ZrO2精细陶瓷材料湿法成型工艺概述
氧化铝陶瓷的成型工艺

氧化铝陶瓷的成型工艺
氧化铝陶瓷的成型工艺一般包括以下几个步骤:
1. 配料:首先需要准备氧化铝陶瓷的原料。
通常使用高纯氧化铝粉末作为主要原料,还可以添
加一些助剂如玻璃粉末或有机粉末以改善成型和烧结性能。
2. 混合:将氧化铝粉末和其他助剂按一定比例混合均匀。
混合可以使用干混合或湿混合的方式,具体取决于成型工艺的要求。
3. 成型:将混合好的粉末通过成型工艺成型。
常用的成型方法包括注塑成型、挤出成型、挤压
成型、压制成型等,具体选用哪种成型方法取决于产品的形状和工艺要求。
4. 干燥:成型后的陶瓷坯体需要进行干燥处理以去除内部和表面的水分。
干燥一般采用自然干
燥或烘干的方式,烘干时需要控制温度和湿度,以避免陶瓷变形或开裂。
5. 烧结:干燥后的陶瓷坯体需要进行烧结。
烧结是将陶瓷坯体加热至高温,使其颗粒间发生熔结,形成致密的氧化铝陶瓷。
烧结一般采用电炉或气氛炉进行,具体的烧结温度和时间根据陶
瓷的要求进行控制。
6. 表面处理:烧结后的氧化铝陶瓷可以进行一些表面处理,如研磨、抛光等,以改善其表面质
量和光洁度。
以上仅是氧化铝陶瓷的一种常见成型工艺流程,具体的成型工艺可能会根据产品的特殊要求进行调整和改变。
湿法成型工艺

湿法成型工艺全文共四篇示例,供读者参考第一篇示例:湿法成型工艺是一种常用于制作陶瓷、陶瓷瓷砖、陶瓷浴缸等制品的工艺方法。
在湿法成型过程中,原料通过混合、加水、成型、干燥等一系列工序,最终制成所需的成品。
湿法成型工艺具有成型速度快、成型精度高、能够生产大量产品等优点,被广泛应用于陶瓷行业。
湿法成型工艺的原料准备非常重要。
通常情况下,陶瓷制品的原料包括粘土、石英、长石等。
在使用之前,这些原料需要通过粉碎、研磨等方式进行处理,以确保原料颗粒的尺寸均匀,从而保证成型时的均匀性和稳定性。
湿法成型的第一步是将经过处理的原料与一定比例的水混合,形成均匀的泥浆状物质。
这一步称为混合成型。
在混合过程中,需要确保原料充分混合,且保持一定的湿度,以便后续的成型操作。
接下来是成型的过程。
通常情况下,湿法成型的方式有很多种,如注射成型、挤压成型、压制成型等。
不同的产品需要使用不同的成型方式,以确保产品能够达到设计要求的形状和尺寸。
在成型过程中,通常采用模具来帮助塑造原料成坯。
完成成型后,陶瓷制品需要进行干燥。
干燥是将成型后的陶瓷坯置于干燥室中,通过加热或自然风力等方式将水分逐渐蒸发,使陶瓷坯得到加固和硬化。
在干燥的过程中,需要控制好温度和湿度,以避免出现开裂或变形等问题。
经过干燥后的陶瓷坯即可进行烧制。
烧制是将陶瓷坯置于窑炉中,通过高温加热使其成为坚固耐用的陶瓷制品。
烧制的温度和时间通常根据产品的要求来确定,不同的陶瓷制品所需的烧制条件也可能有所不同。
湿法成型工艺是一种高效、精确的制作陶瓷制品的工艺方法。
通过对原料的处理、混合成型、干燥和烧制等一系列工序,可以制作出各种形状、尺寸和质地的陶瓷制品。
湿法成型工艺的应用使得陶瓷制品的生产更加快捷、灵活,同时也提高了产品的质量和市场竞争力。
第二篇示例:湿法成型工艺是一种常用的制造工艺,广泛应用于陶瓷、玻璃、建筑材料等领域。
湿法成型工艺利用水或其他溶剂作为介质,将原料制成糊状或流体,通过模具成型后再进行烧结或干燥,最终得到成型体。
陶瓷成型工艺原理及方法

流延膜片的表征
流延膜片表怔 1) 表面特征:颗粒尺寸、粘合剂分布、团聚程度、孔
洞、裂纹(光学显微镜、电子显微镜)
2) 柔韧性:手工反复折叠 3) 强度:拉力仪 4) 厚度:测厚仪 5) 密度:阿基米德定律测量
厚 膜: 刮刀口间隙↑料浆液面↑载体线速↓料浆粘度↓
薄 膜: 相反
Hale Waihona Puke 瓷流延带的干燥开始时失重(蒸发速率保持恒定),在临界点之后开始第二个干燥阶 段,其特征是蒸发速率下降 主要的物理过程
Tape weight
Water LNT particle
1.浆料内部的液体移动到表面 2.表面溶剂挥发 3.蒸汽从接近浆料表面的区域被带走
羧酸盐:硬脂酸钠、丙烯酸共聚物 阴离子型
颗粒表面带正电的 中性或弱碱性料浆
磺酸盐:烷基磺酸钠、木质素磺酸盐 磷酸酯盐:高级醇磷酸酯二钠 硫酸酯盐:十二烷基硫酸钠 伯(仲、叔)胺盐:RNH3Cl, R(CH3)NH2X 、R(R’)2NHX 季胺盐:RN(R’)3X 砒啶盐:R(C5H5N)X 氨基酸:十二烷基氨基丙烯酸钠 甜菜碱:十八烷基二甲基甜菜碱 咪唑啉:R-[CNH(CH2)2N+]-CH2COO聚氧乙烯:脂肪醇聚氧乙烯醚
其沸点应该高于200℃
增塑剂量一般大于粘合剂,但加入塑性剂会使素坯膜的强度降低 玻璃化转变温度(Tg)就是聚合物的性能产生明显变化时的温度, 高于 这个温度聚合物转变成橡胶态, 低于这个温度聚合物转变成玻璃态。玻 璃化转变温度是高分子聚合物的特征温度之一
流延成型的粘合剂和增塑剂的选择
粘合剂 乙基纤维素 PVA PVAc+PVC PVB 塑性剂 二乙基草酸酯 甘油,三乙烯乙二醇 邻苯二甲酸二丁酯(DBP),聚乙二醇 聚乙二醇, 邻苯二甲酸二辛酯(DOP),邻苯二甲 酸二丁酯(DBP),己 烷 邻苯二甲酸二辛酯,邻苯二甲酸二丁酯, 聚乙二醇 邻苯二甲酸二丁酯,聚乙二醇,甘 油
氧化铝陶瓷制作工艺简介

