生料质量对煅烧的影响
高镁石原料对煅烧质量带来的影响与对策措施
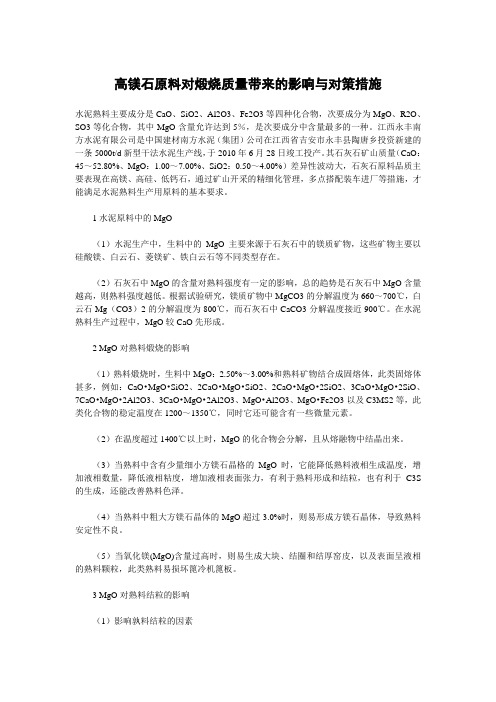
高镁石原料对煅烧质量带来的影响与对策措施水泥熟料主要成分是CaO、SiO2、Al2O3、Fe2O3等四种化合物,次要成分为MgO、R2O、SO3等化合物,其中MgO含量允许达到5%,是次要成分中含量最多的一种。
江西永丰南方水泥有限公司是中国建材南方水泥(集团)公司在江西省吉安市永丰县陶唐乡投资新建的一条5000t/d新型干法水泥生产线,于2010年6月28日竣工投产。
其石灰石矿山质量(CaO:45~52.80%、MgO:1.00~7.00%、SiO2:0.50~4.00%)差异性波动大,石灰石原料品质主要表现在高镁、高硅、低钙石,通过矿山开采的精细化管理,多点搭配装车进厂等措施,才能满足水泥熟料生产用原料的基本要求。
1水泥原料中的MgO(1)水泥生产中,生料中的MgO主要来源于石灰石中的镁质矿物,这些矿物主要以硅酸镁、白云石、菱镁矿、铁白云石等不同类型存在。
(2)石灰石中MgO的含量对熟料强度有一定的影响,总的趋势是石灰石中MgO含量越高,则熟料强度越低。
根据试验研究,镁质矿物中MgCO3的分解温度为660~700℃,白云石Mg(CO3)2的分解温度为800℃,而石灰石中CaCO3分解温度接近900℃。
在水泥熟料生产过程中,MgO较CaO先形成。
2 MgO对熟料煅烧的影响(1)熟料煅烧时,生料中MgO:2.50%~3.00%和熟料矿物结合成固熔体,此类固熔体甚多,例如:CaO•MgO•SiO2、2CaO•MgO•SiO2、2CaO•MgO•2SiO2、3CaO•MgO•2SiO、7CaO•MgO•2Al2O3、3CaO•MgO•2Al2O3、MgO•Al2O3、MgO•Fe2O3以及C3MS2等,此类化合物的稳定温度在1200~1350℃,同时它还可能含有一些微量元素。
(2)在温度超过1400℃以上时,MgO的化合物会分解,且从熔融物中结晶出来。
(3)当熟料中含有少量细小方镁石晶格的MgO时,它能降低熟料液相生成温度,增加液相数量,降低液相粘度,增加液相表面张力,有利于熟料形成和结粒,也有利于C3S 的生成,还能改善熟料色泽。
原燃材料质量波动对熟料煅烧的影响

27 . 27 .5
27 .4
9 .8 95
9 . ’ l 97 37 6
6 中 国 水 泥 2 1 .0 0 11
项 目 铜 矿 渣 含铁 量 / % 熟 料 2 d强 度 /MP ) 8 ( a
Fl — 4. 02 53 8
F2 一 3- 94 5. 79
高 ,当然较用最理 想 的煤 粉仍然有 些差距 。分 析原 因 是 。 生料率值均 没有变化 的情况 下 , 在 煤的发热量 越低
的差异 和液 相性 的不 同 , 熟料 煅 烧温 度 和形成 晶体 反
应时 间 的不 同 .原燃 材料 质量 的波 动及 品位 的高 低 ,
耗煤就会 增加 , 熟料整个 预热 、 在 分解 、 烧过程 中 , 煅 因
A 灰 石 石
B 灰 石 石
4. 3 5
4. 1 9
0 0 3 0 1 5 . 36 _ . 4 34
12 1 6 05 5 . 3 . 4 0 26
1 . 6
1 . 8
9 . 08 6 28 1 2 O9 9 .9 . 2 4 . .8 4
(h t) /
l 11 2.
头 煤 l 尾 煤
69 . 99 .
合 计
l. 68
a O合 格 率/ %
9. 09
强 度/MP ) a 3 d 2d 8
3. 08 5. 88
B 煤
24 . 4
2. 05 5
2 72 4
4. 92 6
‘
∑ fO K S C H a M
9 .4 73 14 . 7 0 O8 .5 O8 1 .9 08 9 8
.
I M
工艺故障处理

④旋风筒漏风造成生料内循环,筒内生料浓度增加到一定程度,当系统操作参数变化时,积料下落;
⑤翻板阀调整不合理,积料过多一次冲下造成塌料。
措施
①严格控制出磨生料水分<0.5%,稳定喂料量;②改造旋风筒结构尺寸,合理调整翻板阀配重;③开窑加料操作尽快跳过低产塌料危险区;④提高系统风量;⑤对于较低程度的塌料,一般不作特别处理;塌料严重,则按窑跑生料处理。
④烟室负压降低、三次风和分解炉出口负压增大且波动大,表示缩口结皮;三次风、炉出口和烟室负压同时增大,表示烟室底部结皮。
原因
①系统有害组分(碱、氯、硫)的循环、富集是形成结皮的重要条件;
②“二次燃烧”形成局部高温和还原气氛是形成结皮的关键因素;
③煤质差、灰分高是引起结皮的重要因素;
④投料初期达到定额喂料量间隔时间太长;窑炉燃料比例不合适使系统局部温度超高而堵塞;
窑内结球
现象
①窑尾温度降低,负压增高且波动大;②三次风、分解炉出口负压增大;③窑功率高,且波动幅度大;④C5和分解炉出口温度低;⑤在筒体外面可听到有振动声响;⑥窑内通风不良.窑头火焰粗短,窑头时有正压。
原因
①配料不当,SM低、IM低,液相量大,液相粘度低;②入窑生料化学成分波动大,导致用煤量不易稳定,热工制度不稳定;③喂料量不稳定;④煤粉燃烧不完全,跑到窑后烧,煤灰不均匀掺入物料;⑤火焰过长,火头后移,窑后局部高温;⑥分解炉温度过高,使入窑物料提前出现液相;⑦煤灰分高,细度粗。⑧原料中有害成分含量高。
原因
①硫酸盐饱和度过高,高温的液相熟料液相表面张力太小。
措施
①控制硫酸盐饱和度在40~70%;②避免使用高碱、高镁和高硫的原燃料;③适当降低窑尾温度,提高窑速,缩短物料在过渡带停留时间。
生料成分对熟料煅烧的影响
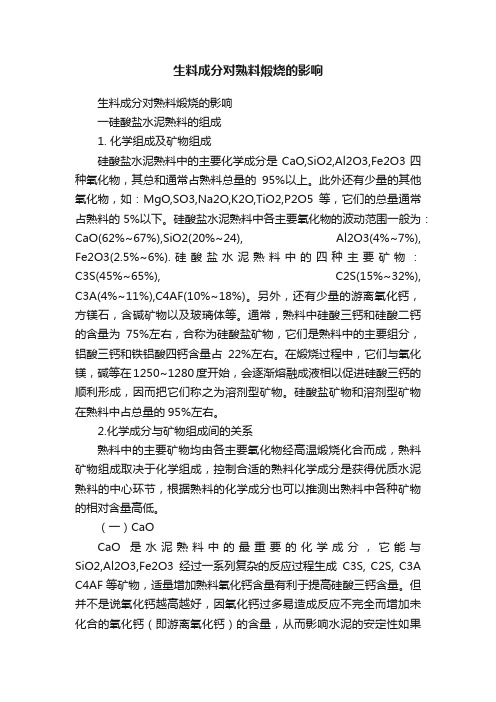
生料成分对熟料煅烧的影响生料成分对熟料煅烧的影响一硅酸盐水泥熟料的组成1. 化学组成及矿物组成硅酸盐水泥熟料中的主要化学成分是CaO,SiO2,Al2O3,Fe2O3四种氧化物,其总和通常占熟料总量的95%以上。
此外还有少量的其他氧化物,如:MgO,SO3,Na2O,K2O,TiO2,P2O5等,它们的总量通常占熟料的5%以下。
硅酸盐水泥熟料中各主要氧化物的波动范围一般为:CaO(62%~67%),SiO2(20%~24), Al2O3(4%~7%), Fe2O3(2.5%~6%).硅酸盐水泥熟料中的四种主要矿物:C3S(45%~65%), C2S(15%~32%), C3A(4%~11%),C4AF(10%~18%)。
另外,还有少量的游离氧化钙,方镁石,含碱矿物以及玻璃体等。
通常,熟料中硅酸三钙和硅酸二钙的含量为75%左右,合称为硅酸盐矿物,它们是熟料中的主要组分,铝酸三钙和铁铝酸四钙含量占22%左右。
在煅烧过程中,它们与氧化镁,碱等在1250~1280度开始,会逐渐熔融成液相以促进硅酸三钙的顺利形成,因而把它们称之为溶剂型矿物。
硅酸盐矿物和溶剂型矿物在熟料中占总量的95%左右。
2.化学成分与矿物组成间的关系熟料中的主要矿物均由各主要氧化物经高温煅烧化合而成,熟料矿物组成取决于化学组成,控制合适的熟料化学成分是获得优质水泥熟料的中心环节,根据熟料的化学成分也可以推测出熟料中各种矿物的相对含量高低。
(一)CaOCaO是水泥熟料中的最重要的化学成分,它能与SiO2,Al2O3,Fe2O3经过一系列复杂的反应过程生成C3S, C2S, C3A C4AF等矿物,适量增加熟料氧化钙含量有利于提高硅酸三钙含量。
但并不是说氧化钙越高越好,因氧化钙过多易造成反应不完全而增加未化合的氧化钙(即游离氧化钙)的含量,从而影响水泥的安定性如果熟料中氧化钙过低,则生成硅酸三钙太少,硅酸二钙却相应增加。
会降低水泥的胶凝性。
水泥烧成系统的调试方法
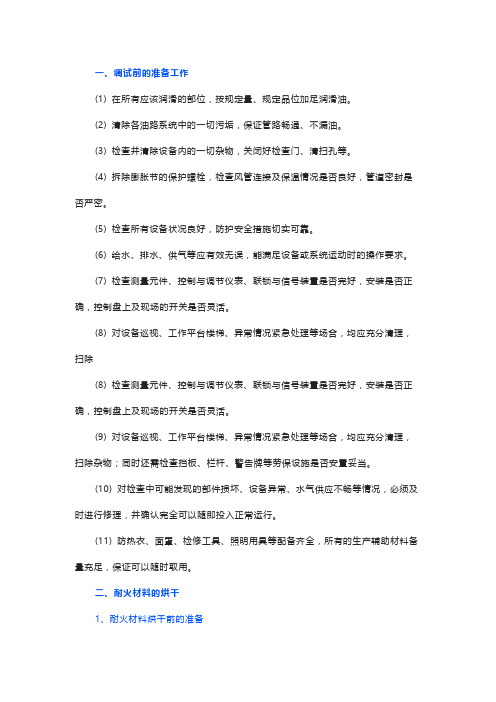
一、调试前的准备工作(1) 在所有应该润滑的部位,按规定量、规定品位加足润滑油。
(2) 清除各油路系统中的一切污垢,保证管路畅通、不漏油。
(3) 检查并清除设备内的一切杂物,关闭好检查门、清扫孔等。
(4) 拆除膨胀节的保护螺栓,检查风管连接及保温情况是否良好,管道密封是否严密。
(5) 检查所有设备状况良好,防护安全措施切实可靠。
(6) 给水、排水、供气等应有效无误,能满足设备或系统运动时的操作要求。
(7) 检查测量元件、控制与调节仪表、联锁与信号装置是否完好,安装是否正确,控制盘上及现场的开关是否灵活。
(8) 对设备巡视、工作平台楼梯、异常情况紧急处理等场合,均应充分清理,扫除(8) 检查测量元件、控制与调节仪表、联锁与信号装置是否完好,安装是否正确,控制盘上及现场的开关是否灵活。
(9) 对设备巡视、工作平台楼梯、异常情况紧急处理等场合,均应充分清理,扫除杂物;同时还需检查挡板、栏杆、警告牌等劳保设施是否安置妥当。
(10) 对检查中可能发现的部件损坏、设备异常、水气供应不畅等情况,必须及时进行修理,并确认完全可以随即投入正常运行。
(11) 防热衣、面罩、检修工具、照明用具等配备齐全,所有的生产辅助材料备量充足,保证可以随时取用。
二、耐火材料的烘干1、耐火材料烘干前的准备(1) 全面检查、排除旋风筒、分解炉、回转窑内的一切杂物,管道畅通无堵。
(2) 打开系统中的烘干排气孔,关闭旋风预热器和分解炉所有的人孔门、清扫孔等。
(3) 打开各级旋风筒的下料翻板阀,并用铅丝固定处于常开状态。
(4) 关闭冷却机至煤磨管道上的热风阀,使烧成系统不受外界因素干扰。
(5) 点火燃油系统准备就绪,柴油备量充足。
(6) 煤粉仓应备有适量煤粉。
(7) 根据衬料材质、砌筑厚度、含水量、砌筑方法等实际情况,制定出切实可行的升温烘干方案。
2、第一次烘窑的升温曲线3、烘窑操作基本方法(1) 通过调节窑尾收尘器排风机进口风门开度来控制窑尾负压约-50 ~-100Pa 。
水泥窑煅烧异常情况分析及操作
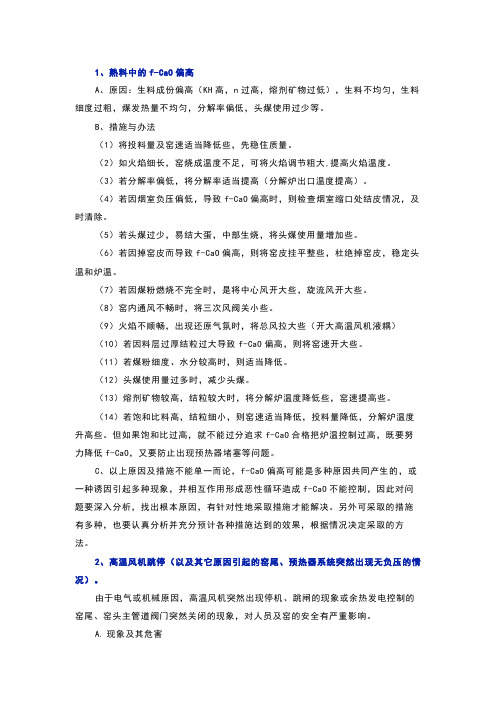
1、熟料中的f-CaO偏高A、原因:生料成份偏高(KH高,n过高,熔剂矿物过低),生料不均匀,生料细度过粗,煤发热量不均匀,分解率偏低,头煤使用过少等。
B、措施与办法(1)将投料量及窑速适当降低些,先稳住质量。
(2)如火焰细长,窑烧成温度不足,可将火焰调节粗大,提高火焰温度。
(3)若分解率偏低,将分解率适当提高(分解炉出口温度提高)。
(4)若因烟室负压偏低,导致f-CaO偏高时,则检查烟室缩口处结皮情况,及时清除。
(5)若头煤过少,易结大蛋,中部生烧,将头煤使用量增加些。
(6)若因掉窑皮而导致f-CaO偏高,则将窑皮挂平整些,杜绝掉窑皮,稳定头温和炉温。
(7)若因煤粉燃烧不完全时,是将中心风开大些,旋流风开大些。
(8)窑内通风不畅时,将三次风阀关小些。
(9)火焰不顺畅,出现还原气氛时,将总风拉大些(开大高温风机液耦)(10)若因料层过厚结粒过大导致f-CaO偏高,则将窑速开大些。
(11)若煤粉细度、水分较高时,则适当降低。
(12)头煤使用量过多时,减少头煤。
(13)熔剂矿物较高,结粒较大时,将分解炉温度降低些,窑速提高些。
(14)若饱和比料高,结粒细小,则窑速适当降低,投料量降低,分解炉温度升高些。
但如果饱和比过高,就不能过分追求f-CaO合格把炉温控制过高,既要努力降低f-CaO,又要防止出现预热器堵塞等问题。
C、以上原因及措施不能单一而论,f-CaO偏高可能是多种原因共同产生的,或一种诱因引起多种现象,并相互作用形成恶性循环造成f-CaO不能控制,因此对问题要深入分析,找出根本原因,有针对性地采取措施才能解决。
另外可采取的措施有多种,也要认真分析并充分预计各种措施达到的效果,根据情况决定采取的方法。
2、高温风机跳停(以及其它原因引起的窑尾、预热器系统突然出现无负压的情况)。
由于电气或机械原因,高温风机突然出现停机、跳闸的现象或余热发电控制的窑尾、窑头主管道阀门突然关闭的现象,对人员及窑的安全有严重影响。
生料的质量控制概要

生料的质量控制金顶集团流云摘要:在实际生产过程中,由于原燃料材料成分的变化、各种物料配比的波动、工艺设备的不完善及分析样品缺乏代表性等因素,生料的化学成分波动较大。
因此,要及时分析、研究、调整,恢复到目标值范围内。
本文简述生料质量的主要控制项目,分析引起生料成分波动的主要原因,提出调整的方法。
关键词:生料质量;成分波动;控制生产质量控制是生产质量管理不可缺少的一个重要环节.它的作用是根据设计和工艺技术文件的规定,控制生产过程各工序可能出现的异常和波动,使生产处于可控状态.生产过程的质量控制目的是产品性能质量控制,使产品达到所需性能的满足程度,保证生产出符合设计和规范质量要求的产品.合理而稳定的生料是保证熟料质量和维持正常煅烧操作的前提。
全合格的生料应当包括三个方面的内容:合理而稳定的化学成分;合理的细度;合理的配煤。
为了获得合格的生料,必须在对各种原燃材料严格控制的情况下加强对生料生产过程的控制,确保配料方案的实现。
笔者认为,生料的质量控制一般分三个方面:生料制备过程中的质量控制、出磨生料质量控制;入窑生料质量控制。
1生料质量的主要控制项目1。
1出磨生料质量控制主要项目(1)碳酸钙滴定值(或氧化钙)控制生料中碳酸钙(或氧化钙)的主要目的是为了控制生料的石灰饱和系数。
通过对其含量的测定,基本上可以判断出生料中石灰石与其他原料的比例。
目前常用的方法有二种:测定生料中的碳酸钙滴定值;测定生料中的氧化钙含量。
出磨生料中碳酸钙合格率要求在60%以上.但实际生产中往往波动较大,有时达不到60%,在这情况下,应该分析原因,立即采取有效措施。
在日常工作中,搞好原材料的预均化,控制入磨物料的水分,经常抽查入磨物料的下料量等,都是减小生料成分的波动,提高出磨生料合格率的具体措施。
(2)氧化铁生产过程中对氧化铁的控制,是为了及时调整铁质原料的加入量,稳定生料成分,达到控制熟料铝率的目的。
在配料方案确定后,就应力求做到使生料铝率相对稳定,这样才能稳定窑的热工制度,有利于熟料质量的提高。
熟料质量控制及煅烧方面的影响因素

培训材料熟之三料质量控制及煅烧方面的影响因素一、熟料质量控制的重要性1、熟料质量是确保水泥质量的核心,熟料质量达不到要求,难以磨制优质的水泥产品。
其中配料和煅烧是决定熟料质量的关键。
2、从生料到熟料,是一个化学反应过程。
化学反应,最基本的核心就是要求参预化学反应的物质间的比例要满足理论要求。
参预化学反应的某一物质的量,不得过剩或者不足,否则,化学反应形成的结果,不是当初设计的结果。
因此,熟料生产过程实际上要求是很精细的,不是表面上的那种粗糙现象。
3、设计合理的熟料率值,通过良好的煅烧,才干生产出优质的水泥熟料。
1、原料磨工艺变化现代水泥企业,以节能高效为主要导向,装备和工艺流程日益简化和高效。
2、原料磨由过去的球磨机改为现代立磨,原料磨工艺装备的改变,对产品质量的影响。
3、球磨机的工艺特点,决定了生料细度更加均匀,900 孔细度小,只在 3.0%以内, 1800 孔细度在 12%以内。
立磨的生料细度粗, 900 孔细度在 6.0-8.0%, 1800 孔细度在 22%摆布。
