连续铸轧技术总结
连铸年终总结范文

时光荏苒,岁月如梭,转眼间又到了一年的尾声。
在过去的一年里,我国连铸行业在技术创新、产业升级、市场拓展等方面取得了显著成绩。
在此,我对本年度连铸工作进行全面总结,以期为新的一年工作提供借鉴和启示。
一、工作回顾1. 技术创新过去的一年,我们紧紧围绕连铸技术的创新与突破,加大研发投入,取得了多项重要成果。
主要体现在以下几个方面:(1)成功研发了新型连铸机,提高了生产效率和产品质量;(2)优化了连铸工艺,降低了能耗和物耗;(3)引进国外先进技术,提升了国产连铸设备水平。
2. 产业升级为了适应市场需求,我们积极推进产业升级,重点发展以下领域:(1)高强度、高性能钢材;(2)绿色、环保型钢材;(3)精密、复杂型钢材。
3. 市场拓展在市场竞争日益激烈的背景下,我们积极开展市场拓展工作,取得了以下成绩:(1)成功开拓了国内外市场,市场份额逐年提升;(2)与多家知名企业建立了长期合作关系;(3)积极参与国际竞争,提升我国连铸产业的国际地位。
二、存在问题1. 技术创新不足,与国外先进水平仍有差距;2. 产业链条不够完善,部分关键设备依赖进口;3. 市场竞争加剧,部分产品价格波动较大。
三、展望未来面对新的一年,我们将继续深化改革,创新发展,为实现以下目标而努力:1. 加大技术创新力度,缩小与国外先进水平的差距;2. 优化产业链条,提升国产设备水平;3. 拓展市场,提高市场份额;4. 强化企业文化建设,提升员工综合素质。
总之,过去的一年,我们在连铸行业取得了丰硕的成果。
在新的一年里,我们将继续努力,为实现我国连铸产业的繁荣发展贡献自己的力量。
让我们携手共进,共创辉煌!。
2024年铝业公司员工铸轧工作个人总结

2024年铝业公司员工铸轧工作个人总结时间如梭,转眼间我已经在铝业公司担任铸轧工作已经三年了。
在这三年的时间里,我积累了丰富的工作经验,提高了自己的专业技能。
通过不断学习和实践,我逐渐成长为一名技术娴熟、责任心强的员工。
在这里,我将对过去三年的工作进行总结和反思。
一、技术能力提升作为铸轧工作员,技术能力是最基本的素质之一。
在这三年里,我通过学习和实践不断提高了自己的技术水平。
首先,我熟练掌握了铸轧设备的操作和维护。
通过与前辈的沟通和观摩学习,我逐渐摸索出了适合自己的铸轧技术方法。
其次,在生产过程中,我注重学习和运用新的技术。
比如,我学习了先进的冷轧技术,在实际工作中运用这些新技术,提高了生产效率和产品质量。
二、团队协作能力铝材生产是一个复杂的系统工程,需要各个环节的紧密配合和协作。
在工作中,我逐渐培养了良好的团队合作精神。
我积极参与团队讨论,与同事们相互配合,解决生产过程中的问题。
我也乐于倾听他人的建议和批评,不断改进自己的工作方式。
在团队合作中,我也学习到了如何与人相处,如何激励和引导团队成员,形成了一种团结互助的氛围。
三、安全生产意识作为一名铝业公司的员工,安全生产是我们永远不能忽视的重点。
在过去三年的工作中,我时刻保持着高度警惕,严格按照安全操作规程进行生产。
我加强了对铸轧设备的日常检修和维护,确保设备正常运行,并及时发现和解决隐患问题。
在生产过程中,我也积极参与企业组织的安全生产活动,增强了自己的安全意识和安全技能。
四、问题解决能力在工作中,经常会遇到各种各样的问题和困难。
面对这些问题,我不回避和逃避,而是勇于迎接和解决。
我积极锻炼自己的问题解决能力,学会分析问题的根源和原因,并提出合理的解决方案。
在过去的三年里,我成功解决了许多生产上的难题,通过不断总结和反思,我也积累了更多解决问题的经验和方法。
总之,这三年来在铝业公司铸轧工作岗位上的经历,让我受益匪浅。
我不仅学到了专业知识和技能,还培养了良好的团队合作精神和安全意识。
2024年铝业公司员工铸轧工作个人总结

2024年铝业公司员工铸轧工作个人总结尊敬的领导:您好!我是铝业公司在2024年度的一名铸轧工,非常荣幸能给您写下这篇个人总结,向您汇报我在过去一年的工作情况和收获。
回顾过去一年,在这个快节奏和竞争激烈的铝业市场中,我充分发挥专业技术和团队合作精神,以高度的责任感和积极主动的工作态度,努力参与和推动铸轧工作的改进和提高。
通过不断学习和实践,我在铝业铸轧领域的专业技术能力和协同沟通能力有了较大的提升。
首先,在工作中,我注重技术的钻研和实践。
铸轧工作需要具备一定的专业知识和操作技能,在铸轧生产线上,我认真学习铸轧的原理和技巧,不断提高自己的铸轧操作能力。
积极配合主管进行设备的调试和运转,关注铸轧工作中的质量控制和生产效率的提高。
通过不断地总结经验,我能够熟练地完成各项工作任务,并能够迅速处理各种工作中的问题和突发事件,保证生产线的正常运行。
其次,在团队合作方面,我始终秉持着积极沟通和团队协作的原则。
铝业铸轧工作需要团队合作,我们的工作涉及到多个环节和多个岗位,所以我非常注重与他人的沟通和协调,互相帮助解决问题。
无论是与设备调试工程师的沟通,还是与生产线上其他工人的合作,我总是以友好、互助的态度面对,并能够与团队成员安排合理的工作任务和时间表。
除了专业能力和团队合作之外,我还注重自我学习和提升。
通过参加公司组织的培训课程,我不仅了解了最新的铝业铸轧技术动态,也掌握了一些管理技巧和沟通技能。
同时,我还积极关注行业内的最新研究和实践,努力与业界前沿保持接轨,为公司的发展和提高做出应有的贡献。
最后,在工作中我非常注重安全生产和环境保护。
作为一名铸轧工,我时刻保持谨慎和主动的工作态度,不仅保障自身的安全,也尽力减少对环境的污染。
我积极参与公司的安全和环保活动,以身作则,带动身边的同事关注和重视安全和环境问题,共同为公司的可持续发展贡献一份力量。
通过一年的工作实践,我认为自己在铸轧领域的专业知识和操作能力有了一定的提高。
连铸技术总结
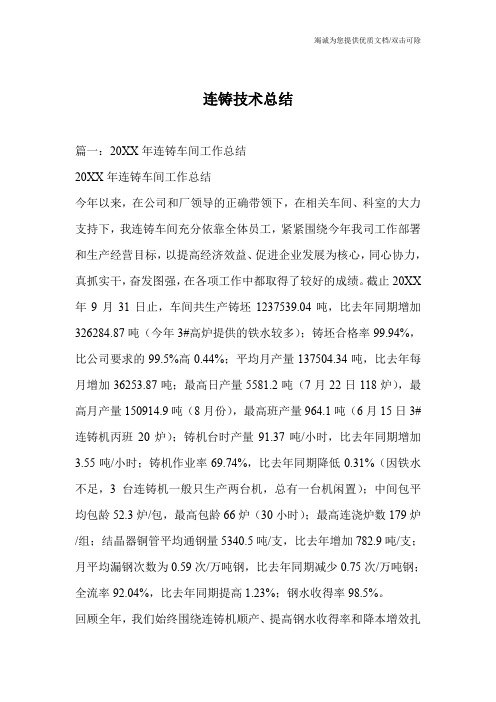
连铸技术总结篇一:20XX年连铸车间工作总结20XX年连铸车间工作总结今年以来,在公司和厂领导的正确带领下,在相关车间、科室的大力支持下,我连铸车间充分依靠全体员工,紧紧围绕今年我司工作部署和生产经营目标,以提高经济效益、促进企业发展为核心,同心协力,真抓实干,奋发图强,在各项工作中都取得了较好的成绩。
