300万吨年直馏柴油加氢精制装置简介解析
柴油加氢精制装置分馏流程比较

2 0 1 3年 5月
第4 2卷第 5期
当
代
化
工
C o n t e mp o r a r y C h e mi c a l I n d u s t r y
V o 1 . 4 2. N 0 . 5 M a y, 2 01 3
柴油加氢精 制装 置分馏 流程 比较
Ab s t r a c t :Hy d r o t r e a t i n g u n i t s o f mi x e d d i e s e l wi t h f e we r LCO h a v e f e we r r e a c t i o n h e a t r e l e a s e a n d l o we r r e a c t i o n
q ua l i t y, l o w i n ve s t a n d S O on.
直馏柴油加氢装置掺炼催化柴油的技术改进
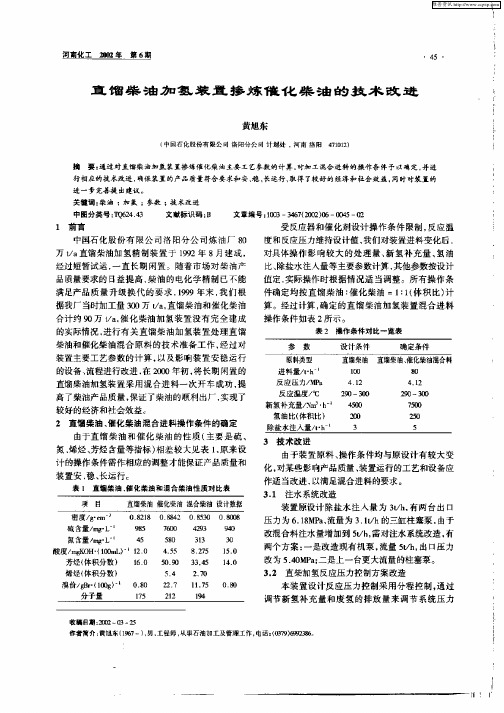
据我厂当时加工量 30 0 万 a直馏柴油和催化柴油 , 合计约 9 万 a催 化柴油加氢装置没有完全建成 0 , 的实 际情 况 , 进行 有 关 直馏 柴油 加氢 装 置处 理直 馏 柴油和催化柴油混合原料的技术准备工作, 经过对
算。经过计算 , 确定的直馏柴油加氢装置混合进料 操作条件如表 2 所示。 表2 操作条件对比一览表 参 数 设 计条 件
1 0 0
确定条 件
装置主要工艺参数的计算, 以及影响装置安稳运行
的设备 、 流程进行改 进 , 20 在 00年初 , 长期 闲置 的 将
——
面———
溴价 g ‘ 0 ) B ( 0 r1g
08 . 2 7 1. 08 0 2 15 7 - 0
本装置设计反应压力控制采用分程控制 2 ( 0 —2 /
!
调节 新氢补充量和废氢的排放量来调节系统压力
作者简介 : 黄旭东( 6 一 , 工程师 . 1 7 ) 男, 9 从事石油加工及管理工作 . 电话 : 3969 3 。 ( 7 ) ". 0 9zm
维普资讯
河 南化 工
抛
年
第 6期
直 馏 柴 油 加 氢 装 置 掺 炼 催 化 柴 油 的 技 术 改 进
黄旭东
( 中国石化股份有 限公司 洛阳分公 司 计划处 , 河南 洛阳 4 11) 702
摘
要: 通过对直馏柴 油加氢装 置掺炼催化 柴油主要 工艺参数的计算 , 对加工混合进料的操作条件 子烈璃定 , 井进
“ 边收边 放” 的方法 ; 为保证 反应 压力控 制平稳 , 调节 及时 , 分程控制 为单 回路 控制 ( 图 2 , 改 见 )将更 加灵
加氢装置介绍

加氢裂化装置原理、流程及特点
加氢裂化是将大分子的重质油转化为广泛使用的小分子 的轻质油的一种加工手段。可加工直馏柴油、催化裂化循环 油、焦化馏出油,也可用脱沥青重残油生产汽油、航煤和低 凝固点柴油。加氢裂化装臵是炼油厂最重要的的生产装臵之 一,在高温、高压、临氢状态下操作。 加氢裂化装臵的工艺流程主要有三种类型方法: ⑴ 一次通过法:所产尾油不参加循环。 ⑵ 部分循环法:所产尾油一部分参加循环,一部分排出 装臵。 ⑶ 全部循环法:所产尾油全部参加循环,不排尾油。 加氢裂化装臵主要设备有加氢精制反应器、加氢裂化反 应器、加热炉、高压热交换器、高压空冷器、高、低压分离 器、高温高压临氢管道、高温阀门等。详见图1、图2、图3、 图4。
2013-8-17 12
H1
H2
H3
凸台
H4
H5
s-k H6
1
图5
2013-8-17
热壁加氢反应器
13
加氢裂化装置常用材料
设备名称
加氢精制、裂化反应器 (设计温度≤ 450 ℃/设 计压力8~20MPa) 高压热交换器(温度≤ 260 ℃)
选用材质
板2.25Cr-1Mo(SA387Gr22CL2) +6.5mm(Tp309+347) 堆焊层 或+4mm(TP347)单层浅熔深堆焊 锻2.25Cr-1Mo(SA336F22CL2) + 6.5mm(Tp309+347) 堆焊层或+4mm(TP347)单层浅熔深堆焊 管程:反应流出物:管箱(碳钢、碳钼钢+4~6mm CA;铬钼钢+3mm CA)管板(碳钢、碳钼钢、铬钼钢 + 8mmTP309+347) 壳程:循环氢、原料:壳体(碳钢、碳钼钢、铬钼 钢+ 3mm CA) 管程:反应流出物:管箱(铬钼钢+3mm 1Cr18Ni9Ti 复合板 或 +6.5mm Tp309+347堆焊层 或 +4mmTP347) 管板(铬钼钢+8mmTP309+347或铬 钼钢+8mmTP410) 壳程:循环氢、原料:壳体(铬钼钢+4mm CA;或 +3mm 1Cr18Ni9Ti 复合板;或+4mmTP347;或 +6.5mm Tp309+347堆焊层) 14
柴油加氢装置
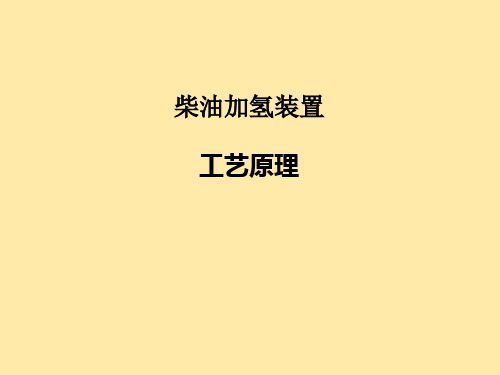
精制反应器内发生的反应
含硫有机物
催化剂
H2
烃类
含氮有机物
H2
催化剂
烃类
含氧有机物
H2
催化剂
烃类
金属有机物
H2
催化剂
烃类
烯烃
催化剂
H2
烷烃
H2S NH3 H2O 金属单质
与重整精制反应不同有:烃类碳数不同,杂质含量不同。 与重整精制反应相同有:均为放热反应,体积缩小反应。
低 分 罐
精制油去分馏塔 污水
在改质反应器内发生的主要反应第1、2步反应,
十六烷值为零
十六烷值约20以上
非柴油组分
