天然气制合成气分析解析
2合成气(化学工艺学)解析

K P1
P CO
P3 H2
P P CH 4 H 2 O
K P2
P P CO 2 H 2 P CO P H 2 O
b.平衡组成的计算
已知条件: m原 料 气 中 的 水 碳 比 (m H2O)
CH4 P 系 统 压 力 ; T 转 化 温 度 假定:无炭黑析出
计算基准:1mol CH4 在甲烷转化反应达到平衡时,设x为按式(2-3)转化了
压力和水碳比确定后,按平衡甲烷的浓度来确定温度。一般要
求yCH4<0.005,出口温度应为1000℃ 左右。实际生产中,转
化炉出口温度比达到出口气体浓度指标对应的平衡温度高, 这个差值叫平衡温距。
T =T-Te(实际温度-平衡温度) 平衡温距低,说明催化剂活性好。一、二段平衡温距通常分 别为 10~15 ℃ 和 15~30 ℃ 。
为代表来讨论气态烃类蒸汽转化 的主要反应及其控制条件。
➢ 烃类主要进行的反应 烷烃
烯烃 CnH2n n2H2O34nCH4 n4CO2 CnH2n nH2OnCO2nH2 CnH2n 2nH2OnCO2 3nH2
2.1.1.1 甲烷蒸汽转化反应
主要反应
高温、催化 剂
( 1 ) C 4 H H 2 O = C 3 H O 2 2.4 0 km 6 J o ( 2 ) C H O 2 O = C 2 H O 2 4 .2 k 1 /m J
水碳比 反应温度 反应压力
➢ 温度增加,甲烷平衡含量下降,反应温度每降 低10℃,甲烷平衡含量约增加1.0%-1.3%;
➢ 增加压力,甲烷平衡含量随之增大;
➢ 增加水碳比,对甲烷转化有力;
➢ 甲烷蒸汽转化在高温、高水碳比和低压下进行 有利
天然气制合成气的新技术

天然气制合成气的新技术摘要:伴随煤炭石油等能源的日益枯竭,天然气等新型能源进入到人们的视野当中,如何更有效的利用天然气成为关键。
本文简单介绍了国内外天然气的化工利用情况,并介绍了天然气为原料制成的合成物,最后分析了天然气制合成气的新技术。
关键词:天然气催化工艺天然气作为一种新兴重要能源,一般情况下不能直接利用,在合成燃料前会先合成气,而在整个天然气转化为使用能源的过程当中,合成气的步骤耗费相当大的成本,能够占到全程的百分之六十左右,因此天然气制合成气工艺的改善是一个巨大挑战。
近年来国外发展了自然重整,非催化部分氧化和联合重整等制合成气新工艺。
一、国内外天然气的化工利用上世纪初西方国家首次铺设了天然气管道为化工使用,自此天然气成功加入了世界能源的行列,各个国家开始了天然气的开发使用,并在相当长时间段内有着飞速发展,从1940年发展速度的开始提升至1960年达到鼎盛,天然气利用技术趋于成熟,转化成各类能源物,一定程度上促进了各国的发展。
至70年代,由于石油化工廉价化,天然气研发的脚步减慢,但仍有着较为稳定的发展速度。
目前,石油供给短缺,价格不断上升,世界石油局势紧张,而天然气作为一种新兴能源,处于开发的初级阶段,且储量巨大,国际能源机构认为,天然气产量增加,并且今后将会作为主要能源之一。
作为21世纪新兴能源,天然气合成燃料的工艺备受关注,不断得到改善,被应用到工业化工中去。
企业中的天然气转化工艺,可分为以下两种方法:1.直接转化法在制作乙烯过程中,当利用甲烷作氧化剂时,可以选择氧化制甲醇和甲醛。
2.间接转化法天然气制燃料常用的就是间接转化法,利用转化器将天然气进行转化,合成的合成气,应用于工业化工上,将之彻底转变成燃料、化肥等。
二、以天然气为原料的化工合成物1.合成氨氨肥是化肥工业中的主导产品,世界各国对化工氨需求量大,氨的产量直接影响到一个国家经济发展,因此提高合成氨产量十分重要。
当前,世界各国合成氨年产量大约为1.5亿吨左右其中百分之八十的合成氨是以天然气为原料制成。
天然气制备合成气

天然气制备合成气天然气作为一种清洁、环境友好的能源,越来越受到广泛的重视。
天然气作为一种清洁、环境友好的能源,越来越受到广泛的重视。
制合成气是间接利用天然气的重要步骤,也是天然气制氢的基础,充分了解天然气制合成气的工艺与催化剂对于我们进一步研究天然气的利用将有很大帮助。
天然气中甲烷含量一般大于90%,其余为小量的乙烷、丙烷等气态烷烃,有些还含有少量氮和硫化物。
其他含甲烷等气态烃的气体,如炼厂气、焦炉气、油田气和煤层气等均可用来制造合成气。
目前工业上有天然气制合成气的技术主要有蒸汽转化法和部分氧化法。
本文主要对蒸汽转化法进行具体的描述,并具体介绍此工艺的发展趋势。
蒸气转化法蒸气转化法是目前天然气制备合成气的主要途径。
蒸汽转化法是在催化剂存在及高温条件下,使甲烷等烃类与水蒸气反应,生成H2、CO等混合气,其主反应为:CH + H O = CO + 3H,A H © 298 = 206KJ / mol该反应是强吸热的,需要外界供热。
因为天然气中甲烷含量在90%以上,而甲烷在烷烃中热力学最稳定,其他烃类较易反应,因此在讨论天然气转化过程时,只需考虑甲烷与水蒸气的反应。
甲烷水蒸气转化反应和化学平衡甲烷水蒸气转化过程的主要反应有:CH4+ H2O o CO + 3H2,A H © 298 = 206KJ / molCH4+ 2 H2O o CO 2 + 4 H 2,A H © 298 = 165KJ /molCO + H 2 O o CO 2 + H2,A H © 298 = 74.9 KJ /mol可能发生的副反应主要是析碳反应,它们是:CH4 o C + 2H2,A H©298 = 74.9KJ /mol2CO o C + CO2,AH © 298 = -172.5 KJ /molCO + H 2 o C + H 2 O,A H © 298 = -131.4KJ /mol甲烷水蒸气转化反应必须在催化剂存在下才有足够的反应速率。
合成气的制备及应用研究

