镇海炼化-Ⅱ加氢装置加氢精制综合能耗现状及对策措施
镇海炼化开展炼化一体化工作的实践与探索

MTBE
煤油 柴油
PP PP
LPG
PX装置
汽油 PX
加氢裂化
蜡油加氢
催化裂化
气化料、燃料
溶剂脱沥青
焦化
焦炭
CFB锅炉
电/蒸汽
沥青
镇海炼化分公司
镇海炼化公司简介 炼油图片:
镇海炼化分公司
镇海炼化公司简介 乙烯图片:
镇海炼化分公司
内容提纲
镇海炼化乙烯工程情况介绍
镇海炼化分公司
镇海炼化乙烯情况介绍
项目 单位
酸性气 W% 干气 W% 液化气 W% 轻石脑油 W% 重石脑油 W% 煤油 W% 柴油 W% 尾油 W% 合计
尾油BMCI
中油型加氢裂化方案
1#加裂 2#加裂
1.00
1.87
2.93
3.66
1.53
2.67
13.94
4.77
13.46
26.16
36.61
18.88
27.49
17.72
3.04
➢ 主要时间节点:
➢ 2006年3月17日, 正式获得国家发改委核准。 ➢ 2006年11月6日,举行开工奠基仪式。 ➢ 2007年4月2日,总体设计获得批复。 ➢ 2010年4月30日,建成投产。 ➢ 2010年6月,实现平稳运行。
➢ 总投资估算为约235亿元,实际节省约30亿元。
镇海炼化分公司
镇海炼化乙烯装置组成及规模
24.27
100.00
100.00
14~16
轻油型加氢裂化
1#加裂 2#加裂
2.01
1.85
0.61
3.18
1.94
2.65
2.92
7-镇海炼化-Ⅱ加氢装置加氢精制石脑油带水解决方案探讨49-51
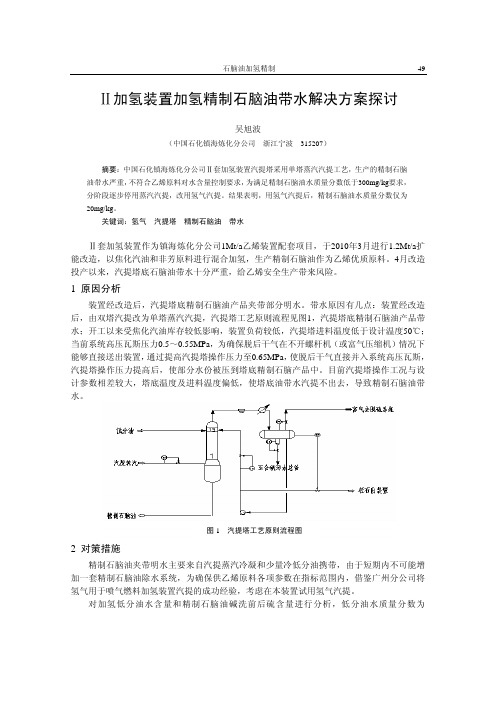
103
塔顶温度
138
115
114
112
103
101
塔底蒸汽量
1.0
0.8
0.6
0.6
0.4
0.3
硫
56
28
35
55
61
125
溴价
1.94
0.49
0.43
0.17
0.17
0.18
从表1中可以看出,当汽提塔降压至0.45MPa,塔底汽提蒸汽量降到0.6t/h时,塔底石脑油
中硫质量分数为35 mg/kg,精制石脑油硫含量能够满足乙烯原料质量指标要求。汽提塔压力从
3.2 第二阶段
通过第一阶段降低塔压和汽提蒸汽流量工况调整,精制石脑油水含量减少,精制石脑油 中硫化氢含量上升,但精制石脑油硫含量符合产品质量要求。第一阶段工况调整,为第二阶 段改用氢气汽提提高可靠数据支撑。
6月25日在塔底汽提蒸汽不停用情况下,打通氢气汽提流程,分步提高塔压至0.65MPa, 逐渐减小汽提蒸汽流量,表2为不同操作工况下精制石脑油分析结果。从表2中可以看出,精 制石脑油硫含量、水含量呈明显下降趋势。
3 措施实施
引一氢气管线至汽提塔,作为氢气汽提线,汽提塔氢气汽提流程见图2。
图2 汽提塔氢气汽提流程
为避免改用氢气汽提后对产品质量造成较大影响,进而污染石脑油产品罐,在投用氢气 汽提的过程中对汽提塔分两个阶段进行摸索调试操作:第一阶段对汽提塔实施降压,降汽提 蒸汽操作;第二阶段停塔底汽提蒸汽,改用氢气汽提操作。
制氢装置能耗分析及节能措施的探讨

制氢装置能耗分析及节能措施的探讨摘要:本文分析了中国石化海南炼化有限公司制氢装置的能耗构成及影响能耗的主要因素,从装置的技术特点出发,对制氢装置的节能减排进行探讨,明确了提高装置利用率、降低燃料气、电的消耗是降低能耗的主攻方向。
通过采用一系列的节能措施,如给鼓引风机增设变频器并投用功率较小的压缩机代替原来功率较大的压缩机,大大降低了电的消耗;对转化炉的内壁进行喷涂红外反辐射涂料,余热回收系统更换热管,提高了装置的利用率,降低了燃料气的消耗。
工业运行结果表明:改进后的方案能保证系统安全平稳运行,经济效益显著。
关键词:制氢装置转化炉余热回收系统能耗节能一、前言中国石化海南炼化分公司制氢装置于2006年建成投产,本装置以燃料气和PSA尾气为原料,设计能力为6×104Nm3/h工业氢,装置的产品氢气纯度为99.99%,年开工时数为8400小时,相当于年产纯氢4.59万吨。
但在生产中为适应下游加氢装置处理量的要求,其实际处理量仅为设计负荷的30%~40%,造成了大马拉小车的现象。
这不仅使装置的生产力没有得到充分利用,并且增加了装置的损耗率,对运行和投资来说都是一种浪费[1-2]。
为了改变装置高能耗低效益的不利局面,尽可能低的降低能耗及生产成本,在2009年至2011年陆续对部分制氢装置进行了技术改造,取得了一定效果。
二、制氢装置技术特点装置采用烃类水蒸气转化法造气和变压吸附法提纯氢气的工艺,以天然气和RDS装置提供的PSA尾气为原料,当PSA尾气及天然气供给量不足时可以以罐区提供的液态烃及石脑油为补充原料,产品氢气纯度可达99.99%,副产品为变压吸附尾气,全部用作转化炉燃料。
装置不设原料预热炉,原料用过热蒸汽预热,并采用三合一产汽流程(即烟道气、转化气、中变气的产气系统共用一台汽水分离器)以及转化炉烟气多段换热系统等诸多措施尽可能回收转化炉的余热,提高了转化炉的利用率。
三、原料能耗分析由表1为2008年2、4、6月该装置的加工能耗统计,由表1可知制氢装置能耗主要由燃料气、蒸汽、水和电等构成,其中燃料(燃料气与脱附气之和)能耗最大,其次是电。
常减压蒸馏装置主要问题和应对措施