想避免第3步反应的发生,就要控制好反应深度,即反应 温度、反应压力、反应空速、氢油比等。
新氢 原料泵
柴油加氢精制装置反应系统工艺流程
循环氢压缩机 冷却器
排放氢
加热炉
1
2
高
低分气
分
罐
低
高 分 罐
污水
冷氢
低分气
低 分 罐
精制油去分馏塔 污水
高分罐分离的是油、水、氢气三相的。
新氢 原料泵
柴油加氢精制装置反应系统工艺流程
循环氢压缩机 冷却器
排放氢
加热炉
1
2
高
低分气
分
罐
低
污水
分 罐
精制反应器
改质反应器
冷氢
精制油去分馏塔 污水
排除的污水中,含有H2S、NH3,这是物 理方法第一次脱除S、N、O元素。
催化剂
烯烃
催化剂
H2
烃类 烃类 烃类 烃类 烷烃
柴油加氢改质装置节能措施效果评估

第53卷第1期 辽 宁 化 工 Vol.53,No. 1 2024年1月 Liaoning Chemical Industry January,2024收稿日期: 2022-11-30柴油加氢改质装置节能措施效果评估马社忠,马可望(濮阳石油化工职业技术学院,河南 濮阳 457000)摘 要:河南丰利石化有限公司建有60 万t ·a -1中芳烃加氢改质装置,设计操作压力为13.4 MPa,设计能耗为每吨原料油20.29 kg 标油,高于中石化同类装置的能耗定额(每吨原料油12 kg 标油),其中电耗占该装置总能耗的60%。
该装置通过投用热进料、新氢压缩机增加无级调节系统、循环氢压缩机增加无级调节系统、高压胺液泵加装变频器等节能措施,达到该装置节能降耗的目的,产生了良好的经济效益。
关 键 词:柴油加氢;节能;无级气量调节;变频器;热进料中图分类号:TE08 文献标识码: A 文章编号: 1004-0935(2024)01-0082-04河南丰利石化有限公司60万t ·a -1中芳烃加氢改质装置采用雅保公司的 STARS 芳烃深度饱和加氢改质工艺技术,于2016年9月建成投产。
该装置以直馏柴油、催化柴油为原料,与氢气进行加氢反应,生产低硫柴油,并副产少量酸性气、石脑油,反应产物分离采用“冷高分+冷低分+汽提塔”工艺流程,设计压力13.4 MPa,操作弹性60%~110%,年开工时间8 000 h。
柴油加氢装置作为炼油企业能源消耗较高的装置类型,其节能降耗也是实现企业降低成本的关键[1]。
1 装置能耗情况该装置设计能耗为每吨原料油20.29 kg 标油,高于中石化同类装置的能耗定额(每吨原料油12 kg 标油),主要原因为电耗高,占该装置总能耗的60%,因为该装置设计氢耗较高,达到3.7%(质量分数),其次,该装置设计操作压力13.4 MPa,远高于同类装置的6.0~8.0 MPa 操作压力。
300万柴油加氢装置标定方案

第1页炼油厂300万吨/年柴油加氢装置标定方案第2页本方案资料目录1、装置概述2、装置标定的目的3、装置标定时间4、装置标定组织机构5、装置标定步骤及内容6、装置标定原始数据记录表7、装置标定风险评价第3页1、装置概述:1.1装置概况兰州石化公司300万吨/年柴油加氢装置由寰球工程公司辽宁分公司设计,究院开发的FHUDS-5超深度加氢脱硫柴油精制催化剂,以化工轻油、直馏柴油、焦化柴油、焦化汽油的混合油作为原料,通过加氢精制把原料转化为加氢石脑油、精制柴油。
装置包括原料预处理系统、反应系统、分馏系统、辅助系统及公用工程系统,采用该装置于2010年10月破土动工,2012年3月9日中交,6月1日生产出合格产品,装置设计 规模为300 X 104t/a ,操作弹性为60%〜120%,年开工时数为 8400小时。
1.2技术特点1.2.1采用抚顺石油化工研究院开发的FHUDS-5超深度加氢脱硫柴油精制催化剂。
该催化剂采用先进的RASS 制备技术,有利于有效活性中心数目的增加。
加氢活性和超深度脱硫活性好,同时具有高的直接加氢脱硫活性,更适合高硫柴油的深度脱硫。
1.2.2设置一台加氢反应器,采用新型的反应器内构件,其气液分配更加均匀,催化剂利用率咼,径向温差小。
加热炉设空气预热器回收烟气余热,降低排烟温度,并选用新型节能燃烧器,提高加热炉热效率。
脱硫化氢汽提塔塔顶注缓蚀剂,以减轻塔顶馏出物中硫化氢对汽提塔顶系统的腐蚀。
在循环氢脱硫塔入口分液罐和循环氢脱硫塔内置了循环氢脱烃旋流器,减少了设备数量,节约了占地面积,有效地脱除循环氢中夹带重烃、胺(碱)米用抚顺石油化工研DCS 控 制。
1.2.3 装置反应部分采用冷高分流程,加热炉采用炉前混氢。
1.2.4 分馏部分设置脱硫化氢汽提塔和产品分馏塔。
1.2.5 滤后原料油缓冲罐采用燃料气保护,防止其与空气接触。
为防止原料中固体杂质带入反应器床层, 堵塞催化剂,造成床层压降过大,原料油进装置后采用自动反冲洗过滤器。
柴油加氢技术总结

柴油加氢技术总结2#柴油加氢装置开工总结宋火军1.开工前的准备1.1 学习装置理论知识生产低硫、低芳烃、低密度、高十六烷值得清洁柴油是今后世界范围内的柴油生产总趋势。
如何满足符合日趋苛刻的车用柴油标准,生产出符合环保要求的清洁柴油将成为炼油技术进步的一个重要课题。
柴油燃料质量升级的趋势与汽油类似,最主要的是对于硫含量的控制,同时对于柴油产品指标中的十六烷值、芳烃含量、冷流动性、密度等也提出了更为严格的要求。
二次加工的柴油含有相当多的硫、氮及烯烃类物质,油品质量差,安定性不好,储存过程容易变质,对直馏柴油而言,由于原油中硫含量升高,环保法规日趋严格,已经不能直接作为产品出厂,也需要经过加氢精制处理。
