塑料注塑加工成型过程中的故障及其排除
塑料注塑加工成型过程中的故障和排除.pptx

注塑成型故障排除
毛边
诊断: •锁模力过低和机构故障 •过高的注射压力 •注射速度太快 •分型面破损 •不匹配 •料温过高
注塑成型故障排除
烧焦
诊断: • 机器止回阀问题 • 注射速度过快 • 背压过大 • 模具排气不良 • 检查浇口 • 料太冷或过热
注塑成型故障排除
浇口斑白/流点
诊断:
材料温度差异的结果.
注塑成型故障排除
沉陷
诊断:
无足够的材料或较厚肋
•注射压力过低 •射胶时间太短 •塑化能力不足 •模温太高 •浇口过小 •流道过长 •错误的肋/壁厚比 •料温过高 •错误浇口位置 •错误的排气位置
注塑成型故障排除
条纹(银纹, 飞溅点, 丝状点)
起因: 塑胶粒中的水分, 残留非水性的挥发物---遍布产品表面 降解---产品部分表面有一团或粗糙线
• 2、Our destiny offers not only the cup of despair, but the chalice of opportunity. (Richard Nixon, American President )命运给予我们的不是失望之酒,而是机会之杯。二〇二〇年八月五日2020年8月5 日星期三
注塑成型故障排除
脱模问题
粘前模/粘后模/粘浇道
粘前模
诊断: •注射压力过高 •注射速度过高 •保压时间过长 •注的过满
• 型腔太热 • 模具太冷 • 模具表面过于粗糙 • 熔料温度过高 • 模具设计问题
注塑成型故障排除
粘后模
诊断
•注射压力过高 •型芯弯曲 •型芯温度过低
• 产生真空---尤其薄壁塑件 • 型芯和型腔温差过大 • 模具设计问题
注塑成型故障排除
注塑过程中常见的问题及解决方案

注塑过程中常见的问题及解决方案一、飞边(披锋)1. 问题描述- 这飞边就像塑料偷偷长出来的小翅膀,在注塑件的边缘或者分型面那里冒出来,看着可闹心了。
就像好好的一块蛋糕,边缘突然多出了一些不规则的奶油坨坨。
2. 解决方案- 首先得检查模具的合模力。
要是合模力不够,那塑料就会像调皮的小孩从门缝里挤出来。
适当增加合模力,把模具紧紧抱住,让塑料乖乖待在该待的地方。
- 模具的磨损也会导致飞边。
就像穿破了的鞋子会漏脚指头一样,磨损的模具缝隙变大了。
这时候就得修模啦,把那些磨损的地方补一补或者磨平。
- 注塑压力也不能太大。
如果压力太大,塑料就像被大力士猛推的水,到处乱流。
降低注塑压力,找到一个合适的值,既能把模具填满,又不会让塑料溢出来。
二、短射(缺料)1. 问题描述- 短射就像给一个杯子倒水,结果没倒满一样。
注塑件看着不完整,有些地方该有塑料的却空着,就像一个没发育好的小怪物。
2. 解决方案- 先看看注塑压力是不是太小。
压力小的话,塑料就像没力气的小蚂蚁,爬不到模具的每个角落。
增加注塑压力,让塑料充满整个模具型腔。
- 塑料的流动性也很关键。
如果塑料太黏,就像浓稠的糨糊,很难流到模具的远端。
这时候可以提高料筒温度,让塑料变得稀一点,流动性更好,就像把糨糊加热变成稀粥一样,能顺利流到各个地方。
- 浇口尺寸也可能有问题。
要是浇口太小,就像一个小得可怜的水龙头,水流不出来多少。
适当扩大浇口尺寸,让塑料能畅快地流进模具。
三、气泡(气穴)1. 问题描述2. 解决方案- 注塑速度可能太快了。
塑料像一阵风呼呼地冲进模具,把空气都裹在里面了。
降低注塑速度,让塑料慢慢流进去,就像散步一样,这样空气就有机会跑出来了。
- 模具的排气也很重要。
如果模具没有排气孔或者排气不良,空气就被困在里面出不来。
在模具上开排气槽或者使用透气钢材料,给空气一条逃跑的路。
- 塑料干燥不彻底也会产生气泡。
如果塑料里有水份,加热的时候就会变成水蒸气,形成气泡。
PVC发泡塑料注塑成型的14个故障,你都知道吗

本文摘自再生资源回收-变宝网()PVC发泡塑料注塑成型的14个故障,你都知道吗PVC发泡塑料注塑成型的14个故障,你都知道吗?溢料飞边(1)模具密封不严.应维修模具。
(2)冷却速度太慢。
应提高冷却效率,增加冷却速度,最好在底模通冷却水,冷却效果较好。
(3)注射量和供料过多。
应适当减少。
(4)塑化时间和注射压力配合不当。
在测定出压力和发泡时间的关系曲线后,合理调整注射压力和发泡时间。
(5)料模内衬板翘曲变形。
应对内衬板进行修理或更换。
(6)液压系统漏油造成合模力不足。
应维修液压系统。
(7)销模钩子上的弹簧太松。
应调换弹簧,增加钩子的拉力。
(8)定型时间不够,制品表层尚未冷透,第一次开模时中间的热料突破表层外溢。
应适当延长第一开模时间。
起大泡(1)发泡剂的粒径太粗,分散不均匀。
一般发泡剂需经三辊研,在料筒内产生磨机研磨2~4遍,将其研细后使用。
(2)捏合及造粒时加工温度太高,发泡剂过早分解,粒子有发泡现象。
应适当降低捏合及造粒温度,挤出的粒子切开时不能有小泡。
(3)熔料在料筒种滞留时间太长或加工温度太高。
应采用快速预塑,已塑化的熔料应一次注完,并尽量采用一机多模生产。
(4)螺杆背压太小,熔料在料筒中受热膨胀。
应加大背压,使熔料内所含的发泡剂受热分解后无预膨胀的机会。
(5)料筒端部漏料,在端部出口处形成低压区,导致熔料在出口处膨胀形成气泡。
应适当降低出料口温度,最好在出料口部采用节流阀式结构,封住端部出口。
(6)再生料回用比例不当。
应适当减少其用量。
发泡倍率太大(1)发泡剂投料量太多,致使发气量过高。
应测定发气量,准确投料。
(2)增塑剂用量太多。
应适当减少。
(3)起模温度太高。