中国常减压蒸馏装置的主要问题和应付举措凌逸群中石化企业炼化部门,北京1000291前言固然在过去的几十年里 , 中国的直流催化裂化技术已获得了日新月异的成就 , 未来加氢办理 ,加氢裂化 ,加氢精制 ,催化重整技术也将跟着环境规那么的愈来愈严格 , 汽油、柴油燃料标准的愈来愈精准而经历飞快的展开。
只管这样,常减压蒸馏装置作为原油加工的第一道工序有着特别大的办理能力,它影响着炼油厂的工艺流程,对经济效益也有侧重要影响。
近来几年,跟着适用技术和高效设施的展开及应用,对于常减压塔操作的问题惹起了高度重视。
2生产和操作上的主要问题到 2001 年末,中石化拥有的48 套常减压蒸馏装置,其总设计办理量为139百万吨,包含一个8 百万的装置,六个 5 百万吨的装置, 14 个 3-4 百万吨的装置和一些办理量少于 3 百万吨的装置。
47套蒸馏装置是在 2001年开始运行的并以均匀 72.7%的负荷率加工了总合百万吨的原油。
当前,在蒸馏装置的操作上存在四个主要问题。
2.1 总能量耗费量较高总能量耗费量是常减压蒸馏装置的一个重要的经济技术困难。
2001 年中石化的蒸馏装置的总能量耗费量是11.85 千克 SOE/ 吨〔包含荒弃的减压蒸馏装置的能量耗费〕,变化围在 10.47 到 16.41 千克 / 吨,与外国先进装置的能量耗费水平对比,中国总的能量耗费量更高些,这类现象的原由归罪于以下几个方面。
2.1.1 小型装置检修率低外国独立蒸馏装置的办理量一般在 5 百万吨 / 年到 1 千万吨 / 年,这些装置的维修率超出 85%,在 2001 年,中石化的独立蒸馏装置的均匀办理能力在290 万吨 / 年,其均匀负荷率为72.7%,致使了更高的原料和能量耗费。
2.1.2 加热炉燃料耗费量高常减压蒸馏装置中加热炉的燃料耗费量占蒸馏装置总燃料耗费量的70% 以上。
加热炉的燃料耗费量过高是造成常减压蒸馏装置总耗费量高的主要原由。
镇海炼化两套加氢装置脱硫系统工况分析与优化

关键词 加氢 脱硫系统 管线泄漏 来自质升级 优化1 装置概况 镇 海 炼 化 3.0Mt/a 柴 油 加 氢 精 制 装 置 ( 简 称 Ⅳ
加 氢)与 1.8Mt/a 蜡 油 加 氢 装 置(简 称Ⅴ加 氢)公 用 一 套脱硫系统,由两个单独的循环氢脱硫塔、一个低 分气脱硫塔、一个脱硫化氢汽提塔顶气脱硫塔和富 溶剂再生设施组成。
· 72 ·
中外能源 SINO-GLOBAL ENERGY
2013年 第 18 卷
镇海炼化两套加氢装置脱硫系统工况分析与优化
叶立峰
( 中 国 石 化 镇 海 炼 化 分 公 司 , 浙 江 宁 波 315207)
摘 要 镇海炼化Ⅳ,Ⅴ加氢装置脱硫系统因长期加工高硫原油 ,造成循环氢脱硫塔看窗引出法兰根部泄漏 、底部液控阀内
富 液 由 Ⅴ 加 氢 循 环 氢 脱 硫 塔 T3104、T3105、 T3106 底 部 抽 出 , 并 与 来 自Ⅳ加 氢 装 置 的 循 环 氢 脱 硫 塔 T2103 富 液 混 合 , 通 过 富 液 过 滤 器 (FI3105) 除 去 杂 质 后 , 再 经 贫 富 液 换 热 器 (E3112A/B) 换 热 至 98℃,进 入 富 液 闪 蒸 罐(V3116)降 压 闪 蒸 。 少 量 的 轻 烃气体汽化后在压力控制下排至火炬,闪蒸后的富 液 由 V3116 底 部 抽 出 ,在 液 位 控 制 下 进 入 溶 剂 再 生 塔(T3107)第 3 层 塔 盘 。 胺 液 由 T3107 下 部 集 液 箱 抽 出 , 作 为 溶 剂 再 生 塔 底 重 沸 器 (E3114) 进 料 , 经 重 沸 加 热 后 返 回 塔 底 部 ,E3114 的 热 源 正 常 生 产 时 由 装 置 自 产 的 0.3MPa 饱 和 蒸 汽 提 供 , 蒸 汽 不 足 时 由 催 化 装 置 过 来 的 蒸 汽 进 行 补 充 , 开 工 时 1.0MPa 蒸 汽 经 减 温 减 压 器(JW3101)后 作 为 E3114 的 热 源 。T3107 顶 部 气 体 经 溶 剂 再 生 塔 顶 空 冷 器 (A3106) 冷 却 至 40℃ 后 , 进 入 溶 剂 再 生 塔 顶 回 流 罐 (V3117),V3117 顶部出来的酸性气在压力控制下送出装置,底部抽 出 的 液 体 经 溶 剂 再 生 塔 顶 回 流 泵(P3110A/B)升 压 后 作 为 T3107 回 流 。
柴油加氢改质装置节能降耗技术分析与对策