柴油加氢精制的生产原理就是在一定温度、压力、氢油比、空速条件下,借助加氢精制催化剂的作用,有效的使油品中的硫、氮、氧、非烃类化合物转化为响应的烃类和H2S、NH3和H2O。
另外,少量的重金属则截留在催化剂中,同时使烯烃和部分芳烃饱和,从而得到安定性、燃烧性、情节性都较好的优质柴油产品和粗汽油(裂解料)。
本装置中大量循环氢的存在能保证气相为连续相,液相为分散相,被气相打散的液相在固定床催化剂上从上至下以液滴的形态流过催化剂床层,从而发生一系列的加氢反应。
循环氢在其中的关键作用是:(1)维持反应所需的氢分压,用来维系气相中的氢气向油相溶解的推动力。
(2)控制催化剂床层的温升。
(3)稀释反应物流杂质的浓度,促进深度脱杂质的反应。
1.2 学习开工方案在开工前两个月,车间开始组织操作人员学习开工方案,让每个人对开工都心里有数,了解每一个步骤,提高了操作人员的操作水平,为这次成功的开工打下了基础。
1.3 联系调度,提供合格氮气,在系统催化剂干燥时能满足供应。
1.4 硫化剂与试车用直馏柴油准备充足。
2.催化剂干燥催化剂在包装、储运和装填中,都难免吸附一定水分,吸附水会降低催化剂的活性和强度。
因此催化剂要在预硫化前进行脱水。
柴油加氢精制装置空冷器腐蚀案例分析

柴油加氢精制装置空冷器腐蚀案例分析摘要:随着时代的发展,世界各国都在加快推进清洁燃料的发展进程。
柴油是生活中常见的能源资源,为保证柴油的质量,克服柴油中硫、氮、氧的含量高的问题,提高柴油的使用性能,一般在柴油的加工过程中,引进加氢工艺。
目前,柴油加氢精制装置是炼厂常见的炼油装置,由于加氢装置具有高温高压特性,容易受到一些物质的腐蚀,在加氢过程中会产生一些H2S,对柴油加氢装置设备的安全运行产生一定的危害。
因此,本文结合某炼油厂一套220万吨/年柴油加氢精制装置开工过程中出现的空冷器泄露事故,对硫化氢腐蚀进行分析和探讨。
关键词:柴油加氢精制装置空冷器硫化氢腐蚀国内某大型石化炼厂的大型千万吨炼油项目新建一套220万吨/年柴油加氢精制装置,在开工过程中发生了空冷器泄露事故,结合该事故的发生对此套装置的设计条件到事故过程,以及空冷器泄露试样的检测,对泄露事故加以分析和总结,杜绝今后类似情况发生。
1.工艺设计技术方案(1)工艺技术路线根据原料油的组成和性质、产品方案和质量要求,采用中国石油石油化工研究院开发的PHF-101加氢精制催化剂和洛阳石化工程公司成熟的柴油加氢工程技术。
(2)工艺技术特点加氢过程中生成的H2S、NH3,在一定温度下会生成NH4HS结晶,沉积在空冷器管束中引起系统压降增大。
因此,在反应流出物进入空冷器前注入除盐水,避免铵盐结晶析出。
(3)原料油该装置以直馏柴油、渣油加氢柴油和催化柴油的混合油为原料油。
(4)氢气该装置所用氢气为重整装置生产氢气和PSA氢气的混合氢气。
(5)开工流程开工油(直馏柴油)从装置外来,经原料油过滤器、原料油缓冲罐、加氢进料泵进入反应系统,从热低压分离器底部排出的油经精制柴油空冷器冷却后返回原料油缓冲罐,反应部分建立循环,同时,开工油引至脱硫化氢汽提塔及产品分馏塔入口,向分馏部分进油,待脱硫化氢汽提塔和产品分馏塔建立液位后,分馏部分可以建立循环,缩短开工时间。
(4)空冷器选型特点该装置共有空冷器17片,其中热高分气空冷器存在严重湿H2S腐蚀,管箱材质选用Q345R(R-HIC),换热管20,每壳程入口管端内衬500mm的S31603套管。
柴油加氢精制装置节能减排措施
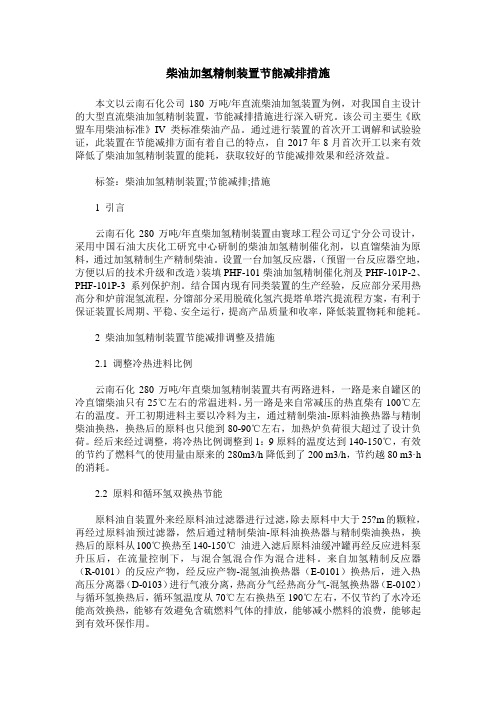
柴油加氢精制装置节能减排措施本文以云南石化公司180万吨/年直流柴油加氢装置为例,对我国自主设计的大型直流柴油加氢精制装置,节能减排措施进行深入研究。
该公司主要生《欧盟车用柴油标准》IV类标准柴油产品。
通过进行装置的首次开工调解和试验验证,此装置在节能减排方面有着自己的特点,自2017年8月首次开工以来有效降低了柴油加氢精制装置的能耗,获取较好的节能减排效果和经济效益。
标签:柴油加氢精制装置;节能减排;措施1 引言云南石化280万吨/年直柴加氢精制装置由寰球工程公司辽宁分公司设计,采用中国石油大庆化工研究中心研制的柴油加氢精制催化剂,以直馏柴油为原料,通过加氢精制生产精制柴油。
设置一台加氢反应器,(预留一台反应器空地,方便以后的技术升级和改造)装填PHF-101柴油加氢精制催化剂及PHF-101P-2、PHF-101P-3系列保护剂。
结合国内现有同类装置的生产经验,反应部分采用热高分和炉前混氢流程,分馏部分采用脱硫化氢汽提塔单塔汽提流程方案,有利于保证装置长周期、平稳、安全运行,提高产品质量和收率,降低装置物耗和能耗。
2 柴油加氢精制装置节能减排调整及措施2.1 调整冷热进料比例云南石化280万吨/年直柴加氢精制装置共有两路进料,一路是来自罐区的冷直馏柴油只有25℃左右的常温进料。
另一路是来自常减压的热直柴有100℃左右的温度。
开工初期进料主要以冷料为主,通过精制柴油-原料油换热器与精制柴油换热,换热后的原料也只能到80-90℃左右,加热炉负荷很大超过了设计负荷。
经后来经过调整,将冷热比例调整到1:9原料的温度达到140-150℃,有效的节约了燃料气的使用量由原来的280m3/h降低到了200 m3/h,节约越80 m3·h 的消耗。
