热喷焊技术的应用综述
热喷涂技术应用与发展调研分析
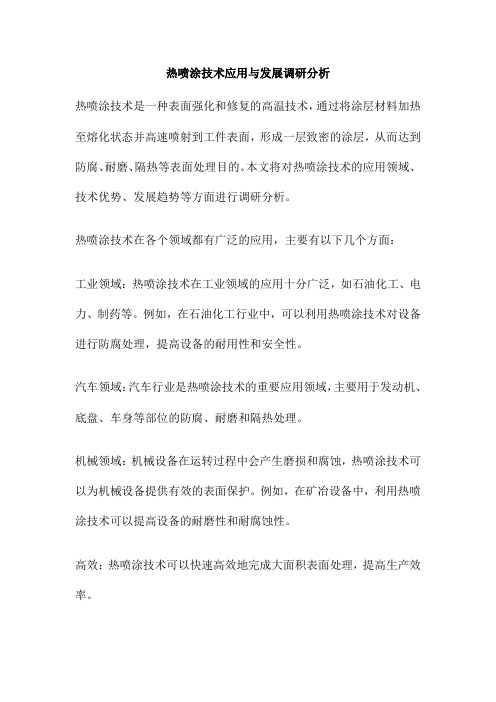
热喷涂技术应用与发展调研分析热喷涂技术是一种表面强化和修复的高温技术,通过将涂层材料加热至熔化状态并高速喷射到工件表面,形成一层致密的涂层,从而达到防腐、耐磨、隔热等表面处理目的。
本文将对热喷涂技术的应用领域、技术优势、发展趋势等方面进行调研分析。
热喷涂技术在各个领域都有广泛的应用,主要有以下几个方面:工业领域:热喷涂技术在工业领域的应用十分广泛,如石油化工、电力、制药等。
例如,在石油化工行业中,可以利用热喷涂技术对设备进行防腐处理,提高设备的耐用性和安全性。
汽车领域:汽车行业是热喷涂技术的重要应用领域,主要用于发动机、底盘、车身等部位的防腐、耐磨和隔热处理。
机械领域:机械设备在运转过程中会产生磨损和腐蚀,热喷涂技术可以为机械设备提供有效的表面保护。
例如,在矿冶设备中,利用热喷涂技术可以提高设备的耐磨性和耐腐蚀性。
高效:热喷涂技术可以快速高效地完成大面积表面处理,提高生产效率。
耐磨:热喷涂材料具有高硬度、高耐磨性等特点,可以延长设备的使用寿命。
防腐:热喷涂技术可以形成致密的涂层,有效防止腐蚀,提高设备的耐久性和安全性。
隔热:热喷涂技术可以形成一层隔热材料,有效降低设备表面的温度,提高设备的使用安全性。
经济:热喷涂技术成本较低,可以降低生产成本,提高经济效益。
随着科学技术的不断进步,热喷涂技术也在不断发展创新。
未来,热喷涂技术的发展趋势主要体现在以下几个方面:新材料的应用:随着新材料的不断涌现,热喷涂技术的材料选择范围也越来越广,未来将会有更多新型、高性能的材料应用于热喷涂技术中。
高能束技术的应用:高能束流技术如激光、等离子等在热喷涂技术中的应用将更加广泛。
这些技术的应用可以提高热喷涂层的结合强度和致密性,进一步提高表面处理的质量和效率。
智能化技术的应用:智能化技术在热喷涂技术中的应用将成为未来的发展趋势。
通过引入机器人和自动化技术,可以实现热喷涂过程的自动化和智能化控制,提高生产效率和产品质量。
热喷焊技术的应用综述
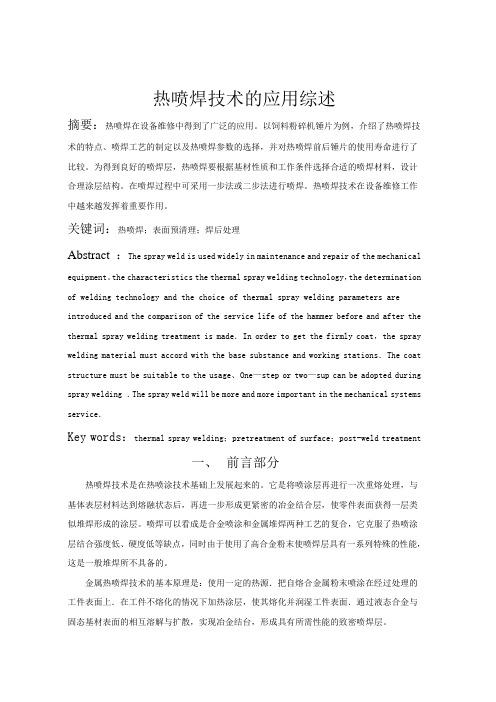
热喷焊技术的应用综述摘要:热喷焊在设备维修中得到了广泛的应用。
以饲料粉碎机锤片为例,介绍了热喷焊技术的特点、喷焊工艺的制定以及热喷焊参数的选择,并对热喷焊前后锤片的使用寿命进行了比较。
为得到良好的喷焊层,热喷焊要根据基材性质和工作条件选择合适的喷焊材料,设计合理涂层结构。
在喷焊过程中可采用一步法或二步法进行喷焊。
热喷焊技术在设备维修工作中越来越发挥着重要作用。
关键词:热喷焊;表面预清理;焊后处理Abstract :The spray weld is used widely in maintenance and repair of the mechanical equipment。
the characteristics the thermal spray welding technology,the determination of welding technology and the choice of thermal spray welding parameters are introduced and the comparison of the service life of the hammer before and after the thermal spray welding treatment is made.In order to get the firmly coat,the spray welding material must accord with the base substance and working stations.The coat structure must be suitable to the usage、One—step or two—sup can be adopted during spray welding .The spray weld will be more and more important in the mechanical systems service.Key words:thermal spray welding;pretreatment of surface;post-weld treatment一、前言部分热喷焊技术是在热喷涂技术基础上发展起来的。
热喷涂技术的原理及应用

热喷涂技术的原理及应用1. 热喷涂技术的原理热喷涂技术是一种通过将材料加热到熔化或半熔化状态,然后将其喷射到被涂覆物表面的技术。
热喷涂技术可以用于提高材料的表面性能,包括抗腐蚀性、耐磨性、耐热性等。
它广泛应用于航空航天、电子、冶金、化工、汽车、机械等领域。
1.1 热喷涂技术的分类热喷涂技术主要有以下几种分类:•火焰喷涂技术:使用火焰作为热源,将涂层材料加热到熔化或半熔化状态,并将其喷射到被涂覆物表面。
•等离子喷涂技术:使用等离子体作为热源,将涂层材料加热到熔化或半熔化状态,并将其喷射到被涂覆物表面。
•电弧喷涂技术:使用电弧作为热源,将涂层材料加热到熔化或半熔化状态,并将其喷射到被涂覆物表面。
•高速火焰喷涂技术:使用高速火焰作为热源,将涂层材料加热到熔化或半熔化状态,并将其喷射到被涂覆物表面。
