储罐组装施工措施方案(内浮顶液压顶升)-通用模版
(整理)内浮顶储罐施工方案
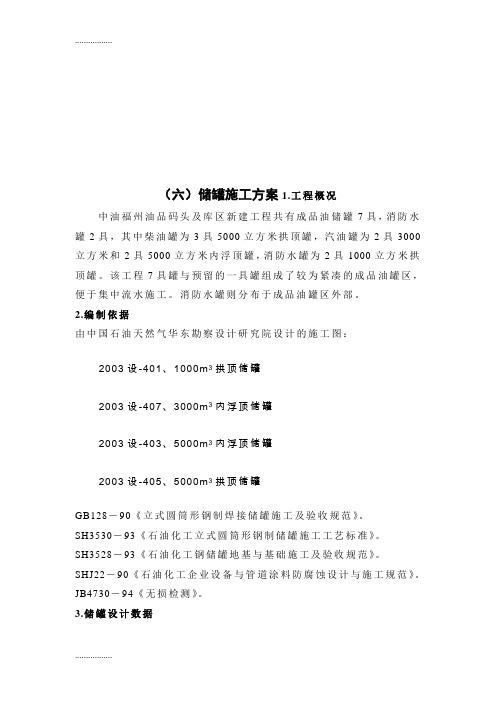
(六)储罐施工方案1.工程概况中油福州油品码头及库区新建工程共有成品油储罐7具,消防水罐2具,其中柴油罐为3具5000立方米拱顶罐,汽油罐为2具3000立方米和2具5000立方米内浮顶罐,消防水罐为2具1000立方米拱顶罐。
该工程7具罐与预留的一具罐组成了较为紧凑的成品油罐区,便于集中流水施工。
消防水罐则分布于成品油罐区外部。
2.编制依据由中国石油天然气华东勘察设计研究院设计的施工图:2003设-401、1000m3拱顶储罐2003设-407、3000m3内浮顶储罐2003设-403、5000m3内浮顶储罐2003设-405、5000m3拱顶储罐GB128-90《立式圆筒形钢制焊接储罐施工及验收规范》。
SH3530-93《石油化工立式圆筒形钢制储罐施工工艺标准》。
SH3528-93《石油化工钢储罐地基与基础施工及验收规范》。
SHJ22-90《石油化工企业设备与管道涂料防腐蚀设计与施工规范》。
JB4730-94《无损检测》。
3.储罐设计数据4.罐体数据(1)1000立方米拱顶罐罐体数据一览表:(单具总重28850Kg)(2)3000立方米内浮顶罐罐体数据一览表:(单具总重76797Kg)(3)5000立方米拱顶罐、内浮顶罐罐体数据一览表:(单具总重119731Kg)5.施工方法5.1施工方法采用群桅起升倒装法:5.2施工用料:每个罐所需倒链和桅杆如下表所示:5.3材料验收储罐所选用的材料和附件,应具有质量合格证明书当无质量合格证明书或质量合格说明书有疑问时,应对材料和附件进行复验。
储罐焊条选用J422、J427电焊条,焊条应具有质量合格说明书。
储罐所选用的钢板,必须逐张进行外观检查,其表面质量应符合现行的相应钢板标准的规定。
钢板表面锈蚀减薄量,划痕深度与钢板实际偏差之和,应符合下表规定。
5.4预制5.4.1罐底预制(1)罐底板预制前应根据实际来料绘制排版图。
并根据图纸放大样,检查无误后方可下料。
(2)罐底的排版直径,宜按设计直径放大0.1-0.2%。
储罐组装施工措施方案(内浮顶液压顶升)-通用模版

储罐组装施工措施(适用于内浮顶罐、液压顶升倒装施工)2.1 储罐新建工程量简介新建10000m3拱顶罐2座,储存介质为柴油,钢板厚度有6mm、8mm、10mm、12mm 和14mm五种,材质有Q235-B和16MnR两种,包边角钢为∟125×10,共9圈壁板。
罐体内直径为30m,总高度为19.341m,总重量为222.83t。
2.2 施工工艺流程本工程10000m3拱顶罐拟采用液压顶升倒装工艺法,施工工序如下:2.3 10000m3罐施工措施2.3.1 原材料检验⑴原材料检验:板材及型钢符合设计要求,•人孔、透光孔、通气孔、清扫孔等外购件出厂合格资料齐全。
⑵制造储罐所用的钢板必须逐张进行外观检查,其表面质量应符合GB6654-1996《压力容器用钢板》的规定。
对钢板表面的锈蚀减薄量、划痕深度与钢板实际负偏差之和,当钢板厚度为6~7mm时,允许偏差为-0.6mm;当钢板厚度为8~25mm时,允许偏差为-0.8mm。
⑶所有工程用钢材、半成品、配件、焊材均应按规格、材质分别堆放,下部垫平填实,防止变形损坏,并做好明显标记。
⑷经检验合格的材料,应设专人管理,按限额领料单发放。
对不合格的材料,严禁在工程中使用。
2.3.2 储罐的预制⑴一般规定:① 储罐在预制、组装及检验过程中所使用的样板应符合下列规定:a . 当构件的曲率半径小于或等于12.5m 时,弧形样板的弦长不得小于1.5m ;当曲率半径大于12.5m 时,弧形样板的弦长不得小于2m 。
b . 直线样板的长度不得小于1m 。
c . 测量焊缝角变形的弧形样板,其弦长不得小于1m 。
② 钢板的切割和焊缝的坡口,宜采用机械加工或自动、半自动火焰切割加工;罐顶板和罐底板边缘板的园弧边缘,可采用手工火焰切割加工。
③ 钢板边缘加工面应平滑,不得有夹渣、分层、裂纹及熔渣等缺陷。
火焰切割坡口产生的表面硬化层应磨除。
④ 所有预制构件在保管、运输及现场堆放时,应采取有效措施防止变形、损伤和锈蚀。
内浮顶罐施工方案

内浮顶罐施工方案内浮顶罐是一种常用于储存液体的容器,其内浮顶设计可以有效减少液体与空气之间的接触,从而减少蒸发和氧化的可能性。
内浮顶罐施工是一个非常重要的环节,直接影响到罐体的使用效果和安全性。
下面将介绍内浮顶罐的施工方案。
1. 施工前准备工作在进行内浮顶罐的施工前,需要完成以下准备工作:•确定罐体的设计图纸和规格要求;•准备施工所需的材料和工具,包括焊接设备、起重机械等;•对施工现场进行安全检查,确保施工环境符合要求。
2. 罐体组装首先,需要进行罐体的组装工作。
根据设计图纸,将罐体的各个部件进行组装,在组装过程中要确保各部件的连接牢固。
组装完成后,进行外观检查和质量检验,确保罐体符合要求。
3. 焊接工作完成罐体组装后,需要进行焊接工作。
在进行焊接前,首先要对焊接工艺进行检查和确认,选择适合的焊接方法。
然后进行焊接操作,确保焊接接头牢固,焊缝平整。
4. 漏检和压力测试在罐体焊接完成后,需要进行漏检和压力测试。
漏检是为了检查焊接接头是否存在漏洞,需要使用相应的检测设备进行检查。
压力测试是为了检查罐体是否能够承受设计压力,确保罐体安全可靠。
5. 内浮顶安装最后,进行内浮顶的安装工作。
根据设计要求,安装内浮顶及相关设备,需要确保内浮顶安装牢固,能够灵活运作。