截止20XX 年9月31日止,车间共生产铸坯1237539.04吨,比去年同期增加326284.87吨(今年3#高炉提供的铁水较多);铸坯合格率99.94%,比公司要求的99.5%高0.44%;平均月产量137504.34吨,比去年每月增加36253.87吨;最高日产量5581.2吨(7月22日118炉),最高月产量150914.9吨(8月份),最高班产量964.1吨(6月15日3#连铸机丙班20炉);铸机台时产量91.37吨/小时,比去年同期增加3.55吨/小时;铸机作业率69.74%,比去年同期降低0.31%(因铁水不足,3台连铸机一般只生产两台机,总有一台机闲置);中间包平均包龄52.3炉/包,最高包龄66炉(30小时);最高连浇炉数179炉/组;结晶器铜管平均通钢量5340.5吨/支,比去年增加782.9吨/支;月平均漏钢次数为0.59次/万吨钢,比去年同期减少0.75次/万吨钢;全流率92.04%,比去年同期提高1.23%;钢水收得率98.5%。
回顾全年,我们始终围绕连铸机顺产、提高钢水收得率和降本增效扎扎实实地抓好了以下几方面工作:1、提高钢水收得率20XX年钢水收得率仅为98.41%,最低的是去年9月只有97.44%。
为此车间从今年6月份开始从各个环节严抓细管,并出台对应的管理措施:(1)定期校核行车和轧钢炉头电子称,确保其精度。
(2)减少非计划停浇事故。
(3)减少漏钢、顶坯、重接等次数。
(4)确保设备运行正常,减少因设备和人为操作原因造成的非定尺坯和弯坯数量。
(5)提高大包工在浇注末期分清钢水和红渣的能力,把钢水浇完。
铝业铸轧年度总结(3篇)
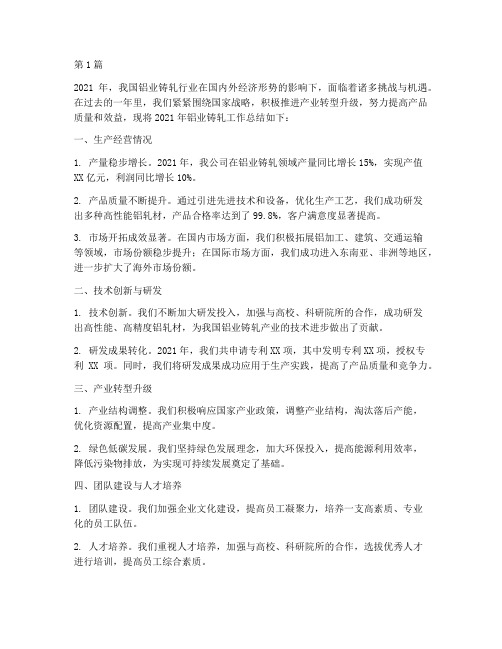
第1篇2021年,我国铝业铸轧行业在国内外经济形势的影响下,面临着诸多挑战与机遇。
在过去的一年里,我们紧紧围绕国家战略,积极推进产业转型升级,努力提高产品质量和效益,现将2021年铝业铸轧工作总结如下:一、生产经营情况1. 产量稳步增长。
2021年,我公司在铝业铸轧领域产量同比增长15%,实现产值XX亿元,利润同比增长10%。
2. 产品质量不断提升。
通过引进先进技术和设备,优化生产工艺,我们成功研发出多种高性能铝轧材,产品合格率达到了99.8%,客户满意度显著提高。
3. 市场开拓成效显著。
在国内市场方面,我们积极拓展铝加工、建筑、交通运输等领域,市场份额稳步提升;在国际市场方面,我们成功进入东南亚、非洲等地区,进一步扩大了海外市场份额。
二、技术创新与研发1. 技术创新。
我们不断加大研发投入,加强与高校、科研院所的合作,成功研发出高性能、高精度铝轧材,为我国铝业铸轧产业的技术进步做出了贡献。
2. 研发成果转化。
2021年,我们共申请专利XX项,其中发明专利XX项,授权专利XX项。
同时,我们将研发成果成功应用于生产实践,提高了产品质量和竞争力。
三、产业转型升级1. 产业结构调整。
我们积极响应国家产业政策,调整产业结构,淘汰落后产能,优化资源配置,提高产业集中度。
2. 绿色低碳发展。
我们坚持绿色发展理念,加大环保投入,提高能源利用效率,降低污染物排放,为实现可持续发展奠定了基础。
四、团队建设与人才培养1. 团队建设。
我们加强企业文化建设,提高员工凝聚力,培养一支高素质、专业化的员工队伍。
2. 人才培养。
我们重视人才培养,加强与高校、科研院所的合作,选拔优秀人才进行培训,提高员工综合素质。
五、未来展望2022年,我们将继续深化改革,创新发展,努力实现以下目标:1. 产量稳定增长。
力争实现产量同比增长10%,产值达到XX亿元。
2. 产品质量持续提升。
加大研发投入,提高产品性能,满足客户需求。
3. 市场份额不断扩大。
钢厂连铸工作总结范文(3篇)

第1篇一、前言随着我国钢铁工业的快速发展,连铸技术已成为现代钢铁生产的重要环节。
作为一名钢厂连铸工作者,我深知连铸工艺在生产中的重要性。
在过去的一年里,我本着对工作的高度负责和对技术的不断追求,积极参与到连铸生产中,现将一年来的工作总结如下:二、工作回顾1. 技术培训与学习(1)参加连铸工艺及设备知识培训,系统地学习了连铸工艺流程、设备操作、故障处理等方面的知识。
(2)参加安全生产培训,提高了安全意识,掌握了安全操作规程。
(3)通过阅读专业书籍、资料,不断丰富自己的专业知识。
2. 生产管理(1)严格执行生产计划,确保生产任务的顺利完成。
(2)加强生产调度,合理分配生产资源,提高生产效率。
(3)加强对生产现场的管理,确保生产环境整洁、设备运行正常。
(4)定期对生产数据进行统计分析,为生产优化提供依据。
3. 设备维护与保养(1)严格执行设备维护保养制度,确保设备正常运行。
(2)发现设备故障,及时上报并参与处理,降低设备故障率。
(3)定期对设备进行巡检,发现隐患及时整改。
4. 安全生产(1)严格遵守安全生产规章制度,确保生产安全。
(2)加强现场安全管理,消除安全隐患。
(3)积极参与安全生产活动,提高安全意识。
5. 团队协作(1)与同事保持良好的沟通,共同解决问题。
(2)关心同事,互相帮助,形成团结协作的氛围。
(3)积极参与团队活动,增强团队凝聚力。
三、工作总结1. 技术方面(1)熟练掌握了连铸工艺及设备操作,能够独立处理生产过程中出现的问题。
(2)对连铸生产中的关键技术有较深入的了解,能够为生产优化提供技术支持。
(3)通过不断学习,提高了自己的专业素养,为今后的工作打下了坚实基础。
2. 管理方面(1)能够按照生产计划合理安排生产任务,确保生产任务的顺利完成。
(2)具备较强的组织协调能力,能够处理生产过程中的突发事件。
(3)对生产现场管理有较深入的了解,能够确保生产环境整洁、设备运行正常。
3. 安全方面(1)严格遵守安全生产规章制度,确保生产安全。
铝业公司铸轧工作个人总结
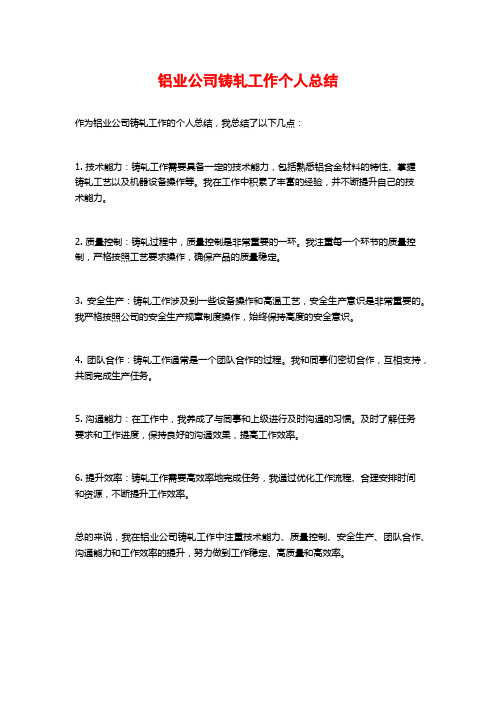
铝业公司铸轧工作个人总结
作为铝业公司铸轧工作的个人总结,我总结了以下几点:
1. 技术能力:铸轧工作需要具备一定的技术能力,包括熟悉铝合金材料的特性、掌握
铸轧工艺以及机器设备操作等。
我在工作中积累了丰富的经验,并不断提升自己的技
术能力。
2. 质量控制:铸轧过程中,质量控制是非常重要的一环。
我注重每一个环节的质量控制,严格按照工艺要求操作,确保产品的质量稳定。
3. 安全生产:铸轧工作涉及到一些设备操作和高温工艺,安全生产意识是非常重要的。
我严格按照公司的安全生产规章制度操作,始终保持高度的安全意识。