柴油加氢改质装置节能降耗技术分析与对策一、柴油加氢改质装置的技术原理柴油加氢改质装置,简称加氢装置,是通过在柴油发动机的进气道中加入氢气,利用氢气与柴油混合燃烧,从而提高燃烧效率,减少尾气排放,降低燃油消耗的一种技术手段。
其技术原理主要包括以下几个方面:1. 燃烧效率提高:通过向柴油中加入氢气,可以使得燃油在燃烧过程中更加充分,提高燃烧效率,从而减少燃油的消耗。
2. 尾气排放降低:氢气在燃烧过程中可以与氧气充分混合,从而减少燃烧产生的有害气体,降低尾气排放。
3. 发动机功率提升:利用氢气的高热值特性,可以提高柴油发动机的实际功率输出,实现动力提升的效果。
2. 排放水平降低:氢气的加入可以改善柴油发动机的燃烧过程,减少有害气体的排放,对环境保护具有显著效果。
在实际应用柴油加氢改质装置时,需要克服一些技术难题,从而实现更好的节能降耗效果。
以下是针对柴油加氢改质装置的技术对策:1. 加氢装置的稳定性:加氢装置在柴油发动机中的工作稳定性是关键,需要解决在车辆长时间运行或在极端环境下出现的稳定性问题。
2. 加氢装置的安全性:在加氢改质过程中,需要保证氢气供应系统的安全和稳定,避免出现安全隐患。
3. 加氢装置的成本控制:加氢装置需要在成本可控的基础上提供良好的节能降耗效果,因此需要在技术和成本的平衡上进行合理的控制。
4. 加氢装置与柴油发动机的匹配问题:加氢装置需要与柴油发动机良好的匹配,保证在不影响发动机正常工作的情况下提供更好的节能降耗效果。
四、结语柴油加氢改质装置的节能降耗技术具有很大的应用前景,需要不断进行技术创新和实践应用,从而为我国能源资源的可持续发展作出更大的贡献。
镇海炼化Ⅰ套加氢裂化装置扩能及节能改造
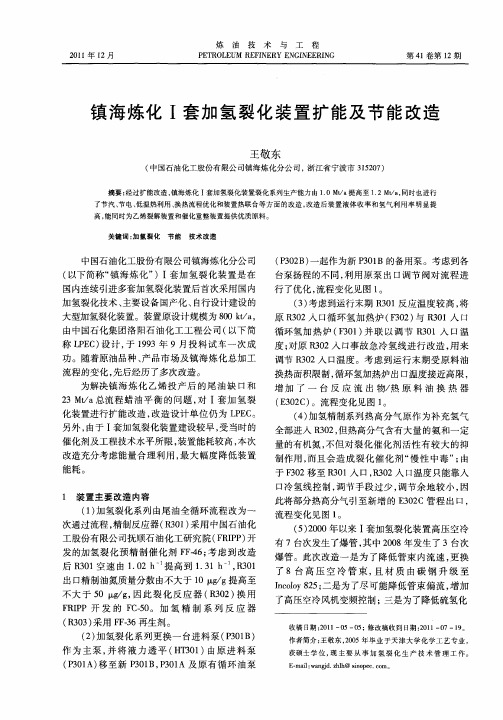
( )00年以来 I 5 20 套加氢裂化装置高压空冷 有 7台次发 生 了爆 管 , 中 20 其 0 8年发 生 了 3台次
爆管 。此次 改造 一 是 为 了降 低 管 束 内流 速 , 换 更
出口精制油氮质量分数由不大于 1 t / 提高至 0 ̄ g g
不 大 于 5 gg 因 此 裂 化 反 应 器 ( 32 换 用 0 /, R0) F IP开 发 的 F . 。 加 氢 精 制 系 列 反 应 器 RP C5 0 ( 33 采用 F 一6再 生剂 。 R0 ) F3 () 2 加氢 裂化 系 列 更换 一 台进 料泵 ( 3 1 P0 B)
了 8台 高 压 空 冷 管 束 , 材 质 由碳 钢 升 级 至 且
Icl 5 二是为 了尽可能降低管束偏流 , no y 2 ; o8 增加
了高压空冷风机变频控制 ; 三是为了降低硫氢化
收稿 日 : 1 — 5 0 ; 期 2 1 0 — 5 修改稿收到 日 :0 1 0 —1 。 0 期 2 1 — 7 9 作者简介 : 王敬东 ,05年 毕业 于天津大 学化 学工 艺专业 , 20
获硕士 学 位 , 主 要 从 事 加 氢 裂 化 生 产 技 术 管 理 工 作 。 现
E m i w n i.hh io e .o — al a g z l @s p c c n。 : d n
作 为主泵 , 并将 液力 透平 ( T0 ) H 3 1 由原 进料泵
(3 1 移 至 新 P0 B,3 1 及 原 有 循 环 油 泵 P0 A) 3 1 P 0A
关键词 : 加氢 裂 化 节能 技 术改 造
中国石油 化工股 份有 限公 司镇海炼 化分 公 司 ( 以下简 称“ 海 炼 化 ” 镇 )I套 加 氢 裂化 装 置 是 在 国内连续 引进 多套加 氢裂化 装置 后首次 采用 国内 加 氢裂化 技术 、 主要 设备 国产 化 、 自行设计 建设 的 大型加 氢裂化装置 。装置原设 计 规模为 80k a 0 t , / 由 中国石化集 团 洛 阳石油 化 工工 程公 司 ( 以下 简 称 L E ) 计 , 19 PC 设 于 93年 9月 投 料 试 车 一 次 成 功 。随着原油 品种 、 品市 场 及镇 海 炼 化 总 加工 产 流程 的变化 , 后经历 了多次改造 。 先 为解 决镇 海 炼 化 乙烯 投 产 后 的 尾 油 缺 口和
炼化企业低负荷工况及停开工节能优化措施
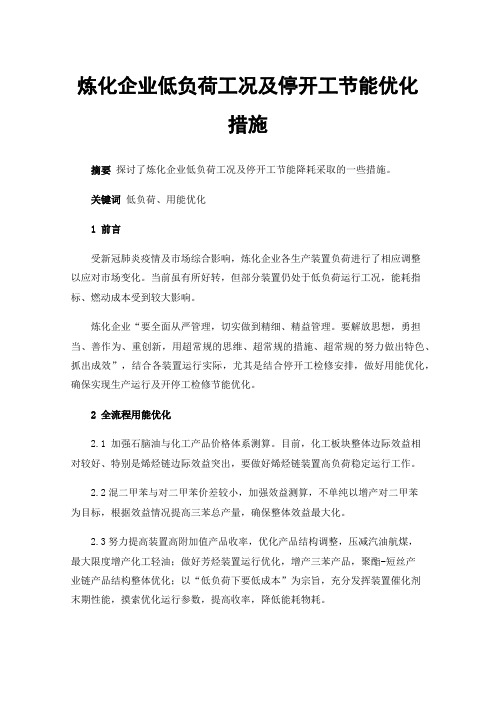
炼化企业低负荷工况及停开工节能优化措施摘要探讨了炼化企业低负荷工况及停开工节能降耗采取的一些措施。
关键词低负荷、用能优化1前言受新冠肺炎疫情及市场综合影响,炼化企业各生产装置负荷进行了相应调整以应对市场变化。
当前虽有所好转,但部分装置仍处于低负荷运行工况,能耗指标、燃动成本受到较大影响。
炼化企业“要全面从严管理,切实做到精细、精益管理。
要解放思想,勇担当、善作为、重创新,用超常规的思维、超常规的措施、超常规的努力做出特色、抓出成效”,结合各装置运行实际,尤其是结合停开工检修安排,做好用能优化,确保实现生产运行及开停工检修节能优化。
2全流程用能优化2.1 加强石脑油与化工产品价格体系测算。
目前,化工板块整体边际效益相对较好、特别是烯烃链边际效益突出,要做好烯烃链装置高负荷稳定运行工作。
2.2混二甲苯与对二甲苯价差较小,加强效益测算,不单纯以增产对二甲苯为目标,根据效益情况提高三苯总产量,确保整体效益最大化。
2.3努力提高装置高附加值产品收率,优化产品结构调整,压减汽油航煤,最大限度增产化工轻油;做好芳烃装置运行优化,增产三苯产品,聚酯-短丝产业链产品结构整体优化;以“低负荷下要低成本”为宗旨,充分发挥装置催化剂末期性能,摸索优化运行参数,提高收率,降低能耗物耗。
2.4把握好生产节奏,根据石脑油进厂资源情况做好整体生产安排,在保证化工板块装置高负荷运行的基础上及时做好船燃出厂及成品油备货等工作。
3公用工程用能优化3.1热电部降低制粉单耗到30千瓦时/吨,降低一二电站给水泵单耗,提升消白系统循环水量及用电能耗指标,合理安排增压泵运行效率;锅炉车间在运锅炉,通过调整提升锅炉效率;一二电站给水温度同比提升2度;严格执行煤炭烧旧存新,降低煤炭入厂入炉热值差;依据煤炭、石油焦价格情况,最大限度调整CFB锅炉石油焦、煤炭比例,降低燃料成本。
3.2水务部优化压力泵站运行,合理安排非汛期启动泵;水处理五车间2#循环水整体优化;大修期间,水源间歇运行方式,供水泵站根据前方用水量随时变化机组运行方式。
镇海炼化:集智创新破解节能降耗密码