2.2 原料和循环氢双换热节能原料油自装置外来经原料油过滤器进行过滤,除去原料中大于25?m的颗粒,再经过原料油预过滤器,然后通过精制柴油-原料油换热器与精制柴油换热,换热后的原料从100℃换热至140-150℃油进入滤后原料油缓冲罐再经反应进料泵升压后,在流量控制下,与混合氢混合作为混合进料。
柴油加氢精制装置运行情况分析

中国石化燕山石化公司(简称燕山石化)是北京地区唯一千万吨级炼化企业,油品质量升级始终走在国内前列,执行着国内最严格的汽柴油标准,2016年底率先推出京VI油品。
燕山石化有一套120万吨/年柴油加氢装置,以直馏柴油掺炼焦化汽油、焦化柴油和催化柴油,生产满足京VI标准车用柴油的调和组分。
1 装置简介燕山石化柴油加氢精制装置由反应部分(包括压缩机、循环氢脱硫)、分馏部分、循环氢脱硫及公用工程等部分组成。
装置原设计加工能力100万吨/年,2001年7月28日一次开车成功,2008 年通过扩能改造,增上了第二反应器,加工能力提高至120万吨/年。
该装置上周期(2017年12月9日—2020年6月)采用石油化工科学研究院(简称石科院)研制开发、中国石化催化剂长岭分公司生产的RS-2100/ RS-2110催化剂。
2020年8月,该装置在检修期间对加氢催化剂进行了再生并在第二反应器补充了部分活性稳定性更好的RS-3100催化剂。
2 装置上周期运行情况柴油加氢精制装置上周期加工的原料硫含量接近10000μg/g、密度在860 kg/m3左右、终馏点接近360℃。
装置运行初期,产品硫含量稳定控制低于10μg/g。
2.1 催化剂装填数据装置上周期催化剂装填数据详见表1。
表1 催化剂装填数据装填物质实际装填量堆密度/体积/m3重量/t(kg·m-3)一反上床层RG-1保护剂10.9 6.4585RS-2100催化剂(普通)17.514.8844一反中床层RS-2100催化剂(普通)30.225.3839一反下床层RS-2100催化剂(部分密相)44.542.9965二反RS-2100新鲜剂(普通)24.920.9840RS-2110新鲜剂(密相)44.047.51079由此可见,装置合计装填主精制催化161.1m3,合计151.4t。
其中,RS-2100催化剂普通装填堆密度在840kg/m3左右,密相装填堆密度达到980kg/m3;而RS-2110催化剂的装填堆密度较RS-2100高10%左右。
(120万吨)柴油加氢精制装置操作规程
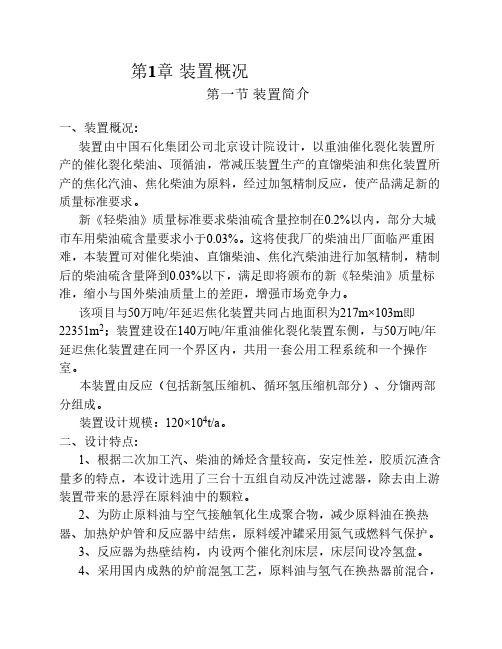
第一节 装置简介
一、装置概况: 装置由中国石化集团公司北京设计院设计,以重油催化裂化装置所
产的催化裂化柴油、顶循油,常减压装置生产的直馏柴油和焦化装置所 产的焦化汽油、焦化柴油为原料,经过加氢精制反应,使产品满足新的 质量标准要求。
新《轻柴油》质量标准要求柴油硫含量控制在0.2%以内,部分大城 市车用柴油硫含量要求小于0.03%。这将使我厂的柴油出厂面临严重困 难,本装置可对催化柴油、直馏柴油、焦化汽柴油进行加氢精制,精制 后的柴油硫含量降到0.03%以下,满足即将颁布的新《轻柴油》质量标 准,缩小与国外柴油质量上的差距,增强市场竞争力。
0.467 0.122 0.015 0.01 0.008 0.004 8.279 91.903
C5+液收
100.19
化学耗氢
0.85
备注:数据由石油化工科学研究院提供。
100.182 0.81
表5 柴油加氢精制产品主要性质
柴油产品要求
S<150ppm
方案一
方案二
主要产品
汽油 柴油 汽油 柴油
馏分范围
反应入口氢分压 MPa
进料量
t/h
体积空速
h-1
催化剂装填量 m3
上床层
下床层
反应温度 ℃
上床层:入口温度
方案一
方案二
RN-10
S<150ppm
6.4
150
1.83
1.82
96.79 32.26 64.53
307
315
出口温度 温升 下床层:入口温度
出口温度
温升
床层平均反应温度 ℃
反应器总温升 ℃ 反应器入口氢油比 床层间冷氢量 Nm3/h 催化剂运转周期 二、高压分离器: 操作压力 MPa(G) 温度 ℃ 三、低压分离器: 操作压力 MPa(G) 温度 ℃ 四、新氢压缩机: 入口温度 ℃ 40 入口压力 MPa(G) 出口压力 MPa(G) 五、循环氢压缩机: 入口温度 ℃ 50 入口压力 MPa(G) 出口压力 MPa(G) 六、汽提塔: 塔顶压力 MPa(G) 进料温度 ℃
提高柴油加氢装置产品质量技术攻关涂银堂

提高柴油加氢装置产品质量技术攻关涂银堂发布时间:2021-09-16T09:18:19.082Z 来源:《中国科技人才》2021年第18期作者:涂银堂[导读] 四川石化有限责任公司300万吨/年柴油加氢裂化装置于2018年6月技改后开车运行,年开工时数为8400小时,操作弹性50%~100%。
中国石油四川石化有限责任公司四川成都 611930摘要:四川石化有限责任公司300万吨/年柴油加氢裂化装置于2018年6月技改后开车运行,年开工时数为8400小时,操作弹性50%~100%。
技改项目反应器由原来的精制剂换成精制和裂化催化剂,分馏塔侧线增设煤油组份分割流程,增设石脑油系统。
改造后装置主要加工的原料为常减压蒸馏装置的直馏柴油和催化裂化装置的催化柴油,氢气为乙烯氢、重整氢、PSA氢。
产品为低硫柴油、航煤,副产品为轻石脑油、重石脑油、低分气、液化气和干气。
关键词:产品质量柴油石脑油馏程一、问题提出装置反应器上床层是精制催化剂,下床层是裂化催化剂,原料经过上床层加氢精制后,进入下床层反应,部分油品加氢裂化生成小分子油品。