4. 团队合作:铸轧工作通常是一个团队合作的过程。
我和同事们密切合作,互相支持,共同完成生产任务。
5. 沟通能力:在工作中,我养成了与同事和上级进行及时沟通的习惯。
及时了解任务
要求和工作进度,保持良好的沟通效果,提高工作效率。
6. 提升效率:铸轧工作需要高效率地完成任务,我通过优化工作流程、合理安排时间
和资源,不断提升工作效率。
总的来说,我在铝业公司铸轧工作中注重技术能力、质量控制、安全生产、团队合作、沟通能力和工作效率的提升,努力做到工作稳定、高质量和高效率。
连铸连轧个人年终总结

连铸连轧个人年终总结2021年即将过去,回首这一年,我作为连铸连轧生产线的一员,不禁感慨万分。
在这一年的工作中,我经历了许多挑战和成长,收获了宝贵的经验和教训。
在这里,我将就我的工作经历和心得体会进行总结和分享。
一、工作概况作为连铸连轧生产线的一员,我的工作职责包括负责设备的操作和维护,确保生产线的稳定运行,保证产品质量。
在这一年中,我积极投入工作,刻苦钻研技术和工艺,努力提升自己的专业素养。
我严格遵守工作纪律,准时到岗上班,严守操作规程,时刻保持警惕,确保生产过程的安全和顺利进行。
二、工作亮点在工作中,我积极参与工作中的各个环节,努力做到精益求精。
首先,我主动学习并熟练掌握了连铸连轧设备的操作和维护知识,能够独立完成设备调试和故障排除。
其次,我不断总结和分享操作经验,帮助团队成员提升工作效率。
同时,我也积极参与改进工作,提出建设性的意见和建议,为生产线的稳定运行和效率提升做出了贡献。
三、工作挑战在工作中,我也遇到了不少挑战。
首先,连铸连轧生产线的工作环境复杂,工作压力大。
面对高强度的工作任务,我时刻保持积极的心态,勇于迎接挑战,在与同事的密切合作中不断学习和成长。
其次,设备故障的处理也是一个不容忽视的问题。
我充分利用公司提供的培训资源,加强了对设备故障排除的技能和知识的学习,提高了自身的解决问题的能力。
四、工作心得通过这一年的工作,我深刻体会到了团队合作的重要性。
在连铸连轧生产线这个大家庭中,每个人的工作都紧密相连,需要相互依赖和支持。
我学会了倾听和理解团队成员的需求,与他们保持良好的沟通和协作,以提高整个团队的工作效率和凝聚力。
此外,对于新技术的学习也至关重要。
我会继续加强对新技术和工艺的学习,不断提升自己的专业素养,为公司的发展做出更大的贡献。
五、展望未来展望未来,我将继续保持对工作的热情和努力,不断提高自己的专业技能和团队协作能力。
我希望能在连铸连轧生产线这个大家庭中,发挥更大的作用,为公司的发展贡献自己的力量。
2024年铝业公司员工铸轧工作个人总结
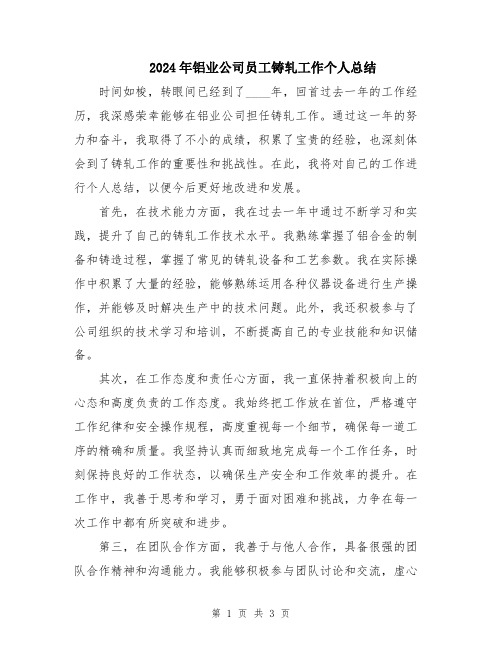
2024年铝业公司员工铸轧工作个人总结时间如梭,转眼间已经到了____年,回首过去一年的工作经历,我深感荣幸能够在铝业公司担任铸轧工作。
通过这一年的努力和奋斗,我取得了不小的成绩,积累了宝贵的经验,也深刻体会到了铸轧工作的重要性和挑战性。
在此,我将对自己的工作进行个人总结,以便今后更好地改进和发展。
首先,在技术能力方面,我在过去一年中通过不断学习和实践,提升了自己的铸轧工作技术水平。
我熟练掌握了铝合金的制备和铸造过程,掌握了常见的铸轧设备和工艺参数。
我在实际操作中积累了大量的经验,能够熟练运用各种仪器设备进行生产操作,并能够及时解决生产中的技术问题。
此外,我还积极参与了公司组织的技术学习和培训,不断提高自己的专业技能和知识储备。
其次,在工作态度和责任心方面,我一直保持着积极向上的心态和高度负责的工作态度。
我始终把工作放在首位,严格遵守工作纪律和安全操作规程,高度重视每一个细节,确保每一道工序的精确和质量。
我坚持认真而细致地完成每一个工作任务,时刻保持良好的工作状态,以确保生产安全和工作效率的提升。
在工作中,我善于思考和学习,勇于面对困难和挑战,力争在每一次工作中都有所突破和进步。
第三,在团队合作方面,我善于与他人合作,具备很强的团队合作精神和沟通能力。
我能够积极参与团队讨论和交流,虚心听取他人的意见和建议,并能够与团队成员有效地协作和配合,共同完成工作任务。
在与同事的合作中,我始终保持着良好的沟通和理解,尊重和包容他人的意见,形成了良好的工作氛围和团队合作精神。
我相信,在团队的力量下,我们能够取得更好的成绩,实现共同的目标。
最后,在问题解决能力方面,我在过去一年的工作中锻炼了自己的问题解决能力。
在生产中,难免会遇到各种各样的问题和困难,如设备故障、工艺问题等等。
我能够迅速分析和解决问题,运用所学的知识和经验找到最佳的解决方案,并及时采取行动。
我懂得从问题中汲取教训,总结经验,不断完善自己的工作方式和方法,以适应不断变化的工作环境和需求。
2024年铝业企业工人铸轧工作总结(2篇)
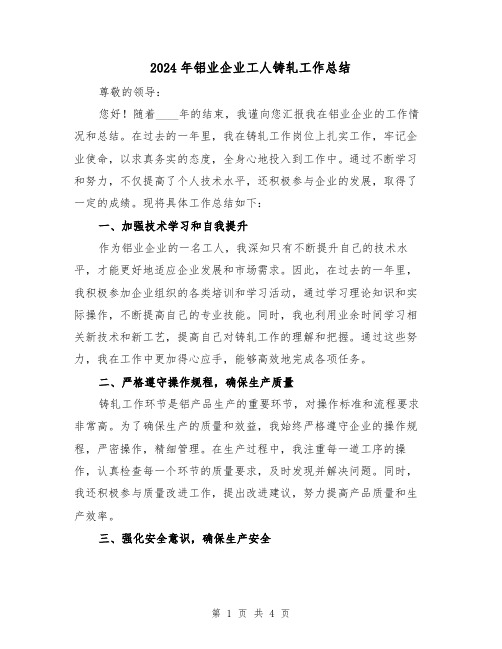
2024年铝业企业工人铸轧工作总结尊敬的领导:您好!随着____年的结束,我谨向您汇报我在铝业企业的工作情况和总结。
在过去的一年里,我在铸轧工作岗位上扎实工作,牢记企业使命,以求真务实的态度,全身心地投入到工作中。
通过不断学习和努力,不仅提高了个人技术水平,还积极参与企业的发展,取得了一定的成绩。
现将具体工作总结如下:一、加强技术学习和自我提升作为铝业企业的一名工人,我深知只有不断提升自己的技术水平,才能更好地适应企业发展和市场需求。
因此,在过去的一年里,我积极参加企业组织的各类培训和学习活动,通过学习理论知识和实际操作,不断提高自己的专业技能。
同时,我也利用业余时间学习相关新技术和新工艺,提高自己对铸轧工作的理解和把握。
通过这些努力,我在工作中更加得心应手,能够高效地完成各项任务。
二、严格遵守操作规程,确保生产质量铸轧工作环节是铝产品生产的重要环节,对操作标准和流程要求非常高。
为了确保生产的质量和效益,我始终严格遵守企业的操作规程,严密操作,精细管理。
在生产过程中,我注重每一道工序的操作,认真检查每一个环节的质量要求,及时发现并解决问题。
同时,我还积极参与质量改进工作,提出改进建议,努力提高产品质量和生产效率。
三、强化安全意识,确保生产安全安全生产是企业的首要任务,也是每一位工人应该高度重视的。
在过去的一年里,我时刻保持对安全工作的高度警惕,严格执行企业的安全制度和操作规程,做到勤思考、勤反思、勤总结。
