圆坯连铸结晶器温度场模拟与坯壳厚度预测
圆坯连铸结晶器内电磁场、流场的数值模拟与实验研究的开题报告

圆坯连铸结晶器内电磁场、流场的数值模拟与实验研究的开题报告一、选题背景连铸技术是钢铁工业生产中重要的工艺环节之一,其直接关系到产品的质量和产量。
圆坯连铸结晶器内流场和电磁场的研究对提高连铸技术的效率和改善产品质量具有重要意义。
因此,本文提出了圆坯连铸结晶器内电磁场、流场的数值模拟及实验研究,以深入了解连铸过程中结晶器内的热传递、流动和结晶行为。
二、研究目的和意义圆坯连铸结晶器内电磁场、流场数值模拟和实验研究旨在:1. 为圆坯连铸结晶器的热流场和结晶行为的研究提供理论基础和实验支持。
2. 分析结晶器内电磁场、流场的特点,为进一步优化结晶器结构、提高产品质量和连铸效率提供基础数据。
3. 提出可以用于优化结晶器中的电磁场和流场的设计建议。
三、研究内容和方法1. 研究结晶器内的电磁场的分布特性,通过建立电磁场的数学模型,利用有限元方法进行数值模拟,验证模型的有效性。
2. 研究结晶器内的流场分布特性,通过建立流场模型,利用计算流体力学(CFD)方法进行数值模拟,验证模型的有效性。
3. 利用热像仪和热电偶等实验手段,对圆坯连铸结晶器内的温度分布情况进行实时监测和记录,验证数值模拟结果的正确性。
4. 基于数值模拟结果和实验数据,分析结晶器内的电磁场、流场与温度分布的关系,并提出结晶器内电磁场、流场优化设计建议。
四、研究进度安排一月份:阐述选题背景和研究目的,并提出研究方法和内容;二月份:对相关领域的文献进行综述和分析,明确研究的重点和难点;三月份:建立连铸结晶器内电磁场的数学模型,进行数值模拟,验证模型的正确性和可行性;四月份:建立连铸结晶器内流场的数学模型,进行数值模拟,验证模型的正确性和可行性;五月份:利用热像仪和热电偶等实验手段,对圆坯连铸结晶器内的温度分布情况进行实时监测和记录;六月份:基于数值模拟结果和实验数据,分析结晶器内的电磁场、流场与温度分布的关系,并提出结晶器内电磁场、流场优化设计建议;七月份:总结研究成果,撰写毕业论文,并进行答辩。
连铸结晶器中坯壳生长有限元分析
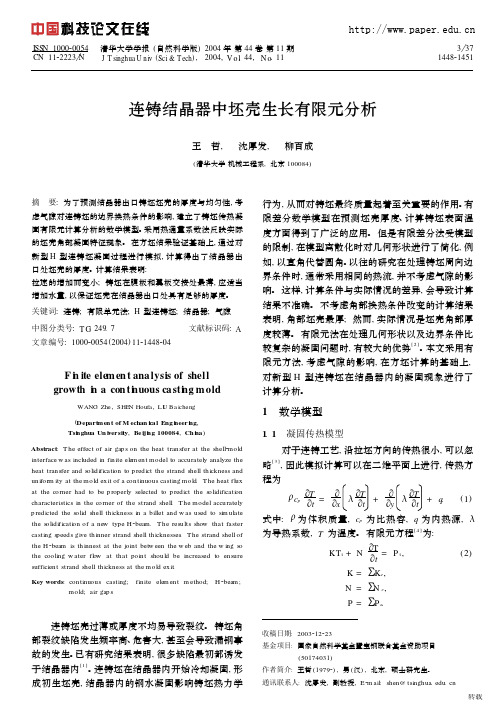
转载
中国科技论文在线
王 哲, 等: 连铸结晶器中坯壳生长有限元分析
式中: K 为温度刚度矩阵, T 为温度列向量, N 为
变温矩阵, P 为常列阵向量, 下标 t 表示某一时刻,
下标 e 表示单元。 对于 3 节点三角形单元, Ke、N e、 P e 中的元素分别如下所示:
kij = Κ(bibj + cicj ) (4∃ ) ,
( i, j = 1, 2, 3) ;
nii = Θcp ∃ 6,
(i = 1, 2, 3) ;
nij = Θcp ∃ 12,
( i, j = 1, 2, 3; i ≠ j ) ;
p i = ∃ qv 3,
( i = 1, 2, 3).
相变潜热作源项处理, 采用修正的方法, 对进入两相
1 数学模型
1. 1 凝固传热模型
对于连铸工艺, 沿拉坯方向的传热很小, 可以忽 略[3], 因此模拟计算可以在二维平面上进行, 传热方 程为
Θcp
9T 9t
=
9 9x
Κ99Tt
+
9 9y
Κ99Tt
+
q.