反应生产油在分馏塔中进行分割,轻组分石脑油经塔顶分离外送,较轻的组分航煤从塔中部抽出并入塔底柴油线出装置。
在生产中存在如下质量[1]问题: 1、重石脑油终馏点偏高装置生产的重石脑油作为重整供料,内控指标要求终馏点≤170℃。
装置在调整柴油产品各项指标,如增大柴油密度、提高柴油粘度时,要求塔顶多抽轻组分,这就造成重石脑油终馏点偏高。
实际生产的重石脑油终馏点常大于170℃,无法作为重整原料。
2、产品柴油的粘度偏低粘度是柴油重要的使用性能项目,它与柴油额供给量、雾化性、燃烧性和润滑性均有密切的关系[2]。
标准中要求0号柴油在20℃时的运动粘度在3.0~8.0mm2/s,只有在这个范围内,才既能保证柴油对发动机燃油供给系统有较好的润滑性,保证柴油有较好的雾化性能和供给量,从而使柴油有较好的燃烧性能。
在柴油加氢装置生产过程中对柴油产品的影响因素分析

第52卷第8期 辽 宁 化 工 Vol.52,No. 8 2023年8月 Liaoning Chemical Industry August,2023在柴油加氢装置生产过程中对柴油产品的影响因素分析侯东听,郭峰荣(山东滨化滨阳燃化有限公司,山东 滨州 251800)摘 要:柴油加氢装置是石油化工行业常见的装置,是提高汽油和柴油产品质量的重要手段,柴油加氢后的产品主要是满足GB19147—2017柴油规格要求、符合半再生重整需要的精制石脑油原料指标。
柴油加氢精制装置在一定条件下将原料油中的含硫、氮、氧等非烃化合物氢解,通过乙醇胺脱硫塔剔除硫化氢,通过注水稀释溶解铵盐经高压分离器界位外送,得到洁净柴油。
关 键 词:化工装置;柴油加氢;影响因素;生产过程;压力;氢油比;温度;空速;催化剂中图分类号:TE966 文献标识码: A 文章编号: 1004-0935(2023)08-1168-04加氢精制是焦化柴油、焦化汽油、减一线油及常压柴油在高压氢气环境中进行脱硫脱氮使得产品满足国家标准的一个统称。
通过反应进料加热炉加温、氢气增压机增压、混合原料和氢,在加氢精制反应器内利用催化剂对混合原料、氢气进行加氢精制反应,使其原料中的有机硫、氮、氧等非烃类物质转化为烃类等易除去的物质。
1 反应压力和温度对加氢的影响分析1.1 反应压力对加氢精制的影响分析加氢精制效果受反应系统压力影响,即氢气分压,反应器入口氢分压的定义为反应器入口总 压×循环氢中氢气纯度。
在高压下镍钼类催化剂利于加氢脱芳烃、低压下利于加氢脱硫。
加快反应速度,促进加氢反应向正方向移动,需要提高氢分压,即提高氢分压就是提高空速。
提高氢分压优势主要体现在两个方面:第一,空速提高,缩短原料在催化剂上停留时间,可抑制保护剂及精制剂结焦,延长催化剂使用寿命;第二,大大提高原料中硫、氮和金属杂质的脱除率[1-3]。
汽柴油加氢精制装置的反应压力一般在 7.0 MPa左右,循环氢中氢气纯度≥90%,氢分压约6.3 MPa。
炼油厂工艺简介
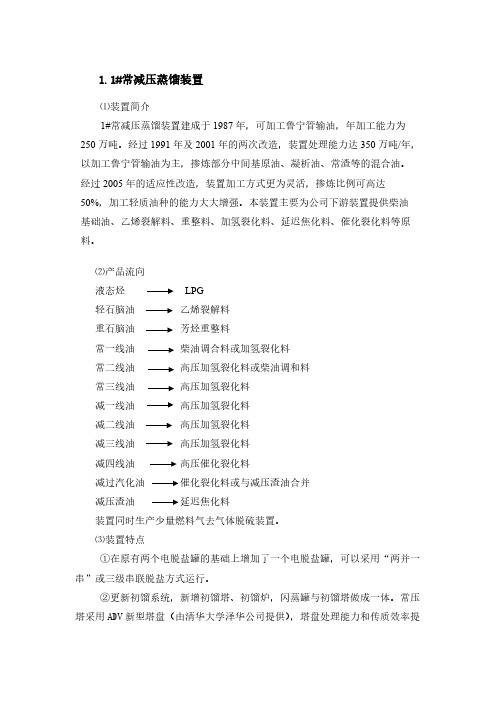
1.1#常减压蒸馏装置⑴装置简介1#常减压蒸馏装置建成于1987年,可加工鲁宁管输油,年加工能力为250万吨。
经过1991年及2001年的两次改造,装置处理能力达350万吨/年,以加工鲁宁管输油为主,掺炼部分中间基原油、凝析油、常渣等的混合油。
经过2005年的适应性改造,装置加工方式更为灵活,掺炼比例可高达50%,加工轻质油种的能力大大增强。
本装置主要为公司下游装置提供柴油基础油、乙烯裂解料、重整料、加氢裂化料、延迟焦化料、催化裂化料等原料。
⑵产品流向液态烃LPG轻石脑油乙烯裂解料重石脑油芳烃重整料常一线油柴油调合料或加氢裂化料常二线油高压加氢裂化料或柴油调和料常三线油高压加氢裂化料减一线油高压加氢裂化料减二线油高压加氢裂化料减三线油高压加氢裂化料减四线油高压催化裂化料减过汽化油减压渣油装置同时生产少量燃料气去气体脱硫装置。
⑶装置特点①在原有两个电脱盐罐的基础上增加了一个电脱盐罐,可以采用“两并一串”或三级串联脱盐方式运行。
②更新初馏系统,新增初馏塔、初馏炉,闪蒸罐与初馏塔做成一体。
常压塔采用ADV新型塔盘(由清华大学泽华公司提供),塔盘处理能力和传质效率提高。
③减压塔填料更换为高效规整填料ZUPAK,采用槽式分布器取代原喷头,进料部位采用流线式快速分布器(天津大学天久公司)。
④加热炉采用LGH-L/Q高效燃烧器(洛阳科恒公司)。
⑤装置增加轻烃回收系统,生产液化气、轻石脑油和重整料。
⑥减压系统采用三级蒸汽抽真空,残压达2.0Kpa以下。
2.2#常减压蒸馏装置⑴装置简介2# 常减压蒸馏装置建成于1995年,该装置主要加工高硫、轻质原油,加工能力为250万吨/年。
2002年装置经过改造,加工能力达450万吨/年,设计加工沙特轻质油、沙特中质混合原油。
800万吨/年炼油改造完成以后,主要以加工沙轻、阿曼等高(含)硫油为主,适当安排部分低硫原油,总硫控制在1.5%左右。
装置主要产品有液化气、乙烯料、重整料、柴油调和基础料、加氢裂化、加氢精制料、催化料、焦化料。
柴油加氢装置掺炼催化柴油试验总结

柴油加氢装置掺炼催化柴油试验总结总结了中国石油哈尔滨石化公司柴油加氢装置掺炼催化柴油试验期间,装置的氢气消耗及产品质量情况。
本次试验,考核了催化剂在原料性质发生变化的时的应用。
标签:加氢;掺炼;催化柴油1.装置简介中国石油哈尔滨石化公司100万吨/年柴油加氢装置2013年7月开始建设,2014年8月工程中交,由中国石化工程设计有限公司(SEI)设计,中油第一建设公司建设。