在工作中,我注重防范安全隐患,及时发现并报告问题,确保生产环境的安全和稳定。
同时,我也积极参与安全培训和演练活动,提高自己的安全意识和应对能力。
四、团结协作,完成生产任务作为一个铝业企业的工人,我深知团队合作的重要性。
在过去的一年里,我积极与同事们进行沟通和协作,共同完成各项生产任务。
面对工作中的困难和问题,我主动提出解决方案,并与团队一起努力克服。
在团队合作中,我积累了丰富的经验,也更加深刻地体会到团队的力量。
2024年铝业公司员工铸轧工作个人总结

2024年铝业公司员工铸轧工作个人总结2024年对于铝业公司员工铸轧工作而言是一个充满挑战和机遇的一年。
在这一年中,我在铸轧工作中取得了一些成绩,同时也面临了一些困难和问题。
首先,我在2024年中通过不断学习和实践,提高了自己在铸轧工作中的技能和知识水平。
我参加了好几次培训课程,学习了最新的铸轧技术和操作方法。
我还积极参与公司内外的铸轧交流和技术研讨会,与同行们分享经验和学习。
通过这些努力,我能够更好地应对日常工作中的难题,提高工作效率和质量。
其次,在2024年中,我在团队合作方面取得了一些进展。
铝业公司的铸轧工作需要各个环节之间的协调和配合。
我积极与其他部门的同事进行沟通和协商,确保生产计划的顺利执行。
我也花时间培养自己的领导能力,能够在铸轧工作中担任一些领导角色,组织和指导团队成员的工作。
然而,2024年的铸轧工作也面临一些困难和问题。
首先,市场需求的变化给铸轧工作带来了不确定性。
铝制品的市场需求受到多种因素影响,预测和应对市场变化成为一项重要挑战。
其次,技术进步需要不断跟进和适应。
铸轧技术在不断发展,新的设备和工艺可能需要我们更新知识和技能。
最后,安全问题也是铸轧工作中不可忽视的因素。
铸轧工作对员工的安全要求非常高,我们需要时刻保持警惕,严格遵守安全操作规程,确保自己和他人的安全。
总的来说,2024年铝业公司员工铸轧工作既有进展又面临挑战。
通过不断学习和努力,我相信我们能够克服困难,保持竞争力,为公
司的发展做出更大的贡献。
在未来,我将继续提升自己的专业能力和领导能力,在铸轧工作中继续取得更好的成绩。
炼钢连铸年度总结(3篇)

第1篇一、前言随着我国经济的快速发展,钢铁行业作为国民经济的重要支柱产业,其地位和作用日益凸显。
炼钢连铸作为钢铁生产的关键环节,其技术水平的高低直接影响着钢铁企业的生产效率和产品质量。
本年度,我单位在炼钢连铸领域取得了显著成绩,现将年度总结如下:二、工作回顾1. 技术创新与改进(1)设备升级:本年度,我单位对炼钢连铸设备进行了全面升级,引进了国际先进的炼钢连铸生产线,提高了生产效率和产品质量。
(2)工艺优化:针对生产过程中存在的问题,我们不断优化炼钢连铸工艺,降低能耗,提高金属收得率,确保产品质量稳定。
(3)技术创新:我单位积极开展技术创新,成功研发了多项新技术、新工艺,为炼钢连铸生产提供了有力保障。
2. 安全生产(1)加强安全管理:我们始终把安全生产放在首位,严格执行安全生产责任制,确保生产过程安全稳定。
(2)隐患排查治理:定期开展安全隐患排查,及时发现并消除安全隐患,降低事故发生率。
(3)员工安全培训:加强员工安全教育培训,提高员工安全意识和操作技能。
3. 降本增效(1)优化生产流程:通过优化生产流程,提高生产效率,降低生产成本。
(2)节能降耗:加大节能降耗工作力度,降低能源消耗,提高资源利用率。
(3)技术创新:通过技术创新,降低原材料消耗,提高产品附加值。
4. 市场拓展(1)开拓新市场:积极拓展国内外市场,提高产品市场占有率。
(2)加强客户关系维护:与客户保持良好沟通,提高客户满意度。
(3)提升品牌形象:通过优质的产品和服务,提升企业品牌形象。
三、工作亮点1. 生产指标完成情况(1)产量:本年度,炼钢连铸产量同比增长10%,超额完成年度生产任务。
(2)质量:产品质量稳定,合格率高达99.8%,顾客满意度不断提高。
(3)能耗:通过节能降耗措施,能耗同比下降5%,为企业节约了大量成本。
2. 技术创新成果(1)成功研发了新型炼钢连铸工艺,提高了生产效率和产品质量。
(2)引进了国际先进的炼钢连铸生产线,提升了企业核心竞争力。
2024年铝业公司铸轧工作个人总结
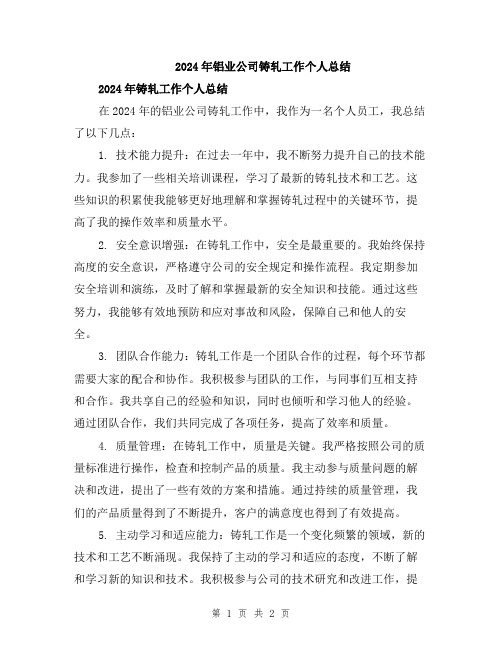
2024年铝业公司铸轧工作个人总结2024年铸轧工作个人总结在2024年的铝业公司铸轧工作中,我作为一名个人员工,我总结了以下几点:1. 技术能力提升:在过去一年中,我不断努力提升自己的技术能力。
我参加了一些相关培训课程,学习了最新的铸轧技术和工艺。
这些知识的积累使我能够更好地理解和掌握铸轧过程中的关键环节,提高了我的操作效率和质量水平。
2. 安全意识增强:在铸轧工作中,安全是最重要的。
我始终保持高度的安全意识,严格遵守公司的安全规定和操作流程。
我定期参加安全培训和演练,及时了解和掌握最新的安全知识和技能。
通过这些努力,我能够有效地预防和应对事故和风险,保障自己和他人的安全。
3. 团队合作能力:铸轧工作是一个团队合作的过程,每个环节都需要大家的配合和协作。
我积极参与团队的工作,与同事们互相支持和合作。
我共享自己的经验和知识,同时也倾听和学习他人的经验。
通过团队合作,我们共同完成了各项任务,提高了效率和质量。
4. 质量管理:在铸轧工作中,质量是关键。
我严格按照公司的质量标准进行操作,检查和控制产品的质量。
我主动参与质量问题的解决和改进,提出了一些有效的方案和措施。
通过持续的质量管理,我们的产品质量得到了不断提升,客户的满意度也得到了有效提高。
5. 主动学习和适应能力:铸轧工作是一个变化频繁的领域,新的技术和工艺不断涌现。
我保持了主动的学习和适应的态度,不断了解和学习新的知识和技术。
我积极参与公司的技术研究和改进工作,提出了一些建议和方案。
通过不断学习和适应,我能够更好地应对各种新的挑战和变化。
总的来说,2024年的铸轧工作对我来说是一个充满挑战和机遇的一年。
通过不断努力和学习,我在技术、安全、团队合作、质量管理和学习能力等方面都有了明显的提升。
在未来的工作中,我将继续保持积极的态度,不断提升自己的能力,为铝业公司的发展做出更大的贡献。
连续铸轧技术总结
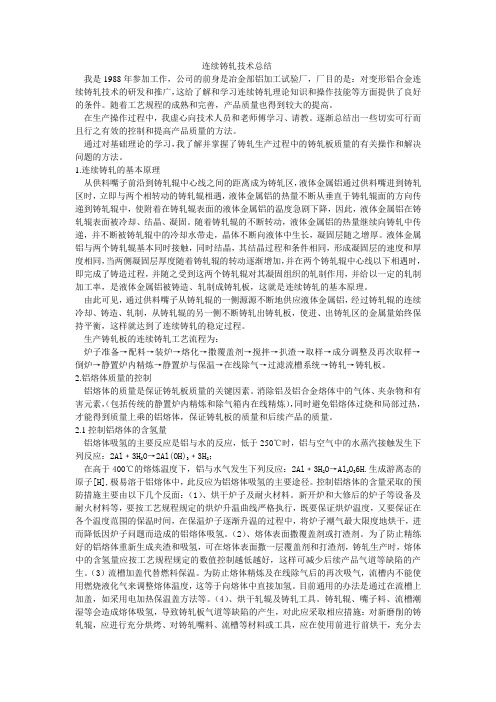