3月份,镇海炼化1号乙烯装置应用理论配比燃烧优化技术,通过控制系统优化燃烧和空气的配比,达到理论值,使得裂解炉能以最小的燃料消耗满足工艺要求。
据测算,单台裂解炉每年可节省燃料气300吨。
这是镇海炼化“东海炉王”技术团队攻关的又一成果。
自2010年乙烯装置开工后,技术团队就开始了节能降耗攻关,十年如一日,从未停止。
他们结合实际工况,通过创新技术应用、设备节能改造、优化能源利用等措施,装置吨乙烯综合能耗逐年下降。
2021年,镇海炼化1号乙烯装置吨乙烯综合能耗比2011年下降了11.5%,创投产11年以来最好成绩,在工业和信息化部组织的遴选中,连续第三年获得全国乙烯行业能效领跑者称号。
本刊记者 卞江岐 通讯员 徐 欣镇海炼化:集智创新破解节能降耗密码关注292022 / 07 中国石化团队攻关破解技术密码裂解炉运行一段时间后,炉管内会结焦,要保证长周期稳定运行,必须进行烧焦操作。
一般单台裂解炉所需烧焦时长接近两天,而1号裂解炉日前烧焦操作只用了24小时就完成了,这得益于镇海炼化“东海炉王”技术团队2021年的创新成果。
炉管上的结焦绝大部分都是碳,烧焦简单的说,就是碳和氧气反应成为二氧化碳,烧焦太快会造成焦块脱落,像“血栓”一样堵塞炉管,不但影响烧焦进程甚至影响裂解炉的长周期运行。
怎么能够做到既快又安全呢?技术团队从2017年开始攻关,他们和北化院合作进行了快速烧焦的试验,积累了部分数据。
此后4年,每次烧焦时,技术团队都加大数据监测的力度。
大数据成为创新攻关的基础,他们在软件上模拟烧焦进程,不断调整优化,形成了新的烧焦技术方案。
新方案实现了烧焦过程提速。
数据统计显示,实施一次快速烧焦,可以节省燃料气34.5吨、中压蒸汽600吨,可节能83.4吨标油。
多年来,围绕节能降耗的目标,技术团队应用新技术,自主创新技术的步伐不曾停歇。
“只要有优化空间就不放过,现在‘西瓜’都捡得差不多了,‘芝麻’我们也要。
”烯烃一部技术组组长陆向东说。
宁波市环保局关于中国石油化工股份有限公司镇海炼化分公司Ⅱ加氢装置扩能改造环境影响报告书的批复-

宁波市环保局关于中国石油化工股份有限公司镇海炼化分公司Ⅱ加氢装置扩能改造环境影响报告书的批复正文:---------------------------------------------------------------------------------------------------------------------------------------------------- 宁波市环保局关于中国石油化工股份有限公司镇海炼化分公司Ⅱ加氢装置扩能改造环境影响报告书的批复中石化镇海炼化分公司:你公司报送的《关于报批中国石化镇海炼化150万吨/年催化汽油吸附脱硫装置等三个项目环境影响报告书(表)的请示》及随文报送的《中国石油化工股份有限公司镇海炼化分公司Ⅱ加氢装置扩能改造环境影响报告书(报批稿)》、镇海区环保局初审意见(镇环许[2009]36号)收悉。
我局经研究,现批复如下:一、根据环境影响报告书结论、报告书专家评审意见、镇海区环保局初审意见,同意镇海炼化Ⅱ加氢装置扩能改造项目于镇海炼化厂区内建设。
该项目环境影响报告书经批复后,可以作为本项目建设和日常运行管理的环境保护依据。
二、本项目在镇海炼化原有Ⅱ加氢装置界区内将原有的柴油加氢改造成非芳汽油与焦化汽油混合加氢,增加一套加氢反应器,使装置加工能力从80万吨/年提高到120万吨/年,产品由精制柴油变更为精制石脑油,用作乙烯装置原料。
三、项目建设和运行管理中应重点做好以下工作:(一)本项目建设应在采用先进生产工艺和技术设备的同时,积极贯彻清洁生产理念,努力探索从源头上减少污染物的排放和降低能耗的运行管理方法,实现项目建设社会效益、环境效益、经济效益的协调发展。
(二)本项目加热炉燃料油含硫率控制在0.5%以下,燃料气含硫量控制在100ppm以下,确保加热炉烟气达到《工业炉窑大气污染物排放标准》(GB9078-1996)二级标准后方可经40米高排气筒排放至大气。
镇海炼化低碳生产实践与探讨

P oche设 lEqui m ent32・ 石r化 m i备 术212)ogy・ 油 工 ca ,1Technol 3 技 p 0 ,( 3 e t
镇 海 炼 化 低 碳 生产 实 践 与 探 讨
江 正 洪
( 国 石 油 化 工 股 份 有 限 公 司 镇 海 炼 化 分 公 司 , 江省 宁 波 市 3 5 0 ) 中 浙 1 2 7
国、 日本等 发达 国家及地 区 的汽 油 、 柴油 质量都 已
达 到硫 含 量 1 g g以 下 的 超 低 硫 标 准 , 我 国 0 / 而
镇海炼 化 1 0 ta乙烯裂 解装置 已于 2 1 0 0k/ 00
年 4月 底 正 式 投 产 。 乙 烯 裂 解 装 置 在 生 产 乙 烯 、
性 指 标 纳 人 国 民 经 济 和 社 会 发 展 的 中 长 期 规 划 的
C 减排 承诺 , 随着 油 品质 量 升级 要 求 越来 越 0 且
严 格 以及 节 能 工 作 难 度 的 加 大 , 司 的 低 碳 生 产 公 将 面临着 严峻挑 战 。 2 1 油 品 质 量 升 级 要 求 越 来 越 严 .
热 电联 产 是热 能和 电能联 合 生产 的一种 高效
能 源 生 产 方 式 。 以燃 煤 方 式 的 热 电 联 产 和 热 电 分 产 进 行 比 较 , 产 出 同样 数 量 的 热 力 和 电 力 , 电 为 热
联产 方 式 比热 电 分 产 可 以节 约 1 3左 右 的燃 煤 / ( 仅从 热 源 角 度 进 行 比较 , 比较 二 者 的 热 网损 未
些减 排措 施 和建议 。
收 稿 日期 : o O 1 一 9 2 1 1O 。 作 者 简 介 : 正 洪 , 任 中 国 石 油 化 工 股 份 有 限 公 司 镇 海 炼 江 现
柴油加氢改质装置节能降耗技术分析与对策

柴油加氢改质装置节能降耗技术分析与对策柴油加氢改质装置是一种能够提高柴油质量并且降低排放的技术装置,它通过将柴油加氢处理,改善了其性能,提高了燃烧效率,达到了节能降耗的效果。
本文将对柴油加氢改质装置的技术原理进行分析,并提出对策,以期为相关领域的研究和实践提供一定的参考价值。
一、柴油加氢改质装置的技术原理分析1.1 加氢改质技术原理柴油加氢改质技术是利用催化剂将柴油中的芳香烃和不饱和烃转化成饱和烃的一种技术。
将芳香烃和不饱和烃加氢处理,生成饱和烃。
然后,饱和烃能够提高柴油的燃烧性能,降低其燃烧排放,达到节能降耗的目的。
加氢催化剂是柴油加氢改质装置中的关键部件,它能够促进柴油中的反应,提高反应速率和选择性。
常用的加氢催化剂有钼镍系和钼铜镍系,它们具有较高的活性和稳定性,能够在高温、高压等恶劣条件下工作,具有较好的加氢改质效果。
1.3 柴油加氢改质装置对节能降耗的影响柴油加氢改质装置可提高柴油的燃烧效率,减少燃烧废气排放,节约能源,降低环境污染。
改善了柴油的性能,还能够降低发动机的磨损、延长使用寿命,从而减少维护成本,达到节能降耗的效果。
2.1 完善催化剂加氢技术针对柴油加氢改质装置中催化剂的研发,应该不断完善加氢催化剂的配方和制备工艺,提高催化剂的活性和稳定性。
还需要加强催化剂的再生技术研究,延长催化剂的使用寿命,降低成本,提高整体性能。
2.2 改进加氢设备技术在柴油加氢改质装置中,加氢设备也是非常重要的一部分。
为了提高加氢设备的效率,可以采用先进的工艺装备和控制手段,优化加氢反应条件,提高反应速率和选择性,从而提高整体加氢改质效果。
2.3 推动技术装备的集成应用随着智能制造技术的不断发展,柴油加氢改质装置的技术装备也在不断更新。
为了实现更好的节能降耗效果,可以推动技术装备的集成应用,形成系统化的柴油加氢改质装置,提高整体效率和性能。
2.4 多方合作促进技术创新柴油加氢改质装置的节能降耗技术需要不断提升,除了企业自身的技术研发,还需要各方合作,共同促进技术创新。
加氢裂化装置的能耗与节能措施

