环己酮的生产现状及预测
2024年环己酮市场分析现状

2024年环己酮市场分析现状简介环己酮是一种重要的有机化工原料,广泛应用于制药、农药、染料、涂料等行业。
本文将对环己酮市场的现状进行分析,包括市场规模、市场需求、竞争格局等方面内容。
市场规模环己酮市场近年来呈现稳步增长的趋势。
据统计数据显示,2019年全球环己酮市场规模约为xxx吨,预计到2025年将达到xxx吨。
市场的快速增长主要得益于能源、化工等领域的高速发展,对环己酮的需求量不断增加。
市场需求环己酮在多个领域中具有广泛的应用。
首先,在制药领域,环己酮是合成多种药物的重要原料,如抗生素、镇痛药等;其次,在农药领域,环己酮可以用于制造多种杀虫剂和除草剂;此外,环己酮还可用作染料和涂料的溶剂,具有广泛的用途。
随着医药、农药、化工等行业的发展,环己酮市场的需求将会进一步增加。
竞争格局目前,环己酮市场竞争格局相对稳定。
全球主要环己酮生产企业包括公司A、公司B、公司C等。
这些企业拥有先进的生产设备和技术,并且具备一定的规模优势。
此外,一些新兴企业也进入了环己酮市场,不断推动市场竞争的加剧。
在市场竞争中,企业除了在产品质量和价格方面进行差异化竞争外,还需要注重创新,提高产品附加值,以获取更大市场份额。
市场趋势随着环保意识的不断提高,环己酮市场将面临新的发展趋势。
首先,环保型环己酮逐渐受到关注和推广。
相比传统环己酮,环保型环己酮具有更低的挥发性和毒性,对环境和人体健康的影响较小。
其次,随着新兴行业的发展,对环己酮的需求将不断增加,如新能源、新材料等领域。
此外,一些新的合成工艺和生产技术的应用,也将推动环己酮市场的发展。
结论环己酮市场具有广阔的发展前景。
在需求不断增加的情况下,企业应通过不断创新和提高产品质量,加强在市场中的竞争力。
同时,关注环保型环己酮的发展趋势,并积极参与环保技术应用,将有助于企业在未来市场中取得更好的竞争优势。
2023年环己酮行业市场调研报告

2023年环己酮行业市场调研报告
环己酮是一种广泛使用的有机溶剂,可用于涂料、印刷油墨、塑料、合成树脂、纤维素、纸张、石油产品、农药和药物等领域。
近年来,随着全球化的发展和经济的增长,环己酮市场也得到了增长。
一、环己酮市场现状
据市场研究机构统计数据,目前全球环己酮市场的年产值约为30亿美元。
主要市场
包括亚洲、欧洲和北美。
其中,亚洲地区占据了最大的市场份额,占到了全球环己酮市场的35%以上,主要是由于中国、印度和日本等国家的需求增长。
欧洲和北美市
场份额则分别为30%和25%左右。
二、环己酮市场趋势
1. 环保趋势
随着全球环保意识的提高,越来越多的国家和地区开始实施环保政策。
环己酮作为一种有机溶剂,受到了环保政策的影响。
未来环己酮市场将逐渐向环保型产品发展。
2. 新技术的应用
随着科技的发展,环己酮市场也会受到新技术的影响。
例如,使用合成生物学和基因编辑技术开发新的工业降解酶,可极大地降低环己酮的生产成本。
3. 产业整合
在全球经济增长放缓的情况下,环己酮市场也不可避免地面临着竞争激烈的局面。
产业整合将是环己酮市场的一个重要趋势。
一些大型企业将通过企业并购、合作等各种形式,进一步扩大生产规模和市场份额。
三、环己酮市场前景分析
随着全球化的进一步发展,环己酮市场将进一步增长。
经济实力强的发展中经济体将继续是环己酮市场的重要驱动力。
针对新技术的研发和环保政策的实施,环己酮市场的需求将逐渐向环保型产品转移。
随着企业整合的加剧,市场份额将进一步集中。
环己酮行业供需现状分析,国内生产能力不断扩张,进口量持续下降「图」

环己酮行业供需现状分析,国内生产能力不断扩张,进口量持续下降「图」环己酮是一种重要的有机化工原料,是制造己内酰胺和己二酸等的主要中间体,进而用于尼龙6(PA6)和尼龙66(PA66)及其他树脂的合成。
此外,环己酮作为性能优异的高档溶剂,在涂料、油墨、制药、农药、胶黏剂、感光材料等行业也被广泛应用。
目前,国内环己酮生产工艺路线按其生产原料分主要有苯酚法、环己烷氧化法和环己烯水合法。
环己酮的主要生产工艺分析资料来源:华经产业研究院整理近年来,国内环己酮产量和表观消费量呈现快速增长势头,2019年国内环己酮产量418万吨,表观消费量416.2万吨。
预计随着国内己内酰胺和己二酸产能进一步增加,国内环己酮消费量将继续增加,2020年将达479万吨。
2015-2019年国内环己酮产量及表观消费量资料来源:公开资料整理随着国内环己酮装置不断兴建,生产能力不断扩张,进口量持续下降。
从2011年开始,我国已成为环己酮的净出口国。
2019年国内环己酮出口量27.5千吨,比2018年大幅增长4.5倍,进口量9.3千吨。
2017—2018年环己酮供需平衡打破是导致2019年环己酮进出口波动较大的主要原因。
2015-2019年国内环己酮进口量及出口量资料来源:公开资料整理更多内容相关报告:华经产业研究院发布的《2020-2025年中国环己酮行业发展趋势预测及投资规划研究报告》环己酮在我国主要用于生产己内酰胺和己二酸。
