S195右侧镗孔组合机床设计开题报告
S195柴油机机体25轴双面钻孔组合机床总体设计及10轴左主轴箱设计

XXXXX大学本科生毕业设计任务书题目:S195柴油机机体25轴双面钻孔组合机床总体设计及10轴左主轴箱设计题目来源:□省部级以上□校级√横向√自选题目性质:□理论研究□应用与理论研究√应用研究分院:机电分院专业:机械制造工艺与设备班级:机制09—3学号:XXXXXXXXX学生姓名:XXXX起讫日期:2013.2.28—2013.5.17指导教师:XXXXXX 职称:XXXX审核日期:说明1.毕业设计任务书由指导教师填写,并经分院审定,下达到学生。
2.学生根据指导教师下达的任务书独立完成开题报告,于3周内提交给指导教师批阅。
3.本任务书在毕业设计完成后,与论文一起交指导教师,作为论文评阅和毕业设计答辩的主要档案资料,是学士学位论文成册的主要内容之一。
一、毕业设计的要求和内容(包括原始数据、技术要求、工作要求)题目:S195柴油机机体25轴双面钻孔组合机床总体设计及10轴左主轴箱设计设计一台用于S195柴油机机体流水线的卧式双面25轴钻孔组合机床,给定条件为:生产纲领20万件/年;装料高度1000 mm;采用卧式双面通过式;采用液压夹紧方式。
具体内容:1、卧式双面25轴钻孔组合机床三图一卡总体设计;2、双面钻孔组合机床10轴左主轴箱的设计,加工内容为:钻左侧面:螺纹底孔9 –Ø6.8,深20;钻左侧面:螺纹底孔Ø8.5,深20;3、左主轴箱主要零件图的设计;4、撰写毕业设计论文(初稿、终稿,8000字以上)。
二、毕业设计图纸内容及张数进度安排:1.查阅文献,撰写开题报告1周2.三图一卡设计(A0 1.5张) 3 周3.绘制10轴左主轴箱总图(A0 1张) 3 周4.绘制左主轴箱主要零件的图纸(A0或A1 1张) 2 周5.整理说明书,准备答辩2周三、毕业设计实物内容及要求1、学生每人应至少完成2张零号图纸的设计工作量,并编写设计说明书,其中的绘图工作,原则上不得全部为计算机绘图或全部手工绘图。
S195柴油机机体三面精镗组合机床总体设计及夹具设计正文1
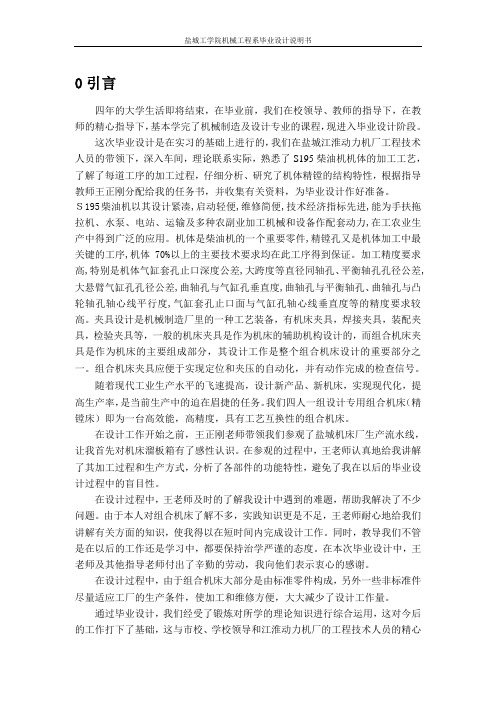
0引言四年的大学生活即将结束,在毕业前,我们在校领导、教师的指导下,在教师的精心指导下,基本学完了机械制造及设计专业的课程,现进入毕业设计阶段。
这次毕业设计是在实习的基础上进行的,我们在盐城江淮动力机厂工程技术人员的带领下,深入车间,理论联系实际,熟悉了S195柴油机机体的加工工艺,了解了每道工序的加工过程,仔细分析、研究了机体精镗的结构特性,根据指导教师王正刚分配给我的任务书,并收集有关资料,为毕业设计作好准备。
S195柴油机以其设计紧凑,启动轻便,维修简便,技术经济指标先进,能为手扶拖拉机、水泵、电站、运输及多种农副业加工机械和设备作配套动力,在工农业生产中得到广泛的应用。
机体是柴油机的一个重要零件,精镗孔又是机体加工中最关键的工序,机体70%以上的主要技术要求均在此工序得到保证。
加工精度要求高,特别是机体气缸套孔止口深度公差,大跨度等直径同轴孔、平衡轴孔孔径公差,大悬臂气缸孔孔径公差,曲轴孔与气缸孔垂直度,曲轴孔与平衡轴孔、曲轴孔与凸轮轴孔轴心线平行度,气缸套孔止口面与气缸孔轴心线垂直度等的精度要求较高。
夹具设计是机械制造厂里的一种工艺装备,有机床夹具,焊接夹具,装配夹具,检验夹具等,一般的机床夹具是作为机床的辅助机构设计的,而组合机床夹具是作为机床的主要组成部分,其设计工作是整个组合机床设计的重要部分之一。
组合机床夹具应便于实现定位和夹压的自动化,并有动作完成的检查信号。
随着现代工业生产水平的飞速提高,设计新产品、新机床,实现现代化,提高生产率,是当前生产中的迫在眉捷的任务。
我们四人一组设计专用组合机床(精镗床)即为一台高效能,高精度,具有工艺互换性的组合机床。
在设计工作开始之前,王正刚老师带领我们参观了盐城机床厂生产流水线,让我首先对机床溜板箱有了感性认识。
在参观的过程中,王老师认真地给我讲解了其加工过程和生产方式,分析了各部件的功能特性,避免了我在以后的毕业设计过程中的盲目性。
在设计过程中,王老师及时的了解我设计中遇到的难题,帮助我解决了不少问题。
深孔镗铰复合刀具设计开题报告

深孔镗铰复合刀具设计开题报告毕业设计开题报告学生姓名: 学号: 学院、系:专业: 机械设计制造及其自动化设计题目: 深孔镗铰复合刀具设计指导教师:2012年3月13日毕业设计开题报告1(结合毕业设计课题情况,根据所查阅的文献资料,撰写2000字左右的文献综述:文献综述一(深孔加工技术在制造业中的地位及作用深孔加工技术一般是指加工长径比(即孔全长与孔径之比)很大,因而为通用工具、机床所不能胜任而必须采用的特殊工艺、工具及设备.在机械制造领域中,深孔加工、齿轮加工等都是制造业的重要分支领域,与一般制造工艺技术相辅相成,在机械制造领域中具有举足轻重的地位.近代深孔加工技术是因枪、炮管制造的需要而发展起来的.直到第二次世界大战时期,深孔加工工具与设备90%以上用于兵器制造.外排屑式的枪钻和单刃平头炮钻曾经是有效的深孔刀具.40年代出现了镶硬质合金枪钻和BTA(内排屑)钻头,使深孔加工的效率提高10倍以上,加工质量相应地大幅度提高,为深孔加工技术在煤炭、石油机具制造中的应用,重型机器、冶金机械、电力设备、液压件制造、航天工业等行业的大量应用开阔了道路.到了80年代,深孔加工技术已成为几乎所有制造行业不可缺少的关键工艺技术.在现代机械产品中,深孔零件常常成为决定产品质量水平和效益的关键件.在我国数百家以深孔零件为主要加工对象的大中型企业中,深孔加工技术已是对企业产品质量和效益起决定作用的技术.即在一般制造业中,深孔加工也常常成为“卡脖子”技术. 二(我国深孔加工技术的现状我国深孔加工技术的总体水平比一般制造工艺水平还要落后,约与先进工业国60年代的水平相当.以枪炮制造业为例,60、70年代已在国际上普及的“高压”排屑型硬质合金深孔钻(包括单管内排屑(STS或BTA)镶硬质合金深孔钻及深孔镗头,焊接式及整体式硬质合金枪钻、枪铰刀,机夹式多刃及单刃钻头),虽然在80年代已为少数民用企业引进或仿制,但兵器工业依然沿用高速钢深孔刀具,更谈不上DF深孔钻的应用.深孔加工机床多为自制或仿制西方40年代的机型,已不适用于采用新技术.在民用制造业中,80年代仅有屈指可数的厂家引进国外深孔加工设备,象硬质合金枪钻、镶齿喷吸钻这样的普通刀具还需仰赖进口.少数工具厂有BTA钻和整体硬质合金枪钻、枪铰刀的生产,但品种有限,远远不能满足需求.例如Φ5mm以下的和加工500mm以上深度的硬质合金枪钻,无厂家供货;加工高强度、超硬超深材料的BT且钻头、撞头无供应渠道,兼具高效、精密加工双重功能的深孔刀具几乎完全不见.事实证明,即使引进现成的技术和设备,也不可能一劳永逸地解决不同行业中提出的特定工艺问题(如兵器工业中的深孔加工特殊工艺技术和设备、深孔工具和装备生产的专业化,各种难加工材料的特需刀具和工具研制等),这就决定了我国的深孔加工技术发展道路必须从开展设计研制工作入手.我们的研究工作,首先从国内(调查研究军民用企业的技术观状和紧迫问题)国外(全面收集国外技术情报,对先进工业国深孔加工技术发展状况和工具设备制造业进行重点考察并了解其发展趋势)调研入手,将移植推广与创新相结合;使设计研制试验面向生产中具有普遍性和紧迫性的实际课题;注意立足于已有旧设备的改造利用,并在此基础上提出创新性的工具、设备、新设计方案;充分考虑成果的多用性(军民生产两用,深孔行业与非深孔行业兼用〕;将CAD,CAM,GT,NC等新技术移植于深孔加加工领域;逐步增加预研成果储备,使先进技术配套和系列化.因此,推出中国自己的原创性深孔加工技术,建立专业化,现代化的配套深孔加工装备产业,引进国外先进深孔加工装备设计生产体系并实现国产化,创建以先进技术武装的深[7]孔零件制造行业,以满足广大中小企业开发新装备的迫切需求。
半精镗及精镗气缸盖导管孔组合机床设计(镗削头设计)-开题报告

6月8日~6月13日.论文定稿阶段。
论文修改、定稿,材料复查。
6月14日~6月16日.毕业答辩。
6月17日~6月18日.材料整理装袋。
五、指导教师意见
年月 日
六、专业系意见
年月 日
七、学院意见
年月 日
毕业设计
开题论证报告
专业
学生姓名
班级
学号
指导教师
完成日期
课题名称:半精镗及精镗气缸盖导管孔组合容及国内外现状综述
不少于400字.
课题来源:课题来源于江苏高精机电装备公司。
课题研究的主要内容:本课题主要研究的是镗削头的设计。镗削头是组合机床通用的部件,其以良好的性能广泛用于组合机床及自动线。镗削头可与同规格的机械或液压滑台配套使用,组成立式或卧式组合机床,具有灵活配置的特点:主要配置成顶置式,也可配置成尾置和侧置式,有高、低两组转速,通过交换齿轮或皮带轮变速。配置齿轮传动装置的镗削头适用于各种材料工件的粗、精镗孔;配置皮带传动装置的镗削头适用于各种材料工件的半精、精加工。
国内外现状:随着汽车工业的兴起而发展。在专用机床中某些部件因重复使用,逐步发展成为通用部件,因而产生了组合机床。组合机床的未来将更多的采用调速电动机和滚珠丝杠等传动,以简化结构、缩短生产节拍;采用数字控制系统和主轴箱、夹具自动更换系统,以提高工艺可调性;以及纳入柔性制造系统等。目前国内外广泛应用可编程控制器(PLC)改造镗组合机床,以提高机床的精度和效率。可编程控制器是以微处理器为核心的一种新型工业控制装置,它具有体积小、功能强、编程简单。采用可编程控制器改造后的机床不仅提高了设备可靠性,大大降低了设备故障率,而且由于可编程控制器( PLC)有I/ O显示,便于找出故障点,给维护和检修带来很大方便。
组合镗床设计开题报告

武汉理工大学本科学生毕业设计(论文)开题报告1、目的及意义(含国内外的研究现状分析)制造业是一个国家或地区经济发展的重要支柱,其发展水平标志着该国家或地区的经济实力、科技水平、生活水准和国防实力。
而制造业的生产能力和制造水平主要取决于机械制造装备——金属切削机床的先进程度。
作为金属切削机床的主力军的组合机床是以通用部件为基础配,以少量专用部件组成的一种专用高效自动化设备,具有设计制造周期短、投资少、加工精度稳定、改装方便、经济效益高等优点。
在机械加工工业中,机械产品大批量生产中,组合机床已得到广泛运用。
一些复杂的壳体类零件,加工工艺复杂、定位夹紧困难的工件,要提高其加工精度、生产效率,单凭普通机床是很难办到的,而在用普通机床加工复杂工件的过程中,对操作者的技术也提了较高的要求,这就迫切的要求生产一定数量的组合机床。
这样,不但可以提高零件的加工精度和生产率,而且成本低、生产周期断,适合我国的经济水平、教育水平和生产水平。
更能够在激烈的竞争中为企业获得更多利润、提高企业核心竞争力。
现代组合机床和自动线作为机电一体化产品,它是控制、驱动、测量、监控、刀具和机械组件等技术的综合反映。
组合机床及其自动线的技术性能和综合自动化水平,在很大程度上决定了机械生产部门产品的生产效率、产品质量和企业生产组织的结构,也在很大程度上决定了企业产品的竞争力。
所以对组合机床的设计研究具有十分重要的意义。
近年来,这些技术有长足进步,同时作为组合机床主要用户的汽车和内燃机等行业也有很大的变化,其产品市场寿命不断缩短,品种日益增多且质量不断提高。
这些因素有力地推动和激励了组合机床和自动线技术的不断发展,目前组合机床的研制正向高效、高精度、高自动化的柔性化方向发展。
我国的机床工业是在1949年新中国成立后才开始建立起来的,组合机床的通用部件起步于80年代,经历了一个从无到有、从点到面、从低到高的逐步发展的历史时期。
进入90年代后,组合机床行业加快发展,行业的整体实力和新产品的质量水平有了显著的提高。
柴油机机体三面精镗组合机床总体及后主轴箱设计

柴油机机体三面精镗组合机床总体及后主轴箱设计摘要:组合机床是集机电于一体的综合自动化程度较高的制造技术和成套工艺装备,它的特征是高效、高质、经济实用,因而被广泛用于工程机械、交通、能源、军工、轻工、家电等行业。
柴油机气缸体是需要大量生产的零件。
为高速、高效的加工S195柴油机气缸体的三面精镗孔及保证相应的加工尺寸精度,本课题是设计一台三面精镗组合机床。
该机床设计的重点分总体设计和零部件设计两部分。
总体设计包括机床配置型式的确定、结构方案的选择以及“三图一卡”的绘制。
在完成“三图一卡”的基础上,主要完成后主轴箱设计。
后主轴箱部件设计包括绘制后主轴箱装配图和箱体补充加工图、确定主轴和齿轮、动力计算、设计传动系统等。
本机床能够满足加工要求,保证加工精度,结构简单,维修方便。
操作的简便减轻了工人的劳动强度,提高了劳动生产率。