加氢裂化装置的能耗与节能措施摘要:加氢裂化装置是炼油企业的重要装置,对企业的能耗和经济效益影响重大。
加氢裂化是在高温高压和催化剂存在的条件下,原料油与氢气充分接触而发生加氢,裂化和异构化反应,转化为轻质油的加工过程,生产过程中能量消耗巨大,对其进行节能研究具有重要的意义。
本文着重分析了影响加氢裂化装置能耗的因素,并提出了相应的节能措施。
关键词:加氢裂化装置;能耗分析;节能措施前言加氢裂化工艺因总输人能量多,能耗较高,装置能耗及产品的收率受操作条件影响。
其工艺用能主要有以下特点:进料和氢气的升温、升压均需要供人大量能量,循环氢压缩机一般由1.0MPa蒸汽驱动,能耗较高;装置低温余热多,高能级的热量输人加氢裂化装置后,通过一系列的化学和物理过程,大部分转化成低温热;加氢过程为强放热反应,可供回收利用的热量多。
1加氢裂化装置工艺简介加氢技术最早起源于上世纪二十年代,二战之后,加氢裂化技术才迅速发展起来。
加氢裂化及中压加氢改质技术的开发和应用则是在上世纪九十年代后。
目前,我国加氢裂化装置种类较多,按照操作压力,可以分为高压加氢裂化和中压加氢裂化;按工艺流程,可以分为一段加氢裂化流程、二段加氢裂化流程、三段加氢裂化流程。
加氢裂化装置的主要组成部分有:加热炉及反应器区、高压分离器及高压空冷区、加氢压缩机厂房、分馏塔等,其应用的过程中具有一定的危险性,因此做好防范措施是非常必要的。
具体的做法是:(1)加氢反应系统干燥、烘炉。
此种做法的目的是清除加氢反应系统内的水分,脱除加热炉耐火材料中的自然睡和结晶水,如此可以避免加热炉加热过程中,燃料气受到影响,增加加氢裂化能生产的危险性。
(2)加氢反应器催化剂填装。
催化剂填装的好坏直接影响加氢裂化装置的运行情况。
为了提高加氢裂化装置应用的安全性,催化剂填装需要在干燥晴朗的气候条件下进行,均匀填装。
(3)加氢反应系统气密。
加氢反应系统气密工作的落实是分为不同压力等级进行的。
6-镇海炼化-构建内部循环经济模式,实现炼化企业节能减排

环境成就
1993年获 “全国工业污染防治十佳企业” 称号 年获 全国工业污染防治十佳企业” 2003年获“浙江省绿色企业”称号 年获“浙江省绿色企业” 年获 2004年被命名为 “ 中国石化首批清洁生产示范企 2004 年被命名为“ 年被命名为 业” 2004年成为首批“国家环境友好企业” 2004年成为首批“国家环境友好企业”之一 年成为首批 2006年获“浙江省环境教育示范基地” 2006年获“浙江省环境教育示范基地”称号 年获 2007年 月获“中华宝钢环境优秀奖” 2007年7月获“中华宝钢环境优秀奖”称号
炼化企业既为社会提供能源产品, 炼化企业既为社会提供能源产品,同时也是能源资 源消耗大户和环境污染源。坚决贯彻落实科学发展观, 源消耗大户和环境污染源。坚决贯彻落实科学发展观, 承担起节能减排的主体责任,依靠企业内涵发展, 承担起节能减排的主体责任,依靠企业内涵发展,集约 发展,清洁发展,实现自我提升,为实现国家“十一五” 发展,清洁发展,实现自我提升,为实现国家“十一五” 节能减排目标做出贡献,是炼化企业的必然选择。 节能减排目标做出贡献,是炼化企业的必然选择。
构建内部循环经济模式 实现炼化企业节能减排
镇海炼化概况
万吨/年原油综合加工能力 万吨/年以上尿 ●2000万吨 年原油综合加工能力、 60万吨 年以上尿 万吨 年原油综合加工能力、 万吨 素生产能力及100万吨 年芳烃 、 20万吨 年聚丙烯生 万吨/年芳烃 万吨/年聚丙烯生 素生产能力及 万吨 年芳烃、 万吨 产能力; 万吨/年吞吐能力的深水海运码头 产能力 ; 4500万吨 年吞吐能力的深水海运码头 , 以 万吨 年吞吐能力的深水海运码头, 及超过280万立方米的储存能力。 万立方米的储存能力。 及超过 万立方米的储存能力 截止2007年 6月 , 公司总资产 亿元, ● 截止 年 月 公司总资产187.84亿元 , 其中净 亿元 资产164.71亿元 , 资产负债率为 亿元, 资产 亿元 资产负债率为12. 31%。 2005年以 。 年以 来连续三年位居“浙江省百强企业”第一位。 来连续三年位居“浙江省百强企业”第一位。
镇海炼化2016年装置开停工用能优化经验交流汇报