(1)
式中: Θ为体积质量, cp 为比热容, q 为内热源, Κ
为导热系数, T 为温度。 有限元方程[4]为:
ICSNSN11120202022300N54
清华大学学报 (自然科学版) J T singhua U niv (Sci & T ech) ,
2004 年 第 44 卷 第 11 期 2004, V o l. 44, N o. 11
3 37 144821451
动的影响, Κ取有效导热系数。
板坯连铸机结晶器内三维流场和温度场的有限元分析的开题报告

板坯连铸机结晶器内三维流场和温度场的有限元分析的开题报告1. 研究背景板坯连铸技术在冶金工业中广泛应用,其中结晶器是板坯连铸机的一个重要部件,决定了板坯的质量和直径。
为了进一步提高板坯连铸机生产效率和产品质量,需要对结晶器内部的流场和温度场进行深入研究。
2. 研究内容本研究旨在通过有限元分析方法,对板坯连铸机结晶器内的三维流场和温度场进行分析,探究结晶器内局部的流动规律和热传递特性,为优化连铸机结构和操作参数提供理论支持。
具体研究内容包括:(1)建立板坯连铸机结晶器的三维模型,包括结晶器下部、侧壁和顶部的几何形状和结构特点等。
(2)采用FLUENT软件对结晶器内部的三维流场进行模拟和计算,考虑板坯连续坯流动、自由液面、宽度变化等实际工况因素,研究结晶器内局部流动规律。
(3)基于ANSYS软件对结晶器内的三维温度场进行模拟和计算,分析板坯在连铸过程中的温度分布情况,并研究热传递特性对板坯成形质量的影响。
3. 研究意义通过对板坯连铸机结晶器内部流场和温度场的有限元分析,可以更加深入地了解结晶器的结构特点和板坯成形过程中关键参数的影响规律,为优化连铸机的生产效率和产品质量提供参考和优化建议。
研究成果可为铸造工艺的科学发展提供重要理论支持。
4. 研究方法本研究主要采用有限元分析方法,包括建立结晶器的三维几何模型、采用FLUENT软件模拟结晶器内的三维流场、采用ANSYS软件模拟结晶器内的三维温度场等。
5. 预期成果经过对板坯连铸机结晶器流场和温度场的有限元分析,本研究将得到以下预期成果:(1)结晶器内部的流场和温度场分布规律图;(2)不同结构和操作参数对流场和温度场的影响规律;(3)结晶器内不同部位的流动规律和温度特性分析和优化建议。
6. 研究进度和计划目前,本研究正在进行模型建立和初步模拟,预计在6个月内完成有限元分析计算和数据处理,整理成篇有关结晶器内的流场和温度场分析的研究论文。
具体研究计划如下:(1)第1-2个月:建立板坯连铸机结晶器的三维模型;(2)第3-4个月:采用FLUENT软件模拟结晶器内的三维流场;(3)第5-6个月:采用ANSYS软件模拟结晶器内的三维温度场,并对数据进行分析和处理;(4)第7个月:编写研究论文并进行修改、定稿及提交。
连铸过程中板坯凝固的数值模拟

连铸过程中板坯凝固的数值模拟
QS C PVT
(5-10) 由式(5-9)与式(5-10)等量置换可得
f S C P T / L
(5-11) 此法采用固相率的增加来代替前热的放出,如果 f S 1 ,则表明该领域 V 的 凝固结束。
热焓法
凝固过程金属的焓可定义为
H cdT (1 f s ) L
L ——潜热, J / kg ;
f s ——固相率;
T ——温度, C ;
——时间, s ;
连铸过程中板坯凝固的数值模拟
——导热系数, W /(m K ) ;
x, y ——二维坐标, m 。
对于实用多元和金,要确定固相率和温度的关系,通常可以先采用热分析法 求出凝固开始温度 TL (液相线温度)和结束温度 TS (固相线温度),假定如下: (1)假定为线性分布时
式中, L ——补偿对流换热的等效导热系数;
m ——经验常数,钢液导入区, m 4 ~ 8 ;
S ——静止钢液的导热系数。
热物性参数的数值处理方法
由于导热系数、比热和密度是随温度变化的,其处理方法一般有常数法、线 形函数法和插值法等,在不同的温度区间内用二次曲线拟合的方法得到温度导热系数、温度-比热之间关系的曲线,来确定导热系数、比热值。 对于板坯密度的取值,可在不同相区内取不同的值。 (1) 固相区: S 7.6 10 3 kg / m 3 ;
板坯连铸过程中铸坯凝固壳厚度的测定
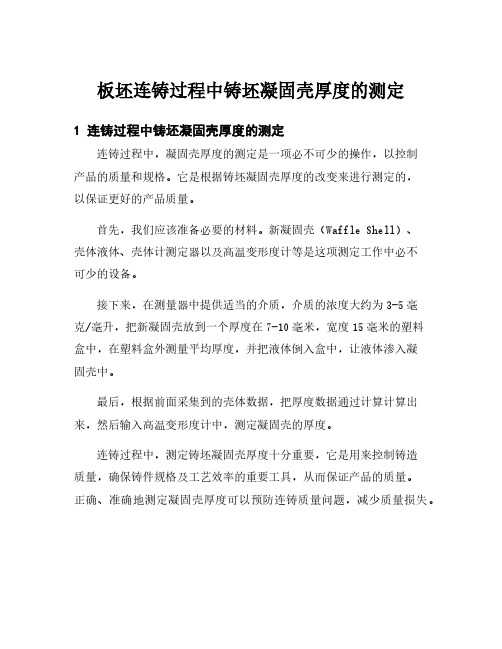
板坯连铸过程中铸坯凝固壳厚度的测定
1 连铸过程中铸坯凝固壳厚度的测定
连铸过程中,凝固壳厚度的测定是一项必不可少的操作,以控制
产品的质量和规格。
它是根据铸坯凝固壳厚度的改变来进行测定的,
以保证更好的产品质量。
首先,我们应该准备必要的材料。
新凝固壳(Waffle Shell)、
壳体液体、壳体计测定器以及高温变形度计等是这项测定工作中必不
可少的设备。
接下来,在测量器中提供适当的介质,介质的浓度大约为3-5毫
克/毫升,把新凝固壳放到一个厚度在7-10毫米,宽度15毫米的塑料
盒中,在塑料盒外测量平均厚度,并把液体倒入盒中,让液体渗入凝
固壳中。
最后,根据前面采集到的壳体数据,把厚度数据通过计算计算出来,然后输入高温变形度计中,测定凝固壳的厚度。
连铸过程中,测定铸坯凝固壳厚度十分重要,它是用来控制铸造
质量,确保铸件规格及工艺效率的重要工具,从而保证产品的质量。
正确、准确地测定凝固壳厚度可以预防连铸质量问题,减少质量损失。
连铸结晶器温度场及热变形的数值模拟

d fr a o n ra e . T e rt fc o i g w tr h r a n u n e o h e e au e f l d t e a e o t n ic e s h ae o o l ae a g e ti e c n t e tmp rt r ed a h r l m i s n s l f i n m
Nu e ia i u a in o e o ma i n a d tm p r t r m rc lSm lto n d f r t n e e a u e o
i l fc ntnu u a tn u d fed o o i o sc si g m o l
K ANG i L ,W A n g n , HE J—h n NG E —a g i e g c
r t n atn p e n t e tmp r t r ed a d d fr t n o l e n e t ae . T e r s s ae a d c i g s e d o h e e u e f l n e o mai f mod w r i v si td h et s a i o e g e s o e h tw e a t g s e d i c e s s h mp r tr n eo ai n as n r a e . W h n t e m伽 l h w d t a h n c si p e n r a e .te t n e e au e a d d fr t l o ic s s m o e e h d
维普资讯
第 5卷 第 3期
20 0 6年 9月
材
料
与 台 金
学
报
Vo. . 15 No 3 S pt e .20 6 0
大圆坯连铸凝固传热过程的数值模拟

表 1 大圆坯连铸机基本参数
项目单位 /
铸 机 基 本 半径 / m
1 铸坯 中心: ) 为轴对称传热,可视为绝热边界 条件 ,
即
技术参数
1 6
一 l.00 f: r> - 刮 0
一
【 ( 8 J )
( 9 )
【 J
铸坯断面直 径/ m m
