品生产中应用较多。
一般注塑机包括注射装置、合模装置、液压系统和电气控制系统等部分。
注塑机原理及成型工艺

注塑机原理及成型工艺引言注塑机是一种常见的塑料加工设备,广泛应用于各个行业中的塑料制品生产。
本文将介绍注塑机的工作原理以及常见的成型工艺。
注塑机工作原理注塑机通过将熔融态的塑料注入到模具腔中,经过冷却和固化后得到所需的塑料制品。
注塑机主要由注射系统、保压系统、温控系统和液压系统组成。
注射系统注射系统是注塑机的核心部分,它负责将固态的塑料颗粒熔化并注入到模具腔中。
注射系统主要由注射缸、螺杆和喷嘴组成。
1.注射缸:注射缸是储存和加热塑料颗粒的容器。
当注射缸内的塑料颗粒被加热至熔融态时,就可以进行注射。
2.螺杆:螺杆是注射缸中的主要元件,负责将熔融态的塑料颗粒推送到喷嘴中。
螺杆通常由螺杆杆身和螺纹组成,通过旋转推动塑料颗粒的移动。
3.喷嘴:喷嘴是连接注射缸和模具的通道,具有开关功能。
当塑料颗粒被推送到喷嘴时,喷嘴关闭,防止塑料回流。
当喷嘴打开时,塑料颗粒就可以注入到模具腔中。
保压系统保压系统负责在注塑过程中对塑料制品进行压力保持,以使其在冷却和固化过程中保持形状和尺寸稳定。
保压系统主要由保压缸和保压阀组成。
1.保压缸:保压缸是储存和施加压力的容器。
当塑料注入到模具腔中后,保压缸施加压力,使塑料充分填满腔体,并保持压力,以保证塑料制品的完整性。
2.保压阀:保压阀用于控制保压缸的压力大小和保持时间。
根据不同的塑料材料和制品要求,可以调整保压阀的参数。
温控系统温控系统是注塑机的控制系统,负责控制注射缸和保压缸内的温度。
良好的温度控制可以确保塑料的熔融和冷却过程顺利进行。
液压系统液压系统是注塑机的动力系统,通过液压传动提供所需的力和速度。
液压系统主要由液压泵、液压缸和液压阀组成。
1.液压泵:液压泵负责为注射、保压和开模等过程提供所需的液压力。
液压泵会将液压油从油箱中抽取,并通过管道传递到不同的液压马达和液压缸中。
2.液压缸:液压缸是液压系统的执行元件,负责产生所需的动力和运动。
液压缸的活塞可以通过液压力对注射系统、保压系统和开模系统进行控制。
注塑机工作原理及工艺

注塑机工作原理及工艺以下从五个方面分析了注塑机的工作原理及工艺:1、注塑机的工作原理:与打针用的注射器相像,它是借助螺杆(或柱塞)的推力,将已塑化好的熔融状态(即粘流态)的塑料注射入闭合好的模腔内,经固化定型后取得制品的工艺过程。
2、注射成型是一个循环的过程,每一周期重要包括:定量加料熔融塑化施压注射充模冷却启模取件。
取出塑件后又再闭模,进行下一个循环。
3、注塑机操作项目:注塑机操作项目包括掌控键盘操作、电器掌控系统操作和液压系统操作三个方面。
分别进行注射过程动作、加料动作、注射压力、注射速度、顶出型式的选择,料筒各段温度的监控,注射压力和背压压力的调整等。
