预分解系统结皮堵塞的原因及处理对策
预分解窑预热器堵塞原因及防范措施_高谦
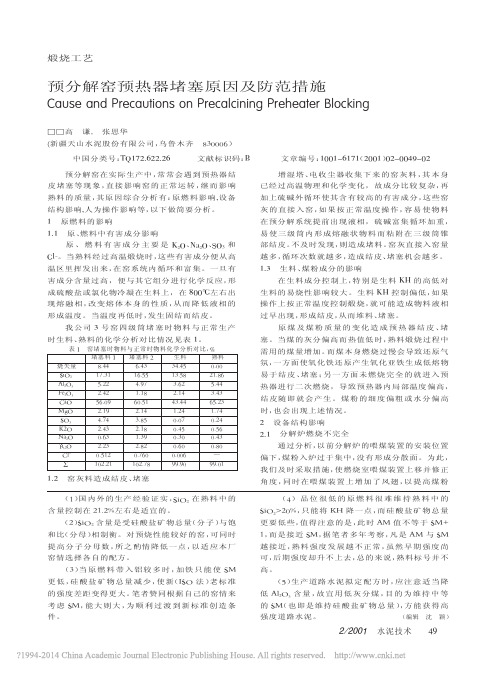
"#*
% %#"
"#%
窑灰料造成结皮、 堵塞 (! ) 国内外的生产经验证实, "#$% 在 熟 料 中 的
含量控制在 %!&%’ 左右是适宜的。 (%) (分子) 与饱 "#$% 含量是受硅酸盐矿物总量 和比 (分母) 相制衡。对预烧性能较好的窑, 可同时 提高分子分母数, 所之酌情降低一点, 以适应本厂 窑情选择各自的配方。 当原燃料带入铝较多时, 加 铁 只 能 使 ") (() 更低, 硅酸盐矿物总量减少, 使新 (*"$ 法 ) 老标准 的强度差距变得更大。 笔者赞同根据自己的窑情来 能大则大, 为顺利过渡到新标准创造条 考 虑 ") , 件。
这些有害成分便从高 +,-。当熟料经过高温煅烧时, 温区里挥发出来, 在窑系统内循环和富集。一旦有 害成分含量过高,便与其它组分进行化学反应, 形 成硫酸盐或氯化物冷凝在生料上,在 .//0 左右出 现熔融相, 改变熔体本身的性质, 从而降低液相的 形成温度。当温度再低时, 发生固结而结皮。 我公司 * 号窑四级筒堵塞时物料与正常生产 时生料、 熟料的化学分析对比情况见表 " 。 表 " 窑堵塞时物料与正常时物料化学分析对比, 9 堵塞料 " 堵塞料 % 生料 熟料 烧失量 6&++ 7&+( (+&+2 -&-!8&(! !7&22 !(&26 %!&67 "#$% 03%$( 2&%% +&98 (&7% 2&++ :;%$( %&+% !&!6 %&!+ (&+( <=$ 27&-9 7-&2! +(&++ 72&%( )>$ %&!9 %&!+ !&%+ !&8+ "$( +&8+ (&62 -&-8 -&%+ .%$ %&+( %&!6 -&+2 -&27 ?=%$ -&7( !&(9 -&(-&+( @%$ %&%( %&6% -&7-&6— <3A -&2!% -&87-&--7 " !-%&%! !-%&86 99&999&-!
预分解系统结皮堵塞的原因及处理对策
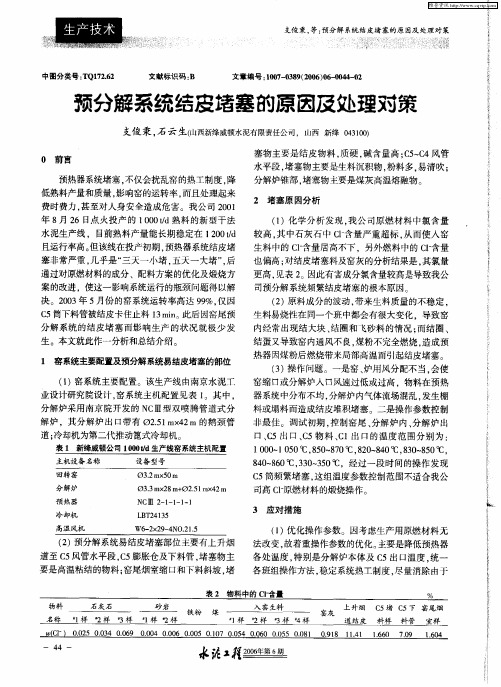
2 堵塞原 因分 析
预热器系统堵塞 , 不仅会扰乱窑的热工制度 , 降 低熟料产量和质量 , 影响窑的运转率, 而且处理起来
费时费力 , 甚至对人身安全造成危害。我公司 20 01 年 8 2 点火投产 的 l 0 t 月 61 3 0/ 0 d熟料的新型干法
法改变, 故着重操作参数的优化。 主要是降低预热器
各处温度 , 特别是分解炉本体及 C 5出 口温度 . 统一
各班组操作方法 , 稳定系统热工制度 , 尽量消除由于
一
4一 4
水滩工 程
维普资讯
支俊秉, : 等 预分解 系统结皮堵塞的原 因及处理对策
维普资讯
支俊秉 , : 等 预分解系统结皮堵塞的原 因及 处理对策
… 一
l i囊 扫 i l : |
曩 0| 跨越0 鼻 嚣 黪
中图分类号 :Q126 T 7. 2
文献标识码 : B
文章编号 :0 7 0 8 (0 6 0 - 04 0 1 0 — 3 9 2 0 )6 0 4 — 2
( )化学分析发现 。 1 我公司原燃材料 中氯含量
水泥生产线 ,目前熟料产量能长期稳定在 1 0 0/ 2 t d 且运行率高。 但该线在投产初期 , 预热器系统结皮堵
较高 , 其中石灰石 中 c一 l 含量严重超标 , 从而使人窑
生料 中的 c一 l 含量居高不下,另外燃料 中的 c一 l 含量 也偏高; 对结皮堵塞料及窑灰的分析结果是 。 其氯量
l0 0 5 0 -l 0℃ , 5 - 7 0 8 0 8 0℃ , 2 ~ 4 8 0 8 0℃ , 3 ~ 5 8 0 8 0℃ ,
窑尾预热器结皮堵塞的原因及预防措施
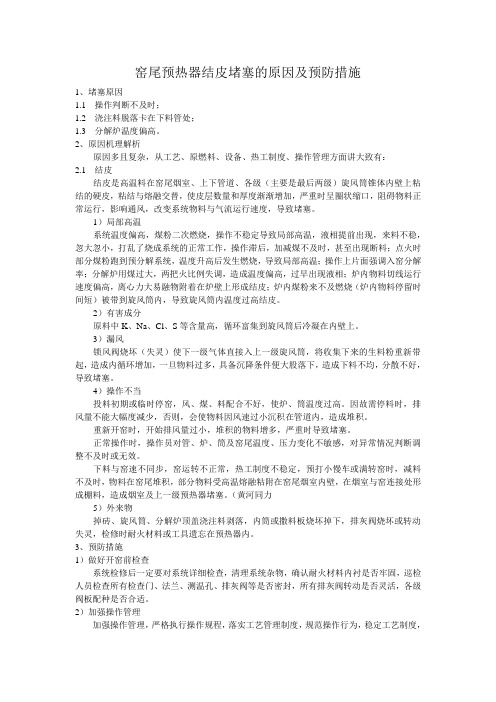
窑尾预热器结皮堵塞的原因及预防措施1、堵塞原因1.1 操作判断不及时;1.2 浇注料脱落卡在下料管处;1.3 分解炉温度偏高。
2、原因机理解析原因多且复杂,从工艺、原燃料、设备、热工制度、操作管理方面讲大致有:2.1 结皮结皮是高温料在窑尾烟室、上下管道、各级(主要是最后两级)旋风筒锥体内壁上粘结的硬皮,粘结与熔融交替,使皮层数量和厚度渐渐增加,严重时呈圈状缩口,阻碍物料正常运行,影响通风,改变系统物料与气流运行速度,导致堵塞。
1)局部高温系统温度偏高,煤粉二次燃烧,操作不稳定导致局部高温,液相提前出现,来料不稳,忽大忽小,打乱了烧成系统的正常工作,操作滞后,加减煤不及时,甚至出现断料;点火时部分煤粉跑到预分解系统,温度升高后发生燃烧,导致局部高温;操作上片面强调入窑分解率;分解炉用煤过大,两把火比例失调,造成温度偏高,过早出现液相;炉内物料切线运行速度偏高,离心力大易融物附着在炉壁上形成结皮;炉内煤粉来不及燃烧(炉内物料停留时间短)被带到旋风筒内,导致旋风筒内温度过高结皮。
2)有害成分原料中K、Na、Cl、S等含量高,循环富集到旋风筒后冷凝在内壁上。
3)漏风锁风阀烧坏(失灵)使下一级气体直接入上一级旋风筒,将收集下来的生料粉重新带起,造成内循环增加,一旦物料过多,具备沉降条件便大股落下,造成下料不均,分散不好,导致堵塞。
4)操作不当投料初期或临时停窑,风、煤、料配合不好,使炉、筒温度过高。
因故需停料时,排风量不能大幅度减少,否则,会使物料因风速过小沉积在管道内,造成堆积。
重新开窑时,开始排风量过小,堆积的物料增多,严重时导致堵塞。
正常操作时,操作员对管、炉、筒及窑尾温度、压力变化不敏感,对异常情况判断调整不及时或无效。
下料与窑速不同步,窑运转不正常,热工制度不稳定,预打小慢车或满转窑时,减料不及时,物料在窑尾堆积,部分物料受高温熔融粘附在窑尾烟室内壁,在烟室与窑连接处形成棚料,造成烟室及上一级预热器堵塞。
2预热器结皮堵塞的原因及处理对策

预分解系统结皮堵塞的原因及处理对策石云生(山西新绛威顿水泥有限责任公司山西新绛043100)预热器系统堵塞,不仅会扰乱窑的热工制度,降低窑产量和熟料质量,影响窑的运转率,而且处理起来费时费力,甚至对人身安全造成危害。
我公司有一条1000t/d的新型干法水泥生产线,由南京设计研究院设计,于2001年8月26日点火,经过调试72小时达标一年达产,目前日产熟料达1200t/d。
在投产初期,预热器系统结皮堵塞严重影响了我们的正常生产,几乎是“三天一小堵,五天一大堵”,后来我们通过对原燃材料的成分、配料方案及煅烧方案的改进,基本解决了这个问题。
值得一提的是:我们在2003年5月份只因为C5筒下料管被结皮卡住止料13分钟,运转率达到了99%。
下面就此问题的成因及处理作一分析。
该生产线由南京水泥工业设计研究院设计,分解炉采用南京院开发的N CⅢ型双喷腾管道式分解炉,分解炉出口带有ф2.51×42m的鹅颈管道,冷却机为第二代推动篦式冷却机。
其窑系统主机设备配置如表一:威顿公司主机设备表(表一)一预热系统易结皮堵塞的部位1 上升烟道至C5风管水平段,C5膨胀仓及下料管,堵塞物主要是高温粘结的物料。
2 窑尾烟室缩口和下料斜坡,堵塞物主要是结皮物料,质硬,碱含量高。
3 C5—C4风管水平段,堵塞物主要是生料沉积物,粉料多,易清吹。
4 分解炉锥部,堵塞物主要是煤灰高温熔融物。
二原因分析1通过对原燃材料的成分分析,发现其碱含量,特别是氯含量较高,我们对进厂原燃料,入窑生料,堵料及窑灰等作了化验分析,结果如表二:物料中的CL-含量(表二)当原燃料中的有害成分含量高时,大量的碱会在烧成带挥发并与气相中的Cl-,SO2发生化学反应形成化合物,而在硫酸碱和氯化碱多组分系统中,最低熔点温度为650-700℃,因此窑气中的硫酸碱和氯化碱凝聚时,会以熔融态形式沉降下来,并与入窑物料和窑内粉尘一起构成粘聚性物质,而这种在生料颗粒上形成的液相物质,会阻碍生料颗粒的流动,使物料的粘度增加,造成粉料的粘结,粘附在各级管道中形成结皮,经过长期的内循环后,结皮越来越多,若不及时处理就会导致系统堵塞;当煤粉中SO3含量过高时,会形成低熔点硫化物,并在还原气氛中其熔点更低,也易导致结皮堵塞;生料中窑灰掺量过高时,由于窑灰中含有较多的有害成分,易形成熔融相,也会导致结皮堵塞。
预热器系统的结皮堵塞及预防

对旋风预热器来说,最容易发生结皮、堵塞的部位是窑尾烟室、下料斜坡、缩口及最下一级旋风筒锥体、最下两级旋风筒等部位。
但是,结皮在整个预热器系统以及预热器主排风机的叶片上都能发生。
结皮增厚时,不但会使通风通道有效面积减小、阻力增大,影响系统通风,结皮严重或塌落时,还容易发生堵塞事故,影响正常生产。
主排风机叶片结皮,会使风机发生震动,影响风机的安全运转。
造成固体颗粒黏结在燃烧装置的内壁而形成预热器内结皮的原因,伦普认为是湿液薄膜表面张力作用下熔融黏结,作用于表面上的吸力造成的表面黏结及纤维状或网状物质的交织作用造成的黏结,由于在窑尾及预热器内的结皮中硫酸碱和氯化碱含量很高,而在硫酸钾、硫酸钙和氯化钾多组分系统中,最低熔点温度为650〜700C。
,因此窑气中的硫酸碱和氯化碱凝聚时,会以熔融态形式沉降下来,并与入窑物料和窑内粉尘一起构成黏聚性物质,而这种在生料颗粒上形成的液相物质薄膜,会阻碍生料颗粒的流动,在预热器内造成黏结堵塞。
此外,生料成分波动、喂料不均、火焰不当、预热器过热、燃料不完全燃烧、窑尾及预热器系统漏风、预热器内衬料剥落、翻扳阀不灵等种种原因,也都会导致结皮、堵塞。
法国拉法基水泥公司研究认为,结皮的形式主要与下列三个因素有关。
①与物料中钾、钠、氯、硫的挥发系数大小有关,特别是在还原气氛中,挥发系数增大时,对结皮影响很大。
②与物料易烧性有关。
若物料易烧性较好,则熟料的烧成温度将会相应偏低,结皮就不易发生。
③与物料中所含的三氧化硫与氧化钾的克分子比大小有关。
物料中的可挥发物含量越大,窑系统的凝聚系数越大,则结皮形成的可能性就越大。
关于结皮的主要矿物成分,一般认为是由于大量的粉尘循环及硫酸盐、氯化物的富集而生成一种灰硅钙石。
中国建筑材料科学研究院曾对8个结皮试样进行了X射线分析,发现8个试样中都含有硫酸盐和以复盐形式存在的硫酸盐化合物,而大部分试样中都有灰硅钙石(2C2S∙Ca∞3)和硫硅钙石(2C2S∙CaSO4)。
预热器堵塞的原因分析及预防处理措施

一、结皮堵塞预分解窑生产工艺线普遍存在着一个常见问题,就是窑尾系统——预热系统与分解炉结皮、积料、堵塞。
预热系统一旦发生结皮堵塞,热工制度打乱,严重影响水泥的生产质量,且处理结皮堵塞,恢复生产比较困难,更有甚者,因堵塞塌料而造成人身伤亡。
如何正确理解、严肃对待这一客观存在的现象,认识其将给生产带来的种种危害,切实通过一些必要的控制手段和一定的工艺处理措施,科学地进行预测与防范,是保障生产顺利进行,确保工艺设施安全,发挥系统优势的关键所在。
针对这些问题,我搜集了水泥生产线的预防解决措施,以期望能够在以后的工作中有所帮助。
结皮的形成预分解窑最易发生结皮的部位是窑尾烟室、下料斜坡、窑尾缩口、最低两级筒的下料管、分解炉内等处。
结皮使通风通道的有效截面积减小,阻力相应增大,影响系统通风,使主排风机拉风加大。
结皮塌落时,还容易发生堵塞。
二、堵塞的症状、多发部位2.1 窑尾系统堵塞症状预热器发生堵料时在中控室和现场都能判断。
正常生产时,双系列预分解窑从中控操作画面上看预热器系统各控制参数是很有规律的:从上至下负压逐级降低,温度逐级升高,且同级两列相差很小。