1.2 热喷涂技术的工作原理热喷涂技术的工作原理可以简要概括为以下几个步骤:1.加热材料:将涂层材料加热到熔化或半熔化状态。
不同的热喷涂技术使用不同的加热源,如火焰、等离子体或电弧。
2.喷射材料:将加热到熔化或半熔化状态的涂层材料喷射到被涂覆物表面。
喷射可以通过喷枪或喷嘴来实现。
3.涂覆形成:涂层材料接触到被涂覆物表面后,由于温度差异,涂层材料会迅速冷却和凝固,形成涂层。
4.涂层熔合:涂层材料凝固后,可以进一步通过热处理或机械加工等方式,使其与被涂覆物表面充分结合。
2. 热喷涂技术的应用热喷涂技术在多个领域都有广泛的应用,主要包括以下几个方面:2.1 防腐领域热喷涂技术可以用于防腐,提高材料的耐蚀性。
热喷涂涂层可以形成致密的结构,能够有效隔离被涂覆物与外界环境的接触,保护被涂覆物不受腐蚀。
2.2 修复与修补领域热喷涂技术可以用于修复与修补受损物体的表面。
通过热喷涂涂层,可以提高受损物体的耐磨性、耐腐蚀性等性能,延长其使用寿命。
2.3 摩擦与磨损领域热喷涂技术可以用于提高材料的耐磨性。
通过热喷涂涂层,可以在材料表面形成硬质的陶瓷涂层,提高材料的摩擦性能和抗磨损性能。
热喷涂焊接技术在航空发动机中的应用

热喷涂焊接技术在航空发动机中的应用航空发动机是现代航空器的核心部件,其性能直接关系到飞机的安全和效率。
为了提高航空发动机的工作效率和寿命,热喷涂焊接技术被广泛应用于航空发动机的制造和维修中。
热喷涂焊接技术是一种将金属粉末或线材喷涂在工件表面并进行熔化的方法,通过高速喷射的热能将金属材料与工件表面融合,形成一层坚固的涂层。
这种技术可以在航空发动机的叶片、涡轮、燃烧室等关键部件上应用,以提高其耐磨、耐腐蚀和高温性能。
首先,热喷涂焊接技术可以用于航空发动机叶片的修复和保护。
航空发动机叶片是承受高温、高速气流和离心力的重要部件,容易受到磨损和腐蚀的影响。
通过热喷涂焊接技术,在叶片表面形成一层高温合金涂层,可以有效地提高叶片的耐磨性和耐腐蚀性,延长叶片的使用寿命。
此外,热喷涂焊接技术还可以修复受损的叶片,使其恢复原有的性能。
其次,热喷涂焊接技术可以用于航空发动机涡轮的制造和修复。
航空发动机涡轮是将燃气能转化为机械能的重要部件,工作环境严苛,容易受到高温和高速气流的侵蚀。
通过热喷涂焊接技术,可以在涡轮叶片和叶盘表面形成一层高温合金涂层,提高涡轮的耐磨性和耐高温性,同时减轻涡轮的重量,提高发动机的效率。
此外,热喷涂焊接技术还可以用于航空发动机燃烧室的制造和维修。
航空发动机燃烧室是燃烧燃料的关键部件,工作环境高温、高压,容易受到高温气体和化学物质的侵蚀。
通过热喷涂焊接技术,在燃烧室内壁形成一层高温合金涂层,可以提高燃烧室的耐热性和耐腐蚀性,延长燃烧室的使用寿命。
总之,热喷涂焊接技术在航空发动机中的应用具有重要的意义。
通过这种技术,可以提高航空发动机的工作效率和寿命,减少维修成本,提高飞机的安全性和经济性。
未来,随着科学技术的不断发展,热喷涂焊接技术在航空发动机中的应用将会得到进一步的拓展和完善,为航空工业的发展做出更大的贡献。
热喷涂技术及其在材料领域的应用
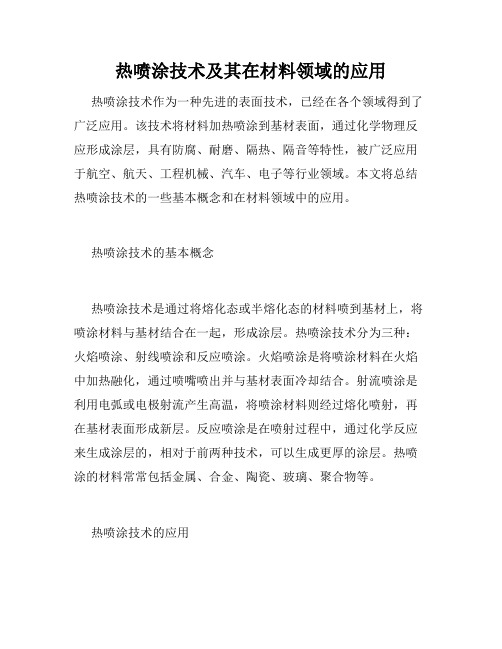
热喷涂技术及其在材料领域的应用热喷涂技术作为一种先进的表面技术,已经在各个领域得到了广泛应用。
该技术将材料加热喷涂到基材表面,通过化学物理反应形成涂层,具有防腐、耐磨、隔热、隔音等特性,被广泛应用于航空、航天、工程机械、汽车、电子等行业领域。
本文将总结热喷涂技术的一些基本概念和在材料领域中的应用。
热喷涂技术的基本概念热喷涂技术是通过将熔化态或半熔化态的材料喷到基材上,将喷涂材料与基材结合在一起,形成涂层。
热喷涂技术分为三种:火焰喷涂、射线喷涂和反应喷涂。
火焰喷涂是将喷涂材料在火焰中加热融化,通过喷嘴喷出并与基材表面冷却结合。
射流喷涂是利用电弧或电极射流产生高温,将喷涂材料则经过熔化喷射,再在基材表面形成新层。
反应喷涂是在喷射过程中,通过化学反应来生成涂层的,相对于前两种技术,可以生成更厚的涂层。
热喷涂的材料常常包括金属、合金、陶瓷、玻璃、聚合物等。
热喷涂技术的应用航空在航空领域,热喷涂技术可以增强飞机结构的强度和刚度,提供耐热、抗腐蚀、防氧化等性能。
在发动机的高压涡轮中,热喷涂可以对叶片进行保护,延长使用寿命。
同时,热喷涂技术还可以在飞机的液压阀、液压管道和传动部分上形成保护层,减少磨损和碰撞损坏。
电子在电子行业,热喷涂技术可以提供防静电、隔热、隔音、导电性等特性。
例如,在太阳能电池板的背面上,可以喷涂一层导电涂层,以确保电池板受到充分利用,提高太阳能电池的效率。
同时,在手机、电脑等大量使用的电子设备中,热喷涂技术还可以用于防止某些塑料部件损坏,例如键盘按钮和鼠标轨迹球等,使它们保持其原因样子的同时,又具有一定的耐腐蚀性和耐磨性。
工业热喷涂技术可用于工业领域的各个方面。
例如,在工程机械制造中,热喷涂技术可以用于制造防护层,避免运输过程中腐蚀或受损。
在建筑领域,也可以利用热喷涂技术来加强防护能力,例如使用热喷涂的防水材料对外墙涂层进行保护。
汽车最后,热喷涂技术在汽车行业中也得到了广泛应用。
通过涂覆车体涂层,汽车可以具有高温和抗腐蚀等特性,同时也可以增强车体的强度和刚度。
热喷涂文献综述
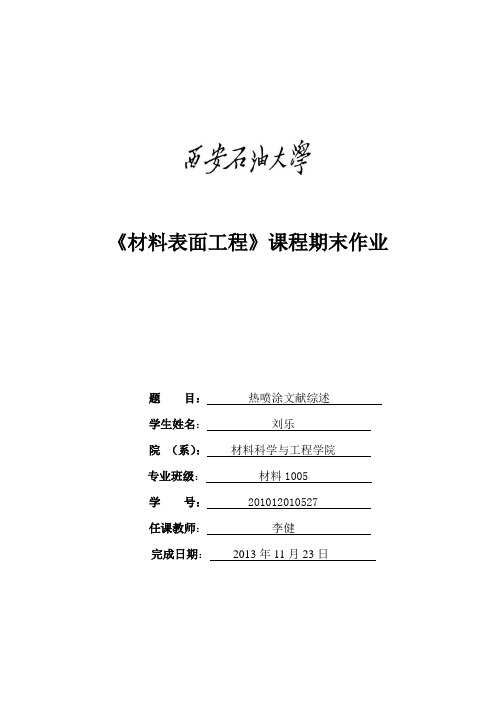