4、一般螺杆式注塑机的成型工艺过程是:首先将粒状或粉状塑料加入机筒内,并通过螺杆的旋转和机筒外壁加热使塑料成为熔融状态,然后机器进行合模和注射座前移,使喷嘴贴紧模具的浇口道,接着向注射缸通人压力油,使螺杆向前推动,从而以很高的压力和较快的速度将熔料注入温度较低的闭合模具内,经过肯定时间和压力保持(又称保压)、冷却,使其固化成型,便可开模取出制品(保压的目的是防止模腔中熔料的反流、向模腔内补充物料,以及保证制品具有肯定的密度和尺寸公差)。
注射成型的基本要求是塑化、注射和成型。
塑化是实现和保证成型制品质量的前提,而为充足成型的要求,注射必需保证有充足的压力和速度。
同时,由于注射压力很高,相应地在模腔中产生很高的压力(模腔内的平均压力一般在20~45MPa之间),因此必需有充足大的合模力。
由此可见,注射装置和合模装置是注塑机的关键部件。
5、对塑料制品的评价重要有三个方面:*是外观质量,包括完整性、颜色、光泽等;第二是尺寸和相对位置间的精准性;第三是与用途相应的物理性能、化学性能、电性能等。
这些质量要求又依据制品使用场合的不同,要求的尺度也不同。
制品的缺陷重要在于模具的设计、制造精度和磨损程度等方面。
但事实上,塑料加工厂的技术人员往往苦于面对用工艺手段来弥补模具缺陷带来的问题而成效不大的困难局面。
注塑原理及成型工艺
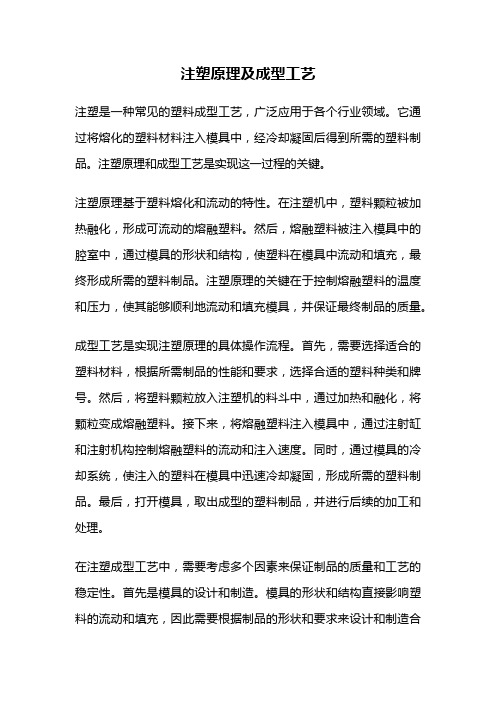
注塑原理及成型工艺注塑是一种常见的塑料成型工艺,广泛应用于各个行业领域。
它通过将熔化的塑料材料注入模具中,经冷却凝固后得到所需的塑料制品。
注塑原理和成型工艺是实现这一过程的关键。
注塑原理基于塑料熔化和流动的特性。
在注塑机中,塑料颗粒被加热融化,形成可流动的熔融塑料。
然后,熔融塑料被注入模具中的腔室中,通过模具的形状和结构,使塑料在模具中流动和填充,最终形成所需的塑料制品。
注塑原理的关键在于控制熔融塑料的温度和压力,使其能够顺利地流动和填充模具,并保证最终制品的质量。
成型工艺是实现注塑原理的具体操作流程。
首先,需要选择适合的塑料材料,根据所需制品的性能和要求,选择合适的塑料种类和牌号。
然后,将塑料颗粒放入注塑机的料斗中,通过加热和融化,将颗粒变成熔融塑料。
接下来,将熔融塑料注入模具中,通过注射缸和注射机构控制熔融塑料的流动和注入速度。
同时,通过模具的冷却系统,使注入的塑料在模具中迅速冷却凝固,形成所需的塑料制品。
最后,打开模具,取出成型的塑料制品,并进行后续的加工和处理。
在注塑成型工艺中,需要考虑多个因素来保证制品的质量和工艺的稳定性。
首先是模具的设计和制造。
模具的形状和结构直接影响塑料的流动和填充,因此需要根据制品的形状和要求来设计和制造合适的模具。
其次是注塑机的选择和调试。
注塑机的性能和参数会影响熔融塑料的温度、压力和流动速度,因此需要根据制品的要求选择合适的注塑机,并进行调试和优化。
另外,还需要控制注塑过程中的温度、压力和速度等参数,以保证制品的尺寸精度和表面质量。
此外,还需要进行质量检测和控制,及时发现和解决制品的缺陷和问题。
注塑原理和成型工艺的应用非常广泛,几乎涵盖了所有塑料制品的生产。
例如,家电、汽车、电子、玩具、包装等行业都需要使用注塑成型工艺来制造各种塑料制品。