连续铸轧技术总结我是1988年参加工作,公司的前身是冶金部铝加工试验厂,厂目的是:对变形铝合金连续铸轧技术的研发和推广,这给了解和学习连续铸轧理论知识和操作技能等方面提供了良好的条件。
随着工艺规程的成熟和完善,产品质量也得到较大的提高。
在生产操作过程中,我虚心向技术人员和老师傅学习、请教。
逐渐总结出一些切实可行而且行之有效的控制和提高产品质量的方法。
通过对基础理论的学习,我了解并掌握了铸轧生产过程中的铸轧板质量的有关操作和解决问题的方法。
1.连续铸轧的基本原理从供料嘴子前沿到铸轧辊中心线之间的距离成为铸轧区,液体金属铝通过供料嘴进到铸轧区时,立即与两个相转动的铸轧辊相遇,液体金属铝的热量不断从垂直于铸轧辊面的方向传递到铸轧辊中,使附着在铸轧辊表面的液体金属铝的温度急剧下降,因此,液体金属铝在铸轧辊表面被冷却、结晶、凝固。
随着铸轧辊的不断转动,液体金属铝的热量继续向铸轧中传递,并不断被铸轧辊中的冷却水带走,晶体不断向液体中生长,凝固层随之增厚。
液体金属铝与两个铸轧辊基本同时接触,同时结晶,其结晶过程和条件相同,形成凝固层的速度和厚度相同,当两侧凝固层厚度随着铸轧辊的转动逐渐增加,并在两个铸轧辊中心线以下相遇时,即完成了铸造过程,并随之受到这两个铸轧辊对其凝固组织的轧制作用,并给以一定的轧制加工率,是液体金属铝被铸造、轧制成铸轧板,这就是连续铸轧的基本原理。
由此可见,通过供料嘴子从铸轧辊的一侧源源不断地供应液体金属铝,经过铸轧辊的连续冷却、铸造、轧制,从铸轧辊的另一侧不断铸轧出铸轧板,使进、出铸轧区的金属量始终保持平衡,这样就达到了连续铸轧的稳定过程。
生产铸轧板的连续铸轧工艺流程为:炉子准备→配料→装炉→熔化→撒覆盖剂→搅拌→扒渣→取样→成分调整及再次取样→倒炉→静置炉内精炼→静置炉与保温→在线除气→过滤流槽系统→铸轧→铸轧板。
2.铝熔体质量的控制铝熔体的质量是保证铸轧板质量的关键因素。
消除铝及铝合金熔体中的气体、夹杂物和有害元素,(包括传统的静置炉内精炼和除气箱内在线精炼),同时避免铝熔体过烧和局部过热,才能得到质量上乘的铝熔体,保证铸轧板的质量和后续产品的质量。
2024年铝业公司铸轧工作个人总结
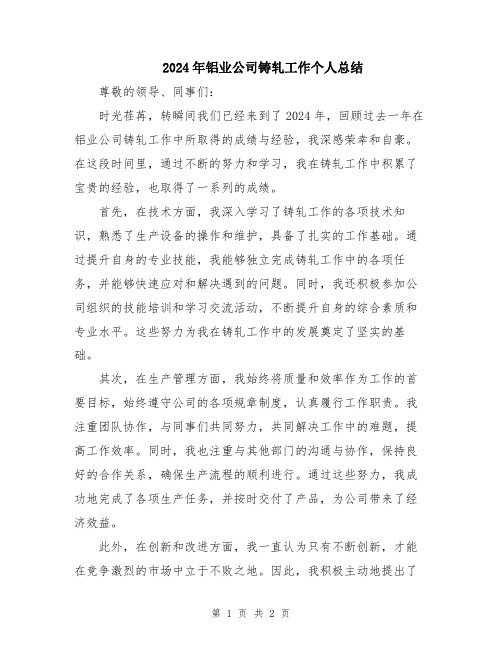
2024年铝业公司铸轧工作个人总结尊敬的领导、同事们:时光荏苒,转瞬间我们已经来到了2024年,回顾过去一年在铝业公司铸轧工作中所取得的成绩与经验,我深感荣幸和自豪。
在这段时间里,通过不断的努力和学习,我在铸轧工作中积累了宝贵的经验,也取得了一系列的成绩。
首先,在技术方面,我深入学习了铸轧工作的各项技术知识,熟悉了生产设备的操作和维护,具备了扎实的工作基础。
通过提升自身的专业技能,我能够独立完成铸轧工作中的各项任务,并能够快速应对和解决遇到的问题。
同时,我还积极参加公司组织的技能培训和学习交流活动,不断提升自身的综合素质和专业水平。
这些努力为我在铸轧工作中的发展奠定了坚实的基础。
其次,在生产管理方面,我始终将质量和效率作为工作的首要目标,始终遵守公司的各项规章制度,认真履行工作职责。
我注重团队协作,与同事们共同努力,共同解决工作中的难题,提高工作效率。
同时,我也注重与其他部门的沟通与协作,保持良好的合作关系,确保生产流程的顺利进行。
通过这些努力,我成功地完成了各项生产任务,并按时交付了产品,为公司带来了经济效益。
此外,在创新和改进方面,我一直认为只有不断创新,才能在竞争激烈的市场中立于不败之地。
因此,我积极主动地提出了改进生产工艺和操作流程的建议,并与相关部门进行沟通和交流。
通过团队的共同努力,我们成功地改进了一些生产工艺,提高了生产效率和产品质量。
这些经验和成果不仅提升了我们自身的竞争力,也为公司的发展做出了积极的贡献。
最后,在安全生产方面,我始终坚持安全第一的原则,不断加强对生产现场的管理和监控。
我积极宣传安全知识,提高员工的安全意识,定期组织安全培训和演练,确保每个员工都能够熟悉安全操作规程和应急预案。
通过这些措施,我们成功地保障了生产的安全与稳定,防范了安全事故的发生,也为公司的可持续发展做出了贡献。
通过一年的铸轧工作,我深刻认识到了铸轧工作的重要性和复杂性。
在今后的工作中,我将继续不断学习和提升自己,不断开拓创新,为公司的发展做出更大的贡献。
铝业公司员工铸轧工作个人总结
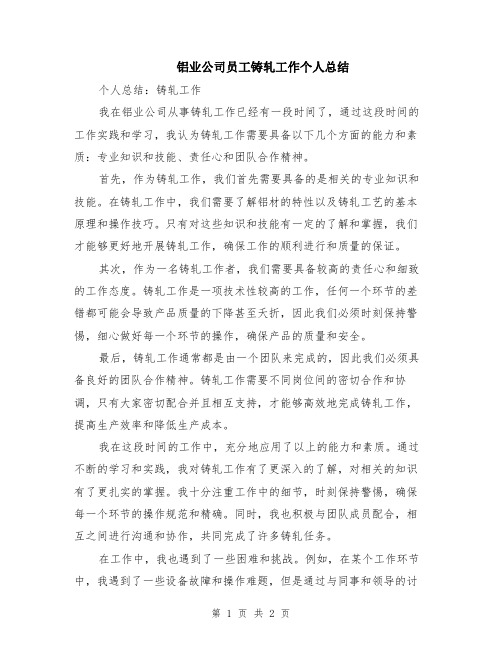
铝业公司员工铸轧工作个人总结个人总结:铸轧工作我在铝业公司从事铸轧工作已经有一段时间了,通过这段时间的工作实践和学习,我认为铸轧工作需要具备以下几个方面的能力和素质:专业知识和技能、责任心和团队合作精神。
首先,作为铸轧工作,我们首先需要具备的是相关的专业知识和技能。
在铸轧工作中,我们需要了解铝材的特性以及铸轧工艺的基本原理和操作技巧。
只有对这些知识和技能有一定的了解和掌握,我们才能够更好地开展铸轧工作,确保工作的顺利进行和质量的保证。
其次,作为一名铸轧工作者,我们需要具备较高的责任心和细致的工作态度。
铸轧工作是一项技术性较高的工作,任何一个环节的差错都可能会导致产品质量的下降甚至夭折,因此我们必须时刻保持警惕,细心做好每一个环节的操作,确保产品的质量和安全。
最后,铸轧工作通常都是由一个团队来完成的,因此我们必须具备良好的团队合作精神。
铸轧工作需要不同岗位间的密切合作和协调,只有大家密切配合并且相互支持,才能够高效地完成铸轧工作,提高生产效率和降低生产成本。
我在这段时间的工作中,充分地应用了以上的能力和素质。
通过不断的学习和实践,我对铸轧工作有了更深入的了解,对相关的知识有了更扎实的掌握。
我十分注重工作中的细节,时刻保持警惕,确保每一个环节的操作规范和精确。
同时,我也积极与团队成员配合,相互之间进行沟通和协作,共同完成了许多铸轧任务。
在工作中,我也遇到了一些困难和挑战。
例如,在某个工作环节中,我遇到了一些设备故障和操作难题,但是通过与同事和领导的讨论和交流,我们成功地解决了这些问题,确保了工作的顺利进行。
这一过程让我明白了团队合作的重要性以及解决问题的能力对于一个铸轧工作者的必要性。
通过这段时间的铸轧工作,我的专业知识和技能得到了进一步的提升,责任心和团队合作的意识也得到了加强。
我相信,只有不断地学习和提升自己,才能够在铸轧工作中取得更好的成绩和进步。
虽然我在这段时间的工作中取得了一定的成绩,但是我也清楚地意识到自己还有很多需要提升的地方。
