汽轮机叶片加工方法
汽轮机叶片设计
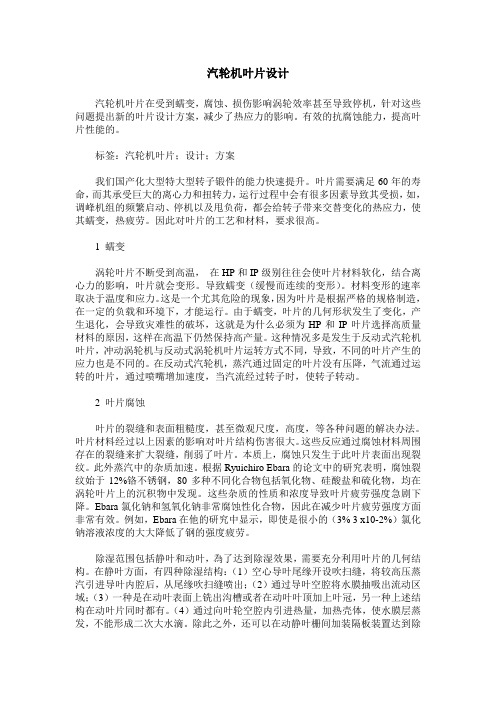
汽轮机叶片设计汽轮机叶片在受到蠕变,腐蚀、损伤影响涡轮效率甚至导致停机,针对这些问题提出新的叶片设计方案,减少了热应力的影响。
有效的抗腐蚀能力,提高叶片性能的。
标签:汽轮机叶片;设计;方案我们国产化大型特大型转子锻件的能力快速提升。
叶片需要满足60年的寿命,而其承受巨大的离心力和扭转力,运行过程中会有很多因素导致其受损,如,调峰机组的频繁启动、停机以及甩负荷,都会给转子带来交替变化的热应力,使其蠕变,热疲劳。
因此对叶片的工艺和材料,要求很高。
1 蠕变涡轮叶片不断受到高温,在HP和IP级别往往会使叶片材料软化,结合离心力的影响,叶片就会变形。
导致蠕变(缓慢而连续的变形)。
材料变形的速率取决于温度和应力。
这是一个尤其危险的现象,因为叶片是根据严格的规格制造,在一定的负载和环境下,才能运行。
由于蠕变,叶片的几何形状发生了变化,产生退化,会导致灾难性的破坏,这就是为什么必须为HP和IP叶片选择高质量材料的原因,这样在高温下仍然保持高产量。
这种情况多是发生于反动式汽轮机叶片,冲动涡轮机与反动式涡轮机叶片运转方式不同,导致,不同的叶片产生的应力也是不同的。
在反动式汽轮机,蒸汽通过固定的叶片没有压降,气流通过运转的叶片,通过喷嘴增加速度,当汽流经过转子时,使转子转动。
2 叶片腐蚀叶片的裂缝和表面粗糙度,甚至微观尺度,高度,等各种问题的解决办法。
叶片材料经过以上因素的影响对叶片结构伤害很大。
这些反应通过腐蚀材料周围存在的裂缝来扩大裂缝,削弱了叶片。
本质上,腐蚀只发生于此叶片表面出现裂纹。
此外蒸汽中的杂质加速。
根据Ryuichiro Ebara的论文中的研究表明,腐蚀裂纹始于12%铬不锈钢,80多种不同化合物包括氧化物、硅酸盐和硫化物,均在涡轮叶片上的沉积物中发现。
这些杂质的性质和浓度导致叶片疲劳强度急剧下降。
Ebara氯化钠和氢氧化钠非常腐蚀性化合物,因此在减少叶片疲劳强度方面非常有效。
例如,Ebara在他的研究中显示,即使是很小的(3% 3 x10-2%)氯化钠溶液浓度的大大降低了钢的强度疲劳。
汽轮机叶片几何建模和网格划分采取的设计方法步骤

汽轮机叶片几何建模和网格划分采取的设计方法步骤1.叶片几何建模:(1)确定叶片的轴向布局:根据汽轮机的设计要求和工况参数,确定叶片的位置、数量和布局形式。
(2)确定叶片的主要几何尺寸:包括叶片根部和尖部的宽度、厚度、弯度曲率等关键参数。
(3)确定叶片的截面形状:根据汽轮机的工况要求和流体力学性能要求,确定叶片的截面曲线形状,常见的有矩形、椭圆形、轮廓线等。
(4)构建叶片整体几何模型:根据叶片的轴向布局和主要几何尺寸,构建叶片的整体三维几何模型,通常使用CAD软件进行建模。
2.叶片网格划分:(1)准备网格划分工具:选择适合的流体力学分析软件和网格划分工具,如ANSYS Fluent、NUMECA等。
(2)预处理:导入叶片几何模型,进行预处理操作,如清理模型、修复几何错误、切割几何体等。
(3)网格生成:根据汽轮机叶片的几何模型和工况要求,通过网格生成工具生成初始网格。
