煤炭直接液化、间接液化等化技术的比较
煤制油的工艺原理及比较
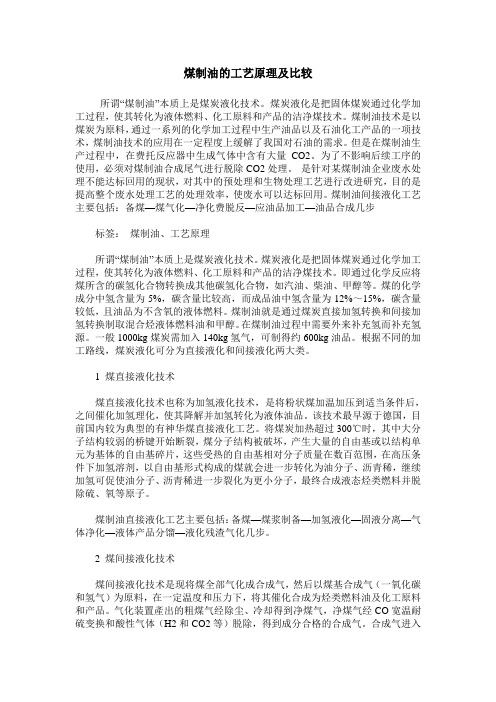
煤制油的工艺原理及比较所谓“煤制油”本质上是煤炭液化技术。
煤炭液化是把固体煤炭通过化学加工过程,使其转化为液体燃料、化工原料和产品的洁净煤技术。
煤制油技术是以煤炭为原料,通过一系列的化学加工过程中生产油品以及石油化工产品的一项技术,煤制油技术的应用在一定程度上缓解了我国对石油的需求。
但是在煤制油生产过程中,在费托反应器中生成气体中含有大量CO2。
为了不影响后续工序的使用,必须对煤制油合成尾气进行脱除CO2处理。
是针对某煤制油企业废水处理不能达标回用的现状,对其中的预处理和生物处理工艺进行改进研究,目的是提高整个废水处理工艺的处理效率,使废水可以达标回用。
煤制油间接液化工艺主要包括:备煤—煤气化—净化费脱反—应油品加工—油品合成几步标签:煤制油、工艺原理所谓“煤制油”本质上是煤炭液化技术。
煤炭液化是把固体煤炭通过化学加工过程,使其转化为液体燃料、化工原料和产品的洁净煤技术。
即通过化学反应将煤所含的碳氢化合物转换成其他碳氢化合物,如汽油、柴油、甲醇等。
煤的化学成分中氢含量为5%,碳含量比较高,而成品油中氢含量为12%~15%,碳含量较低,且油品为不含氧的液体燃料。
煤制油就是通过煤炭直接加氢转换和间接加氢转换制取混合烃液体燃料油和甲醇。
在煤制油过程中需要外来补充氢而补充氢源。
一般1000kg煤炭需加入140kg氢气,可制得约600kg油品。
根据不同的加工路线,煤炭液化可分为直接液化和间接液化两大类。
1 煤直接液化技术煤直接液化技术也称为加氢液化技术,是将粉状煤加温加压到适当条件后,之间催化加氢理化,使其降解并加氢转化为液体油品。
该技术最早源于德国,目前国内较为典型的有神华煤直接液化工艺。
将煤炭加热超过300℃时,其中大分子结构较弱的桥键开始断裂,煤分子结构被破坏,产生大量的自由基或以结构单元为基体的自由基碎片,这些受热的自由基相对分子质量在数百范围,在高压条件下加氢溶剂,以自由基形式构成的煤就会进一步转化为油分子、沥青稀,继续加氢可促使油分子、沥青稀进一步裂化为更小分子,最终合成液态烃类燃料并脱除硫、氧等原子。
煤的液化技术
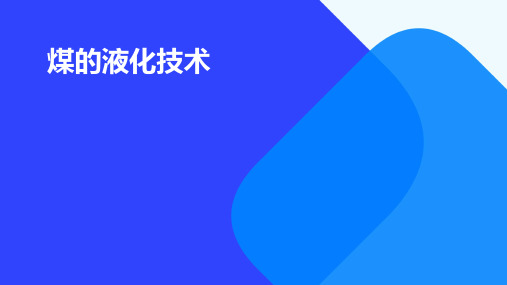
市场发展前景
1 2 3
替代石油资源
随着石油资源的日益枯竭,煤液化技术作为一种 替代石油的能源资源,具有广阔的市场前景。
满足环保要求
煤液化技术能够降低煤炭燃烧过程中的污染物排 放,符合环保要求,有助于推动清洁能源市场的 发展。
对煤液化技术企业给予税收优惠政策,降低企业税负,提高市场 竞争力。
THANKS FOR WATCHING
感谢您的观看
出口潜力
煤液化产品如柴油、汽油等可作为燃料或化工原 料,具有较大的出口潜力,有助于提升我国能源 产业的国际竞争力。
政策支持与推动
产业政策引导
政府通过制定产业政策,鼓励和支持煤液化技术的研发和应用, 推动产业健康发展。
资金扶持
政府提供资金扶持,支持企业进行技术研发和产业化推广,减轻 企业负担。
税收优惠
润滑油
煤液化过程中产生的润滑油具有 优良的润滑性能和稳定性,可用 于机械设备的润滑。
民用燃料
燃气
通过煤液化技术得到的液化石油气可作为居民生活和商业用 途的燃气。
供暖
煤液化燃料可用于集中供暖和家庭采暖,提高居民生活质量 。
化工原料
乙烯
煤液化技术可以生产乙烯等化工原料 ,进一步用于生产塑料、合成纤维等 高分子材料。
该技术最早由南非开发,主要 产品是柴油和航空煤油等。
间接液化技术的优点是工艺流 程相对简单,对原料煤的适应 性较强,但转化效率较低,且 催化剂消耗较大。
合成气液化
合成气液化是指将合成气在一定 条件下转化为液体燃料的过程。
该技术通常采用费托合成工艺, 将合成气在催化剂作用下转化为
煤液化

煤炭液化技术概论引言:我国是一个典型的富煤贫油国家,煤炭资源探明储量远远大于石油储量。
面对国际市场油价不断攀升、世界石油储量逐渐枯竭的情况,我们应该扬长避短——充分利用中国采储量相对较大的煤炭资源,大力推进煤液化产业的成熟与发展。
所谓煤炭液化,是将煤中的有机质转化为液态产品,其目的就是活的和利用液态的碳氢化合物替代石油及其制品,来生产发动机用液体燃料和化学品。
根据加工路线的不同,通常把煤液化分为直接液化和间接液化两大类[]1。
一:煤炭直接液化技术煤炭直接液化是指通过加氢使煤中复杂的有机高分子结构直接转化为较低分子的液态燃料,转化过程是在含煤粉、溶剂和催化剂的浆液系统中进行加氢、解聚,需要较高的压力和温度。
直接液化的优点是热效率较高、液体产品收率较高;主要缺点是煤浆加氢工艺过程的总体操作条件相对苛刻。
煤直接液化技术按照过程工艺特点可分为:①煤直接催化加氢液化工艺,②煤加氢抽提液化工艺,③煤热解和氢解液化工艺,④煤油混合共加氢液化工艺。
(一):煤直接催化加氢液化工艺一般分为几段来进行,即:液相加氢段、气相加氢段和产品精制段。
在第一阶段,所谓液化加氢段中进行裂解加氢,使煤有机大分子热解生成中等奋战死的自由基碎片,随之与氢结合,获得沸点为324℃~340℃以下的产品(合成原油),同时还有O、N、S化合物的初步脱除,生成水、氨及硫化氢。
第二阶段、第三阶段,是在气相及有催化剂的固定床反应器中进行,通过预加氢装置、裂化重整装置,最后获得商品汽油和柴油为主要成分的精制产物。
在第一阶段之前通常还有一个煤浆制备阶段,目的是将细磨的煤粉和催化剂及焦油或循环油共同研磨制成煤糊,供液相加氢。
世界上现有或曾经有过的煤直接催化加氢液化工艺主要有:德国煤直接加氢液化老工艺;德国直接液化新工艺——IGOR工艺;煤氢法(H-Coal);催化两端加氢液化(CTSL)工艺;HTI工艺。
(二):煤加氢抽提液化工艺这类方法是在Pott-Broche溶剂抽提液化法基础上发展的,代表性的工艺有美国的溶剂精炼煤法、埃克森供氢溶剂法和日本NEDOL工艺。
煤炭液化技术

煤炭液化技术[编辑本段] 煤炭液化技术煤炭液化是把固体煤炭通过化学加工过程产品的先进洁净煤技术。