合成气的制备及应用研究一、概述合成气是由一定比例的一氧化碳和氢气组成的混合气体,可被广泛应用于化学工业、能源领域和合成化学等领域,因此,合成气的制备和应用一直备受关注。
二、合成气的制备技术1. 煤制气煤制气是最早用于制备合成气的技术之一。
该技术的原理是将煤通过高温气化反应,产生一氧化碳和氢气混合气体。
2. 天然气重整天然气重整是一种在高温和高压下,将天然气转化为一氧化碳和氢气混合气体的技术。
该技术需要大量的热量来提供反应所需的能量。
3. 生物质气化生物质气化是一种以生物质为原料制备合成气的技术。
该技术的原理是将生物质通过高温和压力下的气化作用,生成一氧化碳和氢气混合气体。
4. 液化石油气重整液化石油气重整是一种以液化石油气为原料制备合成气的技术。
该技术的原理与天然气重整相似,在高温和高压下将液化石油气转化为一氧化碳和氢气混合气体。
三、合成气的应用1. 化工行业合成气可以用于合成各种化学品,例如甲醇、合成氨、丙烯、乙二醇等。
2. 能源行业由于合成气可以被用作燃料,因此它被广泛地用于供热和发电等领域。
3. 合成化学合成气可以被用于合成化学品,例如合成蜡、合成尼龙、合成橡胶等。
4. 煤化工行业煤是制备合成气的主要原料之一,因此,合成气被广泛应用于煤化工行业。
例如,合成气可以被用于生产合成天然气、合成油等。
四、合成气的发展趋势目前,合成气在化学工业、能源领域和合成化学等领域中应用广泛。
随着技术的不断进步,合成气的制备技术将得到更好的发展和应用。
同时,随着石油资源的日益减少,对煤、天然气等非化石能源的需求将不断增加,因此合成气将会得到更广泛的应用。
总之,合成气的制备和应用是一个复杂而广泛的领域。
随着技术的不断进步和应用需求的不断扩大,合成气的发展前景将会更加广阔。
天然气水蒸气转化制合成气的主要反应

天然气水蒸气转化制合成气的主要反应下载提示:该文档是本店铺精心编制而成的,希望大家下载后,能够帮助大家解决实际问题。
文档下载后可定制修改,请根据实际需要进行调整和使用,谢谢!本店铺为大家提供各种类型的实用资料,如教育随笔、日记赏析、句子摘抄、古诗大全、经典美文、话题作文、工作总结、词语解析、文案摘录、其他资料等等,想了解不同资料格式和写法,敬请关注!Download tips: This document is carefully compiled by this editor. I hope that after you download it, it can help you solve practical problems. The document can be customized and modified after downloading, please adjust and use it according to actual needs, thank you! In addition, this shop provides you with various types of practical materials, such as educational essays, diary appreciation, sentence excerpts, ancient poems, classic articles, topic composition, work summary, word parsing, copy excerpts, other materials and so on, want to know different data formats and writing methods, please pay attention!一、背景介绍天然气水蒸气转化制合成气是一种重要的化工过程,通过该过程可以将天然气中的甲烷和水蒸气转化为合成气,为合成气制备提供了一种高效的工艺方法。
能源化工—第15章 天然气转化制合成气讲解

第15章 天然气转化制合成气
15.3.2 Uhde CAR工艺 15.3.3 Topsoe ATR工艺
图15.4 CAR反应器结构示意图
图15.5 ATR反应器结构示意图
将两种转化集于一个反应器内以降低投资和提高能源效率,ATR反应器更 简单而更具应用前景。
溶液无毒,设备无腐蚀,溶液有多种再生方案,用于合
成氨装置脱CO2时通常使用压力下闪蒸加蒸汽汽提的流程。
第15章 天然气转化制合成气
15.4.2 甲烷化
甲烷化是除去合成气中CO和CO2的最后工序,使其转化 为CH4。为了减少氢的消耗,有些大型装置在脱除CO2前增设 一选择催化氧化工序。将CO转化为CO2,CO浓度可降至1~ 2mL/m3。
以空气代替纯氧使天然气部分氧化制含氮合成气它可以节省空分装置 及相应费用、并有助于克服飞温问题。
第15章 天然气转化制合成气
15.3 联合转化工艺
天然气 脱硫
蒸汽 氧气或空气
一段转化 二段转化 合成气
图 天然气联合转化制合成气过程
第15章 天然气转化制合成气
15.3.1 Lurgi联合转化工艺
2)压力:由于CH4的蒸汽转化反应是分子数增加的反 应,所以压力的升高是不利的;但从总体安排考虑, 蒸汽转化还是要在适当压力下进行。
3)水碳比:较高的水碳比有助于CH4的转化。
第15章 天然气转化制合成气
15.1.2氮氢合成气生产工艺流程
用于合成氨的氮氢合成气需在天然气转化过程中导入 氮,通常采用两段转化工艺:在一段进行蒸汽转化,使出 口气中的CH4含量降至10%以下,二段导入空气,利用 CO及H2燃烧所产生的热量使CH4进一步转化降至0.3%左 右。转化的气体经变换工序使CO转化为CO2,在脱碳工 序脱除CO2,再经甲烷化工序除去微量碳氧化物,得到氮 气合成气去合成氨工序。
2.合成气