谢
谢
Ⅲ焦化装置开停工节能优化情况
Ⅲ焦化装置本次为新装置投产以来的 第一次大修,开工能耗为287吨标油,停 工能耗为114吨标油,较开、停工能耗指 标分别减少了63吨、86标油,均低于Ⅰ、 Ⅱ焦化以往的开停工能耗。 主要节能措施:停工时先用蜡油循环 置换重油系统,蜡油置换完后再用柴油置 换蜡油,有效地降低了吹扫难度,并减少 了停工蒸汽消耗。
Ⅰ常减压装置开停工节能优化情况
Ⅰ常减压装置本周期停工能耗为237 吨标油,较本次停工用能计划减少13吨标 油,比上个周期用能低24吨标油。 • 主要原因:1.0MPa蒸汽消耗量较上周 期下降了24.32吨标油。 • 主要节能措施:本次停工吹扫前首次 采用了柴油清洗方案,柴油清洗后降低了 管线吹扫难度,减少了1.0MPa蒸汽消耗 量。
Ⅰ常减压装置开停工节能优化情况
Ⅰ常减压装置开工用能情况:装置本 周期开工实际用能299吨标油,虽较上个 周期有所增加,但主要是受其它装置开工 推迟影响造成的,使得本次开工在150℃ 恒温脱水阶段较上周期多了一天。此外, 在开工过程中增加了柴油置换水分的步骤 ,也使开工能耗有所增加,但柴油置换水 分后,管道内的水分大大减少,有利于机 泵的开工运行,对设备也有利。
Ⅱ催化装置开停工节能优化情况
如:分馏侧线吹扫顺序为回炼油、一 中、顶循,很好地降低了用汽峰值,总用 汽量稳定控制在65t/h左右,既避免了对公 司管网的冲击,同时也降低了停工能耗; 气分单元根据介质特点及以往停工吹扫经 验,缩短了本次放空吹扫时间,由上周期 的放空吹扫24小时缩短到了12小时。 本次Ⅱ催化停工,实际处理时间只有 44小时,较上周期节省了22小时,减少 1.0MPa蒸汽消耗15吨标油。
Ⅱ催化装置开停工节能优化情况
Ⅱ催化装置本周期停工能耗为1013吨 标油,较本次停工用能计划减少了37吨标 油。装置在切断进料后,如果原料油、分 馏塔各侧线都开始往分馏塔吹扫,容易造 成分馏塔液位高,且蒸汽耗量较大。本次 对分馏塔系统制定了较完善的吹扫用汽方 案,使得在确保各条管线吹扫干净的情况 下,基本做到了错时、有序、适量用汽, 也减少了蒸汽的消耗。
加氢装置节能降耗措施
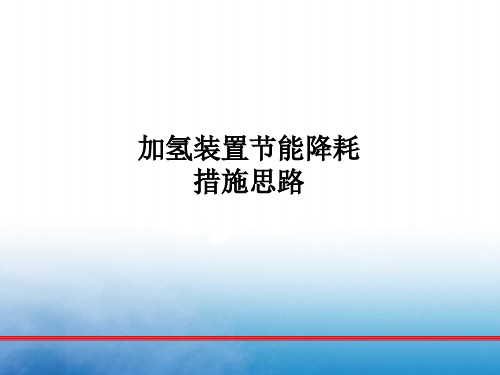
12 降低高压系统压力降
反应高压系统压力降大幅下降,相同进料条件下循环氢压缩机转数大幅
下降。
为降低反应高压系统压力降, 采取了如下
措施: (1)反应系统加注阻垢剂, 防止高压换 热器结垢; (2)加强反应温度监控, 尤其是新催化 剂投用初期,防止反应器飞温导致催化剂 结焦和高压换热器结焦; (3)加强原料性质监控,严格控制减压 蜡油的干点及残炭值,防止精制反应器顶 部压力降急剧增大; (4)匹配裂化催化剂的温度分布,在保 证质量合格及收率最大的基础上降低反应 温度。
(2)循环氢脱硫塔的富胺液通过减压后去富胺液闪蒸罐, 也可以采用液力透 平来回收能量, 辅助驱动高压贫胺液泵。
6 机泵的叶轮切割
切割叶轮的计算依据离心泵叶轮的切割公式:
7 使用变频调速技术
采用变频调速或调节技术是节能的有效途径。一般来说,在电动机实际负 荷低于设计值70%而且额定功率大于10kW时,采用变频调节器有较好的经济效 益。
14 分馏塔进料闪蒸罐压力优化
分馏塔进料闪蒸罐 V208 的操作压力对瓦斯消耗有一定影响。为了考察 V208 降压对分馏炉瓦斯消耗的影响,在确保反应总进料 、反应深度恒定和 V208 入口温度不变的前提下,通过试验逐步降低 V208 操作压力。V208 压力 降至 0.15MPa 后,分馏炉的瓦斯消耗量从2350 m3/h下降到1800 m3/h,分馏 加热炉减少瓦斯消耗 550 m3/h。其主要原因在于分馏进料经过闪蒸罐降压后, 进料中的轻组分最大限度的闪蒸,减少分馏炉进料的流量,在加热炉进出口温 度基本不变的情况下,大大降低了分馏炉的瓦斯消耗。
加氢装置节能降耗 措施思路
1 气封罐顶压力的设计
气封罐顶的压控阀不采取50%时全关的控制方式, 而是采用如图所示方 式。在压控阀PID信号0-45%变化过程中,放火炬B阀慢慢关闭;在压控阀PID 信号45%-55%变化过程中,补气A阀和放火炬B阀全部关闭;在压控阀PID信号 55%-100%变化过程中,补气A阀慢慢打开。这种控制方式避免了罐顶压控阀门 的频繁开关。通过调整PID信号,装置在操作时需要注意使罐的液位和压力稳 定,减少波动开关的次数,大大降低了去火炬系统的排放气量。
镇海炼化:创新实践节能管理_能效水平持续领跑

afety & E nvironment安全环保652023 / 11 中国石化耗,达到了节能目的。
在落实传统节能技术的同时,广州石化积极推进新技术应用,落实绿电示范工程项目,2023年外购电合同中20%为绿电,可再生能源使用比例同比提升,碳排放有效降低。
“在新起点持续推进节能降碳提质增效,推动绿色高质量发展,是广州石化的首要任务、重中之重。
”广州石化分公司代表、党委书记田宏斌表示。
(作者单位:广州石化分公司)镇海炼化:创新实践节能管理 能效水平持续领跑□ 本刊记者 卞江岐 通讯员 徐 欣 周进进中国石油和化学工业联合会日前授予镇海炼化“2022年度能效领跑者标杆企业(乙烯)”称号,这是镇海炼化连续第11次获此荣誉。
镇海炼化充分发挥原料优势、区域优势、炼化一体化优势,对标世界一流,以“资源利用循环化、能源利用高效化”为目标,通过创新实践节能管理,推进节能技术改造,推广应用节能新技术,1号乙烯装置综合能耗投产13年来逐年下降,能效水平持续领跑行业。
创新实践节能管理随着镇海炼化1号乙烯装置3台裂解炉日前陆续投用二级空气预热器,空气温度由60摄氏度预热到85摄氏度,每台每小时节约燃料气130标准立方米,3台裂解炉每年可节能1876吨标煤。
在裂解炉投用二级空气预热器是镇海炼化今年的能效提升计划项目之一,能效提升计划项目按照项目管理法“定目标、定措施、定节点、定责任”,建立跟踪、监督、考核机制,推进公司能源标准化管理。
镇海炼化持续强化能源智慧系统建设,以建设智能工厂为目标,以节能降耗为宗旨,建设能源管理信息化系统(SMES),具备能源运行、能源统计、能源优化、能源监控、评价分析等功能,基本实现能源“说得清,管得住,省得下”目标。
2022年,建成装置能耗监控平台,实时监控装置能耗数据及相关重点参数,乙烯裂解装置的蒸汽、燃料气耗量等参数可直观地在平台上显示,便于技术人员和操作人员及时作出判断,调整优化生产。
多方面节能优化降低柴油加氢装置能耗