常用的网格划分方法有结构化网格和非结构化网格。
(4)网格优化:对初始网格进行优化处理,以改善网格质量,并满足流体力学计算的要求。
通常通过剖分和加密网格来实现。
(5)边界条件划定:根据汽轮机的工况要求,对叶片的边界条件进行划定,如壁面边界条件、进出口边界条件等。
(6)验证和修正:对生成的叶片网格进行验证,如检查网格划分的质量和流体力学计算的准确性,并根据需要进行修正和优化。
以上是汽轮机叶片几何建模和网格划分的基本设计方法步骤。
需要注意的是,叶片几何建模和网格划分的精度和合理性对汽轮机的性能和工作效率有着重要影响,因此在实际设计过程中需要进行反复验证和优化,确保叶片流动特性的准确性和稳定性。
汽轮机叶片毛坯形式的选取及其加工余量的确定
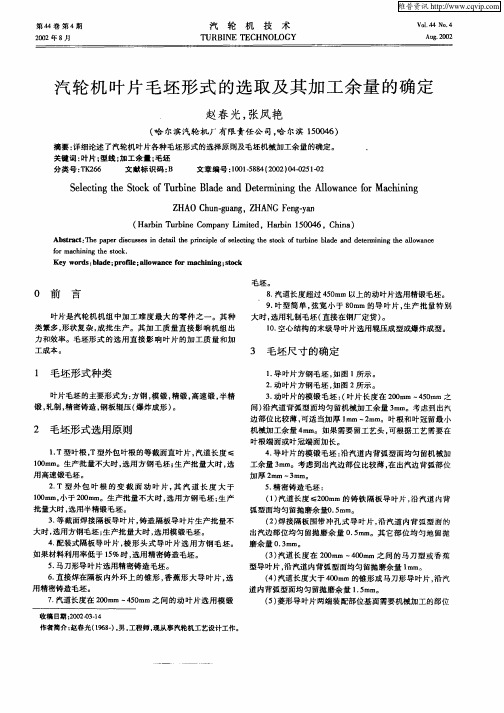
S lc n eSo k o ubn ld n eemiigteA l n efr c iig eet gt tc f r ieB a ea dD tr nn l wa c hnn i h T h o o Ma
Z HAO Ch n g a g HANG e g y h u —u n ,Z F n —a
fr ma h n n h t k. o c i gteso i c
Ke r s b a e; r fl a l wa c o a h n n so k y wo d : l d p o e; l i o n e f r m c i i g:t c
毛坯 。
0 前
言
8 汽道 长度超过 4 0 . 5 mm 以上 的动叶 片选用 精锻毛坯 。 9 叶 型简 单 , 宽 小 于 8 rm 的导 叶 片 。 . 弦 0 a 生产 批量 特 别 大时 , 选用轧制 毛坯 ( 接在 钢厂定货 ) 直 。 l. 0 空心 结构 的末级导 叶片选用辊 压成型或爆 炸成 型 。
叶片是汽轮 机机 组 中加 工难 度 最 大 的零件 之 一 。其 种
类 繁多 , 复杂 , 批 生产 。其 加 工 质 量直 接影 响 机组 出 形状 成
力 和效 率。毛坯形式 的选 用直 接影 响叶 片 的加 工质 量 和加
工成本 。
3 毛坯尺 寸 的确 定
1导 叶片 方钢毛坯 , 图 l所示 。 . 如 2 动 叶片 方钢 毛坯 , 图 2所 示 。 . 如
用 精密铸造毛 坯。
出汽边部位 均匀 留抛 磨 余量 05 m。其 它部 位均 匀地 留抛 .m
磨 余量 0 3 m。 .r a () 3 汽道 长度 在 2 0 m ~4 0I i 间 的马 刀型 或 香蕉 0r a 0I 之 l f 型导叶片 , 汽道 内背弧 型面均匀 留抛 磨余量 1 m。 沿 m () 4 汽道长度 大 于 4 0 0 mm的锥形 或 马刀形导 叶片 , 沿汽 道 内背弧型面均 匀 留抛磨 余量 15 m。 .r a () 5 菱形导 叶片两端 装配部 位基面需 要机械加工 的部位
汽轮机叶片设计和几何成型方法综述
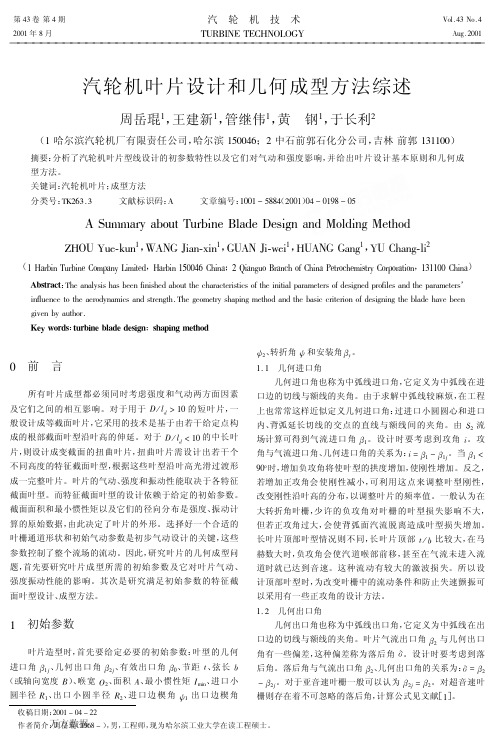
汽轮机叶片设计和几何成型方法综述