注塑工艺具有成本低、生产效率高、制品尺寸精度高等优点,成为了塑料制品生产的主要工艺之一。
注塑原理和成型工艺是塑料制品生产中的重要环节。
注塑机工作原理及成型工艺

05
产品质量控制与检验标准解读
产品质量控制方法论述
原材料控制
严格筛选原材料,确保符合质量要求,避免 因原材料问题影响产品质量。
工艺参数控制
精确控制注塑机工艺参数,如温度、压力、 时间等,确保产品尺寸、性能稳定。
设备维护与保养
定期对注塑机进行维护和保养,确保设备处 于良好状态,提高产品质量稳定性。
注射过程
塑料在注塑机中加热、熔化,然后通过注射 螺杆注入模具型腔。
冷却过程
塑料在模具中冷却定型,然后开模取出制品 。
成型工艺特点分析
适应性强
注塑成型可以生产各种形状和尺的 塑料制品,满足不同需求。
生产效率高
注塑机可以连续生产,提高生产效率 。
制品质量稳定
通过精确控制注射参数和模具温度, 可以获得高质量的塑料制品。
在生产过程中,需要根据实际情况对以上 参数进行调整和优化,以获得最佳的生产 效果。
04
注塑机操作与维护保养规范
注塑机操作规程及注意事项
操作前准备
检查设备是否完好,确认模具安 装牢固,检查原料是否符合要求
。
操作规程
按照生产工艺要求,依次输入参数 ,启动注塑机进行生产。
注意事项
操作过程中要保持专注,注意安全 ,避免发生意外。
顶出装置
通过液压缸或气缸实现制品的 顶出动作。
液压系统
提供注射、保压、合模、顶出 等动作所需的液压动力。
电气控制系统
控制注塑机的各种动作和工艺 参数,实现自动化生产。
03
成型工艺流程及特点
成型工艺流程介绍
注塑前的准备
包括原材料的预处理、模具的安装和调试等 。
保压过程
注射完成后,模具型腔内的塑料在压力作用 下保持形状稳定。
注塑机工作原理

注塑机工作原理标题:注塑机工作原理引言概述:注塑机是一种常见的塑料加工设备,广泛应用于汽车、电子、家电等行业。
它通过将塑料粒子加热融化,然后注入模具中进行成型,是制造塑料制品的重要工具。
本文将详细介绍注塑机的工作原理。
一、加热和融化塑料粒子1.1 控制加热温度:注塑机通过加热筒将塑料粒子加热至一定温度,以使其融化。
加热温度通常根据不同的塑料材料而有所不同。
1.2 保持压力和时间:在加热过程中,需要保持一定的压力和时间,以确保塑料粒子充分融化并达到所需的流动性。
1.3 控制熔体温度:注塑机还需要控制熔体的温度,以确保其在注射过程中能够保持一定的流动性和粘度。
二、注射和充填模具2.1 注射动作:一旦塑料粒子融化并达到所需的熔体状态,注塑机会通过注射缸将熔体注入模具中。
注射动作需要精确控制注射速度和压力。
2.2 充填模具:在注射过程中,熔体会充满整个模具腔,填充模具的每一个细节和空隙,确保成型制品的完整性和精度。
2.3 冷却和固化:一旦模具中的熔体充填完毕,需要进行冷却和固化,以确保成型制品能够保持所需的形状和尺寸。
三、开模和脱模3.1 开模动作:在成型制品冷却固化后,注塑机会进行开模动作,将模具分开,使成型制品脱离模具。