《材料表面工程》课程期末作业题目:热喷涂文献综述****:**院(系):材料科学与工程学院专业班级:材料1005学号: ****************:**完成日期:2013年11月23日一前言 (2)二基本原理及工艺过程 (3)三热喷涂的基本分类 (4)四热喷涂技术的应用 (5)4.1喷涂耐腐浊涂层 (5)4.2喷涂耐磨涂层 (5)4.3喷涂耐高温涂层 (5)4.4喷涂功能涂层 (5)4.5喷涂成型 (5)五热喷涂的优缺点 (6)5.1 优点 (6)5.2 缺点 (6)六热喷涂技术的发展趋势 (7)6.1工艺 (7)6.2材料 (7)参考文献 (9)高新技术的飞速发展对提高金属材料的性能、延长仪器设备中零部件的使用寿命提出了越来越高的要求。
而这两个方面的要求又面临高性能结构材料成本逐年上升的问题。
近年来,表面工程发展很快,尤其是热喷涂技术获得了巨大的进展,为解决上述问题提供了一种新的方法。
热喷涂是一种通过专用设备把某种固体材料熔化并加速喷射到机件表面上,形成一种特制薄层,以提高机件耐蚀、耐磨、耐高温等性能的表面工程技术[1]。
由于热喷涂技术可以喷涂各种金属及合金、陶瓷、塑料及非金属等大多数固态工程材料,所以能制成具备各种性能的功能涂层,并且施工灵活,适应性强,应用面广,经济效益突出,尤其对提高产品质量、延长产品寿命、改进产品结构、节约能源、节约贵重金属材料、提高工效、降低成本等方面都有重要作用。
随着工业和科技的发展,人们对热喷涂技术提出了越来越高的要求,在已有的热喷涂工艺不断得到改进的同时,一些新的工艺也应运而生。
目前,包括航空、航天、原子能设备、电子等尖端技术在内的很多领域内[2]热喷涂技术都得到了广泛的应用,并取得了良好的经济效益。
二基本原理及工艺过程热喷涂技术是通过某种热源将某些材料加热至熔融或半熔融状态,然后喷射到涂敷的基体表面,形成一层性能优于原来基体的涂层,从而使原工件具有更加优异的表面性能,或者是使工件获得一种或几种原来基体材料不具备的表面性能膜状组织[3]。
热喷涂技术综述

热喷涂综述一、热喷涂的定义热喷涂技术,是采用某种高温热源,将欲涂覆的涂层材料熔化或至少软化,并用气体使之雾化成微细液滴或高温颗粒,高速喷射到经过预处理的基体表面形成涂层的技术。
当热源的比能量足以使基体表面发生薄层熔化,与喷射的熔融颗粒形成完全致密的冶金结合涂层时,称为热喷焊,简称喷焊。
使用高温热源,如氧——可燃气体燃烧火焰、电弧、等离子电弧、激光束、爆炸能等,是热喷涂技术区别于其他喷涂方法和表面涂覆方法的主要特征。
不同热源的最高温度列于附表。
附表:不同热源的最高温度二、热喷涂技术的特点采用热喷涂技术,制备各种表面强化和表面防护涂层,具有许多独特的优点。
(1)能够喷涂的材料范围特别广,包括各种金属及合金、陶瓷及金属陶瓷、塑料、非金属矿物等几乎所有固态工程材料。
因而能够制备耐磨、减摩、耐蚀、耐高温、抗氧化、绝缘、导电、催化、辐射、防辐射、抗干扰、超导、非晶态及生物功能等各种功能涂层;(2)能够在多种基体材料上形成涂层,包括金属基体、陶瓷基体、塑料基体、石膏、木材甚至纸板上都能喷涂,被喷涂的材料范围也十分广泛;(3)一般不受被喷涂工件尺寸和施工场所的限制,既可厂内施工,也可现场施工;(4)涂层沉积效率较高,特别适合沉积薄膜涂层。
涂层厚度可以控制,从几十微米到几毫米甚至可厚达20mm;(5)除喷焊外,热喷涂施工对基体的热影响很小,基体受热温度不超过200℃,基体不会发生变形和性能变化;(6)在满足强度要求的前提下,制件基体可以采用普通材料代替贵重材料,仅涂层使用优质材料,使“好钢用在刀刃上”;(7)热喷涂施工艺灵活,方便,迅速,适应性强。
当然,热喷涂技术也有如下一些缺点。
(1)除喷焊外,热喷涂涂层与基体的结合主要是物理机械结合,结合强度不大高,涂层耐冲击和重载性能较差;(2)喷涂涂层含有不同程度的孔隙,对于耐腐蚀、抗氧化、绝缘等应用,一般不如整体材料。
但可通过复合涂层系统设计等方法予以改进提高;(3)喷涂小件时,涂层材料的收得率低;(4)热喷涂手工操作时的劳动条件较差,有噪音、粉尘、热和弧光辐射问题,必须注意劳动保护措施。
焊接中的热喷涂焊技术

焊接中的热喷涂焊技术焊接是工业生产中必不可少的一环,而热喷涂焊技术则是其中的一种。
热喷涂焊技术是一种将焊缝补强的方式,通常使用的材料是金属或者陶瓷粉末。
该技术的应用范围非常广泛,包括工业领域、汽车制造、建筑结构、航空航天、船舶制造等众多领域。
一、热喷涂焊技术的基本原理热喷涂焊技术的基本原理是利用热喷涂焊机,将金属或陶瓷粉末喷射到需要加强的焊缝表面上。
粉末被喷射后,会在钢铁表面上形成一层坚硬的薄壳,并与基材结合形成一种特殊的焊缝结构。
其实,热喷涂焊技术形成的薄壳并不是真正的它,而是一些特殊的化合物,比如说氧化物、氯化物、氟化物等。
这些化合物能够帮助金属或陶瓷粉末更好的与基材表面结合。
经过一系列硬化、淬火等工艺后,最终形成一种非常牢固的焊缝结构。
二、热喷涂焊技术的分类热喷涂焊技术按喷涂方式分为以下几个类别:1. 等离子喷涂:使用等离子灯将金属或陶瓷材料加热成等离子体,然后通过气体的驱动将等离子体喷射到需要加强的焊缝表面上。
2. 弧喷涂:使用高温的电弧将金属或陶瓷材料熔化,然后通过气体的驱动将熔融金属或陶瓷材料喷射到需要加强的焊缝表面上。
3. 火焰喷涂:使用燃气将金属或陶瓷材料加热至熔化状态,然后通过气体的驱动将熔融金属或陶瓷材料喷射到需要加强的焊缝表面上。
4. 冷喷涂:使用压缩空气将金属或陶瓷材料喷射到需要加强的焊缝表面上,然后通过焊后加热硬化工艺使之达到加强效果。