结晶器 有效长度/ mm
M AO n —in EN n — h Bi g l g ,R a Bi g z i ,HAN iwe 。 Zh — i,CAO in f n Ja -e g ,FE NG Ke
(. i guSn nE up n o p h n su 2 5 0 , hn ; 1 J n s u a q ime t u ,C agh 15 0 C ia a Gr 2 Na o aE gn e n eerhC ne rrn Sel aigPatnert n C o gig 4 0 1 ,C ia . t n l n ier g sa etro o & teM kn l tgao , h n qn 0 0 3 hn ) i i R c f I nI i
宽板坯连铸结晶器流场和温度场的数值模拟

宽板坯连铸结晶器流场和温度场的数值模拟
随着工业生产技术的不断发展,连铸技术已经成为宽板坯的主要生产方式,特别是在钢铁行业中,大量的钢铁产品均采用连铸工艺生产。
宽板坯连铸技术的核心是结晶器,结晶器的流场和温度场是宽板坯质量的关键因素,因此对流场和温度场进行数值模拟研究是必要的。
数值模拟能够对结晶器内部的流场和温度场进行快速、准确的计算,揭示了结晶器内的流场和温度场在宽板坯生产中的重要作用。
本文通过对结晶器内流场和温度场的数值模拟分析,提出了一种优化结晶器设计的方法。
首先,本文基于Navier-Stokes方程和热传导方程,建立了数学模型,考虑结晶器内部的流动载荷、热辐射、传导热和对流换热等因素。
其次,利用Fluent软件进行流场和温度场计算,得到了流场和温度场的数值解。
通过对数值模拟结果的分析,发现结晶器内部的流动较为复杂,主要存在四个涡旋,其中两个涡旋在底部,两个涡旋在上部。
涡旋的存在使得物料在结晶器内部获得了良好的混合,进一步提高了结晶器内物料的质量。
另外,结晶器内部的温度场也十分关键。
通过数值模拟结果可以看出,结晶器内部温度分布不均匀,底部温度较高,而顶部温度较低。
这是由于底部邻近铸坯熔池温度较高,导致底部结晶器的温度较高;而顶部的散热较快,导致顶部结晶器的温度较低。
最后,通过对数值模拟结果的分析得出,改变结晶器底部的形状,减少对流热损失,可以提高结晶器内部的温度分布均匀性,进而提高宽板坯的质量,同时也可以减少不必要的生产成本。
连铸坯壳厚度和连铸坯表面温度的关系_概述及解释说明
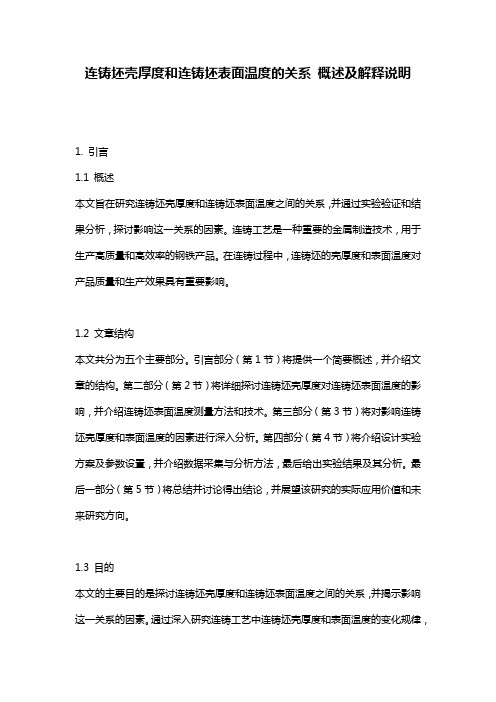
连铸坯壳厚度和连铸坯表面温度的关系概述及解释说明1. 引言1.1 概述本文旨在研究连铸坯壳厚度和连铸坯表面温度之间的关系,并通过实验验证和结果分析,探讨影响这一关系的因素。
连铸工艺是一种重要的金属制造技术,用于生产高质量和高效率的钢铁产品。
在连铸过程中,连铸坯的壳厚度和表面温度对产品质量和生产效果具有重要影响。
1.2 文章结构本文共分为五个主要部分。
引言部分(第1节)将提供一个简要概述,并介绍文章的结构。
第二部分(第2节)将详细探讨连铸坯壳厚度对连铸坯表面温度的影响,并介绍连铸坯表面温度测量方法和技术。
第三部分(第3节)将对影响连铸坯壳厚度和表面温度的因素进行深入分析。
第四部分(第4节)将介绍设计实验方案及参数设置,并介绍数据采集与分析方法,最后给出实验结果及其分析。
最后一部分(第5节)将总结并讨论得出结论,并展望该研究的实际应用价值和未来研究方向。
1.3 目的本文的主要目的是探讨连铸坯壳厚度和连铸坯表面温度之间的关系,并揭示影响这一关系的因素。
通过深入研究连铸工艺中连铸坯壳厚度和表面温度的变化规律,可以为优化生产过程提供指导。
此外,还将通过设计实验并分析实验结果,验证理论模型和推断。
最终,该研究将为钢铁行业相关领域提供较为全面和实用的参考依据。
2. 连铸坯壳厚度和连铸坯表面温度的关系2.1 连铸坯壳厚度对连铸坯表面温度的影响连铸坯壳厚度是指在连铸过程中,在浇注到冷却水中后,铸态钢板外表面所形成的一层冷却壳。
这层壳主要由析出物、氧化物和其他杂质组成。
连铸坯壳厚度对于连铸坯表面温度有着重要的影响。
较薄的坯壳可以提高熔融钢板的传热效率,因为它能够更快地将热量传递给冷却水,并导致较低的表面温度。
此外,薄壳还能有效地减少内部晶界等缺陷,提高连铸坯的质量。
然而,过于薄壳可能会导致传热不足或者产生各种缺陷。
当连铸坯壳过薄时,无法充分吸收冷却水带走的热量,从而使得连铸坯表面温度增加。
同时,在连续注入钢液过程中,由于内部热量继续传递到外壳,必须保证连铸坯壳能够承受这种压力。
连铸结晶器传热实时计算方法的研究

3.2传热反问题结晶器的热行为和铸坯的凝固状态主要受结晶器和坯壳之间复杂的热交换控制,用有效热阻尼,,代表“’。
在传热的正问题计算中,结晶器和铸坯的热阻是作为边界条件提出的,与其他控制方程联立求解后,可得到结晶器和铸坯的温度场分布,再通过与实测温度的对比加以修正,最终求出接近真实情况下的温度分布情况。
而反问题计算则是先通过实测温度确定结晶器与铸坯之间的热阻,计算出更加符合实际的热阻分布情况,再按正问题方法进行传热计算,因此计算得到的温度场也更加真实可靠。
1。
计算时,首先依据经验给局部热阻赋初始值,将利用正问题模型计算出的温度与实测值进行比较,若能满足精度要求则假定热阻为真实热阻;若精度不能满足要求,则需根据计算值与实测值的差值对热阻进行调整,反复迭代直到测点处的计算值与实测值满足要求为止。
本文计算所采用结晶器铜管导热系数为340w・B-1・℃~;密度为8900kg・m一;比热为390J・kg~・℃~。
连铸钢的密度、热容、导热系数的确定方法…1:r.Ps=7402—1.2×【T-TL)kg・m-3(5)<白=666+o.17TJ・kg-1.℃1(6)L-以=1.5×【14.73+o.0125×T)V/・m~・℃1(7)式中,岛、Cs和以分别为连铸钢的密度、比热和导热系数;邢五分别为节点温度和液相线温度。
3.3计算结果验证本文中,将温度计算值与实测温度的收敛误差设为2。
C,当36个热面温度测点的计算误差都小于2"C时,计算停止。
图2(a)为在拉速为2.465m・minl时,距离弯月面不同高度处结晶器温度计算值与实测值的比较。
在该组工艺参数条件下,外弧L2层温度最高,内弧附近区域相对较低。
沿结晶器高度方向,弯月面处温度与热流相对较低,在距弯月面90一110硼区域内温度与热流达到最高值,而后随气隙厚度的增加,结晶器传热减缓,温度与热流的变化逐渐趋于平缓,之后随结晶器锥度的改变,温度与热流略有回升。
7月-连铸初始凝固温度波动数学模拟与解析-连铸自动化研讨会论文(上海大学雷作胜)

连铸初始凝固过程温度波动数学模拟与解析*雷作胜,金小礼,马宁博,任忠鸣,邓康, 钟云波(上海大学,上海市现代冶金与材料制备重点实验室, 上海200072) 摘要通过独特设计的实验测量了结晶器振动过程中,连铸初始凝固点温度变化情况,发现初始凝固点温度存在与结晶器振动相对应的温度波动现象。
一个将结晶器振动考虑进来的三维非稳态传热数学模型的计算结果,也表明该温度波动现象的存在。
另外,传热数学解析表明,在结晶器内侧存在温度波动的情况下,无论有无保护渣,在钢水内部每一点都存在着与表面温度波动频率一致的温度波动,但其幅值随深度的增加而下降;在无保护渣的情况下,表面温度波动在钢水中的渗透深度约为1~2mm;保护渣的存在对温度波动有很大的衰减作用,因而能提高铸坯表面的质量;另外,采用高频率小振幅的振动,降低保护渣导热率,增加保护渣道宽度,都能有效地减小温度波动对初始凝固坯壳的影响。