应降温出模。
(4)保压时间太短。
应保证制品完全定型后出模。
发泡倍率不够(1)发泡剂投料量太少,致使发气量不足。
应测定发气量,准确投料。
(2)增塑剂用量太少。
应适当增加投料量。
(3)制品在第二次加工时,第二次膨胀时间太短。
应适当延长加工时的蒸煮发泡时间,而且第一次和第二次发泡时间间隔不能超过12小时。
注塑成型常见不良现象及处理措施

注塑成型常见不良现象及处理措施在注塑成型过程中,常常会出现一些不良现象,这些现象可能会导致产品的质量下降,甚至无法使用。
因此,及时发现并解决这些问题是非常重要的。
下面将介绍一些常见的注塑成型不良现象及处理措施。
1. 短射短射是指注塑制品在填充过程中未能充满模具腔体,导致制品出现不完整的现象。
短射的原因可能有:- 注塑机温度设置过低,导致熔融物质无法充分流动;- 模具温度过低,使得熔融物质凝固速度过快;- 注射压力过低,无法将熔融物质充分填充到模具腔体中。
处理措施:- 调整注塑机温度,确保熔融物质能够充分流动;- 提高模具温度,延缓熔融物质的凝固速度;- 增加注射压力,确保熔融物质能够充分填充到模具腔体中。
2. 气泡气泡是指制品内部或表面出现的气体聚集现象,给产品的外观和性能带来负面影响。
气泡的原因可能有:- 熔融物质中含有过多的挥发性物质;- 注射速度过快,导致气体无法及时排出;- 模具中存在气体积聚的死角。
处理措施:- 选择低挥发性的熔融物质;- 控制注射速度,避免气体无法及时排出;- 优化模具结构,减少气体积聚的死角。
3. 热胀冷缩热胀冷缩是指注塑制品在冷却过程中由于热胀冷缩系数不一致而导致尺寸变化的现象。
热胀冷缩的原因可能有:- 注塑机温度和模具温度不匹配;- 熔融物质的热胀冷缩系数不一致。
处理措施:- 调整注塑机温度和模具温度的匹配度;- 选择热胀冷缩系数相近的熔融物质。
4. 毛刺毛刺是指制品表面出现的细小突起,给产品的外观和触感带来不良影响。
毛刺的原因可能有:- 模具中存在不平整的表面;- 注塑机压力过高,使得熔融物质溢出模具腔体。
处理措施:- 修复模具表面,保持其光滑平整;- 调整注塑机压力,避免熔融物质溢出模具腔体。
5. 缩水缩水是指注塑制品在冷却过程中由于体积收缩而导致尺寸变小的现象。
缩水的原因可能有:- 熔融物质中含有过多的收缩剂;- 注塑机温度和模具温度不匹配。
处理措施:- 选择低含量的收缩剂;- 调整注塑机温度和模具温度的匹配度。
注塑模具一些常见故障的排除方法

注塑模具一些常见故障的排出方法注塑模具的结构形式和模具加工质量直接影响着塑件制品质量和生产效率。
注塑模具生产和塑料制品生产实践中zui常见,zui常显现的一些模具故障及其重要原因分析排出如下。
1.浇口脱料困难。
在注塑过程中,浇口粘在浇口套内,不易脱出。
开模时,制品显现裂纹损伤。
此外,操必需用铜棒从喷嘴处敲出,使之松动后方可脱模,严重影响生产效率。
这种故障重要原因是浇口锥孔干净度差,内孔圆周方向有刀痕。
其次是材料太软,使用一段时间后锥孔小端变形或损伤,以及喷嘴球面弧度太小,致使浇口料在此处产生铆头。
浇口套的锥孔较难加工,应尽量采纳标准件,如需自行加工,也应自制或购买铰刀。
锥孔需经过研磨至Ra0.4以上。
此外,必需设置浇口拉料杆或者浇口顶出机构。
2.导柱损伤。
导柱在模具中重要起导向作用,以保证型芯和型腔的成型面在任何情况下互不相碰,不能以导柱作为受力件或定位件用。
在以下几种情况下,注射时动,定模将产生巨大的侧向偏移力:(1).塑件壁厚要求不均匀时,料流通过厚壁处速率大,在此处产生较大的压力;(2).塑件侧面不对称,如阶梯形分型面的模具相对的两侧面所受的反压力不相等。
3.大型模具,因各向充料速率不同,以及在装模时受模具自重的影响,产生动﹑定模偏移。
在上述几种情况下,注射时侧向偏移力将加在导柱上,开模时导柱表面拉毛,损伤,严重时导柱弯曲或切断,甚至无法开模。
为了解决以上问题在模具分型面上增设高强度的定位键四周各一个,zui简便有效的是采纳圆柱键。
导柱孔与分模面的垂直度至关紧要.在加工时是采纳动,定模对准位置夹紧后,在镗床上一次镗完,这样可保证动,定模孔的同心度,并使垂直度误差zui小。
此外,导柱及导套的热处理硬度务必达到设计要求。
4.动模板弯曲。
模具在注射时,模腔内熔融塑料产生巨大的反压力,一般在600~1000公斤/厘米?。
模具制造者有时不重视此问题,往往更改原设计尺寸,或者把动模板用低强度钢板代替,在用顶杆顶料的模具中,由于两侧座跨距大,造成注射时模板下弯。
注塑成型不良现象及解决方法
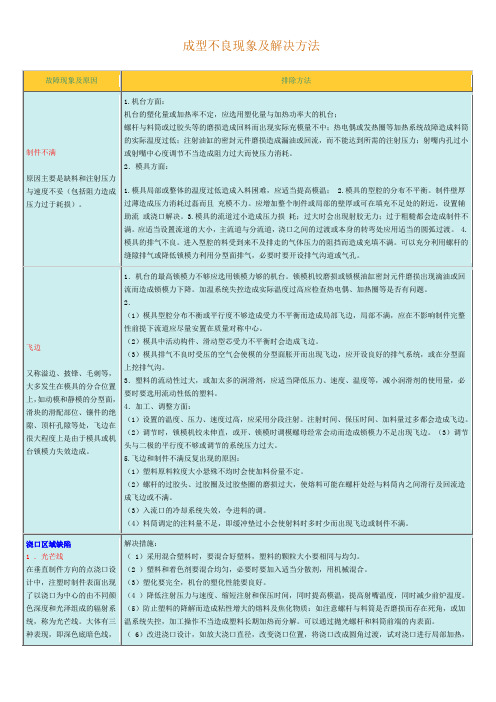
(1)设置的温度、压力、速度过高,应采用分段注射。注射时间、保压时间、加料量过多都会造成飞边。(2)调节时,锁模机铰未伸直,或开、锁模时调模螺母经常会动而造成锁模力不足出现飞边。(3)调节头与二极的平行度不够或调节的系统压力过大。
5.飞边和制件不满反复出现的原因:
(1)塑料原料粒度大小悬殊不均时会使加料份量不定。
(3)对结晶型塑料,尽量使制件各部分的冷却速度一致,对于壁厚差异大的制件,可用着色剂来掩蔽色差,对于壁厚较均匀的制件要固定好料温和模温。
(4)制件的造型和浇口形式,位置对塑料充填情况有影响,使制件的某些局部产生色差,必要时要进行修改。
白霜
