论文题目循环流化床锅炉旋风分离器分析循环流化床锅炉旋风分离器分析[修改版]
循环流化床锅炉中旋风分离器的设计与探讨

粒, 旋风分离器都可以完全捕集 , 而后者对 d。 5 的颗粒
粒径 刚好 有 5 %被 捕 集 , 程上 常 采 用 d 。 进 行 设 0 工 来
Vo | I 3 No. 4
Oc . 2 07 t 0
循 环 流 化 床 锅 炉 中 旋 风 分 离 器 的 设 计 与 探 讨
黄新章 王永波 郑传 贵 徐 有宁 , , ,
( . 阳工程 学院 动力 工程 系 , 阳 1 0 3 ; . 宁科 林环保 工程 有限 责任公 司 , 阳 10 3 ; 1沈 沈 116 2 辽 沈 10 4
计l. 2 临界 分 离 粒 径 的 大 小 决 定 于 分 离 器 的结 构 尺 ] 寸 , 以应在满 足一 定分离 效率 的条件 下 , 算临 界分 所 计
离粒 径 , 临界分 离粒径 确定 后 , 根据 经验公 式来确 定 再
是 用分离器 的效 率和 压 损来 衡 量 、 中分离 效 率 高 低 其
关键 词 :旋 风 分 离 器 ; 离效 率 ; 分 临界 分 离粒 径 中 图分 类 号 :TO 5 0 文 献 标 识 码 :A 文 章 编 号 :17 —1 0 (0 7 0 6 3 6 3 2 0 )4—0 3 3 3—0 2
旋 风分离 器是 结构 简 单 、 易 制造 和 安装 的 常见 容 的化工设 备 , 在食 品 、 医药 、 日用化 工 以及 冶金 电力 等
为衡 量其好 坏 的最 主要 指标 , 即旋 风 分 离 器处 理 后 的
循环流化床锅炉高温绝热旋风分离器超温分析及技术改造浅谈
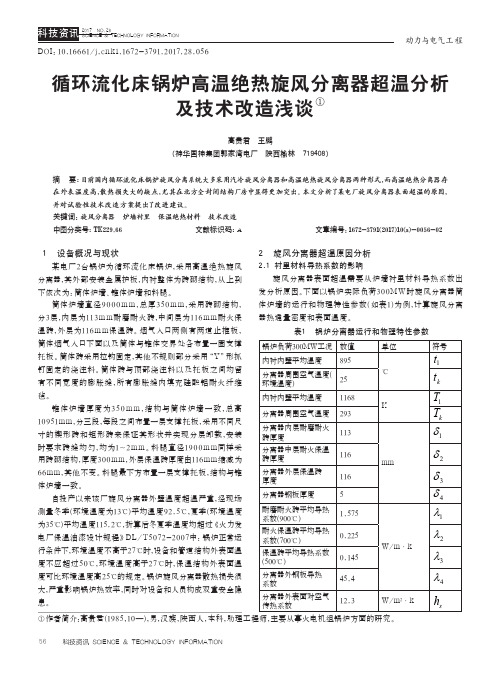
动力与电气工程56科技资讯 SCIENCE & TECHNOLOGY INFORMATIONDOI:10.16661/ki.1672-3791.2017.28.056循环流化床锅炉高温绝热旋风分离器超温分析及技术改造浅谈①高贵君 王鹏(神华国神集团郭家湾电厂 陕西榆林 719408)摘 要:目前国内循环流化床锅炉旋风分离系统大多采用汽冷旋风分离器和高温绝热旋风分离器两种形式,而高温绝热分离器存在外表温度高,散热损失大的缺点,尤其在北方全封闭结构厂房中显得更加突出。
本文分析了某电厂旋风分离器表面超温的原因,并对试验性技术改造方案提出了改进建议。
关键词:旋风分离器 炉墙衬里 保温绝热材料 技术改造中图分类号:TK229.66文献标识码:A文章编号:1672-3791(2017)10(a)-0056-021 设备概况与现状某电厂2台锅炉为循环流化床锅炉,采用高温绝热旋风分离器,其外部安装金属护板,内衬整体为砖砌结构,从上到下依次为:筒体炉墙、锥体炉墙和料腿。
筒体炉墙直径9000m m,总厚350m m,采用砖砌结构,分3层,内层为113m m 耐磨耐火砖,中间层为116m m 耐火保温砖,外层为116m m保温砖。
烟气入口两侧有两道止推板,筒体烟气入口下面以及筒体与锥体交界处各布置一圈支撑托板。
筒体砖采用拉钩固定,其他不规则部分采用“Y”形抓钉固定的浇注料。
筒体砖与顶部浇注料以及托板之间均留有不同宽度的膨胀缝,所有膨胀缝内填充硅酸铝耐火纤维毡。
锥体炉墙厚度为350m m,结构与筒体炉墙一致,总高10951mm,分三段,每段之间布置一层支撑托板,采用不同尺寸的楔形砖和矩形砖来保证其形状并实现分层卸载,安装时要求砖缝均匀,均为1~2m m。
料腿直径1900m m同样采用砖砌结构,厚度300mm,外层保温砖厚度由116mm缩减为66mm,其他不变。
料腿最下方布置一层支撑托板,结构与锥体炉墙一致。
自投产以来该厂旋风分离器外壁温度超温严重,经现场测量冬季(环境温度为13℃)平均温度92.5℃,夏季(环境温度为35℃)平均温度115.2℃,折算后冬夏季温度均超过《火力发电厂保温油漆设计规程》DL/T5072-2007中:锅炉正常运行条件下,环境温度不高于27℃时,设备和管道结构外表面温度不应超过50℃,环境温度高于27℃时,保温结构外表面温度可比环境温度高25℃的规定。
影响循环流化床旋风效率的因素杜英军

影响循环流化床旋风效率的因素杜英军发布时间:2021-08-18T07:15:12.993Z 来源:《基层建设》2021年第16期作者:杜英军[导读] 旋风分离器是目前循环流化床锅炉中应用最广泛的一种分离装置新疆圣雄能源股份有限公司热电厂摘要:旋风分离器是目前循环流化床锅炉中应用最广泛的一种分离装置,其结构简单、压降低、且分离效率高。
但它仍存在一些缺陷,如磨损较严重、热惯性大、体积大等。
关键词:循环流化床;旋风效率前言:由于循环流化床(CFB)风系统的复杂性,相关的风系统配置不合理,造成了高功耗,影响了电厂的经济效益。
因此,现阶段加强循环硫化床锅炉空气系统优化措施的研究,对于优化风口和空气系统的配置,提高电厂的经济效益具有重要的现实意义。
通过对控制方案的比较和实践,对控制方案进行了优化,有效地解决了循环流化床锅炉主要运行参数控制的难题,避免了循环流化床锅炉的翻车现象。
一、循环流化床风系统配置1.一次风。
循环流化床主要由锅炉和一些辅助锅炉设备组成。
具体来说,锅炉外壳由蒸汽水系统组成,用来吸收燃烧燃料产生的热量,然后在一定程度上加热系统中的水,产生符合压力和温度标准的热蒸汽。
身体的第二部分是由燃烧系统、再生系统和通风设备组成的燃烧系统。
完全燃烧剩下的是辅助供水和烟雾处理系统。
循环沸腾的锅炉是锅炉燃烧的流水技术,最重要的基本技术是燃料流动的能量。
在正常使用中,体积通常应达到锅炉中空气量的一半左右,以满足流程质量和更合适的画布面积,以确保空气的均匀分布。
主空气压力的大小主要是由烤箱压力的变化和风扇阻力的大小决定的。
考虑到通风管道和加热器压力的下降,第一个风扇的压力通常约为18000帕。
为了降低风扇压力的最低限度,可以从降低烤箱压力和风扇阻力开始,在目前的技术水平上,可能的方法是通过降低烤箱压力来降低风扇压力。
然而,在具体行动中需要避免一些负面影响。
2.二次风。
另一方面,循环沸腾层中的次级风应参与锅炉燃烧,调节燃烧状态,控制燃烧过程中的氮氧化物排放,减少空气污染。
浅析循环流化床锅炉旋风分离器椎体组合就位技术

浅析循环流化床锅炉旋风分离器椎体组合就位技术摘要:旋风分离器是电厂循环流化床锅炉主要部件之一,旋风分离器由于因其体积大、质量重,为制造、运输方便,通常采用分片制造、供货的方式,旋风分离器运到现场后,通常采用组合和散掉相结合方式进行安装。
通过对旋风分离器锥体使用自制的组合胎具作地面组合、整体吊装的施工方案论述,进而确定了分离器锥体组合及整体吊装技术的可靠性。
关键词:循环流化床锅炉;旋风分离器;椎体组合;就位1前言循环流化床锅炉因为其燃料适用性广、负荷调节性强以及环保性能优良而得到了越来越多的重视。