这一现象可以用来解释现有的一些技术改善铸坯表面质量的原因。
关键词连铸结晶器振动振痕表面质量温度波动The Mathematical Modeling and Analyses on Temperature Fluctuation of Initial Solidified Process in Continuous Casting LEI Zuosheng, JIN Xiaoli, MA Ningbo,REN Zhongming, DENG Kang,ZHONG Yunbo (Shanghai University, Shanghai Key Laboratory of Modern Metallurgy & Material Processing, China) Abstract The Initial Solidified Point (ISP) temperature fluctuation during continuous casting caused by mold reciprocation was measured by a newly developed method. The repeated experiments results show that the ISP temperature varied periodically along with mold oscillation. The phenomena of temperature fluctuation during continuous casting were confirmed by a newly developed 3-dimension non-steady heat transfer mathematical modeling. A one-dimension heat transfer mathematic model shows that when there was a temperature fluctuation in the inner mould wall, there were corresponding temperature fluctuations at every point in the molten steel, whose frequency is the same as the boundary condition and amplitude decreased along with the increasing depth whether there was mould flux between mould and steel or not. The influence depth of surface temperature fluctuation in molten steel is about 1~2 mm when there was no mould flux. The surface temperature fluctuation attenuated rapidly when there was mould flux. Therefore mould flux was helpful to improve the billets surface quality. In addition, high frequency and low amplitude mould oscillation, decrease the thermal conductivity of mould flux and increase the mould flux channel width are all helpful to decrease the influence on early solidified shell caused by surface temperature fluctuation. Based on the phenomenon, the mechanism of how some technologies improve surface quality of continuous casting billets is analyzed. Their common mechanism was the decreasing of the temperature fluctuation of early solidification shell.Key words Continuous casting, Mold oscillation, Oscillation marks, Surface quality, temperature fluctuation.1. 前言随着技术的日益成熟,连铸朝着近终形、高速度、高质量方向发展[1],对铸坯质量的要求不断提高,铸坯表面振痕受到越来越多的关注。
u71mn大方坯凝固坯壳与结晶器铜管温度场的数值模拟
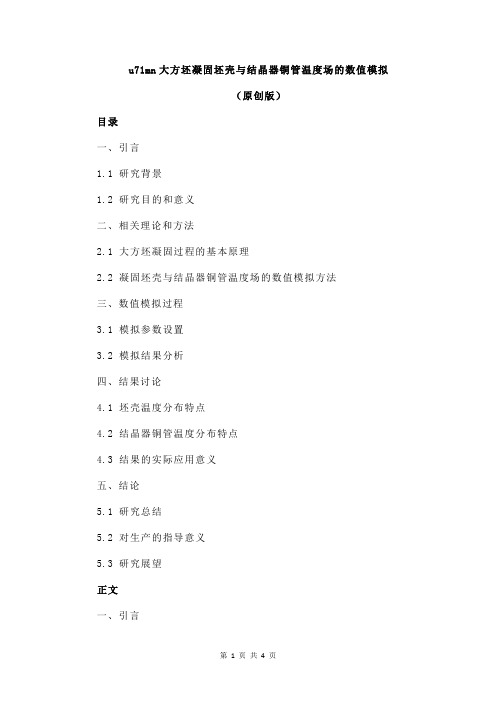
u71mn大方坯凝固坯壳与结晶器铜管温度场的数值模拟(原创版)目录一、引言1.1 研究背景1.2 研究目的和意义二、相关理论和方法2.1 大方坯凝固过程的基本原理2.2 凝固坯壳与结晶器铜管温度场的数值模拟方法三、数值模拟过程3.1 模拟参数设置3.2 模拟结果分析四、结果讨论4.1 坯壳温度分布特点4.2 结晶器铜管温度分布特点4.3 结果的实际应用意义五、结论5.1 研究总结5.2 对生产的指导意义5.3 研究展望正文一、引言1.1 研究背景近年来,我国钢铁工业在产量和质量上取得了显著的成就,大方坯连铸技术在钢铁生产中发挥着重要作用。
大方坯连铸技术是通过连铸机将液态钢水连续浇注成坯壳,然后进行凝固和结晶,最终得到所需的钢材。
在连铸过程中,坯壳与结晶器铜管的温度分布对铸坯的质量和性能具有重要影响。
因此,研究大方坯凝固坯壳与结晶器铜管温度场的数值模拟,对于优化大方坯连铸工艺,提高铸坯质量具有重要的实际意义。
1.2 研究目的和意义本研究旨在通过数值模拟方法,研究大方坯凝固坯壳与结晶器铜管温度场分布特点,为优化大方坯连铸工艺提供理论依据。
通过对比不同参数下的模拟结果,分析其对铸坯质量和性能的影响,为实际生产提供参考。
二、相关理论和方法2.1 大方坯凝固过程的基本原理大方坯凝固过程主要包括液态钢水的连续浇注、坯壳的形成、凝固和结晶过程。
在凝固过程中,钢水与结晶器铜管之间存在热交换,导致温度场的分布。
为了研究这一过程,需要对凝固坯壳与结晶器铜管温度场进行数值模拟。
2.2 凝固坯壳与结晶器铜管温度场的数值模拟方法本研究采用有限元分析(FEA)方法对大方坯凝固坯壳与结晶器铜管温度场进行数值模拟。
首先建立数学模型,包括热传导方程和边界条件。
然后,根据实际生产条件设置模拟参数,如钢水温度、浇注速度、结晶器铜管厚度等。
最后,运用有限元分析软件进行计算,得到温度场分布。
三、数值模拟过程3.1 模拟参数设置本研究根据实际生产条件,设置以下模拟参数:钢水温度为 1500℃,浇注速度为 2m/min,结晶器铜管厚度为 20mm,热传导系数为 5000W/(m·K)。
板坯连铸机结晶器流场数值模拟及结果分析