氧化铝陶瓷制作工艺简介氧化铝氧化铝陶瓷陶瓷目前分为高纯型与普通型两种。
高纯型氧化铝陶瓷系Al2O3含量在99.9%以上的陶瓷材料,9%以上的陶瓷材料,由于其烧结温度高达1650由于其烧结温度高达1650—1990℃,透射波长为1~6μm,一般制成熔融玻璃以取代铂坩埚:利用其透光性及可耐碱金属腐蚀性用作钠灯管;在电子工业中可用作集成电路基板与高频绝缘材料。
普通型氧化铝陶瓷系按Al2O3含量不同分为99瓷、同分为99瓷、95瓷、95瓷、95瓷、90瓷、85瓷等品种,90瓷、85瓷等品种,90瓷、85瓷等品种,有时Al2O3含量在80%或75%者有时Al2O3含量在80%或75%者也划为普通氧化铝陶瓷系列。
其中99氧化铝瓷材料用于制作高温坩埚、耐火炉管及特殊耐磨材料,如陶瓷轴承、陶瓷密封件及水阀片等;95氧化铝瓷主要用作耐腐蚀、耐磨部件;85瓷中由于常掺入部分滑石,提高了电性能与机械强度,可与、铌、钽等金属封接,有的用作电真空装置器件。
其制作工艺如下:用作电真空装置器件。
其制作工艺如下:一 粉体制备:粉体制备:将入厂的氧化铝粉按照不同的产品要求与不同成型工艺制备成粉体材料.粉体粒度在1μm微米以下,若制造高纯氧化铝陶瓷制品除氧化铝纯度在99.若制造高纯氧化铝陶瓷制品除氧化铝纯度在99.99%外,99%外,还需超细粉碎且使其粒径分布均匀。
采用挤压成型或注射成型时,采用挤压成型或注射成型时,粉料中需引入粘结剂与可塑剂,粉料中需引入粘结剂与可塑剂,粉料中需引入粘结剂与可塑剂,一般为重量一般为重量比在10—30%的热塑性塑胶或树脂有机粘结剂应与氧化铝粉体在150—200℃温度下均匀混合,以利于成型操作。
采用热压工艺成型的粉体原料则不需加入粘结剂。
采用热压工艺成型的粉体原料则不需加入粘结剂。
若采用若采用半自动或全自动干压成型,对粉体有特别的工艺要求,需要采用喷雾造粒法对粉体进行处理、使其呈现圆球状,使其呈现圆球状,以利于提高粉体流动性便于成型中自动充填模壁。
氧化锆陶瓷生产工艺

氧化锆陶瓷生产工艺目录一、概述 (2)二、氧化锆陶瓷的特征 (2)三、氧化锆陶瓷的应用 (3)四、普通氧化锆陶瓷产品制备工艺 (4)五、氧化锆陶瓷产品注塑件制备工艺 (10)六、氧化锆陶瓷优势 (12)一、概述氧化锆陶瓷呈白色,含杂质时呈黄色或灰色,一般含有HfO2,不易分离。
在常压下纯ZrO2共有三种晶态。
■ 低温型单斜晶(m-ZrO2)■ 中温型四方晶(t-ZrO2)■ 高温型立方晶(c-ZrO2)上述三种晶型存在于不同的温度范围,并存在如下相互转化关系:二、氧化锆陶瓷的特征高熔点氧化锆的熔点为:2715℃,可作为高温耐火材料硬度大、耐磨性好按莫氏硬度:蓝宝石>氧化锆陶瓷>康宁玻璃>铝镁合金>钢化玻璃>聚碳酸酯强度、韧性大氧化锆的强度可达:1500MPa热导率和膨胀系数低在常见陶瓷材料中,其热导率最低(1.6-2.03W/(m.k)),热膨胀系数与金属接近。
电学性能好氧化锆的介电常数是蓝宝石的3倍,信号更灵敏。
三、氧化锆陶瓷的应用氧化锆陶瓷广泛运用于3C电子、光通讯、智能穿戴、生物医用、珠宝首饰、日常生活、耐火材料等领域。
四、普通氧化锆陶瓷产品制备工艺一般生产制备流程(一)、氧化锆陶瓷粉体的制备微晶陶瓷是一种通过加热玻璃晶化能得到一种含有大量微晶相和少量玻璃相的复合固体材料。
微晶锆系陶瓷简称为微晶锆,具有耐磨、耐腐蚀、高强高韧等性质。
微晶锆陶瓷粉体的质量要求如下:1、粒度分布是正态分布,分级精度要高;2、颗粒形状接近圆形,颗粒强度高,应力均匀;3、分散性要好,无团聚或很少团聚;4、纯度要高有害杂质的含量要尽可能低。
(二)、将氧化锆陶瓷粉体加工成型:目前工艺上主要有下面四种加工成型方法:1、注射成型注射成型是通过在粉体中添加流动助剂,充模得到所需形状胚体。
主要生产外形复杂,尺寸精确或带嵌件的小型精密陶瓷件。
2、模压成型模压成型是将经过造粒、流动性好、粒配合适的粉料,装入磨具内,通过压机的柱塞施加外力使粉料制成一定形状的胚体。
氧化锆陶瓷概述.
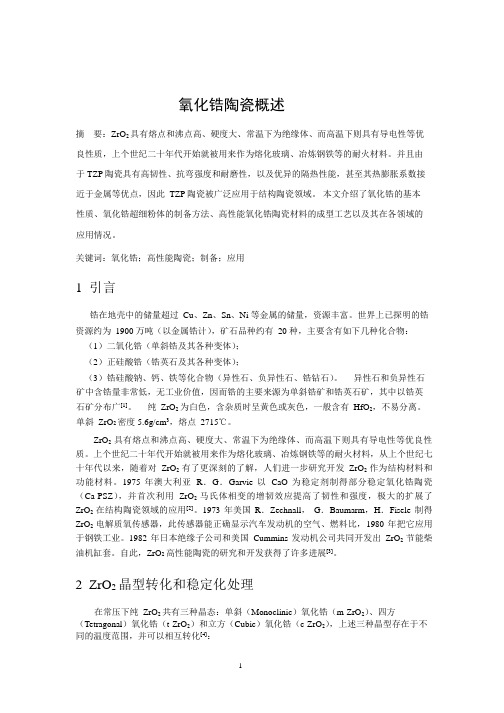
氧化锆陶瓷概述摘要:ZrO2 具有熔点和沸点高、硬度大、常温下为绝缘体、而高温下则具有导电性等优良性质,上个世纪二十年代开始就被用来作为熔化玻璃、冶炼钢铁等的耐火材料。
并且由于TZP 陶瓷具有高韧性、抗弯强度和耐磨性,以及优异的隔热性能,甚至其热膨胀系数接近于金属等优点,因此TZP 陶瓷被广泛应用于结构陶瓷领域。
本文介绍了氧化锆的基本性质、氧化锆超细粉体的制备方法、高性能氧化锆陶瓷材料的成型工艺以及其在各领域的应用情况。
关键词:氧化锆;高性能陶瓷;制备;应用1 引言锆在地壳中的储量超过Cu、Zn、Sn、Ni 等金属的储量,资源丰富。
世界上已探明的锆资源约为1900 万吨(以金属锆计),矿石品种约有20 种,主要含有如下几种化合物:(1)二氧化锆(单斜锆及其各种变体);(2)正硅酸锆(锆英石及其各种变体);(3)锆硅酸钠、钙、铁等化合物(异性石、负异性石、锆钻石)。
异性石和负异性石矿中含锆量非常低,无工业价值,因而锆的主要来源为单斜锆矿和锆英石矿,其中以锆英石矿分布广[1]。
纯ZrO2 为白色,含杂质时呈黄色或灰色,一般含有HfO2,不易分离。
单斜ZrO2 密度5.6g/cm3,熔点2715℃。
ZrO2 具有熔点和沸点高、硬度大、常温下为绝缘体、而高温下则具有导电性等优良性质。
上个世纪二十年代开始就被用来作为熔化玻璃、冶炼钢铁等的耐火材料,从上个世纪七十年代以来,随着对ZrO2 有了更深刻的了解,人们进一步研究开发ZrO2 作为结构材料和功能材料。
1975 年澳大利亚R.G.Garvie 以CaO 为稳定剂制得部分稳定氧化锆陶瓷(Ca-PSZ),并首次利用ZrO2 马氏体相变的增韧效应提高了韧性和强度,极大的扩展了ZrO2 在结构陶瓷领域的应用[2]。
1973 年美国R.Zechnall,G.Baumarm,H.Fisele 制得ZrO2 电解质氧传感器,此传感器能正确显示汽车发动机的空气、燃料比,1980 年把它应用于钢铁工业。
二氧化锆陶瓷的制备及性能分析