关键词:组合机床;总体设计;零部件设计本设计来自:完美毕业设计网登陆网站联系客服远程截图或者远程控观看完整全套论文图纸设计客服QQ:8191040Design of General and Back Headstock of Modular Machine T ool for Finished Boring of Pipe Holes on Three-Side ofBody of DieselAbstract: Modular Machine Tool is a combination of integrated high degree of automation of manufacturing process technology and sets of technology equipment, whose characteristics are high efficiency, high-quality, economical and practical, they have been widely used in construction machinery, transportation, energy, military industry, light industry, appliance and other industries.Diesel engine gear box is a product which needs mass production. It is shrewd to boring hole, guarantees alleviated the labor strength of workers and increase labor productivity. The task is to design a combination of three fine boring machine. The focus of the design of the machine tool includes two parts ,which is general design and design of parts. The general design, includes the determining of the type of machine configuration, the choice of the structure of the program, as well as the drawing of "three plans and a card". The main design is designed after the completion of the design, based on the completion of the "three plans and a card". Components after the design of the back headstock parts includes the drawing of assembly drawing of the back headstock and plans to Cabinet add processing ,the determine of the spindle and gear , the dynamic calculation, the design of transmission and so on. This modular machine tool can meet the processing requirements,ensure the machining accuracy, simple structure, easy maintenance. Simple operation reduces the labor intensity, improves labor productivity.Key word:Modular machine tool; General design ; Parts design。
S195右侧镗孔组合机床设计翻译

Group Technology and Cellular Manufacturing1.PARTFAMILIBSA part family is a collection of parts that are similar either because of geometricshape and size or because similar processing steps are required in their manufacture.The parts within a family are different, but their similarities are close enough to merit their inclusion as members of the part family. Figures 15.1 and 15.2 show two different part families. The two parts in Figure 15. 1 are very similar in terms of geometric design, but quite different in terms of manufacturing because of differences in tolerances, production quantities, and material. The ten parts shown in Figure 15.2constitute a part family inmanufacturing, but their different geometries make them appear quite different from a design viewpoint.Figure 15.2, A family of parts with similar manufacturing processrequirements but different design attributes. All parts are machined fromcylindrical stock by turning; some parts require drilling and/or milling.The biggest single obstacle in changing over to group technology from a conven-tional production shop is the problem of grouping the parts into families. There are three general methods for solving this problem. All three are time consuming and involve the analysis of much data by properly trained personnel. The three methods are: (1) visual inspection, (2) parts classification and coding, and (3) production flow analysis. Let us provide a brief description of the visual inspection method and then examine the second and third methods in more detail.The visual inspection method is the least sophisticated and least expensive method. It involves the classification of parts into families by looking at either the physical parts or their photographs and arranging them into groups having similar Figure 15.1Two parts of identical shape and size but different manufacturingrequirements: (A) 1,000,000 pc/yr, tolerance =±0.01in, material = 1015 CR steel,nickel plate;and (B) 100 pc/yr, tolerance =±0.001in, material=18 - 8 stainless steel.features.2.PARTS CLASSIFICATION AND CODINGThis is the most time consuming of the three methods. In parts classification and coding,similarities among parts are identified, and these similarities are related in a coding system. Two categories of part similarities can be distinguished:(1) design attributes, which are concerned with part characteristics such as geometry, size, and material; and (2) manufacturing attributes, which consider the sequence of processing steps required to make a part. While the design and manufacturing attributes of a part are usually correlated, the correlation is less than perfect. Accordingly, classification and coding systems are devised to include both a part's design attributes and its manufacturing attributes. Reasons for using a coding scheme include:• Design retrieval. A designer faced with the task of developing a new part canuse a design retrieval system to determine if a similar part already exists. A simplechange in an existing part would take much less time than designing a whole newpart from scratch• Automated process planning. The pan code for a new part can be used to searchfor process plans for existing parts with identical or similar codes• Machine cell design.The part codes can be used to design machine cells capableof producing all members of a particular part family, using the composite partconcept (Section 15.4.1).To accomplish parts classification and coding requires examination and analysis of the design and /or manufacturing attributes of each part. The examination is sometimes done by looking in tables to match the subject part against the features described and diagrammed in the tables. An alternative and more-productive approach involves interaction with a computerized classification and coding system, in which the user responds to questions asked by the computer. On the basis of the responses, the computer assigns the code number to the part. Whichever method is used, the classification results in a code number that uniquely identifies the part's attributes.The classification and coding procedure may be carried out on the entire list of active parts produced by the firm, or some sort of sampling procedure may be used to establish part families. For example, parts produced in the shop during a certain time period could be examined to identify part family categories. The trouble with any sampling procedure is the risk that the sample may be unrepresentative of the population.A number of classification and coding systems are