3.2 脱模处理:脱模过程需要谨慎进行,以避免成型制品受损。
通常会采用气体喷射或模具抽真空等方式辅助脱模。
3.3 检查和修整:脱模后,需要对成型制品进行检查和修整,确保其质量和外观符合要求。
四、循环回收利用4.1 废料回收:在注塑过程中产生的废料可以进行回收利用,减少资源浪费和环境污染。
4.2 冷却水回收:注塑机在工作过程中会产生大量热量,需要通过冷却水循环系统进行散热,可以将冷却水进行循环利用。
4.3 节能环保:注塑机在工作原理中注重节能环保,采用高效的加热和冷却系统,减少能源消耗和排放。
五、自动化控制和监控5.1 PLC控制系统:现代注塑机通常配备了PLC控制系统,可以实现自动化控制和监控,提高生产效率和产品质量。
注塑机结构及工作原理

注塑机结构及工作原理一、注塑机的工作原理注塑成型机简称注塑机。
注塑成型是利用塑料的热物理性质,把物料从料斗加入料筒中,料筒外由加热圈加热,使物料熔融,在料筒内装有在外动力马达作用下驱动旋转的螺杆,物料在螺杆的作用下,沿着螺槽向前输送并压实,物料在外加热和螺杆剪切的双重作用下逐渐地塑化,熔融和均化,当螺杆旋转时,物料在螺槽摩擦力及剪切力的作用下,把已熔融的物料推到螺杆的头部,与此同时,螺杆在物料的反作用下后退,使螺杆头部形成储料空间,完成塑化过程,然后,螺杆在注射油缸的活塞推力的作用下,以高速、高压,将储料室内的熔融料通过喷嘴注射到模具的型腔中,型腔中的熔料经过保压、冷却、固化定型后,模具在合模机构的作用下,开启模具,并通过顶出装置把定型好的制品从模具顶出落下。
注塑机作业循环流程如图1所示。
图1 注塑机工作程序框图二、注塑机的分类按合模部件与注射部件配置的型式有卧式、立式、角式三种(1)卧式注塑机:卧式注塑机是最常用的类型。
其特点是注射总成的中心线与合模总成的中心线同心或一致,并平行于安装地面。
它的优点是重心低、工作平稳、模具安装、操作及维修均较方便,模具开档大,占用空间高度小;但占地面积大,大、中、小型机均有广泛应用。
(2)立式注塑机:其特点是合模装置与注射装置的轴线呈一线排列而且与地面垂直。
具有占地面积小,模具装拆方便,嵌件安装容易,自料斗落入物料能较均匀地进行塑化,易实现自动化及多台机自动线管理等优点。
缺点是顶出制品不易自动脱落,常需人工或其它方法取出,不易实现全自动化操作和大型制品注射;机身高,加料、维修不便。
(3)角式注塑机:注射装置和合模装置的轴线互成垂直排列。
根据注射总成中心线与安装基面的相对位置有卧立式、立卧式、平卧式之分:①卧立式,注射总成线与基面平行,而合模总成中心线与基面垂直;②立卧式,注射总成中心线与基面垂直,而合模总成中心线与基面平行。
角式注射机的优点是兼备有卧式与立式注射机的优点,特别适用于开设侧浇口非对称几何形状制品的模具。
注塑成型机工作原理
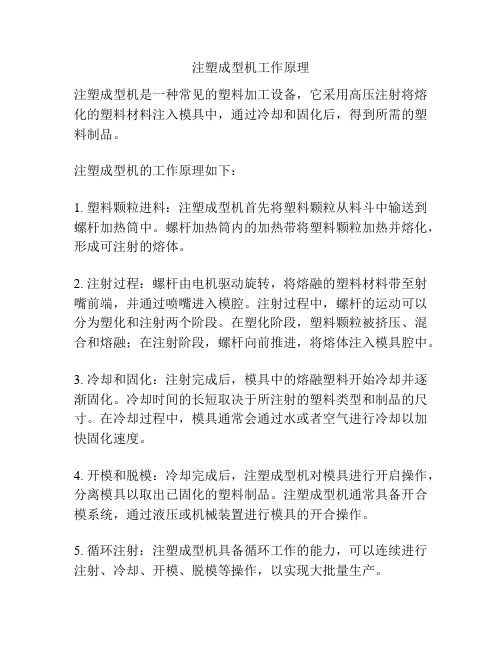
注塑成型机工作原理
注塑成型机是一种常见的塑料加工设备,它采用高压注射将熔化的塑料材料注入模具中,通过冷却和固化后,得到所需的塑料制品。