周岳琨#, 王建新#, 管继伟#, 黄 钢# , 于长利!
(# 哈尔滨汽轮机厂有限责任公司, 哈尔滨 #)""%’;! 中石前郭石化分公司, 吉林 前郭 #*##"")
摘要: 分析了汽轮机叶片型线设计的初参数特性以及它们对气动和强度影响, 并给出叶片设计基本原则和几何成 型方法。 关键词: 汽轮机叶片; 成型方法 分类号: +,!’* - * 文献标识码: . 文章编号: (!""#) #""# $ )((% "% $ "#&( $ ")
收稿日期: !""# $ "% $ !!
" 前
言
# 初始参数
角有一些偏差, 这种偏差称为落后角 #。设计时要考虑到落 后角。落后角与气流出口角!! 、 几何出口角的关系为: # Z!! $!! % 。对于亚音速叶栅一般可以认为 !! % Z!! 。对超音速叶 栅则存在着不可忽略的落后角, 计算公式见文献 [#] 。
# $
#
#
)
式中, ( 1) 、 ( 1) 为叶片 *3 、 /3 为叶片根部截面面积和半径; * / 任意截面面积和半径; % 为叶片材料许用拉应力; $ 为角速 度; 为叶片材料比重。 3 为重力加速度; # 在选定了同一转速下高度相近的叶片作为参考叶片后, 设计新叶片的顶部叶型面积, 推荐下面的计算公式: [! *! % ] 式中, 3 $!( / 1! 4 1$ ) *$ , *! 为新叶片顶部面积; 1! 为新叶片 高度; 1$ 为参考叶片高度; *$ 为参考叶片顶部面积。 !!5 进出口边楔角 叶片进口边楔角 (或进口包含角) 背弧延 &! 是进口内、 长切线间的夹角。叶片出口边楔角 (或出口包含角) &# 是出 口内、 背弧延长切线间的夹角。&! 、 叶型最大 /# 、 &# 是和 /! 、
汽轮机叶片制造工艺过程

轴流式蒸汽轮机动叶片制造工艺简述摘要:介绍了汽轮机等截面直叶片、自由成型叶片、有成型规律叶片汽道加工的毛坯制造、型面加工工艺过程,并介绍了五联动加工中心的基本特点,简单说明了汽轮机叶片几种特种加工方法的基本原理。
关键字:汽轮机动叶片毛坯制造加工工艺特种加工一:汽轮机简介汽轮机是将蒸汽的能量转换为机械功的旋转式动力机械,是蒸汽动力装置的主要设备之一。
主要用作发电用的原动机,也可直接驱动各种泵、风机、压缩机和船舶螺旋桨等。
还可以利用汽轮机的排汽或中间抽汽满足生产和生活上的供热需要。
汽轮机是一种高温高压高速旋转的机械,尤其对于发电用汽轮机来说,又是大功率输出地原动力机械,所以设计要求汽轮机具有高效率,高安全可靠性,而且可调性要好。
目前我国发电用汽轮机以300~600MW居多,体积庞大,结构精细复杂。
由于多级轴流式汽轮机绝热焓降大,能够充分利用蒸汽的热能,因此绝大多数为发电用汽轮机均为多级轴流式汽轮机。
汽轮机本体主要由转动部分和静止部分两个方面组成。
转子包括主轴、叶轮、动叶片和联轴器等。
静子包括进汽部分、汽缸、隔板和静叶栅、汽封及轴承等。
因此汽轮机的制造工艺主要为上述部件的制造工艺。
汽轮机制造工艺的特点为:属单件生产,生产期长,材料品种多,材料性能要求高,零件种类多,加工精度高,设备要求高,操作技能要求高,机械加工工种齐全,设计冷热工艺且面广,检测手段齐备要求高,计量设备、测量工具齐全而且要求高采用专门工装多。