合成天然气、汽油和柴油
CO 3H 2 CH 4 H 2O( SNG)
Ni
煤制合成气通过费托合成可生产液体烃燃料
nCO ( 2n 1) H 2 C2 H 2 n 2 nH 2O
合成气的应用实例
合成气应用新途径
1.
直接合成乙烯等低C烯烃 2CO 4 H 2 C2 H 4 2 H 2O
水蒸气转化法 在高温和催化剂存在下,烷烃与水蒸气反应生 产合成气的方法称为水蒸气转化法。当以天然气为原料时,又 称甲烷蒸汽转化法,是目前工业生产应用最广泛的方法。 部分氧化法 部分氧化法是指用氧气(或空气)将烷烃部分氧化 制备合成气的方法。反应运式表示为, 部分氧化法多用于以石 脑油或重油为原料的合成气生产。
Mobil工艺
2. 合成气经甲醇再转化成烃类
2 2 2nCH3OH H nCH3OCH3 HC2 ~ C4烯烃 O O
3. 甲醇同系化制乙烯
CH 3OH CO 2 H 2 CH 3CH 2OH H 2O CH 3CH 2OH C2 H 4
4. 合成低C醇
合成气的应用实例
另一部分烃类与水蒸气发生吸热反应生成合成气 n Cm H n mH 2O mCO ( m ) H 2 2
iii.
以煤为原料的生产方法
高温条件下,以水蒸气和氧气为气化剂;
C H 2O CO H 2
煤制合成气中H2/ CO比值较低,适于合成有机化合物。
合成气的应用实例
1.
5 天然气蒸气转化过程的工艺条件
(1)压力 从热力学特征看,低压有利转化反应。从动力 学看,在反应初期,增加系统压力,相当于增加了反应物 分压,反应速率加快。但到反应后期,反应接近平衡,反 应物浓度高,加压反而会降低反应速率,所以从化学角度 看,压力不宜过高。但从工程角度考虑,适当提高压力对 传热有利,因为①节省动力消耗② 提高传热效率③ 提高 过热蒸汽的余热利用价值。综上所述,甲烷水蒸气转化过 程一般是加压的,大约3MPa左右。 (2)温度 从热力学角度看,高温下甲烷平衡浓度低, 从动力学看,高温使反应速率加快,所以出口残余甲烷含 量低。因加压对平衡的不利影响,更要提高温度来弥补。 但高温下,反应管的材质经受不了,需要将转化过程分为 两段进行。第一段转化800℃左右,出口残余甲烷10% (干基)左右。第二段转化反应器温度1000℃,出口甲 烷降至0.3%。
合成气的制备与利用技术研究
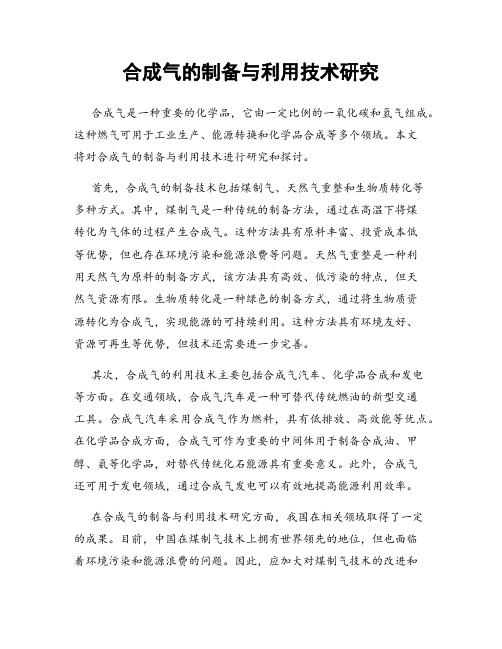
合成气的制备与利用技术研究合成气是一种重要的化学品,它由一定比例的一氧化碳和氢气组成。
这种燃气可用于工业生产、能源转换和化学品合成等多个领域。
本文将对合成气的制备与利用技术进行研究和探讨。
首先,合成气的制备技术包括煤制气、天然气重整和生物质转化等多种方式。
其中,煤制气是一种传统的制备方法,通过在高温下将煤转化为气体的过程产生合成气。
这种方法具有原料丰富、投资成本低等优势,但也存在环境污染和能源浪费等问题。
天然气重整是一种利用天然气为原料的制备方式,该方法具有高效、低污染的特点,但天然气资源有限。
生物质转化是一种绿色的制备方式,通过将生物质资源转化为合成气,实现能源的可持续利用。
这种方法具有环境友好、资源可再生等优势,但技术还需要进一步完善。
其次,合成气的利用技术主要包括合成气汽车、化学品合成和发电等方面。
在交通领域,合成气汽车是一种可替代传统燃油的新型交通工具。
合成气汽车采用合成气作为燃料,具有低排放、高效能等优点。
在化学品合成方面,合成气可作为重要的中间体用于制备合成油、甲醇、氨等化学品,对替代传统化石能源具有重要意义。
此外,合成气还可用于发电领域,通过合成气发电可以有效地提高能源利用效率。
在合成气的制备与利用技术研究方面,我国在相关领域取得了一定的成果。
目前,中国在煤制气技术上拥有世界领先的地位,但也面临着环境污染和能源浪费的问题。
因此,应加大对煤制气技术的改进和创新,优化工艺流程,减少污染排放。
同时,应积极推进天然气重整和生物质转化等清洁能源制备合成气的技术研究,提高能源利用效率,实现能源的可持续发展。
在合成气利用技术方面,应进一步推广合成气汽车的应用。
合成气汽车具有独特的优势,但在推广应用方面还存在一定的障碍,如加氢站建设的不足、燃料成本的高昂等问题。
因此,需要加大政府支持力度,推动加氢站建设,降低燃料成本,提高合成气汽车的市场占有率。
此外,还应强化合成气在化学品合成和发电领域的应用研究,开发新的催化剂和反应工艺,提高产品的质量和产量,提高能源利用效率。
天然气制甲醇合成气转化工艺的分析