注塑成型机的工作原理如下:
1. 塑料颗粒进料:注塑成型机首先将塑料颗粒从料斗中输送到螺杆加热筒中。
螺杆加热筒内的加热带将塑料颗粒加热并熔化,形成可注射的熔体。
2. 注射过程:螺杆由电机驱动旋转,将熔融的塑料材料带至射嘴前端,并通过喷嘴进入模腔。
注射过程中,螺杆的运动可以分为塑化和注射两个阶段。
在塑化阶段,塑料颗粒被挤压、混合和熔融;在注射阶段,螺杆向前推进,将熔体注入模具腔中。
3. 冷却和固化:注射完成后,模具中的熔融塑料开始冷却并逐渐固化。
冷却时间的长短取决于所注射的塑料类型和制品的尺寸。
在冷却过程中,模具通常会通过水或者空气进行冷却以加快固化速度。
4. 开模和脱模:冷却完成后,注塑成型机对模具进行开启操作,分离模具以取出已固化的塑料制品。
注塑成型机通常具备开合模系统,通过液压或机械装置进行模具的开合操作。
5. 循环注射:注塑成型机具备循环工作的能力,可以连续进行注射、冷却、开模、脱模等操作,以实现大批量生产。
通过上述工作原理,注塑成型机可以制造出各种形状和尺寸的塑料制品,广泛应用于日常生活和工业领域中。
塑胶注塑工艺(3篇)
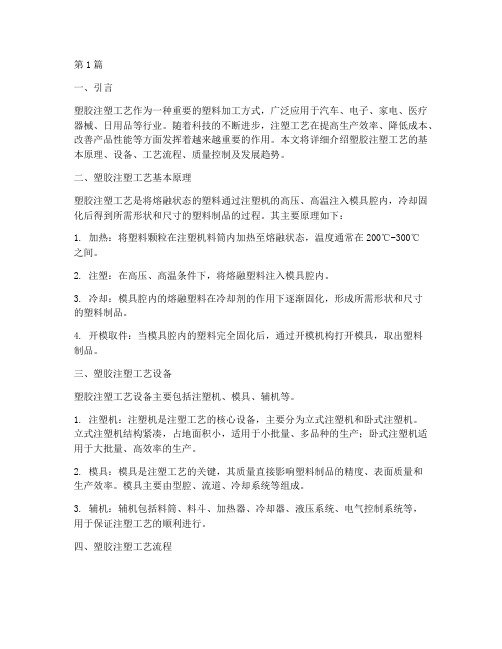
第1篇一、引言塑胶注塑工艺作为一种重要的塑料加工方式,广泛应用于汽车、电子、家电、医疗器械、日用品等行业。
随着科技的不断进步,注塑工艺在提高生产效率、降低成本、改善产品性能等方面发挥着越来越重要的作用。
本文将详细介绍塑胶注塑工艺的基本原理、设备、工艺流程、质量控制及发展趋势。
二、塑胶注塑工艺基本原理塑胶注塑工艺是将熔融状态的塑料通过注塑机的高压、高温注入模具腔内,冷却固化后得到所需形状和尺寸的塑料制品的过程。
其主要原理如下:1. 加热:将塑料颗粒在注塑机料筒内加热至熔融状态,温度通常在200℃-300℃之间。
2. 注塑:在高压、高温条件下,将熔融塑料注入模具腔内。
3. 冷却:模具腔内的熔融塑料在冷却剂的作用下逐渐固化,形成所需形状和尺寸的塑料制品。
4. 开模取件:当模具腔内的塑料完全固化后,通过开模机构打开模具,取出塑料制品。
三、塑胶注塑工艺设备塑胶注塑工艺设备主要包括注塑机、模具、辅机等。
1. 注塑机:注塑机是注塑工艺的核心设备,主要分为立式注塑机和卧式注塑机。
立式注塑机结构紧凑,占地面积小,适用于小批量、多品种的生产;卧式注塑机适用于大批量、高效率的生产。
2. 模具:模具是注塑工艺的关键,其质量直接影响塑料制品的精度、表面质量和生产效率。
模具主要由型腔、流道、冷却系统等组成。
3. 辅机:辅机包括料筒、料斗、加热器、冷却器、液压系统、电气控制系统等,用于保证注塑工艺的顺利进行。
四、塑胶注塑工艺流程1. 塑料原料准备:根据产品要求,选择合适的塑料原料,进行干燥、计量等预处理。
2. 加热:将塑料原料在注塑机料筒内加热至熔融状态。
3. 注塑:在高压、高温条件下,将熔融塑料注入模具腔内。
4. 冷却:模具腔内的熔融塑料在冷却剂的作用下逐渐固化。