该两项目用途占环己酮总消费量的近80%。
目前国内环己酮主要生产厂家主要有中国石油辽阳石油化纤公司、辽宁华峰股份有限公司、内蒙古庆华集团有限公司、石家庄焦化集团有限责任公司、河北旭阳焦化有限公司、唐山中浩化工有限公司等。
2019年国内环己酮主要生产厂家资料来源:公开资料整理随着国内己内酰胺和己二酸能力的不断增长,国内环己酮的需求量还将不断增长。
预计到2020年,我国环己酮消耗总量将达到270万t左右,其中80%以上用于生产己内酰胺和己二酸。
2024年环己酮市场发展现状

2024年环己酮市场发展现状简介环己酮是一种有机化合物,化学式为C6H10O,是一种无色、具有刺激性气味的液体。
环己酮在多个行业中被广泛应用,包括化工、医药、农药等领域。
本文将探讨环己酮市场的发展现状。
环己酮的用途环己酮具有多种用途,其中最主要的是作为溶剂。
由于其良好的溶解性能,环己酮常用于油漆、涂料、胶水等工业产品的制造过程中。
此外,环己酮还可以用作氨基酸和杀菌剂的合成原料,在农业和医药领域中具有重要的应用价值。
市场规模根据市场研究数据,环己酮市场在过去几年中稳步增长并呈现良好的发展势头。
预计未来几年,环己酮市场规模将继续保持增长。
这一增长主要受到以下几个因素的影响:1.工业需求增加:随着全球经济的发展和工业生产的增加,对环己酮的需求量也在逐步增加。
特别是在油漆、涂料等行业中,环己酮的应用日益广泛。
2.农药市场需求增长:环己酮在农药中的应用正在不断扩大。
随着全球农业的发展和农药使用的增加,对环己酮的需求也在逐年增长。
3.新兴市场需求增加:一些发展中国家和地区的经济正在快速增长,对环己酮的需求也在不断增加。
这些新兴市场的需求增长有助于推动全球环己酮市场的发展。
市场竞争态势环己酮市场竞争激烈,主要供应商包括化工公司、制药公司等。
这些公司在产品质量、价格、服务等方面进行竞争,以争夺更多的市场份额。
此外,环己酮市场还面临一些挑战。
首先,环保意识的提高使得对环己酮的使用受到一定限制,要求更加环保的替代品。
其次,价格波动和原材料供应不稳定也影响了市场的发展。
市场前景和机遇尽管环己酮市场面临一些挑战,但仍存在许多机遇和潜力。
随着全球经济的不断发展和工业生产的增加,对环己酮的需求将继续增长。
此外,环己酮在新兴市场和农药行业中的应用前景较好,有望成为市场增长的关键驱动因素。
同时,随着环保意识的提高,对环保替代品的需求也在增加。
这为开发更环保的环己酮替代品提供了机遇。
未来的市场竞争将更多地集中在产品的环保性和创新性上。
2023年环已酮行业市场分析现状
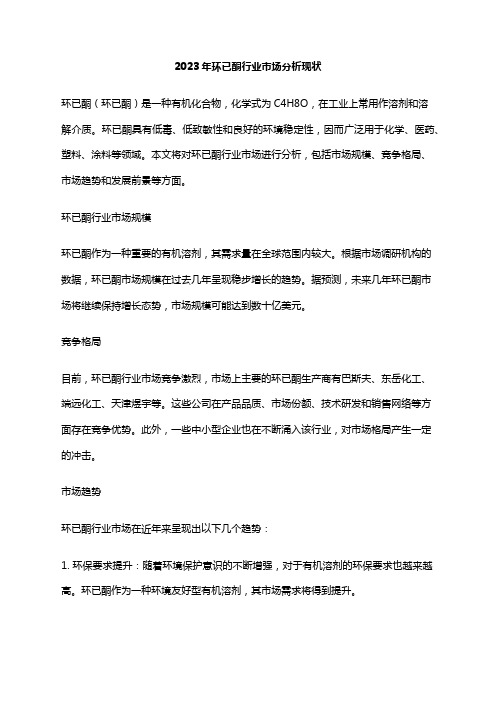
2023年环已酮行业市场分析现状环已酮(环已酮)是一种有机化合物,化学式为C4H8O,在工业上常用作溶剂和溶解介质。
环已酮具有低毒、低致敏性和良好的环境稳定性,因而广泛用于化学、医药、塑料、涂料等领域。
本文将对环已酮行业市场进行分析,包括市场规模、竞争格局、市场趋势和发展前景等方面。
环已酮行业市场规模环已酮作为一种重要的有机溶剂,其需求量在全球范围内较大。
根据市场调研机构的数据,环已酮市场规模在过去几年呈现稳步增长的趋势。
据预测,未来几年环已酮市场将继续保持增长态势,市场规模可能达到数十亿美元。
竞争格局目前,环已酮行业市场竞争激烈,市场上主要的环已酮生产商有巴斯夫、东岳化工、端远化工、天津煜宇等。
这些公司在产品品质、市场份额、技术研发和销售网络等方面存在竞争优势。
此外,一些中小型企业也在不断涌入该行业,对市场格局产生一定的冲击。
市场趋势环已酮行业市场在近年来呈现出以下几个趋势:1. 环保要求提升:随着环境保护意识的不断增强,对于有机溶剂的环保要求也越来越高。
环已酮作为一种环境友好型有机溶剂,其市场需求将得到提升。
2. 新应用领域的开发:除了传统的化学、医药和塑料等领域,环已酮还有一些新的应用领域值得开发,如新能源材料和电子器件等。
随着这些领域的不断发展,对环已酮的需求将进一步增加。
3. 多元化产品需求:市场上对环已酮的需求呈现多元化的趋势,不仅仅是普通的环已酮产品,还有一些具有特殊功能的环已酮产品。
市场上的环已酮生产企业应不断提升产品的质量和功能,以满足不同客户的需求。
发展前景虽然环已酮行业市场发展前景良好,但也面临一些挑战。
环保要求的提升、技术创新和市场竞争都是环已酮行业所面临的挑战。
然而,随着环境保护意识的增强和新应用领域的开发,环已酮行业仍然具有较大的发展潜力。
总的来说,环已酮行业市场规模大,竞争激烈,市场趋势向环保、多元化和新应用领域的方向发展。
在发展前景方面,环已酮行业仍然具有较大的发展潜力,但也需要企业不断提高产品质量和技术水平,适应市场需求的变化。
2024年环已酮市场需求分析

2024年环已酮市场需求分析1. 简介本文对环已酮市场需求进行分析,旨在帮助了解环已酮行业的现状和未来发展趋势。