装置以来自上游常减压装置的常一线和常二线柴油为原料,在高温高压、氢气以及催化剂的作用下脱除原料中的硫、氮等杂质,生产出优质的航煤及柴油产品。
装置采用石油化工科学研究院(RIPP)和中国石化工程建设公司(SEI)联合开发的连续液相加氢(SLHT)技术。
100万吨/年柴油加氢精制装置催化剂采用RS-1100超深度脱硫催化剂和配套的RG-1保护剂。
2016年9月装置进行了第一次检修,对反应器催化剂进行器外再生,并补充部分新鲜催化剂,2016年9月26日装置开车成功。
2.掺炼催化柴油背景本次检修开工后,柴油加氢装置共进行了两次催化柴油掺炼,第一次在10月11日至10月15日期间,由于公司催化柴油原料罐存压力比较大,加氢改质装置处理能力有限,因此公司决定将催化柴油原料按比例引入柴油加氢装置进行试验;第二次在11月6日,装置引入催化柴油直供料进行掺炼,运行2小时后切除。
在掺炼催化柴油直供料之前,对柴油加氢装置原料流程进行改造,改造如下图所示:(1)图中加粗部分流程为新增流程。
(2)掺炼催化柴油过程中,阀(1)、(3)、(4)打开,阀(2)关闭。
(3)通过阀(1)控制催化柴油比例。
3.原料比較催化柴油与直馏柴油性质对比4.掺炼比例及调整过程10月11日至10月15日期间,按催化柴油原料比例10%、15%、20%引入装置,产品质量按普通柴油方案生产,反应器压力控制9.5MPa。
在催化柴油各种比例下观察R-101各床层温度、温升及氢耗情况。
确保反应器床层总温升不大于20℃,反应器床层温升通过以下手段控制:(1)开大E-101冷旁路调节阀TV11207,降低反应器入口温度;(2)调节P-104变频,将循环比提至2;(3)开大E-204管程跨线调节阀TV10402,降低原料油温度;(4)关闭E-203管程跨线阀,降低原料油温度。
柴油加氢装置运行过程中存在的问题及应对措施
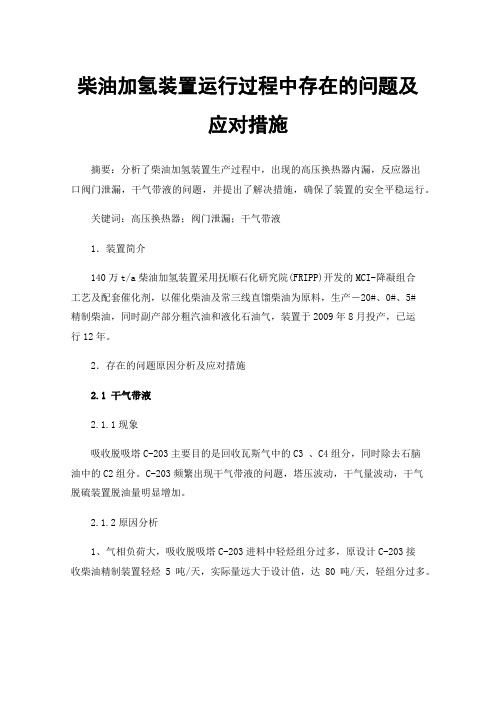
柴油加氢装置运行过程中存在的问题及应对措施摘要:分析了柴油加氢装置生产过程中,出现的高压换热器内漏,反应器出口阀门泄漏,干气带液的问题,并提出了解决措施,确保了装置的安全平稳运行。
关键词:高压换热器;阀门泄漏;干气带液1.装置简介140万t/a柴油加氢装置采用抚顺石化研究院(FRIPP)开发的MCI-降凝组合工艺及配套催化剂,以催化柴油及常三线直馏柴油为原料,生产-20#、0#、5#精制柴油,同时副产部分粗汽油和液化石油气,装置于2009年8月投产,已运行12年。
2.存在的问题原因分析及应对措施2.1干气带液2.1.1现象吸收脱吸塔C-203主要目的是回收瓦斯气中的C3 、C4组分,同时除去石脑油中的C2组分。
C-203频繁出现干气带液的问题,塔压波动,干气量波动,干气脱硫装置脱油量明显增加。
2.1.2原因分析1、气相负荷大,吸收脱吸塔C-203进料中轻烃组分过多,原设计C-203接收柴油精制装置轻烃5吨/天,实际量远大于设计值,达80吨/天,轻组分过多。
2、塔热量平衡影响。
吸收脱吸塔C-203的吸收过程是一放热过程,从塔顶到塔底温度越来越高,随着轻烃量增大,从塔底上升的吸收热量增多,一中、二中回流量小,不能把多余的热量取出来,吸收效果差,可能造成塔顶气体带液。
3、塔顶压力影响。
随着轻烃量增大,塔顶压力高,吸收效果好,脱吸效果差,C2不易脱出,压力低则吸收效果差,脱吸效果好,干气中C5量增加,控制合适的塔压才能保证液化气中的C2脱出,同时干气不带液。
2.1.3应对措施确保液化气中C2不超标的情况下,适当降低调节吸收脱吸塔C-203底温度。
增大吸收脱吸塔C-203一、二中回流量,降低吸收热量,提高了吸收效果。
控制合适的塔顶压力,吸收脱吸效果达到最佳。
表1 吸收脱吸塔参数调整前后对比项目调整前调整后底温/℃一中回流量/(kg/h)75250007028000二中回流量/(kg/h)2500030000塔顶压力/Mpa0.650.60 2.1.4调整后吸收脱吸塔C-203吸收效果对比表2 干气组成对比项目调整前调整后C5/%(w) 6.43 1.86C4/%(w) 3.84 1.75C3/%(w)0.090.09C2/%(w)48.7659.78通过表1和表2来看,在轻烃量增大的工况下,通过调整吸收脱吸塔的底温、压力、一二中回流量,使干气中的C5含量由6.43%降至1.86%,C4含量由3.84%降至1.75%,液化气中C2略有增加,实现了干气不带液。
汽油加氢装置原理简介

a.循环水系统来,至E9101,至E9103,至E9104,至E9202,至E9204, 至E9206,至E9301,至E9304,至P9101,至P9102,至P9103,至P9104, 至P9201,至P9202,至P9203,至P9204,至P9301,至P9302,至P9303, 至P9304,至P9305,至P9101,至P9001,至P9002,至P9003,至压缩机 K9101,至压缩机K9301。 b.除盐水自系统来,至压缩机水箱,至D9201注水罐。 c.新水自系统来,至D-9102,至D-9103,至E-9102,至D-9203,至P-9204。
汽油加氢装置