安装完成后,进行功能测试,确保内浮顶正常运转。
结语内浮顶罐施工是一个复杂的工程,需要严格按照设计要求和工艺流程来进行。
只有做好施工准备工作,认真进行各项施工工作,才能确保内浮顶罐的质量和安全性。
希望以上介绍的施工方案能够对相关从业人员提供帮助。
内浮顶储罐施工方案

(六)储罐施工方案1.工程概况中油福州油品码头及库区新建工程共有成品油储罐7具,消防水罐2具,其中柴油罐为3具5000立方米拱顶罐,汽油罐为2具3000立方米和2具5000立方米内浮顶罐,消防水罐为2具1000立方米拱顶罐。
该工程7具罐与预留的一具罐组成了较为紧凑的成品油罐区,便于集中流水施工。
消防水罐则分布于成品油罐区外部。
2.编制依据由中国石油天然气华东勘察设计研究院设计的施工图:2003设-401、1000m拱顶储罐32003设-407、3000m内浮顶储罐32003设-403、5000m内浮顶储罐32003设-405、5000m拱顶储罐3GB128-90《立式圆筒形钢制焊接储罐施工及验收规范》。
SH3530-93《石油化工立式圆筒形钢制储罐施工工艺标准》。
SH3528-93《石油化工钢储罐地基与基础施工及验收规范》。
SHJ22-90《石油化工企业设备与管道涂料防腐蚀设计与施工规范》。
JB4730-94《无损检测》。
据数计设罐储3.)T-301-01~Q235-A21300215.848172T-301-03~2Q235-A500419.817.863T-301-05~3Q235-A500罐719.817.8642Q235-A100罐2-1/11.513.18)4.罐体数据(1)1000立方米拱顶罐罐体数据一览表:(单具总重28850Kg)K量3933Q235-A6000 ××7罐1壁板板1钢2000 )一(16855罐2壁板2000×板钢56Q235-A×6000)二(168 1 3 =6 顶心板板钢δQ235-A 中46404 皮瓜板板钢16 δQ235-A=6Q235-A.F ×75×钢9 角758 326 钢边5 包角Q235-A 10 δ板9 钢=5 板6 垫6800Q235-A=7δ板钢1板底75.施工方法5.1施工方法采用群桅起升倒装法:5.2施工用料:每个罐所需倒链和桅杆如下表所示:3 5000mφ325×8,L=4000mm,22个3 1000m10T 8个倒手动3 3000m10T 16个链3 5000m10T 22个材5.3料验收合当量无质证合质,料选罐储所用的材和附件应具有量格明书进附料材和件行复验。
整理3万立内浮顶储罐制作安装方案
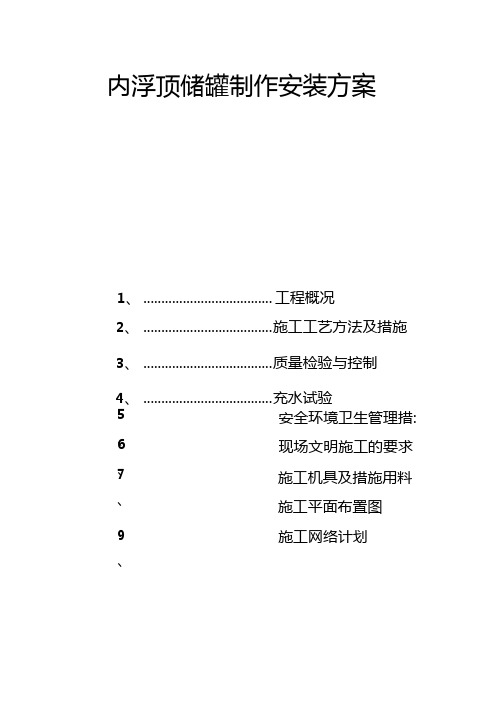
内浮顶储罐制作安装方案1、 .................................... 工程概况2、 .................................... 施工工艺方法及措施3、 .................................... 质量检验与控制4、 .................................... 充水试验5、 安全环境卫生管理措:6、 现场文明施工的要求7、施工机具及措施用料 施工平面布置图 9、施工网络计划1、工程概况Xxxxxxxxx工程,我单位承建公用工程其中两台3万立方米内浮顶储罐制作安装, 该工程工期紧、任务重,必须严格执行方案,才可优质高效完成施工任务。
1、1 30000 m3单盘内浮顶储罐技术参数1、1、1公称容积30000m31、1、2贮罐内径44000mm1、1、3罐壁高度22000mm1、1、4贮罐质量(含顶板、网壳)710100kg1、1、5贮罐本体材质16MnR1、2储罐制造、安装、试验及验收标准1、2、1 30000 m'单盘内浮顶储罐施工图1、2、2 GBJ128-90《立式圆筒型钢制焊接油罐施工及验收规范》1、2、3 SH3530-93《石油化工立式圆筒型钢制储罐施工工艺标准》1、2、5 JB4708-92《钢制压力容器焊接工艺评定》1、2、6 JB/T4709-92《钢制压力容器焊接规程》1、2、7 JB4730-94《压力容器无损检测》1、2、8 GB50205-2002《钢结构工程施工及验收规范》2、施工工艺方法及技术措施本工程主要采用液压提升倒装法进行施工。
2.1机械提升倒装法简介机械提升倒装分为中心柱提升倒装法及导链提升倒装法。
即在罐内设中心柱及伞架或罐内设小立柱,挂导链利用中心柱上起吊滑轮或手动葫芦(导链)作为动力,将贮罐提升,逐片组对焊接,此方法施工简便、安全,但劳动强度大,只能用于容积小于2000m3贮罐施工,由于本工程为30000m3贮罐,所以完全可以釆用液压顶升倒装法施工。
大型储罐内浮盘安装施工方案
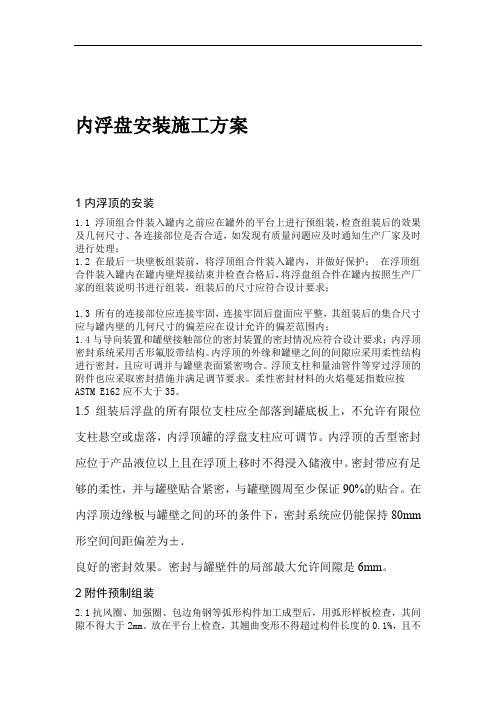
内浮盘安装施工方案1内浮顶的安装1.1 浮顶组合件装入罐内之前应在罐外的平台上进行预组装,检查组装后的效果及几何尺寸、各连接部位是否合适,如发现有质量问题应及时通知生产厂家及时进行处理;1.2 在最后一块壁板组装前,将浮顶组合件装入罐内,并做好保护;在浮顶组合件装入罐内在罐内壁焊接结束并检查合格后,将浮盘组合件在罐内按照生产厂家的组装说明书进行组装,组装后的尺寸应符合设计要求;1.3 所有的连接部位应连接牢固,连接牢固后盘面应平整,其组装后的集合尺寸应与罐内壁的几何尺寸的偏差应在设计允许的偏差范围内;1.4与导向装置和罐壁接触部位的密封装置的密封情况应符合设计要求;内浮顶密封系统采用舌形氟胶带结构。