毕业设计目录摘要············································································································································· - 2 - 英文摘要····································································································································· - 3 - 第一章绪论 ······························································································································· - 4 -1.1结晶器··························································································································· - 4 -1.2结晶器内钢液的流动··································································································· - 4 -1.3结晶器流场的模拟方法······························································································· - 4 -1.4本课题的研究意义、研究内容·················································································· - 5 -1.4.1课题意义············································································································ - 5 -1.4.2本文的主要工作································································································· - 5 - 第二章文献综述······················································································································· - 6 -2.1连铸过程概述··············································································································· - 6 -2.2数值模拟研究现状······································································································· - 6 - 第三章结晶器内流场数学模型的建立··················································································· - 9 -3.1模拟条件······················································································································· - 9 -3.2控制方程······················································································································· - 9 -3.3边界条件的确定··········································································································· - 9 - 第四章模拟计算方法··············································································································- 11 -4.1 GAMBIT ······················································································································- 11 -4.2 FLUENT·······················································································································- 11 -4.3前处理·························································································································- 11 -4.4 求解·····························································································································- 11 -4.5后处理··························································································································- 11 - 第五章计算结果和分析··········································································································- 12 -5.1结晶器内流场基本特征····························································································· - 12 -5.2水口倾角对流场的影响···························································································· - 12 -5.3水口插入深度对流场的影响···················································································· - 