在我国能源与环境的双重压力下,循环流化床锅炉在我国得到了快速发展。
大量循环流化床锅炉机组的装备对于优化我国电力结构、改善电力供应品质、提高我国整体资源利用效率以及降低污染物排放方面发挥出了积极的的作用。
2 旋风分离器锥体设备的特点每个旋风分离器锥体现场到货时10件。
如果不在地面进行组合或预组合,单片管屏直接吊装到锅炉上进行直接安装,会出现由于单片管排变形、弧度与设计不相符,使分离器的拼接、管子对口非常困难,造成分离器锥体的圆度和同心度不可能控制,容易造成安装后成为花瓣形,不满足现场要求。
因此将分离器锥体管排进行地面组合成2半进行吊装,吊装后再拼接两个半分离器椎体。
根据分离器锥体中心到椎体管屏内壁表面的距离尺寸,自行设计一个管屏拼接组合胎具,来保证分离器锥体组合后的圆度。
通过使用该管屏拼接组合胎具,减小组合成半圆拼接的间隙,在吊装安装前认真检查每片管屏的尺寸,保证每片管屏尺寸与图纸相近,从而保证旋风分离器圆锥体上下口同心度。
3旋风分离器椎体胎具的制作及设备组合3.1组合胎具的制作:首先核查图纸,计算出分离器锥体上下口半径尺寸,即到上、下口中心到管壁内径的半径尺寸,根据半径尺寸大小用卷板机卷制14槽钢半圆胎两件,两槽钢半圆胎使用槽钢进行连接,两槽钢半圆距离按照分离器椎体的上下口的距离尺寸进行定位,可见如图1分离器锥体组合架设图1分离器锥体组合架制作图计图,图中1是16槽钢,2是14槽钢,3是16槽钢,4是14槽钢。
循环流化床锅炉改造毕业论文

AGX75-1№17.2 D 左 90
62480m3/h
17000Pa 电动机
型号 功率 转速 电压
Y400-4 450KW 1450rpm 6000V
二次风机
型号
风量 风压
AGX75-2№12.5 D 右 90
41925m3/h
9356Pa 电动机
型号 功率 转速 电压
Y315 L-4 160KW 1450rpm
7
2 峄化公司型锅炉整体情况
2.1 锅炉概况
尾部烟道的前包墙与炉膛后墙水冷壁共用,形成双面水冷壁;低温过热器布置 在尾部烟道内,采用吊管结构;一、二级省煤器支于侧包墙上,并随侧包墙一 同膨胀;空气预热器单独向外拉出,分为一次风及二次风预热器;在炉膛出口, 烟气分为两路分别进入两只旋风分离器,进旋风分离器后的烟气回到炉顶水平 烟道。
(2) 鲁奇(Lurgi)型循环流化床 (3)巴特利(Battelle)的多固体循环流化床锅炉
(4)德国Babcock公司的Cirfluid循环流化床锅炉
4
1.3 国内外循环流化床锅炉的发展
从节约燃料、保护大气环境及回收温室气体CO2这三观点出发, 发展流化床锅炉在以煤为主要能源的国家具有重大意义。
9
设备技术参数
a.锅炉技术规格
表2-1 锅炉主要技术数据
锅筒中心标高 运转层标高 左右柱距 一次风量 锅炉效率
32050mm 8000mm 7200mm 62100m3/h
87%
表2-2 锅炉重要参数表
额定蒸发量 额定蒸汽压力 额定蒸汽温度
连续排污
75t/h 3.82MPa 450℃
2%
操作层标高 烟气量 前后柱距 二次风量
针对该型锅炉在实际运行中存在的问题(带负荷能力不足、水冷壁 管磨损严重、锅炉给煤易堵塞等),我公司结合实际运行经验,通过理论 分析和实践验证,积极采用各类技术和设备先后对一次风风道、风帽、旋 风分离器、给煤机、煤筛分机进行了合理的改造,创造了更好的燃烧条件, 提高了锅炉出力率,有效地延长了锅炉的运行时间。
循环流化床锅炉用旋风分离器分离性能的实验研究的开题报告

循环流化床锅炉用旋风分离器分离性能的实验研究的开题
报告
1. 研究背景和意义
循环流化床锅炉作为目前工业中应用最为广泛、技术水平最高的一种锅炉,其主要优点包括燃烧效率高、排放污染少等。
旋风分离器作为循环流化床锅炉排放废气中
的颗粒物的主要分离设备,其分离效率直接影响着循环流化床锅炉的性能和环保指标。
因此,对循环流化床锅炉用旋风分离器分离性能的研究具有重要意义,可以为循环流
化床锅炉的实际应用提供参考和指导,同时也有利于推动旋风分离器的技术进步和优化。
2. 研究内容和方法
本研究以循环流化床锅炉为对象,通过设计和制作合适的实验装置,实现对旋风分离器分离性能的实验研究。
具体研究内容包括:确定实验条件,测量循环流化床锅
炉废气中的颗粒物粒径分布和浓度,设计旋风分离器的结构参数,测试旋风分离器的
分离效率,并分析影响因素和优化措施。
研究方法包括:实验模拟、数据测量、图像
处理和数据分析。
3. 预期成果和意义
本研究的预期成果包括: 1)确定循环流化床锅炉废气中的颗粒物粒径分布和浓度;2)设计旋风分离器的结构参数;3)测试旋风分离器的分离效率;4)分析影响因素和优化措施。
在此基础上,可以对循环流化床锅炉用旋风分离器的分离性能进行评价,并提出优化建议和措施,有利于提升循环流化床锅炉的性能和环保指标,为推动
循环流化床锅炉和旋风分离器的技术进步做出贡献。
循环流化床锅炉高温旋风分离器设计

摘要在循环流化床锅炉里,通常将旋风分离器布置在锅炉炉膛出口,以便将高温烟气流中的热固体物料分离下来进入回料阀进入炉膛继续循环,以便保证炉膛内一定的灰浓度同时也提高了燃烧效率。
现在我国大部分旋风分离器都是根据烟气量计算出旋风分离器筒体直径后,通过设计手册确定各部分尺寸,但这种设计方法针对性差,实际分离效果不能满足要求。
针对这问题,本设计以130t/hCFBB旋风分离器的设计为例,通过对压降损失和分离效率的计算,筛选出最佳的分离粒径,以该粒径为参考,确定旋风分离器各部分的尺寸关系并最终计算出各部分的尺寸,完成旋风分离器的设计。
通过本设计的设计思路和方法,可有效地提高分离效率,为循环流化床锅炉的稳定运行提供了保障。
关键词:高温旋风分离器;分离效率;压降损失;尺寸计算AbstractCyclone plays an important role in circulating fluidized bed.In the circulating fluidized bed boiler,Usually arranged in the boiler furnace cyclone export to the high temperature gas stream down into the thermal separation of solid materials into the furnace return valve to cycle in order to guarantee a certain degree of gray levels within the furnace also increases combustion efficiency.Now most of our cyclone are calculated according to smoke after the