三、热喷涂焊技术的应用热喷涂焊技术应用非常广泛,随着科技的不断进步,其应用范围也越来越广泛,下面列举几个领域的应用:1. 汽车制造:在汽车制造领域,热喷涂技术通常用于汽车零部件如气门座、汽缸及飞轮等的修复和加固。
2. 航空航天领域:在航空航天领域,热喷涂技术通常用于飞机发动机、火箭喷管、液压组件及导弹等部件的加强和修复。
3. 建筑领域:在建筑领域,热喷涂技术不仅用于加强临时建筑物结构,还广泛应用于钢结构、桥梁及地下管道等方面的加强和防腐。
热喷涂(焊)技术在设备维修中的应用

简单
简单
少
较复杂
较少
复 杂
多
零件表 面 , 以达到延长 易磨 损零件使用寿命 , 可 降低 维
修费用 , 减少设备停机时 间及提高生产效率的 目的。 设备在使 用过程中 ,由于零件表面磨损 和腐 蚀而 引起 的早期失效及报废所造 成的材料损失是 十分惊 人 的。据有关部 门不完全统计 , 我国每年 因零部件磨损所 造成 的损失达 4 0 0 亿元 ,因腐蚀 而造成的损失也将 近 20 0 亿元 。因此 , 复因表面磨损 和腐蚀而造 成失效 的 修 零部件成为设备维修 工作中遇到最多 的问题 。要恢 复 失效零件 的表面性能 , 到经 济有效 的维修 , 做 首先应 分 析其失效的原 因, 明确失效 的类 型 , 从而达到合理选择 材料 , 运用正确修复方法的 目的。
表 1 设 备 维 修 中 常用 的 热 喷涂 、 喷 焊技 术 的 主 要特 点 热
氧乙 炔火熔喷 氧乙 涂 炔火熔喷 焊 金属电弧 喷涂 等 离子喷 涂
广泛的应用 , 并取得了显著 的经济效益 。在设备维修过 程 中, 应用热喷涂( ) 焊 技术修复某些严重磨损或腐蚀的
设 备
投 资 喷 涂材料 表面 预处理 工 件表面温 度 涂 层厚度/m m 结 合强度/P Ma 涂 c 层孑隙度/ %
重熔处理 , 涂层 致密化 的一种方法 。因此 , 使 采用这两 喷涂 层与喷焊层。
热喷涂技术按所采 用的热源类型不 同主要 分为氧 乙炔火焰喷涂 、 金属 电弧喷涂和等离子喷涂 ; 喷焊则 热 有氧 乙炔火焰 喷焊及 相应的加热重熔技术 ,如炉内生
第3卷 6
第 l 期 0
林 业 机 械 与 木 工 设 备
F R S R C I E Y & WO D R I G E U P E T O E T Y MA H N R O WO KN Q IM N
热喷涂技术的应用
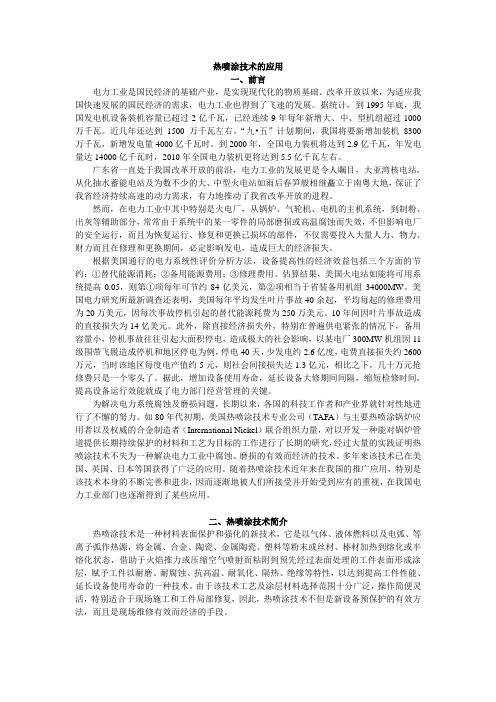
热喷涂技术的应用一、前言电力工业是国民经济的基础产业,是实现现代化的物质基础。
改革开放以来,为适应我国快速发展的国民经济的需求,电力工业也得到了飞速的发展。
据统计,到1995年底,我国发电机设备装机容量已超过2亿千瓦,已经连续9年每年新增大、中、型机组超过1000万千瓦。
近几年还达到1500万千瓦左右。
“九•五”计划期间,我国将要新增加装机8300万千瓦,新增发电量4000亿千瓦时。
到2000年,全国电力装机将达到2.9亿千瓦,年发电量达14000亿千瓦时,2010年全国电力装机更将达到5.5亿千瓦左右。
广东省一直处于我国改革开放的前沿,电力工业的发展更是令人瞩目,大亚湾核电站,从化抽水蓄能电站及为数不少的大、中型火电站如雨后春笋般相继矗立于南粤大地,保证了我省经济持续高速的动力需求,有力地推动了我省改革开放的进程。
然而,在电力工业中其中特别是火电厂,从锅炉、气轮机、电机的主机系统,到制粉、出灰等辅助部分,常常由于系统中的某一零件的局部磨损或高温腐蚀而失效,不但影响电厂的安全运行,而且为恢复运行、修复和更换已损坏的部件,不仅需要投入大量人力、物力、财力而且在修理和更换期间,必定影响发电,造成巨大的经济损失。
根据美国通行的电力系统性评价分析方法,设备提高性的经济效益包括三个方面的节约:①替代能源消耗;②备用能源费用;③修理费用。
估算结果,美国火电站如能将可用系统提高0.05,则第①项每年可节约84亿美元,第②项相当于省装备用机组34000MW。
美国电力研究所最新调查还表明,美国每年平均发生叶片事故40余起,平均每起的修理费用为20万美元,因每次事故停机引起的替代能源耗费为250万美元。
10年间因叶片事故造成的直接损失为14亿美元。
此外,除直接经济损失外,特别在普遍供电紧张的情况下,备用容量小,停机事故往往引起大面积停电,造成极大的社会影响,以某电厂300MW机组因11级围带飞脱造成停机和地区停电为例,停电40天,少发电约2.6亿度,电费直接损失约2600万元,当时该地区每度电产值约5元,则社会间接损失达1.3亿元,相比之下,几十万元抢修费只是一个零头了。
热喷焊技术的研究综述
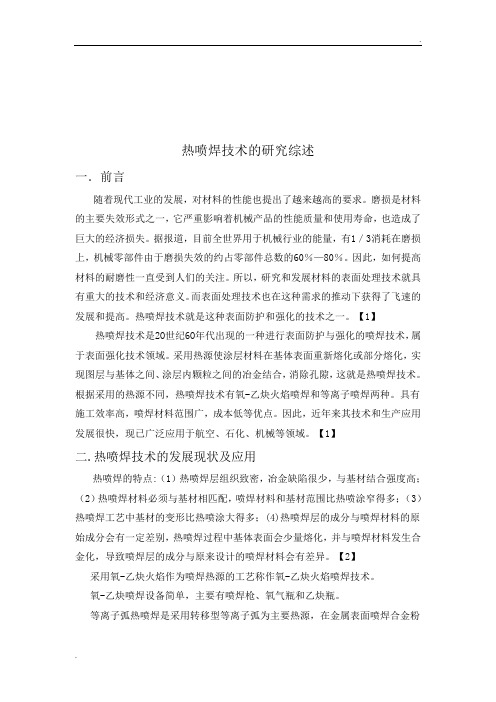
热喷焊技术的研究综述一.前言随着现代工业的发展,对材料的性能也提出了越来越高的要求。
磨损是材料的主要失效形式之一,它严重影响着机械产品的性能质量和使用寿命,也造成了巨大的经济损失。
据报道,目前全世界用于机械行业的能量,有1/3消耗在磨损上,机械零部件由于磨损失效的约占零部件总数的60%—80%。
因此,如何提高材料的耐磨性一直受到人们的关注。
所以,研究和发展材料的表面处理技术就具有重大的技术和经济意义。
而表面处理技术也在这种需求的推动下获得了飞速的发展和提高。
热喷焊技术就是这种表面防护和强化的技术之一。