但当某列发生堵料时:(1)以堵塞部位为界,堵塞部位以上多处负压值急剧上升;堵塞部位以下出现正压; 捅料孔、排风阀等处有冒灰现象发生。
(2)窑头负压不足,严重时会有正压产生,且从观测孔等处往外冒火。
(3)窑尾排风机、一级筒出口、分解炉出口及窑尾等多处温度异常。
(4)被堵预热器的锥体负压急剧下降,甚至达到或接近零压。
(5)下料温度异常下降。
(6)进入窑内的物料减少。
通常,上述这些症状中有3种或3种以上同时出现时,就说明窑尾系统已经产生堵塞,应及时采取措施。
预分解系统内很多部位都可能发生堵塞,但主要发生在五级和四级旋风筒内;各级下料管及翻板阀内,若不及时处理,有时能从下料管堵到预热器锥体,甚至整个旋风筒;再是分解炉及其斜坡,连结管、变型或变径管等处。
2.2 堵塞时间从时间上看,堵塞大部分发生在点火后不久,窑操作不正常,系统热工制度不稳定等情况下。
预热器系统发生结皮、堵塞的原因
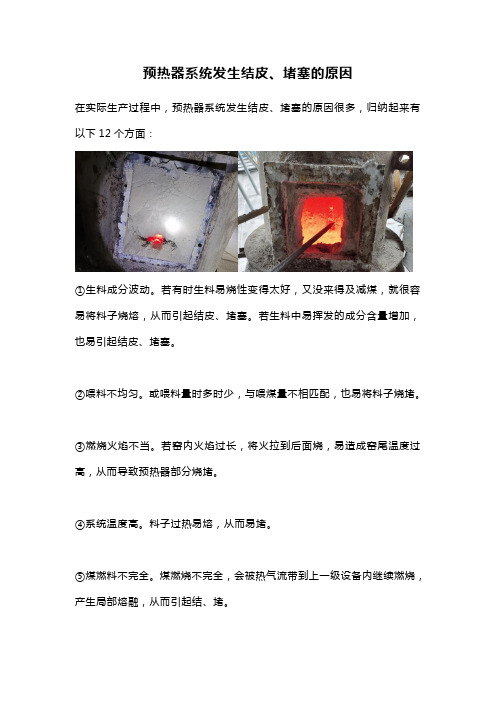
预热器系统发生结皮、堵塞的原因在实际生产过程中,预热器系统发生结皮、堵塞的原因很多,归纳起来有以下12个方面:①生料成分波动。
若有时生料易烧性变得太好,又没来得及减煤,就很容易将料子烧熔,从而引起结皮、堵塞。
若生料中易挥发的成分含量增加,也易引起结皮、堵塞。
②喂料不均匀。
或喂料量时多时少,与喂煤量不相匹配,也易将料子烧堵。
③燃烧火焰不当。
若窑内火焰过长,将火拉到后面烧,易造成窑尾温度过高,从而导致预热器部分烧堵。
④系统温度高。
料子过热易熔,从而易堵。
⑤煤燃料不完全。
煤燃烧不完全,会被热气流带到上一级设备内继续燃烧,产生局部熔融,从而引起结、堵。
⑥窑尾、预热器漏风。
漏风问题是产生结皮、堵塞的一个条件。
无论哪一种结皮,必须有一定的冷凝条件,否则结皮就不会如此集中,哪个地方漏风,该处就会有冷凝现象发生,就可能导致结皮。
⑦窑尾、预热器系统衬料剥落。
掉衬后筒体直接与外界及带有料子的热气流接触,由于内外温差,料子极易在此处聚集。
⑧翻板阀动作不灵活。
使物料下料不均匀和造成系统内部短路漏风,从而引起结、堵。
⑨物料中碱、氯、硫含量过高。
在煅烧中这些挥发性组分在窑系统内处于闭路循环状态。
它在高温下挥发后到低温区又重新凝集。
钾、钠的氯化物和硫化物在凝集后,它们又使物料的熔点降低,引起预热器的结皮、堵塞、料流不畅。
⑩煅烧系统还原气氛严重。
当存在还原气氛时,使SO3的挥发量增加,物料中会产生亚硫酸盐和硫化物,使熔体的量有所增加。
还原气氛严重,必然使CO的含量增加,从而CO2浓度也会增加,这样可能使碳酸盐分解逆转,即:CaO+CO2=CaCO3(再化合),导致粉料板结。
⑪窑内通风不良。
窑内通风不良,易造成还原气氛。
⑫喂煤系统喂煤不稳定。
喂煤计量系统下料不稳,即喂料不均匀,从而易造成系统煅烧匹配失调,也易造成预热器系统粘、堵。
预分解系统的结皮堵塞

• 4.气体温度及料粉浓度 • 气流温度较高时,气体粘度较大,气固间的
相对运动阻力大;气流中料粉浓度较高时, 相互干扰加强,影响分解炉内的旋风、喷腾 效应。 • 注意点: • 对旋风型分解炉,应注意其合理的炉型结构, 加强炉内气流的旋回运动,分解炉的进口风 速一般应在20m/s左右,炉内断面风速一般 4~6m/s。
• ⑵ 外循环
• 是指凝聚生料中的碱、硫、氯等成分,随末 被预热器收集的生科一起排出预热器系统, 当这部分粉尘在收尘器、增湿塔及生料磨、 烘干机系统中被收集重新入窑时,在预热器 与这些设备之间存在循环过程。
• 如果在收尘设备中收集的窑灰丢弃,外循环 则基本消除。但是,由于在预热器系统中 K2O的冷凝率高达79~81%,而Na2O的冷凝 率较低,因而预热器废气中带出的含碱、硫、 氯等有害成分相当低,因此窑灰重新回窑产 生的外循环,对生产影响不大。
• 高温带碱、氯、硫物质受热挥发,随烟气带 往窑后烟道、分解炉、预热器系统,并凝聚 在生料颗粒表面,生料共熔温度降低。当处 于较高温度(1000℃以上)下,产生液相, 与温度较低设备或管道内壁接触时,便可能 粘结在器壁上。
• 碱等含量多,温度较高,液相多而粘,则容 易使料粉层层粘挂,愈结愈厚。尤其气流拐 弯处(如缩口、交叉处),因惯性作用,含 液相的料粉直甩器壁,动能转化为压力,将 有利于料粉的粘挂。
预分解系统的结皮堵塞
• 二、预热器系统的结皮、堵塞 • 1.易发生结皮、堵塞的部位: • 对旋风预热器来说:主要在窑尾烟室、下料
斜坡、缩口及最下一级旋风筒锥体、最下两 级旋风筒等部位。 • 结皮在整个预热器系统以及预热器主排风机 的叶片上都能发生。
预分解系统的结皮堵塞
• 2.危害 • 结皮增厚时,不但会使通风通道有效面积减
预分解系统堵塞与塌料的原因及解决措施

象 ! 增加铝质校正料铝矾土 " 保证熟 料形成过程中所需的液相量 " 控制出 窑 熟 料 率 值 &/0 5*$62 7*$*( ’12 5
吹气
2$,,7*$( ’825($97*$(! 同时利用停窑
撒料板 吹气管
期间进行倒库 " 提高生料均化效果 !
2$%
维护和改造 在停窑检修时 " 认真检查 &’#&%#
<
<
I B @JK 62*
’9*
9
,6*
F**
+**
++*
+6*
*$6
(($,
(+*
’$2
%**
9$’
(*+* 6**
&342 含 量 ≤*$’- " 减 少 结 皮 结 圈 现
下料管 撒料箱
$9 % 保证预热 器 出 口 和 窑 尾 气 体 分析仪的正常 # 准确工作 ! 操作人员 应注意气体分析的分析结果 " 如果有 异常情况 " 应及时做出判断并做相应 的反应 !
M
高温 闸阀 塌料口
M
三次风闸阀
1.2?6 与 生 料 中 C@A2=>0B4?6
含 量 过 高 #< 含 量 循 环 富 积 与 C@A2 会 降 低 物 料 出 现 液
回转窑
图1 通讯地址 $ 福建水泥股份有限公司炼石水泥厂 , 福建 顺昌
离线炉系统
757200; 收稿日期 : 2005-0E-16 ; 编辑 : 吕
+*. 以上 " 窑喂料量由 (,*G(9*A B C 提
高 到 (+*;(6*A B C " 并 能 稳 定 生 产 " 达 到同类型窑的先进水平 " 降低了生产 成本 " 极大提高企业的经济效益 ! % 号 窑正常生产时窑系统主要参数见表
预分解系统结皮的原因及预防措施

预分解系统结皮的原因及预防措施预分解系统结皮是指高温生料与窑气中有害组分经过化学反应后形成粘附在内壁上的层状物。
在窑尾、烟室缩口、最下一级旋风筒及其下料溜子、分解炉等部位最容易产生结皮,结皮可导致通风面积减小,阻力增大,而迫使主排风机负荷增大。
结皮脱落时又极容易造成系统堵塞,影响正常的生产。
一般认为:结皮的产生与所用原料、燃料的成分,系统温度的变化,系统通风的情况,设备运转的情况以及工艺操作因素有关。
下面结合一些的具体情况,通过对预热器各级旋风筒中原、燃料中有害元素的分析,以及设备状况,工艺操作等有关因素,对结皮形成的原因进行分析以及相应的处理方法。
1.有害元素的影响有害元素主要包括硫、碱、氯等,它们是形成结皮的一个很重要的因素,煤炭作为目前水泥窑的主要燃料,是有害元素硫的一个重要来源,煤燃烧的大部分硫进入烟气中,烟气中带有大量的CaO生料粉,它在煅烧过程中与K2O、Na2O和SO3发生反应,生成各种硫酸盐物质,主要是K2SO4、2 CaSO4·K2SO4、K2SO4·H2O,,这些硫酸盐属于低熔点化合物,它们会粘附在器壁表面,使粘度增加,流动性减小,久而久之形成结皮。
消除有害元素的影响主要是控制硫、碱的摩尔比,硫碱的摩尔比过高或过低都易形成结皮。
即使硫、碱含量均较高,只要硫碱比在控制范围之内,对结皮也产生不了太大影响,因为原燃料中的大部分硫、碱可以中和在熟料中被带出。
经过分解后的物料进入回转窑后,在烧成带温度极高的情况下,使K2SO4 分解成气态的K2O 和SO3,挥发进入循环气流。
这些物质通过三次风管和窑返回到预热器中,在遇到低温时又生成成固相或液相化合物,附着在物料上被带回窑中,只有少部分热量和粉尘被排出,如此反复形成了预热器与回转窑中的碱循环。
在新型干法水泥生产线中,由于原、燃料中的氯化物在窑内烧成挥发,并随窑内气体进入预分解系统,在此遇到较低温度而凝结于器壁表面,从而使回旋中的物料发粘,流动性变差,附着于壁,累积而形成结皮,附着在物料上的部分氯又进入窑内煅烧,一部分挥发形成气态进入循环气流,这样就形成了氯化物的循环。
13、预分解窑为何会结皮如何预防

1250℃ 左 右 , CaSO4 、 K2SO4 和 Na2SO4 共 同 存 在时,最低共熔温度可能低于800℃;有氯 化物存在时,最低共熔温度可接近700℃;
另一方面有害组分形成的熔体会在生料 或衬料表面铺展开来,起到“粘结剂”的作 用,在系统温度降低时,就在衬料表面上形 成结皮。
窑内的这种有害组分是导致结皮中间相 形成的重要因素,如:二氧化硫参与形成硫 酸钙(2SO2+O2+2CaO=2CaSO4);氯化物促进 硅方解石的形成;K3Na(SO4)2是在还原气氛 中形成等等。而结皮中间相的形成,常常导
(4)操作、设备维护方面的原因
①操作方面:喂料不均、生料成分波动、 火焰形成不当、窑内还原气氛、不完全 燃烧等容易造成预热系统结皮堵塞。
②设备维护方面:窑尾密封处、人孔、 冷风闸门等漏风、预热器内衬剥蚀、翻 板阀太紧(不灵活)等也容易造成预热系 统结皮堵塞。有时旋风筒顶部的粘灰脱 落排在旋风筒内,就使旋风筒下部堵塞。
结皮是由于熔融湿液薄膜在表面张力作用下 粘结其他物料,不断反复形成纤维状或网状 结构,从而引起结皮。
由于窑气中的碱、氯、硫等有害组分在窑尾 及预热器和分解炉中冷凝时,会使最低共熔 温度降低,因此窑气中的碱、氯、硫等凝聚 时,会以熔态的形式沉降下来,并与入窑物 料和窑内粉尘一起构成粘聚性物质,而这种 在生料颗粒上形成的液相物质薄膜,会阻碍 生料颗粒的流动,从而造成结皮甚至堵塞。
致结皮坚实化,使结皮越结越厚。
(2)局部Байду номын сангаас度过高,这是形成结皮的关键 因素。
系统中如果产生局部高温,一方面促 进生料和燃料中有害组分的挥发及冷凝循 环,并使内循环发生的区域进一步扩大; 另一方面也可能使液相出现,把生料粘附 在衬料的内壁而形成结皮。产生局部高温 的原因,至少有如下几个:
窑尾预热分解窑系统堵塞事故现场处置方案
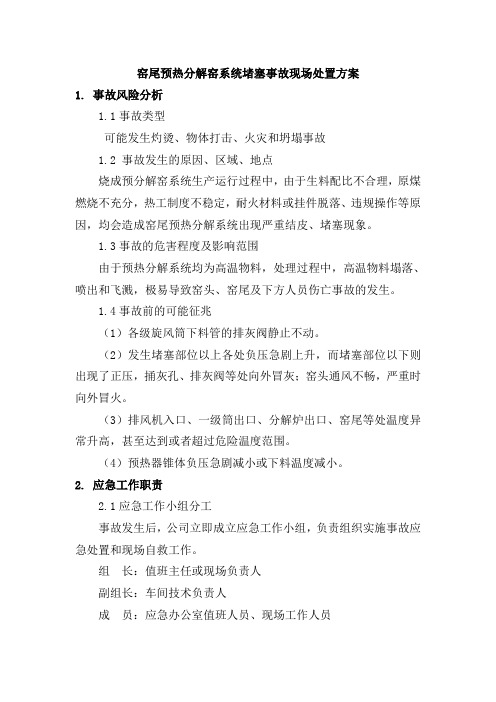
窑尾预热分解窑系统堵塞事故现场处置方案1. 事故风险分析1.1事故类型可能发生灼烫、物体打击、火灾和坍塌事故1.2 事故发生的原因、区域、地点烧成预分解窑系统生产运行过程中,由于生料配比不合理,原煤燃烧不充分,热工制度不稳定,耐火材料或挂件脱落、违规操作等原因,均会造成窑尾预热分解系统出现严重结皮、堵塞现象。
1.3事故的危害程度及影响范围由于预热分解系统均为高温物料,处理过程中,高温物料塌落、喷出和飞溅,极易导致窑头、窑尾及下方人员伤亡事故的发生。
1.4事故前的可能征兆(1)各级旋风筒下料管的排灰阀静止不动。
(2)发生堵塞部位以上各处负压急剧上升,而堵塞部位以下则出现了正压,捅灰孔、排灰阀等处向外冒灰;窑头通风不畅,严重时向外冒火。
(3)排风机入口、一级筒出口、分解炉出口、窑尾等处温度异常升高,甚至达到或者超过危险温度范围。
(4)预热器锥体负压急剧减小或下料温度减小。
2. 应急工作职责2.1应急工作小组分工事故发生后,公司立即成立应急工作小组,负责组织实施事故应急处置和现场自救工作。
组长:值班主任或现场负责人副组长:车间技术负责人成员:应急办公室值班人员、现场工作人员2.2应急工作小组职责组长职责:事故发生后,分析判断事故,立即启动该事故现场处置方案,积极组织现场应急处置和自救。
若事态扩大,立即请求增援。
技术负责人职责:负责救援方面措施的编制和技术资料的提供。
应急办公室值班人员:接到事故报告,按照指令,召集应急小组成员,协调现场自救和应急处置工作,同时做好相关记录。
并向应急办公室主任及应急指挥部汇报情况。
现场工作人员职责:服从指挥,在安全的情况下,开展自救、互救工作3. 事故应急处置3.1 事故应急处置程序3.1.1事故报警事故发生后,事故现场人员应立即撤离作业人员,并电话汇报应急办公室。
3.1.2应急措施的启动发生事故后,值班主任,应当立即按照现场处置方案组织人员,展开自救互救,严格落实相关措施。
1000t_d预分解窑预热器结皮原因及处理措施

F54C442- 3; 处理风量: 150 km3 /h; 有效断面: 54. 4 m2; 集尘面积: 2856m2
Y 4- 73- 11N 020D 左 135b; 流量: 160. 8 km3 /h; 全压: 2 039 Pa; 电机 : Y 355- 8, 160 kW
2070D IBB24左 90b /45b; 流量: 250 km3 /h; 全 压: 8 000 Pa; 电机: Y JS500- 4, 800 kW, 6 kV ë 6. 5 m @ 26 m; 处理风量: 240 km3 /h
F - 106 m2; C1: 2 @ ë 3 700 mm, C2、C3: ë 5 200mm, C4、C5: ë 5 400 mm。H FC 型分解 炉: ë 5 100 m m, ë 3. 3 m @ 48 m; 斜度 4% ; 转速: 0. 14- 3. 47 rpm; 主电机: ZSN 4- 280- 091B, 160 kW
皮。 从表 2、表 3 中看出, 生料中的 CL- 较低, 碱含
量较高, 是影响窑尾系统结皮的重要因素。而碱含 量较高的原因主要是页岩、粘土、石灰石原料中的碱
含量较高。 4. 2 煤的质量
原煤及煤粉质量的变化也是造成预热器结皮的 一个主要原因。由于近年来煤炭供应紧张, 煤质较 差, 煤的灰分从 18- 32% 大幅度波动, 当煤的灰份 偏高而热值低时, 熟料煅烧过程中用煤量增加, 煤的 燃烧特性差, 着火点高, 燃烧时间长, C5 经常出现温 度倒挂现象, 后燃烧现象严重。煤的燃烧慢导致还 原气氛, 使氧化铁还原产生氧化亚铁生成低熔物易 于结皮。另外, 后燃烧现象导致预热器内部局部温 度偏高, 结皮随机就会产生。 4. 3 系统漏风
预分解窑系统结皮的主要因素及预防措施
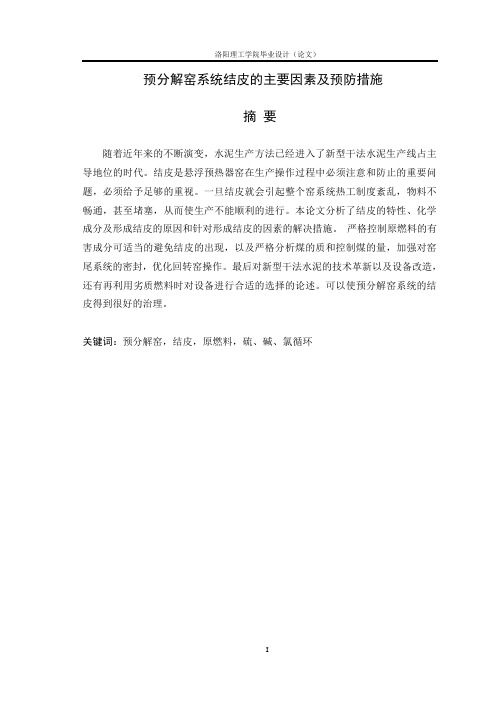
预分解窑系统结皮的主要因素及预防措施摘要随着近年来的不断演变,水泥生产方法已经进入了新型干法水泥生产线占主导地位的时代。
结皮是悬浮预热器窑在生产操作过程中必须注意和防止的重要问题,必须给予足够的重视。
一旦结皮就会引起整个窑系统热工制度紊乱,物料不畅通,甚至堵塞,从而使生产不能顺利的进行。
本论文分析了结皮的特性、化学成分及形成结皮的原因和针对形成结皮的因素的解决措施。
严格控制原燃料的有害成分可适当的避免结皮的出现,以及严格分析煤的质和控制煤的量,加强对窑尾系统的密封,优化回转窑操作。
最后对新型干法水泥的技术革新以及设备改造,还有再利用劣质燃料时对设备进行合适的选择的论述。
可以使预分解窑系统的结皮得到很好的治理。
关键词:预分解窑,结皮,原燃料,硫、碱、氯循环THE MAIN FACTORS CRUST AND PREVENTION OF KILNSYSTEMABSTRACTWith the constant evolution in recent years, cement production methods have entered the new dry cement production line dominated era. Crust is the suspension preheated kiln operation in the production process must pay attention to and prevention of important issues must be given adequate attention. Once the crust can cause the entire kiln system thermal system disorders, materials are not smooth, and even blocked, so that production can not proceed smoothly. This paper analyzes the characteristics of the skin closure, chemical composition and the reasons for the formation of crusts and crust formation factors for the solutions. Strict control of the original Fuel may be appropriate to avoid harmful ingredients Crust occur, and rigorous analysis of the coal the amount of coal quality and control, strengthen the kiln sealing systems, optimizing kiln operation. Finally, technology innovation and new dry cement equipment modification, and reuse of low-grade fuel suitable choice of equipment exposition. Making the kiln system of governance crust well.KEY WORDS: kiln,crust,raw fuel,sulfur、alkali、chlorine cycle目录前言 (1)第1章结皮的特征、组成 (2)1.1 常见结皮区域分布特点 (2)1.1.1 结皮频繁区 (2)1.1.2 结皮较少的区域 (3)1.2 结皮料的化学组成 (3)1.3 结皮的特征 (4)第2章结皮形成的因素 (6)2.1 预分解系统中挥发性组分的循环富集 (6)2.1.1 碱的循环富集 (9)2.1.2 硫的循环与富集 (10)2.1.3 氯的循环与富集 (11)2.2 局部温度过高 (11)2.3 操作不当 (13)第3章防止结皮的措施 (14)3.1 控制原材料质量、减少有害成分 (14)3.1.1 硫碱比的含量控制 (14)3.1.2 氯含量的控制 (15)3.2 避免局部高温 (16)3.2.1 用煤量的控制 (16)3.2.2 窑内通风量的控制 (16)3.2.3 稳定喂料量 (16)3.3 操作及设备方面 (16)第4章技术的革新及改造防结皮 (18)4.1 分解炉用煤的高比控制 (18)4.2 旁路放风 (19)4.3 无烟煤 (20)4.3.1 燃烧器的选择 (20)4.3.2 预热预分解系统 (21)结论 (23)谢辞 (24)参考文献 (25)外文资料翻译 (27)前言近年来,新型干法水泥生产线在水泥行业中所占的比例越来越大,成为我国水泥工业的主要生产工艺形式。
预分解窑预热器堵塞原因及防范措施

预分解窑预热器堵塞原因及防范措施下载提示:该文档是本店铺精心编制而成的,希望大家下载后,能够帮助大家解决实际问题。
文档下载后可定制修改,请根据实际需要进行调整和使用,谢谢!本店铺为大家提供各种类型的实用资料,如教育随笔、日记赏析、句子摘抄、古诗大全、经典美文、话题作文、工作总结、词语解析、文案摘录、其他资料等等,想了解不同资料格式和写法,敬请关注!Download tips: This document is carefully compiled by this editor. I hope that after you download it, it can help you solve practical problems. The document can be customized and modified after downloading, please adjust and use it according to actual needs, thank you! In addition, this shop provides you with various types of practical materials, such as educational essays, diary appreciation, sentence excerpts, ancient poems, classic articles, topic composition, work summary, word parsing, copy excerpts, other materials and so on, want to know different data formats and writing methods, please pay attention!随着工业化生产的不断发展,预分解窑预热器在水泥生产中发挥着至关重要的作用。
预分解窑结皮的原因和机理

预分解窑结皮的原因和机理结皮是指生料粉与窑气中有害组分所形成的粘附在窑尾系统内壁的层状物..预分解窑最易发生结皮的部位是窑尾烟室、下料斜坡、窑尾缩口、最低两级筒的下料管、分解炉内等处..结皮使通风通道的有效截面积减小;阻力相应增大;影响系统通风;使主排风机拉风加大..结皮增厚或塌落时;还容易发生堵塞..1. 结皮机理结皮的原因;是湿液薄膜表面张力作用下的熔融粘结;作用在表面上的吸力造成的表面粘结及纤维状或网状物质的交织作用造成的粘结..由于窑气中的碱、氯、硫等有害组分在窑尾及预热器和分解炉中冷凝时;会使最低共熔温度降低;因此窑气中的碱、氯、硫等凝聚时;会以熔态的形式沉降下来;并与入窑物料和窑内粉尘一起构成粘聚性物质;而这种在生料颗粒上形成的液相物质薄膜;会阻碍生料颗粒的流动;从而造成结皮甚至堵塞..引起预分解窑结皮的因素如下:1系统中有害组分碱、氯、硫等的循环富集..这是形成结皮的重要条件..从原燃料中引入系统的碱、氯、硫等有害组分;在生料通过窑的高温带时会挥发出现;并随着窑气向窑尾运动..挥发出来的有害组分到达窑尾温度较低的区域时;便会以熔态的形式冷凝下来;使生料在煅烧过程中液相开始出现的温度降低而有利于结皮的形成..窑内的这种有害组分是导致结皮中间相形成的重要因素..2局部温度过高;这是形成结皮的关键因素..系统中如果产生局部高温;一方面促进生料和燃料中有害组分的挥发及冷凝循环;另一方面也可能使液相出现;把生料粘附在衬料的内壁而形成结皮..局部温度过高;这是形成结皮的关键因素..产生局部高温的原因;至少有如下几个:①煤粉的不完全燃烧..窑头或分解炉中的煤粉由于多种原因燃烧不完全时;就可能到窑尾或低级旋风筒中去燃烧;从而产生局部高温..②喂料量不稳时;很容易打乱预热器、分解炉和窑的正常工作..由于操作具有滞后的特点;有时跟不上喂料的变化;加减煤不及时;甚至出现短期断料也不能及时减煤;因此很容易因料小出现系统温度偏高;而造成结皮..③由于回灰量小;在生料均化库中不容易被混合均匀;从而造成入窑生料成分的波动..④当预热器漏进冷风与热物料接触;很容易使热物料冷凝而粘附在系统的内壁而产生结皮..2挥发性组分的来源..窑系统的废气中含有大量的挥发性组分;主要是碱、氯、硫..1碱的来源..碱主要来源于原料;尤其是粘土..2硫的来源..燃料中带入的硫通常较原料中多..使用较多的燃料是煤..煤中通常含有C、H、O、N、S等元素..煤中的硫通常有三种存在形式:有机硫、硫化物中的硫、硫酸盐中的硫..存在于硫酸盐中的硫不具有可燃性;在高温下;一部分会分解生成含硫化合物;而大部分留在灰分中..3氯的来源..氯主要来自水溶性碱的氯化物;即通常以KCl、NaCl的形式存在于原料内..3 防止结皮的措施由于结皮影响系统的通风;使阻力增大;这不仅使能耗上升;而且结皮严重造成堵塞时;有时被迫停窑处理;不利于水泥产质量的提高..预防结皮具有重要意义..现将防止结皮的措施简介如下:1减少或避免使用高硫和高氯的原料;这是减少结皮的前提..2如过量的硫和氯难以避免;建议丢弃一部分窑灰;以减少有害组分的循环..3采用旁路放风系统;即将回转窑窑尾高温烟气在预热器前从“旁路”中分离出一部分;与冷风混合;使以气相形态存在的“挥发物”冷凝在飞灰上;由收尘器将此飞灰收捕下来排出窑系统;以减少有害组分的循环..4避免使用高灰分及灰分熔点低的煤..预分解系统结皮原因分析和处理一般认为:结皮的产生与所用原料、燃料的成分;系统温度的变化;系统通风的情况;设备运转的情况以及工艺操作因素有关..下面结合一些的具体情况;通过对预热器各级旋风筒中原、燃料中有害元素的分析;以及设备状况;工艺操作等有关因素;对结皮形成的原因进行分析以及相应的处理方法..1.有害元素的影响有害元素主要包括硫、碱、氯等;它们是形成结皮的一个很重要的因素;煤炭作为目前水泥窑的主要燃料;是有害元素硫的一个重要来源;煤燃烧的大部分硫进入烟气中;烟气中带有大量的CaO生料粉;它在煅烧过程中与K2O、Na2O和SO3发生反应;生成各种硫酸盐物质;主要是K2SO4、2 CaSO4·K2SO4、K2SO4·H2O;;这些硫酸盐属于低熔点化合物;它们会粘附在器壁表面;使粘度增加;流动性减小;久而久之形成结皮..消除有害元素的影响主要是控制硫、碱的摩尔比;硫碱的摩尔比过高或过低都易形成结皮..即使硫、碱含量均较高;只要硫碱比在控制范围之内;对结皮也产生不了太大影响;因为原燃料中的大部分硫、碱可以中和在熟料中被带出..经过分解后的物料进入回转窑后;在烧成带温度极高的情况下;使K2SO4 分解成气态的K2O 和SO3;挥发进入循环气流..这些物质通过三次风管和窑返回到预热器中;在遇到低温时又生成成固相或液相化合物;附着在物料上被带回窑中;只有少部分热量和粉尘被排出;如此反复形成了预热器与回转窑中的碱循环..在新型干法水泥生产线中;由于原、燃料中的氯化物在窑内烧成挥发;并随窑内气体进入预分解系统;在此遇到较低温度而凝结于器壁表面;从而使回旋中的物料发粘;流动性变差;附着于壁;累积而形成结皮;附着在物料上的部分氯又进入窑内煅烧;一部分挥发形成气态进入循环气流;这样就形成了氯化物的循环..试验经验表明:当原燃料中氯含量超过0.02%时就容易形成结皮;这是由于氯所形成的化合物均为低熔点化合物;由于往复循环、累积;而不能被排出;形成较为牢固的结皮成分;若结皮严重时;该因素的影响不可忽略..2.工艺操作的影响2.1煤的控制煤的投入过程不均匀;增量或减量幅度过大;易使煤不完全燃烧;其一可能导致局部形成还原气氛;其二部分没有燃尽的煤粒附着在设备壁上继续燃烧;易产生局部高温而形成结皮..目前;在各水泥厂使用的气体分析仪是一种能反映煤炭是否燃烧完全的一种装置;当气体分析仪检测到CO浓度超过控制值时;为保护电收尘的安全;就会联锁停窑..煤的细度、水分亦影响结皮..煤粉中保持1.0-1.5%的水分可以促进燃烧;但是过量时会阻燃;使火焰伸长;烧成温度降低..煤的细度应严格控制;粗煤粉会使火焰黑火头变长;燃尽时间长;未燃烬的煤粉易掉到熟料中产生还原气氛;引起熟料结块;窑内结圈;从而引起系统通风不良;导致煤燃烧不完全; SO3含量上升;为结皮的形成创造了条件..2.2喂料的控制喂料不均;波动范围比较大时也易形成结皮..实际喂料量经常在设定值处上下波动;当其波动较大时;生料预热不好;分解率低;进入窑后;必然增加窑的热负荷;导致窑头用煤量增加;这样就会造成喂煤量时而大时而小;喂煤不稳定;导致预热器内的温度波动较大..煤的喂入量大时使预热器内部温度高或窑内火焰长时;造成高温带后移;而使预热器中的温度上升;导致一些低熔点化合物在预热器及窑尾处形成;粘附于器壁上而形成结皮..2.3系统的通风生产操作中;在稳定入窑生料和窑炉用煤量的比例后;还要调整好系统风量;分解炉的用风量以炉内形成料、煤能充分悬浮混合为均衡稳定的涡旋为基准..若三次风的量偏小;则影响炉内煤粉的燃烧和物料的分解;三次风量过大;易造成窑内通风不良;甚至造成窑尾缩口处因风速低而塌料..在操作上要根据窑炉内煤粉燃烧情况;保持窑尾上升烟道和三次风管的阻力平衡..窑尾空气过剩系数控制在1.1左右;分解炉的过剩空气系数控制在1.2以内;比较理想;但系统的总风量以保证煤粉的完全燃烧为依据..在操作过程中;过量通风虽然对磨机操作有一定的好处;但使预热器出口温度增高;热量流失多;热耗增加..在正常情况下为维持热工平衡;用煤量应保持相对的稳定..分解炉所用燃烧空气主要来自三次风和窑内排出的热烟气..如通风过大;容易造成分解炉内部压力增大负压;煤粉不完全燃烧;被带到窑尾的烟道上部;与窑尾热烟气接触继续燃烧;这样就使得烟道上部温度过高;使经过此处的气流中的成分易形成低熔点化合物;粘在物料上;附着于壁而形成结皮..3.设备状态的影响1燃烧器磨损;导致燃料不完全燃烧而产生一系列的影响;2投料量设定后;仔细检查计量装置计量是否准确;下料是否均匀;3检查排风机风叶的磨损情况;如供风不足可能是磨损比较严重;这样就使相同转速提供的风量小;局部造成还原气氛;4耐火材料内表面不平滑;有台阶;5密封不严;掺入冷风;会造成物料急冷而粘附于壁形成结皮..4.预防结皮的措施1控制好生料和出磨煤的细度;2确保通风良好;原燃料中有害成分不合理时尽早发现;及时采取措施;合理搭配;3如果结皮中有氯元素时;应分析原燃料中氯的含量;原燃料中局部氯含量超标时;为保证原料利用率应进行合理搭配;使含量高和含量低的混合;均化平衡保证达标后再用..氯是一种顽固成分;一旦进入预热器一直循环挥发不出来..如果某一时间段循环气流超标;可暂时采用旁路放风;以降低其含量;4原料在换堆时难免会使成分产生一定波动;主要表现在率值..这时应该有意识地进行调整;在调整生料时;应根据烧成情况适当调整煤投入量..在整个生产过程煤的投入量及速度一定要与生料的投入量及速度相对应;特别是在提料过程中尤其要重视;5如果窑控制的好;可使硫的挥发系数减小;并能减小还原气氛的产生机会;挥发不出来的硫也会被熟料带走;减少了循环气流中的SO3;6当发现经常有结皮现像产生;且情况比较严重时;可考虑更换衬料的品种;可以使用抗结皮的碳化硅浇注料..7保证耐火材料及设备内壁光滑;防止粘料堵塞..8采用高低碱石灰石合理搭配使用;控制碱含量;9添置氯检测设备;对原料中的氯含量进行测定;一旦发现有氯超标现象尽早采取措施..同时避免频繁的开点检门;加强法兰等部位的密封;以防漏入冷风..窑外分解窑窑尾系统的结皮积料的防治结皮是高温物料在烟室、上升管道、各级主要为三、四级旋风筒锥体内壁上粘结的一层层硬皮;严重的地方呈圈状缩口..阻碍了物料的正常运行;粘结和烧熔交替;使皮层数量和厚度渐渐增加;影响窑内通风、改变了预热器内物料与气流的运行速度和方向;最后甚至导致堵塞..造成这种现象的主要原因有三:1回灰的影响电收尘含增湿塔收下来的物料;已经经过高温物理化学反应;这种物料重新进入预热器时;很容易造成物料及早分解;提前出现液相;来不及到达窑内;在预热器内形成熔融状态;粘附在旋风筒内壁上;形成结皮;严重时导致堵塞..这种情况主要在窑尾系统温度偏高;回灰掺入不均匀或掺入量过大时发生..因此;那些旋风收尘器收尘效率不高;电收尘收下回灰又未进生料储存均化系统;而直接从提升泵等入窑的;或回灰掺入时没有稳料计量设施或此类设施失灵的生产线;更应加强操作;防止高温..同时也很有必要对回灰掺入系统进行调整和改造..提高系统旋风筒特别是顶级旋风收尘器收尘效率;降低进电收尘的粉尘含量;以减少回灰..2有害元素的影响原燃料中有害元素K、Na、Cl、S等含量高时;大量出现的碱便会从烧成带高温区挥发出来;进入气相与其它组分发生反应;首先与氯和二氧化硫反应;随气流带至窑尾系统;温度降低后;以硫酸盐和氯化物的形态冷凝在原料上..这种沉淀物在较低温度下出现熔融相;形成微细熔体;然后发生固体颗粒的固结..它们通过多次高温挥发;低温凝聚循环和附着作用;粘附在预热器、分解炉及联接管道内形成结皮;若处理不及时;继续循环粘附;最终导致堵塞..3局部高温造成结皮预分解系统温度偏高;而导致结皮的因素较多..如料流波动;煤粉因不完全燃烧进入预热器产生二次燃烧;系统操作不稳定等都会导致局部温度偏高;使液相提前出现;形成粘聚性物质结皮..料流忽大忽小;很容易打乱预热器、分解炉及窑的正常工作..而操作上往往滞后;跟不上料流的变化;加减煤不及时;甚至出现短时间断料;不能及时减煤;导致因料少系统温度偏高;造成结皮;堵塞..点火时由于煤粉在窑内或分解炉内燃烧不完全;一部分跑到预热器内附着在锥体和下料管上;温度升高时着火;形成局部高温..操作上;片面强调入窑分解率;分解炉用煤量过大;两把火比例失调;造成炉内温度偏高;过早出现液相;加之炉内物料切线速度高;离心力较大;很容易造成熔融物附着在炉壁上;形成炉内结皮;由于物料在分解炉内的停留时间极短;过量的煤粉在炉内来不及燃烧;被带至四级旋风筒形成二次燃烧;导致旋风筒内温度过高结皮..。
- 1、下载文档前请自行甄别文档内容的完整性,平台不提供额外的编辑、内容补充、找答案等附加服务。
- 2、"仅部分预览"的文档,不可在线预览部分如存在完整性等问题,可反馈申请退款(可完整预览的文档不适用该条件!)。
- 3、如文档侵犯您的权益,请联系客服反馈,我们会尽快为您处理(人工客服工作时间:9:00-18:30)。
塞物主要是结皮物料, 质硬, 碱含量高; C5 ̄C4 风管 水平段, 堵塞物主要是生料沉积物, 粉料多, 易清吹; 分解炉锥部, 堵塞物主要是煤灰高温熔融物。
2 堵塞原因分析
( 1) 化学分析发现, 我公司原燃材料中氯含量 较高, 其中石灰石中 Cl- 含量严重超标, 从而使入窑 生料中的 Cl- 含量居高不下, 另外燃料中的 Cl- 含量 也偏高; 对结皮堵塞料及窑灰的分析结果是, 其氯量 更高, 见表 2。因此有害成分氯含量较高是导致我公 司预分解系统频繁结皮堵塞的根本原因。
主机设备名称
设备型号
回转窑
!3.2 m×50 m
分解炉
!3.3 m×28 m+!2.51 m×42 m
预热器
NCⅢ 2- 1- 1- 1- 1
冷却机
LBT24135
高温风机
W6- 2×29- 4NO.21.5
( 2) 预分解系统易结皮堵塞部位主要有上升烟
道至 C5 风管水平段, C5 膨胀仓及下料管, 堵塞物主 要是高温粘结的物料; 窑尾烟室缩口和下料斜坡, 堵
( 编辑: 刘翠荣) ( 收稿日期: 2006- 02- 28)
征订启事
《中国陶瓷》杂志 月刊
邮发代号: 44- 30; 国外代号: BM1044
《中 国 陶 瓷 》杂 志 是 由 中 国 轻 工 业 陶 瓷 研 究 所 和 全 国 陶 瓷 工 业 信 息 中 心 共 同 主 办 、由 华 南 理 工 大 学 协 办 的 国 家 级大型综合性陶瓷科技期刊, 创刊于 1959 年, 是陶瓷行业 最 早 公 开 发 行 的 科 技 期 刊 。全 方 位 报 道 国 内 外 陶 瓷 行 业 的 发展动态和方向。大 16 开本, 80 页, 每月 15 日出版, 全年 12 期, 国内外公开发行。
( 3) 加强原燃料的质量控制, 尽量控制入厂原 料的有害成分, 稳定煤的发热量及灰分。合理配料, 加强均化, 以稳定生料质量, 减少生料质量波动带来 的一系列不良影响。改进后的熟料三率值控制范围 为: KH=0.88~0.90; SM=2.60~2.70; IM=1.50~1.60。这 一配料方案, 生料的易烧性较好且不易引起窑内结 圈结蛋。
C1 出口温度/℃
342
330
C5 出口压力/Pa
- 1 510 - 1 680
C5 出口温度/℃
830
801
C5 物料温度/℃
838
810
分 解 炉 内 温 度 /℃
865
831
分 解 炉 出 口 温 度 /℃
835
815
窑 尾 温 度 /℃
1 035
1 073
游 离 钙 含 量 /%
0.3
1.0
3 应对措施
( 1) 优化操作参数。因考虑生产用原燃材料无 法改变, 故着重操作参数的优化。主要是降低预热器 各处温度, 特别是分解炉本体及 C5 出口温度, 统一 各班组操作方法, 稳定系统热工制度, 尽量消除由于
表 2 物料中的 Cl- 含量
%
物料
石灰石
砂岩
铁粉 煤
入窑生料
上升烟 C5 堵 C5 下 窑尾烟 窑灰
1 窑系统主要配置及预分解系统易结皮堵塞的部位
( 1) 窑系统主要配置。该生产线由南京水泥工 业设计研究院设计, 窑系统主机配置见表 1。其中, 分解炉采用南京院开发的 NCⅢ型双喷腾管道式分 解炉, 其分解炉出口带有 !2.51 m×42 m 的鹅颈管 道; 冷却机为第二代推动篦式冷却机。
表 1 新绛威顿公司 1 000 t/d 生产线窑系统主机配置
名称 #1 样 #2 样 #3 样 #1 样 #2 样
#1 样 #2 样 #3 样 #4 样
道结皮 料样 料管 室样
w(Cl- ) 0.025 0.034 0.069 0.004 0.006 0.005 0.107 0.054 0.060 0.055 0.081 0.918 11.41 1.660 7.09 1.604
高温风机转速/( r·min-1)
1 245
1 169
高 温 风 机 电 流 /A
66
62
二 次 风 温 度 /℃
1 085
1 020
三 次 风 温 度 /℃
690
701
窑 尾 高 温 闸 阀 开 度 /%
100
50
三 次 风 管 高 温 闸 阀 开 度 /%
100
100
入 炉 三 次 风 压 力 /Pa
( 2) 原料成分的波动, 带来生料质量的不稳定, 生料易烧性在同一个班中都会有很大变化, 导致窑 内经常出现结大块、结圈和飞砂料的情况; 而结圈、 结蛋又导致窑内通风不良, 煤粉不完全燃烧, 造成预 热器因煤粉后燃烧带来局部高温而引起结皮堵塞。
( 3) 操作问题。一是窑、炉用风分配不当, 会使 窑缩口或分解炉入口风速过低或过高, 物料在预热 器系统中分布不均, 分解炉内气体流场混乱, 发生棚 料或塌料而造成结皮堆积堵塞。二是操作参数控制 非最佳。调试初期, 控制窑尾、分解炉内、分解炉出 口 、C5 出 口 、C5 物 料 、C1 出 口 的 温 度 范 围 分 别 为 : 10000~10050 ℃, 850~870 ℃, 820~840 ℃, 830~850 ℃, 840~860 ℃, 330~350 ℃, 经过一段时间的操作发现 C5 筒频繁堵塞, 这组温度参数控制范围不适合我公 司高 Cl- 原燃材料的煅烧操作。
4 结语
通过采取以上措施, 我公司因结皮堵塞停机次 数及停机时间大幅减少, 回转窑工况稳定, 熟料产质 量稳步提高。实践证明, 根据各窑的系统特点和原燃 料状况, 通过配料优化、操作摸索并配以增加相关的 监控设施和加强管理等措施, 减少甚至完全杜绝预 热器系统的结皮堵塞是可实现的。
参考文献
[1] 张卫东.高氯原料在预分解窑系统中的实践和应用[J].水泥 工程,2003, ( 5) [2] 杨书慧,于加滨.2 000 t/d 预分解窑增产后的操作[J].新世纪 水泥导报,2004, ( 1)
定价: 10 元/期, 全年 120 元 地址: 江西省景德镇新厂西路 556 号 邮编: 333000 电话: 0798- 8439093; 8439006 传真: 0798- 8439008 E- mail: china_ceramics@vip.163.com
或 china_ceramics@sina.com
水泥工程 2006 年第 6 期
- 4 -
- 44 -
水泥工程 2006 年第 6 期
支俊秉, 等: 预分解系统结皮堵塞的原因及处理对策
生产技术
操作原因而造成的结皮堵塞。为便于比较, 选取了同 一产量调整前后的操作参数列于表 3。
表 3 窑系统主要参数范围对比
参数名称
调整前 调整后
生料喂料量/( t·h-1)
76
76
C1 出口压力/Pa
- 5 215 - 5 375
生产技术
支俊秉, 等: 预分解系统结皮堵塞的原因及处理对策
中图分类号: TQ172.62
文献标识码: B
文章编号: 1007- 0389( 2006) 06- 0044- 02
预分解系统结皮堵塞的原因及处理对策
支俊秉, 石云生(山西新绛威顿水泥有限责任公司, 山西 新绛 043100)
0 前言
预热器系统堵塞, 不仅会扰乱窑的热工制度, 降 低熟料产量和质量, 影响窑的运转率, 而且处理起来 费时费力, 甚至对人身安全造成危害。我公司 2001 年 8 月 26 日点火投产的 1 000 t/d 熟料的新型干法 水泥生产线, 目前熟料产量能长期稳定在 1 200 t/d 且运行率高。但该线在投产初期, 预热器系统结皮堵 塞非常严重, 几乎是“三天一小堵, 五天一大堵”, 后 通过对原燃材料的成分、配料方案的优化及煅烧方 案的改进, 使这一影响系统运行的瓶颈问题得以解 决。2003 年 5 月份的窑系统运转率高达 99%, 仅因 C5 筒下料管被结皮卡住止料 13 min。此后因窑尾预 分解系统的结皮堵塞而影响生产的状况就极少发 生。本文就此作一分析和总结介绍。
- 300
- 350
窑 尾 负 压 /Pa
- 80
- 160
窑速/( r·min-1)
3.0
3.5
从表 3 可知, 操作参数的调整幅度很大。其中分 解 炉 本 体 温 度 下 降 了 34 ℃, C5 出 口 温 度 下 降 了 29 ℃, 窑尾温度提高了 38 ℃。对我公司采用的高氯 原燃烧料而言, 提高窑尾温度, 抑制了有害成分在窑 内 20~40 m 处的低温粘结富集。在相同喂料量时窑 速的加快, 可明显降低窑内物料填充率, 相对增加了
窑头煤粉的燃烧空间, 减少了煤粉的不完全燃烧, 有 效抑制了预热器的结皮堵塞。
( 2) 对易堵塞的 C5 膨胀仓及下料管部位, 增加 了两个测压点和增设三个空气炮, 并实现中控控制。 同时对增湿塔及电收尘器收集的高氯窑灰料, 经过 技术攻关后有 60%入水泥磨系统, 尽量减少外部循 环富集对预热器的影响。