真空辅助树脂传递模塑工艺
真空辅助树脂传递模塑工艺

真空辅助树脂传递模塑工艺真空辅助树脂传递模塑工艺(VARTM/SCRIMP)适用于质量要求高、小批量和尺寸较大的制品。
它和传统的热压罐成型工艺相比,具有模具低成本,树脂室温固化以及几乎不受限制的制品尺寸等突出的特点。
在国外VAR TM已成功地用于舰船、军事设施、国防工程、航空和民用工业等领域。
目前,真空辅助树脂传递注塑中应用最广泛的工艺之一,SCRIMP TM成型工艺,是在19世纪80年代后期在RTM 工艺基础上发展起来的以低成本、适合制作大型复合材料制品的成型工艺。
该加工工艺的成品有较好的品质,如:孔隙率低、纤维含量高,和良好的机械性能,并且可以将挥发性有毒气体的排放量控制在最小的程度。
SCRIMP真空辅助树脂传递注塑是利用薄膜将增强材料密封于单边模具上,完全借助于真空将低黏度树脂吸入,利用高渗透率介质沿增强材料的表面快速浸渍,并同时向增强材料厚度方向进行浸润的加工工艺。
用这种方法加工的复合材料,纤维含量高,制品力学性能优良,而且产品尺寸不受限制,尤其适合制作大型制品。
最近,由于树脂体系和纺织增强材料成型技术的不断发展,航空制造者们也对VAR TM表现出了浓厚的兴趣,主要表现为采用碳纤维-环氧树脂、碳纤维-双马来酰亚胺树脂的复合材料。
几种常用的纺织复合材料增强体和传统的开模成型工艺相比,SCRIMP成型工艺具有许多的优点。
SCRIMP工艺比手工铺放节约成本约50%,树脂浪费率低于5%,特别是加工过程的环保性,是SCRIM P工艺最突出的优点。
在同样原材料的情况下,与手糊构件相比,复合材料的强度、刚度或硬度及其它的物理特性可提高30%-50%以上。
产品质量不受操作人员影响,产品性能的均匀性和重复性比开模产品好得多,缺陷也少得多。
真空辅助树脂传递模塑成型工艺研究

第14期2020年5月No.14May ,2020作者简介:林涛(1984—),男,江西新余人,硕士;研究方向:风力发电机组叶片制造工艺。
真空辅助树脂传递模塑成型工艺研究江苏科技信息Jiangsu Science &Technology Information林涛,何明,陶生金(国电联合动力技术(连云港)有限公司,江苏连云港222002)摘要:为研究分析风力发电机叶片真空辅助树脂传递模塑成型(VARTM )工艺的影响因素,文章通过采用不同导流网密度、玻纤布型号、玻纤布尺寸、玻纤布铺层厚度研究了其对VARTM 工艺环氧树脂体系导流时间的影响,同时测量对应样品的含胶量,对比分析了VARTM 制品含胶量的影响因素。
关键词:风力发电机叶片;真空辅助树脂传递模塑成型;导流时间;含胶量中图分类号:TB33文献标志码:A 0引言目前应用较广的先进轻质的复合材料,如玻纤/碳纤铺层增强环氧树脂复合材料,因其相对其他材料具有更好的比强度和比模量,较好的抗腐蚀性和疲劳特性,特别是其层铺特性决定了其有非常灵活的材料力学性能设计性。
在风电叶片领域,玻纤/碳纤铺层增强环氧树脂复合材料已经成为叶片设计的主流[1]。
真空辅助树脂传递模塑成型(Vacuum Assisted Resin Transfer Molding ,VARTM )工艺作为一种典型的低成本热固性树脂流体成型工艺已广泛应用于风力发电机组复合材料叶片的制备[2]。
VARTM 工艺具有其他传统工艺无法比拟的优点:它能够用来制造超大型整体复合材料的单一部件,部件整体质量均一,质量控制好,成型时间短,设备要求低,成本低,VOC排放等污染少[3-5]。
叶片制造的大型化和高成型质量、高生产效率要求非常适合采用VARTM 工艺进行生产[6]。