二氧化锆陶瓷的制备及性能分析二氧化锆陶瓷(ZrO2)是一种重要的结构材料,具有高温稳定性、优异的机械性能和优良的化学稳定性,因此在许多应用领域具有广泛的应用前景,如热障涂层、高温结构材料、生物医学材料等。
本文将介绍二氧化锆陶瓷的制备方法以及其性能分析。
二氧化锆陶瓷的制备方法主要包括固相反应法、水热法和溶胶-凝胶法等。
固相反应法是最常用的方法之一,其步骤主要包括将适当比例的锆粉和稳定剂混合、研磨混合均匀之后,在高温(约1300-1600℃)下烧结获得锆粉颗粒之间的结合,形成致密的二氧化锆陶瓷。
水热法则是通过在高温高压的水环境下,将锆盐溶解于水中,经过一系列的化学反应形成二氧化锆的纳米粒子,并在特定的条件下,通过后续的热处理制备得到二氧化锆陶瓷。
溶胶-凝胶法是一种常用的制备纳米颗粒的方法,通过将锆酸醋酸盐等无机盐溶解于溶剂中,得到溶胶,然后通过控制其凝胶过程形成凝胶,最后经过热处理获得二氧化锆陶瓷。
二氧化锆陶瓷的性能分析主要包括物理性能、力学性能和化学性能等。
物理性能主要包括晶体结构和晶型、晶粒大小和分布、密度等。
力学性能主要包括抗压强度、弹性模量和硬度等。
化学性能主要包括化学稳定性和生物相容性等。
在物理性能方面,二氧化锆陶瓷具有良好的热稳定性和机械稳定性,其晶体结构为立方相或四方相,晶粒通常在纳米级别,有利于提高材料的力学性能和化学稳定性。
在力学性能方面,二氧化锆陶瓷具有高抗压强度和硬度,其抗压强度通常在1000-2000MPa之间,硬度在8-12GPa之间。
这使得它适用于各种高强度和高温环境下的应用。
在化学性能方面,二氧化锆陶瓷具有较好的化学稳定性和生物相容性,能够在酸碱环境和生物体内保持稳定。
这使得它在生物医学领域有着广泛的应用,如人工关节、骨修复材料等。
综上所述,二氧化锆陶瓷具有优异的物理性能、力学性能和化学性能,制备方法多样,可以通过调控工艺参数和添加适宜的添加剂来改善其性能。
随着科学技术的进步,二氧化锆陶瓷在材料科学和工程领域的应用前景将更加广阔。
凝胶注模成型Al2O3ZrO2泡沫陶瓷的制备与表征

第5期张小珍等:凝胶注模成型AI:0,-ZrO:泡沫陶瓷的制备与表征1207图2不同相对密度ZTA泡沫陶瓷的SEM图Fig.2SEMcross・sectionsofZTAfoamceramicwithrelativedensityof(a)22%and(b)13%图3不同相对密度ZTA泡沫陶瓷的孔径分布Fig.3CellsizedistributionofZTAfoamceramicswithdifferentrelativedensiyRelativedensity/%图4ZTA泡沫陶瓷相对密度对抗弯强度的影响Fig.4FlexuralstrengthofZTAfoamceramicsproducedwithdifferentrelativedensity3.2ZTA泡沫陶瓷的强度泡沫陶瓷的强度主要取决于泡沫陶瓷制备工艺和相关结构参数,如其相对密度、孑L隙率和孑L壁厚度等h91。
图4为ZTA泡沫陶瓷相对密度与其抗弯强度的关系曲线。
由图可见,泡沫陶瓷相对密度的降低使其承受载荷有效面积减小,从而导致泡沫陶瓷的抗弯强度也相应减小。
根据Gibson和Ashby提出的描述开孔多孔泡沫陶瓷模型,脆性泡沫陶瓷强度与密度的关系可用幂函数表示为‘11|:矿。
,/orb=Cl(p/p。
)1’5(1)其中矿。
,为泡沫陶瓷的脆性破坏应力,仃h为泡沫陶瓷骨架断裂模量,C,为常数,与孑L的几何形状有关;p为泡沫陶瓷体积密度,P。
为骨架密度。
SepulvedaP和OliveiraF.A.Costa等¨2。
141采用一个类似的实验方程(2)很好的描述了泡沫陶瓷强度和密度间关系:tr/o"。
=c=(p/p。
)“(2)其中盯为泡沫陶瓷强度,盯。
为泡沫陶瓷骨架强度,C:和n为常数。
方程式(2)可进一步简化为方程式(3):矿=C3P,4(3)其中c,为一系数,相当于方程式(2)中C:和盯。
的乘积;p,为泡沫陶瓷的相对密度。
精密陶瓷射出成型制程技术简介

精密陶瓷射出成型制程技術簡介一.前言1.定義2.特點:耐腐蝕,耐磨,耐高溫,絕緣,比重輕,隔熱,無磁,人畜無害,耐低溫,熱膨脹系數可控制等.3.主要分類:碳化硅(S i C)=→非常高的硬度與熱傳性.氮化硅(S i3N4)=→良好的高溫強度與韌性.氧化鋁(A l2O3),氧化鋯(Z r O2),4.射出成型二.制程流程1.陶瓷粉末原料1.1粉體對產品性能影響➢堆積密度➢粒徑大小➢粒徑分布➢雜質成分➢比表面積➢顆粒外觀形狀1.2粉體的選擇a.日本第一稀元素化學工業株式會社的H S Y-3.0(見圖2,3)b.T o s o h C e r a m i c s株式會社的T Z-3Y S(見圖4,5)由粒徑分布可知:T o s o h C e r a m i c s的T Z-3Y S氧化鋯陶瓷粉體較細,凝團的程度可以藉由長時間的球磨處理加以降低,但仍然無法完全消除所有的凝團.如果氧化鋯陶瓷粉體的顆粒愈細,所需有機結合劑的添加量必須愈高,由初步實驗結果可以知道,日本的粉體都可以作為陶瓷射出成型的原料,但是T o s o h C e r a m i c s的T Z-3Y S粉體較細,所添加有機結合劑的量大,燒結后的尺寸收縮量較大,尺寸控制精度較不容易達到,但繞結后材料性質較佳.2.結合劑適當含量的粉體對成型很重要,一般控制在40-60%,不同固含量對粘度的影響(見圖6).2.1有機添加劑種類:➢主結合劑:P E,P P,P S,P V A(聚乙烯醇),P V B(聚乙烯縮丁醛)➢次結合劑:蜡,礦物油➢可塑劑:少量添加,可以增加粉未及結合劑在混合后的流動性,降低粘度.➢表面濕潤劑:少量添加,可以改善粉未和結合劑在混合期間的濕潤特性,增強其結合性.2.2結合劑選擇的基本考量:➢低粘度➢射出溫度範圍內粘度變化不大➢燒結后可以完全燒除或可經由溶劑完全萃取無殘留物➢在脫脂過程初期仍可維持相當的生胚強度➢在射出冷卻易凝固➢不會造成粘模➢不會與粉未起反應2.3多成份結合劑➢針對脫脂過程,可使胚件結合劑逐漸燒除避免胚件變形或崩裂,影響精度.➢結合劑的混合:須均勻分散,避免凝團,e g:P E,P P,P S➢結合劑的量2.4結合劑與粉未相容性3.混練與造粒3.1混練的作用:將陶瓷粉未與結合劑均勻混合在一起,使粉未顆粒因結合劑的緣故,產生濕潤現象並均勻分布於粉未周圍,使得整個混合料具有良好的可塑性.3.2混練設備:批式混練機(S i g m a或Z形葉片雙軸混練機)雙行星式行走混練機雙螺杆擠出機3.3混練步驟:➢將結合劑熔化➢將粉未整批或分批加入混練機,以機械剪力將陶瓷粉體分散於結合劑中.3.4造粒目的:控制射出粒的形狀及尺寸,避免射出成型時進料口發生射出料架橋現象,使陶瓷具有良好的流動性與充填性,以控制射出品質能夠穩定.3.5造粒方式:擠出造粒和粉碎造粒4.射出成型4.1成型設備:推杆式(P l u n g e r-T y p e)螺杆式(S c r e w-T y p e)(見圖7)4.2模具及制程參數:➢模具內部寬度變化盡量避免太大,減少射料壓力集中情形,工件肉厚變化量最好控制在3:1之內.➢避免采用大小不同的模穴.➢注口直徑較噴嘴大0.08公分,注口和襯間有5度的斜率,以利脫料.➢流道,較適當的形狀為圓形,而且流道不可太長.➢澆口,口徑較大較好.➢澆口位置,放在射出工件的最薄部位,避免放在模具的上端或下端,且應選擇平行於模具較長的部位.➢料溫➢射壓,盡量降低.➢模溫5.脫脂制程5.1脫脂(D e b i n d i n g,D e w a x i n g)制程是將射出生胚內的結合劑,藉熱分解法或溶劑萃取法移除之.陶瓷生胚一般以熱脫脂方式在大氣中或保護氣體下進行,而溶劑脫脂在金屬射出成型中已相當普遍.5.2脫脂過程➢多段脫脂設計.➢將生胚埋於粉末(e g碳,N i)床(p o w e r b e d)中進行脫脂作業,藉由粉末的毛細管現象將結合劑於低溫熔融狀態下吸出,避免氣化造成內應力再升高溫度,將殘留的主干高分子結合劑快速氣化,降低脫脂變形可能.➢溶劑脫脂.5.3制程參數對脫脂結果的影響➢升溫速率,結合劑開始熔融前,升溫速率可較快熔融后必須緩慢升溫,最后再以較快的升溫速率將高熔點的結合劑除去.➢持溫溫度➢持溫時間➢降溫速率➢鋪粉種類6.燒結制程6.1燒結是胚體經高溫加熱,使其致密化的過程,主要是排除粉末顆粒間的孔隙,達到致密化.6.2燒結的評估:密度及收縮率6.3影響繞結性質的因素:➢粒度分布:粒度愈小,表面積愈大,易燒結.➢充填密度:顆粒堆積密度愈高,愈易繞結.➢燒結溫度及時間➢升降溫速率➢燒結氣氛:高壓氣中燒結,胚體不易破裂.三.結論1.陶瓷射出成型優缺點優點:➢可制作形狀復雜的工件➢工件尺寸精度控制佳➢可以自動化大量生產➢生胚密度分布均勻➢產品表面光滑,性能優異缺點:➢模具費用高➢脫脂時間冗長➢肉厚工件脫脂困難➢制造成本不易降低2.關鍵技術。
ZrO_2泡沫陶瓷的制备及性能研究