2CH4 +O2 2CO+4H2
(5)
甲烷重整反应 (1) 与变换反应 (2) 在重
整温度下为可逆反应,反应 (2) 是微放热的,
在蒸汽重整温度较高时,反应平衡向左移动;当
使用大量过剩蒸汽参与反应时,会消耗 CO,反
应得到更多的 CO2,生成的合成气中 H2 过剩, 未转化的气体在合成甲醇阶段可以回收利用。反
天然气的主要成分为甲烷,甲烷通过与水蒸
产品多样灵活,有利于化解低气价的矛盾,有利 于分散上游开发的风险,有利于提高项目抗风险
气发生重整反应生成以 CO和 H2 为主要成分的 合成气,之后 CO与水蒸气发生变换反应,反应
的韧性。因此,为完善我国石油企业在下游国际 方程式如下:
业务产业链的布局,提高产品的附加值,提升项
[参考文献]
[1]王 充,冯为 健, 何 文 德.化 工 设 备 氢 腐 蚀 研 究 分 析 及 其
[3]冯再南,姚泽龙,楼 韧, 等.百 万 吨 级 大 型 甲 醇 合 成 塔 技术发展探讨 [J].煤炭加工与综合利用,2015 (10):54 -57,8.
第 1期
康英英等:天然气制甲醇合成气转化工艺的分析
应 (3) 为不可逆反应,反应可以一直进行到重
烃完全转化。反应 (4) 与反应 (1)、反应 (2)
是有区别的,据勒夏特列原理 (化学平衡移动
原理),在高温条件下,反应平衡向右移动,甲
烷含量减少,CO含量增高;当反应体系压力增
大时,反应平衡向左移动,甲烷含量增高;当反
应体系水碳比增大时,反应平衡向右移动,甲烷
含量减。
综合以上反应并结合实际生产所需,天然气
制甲醇的主要目标为:① 生产过程中采用适宜
的 H2/CO生产合成气,提高蒸汽转化反应中天 然气的转化率,以及降低吨产品的能耗;② 减少
天然气化工工艺学第03章天然气转化精品文档58页

温度T对Kpi的影响(分析)
• Kp1、 Kp2和T单位
lK n 1 2 p T . 4 3 3 . 3 8 L 0 9 2 . n 2 6 2 1 T 1 6 3 T 0 1 0 . 2 3 1 8 6 T 2 0 8 1 .0 2 1 1 9 1 T 3 0 0 9 3 . 25 lK n 2 4 T p . 8 8 1 . 1 6 L 1 5 3 . n 6 8 1 T 5 7 3 T 0 7 1 . 24 1 8 6 T 2 0 1 2 . 1 7 1 8 1 T 3 0 0 4 0 . 5 5 6
• 不同的合成气衍生化工产品需要不同的H2和CO摩尔比 (简写H2/CO比)的合成气,通常H2/CO→ 2 (摩尔比)。
常见合成气衍生化工产品对H2/CO比的要求
产品
H2/CO比
产品
H2/CO比
甲醇
2
乙醇
2
醋酸
1
醋酸乙酯
1.25
乙二醇
1.5
低碳烯
2
醋酐
1
丁醇
1.9
乙醛
1.5
FT合成油
1.7-2.1
《天然气化工工艺学》第3章
C H O 2 O (g )C 2 H O 2 4 .2 k 1 .m J 1o(2)l
高级烃转化反应
C 2 H 6 H 2 2 C4 H 6.3 5 k.m J 1ol
C 3 H 8 2 H 2 3 C4 H 1.0 2 k.1 m J 1ol
C 3 H 8 3 H 2 O 3 C 7 O H 2 4.2 9 k.m 8 J 1ol
天然气转化制备合成气研究进展安波

天然气转化制备合成气研究进展安波发布时间:2021-10-06T08:35:59.228Z 来源:《基层建设》2021年第18期作者:安波[导读] 随着我国科学技术水平不断提升,各领域均在创新发展阶段加大新技术应用力度,详细探究天然气转化制备合成气工作要点新疆玉象胡杨化工有限公司新疆维吾尔自治区沙雅县 842200摘要:随着我国科学技术水平不断提升,各领域均在创新发展阶段加大新技术应用力度,详细探究天然气转化制备合成气工作要点,核心目的是能对天然气合理开发与利用,有效减少石油资源使用量,并降低环境污染程度,提升资源利用率。
同时,天然气转化制备阶段会应用到先进技术与配套设施,要有完善的实施方案与计划,并对人员技术水平、专业能力等有明确要求,才可保证整体质量与效率。
关键词:天然气;转化制备;合成气引言:在天然气转化制备合成气过程中,所包括的工作流程较多,每项工艺质量控制会影响到整体效果,经专业化技术人员规范操作,能对常规问题详细探究与防控,能在细节上控制转化制备质量。
再加上工艺要求不同,技术手段选择与应用要合理,以CH为主要燃料,经多道程序处理可保证合成气转化质量,整体利用率显著提升。
一、方法应用当前,天然气转化制备合成气的常用方法包括两种:其一,直接转化法,能把天然气直接转化成化工产品;其二,间接转化法,直接把天然气转化成合成气,再经过对合成气的处理才能得到相应的化工产品。
对比两种方法的综合性,前者转化率、产率等较低,无法在短期内实现预期目标。
而后者则分析天然气转化制备要点,借助相应的技术手段,要经过多到程序处理才可生成化工产品,在总体投资方面成本较高,但能保证化工产品质量。
对此情况,无论是对哪种方法应用,均需依据实际情况全面分析,一旦在方法应用方面存在不合理情况,就会影响后续工作进度,更无法保证工艺质量。
对此,还需在转化制备中详细探究,实施效果才能有良好的基础保障。
二、工艺分析(一)甲烷水蒸气重整甲烷的水蒸气重整属于较早的研究内容,所应用的方法也比较简单,只需结合实际情况与各项条件,选择相应的催化剂,就可影响SRM产率(>80%),主要应用在工业领域中。
天然气自热式转化制合成气的aspen plus模拟分析