cyclone cylinder diameter,through the various parts of the design manual to determine size,but targeted poor design, the actual separation can not meet the requirements.To address this problem, The design makes 130t/hCFBB cyclone design for example,On the calculation of the pressure drop and separation efficiency, then select the best particle size, To the diameter of reference to determine the relationship between the size of various parts of cyclone and finally calculate the size of each part to complete the design of cyclone.Through the design of design ideas and methods can effectively improve the separation efficiency, sTab operation of circulating fluidized bed boiler to provide a guarantee.Key Words:high temperature cyclone separator;separation efficiency;pressure drop;size calculation目录前言 (1)1 绪论 (2)1.1 循环流化床锅炉的发展趋势及其所带来的技术难题 (2)1.1.1 国内外循环流化床锅炉发展 (2)1.1.2 循环流化床锅炉大型化的技术难题 (4)1.2 循环流化床分离装置的发展 (4)1.2.1 循环流化床分离装置的分类 (4)1.2.2 分离器的发展及应用 (5)2 旋风分离器的发展及应用 (11)2.1 旋风分离器的结构及工作原理 (12)2.2 旋风分离器气粒两相运动研究的进展 (12)2.3 旋风分离器的分离机理 (14)3 旋风分离器内气流运动概况分析 (16)3.1 颗粒的沉降速度和离心分离速度 (16)3.2 旋风分离器内气流流动概况 (19)3.3 极限粒径 (22)4 压降和效率的计算方法 (27)4.1 压降 (27)4.1.1 压降的影响因素 (27)4.1.2 压降的计算 (27)4.2 效率 (29)4.2.1 表示方法 (29)4.2.2 效率的计算方法 (30)5 结构尺寸的确定 (33)5.1各部尺寸关系 (33)5.1.1 进口管 (33)5.1.2 排气管 (35)5.1.3 筒体直径 (36)5.1.4 圆柱体长度 (36)5.1.5 圆锥体 (37)5.1.6 集灰斗 (37)5.1.7 旁室 (37)5.2 尺寸计算 (38)5.3 小结 (39)6 影响分离性能的因素 (40)7 结论 (41)致谢 (42)参考文献 (43)附录A (44)附录B (53)前言随着经济发展,石油、煤炭等一次能源消耗量不断增加,储量急剧减少,全世界都面临着能源危机。
循环流化床锅炉旋风分离器事故分析与改造措施

循环流化床锅炉旋风分离器事故分析与改造措施【摘要】旋风分离器效率的提高是循环流化床锅炉经济运行的关键,其设备的长期完好运转是循环流化床锅炉稳定运行的关键。
通过对旋风分离器常见事故的分析、总结、提出并实施改造,为循环流化床锅炉满负荷运行提供保证。
【关键词】旋风分离器中心筒分离效率改造措施1 前言循环流化床锅炉的分离机构是循环流化床锅炉的关键部件之一,其主要作用是将大量高温固体物料从气流中分离出来送回燃烧室,以维持燃烧室的快速流化状态,保证燃料和脱硫剂多次循环,反复燃烧和反应,使锅炉达到理想的燃烧效率和脱硫效率。
黑化集团热电分厂的四台济锅生产的YG-75/3.82-M1型循环流化床锅炉采用高温绝热旋风分离器和悬挂中心筒,在运行中出现大量事故。
近几年在实践中对事故的不断分析总结和对设备的不断改造,使锅炉能够长期安全高效稳定运行。
2 旋风分离器中心筒变形脱落的改造措施2.1 问题的提出锅炉投运初期,运行一年以后,6#炉发现旋风分离器处差压增大,分离效率下降,锅炉负荷骤减。
停炉检查发现锅炉中心筒出口处筒壁变形向内突出,四个吊挂开裂两个,造成筒体倾斜。
如继续运行,中心筒就会落入分离器椎体内。
2.2 原因分析中心筒出口与旋风分离器顶棚直接接触,在锅炉启炉和运行中中心筒和分离器顶棚受热膨胀,相互挤压使筒体变形。
进入旋风分离器的烟气一部分由变形处短路,分离效率降低,筒体变形愈加严重。
中心筒是由四根750×80×8mm材料为1Cr25Ni20Si2钢板悬吊,一侧焊接在中心筒外壁上,另一侧焊接在旋风分离器出口外护板上。
在950℃和高速烟气作用下轻微摆动,焊口氧化开裂,造成倾斜和脱落。
2.3 改造措施(1)改变中心筒的结构和材质。
原中心筒由δ8mm的1Cr25Ni20Si2钢板卷制改为δ10mm的0Cr25Ni20钢板卷制,提高其抗压强度和耐热温度。
在筒体外壁上中下三处分别增加了防变形的加强环,出口加强环内焊有8个三角形的加强板。
循环流化床锅炉旋风分离器事故分析与改造措施

循环流化床锅炉旋风分离器事故分析与改造措施作者:王元胜来源:《中国科技纵横》2013年第02期【摘要】旋风分离器效率的提高是循环流化床锅炉经济运行的关键,其设备的长期完好运转是循环流化床锅炉稳定运行的关键。
通过对旋风分离器常见事故的分析、总结、提出并实施改造,为循环流化床锅炉满负荷运行提供保证。
【关键词】旋风分离器中心筒分离效率改造措施1 前言循环流化床锅炉的分离机构是循环流化床锅炉的关键部件之一,其主要作用是将大量高温固体物料从气流中分离出来送回燃烧室,以维持燃烧室的快速流化状态,保证燃料和脱硫剂多次循环,反复燃烧和反应,使锅炉达到理想的燃烧效率和脱硫效率。
黑化集团热电分厂的四台济锅生产的YG-75/3.82-M1型循环流化床锅炉采用高温绝热旋风分离器和悬挂中心筒,在运行中出现大量事故。
近几年在实践中对事故的不断分析总结和对设备的不断改造,使锅炉能够长期安全高效稳定运行。
2 旋风分离器中心筒变形脱落的改造措施2.1 问题的提出锅炉投运初期,运行一年以后,6#炉发现旋风分离器处差压增大,分离效率下降,锅炉负荷骤减。
停炉检查发现锅炉中心筒出口处筒壁变形向内突出,四个吊挂开裂两个,造成筒体倾斜。
如继续运行,中心筒就会落入分离器椎体内。