13 -5.4拉坯速度对流场的影响···························································································· - 14 - 第六章结论······························································································································- 15 - 参考文献····································································································································- 16 - 致谢············································································································································- 17 -- 1 -李佳:板坯连铸机结晶器流场数值模拟及结果分析板坯连铸机结晶器流场数值模拟及结果分析摘要连铸结晶器过程钢水流动与生产工艺顺序和铸坯质量有密切关系,它不仅涉及到夹杂物分离去除效果和防止保护渣卷入,而且对初生凝固坯壳发育和避免漏钢事故发生具有显著影响。
宽板坯连铸结晶器流场和温度场的数值模拟
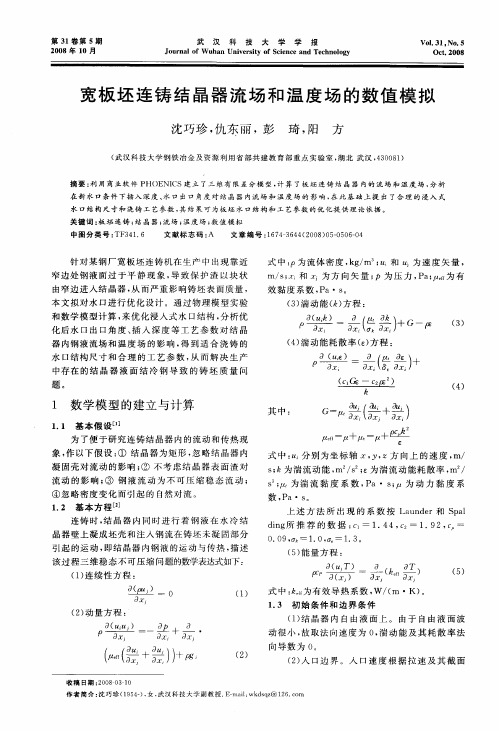
m/ ; 和 z 为方 向矢 量 ; s . P为 压 力 , a 为有 P;
效 黏 度 系 数 , a・ 。 P S
本 文拟对 水 口进行 优化设 计 。通 过物理 模 型实验
和 数学模 型计 算 , 来优 化 浸入式 水 口结 构 , 析优 分 化后 水 口出 口角 度 、 入 深 度 等工 艺 参 数 对结 晶 插 器 内钢液 流场 和 温度 场 的 影 响 , 到 适 合 浇铸 的 得 水 口结 构尺寸 和 合理 的工 艺参 数 , 而 解 决 生产 从
面积 给出 , 浇铸温 度 为 T 一15 0℃。 。 4
( ) 称 面 。对 称 面上 的 边 界 条件 与液 面 处 3对
收 稿 日期 : 0 80 0 2 0 — 31
作者 简 介 : 巧 珍 ( 9 4)女 , 汉 科技 大学 副 教 授 . — i: dq@ 1 6 Cr 沈 1 5一 , 武 E malwk sz 2 .O n
20 0 8年 第 5期
沈 巧珍 。 : 等 宽板 坯 连 铸 结 晶 器 流 场 和 温 度 场 的 数 值 模 拟
( ) 量方 程 : 2动
1 D
,
一 一矗 + . 十 ’
一 一
动很小 , 故取 法 向速度 为 0 湍 动 能及 其 耗 散 率法 ,
( 0+ a) P z ) g u u + , ,
d
向导数 为 0 。
() 2 ( ) 口边 界 2入
。
入 口速度 根 据 拉 速 及 其截 面
针对 某钢 厂宽板 坯连铸 机在 生产 中出现 靠近 窄边 处钢 液面 过 于平 静 现 象 , 导致 保 护 渣 以块 状 由窄边进 入结 晶器 , 而严 重影 响铸坯 表 面质量 , 从
1连铸坯的凝固及其控制汇总

3
315
VAI
合计
36
54
约5500
1)
鞍钢第三炼钢连轧厂工艺流程
转炉 LF炉 RH炉
中包
结晶器
连铸机
步进梁式 加热炉
粗轧机
保温罩 飞 剪
精轧机组
层流冷却 卷取 机
除
除
鳞
鳞
1.2 连铸坯的凝固
➢ 要获得性能优良的铸件,首先就要在工艺上进行 控制获得高质量的铸件,同样的道理,连铸坯质 量也是科技工作者研究的重要课题。
➢ 连铸生产的产品包括:圆钢坯、方坯、板坯以及 各种近终形产品(薄带、异型坯等)。采用连铸 坯取代模铸作轧材,从工艺角度来讲,明显提高 了钢材的收得率,因为连铸工艺完全消除了浇注 系统及冒口切损问题,使得成材率提高约 10%~15%。
铸件宏观组织分布示意图
一、拉速控制
➢ 在保证铸坯质量和安全生产的前提下,拉速主要 受铸坯凝固速度的制约。
连续铸造简图
核心设备:结晶器,二冷设备
钢包 中间包
结晶器 二冷段
空冷段 矫直段
一机四流、一机两流 连铸小方坯
连续铸钢的发展
➢ 连续铸钢技术经历了20世纪40年代的试验开发, 50年代开始步入工业生产阶段,60年代出现弧形 连铸机,经过70年代的大发展,80年代日趋成熟 和90年代的一场新的变革,直到今天,经历了70 年的发展历程。众多专家学者致力于连铸技术及 连铸坯质量的研究。当前,连续铸钢已向薄板坯 连铸连轧、异形坯连铸和高速连铸等高效节能的 高附加值产品的方向发展。
I II
I III
I II
θ
连铸坯及其结晶器的纵剖面温度显示
思考题
➢ 1板坯纵裂是怎样形成的?怎样预防? ➢ 2什么是脱方缺陷,会带来什么影响,怎样
宽板坯连铸结晶器三维流场与温度场的数值模拟的开题报告

宽板坯连铸结晶器三维流场与温度场的数值模拟的开题报告一、选题背景和意义宽板坯连铸技术目前已在钢铁工业的生产中广泛应用。
连铸过程中,结晶器的性能直接影响铸坯的质量和表面质量。
因此,研究宽板坯连铸结晶器内部的流场与温度场,对提高宽板坯连铸的生产效率和质量具有重要的意义。
目前,结晶器内部流场与温度场的研究主要依赖于实验方法,但实验成本高、周期长,而且实验过程存在难以控制的因素。
因此,采用数值模拟方法,结合计算机技术,可以有效地研究结晶器内部流场与温度场。
二、研究内容和方法本文主要研究宽板坯连铸结晶器内部的流场与温度场,依据宽板坯连铸结晶器的结构特点,建立三维流场模型和温度场模型。
对结晶器内部的流动和传热过程进行模拟,得到流体运动状态和液相/固相相变过程的温度分布规律,并分析钢坯内部组织结构的变化。
本文计划采用计算流体力学(CFD)方法,结合有限元法(FEM)对宽板坯连铸结晶器内部的流场与温度场进行数值模拟。
具体操作分为以下几个步骤:1. 根据实际情况建立宽板坯连铸结晶器模型,并确定模拟的范围和边界条件。
2. 进行网格划分,将结晶器模型离散化,生成计算网格。
3. 根据有限元法和控制方程建立数学模型,并进行求解。
4. 根据计算结果分析流场和温度场内部的变化规律,展开数值仿真计算。
三、研究目标和预期成果1. 建立宽板坯连铸结晶器的三维流场和温度场数学模型。
2. 对结晶器内部的流动和传热过程进行数值模拟,得到流体运动状态和液相/固相相变过程的温度分布规律,并分析钢坯内部组织结构的变化。
3. 在数值模拟的基础上,对结晶器内部的结构参数和工艺参数进行优化和分析,提高铸坯的质量和表面质量。
预期成果:基于数值模拟技术对宽板坯连铸结晶器结构参数和工艺参数进行优化和分析,提高铸坯的品质和表面质量。
四、工作计划和进度安排本研究计划分为以下四个阶段:1. 研究阶段一(前期准备阶段)、制定计划和开题报告、收集文献资料,2022年9月-11月完成。
R9m连铸机小方坯结晶器流场和温度场的数值模拟

度 00 62k /m・) 导热 系数 3 ( K)热 膨胀 . g( s ; 0 4W/m・ ;
系数 0 0 K 。 . 01 ~ 0 21 基 本假设 .