described in the literature [13],[16], [31], and there are a number of commercially available coding packages.However, none of the systems has been universally adopted. One of the reasons for this is that a classification and coding system should be customized for a given company or industry. A system that is best for one company may not be best for another company.2.1 Features of Parts Classification and Coding SystemsThe principal functional areas that utilize a parts classification and coding system are design and manufacturing. Accordingly, parts classification systems fall into one of three categories:1.systems based on part design attributes2.systems based on part manufacturing attributes3.systems based on both design and manufacturing attributesTable 15.1 presents a list of the common design and manufacturing attributes typically included in classification schemes. A certain amount of overlap exists between design and manufacturing attributes, since a part's geometry is largely determined by the sequence of manufacturing processes performed on it.In terms of the meaning of the symbols in the code, there are three structures used in classification and coding schemes:1. hierarchical structure, also known as a monocode,in which the interpretation ofeach successive symbol depends on the value of the preceding symbols2. chain-type structure , also known as a polycode , in which the interpretation of each symbol in the sequence is always the same; it does not depend on the value of preceding symbols3. mixed-mode structure , which is a hybrid of the two previous codesTo distinguish the hierarchical and chain-type structures, consider a two-digit code number for a part, such as 15 or 25. Suppose the first digit stands for the general shape of the part: 1 means the part is cylindrical (rotational), and 2 means the geometry is rectangular. In a hierarchical structure, the interpretation of the second digit depends on the value of the first digit. If preceded by 1, the 5 might indicate a length-to-diameter ratio; and if preceded by 2, the 5 indicates an aspect ratio between the length and width dimensions of the part. In the chain-type structure, the symbol 5 would have the same meaning whether preceded by 1 or 2. For example, it might indicate the overall length of the part. The advantage of the hierarchical structure is that in general, more information can be included in a codeof given number of digits. The mixed-mode classification and coding systems use a combination of hierarchical and chain-type structures. It is the most common structure found in GT parts classification and coding systems.The number of digits in the code can range from 6 to 30. Coding schemes that contain only design data require fewer digits, perhaps 12 or fewer. Most modem classification include both design and manufacturing data, and this usually requires 20-30 digits. This might seem like too many digits for a human reader to easilycomprehend, but it must be remembered that most of the data processing of the codes is accomplished by computer, for which a large number of digits is of minor concern.2.2 Examples of Parts Classification and Coding SystemsSome of the important systems (with emphasis on those in the United States)TABLE 15.1 Design and Manufacturing Attributes Typically Included in a Groupinclude: the Opitz classification system, which is nonproprietary; the Brisch System (Brisch-Birn,Inc); CODE (Manufacturing Data Systems, Inc.); CUTPLAN (Mctcut Associates); DCLASS (Brigham Yeung University); MultiClass (OIR: Organization for Industrial Research);and Part Analog System (Lovelace, Lawrence & Co., Inc.). Reviews of these systems and others can be found in [16] and [23].In the following, we discuss two classification and coding systems: the Opitz System and MultiClass. The Opitz system is interest because it was one of the first published classification and coding schemes far mechanical parts [31] and is still widely used. MultiClass is a commercial product offered by the Organization for Industrial Research (OIR).1)Opitz Classification System. This system was developed by H. Opitz of the University of Aachen in Germany. It represents one of the pioneering efforts in group technology and is probably the best known, if not the most frequently used, of the parts classification and coding systems. 11 is intended for machined parts. The Opitz coding scheme uses the following digit sequence:12345 6789 ABCDThe basic code consists of nine digits, which can be extended by adding four more digits. The first nine arc intended to convey both design and manufacturing data. The interpretation of the first nine digits is defined in Figure 15.5. The first five digits, 12345, are called form code. It describes the primary design attributes of the part, such as external shape (e.g. rotational vs. rectangular) and machined features (e g., holes, threads, gear teeth, etc.). The next four digits, 6789, constitute the supplementary code, which indicates some of the attributes that would be of use in manufacturing (e.g. dimensions, work material, starting shape, and accuracy). The extra four digits, ABCD, are referred to as the secondary code and are intended to identify the production operation type and sequence. The secondary code can be designed by the user firm to serve its own particular needs.The complete coding system is too complex to provide a comprehensive description here. Opitz wrote an entire book on his system. However, to obtain a general idea of how it works, let us examine the form code consisting of the first five digits, defined generally in Figure 15.5. The first digit identifies whether the part is rotational or nonrotational. They so describes the general shape and proportions of the part. We limit our survey here to rotational parts possessing no unusual