稳定塔顶部产物经稳定塔顶空冷器(A-9202)冷却至55℃后进入稳定塔顶回流 罐(D-9203)。罐顶酸性气体经稳定塔顶气体冷却器(E-9204)冷却后送至硫磺装 置富气再生塔,回流罐底油由稳定塔顶回流泵(P-9203A/B)送回稳定塔顶部作 回流,回流罐底部含硫污水与加氢脱硫反应产物分离罐(D-9202)含硫污水合 并后送出装置。在稳定塔顶管线注入缓蚀剂,最大限度减少设备腐蚀。稳定塔底 物料一部分经稳定塔底重沸器(E-9205)加热后返回稳定塔,另一部分经重汽油产 品泵(P-9204A/B)和稳定塔进料/稳定塔底油换热器(E-9203A/B/C)换热后与 LCN混合,再经汽油产品空冷器(A-9203)、汽油产品后冷器(E-9206)换热 至40℃以下后作为汽油产品出装置。
汽油加氢装置
为防止反应生成的铵盐在低温下结晶堵塞管道和空冷器管束,在加氢脱硫反应产 物空冷器(A-9201)前注入除盐水以洗去铵盐。加氢脱硫反应产物进入加氢脱硫 反应产物分离罐(D-9202)进行气、油、水三相分离。加氢脱硫反应产物分离罐 (D-9202)顶部气体经循环氢冷却器(E-9202)冷却后进入循环氢脱硫塔入口分 液罐(D-9301)进一步分液,然后进入循环氢脱硫塔(C-9301),与从循环氢脱 硫塔(C-9301)上部注入的贫胺液逆向接触以脱除H2S,富胺液从循环氢脱硫塔 (C-9301)塔底流出进入溶剂再生以循环使用。脱硫后气体进入循环氢压缩机入 口分液罐(D-9304)除去其中夹带的胺液,然后进入循环氢压缩机(K-9301A/B) 升压后循环使用。加氢脱硫反应产物分离罐(D-9202)底部液体至稳定塔进料/稳 定塔底油换热器(E-9203A/B/C)换热后进入稳定塔(C-9201)。稳定塔的作用 是将重汽油产品中的轻烃和溶解的H2S分离出去。
- 1、下载文档前请自行甄别文档内容的完整性,平台不提供额外的编辑、内容补充、找答案等附加服务。
- 2、"仅部分预览"的文档,不可在线预览部分如存在完整性等问题,可反馈申请退款(可完整预览的文档不适用该条件!)。
- 3、如文档侵犯您的权益,请联系客服反馈,我们会尽快为您处理(人工客服工作时间:9:00-18:30)。
三、工艺流程介绍及工艺特点
3.3、工艺技术特点
3.3.1.2反应部分流程
5 、反应器入口温度通过调节反应进料加热 炉燃料来控制。 6 、在反应流出物进入空冷器(及 E - 104 ) 前注入除氧水来溶解铵盐,避免铵盐结晶析出。 7 、为确保催化剂、高压设备和操作人员的 安全,在冷高压分离器上设有紧急泄压设施。 8 、新氢压缩机、循环氢压缩机为组合式往 复压缩机组,由同步电机驱动,一开一备。
四、原料及主要产品性质
2.1.1、原料油性质
项 目 原料类型 流量 API重度 比重 20°C 总硫 总氮量 总芳烃 单 位 正常 直馏柴油 440 38.98 0.8300 %wt ppmwt %wt 0.66 100 20.0 限制值 直馏柴油
近期设计目标
SOR 6.40 5.75 EOR 6.40 5.75
最终设计目标
EOR 6.57 5.91 1.4 30.91 1.34 344 351 358 365 354 361 169 0.28 0.27 SOR 6.57 5.91
2.5 30.91 2.31 340 349 351 360 348 356 169 0.19 0.19
二、公用工程消耗及辅助设施
8.2公用工程消耗
序号 名称 1 除氧水 2 循环冷水 3 循环热水 4 1.0MPa 蒸汽 5 6 7 8 9 10 11 燃料气 氮气 非净化风 净化风 新鲜水 汽提净化水 凝结水 6566 流量Kg/h 13187 235300 235300 12800 温度℃ 66 30 38 300 常温 常温 常温 常温 66 109 压力Mp 协作关系 1.45 自系统管网来 0.45 自系统管网来 0.20 至系统管网 1.3 自系统管网来 0.5 0.6 0.6 0.6 0.95 0.5 0.6 自系统管网来 自系统管网来 自系统管网来 自系统管网来 自系统管网来
自酸性水汽提装置来
1200m3n/h 40
至系统管网
Hale Waihona Puke 二、公用工程消耗及辅助设施8.3能耗分析
装置能耗:408.63MJ/吨原料(9.8 ×104 kcal/t原料)
1 装置为热进料,反应加热炉相应热负荷 较小 2 原料泵采用透平驱动,回收能量203kW 3 充分回收反应流出物热量,反应流出物 空冷入口温度较低 4 新氢进装置原料较高,为2.4Mpa,新氢 压缩机用电较小 5 装置采用单塔汽提流程,塔进料温度低, 塔顶回流量小
二、公用工程消耗及辅助设施
8.4、辅助材料消耗
名称 保护剂(TK-10 ) 保护剂(TK-711 ) 精制剂 (UF-120 ) 惰性瓷球(Ф3、Ф6、Ф19 ) DMDS(SF-121D) 名称 缓蚀剂 一次装入量
2.294t 5.564t 194.515t 41t 44t
年用量 t
15
三、工艺流程介绍及工艺特点
kg/h 13289 7182 168 3634 1651
t/d 319 172 4 87 40
104t/a 11.16 6.03 0.14 3.05 1.39
3
4
5 6 7
362104 8690 304.17 388025 9312 325.94
四、原料及主要产品性质
2.1、原料油
300×104 t/a直馏柴油加氢精制装置的 原料为1000×104 t/a常减压蒸馏装置直馏 柴油,其主要性质见下表。 进装置温度:90 ℃(其中20%wt为 50℃冷进料,80%wt为100℃热进料) 进装置压力:0.75MPa(G)