【1】热喷焊技术是2O世纪6O年代出现的一种进行表面防护与强化的喷焊技术,属于表面强化技术领域。
采用热源使涂层材料在基体表面重新熔化或部分熔化,实现图层与基体之间、涂层内颗粒之间的冶金结合,消除孔隙,这就是热喷焊技术。
根据采用的热源不同,热喷焊技术有氧-乙炔火焰喷焊和等离子喷焊两种。
具有施工效率高,喷焊材料范围广,成本低等优点。
因此,近年来其技术和生产应用发展很快,现已广泛应用于航空、石化、机械等领域。
【1】二.热喷焊技术的发展现状及应用热喷焊的特点:(1)热喷焊层组织致密,冶金缺陷很少,与基材结合强度高;(2)热喷焊材料必须与基材相匹配,喷焊材料和基材范围比热喷涂窄得多;(3)热喷焊工艺中基材的变形比热喷涂大得多;(4)热喷焊层的成分与喷焊材料的原始成分会有一定差别,热喷焊过程中基体表面会少量熔化,并与喷焊材料发生合金化,导致喷焊层的成分与原来设计的喷焊材料会有差异。
【2】采用氧-乙炔火焰作为喷焊热源的工艺称作氧-乙炔火焰喷焊技术。
氧-乙炔喷焊设备简单,主要有喷焊枪、氧气瓶和乙炔瓶。
等离子弧热喷焊是采用转移型等离子弧为主要热源,在金属表面喷焊合金粉未的方法。
一般采用两台整流电源,将负极并联在一起,通过电缆接至喷枪的电极,其中一台电源的正极接喷枪的喷嘴,用于产生非转移弧;另一台电源的正极接工件,用于产生转移弧。
热喷涂技术的现状及应用

热喷涂技术的现状及应用(总6页)本页仅作为文档页封面,使用时可以删除This document is for reference only-rar21year.March热喷涂技术的现状及在锅炉管道方面的应用摘要:热喷涂技术作为材料表面强化、保护和尺寸恢复的新技术,在设备维修、机械制造中得到广泛应用,尤其在电厂部件的修复和维护中得到充分体现。
本文对热喷涂技术进行了简单介绍,综述了该技术在锅炉管道部件的应用。
大力提倡和发展热喷涂技术,在电力工业中具有巨大的应用价值和广阔的市场前景,必将带来愈来愈大的社会和经济效益。
关键词:热喷涂技术;材料表面强化;锅炉管道1 引言电力工业是国民经济的基础,承担着为各行各业和人民生活提供高效、清洁能源的重要任务。
近年来,随着国民经济的飞速发展,使我国对电力的需求日益剧增,特别是南方一些经济发达城市,在炎暑的用电高峰期拉闸限电现象频频发生。
为满足国民经济发展对电力的需求,全国各地兴建了不少电厂,旧电厂也纷纷进行扩容改造。
随着越来越多的高参数、大容量机组投入运行,锅炉受热面的运行工况更为苛刻。
我国目前还是一个以火电发电为主的国家,为使煤炭资源得以充分合理的利用,在电站锅炉中大量使用高含灰量的劣质煤,随着灰分不断升高、热值不断降低,锅炉受热面产生磨损、积灰、结渣、腐蚀等一系列问题,受热面使用寿命降低,锅炉管道爆漏现象频繁。
因此,我们必须尽快找到解决锅炉“四管”爆漏问题的可行方法。
表面处理工艺是指在基体材料表面上人工形成一层与基体的机械、物理和化学性能不同的表层的工艺方法。
它运用物理、化学或物理化学等技术手段来改变材料及其制件表面成份和组织结构,其特点是保持基体材料固有的特征,又赋予表面化所要求的各种性能,从而适应各种技术和服役环境对材料的特殊要求。
最大的优势在于能以极少的材料和能源消耗制备出基体材料难以甚至无法获得的性能优异的表面薄层,从而获得最大的经济效益。
所以我们选用表面处理的方法来解决锅炉“四管”爆漏问题。
热喷涂焊接工艺简介

热喷涂焊接工艺简介热喷涂焊接工艺是一种常用的金属加工技术,用于在工业领域中加强材料表面的耐磨性、耐蚀性和耐高温性能。
本文将简要介绍热喷涂焊接工艺的原理、应用和优势。
一、原理热喷涂焊接工艺是指将金属或陶瓷材料加热至熔点后,通过高速喷涂的方式将其喷射到工件表面形成涂层。
这种工艺利用高温熔融材料与基材表面反应,使涂层与基材牢固结合,从而起到加强表面性能的作用。
二、应用领域热喷涂焊接工艺在各个工业领域中都有广泛的应用。
以下是几个典型的应用领域:1. 航空航天领域:热喷涂焊接技术能够提高飞机发动机的耐磨性和耐高温性能,延长发动机的使用寿命和可靠性。
2. 石油化工领域:在石油化工设备中,热喷涂焊接技术可用于抗硫化物腐蚀的防护,提高设备的耐腐蚀性。
3. 电力行业:热喷涂焊接技术可用于电力设备的绝缘保护、耐污性提升和导热性能的增强。
4. 汽车制造业:热喷涂焊接技术在汽车制造业中可以应用于发动机气缸壁、活塞环和涡轮叶片等部件的表面处理,提高汽车性能。
三、优势热喷涂焊接工艺相比其他表面处理工艺具有以下优势:1. 多材料选择:热喷涂焊接工艺可使用多种金属或陶瓷材料进行涂层制备,以满足不同需求。
2. 高粘附性:热喷涂焊接涂层与基材的结合力强,具有良好的粘附性和耐久性。
3. 表面改性效果显著:通过热喷涂焊接工艺,可以在表面形成薄而坚固的涂层,改善材料的耐磨性、耐腐蚀性和耐高温性。
4. 工艺灵活性:热喷涂焊接工艺可以适应不同工件的形状和尺寸,具有较高的工艺适应性。
总结:热喷涂焊接工艺作为一种常用的表面处理技术,广泛应用于航空航天、石油化工、电力和汽车制造等领域。
其原理简单,应用灵活性强,能够显著提升材料表面的性能。
随着工艺的不断发展和创新,相信热喷涂焊接工艺将在未来继续扮演重要的角色,为各个行业提供更优质的解决方案。
热喷涂技术在火电行业的应用
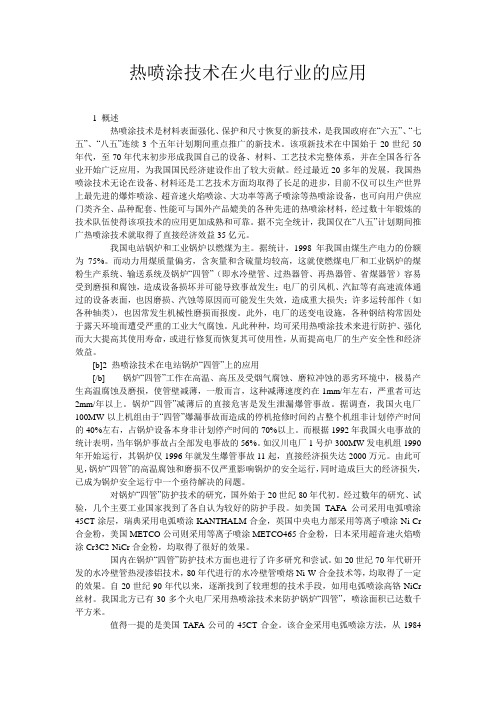