根据不同的加工,使其转化成为液体燃料路线,煤炭液化可分为直接、化工原料和液化和间接液化两大类:一、直接液化直接液化是在高温(400℃以上)、高压(10MPa以上),在催化剂和溶剂作用下使煤的分子进行裂解加氢,直接转化成液体燃料,再进一步加工精制成汽油、柴油等燃料油,又称加氢液化。
1、发展历史煤直接液化技术是由德国人于1913 年发现的,并于二战期间在德国实现了工业化生产。
德国先后有12套煤炭直接液化装置建成投产,到1944年,德国煤炭直接液化工厂的油品生产能力已达到423万吨/年。
二战后,中东地区大量廉价石油的开发,煤炭直接液化工厂失去竞争力并关闭。
70年代初期,由于世界范围内的石油危机,煤炭液化技术又开始活跃起来。
日本、德国、美国等工业发达国家,在原有基础上相继研究开发出一批煤炭直接液化新工艺,其中的大部分研究工作重点是降低反应条件的苛刻度,从而达到降低煤液化油生产成本的目的。
目前世界上有代表性的直接液化工艺是日本的NEDOL 工艺、德国的IGOR工艺和美国的HTI工艺。
这些新直接液化工艺的共同特点是,反应条件与老液化工艺相比大大缓和,压力由40MPa降低至17~30MPa,产油率和油品质量都有较大幅度提高,降低了生产成本。
到目前为止,上述国家均已完成了新工艺技术的处理煤100t/d 级以上大型中间试验,具备了建设大规模液化厂的技术能力。
煤炭直接液化作为曾经工业化的生产技术,在技术上是可行的。
目前国外没有工业化生产厂的主要原因是,在发达国家由于原料煤价格、设备造价和人工费用偏高等导致生产成本偏高,难以与石油竞争。
2、工艺原理煤的分子结构很复杂,一些学者提出了煤的复合结构模型,认为煤的有机质可以设想由以下四个部分复合而成。
第一部分,是以化学共价键结合为主的三维交联的大分子,形成不溶性的刚性网络结构,它的主要前身物来自维管植物中以芳族结构为基础的木质素。
煤的直接液化与间接液化技术进展

氢就是在 比较温和的条件下对煤加氢。通常氢压在 8~1 a 0MP , 温度不超过煤的分解 温度 。在 煤 的轻 度加 氢反 应 中, 的有 机 煤
质 不 能 氢解 为 液 体 产 物 , 的 外 形 也 没 有 发 生 变 化 。虽 然 煤 得 煤 元 素 组 成 变 化 不 大 , 是 许 多 物 理 性 质 、 学 性 质 和 工 艺 性 质 却 但 化 发 生 明 显 的 变化 。 煤的深度加氢是在激 烈 的条件下 与更 多 的氢进 行 的反应 ,
温 度通 常低 于 4 0℃ , 5 氢压在 7 0~10 MP 。煤 中的大部分有机 0 a 质 均转化为液体产 物和少 量气态烃。煤的深度 加氢是 制取液体
燃 料 和 化 工 原料 的基 本方 法 。
1 2 煤加氢 液化 的基本 化 学反应 .
煤 加 氢 液 化是 一 个 复 杂 的化 学 过 程 , 包 括 一 系 列 复 杂 的 它
Ab t a t s r c :Th in fc n e o he c a i u f cin tc oo y i e sg i a c ft o llq ea to e hn l g n Chi ’ c n mi v l p n s a ay e i naS e o o c de eo me twa n lz d. Th e c a iuea t n tc n l g s r ve d,ic u i g d r c o llq e a to n n ie tc a i u  ̄ci n P o p c sa d o ll q fc i e h oo wa e i we o y n l d n ie tc a i u f ci n a d i d r c o llq e to . r s e t n t e eo me tdr c in o h o llq e a to e h l g n Ch na we e s g e td. he d v lp n ie t ft e c a i u f cin t c noo i i r u g se o y Ke r s:tc n l g fc a i u f cin;die tlq e a t n;i d r c i u f ci n y wo d e h oo o o llq ea to y r c i u fc i o n ie tlq ea to
煤质烯烃的工艺技术

煤质烯烃的工艺技术煤质烯烃是指从煤炭中提取出来的烯烃类化合物,具有重要的工业应用价值。
煤质烯烃的工艺技术主要包括煤液化和煤气化两种方法。
1. 煤液化技术煤液化是将煤炭在高温高压下通过催化剂或溶剂作用,将煤中的有机物质转化为液体产品的过程。
煤液化技术可分为直接液化和间接液化两种方法。
直接液化是指将煤炭与溶剂和催化剂混合后,在高温高压下进行反应,通过催化剂的作用将煤转化为液体产品。
在直接液化过程中,溶剂可起到催化剂的作用,帮助提高反应速率和产物收率。
间接液化是指先将煤炭气化生成合成气,再通过催化剂的作用进行反应生成液体产品。
煤液化技术的关键步骤包括煤炭粉碎、石油溶剂提取和催化剂添加等。
煤炭粉碎可以增加煤与溶剂催化剂的接触面积,有利于反应进行。
溶剂的选择对于反应速率和产物性质有重要影响,通常选择具有较高活性和选择性的溶剂。
催化剂的选择和添加方式也会影响反应的进行和产物的性质。
2. 煤气化技术煤气化是指将煤炭在高温下与气化剂(通常为氧气和水蒸气)反应,生成合成气的过程。
合成气主要包括一氧化碳和氢气,可以用作燃料或化工原料。
煤气化技术可分为固定床气化、流化床气化和床层气化等方法。
固定床气化是最传统的煤气化技术,将煤炭放置在反应器中,通过控制气化剂的供气量和反应条件,使煤炭与气化剂反应生成合成气。
流化床气化是指将煤炭破碎成较小的颗粒,通过气流作用使其悬浮在反应器中,与气化剂反应生成合成气。
床层气化是将煤炭放置在床层中,通过控制气化剂的上下供气或其他传质方式使煤炭与气化剂充分接触反应,生成合成气。
煤气化技术的关键步骤包括煤炭预处理、气化剂准备和气化反应等。
煤炭预处理主要包括煤炭粉碎和煤炭干燥,以提高煤与气化剂的接触面积和反应速率。
气化剂的准备包括氧气和水蒸气的供应和净化。
气化反应的温度和压力及气化剂的供气量等条件对反应进行和产物分布有重要影响。