有些聚苯乙烯类制件,在脱模时,会在靠近分型面的局部表面发现附着一层薄薄的白霜样物质,大多经抛光后能除去。这些白霜样物质同样会附在型腔表面,这是由于塑料原料中的易挥发物或可溶性低分子量的添加剂受热后形成气态,从塑料熔体释出,进入型腔后被挤迫到靠近有排气作用的分型面附近,沉淀或结晶出来。这些白霜状的粉末和晶粒粘附在模面上,不单会刮伤下一个脱模制件,次数多了还将影响模面的光洁度。不溶性填料和着色剂大多与白霜的出现无关。白霜的解决方法:加强原料的干燥,降低成型温度,加强模具排气,减少再生料的掺加比例等,在出现白霜时,特别要注意经常清洁模面。
2.模具方面:
1.模具局部或整体的温度过低造成入料困难,应适当提高模温;2.模具的型腔的分布不平衡。制件壁厚过薄造成压力消耗过磊而且充模不力。应增加整个制件或局部的壁厚或可在填充不足处的附近,设置辅助流或浇口解决。3.模具的流道过小造成压力损耗;过大时会出现射胶无力;过于粗糙都会造成制件不满。应适当设置流道的大小,主流道与分流道,浇口之间的过渡或本身的转弯处应用适当的圆弧过渡。4.模具的排气不良。进入型腔的料受到来不及排走的气体压力的阻挡而造成充填不满。可以充分利用螺杆的缝隙排气或降低锁模力利用分型面排气,必要时要开设排气沟道或气孔。
注塑成型常见不良现象及处理措施

注塑成型常见不良现象及处理措施注塑成型常见的不良现象有以下几种:
1. 短射:指注塑料进模型中未充满模腔,导致产品缺陷。
处理措施:增加注射
压力、延长注射时间、增加料缸温度、增加模具温度、增加模具出料口直径等。
2. 气泡:指产品表面或内部出现气泡,影响产品质量。
处理措施:增加注射压力、延长注射时间、增加模具温度、增加料缸温度、增加模具出料口直径、增加模具排气孔等。
3. 热熔线:指产品表面出现细小的线状缺陷,通常是由于注射速度过快导致的。
处理措施:减小注射速度、增加模具温度、增加模具出料口直径等。
4. 毛刺:指产品表面出现细小的凸起,通常是由于模具设计不合理或模具磨损
导致的。
处理措施:修复模具、修改模具设计、增加模具温度、增加模具出料口直径等。
5. 缩水:指产品尺寸缩小,通常是由于注射压力不足或冷却时间不足导致的。
处理措施:增加注射压力、延长冷却时间、增加模具温度等。
6. 毛洞:指产品表面或内部出现凹陷,通常是由于注射速度过快或模具设计不
合理导致的。
处理措施:减小注射速度、修改模具设计、增加模具温度等。
处理不良现象的关键是找到问题的根源,然后针对性地采取相应的处理措施。
同时,注塑成型过程中的参数控制和模具维护也是关键的因素,需要进行定期检查和调整。
塑料注塑成型故障排除

塑料注塑成型故障排除注塑成型是一种广泛应用于各种产品制造过程中的一种技术,它可以将塑料材料通过高温高压下注于模具中,并在冷却后保持原来的形状,形成各种各样的塑料制品。
但是在注塑成型过程中也会出现各种故障,特别是塑料注塑成型故障,因为塑料材料特性的不同,会导致不同的故障原因和对应的解决办法。
今天,我们将重点讨论一下塑料注塑成型中可能出现的故障及其排除方法。
1. 塑料材料不充分塑料注塑成型过程中最常见的故障之一是塑料材料不充分。
当注塑机在注入模具时,塑料材料未能充分注入模具的所有角落和隙缝,这可能导致制品表面上出现缺陷,例如气泡、白点和空洞。
解决这个问题的方法包括:增加注塑机的注塑速度、增加熔融态的体积、调整模具温度和检查射嘴。
2. 模具温度不同模具温度不均是注塑成型过程中另一个常见的问题。
如果模具的温度太高或太低,会导致塑料材料的凝固不均,使成品外观和性能下降。
解决这个问题的方法包括:检查模具的温度设定、调整水温控制阀和增加或减少模具循环时间。
3. 熔体进入模具时速度不同熔体进入模具时速度不同也会导致注塑成型的故障。
如果熔体进入模具的速度过快,可能会导致痕迹和缺陷,而如果速度过慢,则会导致模具中的熔融材料减少,从而使成品缺陷严重。
解决这个问题的方法包括检查注塑机的压力、调整注塑机的压力、检查注塑机的速度和调整塑料温度。
4. 模具中的熔体流动模具中的熔体流动也是注塑成型过程中的一个常见问题。
当模具处于运行状态时,如果熔融材料的流动速度不均,可以导致产品表面崩裂,甚至可能损坏模具。
解决这个问题的方法包括检查模具的设计、融材料的温度、注射压力、喷嘴位置和模具温度。
5. 塑料材料气泡塑料材料中出现气泡也是注塑成型中常见的故障。
当塑料材料中存在饱和的空气或其他气体时,会在塑料成型过程中形成气泡,这可能影响制品的美观,同时还会影响其物理性能。
解决这个问题的方法包括颗粒制造商解决、高压注入气体、在模具中放置真空和减少塑料材料中的空气含量。
注塑成型常见不良现象和处理措施方案
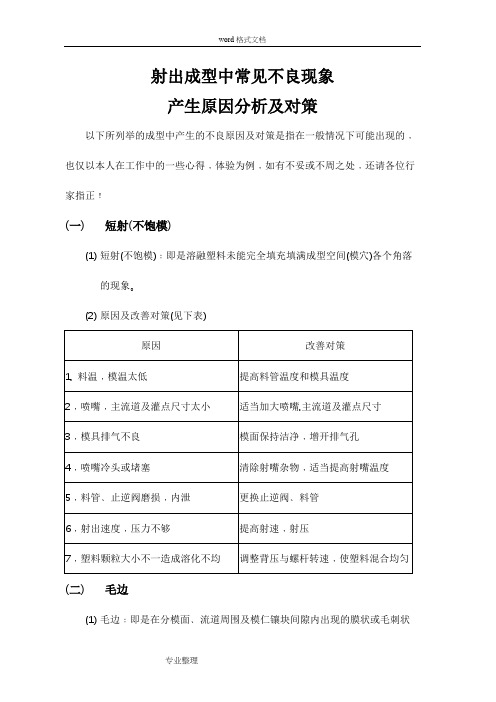
射出成型中常见不良现象产生原因分析及对策以下所列举的成型中产生的不良原因及对策是指在一般情况下可能出现的﹐也仅以本人在工作中的一些心得﹐体验为例﹐如有不妥或不周之处﹐还请各位行家指正﹗(一)短射(不饱模)(1)短射(不饱模)﹕即是溶融塑料未能完全填充填满成型空间(模穴)各个角落的现象。
(2)原因及改善对策(见下表)(二)毛边(1)毛边﹕即是在分模面﹑流道周围及模仁镶块间隙内出现的膜状或毛刺状的多余胶料。
(2)原因及改善对策(见下表)*注﹕成型时间过长﹐模温过低而采用高压﹐高速射出也是产生毛边的常见原因(三)银线(1)银条(银线)即是在成型产品表面或表面附近﹐沿塑料流动方向﹐呈放射状的银白色条纹。
(2)原因及改善对策(见下表)(四)成品光泽度低(1)成品光泽度低是指成品表面光泽达不到质量要求﹐表面无折光度。
(2)原因及改善对策(见下表)(五)变形(1)变形可分为对角线的扭曲及平行边沿的曲翘两种﹐是成品成型中发生的不规则弯曲现象。