5. 开模取件:当模具腔内的塑料完全固化后,通过开模机构打开模具,取出塑料制品。
6. 后处理:对塑料制品进行检验、清洗、去毛刺、热处理等后处理工序。
五、塑胶注塑工艺质量控制1. 原料质量控制:选用符合标准的塑料原料,确保产品质量。
注塑工艺分析(3篇)

第1篇一、引言注塑工艺作为一种重要的成型方法,广泛应用于塑料工业、汽车制造、电子电器、包装材料等领域。
注塑工艺是将熔融的塑料注入模具,经过冷却、固化后形成所需的塑料制品。
本文将从注塑工艺的基本原理、流程、影响因素、常见问题及解决方案等方面进行详细分析。
二、注塑工艺的基本原理注塑工艺的基本原理是将塑料原料在高温、高压的条件下熔化,然后通过注塑机将熔融塑料注入模具,使塑料在模具中冷却、固化,从而形成所需的塑料制品。
注塑工艺主要包括以下几个步骤:1. 塑料原料的熔融:将塑料原料加热至熔融状态,使其具有流动性。
2. 注塑:将熔融塑料注入模具,通过模具的形状和尺寸来控制塑料制品的形状。
3. 冷却、固化:塑料在模具中冷却、固化,形成所需的塑料制品。
4. 取件:将冷却固化后的塑料制品从模具中取出。
三、注塑工艺流程注塑工艺流程主要包括以下步骤:1. 塑料原料的准备:选择合适的塑料原料,进行称重、配料。
2. 加热熔融:将塑料原料加热至熔融状态。
3. 注塑:将熔融塑料注入模具。
4. 冷却、固化:在模具中冷却、固化,形成所需的塑料制品。
5. 取件:将冷却固化后的塑料制品从模具中取出。
6. 后处理:对塑料制品进行检验、修整、包装等。
四、注塑工艺的影响因素1. 塑料原料:塑料原料的种类、质量、性能等对注塑工艺和塑料制品的质量有重要影响。
2. 注塑机:注塑机的类型、规格、性能等对注塑工艺和塑料制品的质量有直接影响。
3. 模具:模具的形状、尺寸、精度、冷却系统等对注塑工艺和塑料制品的质量有重要影响。
4. 注塑参数:注塑温度、压力、速度、时间等参数对注塑工艺和塑料制品的质量有直接影响。
5. 环境因素:温度、湿度、气压等环境因素对注塑工艺和塑料制品的质量有影响。
五、注塑工艺的常见问题及解决方案1. 塑料制品变形:原因可能是模具设计不合理、注塑参数设置不当等。
解决方案:优化模具设计,调整注塑参数。
2. 塑料制品表面缺陷:原因可能是模具表面粗糙、注塑温度过高、塑料原料质量差等。
注塑机原理及工艺流程简单易懂
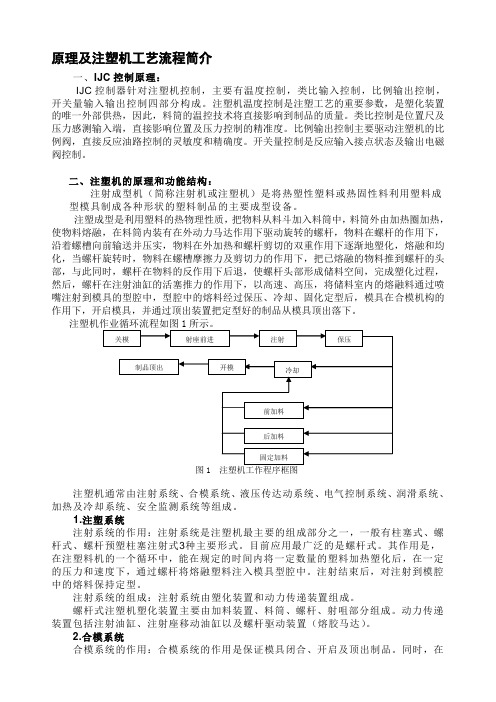
原理及注塑机工艺流程简介一、IJC控制原理:IJC控制器针对注塑机控制,主要有温度控制,类比输入控制,比例输出控制,开关量输入输出控制四部分构成。
注塑机温度控制是注塑工艺的重要参数,是塑化装置的唯一外部供热,因此,料筒的温控技术将直接影响到制品的质量。
类比控制是位置尺及压力感测输入端,直接影响位置及压力控制的精准度。
比例输出控制主要驱动注塑机的比例阀,直接反应油路控制的灵敏度和精确度。
开关量控制是反应输入接点状态及输出电磁阀控制。