热喷涂技术在火电行业的应用1 概述热喷涂技术是材料表面强化、保护和尺寸恢复的新技术,是我国政府在“六五”、“七五”、“八五”连续3个五年计划期间重点推广的新技术。
该项新技术在中国始于20世纪50年代,至70年代末初步形成我国自己的设备、材料、工艺技术完整体系,并在全国各行各业开始广泛应用,为我国国民经济建设作出了较大贡献。
经过最近20多年的发展,我国热喷涂技术无论在设备、材料还是工艺技术方面均取得了长足的进步,目前不仅可以生产世界上最先进的爆炸喷涂、超音速火焰喷涂、大功率等离子喷涂等热喷涂设备,也可向用户供应门类齐全、品种配套、性能可与国外产品媲美的各种先进的热喷涂材料,经过数十年锻炼的技术队伍使得该项技术的应用更加成熟和可靠。
据不完全统计,我国仅在“八五”计划期间推广热喷涂技术就取得了直接经济效益35亿元。
我国电站锅炉和工业锅炉以燃煤为主。
据统计,1998年我国由煤生产电力的份额为75%。
而动力用煤质量偏劣,含灰量和含硫量均较高,这就使燃煤电厂和工业锅炉的煤粉生产系统、输送系统及锅炉“四管”(即水冷壁管、过热器管、再热器管、省煤器管)容易受到磨损和腐蚀,造成设备损坏并可能导致事故发生;电厂的引风机、汽缸等有高速流体通过的设备表面,也因磨损、汽蚀等原因而可能发生失效,造成重大损失;许多运转部件(如各种轴类),也因常发生机械性磨损而报废。
此外,电厂的送变电设施,各种钢结构常因处于露天环境而遭受严重的工业大气腐蚀。
凡此种种,均可采用热喷涂技术来进行防护、强化而大大提高其使用寿命,或进行修复而恢复其可使用性,从而提高电厂的生产安全性和经济效益。
[b]2 热喷涂技术在电站锅炉“四管”上的应用[/b]锅炉“四管”工作在高温、高压及受烟气腐蚀、磨粒冲蚀的恶劣环境中,极易产生高温腐蚀及磨损,使管壁减薄,一般而言,这种减薄速度约在1mm/年左右,严重者可达2mm/年以上。
锅炉“四管”减薄后的直接危害是发生泄漏爆管事故。
热喷涂技术及其应用

热喷涂技术及其应用热喷涂技术是近年来比较火热的表面处理技术之一,能够用于改善材料表面的性能,提高材料的机械性能、耐磨性、耐腐蚀性、热稳定性等方面的属性。
本文将介绍热喷涂技术的原理和应用。
一、热喷涂技术原理热喷涂是一种将涂层材料熔化喷射到被涂层材料上形成一层保护膜的表面处理工艺。
它主要分为火焰喷涂、电弧喷涂、高速喷涂、等离子喷涂、激光喷涂等技术。
火焰喷涂是将喷嘴与燃料气体混合后引燃得到的火焰吹向材料表面,同时将被粘合材料送入火焰中加热,然后在熔化状态下喷向被涂材料。
电弧喷涂利用电极放电引发电弧,使涂层材料瞬间融化,并以高速喷向材料表面。
高速喷涂是将粉末材料经过特殊的加速器加速,超音速喷向材料表面,从而形成涂层。
等离子喷涂是以等离子体为介质进行喷涂。
等离子体是在低压下产生的电离气体,它的能量很高,能使材料直接熔化并在被涂材料上喷涂形成涂层。
激光喷涂是利用激光束将涂层材料加热并熔化,然后以气体喷嘴喷向被涂材料,从而形成涂层。
这些不同类型的热喷涂技术都基于相同的原理,即通过喷射熔化的涂层材料来形成一层保护膜,使被涂层材料的性能发生改变。
二、热喷涂技术的应用热喷涂技术可以应用在各种材料的表面处理上,包括金属、塑料、陶瓷等。
它具有如下的应用:1. 保护性涂层热喷涂技术可以在有害气体作用下保护金属表面,使其不被腐蚀。
例如,在海洋环境中,金属的表面会被盐雾等大气污染物或海水腐蚀,而热喷涂技术可以种植一层高效的电池隔离膜,通过其它层保护金属表面,从而避免材料损坏。
2. 耐磨性提高机械部件经过热喷涂处理后,涂层会形成一种厚度薄、高硬度的涂层,从而耐受各种磨损和冲击。
3. 高科技行业热喷涂技术还广泛应用于高科技领域的材料处理,例如太阳能电池板、微电子制造等瑞士实验室使用热喷涂技术制造电池板,提高电能转换的效率、同时也降低制造成本。
4. 冶金行业热喷涂技术在冶金行业中应用范围广泛,可以用于包括喷涂铺管、喷涂耐火砖、喷涂耐磨材料等。
热喷焊技术在大型钻机牙轮修复中的应用

() 2 喷焊 表面有 裂 纹 。预热 温度 不够 或 喷焊 后
层 的温差 减少 , 降低 由于温 差 引起 的内应 力 。另 外 可减缓冷却 速度 , 防止 冷 却 时 因收缩 发 生 涂层 崩 落 或产生裂 纹 。提 高预 热 温度 有 利 于涂 层 的重 熔 , 能
显著地改 善涂层 的润湿性 。但是 预热温 度过高会 造 成基体金 属 的氧 化 , 阻碍 涂层与 基体 的结 合 , 预热 故 温度不 宜过高 。但预 热 温度 过 低 , 则很 容 易 产生 喷 焊层脱落 、 卷边 等 现象 。一 定 的预 热 温度 既 可 防止 高温粉末 颗粒撞 击 到工 件 表面 时 的剧 冷 、 可 以减 又
响涂层 的结合 强度 。
表 面粗 糙 的工件 润 湿性 好 , 利 于熔 化合 金沿 有 牙轮磨损 表面 流布 , 因此 改善工件 的表面粗糙 度 , 加
间结合强度 , 适用 于氧. 乙炔火焰喷焊 工艺 。
() 2 主要设 备 。选 用 Q 一/ H 2 h型 喷枪 , 乙炔发 生
强微冶金 结合性 , 能增大涂 层与基材 的结合 面积 , 提 高结合 强度 。 采用 砂轮打磨 后喷砂粗 化处理 , 然后进行 喷焊 , 涂 层 与基 材结合 界面 的质 量 比较理想 。
1 7 1
李
强 (9 7 )男 , 士 研 究 生 , 经 理 ,300安 徽 省 淮 北 I6 一 , 硕 总 25 0
市 东 山路 11号 。 3
总第 5 5期 0
3 2 牙轮预热 .