表1天然气和费托尾气组成%摘要针对富平燃气综合利用项目,选择自热式转化技术对天然气和费托合成尾气进行处理以生产合成气。
利用化工流程模拟软件Aspen Plus 对天然气自热式转化装置进行了全流程模拟,建立了以RStoic 和REquil 模块串联的形式进行预转化炉和自热式转化炉模拟的反应器模型,模拟所得的预转化气和转化气组成与设计值十分接近,验证了所建立的模型的准确性。
利用所建立的模型进一步模拟、计算得到装置的转化气组成、设备负荷等工艺参数及公用工程消耗数据,并分别对970℃、1000℃、1020℃、1050℃反应温度下的水碳比、氧碳比、CO 2消耗量进行了定性及定量分析,结果可为设计工作及实际生产提供理论数据支持。
关键词天然气,费托尾气,自热式转化炉,Aspen Plus ,模拟文章编号:1005-9598(2019)-05-0008-05中图分类号:TE665.3文献标识码:A天然气自热式转化制合成气的Aspen Plus 模拟分析王玉龙,周恩利,武麦桂(赛鼎工程有限公司,山西太原030032)收稿日期:2019-07-16作者简介:王玉龙(1990—),男,黑龙江伊春,工程师,硕士,2012年本科毕业于中国石油大学(北京)化学工程与工艺专业,现从事焦炉煤气综合利用、天然气综合利用的工程设计工作,E-mail :wangyulong@ 。
天然气的化工利用技术一直是世界各国的关注热点,比如以天然气为原料来生产合成氨、甲醇、氢气、乙二醇、合成油等技术[1]。
然而,无论生产以上哪种产品,都需先将天然气转化成合成气,再由合成气生产最终的产品。
由此可见,转化工艺技术是整个天然气化工的基础和龙头,在天然气化工中有着举足轻重的地位。
目前,天然气转化制备合成气的主要工艺技术有:蒸汽转化工艺、联合转化工艺、换热式转化工艺、非催化部分氧化工艺、自热式转化工艺等[2-3]。
为提高陕西省天然气管网冬季调峰保障能力,满足产品多元化发展的需求,陕西燃气集团拟在陕西富平县建设富平燃气综合利用项目。
天然气制合成气课件

蒸汽转化炉
利用蒸汽将天然气转化为合成气,是转化反应的核心设备。
燃烧器
为蒸汽转化炉提供热量,确保转化反应的顺利进行。
余热回收系统
回收转化反应产生的余热,提高能源利用效率。
合成气分离与提纯设备
1 2
冷凝器
将合成气中的水蒸气冷凝成液态水,便于后续分 离。
洗涤塔
用化学溶剂吸收合成气中的酸性气体,提高合成 气的纯度。
噪声控制
采取有效的隔音、降噪措施,降低生产过程中产生的噪声对周围环境 的影响。
安全措施与事故预防
设备安全
防火防爆措施
确保设备运行稳定、安全可靠,定期进行 维护和检修,防止设备故障引发的事故。
严格控制可燃物料的储存和使用,采取有 效的防火防爆措施,防止火灾和爆炸事故 的发生。
应急预案
ห้องสมุดไป่ตู้
安全培训与教育
制定完善的事故应急预案,明确应急处置 流程和责任人,确保在事故发生时能够迅 速、有效地进行处置。
多元化原料来源
拓展天然气制合成气的原料 来源,如煤、生物质等,实 现多元化原料供应,降低对 单一资源的依赖。
技术经济性
提高天然气制合成气的技术 经济性,降低生产成本,增 强市场竞争力,是推动该技 术发展的重要因素。
THANKS
感谢观看
原料成本
天然气作为原料,其价格波动对成本有直接影响。
加工成本
包括催化剂、能源消耗、设备维护等费用。
运输和销售成本
将合成气运输到目标市场的费用,以及销售过程中的费用。
天然气制合成气的市场竞争力分析
市场需求
01
合成气作为化工原料,市场需求稳定增长。
竞争状况
02
与其他合成气生产技术相比,天然气制合成气的竞争力分析。
解吸气部分替代天然气制合成气可行性分析

2 0 1 3年 3月
化
学
工
程
Vo 1 . 41 No. 3 Ma r .2 01 3
C H E MI C A L E N G I N E E R I N G ( C H I N A)
解 吸气 部 分 替 代 天 然 气 制 合 成气 可行 性 分 析
Abs t r a c t : Ac c o r di ng t o t he g a s i ic f a t i o n p r o c e s s o f n a t u r l a g a s pa r t l y r e p l a c e d b y de s o r b e d g a s t o p r o d uc e t h e s y ng a s u s e d i n s y n t he t i c a mmo n i a, t h e ma t h e ma t i c a l mo d e l o f t h i s p r o c e s s wa s e s t a b l i s h e d, b a s e d o n As p e n Pl us s o f t wa r e, t h e g a s i ic f a t i o n p r o c e s s o f t wo k i n d s o f f e e d g a s wa s s i mul a t e d, a n d t h e f e a s i b i l i t y o f n a t u r l a g a s p a r t l y r e p l a c e d b y
济性优势 。
关键词 : 解析气 ; A s ቤተ መጻሕፍቲ ባይዱ e n P l u s ; 合成氨
能源化工—第15章 天然气转化制合成气