文章编号:1003-1545(2007)05-0040-06ZrO 2泡沫陶瓷的制备及性能研究郭源源,吴基球(华南理工大学材料学院,广州广东 510640)摘 要:以CeO 2/Y 2O 3复合添加剂共稳定的TZP(四方氧化锆多晶)超细粉末为主要原料,用有机泡沫前驱体浸渍法制备多孔陶瓷。
论述了有机泡沫前驱体性质、浸浆工艺、浆料组分以及烧结温度对泡沫陶瓷力学性能与显微结构的影响。
得出使用弹性好、孔筋强度高、对浆料有良好吸附性的有机前驱体可以获得力学性能优良的泡沫陶瓷,并且当浆料中Al 2O 3为5%(w )、浆料涂覆量在017g/cm 3、烧结温度在1580e 时可获得最优力学性能的泡沫陶瓷材料。
关键词:泡沫陶瓷;二氧化锆;有机前驱体;力学性能中图分类号:TQ 174.75+8.11 文献标识码:A收稿日期:2007-03-09作者简介:郭源源,华南理工大学硕士研究生,研究方向为高性能陶瓷。
泡沫陶瓷是多孔材料的一种,它是具备三维立体网络结构和高孔隙率的多孔陶瓷材料。
其孔径从0.1~3mm 不等,孔率范围在65%~85%不等[1],特殊用途泡沫陶瓷的孔隙率甚至达90%[2]。
由于泡沫陶瓷的特殊结构,使其具有密度小、气孔率高、比表面积大、抗热震性、耐化学腐蚀性能以及对流体自扰性强及过滤吸附性好等特点。
通过调整原料和工艺可制备出具有高强骨架的泡沫体,犹如钢化了的泡沫塑料或瓷化了的海绵体[3]。
因此泡沫陶瓷被广泛应用在气体液体过滤、净化分离、化工催化、吸声减震、高级保温材料、生物植入材料以及特种强体材料和传感器等多方面[4,5]。
目前我国泡沫陶瓷的整体技术水平与国外相比差距较大,主要表现在:(1)品种少,规格小,质量不稳定,成形工艺不成熟,大型制品合格率低。
用于金属过滤领域的泡沫陶瓷,基本依靠进口。
(2)泡沫有机前驱体质量不稳定,弹性和气孔率都比较差,为了追求高的成品质量往往依靠国外进口的泡沫前驱体,增加了产品的成本。
特种陶瓷第二讲1 ZrO2陶瓷

在低温区析出t-ZrO2,这与传统 的t-ZrO2的稳定区间产生矛盾
原因:晶体结构、表面能、析
晶活化能
晶体结构
t-ZrO 2
(-111)
(111)
m-ZrO2
1000 C,1h 800 C,1h
o
o
(111)
600 C,1h
o
400 C,1h
o
光纤连接器用陶瓷:光纤连接器与光纤跳接线是光纤 网路中应用面最广且需求量最大的光无源器件。但是 目前国际上只有美日等发达国家有技术生产氧化锆插 芯和套筒,其毛坯生产技术在国内还是空白。陶瓷插 芯毛坯由于内含一个0.1mm的小孔,且对尺寸同心度 的要求都很高,因此采用传统的陶瓷材料成型方法难 以制备,只有通过注射成型的方法才有可能。
热处理温度 (℃)
t-ZrO2晶粒尺寸 (nm) m-ZrO2晶粒尺寸 (nm)
600
8.6 9.4
800
17 15.5
1000
- 33.8
从表5-1看到500、600和800 ℃热处理后tZrO2晶粒尺寸分别为5.1、8.6和17 nm, 处于表面能起决定作用的t-ZrO2稳定存在 的尺寸范围内,因此亚稳t-ZrO2可在低温 稳定存在。至1000 ℃热处理后,m-ZrO2 晶粒尺寸达到33.8 nm,而此时t-ZrO2已完 全消失,可知由于t-ZrO2此时晶粒尺寸已 大于30.6 nm的保持稳定的临界尺寸,所 以失稳并完全转变为m-ZrO2。
– 氧传感器
– 固体氧化物燃料电池 – 高温发热体
氧化锆陶瓷性质与应用
Y稳定的TZP陶瓷由于具有良好的性能,因此在很多领域 都有广泛的应用。 磨介:Y-TZP相对于锆珠、氧化铝球、玻璃球和钢球而言,其
氧化锆陶瓷球综述