铝业公司铸轧工作个人总结
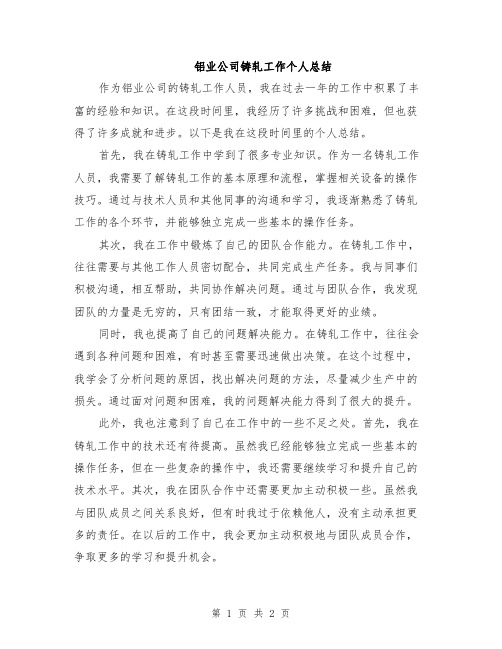
铝业公司铸轧工作个人总结作为铝业公司的铸轧工作人员,我在过去一年的工作中积累了丰富的经验和知识。
在这段时间里,我经历了许多挑战和困难,但也获得了许多成就和进步。
以下是我在这段时间里的个人总结。
首先,我在铸轧工作中学到了很多专业知识。
作为一名铸轧工作人员,我需要了解铸轧工作的基本原理和流程,掌握相关设备的操作技巧。
通过与技术人员和其他同事的沟通和学习,我逐渐熟悉了铸轧工作的各个环节,并能够独立完成一些基本的操作任务。
其次,我在工作中锻炼了自己的团队合作能力。
在铸轧工作中,往往需要与其他工作人员密切配合,共同完成生产任务。
我与同事们积极沟通,相互帮助,共同协作解决问题。
通过与团队合作,我发现团队的力量是无穷的,只有团结一致,才能取得更好的业绩。
同时,我也提高了自己的问题解决能力。
在铸轧工作中,往往会遇到各种问题和困难,有时甚至需要迅速做出决策。
在这个过程中,我学会了分析问题的原因,找出解决问题的方法,尽量减少生产中的损失。
通过面对问题和困难,我的问题解决能力得到了很大的提升。
此外,我也注意到了自己在工作中的一些不足之处。
首先,我在铸轧工作中的技术还有待提高。
虽然我已经能够独立完成一些基本的操作任务,但在一些复杂的操作中,我还需要继续学习和提升自己的技术水平。
其次,我在团队合作中还需要更加主动积极一些。
虽然我与团队成员之间关系良好,但有时我过于依赖他人,没有主动承担更多的责任。
在以后的工作中,我会更加主动积极地与团队成员合作,争取更多的学习和提升机会。
总结而言,过去一年来,我在铝业公司的铸轧工作中积累了很多经验和知识。
我学到了很多专业知识,提高了自己的团队合作能力和问题解决能力。
同时,我也发现了自己在工作中的一些不足之处,需要继续努力提升。
通过总结和反思,我相信我会在未来的工作中更加出色地完成自己的职责,为公司的发展贡献自己的力量。
2024年铝业公司铸轧工作个人总结
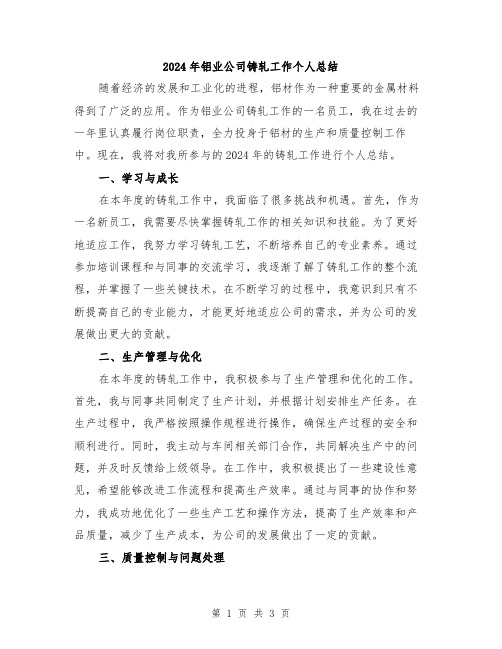
2024年铝业公司铸轧工作个人总结随着经济的发展和工业化的进程,铝材作为一种重要的金属材料得到了广泛的应用。
作为铝业公司铸轧工作的一名员工,我在过去的一年里认真履行岗位职责,全力投身于铝材的生产和质量控制工作中。
现在,我将对我所参与的2024年的铸轧工作进行个人总结。
一、学习与成长在本年度的铸轧工作中,我面临了很多挑战和机遇。
首先,作为一名新员工,我需要尽快掌握铸轧工作的相关知识和技能。
为了更好地适应工作,我努力学习铸轧工艺,不断培养自己的专业素养。
通过参加培训课程和与同事的交流学习,我逐渐了解了铸轧工作的整个流程,并掌握了一些关键技术。
在不断学习的过程中,我意识到只有不断提高自己的专业能力,才能更好地适应公司的需求,并为公司的发展做出更大的贡献。
二、生产管理与优化在本年度的铸轧工作中,我积极参与了生产管理和优化的工作。
首先,我与同事共同制定了生产计划,并根据计划安排生产任务。
在生产过程中,我严格按照操作规程进行操作,确保生产过程的安全和顺利进行。
同时,我主动与车间相关部门合作,共同解决生产中的问题,并及时反馈给上级领导。
在工作中,我积极提出了一些建设性意见,希望能够改进工作流程和提高生产效率。
通过与同事的协作和努力,我成功地优化了一些生产工艺和操作方法,提高了生产效率和产品质量,减少了生产成本,为公司的发展做出了一定的贡献。
三、质量控制与问题处理在本年度的铸轧工作中,我充分认识到质量控制的重要性,并积极参与了相关的工作。
我始终坚持“质量第一”的原则,严格控制每一个环节的质量。
在生产过程中,我严格按照质量标准进行操作,并及时发现和处理质量问题。
在发现问题后,我积极与相关部门沟通,共同解决问题,并采取了一系列有效的措施,防止问题再次发生。
通过我和同事的努力,我们成功地降低了生产中出现的质量问题的数量,提高了产品的质量和可靠性,得到了客户的高度认可和赞扬。
四、团队合作与沟通能力在本年度的铸轧工作中,我始终坚持团队合作的原则,并努力与同事保持良好的沟通和合作关系。
钢厂连铸年度总结(3篇)

第1篇一、前言时光荏苒,岁月如梭。
转眼间,本年度的钢厂连铸工作已接近尾声。
在过去的一年里,在公司的正确领导和全体员工的共同努力下,钢厂连铸生产线取得了显著的成绩。
现将本年度连铸工作总结如下:二、工作回顾1. 设备管理与维护本年度,我们高度重视连铸设备的维护与管理工作,确保了设备的稳定运行。
主要工作如下:(1)加强设备巡检,及时发现并处理设备隐患;(2)严格执行设备维护保养制度,确保设备处于最佳工作状态;(3)针对设备老化、磨损等问题,及时进行更换和改造,提高设备使用寿命。
2. 生产工艺优化为了提高连铸产品质量和生产效率,我们不断优化生产工艺,主要措施如下:(1)优化铸机操作参数,确保铸坯质量;(2)改进冷却水系统,提高冷却效果;(3)加强过程控制,确保铸坯尺寸精度;(4)开展工艺攻关,解决生产过程中遇到的难题。
3. 产品质量提升产品质量是连铸工作的核心,本年度我们重点加强了以下工作:(1)严格执行生产工艺,确保铸坯质量;(2)加强原材料质量控制,从源头上保证产品质量;(3)开展质量攻关活动,解决铸坯质量缺陷;(4)加强员工质量意识教育,提高全员质量素质。
4. 安全生产安全生产是企业发展的基石,本年度我们始终把安全生产放在首位,主要工作如下:(1)加强安全生产教育培训,提高员工安全意识;(2)完善安全管理制度,落实安全生产责任制;(3)加强设备安全管理,消除安全隐患;(4)开展安全生产检查,确保生产安全。
三、取得的成绩1. 设备运行稳定通过加强设备维护与管理,本年度连铸设备运行稳定,故障率明显下降,为生产提供了有力保障。
2. 产品质量提升通过优化生产工艺和加强质量控制,本年度连铸产品质量得到显著提升,客户满意度不断提高。
3. 安全生产形势良好通过加强安全生产管理,本年度连铸生产线未发生重大安全事故,安全生产形势良好。
四、存在的问题1. 设备老化严重部分连铸设备已运行多年,存在老化严重的问题,影响了生产效率和产品质量。
连铸年终总结范文(3篇)

第1篇一、前言时光荏苒,岁月如梭。
转眼间,一年又即将过去。
在这一年里,我国连铸行业在技术创新、设备升级、产品质量提升等方面取得了显著成果。