2.2 原因分析中心筒出口与旋风分离器顶棚直接接触,在锅炉启炉和运行中中心筒和分离器顶棚受热膨胀,相互挤压使筒体变形。
进入旋风分离器的烟气一部分由变形处短路,分离效率降低,筒体变形愈加严重。
中心筒是由四根750×80×8mm材料为1Cr25Ni20Si2钢板悬吊,一侧焊接在中心筒外壁上,另一侧焊接在旋风分离器出口外护板上。
在950℃和高速烟气作用下轻微摆动,焊口氧化开裂,造成倾斜和脱落。
2.3 改造措施(1)改变中心筒的结构和材质。
原中心筒由δ8mm的1Cr25Ni20Si2钢板卷制改为δ10mm 的0Cr25Ni20钢板卷制,提高其抗压强度和耐热温度。
循环流化床锅炉旋风分离器的最新发展与高效运行 刘佳斌资料

循环流化床锅炉旋风分离器的最新发展与高效运行刘佳斌(山东大学能源与动力工程学院济南250010)摘要:循环流化床的分离机构是循环流化床的关键部件之一,其主要作用是将大量高温固体物料从气流中分离出来,送回燃烧室,以维持燃烧室的快速流态化状态,保证燃料和脱硫剂多次循环、反复燃烧和反应。
这样,才有可能达到理想的燃烧效率和脱硫效率。
关键词: 旋风分离器、循环流化床锅炉、循环效率、发展。
图1 75t/h循环流化床锅炉简图1.循环流化床旋风分离器的工作原理如图2、3为普遍采用的高温旋风分离器结构。
此类分离器的体积庞大,占地面积与炉膛基本相当,它是利用旋转的含尘气体所产生的离心力,将颗粒从气流中分离出的一种干式气固分离装置。
含灰烟气在炉膛出口处分进入旋风分离器,旋风分离器的圆形筒体和气体的切向入口使气固混合物进入围绕旋风分离器的2个同心涡流,外部涡流向下,内部涡流向上。
由于固体密度比烟气密度大,在离心力作用下固体离开外部涡流移向壁面, 再沿旋风分离器的循环流化床的分离机构是循环流化床的关键部件之一,其主要作用是将大量高温固体物料从气流中分离出来,送回燃烧室,以维持燃烧室的快速流态化状态,保证燃料和脱硫剂多次循环、反复燃烧和反应。
这样,才有可能达到理想的燃烧效率和脱硫效率。
因此,循环流化床分离机构的性能优劣,将直接影响整个循环流化床锅炉的出力、效率及运行寿命。
随着循环流化床锅炉大型化的发展,对分离器提出了更高的要求,它不但要能处理大容量的烟气,还要求能在恶劣的环境中可靠、稳定运行。
多年的商业运行经验表明,高温旋风分离器目前仍是最适合(大型)循环流化床锅炉的分离器之一。
图 3 高温旋风分离壁面滑落,经返料器返回炉膛循环再燃,相对干净的气体通过内部涡流向上移动,由旋风分离器顶部的中心筒出口排出。
烟气经过过热器、省煤器、空气预热器进入尾部烟道,随烟气排出的微细颗粒由锅炉后部的静电除尘器收集。
此类分离器在设计保留了传统的旋风分离器的设计特点,从目前的情况来看,运行情况良好,但由于分离器体积过大,且由于大量采用耐火,保温材料,机组具有热惯性大,易于磨损。
浅析循环流化床锅炉旋风分离器安装doc

浅析循环流化床锅炉旋风分离器安装刘贵明(青海火电工程公司810003)摘要:青海盐湖三期4×480T/H循环流化床锅炉布置了汽冷式旋风分离器。
本文详细论述了旋风分离器的安装步骤及注意事项,为火电安装单位安装同类或相似设备具有重要的参考价值。
1、概述:旋风分离器上半部分为圆柱形,下半部分为锥形,为膜式包墙过热器结构(也有钢板卷制成圆桶形状的,安装相对简单,不在本文论述之例),其顶部与底部均与环形集箱相连,墙壁管子在顶部向内弯曲,使得在旋风分离器管子和烟气出口圆筒之间形成密封结构。
烟气出口为圆筒形钢板件,形成一个端部敞开的圆柱体。
细颗粒和烟气先旋转下流至圆柱体的底部,而后向上流动离开旋风分离器。
粗颗粒落入直接与J型回料器相连接的立管。
另有进口烟道与出口烟道分别与直段管屏和分离器中心筒相连接,形成通向尾部的烟气通道。
旋风分离器由 42的管子与扁钢包覆,并通过上、下环形集箱联系。
旋风分离器内表面敷设防磨材料,其厚度距管子外表面25mm,采用高密度销钉固定。
旋风分离器设备在循环流化床锅炉的安装中是一个非常关键的部件。
在以往的工程施工中,因为采取的施工措施不当,曾经造成工期迟滞拖延,质量问题频仍,运行事故不断的“顽症”。
如何提高分离器的安装效率和质量,是所有火电安装单位面临的一个亟需解决的重要课题。
本文尝试就分离器的安装步骤和安装要点做一浅要分析,旨在抛砖引玉,共同提高对分离器安装工作的认识。
例图一:旋风分离器及下部J阀回料装置2、安装步骤:2.1、旋风分离器进口烟道安装:分离器主体筒身在安装前应先将分离器进口烟道与非金属膨胀节组合在一起先行吊装。
如果这部分工作放在主体部件吊装之后进行,将造成进口烟道安装困难,使安装成本增大。
尤其是非金属膨胀节,因为其自身刚性较差,在无足够的安装空间的情况下,会造成设备的破损变形,以至于无法正常使用。
因此,将其与进口烟道在地面组合在一起吊装,既能保证膨胀节的外观形状不被破坏,又能使该部件的安装工效达到事半功倍的效果。
300MW CFB锅炉旋风分离器中心筒变形脱落问题分析

300MW CFB锅炉旋风分离器中心筒变形脱落问题分析旋风分离器是循环流化床锅炉的重要部件,分离器的分离效率直接关系到锅炉的安全经济运行。
旋风分离器中心筒变形下移,造成气体短路引起分离器分离效率下降,分离器中心筒脱落,影响了锅炉的安全经济运行。
本文针对这些问题,分析了原因并采取了一系列措施,取得了一定的效果。
标签:旋风分离器;中心筒变形;措施循环流化床锅炉的旋风分离器是循环流化床锅炉的核心部件之一,中心筒是连接安装在旋风分离器上部部件,即排气管。
它不仅排出分离后的烟气,与分离器的外筒体形成环形通道,进入分离器的烟气绕着中心筒旋转,在离心力和重力作用下,大部分灰粒被分离出来,送回炉膛,以保证燃料多次循环燃烧反应,含有细灰的烟气向上折转成为旋流,由中心筒排出进入尾部烟道。
1 300 MW CFB锅炉及其分离器内蒙古京泰电厂采用DG1089/17.45-II1 型锅炉,锅炉为循环流化床、亚临界参数,一次中间再热自然循环汽包炉、紧身封闭、平衡通风、固态排渣、全钢架悬吊结构、炉顶设密封罩壳。
锅炉主要由一个膜式水冷壁炉膛,三台汽冷式旋风分离器和一个由汽冷包墙包覆的尾部竖井(HRA)三部分组成。
2 分离器出现问题分析2.1 13分离器中心筒变形及参数变化中心筒变形的影响:(1)中心筒变形后,炉膛上部差压低,带来床温升高,回料器温度升高、分離器入口烟温升高。
(2)影响烟气流旋转速度和分布,导致分离效率下降,循环物料浓度降低,锅炉烟气飞灰含碳量升高,锅炉不完全燃烧损失增大,锅炉效率降低。
烟气中的固体颗粒增加还会使过热器和烟道受热面磨损加剧,影响锅炉的安全运行。
(3)中心筒严重变形引起的浇注料脱落,进而使中心筒与烟道接口处超温烧红。
脱落的浇注料引起回料器回料不畅,回料器振动。