(2)原因及发善对策(见下表)(六)顶白(1)顶白(也叫白化)是指成品在脱模之际﹐在顶针或其它脱模部位出现白色痕迹。
(2)原因及改善对策(见下表)(七)结合线(1)结合线是指在成型中﹐二道或多道熔融材料融合时出现的细线状。
(2)原因及改善对策(见下表)(八)冲料痕(1)冲料痕是指熔融材料在进料点附近﹐以浇口为中心而呈现的条纹状。
(2)原因及改善对策(九)异色(黑纹)(1)异色(黑纹)是指在成型过程中﹐在成品表面出现的黑色或其它深色条纹。
(2)原因及改善对策(见下表)(十)气泡(1)气泡是熔融塑料中的水份﹐挥发气体于成型过成中被封入内部而残留的空动现象。
(2)原因及改善对策(见下表)射出换料要诀在射出成型作业中﹑换料﹑换色的问题﹐值得吾入深入探讨﹒如何以最快速的方法完成换料﹑换色﹐除可节省时间外﹐并可降低一笔相当可观的生产成本。
一﹑同一材料之换色1﹒1同一材料的换色时﹐原则上从淡色材料换为深浓色材料﹐较从不透明材料换为透明材料容易。
塑料注塑成型不良现象原因及处理办法

塑料注塑成型不良现象原因及处理办法一、气泡气泡是一种常见的注塑不良现象,造成气泡的原因可以分为产品设计、原料选择和注塑工艺三个方面。
1.产品设计问题:设计中未考虑到壁厚梯度过大、封闭空腔、通孔无曲线等情况,导致气泡无法排除。
处理办法:合理优化产品设计,减小壁厚梯度、增加封闭空腔的通气孔。
2.原料选择问题:原料中含有过多的挥发性成分、水分或杂质,或者原料中添加了过多的促进剂。
处理办法:使用质量可靠的原料,并严格控制原料中的水分和杂质含量。
3.注塑工艺问题:温度、压力、注射速度等工艺参数设置不合理,导致气泡无法排除。
处理办法:合理调整注塑工艺参数,保持合适的温度、压力和注射速度,防止气泡产生。
二、热缩痕热缩痕是注塑过程中产生的一种表面缺陷,常见于产品壁厚不一致、结构复杂的部分。
1.壁厚不一致问题:在产品设计中,壁厚过大或过小的部分易产生热缩痕。
处理办法:调整产品结构,减小壁厚梯度,避免热缩痕的产生。
2.注塑工艺问题:注塑过程中温度、压力不稳定,或者注射速度过快,都会导致热缩痕的产生。
处理办法:优化注塑工艺参数,保持合适的温度、压力和注射速度,避免热缩痕的产生。
三、翘曲变形翘曲变形是注塑成型中常见的一种现象,主要是由于材料流动不均匀或受力不平衡造成的。
1.部件结构问题:产品设计中存在壁厚不均匀、结构不合理等问题,易导致翘曲变形。
处理办法:优化产品结构设计,减小壁厚梯度,增加强度和刚度。
2.注塑工艺问题:注塑过程中温度、压力、注射速度等参数设置不合理,也会导致翘曲变形。
处理办法:调整注塑工艺参数,保持合适的温度、压力和注射速度,控制注塑过程中的变形。
四、色差色差是指注塑成型产品的颜色不均匀或与要求的颜色不符,主要由原料或工艺引起。
1.原料问题:原料中的色母粒质量不好、色母粒加入不均匀等原因,导致产品的色差问题。
处理办法:选用质量可靠的色母粒,并加入均匀进行混合。
2.注塑工艺问题:注塑过程中温度控制不当,熔融状态不稳定,颜色出现偏差。
注塑件常见成型缺陷及解决方案

注塑件常见成型缺陷及解决方案注塑件常见成型缺陷及解决方案前言在注塑成型加式过程中,可能由于原材料处理不好、塑件或模具设计不合理、操作工没有掌握合适的工艺操作条件,或者因机械方面的原因,常常使塑件产品短射、凹痕、飞边、困气、开裂、翘曲变形等成型缺陷。
本文针对塑件在成型过程中出现的各种注塑缺陷,主要是:短射,困气,发脆,烧焦,飞边,分层起皮,喷流痕,流痕,雾斑(浇口晕),银纹(水花纹),凹痕,熔接痕,成型周期过长,翘曲变形,分析了问题产生的可能原因,从原材料、塑件或模具设计、成型工艺等各方面,提出解决方案。
一.短射短射是指模具型腔不能被完全充满的一种现象。
短射形成原因:1、模温、料温或注塑压力和速度过低2、原料塑化不均3、排气不良4、原料流动性不足5、制件太薄或浇口尺寸太小6、聚合物熔体由于结构设计不合理导致过早固化短射解决方案:材料:选用流动性更好的材料模具设计:1、填充薄壁之前先填充厚壁,避免出现滞留现象2、增加浇口数量和流道尺寸,减少流程比及流动阻力3、排气口的位置和尺寸设置适当,避免出现排气不良的现象注塑机:1、检查止逆阀和料筒内壁是否磨损严重2、检查加料口是否有料或是否架桥工艺条件:1、增大注塑压力和注塑速度,增强剪切热2、增大注塑量3、增大料筒温度和模具温度二.困气困气是指空气被困在型腔内而使制件产生气泡。
困气形成原因:它是由于两股熔体前锋交汇时气体无法从分型面、顶杆或排气孔中排出造成的。
困在型腔内气体不能被及时排出,易导致出现表面起泡,制件内部夹气,注塑不满等现象。
困气解决方案:结构设计:减少厚度的不一致,尽量保证壁厚均匀模具设计:1、在最后填充的地方增设排气口2、重新设计浇口和流道系统工艺条件:1、降低最后一级注塑速度.2、增加模温三.发脆塑件发脆是指制件在某些部位出现容易开裂或折断。
发脆原因:1、干燥条件不适合;使用过多回收料2、注塑温度设置不对3、浇口和流道系统设置不恰当4、熔解痕强度不高发脆解决方案:材料:1、注塑前设置适当的干燥条件2、减少使用回收料,增加原生料的比例.3、选用高强度的塑胶.模具设计:增大主流道、分流道和浇口尺寸注塑机:选择设计良好的螺杆,使塑化时温度分配更加均匀工艺条件:1、降低料筒和喷嘴的温度2、降低背压、螺杆转速和注塑速度3、通过增加料温,加大注塑压力,提高熔解痕强度四.烧焦焦痕是指型腔内气体不能及时排走,导致在流动最末断产生烧黑现象。
注塑中产生的问题及解决办法
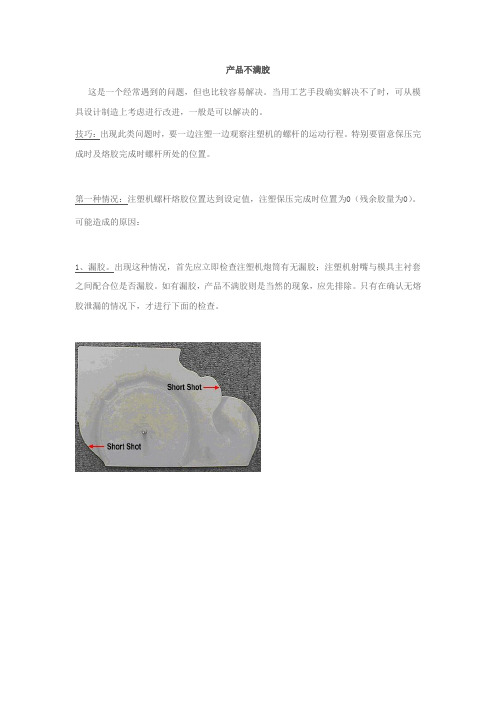