内浮顶的外缘和罐壁之间的间隙应采用柔性结构进行密封,且应可调并与罐壁表面紧密吻合。
浮顶支柱和量油管件等穿过浮顶的附件也应采取密封措施并满足调节要求。
柔性密封材料的火焰蔓延指数应按ASTM E162应不大于35。
1.5 组装后浮盘的所有限位支柱应全部落到罐底板上,不允许有限位支柱悬空或虚落,内浮顶罐的浮盘支柱应可调节。
内浮顶的舌型密封应位于产品液位以上且在浮顶上移时不得浸入储液中。
密封带应有足够的柔性,并与罐壁贴合紧密,与罐壁圆周至少保证90%的贴合。
在内浮顶边缘板与罐壁之间的环的条件下,密封系统应仍能保持80mm形空间间距偏差为±.良好的密封效果。
密封与罐壁件的局部最大允许间隙是6mm。
2附件预制组装2.1抗风圈、加强圈、包边角钢等弧形构件加工成型后,用弧形样板检查,其间隙不得大于2mm。
放在平台上检查,其翘曲变形不得超过构件长度的0.1%,且不得大于4mm。
2.2 热煨成型的构件,不得有过烧、变质现象。
其厚度减薄量不应超过1mm。
2.3罐体的开孔接管,应符合下列要求:2.3.1、开孔接管的中心位置偏差,不得大于10mm;按管外伸长度的允许偏差应为±5mm。
2.3.2、开孔补强板的曲率,应与罐体曲率一致;2.3.3、开孔接管法兰的密封面应平整,不得有焊瘤和划痕,法兰的密封面应与接管的轴线垂直,倾斜不应大于法兰外径的1%,且不得大于3mm,法兰的螺栓孔,应跨中安装。
浮仓内浮顶贮罐施工方案

浮仓内浮顶贮罐施工方案一、前言浮仓(浮式屋顶)内浮顶贮罐是一种常见的储罐形式,广泛应用于石油、化工、食品、饮料等行业。
本文将详细介绍浮仓内浮顶贮罐的施工方案。
二、施工准备工作1.施工组织设计:根据具体施工情况,制定施工组织设计方案,明确负责人和施工人员的职责。
2.打样审批:根据设计图纸和规范要求,制作浮式屋顶和浮顶,进行样板审批。
3.施工图纸和材料准备:根据设计要求,制定施工图纸,并准备好所需材料,如钢材、焊材、涂料等。
4.原材料检验:对所购买的原材料进行检验,确保其质量符合要求。
5.施工设备准备:准备好所需施工设备和机具,如起重机、电动焊机、气瓶等。
6.现场布置:对施工现场进行布置,划定区域,确保施工安全和顺利进行。
三、施工步骤1.钢结构制作:根据设计图纸,制作浮式屋顶的钢结构。
包括制作顶拱构件、校正并焊接顶拱,制作安装导轨等。
2.钢结构安装:将制作好的钢结构进行现场安装,按照设计要求进行组装,并进行调整和校正,确保各构件的精度和平整度。
3.焊接工艺:根据焊接工艺规程,进行钢结构的焊接。
确保焊缝的质量和可靠性。
4.涂装防腐:对已焊接好的钢结构进行涂装和防腐处理,保护其免受腐蚀和氧化。
选用耐酸碱的涂料,确保涂装层的质量。
5.安装浮顶:将制作好的浮顶安装在钢结构之上,并进行调整和校正,确保浮顶与钢结构的接触紧密、平整度良好。
6.导轨安装:安装导轨,确保浮顶的顺畅移动。
7.测量调整:对浮顶进行测量和调整,确保其水平度和平整度满足要求。
8.清洁挂钩:安装清洁挂钩,方便后续清洁维护工作。
9.试运行:对浮仓内浮顶贮罐进行试运行,检查其运行是否正常。
四、安全措施1.施工现场设置警示标志,划定施工区域,保持施工现场的秩序和安全。
2.使用符合规范要求的施工设备和机具,严格按照操作规程进行施工。
3.对施工人员进行安全培训和技术指导,确保其具备相关的安全知识和操作技能。
4.施工期间,严禁酒后上岗和疲劳驾驶,确保施工人员的身体健康和精力充沛。
内浮顶储罐施工方案
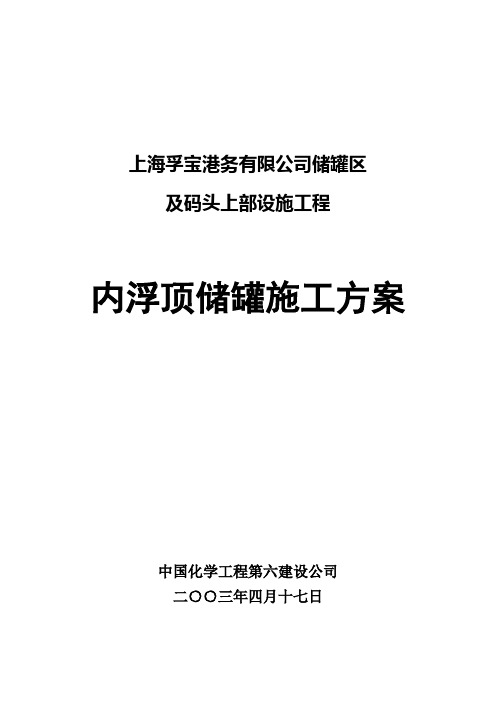
上海孚宝港务有限公司储罐区及码头上部设施工程内浮顶储罐施工方案中国化学工程第六建设公司二○○三年四月十七日目录1 编制说明2 编制依据3 施工方法及技术措施3.1 施工程序3.2 预制加工3.3 组装焊接3.4 罐体检验及试验3.5 罐体防腐施工4 劳动力计划5 工机具使用计划6 施工手段用料计划7 质量控制措施8 安全及文明施工1 编制说明上海孚宝港务有限公司储罐区共有内浮顶罐13台,其最大容积为5600m3。
罐体为普通C·S钢板材料,单台最大重量193.6吨,全部采用现场制造,各浮顶罐特性见下表。
2 编制依据2.1 上海孚宝港务有限公司包储顶目初步设计;2.2 《立式圆筒形钢制焊接油罐施工及验收规范》GBJ128-902.3 《现场设备、工业管道焊接工程施工及验收规范》GB50236-982.4 《石油化工立式圆筒形钢制焊接油罐设计规范》SH3064-923 施工方法及技术措施罐体制作采用倒装法施工,即采用先底、顶,后罐壁的方法,具体施工过程和控制措施如下:3.1 施工程序材料验收→放样下料→预制→基础验收→底板组焊及试验检验→最顶层带板组焊→拱顶组焊→倒数第二层带板组焊→钢结构、梯子平台及附件施工→罐体试验→内浮顶安装→罐体防腐→竣工验收。
3.2 基础验收3.2.1 基础表面尺寸要求见表3-1。
3.2.2 以基础中心为圆心,以不同直径作同心圆,将各圆周分成若干等分,在等分点测量基础表面的标高,同一圆周上的测点,其测量标高与计算标高之差不得大于12mm;检查基础表面凹凸度的同心圆直径及测量点数,见表3-2。
基础表面尺寸允许偏差表3-1基础表面凹凸度的同心圆直径及测量点数3.3.1 罐顶板预制3.3.1.1 罐顶下料依据施工图下料,采用氧乙炔焰半自动切割机切割。
罐顶弧形板采用胎具压制加工成形,现场拼装。
因为该板压制后有一定的反弹,该胎具的半径应比拱顶板的弧形半径小20mm。
3.3.1.2 罐顶弧形板每隔1米的距离加压一次,成型后的拱顶板必须用长L=2m的弧形样板检查,不合格的部位需重新压制。