salt Natrural gas Petroleum
第15章 天然气转化制合成气
第15章 天然气转化制合成气
一段转化 二段转化
图13-3 榆天化工艺图
第15章 天然气转化制合成气
图13-4 一段转换炉
图13-5 二段转换炉
第15章 天然气转化制合成气
第15章 天然气转化制合成气
第15章 天然气转化制合成气 15.4 天然气制氢生产工艺
图15.3 Lurgi联合转化工艺流程图
顺次进行蒸汽转化及自热转化反应。
第15章 天然气转化制合成气
15.3.2 Uhde CAR工艺 15.3.3 Topsoe ATR工艺
图15.4 CAR反应器结构示意图
图15.5 ATR反应器结构示意图
将两种转化集于一个反应器内以降低投资和提高能源效率,ATR反应器更 简单而更具应用前景。
第15章 天然气转化制合成气
15.2 天然气的部分氢化
15.2.1 反应原理
第15章 天然气转化制合成气
(2)工艺参数的影响 1)温度。非催化条件下要使CH4获得完全转化,温度需
高于1200℃;使用催化剂,有可能使温度显著降低,从而大
大降低能耗并抑制析炭反应。 2)压力。作为分子数增加的反应,压力的升高是不利的。 但这决定于总体安排。 3)氧比。按化学汁量关系氧比应为0.5、随比上升,温度
下运行,并达到90%以上的热力学平衡转化。CO和H2的选择性高达95 %。基本避免了高温非催化部分氧化工艺伴生的燃烧生成CO2的反应, 能耗大幅降低.制得的合成气H2/CO比接近2。 与蒸汽转化和联合转化相比,反应器体积小、效率高、能耗低,投 资和合成气成本可显著降低。 天然气催化部分氧化的首要关键是催化剂,现主要集中在过渡金属 (Ni,Co和Fe)及贵金属(Pt族金属),避免积炭是研究重心。此外, 由于在上况条件下(高温、高压及CH4/O2=2),体系处于燃烧和爆炸 极限内,需解决安全问题。由于部分氧化反应的高放热性质,防止催化
天然气制备合成气工艺
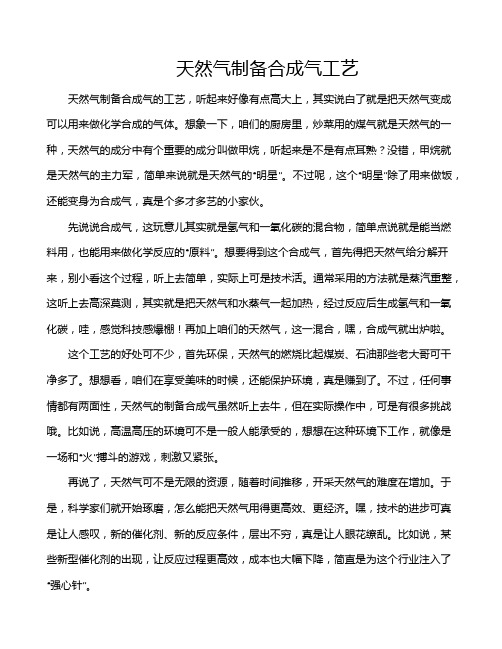
天然气制备合成气工艺天然气制备合成气的工艺,听起来好像有点高大上,其实说白了就是把天然气变成可以用来做化学合成的气体。
想象一下,咱们的厨房里,炒菜用的煤气就是天然气的一种,天然气的成分中有个重要的成分叫做甲烷,听起来是不是有点耳熟?没错,甲烷就是天然气的主力军,简单来说就是天然气的“明星”。
不过呢,这个“明星”除了用来做饭,还能变身为合成气,真是个多才多艺的小家伙。
先说说合成气,这玩意儿其实就是氢气和一氧化碳的混合物,简单点说就是能当燃料用,也能用来做化学反应的“原料”。
想要得到这个合成气,首先得把天然气给分解开来,别小看这个过程,听上去简单,实际上可是技术活。
通常采用的方法就是蒸汽重整,这听上去高深莫测,其实就是把天然气和水蒸气一起加热,经过反应后生成氢气和一氧化碳,哇,感觉科技感爆棚!再加上咱们的天然气,这一混合,嘿,合成气就出炉啦。
这个工艺的好处可不少,首先环保,天然气的燃烧比起煤炭、石油那些老大哥可干净多了。
想想看,咱们在享受美味的时候,还能保护环境,真是赚到了。
不过,任何事情都有两面性,天然气的制备合成气虽然听上去牛,但在实际操作中,可是有很多挑战哦。
比如说,高温高压的环境可不是一般人能承受的,想想在这种环境下工作,就像是一场和“火”搏斗的游戏,刺激又紧张。
再说了,天然气可不是无限的资源,随着时间推移,开采天然气的难度在增加。
于是,科学家们就开始琢磨,怎么能把天然气用得更高效、更经济。
嘿,技术的进步可真是让人感叹,新的催化剂、新的反应条件,层出不穷,真是让人眼花缭乱。
比如说,某些新型催化剂的出现,让反应过程更高效,成本也大幅下降,简直是为这个行业注入了“强心针”。
合成气还可以通过后续反应,转化成其他有价值的化学品,比如说甲醇、氨等,听起来是不是很诱人?想象一下,天然气变身成合成气,再转化成你平时用的化学产品,仿佛天然气在演绎一场华丽的“变身秀”。
所以说,天然气的制备合成气,不仅仅是一个简单的过程,更是一个神奇的化学旅程。
天然气制甲醇合成气工艺探讨