环已酮是一种重要的化工原料,广泛应用于医药、农药、染料等领域。
通过深入研究市场需求,可以帮助企业制定有效的市场推广策略,提高市场份额和竞争力。
2. 市场规模根据市场调研数据显示,近年来环已酮市场规模呈现稳步增长的趋势。
环已酮作为一种重要原料,广泛应用于医药行业的药物合成和农药制备,随着医药和农药市场的增长,环已酮需求也在不断提升。
此外,环已酮还被应用于染料、涂料、塑料等行业,这些领域的发展也为环已酮市场增加了需求。
3. 市场驱动因素环已酮市场需求增长的主要驱动因素包括:3.1. 合成药物需求增加随着人口老龄化和人们对健康的关注增强,合成药物市场持续增长。
环已酮作为众多药物合成过程中的重要原料,其需求也随之增加。
3.2. 农药需求增长全球农业生产的规模不断扩大,为了提高农作物产量和质量,农药的需求增长迅速。
环已酮广泛应用于农药的制备过程,市场需求与农药市场密切相关。
3.3. 环境保护要求环境保护意识日益增强,对环境友好型产品的需求也在提升。
环已酮具备优良的环境友好性,在染料、涂料、塑料等行业中得到广泛应用。
4. 市场竞争格局目前,环已酮市场存在着一定的竞争,行业内主要企业包括国内外的生产厂商。
这些企业竞争激烈,不断推出新产品、降低成本、提高品质,以吸引客户并获得市场份额。
5. 市场趋势和机遇未来环已酮市场的发展趋势和机遇主要包括:5.1. 技术升级和创新随着科技的进步,环已酮的合成技术将不断改进,使生产成本和污染减少。
同时,环已酮的新应用领域也将不断涌现,为企业提供新的发展机会。
5.2. 市场多元化随着环已酮在医药、农药、染料、涂料、塑料等领域的应用,市场需求呈现多元化趋势。
企业可以根据不同领域的需求差异,进行定制化生产和市场开拓。
5.3. 国际市场扩张环已酮是一种广泛应用于全球市场的化工原料,随着全球市场的快速增长,企业可以通过拓展国际市场来获得更大发展空间。
2023年环己酮行业现状:环己酮上游产品市场上升
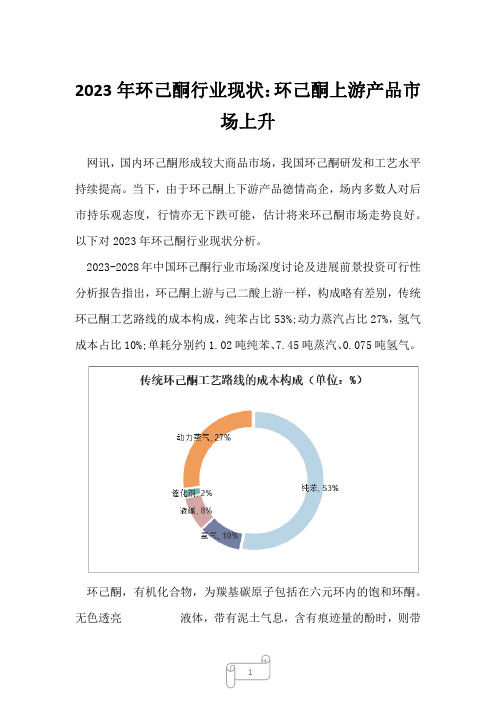
2023年环己酮行业现状:环己酮上游产品市场上升网讯,国内环己酮形成较大商品市场,我国环己酮研发和工艺水平持续提高。
当下,由于环己酮上下游产品德情高企,场内多数人对后市持乐观态度,行情亦无下跌可能,估计将来环己酮市场走势良好。
以下对2023年环己酮行业现状分析。
2023-2028年中国环己酮行业市场深度讨论及进展前景投资可行性分析报告指出,环己酮上游与己二酸上游一样,构成略有差别,传统环己酮工艺路线的成本构成,纯苯占比53%;动力蒸汽占比27%,氢气成本占比10%;单耗分别约1.02吨纯苯、7.45吨蒸汽、0.075吨氢气。
环己酮,有机化合物,为羰基碳原子包括在六元环内的饱和环酮。
无色透亮液体,带有泥土气息,含有痕迹量的酚时,则带有薄荷味。
不纯物为浅黄色,随着存放时间生成杂质而显色,呈水白色到灰黄色,具有剧烈的刺鼻臭味。
与空气混合爆炸极与开链饱和酮相同。
环己酮致癌证据不足,在工业上主要用作有机合成原料和溶剂,例如它可溶解硝酸纤维素、涂料、油漆等。
现从四大市场状况来分析2023年环己酮行业现状。
(1)环己酮宏观经济。
2000年国内外宏观济状况较好,己内酰胺的下游民用丝、工业丝市场需求旺盛,从而促使环己酮、己内酰胺的价格上升;2022年世界经济疲软,需求不旺,己内酰胺、环己酮的价格相应走低。
(2)环己酮与己内酰胺市场亲密相关。
环己酮最主要的用途是作为制造己内酰胺的原料,这主要是由于大型己内酰胺装置均与环己酮装置配套,当消失己内酰胺价格变化较大时,己内酰胺生产厂家将考虑综合经济效益,以确定其中间产品环己酮进入市场的商品量,供求关系的变化将影响环己酮的价格。
2000年己内酰胺价格坚挺,国内市场价格在14500元/吨,环己酮也表观良好,基本在10500元/吨;但2022~2022年底,己内酰胺价格大幅度下降,最低只有9000元/吨左右,环己酮的价格也只有6000元/吨左右。
(3)石油苯价格导致环己酮下跌。
2023年环己酮行业市场分析现状

2023年环己酮行业市场分析现状环己酮是一种重要的有机溶剂,具有广泛的应用领域,包括化工、塑料、合成纤维、油漆、印刷油墨等。
在化工行业中,环己酮主要用于涂料、树脂、胶黏剂的生产,占据很重要的地位。
本文将对环己酮的市场分析现状进行详细介绍。
一、行业市场规模及增长趋势环己酮是一种广泛应用的化工原料,市场规模较大且保持较高的增长率。
根据市场研究机构的数据显示,全球环己酮市场规模在过去几年内以每年约3%的速度增长,预计到2025年将超过10亿美元。
主要驱动因素包括建筑和汽车行业的增长,以及对环保和高性能产品的需求增加。
二、行业市场竞争格局目前,环己酮市场竞争格局较为集中,主要的市场参与者包括化工巨头和一些中小型企业。
在全球范围内,巴斯夫、索尔维、苏美达等大型企业占据较大市场份额,并拥有较高的技术实力和生产能力。