A otl i 人耦合 计算 了结 晶器 内流场 、 buae 等 b 温度 场 以
及溶 质 的输运 行 为 , 算得 到 的结 果与试 验 测量 数 计
生 凝 固坯 壳厚 度 降低 。伴 随着 水 口浸入 深 度 的增 加, 内外 弧侧环 流 区均逐 渐增 大 。较 浅 的浸入 深度 导致 环 流区未 获得很 好 的发展 , 钢水 向上 回流速度 快 , 晶器 中钢 液 面易受 强烈 扰 动 , 成卷 渣 。 浸 结 造
收敛 标准要 求 , 各节 点质量残差 控制在 R S 0 。 M <1~
况, 分析 了不 同条件下 的结晶器 内流场 、 面波动 、 液 温度 分布及坯 壳厚度 。结 果表明 , 较小尺寸和浸入 深度 的水 口作用 在 下, 钢液对外弧壁面 的冲刷作用 明显 , 易降低 结晶器寿命 。随着水 口内径 和浸入深度 的增大 , 钢液面扰动减弱 , 易于防止卷
渣 。试验 条件下 , 采用 3 n 0I n内径水 口、0 10mm浸入深度较为合理。 关键词 : 小方 坯结晶器 ; 浸人式水 日; 流场 ; 温度场 ; 数值模拟
徐 永斌 , 马春武 , 幸 伟, 徐海伦
( 中冶南方T程技术有 限公 司 技术研究 院, 湖北 武汉 4 0 2 ) 3 2 3 摘 要 : 用 A S SC X 1 .软件 , 采 N Y F 21 对结晶器浸入式水 口的尺 寸和浸入深度进行建模 , 研究 了相应 的流场 和温度场分布情
23 数值求解 .
考 虑铸 坯 流 场 和 温度 场 分 布 的 对称 性 , 1 以 / 2 结 晶器 为模型 , 利用 A S SC X1.软件计算 。收 N Y F 21
- 1、下载文档前请自行甄别文档内容的完整性,平台不提供额外的编辑、内容补充、找答案等附加服务。
- 2、"仅部分预览"的文档,不可在线预览部分如存在完整性等问题,可反馈申请退款(可完整预览的文档不适用该条件!)。
- 3、如文档侵犯您的权益,请联系客服反馈,我们会尽快为您处理(人工客服工作时间:9:00-18:30)。
件. 设开浇时刻 ( t = 0) 已存在钢液的温度为浇注温
度 ;在浇注过程中 ,所有新浇入的钢液温度为浇注温
度 ,则初始条件已知.
依据结晶器与坯壳的接触模型 , 设定如下的边
界条件.
(i) 铸坯/ 铜板边界 :
-
kc
5 Tc 5r
=
-
ks
5 Ts 5r
=
qc .
(ii) 铸坯中心 :
-
ks
5 Ts 5r
由于计算结果是温度场的离散值 , 并没有直接 得到凝固壳厚度分布 , 因此需要对温度场采用一种 办法进行处理得到凝固壳厚度分布. 大多数研究者 直接取一个在液相线和固相线之间的经验温度值来 处理. 此方法固然简单 , 但是没有考虑到材料成分 的影响. 本文考虑了钢液中碳含量的影响 , 采用 Scheil 方程计算固相率得到坯壳厚度 , 即任意取得 一个面 ,如果能够在离散化的温度场上计算出固相 率 f s 等温线 ,以 f s = 017 为分界线 ,则从 f s = 017 处 直线到外边界的距离就是凝固壳的厚度.
2 模型验证
为校核与验证模型计算结果的可靠性 ,结晶器 温度计算的结果直接可以通过实测的数据进行验 证. 图 1 和图 2 是拉速为 2 m·min - 1 ,在其他工艺参
图 1 结晶器温度计算值与实测值比较曲线 Fig. 1 Comparison of the calculated with measured values of mould temperature
272
钢水密度/ ( kg·m - 3) 7 200
碳质量分数/ %
0136
液相线温度/ ℃ 1 500 铸坯比热容/ (J ·kg - 1 ℃- 1) 680
固相线温度/ ℃ 1 445 导热系数/ ( W·m - 1 ℃- 1) 34
第四排测点 ,即高度为 280 mm 处 , 测量热流又相对 有所回升. 经分析发现高度在 300 mm 左右 ,刚好是 结晶器锥度改变处. 结晶器采用这种特殊的锥度设 计 ,使得从此部位以下形成的气隙宽度减少而引起 热流略有回升. 在结晶器出口处热流的回升 , 是由 于此时铸坯结晶器之间的渣膜大部分呈现固态 , 固 态渣膜尤其是玻璃态的渣膜具有良好的导热性能 , 加速了铸坯向结晶器传热所致.
根据铸坯的温度场 , 由 平 衡 方 程 和 Scheil 方 程[10]分别计算出铸坯的固相率与坯壳厚度如图 5 和图 6 所示. 图 5 是由 Scheil 方程计算得到的内弧 处固相率分布图. 由图 5 可知 , 铸坯根据固相率可 分为三个区 : f s ≤013 划为液相区 , f s ≥017 划为固 相区 ,两固相率之间为液固两相区 ,以初步估算坯壳 的厚度. 图 6 (a) 是结晶器出口内弧处铸坯固相率沿
1 模型描述
根据圆坯形状的对称性特点 , 在圆柱坐标系内 建立传热模型. 首先对铸坯温度场计算模型作如下 假设 :
(1) 铸坯传热以热传导方式为主 , 钢液流动对 传热的影响通过增大钢液导热性来体现 ;
(2) 铸坯为不可压缩材料 , 忽略因粘滞行为而 引起的能耗 ;
收稿日期 : 2006207215 修回日期 : 2006209226 基金项目 : 教育部科技研究重点项目 (No . 03051) 作者简介 : 姚 曼 (1962 —) ,女 ,教授 ,博士
数相同条件下 ,计算的结晶器温度 、热流与实际测量 温度 、热流数据平均值的比较曲线. 其中 , 图 1 中 C 表示结晶器的冷面 , H 表示结晶器的热面.