在此,我对本年度连铸工作进行全面总结,以期在新的一年里,我们能够再接再厉,继续推动我国连铸事业的发展。
二、工作回顾1. 技术创新与研发(1)技术突破:本年度,我单位在连铸技术领域取得了多项突破。
例如,成功研发了一种新型连铸机控制系统,提高了铸机稳定性,降低了故障率。
(2)专利申请:积极申请连铸相关专利,截止目前,已获得授权专利X项,为企业的技术创新提供了有力保障。
(3)技术引进:引进国外先进连铸技术,结合我国实际情况进行消化吸收,提高了我国连铸技术的整体水平。
2. 设备升级与改造(1)设备更新:对老旧连铸设备进行升级改造,提高设备运行效率,降低能耗。
(2)自动化程度提升:加大自动化设备投入,提高生产效率,降低人工成本。
(3)节能减排:通过设备升级,降低生产过程中的能源消耗,实现绿色生产。
3. 产品质量提升(1)工艺优化:优化连铸工艺,提高铸坯质量,降低缺陷率。
(2)质量控制:加强生产过程中的质量控制,确保产品质量稳定。
(3)售后服务:提高售后服务水平,及时解决客户在使用过程中遇到的问题。
4. 人才培养与团队建设(1)培训体系:建立完善的培训体系,提高员工技能水平。
(2)团队建设:加强团队建设,提高团队凝聚力和战斗力。
(3)激励机制:实施激励机制,激发员工工作积极性。
三、工作亮点1. 生产效率提升:通过技术创新和设备升级,生产效率较去年同期提高X%。
2. 产品质量稳定:铸坯缺陷率较去年同期降低X%,产品质量得到明显提升。
3. 节能减排成效显著:能源消耗较去年同期降低X%,节能减排工作取得显著成效。
4. 市场竞争力增强:产品质量和品牌形象得到客户认可,市场竞争力不断增强。
四、存在问题与改进措施1. 问题:部分连铸设备老化,存在安全隐患。
改进措施:加大设备更新改造力度,确保生产安全。
- 1、下载文档前请自行甄别文档内容的完整性,平台不提供额外的编辑、内容补充、找答案等附加服务。
- 2、"仅部分预览"的文档,不可在线预览部分如存在完整性等问题,可反馈申请退款(可完整预览的文档不适用该条件!)。
- 3、如文档侵犯您的权益,请联系客服反馈,我们会尽快为您处理(人工客服工作时间:9:00-18:30)。
连续铸轧技术总结我是1988年参加工作,公司的前身是冶金部铝加工试验厂,厂目的是:对变形铝合金连续铸轧技术的研发和推广,这给了解和学习连续铸轧理论知识和操作技能等方面提供了良好的条件。
随着工艺规程的成熟和完善,产品质量也得到较大的提高。
在生产操作过程中,我虚心向技术人员和老师傅学习、请教。
逐渐总结出一些切实可行而且行之有效的控制和提高产品质量的方法。
通过对基础理论的学习,我了解并掌握了铸轧生产过程中的铸轧板质量的有关操作和解决问题的方法。
1.连续铸轧的基本原理从供料嘴子前沿到铸轧辊中心线之间的距离成为铸轧区,液体金属铝通过供料嘴进到铸轧区时,立即与两个相转动的铸轧辊相遇,液体金属铝的热量不断从垂直于铸轧辊面的方向传递到铸轧辊中,使附着在铸轧辊表面的液体金属铝的温度急剧下降,因此,液体金属铝在铸轧辊表面被冷却、结晶、凝固。
随着铸轧辊的不断转动,液体金属铝的热量继续向铸轧中传递,并不断被铸轧辊中的冷却水带走,晶体不断向液体中生长,凝固层随之增厚。
液体金属铝与两个铸轧辊基本同时接触,同时结晶,其结晶过程和条件相同,形成凝固层的速度和厚度相同,当两侧凝固层厚度随着铸轧辊的转动逐渐增加,并在两个铸轧辊中心线以下相遇时,即完成了铸造过程,并随之受到这两个铸轧辊对其凝固组织的轧制作用,并给以一定的轧制加工率,是液体金属铝被铸造、轧制成铸轧板,这就是连续铸轧的基本原理。
由此可见,通过供料嘴子从铸轧辊的一侧源源不断地供应液体金属铝,经过铸轧辊的连续冷却、铸造、轧制,从铸轧辊的另一侧不断铸轧出铸轧板,使进、出铸轧区的金属量始终保持平衡,这样就达到了连续铸轧的稳定过程。
生产铸轧板的连续铸轧工艺流程为:炉子准备→配料→装炉→熔化→撒覆盖剂→搅拌→扒渣→取样→成分调整及再次取样→倒炉→静置炉内精炼→静置炉与保温→在线除气→过滤流槽系统→铸轧→铸轧板。
2.铝熔体质量的控制铝熔体的质量是保证铸轧板质量的关键因素。
消除铝及铝合金熔体中的气体、夹杂物和有害元素,(包括传统的静置炉内精炼和除气箱内在线精炼),同时避免铝熔体过烧和局部过热,才能得到质量上乘的铝熔体,保证铸轧板的质量和后续产品的质量。
2.1控制铝熔体的含氢量铝熔体吸氢的主要反应是铝与水的反应,低于250℃时,铝与空气中的水蒸汽接触发生下列反应:2Al﹢3H2O→2Al(OH)3﹢3H2;在高于400℃的熔炼温度下,铝与水气发生下列反应:2Al﹢3H2O→Al2O36H.生成游离态的原子[H],极易溶于铝熔体中,此反应为铝熔体吸氢的主要途径。
控制铝熔体的含量采取的预防措施主要由以下几个反面:(1)、烘干炉子及耐火材料。
新开炉和大修后的炉子等设备及耐火材料等,要按工艺规程规定的烘炉升温曲线严格执行,既要保证烘炉温度,又要保证在各个温度范围的保温时间,在保温炉子逐渐升温的过程中,将炉子潮气最大限度地烘干,进而降低因炉子问题而造成的铝熔体吸氢。
(2)、熔体表面撒覆盖剂或打渣剂。
为了防止精练好的铝熔体重新生成夹渣和吸氢,可在熔体表面撒一层覆盖剂和打渣剂,铸轧生产时,熔体中的含氢量应按工艺规程规定的数值控制越低越好,这样可减少后续产品气道等缺陷的产生。
(3)流槽加盖代替燃料保温。
为防止熔体精炼及在线除气后的再次吸气,流槽内不能使用燃烧液化气来调整熔体温度,这等于向熔体中直接加氢。
目前通用的办法是通过在流槽上加盖,如采用电加热保温盖方法等。
(4)、烘干轧辊及铸轧工具。
铸轧辊、嘴子料、流槽潮湿等会造成熔体吸氢,导致铸轧板气道等缺陷的产生,对此应采取相应措施:对新磨削的铸轧辊,应进行充分烘烤、对铸轧嘴料、流槽等材料或工具,应在使用前进行前烘干,充分去除潮气。
延长精炼时间。
其他环节的原因,也会造成铝熔体吸氢,比如夏季空气中的潮气大,可通过适当增加精炼次数,延长精炼时间等措施来缓解这些原因造成的影响,(6)、提高精炼质量及除气效率。
为确保铝熔体氢含量符合技术要求,最主要的措施应当是在确保精炼气体纯净的前提下,提高精炼质量及在线除气效率,精练时,将选好的精炼剂压入熔体接近底部,缓慢移动,这样才有利于除渣、除气。
与此同时应保证在线除气设备正常运转,使实测氢含量小于技术要求规定的指标。