此外,中国和印度等新兴市场也成为环己酮市场的重要参与者,一些本土企业逐渐崛起,正在逐步改变市场格局。
三、环己酮市场的应用领域环己酮在化学及其他行业中有着广泛的应用。
在涂料领域,环己酮主要用于溶解调整和增加膜形成,改善涂层的光泽和稳定性。
在塑料领域,环己酮可作为增塑剂使用,提高塑料的柔韧性和耐久性。
在合成纤维领域,环己酮可用作溶剂,用于聚合物的合成。
此外,环己酮还可以用于油漆、印刷油墨和胶黏剂等领域。
随着全球化和科技进步的不断推进,环己酮的应用领域将进一步扩大。
四、环己酮市场面临的挑战与机遇环己酮市场面临着一些挑战与机遇。
首先,环己酮的原材料价格波动较大,原材料的供需关系对产品价格和利润率产生重要影响。
其次,环境法规的加强对环己酮产业的发展提出了更高要求,需要研发和应用更环保的生产技术和产品。
另外,随着工业化进程的推广,新兴市场的快速增长为环己酮市场提供了新的机遇,如中国、印度等新兴市场的需求不断增加,将带动行业市场的增长。
总之,环己酮作为一种重要的有机溶剂,在化工、塑料、合成纤维、油漆、印刷油墨等领域具有广泛的应用。
2024年环己酮市场需求分析

2024年环己酮市场需求分析引言环己酮,也被称为己内酮,是一种无色液体化合物,具有特殊的酮类结构。
它具有许多重要的应用,如溶剂、溶解剂、原料等。
本文将对环己酮市场需求进行分析,以了解其当前的市场需求情况。
环己酮市场概览环己酮是广泛应用于化工、制药和农业等领域的重要化学品。
它在溶剂和溶解剂方面具有广泛的用途,可用于油漆、胶水、塑料等制造业中。
此外,环己酮还可以作为制药行业中合成药物的重要原料。
随着化工行业的发展和全球市场需求的增加,环己酮市场的前景非常广阔。
市场需求分析1. 化工行业需求增长随着全球化工行业的发展,环己酮作为重要的溶剂和溶解剂在该行业中的需求越来越大。
制造业的快速增长和全球市场对高质量产品的需求,加速了环己酮市场的发展。
尤其是在亚洲地区,尤其是中国,化工行业的增长对环己酮市场的需求起到了重要的推动作用。
2. 制药行业的需求稳定增长环己酮作为制药行业中的重要原料,其在药物合成中的应用不可替代。
随着全球人口的增长和人们对健康问题的关注度提高,制药行业的需求也在不断增长。
环己酮的稳定需求将继续推动市场的发展。
3. 环己酮替代品的竞争尽管环己酮市场前景看好,但其仍然面临来自替代品的竞争。
一些新型的溶剂或溶解剂正在逐渐进入市场,与环己酮竞争。
这些替代品可能在某些方面具有更好的性能或更低的成本,因此对环己酮的需求可能会受到一定影响。
市场前景与发展趋势环己酮市场的前景非常广阔。
随着全球化工行业和制药行业的快速发展,环己酮的需求将持续增长。
此外,环己酮的广泛用途也为其市场发展提供了更多可能性。
然而,替代品的竞争也需要引起我们的重视。
为了在竞争激烈的环境中保持竞争力,环己酮生产商需要优化生产工艺,提高产品质量,降低成本,并不断创新。
结论环己酮作为化工和制药行业的重要化学品,在全球市场中具有巨大的市场需求。
随着全球化工和制药行业的发展,环己酮市场的前景非常广阔。
然而,市场竞争激烈,替代品的出现对环己酮的需求可能会产生一定影响。
2024年环已酮市场环境分析

2024年环已酮市场环境分析1. 简介环已酮(Cyclohexanone)是一种常用的有机化学品,具有广泛的应用领域。
本文将对环已酮市场环境进行分析,包括市场规模、市场竞争、市场趋势等方面。
2. 市场规模分析环已酮作为一种重要的化工原料,在市场上有着广泛的应用。
根据行业数据,环已酮市场呈现稳定增长的趋势。
预计在未来几年内,环已酮市场的规模将进一步扩大。
3. 市场竞争分析环已酮市场存在着较高的竞争程度。
目前市场上存在多家环已酮生产厂家,产品供应相对充足。
竞争主要体现在产品质量、价格、服务等方面。
在产品质量方面,具有高纯度、低杂质的环已酮在市场上具有竞争优势。
价格方面,市场上价格浮动较大,供应商之间通过降低价格来争夺市场份额。
此外,供应商还通过提供定制化服务和技术支持等方式来增加竞争力。
4. 市场趋势分析未来环已酮市场的发展趋势有以下几点:4.1 技术进步促进行业发展随着科技的不断进步,环已酮的生产工艺不断改进,生产效率提升,产品质量不断提高。
这将为环已酮市场的发展提供有利条件。
4.2 环境意识的增强随着全球环保意识的增强,环已酮市场将受到更加严格的环保法规的监管。
环保要求的提升将促使企业加强技术创新和环境治理,提高环境友好型产品的市场份额。
4.3 新兴领域的应用拓展环已酮作为有机合成中的重要原料,在多个领域都有应用潜力。
例如,医药、染料、香料等行业都有可能成为环已酮的新的应用领域。
随着新技术和新产品的不断涌现,新兴领域的应用拓展将带动环已酮市场的增长。
5. 总结综上所述,环已酮市场呈现出稳定增长的趋势。
市场竞争激烈,供应商之间在产品质量、价格、服务等方面进行竞争。
未来环已酮市场将受到技术进步、环保意识增强和新兴领域的应用拓展等因素的影响。