多方面节能优化降低柴油加氢装置能耗摘要:随着我国柴油加氢装置的应用规模不断扩大,市场竞争压力持续增加,借助于柴油加氢装置能耗控制策略来解决能耗问题逐渐成为企业获得良好竞争力,立足于市场的重要环节。
柴油加氢装置采取节能设计理念实施科学设计,能够有效提升装置的经济效益,同时保持企业良好的企业竞争力。
从节能环保的角度出发,对柴油加氢精制装置实施技术改造,也能够确保整体目标的高效实现,本文结合实际生产情况,对柴油加氢装置的能耗结构现状进行分析。
关键词:节能优化;柴油加氢装置;降低能耗1柴油加氢装置主要节能措施1.1缓冲罐处理根据柴油加氢装置能耗的分析结构我们可以看出,整体热能回流以及超负荷因素是能耗控制的关键。
在针对缓冲罐进行处理时,要考虑到大规模结垢的问题,一旦出现上述情况,会导致停机维护,严重影响生产效率与衔接性。
具体来说,可以通过添加阻垢剂的方式来化解,借助于阻垢剂的基本原理来确保整体处理效果,避免节能成本较高也是该处理环节需要特别注意的问题。
1.2结构优化对柴油加氢装置的结构实施优化,主要包括有加热反应炉的结构以及整体工作效率,以降低热平衡时的热量负荷为设计要求和基本条件。
结构优化过程中可以添加专用平衡压缩设备,该类型的设备效率较高、运行的能耗较低,能够适应能耗管理要求。
1.3工艺改善对工艺实施改造是柴油加氢装置能耗控制的关键途径,涉及到的多个工艺都是与热能相关的部分,降低操作压力,提升系统的稳定性有助于工艺的改善。
1.4材料升级对原材料进行升级,降低腐蚀元素的影响,延长设备的使用寿命等,都有助于企业节约成本,进而实现能耗控制的基本要求。
2柴油加氢装置流程的选择2.1重沸炉计划流程柴油加氢装置加工的主要原料为直馏柴油,因其反应热少,所以需要在分馏部分加装加热炉或是重沸炉来满足供热需求,在分馏塔底进料方案中,分馏塔底部进料使用加热炉需要进行低压蒸汽汽提,在汽提过程中会导致油中有水,因此又必须添加除水装置进行除水;而分馏塔底使用重沸炉,则不要再增加脱水装置,从经济性来说,虽然重沸炉的负荷大一些,但更有利于减少装置污水排放。
镇海炼化开展炼化一体化工作的实践与探索 ppt课件