features, those with first digit values of 0, 1 or 2.2)MultiClass, MultiClass is a classification and coding system developed by the Organization for Industrial Research (OIR). The system is relatively flexible, allowing the user company to customize the classification and coding scheme to a large extent to fit its own products and applications. MultiClass can be used for a variety of different types of manufactured items, including machined and sheet metal parts, tooling, electronics, purchased parts assemblies an subassemblies, machine tools, and other elements. Up to nine different types of components can be included within a single MultiClass software structure.MultiClass uses a hierarchical or decision-tree coding structure in which the suc-ceeding digits depend on values of the previous digits. In the application of the systems series of menus, pick lists, tables, and other interactive prompting routines are used to code the part. This helps to organize and provide discipline to the coding procedure.The coding structure consists of up to 30 digits. These are divided into two regions, one provided by OIR, and the second designed by the user to meet specific needs and requirements. A prefix precedes the code number and is used to identify the type of part (e.g., a prefix value of 1 indicates machined and sheet metal parts). For a machined part, the coding for the first 18 digit positions (after the prefix) is summarized in Table 15.2.TABLE 15.2 First 18 digits of the MultiClass Classification and成组技术和单元化制造一、 零件族零件族(part families)是具有相似的几何形状和大小或具有相似的制造工艺的零件的集合。
S195柴油机镗孔组合机床夹具设计及研究

S195柴油机镗孔组合机床夹具设计及研究作者:王翔陈小瑞杨升娄高翔王慧玲杨静赵圆圆来源:《科技探索》2013年第01期摘要:本文介绍了S195柴油机镗孔组合机床夹具的设计,对其设计流程进行概述及研究。
关键词:夹具定位夹紧力夹具体引言S195柴油机在工农业生产中广泛应用,机体是柴油机重要零件,镗孔是机体加工中最重要的工序,故提供高精度适用的组合机床对S195柴油机提高生产质量有着重要作用。
夹具是机械制造厂里的一种重要的工艺装备,组合机床的夹具是作为机床的主要部分,其设计是整个组合机床设计的重要组成部分之一,组合机床夹具应便于实现定位夹紧的自动化,保证加工精度。
1 专用夹具设计的基本要求1.1 稳定的保证工件的加工精度:专用夹具要有合理的定位、夹紧方案,选择适当的尺寸公差及其技术要求,进行精度分析。
1.2提高生产率并降低成本:根据生产批量的大小,设计不同复杂的高效夹具,缩短辅助时间,提高生产率。
1.3具有良好的使用性:尽量使用专用夹具操作方便、省力、安全可靠,设计和配备安全防护装置。
1.4具有良好的结构工艺性:专用夹具应便于制造、检验、装配、调整和维修等。
2 定位支撑系统在组合机床上加工时,必须使被加工零件对刀具及其导向保持正确的相对位置,这靠夹具的定位支承系统来实现。
定位支承系统由定位支承,辅助支承和一些限位元件组成,设计原则:2.1合理布置定位支承元件,使其组成较大的定位支承界面;2.2提高刚性,减少定位支承系统的变形;2.3提高定位支承系统的精度及元件的耐磨性,保持夹具的定位精度;2.4可靠的排除定位支承部位的切削。
S195 柴油机侧面粗镗组合机床加工零件采用一面两销定位方式:底平面取三点限制工件沿 Z 轴向移动、绕 X 轴和 Y 轴转动三个自由度。
两个定位销一个采用圆柱形,一个采用菱形,圆柱定位销限制工件沿 X 轴和 Y 轴轴向移动,菱形销限制绕 Z 轴转动。
3 定位夹紧设计3.1 定位误差的分析由六点定位原理,设计和检查工件在夹具上的正确位置,能否满足工件对工序加工精度的要求,取决于刀具与工件之间正确的相互位置。
S195-05006型曲轴铣端面打中心孔组合机床及专用夹具设计
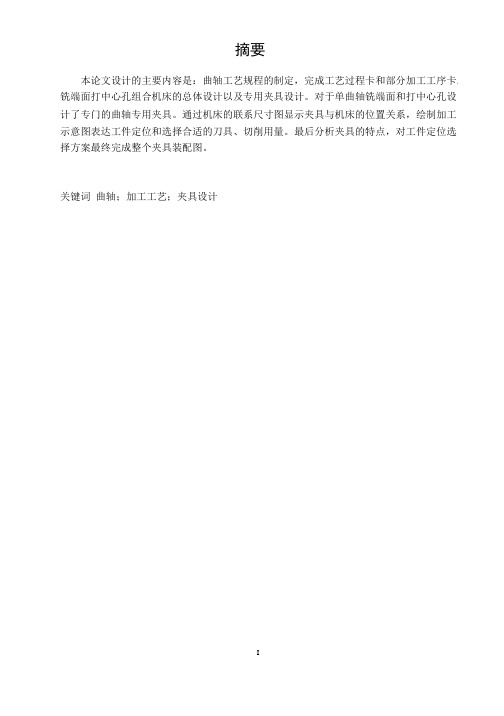
摘要本论文设计的主要内容是:曲轴工艺规程的制定,完成工艺过程卡和部分加工工序卡,铣端面打中心孔组合机床的总体设计以及专用夹具设计。
对于单曲轴铣端面和打中心孔设计了专门的曲轴专用夹具。
通过机床的联系尺寸图显示夹具与机床的位置关系,绘制加工示意图表达工件定位和选择合适的刀具、切削用量。
最后分析夹具的特点,对工件定位选择方案最终完成整个夹具装配图。
关键词曲轴;加工工艺;夹具设计Abstrac tThe main contents of this paper are: the development of crankshaft design process, complete the process card and process card, the overall design center bore modular machine milling and special fixture design. For single shaft end face milling and the center hole of crankshaft fixture design special. Thr ough the contact size map machine display position between the clamping and the machine,drawing processing sketch expression of workpiece positioning and selection of cutter s, cutting the right. Finally, analys is the characteristic of fixture,scheme and ultimately complete the workpiece positioning optionsKeywordss crankshaft processing technology fixture design目录摘要................................................................................................................................................................................................... Absttract..................................................................................................................................................................................... ...I II目录....................................................................................................................................................................................... 1绪论.............................................................................................................................................................................................. 1.1序言....................................................................................................................................................................................III 1 11.2曲轴的结构特点 (1)1.3曲轴的工艺特征 (1)1.4零件的技术要求 (2)1.5设计要求 (2)2工艺规程的制定 (3)2.1曲轴材料及毛坯 (3)2.2生产类型及工艺特征 (3)2.3定位基准的选择 (4)2.4工艺路线的拟定 (4)2.5毛坯机械加工余量及工序尺寸确定 (5)2.5.1毛坯机械加工余量确定 (5)2.5.2主要切削用量的确定 (6)3铣端面打中心孔组合机床的总体设计 (8)3.1组合机床结构方案的确定 (8)3.2铣端面打中心孔组合机床配置形式的选择 (8)3.2.1组合机床配置形式 (8)3.3被加工零件的工序图 (9)3.3.1被加工零件工序图的作用和要求 (9)3.3.2零件工序图的内容 (9)3.4被加工零件加工示意图 (10)3.4.1加工示意图的作用和内容103.5.1 3.5.2 3.5.3机床装料高度的确定 (12)夹具外形轮廓尺寸的确定 (13)机床通用部件的选择 (13)4专用夹具设计 (16)4.1专用夹具特点及步骤 (16)4.1.1组合机床专用夹具的特点 (16)4.1.2组合机床夹具设计步骤 (16)4.2夹具定位支撑系统 (17)4.2.1工件定位方案 (17)4.2.2定位误差分析 (18)4.3夹紧机构 (18)4.4夹紧装置设计的步骤 (19)4.5铣床夹具设计要点 (21)4.6对刀引导装置的设计 (21)4.6.1对刀块的设计 (21)4.6.2钻套、衬套设计 (22)5夹具体结构设计 (25)结论 (26)致谢 (27)参考文献 (28)1绪论1.1序言毕业设计是对所学各课程的一次深入的综合性的复习,也是一次理论联系实际的训练。
S195机体机械加工工艺及精镗三面孔工序夹具设计

关键词:S195机体;机械加工工艺规程;精镗夹具
The Design of Process Plan and Fixture for Finishing Boring of The Three Dimensional for S195 Diesel Engine Frame
Abstract
Modern manufacturing process is not only an important part of advanced manufacturing technology, but also its most dynamic part. A product from design to reality must be completed through the production process, and therefore the process is designed, manufactured bridge, the general feasibility of the design will be the level of technology constraints. Meanwhile, in the machining process, the fixture occupies a very important position, it is reliably ensure the machining accuracy of the workpiece, improve processing efficiency, reduce the intensity of labor.