企业应密切跟踪市场动态,不断创新和改进,以保持竞争优势。
环己酮的生产现状及预测

环己酮的生产现状及预测3.1 世界环己酮生产现状及预测3.1.1 世界环己酮的发展及现状分析环己酮为生产PA6、PA66的原料,也是生产己二酸的原料之一。
世界上主要是以苯为原料来合成的。
1960年德国BASF公司采用环己烷氧化法建成大型环己酮生产装置,使环己烷氧化技术得以迅速发展,并导致聚酞胺纤维的大规模发展。
1967年,荷兰国家矿业公司(DSM)研究的苯酚加氢一步制取环己酮方法实现了工业化,但是,由于苯酚产量小,且价格偏高,用苯酚作为原料生产环己酮受到了限制。
1995年欧美经济复苏,自用品增加,国际市场民用丝、工业丝生产恢复,对己内酰胺的需求量增加,从而促使环己酮、己内酰胺价格上升。
1997年亚洲金融危机的影响,化工市场整体效益下滑,特别是消耗苯的产品如苯酚、苯胺、环己酮、硝基苯、氯苯等市场平淡;苯乙烯虽然国内市场缺口很大,但由于进口过多,市场也处于颓势。
1998-2000年美国进口的环己酮主要来自于荷兰和斯洛伐克,美国的环己酮主要出口到远东、加拿大和拉丁美洲。
2003年,乌兹别克斯坦也购买了48吨含量为99.9%的巴陵牌环己酮优级品,使该产品首次打入中亚市场。
在国外,纯净环己酮基本上是作为生产己内酰胺的中间产物而存在的,在国外,环己酮装置均与己内酰胺相配套,因此很少单独统计环己酮的产能、产量、消费量等,用环己酮路线生产1吨己内酰胺约消耗环己酮0.897吨左右,所以我们通过己内酰胺的统计数据间接了解国外环己酮的生产状况,通过下表我们可以了解环己酮的国外生产情况。
此外,由于环己酮是己二酸的中间产物,有时己二酸生产厂家也生产环己酮,如日本旭化成,其环己酮生产能力为15万吨/年,还有中国的辽阳石化公司、博汇化工、海力化工等。
表3.1 2004-2010年国外环己酮产品装置状况单位:万吨/年3.1.2 世界环己酮未来发展预测全球主要新增产能都在亚洲,尤其是中国。
日本宇部原计划对泰国己内酰胺生产工厂进行扩建,其中己内酰胺生产工厂产能计划到2010年扩至13万吨/年。
2024年环己酮市场前景分析

2024年环己酮市场前景分析摘要本文主要分析了环己酮的市场前景,包括市场规模、竞争状况以及发展趋势。
通过对行业内相关因素的考察,我们认为环己酮市场在未来几年将保持稳定增长态势,而且前景非常有望。
1. 引言环己酮是一种重要的有机化学品,被广泛应用于化工、医药和农药等领域。
随着全球经济的发展和技术的进步,环己酮市场也逐渐显示出巨大的潜力。
本章将对环己酮市场的概况进行介绍。
2. 市场规模环己酮市场的规模受多种因素影响,包括供需情况、价格变动和应用领域扩展等。
根据市场调研数据显示,环己酮市场的年均复合增长率约为X%,市场规模预计将在未来几年内达到XX亿美元。
3. 竞争状况环己酮市场存在较为激烈的竞争,主要来自于国内外相关企业。
近年来,行业内竞争更加激烈,主要表现为产品质量、价格和服务等方面的竞争。
优质产品和服务将成为企业竞争的关键要素。
4. 发展趋势环己酮市场的发展趋势主要受以下因素影响:4.1 产业政策政府对环己酮行业的政策支持将对市场前景起到重要作用。
例如,政府鼓励环保、绿色生产等政策,将促使环己酮市场朝着更加可持续发展的方向发展。
4.2 技术创新随着科技的不断进步,新的生产技术和工艺不断涌现,将推动环己酮市场的发展。
例如,高效催化剂的研发,可以提高环己酮的生产效率和质量。
4.3 应用领域扩展环己酮的应用领域不断扩展,包括化工、医药和农药等行业。
随着这些领域的发展,环己酮市场的需求也将持续增长。
5. 市场风险尽管环己酮市场前景看好,但仍存在一定的市场风险,主要有以下几个方面:5.1 原材料价格波动环己酮的生产原料价格波动较大,不稳定因素可能会对市场造成影响。
企业需要制定合理的原材料采购策略,以降低成本风险。
5.2 环保压力环境保护要求的提高,对环己酮行业提出了更高的要求,企业需要加强环保措施,确保生产过程环保合规。
6. 结论通过对环己酮市场的分析,我们可以得出以下结论:环己酮市场具有稳定增长的潜力,未来几年将保持较为良好的发展态势。
2023年环已酮行业市场发展现状

2023年环已酮行业市场发展现状近年来,环已酮(Cyclohexanone)作为一种重要的有机化工原料,在化工、塑料、橡胶、杀菌剂等领域得到了广泛的应用,市场需求量也在不断增大。
本文将从国内外环已酮市场供需情况、市场价格、行业主要企业和未来发展趋势等方面进行分析。
一、国内外环已酮市场现状1.国内市场根据市场调研机构全球信息发布的报告,近年来,我国环已酮市场需求呈现出高速增长的趋势,需求量逐年提高。
其中,环已酮在亚洲地区是市场需求最大的国家之一。
目前,中国环已酮产能较大的和主要的生产商有赣锋化工、华鸿化学、泰力化学等,这些生产商产能占国内环已酮总产能的较大比例。
2.国际市场在国际市场上,环已酮的主要需求市场集中在欧洲和北美地区。