具体参数变化如下:机组负荷315MW,13分离器中心筒脱落时参数有较为明显的波动,脱落前后参数变化如下:回料器入口静压由-0.5KPa突升至1.2KPa;分离器出入口差压由1369Pa降至1235Pa;回料器料位有波动,由22.5KPa降至20KPa后升高至25.5KPa,稳定约2分钟后又降至至21.6KPa左右达到平衡状态;伴随床压由5.6KPa降至4.5KPa,炉膛上部差压由1.15KPa降至0.99KPa,锅炉床温由942℃升高至958℃。
循环流化床锅炉旋风分离器中的事故分析
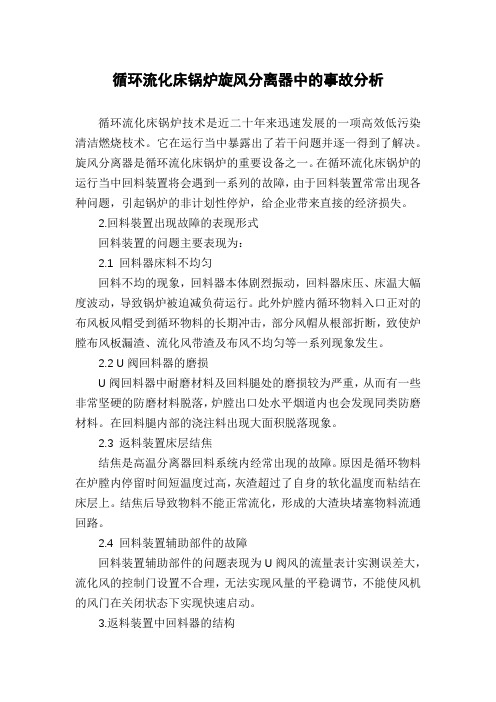
循环流化床锅炉旋风分离器中的事故分析循环流化床锅炉技术是近二十年来迅速发展的一项高效低污染清洁燃烧枝术。
它在运行当中暴露出了若干问题并逐一得到了解决。
旋风分离器是循环流化床锅炉的重要设备之一。
在循环流化床锅炉的运行当中回料装置将会遇到一系列的故障,由于回料装置常常出现各种问题,引起锅炉的非计划性停炉,给企业带来直接的经济损失。
2.回料裝置出现故障的表现形式回料装置的问题主要表现为:2.1 回料器床料不均匀回料不均的现象,回料器本体剧烈振动,回料器床压、床温大幅度波动,导致锅炉被迫减负荷运行。
此外炉膛内循环物料入口正对的布风板风帽受到循环物料的长期冲击,部分风帽从根部折断,致使炉膛布风板漏渣、流化风带渣及布风不均匀等一系列现象发生。
2.2 U阀回料器的磨损U阀回料器中耐磨材料及回料腿处的磨损较为严重,从而有一些非常坚硬的防磨材料脱落,炉膛出口处水平烟道内也会发现同类防磨材料。
在回料腿内部的浇注料出现大面积脱落现象。
2.3 返料装置床层结焦结焦是高温分离器回料系统内经常出现的故障。
原因是循环物料在炉膛内停留时间短温度过高,灰渣超过了自身的软化温度而粘结在床层上。
结焦后导致物料不能正常流化,形成的大渣块堵塞物料流通回路。
2.4 回料装置辅助部件的故障回料装置辅助部件的问题表现为U阀风的流量表计实测误差大,流化风的控制门设置不合理,无法实现风量的平稳调节,不能使风机的风门在关闭状态下实现快速启动。
3.返料装置中回料器的结构U型回料器由立管、布风板、松动室、回料室、风室、舌板等组成。
U型回料器的结构如图1所示。
4.返料器投运时的注意事项及处理措施分离器工作时分离下来的物料落入U型回料器立管,立管下方为松动风侧,以舌板为分界线,另一侧为流化风侧。
实际上,旋风分离器就是一个小型流化床。
在运行时,由于分离器分离下来的物料在立管内聚积,所以松动风侧的压力大于流化风侧的压力。
因此物料在松动风、流化风的作用下,依靠压差的作用顺利的进入料腿,物料经过回料腿进入炉膛进一步燃烧,从而完成整个物料循环过程。
循环流化床锅炉旋风分离器气流温度性能研究

循环流化床锅炉旋风分离器气流温度性能研究摘要:本文在对江苏某电厂循环流化床旋风分离器数值研究的基础上,结合生产现场实践,对分离器气流温度的性能特性进行研究分析,研究结果表明:随着入口温度的升高,旋风分离器内部轴向速度升高,切向速度减小,压力损失与分离效率减小,但是幅度均不明显。
因而在保证锅炉稳定燃烧基础上的实际运行中,提高入口处温度不能够达到提高旋风分离器分离效率的目的,同时还会出现分离器内壁形成结渣等状况,对旋风分离器的运行安全造成影响。
关键词:循环流化床旋风分离器性能研究旋风分离器是循环流化床锅炉的主要部件之一,其性能对循环流化床锅炉的燃烧及效率有着十分重要的影响。
而旋风分离器作为一种重要的分离设备,虽其结构简单,但内部三维湍流流场十分复杂,对此,本文选用FLUENT流体分析软件,采用计算流体力学方法,从计算模型入手,同时以电厂75 t/h循环流化床锅炉的旋风分离器实际运行参数为基础,分析研究在额定工况下温度变化对旋风分离器性能的影响,并通过飞灰含碳量的测定数据对其性能影响进行了分析验证。
1 旋风分离器数值模拟1.1 数值模拟理论基础本文对江苏徐州大屯某电厂75 t/h循环流化床锅炉锅炉额定负荷的实际数据进行了计算,为旋风分离器进行数值模拟提供了理论基础。
1.2 湍流模型本文选取连续性方程、动量方程以及能量方程等对控制流体运动的方程进行描述,并采用SIMPLEC算法求解控制方程。
一般的,对于旋风分离器气相流场多使用标准模型,模型以及RSM模型进行模拟。
但标准模型与模型都主要基于各项同性的模型,对此,本文选用了更适合强旋流场模拟的雷诺应力模型(RSM)。
1.3 计算模型与网格划分1.3.1 几何模型与网格划分本文选用的是现场实际的直切式旋风分离器为模型,其模型和结构尺寸如图1所示。
同时针对其筒体与进气管连接处形状尖锐等结构特点,采用了分块生成网格的办法。
对于分离特性比较明显的区域如旋风分离器内部、圆筒体以及圆锥体,本文选取了Y=3 m和Y=9 m两个曲线对旋风分离器的性能进行研究,并将坐标轴的横坐标定为曲线长度,具体曲线起点至终点的长度如图1所示。
论文题目循环流化床锅炉旋风分离器分析循环流化床锅炉旋风分离器分析[修改版]
![论文题目循环流化床锅炉旋风分离器分析循环流化床锅炉旋风分离器分析[修改版]](https://img.taocdn.com/s3/m/df8cc5bfcf84b9d529ea7a8d.png)
第一篇:论文题目循环流化床锅炉旋风分离器分析循环流化床锅炉旋风分离器分析自循环流化床燃烧技术出现以来,循环床锅炉在世界范围内得到广泛的应用,大容量的循环床锅炉已被发电行业所接受。
循环流化床低成本实现了严格的污染排放指标,同时燃用劣质燃料,在负荷适应性和灰渣综合利用等方面具有综合优势,为煤粉炉的节能环保改造提供了一条有效的途径主循环回路是循环流化床锅炉的关键,其主要作用是将大量的高温固体物料从气流中分离出来,送回燃烧室,以维持燃烧室稳定的流态化状态,保证燃料和脱硫剂多次循环、反复燃烧和反应,以提高燃烧效率和脱硫效率。
主循环回路是循环流化床锅炉的关键,其主要作用是将大量的高温固体物料从气流中分离出来,送回燃烧室,以维持燃烧室的稳定的流态化状态,保证燃料和脱硫剂多次循环、反复燃烧和反应,以提高燃烧效率和脱硫效率。
主循环回路不仅直接影响整个循环流化床锅炉的总体设计、系统布置,而且与其运行性能有直接关系。
分离器是主循环回路的主要部件,因而人们通常把分离器的形式,工作状态作为循环流化床锅炉的标志。
分离器是主循环回路的关键部件,其作用是完成含尘气流的气固分离,并把收集下来的物料回送至炉膛,实现灰平衡及热平衡,保证炉内燃烧的稳定与高效。
从某种意义上讲,CFB 锅炉的性能取决于分离器的性能,所以循环床技术的分离器研制经历了三代发展,而分离器设计上的差异标志了CFB 燃烧技术的发展历程。
循环流化床循环流化床循环流化床循环流化床1.1 循环流化床锅炉简介循环流化床(CFB)燃烧技术是一项近二十年发展起来的清洁煤燃烧技术。
流化床燃烧是床料在流化状态下进行的一种燃烧,其燃料可以是化石燃料(如煤、煤矸石)、工农业废弃物(如可燃垃圾、高炉煤气)和各种生物质燃料(如秸秆)。
流化燃烧是一种介于层状燃烧与悬浮燃烧之间的燃烧方式。