13万吨/年,作为汽油调和组分,顶出调入汽油中的碳五、非芳 等石脑油组分,作为乙烯装置原料。
镇海炼化分公司
措施8:优化公用工程
充分利用价格相对较低的煤炭和石油焦资源,通过自 建的CFB锅炉进行热电联产。 蒸汽系统按能级匹配和热能梯级进行优化利用。 开展原水用量优化、循环水量优化,进一步提高污水回 用率和循环水浓缩倍数,减少新鲜水用量和外排污水量。
镇海炼化分公司
镇海炼化乙烯开工及运行情况
2010年4 月20日 一次开 车成功 。
7月份 当月就 实现了 盈利。
8月份 勇夺化工 利润第一 ,装置负 荷达到 100%。
2011~2012年
2011年装置投产后 第一个完整年, 乙烯产量达到 110.8万吨,乙烯 能耗553千克标油/ 吨;2012年预计产 量110.6万吨,乙 烯能耗541千克标 油/吨。
镇海炼化2012年预计加工原油2020万吨,生产乙烯110.6 万吨。全年炼油能耗45.8千克标油/吨,乙烯综合能耗 541千克标油/吨。2012年预计完成利润30亿元。
附:镇海炼化炼油总流程示意图
镇海炼化分公司
镇海炼化炼油总流程示意图
煤油
柴油
算山码头 原油 常 减 压 蜡油
渣油
煤油精制
汽柴油精制
27.40
PP
25.49
丁二烯 14.25
甲苯
16.30
混合二甲苯 8.24
抽余油
9.30
C5
13.12
C9+
5.54
PFO
7.06
PGO
5.00
镇海炼化分公司
镇海炼化乙烯设计原料组成:
原料名称
工况一
工况二
中国石油化工股份有限公司镇海炼化分公司150万吨年加氢裂化生产运行总结(第一周期)
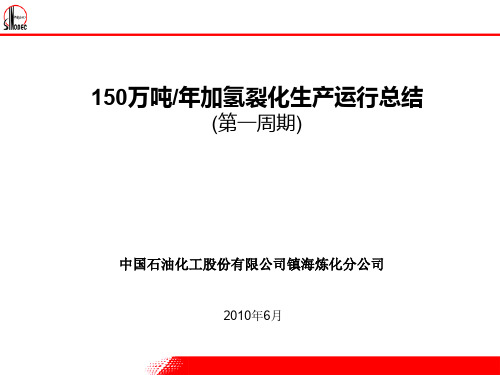
25141.2 1.63
80715.6 5.22
重石 507956.4 32.88
2007年
吨
%
983769 96.66
33952 3.34
32553 3.20
7243 0.71
28603 2.81
54291 5.33
255270 25.08
2008年
吨
%
1324237 96.54
47489 3.46
设计值
178.6 13.5 348/392 374/392 1.1 377/386 377/387 377/388 377/390 2.4 72/43 378/382 <20 283
75
4月21日8:00
4月22日8:00
178 13.51 358.3/398.5 369.8/387.3
1.1 366.9/369.0 367.6/372.6 368.1/374.5 368.5/371.2
0.6 2.18
实际能耗 kgEO/t 0.45 0.18 -0.3 15.01 5.94 4.39 3.4 11.75
0.71
45.39
41.54
中国石化镇海炼化分公司
• 产品质量 • 重石脑油硫、氮含量均小于1mg/kg,芳潜51,是优质重
整原料。
• 航煤芳烃含量12%左右,烟点在23mm左右,与设计偏差 较大,其它指标均合格,是优质民用航煤。
图1
循 环 氢 脱 硫
V1002
干气
分馏塔
液化气 轻石 重石 航煤
柴油
尾油
中国石化镇海炼化分公司
几个亮点:
• 裂化催化剂高空速2.4 • 缠绕管式换热器在加氢裂化装置首次使用 • 原料油过滤器RPA-Ⅴ型,简单高效 • 循环氢脱硫设置旋流器,避免胺液发泡
- 1、下载文档前请自行甄别文档内容的完整性,平台不提供额外的编辑、内容补充、找答案等附加服务。
- 2、"仅部分预览"的文档,不可在线预览部分如存在完整性等问题,可反馈申请退款(可完整预览的文档不适用该条件!)。
- 3、如文档侵犯您的权益,请联系客服反馈,我们会尽快为您处理(人工客服工作时间:9:00-18:30)。
Ⅱ加氢装置加氢精制综合能耗现状及对策措施
吴旭波
(中国石化镇海炼化分公司浙江宁波 315207)
摘要:2007年11月Ⅱ加氢精制改造为30万吨/年焦化汽油与50万吨/年直馏煤油混合加氢,装置投产以来,装置综合能耗与国内同类装置能耗进行对比、分析,查找存在的问题,结合2010
年3月装置扩能改造的机会,制定相应降耗措施,通过优化操作工况,使装置综合能耗大幅下降,
8月份综合能耗5.035kgEO/t,创国内同类装置最好成绩。
关键词:加氢精制措施综合能耗国内同类装置
1 扩能改造前装置能耗状况
2007年11月Ⅱ加氢精制改造为30万吨/年焦化汽油与50万吨/年直馏煤油混合加氢,同年12
月根据公司安排,装置处理焦化汽油和直馏柴油混合加氢。
Ⅱ加氢装置投产后,平衡了因延
迟焦化装置扩能后公司焦化汽油资源较高的压力,但在装置运行过程中暴露装置能耗较高的
问题,2008年1月至2010年1月装置能耗平均值11.272kgEO/t。
1.1 Ⅱ加氢精制装置综合能耗构成
Ⅱ加氢精制装置综合能耗由新鲜水、循环水、软化水、电、蒸汽、循环水、燃料气物料
构成。
2008年1月至2010年1月装置综合能耗平均值11.272kgEO/t,其中新鲜水、循环水、软化
水总共占7.64%,电、蒸汽、燃料气三项能耗总共占了92.36%。
1.2 与国内同类装置能耗对比
表1是2009年度本装置与中国石化系统内同类装置综合能耗最低的广州分公司(Ⅱ)的各
单耗对比,装置各单项能耗都高于广州分公司(Ⅱ),主要集中在电、蒸汽、燃料气三项能耗,
如何降低电、蒸汽、燃料气单耗,作为降低装置综合能耗着力点。
表1 2009年镇海炼化(Ⅱ)和广州分公司(Ⅱ)装置综合能耗对比(单位:kgEO/t)
新鲜水循环水软化水电 1.0MPa蒸汽 3.5MPa蒸汽燃料气综合能耗
镇海炼化(Ⅱ) 0 0.844 0.046 2.5142-7.6 9.68 5.111 10.595 广州分公司(Ⅱ) 0 0 0
5.7749
3.8350.5244 1.4155
2 存在问题
(1)富气脱硫塔操作压力过低
目前装置贫液(二乙醇胺)由加氢裂化装置提供,但其贫液泵出口压力只有0.7MPa,导
致富气脱硫塔操作压力不能大于0.5MPa,否则贫液不能进富气脱硫塔。
因富气脱硫塔操作压
力过低,脱后富气不能通过自压方式并入高瓦系统(0.5~0.6MPa)。
(2)汽提塔操作压力过低
4月份装置改造投产以来,汽提塔底精制石脑油带水十分严重,约1%~3%,精制石脑油
带水对乙烯安全生产存在一大风险。
精制石脑油产品带水现象严重,带水原因有几点:原先
双塔汽提改为单塔蒸汽汽提,汽提塔底精制石脑油产品带水;开工以来受焦化汽油库存较低影响,装置负荷较低,汽提塔进料温度低于设计温度50℃。
通过降低汽提塔操作压力,减少精制石脑油水含量。
(3)反应系统压降上升
从图1可以看出,反应生成油进高压换热器E202CD入口温度178℃,V243热高分气进E204换热器入口温度153℃,在此操作条件下,E202CD和E244处铵盐结晶严重,E202CD压差和E244压差均为0.2MPa。
反应系统压降上升,导致循环氢出口压力相应上升,3.5MPa蒸汽消耗增加。
图1 反应生成油流程
(4)反应热富裕
装置改造后,焦化汽油产量比例大幅增加,不饱和烃加氢反应释放大量热量,反应加热炉负荷较小。
一方面反应热不能充分吸收,增加了水耗、电耗,另一方面却在维持反应加热炉低负荷运行。
3 对策措施
3.1 节燃料气措施
Ⅱ加氢装置扩能改造后,处理以焦化汽油和非芳原料为主进行混合加氢,因焦化汽油不饱和烃含量较高,其溴价在80gBr/100g左右,不饱和烃加氢饱和后产生巨大反应热,充分考虑到反应热的充分利用,增加反应加热炉跨线和气动阀,加热炉只作为开工炉,装置正常生产后停用加热炉,燃料气可下降300Nm3/h,年节能2268吨标油。
3.2 节汽措施
(1)汽提塔改用氢气代替蒸汽汽提
借鉴广州分公司将氢气用于航煤加氢装置汽提的成功经验,在本装置试用氢气汽提。
引一氢气管线(DN20)至汽提塔,作为氢气汽提线(见图2)。
通过用150~200Nm3/h氢气汽提替代蒸汽汽提,使装置精制石脑油水含量在20mg/kg左右。
通过汽提方式的改变,确保了精制石脑油品质的提高,同时用于汽提的1.3t/h1.0MPa蒸汽停用,年可节能829.92吨标油。
(2)降低循环氢压缩机汽轮机3.5MPa 蒸汽流量
停运F201后,反应原料改走F201跨线,系统压降减少0.4MPa 左右,C202出口压力相应减少,压缩机出口反飞动线阀门全部关闭,3.5MPa 蒸汽下降约0.86t/h 。
将反应注水点进行调整,从原先的高压空冷注水点移至E244,热高分压力从原先3.83MPa 降至目前的3.67MPa ,循环氢压缩机出口压力相应降低,3.5MPa 蒸汽下降0.3t/h 。
通过调整、优化,3.5MPa 蒸汽下降明显,年节能777.92吨标油。
3.3 节电措施
(1)停运螺杆机C204
Ⅱ加氢装置进行扩能改造后,脱后富气经螺杆机C204增压后,并入高瓦系统(见图3)。
2010年4月份T202富气脱硫系统生产工况受加氢裂化装置来贫液压力低影响,脱后干气直接并入高瓦系统(不进行增压)存在难度。
采用原先富气去加氢裂化脱硫流程和对相关设备进行扩径等措施,使富气脱硫后并入加氢裂化瓦斯系统(由于V208富气压力0.5MPa ,高于加氢裂化瓦斯系统,两者存在0.1MPa 左右的压差),在不开C204的情况下,解决了脱后富气后路问题。
利用加氢裂化2010年6月份停工检修的机会,供加氢贫液由原先的加氢裂化低压泵改由高压泵提供,使Ⅱ加氢装置贫液压力提高至1.5MPa ,实现将T201操作压力提至0.65MPa ,成功将脱后富气并入高瓦系统。
通过上述流程优化、操作优化,实现了C204停运,C204轴功率160kWh ,年节能349.44吨标油。
图2 汽提塔氢气汽提流程
图3 富气脱硫流程
(2)停运石脑油泵
II 加氢装置进行扩能改造后,汽提塔底石脑油经石脑油泵增压后出装置。
提高汽提塔T201操作压力至0.65MPa ,加上自身液位差0.05MPa ,T201底石脑油压力0.7MPa ,在不开石脑油泵的情况下,通过自压的方式直接出装置。
石脑油泵停运后,冲洗油冷却器软化水、端面冷却水停用。
P209轴功率151kWh ,年节能339.344吨标油,同时装置软化水减少4t/h 左右。
(3)停新氢压缩机操作
由于Ⅱ加氢装置属于低压加氢,系统压力3.5MPa ,充分利用氢气系统管网,引高压力的化肥氢作为新氢,因其压力在6.0MPa 以上,无须再通过新氢压缩机进行增压。
C201轴功率427kWh ,每台新氢机年节能959.61吨标油,同时新氢压缩机停用后,级间冷却器循环水用水、润滑油泵电耗等无消耗。
4 节能效果及今后的节能打算
4.1 节能效果
通过装置优化调整,2010年使Ⅱ加氢装置装置能耗下降明显,且能耗呈逐月下降趋势(见图4),其中10月份能耗5.03kgEO/t 。
4.2 今后的节能打算
(1)循环氢抽真空冷凝水目前直接就地排放,排量约1t/h 左右,考虑将其作为装置软化水,因软化水罐为常压,所以可直接配管至软化水罐。
(2)尽可能提高装置负荷,降低装置能耗。
(3)Ⅱ非芳加氢改为一次通过后,Ⅱ加氢装置可停运非芳原料泵P204,进一步节能。
(4)进一步对高换各混氢点进行调整、摸索,降低系统阻力。
目前装置反应热较高,下一周期停工检修时,对换热流程进行优化,使反应热得到进一步充分利用。
(5)待精制石脑油脱水设施完善后,部分反应注水移至E202CD 入口,溶解E202CD 内铵盐,降低E204CD 压差,降低能耗。
图4 Ⅱ加氢装置综合能耗
k g E O /t -。