VARTM 工艺的一般实现方式为:首先,在叶片模具上铺设增强材料(包括纤维增强材料玻璃纤维、碳纤维或混编纤维、BALSA 芯材、PVC 或PET 芯材等),其次,铺设布置导流系统和抽气系统,再次用真空袋膜整体封闭再抽真空,最后将液态树脂体系从主导流管路导入,由真空形成的负压动力将流体树脂引入最终到达抽气系统侧,完成树脂对增强材料的完全浸润并固化成型[7]。
RTM技术工艺详解
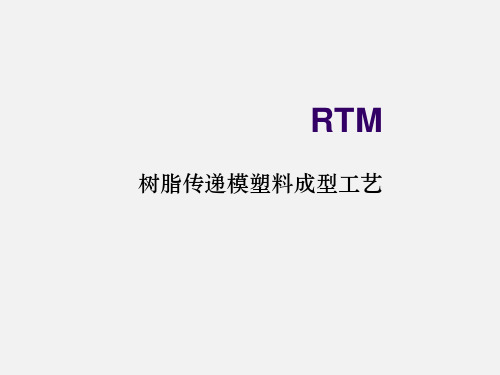
增强材料
由于在RTM成型过程中,增强材料在模具型腔 中要经过带压树脂流动充模过程,会带动或充 散纤维,造成制品出现“冲浪”或“跑道”现 象。因此,为保证制品质量,RTM工艺适用于 采用长纤维和连续纤维织物作为增强材料
工艺因素
影响RTM工艺的因素
VARTM(真空辅助RTM)工艺
一般RTM工艺在树脂注入时,模具型腔内可积起几吨压力。 通过使用了真空,模具内形成这种压力的趋势得到了减少, 因而增加了使用更轻模具的可能性,真空的使用也可提高 玻璃纤维的含量,而且有助于树脂对纤维的浸渍。纤维含 量可达65%以上,空隙率小于2%。
VARTM工艺过程
ห้องสมุดไป่ตู้合模
注射树脂
RTM – 脱模
RTM的优点
无需胶衣涂层即可为 构件提供光滑表面, 能制造出具有良好表 面的高精度复杂制品
模具制造及选材灵 活性大,设备及模 具投资小,产品只 需做小的修边
产品铺层过程中 可加入嵌件及对 局部进行加强
制品纤维含量高, 空隙率低(<0.2%)
成型过程中挥发物少, 车间环境及气味较好
在制作高质量RTM制品时,会让出口流出一定 量的树脂以后才结束充模。
目的是改善树脂对纤维的浸渍程度及排出微观 气泡。即改善了纤维与树脂的物理结合强度, 又改善了制品的密实程度。
一般浪费树脂量可达模制品重量的1/3~2/3。
注胶压力
压力的高低决定模具的材料要求和结构设计, 高压力需要高强度、高刚度和大的合模力。
基体树脂
室温或工作温度下具有低的粘度(小于1.0Pas) 及一定长的适用期
树脂对增强材料具有良好的浸润性、匹配性、 粘附性
树脂在固化温度下具有良好的反应性且后处理 温度不应过高
树脂传递模塑料成型工艺

胶衣准备
铺层
合模
模具 准备
脱模
固化
树脂 注射
后处理
检验
制品
RTM成型工艺流程图
树脂传递模塑料成型工艺
RTM-模具准备
1.检查模具有无缺损,并 2.
用压缩空气把模具表面的 疏
杂志清楚干净。注射口、 通
排气口设计是否合理。
进
料
口
和
排
气
口
是
重 点 树脂传递模塑料成型工艺
进料口
排气口
紧固的方式通常有两种 1.搭扣紧固 2.螺栓紧固
树脂传递模塑料成型工艺
搭扣紧固
树脂传递模塑料成型工艺
螺栓紧固
树脂传递模塑料成型工艺
合模类型
上下模完全靠螺栓锁 紧至上下定位销完全吻合
定位销完全吻合
树脂传递模塑料成型工艺
油缸或气缸举升下模与上模合模
半圆支架可以使 上模360度旋转
油缸举升上模, 并限位
树脂传递模塑料成型工艺
铰链式搭扣合模
铰链 搭扣紧固
树脂传递模塑料成型工艺
铰链
油缸举升上模, 并限位
注胶口和排气口的位置
1、中心注入 2、四周注入 四周浇注可以比中心浇注充模时间减少60%以上,孔隙率可 以比之降低25%以上,同时也能提高一定的力学性能。 另外还有真空辅助和充模时间的控制。
树脂传递模塑料成型工艺
模具的密封
密封是整个模具制作过程中较为关键的一步,根 据产品大小结构的不同大致分为以下7种方法: 矩形密封、半圆形密封、蘑菇形密封、半圆形+V 型两道密封、圆形真空密封、圆形充气密封、半 圆形两道密封。
树脂传递模塑料成型工艺
复合材料树脂渗透成型工艺(详细)
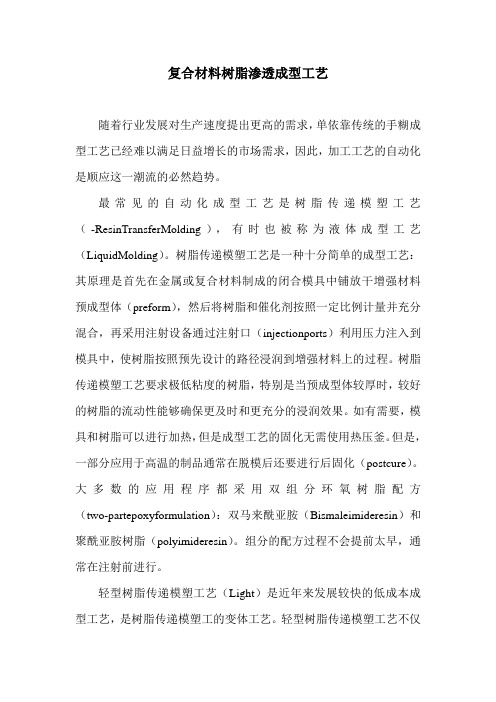
复合材料树脂渗透成型工艺随着行业发展对生产速度提出更高的需求,单依靠传统的手糊成型工艺已经难以满足日益增长的市场需求,因此,加工工艺的自动化是顺应这一潮流的必然趋势。