总之,铝熔体中氢的来源主要是水份被熔体吸收产生的,提高精炼过程的质量及减少原辅材料水份含量(或不含水份),以及对精炼好的铝熔体采取防止吸氢的措施,是保证熔体中氢含量降低的主要方法。
2.2避免铝熔体过烧和局部过热熔体过高和局部过热,不仅耗费能源,更主要的是容易使铸轧板晶粒粗大。
熔体温度的不稳定,容易使液体金属产生吸氢现象,同时,熔炼过程的无序控制,还容易造成燃烧不完全和过烧现象,增加金属烧损,污染环境,以及对熔炼设备的损坏。
许多铸轧板质量缺陷是由于铝熔体过烧和局部过热而造成的。
为了解决铝熔体过热和局部过热的问题,在公司和分厂进行设备改造的同时,我们在操作方法上进行积极的探索,经过反复的摸索,提出了“三、四、五”熔炼工作程序。
即:“三”、补料后到倒炉前必须进行充分搅拌三次,达到熔体各部分温度均匀;“四”每次搅拌前进、后退各四部,这样既能搅拌到熔炼炉的各个角落,又利于搅拌人员的步伐协调一致;“五”每次搅拌不低于五十下,达到充分搅拌的目的。
此方法能够有效的控制熔体温度,并使熔体的化学成份均匀、准确。
在工段推广实施中取得了非常好的效果。
3、保证立板成功率和生产正常运行立板是铸轧分厂各种消耗最多的工作,减少立板次数,提高连续轧制时间是铸轧分厂提高产量、降低消耗的主攻方向。
通过研究每次立板失败的原因和影响生产正常运转的意外停机(漏铝停机)的原因,我发现供料咀耳子与铸轧辊上下间隙过大是造成立板失败和漏铝的主要原因。
通过在每次立板前采取石棉耳朵沿轧辊弧度周向打磨,使耳子弧度与轧辊的弧度一致,耳子上下弧度与轧辊弧度贴实的方法,可使耳子上下缝隙均匀且与轧辊附帖,有效地解决了立板失败这一常见技术难题。
耳朵导角小也是造成立板失败的原因之一。
在立板过程中,熔融金属在铸轧区内受轧制力的作用向两侧外展,耳子导角过小,受力增强或被带出或严重磨损,耳朵磨损严重在正常生产时还易造成边部‘缺肉’或大裂边成为铸轧质量缺陷。
在争得技术员同意后,每次立板前适当加大耳子的导角角度,把角度基本控制在15℃-20℃之间,经过多年实验生产得到检验受到了比较好得成效。
4.保证铸轧板的产品质量技术标准要求铸轧板表面平整、结净、板型良好,化学成分符合国家标准或有关技术标准,不允许有裂纹、热带、夹渣、气道、孔洞及影响使用的表面偏析、条纹等缺陷。
铸轧板组织细小、致密、均匀,组织不能有夹渣孔洞、分层、晶粒粗大等缺陷。
质量缺陷直接影响铸轧板的产品质量,认识质量缺陷形成的原因,了解工艺参数与生产缺陷之间的因果关系,是铸轧正常生产的关键所在。
通过参加公司和分厂组织的各种技术培训,我掌握了一些以调整工艺参数来预防产品缺陷产生的方法。
4.1铸轧板型控制及影响因素板型主要是控制板厚的突变,铸轧辊套凸度、预压力、铸轧区、循环冷却系统、张应力是影响板差变化的主要因素。
各因素对板型的影响及控制主要体现为:(1)轧辊的凸度直接影响板厚不均性。
当辊套内循环水通路局部堵塞,造成热传导不良,使得堵塞处横向板厚突然偏薄,造成纵向连续偏薄。
冷轧第一道出现不均匀变形,不适合干铝箔毛料。
(2)预压力对板型没有直接的影响,生产中单独调整一侧预压力,可以改变板厚。
通常板坯偏薄一侧,在线减小预应力可微增板厚,避免了两边厚差过大。
(3)控制铸轧区同样可以减少两边厚度差过大,经过将嘴子平台板坯偏薄侧微调后撤,单侧延长铸轧区长度,改变轧辊接触压力分布和板坯轧制变形率,微增板厚,缩小铸轧板横向厚度。
当板面出现明显中心错层时,通过咀子中心线与轧辊中心线平稳来消除中心错层。
(4)粘辊是板型的一大缺陷,粘辊形成沿板带纵向某一点,板厚突然增厚,形成一个台阶厚差0.15mm以上,铝箔轧制时引起断带,一定的张应力可以在一定程度对板型进行张力矫平,减少粘辊现象并改变板型。
(5)辊套上温度分布不均,引起辊套表面硬度不均,使辊套生产不均匀变形,造成铸轧板硬度和厚度不均,形成纵向周期分布的局部偏厚。
4.2铸轧板粗大晶粒形成及防止措施:铸态的晶粒大小和晶粒的生长方式取决于金属液体内部的晶粒数量和凝固结晶时的冷却条件。
铸轧生产中,铸轧辊具有较大的热传导系数,铸轧区内铝液与铸轧辊接触瞬间,铝液受到激冷,迅速形成稳定的凝壳,晶粒难以脱落和游离,又因为冷却强度越大,凝固结晶过冷度越大,形核率越多,夹层柱状晶粒越细小,同时还可以使整个铸轧板断面为细小晶粒。
当冷却强度不足以使整个铝液温断面同时产生较大的过冷,而仅能保持胞状晶生长所需要的体液温度梯度时,铸轧板就会出现粗大晶粒,当熔体过热,静置时间过长,温度过高,也是粗大晶粒产生的原因。
粗大晶粒铸轧板,在轧制板材时表面会产生许多沿轧制方向的白色条纹缺陷,严重影响板材表面质量;在轧制铝箔时将出现针孔增多,严重影响产品质量。
通过产生原因的分析,粗大晶粒的防止措施主要有以下几点:(1) 降低铸轧速度;(2)减薄铸轧板厚度;(3)适量、均匀、稳定地喷涂烟尘,防止氧化铝层增厚;(4)定期清洗铸轧辊冷却水道,除铁锈和水垢;(5)降低前箱温度;(6)添加AlTiB丝。
4.3铸轧板裂边的产生原因及防止措施在铸轧过程中金属受到轧制变形时,金属表面与轧辊表面贴合无相对滑动,由于金属变形变薄,只在金属中心有较大的后滑动,因此金属表面与内层手剪切力和压力作用,产生变形并传递到液穴的凝固硬壳内,使使凝固壳内部产生同样变形与剪切力。
当变形产生的剪切力超过凝固壳金属的剪切力时,在材料的薄弱处首先裂开。
当液穴越深时,凝固壳就越薄,越不坚固,抗剪切强度越低,随着轧制力越大,后滑区内层与表面剪切力就越大。
在变形区内,边部金属由于同时受到来自耳子施加于两边的拉应力,这两种方向相反的应力作用使铸轧板开裂形成裂口,因此大晶粒是裂边产生又一原因。
裂边铸轧板冷轧过程中不断受到拉应力作用,裂边逐渐扩展,严重造成裂边废品,大裂边还会出现断带。
防止铸轧板裂边的主要措施有:(1)适当减少铸轧区高度,并相应调整其他铸轧工艺参数,如,提高浇铸温度,控制适当液面高度,降低铸轧速度。
(2)改进共咀结构,提高材质性能和加工组装质量,如,改进供料咀垫片,使得两边空间增大,保证铝液流动温度均衡,增加红耳子尖部倾斜度,在铸咀边部与耳朵间采用双保护层保温毡耳子。
(3)随铸轧辊辊径减小,铸轧区长度亦调整缩短。
(4)使用铝太硼丝晶粒细化剂细化结晶组织,改善加工性能。
4.4铸轧板热带产生及防止措施铸轧板热带产生主要原因:(1)由于前箱内液体金属温度偏高,在流入铸轧区时,温度分布不均,在局部温度过高处,液穴偏深,当液穴深度等于或超过铸轧区时,铸轧板表面在该处出现热带。