浮顶储罐施工方案

浮顶储罐施工方案一、工程概况与目标本施工方案针对浮顶储罐的建设过程,涵盖了从施工准备到工程验收与交付的全部流程。
本工程旨在安全、高效地建设一座质量稳定、功能完备的浮顶储罐,以满足使用方的存储需求。
二、施工准备工作人员配置:组建专业的施工团队,包括项目经理、技术负责人、安全员、质检员等关键岗位。
材料采购:根据设计要求,采购合格的材料和构配件,并确保其质量和数量满足施工需求。
设备准备:准备必要的施工机械和设备,如挖掘机、吊车、焊接设备等。
现场勘查:对施工现场进行详细勘查,了解地形、地质、气象等条件,为施工提供基础数据。
三、基础施工与验收基础施工:按照设计要求进行基础施工,确保基础平整、稳固。
基础验收:基础施工完成后,进行基础验收,确保基础质量符合设计要求。
四、浮顶储罐安装罐体安装:按照设计图纸和工艺要求,进行罐体的安装工作。
浮顶安装:罐体安装完成后,进行浮顶的安装工作,确保浮顶与罐体连接紧密、密封良好。
五、防腐与保温处理防腐处理:对罐体进行防腐处理,以防止罐体受到腐蚀影响。
保温处理:根据使用需求,对罐体进行保温处理,以减少能源浪费。
六、安全与环保措施安全管理:制定详细的安全管理制度和操作规程,确保施工过程安全可控。
环保措施:采取有效的环保措施,减少施工对环境的影响。
七、质量控制与检验质量控制:建立严格的质量管理体系,确保施工质量符合设计要求。
检验与测试:对施工过程进行全程检验与测试,确保工程质量符合要求。
八、工程验收与交付工程验收:工程完成后,进行全面的工程验收,确保工程质量和使用功能符合设计要求。
交付与使用:工程验收合格后,进行交付使用,并提供必要的技术支持和售后服务。
本施工方案旨在确保浮顶储罐建设过程的安全、高效和质量稳定。
我们将严格按照施工方案进行操作,确保工程顺利完成,并满足使用方的需求。
储罐安装顶升专项施工方案
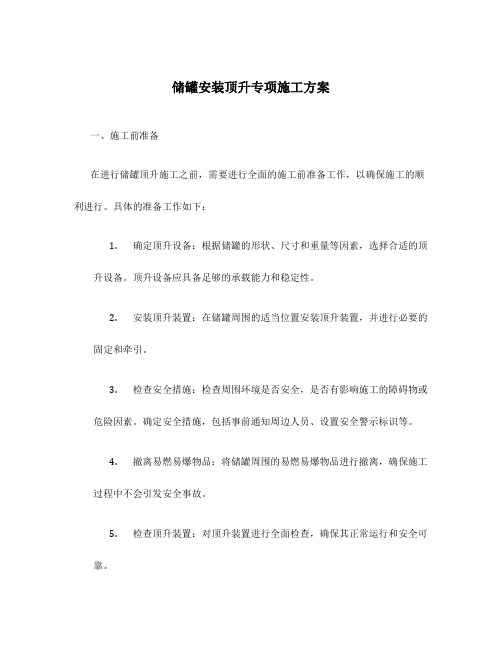
储罐安装顶升专项施工方案一、施工前准备在进行储罐顶升施工之前,需要进行全面的施工前准备工作,以确保施工的顺利进行。
具体的准备工作如下:1.确定顶升设备:根据储罐的形状、尺寸和重量等因素,选择合适的顶升设备。
顶升设备应具备足够的承载能力和稳定性。
2.安装顶升装置:在储罐周围的适当位置安装顶升装置,并进行必要的固定和牵引。
3.检查安全措施:检查周围环境是否安全,是否有影响施工的障碍物或危险因素。
确定安全措施,包括事前通知周边人员、设置安全警示标识等。
4.撤离易燃易爆物品:将储罐周围的易燃易爆物品进行撤离,确保施工过程中不会引发安全事故。
5.检查顶升装置:对顶升装置进行全面检查,确保其正常运行和安全可靠。
二、顶升施工步骤储罐顶升施工需要按照一定的步骤进行,以确保施工的顺利进行和安全性。
具体的施工步骤如下:1.取消固定装置:在开始顶升施工前,需要先将储罐的固定装置取消,并确保储罐能够自由移动。
2.安装顶升装置:根据储罐的形状和重量等因素,将顶升装置正确地安装在储罐上。
确保顶升装置与储罐连接牢固,能够承受储罐的重量。
3.顶升储罐:通过操作顶升装置,逐步将储罐顶升至所需的高度。
在顶升过程中,需要注意保持储罐的平衡,避免倾斜或偏移。
4.固定储罐:当储罐达到所需的高度后,需要及时进行固定,防止其再次下降或移动。
固定方式可以采用螺栓固定、钢丝绳固定等方法,确保储罐的稳定性。
5.检查顶升装置:在施工完成后,对顶升装置进行检查,确保其正常运行和安全可靠。
如有异常情况,及时进行维修或更换。
6.清理施工场地:清理施工场地,将施工过程中产生的垃圾和废弃物进行分类和处理,确保环境的整洁和安全。
三、施工安全措施储罐安装顶升施工涉及到的安全问题较多,需要采取一系列的安全措施来保障施工人员和周围环境的安全。
以下是一些常见的安全措施:1.施工人员佩戴个人防护装备,包括安全帽、防护眼镜、耳塞、防护服等。
2.在施工现场设置警示标识,在施工区域周围划定安全警戒线,防止未授权人员进入。
内浮顶油罐施工方案

内浮顶油罐施工方案油罐作为存储石油等液态介质的重要设施,在石油工业中占有重要地位。
内浮顶油罐是一种用于储存液态石油产品的储罐,具备防止产品挥发和外部物体进入的功能,保障了储存产品的安全性。
内浮顶油罐的施工方案至关重要,本文将探讨内浮顶油罐施工的具体方案。
1. 施工前准备工作在进行内浮顶油罐的施工前,必须做好充分的准备工作,包括但不限于以下方面:•资质审查:确保施工团队拥有相关的资质和技术经验。
•现场检查:对施工现场进行全面检查,确保环境符合安全要求。
•材料准备:准备所需的施工材料和设备。
•人员培训:对参与施工的人员进行必要的安全培训。
2. 施工流程2.1 准备工作在施工开始前,需要对施工现场进行清理,确保施工区域干净整洁,避免杂物影响施工进度和质量。
此外,还需要准备好所需的材料和设备,如吊车、焊接机等。
2.2 油罐安装首先,需要将油罐的主体部分运送至施工现场,然后使用吊车等设备进行安装。
在安装过程中,要确保油罐的稳定性和密封性,避免发生安全事故。
2.3 内浮顶安装内浮顶是内浮顶油罐的重要组成部分,能够有效减少产品挥发和外部污染。
在安装内浮顶时,需要注意以下几点:•内浮顶的安装位置应符合设计要求,确保油罐的正常运行。
•内浮顶与油罐壁应有适当的间隙,以便内浮顶的自由上下移动,保证其正常工作。
•内浮顶的密封性能需要得到充分的验证,确保产品不会泄漏。
2.4 安全检查施工完成后,需要对油罐进行全面的安全检查,确保所有的安全措施和设备都得到有效安装和调试。