其中,美国、德国、日本和中国是环已酮市场需求最大的国家。
在这些国家,环已酮主要应用于生产塑料、橡胶、化学纤维、清漆、农药、有机合成和制药等领域。
二、环已酮市场价格环已酮市场价格是市场供求关系的体现,是衡量市场需求和生产能力关系的重要指标。
在国内,环已酮市场价格受到生产成本、市场需求及国际市场价格影响。
在近几年,由于市场需求量大,使环已酮价格呈持续上涨趋势。
三、行业主要企业1.赣锋化工赣锋化工是一家专业生产环已酮的化工企业,其生产环已酮的工艺已达到国内先进水平,并获得了国家二级安全生产标准化企业证书。
公司已成为中国国内环已酮行业的领先企业之一。
2.华鸿化学华鸿化学是一家集研发、生产、销售于一体的化工企业,主要生产环已酮、环己酮、环丙烷等一系列有机化工产品。
公司产品具有较高市场占有率,在行业内有一定的知名度。
3.泰力化学泰力化学是一家生产环已酮、环己酮等一系列有机化工原料的企业,拥有千吨级的生产能力。
公司产品出口众多,客户遍布世界各地。
四、未来发展趋势1.市场需求持续增长环已酮作为有机化工原材料的重要组成部分,在化工、塑料、橡胶、杀菌剂等领域得到了广泛的应用。
随着新型材料、新工艺和新技术的不断出现和应用,环已酮市场需求将持续增长。
2024年环已酮市场规模分析

2024年环已酮市场规模分析摘要本文对环已酮市场规模进行了分析。
首先介绍了环已酮的基本信息和应用领域。
然后,通过调查研究和市场数据分析,对环已酮市场规模进行了预测和分析。
最后,提出了环已酮市场发展的建议。
1. 引言1.1 研究背景环已酮是一种重要的有机化合物,广泛应用于医药、农药、香精香料等领域。
随着人们对环保和健康的重视,环已酮市场需求不断增长,市场规模也在不断扩大。
因此,对环已酮市场规模进行深入分析具有重要意义。
1.2 研究目的本文旨在对环已酮市场规模进行全面分析,包括市场现状、市场发展趋势以及市场规模预测。
通过对市场规模的分析,可以为环已酮相关企业提供决策参考,推动市场的健康发展。
2. 环已酮的应用领域环已酮作为一种重要的有机化合物,具有广泛的应用领域,主要包括以下几个方面:•医药领域:环已酮作为一种重要的原料药,在抗生素、抗肿瘤药物等方面有着广泛的应用。
•农药领域:环已酮作为一种杀虫剂,可以有效防治农田虫害,提高农作物产量。
•香精香料领域:环已酮具有独特的香气,广泛应用于食品、化妆品等领域,为产品增添香味。
3. 2024年环已酮市场规模分析3.1 市场现状根据市场调查数据显示,近年来环已酮市场规模不断扩大。
市场需求主要来自医药、农药和香精香料领域。
特别是在环境保护和健康意识提升的背景下,环已酮市场有望迎来更多的发展机遇。
3.2 市场发展趋势根据对市场的分析,环已酮市场发展呈现以下趋势:•技术进步:随着科技的不断进步,环已酮的合成工艺不断改进,产品质量得到提高。
•应用拓展:随着环保和健康意识的提升,环已酮在更多领域的应用将得到拓展。
•国际市场开拓:环已酮市场的开拓将不仅仅局限于国内市场,在国际市场也有巨大发展潜力。
3.3 市场规模预测根据对市场趋势和需求的分析,预测未来几年环已酮市场规模将持续扩大。
预计到2025年,环已酮市场规模有望达到X亿美元。
4. 环已酮市场发展建议4.1 加强科研力量在环已酮市场发展过程中,加强科研力量是关键。
- 1、下载文档前请自行甄别文档内容的完整性,平台不提供额外的编辑、内容补充、找答案等附加服务。
- 2、"仅部分预览"的文档,不可在线预览部分如存在完整性等问题,可反馈申请退款(可完整预览的文档不适用该条件!)。
- 3、如文档侵犯您的权益,请联系客服反馈,我们会尽快为您处理(人工客服工作时间:9:00-18:30)。
环己酮的生产现状及预测3.1 世界环己酮生产现状及预测3.1.1 世界环己酮的发展及现状分析环己酮为生产PA6、PA66的原料,也是生产己二酸的原料之一。
世界上主要是以苯为原料来合成的。
1960年德国BASF公司采用环己烷氧化法建成大型环己酮生产装置,使环己烷氧化技术得以迅速发展,并导致聚酞胺纤维的大规模发展。
1967年,荷兰国家矿业公司(DSM)研究的苯酚加氢一步制取环己酮方法实现了工业化,但是,由于苯酚产量小,且价格偏高,用苯酚作为原料生产环己酮受到了限制。
1995年欧美经济复苏,自用品增加,国际市场民用丝、工业丝生产恢复,对己内酰胺的需求量增加,从而促使环己酮、己内酰胺价格上升。
1997年亚洲金融危机的影响,化工市场整体效益下滑,特别是消耗苯的产品如苯酚、苯胺、环己酮、硝基苯、氯苯等市场平淡;苯乙烯虽然国内市场缺口很大,但由于进口过多,市场也处于颓势。
1998-2000年美国进口的环己酮主要来自于荷兰和斯洛伐克,美国的环己酮主要出口到远东、加拿大和拉丁美洲。
2003年,乌兹别克斯坦也购买了48吨含量为99.9%的巴陵牌环己酮优级品,使该产品首次打入中亚市场。