现代矿 业 堆 与基材接 合不好 的缺 陷。
21 0 1年 5月第 5期
预热 温度控 制 在 3 0~ 0 5 4 0℃ 。使 基体 与 喷 焊
热喷涂技术原理及应用

热喷涂技术原理及应用
热喷涂技术是一种将熔融或煅烧的材料喷射到被涂物表面形成涂层的
方法,主要通过机械喷涂、火焰喷涂和等离子喷涂等方式实现。
该技术具
有简单、快速、高效、易实施等特点,广泛应用于航空航天、冶金、化工、电子等工业领域。
1.加热原理:通过燃烧或电阻加热等方式,将喷射材料加热到熔点或
半熔状态,使其具有液态或半固态的物理性质。
2.喷射原理:通过高压气体或等离子体流体作为介质,将加热后的喷
射材料喷射到被喷涂的物体表面,形成涂层。
3.冷却原理:当喷射材料接触到物体表面后,快速冷却凝固,形成均
匀而紧密的涂层。
1.表面保护:热喷涂技术能够在被涂物表面形成一层坚硬、耐磨、耐
腐蚀的保护层,提高工件的使用寿命和性能。
2.涂料修复:热喷涂技术可用于修复损坏或磨损的表面涂层,恢复工
件的使用功能。
3.表面改性:通过选择不同材料和涂层结构,可调整涂层的表面形貌、化学成分和物理性能,实现对工件表面性能的改善与调控。
4.温度管理:利用热喷涂技术可制备出具有更好的导热性能的绝热和
散热涂层,用于温度管理和热障涂层的制备。
5.功能涂层:热喷涂技术可制备出各种功能涂层,如阻焊涂层、导电
涂层、耐磨涂层等,以满足特殊技术要求。
6.修饰美化:通过热喷涂技术,可在工件表面形成一层具有良好的光滑度和装饰性的金属涂层,提高工件的外观质量。
总的来说,热喷涂技术是一种常用的涂层制备技术,其应用广泛且多样化,具有改善材料性能、延长使用寿命、提高外观质量等优点。
随着科学技术的不断发展,热喷涂技术在新材料、新工艺、新应用等方面仍有很大的发展空间。
热喷涂技术
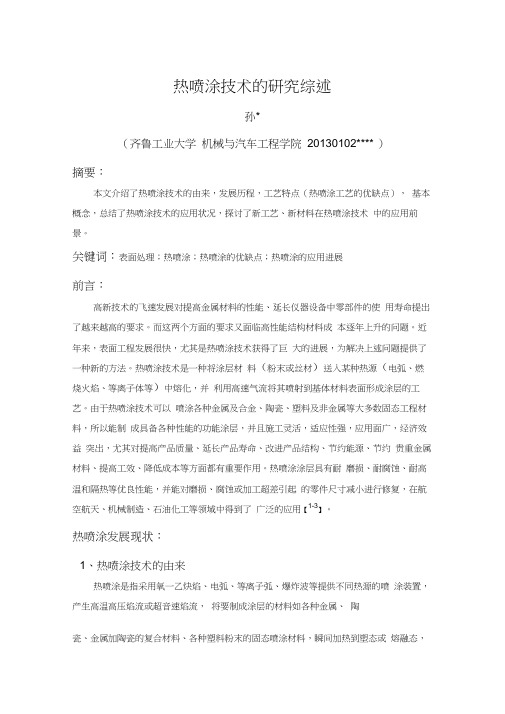
热喷涂技术的研究综述孙*(齐鲁工业大学机械与汽车工程学院20130102**** )摘要:本文介绍了热喷涂技术的由来,发展历程,工艺特点(热喷涂工艺的优缺点),基本概念,总结了热喷涂技术的应用状况,探讨了新工艺、新材料在热喷涂技术中的应用前景。
关键词:表面处理;热喷涂;热喷涂的优缺点;热喷涂的应用进展前言:高新技术的飞速发展对提高金属材料的性能、延长仪器设备中零部件的使用寿命提出了越来越高的要求。
而这两个方面的要求又面临高性能结构材料成本逐年上升的问题。
近年来,表面工程发展很快,尤其是热喷涂技术获得了巨大的进展,为解决上述问题提供了一种新的方法。
热喷涂技术是一种将涂层材料(粉末或丝材)送入某种热源(电弧、燃烧火焰、等离子体等)中熔化,并利用高速气流将其喷射到基体材料表面形成涂层的工艺。
由于热喷涂技术可以喷涂各种金属及合金、陶瓷、塑料及非金属等大多数固态工程材料,所以能制成具备各种性能的功能涂层,并且施工灵活,适应性强,应用面广,经济效益突出,尤其对提高产品质量、延长产品寿命、改进产品结构、节约能源、节约贵重金属材料、提高工效、降低成本等方面都有重要作用。
热喷涂涂层具有耐磨损、耐腐蚀、耐高温和隔热等优良性能,并能对磨损、腐蚀或加工超差引起的零件尺寸减小进行修复,在航空航天、机械制造、石油化工等领域中得到了广泛的应用【1-3】。
热喷涂发展现状:1、热喷涂技术的由来热喷涂是指采用氧一乙炔焰、电弧、等离子弧、爆炸波等提供不同热源的喷涂装置,产生高温高压焰流或超音速焰流,将要制成涂层的材料如各种金属、陶瓷、金属加陶瓷的复合材料、各种塑料粉末的固态喷涂材料,瞬间加热到塑态或熔融态,高速喷涂到经过预处理(清洁粗糙)的零部件表面形成涂层的一种表面加工方法。
我们把特殊的工作表面叫“涂层”,把制造涂层的工作方法叫“热喷涂”,它是采用各种热源进行喷涂和喷焊的总称。
热喷涂技术最早出现在20世纪早期的瑞士,随后在前苏联、德国、日本、美国等国得到了不断的发展,各种热喷涂设备的研制、新的热喷涂材料的开发及新技术的应用,使热喷涂涂层质量不断得到提高并开拓了新的应用领域【4】。
- 1、下载文档前请自行甄别文档内容的完整性,平台不提供额外的编辑、内容补充、找答案等附加服务。
- 2、"仅部分预览"的文档,不可在线预览部分如存在完整性等问题,可反馈申请退款(可完整预览的文档不适用该条件!)。
- 3、如文档侵犯您的权益,请联系客服反馈,我们会尽快为您处理(人工客服工作时间:9:00-18:30)。
热喷焊技术的应用综述摘要:热喷焊在设备维修中得到了广泛的应用。
以饲料粉碎机锤片为例,介绍了热喷焊技术的特点、喷焊工艺的制定以及热喷焊参数的选择,并对热喷焊前后锤片的使用寿命进行了比较。
为得到良好的喷焊层,热喷焊要根据基材性质和工作条件选择合适的喷焊材料,设计合理涂层结构。
在喷焊过程中可采用一步法或二步法进行喷焊。
热喷焊技术在设备维修工作中越来越发挥着重要作用。
关键词:热喷焊;表面预清理;焊后处理Abstract :The spray weld is used widely in maintenance and repair of the mechanical equipment。
the characteristics the thermal spray welding technology,the determination of welding technology and the choice of thermal spray welding parameters are introduced and the comparison of the service life of the hammer before and after the thermal spray welding treatment is made.In order to get the firmly coat,the spray welding material must accord with the base substance and working stations.The coat structure must be suitable to the usage、One—step or two—sup can be adopted during spray welding .The spray weld will be more and more important in the mechanical systems service.Key words:thermal spray welding;pretreatment of surface;post-weld treatment一、前言部分热喷焊技术是在热喷涂技术基础上发展起来的。
它是将喷涂层再进行一次重熔处理,与基体表层材料达到熔融状态后,再进一步形成更紧密的冶金结合层,使零件表面获得一层类似堆焊形成的涂层。
喷焊可以看成是合金喷涂和金属堆焊两种工艺的复合,它克服了热喷涂层结合强度低、硬度低等缺点,同时由于使用了高合金粉末使喷焊层具有一系列特殊的性能,这是一般堆焊所不具备的。
金属热喷焊技术的基本原理是:使用一定的热源.把自熔合金属粉末喷涂在经过处理的工件表面上.在工件不熔化的情况下加热涂层,使其熔化并润湿工件表面.通过液态合金与固态基材表面的相互溶解与扩散,实现冶金结台,形成具有所需性能的致密喷焊层。
热喷焊不仅可以用来修复表面磨损的零件,当使用合金粉喷焊时还能使修复件比新零件更耐磨,所以也将其用于新零件表面的强化和装饰等,使零件的使用性能更好,寿命更长。