只有通过严格的安全检查,油罐才能投入使用,保障工作人员和环境的安全。
3. 施工质量管理为确保内浮顶油罐的施工质量,施工过程中需要进行严格的质量管理,包括但不限于以下方面:•施工过程中及时记录和处理施工中的问题和不良现象。
•对施工中的材料和设备进行质量检查,确保符合相关标准。
•对施工现场进行定期巡检,及时发现并解决问题。
通过严格的质量管理,可以确保内浮顶油罐的施工质量达到要求,从而提高其工作效率和安全性。
内浮顶密封安装施工方案

内浮顶密封是内浮顶油罐的关键部件,其主要作用是防止油罐内的油气外泄,确保油品质量,同时降低油气对环境的污染。
为了确保内浮顶密封安装施工质量,制定以下施工方案。
二、施工准备1. 技术准备(1)熟悉内浮顶密封的安装工艺、技术要求及验收标准;(2)了解油罐的结构、尺寸及设备性能;(3)学习相关安全操作规程。
2. 组织准备(1)成立施工队伍,明确各工种人员职责;(2)编制施工组织设计,确保施工进度和质量;(3)配备施工所需的机械设备、工具及材料。
3. 供应工作准备(1)确保内浮顶密封、密封圈、垫片等材料质量符合要求;(2)检查施工设备、工具是否齐全,性能良好;(3)做好现场清理工作,确保施工环境整洁。
三、施工步骤1. 油罐底部检查与处理(1)检查油罐底部是否有凹凸不平、锈蚀等现象;(2)对凹凸不平、锈蚀部位进行打磨、清理;(3)涂刷防锈漆,确保油罐底部平整、干净。
2. 内浮顶密封安装(1)将内浮顶密封按照设计要求放置在油罐底部;(2)安装密封圈,确保密封圈与密封面接触紧密;(3)将密封圈与密封面之间的间隙调整至规定范围;(4)安装垫片,确保垫片与密封面接触紧密;(5)检查内浮顶密封安装位置,确保其与油罐底部垂直。
3. 内浮顶密封检查与调试(1)检查内浮顶密封的密封性能,确保无泄漏;(2)检查内浮顶密封的安装位置,确保其与油罐底部垂直;(3)检查内浮顶密封的固定螺栓,确保其紧固度符合要求;(4)对内浮顶密封进行调试,确保其运行平稳、无异常。
4. 施工验收(1)检查内浮顶密封的安装质量,确保符合设计要求;(2)检查内浮顶密封的密封性能,确保无泄漏;(3)检查施工记录,确保施工过程符合规范。
四、施工注意事项1. 施工过程中,注意安全操作,防止发生意外事故;2. 严格按照施工方案进行施工,确保施工质量;3. 施工过程中,注意保护油罐,防止损坏;4. 施工完成后,及时清理现场,确保环境整洁。
五、结论内浮顶密封安装施工是油罐建设的关键环节,通过以上施工方案,确保内浮顶密封安装质量,为油罐的正常运行提供保障。
内浮顶储罐施工方案
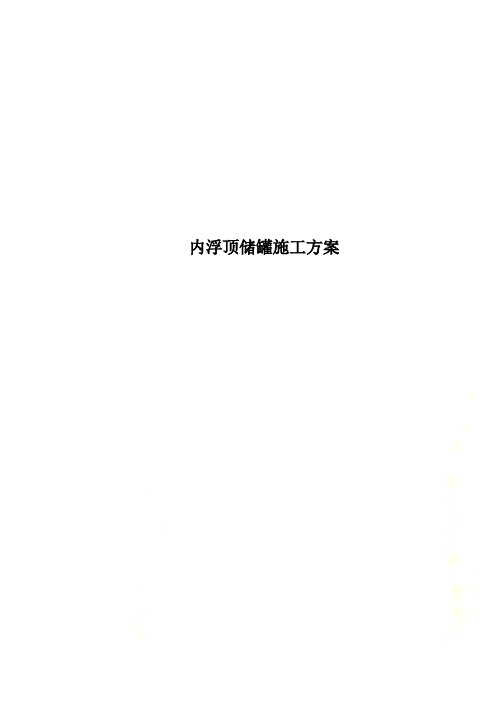
内浮顶储罐施工方案(六)储罐施工方案1.工程概况中油福州油品码头及库区新建工程共有成品油储罐7具,消防水罐2具,其中柴油罐为3具5000立方米拱顶罐,汽油罐为2具3000立方米和2具5000立方米内浮顶罐,消防水罐为2具1000立方米拱顶罐。
该工程7具罐与预留的一具罐组成了较为紧凑的成品油罐区,便于集中流水施工。
消防水罐则分布于成品油罐区外部。
2.编制依据由中国石油天然气华东勘察设计研究院设计的施工图:2003设-401、1000m3拱顶储罐2003设-407、3000m3内浮顶储罐2003设-403、5000m3内浮顶储罐2003设-405、5000m3拱顶储罐GB128-90《立式圆筒形钢制焊接储罐施工及验收规范》。
SH3530-93《石油化工立式圆筒形钢制储罐施工工艺标准》。
SH3528-93《石油化工钢储罐地基与基础施工及验收规范》。
SHJ22-90《石油化工企业设备与管道涂料防腐蚀设计与施工规范》。
JB4730-94《无损检测》。
3.储罐设计数据4.罐体数据(1)1000立方米拱顶罐罐体数据一览表:(单具总重28850Kg)(2)3000立方米内浮顶罐罐体数据一览表:(单具总重76797Kg)(3)5000立方米拱顶罐、内浮顶罐罐体数据一览表:(单具总重119731Kg)5.施工方法5.1施工方法采用群桅起升倒装法:5.2施工用料:每个罐所需倒链和桅杆如下表所示:5.3材料验收储罐所选用的材料和附件,应具有质量合格证明书当无质量合格证明书或质量合格说明书有疑问时,应对材料和附件进行复验。
储罐焊条选用J422、J427电焊条,焊条应具有质量合格说明书。
储罐所选用的钢板,必须逐张进行外观检查,其表面质量应符合现行的相应钢板标准的规定。
钢板表面锈蚀减薄量,划痕深度与钢板实际偏差之和,应符合下表规定。
5.4预制5.4.1罐底预制(1)罐底板预制前应根据实际来料绘制排版图。
并根据图纸放大样,检查无误后方可下料。
大型储罐液压顶升施工方法
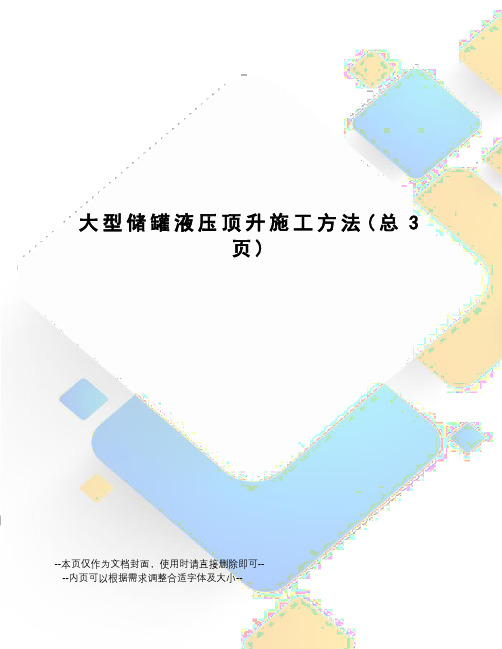
大型储罐液压顶升施工方法(总3页)--本页仅作为文档封面,使用时请直接删除即可----内页可以根据需求调整合适字体及大小--大型储罐液压顶升施工方法目前国内大型储罐施工方法有以下六种:液压提升倒装、中心柱倒装,充气顶升倒装、水浮倒装、正装法、机械顶升倒装。
六种施工方法从施工质量、安全、进度和经济效益等方面作如下比较:施工方法液压提升中心柱充气顶升水浮正装正装法机械顶升施工质量易保证易保证较难保证较难保证较难保证中施工进度快较快较快慢慢较快离工成本低中较低高高高施工环境好较好差差差中劳动强度小中较小大大大适应范围广窄窄窄窄中安全性好好差较差差中机具占用少中少多多多场地占用少多少少多中液压提升倒装法介于几种施工方法之间,其特点一是适应范围广,理论上可适用于任意大小的储罐,二是操作控制简单、可靠、危险性小,因此已经越来越多的被采用,其主要缺点是目前成套设备价格较贵,设备购置一次性投入较大。