由图 1 和图 2 对结晶器温度和热流进行比较 , 计算值和实测值大致吻合 , 曲线变化趋势相似. 在 弯月面区域 ,坯壳快速冷凝收缩 ,在铸坯与结晶器之 间很快出现了气隙 ,使得铸坯与结晶器迅速脱离 ,因 此这里热流不大. 随着铸坯向下移动 , 钢液静压力 的作用将铸坯重新压回结晶器 ,使得气隙减小 ,致使 热流迅速升高 , 在第二排测点高度附近达到最大.
图 5 由 Scheil 方程计算的铸坯凝固率分布 Fig. 5 Distribution of solidif ied fraction in the round billet calcu2 lated by the Scheil equation
图 6 结晶器出口处固相率沿半径方向的分布( a) 和坯壳厚度沿 结晶器纵向的变化( b) Fig. 6 Distribution of solidif ied fraction in the round billet at the outlet of the mould ( a) and shell thickness along the mould ( b)
图 3 不同高度位置( a) 和半径( b) 圆坯温度沿纵向变化 Fig. 3 Longitudinal distribution of temperature in the round billet at different heights ( a) and different radii ( b)
第 29 卷 第 11 期 2007 年 11 月
北京科技大学学报 Journal of University of Science and Technology Beijing
Vol. 29 No. 11 Nov. 2007
圆坯连铸结晶器温度场模拟与坯壳厚度预测
姚 曼1) 詹慧英1) 王旭东1) 郭亮亮1) 尹合壁1) 刘 晓2) 于 艳2)
=
0.
(iii) 铸坯/ 保护渣边界 :
-
ks
5 Ts 5z
=
-
kf
5 Tf 5z
=
(
Ts
-
Tf) / R .
式中 , h 为对流换热系数 , k 为导热系数 , qc 为单位 时间单位面积上坯壳通过结晶器传出的热量 , 脚标
c 、f 和 s 分别表示结晶器 、渣 、铸坯 , R 为渣/ 钢界面
接触热阻.
表 1 基本条件及主要工艺参数 Table 1 General conditions and main process parameters
参数
数值
参数
数值
结晶器长度/ mm 780
浇注温度/ ℃
1 523
结晶器厚度/ mm 15
拉速/ ( m·min - 1)
210
圆坯直径/ mm
178
潜热/ ( kJ ·kg - 1)
目前我国已经建设了多台圆坯连铸机 , 而现有 文献的报道常集中在板坯和方坯方面[4- 6 ] , 对圆坯 结晶器内凝壳规律研究不多. 且通常用于预测坯壳 厚度的平方根定律也只是适用于板坯等平面一维的 凝固过程[7 ] ,对于圆坯并不适用. 针对此种情况 , 本 文建立三维圆坯结晶器传热模型 , 计算得到结晶器 与铸坯的温度场 ,并利用实测温度数据进行了验证. 通过固相率的计算获得了坯壳厚度分布状况 , 并分 析了主要参数对结晶器出口处坯壳厚度的影响 , 同 时对利用模型与经验公式计算出的坯壳厚度进行了 对比和分析.
图 4 结晶器与铸坯温度场分布 Fig. 4 Temperature f ields of the mould and round billet
312 铸坯固相率分布与坯壳厚度计算 固相率控制着整个钢液的凝固进程 , 计算中用
到的许多变量都与它相关 ,如凝固潜热的释放 、导热 系数等. 固相率不仅与温度有关 , 而且与材料的成 分相关[9 ] . 由于连铸坯壳在凝固过程中受不同冷却 条件的影响 ,因此非平衡凝固存在于整个凝固过程 中. 同时 ,由于在凝固过程中部分组元在液相中富 集 ,影响了液相线温度. 所以 , 固相率也是精确预测 组织性能的一个重要参数[9 ] .
图 4 中用渐变色显示了圆坯连铸结晶器与铸坯
第 11 期
姚 曼等 : 圆坯连铸结晶器温度场模拟与坯壳厚度预测
·1093 ·
温度场分布 ,左侧与右侧分别为结晶器与铸坯的温 度标示. 由图 4 可以看出 , 铸坯内温度的变化在 1 523~1 000 ℃之间. 弯月面附近的铸坯温度最高 , 接近钢水浇注温度 , 再往下沿拉坯方向温度逐渐 降低.
半径方向的分布. 由图 6 (a) 可知 , 平衡方程计算得 到的固相率比 Scheil 方程的稍高. 这是由于平衡方 程假设固液相均完全混合 , 实际铸坯凝固时固相只 能以有限扩散方式进行. 本文采用 Scheil 方程计算 得到固相率. 图 6 (b) 是坯壳厚度沿结晶器纵向变化 曲线. 由图可知 ,最终坯壳厚度大约在 20 mm 左右.
图 2 结晶器热流密度计算值与实测值比较曲线 Fig. 2 Comparison of the calculated with measured values of mould heat flux
3 计算结果分析
311 结晶器内铸坯温度场分布 对表 1 中给出的计算条件进行数值模拟. 图 3 (a) 所示是在不同半径处铸坯温度沿结晶
(3) 开浇时结晶器钢水温度为浇注温度 ;
(4) 铸坯是稳态导热并以拉速 V 匀速运动.
111 传热微分方程
在温度场计算中 ,采用三维计算模型 ,圆柱坐标
系传热基本方程为 :
15T α 5τ
=
15T r 5r
+
52 5
T r2
+
1 52 T r2 5Φ2
+
52 T 5 z2
+
Q
(1)
式中 , α , W ·
m - 1 ℃- 1 ; C 为比热容 ,J ·kg - 1 ℃- 1 ;ρ为密度 , kg·
m - 3 ; r 、Φ 和 z 为圆柱坐标系三个方向的坐标 , m ;
T 为温度 , ℃; Q 为潜热 , kJ ·kg - 1 . 本文中采用温
度回升法[8 ]进行处理.