因此,热喷焊技术得到了比较广泛的应用。
二、主体部分1、热喷焊技术特点热喷焊是以氧气和乙炔燃烧产生的热量为能源,通过特制的喷枪将具有特殊性能的合金粉末加热到熔融或高塑性状态,然后以较高的速度喷射到经过净化预处理的零件表面上,使其获得均匀致密的金属表层,起到耐磨、耐蚀、耐热、抗氧化等作用,达到修复零件和延长其使用寿命的目的。
氧乙炔焰合金粉末喷涂焊具有以下特点。
1.1、焊层具有耐磨、耐蚀、抗高温氧化等性能,可满足各种工况要求,一般情况下与母材结合时的结合强度可达到294MPa。
1.2、可修复废旧零件,修复后的零件具有较优良的性能和较长的使用寿命,且修复速度陕,可减少停机时间。
1.3、喷焊法综合性能好,元素稀释率小,对母材适应性强,不受母材化学成分的影响,尤其是要求工作表面具有高硬度而心部要求韧性好的零件,很适合采用喷焊法。
1.4、焊层厚度可以在0.2Z3mm范围内调整,喷焊覆盖层薄而均匀。
热喷焊的主要缺点是被处理的工件易变形。
喷焊层结构示意图2、喷焊材料及涂层设计2.1 喷焊材料喷焊技术的应用需要具备的物质条件有喷焊设备和喷焊材料两方面。
在设备维修中零件的材料性质和表面要求各不相同,为满足零件的使用要求,选择合理的喷焊材料成为保证修复性能的重要因素之一。
热喷焊所用的材料主要是自熔性合金粉末。
所谓自熔性合金粉末是指合金粉末熔化时合金成份能自行脱氧并形成低熔渣,从而与基材形成良好的结合。
粉末材料的主要特点是可喷焊材料的范围特别广,调整合金基涂层层份比较容易;但粉末的形状、粒度及粒度分布、湿度等因素对粉末材料的性能会产生不同的影响。
自熔性合金粉末的突出特点是粉末的熔点较低,有良好的自熔性。
在熔融状态下与基材有良好的润湿性,液一固相线之间的温度范围较宽,可以制备耐磨、耐腐蚀、抗氧化和耐热等表面强化和表面防护涂层。
常用的有铁基、镍基、钴基、铜基和碳化钨的五大类。
镍基粉末价格适中,其粉末熔点低(1 100~l 150℃),自熔成渣性良好,固液相线温度范围宽,对多种坯料机体润湿能力强,涂层韧性好,喷焊工艺性良好。
其涂层具有优异的耐腐蚀性、耐磨性和良好的耐热性,是应用最广的一类自熔性合金。
它可以用于具有综合性能要求的涂层或在600℃以下代替钴基合金。
钴基合金粉末的价格较高,其主要特点是具有优良的耐高温性、红硬性、耐腐蚀、耐磨和抗氧化等性能,最适合700℃左右高温下作抗氧化、耐腐蚀、耐磨损的表面涂层。
含碳化钨的自熔性合金粉末通常是由镍基自熔性合金粉末中加入一部分纯钴(镍),包括碳化钨粉末(铁基、钴基也可以)。
通过调节碳化钨与铁、镍和钴基合金粉末的比例,可以获得不同硬度、耐磨性的涂层。
采用含碳化钨的自熔性合金粉末喷焊时,其涂层的硬度比单用自熔性合金粉末涂层的硬度高HRC5 HRC10。
2.2 涂层设计如果说喷焊设备和材料是喷焊技术的物质条件,那么涂层设计和喷焊工艺则成为保证修复零件使用性能和质量的技术条件。
涂层设计是选择工艺方法的前提,工艺方法是保证涂层使用性能和质量的措施。
涂层设计的主要任务是确定涂层类型、选择涂层材料和设计涂层结构。
采用热喷焊技术可以获得致密、整体硬度高的涂层,适用于抗磨粒磨损、抗表面疲劳磨损以及抗腐蚀磨损涂层。
涂层材料的选择主要考虑需修零件的工作条件(如工作温度、滑动速度、润滑条件等)和表面破坏形式(磨损、腐蚀等);其次还应考虑所选喷焊材料的经济合理眭。
但最终还应使涂层的性能满足使用要求。
涂层材料的设计重点要解决涂层与基材的结合强度和确定涂层厚度的问题。
3、热喷焊工艺3.1 氧乙炔火焰喷焊工艺氧乙炔火焰喷焊所使用的设备比较简单,除了需要专用喷枪以外,其他的设备都是一般气焊所用设备。
喷枪除了有用喷涂或喷焊送粉的两用枪以外,还需要重熔枪,如SCR一100型和SHP—C型等。
此外还有喷焊一步法用枪,如SPH一1/h、SPH一21h和SPH一41h等。
这类枪的特点是即可送粉又可重熔。
喷焊工艺可分为三个阶段。
3.1.1、喷前准备这个阶段的第一个重点是喷焊表面的除油去污。
对某些多孔铸件,孔内油污仅靠清洗很难除尽,可用火焰加热到300℃或更高,将孔内油污烧净。
第二个是除去表面的氧化物和疲劳层,可采用喷砂、机加工或打磨等方法。
第三个就是除去表面处理层(如渗碳、镀铬、淬火层等)。
这是因为这些处理层常常在喷粉或重熔时产生气体溢出或是焊层与基体结合不良。
3.1.2 喷焊。
氧乙炔火焰喷焊自熔合金一般可分为“一步法”和“二步法”两种工艺。
“一步法”是喷粉与重熔几乎同时进行的。
其优点是对工件的输入量较“二步法”小。
适用于大工件小面积或小工件表面的喷焊修复。
“一步法”喷焊的工艺流程:工件预热一喷粉重熔一缓冷。
一步法喷焊的预热温度应在300℃左右。
每次喷涂重熔的面积为直径范围。
缓冷的面积应加热到500℃以上。
“二步法”喷焊的工艺流程是:工件预热一喷粉一重熔一缓冷。
预热温度一般视工件的大小、部位和材质而定。
一般选在200-450℃左右。
对大工件、大面积或膨胀系数大的工件预热温度应偏高。
对极小件、薄板及含有氧化元素的合金基材,预热温度应编低。
必要时可以先预热到100~200℃,接着喷涂一层0.2~0.3 mm厚的喷粉,然后继续加热到所需温度。
喷涂层厚度一次不易超过1.25 mill,若一次不够可以先重熔次后再喷焊。
重熔是喷焊二步法工艺中的关键环节。
除了用火焰重熔以外,还可以采用感应重熔。
一般的自熔合金的膨胀系数都偏高,因此,被喷焊的工件从高温急剧冷却下来会使涂层出现裂纹,必须视具体情况采用缓冷措施。
(3)喷后处理。
喷焊后的零件要进行检查。
喷焊层常见的缺陷有喷焊层剥落、喷焊层裂纹、喷焊层夹渣、喷焊层气孔和喷焊层漏底。
对于表面精度要求不高的零件,喷焊后不加工即可使用。
对有配合精度要求的零件,喷焊后需要进行机加工。
加工方法有车削和磨削。
3.2 应用氧乙炔火焰喷焊主要用于对承受高应力载荷和承受冲击磨损的部件进行强化,提高工件的耐磨性,增加工件的使用寿命。
如对汽车中的各种齿轮、花键轴、活塞销、气门、变速杆拨叉等进行喷焊强化或修复,不仅能使报废零件修复后继续使用,还可使新制零部件的寿命延长。
上述汽车零部件经喷焊强化后,其寿命可提高2~5倍。
喷焊层常见质量缺稿及控嗣方法4、热喷焊参数选择在喷焊工艺中,气体压力和喷枪至工件的距离是两个重要的参数,它们与合金粉末种类有关。
如采用F Ni一15粉末,气体压力分别为:氧气3~5MPa、乙炔0.5~0.7MPa,喷枪至工件距离约100mm左右;当采用Ni60合金粉末时,气体压力分别为:氧气0.3~0.5MPa、乙炔0.04~0.07MPa,喷枪至工件距离约100~150mm。
在上述参数范围内可获得平整、银白色的致密焊层。
增加气体压力或缩短喷枪与工件之间的距离,喷焊层会出现过烧现象,甚至会有绿色氧化皮出现。
反之,气体压力过小、喷射间距过大则会造成焊层粉末重熔不好。
喷射角(即粉末流动方向与工件表面的夹角)对焊层质量也有一定影响。
当喷射角为90。
时,喷射功最大,粉末在空中行进距离最短,氧化程度也较小,这时焊层气孔率低,组织致密。
喷射角过小(如小于45。
)则焊层组织疏松,粉末利用率降低。
将喷焊后的锤片和未喷焊的锤片分别安装在同一型号的两台饲料粉碎机上进行试验,结果表明,经喷焊后锤片的使用寿命是未经喷焊锤片使用寿命的4—6倍。
热喷焊技术操作方便,设备简单,一般工厂均可利用现有的气焊设备再添置少量专用器材进行热喷焊作业,其广泛应用于制造业和修理业。
三、结论部分目前,我国生产的热喷焊设备已很完善,还发展了前处理、后加工的专用设备和刀具。