组合机床及夹具设计开题报告
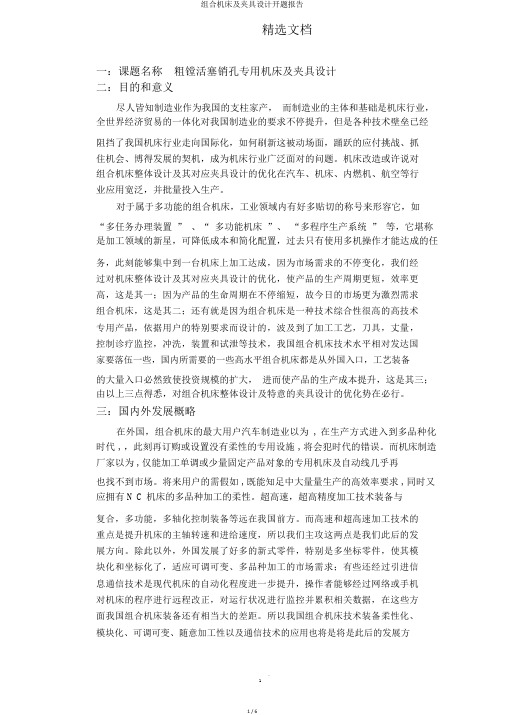
精选文档一:课题名称粗镗活塞销孔专用机床及夹具设计二:目的和意义尽人皆知制造业作为我国的支柱家产,而制造业的主体和基础是机床行业,全世界经济贸易的一体化对我国制造业的要求不停提升,但是各种技术壁垒已经阻挡了我国机床行业走向国际化,如何刷新这被动场面,踊跃的应付挑战、抓住机会、博得发展的契机,成为机床行业广泛面对的问题。
机床改造或许说对组合机床整体设计及其对应夹具设计的优化在汽车、机床、内燃机、航空等行业应用宽泛,并批量投入生产。
对于属于多功能的组合机床,工业领域内有好多贴切的称号来形容它,如“多任务办理装置” 、“ 多功能机床”、“多程序生产系统” 等,它堪称是加工领域的新星,可降低成本和简化配置,过去只有使用多机操作才能达成的任务,此刻能够集中到一台机床上加工达成,因为市场需求的不停变化,我们经过对机床整体设计及其对应夹具设计的优化,使产品的生产周期更短,效率更高,这是其一;因为产品的生命周期在不停缩短,故今日的市场更为激烈需求组合机床,这是其二;还有就是因为组合机床是一种技术综合性很高的高技术专用产品,依据用户的特别要求而设计的,波及到了加工工艺,刀具,丈量,控制诊疗监控,冲洗,装置和试泄等技术,我国组合机床技术水平相对发达国家要落伍一些,国内所需要的一些高水平组合机床都是从外国入口,工艺装备的大量入口必然致使投资规模的扩大,进而使产品的生产成本提升,这是其三;由以上三点得悉,对组合机床整体设计及特意的夹具设计的优化势在必行。
三:国内外发展概略在外国,组合机床的最大用户汽车制造业以为, 在生产方式进入到多品种化时代 , ,此刻再订购或设置没有柔性的专用设施 , 将会犯时代的错误。
而机床制造厂家以为 , 仅能加工单调或少量固定产品对象的专用机床及自动线几乎再也找不到市场。
将来用户的需假如 , 既能知足中大量量生产的高效率要求 , 同时又应拥有 N C 机床的多品种加工的柔性。
超高速,超高精度加工技术装备与复合,多功能,多轴化控制装备等远在我国前方。
高精度三轴镗孔专用机床的设计和研究的开题报告
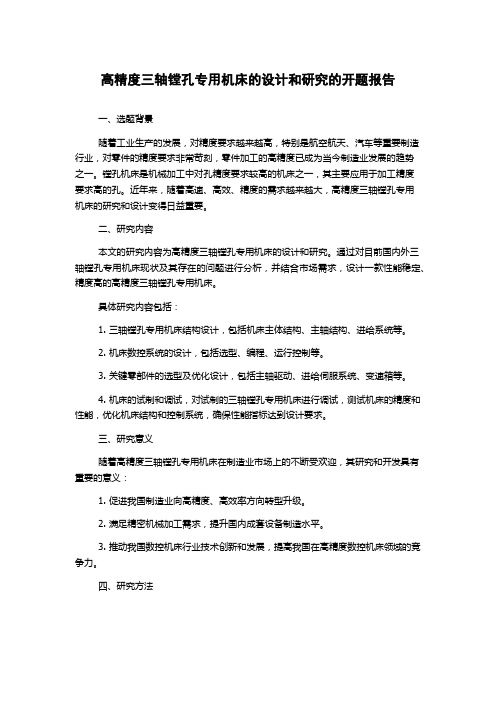
高精度三轴镗孔专用机床的设计和研究的开题报告一、选题背景随着工业生产的发展,对精度要求越来越高,特别是航空航天、汽车等重要制造行业,对零件的精度要求非常苛刻,零件加工的高精度已成为当今制造业发展的趋势之一。
镗孔机床是机械加工中对孔精度要求较高的机床之一,其主要应用于加工精度要求高的孔。
近年来,随着高速、高效、精度的需求越来越大,高精度三轴镗孔专用机床的研究和设计变得日益重要。
二、研究内容本文的研究内容为高精度三轴镗孔专用机床的设计和研究。
通过对目前国内外三轴镗孔专用机床现状及其存在的问题进行分析,并结合市场需求,设计一款性能稳定、精度高的高精度三轴镗孔专用机床。
具体研究内容包括:1. 三轴镗孔专用机床结构设计,包括机床主体结构、主轴结构、进给系统等。
2. 机床数控系统的设计,包括选型、编程、运行控制等。
3. 关键零部件的选型及优化设计,包括主轴驱动、进给伺服系统、变速箱等。
4. 机床的试制和调试,对试制的三轴镗孔专用机床进行调试,测试机床的精度和性能,优化机床结构和控制系统,确保性能指标达到设计要求。
三、研究意义随着高精度三轴镗孔专用机床在制造业市场上的不断受欢迎,其研究和开发具有重要的意义:1. 促进我国制造业向高精度、高效率方向转型升级。
2. 满足精密机械加工需求,提升国内成套设备制造水平。
3. 推动我国数控机床行业技术创新和发展,提高我国在高精度数控机床领域的竞争力。
四、研究方法本论文采用文献资料法、试制法、数值模拟法等多种研究方法,以确定高精度三轴镗孔专用机床的性能指标,进行机床结构设计、数值模拟、试制和测试,最终确定性能指标符合要求的三轴镗孔专用机床。
五、预期成果本论文研究结果将主要表现在以下几个方面:1. 设计出一种性能稳定、精度高的高精度三轴镗孔专用机床。
2. 对数控机床控制系统进行优化,提高数控机床的加工效率和精度。
3. 完成试制和调试工作,对机床进行有效的性能测试,以达到设计与市场要求的精度标准。
S195柴油机机体双面粗镗组合机床 总体及夹具设计
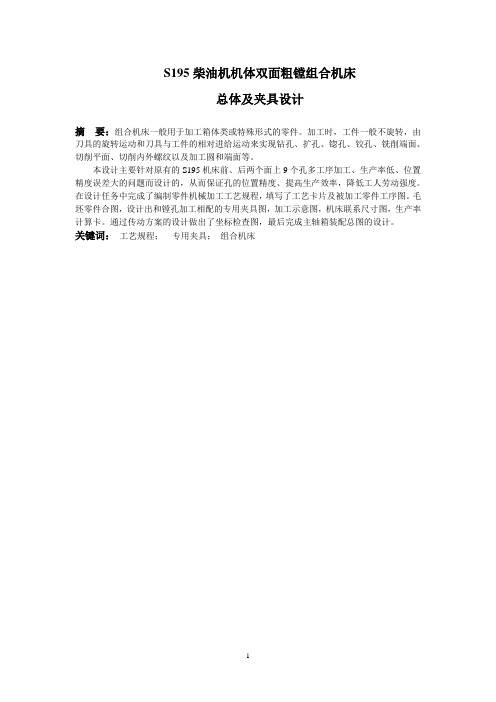
S195柴油机机体双面粗镗组合机床总体及夹具设计摘要:组合机床一般用于加工箱体类或特殊形式的零件。
加工时,工件一般不旋转,由刀具的旋转运动和刀具与工件的相对进给运动来实现钻孔、扩孔、锪孔、铰孔、铣削端面、切削平面、切削内外螺纹以及加工圆和端面等。
本设计主要针对原有的S195机床前、后两个面上9个孔多工序加工、生产率低、位置精度误差大的问题而设计的,从而保证孔的位置精度、提高生产效率,降低工人劳动强度。
在设计任务中完成了编制零件机械加工工艺规程,填写了工艺卡片及被加工零件工序图。
毛坯零件合图,设计出和镗孔加工相配的专用夹具图,加工示意图,机床联系尺寸图,生产率计算卡。
通过传动方案的设计做出了坐标检查图,最后完成主轴箱装配总图的设计。
关键词:工艺规程;专用夹具;组合机床S195 Diesel Engine Organism Two-sided Thick Boring Aggregate Machine-tool Overall and Jig DesignAbstract:The aggregate machine-tool uses in processing the box body class generally or the special form components. When processing,the work piece does not revolve generally,realizes the drill hole,the broaching by cutting tool’s rotary motion and the cutting tool and the work piece