1 .液压顶升法,是倒装法的一种形式,其安装步骤与程序是:下图2 .液压提升方法:在先期施工的罐底板上安装数个固定垫墩 (400mm 高 , 间距 3-4 米 ), 然后组装第一层壁板和顶盖板 , 沿罐内壁 400mm 处均布数台(根据计算确定)液压提升机,以提升机的滑动托架托住固定在罐内壁的胀圈下部 , 操纵液压提升机的控制柜,集中控制各液压机的动作 , 液压提升机提升扒杆时 , 同时也将罐体提升 , 升至下一带壁板高度时 , 可进行一带壁板组装 , 然后落下扒杆、胀圈 , 再进行下一带提升组装 , 直到整个油罐倒装完毕。
3 .施工技术2 罐底板预制:按设计排板图编号下料,并按号堆放好。
下料时要注意考虑焊接收缩量 50 毫米。
罐底板下好料后,反面要按要求防腐,编号应在正面,使其在罐底铺设时能够按号施工。
罐底边缘板和中幅板最少宽度和长度必须符合图纸和规范要求,尺寸要严格控制,防止变形过大。
2 罐壁板预制“壁板下料、滚圆,为了保证壁板预制质量,壁板下料采用半自动切割机切割。
内浮顶罐施工方案
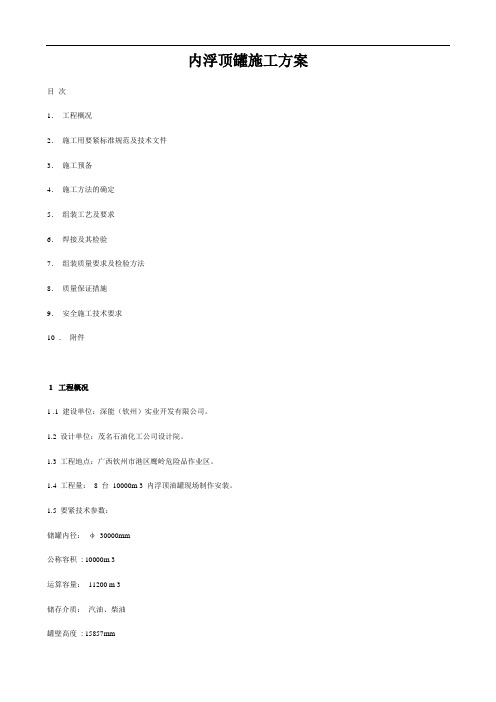
内浮顶罐施工方案目次1.工程概况2.施工用要紧标准规范及技术文件3.施工预备4.施工方法的确定5.组装工艺及要求6.焊接及其检验7.组装质量要求及检验方法8.质量保证措施9.安全施工技术要求10 .附件1工程概况1 .1 建设单位:深能(钦州)实业开发有限公司。
1.2 设计单位:茂名石油化工公司设计院。
1.3 工程地点:广西钦州市港区鹰岭危险品作业区。
1.4 工程量:8 台10000m 3 内浮顶油罐现场制作安装。
1.5 要紧技术参数:储罐内径:φ30000mm公称容积: 10000m 3运算容量:11200 m 3储存介质:汽油、柴油罐壁高度: 15857mm主体材质: Q235 - A设计压力:+1960Pa -490Pa设计温度:40 ℃设计风压: 700Pa地震烈度: 7焊缝系数:0.9腐蚀裕度:1mm试验压力:+2200Pa -1800Pa铝制内浮盘: WES -φ30000罐体质量: 221886kg (单台)2施工用要紧标准规范及技术文件2.1 施工图纸及相关技术文件2.2 GBJ128—90 《立式圆筒形钢制焊接油罐施工及验收规范》2.3 JB4730—94 《压力容器无损检测》2.4 GBJ50205 —95 《钢结构工程施工及验收规范》3施工预备3.1 现场平台:现场设置二个预制钢平台,尺寸为6m ×12m 。
用δ=14mm 、材质为Q235 -A 的钢板铺设。
3.2 施工机具的预备及人员配备。
3.2.1 需预备的施工机具如下表:3.2.2 施工人员:3.3 施工平面布置图见施工组织设计。
3.4 施工手段用料预备如下表:3.5 材料验收3.5.1 油罐用钢材、配件必须符合设计和规范要求,具有产品质量证明书或检验报告。
3.5.2 油罐用钢板应逐张进行外观检查,其表面不得有气孔、裂纹、拉裂、夹渣、重皮现象。
钢板厚度要求:板厚为6 ~7mm 钢板承诺偏差:-0.6mm ;板厚为8mm ~18mm 钢板承诺偏差:-0.8mm 。
罐液压提升施工方案

罐液压提升施工方案1.编制说明储罐为装置的重点设备,由于体积大重量重,罐体材质又为不锈钢,焊接收缩量大,变形难以控制。
为指导储罐的施工保证储罐的施工质量及进度,特编制本方案。
本方案仅用于投标,施工时根据详细设计资料补充修改。
2.编制依据1)招标文件2)安装工程施工招标文件问题答疑3)我公司的《大型储罐液压提升工法》4)《园筒形钢制焊接贮罐施工及验收规范》HGJ210-835)《立式园筒形钢制焊接油罐施工及验收规范》GBJ128-903.工程概述3.1 储罐的地理位置储罐位于甲醛罐区和甲醇罐区内。
甲醛罐区占地面积513m2,甲醇罐区占地面积2049.3m2。
3.2 EG储存罐的设计情况4.施工方法的选定考虑到方案的先进性、经济性、合理性及工期,通过综合比较多种施工方法,拟选用我公司“大型储罐液压提升工法”完成甲醇罐区的施工,甲醛罐区的储罐采用吊车倒装的施工工艺这里不再赘述。
采用此工法我公司先后完成了西安化工总厂10000 m3拱顶罐、甘肃柳元油库2×2000 m3等油罐的施工,经济效益显著。
5.施工程序施工程序见图16.操作要点罐施工时液压装置置于罐外,控制台放在两罐中央,同时控制2台罐施工。
提升架布置在罐壁内侧,以便操作时方便指挥与控制。
6.1 选提升架数量,则12单台提升重量为:Q=69.94 吨。
单台需要的提升架数量:N=5.5选6台提升架,两相邻提升架间距6-7.5m,单台荷重11.7吨6.2 提升架的平面布置提升支架应均匀布置在罐壁内侧,尽量靠近壁板以工作时不碰上面的包边角钢为原则。
安装时用线锤测量,支架安装要垂直平面。
由高压软管连接油缸的上下油孔。
由于支架的稳定性影响整个罐体提升的稳定,必须平稳垂直固定。
支座板靠罐心的一边与底板焊接,支架上焊两根斜支撑和一根连到中心的径向水平拉杆,并把所有支架呈辐射形式连接在一起。
这种布置方式可使单个支架有足够的刚度,又使所有支架形成封闭系统,充分保证提升系统的稳定性。
- 1、下载文档前请自行甄别文档内容的完整性,平台不提供额外的编辑、内容补充、找答案等附加服务。
- 2、"仅部分预览"的文档,不可在线预览部分如存在完整性等问题,可反馈申请退款(可完整预览的文档不适用该条件!)。