概述氧化锆球是氧化锆材料中一类用量很大、应用面很广的产品,除了在氧化锆类陶瓷粉体研磨中大量使用外,在其它电子陶瓷粉料,磁性材料粉料、高技术结构和功能陶瓷粉料、日用陶瓷色料和釉料,化工和各类涂料,机械抛光用粉料,医药和食品粉剂的超细研磨中也发挥了为重要的作用。
氧化锆球就得解决在通常使用温度范围内(0-80℃)的单斜晶系转变成四方晶系的问题,掺杂碱土和稀土氧化物是一种有效的方法,这样就出现了不同的稳定剂,如氧化钇、氧化铈、氧化镁和氧化钙等。
实践证明,氧化钇和氧化铈稳定的氧化锆珠是较理想的研磨介质,具有较高的断裂强度和耐磨性。
常见的几种晶相的氧化锆。
不同的稳定剂、同一种稳定剂不同的量所稳定的氧化锆,晶相结构都不一样。
一、全稳定的氧化锆FSZ(Full Stabilized Zirconia):加8%摩尔比的氧化钇或15%摩尔比的氧化钙可得到正方晶相氧化锆,因此体系不会转变,故称为全稳定的氧化锆FSZ(Full Stabilized Zirconia),或称正方相氧化锆。
主要用作人工宝石、感应头、耐火材料和颜料等。
二、部分稳定的氧化锆PSZ(Partical Stabilized Zirconia):单斜相和正方相呈现这种结构。
因其具有的导热性而通常被用于加热和导热材料。
三、四方相氧化锆TZP(Tetragonal Zirconium Polycrystal) 或TTZ(Tetragonal Toughened Zirconia):加3%摩尔比的氧化钇或约12%摩尔比的氧化铈成为四方晶相氧化锆,此晶相的产品特别适合作研磨材料。
如韩国赛诺氧化锆珠CZY-95(密度≥6.0kg/dm3),CZC-80(密度≥6.2kg/dm3)和耐诺氧化锆球(NanorZr-95B),因它们具有较高的耐压强度和较的磨耗率而成为研磨介质的标杆产品。
陶瓷介质球常见的几种成型工艺1、毫米级氧化锆陶瓷球的制备方法毫米级陶瓷球的制备方法目前,制备毫米级陶瓷球的方法主要有模具压制法、“行星式”滚动法、直接热解法等。
5.2 氧化锆陶瓷(氧化锆增韧陶瓷)(2009.11.13)解析

1)相变增韧
ZrO2 颗粒弥散在其它陶瓷基体中,当基体对ZrO2颗粒有足 够的正应力,而ZrO2的颗粒度又足够小,则其相变温度可 降至室温以下,这样在室温时ZrO2 仍可以保持四方相。当 材料受到外应力时,基体对ZrO2 的压抑作用得到松弛, ZrO2 颗粒即发生四方相到单斜相的转变,并在基体中引起 微裂纹,从而吸收了主裂纹扩展的能量,达到增加断裂韧 性的效果,这就是ZrO2 的相变增韧。
氧化锆拉丝模与研磨环
氧化锆陶瓷轴承
陶瓷厨具和办公用品
手表表壳
光通讯用光纤陶瓷插芯
光纤连接器
氧化锆陶瓷人工关节球
陶瓷关节
五、ZrO2 增韧陶瓷
陶瓷材料虽然有许多优越的特性,如高温力学性能、抗 化学侵蚀性能、电绝缘性、较高的硬度和耐磨性等。但 由于其结构决定了陶瓷材料缺乏象金属那样在受力状态 下发生滑移引起塑性变形的能力,容易产生缺陷,存在 裂纹,且易于导致高度的应力集中,因而决定了陶瓷材 料脆性的本质。 因此,改善陶瓷材料的脆性是陶瓷学家的长期关注的问 题。近年来,纤维补强及氧化锆相变增韧在实践中被证 实对改善陶瓷的脆性以及强化陶瓷是两条有效的途径。
较纯的ZrO2粉呈黄色或灰色,高纯的ZrO2粉呈白色。ZrO2 的密度为5.49g/cm3 ,熔点为2715℃ 。
二、 ZrO2的结晶形态和晶形转化
在不同温度下,以三种同质异形体(allomorphish)存在,即 单斜晶系(monoclinie system,m- ZrO2)、四方晶系 (taragonal system,t- ZrO2)、立方晶系(cubie system,cZrO2)。三种晶型的ZrO2密度为:单斜型为5.65g/cm3 ,四方 型为6.10g/cm3 ,立方型为6.27g/cm3 。
ZrO2陶瓷粉末的制备方法

ZrO2陶瓷粉末的制备方法
佚名
【期刊名称】《无机化工信息》
【年(卷),期】2001(000)003
【摘要】ZrO2陶瓷由于其独特的相变效应与高温氧离子导电现象使其得到越来越广泛的应用。
在制作ZrO2陶瓷的过程中,制得性能优良的粉末是关键的第一步。
性能优良的粉末粒度要细且粒度分布范围窄。
此外,超细粉具有强烈的扩散能力,在烧结后期容易达到高密度甚至完全致密化。
【总页数】3页(P16-18)
【正文语种】中文
【中图分类】TQ174.758
【相关文献】
1.化学共沉淀法制备Sc2O3-Y2O3-ZrO2纳米陶瓷粉末及其高温相稳定性
2.反向共沉淀法制备Y2O3-ZrO2陶瓷粉末
3.化学沉淀法制备CeO2-La2O3-ZrO2陶瓷粉末
2O3-Y2O3-ZrO2低团聚纳米复合陶瓷粉末的制备
5.热障涂层用
Nd2O3-CeO2-ZrO2陶瓷粉末制备及其性能研究
因版权原因,仅展示原文概要,查看原文内容请购买。
zro2增韧Al2O3陶瓷

zro2增韧Al2O3陶瓷的制备(ZTA)摘要:ZrO2/Al2O3复相陶瓷是高温结构陶瓷中最有前途的材料之一,由于其优越的性能和丰富的原料来源,已受到广泛的关注,成为陶瓷材料领域研究的一大热点.本文对氧化锆/氧化铝复相陶瓷的复合机理、最近几年粉体制备常用和最新工艺和ZTA陶瓷应用方面的研究进展进行了综述,并对ZTA复相材料今后的发展进行了展望.关键词:ZTA;增韧机理;复合粉体制备;研究进展;发展趋势Abstrac t:Zirconia toughened aluminum (ZTA) hasbeenwidely studied as a new type of toughened ceramic.The aim of this investigation is to review the recent literatures on its synthesismechanisms, new preparation.methods of composite powders and applications. The problems in preparation techniques and developmental trend are discussed aswel.lKey words:ZTA; strengthening and tougheningmechanisms; preparation technology of composite powders;current research situation; development trendAl2O3陶瓷被广泛应用于一些耐高温、强腐蚀环境中,而Al2O3陶瓷断裂韧性较低的致命弱点,限制了它更大范围的使用.采用ZrO2相变增韧、颗粒弥散强化或纤维及晶须补强等方法,可使陶瓷材料的力学性能大大提高,是先进复相结构陶瓷材料的重要发展方向.从ZrO2/Al2O3系统相图[1]可知,即使在很高的温度下ZrO2与Al2O3之间都不会生成固溶体,这就为研究ZrO2/Al2O3复相陶瓷提供了理论依据.由于,ZTA陶瓷是zro2增韧陶瓷中效果最佳者,近年来,不少学者对该系统复相陶瓷进行了大量研究,随着复相陶瓷技术的发展, ZTA 复相陶瓷的研究成为陶瓷材料领域研究的一大热点.本文就近年来国内外文献对ZTA陶瓷的复合机理、制备方法、发展趋势等研究进展做如下综述.一、ZTA陶瓷的增韧机理ZTA陶瓷的增韧机理是晶须及纤维增韧,第二相弥散强化增韧, ZrO2相变增韧,以及与金属复合形成金属基复相陶瓷,残余应力增韧等等。
材料成型本科毕业论文选题(1116个)