天然气制甲醇合成气工艺探讨摘要:天然气制甲醇合成气是当前燃料开发和发展中的重要方式,天然气合成气所应用的主要工艺为水蒸气催化法,这种方式工艺简单,操作容易,但是由于能耗和投资较大,使得其不适用于天然气制甲醇合成气。
本文主要对天然气制甲醇合成气的工艺进行分析,并提出各种工艺的优缺点。
关键词:天然气;甲醇合成气;工艺甲醇是工业生产中的重要原料,具有非常广泛的工艺用途。
但是随着甲醇工业的发展以及需求的增大,甲醇能源的需求量也不断的提升。
所以当前甲醇的生产具有巨大的发展空间。
合成甲醇的反应气成份包括氢气,一氧化碳、二氧化碳等混合气体。
当前工业甲醇的合成方式比较多,但是每种生产方式都具有一定的优缺点,为了实现节约能源,提升经济效益的目的,还需进一步对甲醇合成工艺分析,探索更多的工艺方法,提升甲醇合成气的生产效率。
一、天然气与二氧化碳结合利用一段蒸汽转化利用天然气与二氧化碳或蒸汽进行的转化工艺,是生成合成气的主要工艺形式,在操作中需在催化剂、高温条件下进行,生成一氧化碳、二氧化碳、氢气等混合气体,在这个反应中需要吸收大量的热量,所以必须要有外界供热。
但是在具体的工艺反应中,合成气会产生氢过量的情况[1]。
具体反应方程式如下:CH4+H2O→CO+3H2CH4+2H20→CO2+4H2CH4+CO2→2CO+2H2CO+H2O→CO2+H2最后的合成反应为:CO+2H2→CH3OHCO2+3H2→CH3OH+H2O由此可见,无论是与一氧化碳的反应还是与二氧化碳的反应,在生成1mol甲醇的同时都会产生1mol的氢气,对于这些多余的氢气必须要通过分离的方式进行清除,或者继续补入二氧化碳。
二氧化碳的添加量可以有效的节约天然气,降低生产能耗。
利用天然气蒸汽工艺制造甲醇合成气,涉及到的工艺流程比较多,比较常用的方式有考洛格法、ICI法等,这几种方式在烧嘴以及炉型等方面存在比较大的差别,但是在工艺流程方面比较相似,都是采用转化炉、余热回收以及原料预热等方式进行,所以当前这种工艺流程技术方面比较成熟。
- 1、下载文档前请自行甄别文档内容的完整性,平台不提供额外的编辑、内容补充、找答案等附加服务。
- 2、"仅部分预览"的文档,不可在线预览部分如存在完整性等问题,可反馈申请退款(可完整预览的文档不适用该条件!)。
- 3、如文档侵犯您的权益,请联系客服反馈,我们会尽快为您处理(人工客服工作时间:9:00-18:30)。
脱碳
变换
工艺流程充分合理地利用不同温位的余热,加热 各种物料和产生动力及工艺蒸汽。。
天然气蒸汽转化流程
天然气压缩到3.6MPa并配氢氮混合气,到一段炉的对流段3 预热至380~400℃,热源是辐射段4的高温烟道气。预热后 进钴钼催化脱硫器l,有机硫加氢成硫化氢,再到氧化锌脱 硫罐2脱除硫化氢,总含硫量降至0.5×10-6以下。脱硫后与 中压蒸汽混合,送至对流段加热到500~520℃,分流进入辐 射段4的转化管,自上而下经管内催化剂层转化反应,热量 由管外燃烧天然气提供。 反应管底部转化气温度为800~820℃,甲烷含量约9.5%,汇 合于集气管沿中心管上升,由炉顶送往二段转化炉5。二段 炉入口引入预热450℃的空气,与部分甲烷在炉顶燃烧,温 度升至1200℃,经催化剂层继续转化,二段炉出口转化气温 度约1000℃,压力3.0MPa,残余甲烷低于0.3%,(H2+CO)/ N2=3.1~3.2。二段炉出来高温转化气先后经二个废热锅炉 6,7,回收显热产生蒸汽.此蒸汽经对流段加热成高压过热蒸 汽,作为工厂动力和工艺蒸汽。转化气温度降至370℃,送 变换工段。
不同用途要求的合成气组成
用途 合成氨 合成甲醇 羰基合成高级醇 生产氢气 CO/ H2 1:3 1:2 1:1 H2>95%
一 合成气的应用实例 1. 已工业化的主要产品
(1)合成氨
N2 3H2 2NH3
20世纪初,德国人哈伯发明了由氢气和氮气直接合 成氨,并于1913年与博茨创建了合成氨工艺,由含 碳原料与水蒸气、空气反应制成含H2和N2的粗原 料气,再经精细地脱除各种杂质,得到H2:N2=3:l( 体积比)的合成氨精原料气,使其在500~600℃、 17.5~20MPa及铁催化剂作用下合成为氨。近年来 ,该过程已可在400~450℃、8~15MPa下进行。 •氨的最大用途是制氮肥,这是目前世界上产量最 大的化工产品之一,氨还是重要的化工原料。
(一)甲烷水蒸气转化反应和化学平衡
主反应
变换反应
CH 4 H 2O CO 3H 2 CH 4 2 H 2O CO2 4 H 2 CO H 2O CO2 H 2
H 298 206kJ / mol H 298 165kJ / mol
H 298 41.2kJ / mol
一 合成气的应用实例
合成气
合成气
NH3
改进的费托合成催化剂 锌、铬系催化剂 高压、380℃
乙烯、丙烯
合成气
甲醇
铑络合物-HI催化剂 3MPa,175℃
醋酸
铜、锌系催化剂 中低压、230-270℃
汽油、烯烃、芳烃 乙二醇 乙烯
甲醇 同系化 乙醇 合成气 + 丙烯醇 1,4-丁二醇
第二节
天然气制造合成气
B
蒸汽催化转化
CO+H2
2.45MPa,950~1030℃,H2/CO可在0.99~2.97间灵活调节,空速大
Sparg工艺 :关键解决热效应和催化剂结碳
CH4+CO2
Ni催化剂
2CO + 2H2 水蒸汽
△Hθ
298 K
= 247kJ/mol
CH4+CO2
预转化器
主转化反应器
预转化器:天然气中的C2和更重的烃,更易积炭,使用较
低温度、较高活性的未硫化催化剂(300~350℃),使其转化. 主转化器:硫钝化的Ni基催化剂,抗积炭,以防止H2偏低 造成积炭。 (900℃,0.7~1.2MPa)
利用烟道气预热加热各种物料
调节原料气的CO2/CH4和 H2O/CH4,保障 H2/CO 在1.8~2.7 之间