产品不满胶这是一个经常遇到的问题,但也比较容易解决。
当用工艺手段确实解决不了时,可从模具设计制造上考虑进行改进,一般是可以解决的。
技巧:出现此类问题时,要一边注塑一边观察注塑机的螺杆的运动行程。
特别要留意保压完成时及熔胶完成时螺杆所处的位置。
第一种情况:注塑机螺杆熔胶位置达到设定值,注塑保压完成时位置为0(残余胶量为0)。
可能造成的原因:1、漏胶。
出现这种情况,首先应立即检查注塑机炮筒有无漏胶;注塑机射嘴与模具主衬套之间配合位是否漏胶。
如有漏胶,产品不满胶则是当然的现象,应先排除。
只有在确认无熔胶泄漏的情况下,才进行下面的检查。
当产品不满胶,而又无胶体泄漏时,可能是胶量不够。
这时需要增加熔胶行程,增加胶量。
增加熔胶行程后要继续一边注塑一边观察螺杆残余胶量、熔胶行程及产品的进胶情况。
2、胶量不够。
增加熔胶行程后,产品进胶增加,说明胶量不够,需要继续增加熔胶行程。
当熔胶行程达到最大后,产品仍不满胶,则需要更换大型号的注塑机。
3、过胶介子漏胶。
如随着熔胶行程的增加,注塑时产品的进胶量并没有相应的增加,则可能为注塑机的过胶介子漏胶。
检查过胶介子漏胶的方法:保留某一注塑循环的产品于模腔内,改用手动射胶。
注塑压力由小变大,观察螺杆的前进量就可以判断过胶介子的漏胶情况。
手动射胶时,螺杆不前进的,说明过胶介子密封良好,不漏胶。
在较大的注塑压力下,螺杆有少许前进量,是允许的,此时不是熔胶泄漏,而是熔胶受压何种收缩所致。
凡是出现产品不满胶的情况,首先必须检查注塑机炮筒、注塑机射嘴模具间有无漏胶的情况发生;其次是检查注塑机螺杆前端的过胶介子有无漏胶。
只有排除了这两种情况后,才能进行其它方面的判定,下面的判定方法,都是建立在排除了这两种情况后的情况下,不再作累述。
第二种情况:注塑机螺杆能达到设定的熔胶行程,但达不到设定的注塑行程(有残余胶量)。
这种情况即是说:炮筒中有熔胶,但射不进模腔。
可能造成的原因:1、熔胶的流动性不够。
模具注塑常见问题及解决方法

模具注塑常见问题及解决方法模具注塑是一种常见的塑料加工方法,在生产过程中常常会遇到一些问题。
本文将针对模具注塑常见问题进行分析,并提出相应的解决方法,以帮助读者更好地应对这些问题。
一、模具注塑常见问题及解决方法1. 产品缺陷问题在模具注塑过程中,常常会出现产品缺陷问题,如翘曲、热缩、短射等。
这些问题的出现可能是由于模具设计不合理导致的,解决方法是对模具进行优化设计,确保模具的结构合理,避免产品缺陷的出现。
2. 模具磨损问题随着模具的使用,模具表面会出现磨损现象,这可能会导致产品的尺寸不准确或表面粗糙。
为了解决这个问题,可以采用定期维护模具的方法,及时清理模具表面的污垢,使用润滑剂减少磨损,并定期对模具进行研磨或更换磨损部位。
3. 模具温度控制问题在模具注塑过程中,温度的控制对产品质量至关重要。
如果温度控制不当,可能会导致产品尺寸不稳定、表面质量差等问题。
解决这个问题的方法是通过调节注塑机的温度控制系统,确保模具的温度在合适的范围内,并根据具体产品的要求进行调整。
4. 模具开裂问题模具在使用过程中可能会出现开裂的情况,这可能是由于模具材料强度不够或者受到过大的应力导致的。
解决这个问题的方法是选择合适的模具材料,并进行合理的模具结构设计,以增强模具的强度和稳定性。
5. 模具尺寸偏差问题在模具注塑过程中,由于材料的收缩和其他因素的影响,可能会导致产品尺寸与设计要求有偏差。
解决这个问题的方法是通过调整注塑工艺参数,如注塑温度、注塑压力等,来控制产品的尺寸,并根据实际情况进行模具结构的调整。
6. 模具堵塞问题在模具注塑过程中,有时会出现模具堵塞的情况,导致无法正常注塑。
解决这个问题的方法是通过清理模具内部的积聚物,如残留物、杂质等,并确保模具的通道畅通,以保证正常的注塑。
7. 模具寿命问题模具在长时间的使用过程中,可能会出现疲劳、损耗等问题,导致模具寿命减少。
为了延长模具的寿命,可以采取以下措施:定期对模具进行维护和保养,及时更换损坏的模具零件,提高模具的使用寿命。
塑料注塑成型故障排除不良现象的原因及处理办法1充填不足2溢料

塑料注塑成型故障排除不良现象的原因及处理办法1.充填不足2.溢料3.气孔4.波纹5.银条纹6.表面晕喑7.融合线8.气泡9.黑条纹及烧痕 10.龟裂11.离模溢料12.弯曲13.脱模不良14.直浇口的脱模不良15.材料的叠边不良不良现象及其原因处理办法1、充填不足 [1] 成形品的体积过大[2] 流道、浇口过小[3] 喷头温度低[4] 材料的温度或者射出压力低 [5] 内腔里的流体流动距离过长[6] 模具温度低了 [7] 射出速度慢了 [8] 材料的供给量过少[9] 排气不良2、溢料 [1]锁模力不足[2]模具不好[3]模具面的杂质 [4]成形品的投影面积过大 [5]材料的温度过高 [6]材料供给量过剩[7]射出压力高3气孔在材料为充分干燥时,是挥发物或空气所致;大多时候发生在产品胶厚的位置,实际是材料的收缩引起的真空气泡 [1] 流道或浇口过小[2] 成形品的壁厚差大[3] 材料的温度高 [4] 离浇口的流动距离长[5] 脱模过早[6] 射出压力低[7] 冷却时间短 [8] 保压不充分4 波纹[1]材料流动不畅[2]模具温度低 [3]进浇口过小5 银条纹[1]水分或挥发成分[2]材料的温度过高[3]模具温度低[4]排气不良[5]成形品或模具的设计不良[6]模具面上的水分或挥发成分[8]混入夹杂的材料[9]螺桨的运转不当6.表面晕暗[1] 润滑或挥发成分过多[2]脱模材过多7 融合线------实际是2股或多股材料汇合时,材料的融合线。