总之,煤质烯烃的工艺技术主要包括煤液化和煤气化两种方法。
煤液化通过催化剂或溶剂作用,将煤中的有机物质转化为液体产品。
煤的气化与液化技术及应用前景
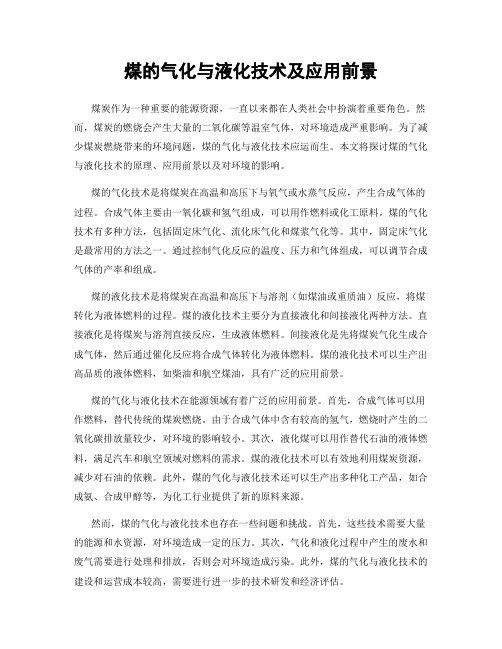
煤的气化与液化技术及应用前景煤炭作为一种重要的能源资源,一直以来都在人类社会中扮演着重要角色。
然而,煤炭的燃烧会产生大量的二氧化碳等温室气体,对环境造成严重影响。
为了减少煤炭燃烧带来的环境问题,煤的气化与液化技术应运而生。
本文将探讨煤的气化与液化技术的原理、应用前景以及对环境的影响。
煤的气化技术是将煤炭在高温和高压下与氧气或水蒸气反应,产生合成气体的过程。
合成气体主要由一氧化碳和氢气组成,可以用作燃料或化工原料。
煤的气化技术有多种方法,包括固定床气化、流化床气化和煤浆气化等。
其中,固定床气化是最常用的方法之一。
通过控制气化反应的温度、压力和气体组成,可以调节合成气体的产率和组成。
煤的液化技术是将煤炭在高温和高压下与溶剂(如煤油或重质油)反应,将煤转化为液体燃料的过程。
煤的液化技术主要分为直接液化和间接液化两种方法。
直接液化是将煤炭与溶剂直接反应,生成液体燃料。
间接液化是先将煤炭气化生成合成气体,然后通过催化反应将合成气体转化为液体燃料。
煤的液化技术可以生产出高品质的液体燃料,如柴油和航空煤油,具有广泛的应用前景。
煤的气化与液化技术在能源领域有着广泛的应用前景。
首先,合成气体可以用作燃料,替代传统的煤炭燃烧。
由于合成气体中含有较高的氢气,燃烧时产生的二氧化碳排放量较少,对环境的影响较小。
其次,液化煤可以用作替代石油的液体燃料,满足汽车和航空领域对燃料的需求。
煤的液化技术可以有效地利用煤炭资源,减少对石油的依赖。
此外,煤的气化与液化技术还可以生产出多种化工产品,如合成氨、合成甲醇等,为化工行业提供了新的原料来源。
然而,煤的气化与液化技术也存在一些问题和挑战。
首先,这些技术需要大量的能源和水资源,对环境造成一定的压力。
其次,气化和液化过程中产生的废水和废气需要进行处理和排放,否则会对环境造成污染。
此外,煤的气化与液化技术的建设和运营成本较高,需要进行进一步的技术研发和经济评估。
综上所述,煤的气化与液化技术具有重要的应用前景。
煤炭直接液化、间接液化等化技术的比较

工业化程度 可以
反应器类型 悬浮床
温度/℃ 压力/MPa
440-450 17
催化剂
GelCaTM
可以 鼓泡床 470 30 炼铝赤泥
用量/%
0.5
3-5%
固液分离方 法 在线加氢 循环溶剂加 氢 工业性试验 规模
临界溶剂萃取 有或无 部分
600t/d
减压蒸馏 有 在线
200t/d
试验煤
神华煤
先锋褐煤
目前国内外的主要工艺有: 1.美国HTI工艺
该工艺是在两段催化液化法和H-COAL工艺基础上发展起来的,采用近十 年来开发的悬浮床反应器和HTI拥有专利的铁基催化剂(GelCatTM)。反应温度 420~450℃,反应压力17MPa;采用特殊的液体循环沸腾床反应器,达到全返混 反应器模式;催化剂是采用HTI专利技术制备的铁系胶状高活性催化剂。在高温 分离器后面串联一台加氢固定床反应器,对液化油进行在线加氢精制。 2.日本 NEDOL 工艺
转化率/% 93.5
97.5
生成水/% 13.8
28.6
烯烃油/% 67.2
58.6
残渣/%
13.4
11.7
氢耗/%
8.7
11.2
注:daf 煤
可以 鼓泡床 465 18 天然黄铁矿
3-4%
未进行 平推流 425~435 6~10 乳化 Mo 0.02%~ 0.05%
已进行 强制内循环悬浮床
455 19 人工合成铁基
1.间接液化工艺
优点: (1)合成条件较温和。无论是固定床、流化床还是浆态床,反应温度均低于
350℃,反应压力2.0—3.0MPa。 (2)转化率高。如SASOL公司SAS工艺采用熔铁催化剂,合成气的一次通过
煤制油

煤制油煤制油包括直接液化和间接液化两种工艺技术路线。
1.煤炭直接液化技术煤在高压和一定温度下直接与氢气反应生成液体燃料油的工艺技术称为直接液化。
煤炭直接液化主要产品为汽油、柴油、航空煤油、石脑油、LPG(液化石油气),另外还可以提取BTX(苯、甲苯、二甲苯),副产品有硫磺、氨或尿素等。
直接液化工艺的产品中,柴油的比例在60~70%,汽油和LPG占40~30%左右。
直接液化的工艺主要有Exxon供氢溶剂法(EDS)。
氢-煤法等。
EDS法是煤浆在循环的供氢溶剂中与氢混合,溶剂首先通过催化器,拾取氢原子,然后通过液化反应器,释放出氢原子,使煤分解。
氢-煤法是采用沸腾床反应器,直接加氢将煤转化成液体燃料。
直接液化过程流程现代煤炭直接液化技术提高了产品质量,特别是通过液化后的提质加工工艺,使液化油通过加氢精制、重整、加氢裂化,可得到合格的汽油、柴油或航空煤油。
尤其是柴油的凝点很低,可以在高寒地区使用,所得航空煤油的比重较大,同样容积的油箱可使飞机的续航距离增加。
2. 煤炭间接液化技术间接液化是把煤炭先气化再合成,煤在高温下与氧气和水蒸气反应生成合成反应气(CO+H2),合成反应气再经F-T合成催化反应合成液体燃料及其化学品。
煤炭间接液化主要产品为汽油、柴油、航空煤油、石脑油、LPG、以及乙烯、丙稀等重要化工原料,副产品有α烯烃、硬蜡、氨、醇、酮、焦油、硫磺、煤气等。
间接液化的产品品种是可以变通的,即可以生产油品,又可以根据市场需要加以调节,生产高附加值、价格高、市场紧缺的化工产品。
对中国的石油产品市场而言,以优质石脑油和高质量柴油、烯烃、LPG 和石蜡等产品为好。
另外烯烃的价值较高,LPG也是市场紧俏物资。
此外我国石蜡生产和销售市场上,高熔点微晶蜡缺口较大,高品位润滑油也是国内比较紧缺的。
因此,汽油、柴油与高附加值的润滑油、微晶蜡等市场紧缺的产品并举,可以作为合成油产品的主攻方向。
间接液化在可控制的条件下进行合成,获得的柴油的十六烷值达70,且低硫、无芳烃,既可直接供给环保要求高的地区使用,也可作为优质油与其它油品调配。
现代煤化工新技术

现代煤化工新技术随着世界能源消费量的不断增加,煤炭作为一种重要的化石能源,一直扮演着重要的角色。