毕业论文(设计)题目学院学院专业学生姓名学号年级级指导教师教务处制表二〇一五年十二月一日材料成型毕业论文选题(1116个)一、论文说明本写作团队致力于毕业论文写作与辅导服务,精通前沿理论研究、仿真编程、数据图表制作,专业本科论文300起,具体可以联系二、论文参考题目材料成型与控制专业《材料成形原理》课程教学探讨简析材料成型与控制工程的模具制造技术浅谈高校转型背景下材料成型专业毕业设计的改革研究材料成型及控制工程专业实践教学建设与改革探索试述新型金属材料成型加工技术以专业认证为导向的材料成型及控制工程专业课程设置具有交通特色的材料成型及控制工程专业课程体系探索与构建复合材料成型工艺方法的探讨高分子材料成型加工技术及应用浅析高分子材料成型加工技术提高材料成型专业本科生CAE技术应用能力的措施基于DSP的冲压材料成型控制规律的研究先进复合材料成型工艺过程中的质量控制高分子材料成型及其控制浅谈新型金属材料成型加工技术对高分子材料成型加工技术关键点的分析浅谈材料成型与控制技术的发展历程《材料成型力学》课程的软件建设的几点体会试论材料成型及控制与自动化技术浅析树脂基复合材料成型工艺《材料成型力学》课程的硬件改革与实践试析高分子材料成型加工技术材料成型及控制工程专业英语教学方法探讨浅谈材料成型及焊接的控制工艺谈材料成型及焊接的控制工艺校企合作培养材料成型及控制工程专业人才的思考*材料成型及控制工程专业的改革与实践探索材料成型原理课程教学改革与探索材料成型技术的现状及发展趋势关于材料成型及控制与自动化技术的研究初探关于《材料成型及控制工程》应用型本科人才培养方案修订工作的研究以工作为向导构建材料成型及控制工程课程体系建设新形势下材料成型与控制专业本科生毕业设计新模式研究EP/CF复合材料成型工艺分析浅析材料成型与控制技术专业人才的培养材料成型及控制工程专业本科人才培养方案问卷调查与分析高分子材料成型加工技术研究浅谈如何提高复合材料成型工艺实验的教学效果浅析高分子材料成型加工技术及其发展材料成型与控制工程模具制造技术分析复合材料成型工艺方法及优缺点分析对材料成型技术的现状及发展趋势的探讨材料成型与控制专业校外实习基地建设探索有关高分子材料成型加工技术研究对高分子材料成型加工技术关键点的分析《材料成型技术》课程改革探索材料成型及控制工程专业实践教学研究与探索材料成型及控制工程专业英语教学的思考“材料成型设备及自动化”课程教学方法探析浅析高分子材料成型加工技术关于高分子材料成型加工技术的探讨关于材料成型及控制工程专业建设的思考材料成型及控制工程专业卓越工程师培养的创新与实践高分子材料成型加工实验面向学生实践和创新能力培养的改革与探索关于材料成型原理的教学初探高分子材料成型加工技术的进展探析基于CDIO构建材料成型及控制工程专业模具方向课程群树脂基复合材料成型工艺发展进程研究浅谈如何提高复合材料成型工艺实验的教学效果浅谈如何提高复合材料成型工艺实验的教学效果高分子材料成型加工课程教学改革探索“焊接”与“材料成型”专业人才培养目标的差异性探究材料成型与控制工程模具制造技术分析浅谈材料成型及控制工程专业实践教学材料成型及控制工程专业应用创新型人才培养模式研究高分子材料成型加工技术的相关探究加强高分子材料成型加工课程实践性教学的探讨问题探究式教学法在材料成型工艺基础课中的应用材料成型专业课程实训实践体系构建与应用材料成型及控制工程专业教学探讨地方高校材料成型专业应用型人才的培养模式探讨材料成型CAD/CAE/CAM综合性实验教学方法初探析高分子材料成型加工技术材料成型及控制工程专业的改革与实践探索材料成型技术基础实验教学改革初探材料成型与控制工程专业英语教学改革探索基于实践的应用型本科院校“高分子材料成型加工实验”教学模式的探索研究高分子材料成型加工实验教学的改革与探索浅析高分子材料成型加工技术谈材料成型及焊接的控制工艺网络资源平台在材料成型及控制工程专业教学中的应用材料成型及控制工程培养方案修订的思考材料成型及控制工程专业卓越工程师培养的创新与实践材料成型及控制工程专业“基础+专业”双重特色教育的探索材料成型及控制工程专业英语教学实践与思考依托科研优势开展材料成型及控制工程专业特色化教育《复合材料成型工艺》课程教学改革探索与实践材料成型与控制工程模具制造技术分析初探构建新升本科院校材料成型与控制专业(模具方向)应用型人才培养模式基于应用型人才培养的材料成型专业实践教学模式分析高分子材料成型加工技术的进展分析对材料成型及控制工程专业实践教学的思考浅谈我校材料成型及控制工程专业课程体系改革材料成型及控制工程专业相关问题探讨与实践材料成型及控制工程专业实验课教学的探讨探析高分子材料成型及其控制技术高分子材料成型加工技术初探材料成型与控制工程专业毕业设计模式研究新形势下材料成型专业应用型人才培养探讨高分子材料成型加工技术的探索关于高分子材料成型技术的探讨地方本科院校材料成型及控制工程专业培养方向多元化的探索和实践材料成型原理课程教学改革的探索聚乳酸材料成型方法探析对材料成型及控制工程专业实践教学的思考与探索《材料成型力学》课教学手段改革初探浅谈高分子材料成型加工技术材料成型及控制工程应用型人才培养的探讨材料成型及控制工程专业实践教学的研究基于创业教育的材料成型与控制工程专业选修课程模块化设想关于高分子材料成型加工技术的探讨浅谈激光相变技术在材料成型中的应用基于卓越计划目标下的材料成型及控制工程专业认识实习改革高分子材料成型加工技术研究在材料成型及控制工程专业实施模块化培养的必要性材料成型及控制工程专业基础课程体系和实践实训的融合x浅谈地方高校材料成型与控制专业特色建设浅谈基于金属热处理的材料成型技术发展卓越计划背景下材料成型专业人才数字化技术培养体系的研究与实践“金属材料成型加工工艺”课程教学浅析材料成型工艺课程教学改革初探材料成型及控制工程专业特色及核心课程体系研究应用型本科院校在校企合作中材料成型专业的人才培养材料成型及控制工程专业仿真实习系统面向新能源发展的材料成型及控制工程专业课程体系优化方向地方院校建设材料成型及控制工程专业的探讨材料成型及控制工程专业课程群建设研究民办高校材料成型及控制工程专业教学的几点思考提高“材料成型”专业本科毕业设计质量的管理模式探讨基于应用型人才培养的材料成型专业实践教学模式探索材料成型与控制工程专业教学改革研究①基于校企合作材料成型专业应用型人才培养模式研究对高分子材料成型技术的思考新型金属材料成型加工技术研究《材料成型与控制》课程教学改革的探讨新型复合材料成型设备的现状分析地方高校材料成型及控制工程专业毕业设计环节创新与实践对材料成型及控制工程专业综合实训的思考材料成型及控制工程专业校外实习模式研究“材料成型技术基础”案例教学的设计与实践材料成型及控制工程专业动态实践教学的探索材料成