二:轴流式蒸汽轮机动叶片制造工艺1:叶片的结构静叶片一般由工作部分和安装部分组成动叶片一般由叶根、叶型部分和叶顶三部分组成2:叶片的工作条件及材料选择叶片的工作条件复杂,除因高速旋转和气流作用而承受较高的静应力和动应力外,还因其分别处在过热蒸汽区、两相过渡区、和湿蒸汽区段内工作而承受高温、高压、腐蚀和冲蚀作用。
因此叶片的材料要满足以下要求:良好的常温和高温机械性能、良好的抗蚀性、良好的减震性、和一定的耐磨性良好的冷热加工性能。
叶片中汽轮机低压缸二级动锁叶片机械加工工艺及其型线数控加工工艺的分析
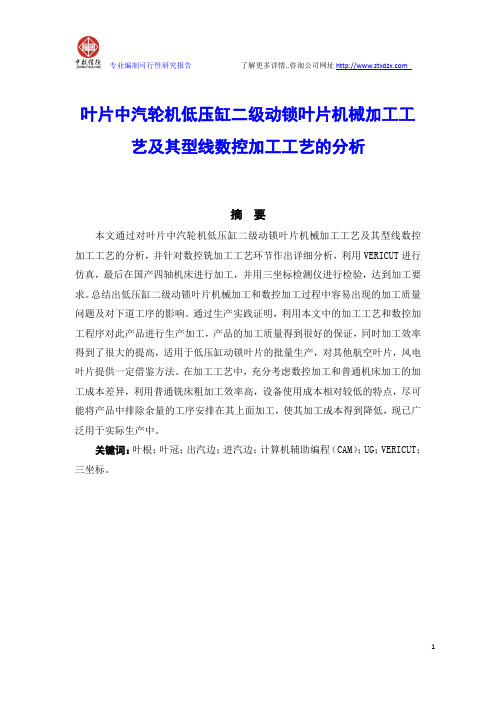
叶片中汽轮机低压缸二级动锁叶片机械加工工艺及其型线数控加工工艺的分析摘要本文通过对叶片中汽轮机低压缸二级动锁叶片机械加工工艺及其型线数控加工工艺的分析,并针对数控铣加工工艺环节作出详细分析,利用VERICUT进行仿真,最后在国产四轴机床进行加工,并用三坐标检测仪进行检验,达到加工要求。
总结出低压缸二级动锁叶片机械加工和数控加工过程中容易出现的加工质量问题及对下道工序的影响。
通过生产实践证明,利用本文中的加工工艺和数控加工程序对此产品进行生产加工,产品的加工质量得到很好的保证,同时加工效率得到了很大的提高,适用于低压缸动锁叶片的批量生产,对其他航空叶片,风电叶片提供一定借鉴方法。
在加工工艺中,充分考虑数控加工和普通机床加工的加工成本差异,利用普通铣床粗加工效率高,设备使用成本相对较低的特点,尽可能将产品中排除余量的工序安排在其上面加工,使其加工成本得到降低,现已广泛用于实际生产中。
关键词:叶根;叶冠;出汽边;进汽边;计算机辅助编程(CAM);UG;VERICUT;三坐标。
目录一、低压缸动锁叶片加工工艺分析以及工序制定。
(1)(一)低压缸动锁叶片加工工艺分析。
(1)(二)低压缸动锁叶片加工工序制定。
(2)二、低压缸动锁叶片型线数控铣加工工艺分析及制定。
(12)(一)低压缸动锁叶片型线数控铣加工工艺分析。
(12)(二)低压缸动锁叶片型线数控铣加工工艺制定。
(12)三、VERICUT仿真检验 (34)四、三坐标型线检测: (37)结束语 (40)参考文献 (41)致谢 (42)汽轮机中低压缸动锁叶片是将高压高温气流通过进汽侧出汽侧带动汽轮转动,是机汽轮机设备中的核心部件,它的加工质量的好坏直接影响汽轮机工作效率,特别是其型线的加工精度要求很高,叶片型线的实际几何形状与设计尺寸越逼近,则汽轮机能量转换过程中的能耗就越少,其工作就越稳定。
在当今环保理念的倡导下,节约能源是全世界企业的责任,所以研究压缸锁叶片的加工工艺和方法,对汽轮机的发展有很大的促进作用。
汽轮机叶片

汽轮机叶片选材及工艺制订(徐州工程学院08材控卢辉20080607146郭淇源20080607147 )叶片的服役条件a)每一级叶片的工作温度都不相同;b)工作在高温、高压、高转速或湿蒸汽区等恶劣环境中,经受着离心力、蒸汽力、蒸汽激振力、腐蚀和振动以及湿蒸汽区高速水滴冲蚀的共同作用;c)汽轮机在工作过程中,动叶片承受着最大的静应力、动应力和交变应力。
对叶片材料性能的要求:a)应具有足够的室温和高温机械性能;b)良好的耐蚀性和抗冲蚀性;c)良好的减振性;d)高的断裂韧性;e)优良的冷、热加工工艺性能。
(1)銘不锈钢,lCrl3和2Crl3:热处理工艺:在调质状态下使用。
lCrl3: 1000〜1050C油淬,700〜750C回火;2Crl3: 950~1000C 油淬,640、720C 回火,金相组织:lCrl3:回火索氏体+少量铁素体;2Crl3:回火索氏体。
优点:在室温和工作温度下具有足够的强度,还具有很好的耐腐蚀性能和减振性。
缺点:当温度超过500C时,热强性明显下降,使用工作温度在450~500C以下。
lCrl3钢若锻造或淬火温度过高,奥氏体晶粒粗大,有大量块状铁素体生成,振动衰减率和冲击韧性降低。
銘不锈钢抗水冲蚀的能力较差。
(2)强化型銘不锈钢牌号1: 2Crl2NiMolWlV2Crl2NiMolWIV钢作为GB8732—88《汽轮机叶片用钢》标准的一个专用钢种和GB1221 标准中的2Crl2NiMoIWIV钢种相比,其Cr. Mo. W. V和P. S的含量控制范围要求更严格一些,从而中和力学性能也更好一些,两种钢的化学成分。
热处理规范及力学性能指标的比较见表1和表2表1 2 Crl2NiMolWlV 钢和2 Crl2NiMoWV 钢化学成份表2 2 Crl2NiMolWlV钢和2 Crl2NiMoWV钢处理规范和力学性能(3)低合金珠光体耐热钢牌号:20CrMo> 24CrMoV该类钢特点是合金元素含量较低,比较经济,工艺性能良好,经过调质处理后强度、塑韧性都比较满意,主要用于制造在450C以下的中压汽轮机的压力级各级动叶片和隔板静叶片。
汽轮机的叶片加工工艺过程

汽轮机的叶片加工工艺过程
汽轮机的叶片加工工艺过程主要包括以下几个步骤:
1.叶片设计:根据汽轮机的使用要求,选择合适的叶片材料、形状和尺寸,并进行CAD图纸设计。
2.叶片制模:制作叶片模具,一般采用数控加工中心或电火花加工机完成。
3.叶片铸造:根据叶片模具进行熔炼和铸造,一般采用熔模法或精密铸造法完成。
4.叶片抛光:将铸造好的叶片进行表面抛光,使其表面光洁度达到要求。
5.叶片修整:对铸造完毕的叶片进行尺寸修整和检验,标记质量合格的叶片。
6.叶片装配:将质量合格的叶片与转子进行装配,用螺栓等固定在合适的位置,形成完整的汽轮机转子部件。
在这个过程中,需要使用一些特殊的工具和设备,如数控加工中心、电火花加工机、熔模炉、抛光机等。
在整个工艺过程中,需要高度的技术水平和严格的质量控制,以确保叶片的质量、性能和使用寿命符合要求。
大尺寸燃气轮机叶片的熔模铸造工艺

大尺寸燃气轮机叶片的熔模铸造工艺作者:朱秋菊荀艳华来源:《科学与财富》2019年第05期摘; 要:燃气轮机在我国的各个领域中都有着比较高的应用价值,直接影响到人们日常生活的质量,例如说燃气轮机在发电方面的应用,直接影响人们的日常用电质量,一直受到国家和人民的高度重视。
叶片作为燃气轮机的重要零件组成,对其工作的各方面都有着很大的影响,我国现阶段的对于叶片的熔模铸造工艺经过多年的发展已经取得了一定的成果,但还是存在很多缺陷和不足,限制我国燃气轮机的发展也研究,需要我们对国外的一些先进技术进行学习。