独山子石化 1000万吨/年炼油工程新区炼油
第一联合装置
4 300×10 t/a
直馏柴油加氢精制装置简介
目 录
一、装置概述 二、公用工程情况 三、工艺流程介绍及工艺特点 四、原料及主要产品性质 五、主要自动控制方案 六、装置联锁方案 七、主要设备及引进设备简介 八、电气
一、概 述
独山子石化1000万吨/年炼油及120万吨/年 乙烯技术改造工程(炼油部分)第一联合装置 包括四个装置,即:200×104 t/a加氢裂化、 300×104 t/a直馏柴油加氢精制、80×104 t/a 催焦化柴油加氢精制、8×104 m3n/h制氢。其 中300×104 t/a直馏柴油加氢精制装置的原料 为1000×104 t/a常减压蒸馏装置直馏柴油。开 工近期生产硫含量<50ppm的精制柴油产品,最 终设计目标生产硫含量<10ppm、多环芳烃≤2v %的精制柴油产品。
汽提塔顶空冷器 汽提塔顶后冷器 汽提塔顶回流罐
干气至 加氢裂化
自反应流出物/ 汽提塔进料换 热器来 中压蒸汽 至反应流出物/汽 提塔进料换热器
汽 提 塔
产品空冷器
含硫污水
精制柴油聚结器 汽提塔顶回流泵 酸性水 去汽提
精制柴油泵 自低压分离器来 含油污水
酸性水泵 精制柴油 去罐区
三、工艺流程介绍及工艺特点
新氢
注水 汽提蒸汽 合计
0.32
3.61 2.42 106.35
1157
13187 8827 388025
28
316 212 9312
0.97
11.08 7.41 325.94
3 4
5
三、工艺流程介绍及工艺特点
3.6.2、开工近期运转末期物料平衡表(出方)
序号 1 2 物料名称 数量
收率%(w)
低分酸性水 塔顶酸性水 低分酸性气 塔顶酸性气 塔底含油污水 精制柴油 合计 3.64 1.97 0.05 1.00 0.45 99.25 106.35
一、概 述
1.6、引进设备材料
序 引进项目内容 号 1 加氢进料泵组 2 联合压缩机组 3 4 5 6 7 数量 备注 2 2 电机国产
液力透平
1 √ 反应加热炉炉管、急弯弯管 部分高压临氢阀门、管道及管配件 √ 1 DCS系统 1 ESD系统
1.7、进出装置物料走向
序号 物料名称 1 2 3 4 5 直柴 直柴 氢气 燃料气 石脑油或航煤 流量kg/h 72971 291883 温度℃ 50 100 压力Mp 0.75 0.75 2.4 0.5 0.75 走向 自罐区来 自常减压来 自系统来 自系统来 自罐区
三、工艺流程介绍及工艺特点
3.3、工艺技术特点
3.3.2、分馏部分流程
1 、分馏部分采用单塔汽提流程 , 塔底采用 1.0MPa蒸汽汽提。 2 、产品汽提塔塔顶馏出 H2、 H2S 和轻烃;塔 顶酸性气送加氢裂化装置脱硫。 3 、汽提塔顶设注缓蚀剂设施,减轻塔顶流 出物中硫化氢对汽提塔顶系统腐蚀。 4 、设置柴油聚结器,使产品满足水含量要 求。
一、概 述
15959m3n/h 40 1300m3n/h 40 40
6
7 8
精制柴油
粗石脑油 低分气
362335
正常无量 168
50
38 54
0.6
1.0max 2.9
至罐区
至加氢裂化装置 至加氢裂化装置
9
10 11
汽提塔顶气
含硫污水 含油污水
3634
20471
38
53 40
0.38
0.5 常压
至加氢裂化装置
反应流出物/热 循环氢换热器
反应流出物/循 环氢换热器
反应流出物/ 原料油换热器
高压分离器
低分气至 低压分离器 加氢裂化
原料油(罐区) 原料油(常减压)
原料油过滤器 原料油 缓冲罐
自精制柴油/ 汽提塔进料 换热器来
至精制柴油 /汽提塔进 料换热器
原料油泵
原料油泵液力透平
酸性水至汽提
3.2.2、工 艺 流程 分馏部分流程简图
实际处理量
年开工时数
306.5×104
8400
t/a
h
操作弹性
50-110
%
一、概 述
1.3、平面布置及占地
平面布置在满足有关防火、防爆及安全卫生 标准和规范要求的前提下,尽量采用露天化、集 中化和按流程布置,并考虑同类设备相对集中, 以达到减少占地、节约投资、降低能耗、便于安 全生产操作和检修管理,实现安全生产的目的。 装置占地: 230×90=20700m2
3484
1652
84
40
2.93
1.39
362289 8695 304.32 388056 9313 325.97
三、工艺流程介绍及工艺特点
3.6.1、开工近期运转末期物料平衡表(入方)
序号 物料名称 收率%(w) 数量
kg/h
364854
t/d
8756
104t/a
306.48
一
1 2
入方
原料油 100.00
3.5.2、开工近期运转初期物料平衡表(出方)
物料名称
收率%(w) 数量 kg/h t/d 104t/a
低分酸性水
塔顶酸性水 低分酸性气
3.64
1.97 0.04
13289
7182 162
319
172 4
11.16
6.03 0.14
塔顶酸性气
塔底含油污水 精制柴油 合计
0.95
0.45 99.30 106.36
t/d
8756 28
104t/a
306.48 1.00
一 1
2 3 4 5
入方
原料油 新氢 100.00 0.33
注水
汽提蒸汽 合计
3.61
2.42 106.36
13187
8829 388056
316
212 9313
11.08
7.42 325.97
三、工艺流程介绍及工艺特点
序号 1
2 3 4 5 6 7
三、工艺流程介绍及工艺特点