二、注塑机的原理和功能结构:注射成型机(简称注射机或注塑机)是将热塑性塑料或热固性料利用塑料成型模具制成各种形状的塑料制品的主要成型设备。
注塑成型是利用塑料的热物理性质,把物料从料斗加入料筒中,料筒外由加热圈加热,使物料熔融,在料筒内装有在外动力马达作用下驱动旋转的螺杆,物料在螺杆的作用下,沿着螺槽向前输送并压实,物料在外加热和螺杆剪切的双重作用下逐渐地塑化,熔融和均化,当螺杆旋转时,物料在螺槽摩擦力及剪切力的作用下,把已熔融的物料推到螺杆的头部,与此同时,螺杆在物料的反作用下后退,使螺杆头部形成储料空间,完成塑化过程,然后,螺杆在注射油缸的活塞推力的作用下,以高速、高压,将储料室内的熔融料通过喷嘴注射到模具的型腔中,型腔中的熔料经过保压、冷却、固化定型后,模具在合模机构的作用下,开启模具,并通过顶出装置把定型好的制品从模具顶出落下。
注塑机通常由注射系统、合模系统、液压传达动系统、电气控制系统、润滑系统、加热及冷却系统、安全监测系统等组成。
1.注塑系统注射系统的作用:注射系统是注塑机最主要的组成部分之一,一般有柱塞式、螺杆式、螺杆预塑柱塞注射式3种主要形式。
目前应用最广泛的是螺杆式。
其作用是,在注塑料机的一个循环中,能在规定的时间内将一定数量的塑料加热塑化后,在一定的压力和速度下,通过螺杆将熔融塑料注入模具型腔中。
注射结束后,对注射到模腔中的熔料保持定型。
注射系统的组成:注射系统由塑化装置和动力传递装置组成。
注塑机原理及成型工艺
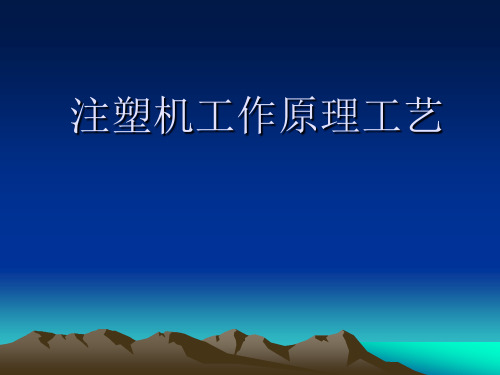
√
部位
保养内容
周 月 年
6氮气系统
蓄压器 7机器润滑 检查氮气,必要时补充 HLP-68 ISO VG68 VI≧25.4 6升 √
中央润滑
油脂润滑 DIN51825
检查油位必要时添加
润滑注射装置的杆
√
√
目检润滑点的连接
√
部位
8电器设备
保养内容
周 月 年
√ √
控制柜区域 检查螺旋接头,必要时上 1 紧 控制柜2、3、检查风扇 4 编程控制台 检查风扇 更换过滤垫 驱动装置 清洁电动机
必要时更换
√
√
干燥机过滤器、 清洁回收料斗 回收料斗
除湿机
冷水机
8、底部凹凸:减小填充压力、减小注射时 间。 9、底部拉丝:降低喷嘴温度、增加注射时 间、提高填充压力、提高开模速度、增 加冷却时间、检查料的干燥状况、增加 延迟关闭时间、 10、底部小孔:降低喷嘴温度、增加填充 压力、增加注射时间、增加冷却时间、 减小注射速度、检查干燥情况、减小延 迟关闭时间。
√ √ √
√ √ √ √ √ √
部位
9脱模装置、冷却站 导轨、齿带 连接/拉紧套件、电 动机和传动装置 水平导轨 真空的产生
保养内容
周 月 年
清洁、上油 目检、维护、必要 时更换 清洁、上油 真空泵维护 √
√ √
√
部位 11其他 料斗、料斗磁 铁 回收油箱
保养内容
周 月 年
清洁 排空
√ √
除湿机过滤网
保养内容 目检必要时拧紧
周 √
月
年
检查油位必要时添加 /油路是否漏油 检查油质,如果不正 常更换油和所有油过 滤器
√
部位 5冷却系统和压 缩空气系统 冷却系统