关键词:大尺寸叶片;熔模铸造;关键技术随着我国科技的发展,燃气轮机的科技水平不断进步,为很多领域的发展进步提供了坚实的基础。
随着人们环保意识的不断增强,清洁能源的使用被提上议程,燃气轮机可以很好的为天然气的应用提供帮助。
高效和节能已经成为燃气轮机现阶段发展的主要方向,为电力供应提供了坚实的技术和设备基础。
但是我国的轮汽轮机研发水平较国际水平还有着不小的差距,文主要对叶片的熔模铸造工艺进行研究,希望可以为我国燃气轮机今后发展提供帮助。
1 燃气轮机涡轮叶片熔模铸造工艺发展1.1 模具设计及制造技术在燃气轮机发展的初期,模具的制作难度较高,主要是通过人工设计画图的方式进行制造,不但制造的效率较低,制造的质量比较低。
随着时代的发展进步,出现了计算机技术,通过计算机技术的应用可以通过计算机软件进行设计制造,代替原来的手工操作,使制造的效率不断提升。
为了满足模具制造的实际需求,计算机软件开始不断更新换代,为设计提供更高的技术支持,模具的各方面性能和制造的效率不断提升。
多年的模具制造形成了两种比较常用的制造方法,其中一种的方法主要是通过多种能量低价的方式对材料按照一定的要求进行切除,这种方法称之为复合加工方法。
还有一种方法是近几十年出现的模具制造方法,较复合加工方法具有更先机的技术。
这种方法具有很多优势,不断可以实现模具制造的高效性,制造出来的模具还具有有很广泛的使用范围。
汽轮机结构:第四节动叶片

工作时对叶片自振频率的影响因素有:
(1)叶根的连接刚度。连接不牢,会使叶片 自振频率降低。可用叶根牢固系数Kr修正。 (2)工作温度。工作温度升高会使E减小,叶 片自振频率降低。可用温度修正系数Kt修正。 (3)离心力。工作时叶片偏离了平衡位置, 离心力会增加叶片的刚度,使叶片自振频率提 高。 (4)叶片成组。用围带和拉金将叶片连接成 组对叶片的自振频率有两方面的影响(增大和 减小)。
4、叶片振动的安全准则
(1)概述 叶片上受到的应力:静应力σ m + 动应力σ d 动应力由汽流力引起,与汽流力成正 比 σ = Dσ 。 安全要求:叶片必须满足静强度、动强 度的要求。 ∗ 校核指标——耐振强度 σ a 。
d sb
耐振强度(复合疲劳强度):指在一定 工作温度和一定静应力作用下,叶片所 能承受的最大交变应力的幅值。 调频叶片:将叶片的自振频率与激振力 频率调开,避免运行中发生共振的叶片。 不调频叶片:允许叶片在共振状态下长 期工作的叶片。
叶片的动频率:叶片在旋转状态下的自 振频率。
fd = f 2 + Bn 2
影响叶片自振频率的因素:
(1)叶片的抗弯刚度(EI)。抗弯刚度越 大,叶片自振频率越高。 (2)叶片的高度。叶片越高(越长),叶 片自振频率越低。 (3)叶片的质量。叶片越重,叶片自振频 率越低。 (4)叶片的振型。振型越复杂,叶片自振 频率越高。
C.进行总结,发现安 全工作叶片和损坏叶 片有一条明显的分界 线,分界线上的安全 倍率为安全倍率界限 值,称为许用安全倍 率[Ab]。
不调频叶片的振动强度安全准则为:
∗ K 1 K 2 K d σ a (修正后的耐振强度) Ab = ≥ [ Ab ] K 3 K 4 K 5 K µ σ sb (修正后的汽流弯应力 )
- 1、下载文档前请自行甄别文档内容的完整性,平台不提供额外的编辑、内容补充、找答案等附加服务。
- 2、"仅部分预览"的文档,不可在线预览部分如存在完整性等问题,可反馈申请退款(可完整预览的文档不适用该条件!)。
- 3、如文档侵犯您的权益,请联系客服反馈,我们会尽快为您处理(人工客服工作时间:9:00-18:30)。
汽轮机叶片的加工方法
一、汽轮机叶片的介绍
汽轮机是以高温、高压的水蒸汽作为工作介质 的流体机械,其最基本的做功单元是由喷嘴叶片 ( 静叶片 ) 和转子叶片 ( 动叶片 ) 组成。通常将这基本 的做功单元称之为汽轮机的级。 叶片是汽轮机关键 零件之一,工作于高温、高压、易腐蚀的环境,特 别是动叶片还要承受离心力、 蒸汽弯曲应力以及复 杂的振动应力。因此,叶片多采用 lCr 1 3、2Cr l 3、1 Cr ll MoV 及l Crl 2wMoV 等不锈钢材料,其 强度高、 韧性大、热硬性好, 但机械加工困难。典 型的汽轮机叶片如图 1-1 所示。
(3)简化机械加工过程,精锻叶片型面和缘板 内侧不需要机械加工, 可以减少大量金属切削机床 和机械加工工时,缩短机械加工过程。
(4)解决了难加工材料和型面薄的叶片机械加 工的困难,汽轮机叶片材料一般为不锈钢甚至钛合
4
金材料。 加工性能差, 叶片型面薄而复杂, 加工极 易变形,采用精锻可以解决这些问题。
(1)力求使叶身型面平坦。叶身平坦可以减小 锻造载荷和侧向力, 防止过大的侧向力产生错模现 象。
(2)有利于叶片锻件各部位的充足成形。叶身 不同的部位成形难度各不相同, 必须全局考虑成形 的过程以做到完好充模。
(3)配合锻坯形状的确定和锻坯在模具型腔中 定位的考虑。确定平衡角有计算法和作图法两种, 两种方法各有特点。以下介绍计算法 计算法确定平衡角 计算法分三种分别如下:
3
叶片模锻则锻件具有较大的加工余量两者相比, 精 锻有如下优点:
(1)可以提高叶片的性能和使用寿命,叶片精 锻由于采用了合理的模具设计和先进工艺技术, 能 够保证金属具有良好的成形条件和合适的变形程 度,获得沿叶身形状分布的流线和均匀细小的晶 粒,增加了强度。 同时由于金属沿着模具的形状流 动叶身型面和缘板内侧面及其与型面转接部分不 需要机械加工,使外露出来的端向晶粒最少流线不 被破坏,减少了应力腐蚀和裂纹, 提高了疲劳强度 冲击强度和抗腐蚀性能力。
6
(1) 将靠近叶根的截面和靠近叶冠的截面的夹角 相加求其平均值
(2)将靠近叶根的截面和靠近叶冠的截面以及叶身 中部的夹角相加求其平均值
就汽轮机的动叶片而言, 也有各种不同的结构形式, 但就其整体结构可将之分为叶身、 叶顶和叶根三个组成部分 :
1) 叶身是从叶身某个截面轮廓可见,叶身型面是由进汽边、出汽边、盆弧和背弧几个部分组 成,如
2) 叶根叶根是叶片与叶轮相连接的部分。叶根结构要求在任何运行条件下都要保证叶 片牢牢地固定在叶轮上,同时力求结构简单,便于制造和装配。叶根的结构有多种,常见 的有直叉型、阶梯叉型、 T型、菌型、榫齿型、纵树型等