煤预先经破碎加工成一定大小的颗粒(一般为<8mm)后置于布风板上,煤经给煤机进入燃烧室,燃烧室内料层的静止高度约在350~500mm,空气则通过布风板由下向上吹送。
毕业设计(论文)循环流化床锅炉工作分析及除尘系统设计

前言进入21世纪,在经济全球化的新形势下,经济的全面发展,几乎所有城市都存在烟尘污染问题,冬季的北方城市尤为重要。
全国二氧化硫排放量逐年增长,并形成南方大面积酸雨期,已发现对森林、土壤、农作物和建筑物造成伤害。
大气中污染物或由它转化成的二次污染物的浓度达到了有害程度的现象,就称为大气污染。
大气污染物主要分为有害气体及颗粒物。
它们的主要来源是燃料的燃烧和工业生产过程。
由于工业的发展、人口增加、森林砍伐等原因,使大气成分发生了很大变化。
这种变化主要表现为二氧化碳、甲烷、氯氟烃等温室气体的含量上升。
通常我们所说的大气污染就是指温室气体急剧增加的现象。
全球大气污染产生的后果有气候变暖,平流层臭氧层变薄,陆地和海洋生物受到污染和产生酸雨等。
这些燃料的燃烧是通过锅炉来完成的,但是先进实用的锅炉除尘技术仍十分缺乏。
中小型工业锅炉和炉窑的烟气治理技术尚需有新的突破,适合我国国情的实用控制技术也十分缺乏。
工业化起点低,生产规模小,污染物排放量大。
如大电厂中小型发电机组的发电煤耗高出发达国家约30%;大量中小型水泥厂的水泥排尘量在3.5公斤/吨的水平。
而这些污染物的排放许多都和锅炉除尘有关,所以应用循环流化床锅炉和好的锅炉除尘系统设计是十分必要的。
循环流化床锅炉也正广泛的应用在各国的各种工业,除尘系统也在慢慢改善,不久的将来大家的生活环境也会变得越来越清新。
作为一名大学生,有责任和义务保护生态环境,针对这个问题本设计选择了除尘系统设计的课题,通过利用专业的理论知识和在外实习的实践知识的运用来完成设计,本设计涉及了除尘器、风机、电动机的选型,管道设计及阻力计算,系统的经济性分析等。
经过计算,烟气能够达到国家要求的标准。
希望本设计能对以后的工作有所帮助。
1 绪论1.1 国内外循环流化床锅炉现状和发展趋势循环流化床锅炉具有高效率、低污染、燃料适应性强、负荷调节比大等优点。
目前,在我国能源与环境的双重压力下,循环流化床锅炉在我国得到了迅速的发展,据电力行业CFB机组技术交流协作网统计,截止到目前为止,我国现有不同容量的循环流化床锅炉将近3000台,约63000MW的容量投入到商业运行中,占电力行业中锅炉总台数的三分之一。
循环流化床锅炉旋风分离器的最新发展与高效运行 刘佳斌
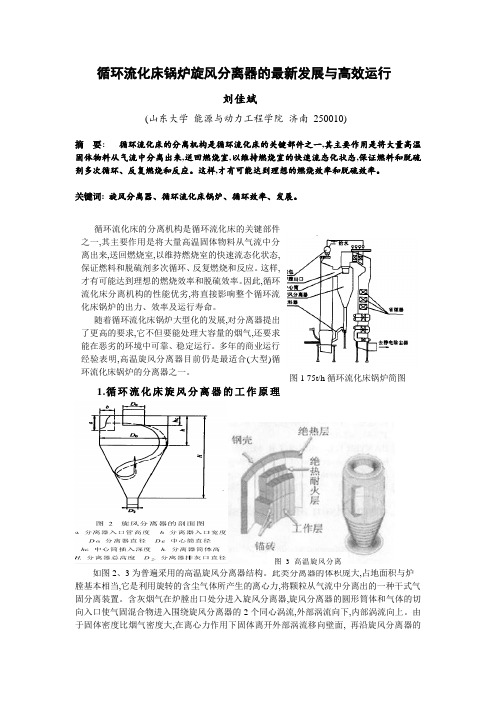
循环流化床锅炉旋风分离器的最新发展与高效运行刘佳斌(山东大学 能源与动力工程学院 济南 250010)摘 要: 循环流化床的分离机构是循环流化床的关键部件之一,其主要作用是将大量高温固体物料从气流中分离出来,送回燃烧室,以维持燃烧室的快速流态化状态,保证燃料和脱硫剂多次循环、反复燃烧和反应。
这样,才有可能达到理想的燃烧效率和脱硫效率。
关键词: 旋风分离器、循环流化床锅炉、循环效率、发展。
图1 75t/h 循环流化床锅炉简图 1.循环流化床旋风分离器的工作原理如图2、3为普遍采用的高温旋风分离器结构。
此类分离器的体积庞大,占地面积与炉 膛基本相当,它是利用旋转的含尘气体所产生的离心力,将颗粒从气流中分离出的一种干式气 固分离装置。
含灰烟气在炉膛出口处分进入旋风分离器,旋风分离器的圆形筒体和气体的切向入口使气固混合物进入围绕旋风分离器的2个同心涡流,外部涡流向下,内部涡流向上。
由于固体密度比烟气密度大,在离心力作用下固体离开外部涡流移向壁面, 再沿旋风分离器的 循环流化床的分离机构是循环流化床的关键部件之一,其主要作用是将大量高温固体物料从气流中分离出来,送回燃烧室,以维持燃烧室的快速流态化状态,保证燃料和脱硫剂多次循环、反复燃烧和反应。
这样,才有可能达到理想的燃烧效率和脱硫效率。
因此,循环流化床分离机构的性能优劣,将直接影响整个循环流化床锅炉的出力、效率及运行寿命。
随着循环流化床锅炉大型化的发展,对分离器提出了更高的要求,它不但要能处理大容量的烟气,还要求能在恶劣的环境中可靠、稳定运行。
多年的商业运行经验表明,高温旋风分离器目前仍是最适合(大型)循环流化床锅炉的分离器之一。
图 3 高温旋风分离壁面滑落,经返料器返回炉膛循环再燃,相对干净的气体通过内部涡流向上移动,由旋风分离器顶部的中心筒出口排出。
烟气经过过热器、省煤器、空气预热器进入尾部烟道,随烟气排出的微细颗粒由锅炉后部的静电除尘器收集。
此类分离器在设计保留了传统的旋风分离器的设计特点,从目前的情况来看,运行情况良好,但由于分离器体积过大,且由于大量采用耐火,保温材料,机组具有热惯性大,易于磨损。
循环流化床锅炉旋风分离器磨损问题

循环流化床锅炉旋风分离器磨损问题摘要本文介绍了循环流化床锅炉旋风分离器的结构特征和作用,通过对旋风分离器磨损问题的分析和研究,找出了磨损的原因和影响磨损严重程度的主要因素。
同时针对以上问题采取了改变原旋风分离器材质、改变旋风分离器的几何尺寸改变旋风分离器的烟气动力场、改变旋风分离器工作环境等措施,达到减少旋风分离器的磨损,延长旋风分离器的使用时间,特别是筒芯的使用时间可以延长了3倍以上,降低了锅炉的故障率,减少了锅炉的检修费用,提高了锅炉运行的经济性。
关键词旋风分离器;磨损原因;解决方法1 概述循环流化床锅炉以其适应燃烧煤种广,特别是能够燃烧低热值的褐煤,近二十多年在我国迅速发展起来,成为小型热电厂和供暖锅炉的首选炉型。
我公司从1992年~2002年先后建设了五台75吨/小时的循环流化床锅炉,在长期的生产运行过程中,我们发现旋风分离器磨损问题非常严重,通过我们的研究和分析,找到了一些解决方法,达到减少旋风分离器的磨损,延长旋风分离器的使用时间,特别是筒芯的使用时间可以延长了3倍以上,降低了锅炉的故障率,减少了锅炉的检修费用,提高了锅炉运行的经济性。
2 旋风分离器的结构特征和作用旋风分离器的结构主要是由外筒和筒芯组成的,挟带煤粉的烟气沿外筒内侧切向进入,在外筒和筒芯之间旋转,靠贯性作用,较大的煤粉颗粒撞向外筒,并沿筒壁下降,返回到炉膛继续燃烧,较小的粉尘随烟气经筒芯进入尾部烟道。
旋风分离器的作用就是风粉分离,这是循环流化床锅炉区别其他炉型的基本特征,有了旋风分离器使飞出炉膛的较大煤粒再返回炉膛,继续燃烧,与沸腾炉相比提高了锅炉的效率,与煤粉锅炉相比节约了碎煤机电耗,因此,循环流化床锅炉近年来得到了迅速发展。
3 旋风分离器存在的问题原设计的旋风分离器外筒和筒芯的材质是普通碳钢,在外筒内侧挂碳化硅砖,在运行的过程中由于温度的变化和磨损因素的影响,经常会发生碳化硅砖脱落的现象,碳化硅砖脱落后,外筒壁磨损非常快,3个月左右的时间就会把外筒壁磨漏,造成被迫停炉事故;筒芯的磨损相对于外筒小一些,一个新的筒芯,壁厚10mm,连续运行时间在一年左右,再坚持运行就要影响到锅炉的效率和出力,因此,循环流化床锅炉旋风分离器防磨问题是必须要认真对待和解决的。