2. 天然气蒸汽转化过程工艺原理
0 1.4 2.8 3.5
16
反应压力影响
压力降低有利于甲烷转化, 但低压易使其分解析炭。 在蒸汽转化法的发展过程中 ,压力都在逐步提高,主要 原因是加压比常压转化经济 效果好。
反应压力 MPa 水碳比=2、T=800℃
低压,但实际高压。
甲烷蒸气转化催化剂
蒸汽转化活化能极大,T>1300℃才有工业应用 价值,但大量甲烷裂解析碳,反应选择性急剧降低 .
(2)合成甲醇
. CO 2 H 2 Cat CH 3OH
将合成气中H2/CO的摩尔比调整为2.2左右, 在260~270℃、5~10MPa及铜基催化剂作用 下可以合成甲醇。 甲醇可用于制醋酸、醋酐、甲醛、甲酸甲酯、 甲基叔丁基醚等产品;由甲酵脱水或者由合成 气直接合成生成的二甲醚(CH3OCH3),其十六 烷值高达60,是极好的柴油机燃料,燃烧时无 烟,NOx排放量极低,被认为是2l世纪新燃料 之一。此外,目前正在开发甲醇制汽油、甲醇 制低碳烯烃、甲醇制芳烃等过程。
CH 4 C 2 H 2
H 298 74.9kJ / mol H 298 172.5kJ / mol H 298 131.4kJ / mol
副反应 (析碳) 2CO C CO2
CO H 2 C H 2O
炭黑覆盖在催化剂表面,堵塞微孔,降 低催化剂活性。 影响传热,使局部反应区产生过热而缩
天然气制合成气
第一节 第二节 第三节
概
述
天然气制合成气 一氧化碳变换过程 二氧化碳的脱除
第四节
第一节 概述
料和生产方法不同而异,其H2/CO(mol)从0.5~3。
合成气(synthesis gas or syngas) CO和H2的混合物 — 合成气中H2和CO比例随原
用途 生产氢气; 生产CO; 有机合成原料之一 原料来源 煤、天然气、石油馏分、农林废料、城市垃圾
CH4 > 0.3% 3.0MPa
入口端:甲烷含量最高,着重抑制甲烷裂解析碳反应趋势,
故温度不宜过高, T ≤ 500℃; 因有催化剂,转化反应速率尚 可;析出的碳可及时气化,不会积碳;选择性好。
入口1/3处:温度≤650℃,在高活性催化剂存在下,大量甲烷
转化。
1/3处以后:T>650℃ ,H2增多, 可抑制裂解生碳,水碳比
影响甲烷蒸汽转化反应 平衡组成的因素
反应温度 水碳比 反应压力
反应温度的影响
甲烷平衡含量% 压力 (MPa) 1 2 800 870 870 950 5.0 2.0 1.0 温度 ℃ 910 1000 950 1030 1000 1100 0.5 0.2
4
940
1020
1080
1130
转化,最高温度800 ℃左右, 出口CH4约 10%(干基).
② 在较高温度下,耐火砖衬里的钢制圆筒,
可耐1000 ℃以上高温。加入氧气,利用反应 热继续甲烷转化反应。
CH4 ,H2O
500° C
650° C
CH4 >10% 800° 1100° C C O2
C 1000 °
3.6MPa 一段转化炉为变温反应器
2.75~ 2.5
(四)气流速度 气体流速高,提高生产能力;有利于传热,降低炉管外壁温 度,延长炉管寿命。但不宜过高,床层阻力增大,能耗增加. 碳空速:每立方米催化剂每小时通过甲烷的标准立方米数。 1000 ~2000h-1
天然气蒸汽转化流程和主要设备
水蒸气 空气或氧气
天然气
脱硫
一段转化
二段转化
合成气
(二)反应温度
气质要求: CH4<0.3%
3MPa下,若转化气中CH4≤ 0.3%(干基), 则要求T>1000 ℃。 3MPa下,目前耐热合金钢HK-40使用十年, T壁 ≤ 920℃ ,T内=800~820℃。
分段反应
(二)反应温度
解决方式-转化过程分段
① 在较低温度下,外热式转化管中进行蒸汽
天然气
优质、清洁、环境友好的能源。
一
以天然气为原料的生产方法
H (298K ) 206kJ / mol
水蒸气转化法 Steam reforming
CH 4 H 2O CO 3H 2
特点:目前工艺多采用的方法,H2/CO=3, 以天然气为原料的大型合成氨厂广泛采用。
强吸热反应
非催化部分氧化法 Partial oxidation
析 炭 危 害
短反应管使用寿命。
催化剂内表面炭与水蒸气反应,使催化
剂破碎,影响生产能力。
防止析碳的原则
第一,使转化过程不在热力学析碳的条件下进行,蒸汽 用量大于理论最小水碳比,是防止析碳的前提。 第二,选择适宜的操作条件。例如:原料的预热温度不 要太高,采用变温反应器。 第三,选用适宜的催化剂并保持活性良好。 第四,检查炉管内是否有积碳,可通过观察管壁颜色, 转化管内阻力增加,可帮助判断。当催化剂活性下 降时,可采用减少原料流量,提高水碳比等除碳。
(3)合成醋酸
CH 3OH CO CH 3COOH
首先将合成气制成甲醇,再将甲醇与CO羰基化合成 醋酸. 1960年.德国的BASF公司将甲醇羰基化合成醋酸的 工艺工业化,此法比正丁烷氧化法和乙醛氧化法工 艺更经济。BASF公司的工艺需要70MPa高压.醋酸 收率90%。1970年,美国Monsanto公司推出了低压 法工艺,开发出一种新型催化剂(碘化物促进的铑络 合物)使甲醇羰基化反应能在180℃和3~4 MPa的温 和条件下进行,醋酸收率高于99%,现已成为生产 工业醋酸的主要方法。并且,带动了有关羰基过渡 金属络合物催化作用的基础研究,促进了合成气化 学和C1化工的发展。
相对变大,消碳速率增加。
出口端:T=800℃,保证低甲烷残余量(10%)。 一段转化炉为变温反应器(防止CH4裂解,避免积 炭),二段转化炉温度更高(1050℃ ),CH4含量很 低,补充氧,更不会积碳。
(三)水碳比 高水碳比可控制析碳、降低甲烷平衡含量,但太大经济上不 合理,还增加热负荷。