型及控制工程专业特色培育的研究与实践浅谈高分子材料成型加工技术提高材料成型及控制工程专业毕业设计质量的研究快速原型技术在复合材料成型方面的应用浅谈高校材料成型及控制工程专业的教学建设探讨宽口径材料成型及控制工程的发展“材料成型工艺基础”课程教学改革研究与实践讨论式教学法在材料成型及控制工程专业教学中的应用一般普通高校材料成型与控制工程专业培养模式探索材料成型与控制工程专业建设探索谈材料成型及控制工程专业学生的创新能力计算机技术在材料成型专业教学中的应用材料成型与控制技术专业人才需求分析及培养模式研究材料成型与控制工程专业实践教学思考地方高校材料成型及控制工程专业培养方案探讨材料成型专业综合实践训练的实施与监控校企合作制定高职材料成型专业职业岗位标准的探索与实践大众教育下材料成型专业生产实习模式的探讨材料成型及控制工程专业应用型本科人才培养方案的构建与探索金属材料成型专业生产实习教学改革的探索材料成型及控制工程专业本科毕业设计(论文)指导的思考高职材料成型专业实训基地建设模式的思考与实践材料成型及控制工程专业建设探讨材料成型及控制工程专业实践教学的改革探索材料成型及控制工程专业本科毕业设计创新与实践材料成型及控制工程专业英语课程教学方法的思考与探究应用型高校“材料成型及控制工程”专业实验教学的改革与实践 CDIO指导下材料成型及控制工程专业人才培养模式研究浅析高分子材料成型材料成型与控制工程专业本科毕业设计研究谈材料成型及控制工程专业的人才培养材料成型专业应用型人才的培养目标及实现途径地方高校材料成型及控制工程专业实践教学体系研究关于强化材料成型及控制工程专业生产实习教学的探讨关于材料成型及控制工程专业英语课程教学改革的思考材料成型专业生产实习教学改革的探索与实践材料成型与控制工程专业精品课的建设材料成型及控制工程专业课程体系的改革《材料成型工艺基础》多媒体立体化教学模式的构建与实践《材料成型原理》课程建设与改革浅析高分子材料成型加工技术材料成型专业学生进行“双创”教育模式试点与研究关于“材料成型”专业建设的思考材料成型及控制工程专业教学内容与课程体系的改革与实践碳纤维复合材料的成型工艺浅析《金属材料及成型工艺》课程标准制订中间相沥青纤维基自粘结炭材料的成型与微观形貌研究地方本科院校《工程材料及成型技术基础》课程教学研究从微观设计角度谈材料、成型及形态的互动探析金属材料焊接成型中的主要缺陷及控制措施耐火材料机械成型的几点经验探析金属材料焊接成型中的主要缺陷及控制措施材料焊接成型方法的选择原则与依据ZrO2精细陶瓷材料湿法成型工艺概述航空工业复合材料制件成型工艺进展半刚性基层材料振动成型设计方法复合材料整体成型关键技术现状分析研究玻纤增强材料注塑成型工艺特点研究华南理工大学:产学研合作推动高分子材料新型成型装备产业化pc材料特性及成型工艺浅析PC材料特性及成型工艺PC材料特性及成型工艺高强混凝土的原材料选择与成型养护工艺新型摩擦材料的低温成型工艺研究塑木复合材料的挤出成型加工工艺研究防火门门芯材料填充一体成型工艺解决方案冲压成型材料综述复合材料结构件固化成型工艺参数控制复合材料LCM整体成型工艺发展及应用复合材料长桁共固化成型工艺研究复合材料叶片RTM成型缺陷研究高分子材料加工(塑料成型工艺方向)专业教学改革的探讨舞美制作材料与舞台道具成型Nd-Fe-B永磁材料的粉末注射成型技术材料机械性能在挤压成型中的作用探析材料机械性能在挤压成型中的作用探析三维立体打印成型技术及其材料研究攻克Z8CND17-04材料中间部位变形的卧锻成型材料参数对汽车发动机隔热板冲压成型性能影响Z值对凝胶注模成型SiC—Sialon材料烧结性能的影响成型压力对Al2O3基复合材料中铁纤维氧化程度的影响压力成型制备SiC—Sialon复相材料材料成型与控制专业《材料成形原理》课程教学探讨简析材料成型与控制工程的模具制造技术浅谈高校转型背景下材料成型专业毕业设计的改革研究材料成型及控制工程专业实践教学建设与改革探索试述新型金属材料成型加工技术以专业认证为导向的材料成型及控制工程专业课程设置具有交通特色的材料成型及控制工程专业课程体系探索与构建复合材料成型工艺方法的探讨高分子材料成型加工技术及应用浅析高分子材料成型加工技术提高材料成型专业本科生CAE技术应用能力的措施基于DSP的冲压材料成型控制规律的研究先进复合材料成型工艺过程中的质量控制高分子材料成型及其控制浅谈新型金属材料成型加工技术对高分子材料成型加工技术关键点的分析浅谈材料成型与控制技术的发展历程《材料成型力学》课程的软件建设的几点体会试论材料成型及控制与自动化技术浅谈高分子材料成型及其控制技术浅析树脂基复合材料成型工艺《材料成型力学》课程的硬件改革与实践试析高分子材料成型加工技术材料成型及控制工程专业英语教学方法探讨浅谈材料成型及焊接的控制工艺谈材料成型及焊接的控制工艺校企合作培养材料成型及控制工程专业人才的思考*材料成型及控制工程专业的改革与实践探索材料成型原理课程教学改革与探索材料成型技术的现状及发展趋势关于材料成型及控制与自动化技术的研究初探关于《材料成型及控制工程》应用型本科人才培养方案修订工作的研究以工作为向导构建材料成型及控制工程课程体系建设新形势下材料成型与控制专业本科生毕业设计新模式研究EP/CF复合材料成型工艺分析浅析材料成型与控制技术专业人才的培养材料成型及控制工程专业本科人才培养方案问卷调查与分析高分子材料成型加工技术研究浅谈如何提高复合材料成型工艺实验的教学效果浅析高分子材料成型加工技术及其发展。
电瓷湿法成型工艺特点
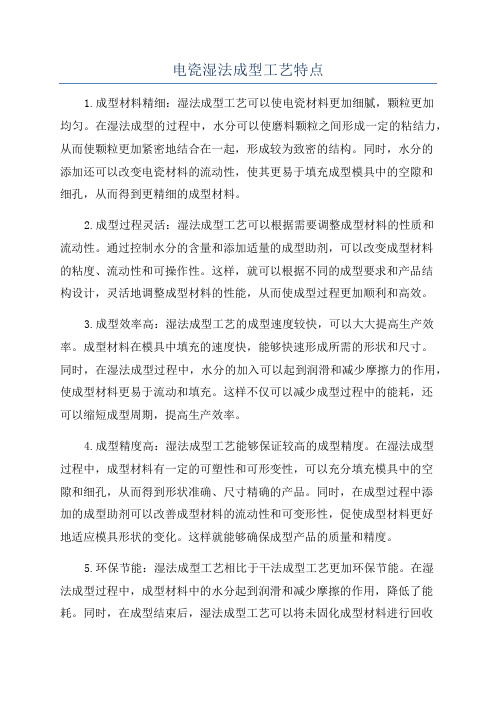
电瓷湿法成型工艺特点1.成型材料精细:湿法成型工艺可以使电瓷材料更加细腻,颗粒更加均匀。
在湿法成型的过程中,水分可以使磨料颗粒之间形成一定的粘结力,从而使颗粒更加紧密地结合在一起,形成较为致密的结构。
同时,水分的添加还可以改变电瓷材料的流动性,使其更易于填充成型模具中的空隙和细孔,从而得到更精细的成型材料。
2.成型过程灵活:湿法成型工艺可以根据需要调整成型材料的性质和流动性。
通过控制水分的含量和添加适量的成型助剂,可以改变成型材料的粘度、流动性和可操作性。
这样,就可以根据不同的成型要求和产品结构设计,灵活地调整成型材料的性能,从而使成型过程更加顺利和高效。
3.成型效率高:湿法成型工艺的成型速度较快,可以大大提高生产效率。
成型材料在模具中填充的速度快,能够快速形成所需的形状和尺寸。
同时,在湿法成型过程中,水分的加入可以起到润滑和减少摩擦力的作用,使成型材料更易于流动和填充。
这样不仅可以减少成型过程中的能耗,还可以缩短成型周期,提高生产效率。
4.成型精度高:湿法成型工艺能够保证较高的成型精度。
在湿法成型过程中,成型材料有一定的可塑性和可形变性,可以充分填充模具中的空隙和细孔,从而得到形状准确、尺寸精确的产品。
同时,在成型过程中添加的成型助剂可以改善成型材料的流动性和可变形性,促使成型材料更好地适应模具形状的变化。
这样就能够确保成型产品的质量和精度。
5.环保节能:湿法成型工艺相比于干法成型工艺更加环保节能。
在湿法成型过程中,成型材料中的水分起到润滑和减少摩擦的作用,降低了能耗。
同时,在成型结束后,湿法成型工艺可以将未固化成型材料进行回收利用,降低了材料的浪费。
这样不仅可以减少资源消耗,还可以减少对环境的污染。
总之,电瓷湿法成型工艺具有精细成型,灵活性高,效率高,精度高和环保节能等特点,可以满足电瓷材料成型的需求,提高产品质量和生产效率。
- 1、下载文档前请自行甄别文档内容的完整性,平台不提供额外的编辑、内容补充、找答案等附加服务。
- 2、"仅部分预览"的文档,不可在线预览部分如存在完整性等问题,可反馈申请退款(可完整预览的文档不适用该条件!)。
- 3、如文档侵犯您的权益,请联系客服反馈,我们会尽快为您处理(人工客服工作时间:9:00-18:30)。
ZrO2精细陶瓷材料湿法成型工艺概述
摘要:Zr02具有熔点和沸点高、硬度大、常温下为绝缘体、而高温下为导体等良性质。
在20世纪70年代出现了氧化锆陶瓷增韧材料,使氧化锆陶瓷材料的力学性能获得了大幅度的提高,极大的扩展了Zr02在结构陶瓷领域的应用。
本文主要介绍了论述了氧化锆精细陶瓷材料的湿法成型工艺的有关研究现状,分析了不同工艺方法的优缺点和应用领域。
关键词:关氧化错高性能陶瓷制备应用
就目前陶瓷制备工艺的发展水平来看,成型工艺在整个陶瓷材料的制备过程中起着承上启下的作用,是保证陶瓷材料及部件的性能可靠性及生产可重复性的关键,与规模化和工业化生产直接相关。
下面介绍氧化锆精细陶瓷材料湿法成型较为常用的几种方法。
一、注浆成型
注浆成型属于传统工艺,适合制备形状复杂的大型陶瓷部件,但坯体质量,包括外形、密度、强度等都较差,工人劳动强度大且不适合自动化作业。
二、热压铸成型
热压铸成型是在较高温度下使陶瓷粉体与粘结剂(石蜡)混合,获得热压铸用的浆料,浆料在压缩空气的作用下注入金属模具,保压冷却,脱模得到蜡坯,蜡坯在惰性粉料保护下脱蜡后得到素坯,素坯再经高温烧结成瓷。
热压铸成型的生坯尺寸精确。
内部结构均匀,模具磨损较小,生产效率高,适合各种原料。
蜡浆和模具的温度需严格控制,否则会引起欠注和变形,因此不适合用来制造大型部件,同时两步烧成工艺较为复杂,能耗较高。
三、流延成型
流延成型是把陶瓷粉料与大量的有机粘结剂、增塑剂、分散剂等充分混合,得到可以流动的粘稠浆料,把浆料加人流延机的料斗,用刮刀控制厚度,经加料嘴向传送带流出.烘干后得到膜坯。
此工艺适合制备薄膜材料,为了获得较好的柔韧性而加入大量的有机物,要求严格控制工艺参数,否则易造成起皮、条纹、薄膜强度低和不易剥离等缺陷。
所用的有机物有毒性,会产生环境污染,应尽可能采用无毒或少毒体系,减少环境污染。
四、直接凝固注模成型
直接凝固注模成型是由苏黎世联邦工学院开发的一种成型技术。
将溶剂水、陶瓷粉体和有机添加剂充分混合形成静电稳定、低粘度、高固相含量的浆料,在其中加入可改变浆料pH值或增加电解质浓度的化学物质,然后将浆料注入到无孔模中。
工艺过程中控制化学反应的进行,使注模前反应缓慢,浆料保持低粘度,注模后反应速度加快,使流态的浆料转变为固态的坯体。
得到的生坯具有很好的机械性能,强度可以达5×103Pa。
生坯经脱模、干燥、烧结后,形成所需形状的陶瓷部件。
其优点是不需或只需少量的有机添加剂(小于1%),坯体不需脱脂,密度均匀,相对密度高(55~70%),可以成型大尺寸、形状复杂的陶瓷部件。
其缺点是添加剂价格昂贵,反应过程中一般有气体放出。
五、注射成型
注射成型在20世纪70年代末80年代初开始应用于陶瓷零部件的成型。
该方法通过添加大量有机物来实现瘠性物料的塑性成型,是陶瓷可塑成型工艺中最普遍的一种方法。
在成形过程中,除了使用热塑性有机物(如聚乙烯、聚苯乙烯)
或热固性有机物(如环氧树脂、酚醛树脂),或水溶性的聚合物作为主要的粘结剂以外,还必须加入一定数量的增塑剂、润滑剂和偶联剂等工艺助剂,以改善陶瓷注射悬浮体的流动性,并保证注射成型坯体的质量。
注射成型工艺具有自动化程度高、成型坯体尺寸精密等优点。
但注射成型陶瓷部件的生坯中有机物含量多达50%(体积分数),在后续烧结过程要排除这些有机物需要很长时间,甚至长达几天到数十天,而且容易造成质量缺陷。
因此,排胶始终是制约其应用的一个关键环节,至今尚未完全突破。
六、胶态注射成型
为解决传统注射成型工艺中有机物加入量大、排除困难等问题,清华大学创造性地提出了陶瓷胶态注射成型新工艺,并自主开发了胶态注射成型样机,实现了瘠性陶瓷料浆的注射成型。
其基本思路是将液态成型与注射成型相结合,利用专用的注射成型设备和胶态原位凝固成型的固化技术,进行陶瓷材料的注射成型。
这一新工艺,使用的有机物最多不超过4%(质量分数),利用水基悬浮体中少量的有机单体或有机化合物在注人模具后快速诱发有机单体聚合生成有机网络骨架,将陶瓷粉体均匀包裹其中,不但使排胶时间大为缩短,同时也大大降低了排胶开裂的可能性。
既具有胶态原位凝固成型坯体均匀性好,有机物含量低的特色,又具有注射成型自动化程度高的优点,是胶态成型工艺的一种质的升华,将成为高技术陶瓷走向产业化的希望所在。
不同的工艺方法试用与不同的领域和环境,只有采用事宜的方法,才能展现不同工艺的优越性,提高产品性能。
同时,不断涌现的新技术也给我们更多的启示,为制造性能更为优良的材料提供新的思路和方法。
参考文献
[l]Garcie R C’Harmlnk R H2aseoe R T Cerma_Licstee|NatureⅡ],1975,258:703~704.
[2]王零森.陶瓷工程[J],1997,31(1):40~44.
[3]Wo]ton G M et aj J Am Ceram SocⅡ]’1963,46(9):418~422.
[4]王钢,等.西北轻工业学院学报[J].2000,18(1):99~103.
[5]李蔚,等无机材料学报[J],1999,14(1):161~164.
[6]EL Yuan ef a/.Solid State Inoics[J].1998(1):119~123.
[7]黄勇,等.现代技术陶瓷[J],1995,16(4):4~11.
[8]Young AC,et越J Am.Ceraw.SocⅡ].1991,74(3):612~618.
[9]杨金龙陶瓷胶态成型工艺及其原位凝固机制的研究
北京:清华大学.1996.
[10]李家驹.陶瓷工艺学.北京:中国轻工业出版社,2001.。