relative feed motion,hue the hole,to bore,the milling end surface,the cutting plane,to cut the inside and outside threads as well as the processing circle and the end surface and so on.This design mainly aims at the original S195 organism before and,on two surface 9 hole multi-working processing,the productivity to be low,the position curry error major problem design,thus the guarantee hole’s position precision,the enhancement production efficiency,reduces the worker labor intensity. Has completed the establishment components machine-finishing technological process in the task of design,has filled in the process chart and is processed the components working procedure chart,the semi finished materials components gathers the chart,designs and bores the processing appropriate match unit clamp chart,the processing schematic drawing,the engine bed relation dimensional drawing,the productivity computation card. Made the coordinate inspection chart through the transmission plan’s design,finally completed the head stock assembly drawing the design.Keywords:Manufacturing Process Planning; Special Jig Design Combination; Machine-tool前言 (4)1 工艺规程设计 (5)1.1 总体方案设计 (5)1.1.1 工艺方案的拟定 (5)1.1.2 定位基准的选择 (21)1.2 确定切削用量及选择刀具 (21)1.2.1 选择切削用量 (21)1.2.2 计算切削力、切削扭矩及切削功率 (22)1.2.3 选择刀具结构 (23)1.3 组合机床总体设计——三图一卡 (23)1.3.1 被加工零件工序图 (23)1.3.2 加工示意图 (24)1.3.3 机床尺寸联系总图 (25)1.3.4 机床生产率计算卡 (27)1.4 夹具设计 (28)1.4.1专用夹具设计的基本要求 (29)1.4.2 夹具设计的规范程序 (29)2 组合机床主轴箱设计 (31)2.1 绘制主轴箱原始依据图 (31)2.2 主轴结构型式的选择和动力计算 (31)2.2.1 主轴结构型式的选择 (31)2.2.2 主轴直径和齿轮模数的确定 (32)2.3 主轴箱传动系统的设计与计算 (32)2.3.1 根据原始依据图计算坐标尺寸 (32)2.3.2 拟订主轴箱传动路线 (33)2.3.3 确定传动轴位置及齿轮齿数 (33)2.4 主轴箱坐标计算、绘制作表检查图 (35)2.4.1 计算传动轴的坐标 (35)2.4.2 绘制坐标检查图 (35)2.5 轴、齿轮的校核 (35)2.5.1 轴的校核 (35)2.5.2 齿轮的校核 (36)结论 (38)致谢 (39)参考文献 (40)前言在机械制造中,对于单件或小批量生产的工件,许多工厂采用通用机床进行加工。
2151 S195柴油机机体三面精镗组合机床总体设计及左主轴箱设计(DOC)
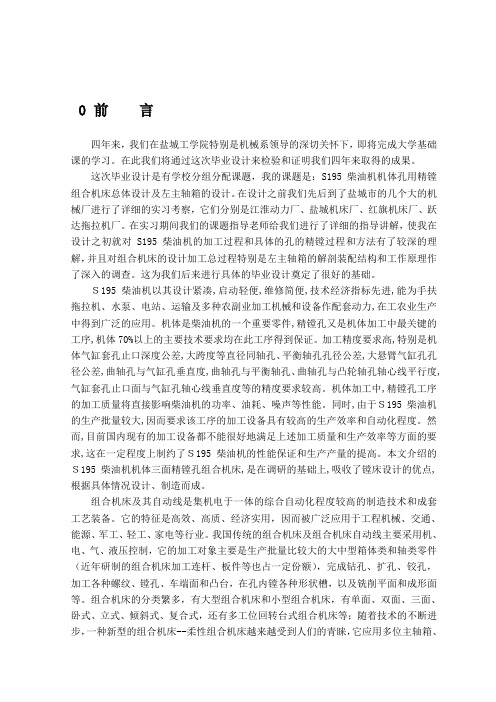
0 前言四年来,我们在盐城工学院特别是机械系领导的深切关怀下,即将完成大学基础课的学习。
在此我们将通过这次毕业设计来检验和证明我们四年来取得的成果。
这次毕业设计是有学校分组分配课题,我的课题是:S195柴油机机体孔用精镗组合机床总体设计及左主轴箱的设计。
在设计之前我们先后到了盐城市的几个大的机械厂进行了详细的实习考察,它们分别是江淮动力厂、盐城机床厂、红旗机床厂、跃达拖拉机厂。
在实习期间我们的课题指导老师给我们进行了详细的指导讲解,使我在设计之初就对S195柴油机的加工过程和具体的孔的精镗过程和方法有了较深的理解,并且对组合机床的设计加工总过程特别是左主轴箱的解剖装配结构和工作原理作了深入的调查。
这为我们后来进行具体的毕业设计奠定了很好的基础。
S195柴油机以其设计紧凑,启动轻便,维修简便,技术经济指标先进,能为手扶拖拉机、水泵、电站、运输及多种农副业加工机械和设备作配套动力,在工农业生产中得到广泛的应用。
机体是柴油机的一个重要零件,精镗孔又是机体加工中最关键的工序,机体70%以上的主要技术要求均在此工序得到保证。
加工精度要求高,特别是机体气缸套孔止口深度公差,大跨度等直径同轴孔、平衡轴孔孔径公差,大悬臂气缸孔孔径公差,曲轴孔与气缸孔垂直度,曲轴孔与平衡轴孔、曲轴孔与凸轮轴孔轴心线平行度,气缸套孔止口面与气缸孔轴心线垂直度等的精度要求较高。
机体加工中,精镗孔工序的加工质量将直接影响柴油机的功率、油耗、噪声等性能。
同时,由于S195柴油机的生产批量较大,因而要求该工序的加工设备具有较高的生产效率和自动化程度。
然而,目前国内现有的加工设备都不能很好地满足上述加工质量和生产效率等方面的要求,这在一定程度上制约了S195柴油机的性能保证和生产产量的提高。