(完整版)循环流化床锅炉运行中的问题本科毕业设计
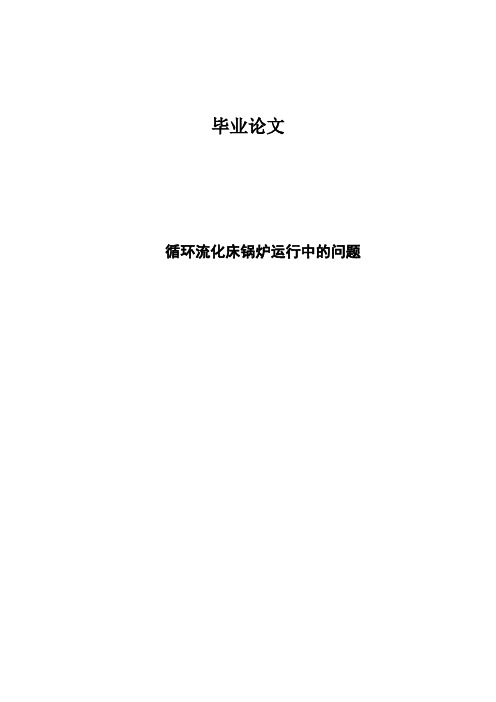
毕业论文循环流化床锅炉运行中的问题网络教育学院毕业设计(论文) 任务书一、毕业设计(论文)题目循环流化床锅炉运行中的问题二、毕业设计(论文)工作自 2012 年12月14日起至2013年2月26日止三、毕业设计(论文)基本要求:指导教师:孙鹏网络教育学院毕业设计(论文)考核评议书论文题目:循环流化床锅炉运行中的问题学科(专业):热能及动力工程申请人:指导教师:孙鹏摘要我国是一个以煤为主要能源的国家,煤在一次能源结构中约占75%。
煤的燃烧带来了严重的污染。
循环流化床锅炉具有高效、低污染的特点,近些年来在世界上和我国得到了迅速的发展。
结合我国国情发展循环流化床锅炉,其意义更为重大。
循环流化床锅炉的应用可以节约煤炭资源;利用劣质煤燃料;清洁能源;灰渣综合利用、保护耕地面积;改善电网调峰能力等。
循环流化床锅炉对于中国未来的能源利用,经济的发展以及社会的进步都有很重要的作用。
我国现有不同容量的循环流化床锅炉近 3000台,约 63000MW 的容量投入商业运机组达到了 13 台。
与此同时,我国在建与拟建的 300MW 循环流化床锅炉机组也已超过了 50 台,超过了世界上中国外的总和;关键词:循环流化床锅炉;耐磨层磨损;运行控制;论文类型:理论研究目录摘要 (V)目录 (VII)1 绪论 (1)1.1 循环流化床锅炉特点 (1)1.2 循环流化床锅炉简介 (1)1.3 循环流化床锅炉特点 (2)2 循环流化床锅炉运行中问题 (5)2.1 循环流化床锅炉运行原理 (5)2.2 循环流化床锅炉运行中问题分析 (7)3 循环流化床锅炉运行事故分析及处理 (9)3.1 循环流化床锅炉流化技术分析 (9)3.2 炉膛爆炸事故 (11)3.3 燃烧熄火 (12)3.4 床料结渣事故 (13)3.5 过热器超温和低温 (14)4 循环流化床磨损问题分析及解决方案 (15)4.1循环流化床锅炉磨损问题概述 (15)4.2 循环流化床金属部件的磨损 (15)4.3 循环硫化床锅炉磨损分布及特点 (16)4.4 循环流化床锅炉防磨措施 (17)4.5 磨损问题综述 (19)5 结论与展望 (20)致谢 (21)参考文献 (23)声明 (27)1 绪论循环流化床锅炉采用流态化的燃烧方式,是介于煤粉炉悬浮燃烧和链条炉固定燃烧之间的燃烧方式,即通常所讲的半悬浮燃烧方式。
- 1、下载文档前请自行甄别文档内容的完整性,平台不提供额外的编辑、内容补充、找答案等附加服务。
- 2、"仅部分预览"的文档,不可在线预览部分如存在完整性等问题,可反馈申请退款(可完整预览的文档不适用该条件!)。
- 3、如文档侵犯您的权益,请联系客服反馈,我们会尽快为您处理(人工客服工作时间:9:00-18:30)。
第一篇:论文题目循环流化床锅炉旋风分离器分析循环流化床锅炉旋风分离器分析自循环流化床燃烧技术出现以来,循环床锅炉在世界范围内得到广泛的应用,大容量的循环床锅炉已被发电行业所接受。
循环流化床低成本实现了严格的污染排放指标,同时燃用劣质燃料,在负荷适应性和灰渣综合利用等方面具有综合优势,为煤粉炉的节能环保改造提供了一条有效的途径主循环回路是循环流化床锅炉的关键,其主要作用是将大量的高温固体物料从气流中分离出来,送回燃烧室,以维持燃烧室稳定的流态化状态,保证燃料和脱硫剂多次循环、反复燃烧和反应,以提高燃烧效率和脱硫效率。
主循环回路是循环流化床锅炉的关键,其主要作用是将大量的高温固体物料从气流中分离出来,送回燃烧室,以维持燃烧室的稳定的流态化状态,保证燃料和脱硫剂多次循环、反复燃烧和反应,以提高燃烧效率和脱硫效率。
主循环回路不仅直接影响整个循环流化床锅炉的总体设计、系统布置,而且与其运行性能有直接关系。
分离器是主循环回路的主要部件,因而人们通常把分离器的形式,工作状态作为循环流化床锅炉的标志。
分离器是主循环回路的关键部件,其作用是完成含尘气流的气固分离,并把收集下来的物料回送至炉膛,实现灰平衡及热平衡,保证炉内燃烧的稳定与高效。
从某种意义上讲,CFB 锅炉的性能取决于分离器的性能,所以循环床技术的分离器研制经历了三代发展,而分离器设计上的差异标志了CFB 燃烧技术的发展历程。
循环流化床循环流化床循环流化床循环流化床1.1 循环流化床锅炉简介循环流化床(CFB)燃烧技术是一项近二十年发展起来的清洁煤燃烧技术。
流化床燃烧是床料在流化状态下进行的一种燃烧,其燃料可以是化石燃料(如煤、煤矸石)、工农业废弃物(如可燃垃圾、高炉煤气)和各种生物质燃料(如秸秆)。
流化燃烧是一种介于层状燃烧与悬浮燃烧之间的燃烧方式。
煤预先经破碎加工成一定大小的颗粒(一般为<8mm)后置于布风板上,煤经给煤机进入燃烧室,燃烧室内料层的静止高度约在350~500mm,空气则通过布风板由下向上吹送。
当空气以较高的气流速度通过料层时,煤粒间的空隙加大,料层膨胀增高,所有的煤粒、灰渣纷乱混杂,上下翻腾不已,颗粒和气流之间的相对运动十分强烈。
这种处于沸腾状态的料床,称为流化床。
这种燃烧方式即为流化燃烧。
流化燃烧后的细小颗粒燃料随高温烟气飞出炉膛,大部分被固态物料分离器捕捉,经返料器送回炉膛循环燃烧,这就是循环流化燃烧技术,采用循环流化燃烧技术生产的锅炉即为循环流化床锅炉。
从已投运流化床锅炉分折,流化床锅炉具有独特的优越性:(1)燃烧效率高:国外循环流化床锅炉,燃烧效率高达99%;我国设计,投运流化床锅炉效率也高达95-98%。
该炉型燃烧效率高的主要原因是煤燃烬率高。
煤粒燃烬率分三种情况分析:较小的颗粒(小于0.04mm),随烟气速度进行流动,它们未达到对流受热面就完全燃烬了,在炉膛高度有效范围内,它们燃烬时间是足够的;对于较大一些煤粒(大于0.6mm),其沉降速度高,只有当其直径进一步燃烧或相互磨擦碎裂而减小时,才能随烟气逸出,较大颗粒经分离器分离返回炉膛循环燃烧;对于中等粒度煤,其燃烧时间要比停留时间长,这给颗粒燃烬提供了足够时间,未燃烬颗粒循环燃烧,达到燃烬的目的。
(2)、煤种适应性强:流化床炉可燃用低热值的劣质烟煤、页炭、炉渣矸石甚至垃圾、秸秆等,对煤种适应性比煤粉炉、层燃炉好。
在循环床锅炉中,通过粒子的循环回燃,炉膛温度能被控制,煤粒着火和燃烬较好。
流化床锅炉设计特点是炉膛高,给煤、布风、出渣等设计都适应劣质煤的燃烧,布风装置将空气分别送入一次风的风室及分布板,送入二次风的风道喷咀。
一次风约占总风量60%,由燃烧室底部送入,二次风由密相区的不同高度送入,给高效燃烧提供了条件。
由于采用了分离回料装置,为劣煤分级燃烧、回燃提供了条件,循环流化床锅炉有两种类型分离装置,一种是惯性分离,一种是旋风分离;现在生产的锅炉多采用一级高温分离器。