最常见的自动化成型工艺是树脂传递模塑工艺(-ResinTransferMolding),有时也被称为液体成型工艺(LiquidMolding)。
树脂传递模塑工艺是一种十分简单的成型工艺:其原理是首先在金属或复合材料制成的闭合模具中铺放干增强材料预成型体(preform),然后将树脂和催化剂按照一定比例计量并充分混合,再采用注射设备通过注射口(injectionports)利用压力注入到模具中,使树脂按照预先设计的路径浸润到增强材料上的过程。
树脂传递模塑工艺要求极低粘度的树脂,特别是当预成型体较厚时,较好的树脂的流动性能够确保更及时和更充分的浸润效果。
如有需要,模具和树脂可以进行加热,但是成型工艺的固化无需使用热压釜。
但是,一部分应用于高温的制品通常在脱模后还要进行后固化(postcure)。
大多数的应用程序都采用双组分环氧树脂配方(two-partepoxyformulation):双马来酰亚胺(Bismaleimideresin)和聚酰亚胺树脂(polyimideresin)。
组分的配方过程不会提前太早,通常在注射前进行。
轻型树脂传递模塑工艺(Light)是近年来发展较快的低成本成型工艺,是树脂传递模塑工的变体工艺。
轻型树脂传递模塑工艺不仅具备工艺的所有特点,还降低了成型工艺对一系列指标的要求,例如,注射压力,真空耦合(coupledwithvacuum),和模具的造价和刚性指标。
树脂传递模塑工艺具有许多显著的优点。
一般来说,在树脂传递模塑工艺过程中所使用的干预成型体和树脂材料的价格都比预浸料便宜,而且还可以在室温下存放。
利用这种工艺可以生产较厚的净成形零件,同时免去许多后续加工程序。
该工艺还能帮助生产尺寸精确,表面工艺精湛的复杂零件。
RTM相关资料

RTM相关资料1.前言所谓闭模成型工艺就是在阴、阳模闭合的情况下成型复合材料构件的工艺方法。
SMC、BMC模压、注射成型、RTM、VEC技术都属闭模成型工艺。
由于环境法的制定和对产品要求的提高使敞模成型复合材料日益受到限制,促使了闭模成型技术的应用,近年来尤其促进了RTM技术的革新和发展。
2.RTM的类型RTM工艺,即树脂传递模塑工艺,是一种新型的模压成型方法。
它具有模具造价低、生产周期短、劳动力成本低、环境污染少、制造尺寸精确、外形光滑、可制造复杂产品等优点。
40年代来,该工艺是为适应飞机雷达罩成型而发展起来的。
目前,RTM成型工艺己广泛应用于建筑、交通、电讯、卫生、航天航空等领域。
下面介绍几种RTM技术。
1)TM,树脂传递模塑。
该技术源自聚氨酯技术,成型时关闭模具,向预制件中注入树脂,玻纤含量低,约20-45%。
2)VARIT,真空辅助树脂传递注塑。
该技术利用真空把树脂吸入预制件中,同时也可压入树脂,真空度约10-28英寸汞柱。
3)VARTM,真空辅助树脂传递注塑。
制品孔隙一般较少,玻纤含量可增高。
4)VRTM,真空树脂传递模塑。
5)VIP,真空浸渍法。
6)VIMP,可变浸渍塑法。
树脂借助真空或自重移动,压实浸渍。
7)TERTM,热膨胀RTM。
在预制件中插入世材,让树脂浸渍并对模具与成形品加热。
芯材受热膨胀,压实铺层。
利用这种压实作用,结合表面加压成型。
8)RARTM,橡胶辅助RTM。
在TERTM方法中不用芯材而用橡胶代之。
橡胶模具压紧成型品,使孔隙大大减少,玻纤含量可高达60-70%。
9)RIRM,树脂注射循环模塑。
真空与加压结合,向多个模具交替注入树脂,使树脂循环,直至预制件被充分浸透。
10)CIRTM,Co-Injection RTM。
共注射RTM,可注入几种不同的树脂,也可使用几种预制件,可利用真空袋和柔性表面的模具。