与材料汇合时,材料的粘度有很大的关系。
从理论上讲,材料的汇合肯定会产生融合线,只是明显程度的不同而已。
[1]材料的温度[2]浇口的设计不当[3]材料里的挥发成分或脱模剂过多[4]材料的凝固快[5]成形品的设计不良8 气泡------在材料为充分干燥时,是挥发物或空气所致;大多时候发生在产品胶厚的位置,实际是材料的收缩引起的真空气泡[1]浇口或流道过小[2]射出压力低[3]过剩的水分[4]成形品的设计不良[5]排气不良9 黑条纹及烧痕------实际是材料受到高温、高压的作用出现分解烧焦的现象。
塑胶产品注塑成型常见问题及改善对策
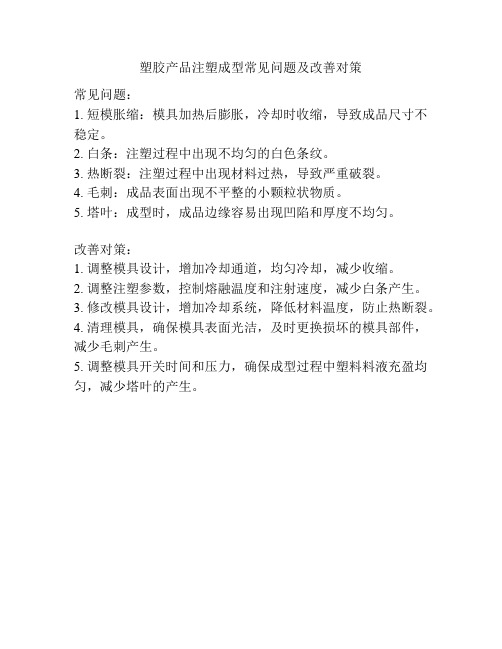
塑胶产品注塑成型常见问题及改善对策
常见问题:
1. 短模胀缩:模具加热后膨胀,冷却时收缩,导致成品尺寸不稳定。
2. 白条:注塑过程中出现不均匀的白色条纹。
3. 热断裂:注塑过程中出现材料过热,导致严重破裂。
4. 毛刺:成品表面出现不平整的小颗粒状物质。
5. 塔叶:成型时,成品边缘容易出现凹陷和厚度不均匀。
改善对策:
1. 调整模具设计,增加冷却通道,均匀冷却,减少收缩。
2. 调整注塑参数,控制熔融温度和注射速度,减少白条产生。
3. 修改模具设计,增加冷却系统,降低材料温度,防止热断裂。
4. 清理模具,确保模具表面光洁,及时更换损坏的模具部件,减少毛刺产生。
5. 调整模具开关时间和压力,确保成型过程中塑料料液充盈均匀,减少塔叶的产生。
塑料注塑缺陷及解决方法
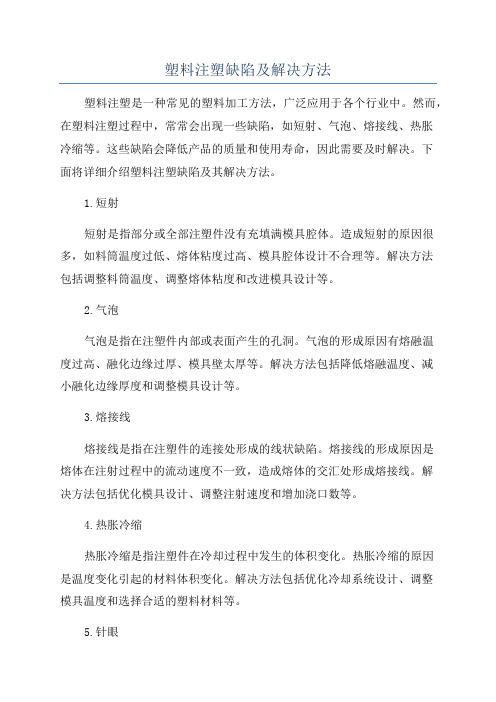
塑料注塑缺陷及解决方法塑料注塑是一种常见的塑料加工方法,广泛应用于各个行业中。
然而,在塑料注塑过程中,常常会出现一些缺陷,如短射、气泡、熔接线、热胀冷缩等。
这些缺陷会降低产品的质量和使用寿命,因此需要及时解决。
下面将详细介绍塑料注塑缺陷及其解决方法。
1.短射短射是指部分或全部注塑件没有充填满模具腔体。
造成短射的原因很多,如料筒温度过低、熔体粘度过高、模具腔体设计不合理等。
解决方法包括调整料筒温度、调整熔体粘度和改进模具设计等。
2.气泡气泡是指在注塑件内部或表面产生的孔洞。
气泡的形成原因有熔融温度过高、融化边缘过厚、模具壁太厚等。
解决方法包括降低熔融温度、减小融化边缘厚度和调整模具设计等。
3.熔接线熔接线是指在注塑件的连接处形成的线状缺陷。
熔接线的形成原因是熔体在注射过程中的流动速度不一致,造成熔体的交汇处形成熔接线。
解决方法包括优化模具设计、调整注射速度和增加浇口数等。
4.热胀冷缩热胀冷缩是指注塑件在冷却过程中发生的体积变化。
热胀冷缩的原因是温度变化引起的材料体积变化。
解决方法包括优化冷却系统设计、调整模具温度和选择合适的塑料材料等。
5.针眼针眼是指注塑件表面出现的小孔。
针眼的形成原因是注射过程中的气体没有完全排出,导致气泡留在产品表面。
解决方法包括增加排气系统、调整注射速度和改善模具设计等。
6.彩色条纹彩色条纹是指注塑件表面出现的条纹状缺陷。
彩色条纹的形成原因是在注塑过程中由于溶解、降解等原因导致颜色不均匀。
解决方法包括优化塑料配方、调整料筒温度和改善模具设计等。
除了以上常见的缺陷,塑料注塑过程中还可能出现其他问题,如烧焦、流痕、毛刺等。
解决这些问题的方法往往需要结合具体情况进行调整和改进。
在塑料注塑过程中,缺陷的产生是由于多个因素的综合作用。
因此解决问题也需要综合考虑各个方面的因素。
通过调整塑料配方、优化注塑参数、改进模具设计等方法,可以有效降低缺陷的产生,提高产品的质量。
同时,加强质量控制,进行合格率的检测和管理也非常重要。
注塑成型出现的问题及解决方法

注塑成型出现的问题及解决方法注塑过程中,有缺陷的塑料制品通常由下面一个或几个原因造成。
(1)模塑前:原材料的处理和贮存;(2)模塑阶段:成型周期内的成型条件;(3)模塑之后:制品的处理和修饰.在制品模塑前后出现的问题可能与污染、颜色、静态粉尘收集器等相关的问题有关;在模塑阶段,操作人员应能生产出质量好的熔体,在自测的基础上保证熔体从喷嘴自由流出。
每—套模具和每种原料都不同,因此无法概括好的熔体如何得到,操作人员的经验和加工需要成为最终点决定因素。
注塑制品的质量出现问题,应从模具设计和制造精度、成型条件、成型材料、成型前后的环境四个方面来考虑。
下面给出常见的问题及改进办法。
1 注塑制品表面缺陷(1-1)充填不足原因在于:供料不足;压力不够;加热不当;注塑时间不够;模具温度过低;夹入空气造成反压;多模腔中,各模腔的流道不平衡。
①制品整体有塌瘪倾向的充填不足。
成型材料的改进:选用流动性好的材料。
成型条件的改进:提高注射温度、压力、速度;提高保压压力、加大从注射到保压的变换时间;提高模具温度;调整喷嘴逆流阀。
模具结构的改进;改变浇口的位置;浇口变短、加大;流道变短、加宽:加大冷料穴;喷嘴和模具口配合完好。
制品设计的改进:调整树脂流动长度与厚度的比值:②一模多腔时某些型腔不能充填成型条件的改进:减小浇口充满前的注射速度;提高通过浇口后的注射速度。
制品设计的改进:尽量使各分流道的长度一致;加大充填不足型腔的浇口:③制品形状完整但某特定部分充填不足成型材料的改进;选用不易分解的材料;成型条件的改进:降低最后一级注射速度模具结构的改进:改变浇口的位置、增加排气槽:制品设计的改进:在顶杆上开斜口等。
(1-2)制品缩瘪(凹坑、凹痕) 原因在于浇口固结时料温过高:保压时间不够;进入模具型腔的物料不够。