然而,传统的煤炭化工过程还存在着许多问题,如排放量大、能源利用率低、资源浪费等。
为此,煤炭化工领域的科学家和工程师一直在探索和研究新的技术和方法,降低煤炭化工过程的成本和环境影响,提高能源利用效率。
以下将介绍几种现代煤化工新技术。
1.煤间接液化技术煤间接液化技术是一种将煤转化为液体燃料的方法,通过间接液化将煤转化为燃油、柴油等燃料。
这种技术可以大幅度降低煤的排放量,使得煤成为一种十分可持续的能源形式。
目前,美国、日本等国家的研究机构都在推动这一技术的发展。
2.煤直接液化技术煤直接液化技术是一种将煤转化为液态燃料的方法。
这种技术可以在较低温度和压力下将煤转化为液态燃料,比传统方法更为高效。
但是,这种技术需要大量的煤来转化为液态燃料,同时还需要大量的水和氢气。
因此,这种技术在现阶段还需要更多的研究和改进。
3.煤气化技术煤气化技术是一种将煤转化为气体燃料的方法。
它可以将煤中的碳转化为一种气体,称为合成气。
可以通过合成气来生产燃料、化学品和电力。
许多国家已经开始使用煤气化技术,因为它的产出比石油更为经济。
4.超临界水气化技术超临界水气化技术是一种将煤转化为液体燃料的方法。
超临界水是指在高温和高压下,水的状态不再是液态或气态。
这种技术可以在较短的时间内将煤转化为液体燃料,同时还可以降低污染物的排放。
目前,中国等国家的科学家正在探索和发展这种技术。
总结现代煤化工新技术的出现,不仅可以提高煤炭化工的环保性、效率,还可以促进能源行业的可持续发展。
虽然这些技术还存在一些问题和挑战,但是相信会有更多的煤化工科学家和实践者不断地探索和改进这些技术。
煤的液化和气化

煤的液化和气化煤的液化是先进的煤炭转化技术之一, 是以煤为原料制取液体烃类为主要产品的技术。
煤液化分为煤的直接液化和煤的间接液化两大类.一.煤炭直接液化是把煤直接转化成液体燃料,煤直接液化的操作条件苛刻,对煤种的依赖性强。
典型的煤直接液化技术是在400摄氏度、150个大气压左右将合适的煤催化加氢液化,产出的油品芳烃含量高,硫氮等杂质需要经过后续深度加氢精制才能达到目前石油产品的等级。
一般情况下,一吨无水无灰煤能转化成半吨以上的液化油。
煤直接液化油可生产洁净优质汽油、柴油和航空燃料。
但是适合于大吨位生产的直接液化工艺目前尚没有商业化,主要的原因是由于煤种要求特殊,反应条件较苛刻,大型化设备生产难度较大,使产品成本偏高。
煤直接液化煤在氢气和催化剂作用下,通过加氢裂化转变为液体燃料的过程称为直接液化。
裂化是一种使烃类分子分裂为几个较小分子的反应过程。
因煤直接液化过程主要采用加氢手段,故又称煤的加氢液化法。
二.煤间接液化是先把煤炭在高温下与氧气和水蒸气反应,使煤炭全部气化、转化成合成气(一氧化碳和氢气的混合物),然后再在催化剂的作用下合成为液体燃料的工艺技术。
间接液化首先将原料煤与氧气、水蒸汽反应将煤全部气化,制得的粗煤气经变换、脱硫、脱碳制成洁净的合成气(CO+H2),合成气在催化剂作用下发生合成反应生成烃类,烃类经进一步加工可以生产汽油、柴油和LPG等产品。
特点在煤炭液化的加工过程中,煤炭中含有的硫等有害元素以及无机矿物质(燃烧后转化成灰分)均可脱除,硫还可以硫磺的形态得到回收,而液体产品品质较一般石油产品更优质。
编辑本段煤间接液化技术的发展70 年代以后, 德国、美国、日本等主要工业发达国家, 为提高效率、降低生成成本, 相继开发了许多我国煤炭直接液化技术的开发研究为了解决我国石油短缺的问题, 寻求廉价生产人造石油的有效途径, 我国自1980 年重新开展煤炭直接液化技术研究。
在煤炭科学研究总院北京煤化学研究所建成具有先进水平的煤炭直接液化、油品提质加工、催化剂开发和分析检验实验室, 开展了基础和技术研究, 取得了一批科研成果, 培养了一支技术队伍, 为深入进行工艺开发和筹建大型煤炭直接液化生产厂奠定了基础。
煤液化技术考试复习大全

1、所谓煤炭液化,是将煤中的有机质转化为液态产物,其目的就是获得和利用液态的碳氢化合物替代石油及其制品,来生产发动机用液体燃料和化学品。
煤炭液化有两种完全不同的技术路线,一种是直接液化,另一种是间接液化。
2、煤炭的直接液化是指通过加氢使煤中复杂的有机高分子结构直接转化为较低分子的液体燃料,转化过程是在含煤粉、溶剂和催化剂的浆液系统中进行加氢、解聚,需要较高的压力和温度。
优点:热效率较高,液体产品收率高;缺点:煤浆加氢工艺过程的总体操作条件相对苛刻。
3、煤炭间接液化是首先将煤气化制合成气(CO+H2),合成气经净化、调整H2/CO比,再经过催化合成为液体燃料。
优点:煤种适应性较宽,操作条件相对温和,煤灰等三废问题主要在气化过程中解决;缺点:总效率比直接液化低。
煤液化的实质就是在适当温度、氢压、溶剂和催化剂条件下,提高H/C比,使固体煤转化为液体的油。
4、在煤的初级液化阶段,煤有机质热解和供氢是两个十分重要的反应。
可认为发生下列四类化学反应:(1)煤的热解(2)对自由基“碎片”的供氢(3)脱氧、硫、氮杂原子反应(4)缩合反应。
5、供给自由基的氢源主要来自以下几个方面:(1)溶解于溶剂油中的氢在催化剂的作用下变为活性氢;(2)溶剂油可供给的或传递的氢;(3)煤本身可供应的氢;(4)化学反应生成的氢。
提高供氢能力的主要措施有:增加溶剂的供氢能力;提高液化系统氢气压力;使用高活性催化剂;在气相中保持一定的H2S浓度等。
6、煤有机结构中的氧存在形式主要有:含氧官能团,如-COOH、-OH、-CO和醌基等;醚键和杂环(如呋喃)。
煤有机结构中的硫以硫醚、硫醇和噻吩等形式存在,脱硫反应与上述脱氧反应相似。
由于硫的负电性弱,所以脱硫反应更容易进行。
煤中的氮大多存在于杂环中,少数为氨基,与脱硫和脱氧相比,脱氮要困难得多。
7、为提高煤液化过程的液化效率,可采取以下措施防止结焦:(1)提高系统的氢分压(2)提高供氢溶剂的浓度(3)反应温度不要太高(4)降低循环油中沥青烯含量(5)缩短反应时间。
煤炭液化

煤直接液化定义及其液化的实质
煤直接液化的定义: 煤直接液化的定义:
基本公式: 氢气→液体产物 气体产物+固体残渣 基本公式:煤+氢气 液体产物 气体产物 固体残渣 氢气 液体产物+气体产物