本文介绍的S195柴油机机体三面精镗孔组合机床,是在调研的基础上,吸收了镗床设计的优点,根据具体情况设计、制造而成。
组合机床及其自动线是集机电于一体的综合自动化程度较高的制造技术和成套工艺装备。
开题报告-连杆镗孔专用机床设计

开题报告“连杆镗孔专用机床设计”开题报告1.选题背景及其意义1.1国内外研究动态2003 年开始,中国就成了全球最大的机床消费国,也是世界上最大的数控机床进口国。
目前正在提高机械加工设备的数控化率,1999 年,我们国家机械加工设备数控华率是5-8%,目前预计是15-20%之间。
车、铣、刨、磨、镗、钻、电火花、剪板、折弯、激光切割等等都是机械加工方法,所谓机械加工,就是把金属毛坯零件加工成所需要的形状,包含尺寸精度和几何精度两个方面。
能完成以上功能的设备都称为机床,数控机床就是在普通机床上发展过来的,数控的意思就是数字控制。
给机床装上数控系统后,机床就成了数控机床。
当然,普通机床发展到数控机床不只是加装系统这么简单,例如:从铣床发展到加工中心,机床结构发生变化,最主要的是加了刀库,大幅度提高了精度。
加工中心最主要的功能是铣、镗、钻的功能。
我国目前各种门类的数控机床都能生产,水平参差不齐,有的是世界水平,有的比国外落后10-15 年,但如果国家支持,追赶起来也不是什么问题,例如:去年,沈阳机床集团收购了德国西思机床公司,意义很大,如果大力消化技术,可以缩短不少差距。
大连机床公司也从德国引进了不少先进技术。
上海一家企业购买日本著名的机床制造商池贝。
近几年随着中国制造的崛起,欧洲不少企业倒闭或者被兼并,如马毫、斯滨纳等。
日本经济不景气,有不少在80 年代很出名的机床制造商倒闭,例如:新泻铁工所。
现代机床的研究方向包括六个方面:智能化、网络化、高速、高精度、符合、环保。
目前德国和瑞士的机床精度最高,综合起来,德国的水平最高,日本的产值最大。
美国的机床业一般。
中国大陆、韩国。
台湾属于同一水平。
但就门类、2种类多少而言,我们应该能进世界前4 名。
长期以来,国产数控机床始终处于低档迅速膨胀,中档进展缓慢,高档依靠进口的局面,特别是国家重点工程需要的关键设备主要依靠进口,技术受制于人。
究其原因,国内本土数控机床企业大多处于“粗放型”阶段,在产品设计水平、质量、精度、性能等方面与国外先进水平相比落后了5-10 年;在高、精、尖技术方面的差距则达到了10-15 年。
S195柴油机镗孔组合机床液压系统概述及研究

S195柴油机镗孔组合机床液压系统概述及研究作者:黄作同白泳涛来源:《科技探索》2013年第07期摘要:本文介绍了应用在S195柴油机镗孔组合机床上的液压系统的结构,介绍了液压技术的发展现状和趋势,了解了液压技术的发展情况和应用的情况,同时,简明扼要地概述了设计液压系统的过程及步骤。
关键词:组合机床液压传动工况分析液压泵站引言组合机床是一种工序集中的高效率专用机床,它具有加工范围较广、自动化程度较高,经济性好等优点,故在机械制造业的成批和大量生产中得到普遍应用。
S195柴油机在生产中应用广泛,镗孔是其机体加工中最重要的工序,故提供高精度的组合机床对提高S195柴油机生产效率有重要作用。
液压传动装置是本组合机床的动力源,液压传动技术是在在工业生产中应用相当广泛的一种传动技术,液压技术发展到今天已经成为一门重要的自动化技术,是衡量一个国家工业化水平的重要标志。
1液压技术的发展及S195柴油机镗孔组合机床液压系统概述1.1液压技术在国内外的发展趋势近年来,国外、国内液压技术由于广泛应用了高新技术成果,如自动控制技术、计算机技术、微电子技术、磨擦磨损技术、可靠性技术及新工艺和新材料,使传统技术有了新的发展,也使液压系统和元件的质量、水平有一定的提高。
主要的发展趋势将集中在以下几个方面:1.减少能耗,充分利用能量 2.主动维护和故障预测 3.机电一体化。
液压技术作为便捷和廉价的自动化技术,有着良好的前景。
其产品不仅在机电、轻纺、家电等传统领域有着很大的市场,且在新兴的产业如信息技术产业、生物制品业、微纳精细加工等领域都有广阔的发展空间。
1.2 S195柴油机组合机床液压传动系统组合机床液压传动系统的结构这样布置:其动力箱安装在滑台上,动力箱上的电动机带动刀具实现运动。
滑台采用液压驱动,完成刀具的进给运动,根据不同的加工需要可实现多种进给工作循环。
一个完整的液压系统由五个部分组成,即动力元件、执行元件、控制元件、辅助元件和液压油。
- 1、下载文档前请自行甄别文档内容的完整性,平台不提供额外的编辑、内容补充、找答案等附加服务。
- 2、"仅部分预览"的文档,不可在线预览部分如存在完整性等问题,可反馈申请退款(可完整预览的文档不适用该条件!)。
- 3、如文档侵犯您的权益,请联系客服反馈,我们会尽快为您处理(人工客服工作时间:9:00-18:30)。
〔7〕堵顺芬.小型组合机床简介[J].机械制造, 1981, (3).
〔8〕焦丽丽,刘德仿.组合机床CAD技术的研究现状及发展趋势[J].机械科学与技术, 2012, 29(2):1-5.
〔9〕闫海鹏,王建国,肖楠.加工中心床头箱箱体双面镗孔组合机床设计[J].组合机床与自动化加工技术, 2015, (1).
因此,本课题就S195柴油机缸体侧面镗孔工艺设计组合机床,保证加工质量并提高生产效率。
二.组合机床的发展
最早的组合机床是1911年在美国制成的,用于加工汽车零件。初期,各机床制造厂都有各自的通用部件标准。为了提高不同制造厂的通用部件的互换性,便于用户使用和维修,1953年美国福特汽车公司和通用汽车公司与美国机床制造厂协商,确定了组合机床通用部件标准化的原则,即严格规定各部件间的联系尺寸,但对部件结构未作规定。
〔2〕李纪明,许敬成. S195柴油机机体三面精镗孔组合机床[J].组合机床与自动化加工技术, 1998, (11):9-14.
〔3〕《组合机床设计》.辽宁:大连机床厂,1978.
〔4〕《组合机床及其自动化》.北京:人民交通出版社,2009.
〔5〕《组合机床设计简明手册》.北京:机械工业出版社,2014.