11)RLI,树脂液体浸(渗)渍。
在下模内注入树脂,入入预制件后覆盖上模,加热并用热压釜的成型压力成型。
树脂渗透工艺

复合材料的树脂渗透成型工艺树脂渗透工艺:随着行业发展对生产速度提出更高的需求,单依靠传统的手糊成型工艺已经难以满足日益增长的市场需求,因此,加工工艺的自动化是顺应这一潮流的必然趋势。
最常见的自动化成型工艺是树脂传递模塑工艺(-ResinTransferMolding),有时也被称为液体成型工艺(LiquidMolding)。
树脂传递模塑工艺是一种十分简单的成型工艺:其原理是首先在金属或复合材料制成的闭合模具中铺放干增强材料预成型体(preform),然后将树脂和催化剂按照一定比例计量并充分混合,再采用注射设备通过注射口(injectionports)利用压力注入到模具中,使树脂按照预先设计的路径浸润到增强材料上的过程。
树脂传递模塑工艺要求极低粘度的树脂,特别是当预成型体较厚时,较好的树脂的流动性能够确保更及时和更充分的浸润效果。
如有需要,模具和树脂可以进行加热,但是成型工艺的固化无需使用热压釜。
但是,一部分应用于高温的制品通常在脱模后还要进行后固化(postcure)。
大多数的应用程序都采用双组分环氧树脂配方(two-partepoxyformulation):双马来酰亚胺(Bismaleimideresin)和聚酰亚胺树脂(polyimideresin)。
组分的配方过程不会提前太早,通常在注射前进行。
轻型树脂传递模塑工艺(Light)是近年来发展较快的低成本成型工艺,是树脂传递模塑工的变体工艺。
轻型树脂传递模塑工艺不仅具备工艺的所有特点,还降低了成型工艺对一系列指标的要求,例如,注射压力,真空耦合(coupledwithvacuum),和模具的造价和刚性指标。
树脂传递模塑工艺具有许多显著的优点。
一般来说,在树脂传递模塑工艺过程中所使用的干预成型体和树脂材料的价格都比预浸料便宜,而且还可以在室温下存放。
利用这种工艺可以生产较厚的净成形零件,同时免去许多后续加工程序。
该工艺还能帮助生产尺寸精确,表面工艺精湛的复杂零件。
树脂传递模塑工艺
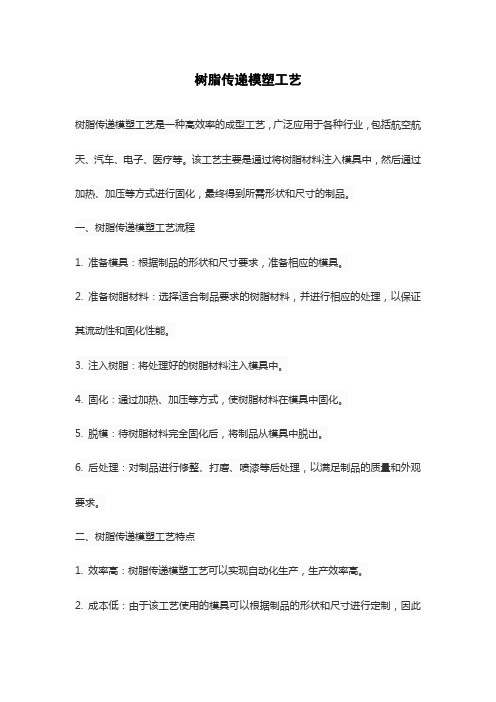
树脂传递模塑工艺树脂传递模塑工艺是一种高效率的成型工艺,广泛应用于各种行业,包括航空航天、汽车、电子、医疗等。
该工艺主要是通过将树脂材料注入模具中,然后通过加热、加压等方式进行固化,最终得到所需形状和尺寸的制品。
一、树脂传递模塑工艺流程1. 准备模具:根据制品的形状和尺寸要求,准备相应的模具。
2. 准备树脂材料:选择适合制品要求的树脂材料,并进行相应的处理,以保证其流动性和固化性能。
3. 注入树脂:将处理好的树脂材料注入模具中。
4. 固化:通过加热、加压等方式,使树脂材料在模具中固化。
5. 脱模:待树脂材料完全固化后,将制品从模具中脱出。
6. 后处理:对制品进行修整、打磨、喷漆等后处理,以满足制品的质量和外观要求。
二、树脂传递模塑工艺特点1. 效率高:树脂传递模塑工艺可以实现自动化生产,生产效率高。
2. 成本低:由于该工艺使用的模具可以根据制品的形状和尺寸进行定制,因此可以大大降低生产成本。
3. 适用范围广:树脂传递模塑工艺可以用于各种形状和尺寸的制品生产,适用范围广。
4. 环保:该工艺使用的树脂材料可以循环使用,对环境友好。
三、树脂传递模塑工艺的应用1. 航空航天领域:在航空航天领域,树脂传递模塑工艺被广泛应用于制造各种形状和尺寸的轻量化制品,如飞机零部件、卫星零部件等。
2. 汽车领域:在汽车领域,树脂传递模塑工艺被广泛应用于制造各种零部件,如汽车车门、汽车发动机罩等。
3. 电子领域:在电子领域,树脂传递模塑工艺被广泛应用于制造各种电子元器件,如电路板、电池等。
4. 医疗领域:在医疗领域,树脂传递模塑工艺被广泛应用于制造各种医疗器材,如医疗器械外壳、医疗容器等。
树脂传递模塑工艺是一种高效、环保、低成本的成型工艺,具有广泛的应用前景。
随着科技的不断发展,该工艺将会不断创新和完善,为各行各业的发展提供更加优质的技术支持。
真空辅助RTM成型技术应用及适用树脂体系

应用领域真空辅助RT M成型技术应用及适用树脂体系刁 岩,陈一民,洪晓斌,李 华(国防科学技术大学航天与材料工程学院,长沙 410073) 摘要:简要介绍了真空辅助RT M技术(VART M)对其所需树脂体系的基本要求,该技术在国内外的应用情况,并对适用于该技术的树脂体系进行综述。
关键词:真空辅助RT M成型;环氧树脂;乙烯基酯;酚醛树脂在树脂传递模塑(RT M)工艺发展过程中,真空辅助RT M工艺(VART M)的开发成功可谓具有里程碑意义,它是“因改进产品质量的要求而得到普遍应用的技术”。
这一技术的应用不仅增加了树脂传递动力,排除了模具及树脂中的气泡和水分,更重要的是为树脂在模腔中的流动打开了通道,形成了完整的通路[1]。
真空辅助成型技术(VART M)是一种新型的低成本的复合材料(FRP)大型制件的成型技术,它是在真空状态下排除纤维增强体中的气体,通过树脂的流动、渗透,实现对纤维及其织物的浸渍,并在室温下进行固化,形成一定树脂Π纤维比例的工艺方法[2]。
对于大尺寸、大厚度的复合材料制件,VART M是一种十分有效的成型方法,采用以往的复合材料成型工艺,大型模具的选材困难,而且成本昂贵,制造十分困难,尤其是对于大厚度的船舶、汽车、飞机等结构件。
VART M工艺制造的复合材料制件具有成本低、空隙含量小、成型过程中产生的挥发气体少、产品的性能好等优点,并且工艺具有很大的灵活性。
在过去的十年里VART M工艺在商业,军事,基础行业以及船舶制造业等方面都有广泛的应用。
VART M成型技术对基体树脂的要求[3]:(1)低粘度,仅借助真空即可在增强剂堆积的高密度预成型体中流动、浸润、渗透;(2)适用期长,有利于浸透、排气,树脂工作寿命满足结构要求;(3)可在室温下固化;(4)固化时无需额外压力,只需真空负压;(5)具有良好的韧性与高于一般树脂的弹性模量,以及抗腐蚀性(耐酸、碱和海水)和可加工性;(6)具有较高的玻璃化转变温度,以满足耐热要求,经后处理后可以在较高的温度下使用;(7)具有优良的阻燃性能。
传递模塑工艺

树脂传递模塑工艺(树脂压铸成型)属于复合材料的液体成型工艺
(Liquid composite molding)。
它是在20世纪70年代发展起来的复合材料成型新工艺,也有资料认为它是由20世纪30年代的浇铸冷模工艺演变而来的,在西欧RTM工艺也称"树脂注射"工艺。
RTM 工艺的基本原理示意如图-1(a)所示,在一定的温度、压力下,低黏度的液体树脂被注人铺有预成型坯(增强材料)的模具中,注人树脂,固化成型,然后脱模。
工艺过程图解如图- 1 (10所示,包括预成型坯的加工与树脂的注入和固化两步。
由于这两步可分开进行,所以说RTM工艺具有髙度的灵活性和组合性,便于实现"材料设计",同时使操作工艺简单。
图-1RTM成型工艺
RTM工艺的注射操作一般要求在1/4 ~ 1/2树脂凝胶时间内完成,传递时间为2~15min,传递压力为0.3~0.7MPa。
为脱除模腔内的气泡,促进树脂的流动和改善浸渍性,还发展了一种在注入树脂的同时抽真空的新工艺——真空辅助RTM工艺。
真空辅助树脂转移模塑(VARTM)技术-综述 [兼容模式]
![真空辅助树脂转移模塑(VARTM)技术-综述 [兼容模式]](https://img.taocdn.com/s3/m/1c5acbac0029bd64783e2c93.png)
Seeman Composites Resin Infusion Molding Process (SCRIMP®)
SCRIMP 工艺在预制体表面贴附高渗透率导流介质层,注入过程中树 脂快速通过预制体表面,同时在厚度方向渗透 控制树脂流向,提高注入速度,满足大尺寸制件的注入时间要求
Seeman Composites Resin Infusion Molding Process (SCRIMP®) 特点
技术需求
深入把握树脂流动行为,指导模具工装设计,包括注入口、真空口布置以及相应的传感 器布设 建模计算流动参数,可以优化工艺设计变量,如分段间隔时间和注入总时间,注射口的 间距等,并且给出这些参数与导流介质和预制体渗透率、制件尺寸、树脂粘度的函数关 系
解析模型
树脂波前稳定,速度不变 Darcy’s law 归一化处理后求解方程组,给出流动波前形状,以及饱和浸润区域随 时间的扩展规律
优势与问题
模具,工装,大尺寸产品,低成本 工艺可重复性,尺寸公差,力学性能,低于预浸料热压罐制品 主导风能,船舶领域,面向航空主承力结构
最新进展
技术进步与航空应用演示
VARTM的三种专利变化形式
① the Seeman Composites Resin Infusion Molding Process (SCRIMP®),patent held by TPI Composites; ② the VAP, patent held by EADS; ③ Controlled Atmospheric Pressure Resin Infusion (CAPRI), patent held by The Boeing Company.
试验平台
新型树脂传递模塑技术

万方数据第3期齐燕燕等:新型树脂传递模塑技术分对人体和环境的毒害;(5)RTM一般采用低压注射技术(注射压力<4kg/cm2),有利于制备大尺寸、外形复杂、两面光洁的整体结构,及不需后处理制品;(6)加工中仅需用树脂进行冷却;(7)模具可根据生产规模的要求选择不同的材料,以降低成本。
2RTM工艺的发展目前,RTM技术国内外普遍存在的难点和问题表现在以下三个方面[6’7]:(1)树脂对纤维的浸渍不够理想,导致成型时间加长,制品空隙率较高;(2)制品的纤维含量较低(一般约50%);(3)大面积、结构复杂的模具型腔内,树脂流动不均衡,而这个动态过程无法观察,更不能进行预测和控制。
产生上述难点和问题的主要原因有:物料里残存、截留着气泡,树脂的浸渍性差等。
近年来,为解决这些问题,RTM工艺广泛吸取其他成型工艺的特点,发展成为RTM系列,常用的有真空辅助RTM(VacuumAssistedRTM)、See—mann复合材料树脂浸渍模塑成型工艺SCRIMP(SeemannCompositesResinInfusionMoldingProcess)、树脂膜渗透成型工艺RFI(Resinfilmin-fusion)。
2.1真空辅助RTIVl工艺(VARTM)VARTM是在注射树脂的同时,在排出口接真空泵抽真空。
与RTM相比,VARTM的优点有:(1)模腔内抽真空使压力减小,增加了使用更轻型模具的可能性,从而使模具的使用寿命更长、可设计性更好;(2)真空袋材料取代了在RTM中的需相配对的金属模具[83;(3)真空也可提高玻璃纤维与树脂的比率,使玻璃纤维的含量更高,增加制品的强度;(4)无论增强材料是编织的还是非编织的,无论树脂类型及粘度如何,VARTM都能大大改善模塑过程中纤维的浸润性,使树脂和纤维的结合界面更完美,提高制品的质量;(5)用Ⅵ气R1M工艺可使直径38.11mm的致密预成型坯的纤维体积含量为16%~68%,累计孔隙率为1.7%,而普通的预浸料的孔隙率为5%~7%[9]。
树脂传递模塑成型工艺
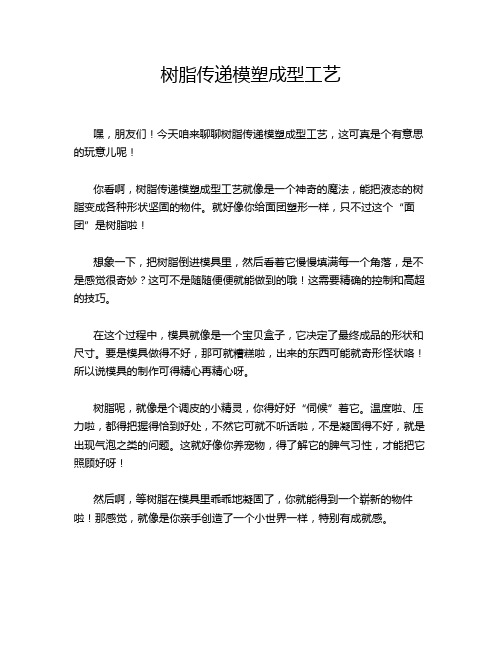
树脂传递模塑成型工艺嘿,朋友们!今天咱来聊聊树脂传递模塑成型工艺,这可真是个有意思的玩意儿呢!你看啊,树脂传递模塑成型工艺就像是一个神奇的魔法,能把液态的树脂变成各种形状坚固的物件。
就好像你给面团塑形一样,只不过这个“面团”是树脂啦!想象一下,把树脂倒进模具里,然后看着它慢慢填满每一个角落,是不是感觉很奇妙?这可不是随随便便就能做到的哦!这需要精确的控制和高超的技巧。
在这个过程中,模具就像是一个宝贝盒子,它决定了最终成品的形状和尺寸。
要是模具做得不好,那可就糟糕啦,出来的东西可能就奇形怪状咯!所以说模具的制作可得精心再精心呀。
树脂呢,就像是个调皮的小精灵,你得好好“伺候”着它。
温度啦、压力啦,都得把握得恰到好处,不然它可就不听话啦,不是凝固得不好,就是出现气泡之类的问题。
这就好像你养宠物,得了解它的脾气习性,才能把它照顾好呀!然后啊,等树脂在模具里乖乖地凝固了,你就能得到一个崭新的物件啦!那感觉,就像是你亲手创造了一个小世界一样,特别有成就感。
树脂传递模塑成型工艺的好处可不少呢!它能做出很复杂的形状,那些传统工艺很难做到的,它都能轻松搞定。
而且啊,成品的质量还特别好,坚固又耐用。
咱再说说它在实际生活中的应用吧,汽车零件、飞机部件,好多地方都有它的身影呢!你想想,那些精致的零件,可都是通过这个工艺制造出来的呀,多厉害!咱普通人虽然不会直接去用这个工艺做东西,但了解了解也挺有意思的呀,说不定哪天就能派上用场呢!比如说你突然想自己动手做个小玩意,这时候知道树脂传递模塑成型工艺不就派上用场啦?总之呢,树脂传递模塑成型工艺真的是个很了不起的工艺,它让我们的生活变得更加丰富多彩。
它就像一个默默奉献的幕后英雄,为我们制造出各种好用又好看的东西。
咱可得好好感谢这个工艺呀,不是吗?。
- 1、下载文档前请自行甄别文档内容的完整性,平台不提供额外的编辑、内容补充、找答案等附加服务。
- 2、"仅部分预览"的文档,不可在线预览部分如存在完整性等问题,可反馈申请退款(可完整预览的文档不适用该条件!)。
- 3、如文档侵犯您的权益,请联系客服反馈,我们会尽快为您处理(人工客服工作时间:9:00-18:30)。
真空辅助树脂传递模塑工艺
真空辅助树脂传递模塑工艺(VARTM/SCRIMP)适用于质量要求高、小批量和尺寸较大的制品。
它和传统的热压罐成型工艺相比,具有模具低成本,树脂室温固化以及几乎不受限制的制品尺寸等突出的特点。
在国外VARTM已成功地用于舰船、军事设施、国防工程、航空和民用工业等领域。
目前,真空辅助树脂传递注塑中应用最广泛的工艺之一,SCRIMPTM成型工艺,是在19世纪80年代后期在RTM 工艺基础上发展起来的以低成本、适合制作大型复合材料制品的成型工艺。
该加工工艺的成品有较好的品质,如:孔隙率低、纤维含量高,和良好的机械性能,并且可以将挥发性有毒气体的排放量控制在最小的程度。
SCRIMP真空辅助树脂传递注塑是利用薄膜将增强材料密封于单边模具上,完全借助于真空将低黏度树脂吸入,利用高渗透率介质沿增强材料的表面快速浸渍,并同时向增强材料厚度方向进行浸润的加工工艺。
用这种方法加工的复合材料,纤维含量高,制品力学性能优良,而且产品尺寸不受限制,尤其适合制作大型制品。
最近,由于树脂体系和纺织增强材料成型技术的不断发展,航空制造者们也对VARTM表现出了浓厚的兴趣,主要表现为采用碳纤维-环氧树脂、碳纤维-双马来酰亚胺树脂的复合材料。
几种常用的纺织复合材料增强体
和传统的开模成型工艺相比,SCRIMP成型工艺具有许多的优点。
SCRIMP工艺比手工铺放节约成本约50%,树脂浪费率低于5%,特别是加工过程的环保性,是SCRIMP工艺最突出的优点。
在同样原材料的情况下,与手糊构件相比,复合材料的强度、刚度或硬度及其它的物理特性可提高30%-50%以上。
产品质量不受操作人员影响,产品性能的均匀性和重复性比开模产品好得多,缺陷也少得多。
SCRIMP由于是采用闭模成型工艺,挥发性有机物和有毒空气污染物均受到很大程度的控制,VOC排放不超过5PPm的标准,而开模成型的苯乙烯的挥发量超过500PPm。
SCRIMP工艺特别适合制造较大的制品,并且可以进行芯材、加筋结构件的一次成型以及厚的、大型复杂几何形状的制造,提高了产品的整体性,而且材料和人工的节省实为可观。
采用SCRIMP制作的构件,不论是同一构件还是构
件与构件间,制品都有保持着良好的重复性。
SCRIMP成型时树脂的消耗量可以进行严格控制,纤维体积比可高达60%,制品孔隙率小于1%。
国内外复合材料生产厂家,特别是一些造船厂、游艇工厂和风力发电叶片厂,目前已经有不少已经采用SCRIMP方法,但多数的制造技术在使用上都是以“试误(TrialandError)”的方式来积累加工经验的,这样就使得制品的品质受到很大的影响。
而要充分发挥采用SCRIMP工艺制品的特点,达到高水平的品质,生产企业应该注意诸如:浸渍时的真空度的选择、增强材料的特性、树脂黏度、树脂种类、浸渍程度、树脂的凝胶及固化情况等。
LCM工艺用纺织增强材料目前,常用的增强材料主要是玻璃纤维、碳纤维、芳纶和高密度聚乙烯纤维等等。
而增强材料的结构可以有许多种类可供选择,图1为常用的增强材料的结构形式,如机织的方格布、三维正交机织物、经编多轴向织物、2D和3D的编织织物以及缝编织物。
在复合材料加工过程中,增强材料的结构、材质和铺放形式都直接影响到树脂浸润和加工工艺。
LCM工艺技术的应用SCRIMP工艺的高纤维含量、优异的制品性能、良好的生产重复性、特别是低成本的快速成型,使其制品性能可以与航空、宇航等领域广泛采用的热压釜工艺相媲美。
随着SCRIMP技术从早期的海军军事和国防军工领域应用向民用工业的拓展,SCRIMP工艺已经大量地应用于制造船体、船舶甲板、巡逻艇、风机叶片、桥梁、运输壳体以及其它民用和海洋基础工程。
目前SCRIMP工艺可成型面积达185m2、厚度达700mm、纤维重量含量达70~80%、孔隙率低于1%的制品,其树脂浪费率低于5%,与手工铺放相比,节约劳动成本50%以上。
SCRIMP制品的主要应用领域是是船体结构,瑞典海军的隐型护卫舰Visby,艇长72m,是目前建造的最大的FRP夹芯结构,舰上的部件如船体、甲板和上层建筑都也都是用SCRIMP法制造的。
图2为作者在美国特拉华大学复合材料中心主持的《低成本制造大型流体动力表面》项目所完成的复合材料船舵的计算机模型和实际的增强体铺放。
图中模型,高38”,宽42”,为真实船舵大小的1/4。
SCRIMP工艺的另一个主要应用领域是风机叶片的制造。
国内目前的我国风机叶片制造厂家由于受市场、技术、材料及资金等方面的影响,大多采用湿法手
糊工艺,常温固化。
能够实现600KW和750KW机组叶片的批量生产。
湿法手糊工艺工艺相对简单,不需要加温加压装置,不需要昂贵的工装设备。
成型工艺具有生产效率低、劳动强度大、劳动卫生条件差、产品质量不易控制、性能稳定性不高、产品力学性能较低等的缺点,该工艺通常只用于生产叶片长度比较短和批量比较小的时候。
但对于大型的兆瓦级风力机叶片,由于叶片体形庞大,最宽处达300cm左右,最高处大于200cm,手糊成型工艺是无法胜任的。
目前,国外采用闭模的真空辅助成型工艺用于生产大型叶片(叶片长度在40m以上时)和大批量的生产。
这种工艺适宜一次成型整体的风力发电机叶片(纤维、夹芯和接头等可一次模腔中共成型),而无需二次粘接。
世界著名的叶片生产企业LM公司开发出56M的全玻纤叶片就是采用这种工艺生产的。