- 3、如文档侵犯您的权益,请联系客服反馈,我们会尽快为您处理(人工客服工作时间:9:00-18:30)。
储罐组装施工措施(适用于内浮顶罐、液压顶升倒装施工)2.1 储罐新建工程量简介新建10000m3拱顶罐2座,储存介质为柴油,钢板厚度有6mm、8mm、10mm、12mm 和14mm五种,材质有Q235-B和16MnR两种,包边角钢为∟125×10,共9圈壁板。
罐体内直径为30m,总高度为19.341m,总重量为222.83t。
2.2 施工工艺流程本工程10000m3拱顶罐拟采用液压顶升倒装工艺法,施工工序如下:2.3 10000m3罐施工措施2.3.1 原材料检验⑴原材料检验:板材及型钢符合设计要求,•人孔、透光孔、通气孔、清扫孔等外购件出厂合格资料齐全。
⑵制造储罐所用的钢板必须逐张进行外观检查,其表面质量应符合GB6654-1996《压力容器用钢板》的规定。
对钢板表面的锈蚀减薄量、划痕深度与钢板实际负偏差之和,当钢板厚度为6~7mm时,允许偏差为-0.6mm;当钢板厚度为8~25mm时,允许偏差为-0.8mm。
⑶所有工程用钢材、半成品、配件、焊材均应按规格、材质分别堆放,下部垫平填实,防止变形损坏,并做好明显标记。
⑷经检验合格的材料,应设专人管理,按限额领料单发放。
对不合格的材料,严禁在工程中使用。
2.3.2 储罐的预制⑴一般规定:① 储罐在预制、组装及检验过程中所使用的样板应符合下列规定:a . 当构件的曲率半径小于或等于12.5m 时,弧形样板的弦长不得小于1.5m ;当曲率半径大于12.5m 时,弧形样板的弦长不得小于2m 。
b . 直线样板的长度不得小于1m 。
c . 测量焊缝角变形的弧形样板,其弦长不得小于1m 。
② 钢板的切割和焊缝的坡口,宜采用机械加工或自动、半自动火焰切割加工;罐顶板和罐底板边缘板的园弧边缘,可采用手工火焰切割加工。
③ 钢板边缘加工面应平滑,不得有夹渣、分层、裂纹及熔渣等缺陷。
火焰切割坡口产生的表面硬化层应磨除。
④ 所有预制构件在保管、运输及现场堆放时,应采取有效措施防止变形、损伤和锈蚀。
⑵ 底板的预制:① 绘制底板排板图,根据设计图纸,板材尺寸及标准要求绘制排板图,为补偿焊接收缩,罐底的的排板直径应比设计图样尺寸大0.1~0.2% 。
②根据排板图进行下料,中幅板用自动磁轮切割机下料,边缘板用半自动火焰切割机下料,自动磁轮切割机加工坡口。
弓形边缘板尺寸偏差应下表的规定;③ 弓形边缘板的对接接头宜采用不等间隙,外侧间隙宜为6~7mm ,内侧间隙宜为8~12mm 。
④ 罐底板应平整,用直线样板(样板长不小于2米)检查凹凸度,其间隙不应大于5mm 。
⑶ 罐壁板预制① 绘制排板图:最窄板宽和板长:直径小于12.5m 的储罐,板宽不得小于500mm ,板长不得小于1000mm ;直径大于或等于12.5m 的储罐,板宽不得小于1000mm ,板长不得小于2000mm 。
各圈壁板的纵向焊缝宜向同一方向逐圈错开,其间距宜为板长的1/3,且不得小于500mm ;底圈壁板的纵向焊缝与罐底边缘板对接焊缝之间的距离,不得小于200mm ;罐壁接管开孔补强板外缘焊缝与罐壁纵向焊缝之间的距离不得小于200mm ,与环向焊缝之间的距离不得小于100mm 。
A B CDEF② 壁板下料:用自动磁轮切割机下料(最上一圈下净料,其余均留尾板)并加工坡口。
壁板下料后用钢卷尺检查尺寸,允许偏差应符合GBJ128-90中第3.2.2条(列表说明)的要求;③ 壁板滚圆:在滚弧过程中注意经常检查弧度,防止滚过头。
壁板两端滚不到的地方采用加垫板的方法滚圆,垫板应比被加工的壁板厚2mm ,对于因板厚无法加垫板时,应将无法滚圆部分切除。
壁板滚圆后,立放在平台上用弧形样板检查弧度,间隙不应大于4mm ;在壁板宽度方向用直线样板检查,间隙不应大于1mm 。
④ 坡口:⑤ 预制合格的壁板堆放在等弧度的胎具上,以免壁板变形。
每块壁板按排板图编上号,先编圈号,后写板号,中间加“-”,用阿拉伯数字书写。
⑷ 顶板预制①根据施工图,确定顶板的块数,绘制排版图,并根据板料尺寸合理使用,同时应使顶板任意两相邻焊缝的间距不小于200mm 。
② 样板制作:找一处平整宽敞的平台,把油毡纸平铺,利用计算出的尺寸划出瓜皮板样板。
油毡纸宽度不够可用火焊把微烤后粘合。
样板成形后两道长边应为弧形,用剪刀仔细剪切修整合格后方可在钢板上下料。
③ 把样板平铺在钢板上划线,瓜皮板小端长度方向应留出10~20mm 余量。
④ 下料时采用半自动火焰切割器进行切割。
⑤ 罐顶胎具制作详图:ABCDEF⑥拱顶的顶板及加强筋应进行成型加工。
加强筋用弧形样板检查,其间隙不得大于2mm;加强筋与顶板组焊时应采取防变形措施。
加强筋的拼接采用对接接头时应加垫板,且必须完全焊透;采用搭接接头时,其搭接长度不得小于加强筋宽度的2倍。
⑦拱顶的顶板预制成型后,用弧形样板检查,其间隙不得大于10mm。
⑧罐顶瓜皮板与筋板组焊步骤:a)罐顶瓜皮板上胎。
b)组对长度方向筋板。
c)组对双弧筋板。
d)点焊完毕后整体检测。
⑸浮顶预制(如是成品内浮盘则无此内容)①根据施工要求,结合图纸设计,绘制浮顶底板和顶板排板图;②为施工方面快捷,拟将底板和顶板采用同样的排板形式,即船舱上下板均按弓形板下料;浮顶中幅板的下料排板形式同罐底。
根据弓形板下料尺寸和内外边缘板的长度,结合吊车的起重能力,确定船舱分段施工情况;③船舱隔板、肋板和桁架的预制应保证几何尺寸,其允许偏差宜为±2mm。
④浮舱底板可采用双面对接焊,舱与舱之间的底板可采用搭接焊。
桁架结构按图纸要求预制焊接,标识后分类放置;桁架组对宜在胎具上进行,可采用反变形胎具进行焊接。
⑤浮舱组对,宜在固定的平台上进行。
铺设浮舱底板后,组对隔板,肋板和桁架,最后组对内(外)边缘板。
焊接过程中,应采用焊接变形小的焊接工艺施焊。
⑥预制船舱几何尺寸测量部位及允许偏差见下图和下表:测量部位允许偏差(mm)高度AE、BF、CG、DH ±1⑹盘梯预制①根据图纸尺寸计算盘梯内侧板的放样半径。
②根据踏步板数量,确定内外侧板长度,并且两端预留不少于500mm的长度,侧板之间可采用全焊透的对接形式。
③在平台上画出侧板位置线,把内外侧板定位,然后用样板在内外侧板上画上踏步位置线,按位置线组焊踏步。
④盘梯在平台上整体预制,预制完毕后从中间割开分成两半,以方便拉运。
⑹包边角钢、抗风圈、加强圈等构件预制包边角钢、抗风圈、加强圈等构件预制成型后,用弧形样板检查,其间隙不得小于2mm,放在平台上检查,其翘曲变形不得超过构件长度的0.1%且不大于4mm。
2.3.3 罐体现场组装2.3.3.1 罐底板安装⑴储罐基础检查验收合格后方可进行罐底安装,底板铺设前,其表面喷砂除锈达到Sa2.5级,在其下表面刷底漆,每块底板边缘50mm范围内不刷。
⑵基础放线,在基础上打出十字中心线,并划出边缘板外缘的圆周线,然后按排板图划出边缘板对接缝的位置。
铺设边缘板时,应按安装位置线两边对称铺设,并在对接焊缝处点焊上垫板。
垫板与相邻两块底板中的一块先点焊,底板与垫板应贴紧,其间隙不大于1mm。
⑶边缘板铺完后再进行调整,对接缝外侧间隙为6~7mm,内侧间隙宜为9~11mm,以吸收焊接时的旋转变形。
⑷铺设中幅板,搭接宽度偏差控制在±5mm内,中幅板铺设从中心开始向两边进行,先铺中条板,再铺两侧条板,依次交叉,直到整个中幅板铺完。
⑸底板焊接顺序:先焊中幅板,再焊边缘板。
中幅板焊接时,先焊短焊缝,再焊长焊缝(焊长缝时由中心向两侧分段退焊),焊接时,初层焊道应采取分段退焊或跳焊的方法。
当罐底板面积较大时,将中幅板划分为若干区域,先焊某个区域内的短缝和长缝,再将区域联成大片,焊大片之间的短缝和长缝。
边缘板焊接时先焊靠外缘300mm内的焊缝。
待罐底与罐壁连接的角焊缝焊完后,再焊边缘板上剩余的对接焊缝,最后焊中幅板和边缘板之间的伸缩缝。
具体的焊接顺序见下图和表:2.3.3.2 第一圈壁板安装⑴施工准备:①焊中心桩:划十字中心线在罐底中心用Ф18的圆钢(L=200)焊一中心桩。
②壁板组装前首先检查壁板下各边缘板焊缝是否焊好、磨平,而且要求真空试验及无损检测合格。
③在边缘板上画出壁板内圆周线(控圆线),要考虑到焊接收缩量和罐底坡度来确定罐壁板的放线内半径,按板数和规格标出各立缝中心位置。
④在壁板内侧100mm画出组装检查基准线,以备检查罐的圆度。
⑤焊操作平台支架:沿圆周每800mm一处,焊接在底板上,并在支架上焊自动焊机导轨(扁铁-80×8)沿圆周一圈。
自动焊机导轨支架⑥在放好的控圆线内侧每隔500mm,设一个三角挡板,焊于罐底板,三角挡板用10mm 厚钢板制作,为100×100的直角三角形,以直角抵近控圆线。
同时在控圆线内侧沿控圆线圆周每隔2m 左右点焊一个垫块,垫块用18#或20#槽钢制作,将其割成长150mm 左右的小段,放置时使翼板与水平面平行,腹板与控圆线垂直。
⑦ 胀圈准备:用[22槽钢滚制后焊接而成,共分10段,段与段之间用加减丝(M60)或螺旋千斤顶(40T )连接。
胀圈的质量(主要是圆度、挠曲)对壁板有较大影响,制作时应精确校正,滚压好的槽钢,在钢平台上用火焰加热辅以千斤顶顶的方法校正,校正合格后焊接成形。
⑵ 第一圈壁板围板:① 将成型壁板吊至控圆线上使其紧靠控圆线上事先点焊的三角挡板,同时应确保立缝与事先在底板上标出的立缝位置对齐,然后在内侧架支撑杆(Ф48×3.5)固定,底部加楔块固定,壁板与壁板之间的立缝用“龙门板”连接并调节焊缝间隙。
立缝组对间隙:(GBJ128-90第15页)。
② 第一圈壁板全部围完后,最后一块板(带500mm 长尾板)用倒链或加减丝连接,调节所有壁板的垂直度不应大于3mm (用线坠测量);调节立缝间隙,保证内壁平齐,且错边量不应大于1mm ;用水准仪检查板顶高度(相邻两壁板上口水平的允许偏差不应大于2mm ,在整个圆周上任意两点水平的允许偏差,不应大于6mm )合格后,进行立缝焊接,先焊内侧后焊外侧,多名焊工对称同时焊接,分段跳焊。
待立缝焊接完毕并冷却后,再次检查、调节罐壁垂直度,最后将尾板多余部分割除并组对焊接。
胀 圈胀圈断面胀圈连接处龙门板2.3.3.3 罐顶安装⑴第一圈罐壁焊接完毕后安装包边角钢,安装前先用弧形样板检查其弧度,间隙不大于4mm(注意角钢滚弧方向)。
包边角钢对接接头与壁板纵向焊缝之间的距离不得小于200mm。
包边角钢安装好后,在包边角钢上用累积分尺法进行放线,进行拱顶安装。
顶板搭接宽度允许偏差为±5mm。
⑵架设顶板支撑环:顶板铺设时用角钢架设支撑环,用钢管作为支撑柱,支撑柱数量应根据罐的直径周向均布设置。
⑶支撑柱的架设高度、计算公式及示意图如下:H=(H1+H2+H3 +h1-h2-h3-h4-Δh)+H1式中:H——支撑柱高度H1——第一圈罐壁的宽度H2——拱顶高度H3——包边角钢高出罐壁的高度h1——支撑环处罐顶的弦高h2——罐顶板的厚度h3——罐顶加强筋板的宽度h4——罐顶支架圈的高度Δh——支撑柱所在罐底板位置的坡高H1——预拱量接板;接着焊罐顶外侧径向搭接焊缝,用多名焊工均布,采用隔缝对称施焊的方法,由中心向外分段退焊;最后焊罐顶与包边角钢的连接焊缝,多名焊工均布,沿同一方向分段退焊。