狭义定义:将煤与某种溶剂充分混合后,通入氢气, 狭义定义:将煤与某种溶剂充分混合后,通入氢气,在一定温度和压 力下,经过复杂的物理、化学过程, 力下,经过复杂的物理、化学过程,使固体煤转化为液体产物的过程称 为煤的直接液化。 为煤的直接液化。 广义定义:将固态煤经过一定的物理、 广义定义:将固态煤经过一定的物理、化学作用转化为液态产物的过 程称为煤液化。 程称为煤液化。
发展煤炭液化工业的 政策建设建议
• (1)增加投入,改进和开发新的煤炭液化 新技术,形成具有我国自主知识产权的煤 直接液化工艺 。 • (2)制定政策法规,鼓励发展煤炭液化技 术 • (3)加强宣传,支持发展煤炭液化技术
没了
谢谢
煤的直接液化工艺流程简图
• 。
煤的直接液化技术是将固体煤在高温高压下与氢反应,将其降解和加氢从而 转化为液体油类的工艺,又称加氢液化。一般情况下,一吨无水无灰煤能转化 成半吨以上的液化油。煤直接液化油可生产洁净优质汽油、柴油和航空燃料。
煤直接液化的工艺特点
• (1)液化油收率高。 • (2)煤消耗量小,一般情况下,1吨无水 无灰煤能转化成半吨以上的液化油 • (3)馏份油以汽、柴油为主,目标产品的 选择性相对较高; • (4)氢耗量大 • (5)反应条件相对较苛刻,如德国老工艺 液化压力甚至高达70MPa
煤炭间接液化与直接液化简要论述

化简要论述
马 时锋
( 西潞 安 煤基 合 成 油 有 限 公 司 ) 山 摘 要 : 述 煤 炭 液 化技 术 即煤 的 间接 液 化 和 直 接 液 化 的 工 艺特 征 。煤 直 接 液化 对 煤 质 要 求较 高 , 间接 液 化 对 煤 质要 求低 , 合 不 论 而 结 同的煤质要求选择相应 的煤炭液化技术 , 具有较强的价值 和意义。 关键 词 : 煤炭 ; 间接 液化 ; 直接 液 化
煤炭 液化 , 即煤基液体燃料合成技术 , 是将煤炭在高温 下加 氢 、 1. .2中国 自主间接液化技术 3 加压 、 加催化剂 , 产生粗油再经炼化制得汽油 、 柴油, 同时制得乙烯 、 山西煤化所对铁系和钴 系催化剂进行 了较 系统 的研究。共沉淀 丙烯 、 石蜡 、 醇等多种 附产 品。煤炭液 化方 法主要分为煤的间接液 F — u e c 催化 剂( 编号为 I C I) 19 C —A 自 9 0年 以来一 直在 实验室 中进行 化 、 接 液化 。 直 固定床试验, 主要 目的是获得动力学参数 。F — n催化 ̄ ( C I eM /I —I UC A、 1 煤炭 间接液化 IC I ) C —I 和钴催 化 ̄ ( C IA、C —I 、C — G的研究集 中在催 B I C —I I C I B I C r ) J I I I a 间接液化首先将原料煤与氧气 、水蒸 汽反应将 煤全 部气化, 化剂的优化 和动力学研究 以及过程模拟 。 制 其中 IC I C — 型催化剂用于 得的粗煤气经变换 、 脱硫 、 脱碳制成洁净 的合成气(O H) C +2 , 合成气在 重质馏分工艺, C I型催化剂用于轻质馏分工艺。I C I I —I C C —A催化剂 催化 剂作用下发生合成反应生成烃类, 烃类经进一步加工可 以生产 已经定型, 实现 了中试放 大生产, 进行 了充分 的中试验证 , 并 完成 了 汽油 、 柴油和 L G等产品 。 P 累计 4 0 0 0小时的中试工艺试验, 稳定运转 1 0 5 0小时, 满负荷运转达 11 . 间接液化工艺特征 8 0 时。I C I 0小 C —I A型催化剂也已经实现 中试放大生产, 在实验 室进 煤炭 间接液化 主要包 括: 的加 压气化 、 煤 煤气净化 、 费托合成 、 行 了长期运转试验, 最长连续运转达 4 0 80小 时, 近期将进 行首次 中 油 品加工等工艺 。煤经加压气化炉气化成粗合成气 , 粗合成气经脱 试运转试验 。此外, 中科院山西煤化所 还对 IC I A钴催化剂进行 C —l I 硫 、脱 碳净 化 后,经 水 汽变换 反 应调 整为 高 H C J O比 的合 成气 了研究 和开发 。目前, 用于浆态床的 I C I C —A和 IC I C —I A催 化剂成本 (. 21 1 - .) 固定床反应器合成烃或直接采用低 H C 5 进入 J O比的合成气 大幅度下降, 品率 明显提高, 成 催化剂性 能尤其是产 品选择性得 到明 (. 1 ) 入浆态床反应 器合 成烃, 同链长 的烃经 加工改质后 即 显提高, 0 —.进 5 0 不 在实验 室模拟验证浆态床装置上, 催化剂 与液体产物 的分离 可制得汽油 、 柴油等塔0 产硬蜡, 尾气可深冷分离得到低碳 烯烃, 或重 和催化剂磨损问题得到根本性 的解决, 术上 突破了煤基合成油 从技 整为合成气返 回用 于合成烃, 弛放气可用于供热 、 电或合成氨等 。 过 程 的 技术 经 济 瓶 颈 。 发 1 . 2间接液化工艺优缺点 20 0 6年采用 中科合成油低温铁 系催化剂浆 态床费托 合成技术 优点: 先后在 内蒙伊泰 、山西潞安 和内蒙鄂尔多斯开工建设 三套规模为 a . 合成反应条件较适 中。固定床 、 流化床 、 浆态床反应器其反应 1 ~ 8万 t 6万 1 油品 / 的合成油厂 。 2 0 a 至 0 9年, 三套工业示 范装置 已 温度 均 低 于 3 0C反应 压 力 在 20 3 Mp 。 5 q, . . a —0 先 后 开 工运 行 ,三 套装 置 的费 托 合 成 技 术 为 同 一基 础 ,以 山西 潞 安 b转化效率高。以 S S L公司 S S工艺为例, . AO A 采用熔铁催化剂 1 t 6万 级合成油 品工业化示范项 目为例, 该联合装置主要包括: 费托 其 合成气通过 转化率达 6 %以上,循环 比 2 3时,其转 化率可达 合成 、 0 - 油品加工 、 碳油洗 、 脱 催化 剂预处理 、 合成水处 理及公用工程 9 %。钴基催化剂 的转化率更高些 。 0 部分 。 此外, 山西煤化所研发 的钴催化剂系列 为 I C I A、 C IB、 C —I 1 —I I C I c . 适应性煤种多样化 。 不仅适用于年轻煤质( 、 褐煤 烟煤等) , 而且 I C IC反应器 为列管式 固定床反应器 。目前其开发的低 温钻 系催 C —I , I 特别适合 中国主要煤炭种类( 年老煤 、 高灰煤等) 。 化剂固定床 费托合成工艺 已完成小试开发, 0 2 9年进行 了工业侧线 0 d其 产品洁净 、 . 无硫氮等污染 物。可以进一步加 工成汽油 、 柴 单管试验, 于中试放大阶段 。 正处 油、 航煤等多种燃料产 品和石油化工原材料。 2煤 炭 直 接 液化 缺点 : 直接液化是指将原料煤 在一定 的温度和压 力下 , 与氢气 、 催化剂 a油品回收率较低。一般情况下, 5 8 原煤产 l成品油 。 . 约 —t t 发生作用, 通过加氢裂化转变为液体燃料的过程 称为煤炭 的直接液 b设备体积庞大 、 . 投资高, 运行费用相对较高 。 化 。因原料煤直接液化过程主要采用加氢手段, 故又称煤 的加氢液 c . 合成油 品的选择性 较差 ,副产物较多 。正构链烃的范 围为 化 法 C 一 10随合成温度及 氢碳 比的降低, 1C 0 ; 重烃类产 量增 大, 轻烃类产量 21 接 液 化工 艺 特 征 .直 减少 。 典型的煤直接加氢液化工艺包括: 相( 浆1 煤糊 油煤 制备 、 氢气制 1 . 型 间接 液化 工 艺 3典 备、 加氢液化反应 、 油品加工等“ 先并后 串” 四个步骤 。 氢气制备是加 1 .南非 S S L间接液化工艺 .1 3 AO 氢液化 的重要环节, 大规模制氢通常采用煤气化 或天然气转化 。液 S S L的 相 浆态床反应器( urP ae ec r AO S r hsR at ) l y o 使用铁催化剂 化过程 中, 将煤 、 催化 剂和循环油制成的煤浆, 与制得 的氢气混合送 生产 蜡 、 燃料和溶剂 。其反应压力 20 a . MP , 反应温度达 2 0 2 0  ̄以上 。 入液化反应器 。在液化反应器 内, 煤首先发生热解反应, 生成 自由基 反应器 内有鼓泡的液态反应产物( 主要为费托产 品蜡) 和悬浮的催化 “ 片” 碎 , 不稳定 的 自由基“ 碎片” 再与氢在催化剂存在条件下结合, 形 剂颗粒 。A O S S L浆态床专利技术的核心和创新是其蜡产物和催化剂 成分子量 比煤低得多的初级加氢产物。 出反应器的产物结 构十分复 实现分离的工艺; 此技术避免了传统 反应器需停车更换催化剂 。浆 杂, 包括气 、 、 液 固三相 。气相的主要成分是氢气, 分离后循环返 回反 态床反应器可连续运转两年, 中间仅 维护性停 车一次 。反应 器设 计 应器重新参 与反应 ; 固相为未反应 的煤 、 矿物质及催化剂 ; 液相则为 简单。 A O S S L浆态床技术 的另一专利技术是把反应器出 口气体中所 轻油 、 中油等馏份油及重油 。 22 接 液 化 工 艺优 缺 点 .直 夹带的“ 有效地分离出来 。 浆” Ssl ao 浆态床反应器结构比列管式 固定床反应器较简单, 便于安 优点: 装, 放大更容易, 台反应器生产能力 高。其最大优势是反应 物混合 单 a .油 品 回收 率 较 高 。 以神 东 H I工艺 为例 油 品 回收 率 达 T 好 、 有 良好的传热性能, 于反应 温度 的控制和反应热的移 出, 6 — 8 具 有利 3 6 %以上 。 可等温操 作,从而可用更高 的平 均操作温度而 获得更高的反应 速 b原料煤消耗低 。1无水无灰煤能转化半吨 以上的液化油 品, . t 加 率。单位反应器体积的产率高, 每吨产品催化剂 的消耗 仅为列管式 上制氢用煤, 3 4 原料煤可产 I液化油品。 约 —t t 固定床反应器 的 2 % 0 另一 大优势是可在线装卸催化剂。 0 3 %。 通过 c . 设备体积小 、 投资低 , 运行费用相对较低 。 有规律的替换催化剂, 平均催 化剂寿命易于控制, 从而更易于控制过 d合成油 品的选择性相对较高。主要 以汽油 、 . 柴油为主 。 程的选择性, 提高粗产 品的质量。 缺点:
煤液化论述
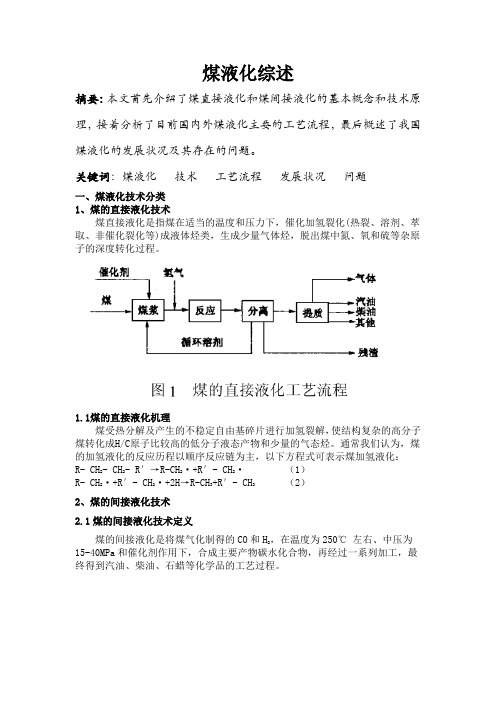
煤液化综述摘要:本文首先介绍了煤直接液化和煤间接液化的基本概念和技术原理,接着分析了目前国内外煤液化主要的工艺流程,最后概述了我国煤液化的发展状况及其存在的问题。
关键词:煤液化技术工艺流程发展状况问题一、煤液化技术分类1、煤的直接液化技术煤直接液化是指煤在适当的温度和压力下,催化加氢裂化(热裂、溶剂、萃取、非催化裂化等)成液体烃类,生成少量气体烃,脱出煤中氮、氧和硫等杂原子的深度转化过程。
1.1煤的直接液化机理煤受热分解及产生的不稳定自由基碎片进行加氢裂解,使结构复杂的高分子煤转化成H/C原子比较高的低分子液态产物和少量的气态烃。
通常我们认为,煤的加氢液化的反应历程以顺序反应链为主,以下方程式可表示煤加氢液化:R- CH2- CH2- R′→R-CH2·+R′- CH2· (1)R- CH2·+R′- CH2·+2H→R-CH3+R′- CH3 (2)2、煤的间接液化技术2.1煤的间接液化技术定义煤的间接液化是将煤气化制得的CO和H2,在温度为250℃ 左右、中压为15-40MPa和催化剂作用下,合成主要产物碳水化合物,再经过一系列加工,最终得到汽油、柴油、石蜡等化学品的工艺过程。
2.2煤的间接液化过程煤的间接液化一般认为有如下步骤:(1)煤的气化;(2)合成气的转变;(3)粗合成气的转变;(4)合成反应;(5)合成气的加工。
二、煤液化工艺分类1、煤直接液化工艺世界上有代表性的煤直接液化工艺是德国的新液化(IGoR)工艺,美国的HTI 工艺和日本的NEDoL工艺。
(1)德国IGOR工艺:1981年德国鲁尔煤矿公司和费巴石油公司对最早开发的煤加氢裂解为液体燃料的柏吉斯法进行了改进,建成了日处理煤200吨的半工业试验装置,操作压力由原来的70兆帕降至30兆帕,反应温度450~480摄氏度,固液分离由过滤、离心改为真空闪蒸方法,将难以加氢的沥青烯留在残渣中气化制氢,轻油和中油产率可达50%。
间接液化与直接液化对比分析
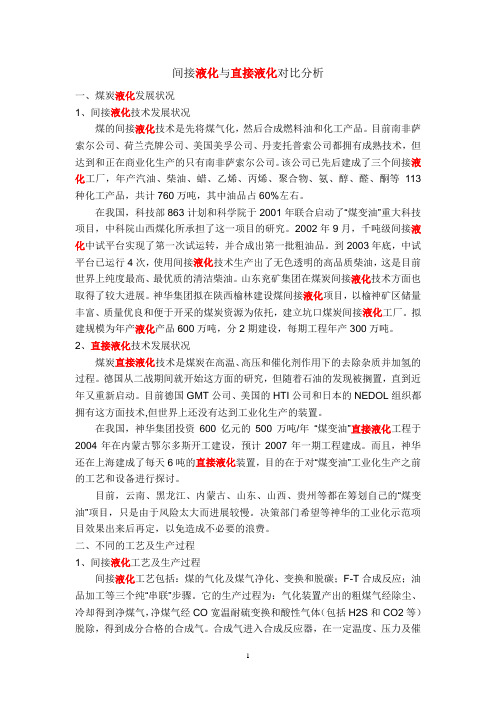
间接液化与直接液化对比分析一、煤炭液化发展状况1、间接液化技术发展状况煤的间接液化技术是先将煤气化,然后合成燃料油和化工产品。
目前南非萨索尔公司、荷兰壳牌公司、美国美孚公司、丹麦托普索公司都拥有成熟技术,但达到和正在商业化生产的只有南非萨索尔公司。
该公司已先后建成了三个间接液化工厂,年产汽油、柴油、蜡、乙烯、丙烯、聚合物、氨、醇、醛、酮等113种化工产品,共计760万吨,其中油品占60%左右。
在我国,科技部863计划和科学院于2001年联合启动了“煤变油”重大科技项目,中科院山西煤化所承担了这一项目的研究。
2002年9月,千吨级间接液化中试平台实现了第一次试运转,并合成出第一批粗油品。
到2003年底,中试平台已运行4次,使用间接液化技术生产出了无色透明的高品质柴油,这是目前世界上纯度最高、最优质的清洁柴油。
山东兖矿集团在煤炭间接液化技术方面也取得了较大进展。
神华集团拟在陕西榆林建设煤间接液化项目,以榆神矿区储量丰富、质量优良和便于开采的煤炭资源为依托,建立坑口煤炭间接液化工厂。
拟建规模为年产液化产品600万吨,分2期建设,每期工程年产300万吨。
2、直接液化技术发展状况煤炭直接液化技术是煤炭在高温、高压和催化剂作用下的去除杂质并加氢的过程。
德国从二战期间就开始这方面的研究,但随着石油的发现被搁置,直到近年又重新启动。
目前德国GMT公司、美国的HTI公司和日本的NEDOL组织都拥有这方面技术,但世界上还没有达到工业化生产的装置。
在我国,神华集团投资600亿元的500万吨/年“煤变油”直接液化工程于2004年在内蒙古鄂尔多斯开工建设,预计2007年一期工程建成。
而且,神华还在上海建成了每天6吨的直接液化装置,目的在于对“煤变油”工业化生产之前的工艺和设备进行探讨。
目前,云南、黑龙江、内蒙古、山东、山西、贵州等都在筹划自己的“煤变油”项目,只是由于风险太大而进展较慢。
决策部门希望等神华的工业化示范项目效果出来后再定,以免造成不必要的浪费。
[【煤化工】煤的气化、液化和干馏技术【2】煤的液化和干馏

【煤化工】煤的气化、液化和干馏技术【2】煤的液化和干馏小化03-20原文二.煤的液化煤液化是把煤转化为液体产物,包括直接液化和间接液化。
I.煤的直接液化:煤的直接液化是通过加氢使煤中复杂的有机化学成分直接转化为液体燃料,转化过程是在含煤粉和溶剂的浆液系统中进行加氢,需要较高的压力和温度。
直接液化的优点是热效率高,液体产品收率高;主要缺点是煤浆加氢工艺过程中,各步骤的操作条件相对苛刻,对煤种适应性差。
德国是最早研究和开发直接液化工艺的国家,其最初的工艺被称为IG 工艺。
气候不断改进,开发出被认为世界上最先进的IGOR工艺。
其后美国也在煤液化工艺的开发上做了大量的工作,开发出供氢溶剂(EDS)、氢煤(H-Coal)、催化两段液化工艺(CTSL/HTI)和煤油共炼等代表工艺。
此外日本的NEDOL工艺也有相当出色的液化性能。
此外,我国在建的神华煤直接液化所采用工艺也是在其他工艺的基础上发展的具有自身特色的液化工艺。
1.德国的IG工艺和IGOR工艺德国的IG工艺可分为两段加氢过程,第一段加氢是在高压氢气下,煤加氢生成液体油(中质油等),又称煤浆液相加氢。
第二段加氢是以第一段加氢的产物为原料,进行催化气相加氢制得成品油,又称中油气相加氢,所以IG法也常称作两段加氢法。
德国的IG工艺流程20世纪80年代,德国在IG法的基础上开发了更为先进的煤加氢液化和加氢精制一体化联合工艺(IGOR)。
其最大的特点是原料煤经该工艺过程液化后,可直接得到加氢裂解及催化重整工艺处理的合格原料油,从而改变了两段加氢的传统IG模式,简化了工艺流程,避免了由于物料进出装置而造成的能量消耗和大量的工艺设备。
IGOR直接液化法工艺流程2.美国的H-Coal、CTSL和HTI工艺H-Coal工艺是美国HRI公司在20世纪60年代,从原有的重油加氢裂化工艺(H-oil)的基础上开发出来的,它的主要特点是采用了高活性的载体催化剂和流化床反应器,属于一段催化液化工艺。
- 1、下载文档前请自行甄别文档内容的完整性,平台不提供额外的编辑、内容补充、找答案等附加服务。
- 2、"仅部分预览"的文档,不可在线预览部分如存在完整性等问题,可反馈申请退款(可完整预览的文档不适用该条件!)。
- 3、如文档侵犯您的权益,请联系客服反馈,我们会尽快为您处理(人工客服工作时间:9:00-18:30)。
和孔容积。同时可以减少煤颗粒粒度,有利于煤加氢液化反应的强化。 (4)采用半离线固定床催化反应器对液化粗油进行加氢精制,便于操作。
缺点: (1)没有大规模中试装置运行检验和验证。技术不成熟。 (2)催化剂回收经济性不确定。 (3)液化条件对煤质要求高。
离相对困难。
(4)氢耗量大,一般在6%-10%。工艺过程中不仅要补充大量新氢,还需要 循环油作供氢溶剂,使装置的生产能力降低。
(5)工艺不够成熟。目前国内只有神华一套产业化装置在运行,而且运行不 稳定。
3.工艺选择
同一煤种在既适合间接液化工艺又适合直接液化工艺的前提条件下,若间接 液化与直接液化两种工艺均以生产燃料油品为主、化学品为副,则煤直接液化的 经济效益将明显优于前者,以选择直接液化为好。如果以生产化学品(直链烃) 为主、燃料油品为副,则间接液化的经济效益将明显优于后者,故以选择间接液 化为好。
工艺特点:一是采用了自行开发的瞬间涡流仓煤粉干燥技术,使煤发生热粉 碎和气孔破裂,水分在很短的时间内降到 1.5%~2%,并使煤的比表面积增加了 数倍,有利于改善反应活性。该技术主要适用于对含内在水分较高的褐煤进行干 燥。二是采用了先进高效的钼催化剂,即钼酸铵和三氧化二钼。催化剂添加量为 0.02%~0.05%,而且这种催化剂中的钼可以回收 85%~95%。三是针对高活性 褐煤,液化压力低,可降低建厂投资和运行费用,设备制造难度小。由于采用了 钼催化剂,俄罗斯高活性褐煤的液化反应压力可降低到 6~10MPa,减少投资和 动力消耗,降低成本,提高可靠性和安全性。但是对烟煤液化,必须把压力提高。 5.神华煤直接液化工艺.
3.NEDOL的烟煤液化工艺
优点: (1)反应压力相对传统工艺较低。压力为17~19MPa,反应温度455—465℃。 (2)催化剂价格低廉。采用合成硫化铁或天然硫铁矿。 (3)固液分离方法简便。采用蒸馏的方法进行固液分离。 (4)两个加氢提质反应器采用离线的方式,操作灵活,加氢催化剂寿命得到
保障。 (5)溶剂供氢能力强。配煤浆用的循环剂单独加氧。
系统内。该液化油经过蒸馏就可以得到十六烷值大于45的柴油,汽油馏分再经重 整即可得到高辛烷值汽油。 缺点:
(1)反应条件苛刻:温度470℃,压力30MPa。 (2)投资高。 (3)单系列处理量相对神华工艺要小。
2.美国的HTI工艺
优点: (1)反应条件相对IGOR温和。反应温度440-450℃,反应压力17 MPa;
目前国内外的主要工艺有: 1.美国HTI工艺
该工艺是在两段催化液化法和H-COAL工艺基础上发展起来的,采用近十 年来开发的悬浮床反应器和HTI拥有专利的铁基催化剂(GelCatTM)。反应温度 420~450℃,反应压力17MPa;采用特殊的液体循环沸腾床反应器,达到全返混 反应器模式;催化剂是采用HTI专利技术制备的铁系胶状高活性催化剂。在高温 分离器后面串联一台加氢固定床反应器,对液化油进行在线加氢精制。 2.日本 NEDOL 工艺
2.直接液化工艺
优点: (1)油收率高。例如采用 HTI 工艺。神东煤的油收率可高达 63%到 68%。 (2)煤消耗量小。一般情况下.1吨无水无灰煤能转化成半吨以上的液化油,
加上制氢用煤,约3—4吨原料产1吨液化油。 (3)馏份油以汽、柴油为主,目标产品的选择性相对较高。 (4)油煤浆进料,设备体积小,投资低,运行费用低。
缺点: (1)液化油含有较多的杂原子,还需加氢提质才能得到合格产品。 (2)单系列处理量相对神华工艺要小。 (3)相对俄罗斯FFI工艺,反应条件苛刻。 (4)工艺不适用于褐煤。
4.俄罗斯FFI工艺
优点: (1)催化剂可以回收。催化剂Mo可采用离心溶剂循环和焚烧两步回收,报
道称回收率95%以上。 (2)反应条件温和。褐煤加氢液化压力6.0MPa,烟煤次烟煤加氢液化压力
(3)煤种适应性强。间接液化不仅适用于年轻煤种(褐煤、烟煤等),而且 特别适合中国主要煤炭资源(年老煤、高灰煤等)的转化。
(4)间接液化的产品非常洁净,无硫氮等污染物,可以加工成优良的柴油(十 六烷值75),航煤,汽油等多种燃料,并且可以提供优质的石油化工原料。
(5)工艺成熟,有稳定运行的产业化工厂。煤间接液化的大型工业过程在南 非经过50年的生产实践。目前已经形成了年产500多万吨油品和约200万吨化学品 的产业,是南非的支柱产业。 缺点: (1)油收率低。煤消耗量大,一般情况下,约5—7t原煤产lt成品油。 (2)反应物均为气相,设备体积庞大,投资高,运行费用高。 (3)目标产品的选择性较低,合成副产物较多。正构链烃的范围可从C1至C100; 随合成温度的降低,重烃类(如蜡油)产量增大。轻烃类(如CH4,C2H4,C2H6 等)产量减少。
转化率/% 93.5
97.5
生成水/% 13.8
28.6
烯烃油/% 67.2
58.6
残渣/%
13.4
11.7
氢耗/%
8.7
11.2
注:daf 煤
可以 鼓泡床 465 18 天然黄铁矿
3-4%
未进行 平推流 425~435 6~10 乳化 Mo 0.02%~ 0.05%
已进行 强制内循环悬浮床
455 19 人工合成铁基
煤炭液化技术比较
汇编日期:2011 年 7 月 4 日
一.煤间接液化介绍
煤的间接液化技术是先将煤全部气化成合成气,然后以合成气为原料,在一 定温度、压力和催化剂存在下,通过F-T合成为烃类燃料油及化工原料和产品的 工艺。包括煤气化制取合成气、催化合成烃类产品以及产品分离和改制加工等过 程。煤炭间接液化技术主要有南非的萨索尔(Sasol)费托合成法、美国的Mobil (甲醇制汽油法)和荷兰SHELL的中质馏分合成(SMDS)间接液化工艺。
缺点: (1)反应条件相对较苛刻。如德国老工艺液化压力甚至高达70MPa。现代工
艺如IGOR、HTI、NEDOL等液化压力也达到17-30MPa。液化温度420—470℃。 (2)煤种适应范围窄。直接液化主要适用于褐煤、长焰煤、气煤、不粘煤、
弱粘煤等年轻煤。 (3)出液化反应器的产物组成较复杂。液、固两相混合物由于粘度较高,分
工业化程度 可以
反应器类型 悬浮床
温度/℃ 压力/MPa
440-450 17
催化剂
GelCaTM
可以 鼓泡床 470 30 炼铝赤泥
用量/%
ቤተ መጻሕፍቲ ባይዱ0.5
3-5%
固液分离方 法 在线加氢 循环溶剂加 氢 工业性试验 规模
临界溶剂萃取 有或无 部分
600t/d
减压蒸馏 有 在线
200t/d
试验煤
神华煤
先锋褐煤
该工艺对美国 HTI 工艺进行了优化。采用两段反应,反应温度 455℃,压力 19MPa,采用人工合成超细铁基催化剂,催化剂用量 1.0%(质量)(Fe/干煤)。 采用较成熟的减压蒸馏进行固液分离,循环溶剂全部加氢。C4 以上油收率为 55% 左右,油品重馏分较多,适宜于柴油产品的生产。
三.煤间接液化与直接液化的比较
1.间接液化工艺
优点: (1)合成条件较温和。无论是固定床、流化床还是浆态床,反应温度均低于
350℃,反应压力2.0—3.0MPa。 (2)转化率高。如SASOL公司SAS工艺采用熔铁催化剂,合成气的一次通过
转化率达到60%以上.循环比为2.0时,总转化率即达90%左右。SheⅡ公司的 SMDS工艺采用钴基催化荆,转化率甚至更高。
(4)固液分离采用成熟可靠的减压蒸馏方式。 (5)加氢采用T-Star工艺。T-Star 工艺溶剂加氢比日本的固定床溶剂加氢和 德国的在线固定床加氢更稳定、操作周期更长 缺点: (1)减压蒸馏,液体油品和固体分离不完全,油品损失多。 (2)相对俄罗斯FFI工艺,反应条件苛刻。 (3)减压阀芯使用寿命短。 (4)不适用于褐煤。
5.神华直接液化技术
优点: (1)催化剂为自主研发,原料国内供给充足,价格便宜,制备工艺简单,操
作稳定。活性高、添加量少。油收率高。 (2)供氢溶剂预加氢,供氢能力强。 (3)强制循环悬浮床反应器具有空塔液速高,矿物质不易沉积;反应温度控
制容易,产品性质稳定;气体滞留系数低,反应器利用率高;有大的高径比,单 系列处理量大等优点
(2)催化剂活性高,用量少。催化剂为胶体铁基催化剂。 (3)液化油收率高。固液分离采用超临界溶剂萃取方法,从液化残渣中最大 限度地回收重油,从而大幅度提高了液化油收率。 (4) 氢耗低。 缺点: (1)用甲苯类溶剂萃取物做循环溶剂使用时,因沥青烯的存在和积累会导致 煤浆粘度上升,使操作出现问题。 (2)相对俄罗斯 FFI 工艺,反应条件苛刻。 (3)工艺不适用于褐煤。
F-T合成的特点是:合成条件较温和,无论是固定床、流化床还是浆态床, 反应温度均低于350℃,反应压力2.0-3.0MPa;转化率高,如SASOL公司SAS工 艺采用熔铁催化剂,合成气的一次通过转化率达到60%以上,循环比为2.0时, 总转化率即达90%左右。
二.煤直接液化介绍
煤的直接液化是煤在适当的温度和压力下,催化加氢裂化生成液体烃类及少 量气体烃,脱除煤中氮、氧和硫等杂原子的转化过程。
该工艺由煤前处理单元、液化反应单元、液化油蒸馏单元及溶剂加氢单元等 4 个主要单元组成。反应压力 17M~19MPa,反应温度为 430~465℃;催化剂采 用合成硫化铁或天然硫铁矿。离线加氢方式。
3.德国煤液化新工艺(IGOR 工艺) 1981 年,德国鲁尔煤矿公司和费巴石油公司对最早开发的煤加氢裂解为液
1.0%
减压蒸馏
减压蒸馏
减压蒸馏
无
有
无
离线
半离线
离线
150t/d
神华煤
89.5 7.3 52.8 28.1 6.1