在国外,纯净环己酮基本上是作为生产己内酰胺的中间产物而存在的,在国外,环己酮装置均与己内酰胺相配套,因此很少单独统计环己酮的产能、产量、消费量等,用环己酮路线生产1吨己内酰胺约消耗环己酮0.897吨左右,所以我们通过己内酰胺的统计数据间接了解国外环己酮的生产状况,通过下表我们可以了解环己酮的国外生产情况。
此外,由于环己酮是己二酸的中间产物,有时己二酸生产厂家也生产环己酮,如日本旭化成,其环己酮生产能力为15万吨/年,还有中国的辽阳石化公司、博汇化工、海力化工等。
表3.1 2004-2010年国外环己酮产品装置状况单位:万吨/年3.1.2 世界环己酮未来发展预测全球主要新增产能都在亚洲,尤其是中国。
日本宇部原计划对泰国己内酰胺生产工厂进行扩建,其中己内酰胺生产工厂产能计划到2010年扩至13万吨/年。
但遭遇金融危机后,宇部决定延迟该项目并重新审查。
据专家调查,2010年世界己内酰胺生产能力约达到485万吨,产量为450万吨。
对应环己酮生产能力达435万吨,产量404万吨。
预计2011年以后国外环己酮的生产能力将以2%-3%左右的速率增长。
表3.2 2010-2015年全球环己酮产品生产能力、产量预测图3.1 2010-2015年全球环己酮产能、产量预测走势图单位:万吨/年3.2 我国环己酮生产现状及预测3.2.1 我国环己酮的发展我国的环己酮是伴随着己内酰胺行业的成长而发展起来的,在己内酰胺生产技术由苯酚路线变成环己烷路线时,环己酮行业才发展成为一个独立的行业。
在早期,环己酮只是己内酰胺和聚酰胺66的中间产物,各生产厂家的产品主要是自用,并无商品量形成。
随着己内酰胺产品结构的调整和非酰胺应用领域的扩大,才形成了相当规模的商品量和环己酮行业。
1994年我国环己酮生产能力为11.59万吨/年,生产厂家有6家,能力最大的厂家分别为中石化巴陵石化厂(原鹰山石化厂)和中石化南京东方化工厂引进DSM技术建设的4.4万万吨/年的生产装置,其余厂家的生产能力均在1万万吨/年以下。
1996年我国有环己酮生产企业7家,环己酮产量达到9.96万吨。
其中,巴陵石油化工公司是当时我国环己酮产量最大的企业,1996 年产量达到5.55万吨,占全国总产量的55.7%。
1998年我国环己酮生产能力约15.5万吨,产量14.5万吨,每年进口环己酮近万吨。
2000 年我国环己酮的产量约为21.4万吨,开工率接近90%,其中环己酮商品量约为4.6万吨。
在这9家生产厂中,有4家环己酮全部用于自己生产己内酰胺和尼龙66,合计生产能力为 18.1万吨/年,占国内总生产能力的3/4。
2000年上述4家企业约生产环己酮16万吨,占全国总产量的76%。
2002年,我国的环己酮生产能力为30万吨,生产量约26万吨,其中20万吨为生产厂家自用生产己内酰胺或聚酰胺66,约有4~6万吨为市场商品量。
加上每年进口约4万吨,我国环己酮表现需求量约为30万吨,商品量约为10万吨,虽然有部分进口,但产销总体处于平衡状态。
近年来,国内环己酮需求不断扩大,企业出于发展的需要,纷纷考虑采用先进技术,扩大生产能力,以求达到经济规模,提高企业经济效益。
2004年巴陵有限公司对原有的4.5万吨/年环己酮装置改扩建到7万吨/年。
今年巴陵石化环己酮事业部在生产经营遭遇严峻形势的情形下,瞄准行业先进水平,层层动员,对标挖潜,将指标进行逐级分解落实,切实抓好挖潜增效工作,在逆境中力求新突破。
截至6月30日,该部环己酮装置共产优质产品4.25万吨,同比增产1000余吨。
其产品综合配套能力得到进一步提升。
今年初,该部依托现有装置,自主进行装置由年产7万吨向年产10万吨的挖潜扩能改造一期工程。
经40多天奋战,于1月6日打通全部流程,产出优质环己酮产品。
与此同时,为消除生产瓶颈,增强装置竞争力,该事业部还通过每次提高100标方气量,杜绝非计划停车,逐步提高氧化生产负荷,将氧化负荷提至14200标方/小时,装置产酮最高达到270吨/天,使装置满负荷生产。
该部技术人员还充分挖掘烷三塔的潜力,努力提高采出量,在原有基础上,烷循环量提高了13吨/小时,保证了整个装置在产量提高的同时,收率也大幅提高,使环己酮精馏产酮能力达到10万吨/年,并相应增加了环己烷产品的生产能力。
产品质量进一步改善,该事业部层层建立质量责任制,以抓质量问题的整改、质量措施的落实和推进为重点,全力提升产品质量。
为了使产品的应用领域从低档油漆、油墨向高档环保型涂料转型,从溶剂应用向原料型应用转移,该部通过持续开展质量攻关,提高了产品微观质量,不仅实现了对产品质量要求更高的化纤级环己酮的连续生产,还能联产溶剂环己酮。
该部还采用超重力分离新技术,使设备运行周期由原来的两个月延长至一年以上,不但使装置运行更平稳,还提高了产品实物质量。
今年2月,该部科研人员通过大胆尝试“双塔倒开”全新生产工艺,不但减少了醛类杂质,且将醛类、2—庚酮彻底清除,成功生产出含量达99.95%以上、庚酮含量小于30ppm的化纤级环己酮,质量高于国家标准,成了市场的“抢手货”。
事业部已经向国内三家使用进口装置的下游企业提供1.4万余吨化纤级环己酮。
成本指标进一步优化。
该事业部抓住工序成本“牛鼻子”,加大各项降本增效措施实施力度。
环己酮车间针对不同岗位,在科学调度的基础上,围绕目标成本,持续推行成本核算体系,班组每天进行消耗核算,定期进行消耗分析与总结,使产品的各项消耗指标处于受控状态。
他们调整和优化工艺指标,使苯耗逐步接近预订目标。
他们还严格控制与缩小尾气含氢指标范围,既降低了氢气的耗量,又保证了环己烷的凝固点,达到了产品成本与产量的双赢。
仅4月份,装置主要物耗指标——每吨苯耗比上月下降7公斤。
该部焚烧环己酮生产过程中产生的废碱液的环保装置,多年来一直采用干气乳化油燃料配比焚烧方式。
在燃料乳化油价格不断上涨的情形下,该部通过试验,将纯干气引入焚烧炉代替乳化油。
正式采用干气引入焚烧炉燃烧的装置运行稳定,此举每天可少用7.2吨乳化油,按全年1万小时的生产时间计算,每年可节约燃料成本200万元以上。
此外,该部还进行变压吸附真空泵更新改造,自3月底投用后,只需开一台就能满足工况的要求,不但收率由92%提高到94%,当月多产氢气7.5吨以上,干气消耗每吨氢同比下降85公斤,各项技术指标取得了明显进步。
6 月5日,该部实施干气换热器节能项目后,每年可节约燃烧气和冷却水费用80多万元。
巨化集团公司锦纶厂自1987年建成4500吨/年环己酮国产装置以来,在1995年~1997年进行万吨环己酮扩改的基础上,2003年顺利完成了投资近亿元的3万吨/年环己酮的扩建改造,实现了一次开车成功。
2004、2005、2006年在保持原主体工艺流程和总体平面布置的前提下,采用消除部分设备瓶颈、改动局部工艺配管、引进新技术、调整有关指标等措施,实现装置3改4、4改5和5改6,一年迈上一个台阶,实现6万吨/年生产能力。
山东洪业化工集团有限公司总投资2.8亿元,占地462亩,建设的6万吨/年环己酮项目于2005年2月18日开始破土施工,2005年12月8日竣工建成,2006年3月28日该公司环已酮装置打通全部流程,生产出符合国标优级品的环已酮产品。
这是该公司新建的第一个主导产品,它创造了国内外同类装置的最快速度,同样难得的是,洪业公司还是国内第一个涉足环已酮项目的民营企业,其配套建设16万吨/年己内酰胺装置处于前期准备中。
山东方明化工有限公司在原山东天源化学工业公司的0.65万吨/年环己酮装置改扩建为1.5万吨/年,于2006年初顺利投产。
2006年内江天科化工有限责任公司利用原有生产1万吨环己酮的基础上进行改造形成年产2万吨环己酮生产能力。
该产品是西南地区唯一家生产企业,其主要销售在成渝两地,现阶段产品供不应求。
2005年国内环己酮生产能力34.75万吨,产量约为29.5万吨。
2006年国内环己酮生产能力达到42.6万吨,产量约为35万吨。
南京帝斯曼东方化工有限公司自行设计、制造、施工的6万吨/年环己酮装置于2007年1月26日投料一次开车成功后,成为国内同类装置中开车周期最短,产出合格产品的装置。
2007年12月,山东海力一期6万吨/年环己酮装置投产,二期6万吨/年环己酮于2009年1月投产。
2009年4月30日,石家庄焦化集团年产10万吨环己酮项目正式投产。
2010年5月8日,浙江巨化环己酮装置开始停车扩能,维持15天。
厂家原产能为8万吨,扩能后达到9万吨。
2009年开始动工建设的福建泉港东鑫石化环己酮装置在2010年5月底进入调试阶段,6月中旬有合格品产出,投入市场试用中。
但在7月份因装置设备问题,合格品产出不正常,直至8月中旬正常运行。
产品起初仅供华南市场,后续陆续到华东市场,且与下游工厂开始合作。
该装置产能为6万吨/年。
2010年……2011年……3.2.2 我国环己酮生产现状分析…。
2005-2010年国内环己酮产品装置情况见下表。
表3.3 2005-2010年国内环己酮产品装置状况单位:万吨/年我国环己酮近几年产能、产量情况见下表和图:表3.4 2003-2010年我国环己酮产能产量统计表图3.2 2003-2010年我国环己酮产能产量走势图单位:万吨/年3.2.3 我国环己酮生产预测我国环己酮已暂时进入相对产能过剩阶段,预计未来随着下游己内酰胺和己二酸的扩能,环己酮产能还将增加。
……随着我国环己酮消费量的持续增长,我国未来几年环己酮产能产量预测见下表和图:表3.5 2011-2015年我国环己酮生产能力与产量预测表图3.3 2011-2015年我国环己酮生产能力与产量预测图单位:万吨/年3.3 环己酮主要生产企业产能统计我国的环己酮生产厂家不多,其中3万吨/年规模以上的有13大生产厂家,分别是山东海力化工集团、南京帝斯曼东方化工有限公司、中石化股份有限公司巴陵分公司、山东方明化工有限公司、石家庄焦化集团、巨化集团公司锦纶厂、山东洪业化工集团有限公司、南京化学工业有限公司、福建泉港东鑫石化公司、辽阳石化公司、中国神马集团尼龙66盐公司和太化集团公司太原化工厂、内江天科化工有限责任公司。