二○一五届毕业设计
开题报告
学院:工程机械学院
专业:机械设计制造及其自动化
姓名:芦瑶
学号:201125040323
指导教师:张接信
完成时间:2014年3月28日
课题名称
S195柴油机镗孔(右)组合机床设计
课题来源
自选项目
课题类型
机械设计
指导教师
张接信
学生姓名
芦瑶
学号
201126040323
专业
机械设计制造及其自动化
a)组合机床被加工零件的夹具设计
b)主轴箱传动系统的设计
c)组合机床的总体配置形式
解决方法是通过已学过的基础理论和专业知识并参考各类相关专业书籍,熟悉组合机床工作原理和设计原则,了解各项设计参数和技术要求进行设计计算,同时利用绘图软件进行初步结构设计,参考已有的先进设计实例,学习其计算过程和其中的先进创新理念并运用到自己的计算创新设计中。相关难以解决的问题可以与同学讨论解决,一些自己的创新思想也可与同学讨论其可行性,或者向指导教师请教。
四.课题的目的和意义
本设计涉及到机制专业学生所学的主要专业课和专业基础课,根据被加工零件的特点及工艺要求,考虑制定零件在组合机床上合理可行的加工方案,确定机床配置型式和结构方案,并合理解决工序集中的问题,考虑结构方案实现的可能性和工作的可靠性及其他各方面应注意的问题,得到机制专业方面能力的训练,对即将从事的工作起到一定适应性的作用。
柴油机是拖拉机上的主要零件,属于大批大量生产。生产中常用组合机床和专用机床组成的流水线进行组织生产。通过对组合机床结构原理和设计的了解,设计出符合生产要求的镗孔组合机床,并且在一定层次上有所发现,进而推动S195柴油机制造行业的发展。
主要参考资料
〔1〕吴立梅.组合机床发展及相关特点分析[J].科技资讯, 2010, (8):86-86.
长安大学毕业设计(论文)开题报告表
一定孔内镗各种形状槽,以及铣削平面和成形面等。【2】组合机床的分类繁多,有大型组合机床和小型组合机床,有单面、双面、三面、卧式、立式、倾斜式、复合式,还有多工位回转台式组合机床等;【3】随着技术的不断进步,一种新型的组合机床——柔性组合机床越来越受到人们的青睐,它应用多位主轴箱、可换主轴箱、编码随行夹具和刀具的自动更换,配以可编程序控制器(PLC)、数字控制(NC)等,能任意改变工作循环控制和驱动系统,并能灵活适应多品种加工的可调可变的组合机床。【4】另外,近年来组合机床加工中心、数控组合机床、机床辅机(清洗机、装配机、综合测量机、试验机、输送线)等在组合机床中所占份额也越来越大。由于组合机床及其自动线是一种技术综合性很高的高技术专用产品,是根据用户特殊要求而设计的,它涉及到加工工艺、刀具、测量、控制、诊断监控、清洗、装配和试漏等技术。【5】我国组合机床及组合机床自动线总体技术水平比发达国家要相对落后,国内所需的一些高水平组合机床及自动线几乎都从国外进口。工艺装备的大量进口势必导致投资规模的扩大,并使产品生产成本提高。因此,市场要求我们不断开发新技术、新工艺,研制新产品,由过去的“刚性”机床结构,向“柔性”化方向发展,满足用户需求,真正成为刚柔兼备的自动化装备
五.预期完成成果及提交文件
1.计算说明书部分:设计、计算、验证过程;组合机床生产率计算卡;设计说明书。
2.图纸部分:S195柴油机零件图;工序图(右);加工示意图(右);尺寸联系图(右);零件图(右)。
六.毕业设计(论文)进程安排
毕业设计(论文)进程安排
序号设计(论文)各阶段名称日期(教学周)
1课题调研、查阅资料1-3
组合机床未来的发展将更多的采用调速电动机和滚珠丝杠等传动,以简化结构、缩短生产节拍;采用数字控制系统和主轴箱、夹具自动更换系统,以提高工艺可调性;以及纳入柔性制造系统等。
三.组合机床的研究现状
在我国,组合机床发展已有28年的历史,其科研和生产都具有相当的基础,应用也已深入到很多行业。是当前机械制造业实现产品更新,进行技术改造,提高生产效率和高速发展必不可少的设备之一。组合机床及其自动线是集机电于一体的综合自动化程度较高的制造技术和成套工艺装备。它的特征是高效、高质、经济实用,因而被广泛应用于工程机械、交通、能源、军工、轻工、家电等行业。我国传统的组合机床及组合机床自动线主要采用机、电、气、液压控制,它的加工对象主要是生产批量比较大的大中型箱体类和轴类零件(近年研制的、板件等也占份额),完成钻孔、扩孔、铰孔,加工各种螺纹、镗孔、车端面和凸台,在
(4)组合机床的部件设计夹具设计步骤:①明确设计要求,收集和研究有关资料。②确定夹具的结构方案。③绘制夹具的装配草图和装配图。④确定并标注有关尺寸、配合及技术要求。⑤绘制夹具零件。⑥图编写夹具设计说明书;
主轴箱设计步骤:①确定有关尺寸参数、运动参数及动力参数。②据所求得的有关运动参数及给定的公比,写出结构式,校验转速范围,绘制转速图。③确定各变速组传动副的传动比值,定齿轮齿数、带轮直径,校验三联滑移齿轮齿顶是否相碰,校验各级转速的转速误差。④绘制传动系统图。
(2)机床结构的方案的分析和确定根据工艺方案确定机床的形式和布局。在选择机床的配置形式时候,既要实现工艺方案,保证加工精度,技术要求及生产率;又要考虑机床操作维护,修理是否方便,排屑情况是否良好;还要注意被加工零件的生产质量,以便设计的组合机床符合多快好省的要求。
(3)组合机床总体设计这里要确定机床各部件的间的相互关系,选择通用部件的导向,计算切削用量及机床的生产率。绘制三图一卡:被加工零件工序图、加工示意图、机床尺寸联系尺寸图、编绘生产率计算卡。
指导教师意见及建议:
指导教师签名:
注:1、课题来源分为:国家重点、省部级重点、学校科研、校外协作、实验室建设和自选项目;课题类型分为:工程设计、专题研究、文献综述、综合实验
2、此表由学生填写,交指导教师签署意见后方可开题。
四.本课题的研究内容、方法、手段及预期成果
1.研究内容:S195柴油机侧面镗孔组合机床设计(右侧)
2.设计原始资料:S195柴油机零件图,柴油机机体工序图、组合机床设计、机械结构设计等参体步骤:
(1)制定工艺方案了解被加工零件的加工特点,精度和技术要求,定位夹紧情况以及生产率的要求等等。确定在组合机床上完成的工艺内容和其加工方法。确定加工步数,决定刀具的种类及形式。
一.课题背景
柴油机是以柴油为燃料的内燃机,柴油机的缸体是柴油机最重要的部件,它支撑气缸内部的运动,保证动力及运动进给的稳定。S195柴油机以其设计紧凑,启动轻便,维修简便,技术经济指标先进,能为手扶拖拉机、水泵、电站、运输及多种农副业加工机械和设备作配套动力,在工农业生产中得到广泛的应用。缸体是柴油机的一个重要零件,镗孔又是缸体加工中最关键的工序,缸体主要技术要求均在此工序得到保证。加工精度要求高,特别是机体气缸套孔止口深度公差,大跨度等直径同轴孔、平衡轴孔孔径公差,大悬臂气缸孔孔径公差,曲轴孔与气缸孔垂直度,曲轴孔与平衡轴孔、曲轴孔与凸轮轴孔轴心线平行度,气缸套孔止口面与气缸孔轴心线垂直度等的精度要求较高。【1】机体加工中,镗孔工序的加工质量将直接影响柴油机的功率、油耗、噪声等性能。同时,由于S195柴油机的生产批量较大,因而要求该工序的加工设备具有较高的生产效率和自动化程度。然而,目前国内现有的加工设备都不能很好地满足上述加工质量和生产效率等方面的要求,这在一定程度上制约了S195柴油机的性能保证和生产产量的提高。
2外文资料翻译、开题报告4-5
3方案设计6
4具体内容设计、计算、分析7-15
5图纸设计7-15
6撰写毕业设计说明书、毕业答辩16-18
六.完成任务所具备的条件因素
机械加工机床设计是该专业的主干技能之一,我已经完成了机械制造装备设计的相关知识和实训,具有一定的专业基础,在设计的过程会面相对实际具体的问题如: