通用对供应商特殊要求
上海通用对供应商质量要求的规定

(2006年5月版)前言SGM要求其供应商满足最新版ISO/TS16949及相关参考手册的要求,并适用所有通用汽车的相关顾客特殊要求(明确不适用于通用汽车亚太区的部分除外)。
要求供应商满足通用汽车供应商质量SOR的要求及通用汽车一般程序的适用部分(如GP4, GP5,GP9,GP10,GP11,GP12等)。
本文件概述了上海通用汽车对供应商质量方面的基本要求,是有关SGM供应商质量工作相关的程序和规定的节录,目的是为了帮助供应商更好地了解和执行SGM的相关要求。
欲了解相关具体要求和规定,请参考ISO/TS16949系列、GM9000、GM Global APQP等文件,及SGM其他有关程序。
如有任何问题,请与相关主管SQE联系。
欢迎各位SQE、供应商或其他使用人员反馈您的修改意见。
有关意见请反馈至上海通用汽车采购部SDE小组。
本文件的最新版本将在上海通用汽车网站站点导航中的“联合发展中心“下载。
通用汽车的一般程序可以从下载。
上海通用汽车采购部供应商质量及开发科2006年5月23日(2006年5月版)主要修订记录2004年10月,第一版制订2005年6月主要修订内容:1. SGM供应商质量声明参考GM2005年3月版本更新,并增补SGM对Consignment(集成供货)供应商的要求2. APQP增补对车身焊接总成供应商的要求3. FE按SGM有关程序(2005年2月版)改版4. PPAP删除对临时批准的具体定义,以适应GM临时批准的新分类标准5. 受控发运明确对一级发运不及时关闭时,直接进入二级发运控制的规定6. 增加GP9的具体规定2006年5月主要修订内容:1. 按ISO/TS16949通用汽车特殊要求2006年3月版修订补充通用汽车的特殊要求2. 按PPAP 4.0修订相关要求3. GM SQ SOR的最新更新4. 修订并单列SGM对集成供货供应商的要求。
(2006年5月版)目 录一、 SGM供应商质量声明二、 对Consignment(集成供货)供应商的附加要求三、 APQP四、 FE五、 PPAP六、 GP12七、 GP9八、 PTR/断点九、 控制计划审核十、 PRR十一、 受控发运十二、 产品与体系审核十三、 供应商易地生产十四、 年度优秀供应商评选十五、 持续改进附件(2006年5月版)一、SGM 供应商质量声明:1. Supplier Quality Base Requirements: 供应商质量基本要求:•Seller agrees to participate in Buyer’s supplier quality and development program(s) and to comply with all quality requirements and procedures specified by Buyer, as revised from time to time, including those applicable to Seller as set forth in Quality System Requirements QS-9000. In addition, Buyer shall have the right to enter Seller’s facility at reasonable times to inspect the facility, goods, materials and any property of Buyer covered by this contract. Buyer’s inspection of the goods, whether during manufacture, prior to delivery or within a reasonable time after delivery, shall not constitute acceptance of any work-in-process or finished goods.供应商应同意买方制定的供应商质量和开发程序并遵守买方列出的所有质量要求和程序(有时会修订), 以及QS9000质量体系提出的对供应商适用的要求. 除此之外,买方有权随时进入供应商的设施来检查设备,产品,材料和合同规定的SGM 所有物. 无论在制造期间,发运之前还是在发运后的某段时间,买方对产品的检查,不能够免除供应商对在制品或成品检查的责任。
顾客特殊要求CSR-IATF标准的补充

汽车上成千上万的零 部件,除了极少数的 零件,主机厂一般是 没有入库检验的,可 以想象,如果这么多 零件都被检验,那将 是多么壮观的场景呢!
那么如何保证零件质 量呢?
零件质量
过程质量 体系质量
QSB+(Quality Systems Basic Plus,质量体系基础+)是QSB 的最新版本,从13个战略方向不断提升整个供应链质量管理水平。
QSB+质量体系基础
其认证/审核流程如下:
IATF16949提供了一个通用的、系统的管理框架与标 准。
QSB+则接地气、具体的多,是一套非常实用的工 厂管理工作,每个要素都有详细的展开步骤,可以理 解成对ISO/TS16949的强化和补充
FORD审核表内容
制造过程能力计划 —质量程序计划 —FMEA/控制计划 —足够的人员配置/培训
—PPAP评审和节拍生产评审 —更改管理
证明制造过程能力 —分供方质量体系管理 —进料质量控制
—控制计划/作业指导书 —过程变异监控 —量具的校准和使用 —零件标识,不合格的零件,包装和 发货 —测量、工程规范 —预防性维护/仓库 —制造过程流程,精益生产 —问题解决,纠正措施
—召回
—停止发运 —同类产品PPM业绩
—交货业绩
—现场评审
—每月Q1总分 —违背诚信原则 —工厂背书 (证明或声明的意思) —售后服务件及维修 —投产表现(只适用于生产件) 每一个供应商的Q1初始分为1000分;为了保持Q1,供应商必须维持至
少800分。根据工厂以上业绩表现加减分数。
c 现场的行动计划
IATF16949顾客特殊要求顾客特定要求识别清单
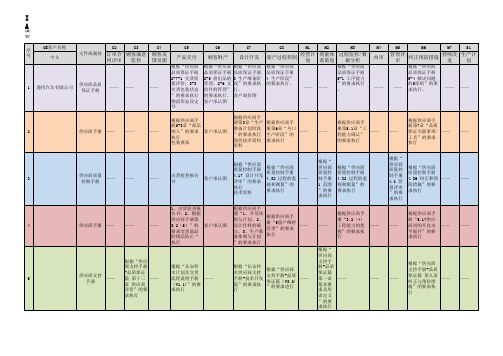
C8
M1
M2
M3
量产过程控制
经营计 划
质量体 系策划
过程监控/数 据分析
根据“供应商 品质保证手册 4 生产阶段” 的要求执行。
—— ——
根据“供应商 品质保证手册 5-1 工序能力 ”的要求执行 。
M4 内审
——
M5
M6
M7
S1
管理评 审
纠正预防措施
持续改 进
生产计 划
——
根据“供应商 品质保证手册 5-4 解决问题 的5原则”的要 求执行。
行
要求执行
——
——
根据“ 供应商 品质保 证手册 第二章 量产后 质量控 制 4.2 供应商 实施的 自主审 核”的 要求执 行
——
根据“
供应商
品质保
根据“供应商 证手册
品质保证手册 第二章
第二章 量产后 量产后
质量控制
质量控
3.1.4 持续改 制
进”的要求执 3.1.4
行
持续改
进”的
要求执
行
——
8
根据供应商手 册“5量产维持 管理”的要求 执行
——
——
根据供应商手 册“3.2(4) 工程能力的把 握”的要求执 行
——
——
根据供应商手 册“5.17供应 商间的不良水 平展开”的要 求执行
——
——
执行
”的要求执行
根据“
供应商
5
供应商支持 手册
——
根据“供应 商支持手册 -品质保证 篇 第十三 —— 章 供应商 评价”的要 求执行
—— ——
2
供应商手册 —— ——
——
根据供应商手 册5-3章“部品 纳入”的要求 客户承认图 执行 包装要求
③顾客特殊要求识别表
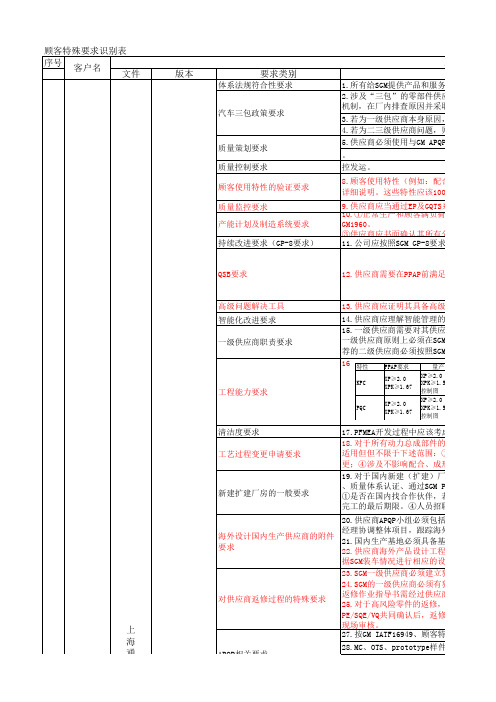
7.分阶段更新控制计划,并确保在前阶段生 8.供应商应在以下情况时告知上汽乘用车: 布置;任何影响匹配、形状、功能、性能的 9.供应商在全工装模具件(OTS)制造时,应 完成制造,并获得DRE和SQE的书面确认,以
10.供应商应在PPV阶段(首批样件评审)向 11.上汽按照以下程序实施质量问题的处理及 8D/PR&R→CS1→CS2→TOP-Q
GP-12退出要求
39.GP-12要有专门的区域及标识。 40.供应商在执行早期生产遏制时要按照GP运标签旁。 41.退出原则:①如GP-12期间在SGM现场无质 闭。②供应商现场的过程稳定受控,产品质 出退出申请,SGM SQE进行确认。④供应商在
42.按节拍生产的两种类型,顾客监控和供应 GP-9要求
上 海 通 用 汽 车 对
20.供应商APQP小组必须包括海外设计人员及 经理协调整体项目,跟踪海外设计进度,输 21.国内生产基地必须具备基本的人力资源和 海外设计国内生产供应商的附件要求 22.供应商海外产品设计工程师必须现场参与 据SGM装车情况进行相应的设计更改。 23.SGM一级供应商必须建立独立的返修流程 24.SGM的一级供应商必须有独立的返修区域 返修作业指导书需经过供应商技术部、质量 对供应商返修过程的特殊要求 25.对于高风险零件的返修,无论该零件来自 PE/SQE/VQ共同确认后,返修方可进行。供应 现场审核。 27.按GM IATF16949、顾客特殊要求、PPAP APQP相关要求
34.供应商提出的PPAP文件一律在EP系统中直
35.临时批准时供应商的责任:所有PPAP临时 临时批准的主要原因;②供应商应当明确所 施,以保证今后递交能够满足所有PPAP要求 36.PPAP的临时批准时间一般不超过3个月, 延长。 37.适用于所有新零件或工程更改新零件,从 GP-12要求
电子物料采购标准
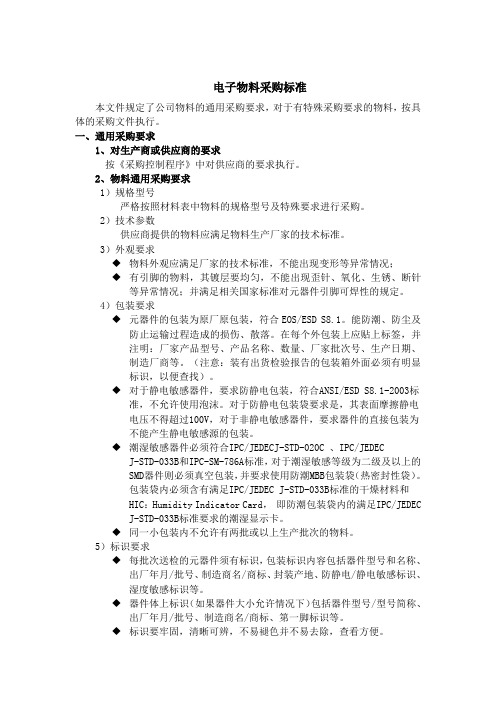
电子物料采购标准本文件规定了公司物料的通用采购要求,对于有特殊采购要求的物料,按具体的采购文件执行。
一、通用采购要求1、对生产商或供应商的要求按《采购控制程序》中对供应商的要求执行。
2、物料通用采购要求1)规格型号严格按照材料表中物料的规格型号及特殊要求进行采购。
2)技术参数供应商提供的物料应满足物料生产厂家的技术标准。
3)外观要求◆物料外观应满足厂家的技术标准,不能出现变形等异常情况;◆有引脚的物料,其镀层要均匀,不能出现歪针、氧化、生锈、断针等异常情况;并满足相关国家标准对元器件引脚可焊性的规定。
4)包装要求◆元器件的包装为原厂原包装,符合EOS/ESD S8.1。
能防潮、防尘及防止运输过程造成的损伤、散落。
在每个外包装上应贴上标签,并注明:厂家产品型号、产品名称、数量、厂家批次号、生产日期、制造厂商等。
(注意:装有出货检验报告的包装箱外面必须有明显标识,以便查找)。
◆对于静电敏感器件,要求防静电包装,符合ANSI/ESD S8.1-2003标准,不允许使用泡沫。
对于防静电包装袋要求是,其表面摩擦静电电压不得超过100V,对于非静电敏感器件,要求器件的直接包装为不能产生静电敏感源的包装。
◆潮湿敏感器件必须符合IPC/JEDECJ-STD-020C 、IPC/JEDECJ-STD-033B和IPC-SM-786A标准,对于潮湿敏感等级为二级及以上的SMD器件则必须真空包装,并要求使用防潮MBB包装袋(热密封性袋)。
包装袋内必须含有满足IPC/JEDEC J-STD-033B标准的干燥材料和HIC:Humidity Indicator Card,即防潮包装袋内的满足IPC/JEDECJ-STD-033B标准要求的潮湿显示卡。
◆同一小包装内不允许有两批或以上生产批次的物料。
5)标识要求◆每批次送检的元器件须有标识,包装标识内容包括器件型号和名称、出厂年月/批号、制造商名/商标、封装产地、防静电/静电敏感标识、湿度敏感标识等。
全球OEM汽车客户对于供应商执行IATF16949的特殊要求
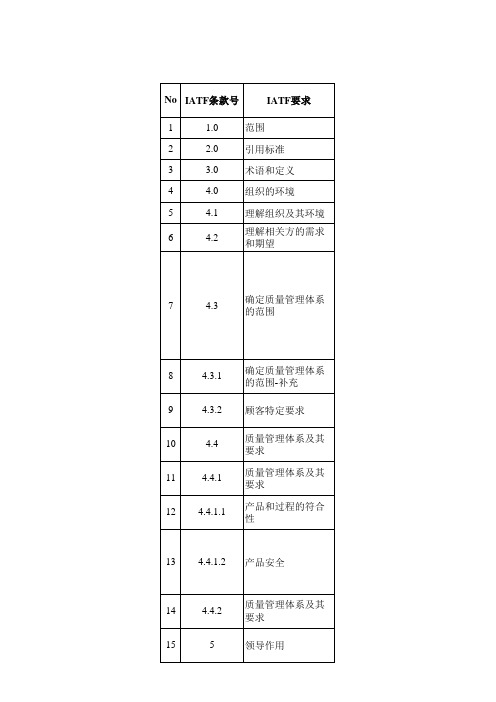
110
8.5
生产和服务提供
111
8.5.1
生产和服务提供的 控制
112 8.5.1.1 控制计划ຫໍສະໝຸດ 1128.5.1.2
标准化作业-操作指 导书和目视标准
109 8.5.1.3 作业准备的验证 110 8.5.1.4 停工后的验证
111 8.5.1.5 全面生产维护
生产工装及制造、 112 8.5.1.6 试验、检验工装和
设备的管理
112 8.5.1.7 生产排程
109 8.5.2 标识和可追溯性
110
8.5.2.1
标识和可追溯性-补 充
111
8.5.3
属于顾客或外部供 方的财产
112 8.5.4 防护
112 8.5.4.1 防护-补充 109 8.5.5 交付后的活动 110 8.5.5.1 服务信息的反馈
111 8.5.5.2 与顾客的服务协议 112 8.5.6 更改的控制
8.2.3.1.1
产品和服务要求的 评审-补充
87
8.2.3.1.2
顾客指定的特殊特 性
88 8.2.3.1.3 组织制造可行性
89
8.2.3.2
参见ISO 9001: 2015的要求。
90
8.2.4
产品和服务要求的 更改
91
8.3
产品和服务的设计 和开发
92
8.3.1 总则
产品和服务的设计 93 8.3.1.1 和开发-补充
67
7.5.1 总则
68 7.5.1.1 质量管理体系文件
69
7.5.2 编制和更新
70
7.5.3
形成文件的信息的 控制
71
7.5.3.1
通用汽车公司顾客特殊要求- ISO TS 16949 与 PPAP 第四版特别说明书
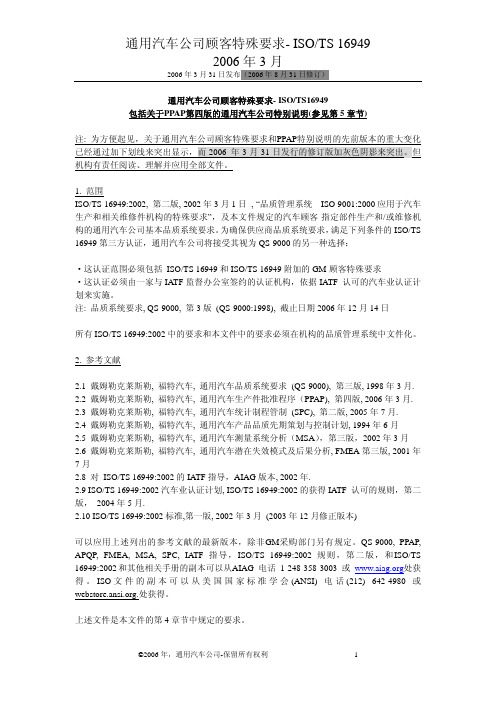
2006年3月31日发布(2006年8月31日修订)通用汽车公司顾客特殊要求- ISO/TS16949包括关于PPAP第四版的通用汽车公司特别说明(参见第5章节)注: 为方便起见,关于通用汽车公司顾客特殊要求和PPAP特别说明的先前版本的重大变化已经通过加下划线来突出显示,而2006 年3月31日发行的修订版加灰色阴影来突出。
但机构有责任阅读、理解并应用全部文件。
1. 范围ISO/TS 16949:2002, 第二版, 2002年3月1日 , “品质管理系统 –ISO 9001:2000应用于汽车生产和相关维修件机构的特殊要求”,及本文件规定的汽车顾客-指定部件生产和/或维修机构的通用汽车公司基本品质系统要求。
为确保供应商品质系统要求,满足下列条件的ISO/TS 16949第三方认证,通用汽车公司将接受其视为QS-9000的另一种选择:·这认证范围必须包括 ISO/TS 16949和ISO/TS 16949附加的GM-顾客特殊要求·这认证必须由一家与IATF监督办公室签约的认证机构,依据IATF 认可的汽车业认证计划来实施。
注: 品质系统要求, QS-9000, 第3版 (QS-9000:1998), 截止日期2006年12月14日所有ISO/TS 16949:2002中的要求和本文件中的要求必须在机构的品质管理系统中文件化。
2. 参考文献2.1 戴姆勒克莱斯勒, 福特汽车, 通用汽车品质系统要求 (QS-9000), 第三版, 1998年3月.2.2 戴姆勒克莱斯勒, 福特汽车, 通用汽车生产件批准程序(PPAP), 第四版, 2006年3月.2.3 戴姆勒克莱斯勒, 福特汽车, 通用汽车统计制程管制 (SPC), 第二版, 2005年7月.2.4 戴姆勒克莱斯勒, 福特汽车, 通用汽车产品品质先期策划与控制计划, 1994年6月2.5 戴姆勒克莱斯勒, 福特汽车, 通用汽车测量系统分析(MSA),第三版,2002年3月2.6 戴姆勒克莱斯勒, 福特汽车, 通用汽车潜在失效模式及后果分析, FMEA第三版, 2001年7月2.8 对 ISO/TS 16949:2002的IATF指导,AIAG版本, 2002年.2.9 ISO/TS 16949:2002汽车业认证计划, ISO/TS 16949:2002的获得IATF 认可的规则,第二版, 2004年5月.2.10 ISO/TS 16949:2002标准,第一版, 2002年3月 (2003年12月修正版本)可以应用上述列出的参考文献的最新版本,除非GM采购部门另有规定。
公司物资采购标准技术规范通用部分

公司物资采购标准技术规范通用部分1. 引言本文档是公司物资采购标准技术规范的通用部分,旨在规范公司物资采购过程,提高物资采购的质量和效率。
本文档适用于公司对各类物资的采购需求,包括但不限于原材料、设备、工具、耗材等。
2. 规范要求2.1 法律法规采购物资必须符合当地国家、地区、行业相关法律法规,特别是产品制造、产品进口和贸易等领域相关的法律法规。
在采购物资前,仔细检查物资供应商是否具有相应的资质和许可证,并核验所提供资质和许可证的真实性和有效性。
2.2 质量要求所采购的物资必须符合国家或行业标准,或经专业检验机构检测合格。
对于特殊的物资,应参照相关的行业标准或规范。
在采购完成后,应对物资进行检验,确保其质量达到要求。
2.3 价格要求所采购的物资价格必须合理、公正、透明。
在确定采购物资价格时,应当考虑到物质、工艺、成本、市场供需等因素,做到合理定价。
同时,为了保障采购过程的公正、透明,应当多方比较,选择最优的供应商。
2.4 交期要求采购物资的交货期限必须严格按照合同约定的时间内交货。
在签署采购合同时,应与供应商确认交货时间,以确保在所需时间内完成交货。
同时,在采购过程中,要时刻关注物资的采购情况,以避免采购过程延误,对后续工作造成不良影响。
2.5 环保要求采购物资时,必须遵守环保法规和企业环保政策,选择符合环保要求的物资。
并强烈建议选择符合国家或行业环保标准的物资,以达到资源节约、环保减排的目的。
2.6 售后服务采购完成后,供应商应该提供有效的售后服务。
特别是对于质量问题或装配不良等特殊情况,供应商应当积极协调解决,确保业务的正常运转。
3. 采购管理3.1 采购计划在采购物资前,应制定详细的采购计划,包括采购的每个物资的需求情况、采购时间、采购数量、预算等详细信息。
采购计划应当充分考虑生产、工程等业务的实际情况,保障正常业务的需求。
3.2 采购流程采购流程包括需求确认、供应商选择、采购合同签订、货款支付、物资验收等环节。
顾客特殊要求

通用公司顾客特殊要求-ISO/TS 169492002年9月1. 范围ISO/TS16949:2002,第二版,2002年3月1日,“质量管理体系—汽车业产品和相关服务件组织实施ISO 9001:2000特殊要求”和本文件定义了通用公司对制造汽车业顾客指定零件的产品和/或服务的组织的基本质量体系要求。
为确保供方质量体系要求,作为QS-9000的选择,通用公司将接受满足下列条件的ISO/TS 16949的第三方认证。
认证范围必须包括ISO/TS 16949和附随的ISO/TS 16949通用顾客特殊要求。
认证必须由与IATF监督办公室有契约的认证机构按符合IATF认可的汽车业认证计划来实施。
注:质量体系要求,QS-9000第三版(QS-9000:1998)将在2006年12月14日终止。
所有ISO/TS 16949:2002要求和本文件的要求必须文件化于组织的质量体系中。
2. 参考书目2.1 戴姆勒·克莱斯勒,福特,通用“质量体系要求(QS-9000),第三版”,1998年3月。
2.2 戴姆勒·克莱斯勒,福特,通用“生产件批准程序,PPAP),第三版”,1999年9月。
2.3 戴姆勒·克莱斯勒,福特,通用“统计过程控制(SPC),第一版”,1992。
2.4 戴姆勒·克莱斯勒,福特,通用“产品质量先期策划和控制计划”,1994。
2.5 戴姆勒·克莱斯勒,福特,通用“测量系统分析,MSA,第三版”,2002年3月。
2.6 戴姆勒·克莱斯勒,福特,通用“潜在失效模式及后果分析,FMEA,第三版”,2001年4月。
2.7 ISO/IEC 导则62:1996 I AF的实施指南,2001,12月。
2.8 IATF的ISO/TS 16949:2002指南,AIAG出版,2002。
2.9 ISO/TS 16949:2002达到IATF认可规则的汽车业认证计划, ISO/TS 16949:2002第一版,2002年3月。
询价文件范本(通用)
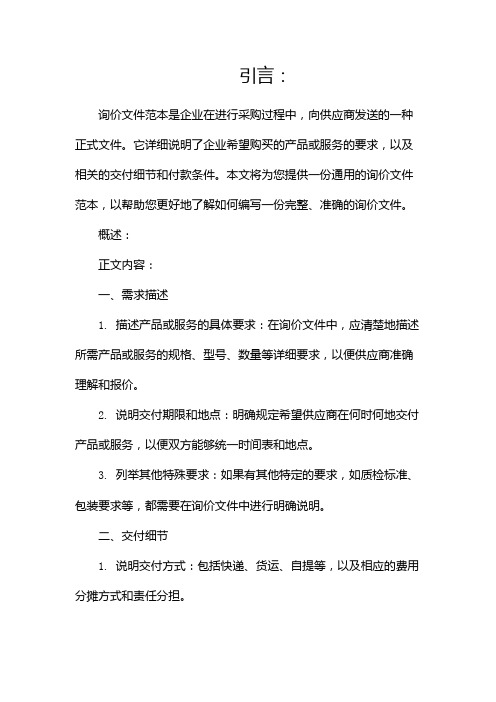
引言:询价文件范本是企业在进行采购过程中,向供应商发送的一种正式文件。
它详细说明了企业希望购买的产品或服务的要求,以及相关的交付细节和付款条件。
本文将为您提供一份通用的询价文件范本,以帮助您更好地了解如何编写一份完整、准确的询价文件。
概述:正文内容:一、需求描述1. 描述产品或服务的具体要求:在询价文件中,应清楚地描述所需产品或服务的规格、型号、数量等详细要求,以便供应商准确理解和报价。
2. 说明交付期限和地点:明确规定希望供应商在何时何地交付产品或服务,以便双方能够统一时间表和地点。
3. 列举其他特殊要求:如果有其他特定的要求,如质检标准、包装要求等,都需要在询价文件中进行明确说明。
二、交付细节1. 说明交付方式:包括快递、货运、自提等,以及相应的费用分摊方式和责任分担。
2. 确定交货日期:在询价文件中明确指定供应商应当在何时交付产品或服务,并说明是否接受提前或延期交付。
3. 要求供应商提供交货进度报告:要求供应商在交付过程中向采购方提供交货进度报告,以便及时掌握交货进度。
三、付款条件1.明确支付方式:询价文件中应明确规定支付方式,如电汇、支票、现金等,并提醒供应商提供相应的收款信息。
2.约定付款期限:设定付款期限,例如收到发票后15天内支付,并说明逾期付款的惩罚措施。
3.说明税费责任:明确支付过程中,采购方和供应商需要承担的税费责任。
四、质量要求1.指定质量验收标准和方法:在询价文件中具体描述产品或服务的质量标准和验收方法,包括抽样检验、检测要求等。
2.约定不符合质量标准的处理措施:明确规定如果供应商提供的产品或服务不符合质量标准,应采取何种处理措施,如退货、更换等。
3.要求供应商提供质量保证书:如果有特殊需求,可以要求供应商提供相应的质量保证书,以确保产品或服务的质量。
五、报价要求1.明确报价有效期:询价文件中应明确要求供应商提供报价的有效期,以保证价格不会在一段时间内变动。
2.要求报价明细:询价文件中要求供应商详细列出产品或服务的单价、总价、运费、税费等细节,方便采购方进行比较和选择。
IATF顾客特殊要求管理规定

IATF顾客特殊要求管理规定
1.顾客特殊要求的识别和理解:供应商需要确保能够识别和理解顾客
的特殊要求,这可能包括对产品质量、性能、可靠性等方面的要求。
供应
商需要与顾客密切合作,了解他们的要求,并确保在生产和服务过程中充
分遵守这些要求。
2.文件化和记录:供应商需要将顾客特殊要求进行适当的文件化和记录,并确保这些文件被所有相关人员充分理解和遵守。
这些文件可能包括
顾客要求的规范、标准和流程,供应商需要确保这些文件的准确性和及时
更新。
3.过程控制和改进:供应商需要建立有效的过程控制措施,确保能够
满足顾客的特殊要求。
这可能包括对关键过程的监控和测量,以确保产品
的质量和性能符合顾客的需求。
同时,供应商还需要及时识别和纠正任何
不符合的情况,并采取适当的改进措施。
4.培训和意识提升:供应商需要确保所有员工都被培训和意识提升,
以确保他们能够充分理解和遵守顾客的特殊要求。
培训内容可能包括顾客
的要求和标准、过程控制方法等,供应商需要确保培训的全面性和有效性。
5.风险管理:供应商需要对顾客特殊要求可能带来的风险进行有效管理,包括供应链风险、质量风险、交付风险等。
供应商需要建立有效的风
险评估和管理机制,确保能够及时识别和应对任何风险。
浅谈产品和过程的特殊特性

浅谈产品和过程的特殊特性特殊特性定义ISO/TS16949 : 2002第3.1.12条款对特殊特性给出了明确的定义:可能影响安全性或法规的符合性、产品的配合、功能、性能,或产品后续生产过程的产品特性或制造过程参数。
从上述定义可以看出,特殊特性可分为两大方面,一是与安全性或政府法规有关的特性,二是与安全性或政府法规无关的特性。
与安全性或政府法规有关的特性是指可能影响产品的安全性或政府法规的符合性的特性,如阻燃性、车内人员保护、转向、制动等车辆安全以及排放、噪声和防盗等方面的要求等,这些特性要求一般都是强制性的。
与安全性或政府法规无关的特性主要是指除安全或法规方面可能显著影响顾客对产品的满意度的特性,如产品性能、装配性和外观等。
具体来讲,特殊特性又可分为产品特殊特性和过程特殊特性。
产品的实现必然经过一定的过程,产品的特性必须通过特定的过程得以保证。
所以我们在实际工作当中,产品的特殊特性和过程的特殊特性通常是放在一起进行讨论的。
以注射成型塑料件为例,塑料件安装孔的位置属于产品的特殊特性,而塑料件成型的关键过程——注塑,即是决定安装孔位置的过程特殊特性。
这些特性一般都以量化形式来表现(见表)。
产品/过程特珠特性量化示例产品和过程特殊特性的重要性从特殊特性的定义可知,产品的特殊特性是一个产品区别于其他产品的非常关键的参数,这些参数直接影响到产品的安全性、性能、装配性及外观等。
所以从产品的设计开始到批量生产,产品和过程的特殊特性一直是顾客和企业对产品实现过程关注的焦点。
ISO/TS16949 : 2002第7.3.2.3特殊特性条款规定:组织必须识别特殊特性和-在控制计划中包含所有特殊特性,-与顾客规定的定义和符号相一致,和-识别过程控制文件,包括图样、FMEAs、控制计划及作业指导书,必须标明顾客的特殊特性符号或组织的特效符号或记号,以包括对特殊特性有影响的过程步骤。
由此可见,体系对特殊特性识别的要求是非常高的。
QS9000是什么

QS9000是什么QS9000是“QS9000质量体系要求”的简称。
1987年以前,美国三大汽车厂通用(General Motors)、福特(Ford)、戴姆勒—克莱斯勒(Daimler—Chrysler)分别发展了他们各自所期望的质量体系要求,以应用于供方质量体系和相关文件方面评鉴。
这些体系分别为克莱斯勒的《供方质量保证手册》(Supplier Quality Manual),福特的《Q—101质量体系标准》(Q101Quality System Standard)及通用的《北美创优目标》及采购物料通用质量标准(Targets for Excellence)&(General Quality Standard for Purchased Materials)。
三大汽车公司根据各自的质量体系要求对供应商实施质量控制,并根据各自的情况对供应商提出特殊要求,因此,这些要求在内容、术语、文件形式等方面存在差异。
而有些供应商可能是三大公司或其中两大公司共同的供应商,所以,这些供应商感受到对不同公司的不同要求难以同时满足,也造成了不必要的浪费。
如为了满足某公司的特殊要求,供应商不得不增加投入一些额外的资源。
供应商们纷纷要求三大公司能够有一个统一的标准。
1987年国际标准组织(ISO)颁布了ISO9000系列质量管理体系标准后,受其影响,三大汽车厂之采购及供应部门的副总裁们,于1988年成立特别工作小组,将参考手册、报告表格及技术用语命名予以标准化,因此发行了五本标准手册,并采用ISO9001:1987版之20项质量体系要素和加入三大汽车厂的特殊要求,形成了QS—9000标准,并于1994年8月颁布发行了第一版。
其后,由于IS09000标准于1994年改版,OS—9000随之采用ISO9001:1994版并于1995年2月颁布发行了第二版,而后1998年3月颁布发行了第三版,也是QS-9000的最终版本。
政府采购法颁布20周年知识竞赛有奖问答原题+答案

2022年政府采购法颁布20周年知识竞赛一、单选题(共25题,共50分)1、()可以根据采购项目的特殊要求,规定供应商的特定条件,但不得以不合理的条件对供应商实行差别待遇或者歧视待遇。
•A、财政部门•B、采购人•C、采购代理机构•D、评标委员会回答正确正确答案:B2、货物、服务公开招标采用综合评分法的,除执行国家统一定价标准和采用固定价格采购的项目外,服务项目的价格分值占总分值的比重不得低于()。
•A、0.1•B、0.2•C、0.3•D、0.4回答正确正确答案:A3、货物、服务公开招标采用综合评分法的,评标结果排列方法正确的是()。
•A、按投标报价由低到高顺序排列。
投标报价相同的,按评审后得分由高到低顺序排列。
•B、按投标报价由低到高顺序排列。
投标报价相同的,按评审后得分由低到高顺序排列。
•C、按评审后得分由高到低顺序排列。
得分相同的,按投标报价由高到低顺序排列。
•D、按评审后得分由高到低顺序排列。
得分相同的,按投标报价由低到高顺序排列。
回答正确正确答案:D4、根据法律、行政法规、规章关于提供招标文件的相关规定,下列选项错误的是()。
•A、招标文件提供期限自招标公告发布之日起计算不得少于5个工作日。
•B、资格预审文件提供期限自资格预审公告发布之日起计算不得少于5个工作日。
•C、提供期限届满后,获取招标文件的潜在投标人不足3家的,应当顺延提供期限,并予公告。
•D、公开招标进行资格预审的,招标文件应当向所有通过资格预审的供应商提供。
回答正确正确答案:C5、下列供应商中,依法可以参加政府采购活动的是()。
•A、某医疗设备经销商,上一年度因违法经营被吊销医疗器械经营许可证。
•B、某进口设备代理商,中标后因该进口设备涨价而放弃中标,被禁止在一年内参加政府采购活动,禁止期限尚未届满。
•C、某会计师事务所因出具的审计报告存在虚假记载,被处以260万元罚款,处罚日期距今尚不满3年。
•D、某印刷企业因生产过程中违反环境保护法规,被处以20万元罚款。
检验规范通用要求

一、关于检验通用规范的规定1、目的:确保供应商供应的产品质量符合我公司以及国家标准规定的要求。
我公司生产的产品满足客户要求并符合国家、国际及地区的法律法规;2、范围:公司所有产品的采购、生产、转运、储存、包装、发货的通用要求。
本公司的所有检验人员以及与产品质量有关的其他人员;3、通用检验规范公司所有产品(原材料,半成品,成品)原则上均需执行抽样检验,合格品才能入库或出货检验员以满足客户需求为宗旨,对每一批来料入库或出货执行下述项目之检验:包装、标签、数量、型号等项目的核对产品规格(外观、结构、装配、电气性能、安全规定)做选择性或必要性之检验。
(1)若客户有特殊要求,则按客户要求检验(2)若产品出货到有ROHS要求国家或地区,其来料产品或出货产品要求能满足ROHS要求抽样计划一般特性采用,均以GB2828-2003单次正常随机抽样一般检验水平Ⅱ;特殊特性采用,均以GB2828-2003单次正常随机抽样特殊S-2水准;AQL值:CR(致命缺陷): 0 MA(重要缺陷): MI(次要缺陷):定义:CR(致命缺陷):指产品存在可能对生产者或使用者造成人身意外伤害或可能造成客户抱怨之财产损失、违反法律法规及环境规定。
(安全/绿色环保等)MA(重要缺陷):产品某一特性为满足规定要求(结构或功能)或严重外观缺陷。
MI(次要缺陷):产品存在一些不影响功能与使用性的缺陷(一般指外观小瑕疵)。
检验项目大致可区分为:a.外观检验b.尺寸、结构性检验c.电气特性检验d.化学特性检验e.物理特性检验检验方法大致可区分为:a.外观检验:一般用目视、手感、限度样本。
b.尺寸检验:如游标卡尺、量表。
c.结构性检验:如拉力计、扭力计。
d.特性检验:使用检测仪器或设备(如万用表、电容表、试剂、试验机等)。
检验分类:产品(原材料,半成品,成品)因供料厂商的品质信赖度,公司生产熟练度及物料的数量、单价、体积等区分为全检、抽检、免检。
全检:数量少,单价高;抽检:数量多,或经常性之物料;免检:数量多,单价低,或一般性补助或局限性之物料。
16949标准 八项原则
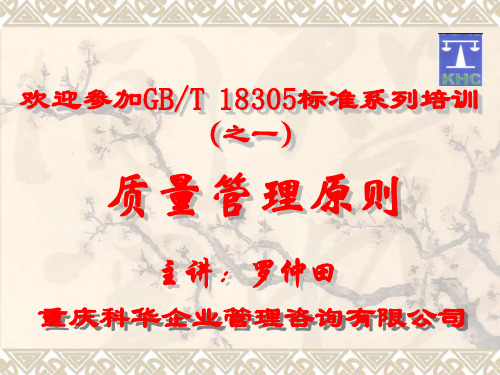
科华咨询
14
GB/T 18305-2003标准培训之一
基本概念
建立质量管理体系应注意的问题
—— 转变观念
先看一些现象: 注重形式、忽略本质 有证书、无体系
有能力开发新产品、批量生产质量不稳定
将标准的要求融入正常运行的体系,不要在此 之外另加一个“符合标准要求”的体系。 学会开车
2008年7月23日
2008年7月23日
科华咨询
20
GB/T 18305-2003标准培训之一
八项原则 各级人 员是组织之 本。只有他 们的充分参 与,才能使 他们的才干 为组织带来 收益。
一、以顾客为关注焦点 二、领导作用
三、全员参与
四、过程方法 五、管理的系统方法 六、持续改进 七、基于事实的决策方法 八、与供方互利的关系
“质量从设计抓起!”
科华咨询
2008年7月23日
4
GB/T 18305-2003标准培训之一
基本概念
要求 ——
明示的、通常隐含的或必须履行的需求或期 望。(ISO 9001 3.1.2)
—— 谁的要求?
质量应当满足顾客和其他相关方的要求
“顾客”是: “接受产品的组织或个人” ( GB/T 19000-2000 3.3.5 条)
2008年7月23日
科华咨询
16
GB/T 18305-2003标准培训之一
—— 员工理解
基本概念
将道理告诉员工,让其理解,可能比简单的命令 和处罚更有效。
2008年7月23日3标准培训之一 一、以顾客为关注焦点 二、领导作用 三、全员参与
八项原则
1、信仰这八项原则应成为实施 TS16949的前题
固有特性—— 某事或某物中本来就有的, 尤其是那种永久的特性。 固有特性是质量的载体。
通用对供应商特殊要求

分享
45 2.5.17 库存周转期 2.5.18 年增长率是否达到环比增长 2.5.19 流动资金状况
46 三、采购定点
3.1 评审准则 3.2 评审状态(通知对方) 3.3 确定试点原则(优选)
3.1 评审准则 47 3.1.1 风险度构成
● 制造风险度 ● 质量风险度 ● 技术风险度 ● 服务风险度 ● 价格风险度
本课程内容
6 ● 鉴于大家关注如何成为 GM 合格供应商,
因此仅介绍前八步。
● 鉴于课程安排限制,本课程重点介绍 PA/PSA,
其它六步粗略介绍。
PA/PSA 评审要点(计 38 条)
7 一、PA 的评审要点( ) 1.1 人员(9 条) 1.2 生产(12 条) 1.3 商务(7 条) 1.4 物流(9 条) 1.5 售后件(1 条)
39 2.4.12 全员培训程序及其效果评价 2.4.13 内、外部语言障碍的处置 2.4.14 额外运费发生数据 2.4.15 额外运费处理流程 2.4.16 交付绩效
41 2.5 价格能力评估 2.5.1 公司性质(私/公/股份) 2.5.2 是否合资 2.5.3 工会组织与劳工权利 2.5.4 公司财务状况
正式批准/持续改进 成效监控 5 问题报告和解决 PRR 一级受控发运 二级受控发运 质量研讨 供应商改进会议 除名后再进行全球采购
通用(以下用 GM)对潜在 供应商评审步骤
4 正式批准 SORP
初期生产次品遏制 产能评估/验证 PPAP 样件审批/评估 APQP 采购定点(试点组织确定) PA/PSA
53 4.3 GM 的特殊要求
4.3.5 根据详细的风险评估,对弱点活动的改进,
54
降低风险。
4.3.1 强调了与各供应商在 APQP 过程中
关于对供应商的检验要求1

关于对供应商的检验要求
为了保证外购成品的质量,提高公司的质量声誉,现对供应商提出以下要求:
1、供应商加工产品必须严格按图纸要求来加工。
如有特殊要求,要根据现场实际来加工的产品,图纸必须有现场负责人和我公司签字认可后方可加工。
在加工过程中,如有改动部分,必须有书面材料并有责任人签字方可更改。
如未按照以上程序执行,造成的损失由供应商承担。
2、产品材质必须严格按照供应商提供的样品为标准,不允许加工过程中以次充好。
如有发现,一切损失由供应商承担,同时根据问题的严重性,来进行必要的处罚。
3、供应商加工好的成品,发货前必须做好包装处理,对易碎易损伤产品要特殊包装,保证产品到货后的完美。
如在运输过程中出现的任何损伤由供应商自行承担一切损失,供应商产品直接送往工地的,要与工地负责人签订接收单,双方签字确认产品的质量,如没有签收手续,一切后果由供应商承担。
质检部。
上海通用汽车对供应商质量要求的规定

SGM SQ SOR
➢ 所有向SGM直接提供 a)生产材料,b)生产或服务件,或c)热处理、涂 镀、油漆或其他加工服务的供应商必须通过ISO/TS 16949 标准的认证, 并且取得相应证书。
➢ 须根据AIAG发布的CQI-9,CQI-11, CQI-12评估热处理、电镀、油漆 过程的有效性。
➢ 供应商如果没有通过ISO/TS 16949认证,供应商在报价时必须包括通 过认证的计划。
➢ 质量数据:如SGM要求,供应商必须提供相关的质量数据(例如历史检验数据,一次 合格率,废品率) 。这些数据可能在SGM制造厂或总装厂在确定质量问题的趋势和根 本原因时需要用到。
SDE Module
SGM Confidential
14
一、SGM供应商质量声明
一级供应商职责
SGM SQ SOR
➢ 除非供应商质量总监批准,供应商负责对所有的装配零件包括指定分供方 的零件坚持执行AIAG and SGM的要求。
SGM Confidential
19
四、对Consignment供应商的特殊补充要求SGM SQ SOR
Consignment供应商应建立尺寸评估流程,在新项目开发阶段,按照尺寸 评估流程并根据产品的CVIS\DTS,对整个总成进行匹配、功能验证,并 进行问题初步分析和判定,将匹配、功能信息及时传递给SGM SQE和PE, 协助完成前期质量和功能问题的评估和解决。
特性ppap要求量产kpcxpk167xp167完全批准xpk167xp167完全批准xpk133xp167可接受xpk133可接受pqcxp167xpk10完全批准xp133xpk10可接受需满足规范要求标准特性抽取一个样本检查须满足规范要求需满足规范要求四对对consignment供应商的特殊补充要求sgmsqsorsgmconfidential20sdemodule?consignment供应商应建立尺寸评估流程在新项目开发阶段按照尺寸评估流程并根据产品的cvisdts对整个总成进行匹配功能验证并进行问题初步分析和判定将匹配功能信息及时传递给sgmsqe和pe协助完成前期质量和功能问题的评估和解决
供方特批理由

供方特批理由一、引言供方特批是指在采购过程中,为了满足特殊需求或解决特定问题,对供应商提出的特殊要求进行审批的过程。
供方特批的目的是确保采购过程的合规性和有效性,同时也是对供应商能力和信誉的一种考察。
二、背景在采购过程中,供应商通常需要按照采购方提供的规范进行投标。
然而,有些情况下,采购方的规范无法满足特殊需求或存在一定的局限性,这时就需要通过供方特批来解决问题。
三、供方特批的作用1. 解决特殊需求:供方特批可以允许供应商根据实际情况进行某些特殊要求的调整或变更,以满足采购方的特殊需求。
比如,在某些特定场合下,采购方可能需要供应商提供一定数量的产品或服务,但规范中并未明确要求,这时就可以通过供方特批来解决。
2. 确保合规性:采购过程中,供应商需要按照采购方提供的规范进行投标,但有时由于技术或其他因素,供应商无法满足所有的规范要求。
通过供方特批,采购方可以对供应商提出的特殊要求进行审批,确保供应商在特定情况下的合规性。
3. 评估供应商能力:供方特批也是对供应商能力和信誉的一种考察。
通过对供应商提出的特殊要求进行审批,采购方可以评估供应商在解决特殊问题时的能力和灵活性,从而更加准确地评估供应商的综合实力。
四、供方特批的流程1. 提出申请:供应商在发现无法满足采购方规范要求或遇到特殊情况时,可以向采购方提出供方特批申请。
申请需要包括详细的解释和理由,以及可能的解决方案。
2. 内部审批:采购方内部会对供方特批申请进行审查和评估。
审批人员会根据申请的合理性、可行性和风险等因素进行综合考虑,并做出相应的决策。
3. 与供应商协商:如果供方特批申请获得通过,采购方会与供应商进行进一步的协商和沟通,以确定具体的解决方案。
双方需要就价格、交付时间、质量标准等进行协商,并最终达成一致。
4. 签署协议:在确定解决方案后,采购方和供应商会签署供方特批协议,明确双方的权责和约定事项。
五、供方特批的注意事项1. 合理性和可行性:供方特批申请需要具备合理性和可行性,不能过于主观或片面。
- 1、下载文档前请自行甄别文档内容的完整性,平台不提供额外的编辑、内容补充、找答案等附加服务。
- 2、"仅部分预览"的文档,不可在线预览部分如存在完整性等问题,可反馈申请退款(可完整预览的文档不适用该条件!)。
- 3、如文档侵犯您的权益,请联系客服反馈,我们会尽快为您处理(人工客服工作时间:9:00-18:30)。
正式批准/持续改进 成效监控 5 问题报告和解决 PRR 一级受控发运 二级受控发运 质量研讨 供应商改进会议 除名后再进行全球采购
通用(以下用 GM)对潜在 供应商评审步骤
4 正式批准 SORP
初期生产次品遏制 产能评估/验证 PPAP 样件审批/评估 APQP 采购定点(试点组织确定) PA/PSA
40 2.4.17 内部 PPM 2.4.18 零件防护措施 2.4.19 原型样件制造能力 2.4.20 供应商是否具有 SLA/SLS (激光成型/脉冲成型)技术 2.4.21 法律诉讼是否曾发生? 2.4.22 法律处罚数据
42 2.5.5 对分供方的付款期限和条件 2.5.6 领导管理层对财务绩效的评审 2.5.7 工程更改后的报价响应 2.5.8 产能计划与分供方供货能力的适合度 2.5.9 与分供方的售后配件协议
二、PSA 评审要点(计 134 条)
8
2.1 制造能力评估(34 条)
2.2 质量能力评估(27 条)
2.3 技术/开发能力评估(22 条)
2.4 服务能力评估(22 条)
2.5 价格(经济)评估(19 条)
1.1 人员
9 ● 组织机构和分工(高层/部门设置) 1.11 质量人员素质(数量/资历/经验) 1.12 技术人员素质(数量/资历/经验) 1.13 研发人员素质(数量/资历/经验)
30 2.2.21 对 AIAG 要求的理解水平 2.2.22 产品是否有出口 2.2.23 员工参与机制(激励) 2.2.24 激励程序的实施及其有效性 2.2.25 员工成果的认可
31 2.2.26 内部沟通(应用等) 2.2.27 关注体育竞赛等员工业余生活 (野餐、公益活动)
32 2.3 技术能力评估 2.3.1 有无工程支持 2.3.2 工程和制造是否在同一区域 2.3.3 参与研发 GM 的能力
● 其它部分如:质量体系/认证 PPAP,实验室 等不予介绍
(大家可在 GM 公开网站查阅)
51
4.1 APQP 基本要求
● 满足 AIAG 和通用发布的参考手册的要求 ● 认真组织实施 ● 定期评估
4.2 APQP 基本步骤
52 4.2.1 定点前活动
4.2.2 计划与定义项目 4.2.3 产品设计和开发 4.2.4 过程设计和开发 4.2.5 成品和过程确认 4.2.6 返馈、跟踪和改进
24 2.1.25 设备维护的资源配置 2.1.26 预见性/预防性维护系统 2.1.27 备品备件 2.1.28 工装/量具的设计能力 2.1.29 工装/量具的制造能力
25 2.1.30 工装/量具的改进能力 2.1.31 工装/量具的维护能力 2.1.32 预见性/预防性工装维护系统 2.1.33 工装的备品备件 2.1.34 公共设施以及应急计划
1.14 员工素质(数量/技能) 10 1.1.5 员工平均工龄(经验)
1.16ห้องสมุดไป่ตู้员工流动(百分比) 1.1.7 工会组织 1.1.8 班次(有效工作天数) 1.1.9 人力资源的改善能力
1.2 生产能力
11 1.2.1 工厂面积 1.2.2 产能利用率(%) 1.2.3 增加人力对产能利用率影响(%) 1.2.4 报价业务占产能比率(%) 1.2.5 有无产能增加计划
分享
45 2.5.17 库存周转期 2.5.18 年增长率是否达到环比增长 2.5.19 流动资金状况
46 三、采购定点
3.1 评审准则 3.2 评审状态(通知对方) 3.3 确定试点原则(优选)
3.1 评审准则 47 3.1.1 风险度构成
● 制造风险度 ● 质量风险度 ● 技术风险度 ● 服务风险度 ● 价格风险度
2.2 质量能力的评估 26 2.2.1 过程流(流程图/路线设置的效率)
2.2.2 安全库存(应急计划的一部分) 2.2.3 过程验证(作业准备的验证)
27 2.2.4 产品标识与可追溯性 2.2.5 对一级供应商的管理能力 2.2.6 工程更改能否影响整个供应链 2.2.7 内部审核能力 2.2.8 对分供方的审核能力 2.2.9 整个供应链的不合格品控制能力
2.1.11 实验/设备的标定能力 21 2.1.12 作业测量环境
2.1.13 人机工程 2.1.14 5S 管理 2.1.15 现场物品的管理状况
22 2.1.16 个人安全防护 2.1.17 安全/健康的培训 2.1.18 安全审核实施状况 2.1.19 安全风险评估 2.1.20 应急预案
23 2.1.21 安全事故的管理 2.1.22 安全作业的评估 2.1.23 行政部门批评 2.1.24 五年内的安全重大事故率
35 2.3.13 设计变更控制 2.3.14 技术伙伴 2.3.15 开发周期(18 个月) 2.3.16 电子数据传输能力 2.3.17 电子数据传输是否适应 GM 要求
36 2.3.18 连接方式(宽带/非对称的/拨号) 2.3.19 是否知晓 GMW3059 程序(危险物 料的控制)
2.3.20 设计验证计划与实施 2.3.21 性能试验 2.3.22 设计数据库
12 1.2.6 未来五年的产能利用率 1.2.7 标准的产品周期时间
● 从定点(试点)到 PPAP 的周期时间
● 从接到订单到产品发运的周期时间
1.2.8 工厂目前的 PPM 内、外部出现的所有不合格数占百万分比
1.2.9 能否达到 GM 最低贮存要求 13 1.2.10 工装设计能力
1.2.11 工装维护能力 1.2.12 工装制造能力
48 3.2 评审状态
● 风险度可接受状态 ● 风险度改进后接受状态 ● 不接受状态
49 3.3 试点组织的确定
● 排序法则(优选) ● 进入接受状态的潜在供方数量不足时 ● 则考虑改进后可接受的供应商 ● 最后选择一家或者多家进入下一轮评审
4.GM 对供应商的特殊要求 50 ● 重点介绍 APQP 部分
2.2.10 来料处理系统(标识/验证/文档等) 28 2.2.11 在制品的识别方法(标识与可追溯性)
2.2.12 PFMEA 的应用水平 2.2.13 控制计划实施有效性 2.2.14 设计记录中的相关文件的一致性 2.2.15 更改状态的识别系统
29 2.2.16 检验计划 2.2.17 MSA 的实施 2.2.18 暗灯系统及其应用 2.2.19 SPC 的应用 2.2.20 整车厂配套经验
本课程内容
6 ● 鉴于大家关注如何成为 GM 合格供应商,
因此仅介绍前八步。
● 鉴于课程安排限制,本课程重点介绍 PA/PSA,
其它六步粗略介绍。
PA/PSA 评审要点(计 38 条)
7 一、PA 的评审要点( ) 1.1 人员(9 条) 1.2 生产(12 条) 1.3 商务(7 条) 1.4 物流(9 条) 1.5 售后件(1 条)
4.3.13 项目评审增加可追溯要求
4.3.14 与 GM 双向沟通的详细清单
其它内容如 PPAP 等略 谢 谢 大 家!
杨州振权质量管理顾问有限公司
2.3.4 CAD/CAE 的配置与应用能力 33 2.3.5 设计验证能力
2.3.6 UG 的能力
2.3.7 设计评估工具的应用
34 2.3.8 DFMEA 的知识和应用 2.3.9 设计的基准研究 2.3.10 设计计划中的设计评审活动的实施 2.3.11 领导参与的设计评审 2.3.12 设计评审和批准
37 2.4 服务 2.4.1 产品的生产经验 2.4.2 为整车厂配套级别 2.4.3 PPM 跟踪能力 2.4.4 顾客呼声的内部动作
38 2.4.5 研究关注问题的解决能力 2.4.6 内部沟通网络机制 2.4.7 产品变更程序及其实施 2.4.8 项目小组的管理流程 2.4.9 包装、运输能力
2.1.2 过程物流的类型(流动水平)
2.1.3 作业指导书(信息的完整性、易理解)
2.1.4 现场文件(易于得到)
2.1.5 操作工培训组织(管理) 2.1.6 工艺贯彻率的监控 2.1.7 产能分析(基于实际数据) 2.1.8 接受新业务能力(是否需要增添资源) 2.1.9 过程能力和性能 2.1.10 实验能力(3/8/24)
4.3.3 增加了供应商质量 SOR
制造能力和生产能力进行评估并对通用作
4.4.4 提交“质量信息”和质量计划
出书面承诺。
4.3.9 项目各阶段的详细核查表或指导文 56
55
件
4.3.10 数据库的充份利用
4.3.11 分供方的 APQP 要求
4.3.12 对 PFMEA 中的严重度,不可探测
度,频度定义更加明确
39 2.4.12 全员培训程序及其效果评价 2.4.13 内、外部语言障碍的处置 2.4.14 额外运费发生数据 2.4.15 额外运费处理流程 2.4.16 交付绩效
41 2.5 价格能力评估 2.5.1 公司性质(私/公/股份) 2.5.2 是否合资 2.5.3 工会组织与劳工权利 2.5.4 公司财务状况
1.4.3 如何发货
1.4.4 为装配厂提供排序产品
17 1.4.5 额外运费 1.4.6 电子数据的传输能力 1.4.7 库存管理系统 1.4.8 半成品库存量
18 1.5 售后件 1.5.1 有无直接供货给经销商的能力
19 二、正式评审(PSA)
20
2.1 制造能力评估
2.1.1 在制品的处理方式(防护、标识等)
1.3 商务 14 1.3.1 报价所需时间
1.3.2 产品类型 1.3.3 外部生产基地(报价产品)
15 1.3.4 法律诉讼情况 1.3.5 两年内的法律判决书(有/无) 1.3.6 法律处罚(有/无) 1.3.7 产权变更情况(有/无)
1.4 物流 16 1.4.1 有无产品出口