国产循环流化床锅炉采用较低流化速度(一般4.5m/s -5.5m /s)、较低循环倍率约(10-20),因此,分离受热面磨损较小。
(3)、添加石灰石,有较高脱硫效果:流化床锅炉脱硫原理是:煤燃烧过程中产生氧化硫与流化床炉燃烧添加剂一氧化钙发生反应,产生的硫酸钙随炉渣排出,脱硫效果可800-900低温下燃烧,可控制NOx 生成。
流化床炉NOx 生成原理是空气中氮气和氧气,在燃烧时产生NO。
在流化床炉燃烧过程中,燃料中90%的氮原素转化成NO2,大约10%的氮元素反应生成NO。
在燃烧过程中,生成的NOx CaO还原,减少了NOx 排放。
(5)、系统简单、运行操作方便。
(6)、灰渣综合利用,前途广泛:由于流化床炉渣可燃物极低(约1-1.5%),而且具有较经济的脱硫效果,增加了灰中硫酸钙含量,这对综合利用提供了有利条件。
灰渣可做各种建材的最好掺合料,水泥行业、制砖行业利用灰渣前途最广泛该炉型推广应用,可减少除灰渣场地,对无灰场条件的中,小城市而言不仅可以大大改善环境条件,而且可以推进建材行业发展,变废为宝,使煤碳发挥综合效益。
1.1.1 循环流化床锅炉结构锅炉采用单锅筒,自然循环方式,总体上分为前部及尾部两个竖井。
前部竖井为总吊结构,四周有膜式水冷壁组成。
自下而上,依次为一次风室、浓相床、悬浮段、蒸发管、高温过热器、低温过热器及高温省煤器。
尾部竖井采用支撑结构,由上而下布置低温省煤器及管式空气预热器。
两竖井之间由立式旋风分离器相连通,分离器下部联接回送装置及灰冷却器。
燃烧室及分离器内部均设有防磨内衬,前部竖井用敖管炉墙,外置金属护板,尾部竖井用轻型炉墙,由八根钢柱承受锅炉全部重量。
锅炉采用床下点火(油或煤气),分级燃烧,一次风率占50—60%飞灰循环为低倍率,中温分离灰渣排放采用干式,分别由水冷螺旋出渣机、灰冷却器及除尘器灰斗排出。
炉膛是保证燃料充分燃烧的关键,采用湍流床,使得流化速度在3.5—4.5m/s,并设计适当的炉膛截面,在炉膛膜式壁管上铺设薄内衬(高铝质砖),即使锅炉燃烧用不同燃料时,燃烧效率也可保持在98—99%以上。
分离器入口烟温在450 度左右,旋风筒内径较小,结构简化,筒内仅需一层薄薄的防磨内衬(氮化硅砖)。
其使用寿命较长。
循环倍率为10—15 左右。
循环灰输送系统主要由回料管、回送装置,溢流管及灰冷却器等几部分组成。
床温控制系统的调节过程是自动的。
在整个负荷变化范围内始终保持浓相床床860度的恒定值,这个值是最佳的脱硫温度。
当自控制不投入时,靠手动也能维持恒定的温床。
保护环境,节约能源是各个国家长期发展首要考虑的问题,循环流化床锅炉正是基于这一点而发展起来,其高可靠性,高稳定性,高可利用率。
最佳的环保特性以及广泛的燃应性,越来越受到广泛关注,完全适合我国国情及发展优势。
1.1.2 当固体颗粒中有流体通过时,随着流体速度逐渐增大,固体颗粒开始运动,且固体颗粒之间的摩擦力也越来越大,当流速达到一定值时,固体颗粒之间的摩擦力与它们的重力相等,每个颗粒可以自由运动,所有固体颗粒表现出类似流体状态的现象,这种现象称为流态化。
对于液固流态化的固体颗粒来说,颗粒均匀地分布于床层中,称为“散式”流态化。
而对于气固流态化的固体颗粒来说,气体并不均匀地流过床层,固体颗粒分成群体作紊流运动,床层中的空隙率随位置和时间的不同而变化,这种流态化称为“聚式”流态化。
循环流化床锅炉属于“聚式”流态化。
固体颗粒(床料)、流体(流化风)以及完成流态化过程的设备称为流化床。
1.1.3 临界流化速度对于由均匀粒度的颗粒组成的床层中,在固定床通过的气体流速很低时,随着风速的增加,床层压降成正比例增加,并且当风速达到一定值时,床层压降达到最大值,该值略大于床层静压,如果继续增加风速,固定床会突然解锁,床层压降降至床层的静压。
如果床层是由宽筛分颗粒组成的话,其特性为:在大颗粒尚未运动前,床内的小颗粒已经部分流化,床层从固定床转变为流化床的解锁现象并不明显,而往往会出现分层流化的现象。
颗粒床层从静止状态转变为流态化进所需的最低速度,称为临界流化速度。
随着风速的进一步增大,床层压降几乎不变。
循环流化床锅炉一般的流化风速是倍的临界流化速度。
1.1.4 影响临界流化速度的因素(1)料层厚度对临界流速影响不大。
(2)料层的当量平均料径增大则临界流速增加。
(3)固体颗粒密度增加时临界流速增加。
提高循环流化床锅炉热效率的措施提高循环流化床锅炉热效率的措施提高循环流化床锅炉热效率的措施提高循环流化床锅炉热效率的措施适当提高燃烧温度,碳粒子的燃烬时间与燃烧温度有关,提高燃烧温度能明显的缩短碳粒子的燃烬时间。
如下式16 exp(10 77 其中:τp为碳粒子的燃烬时间s;T 为燃烧温度;dp为碳粒子直径cm。
当τp 从800升高到950时,碳粒子的燃烬时间缩短6 倍左右。
当燃烧温度从870提高到920,燃烧温度增加50 时,锅炉燃烧效率提高了2 个百分点左右。
降低飞灰含碳量提高锅炉燃烧效率,影响飞灰含碳量的因素有如下方面:燃烧温度、煤的种类、分离飞灰的循环倍率、燃烧室上部燃烧偏斜、燃烧氧量的供给、分离器的分离效率、除尘灰再循环燃烧。
(1)温度的影响:经试验证明当燃烧温度从900提高到950 时,飞灰含碳量从22.5%降到10%左右,降低了12.5 个百分点。
燃烧温度提高1,飞灰含碳量降低0.25 个百分点,这个影响程度的不同是由煤的燃烧反应性差异所决定的。
(2)挥发分低的难燃煤种,飞灰含碳量较高,挥发分高的易燃煤种,飞灰含碳量较低,一般无烟煤的飞灰含碳量比烟煤要高5-10 个百分点。
(3) 分离灰循环倍率的影响:1-1从图上可以看出分离灰循环倍率为5 时,飞灰含碳量为12.5%左右,而分离灰循环倍率从提高到4,飞灰含碳量降低约2.5个百分点,7 提高到8 时,降低了1 个百分点,14 18时,只降低了0.5 个百分点,离灰循环倍率在2-6 之间变化,对飞灰含碳量的影响是最有效的。
(4)器分离效率:分离器的分离效率与分离灰循环倍率的关系为为分离灰循环倍率,ηc为分离器分离效率,Ay 为燃煤灰分含量,α灰份额。
分离效率高,分离灰循环倍率大;煤中灰份含量高,分离灰循环倍率大;燃烧室出口飞灰份额大,分离灰循环倍率高。
(5)优化燃烧调整和控制:提高燃烧效果,900 -950;改善脱硫效果,830-880;控制NOX 的生成量200mg/Nm3-400 mg/Nm3 间,(830-930);烟气成分包括O2、NO2(NO)、N2O、SO2(SO3)、CO2、CO、N2等,根据O2,CO 和CO2 含量控制空气量,根据SO2 含量控制石灰石加入量,根据NOX 含量控制燃烧温度。
降低床底渣含碳量,粗粒子在浓相床内的停留时间:Hb 静止床料高度,m;Fd 布风板面积,m2;ρb--静止床料的堆积密度,kg/m3;为燃煤消耗量,kg/h;δ为燃煤中粗粒子的份额。