由上看出,现代水泥工业改成立磨后,生料的颗粒级配产生了较大的变化,立磨的生料粗大颗粒占比例明显上升,中等颗粒的比例,也较球磨机增加了一倍。
4、现代水泥工业、细度标准的变化。
80 年代,国家旋窑管理规程对细度有控制要求,最开始的标准规定生料细度小于等于 10%,作为一次水泥工艺管理的标准来执行,其后更改为 12%。
后来随着先进水泥工艺发展,生料细度作为一次过程控制指标,再也不强制执行,由企业根据自身生产需要自行控制。
质量体系认证,也将细度标准作为企业自行制定来审核,细度标准被企业自身不断放松标准。
按照现行立磨的生产工艺,生料细度按 10%、12%、16% 等等标准,已经无法满足当前立磨工艺的要求,根据立磨的特点及与窑的产能关系,细度只能控制在 20-22%之间,即使控制较好的工厂细度也在 8 摆布。
但是 , 目前的细度控制指标,不表示细度粗对煅烧没有影响。
生料质量对水泥熟料煅烧的影响
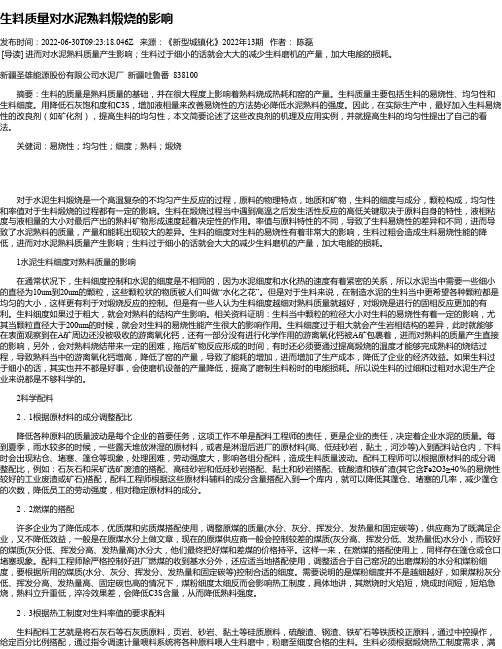
生料质量对水泥熟料煅烧的影响发布时间:2022-06-30T09:23:18.046Z 来源:《新型城镇化》2022年13期作者:陈磊[导读] 进而对水泥熟料质量产生影响;生料过于细小的话就会大大的减少生料磨机的产量,加大电能的损耗。
新疆圣雄能源股份有限公司水泥厂新疆吐鲁番 838100摘要:生料的质量是熟料质量的基础,并在很大程度上影响着熟料烧成热耗和窑的产量。
生料质量主要包括生料的易烧性、均匀性和生料细度。
用降低石灰饱和度和C3S,增加液相量来改善易烧性的方法势必降低水泥熟料的强度。
因此,在实际生产中,最好加入生料易烧性的改良剂(如矿化剂),提高生料的均匀性,本文简要论述了这些改良剂的机理及应用实例,并就提高生料的均匀性提出了自己的看法。
关健词:易烧性;均匀性;细度;熟料;煅烧对于水泥生料煅烧是一个高温复杂的不均匀产生反应的过程,原料的物理特点,地质和矿物,生料的细度与成分,颗粒构成,均匀性和率值对于生料煅烧的过程都有一定的影响。
生料在煅烧过程当中遇到高温之后发生活性反应的高低关键取决于原料自身的特性,液相粘度与液相量的大小对最后产出的熟料矿物形成速度起着决定性的作用。
率值与原料特性的不同,导致了生料易烧性的差异和不同,进而导致了水泥熟料的质量,产量和能耗出现较大的差异。
生料的细度对生料的易烧性有着非常大的影响,生料过粗会造成生料易烧性能的降低,进而对水泥熟料质量产生影响;生料过于细小的话就会大大的减少生料磨机的产量,加大电能的损耗。
1水泥生料细度对熟料质量的影响在通常状况下,生料细度控制和水泥的细度是不相同的,因为水泥细度和水化热的速度有着紧密的关系,所以水泥当中需要一些细小的直径为10um到20um的颗粒,这些颗粒状的物质被人们叫做“水化之花”。
但是对于生料来说,在制造水泥的生料当中更希望各种颗粒都是均匀的大小,这样更有利于对煅烧反应的控制。
但是有一些人认为生料细度越细对熟料质量就越好,对煅烧是进行的固相反应更加的有利。
水泥生料易烧性与熟料煅烧效率

Cement and concrete production 水泥与混凝土生产1 水泥生料易烧性与熟料煅烧效率扈德鹏(酒钢宏达建材有限责任公司,甘肃嘉峪关735100)中图分类号:TQ172 文献标识码:B 文章编号1007-6344(2019)11-0001-01摘要:对于水泥来讲,生料的易烧性会直接影响到熟料的煅烧效率,并且生料的易烧性也会对熟料的烧成热耗和窑的产量产生非常大的影响。
在目前的水泥烧窑的过程当中,经常加入改良剂来提高熟料的煅烧效率。
本篇文章通过对水泥生料易烧性与熟料煅烧效率进行分析研究,并且提出一定意见,为水泥熟料的煅烧效率提供意见参考。
关键词:水泥生料;易烧性;熟料煅烧效率0 引言在水泥生产的过程当中,熟料煅烧是非常重要的一部分内容。
提高水泥熟料煅烧的质量,保证水泥的质量,提高水泥的产量,降低生产水泥的消耗对于企业的发展来说具有非常重要的意义,然而要做到这三方面的内容不仅要控制水泥生产的过程以及相关技术的应用,也要控制水泥生产原料的质量。
对于水泥生产来说,生产原料的质量包括三大内容,分别是生料的易烧性,生料的均匀性以及生料的细度,在这三方面内容当中生料的易烧性会直接影响到水泥熟料的煅烧效率,直接影响到水泥的生产。
1 生料的易烧性基本概念在水泥的生产过程当中,原材料的燃烧过程会受到原材料本身的物质组成,颗粒大小,化学成分等因素的影响。
原材料的燃烧程度会直接影响到窑的产量,熟料的煤耗以及熟料的质量。
实际上水泥生料的易烧性是指水泥在煅烧的过程当中形成熟料的难易程度。
水泥生料的易烧性会受到原材料的物质组成,颗粒大小化学成分等因素的影响,如果易烧性好,则煅烧过程中所需要的温度较低,如果易烧性不好,则煅烧过程当中所需要的温度较高。
一般通过对水泥的原材料进行灼烧后,检验原材料当中的氧化钙含量来测定该原材料的易烧性的高低。
如果灼烧后氧化钙的含量过高,则说明原材料的易烧性很低,如果氧化钙的含量低则说明原材料的易烧性高。
生料的最佳细度

生料的最佳细度2009-02-03 13:15生料的最佳细度应由各厂的原料实验及生产实践来确定,其确定原则是: (1)只要在窑的煅烧允许范围内,生料粒度宜于放粗。
一般讲,生料应当磨至1‘70#(90 u m)的筛余量为15%,而50#(300 u m)的筛余量为1.5%~2.5%。
大多数企业已基本掌握此控制原则。
实际上,根据上述理论依据,细度仍可进一步放粗。
所以,有的生产线已将生料细度调整为807pm筛余量22%,其效果很好。
在满足并有利煅烧条件下,提高了磨机产量,降低了电耗,一举三得。
(2)增加200 um的筛余量的控制指标。
国内大多数生产线仍以控制80 μm作为考核指标,对200 um的筛余量不做检验。
这样控制的结果可能是:即使将80 μ m的筛余量控制放宽到15%,也并不能说明大于200 μ m的筛余量就一定很小。
一旦影响窑的煅烧,究竟是因为200 μ m的筛余量过小,还是80 u m筛佘量过大,就难以下结论。
反之,如果200 μ m的筛余量能控制在2%以下,窑的煅烧情况很好,能否使80μ m的筛余量过大,以求节能增产,这就是精细运转需要做的工作。
生料0.2mm筛余比80μm筛余更重要。
作为生料粉磨质量控制指标,80μm 筛余比0.2mm筛余更适宜。
在生料粒度分布没用明显改变的情况下,80μm筛余与0.2mm筛余具有良好的相关性。
窑内的煅烧类似于分步反应,整个反应速度是由反应速度最慢的那部分物料决定的。
0.2mm筛余对生料易烧性的影响更大。
方解石颗粒大于125μm,石英颗粒大于45μm即可影响熟料的煅烧速度。
在生料粉磨过程中,不同原料的实际粒度分布与期待的正好相反。
按照反应活性要求,硅质原料的粒径应该粉磨至比其它原料更细,但实际上因为硅质原料不但难烧而且难磨,会比其它原料的粒径更大。
生料粗颗粒部分中的SiO2含量更高。
检验80μm筛余的化学成分有助于了解这一点,但是实际上很难改善。
试验结果表明,在相同的煅烧条件下,0.2mm筛余与f-CaO的关系如表4所示。
浅析影响熟料煅烧煤耗的主要因素与降耗措施
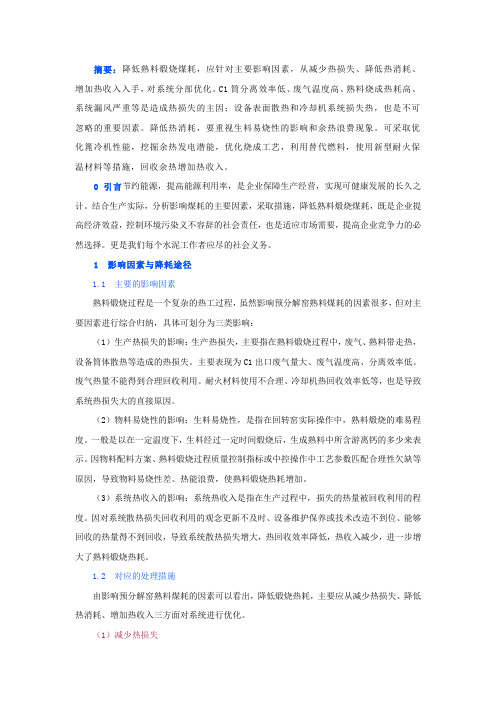
摘要:降低熟料煅烧煤耗,应针对主要影响因素,从减少热损失、降低热消耗、增加热收入入手,对系统分部优化。
C1筒分离效率低、废气温度高、熟料烧成热耗高、系统漏风严重等是造成热损失的主因;设备表面散热和冷却机系统损失热,也是不可忽略的重要因素。
降低热消耗,要重视生料易烧性的影响和余热浪费现象。
可采取优化篦冷机性能,挖掘余热发电潜能,优化烧成工艺,利用替代燃料,使用新型耐火保温材料等措施,回收余热增加热收入。
0 引言节约能源,提高能源利用率,是企业保障生产经营,实现可健康发展的长久之计。
结合生产实际,分析影响煤耗的主要因素,采取措施,降低熟料煅烧煤耗,既是企业提高经济效益,控制环境污染义不容辞的社会责任,也是适应市场需要,提高企业竞争力的必然选择。
更是我们每个水泥工作者应尽的社会义务。
1 影响因素与降耗途径1.1 主要的影响因素熟料煅烧过程是一个复杂的热工过程,虽然影响预分解窑熟料煤耗的因素很多,但对主要因素进行综合归纳,具体可划分为三类影响:(1)生产热损失的影响:生产热损失,主要指在熟料煅烧过程中,废气、熟料带走热,设备筒体散热等造成的热损失。
主要表现为C1出口废气量大、废气温度高、分离效率低。
废气热量不能得到合理回收利用。
耐火材料使用不合理、冷却机热回收效率低等,也是导致系统热损失大的直接原因。
(2)物料易烧性的影响:生料易烧性,是指在回转窑实际操作中,熟料煅烧的难易程度。
一般是以在一定温度下,生料经过一定时间煅烧后,生成熟料中所含游离钙的多少来表示。
因物料配料方案、熟料煅烧过程质量控制指标或中控操作中工艺参数匹配合理性欠缺等原因,导致物料易烧性差、热能浪费,使熟料煅烧热耗增加。
(3)系统热收入的影响:系统热收入是指在生产过程中,损失的热量被回收利用的程度。
因对系统散热损失回收利用的观念更新不及时、设备维护保养或技术改造不到位、能够回收的热量得不到回收,导致系统散热损失增大,热回收效率降低,热收入减少,进一步增大了熟料煅烧热耗。
[终稿]生料质量对煅烧的影响
![[终稿]生料质量对煅烧的影响](https://img.taocdn.com/s3/m/a5f1923dcec789eb172ded630b1c59eef9c79a59.png)
一、专题——生料质量对窑煅烧及熟料质量的影响。
熟料煅烧是水泥生产的中心环节,能否做到优质、高产、低耗,对一个企业的经济效益和竞争能力,都是一个举足轻重的问题。
然而要做到熟料煅烧的优质、高产、低耗,与生产过程控制和窑的工艺管理及操作技术有关外,保证生料的质量就更为重要。
生料的质量包括很多内容.主要有:生料的三率值饱和比(KH),硅酸率(SM),铝氧率(IM),生料水份,生料细度,生料的化学成份及有害成份,均匀性等,下面对影响熟料煅烧及质量因素分别进行阐述。
生料的三率值饱和比(KH),硅酸率(SM),铝氧率(IM)对窑煅烧及熟料质量的影响石灰饱和比:熟料中全部氧化硅生成硅酸钙(C3S+C2S)所需的氧化钙含量与全部二氧化硅理论上生成硅酸三钙所需的氧化钙含量的比值,表示熟料中氧化硅被氧化钙饱和形成的硅酸三钙程度。
CaO-1.65Al2O3-0.35Fe2O3KH=2.80SiO2KH过高,熟料煅烧困难,必须延长煅烧时间,否则会出现f-CaO,同时窑的产量低,热耗高。
KH过低,熟料煅烧容易,但熟料强度也低。
硅酸率:表示熟料中而SiO2的百分含量与AI2O3和Fe2O3百分含量之比。
SiO2SM=Al2O3+Fe2O3硅率随硅酸盐矿物与溶剂矿物之比而增减。
如果熟料中硅率过高时,则煅烧时由于液相量显著减少,熟料煅烧困难,特别当氧化钙含量低,硅酸二钙含量高时,熟料易于粉化。
硅率过低则熟料中硅酸盐矿物太少而影响水泥强度,且由于液相过多,易出现结大块,结圈等,影响窑的操作。
铝氧率:又称铝率或铝氧率,是表示熟料中氧化铝和氧化铁含量的质量比,也表示熟料熔剂矿物中铝酸三钙与铁铝酸四钙的比例。
Al2O3IM=Fe2O3铝率高,熟料中铝酸三钙多,相应铁铝酸四钙就较少,则液相粘度大,物料难烧。
铝率过低,虽然液相粘度较小,液相中质点易于扩散,对硅酸三钙形成有利,但烧结范围变窄,窑内易结大块,不利于窑的操作。
生料的水份和细度对窑煅烧及熟料质量的影响水份:出磨生料水份偏高,热耗上升,另外水份大,生料粉的流动性变差,流速变慢,导致生料均化效果变差,易产生结库现象。
水泥工艺培训材料(生料、熟料部分)

水泥工艺培训材料(生料、熟料部分)一新型干法工艺流程二、水泥生产的原燃料及配料2.1、水泥生产原料2.1.1.石灰质原料:(石灰石、大理石等)占生料70~75% (本厂82~87%)2.1.2粘土质原料:(硅铝质原料、粘土、砂岩等)占生料10~20% (砂岩4~6%)2.1.3.校正原料:(铁质、铝质原料、外加剂等)占生料5~10% (煤矸石3~4% 粉煤灰3~4% 钢渣3~4%)(有3、4、5组分配料。
其中组分多、易于调整。
我们厂现在是5组分配料)2.2、水泥生产燃料1.固体燃料(1)烟煤:挥发分≥14% 回转窑主要使用烟煤。
Vf(30~36%)Af(8~12%)Qdwf(6000~6500)(2)无烟煤:挥发分≤10%(3)低质煤:热值≤4000×4.18kJ/kg2.液体和气体燃料重油、渣油、天然气、煤气等。
2.3水泥熟料的矿物组成2.3.1、熟料矿物组成C3S ——硅酸三钙(含量:50~60%)(强度高)C2S ——硅酸二钙(含量:15~32%)(强度较高)C3A ——铝酸三钙(含量:3~11%)(凝结快)C4AF——铁铝酸四钙(含量:8~18%)(耐磨耐蚀)2.3.2、主要化学成分:CaO 62~67%、SiO2 20~24%、Al2O3 4~7%、Fe2O3 2.5~6%。
MgO R2O SO3 CL-2.4、硅酸盐水泥熟料的率值2.4.1.率值:水泥熟料中各氧化物之间的相对含量的比值。
它与熟料的矿物组成、熟料质量、生料的易烧性有密切的关系,是水泥生产中的重要控制指标之一。
2.4.2常用率值:(1)石灰饱和比(KH):表示SiO2被CaO饱和成C3S的程度。
KH={CaO-(1.65*AL2O3+0.35*Fe2O3+0.7SO3)}/2.8SiO2(2)硅酸率(n或SM):表示SiO2与Al2O3及Fe2O3之和的比值。
SM=SiO2/(Al2O3+Fe2O3)(3)铝氧率(P或IM):表示Al2O3与Fe2O3的比值。
关于做好生料配料工作确保熟料煅烧质量
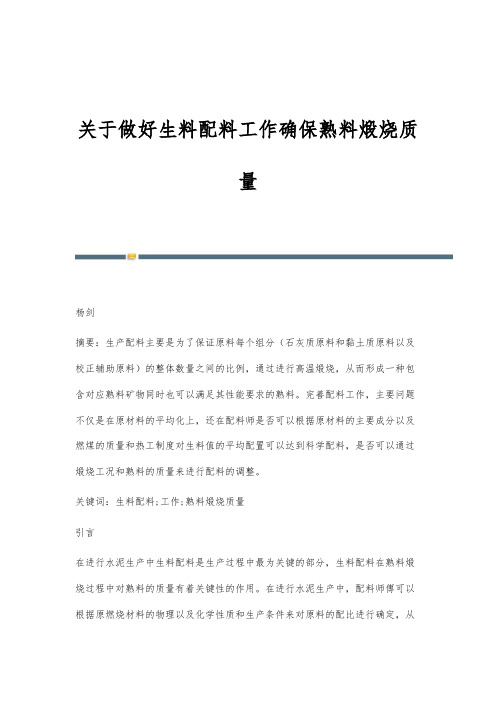
关于做好生料配料工作确保熟料煅烧质量杨剑摘要:生产配料主要是为了保证原料每个组分(石灰质原料和黏土质原料以及校正辅助原料)的整体数量之间的比例,通过进行高温煅烧,从而形成一种包含对应熟料矿物同时也可以满足其性能要求的熟料。
完善配料工作,主要问题不仅是在原材料的平均化上,还在配料师是否可以根据原材料的主要成分以及燃煤的质量和热工制度对生料值的平均配置可以达到科学配料,是否可以通过煅烧工况和熟料的质量来进行配料的调整。
关键词:生料配料;工作;熟料煅烧质量引言在进行水泥生产中生料配料是生产过程中最为关键的部分,生料配料在熟料煅烧过程中对熟料的质量有着关键性的作用。
在进行水泥生产中,配料师傅可以根据原燃烧材料的物理以及化学性质和生产条件来对原料的配比进行确定,从而得到煅烧合格的熟料在使用中的成分。
本文主要根据实际情况,来对每一个环节进行配料质量中存在的影响以及配料质量在生产中的影响,对配料工程师如何进行配料工作以及质量的控制和生产操作进行有效研究。
1科学配料根据原材料的成分调整配比现如今,每个企业的首要工作是减少各种原料的质量波动,减少原料的质量波动不仅是配料工程师的责任,同时也是企业进行发展的保证,对企业生水泥的质量有着重要的保证。
在夏季到来时,雨季较多,由于在外放置的原材料被淋湿,或者是在淋湿之后放置在配料站仓中,往往在下料中会出现粘仓和堵塞的情况,并且在进行处理中较为困难,进行清理工作量较大,从而对每一组进行配料区分有着严重的影响,对生料的质量带来了较大的波动。
配料工程师在进行配料中可以根据原材料的成分来进行调整配比,比如,在将石灰石与采矿选矿废渣进行搭配时,或者是高硅砂岩和低硅砂岩搭配、黏土和砂岩搭配、硫酸渣和铁矿渣其中包含的都是容易燃烧的工业废料进行搭配,配料工程师可以根据原材料中的辅助成分的含量来放置在一个库内,这样可以有效的减少出现蓬仓和堵塞的情况,同时可以有效的降低出现蓬仓的次数,并有效的降低了员工进行工作的强度,对原材料的成分有着稳定的作用。
水泥的物理化学性质

2.2<SM<3.2
f-CaO
更易烧结
硅酸率为 2.2%以便获得足够的
硅酸率最高不能超过 3.2%最低
C2S、C3S 和较高的物理强度
限度地保证溶剂量(液相)
◇ AM 铝氧率 AM = A / F 通过 AM 来控制 C3A /C4AF 的比例。1<AM<2.5
小结
氧化钙不饱和系
0<△<3% △<7%
★生料里都含什么那?
★煅烧过程都发生那些变化?
第 6 页 共 43 页
★煅烧过程都都释放出什么? ★熟料里有那些矿物组成?
你将收获co3 铝矾土 Al2O3 铁粉 Fe2O3
如果用煤做燃料灰
分中会掺入微量 sio2
Fe2O3
Al2O3
石灰石和硅质原料(黏土\砂岩)不是很纯,互相掺有成分.为了达到一个合理的配值,人们会使用一些辅助纯净产
每天收获一点
第三种微量元素 : 氧化镁 MgO 来源:碳酸盐分解中产生的。
性质:当氧化镁以晶体存在时 它的水化速度很缓慢。如果混凝土暴露在一定温度下。几年后会产生极大的膨胀。
控制方法:使熟料迅速急冷,使液相固化将氧化镁吸收(防止其结晶)。
小结
f-CaO K2SO3 Na2SO3 Na2O K2O
Ca2SO3
水泥是什么?
石膏
熟料 +
混合材 研磨
水泥
石子
水
水泥:熟料加适量石膏和混合材经过研磨成粉状,具有水硬性胶凝材料。
即使在缺少空气和水下,也逐渐凝固变硬。
石膏可调节混凝土的凝结时间,起缓凝作用。
水泥的质量(标号)是由水泥 28 天达到的抗压强度定义的。
第 2 页 共 43 页
学习他的精神
生料质量对水泥熟料煅烧的影响_1

生料质量对水泥熟料煅烧的影响发布时间:2022-07-26T07:35:20.309Z 来源:《新型城镇化》2022年15期作者:栾科军[导读] 生料的质量是熟料质量的基础,并在很大程度上影响着熟料烧成热耗和窑的产量。
生料质量主要包括生料的易烧性、均匀性和生料细度。
新疆圣雄能源股份有限公司水泥厂新疆吐鲁番 838100摘要:生料的质量是熟料质量的基础,并在很大程度上影响着熟料烧成热耗和窑的产量。
生料质量主要包括生料的易烧性、均匀性和生料细度。
用降低石灰饱和度和C3S,增加液相量来改善易烧性的方法势必降低水泥熟料的强度。
因此,在实际生产中,最好加入生料易烧性的改良剂(如矿化剂),提高生料的均匀性,本文简要论述了这些改良剂的机理及应用实例,并就提高生料的均匀性提出了自己的看法。
关健词:易烧性;均匀性;细度;熟料;煅烧熟料煅烧是水泥生产的中心环节,能否做到优质、高产、低耗,对一个企业的经济效益和竞争能力,都是一个举足轻重的问题。
然而要做到熟料煅烧的优质、高产、低耗,与生产过程控制和窑的工艺管理及操作技术有关外,保证生料的质量就更为重要。
1生料的易烧性对熟料煅烧的影响1.1易烧性的基本概念水泥生产中,生料在烧结过程中受其自身化学、矿物成份和颗粒组成的影响很大,特别对窑的产量、熟料煤耗以及熟料质量的影响最为显著。
一般来讲,水泥生料易烧性是说明其煅烧过程中形成熟料的难易程度的特性指标,受生料的化学、物理性质及矿物组成等多种因素的影响。
易烧性好则生料的煅烧温度可较低。
习惯上,生料在一定的温度(T)条件下经过一定时间(Q)煅烧后,通过测定f-CaO来衡量其易烧性,即:f-CaO=f(Q∶T),当温度超过1 300℃时,熔融相形成,易烧性随f-CaO的增大而降低。
易烧性通常用下列两个量中的一个表示。
在给定温度条件下,准等时线(Q=常数),测定f-CaO的值。
f-CaO的值增加,易烧性降低。
准等温线(T=常数),f-CaO≤1%的时间(Q)长,易烧性降低。
试析生料质量对水泥熟料煅烧的影响

试析生料质量对水泥熟料煅烧的影响摘要:生料品质是水泥熟料品质的根本,对水泥熟料的烧成热消耗及窑产有重要影响。
生料的品质主要有易烧性、均匀性及细度三个方面。
通过减少石灰饱和度、减少C3、S含量、提高液相含量等措施来提高易烧性,必然导致水泥熟料强度的下降。
文章对几种改性剂的作用机制和应用实例进行了简单探讨,并对如何改善生料均匀度提出了一些见解。
关键词:生料质量;水泥;熟料;煅烧引言:在水泥生产过程中,熟料锻烧质量好,产量高,能耗低,它与企业的经济效益、市场竞争能力有直接的联系。
然而,要达到优质、高产、低耗的熟料锻烧,除了涉及到生产过程的控制、窑炉的工艺管理和操作技术外,生料的质量也起着举足轻重的作用。
影响水泥熟料的品质有很多因素,接下来,我们将分别阐述这几个影响熟料锻烧的因素[1]。
一、生料易烧性对熟料锻烧效果的影响(一)易烧性的概念在水泥工业中,生料的化学成分、矿物成分及颗粒成分对其烧结率、熟料煤耗及熟料品质有较大的影响。
生料可烧性通常是反映水泥的一个重要特性,与水泥的物理化学特性及矿物学特性等有关。
随着可燃性的提高,生料的焙烧温度也随之降低2]。
一般来讲,在一定的温度(T)下,通过对一定时间(Q)的锻烧后,通过对f-CaO的测定来度量其易烧性,即:f-CaO= f (Q: T),在温度高于1300℃时,会产生熔融相,易烧性随着f-CaO的增大而降低。
可燃性一般由以下两个参数之一来表示。
然后,通过准等时线(Q为常量),在一定的温度下,测量f-CaO的含量。
氟钙氧含量提高,可燃性下降。
F-CaO含量低于1%时,呈现出准等温线(T为常量),其耐火性能下降[3]。
(二)易烧性的影响因素煤灰和炉子的气体是生料控制的问题,而不是生料本身。
但是需要指出的是,很多企业在生产过程中并没有充分考虑到生料的易烧性,只考虑了生料的化学成分、熟料的相态成分,而没有讨论生料的矿物成分、粒度成分等。
在反应动力学方面,除了生料的化学成分外,还应考虑生料中的矿物成分,生料中的碳酸盐岩在生料中的分解过程与生料中的碳酸盐岩的类型及粒度密切相关。
- 1、下载文档前请自行甄别文档内容的完整性,平台不提供额外的编辑、内容补充、找答案等附加服务。
- 2、"仅部分预览"的文档,不可在线预览部分如存在完整性等问题,可反馈申请退款(可完整预览的文档不适用该条件!)。
- 3、如文档侵犯您的权益,请联系客服反馈,我们会尽快为您处理(人工客服工作时间:9:00-18:30)。
一、专题——生料质量对窑煅烧及熟料质量的影响。
熟料煅烧是水泥生产的中心环节,能否做到优质、高产、低耗,对一个企业的经济效益和竞争能力,都是一个举足轻重的问题。
然而要做到熟料煅烧的优质、高产、低耗,与生产过程控制和窑的工艺管理及操作技术有关外,保证生料的质量就更为重要。
生料的质量包括很多内容.主要有:生料的三率值饱和比(KH),硅酸率(SM),铝氧率(IM),生料水份,生料细度,生料的化学成份及有害成份,均匀性等,下面对影响熟料煅烧及质量因素分别进行阐述。
生料的三率值饱和比(KH),硅酸率(SM),铝氧率(IM)对窑煅烧及熟料质量的影响
石灰饱和比:熟料中全部氧化硅生成硅酸钙(C
3S+C
2
S)所需的氧化钙含量与
全部二氧化硅理论上生成硅酸三钙所需的氧化钙含量的比值,表示熟料中氧化硅被氧化钙饱和形成的硅酸三钙程度。
CaO-1.65Al
2O
3
-0.35Fe
2
O
3
KH=
2.80SiO
2
KH过高,熟料煅烧困难,必须延长煅烧时间,否则会出现f-CaO,同时窑的产量低,热耗高。
KH过低,熟料煅烧容易,但熟料强度也低。
硅酸率:表示熟料中而SiO2的百分含量与AI2O3和Fe2O3百分含量之比。
SiO2
SM=
Al2O3+Fe2O3
硅率随硅酸盐矿物与溶剂矿物之比而增减。
如果熟料中硅率过高时,则煅烧时由于液相量显著减少,熟料煅烧困难,特别当氧化钙含量低,硅酸二钙含量高时,熟料易于粉化。
硅率过低则熟料中硅酸盐矿物太少而影响水泥强度,且由于液相过多,易出现结大块,结圈等,影响窑的操作。
铝氧率:又称铝率或铝氧率,是表示熟料中氧化铝和氧化铁含量的质量比,也表示熟料熔剂矿物中铝酸三钙与铁铝酸四钙的比例。
Al
2O 3
IM=
Fe
2O 3
铝率高,熟料中铝酸三钙多,相应铁铝酸四钙就较少,则液相粘度大,物料难烧。
铝率过低,虽然液相粘度较小,液相中质点易于扩散,对硅酸三钙形成有利,但烧结范围变窄,窑内易结大块,不利于窑的操作。
生料的水份和细度对窑煅烧及熟料质量的影响
水份:出磨生料水份偏高,热耗上升,另外水份大,生料粉的流动性变差,流速变慢,导致生料均化效果变差,易产生结库现象。
生料细度偏粗:(1)细度大,特别是0.20mm筛余大,颗粒表面积减少了煅烧过程中颗粒之间的接触,同时颗粒表面积小,自由能减少,不易参加反应,致使生料中碳酸钙分解不完全,易造成f-CaO增加,熟料质量下降。
(2)熟料矿物主要通过固相反应形成的。
固相反应的速度除与原料的矿物性质有关外,在均化程度、煅烧温度和时间相同的前提下,与生料的细度成正比关系,细度愈细,反应速度愈快,反应过程愈易完全。
生料的均匀性对窑煅烧及熟料质量的影响
生料的均匀性差,生料成分波动大,影响燃烧的稳定性,热耗增加;窑内热工紊乱,降低窑砖使用寿命,降低窑产量,加剧SO3挥发;熟料质量下降。
造成生料均匀性差,生料成分波动大的因素:矿山开采造成石灰石波动大,石灰石及辅料的预均化效果,配料仓堵料,分析仪器故障,出磨生料质量的波动,生料磨配料称计量的准确性,均化库的均化效果及窑灰的处理等。
各氧化物对窑煅烧及熟料的影响
(1) 氧化钙(CaO):它是熟料中最重要的化学成份,它与生料中的SiO2、Al2O3、Fe2O3在1260℃~1450℃高温下煅烧生成C3S、C2S、C3A、C4AF。
一般说来,增加生料中CaO含量,当煅烧温度正常时,能得到较多的C3S、C2S,水泥熟料质量好,强度高,但煅烧温度低时,则会产生大量游离CaO,易引起水泥安定性不良。
所以氧化钙含量最高的生料一般需要高温煅烧而且较难煅烧。
(2) 二氧化硅(SiO2):SiO2也是熟料中的主要成份之一,在高温下,它能与CaO 生成具有水硬性的硅酸钙(C3S、C2S),当生料中的CaO含量一定时,SiO2含量越多,高温下生成的硅酸钙越多,但形成的C3S较少,C2S较多,煅烧的熟料早期强度低、且增长变慢,而且SiO2高时Al2O3及Fe2O3相对含量降低,造成熟料煅烧困难。
如果SiO2低时,相应的Al2O3和Fe2O3的含量就增加,这样相应的硅酸盐矿物减少,而降低熟料强度,且窑内易结圈、结大块不利于窑的煅烧。
(3) 三氧化二铝(Al2O3):在煅烧过程中Al2O3与CaO、Fe2O3作用生成C3A和C4AF,并熔融为液相,促使C3S形成。
但Al2O3含量高时C3A生成量增多,熟料早期强度高,凝结时间快,且液相粘度大,不利于C3S形成。
窑内容易结大块,不利于窑的煅烧。
(4) 三氧化二铁(Fe2O3):在煅烧过程中与CaO、Al2O3生成C4AF并熔融成液相,且液相粘度小,Fe2O3过多时,熟料烧结温度范围变窄,尤其是在窑还原所氛严重时,Fe2O3被还原成FeO,物料过早出现低熔液相,易结大块,甚至结圈,且煅烧的熟料凝结的速度慢,强度绝对值不高。
(5)其它氧化物:其它氧化物的带入,可以降低熟料烧成温度,对C3S形成有利。
但过多会引起窑内结大块,使煅烧气氛恶化,除此之外,氧化镁过多,则使水泥
安定性不良。
硫、碱成分对煅烧存在不利的影响
1)影响煅烧过程的正常进行。
碱与硫的单独影响是,当熟料中碱的总含硫量或SO
3
超过熟料重量的1%时,过量的碱(K、Na)会影响窑尾烟室的结皮;过量的硫会引起窑内结圈。
当熟料
中SO
3
含量在1%左右时,会有利于改善生料易烧性,并提高熟料强度,但要以硫的含量增加不降低饱和比为前提。
考虑硫碱比对生产的影响就更为复杂。
在预分解窑中,保持硫碱比值的恒定是动态的。
由于物料在窑内停留时间特别短,热负荷又小,碱(K、Na)很容易随熟料带走,而硫化物仍在窑内挥发循环,此时由于碱的缺乏,在窑的后部会形成结皮的恶性循环,如果窑的煅烧温度过高,或火焰直扫到物料上,这种循环更会加剧,直到结皮或预热器堵塞发生。
而一旦在窑的低温区域,这些硫化物还要释
放出来,使生成的熟料中SO
3
变高。
硫在窑内的循环与富集机理是:窑内的硫化物主要形式是SO
2
,它在窑内的来
源是燃料中硫的氧化及硫酸盐的分解,理论上SO
2低温下可氧化成SO
3
,但实际
上99%的气态硫化物将是SO
2
,这样形成区域再度挥发,并在窑尾和四、五级预热器形成硫循环结皮时,碱性硫酸盐的挥发性将使它们存在于熟料中,这样循环严重时将引发预热器结瘤和堵塞出现。
2)不合理的硫碱比值会影响熟料质量及易烧性。
熟料中因SO
3过量会阻止C
3
S的形成。
成为形成黄心料的另一种原因。
熟料的褐色核心一般都认为是由窑内的还原气氛所致,但是由于形成高贝利特和硫酸盐浓缩减少了熟料的渗透性,阻止了冷却区亚铁(Fe2+)氧化成三价铁(Fe3+),这就成为黄心料出现的另一条途径,这本身又是由喂料的化学成分变化和硫化物在窑内的低挥发性造成的。
褐色熟料的不良结果就是热耗增加、降低易磨性、损失水泥强度和造成水泥快凝。
热生料中SO
3应小于3%,SO
3
和Cl-的总和应小于4%,其中Cl-含量对硫碱比
值影响很大,因为碱先是与氯化合为氯化碱,剩余的碱与硫结合成为硫碱化物。
正常硫碱含量比值应当保持在0.8~1.2。