成型材料的改进:选用收缩率小的材料。
成型条件的改进:提高注射压力;增大后期保压压力;降低缩瘪部分对应的注射速度;降低模具温度;降低注射温度。
塑料注塑加工成型过程中的故障及其排除

注塑成型故障排除
喷射痕
诊断: • 注射速度太快 • 浇口太小 • 错误浇口位置(直接到壁或柱) • 浇口太长 • 模具过冷 • 料温过低 • 喷嘴有滴垂 • 水或油漏入模穴
注塑成型故障排除
粘流道
诊断
•注射压力过高 •喷嘴凝固 •喷嘴直径大于主流道衬套口直径 •不足够的斜度 •喷嘴漏料
• 差的主流道拉料杆
• 喷嘴与主流道衬套口未对准
• 主流道抛光度不足
• 不合适的主流道锥度(正常: 1:20, 困难: 1:15)
注塑成型故障排除
黑点
• 诊断
• 停机时间过长 • 机器长时间不用 • 未清干净料筒 • 不合适的喷嘴 • 脏的塑化单元 • 在浇口和流道上有死角 • 塑胶粒中杂质 • 其它树脂降解 • 来自料筒壁面降解材料
注塑成型故障排除
毛边
诊断: •锁模力过低和机构故障 •过高的注射压力 •注射速度太快 •分型面破损 •不匹配 •料温过高
注塑成型故障排除
烧焦
诊断: • 机器止回阀问题 • 注射速度过快 • 背压过大 • 模具排气不良 • 检查浇口 • 料太冷或过热
注塑成型故障排除
浇口斑白/流点
诊断:
材料温度差异的结果.
料温必须高以确保充分融合. •增加注射速度 •升高注塑压力 •延长保压时间 •升高模具温度 •升高熔料温度 •使熔接线位置的型腔排气 •使熔接线位置旁边加设溢料井
每一个成功者都有一个开始。勇于开始,才能找到成
•
1、
功的路 。20.11.1020.11.10Tuesday, November 10, 2020
注塑问题及解决方案(3篇)

第1篇一、引言注塑成型是一种常见的塑料加工方式,广泛应用于汽车、电子、家电、医疗器械等领域。
注塑成型具有生产效率高、精度高、成本低的优点,但在实际生产过程中,常常会遇到各种问题。
本文将针对注塑过程中常见的问题及解决方案进行探讨。
二、注塑问题及解决方案1. 塑料熔体流动不平衡(1)问题表现:塑料熔体在模具内部流动不平衡,导致注塑制品表面出现凹痕、气泡、纹路等缺陷。
(2)原因分析:模具设计不合理、注塑机参数设置不当、原料质量不合格等。
(3)解决方案:①优化模具设计:合理设计模具流道,使熔体在模具内部流动均匀。
②调整注塑机参数:合理设置注塑速度、压力、温度等参数,确保熔体在模具内部流动均匀。
③提高原料质量:选用质量合格的原料,避免原料中存在杂质、水分等影响熔体流动。
2. 注塑制品表面缺陷(1)问题表现:注塑制品表面出现麻点、划痕、斑痕等缺陷。
(2)原因分析:模具表面粗糙、原料表面污染、冷却不足等。
(3)解决方案:①提高模具表面光洁度:对模具表面进行抛光、电镀等处理,提高模具表面光洁度。
②清理原料:选用质量合格的原料,并确保原料表面清洁。
③加强冷却系统:优化冷却水道设计,提高冷却效率,确保制品表面冷却均匀。
3. 注塑制品尺寸不稳定(1)问题表现:注塑制品尺寸偏差较大,影响产品性能。
(2)原因分析:注塑机精度不足、模具精度不足、原料收缩率不一致等。
(3)解决方案:①提高注塑机精度:选用高精度注塑机,确保注塑过程稳定。
②提高模具精度:选用高精度模具,减少制品尺寸偏差。
③选用收缩率一致的原料:选用收缩率一致的原料,降低制品尺寸偏差。
4. 注塑制品变形(1)问题表现:注塑制品在冷却过程中出现变形,影响产品性能。
(2)原因分析:冷却不均匀、模具设计不合理、原料性能不佳等。
(3)解决方案:①优化冷却系统:合理设计冷却水道,确保制品冷却均匀。
②优化模具设计:设计合理的冷却系统,提高制品冷却均匀性。
③选用性能稳定的原料:选用性能稳定的原料,降低制品变形风险。
- 1、下载文档前请自行甄别文档内容的完整性,平台不提供额外的编辑、内容补充、找答案等附加服务。
- 2、"仅部分预览"的文档,不可在线预览部分如存在完整性等问题,可反馈申请退款(可完整预览的文档不适用该条件!)。
- 3、如文档侵犯您的权益,请联系客服反馈,我们会尽快为您处理(人工客服工作时间:9:00-18:30)。
注塑成型故障排除
气泡
诊断
• 注射压力太低 • 止回阀功能不足够 • 塑化太快 • 射退太长 • 不正确进料 • 在料斗进料中夹带空气 • 模具排气不良 • 模温过低 • 流动从薄到厚 • 熔料过热
注塑成型故障排除
变色
诊断
•料筒污染 •检查主流道直径 •排气不良 •针点式浇口太小
• 料温太高或太低 • 料停留时间过长 • 材料基材/色粉不稳定
•注射速度太低或过快 •注射压力太低 •保压过长 •不足够模具冷却 •浇口区模具过热 •模具过冷 •浇口位置不当 •浇口过长 •料温过低 •不合适的热流道
注塑成型故障排除
喷射痕
诊断: • 注射速度太快 • 浇口太小 • 错误浇口位置(直接到壁或柱) • 浇口太长 • 模具过冷 • 料温过低 • 喷嘴有滴垂 • 水或油漏入模穴
料温必须高以确保充分融合. •增加注射速度 •升高注塑压力 •延长保压时间 •升高模具温度 •升高熔料温度 •使熔接线位置的型腔排气 •使熔接线位置旁边加设溢料井
•
树 立 质 量 法 制观念 、提高 全员质 量意识 。20.10.2020.10.20Tuesday, October 20, 2020
注塑成型故障排除
渗液
诊断: 添加剂在产品表面渗出
注塑成型故障排除
产品过饱
诊断: 过多材料压入模腔, 造成产品较重和模塑内应力.
注塑成型故障排除
顶出痕
诊断:
•不合适的脱模斜度 •不合适的产品表面 •保压过大 •顶针过少或太小 •顶针粘住制品
注塑成型故障排除
缺胶
诊断:
•不正确的进料 •注射压力和速度过低 •注射时间太短 •有问题的止回阀 •不良的排气 •模温过低 •料温过低或料熔体粘度太高
•
人 生 得 意 须 尽欢, 莫使金 樽空对 月。17:29:5517:29:5517:2910/20/2020 5:29:55 PM
•
安 全 象 只 弓 ,不拉 它就松 ,要想 保安全 ,常把 弓弦绷 。20.10.2017:29:5517:29Oct-2020-Oct-20
•
加 强 交 通 建 设管理 ,确保 工程建 设质量 。17:29:5517:29:5517:29Tuesday, October 20, 2020
好 的 事 情 马 上就会 到来, 一切都 是最好 的安排 。下午 5时29分 55秒下 午5时 29分17:29:5520.10.20
•
一 马 当 先 , 全员举 绩,梅 开二度 ,业绩 保底。 20.10.2020.10.2017:2917:29:5517:29:55Oct-20
•
牢 记 安 全 之 责,善 谋安全 之策, 力务安 全之实 。2020年 10月 20日星 期二5时 29分55秒 Tuesday, October 20, 2020
注塑成型故障排除
沉陷
诊断:
无足够的材料或较厚肋
•注射压力过低 •射胶时间太短 •塑化能力不足 •模温太高 •浇口过小 •流道过长 •错误的肋/壁厚比 •料温过高 •错误浇口位置 •错误的排气位置
注塑成型故障排除
条纹(银纹, 飞溅点, 丝状点)
起因: 塑胶粒中的水分, 残留非水性的挥发物---遍布产品表面 降解---产品部分表面有一团或粗糙线
注塑成型故障排除
射纹
烧焦射纹
•在料筒停留时间 过长
水纹
•塑胶粒中过多的 水分
空气纹(近流道 处)
•在减压过程中吸 入空气
玻纤纹 •可以清晰看到熔 接线
诊断:
•止回环破裂
•料筒有死角
•料筒有热点
•材料被污染: 稳定 ---机器; 无规律--材料着色/材料不 稳定
注塑成型故障排除
熔结线
诊断: 来源于两股熔料流前部的交汇而产生
•
相 信 相 信 得 力量。 20.10.202020年 10月 20日 星期 二5时 29分55秒 20.10.20
谢谢大家!
注塑成型故障排除
毛边
诊断: •锁模力过低和机构故障 •过高的注射压力 •注射速度太快 •分型面破损 •不匹配 •料温过高
注塑成型故障排除
烧焦
诊断: • 机器止回阀问题 • 注射速度过快 • 背压过大 • 模具排气不良 • 检查浇口 • 料太冷或过热
注塑成型故障排除
浇口斑白/流点
诊断:
材料温度差异的结果.
云状物
诊断: 水分/污染/冷料
注塑成型故障排除
剥离/分层
诊断: • 注射速度过高 •模温过冷 •浇口区有锐角 •料温过高 •塑化不充分 •不相容的色粉 •交叉污染 •过多的回收料
注塑成型故障排除
指印
诊断: 1. 注射压力过低, 2. 注射速度过低, 3. 模温 过低, 4. 模具皮纹, 5. 料温过低
注塑成型故障排除
条纹(银纹, 飞溅点, 丝状点)
诊断: •材料降解(料筒有热点, 材料在喷嘴处有死角) •注射压力或速度过低或过高 •背压过低 •被困的挥发性物质 •过多水分 •材料干燥过度 •在机嘴, 浇口或热流道处摩擦燃烧
注塑成型故障排除
塑件表面烧焦
原因: •过高的储料温度 •高背压造成过多剪切热 •排气是否足够 •使用高注射速度克服流动限制时,
注塑成型故障排除
脱模问题
粘前模/粘后模/粘浇道
粘前模
诊断: •注射压力过高 •注射速度过高 •保压时间过长 •注的过满
• 型腔太热 • 模具太冷 • 模具表面过于粗糙 • 熔料温度过高 • 模具设计问题
注塑成型故障排除
粘后模
诊断
•注射压力过高 •型芯弯曲 •型芯温度过低
• 产生真空---尤其薄壁塑件 • 型芯和型腔温差过大 • 模具设计问题
•
严 格 把 控 质 量关, 让生产 更加有 保障。 2020年 10月下 午5时29分 20.10.2017:29October 20, 2020
•
作 业 标 准 记 得牢, 驾轻就 熟除烦 恼。2020年 10月 20日 星期二 5时29分 55秒17:29:5520 October 2020
•
也会摩擦烧焦.
注塑成型故障排除
塑件表面烧焦
• 减少储料温度 • 减少注射速度 • 检查模具排气 • 加大浇口
措施
• 检查锁模力 • 清洗料筒 • 检查主流道
注塑成型故障排除
空穴
诊断: •注射速度过快 •注塑压力过低 •保压不够 •料温过高 •模具温度过低 •浇口过小, 浇口分型面过长 •不合适的流道系统和/或喷嘴尺寸 •制件壁厚 •错误的材料等级 •不正确的料流
•计划 •一次只做一各独立变数 •耐心, 仔细观察, 每次都行之有效 •保持机器稳定运行 •做好每一变化记录
注塑成型故障排除
注塑成型故障诊断 •提问
改变过什么? 什么问题? 何时出现? 比率多少? 问题位置? 随机/同一位置? 等 •诊断
计划, 试验, 观察, 结论和记录改正措施
注塑成型故障排除
e
GE Plastics
塑料注塑加工成型过程中 的故障和排除
注塑成型故障排除
空洞
翘曲
粘模
条纹
波流痕
光泽
溢料
喷射痕 烧焦
毛边
缩水
缺胶
熔结痕
注塑成型故障排除
当出现问题时, 第一反应是什么?
比如 ... 一定料有问题 !
注塑成型故障排除
基本程序: 在处理注塑成型问题过程中, 需遵守一些行之 有效的准则 在 麻痹。 20.10.2020.10.2017:29:5517:29:55October 20, 2020
•
踏 实 肯 干 , 努力奋 斗。2020年 10月 20日 下午5时 29分20.10.2020.10.20
•
追 求 至 善 凭 技术开 拓市场 ,凭管 理增创 效益, 凭服务 树立形 象。2020年 10月 20日 星期二 下午5时 29分55秒 17:29:5520.10.20
注塑成型故障排除
粘流道
诊断
•注射压力过高 •喷嘴凝固 •喷嘴直径大于主流道衬套口直径 •不足够的斜度 •喷嘴漏料
• 差的主流道拉料杆
• 喷嘴与主流道衬套口未对准
• 主流道抛光度不足
• 不合适的主流道锥度(正常: 1:20, 困难: 1:15)
注塑成型故障排除
黑点
• 诊断
• 停机时间过长 • 机器长时间不用 • 未清干净料筒 • 不合适的喷嘴 • 脏的塑化单元 • 在浇口和流道上有死角 • 塑胶粒中杂质 • 其它树脂降解 • 来自料筒壁面降解材料