叶片的种类较多,根据功能作用和结构形状的 不同,按叶片的功能作用分, 可以将叶片分为动叶 片和静叶片: 所谓动叶片是安装在汽轮机的转子,随转子一同旋转,将蒸汽流
的动能转化为转子的机械能 。而静叶片则安装在汽轮机的壳体上,处 于静止状态,主要起着改 变汽流方向的作用 ,动叶片和静叶片一般都是成对作用的, 也就是一级动叶片对应于一级 静叶片,动叶片的结构要比静叶片复杂得多。
(5)叶片制造的总成本大大降低,采用叶片精 锻技术其所用的模具费用和锻造费用较普通锻造 提高约 5 倍左右,增加了锻件的成本但是对整个制 造过程而言由于节省了材料, 缩短了生产周期, 大 大减少了机械加工费用。 而且精锻叶片的使用寿命 长。所以其总成本比普通的大余量锻造要低的多。
三、叶片精锻件设计及工艺参数计算
(2)与普通模锻叶片相比,可以节省 20%— 25% 左右的金属材料,在各种类型的叶片生产中, 由于叶片形状复杂, 材料的利用率都比较低, 用方 钢铣削汽轮机叶片材料利用率只有 7 %— 15%,普 通模锻叶片材料利用率只有 25%— 40%,这些叶 片的材料除了锻造过程中较大的毛边消耗外, 大量 消耗于为机械加工所留的余量, 精锻叶片的材料利 用率可以达到 50% 以上。
1、叶片锻造平衡角的确定
工艺分析中,叶片锻造转角又称平衡角的确定 是叶片锻造成形的关键, 也是锻造模具型腔设计时 首先考虑的问题。扭角是叶身各型面弦长线与发电 机转子中心线的夹角如图 2-1 所示
的确定
图2-1 叶片锻造转角
5
汽轮机上绝大多数叶片都具有变化的曲面, 其各截 面的扭角大小不同, 靠近叶冠部分的扭角最大, 靠 近叶根部位的扭角最小, 甚至是负值。 扭角大的叶 片会给锻造带来如变形、 水平错移力大、 尺寸精度 不稳定等各种困难。 如果把发电机中心线平面当作 分模面必然导致模锻过程中产生较大的单向水平 推力,使压力机滑块导轨和模具导柱急剧磨损并造 成模具错移。在进行叶片锻件设计时为了克服这一 水平力,应将叶片设计基准沿发电机中心线旋转一 定合适的角度, 放置于锻模上。 锻件图上所示的状 态也就是叶片在锻模上放置的状态。 叶片所需旋转 的角度称为平衡角。确定锻造转角应遵循如下准 则:
3) 叶顶是叶身以上的叶片结构,又叫叶冠。叶项也有不同的结构,有的叶片在叶顶部 分装有围带,以增强叶片刚度,调整叶片的自震频率,此外还有防止漏汽的作用。
2
型的汽轮机叶片
图1-1 典
二、精锻的优点
锻造是叶片制造的主要成形加工工艺, 汽轮 机中相当一部分叶片几乎全部采用锻造方法生产。 精密模锻是在一般模锻基础上逐步发展起来的一 种少无切削加工新工艺, 与一般模锻相比, 它能获 得表面质量好,机械加工余量少和尺寸精度高的锻 件,取消或部分取消了切削加工工序, 从而提高材 料利用率。可以使金属流线沿零件轮廓合理分布提 高零件的承载能力, 降低零件生产成本, 叶片锻造 工艺有精锻、 半精锻和模锻三种方式。 在现行叶片 生产中目前尚无严格区分精锻和模锻的标准。 一般 而言,所谓精锻是指锻件叶身部分余量小少于 0.3 mm, 公差小约为 1/3 模锻公差, 叶身表面不再需 要切削加工, 而只需要进行精抛光或化学铣削。 而